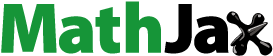
ABSTRACT
This paper introduces a novel hybrid honeycomb (HC) design achieved by continuously blending non-auxetic hexagonal and auxetic re-entrant cell geometries along the out-of-plane direction. These novel hybrid HCs are additively manufactured via fused deposition modelling (FDM) using PA12 polymer reinforced with 15 wt.% of discontinuous carbon fibres. We study the mechanical and piezoresistive performance of hybrid HCs under quasi-static in-plane and out-of-plane loading performed at temperatures ranging between 25-125°C. The results demonstrate significant in-plane compression performance enhancements in the hybrid configuration, achieving up to 43% increase in the collapse strength and 119% in absorbed energy. The incorporation of multiple hybrid layers in the honeycomb structure further enhanced the in-plane properties, ultimately achieving a 181% enhancement in energy absorption. The hybrid honeycombs also showed a pronounced piezoresistive response with gauge factors in the range of 18–37 within the elastic regime, making them suitable for a wide range of multifunctional applications.
1. Introduction
In advanced high-performance engineering applications, there is a need for materials that possess specific combinations of mechanical properties (e.g. stiffness, strength, toughness) while maintaining a low density [Citation1,Citation2]. While some mechanical properties, such as stiffness and strength, can be readily improved simultaneously, several others, such as the interplay between stiffness and toughness or the balance between strength and flexibility, often present conflicting demands. This tradeoff in performance constrains the development of materials that can achieve the desired combination of target properties [Citation3–5].
One possible solution to overcoming the material property tradeoff is the utilisation of lattice structures featuring micro/meso architectural configurations, commonly referred to as architected materials [Citation3,Citation5–7]. Architected lattice structures represent a category of lightweight cellular structures that can be either naturally inspired or rationally designed [Citation8–12]. They offer significant advantages over bulk materials, including low weight, high weight-specific strength and stiffness, and the ability to customise geometrical configurations. Lattice structures hold the potential to provide exceptional performance and functionalities across a wide range of high-performance applications [Citation13–16]. Historically, lattice structures have found most common use in aerospace applications. While these lattice structures can be relatively costly, they are often indispensable. For example, in the case of NASA's Apollo space capsule, a multi-material heatshield incorporating a honeycomb (HC) lattice structure composed of epoxy resin reinforced with fiberglass was employed. This lattice structure featured fail-safe characteristics, eliminating the need for frequent and expensive inspection routines [Citation17].
Recent research has increasingly emphasised the development of high-performance lightweight lattices with multifunctional attributes. These materials are essential for advanced structural applications, offering excellent mechanical properties, while also providing additional functionalities through their electrical, magnetic, thermal, or chemical properties, as referenced in [Citation18–23]. Discontinuous micro-scale electro-conductive fibres (e.g. carbon fibres) are often used to reinforce thermoplastic polymer-based lattice structures, enhancing mechanical properties and forming an electrical percolation network that changes resistance with applied strain, enabling piezoresistive strain and damage sensing [Citation14,Citation24–26]. These reinforcements also possess excellent thermal stability in addition to their superior mechanical characteristics [Citation27]. As a result, incorporating discontinuous fibres into polymers provides a pathway to create versatile engineering composite lattices with enhanced electrical and thermal properties. Additionally, advancements in additive manufacturing techniques, such as material extrusion with high-speed printing processes, have enabled the fabrication of large-size metastructures with efficient electromagnetic absorption and mechanical adaptation [Citation18]. These metastructures have shown promising performance in achieving broadband microwave absorption and effective load-bearing capabilities, making them suitable for a diverse range of applications [Citation21].
Advancements in additive manufacturing (AM) have made it possible to efficiently customise micro/meso architectural configurations and produce them economically [Citation28,Citation29]. This has led to the creation of some of the lightest, most rigid, and strongest materials currently in existence. By employing intricate architectural designs, lattice structures manufactured through additive manufacturing have managed to overcome the traditional trade-off between strength and toughness [Citation30,Citation31]. Techniques like density or configuration grading within these lattices have been suggested to control deformation modes and enhance energy absorption [Citation32,Citation33]. Biomimetic approaches, such as staggered and co-continuous composites, have enabled the development of stiffer yet tougher materials [Citation34]. Some studies in the literature have explored the concept of functionally graded cellular materials (FGCMs) to achieve simultaneous enhancements in stiffness and toughness [Citation3,Citation34]. There is a growing interest in incorporating multiple materials into lattice structures to leverage load-bearing and toughening mechanisms, which has been a well-established practice [Citation35]. Despite several initiatives aimed at enhancing multi-material lattices through hierarchical geometries and innovative cell configurations, there is an ongoing need to economically develop materials that are simultaneously stiffer, stronger, and tougher [Citation17,Citation29].
Some researchers have explored hybrid lattice configurations consisting of two or more types of similar unit cells, whether auxetic or non-auxetic, which have demonstrated superior strength and/or energy-absorption properties compared to homogeneous counterparts [Citation36–38]. While many prior studies have focused on optimising single lattice architectures, there is a growing interest in multi-architected lattices, driven by advancements in additive manufacturing (AM) capabilities that enable the fabrication of such configurations. For example, combining bend-dominated and stretch-dominated elementary structures within a lattice can result in an exceptional balance of strength and toughness [Citation37,Citation39]. In architectural hybridisation, achieving interfacial compatibility between different configurations is of paramount importance. The mechanical behaviour of multi-architected lattices is closely linked to the interfacial compatibility between elementary lattices, as mechanical stress is transmitted across these interfaces. Interfaces between mechanically dissimilar elementary structures can inherently introduce weak points prone to fracture, potentially diminishing the material's mechanical performance [Citation14,Citation40–44].
This study leverages AM technology to precisely realise a continuous transition between dissimilar honeycomb cells by cross-sectional blending, thereby promoting effective load transfer throughout the structure and a controlled progression of damage. To the best of our knowledge, these continuously blended hybrid honeycomb structures are investigated for the first time in this study, representing a novel approach in honeycomb design aimed at achieving enhanced mechanical properties by seamlessly blending different types of unit cell architectures along the out-of-plane direction. Unlike traditional hybrid configurations consisting of discrete layers of different unit cells, continuously blended hybrid honeycombs feature a smooth transition between the constituent cell architectures, thus mitigating stress concentrations at the interface [Citation45,Citation46]. Specifically, this paper explores the hybridisation of hexagonal and re-entrant honeycomb architectures to leverage the complementary mechanical behaviours of both lattice topologies. Hexagonal honeycombs typically exhibit an extended stress plateau during in-plane compression due to their non-auxetic behaviour, expanding laterally and allowing cell walls to pack closely without a significant increase in applied load. In contrast, re-entrant honeycombs incorporate inward-pointing cell walls which result in auxetic behaviour under in-plane compression [Citation47]. While re-entrant honeycombs often show higher elastic modulus and yield stress, their inward-pointing cell walls tend to get into contact at lower macroscopic strains, thus shortening the stress plateau and limiting their energy absorption capacity [Citation14,Citation48]. By combining the favourable attributes of the hexagonal honeycomb, such as the extended stress plateau and higher densification strain, with the attractive strength and stiffness properties of the re-entrant honeycomb, the hybrid structure promises to offer a beneficial balance between strength and energy absorption [Citation41,Citation45]. Herein, the continuously blended hybrid honeycombs are additively manufactured via fused filament fabrication (FFF) utilising PA12 polymer filaments reinforced with 15 wt.% short carbon fibres. The present study systematically examines the quasi-static in-plane and out-of-plane compression performance, as well as the piezoresistive self-sensing behaviour of the fabricated hybrid honeycombs at room and elevated temperatures. Furthermore, this research provides insight into how the incorporation of multiple hybrid layers can influence the mechanical properties of the structure, thus adding another dimension to the hybrid design options.
2. Experimental procedure
2.1. Materials
The honeycomb samples were 3D printed using filament feedstocks composed of polyamide-12 (PA12) reinforced with discontinuous carbon fibres (CF), having a diameter of 1.75 mm. These filaments were supplied by Fiberlogy, Poland. Specifically, we worked with PA12 filaments with varying reinforcement levels: pure PA12 (referred to as PA12), and PA12 with 15 wt.% CF (referred to as CF/PA12). Note that the weight fraction of fibres in the filament was measured via Thermogravimetric Analysis (TGA), and the obtained values were in close agreement with the nominal values quoted by the supplier (see section S2.1, Supplementary Material). Detailed information regarding the properties of these PA12-based filaments can be found in Table S1 (refer to Supplementary Material sourced from the manufacturer's datasheet).
2.2. Additive manufacturing via fused filament fabrication (FFF) 3D printing
The proposed lattice structures were fabricated utilising a Fused Filament Fabrication (FFF) 3D printer, specifically, the Creator 3 model from Zhejiang Flashforge 3D Technology Ltd. Molten filament feedstocks were extruded through a 0.4 mm diameter nozzle, and the printing process was configured and GCode was generated using FlashPrint software (version 5.1.0). The specific FFF process parameters used for 3D printing various material systems are outlined in Table S2 (as per the recommendations of the material supplier).
In this investigation, we initially examined three distinct honeycomb configurations, as illustrated in . These configurations comprised a 4 × 3 array of unit cells and encompassed two elementary honeycomb structures, specifically the hexagonal and re-entrant cell arrays, along with a hybrid structure combining hexagonal and re-entrant elements, referred to as hybrid cell arrays. The hybrid lattices featured an arrangement where hexagonal and re-entrant unit cells were alternated and continuously blended, as depicted in . Subsequently, we manufactured multi-layered hybrid honeycomb structures with options for 2, 4, and 8 hybrid layers. These honeycomb samples, whether elementary, hybrid, or multi-layered, shared identical overall dimensions, measuring 40 mm in length, 35 mm in width, and 23 mm in height. The relative density () was consistently set at 20%. Consequently, variations in the thickness of the ligaments among different honeycomb types were dictated by the volume of cell walls within each lattice. For specific details regarding cell-wall thickness and unit cell dimensions across the various honeycomb samples, the reader is referred to Table S3 in the Supplementary Material.
Figure 1. Geometric models and representative printed samples: hexagonal (top row), re-entrant (second row), hybrid (hexagonal/re-entrant – third row) and multi-layer lattices (bottom row), all with a relative density of 20%. Samples printed using CF/PA12 are shown for illustration.
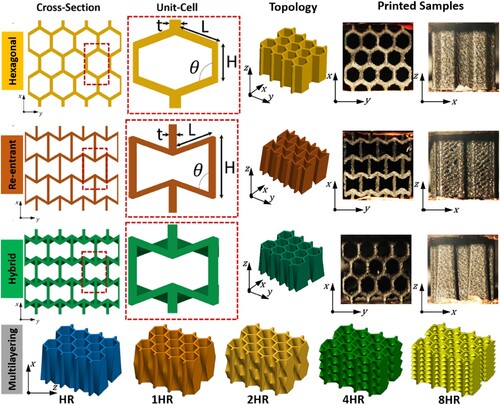
To comprehensively assess the tensile and compressive properties of the bulk materials, we also manufactured bulk specimens with standard dimensions (further details are given in ). Section S2 of the Supplementary Material provides a summary of the material characterisation data, including thermogravimetric analysis (TGA), differential scanning calorimetry (DSC), and microstructure analysis (μCT), as well as mechanical test results for the bulk specimens. The final weights of the elementary, hybrid, and multi-layered samples are listed in Table S4 (Supplementary Material).
Table 1. ASTM standard, dimensions, crosshead speed, and other parameters used to characterise the quasi-static tensile and compressive properties of the 3D printed PA12, and CF/PA12.
2.3. Quasi-static mechanical tests
We conducted quasi-static compression tests to evaluate the crushing behaviour of the honeycomb structures under both in-plane and out-of-plane loading. These tests were carried out using an Instron universal testing machine (UTM) with a maximum load capacity of 50 kN. An environmental chamber was used to maintain isothermal conditions during the compression tests with the chamber temperature set to 25, 75, and 125°C. To ensure that the specimens reached their steady-state temperature, the samples were kept in the environmental chamber for a duration of 30 min prior to testing. Herein, the temperatures of 75°C and 125°C were chosen below the melting temperature of PA12 (Tm = 178°C, see supplementary Table S1) but above the glass transition temperature (typically between 50 and 60°C [Citation49]) to examine the thermal softening behaviour of the honeycomb structures. Note that temperatures greater than 125°C resulted in excessive softening of the material and caused the material to adhere to the compression platens of the UTM, thus rendering the accurate evaluation of mechanical and piezoresistive responses difficult.
The real-time piezoresistivity of the cellular samples was recorded using a data-logging multimeter (DMM 4050 digital multimeter, Tektronix, USA) with a measurement range spanning from 10 Ω to 1 GΩ and a resolution of 10 µΩ. Electrical contact was established through two copper electrodes positioned between the sample and the loading platens, serving as the interface for electrical connectivity. Note that the loading platens were covered with a thin layer of insulating tape. The multimeter probes were directly attached to the copper electrodes, and the electrical resistance was measured using the two-electrode method. The gauge factor, denoted as , was employed to quantify the piezoresistive sensitivity of the sample with respect to a given strain increment,
[Citation14]:
(1)
(1) where ϵ is the mechanical strain, R0 is the initial zero-load resistance, R is the resistance, and ΔR = R – R0.
To capture the deformation characteristics of the honeycombs, we utilised a DSLR camera (Nikon D5300) to record videos at a resolution of 256 × 112 pixels, operating at a frame rate ranging from 40 to 50 μs per frame. The specifics of the dimensions, crosshead speed, and the ASTM standard adhered to for testing both bulk and cellular samples are outlined in . We manufactured and tested three samples for each configuration to ensure that the measurements are consistent and reliable.
3. Results and discussion
3.1. Effect of cell topology on in-plane compressive response
3.1.1. Mechanical response and energy absorption characteristics
(a) shows typical stress–strain curves acquired from in-plane compression experiments performed on CF/PA12 elementary (hexagonal and re-entrant) and hybrid honeycombs. Here, the stress σ was obtained by dividing the measured force (F) by the projected area (Ap) of the sample (40 × 23 mm2), , while the strain ϵ is defined as the ratio of the measured cross-head displacement (δ) over the initial sample height (h = 35 mm),
. The stress–strain curves are accompanied by selected photographs (see (b)) that display frontal perspectives of the deformation at different stages of loading. The quasi-static compression responses of the three cellular structures exhibit similar patterns. In all cases, the stress–strain curve shows an initial peak followed by a plateau, culminating in a rapid ascent attributed to densification.
Herein, several metrics are employed to assess the compression performance of the honeycomb structures; these encompass elastic modulus, initial collapse stress, densification strain and absorbed energy. The absorbed energy (Ea) was calculated through an integration procedure [Citation28]:
(2)
(2) where V is the volume enclosing the boundaries of the sample (40 × 35 × 23 mm3), and
is the densification strain. In line with previous studies (see e.g. [Citation50]),
was taken as the strain where the energy absorption efficiency
attains a global maximum (see Figure S4, Supplementary Material), where
is defined as
(3)
(3) Here,
is the compressive stress induced in the honeycomb at a strain ϵ, and
is the peak compressive stress within the strain range [0, ϵ].
(c–f) present the in-plane elastic moduli, initial collapse stresses, densification strains, and absorbed energies of the elementary and hybrid honeycomb structures (deduced from the stress–strain curves in (a)). The re-entrant HC shows the highest elastic modulus (see (c)) and experiences a more significant decline in stress following the initial peak load (see (a)). During the subsequent collapse phase, notable fluctuations in stress are observed in the stress–strain response of the re-entrant HC. This can be explained by the greater volume of vertical ligaments in the re-entrant HC, which deform in the stretching mode and are therefore prone to buckling. However, the re-entrant HC shows the lowest densification strain among all configurations considered (see (e)) which significantly curtails its energy absorption capacity (see (f)). The accompanying photographs show that rapid strain hardening commences in the re-entrant HC (refer to frame B in (b)) before all the cells have fully collapsed, due to the presence of the re-entrant corners that confer auxetic behaviour to the structure [Citation14]. Among the three topologies, the hexagonal honeycomb exhibits the longest stress plateau (see (b)) and the highest densification strain (see (e)). This behaviour can be explained by the fact that the hexagonal HC is non-auxetic under in-plane loading and therefore expands in the lateral direction during compression, which gives the collapsing cell walls enough space to pack together closely without a significant increase in the applied load (see (b)). However, the relatively low collapse stress of the hexagonal HC (see (d)) greatly limits its energy absorption capacity, as seen from (f).
The hybrid HC shows an initial collapse stress and densification strain comparable to those of its re-entrant counterpart (see (d–e)), but exhibits a relatively flat stress plateau during the collapse phase (see (a)), which is highly favourable for effective energy absorption. Consequently, the energy absorption capacity of the hybrid HC is ∼42% higher than that of the re-entrant HC (see (f)). As seen from the photographs in (b), the hybrid HC shows nearly uniform deformation across all cell layers during the initial phase of loading, which contributes to a steady and progressive collapse during the plateau stage. These observations can be attributed to the opposing lateral deformations of the non-auxetic hexagonal and auxetic re-entrant cell topologies in the hybrid HC, effectively delaying the plastic collapse of the HC cells.
3.1.2. Piezoresistive response
(a) shows the strain-dependent changes in of CF/PA12 hexagonal, re-entrant, and hybrid HCs under in-plane compressive loading. It's notable that, as the compressive strain increases,
consistently decreases for all the samples, implying a reduction in electrical resistance with growing compressive deformation.
Figure 3. In-plane piezoresistive responses of hexagonal, re-entrant and hybrid CF/PA12 HCs: (a) typical ΔR/R0 vs. strain curves, and (b) gauge factors evaluated within the elastic regime (0 ≤ ϵ ≤ 0.2%).
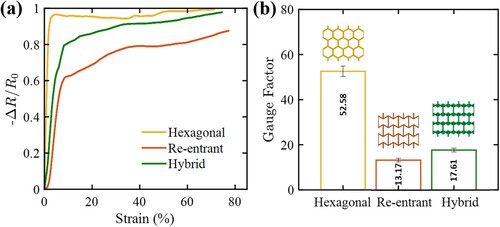
The curves exhibit a rapid decline during the elastic phase, followed by a more gradual decrease during the collapse phase. It is also seen that the hexagonal HC approaches a limiting value of
at large compressive strains, indicating a complete loss of electrical resistance. The decreasing electrical resistance under compressive loading is primarily attributed to two key mechanisms [Citation14,Citation51,Citation52]: (i) the intrinsic piezoresistivity of the CF/PA12 composite material which shows similar trends, as demonstrated in Figure S3c (Supplementary Material), and (ii) the increasing number of contacts established between the crushed cell walls of the honeycomb structure, resulting in the formation of new conducting channels in the percolated network and thus contributing to a reduction in electrical resistance. (b) presents the corresponding gauge factors (
) evaluated within 0 ≤ ϵ ≤ 0.2% for all samples using Eq. (1). (b) reveals the hexagonal HC possesses the highest gauge factor k = 52.58, followed by the hybrid (17.61) and re-entrant (13.17) ones. This result suggests that the incorporation of the auxetic re-entrant topology into the hybrid HC reduces the piezoresistive sensitivity of the structure within the elastic phase.
3.2. Effect of temperature on in-plane response
Based on the aforementioned results from diverse topologies, it is evident that the hybrid HC exhibits the most impressive in-plane compression performance. Consequently, we now embark on the examination of the temperature-dependent mechanical and piezoresistive characteristics of hybrid HCs under in-plane compression.
3.2.1. Mechanical response and energy absorption characteristics
(a) illustrates the stress–strain curves of CF/PA12 hybrid HCs at three distinct temperatures (25, 75, and 125°C). As the temperature rises from 25 to 125°C, the CF/PA12 structures display a characteristic thermal softening behaviour, marked by a substantial decrease in both elastic modulus and strength. The latter decline in the mechanical properties occurs mainly between 25 to 75°C; a further increase in temperature to 125°C reduces the latter properties only slightly. We observed comparable trends for the PA12 honeycombs, as can be seen in Figure S5 (Supplementary Material).
Figure 4. Temperature effect on the in-plane compressive response of hybrid CF/PA12 HC lattices: (a) typical stress-strain curves at 25, 75 and 125°C; (b–d) compressive properties at various temperatures.
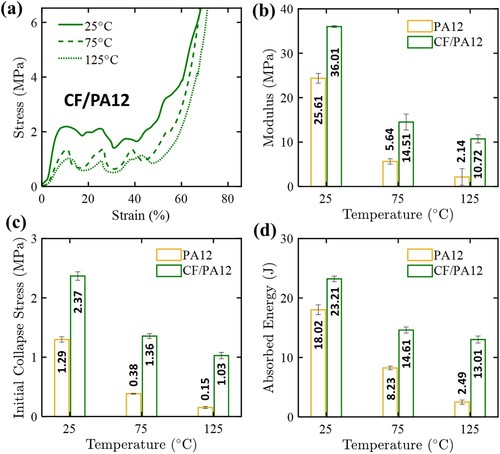
(b–d) illustrates the modulus, strength, and absorbed energy of hybrid HCs made of PA12, and CF/PA12 at different temperatures. Among these samples, the CF/PA12 HCs consistently show the highest modulus, strength, and absorbed energy across all tested temperatures, followed by the PA12 samples. Furthermore, these properties abruptly decrease as the temperature increases because the enhanced chain mobility in the PA12 matrix beyond the glass transition temperature ( = 38.43°C, refer to Figure S1b in the Supplementary Material) weakens the interactions between the molecular chains [Citation53,Citation54].
Figure S6 in the Supplementary Material displays SEM images of the fracture surfaces of the collapsed CF/PA12 honeycombs. The samples tested at 75 and 125°C exhibit indications of fibre/matrix debonding and fibre pull-out, implying that the interfaces between the fibres and matrix were weakened at elevated temperatures. Conversely, the samples tested at 25°C did not show any signs of fibre/matrix debonding. Instead, numerous fibres were observed protruding from the fracture surface, indicating that fibre pull-out and breakage were the primary failure mechanisms at this temperature.
3.2.2. Piezoresistive behaviour
In (a), the normalised variations in electrical resistance () are illustrated as functions of strain, with measurements taken at 25, 75, and 125°C for hybrid CF/PA12 HCs. The 3D printed HCs displayed notable thermoresistive characteristics (see (b)), characterised by a steady decrease in the zero-load resistances (
) with increasing temperature; at 125°C,
was 28.57% lower than at room temperature (25°C). In networks of short carbon fibres that form percolating paths, the conductance of both hopping and migrating electrons increases as the temperature rises [Citation55]. This increase in conductance results in a decrease in electrical resistance.
Figure 5. Effect of temperature on the piezoresistive response of CF/PA12 hybrid HC lattices under in-plane compression: (a) typical vs. strain responses for CF/PA12 honeycombs at 25, 75 and 125°C and (b) the measured zero load resistance and gauge factor corresponding to the elastic response (within 0 ≤ ϵ ≤ 0.2%).
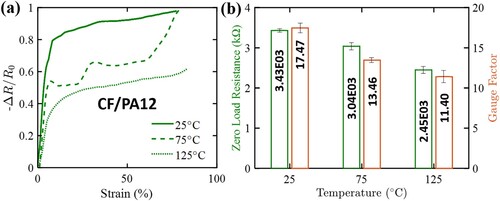
The gauge factors () corresponding to the initial elastic response (0 ≤ ϵ ≤ 0.2%) are illustrated in (b), showing a steady decrease with rising temperature. This decrease can be attributed to the fact that an increase in temperature generally augments the conductance of electrons within the percolating network. Consequently, larger macroscopic strains are necessary to produce a specific alteration in electrical resistance, leading to diminished strain sensitivity.
3.3. Effect of multi-layering on the in-plane response
We embarked on a detailed investigation of multi-layering, aiming to improve the compressive performance of hybrid HCs under in-plane loading. To ensure fairness in comparison, the overall relative density for the multi-layer HCs was kept constant (20%). (a) presents characteristic stress–strain curves of the multi-layered hybrid HCs (1HR, 2HR, 4HR, and 8HR) acquired from in-plane compression tests, while (b–d) provide a comparison of the measured in-plane elastic moduli, initial collapse stresses, and absorbed energies. It is interesting to note that the latter properties increase as the number of layers rises from 0 to 4, reporting enhancements of 115.7%, 22.4%, and 47.2% in the elastic modulus, collapse stress and absorbed energy, respectively. When more layers are added, however, these properties are seen to decline. These observations can be explained by analyzing the stress–strain responses in (a), where the multi-layered hybrid HCs with up to 4 layers (1HR, 2HR, 4HR) show more distinct load drops following the initial stress peaks as compared to the single-layer hybrid HC (HR). These trends suggest that the first layer in these hybrid HCs collapsed suddenly by fast fracture of cell walls [Citation3], similar to what was observed for the re-entrant HC in . The latter failure mode is promoted by the more robust constraints on the in-plane deformation stemming from the presence of multiple layers in the hybrid HC structure. Following the initial load drop, the stress–strain curve swiftly rebounds to a higher level, indicating that the resistance against structural collapse increases after the first layer has failed. Notably, the 4HR structure demonstrates the most pronounced load recovery, evinced by the highest plateau peak stress. In contrast, when the number of layers further increases to 8, both the elastic modulus and the peak stress at the point of first collapse decline significantly, and this is followed by a relatively stable stress plateau that terminates at the onset of densification (see (a)). This observation suggests that the 8HR structure collapsed in a more stable manner by folding of the cell walls (rather than sudden fracture or fragmentation), similar to what was observed for the hexagonal HC in . This behaviour allows the 8HR structure enter the densification phase at a lower strain of around 40% which negatively affects its energy absorption capacity.
Figure 2. In-plane quasi-static compressive responses of hexagonal, re-entrant and hybrid CF/PA12 HCs: (a) typical stress-strain curves along with (b) photographs showing the deformation profiles at selected strain levels; (c-f) bar charts comparing the elastic moduli, collapse stresses, densification strains and absorbed energies of the three HC topologies.
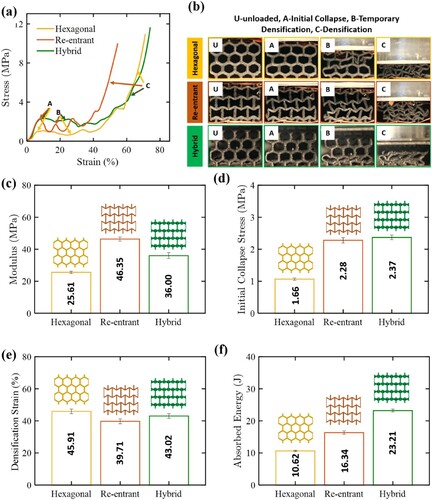
3.4. Effect of cell topology on out-of-plane compressive response
3.4.1. Mechanical response and energy absorption characteristics
(a) shows typical stress–strain curves acquired from out-of-plane compression tests performed on CF/PA12 elementary (hexagonal and re-entrant) and hybrid honeycombs. (b) presents photographs of the deformation profiles during specific loading phases, showing the initiation and progression of damage with increasing out-of-plane compression. All samples exhibit an ascent in the stress–strain curve leading to an initial peak, followed by a plateau region and a sharp increase in stress attributed to densification, similar to what is observed under in-plane compression (see (a)).
Figure 7. Out-of-plane compressive responses of hexagonal, re-entrant and hybrid CF/PA12 HCs: (a) typical stress-strain curves along with (b) photographs showing the deformation profiles at selected strain levels; (c–f) bar charts comparing the elastic moduli, collapse stresses, densification strains and absorbed energies of the three HC topologies.
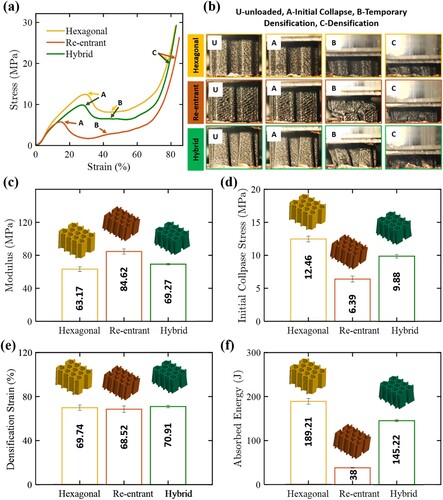
The bar charts presented in (c–f) provide a summary of the measured in-plane elastic moduli, initial collapse stresses, densification strains, and absorbed energies of the three HC topologies. Under compression, the differences in mechanical response among various honeycomb configurations arise from their distinct structural features and deformation mechanisms. The re-entrant honeycombs exhibit the highest elastic modulus of ∼84.62 MPa, followed by the hybrid and hexagonal HCs with ∼ 69.27 and 63.17 MPa, respectively. This result suggests that the auxetic behaviour of the re-entrant HC imposes a strong constraint on the out-of-plane deformation during the elastic phase [Citation14], which mirrors the trends obtained for in-plane compression (see (c)). In contrast, the re-entrant honeycomb shows the lowest peak stress at the point of collapse, which is followed by a pronounced load drop. The observed differences in the out-of-plane compression performance of various honeycomb configurations arise from their distinct structural features and collapse mechanisms. As seen from the photographs presented in (b), the re-entrant HC collapses by an antisymmetric deformation mechanism, which results in a sudden loss of load-carrying capacity. The inward-pointing cell walls of the re-entrant honeycomb may lead to localised stress concentrations and buckling, resulting in a sudden loss of load-carrying capacity. Both the hexagonal and hybrid honeycombs collapse in a more stable manner by bulging of cell walls ((b)), which allows these structures to sustain higher peak loads (see (d)) and absorb a greater amount of energy (see (f)). The distinct collapse mechanisms observed in (b) illustrate how subtle variations in honeycomb topology can significantly alter the mechanical behaviour, underscoring the importance of topology selection in the design of lattice structures. Further, it should be noted that the hybrid HC collapses at a lower load and absorbs less energy than its hexagonal counterpart. This can be explained by the presence of corrugated cell walls in the hybrid HC, which attract bending stresses under axial loading that ultimately limit structural efficiency.
Based on the experimental results presented in this section, we conclude that the hexagonal honeycombs exhibit superior out-of-plane compression performance compared to the hybrid and re-entrant honeycombs. While the hybridisation effect doesn't offer significant advantages under out-of-plane loads, the hybrid HC offers far superior strength and energy absorption attributes as compared to the re-entrant HC, and can compete with the conventional hexagonal HC in terms of elastic modulus (+10%), collapse stress (−30%) and energy absorption (−23%).
3.4.2. Topology effect on out-of-plane piezoresistive behaviour
(a) shows the strain-dependent changes in of hexagonal, re-entrant and hybrid CF/PA12 HCs under out-of-plane compressive loading. We observe a steep decline in the
values during the elastic stage, followed by the emergence of a clear
plateau as the structure undergoes collapse. In certain instances, this plateau tends to approach the theoretical limit of −1 (complete loss of resistance) as the macroscopic deformation nears the point of densification. The corresponding gauge factors (k) evaluated within the elastic regime (0 ≤ ϵ ≤ 0.2%) are plotted in (b). It is notable that the hexagonal HCs show the highest gauge factor of 42.51, followed by the hybrid (37.34) and re-entrant (18.91) structures in descending order. Similar trends were observed for in-plane loading, as detailed in section 3.1.2.
4. Conclusion
This paper introduces a novel hybrid structure fabricated via FDM additive manufacturing, combining non-auxetic hexagonal and auxetic re-entrant lattice features in a seamless manner. We employed Polyamide-12 (PA12) reinforced with 15% carbon fibres (CF) for 3D printing and systematically studied the in-plane and out-of-plane compression performance and piezoresistive self-sensing behaviour of the hybrid honeycombs under quasi-static loading conditions. Additionally, we studied the multifunctional properties of the hybrid HCs at elevated temperatures up to 125°C, and explored the effect of multi-layering on their compressive response.
It was found that the geometric hybridisation of the honeycomb structures considerably improved their in-plane compression performance, reporting enhancements in elastic modulus, collapse strength and energy absorption of 40%, 43% and 119%, respectively, when compared to conventional hexagonal honeycombs of equal mass. This impressive performance was accredited to the opposing lateral deformations of the non-auxetic hexagonal and auxetic re-entrant cell topologies in the hybrid honeycomb, effectively delaying the plastic collapse of the cell layers and contributing to a stable collapse response. Moreover, the incorporation of multiple hybrid layers in the honeycomb structure further enhanced the in-plane properties as long as the number of layers was four or less. At elevated temperatures, the in-plane properties of the hybrid CF/PA12 HCs significantly declined by ∼ 50–70% when heated up to 125°C due to weakening molecular interactions in the PA12 matrix which led to extensive fibre/matrix debonding and fibre pull-out. Under out-of-plane loading, the collapse strength and energy absorption of the hybrid honeycomb were found to be slightly lower than that of the conventional hexagonal honeycomb (by 30 and 23%, respectively) due to the bending stresses induced in the corrugated cell walls of the hybrid structure, limiting structural efficiency.
Regarding the piezoresistive performance, the gauge factor of the hybrid CF/PA12 honeycomb was found to be lower than the hexagonal one, but higher than its re-entrant counterpart under both in-plane and out-of-plane loading. The hybrid honeycombs showed gauge factors in the range of 18–37 within the elastic regime, which renders them suitable for detecting small changes in the applied load, opening the door for a diverse range of multifunctional applications.
Author contributions
Jefferson Andrew J: Conceptualisation, Methodology, Formal analysis, Data curation, Investigation, Writing – original draft. Kamran A Khan: Supervision, Funding acquisition, Writing – review & editing. Rehan Umer: Writing – review & editing, Supervision. Andreas Schiffer: Conceptualisation, Writing – review & editing, Supervision, Resources, Funding acquisition.
Supplemental Material
Download MS Word (4.2 MB)Acknowledgements
The authors acknowledge the help of Pradeep George from Khalifa University of Science and Technology. The XCT scan tasks in this work were conducted at the Advanced Research and Innovation Center (ARIC), which is funded by STRATA Manufacturing PJSC (a Mubadala company) and Khalifa University of Science and Technology. This publication is based on work supported by the Khalifa University of Science and Technology under Award No. CIRA-2021-109 / 8474000423. This work was partially funded by ASPIRE, the technology program management pillar of Abu Dhabi’s Advanced Technology Research Council (ATRC), via the ASPIRE Award for Research Excellence [grant number: AARE19-148].
Disclosure statement
No potential conflict of interest was reported by the author(s).
Data availability statement
The data will be made available on request.
Additional information
Funding
References
- Jiao P, Mueller J, Raney JR, et al. Mechanical metamaterials and beyond. Nat Commun. 2023;14(1):6004. doi:10.1038/s41467-023-41679-8
- Ha CS, Yao D, Xu Z, et al. Rapid inverse design of metamaterials based on prescribed mechanical behavior through machine learning. Nat Commun. 2023;14(1):5765. doi:10.1038/s41467-023-40854-1
- Schneider JAJ,J, Schiffer A, Hafeez F, et al. Dynamic crushing of tailored honeycombs realized via additive manufacturing. Int J Mech Sci. 2022;219:107126. doi:10.1016/j.ijmecsci.2022.107126
- Andrew JJ, Ubaid J, Hafeez F, et al. Impact performance enhancement of honeycombs through additive manufacturing-enabled geometrical tailoring. Int J Impact Eng. 2019;134:103360. doi:10.1016/j.ijimpeng.2019.103360
- Jia Z, Yu Y, Wang L. Learning from nature: use material architecture to break the performance tradeoffs. Mater Des. 2019;168:107650. doi:10.1016/j.matdes.2019.107650
- Jia Z, Liu F, Jiang X, et al. Engineering lattice metamaterials for extreme property, programmability, and multifunctionality. J Appl Phys. 2020;127(15).
- Vangelatos Z, Komvopoulos K, Grigoropoulos CP. Regulating the mechanical behavior of metamaterial microlattices by tactical structure modification. J Mech Phys Solids. 2020;144:104112. doi:10.1016/j.jmps.2020.104112
- Mistry Y, Weeger O, Morankar S, et al. Bio-inspired selective nodal decoupling for ultra-compliant interwoven lattices. Commun Mater. 2023;4(1):35. doi:10.1038/s43246-023-00363-6
- Andrew JJ, Verma P, Kumar S. Impact behavior of nanoengineered, 3D printed plate-lattices. Mater Des. 2021;202:109516. doi:10.1016/j.matdes.2021.109516
- Jia Z, Chen H, Deng Z, et al. Architected microlattices for structural and functional applications: Lessons from nature. Matter. 2023;6(4):1082–1095. doi:10.1016/j.matt.2023.01.017
- Chen Y, Mai Y-W, Ye L. Perspectives for multiphase mechanical metamaterials. Mater Sci Eng R Rep. 2023;153:100725. doi:10.1016/j.mser.2023.100725
- Yu H, Zhang J, Zhang S, et al. Bionic structures and materials inspired by plant leaves: a comprehensive review for innovative problem-solving. Prog Mater Sci. 2023;139:101181. doi:10.1016/j.pmatsci.2023.101181
- Surjadi J, Gao L, Du H, et al. Mechanical metamaterials and their engineering applications, Adv Eng Mater. 2019;21.
- Andrew JJ, Alhashmi H, Schiffer A, et al. Energy absorption and self-sensing performance of 3D printed CF/PEEK cellular composites. Mater Des. 2021;208:109863. doi:10.1016/j.matdes.2021.109863
- Sinha P, Mukhopadhyay T. Programmable multi-physical mechanics of mechanical metamaterials. Mater Sci Eng R Rep. 2023;155:100745. doi:10.1016/j.mser.2023.100745
- Gao J, Cao X, Xiao M, et al. Rational designs of mechanical metamaterials: Formulations, architectures, tessellations and prospects. Mater Sci Eng R Rep. 2023;156:100755. doi:10.1016/j.mser.2023.100755
- Le VT, Ha NS, Goo NS. Advanced sandwich structures for thermal protection systems in hypersonic vehicles: A review. Compos Part B Eng. 2021;226:109301. doi:10.1016/j.compositesb.2021.109301
- Zhang Y, Zhao P, Lu Q, et al. Functional additive manufacturing of large-size metastructure with efficient electromagnetic absorption and mechanical adaptation. Compos A Appl Sci Manuf. 2023;173:107652. doi:10.1016/j.compositesa.2023.107652
- An Z, Huang Y, Zhang R. High-temperature multispectral stealth metastructure from the microwave-infrared compatible design. Compos Part B Eng. 2023;259:110737. doi:10.1016/j.compositesb.2023.110737
- Lei H, Shan M, Zhang Y, et al. Design-manufacturing-evaluation integration of microwave absorbing metastructures based on additive manufacturing. Compos Sci Technol. 2023;243:110270. doi:10.1016/j.compscitech.2023.110270
- Zhang Y, Xu Y, Yu C, et al. Electromagnetic functionalization of mechanical lattice to metastructure with oblique incident broadband microwave absorption. Compos Sci Technol. 2023;244:110308. doi:10.1016/j.compscitech.2023.110308
- Li J, Fang L, Sun B, et al. Review—Recent Progress in Flexible and Stretchable Piezoresistive Sensors and Their Applications. J Electrochem Soc. 2020;167(3):037561. doi:10.1149/1945-7111/ab6828
- Gibson RF. A review of recent research on mechanics of multifunctional composite materials and structures. Compos Struct. 2010;92(12):2793–2810. doi:10.1016/j.compstruct.2010.05.003
- Sharma S, Verma A, Rangappa SM, et al. Recent progressive developments in conductive-fillers based polymer nanocomposites (CFPNC's) and conducting polymeric nanocomposites (CPNC's) for multifaceted sensing applications. J Mater Res Technol. 2023;26:5921–5974. doi:10.1016/j.jmrt.2023.08.300
- Zhao T, Lu M, Mei H, et al. Tetrachiral honeycomb regulated polymer-derived SiFeOC ceramics with tunable piezoresistive effect. Carbon N Y. 2023;210:118076. doi:10.1016/j.carbon.2023.118076
- Shi X, Zhu Y, Fan X, et al. An auxetic cellular structure as a universal design for enhanced piezoresistive sensitivity. Matter. 2022;5(5):1547–1562. doi:10.1016/j.matt.2022.02.022
- Sajjad U, Rehman T-U, Ali M, et al. Manufacturing and potential applications of lattice structures in thermal systems: A comprehensive review of recent advances. Int J Heat Mass Transfer. 2022;198:123352. doi:10.1016/j.ijheatmasstransfer.2022.123352
- Andrew JJ, Schneider J, Ubaid J, et al. Energy absorption characteristics of additively manufactured plate-lattices under low- velocity impact loading. Int J Impact Eng. 2021;149:103768. doi:10.1016/j.ijimpeng.2020.103768
- Laguna OH, Lietor PF, Godino FJI, et al. A review on additive manufacturing and materials for catalytic applications: Milestones, key concepts, advances and perspectives. Mater Des. 2021;208:109927. doi:10.1016/j.matdes.2021.109927
- Babamiri BB, Barnes B, Soltani-Tehrani A, et al. Designing additively manufactured lattice structures based on deformation mechanisms. Addit Manuf. 2021;46:102143. doi:10.1016/j.addma.2021.102143
- Lu C, Hsieh M-T, Huang Z, et al. Architectural design and additive manufacturing of mechanical metamaterials: a review, Engineering. 2022;17.
- Ozdemir Z, Hernandez-Nava E, Tyas A, et al. Energy absorption in lattice structures in dynamics: Experiments. Int J Impact Eng. 2016;89:49–61. doi:10.1016/j.ijimpeng.2015.10.007
- Zhou S, Liu H, Ma J, et al. Deformation behaviors and energy absorption characteristics of a hollow re-entrant auxetic lattice metamaterial. Aerosp Sci Technol. 2023;142:108583. doi:10.1016/j.ast.2023.108583
- Shu X, Mao Y, Lei M, et al. Toughness enhancement of honeycomb lattice structures through heterogeneous design. Mater Des. 2022;217:110604. doi:10.1016/j.matdes.2022.110604
- White BC, Garland A, Alberdi R, et al. Interpenetrating lattices with enhanced mechanical functionality. Additive Manufacturing. 2021;38:101741. doi:10.1016/j.addma.2020.101741
- J. Zhang, G. Lu, Z. You. Large deformation and energy absorption of additively manufactured auxetic materials and structures: A review. Compos Part B Eng. 2020;201:108340. doi:10.1016/j.compositesb.2020.108340
- Dutta S, Menon HG, Hariprasad MP, et al. Study of auxetic beams under bending: a finite element approach. Mater Today Proc. 2021;46:9782–9787. doi:10.1016/j.matpr.2020.10.479
- Zhang Z, Tian Z, Mei Y, et al. Shaping and structuring 2D materials via kirigami and origami. Mater Sci Eng R Rep. 2021;145:100621. doi:10.1016/j.mser.2021.100621
- Verma S, Yang C-K, Lin C-H, et al. Additive manufacturing of lattice structures for high strength mechanical interlocking of metal and resin during injection molding. Addit Manuf. 2022;49:102463. doi:10.1016/j.addma.2021.102463
- Wu W, Xia R, Qian G, et al. Mechanostructures: Rational mechanical design, fabrication, performance evaluation, and industrial application of advanced structures. Prog Mater Sci. 2023;131:101021. doi:10.1016/j.pmatsci.2022.101021
- Gao Z, Wang H, Sun H, et al. Additively manufactured high-energy-absorption metamaterials with artificially engineered distribution of bio-inspired hierarchical microstructures. Compos B Eng. 2022;247:110345. doi:10.1016/j.compositesb.2022.110345
- Dwyer CM, Carrillo JG, De la Peña JAD, et al. Impact performance of 3D printed spatially varying elastomeric lattices. Polymers (Basel). 2023;15(5):1178. doi:10.3390/polym15051178
- Xu'Loker Z, la Mendola I, Razavi N, et al. Additive manufactured triply periodical minimal surface lattice structures with modulated hybrid topology. Eng Struct. 2023;289:116249. doi:10.1016/j.engstruct.2023.116249
- Levente S, Horváth R, Rádics J. Design and Study of Fractal-Inspired Metamaterials with Equal Density Made from a Strong and Tough Thermoplastic. Polymers (Basel). 2023;15:2650. doi:10.3390/polym15122650
- Ingrole A, Hao A, Liang R. Design and modeling of auxetic and hybrid honeycomb structures for in-plane property enhancement. Mater Des. 2017;117:72–83. doi:10.1016/j.matdes.2016.12.067
- Nazir A, Arshad AB, Lin SC, et al. Mechanical performance of lightweight-designed honeycomb structures fabricated using multijet fusion additive manufacturing technology. 3D Print Addit Manuf. 2022;9(4):311–325. doi:10.1089/3dp.2021.0004
- Dhari R, Javanbakht Z, Hall W. On the deformation mechanism of re-entrant honeycomb auxetics under inclined static loads, Mater Lett. 2020;286:129214.
- Nugroho WT, Dong Y, Pramanik A, et al. Additive manufacturing of re-entrant structures: Well-tailored structures, unique properties, modelling approaches and real applications. Addit Manuf. 2023;78:103829. doi:10.1016/j.addma.2023.103829
- Ma N, Wentao L, Ma L, et al. Crystal transition and thermal behavior of Nylon 12. e-Polymers. 2020;20:346–352. doi:10.1515/epoly-2020-0039
- Fischer SF. Energy absorption efficiency of open-cell pure aluminum foams. Mater Lett. 2016;184:208–210. doi:10.1016/j.matlet.2016.08.061
- Aviles F, Oliva-Avilés A, Cen-Puc M. Piezoresistivity, strain, and damage self-sensing of polymer composites filled with carbon nanostructures. Adv Eng Mater. 2018;20:1701159. doi:10.1002/adem.201701159
- Verma P, Ubaid J, Varadarajan KM, et al. Synthesis and characterization of carbon nanotube-doped thermoplastic nanocomposites for the additive manufacturing of self-sensing piezoresistive materials. ACS Appl Mater Interfaces. 2022;14(6):8361–8372. doi:10.1021/acsami.1c20491
- Roudaut G, Simatos D, Champion D, et al. Molecular mobility around the glass transition temperature: A mini review. Innov Food Sci Emerg Technol. 2004;5:127–134. doi:10.1016/j.ifset.2003.12.003
- Colombo D, Montes H, Lequeux F, et al. Thermo-mechanical modeling of a filled elastomer based on the physics of mobility reduction. Mech Mater. 2020;143:103319. doi:10.1016/j.mechmat.2020.103319
- Cao M-S, Song W-L, Hou Z-L, et al. The effects of temperature and frequency on the dielectric properties, electromagnetic interference shielding and microwave-absorption of short carbon fiber/silica composites. Carbon N Y. 2010;48(3):788–796. doi:10.1016/j.carbon.2009.10.028