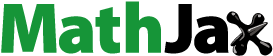
ABSTRACT
3D-printed ABS samples are treated with acetone and coated with copper oxide (CuO) for varying durations to understand how these treatment processes affect their mechanical and tribological properties. Tensile strength, flexural strength, coefficient of friction, and wear of ABS were analyzed under various pre-treatment and coating conditions and it is proved that acetone treatment and CuO coating can be effectively used to tune such properties to meet desired specifications. For 3D-printed ABS structures, CuO coating significantly enhances their tensile strength without acetone treatment. Although acetone treatment reduces their tensile strength as demonstrated, CuO coating can increase it again which means their tensile strength can be tuned by using the two processes. Furthermore, both acetone treatment and CuO coating improve their flexural strength. Additionally, acetone treatment and CuO coating both decrease their coefficient of friction. FESEM and EDS analyses were conducted on the structures to analyze and verify their wear properties.
1. Introduction
Plastic components offer advantages over their metal counterparts, such as reduced weight, improved corrosion resistance, and enhanced flexibility. However, in some cases, metals are used due to their superior properties, such as strength and durability. Plastic components can be metalised through a coating process by depositing a thin metal layer on their outer surface. This coating process changes and enhances properties like reflectivity, abrasion resistance, conductivity, hardness, and wear resistance. Acrylonitrile butadiene styrene (ABS) and polylactic acid (PLA) are commonly used plastics for three-dimensional (3D)-printing and mentalization due to their ability to combine outstanding engineering properties with metal-like characteristics [Citation1–3]. The selection of ABS materials can be based on different grades based on the percentage of butadiene, which can be used as a varying parameter to assess the corrosion resistance of ABS structures [Citation4].
Numerous studies investigated the effects of pre-treatment methods on non-conductive materials and structures, particularly ABS materials and structures. For example, environmentally friendly chromium- and palladium-free pre-treatments were explored, and conductive coatings were achieved through electroless plating on ABS substrates [Citation5–7]. In addition, direct copper plating was employed using techniques like etching and activation, which improved ABS properties with slight modifications in the pre-treatment process [Citation8]. Furthermore, the surface of ABS materials was rendered hydrophilic through etching, followed by applying a metal catalyst (i.e. palladium) on the ABS substrate [Citation9–11]. Moreover, the polymerisation of ABS substrates was achieved using a primary polyaniline thin film, and the deposition of silver metal fragments was utilised to enhance their electrical conductivity, facilitating the direct electroplating of nickel onto their surface [Citation12–14]. Li et al. investigated and developed a membrane composed of poly-thiophene conductive polymers to replace electroless plating [Citation13]. Bari et al. proposed a novel method by introducing silver nanowires (AgNWs) into (3,4-ethylenedioxythiophene)-poly (styrene sulfonate) (PEDOT: PSS) as a conductive seed layer to realise the direct copper electroplating on insulating substrates [Citation14]. Additionally, molecular grafting techniques were used to enhance the adhesion between ABS substrates and nickel coating films, leading to improved corrosion resistance, followed by the application of silver films [Citation9,Citation15].
All ABS coatings can be characterised based on micro-hardness, surface roughness, and current density. In the characterisation process, dominant parameters, such as current density, were determined using the Taguchi method and analysis of variance (ANOVA) [Citation16]. A direct electroplating technique was developed to simplify the plating process for ABS to reduce the steps and costs associated with traditional methods [Citation17]. For example, the application of nickel and copper coatings on ABS revealed that the thickness of the coating depends on the electrolysis time and current density [Citation18–20]. In addition, chemical roughening was employed for pre-treatment on ABS and Nylon-6 structures with conductive paints, where a uniform coating thickness was investigated to understand its effect on the mechanical performance of the structures [Citation21].
One comprehensive study demonstrated the potential to enhance desirable characteristics of ABS material through post-processing techniques, specifically cold acetone vapour treatment using a customised mechanical system [Citation22]. To tackle global issues like access to clean water, functionalised 3D-printed materials are gaining significant attention [Citation23]. For example, the use of electroless plating for silver coating on 3D-printed resins emphasises sustainability in manufacturing [Citation24]. Moreover, various studies have investigated the significance of post-processing in enhancing the properties of 3D-printed polymers. These studies show that finishing methods and treatments are important for improving the mechanical, chemical, and aesthetic attributes of polymers [Citation25–27]. Particularly, advancements in surface modification through electroless nickel-phosphor plating techniques [Citation28] and the integration of graphene nanocomposites in polymer matrices [Citation29] showcase the diverse array of approaches enriching the landscape of additive manufacturing technologies. Furthermore, the exploration of metallization techniques for both conventionally manufactured and 3D-printed polymeric structures highlights the versatility and potential of additive manufacturing in creating complex architectures [Citation30]. As the scientific community and industry continue to innovate, the comprehensive review of post-processing treatments offered in recent literature serves as a roadmap for optimising and customising polymeric structures manufactured through additive technologies [Citation27]. This research on post-processing treatments not only advances our understanding of additive manufacturing technologies but also offers practical insights into the multifaceted realm of post-processing methods that lead to greater efficiency, sustainability, and functionality.
Polymer properties can also be enhanced by incorporating composite materials, as demonstrated in several studies. For instance, in the work by Gackowski et al. [Citation31], additive manufacturing techniques were utilised to fabricate nylon composites embedded with multi-material piezoresistive strain sensors for structural health monitoring. The study showcased a novel hybrid additive manufacturing process, resulting in customisable 3D-printed piezoresistive sensors capable of detecting global or local damage in real time. Furthermore, the study conducted by Tran et al. [Citation32] presented a post-treatment method to improve the transverse strength of 3D-printed ABS structures by embedding commercial carbon fibre/epoxy pins into the internal channels of the printed structures. This method significantly enhanced the mechanical performance of the ABS structures, demonstrating the effectiveness of composite materials in strengthening printed components. Moreover, in the research by Brown et al. [Citation33], the feasibility of printing multifunctional composite structures using continuous carbon fibre was explored. By leveraging the electrical properties of carbon fibre, the study demonstrated the potential for self-sensing capabilities in additively manufactured parts. These findings emphasise the utility of composite materials in improving polymer properties and expanding the functionality of additive manufacturing processes.
It is important to note that one of the most widely adopted additive manufacturing technologies is fused deposition modelling (FDM) 3D-printing to fabricate ABS samples and characterise them since the FDM 3D printers are affordable and accessible and can be used with a wide range of materials such as thermoplastics and thermoplastic polyurethanes (TPUs) [Citation34–36].
Although the literature presents many ways to enhance the properties of 3D-printed ABS structures through coating processes and various pre-treatment methods it lacks a specific study on the combined effect of CuO coating and pre-treatment on the mechanical and wear properties of 3D-printed ABS samples with acetone. Existing research focuses on the individual effects of either acetone treatment or CuO coating on ABS structures. This work investigates how the combination and interaction between these processes affect the mechanical and tribological properties of 3D-printed ABS structures and how such processes can be combined to tune the mechanical properties of 3D-printed ABS structures, such as tensile and flexural strength, and tribological properties, such as wear and coefficient of friction, to meet a desired application. The novelty lies in demonstrating that the mechanical and wear properties of 3D-printed ABS samples can be tuned based on a combination of a pre-treatment process (i.e. acetone pre-treatment) and a CuO coating process. The study shows how each and both processes combined affect the mechanical and wear properties and how such processes can be used to obtain desired properties for specific applications.
The 3D-printed ABS samples were subjected to acetone treatment for varying durations and coated with CuO using a sol–gel solution. The mechanical properties of ABS such as tensile and flexural strength and tribological properties such as wear were analyzed under various coating and pre-treatment conditions. The results of this work summarise how acetone treatment and CuO coating of 3D-printed ABS structures can be used to tune specific mechanical properties such as tensile strength and flexural strength and wear properties such as the coefficient of friction to meet certain requirements for a desired application.
2. Materials and methods
2.1. Materials
ABS was used in the form of filament with a diameter of 1.75 mm (1 kg spool). In addition, acetone-99% grade was used for the pre-treatment of the ABS samples.
2.2. 3D-Printing of ABS substrates
The ABS samples were fabricated in three shapes, including dog-bone (), rectangular (), and cylindrical forms () for the mechanical and wear tests. An FDM 3D printer (Creality Ender 3 Pro, Shenzhen Creality 3D Technology Co., Ltd.) was used to 3D-print all the ABS samples with different shapes. All the samples were designed using computer-aided design (CAD) modelling software (SolidWorks, SolidWorks Corp., Dassault Systèmes), and the CAD models were sliced using an open-source slicer (Ulti-maker Cura, Ultimaker).
Figure 1. 3D-printed dog-bone specimen ABS sample shape and dimensions based on ASTM D638 standard for use in tensile tests. (A) 3D-CAD model showing all the dimensions in mm. l1: 22.50, l2: 33.00, l3: 115.00, r1: 25.00, r2: 14.00, w1: 19.00, and w2: 6.00. Sample thickness t: 3.00. (B) 3D-printed dog-bone specimen ABS sample.
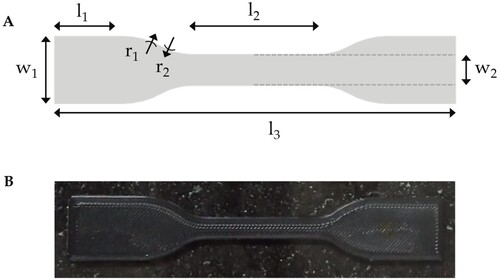
Figure 2. 3D-printed rectangular ABS sample shape and dimensions based on ASTM D790 standard for use in bending/flexural tests. (A) 3D-CAD model showing all the dimensions in mm. h: 12.50, l: 90.00, and t: 3.00. (B) 3D-printed ABS sample.
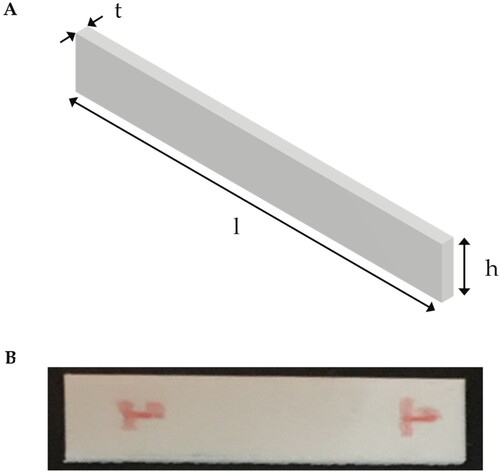
Figure 3. 3D-printed cylindrical ABS sample shape and dimensions based on ASTM G99 standard for use in wear tests. (A) 3D-CAD model showing all the dimensions in mm. d: 8.00 and l: 30.00. (B) 3D-printed cylindrical ABS sample.
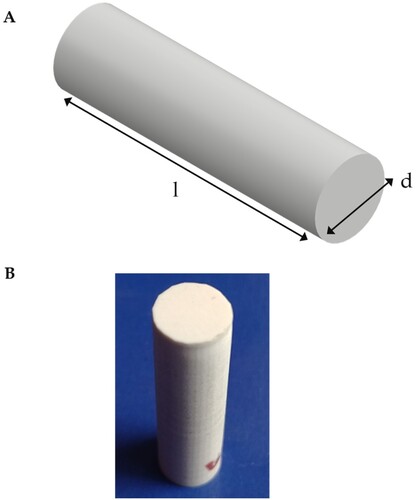
For the 3D-printing parameters, the infill density used is 100% for all samples, and the infill type used is a line-type infill pattern with line directions of (90,90). The 3D-printing temperature is 210°C with a print speed of 60 mm/s. The 3D-printing parameters used to fabricate all the ABS samples are listed in [Citation37,Citation38]. In addition, the dog-bone and rectangular samples were printed along their thickness, and the cylindrical samples were printed along their length.
Table 1. The 3D-printing parameters used for the fabrication of the ABS samples.
All the ABS samples were designed and fabricated with the abovementioned specifications and based on the ASTM standards, including Tensile specimen – ASTM D638 standard, Bending specimen – ASTM D790 standard, and Wear specimen – ASTM G99 standard.
2.3. Acetone treatment of ABS
An acetone treatment is carried out on the ABS samples to improve their surface roughness. The specimens were immersed in an acetone bath for varying periods of 10 and 20 s. When ABS is dipped in an acetone bath [Citation39], its surface melts, and the acetone clings to it, resulting in a smooth surface.
2.4. Sol–gel preparation
The sol–gel process, a wet chemical method, can be used for coating or synthesising various materials [Citation40,Citation41]. Typically, metal oxides are prepared to coat the desired materials. To create a sol–gel solution, copper acetate powder was selected and dissolved in a mixture of diethanolamine (DEA) and isopropanol (IPA), based on a molar concentration of 0.25 M. A stabiliser, namely polyethylene glycol (PEG), was then introduced [Citation42,Citation43]. The solution was stirred on a hot plate stirrer for 10 min until all the ingredients were completely dissolved. The resulting sol–gel solution was dark blue and transparent with no visible particle suspension. It is important to note that the sol–gel solution was prepared at room temperature (i.e. around 25–28°C).
The 3D-printed ABS samples with and without pre-treatment with acetone were dipped in the sol–gel solution for varying time durations of 1 and 2 h. Then, the immersed ABS samples in the sol–gel solution were air-dried and used to perform the mechanical and wear tests.
2.5. Tensile and bending tests
Tensile tests are performed to determine the strength of the material and the force required to break it. The dog-bone ABS samples were used to perform the tensile tests (). A bending test is carried out to extract the flexural strength of the material when flexed (i.e. bent). The rectangular ABS samples were used to perform the bending tests (). The tensile tests were conducted using a computerised universal testing machine (UTM) with a 10 kN load cell and 5 mm/min pulling speed (KIC-2-1000C, Kalpak Instruments and Controls). The bending tests were conducted using the same UTM using a fixture with a 3-point loading condition, a speed of 3 mm/min, and a span-to-depth ratio of 16. As noted, both tests were performed on ABS samples with and without acetone pre-treatment. Five test samples were prepared for each test and the average data was used for the analysis and comparison of results.
2.6. Wear tests
A wear test is carried out to extract the coefficients of friction of the ABS samples. The effect of acetone on the coefficient of friction is investigated at different loads, speeds, and sliding distances. The Taguchi method is implemented to carry out the tests. For the design of experiments, Minitab (Version 19.1, Minitab, LLC.) is employed. The factors considered are load (10, 30, and 50 N), speed (1, 1.5, and 2 m/s), and sliding distance (1000, 2000, and 3000 m) with multiple levels as shown in . The values selected for the parameters in are close, with an upper and a lower limit, to practical applications where FDM 3D-printed ABS samples might be used.
Table 2. The factors and levels of the wear test.
All the tests were performed on a pin-on-disc apparatus. The disc diameter (d) was set to 70 mm. The number of rotations (N) is computed using Equation (1) for the speed (V) and the number of revolutions (R) is computed using Equation (2) for a particular sliding distance (D). The frictional force (Fr) divided by its corresponding applied load (W) results in the coefficient of friction (μ) as shown in Equation (3) [Citation44].
(1)
(1)
(2)
(2)
(3)
(3)
The extent of wear was assessed by determining the reduction in weight of both the pin and the disc, utilising a precise analytical balance with a precision of 0.001 mg. The wear rate (denoted as K and measured in mm3/N.m) presented in this work was computed using Equation (4) [Citation45]:
(4)
(4) where Δm represents the weight loss in g and ρ represents the density of the polymers in g/cm³.
The wear test apparatus (i.e. setup) is shown in . The setup shows the ABS cylindrical sample held on a fixture and pressed against a rotating metallic disc in which the ABS sample gets worn out, as evident in the circular trace of worn ABS particles. Standard high-carbon steel (EN-31) was selected as the metallic disc material with a hardness of 62 HRC (Rockwell Hardness on the C scale). The specimens were subjected to field emission scanning electron microscopy (FESEM) and dispersive spectroscopy (EDS) analysis to analyze the fabricated polymers wear mechanism.
3. Results
The effect of acetone pre-treatment and CuO coating on the ABS samples is assessed through the experimental characterisation of the mechanical and wear properties of the samples. For each ABS sample shape, the tests were carried out on three types of samples including (1) ABS samples without acetone treatment with (1 and 2 h) and without CuO coating (i.e. processing), (2) ABS samples with 10 s of acetone treatment with (1 and 2 h) and without CuO coating (i.e. processing), and ABS samples with 20 s of acetone treatment with (1 and 2 h) and without CuO coating (i.e. processing). The cylindrical samples coated with CuO were chosen and analyzed using EDS to confirm successful coating. The EDS analysis results demonstrated successful CuO coating on the ABS samples as shown in .
3.1. Tensile tests
The stress–strain results for all the tests are shown in . (A–C) shows the stress–strain curves (i.e. tensile strength) for the different ABS samples with and without acetone treatment and with and without CuO coating. In addition, D shows the tensile strength for all samples. In D, the tensile strength of the ABS samples without acetone treatment and with CuO coating for 1 and 2 h increased by 10% and 17.12%, respectively, compared to the tensile strength of 34.6 ± 5.20 MPa for the ABS samples without acetone treatment and CuO coating.
Figure 6. The tensile test stress-strain curves (A) for the ABS samples without acetone treatment with (1 and 2 h) and without CuO coating, (B) for the ABS samples with 10 s of acetone treatment with (1 and 2 h) and without CuO coating, and (C) for the ABS samples with 20 s of acetone treatment with (1 and 2 h) and without CuO coating. (D) The tensile strength (i.e. stress) for all tested samples.
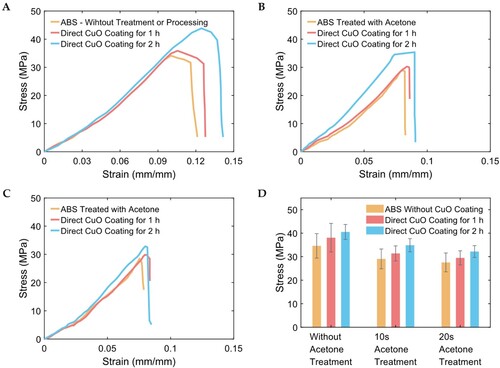
Similarly, the tensile strength of the ABS samples with acetone treatment for 10 s and with CuO coating for 1 and 2 h increased by 7.99% and 20%, respectively, compared to the tensile strength of 29.05 ± 4.20 MPa for the ABS samples with ace-tone treatment for 10 s and without CuO coating.
Likewise, the tensile strength of the ABS samples with acetone treatment for 20 s and with CuO coating for 1 and 2 h increased by 7.01% and 16.81%, respectively, compared to the tensile strength of 27.55 ± 4.0 MPa for the ABS samples with acetone treatment for 20 s and without CuO coating.
Moreover, based on these results, it is evident that the etching effect during the ace-tone treatment process reduces the overall tensile strength of ABS. The tensile strength of the ABS samples without CuO coating and with 10 and 20 s of acetone treatment decreased by 9.34% and 14.80%, respectively, compared to the tensile strength of 34.60 ± 5.20 MPa for the ABS samples without CuO coating and acetone treatment.
However, the CuO coating of the ABS samples enhanced their tensile strength. It is important to note that there is a positive relationship between the duration of the acetone treatment process and the decrease in the tensile strength. There is a positive relationship between the duration of the CuO coating process and the increase in the tensile strength of the ABS samples.
3.2. Bending test
The bending test is performed to assess and extract the flexural strength of the various ABS samples. A–C shows the stress–strain curves (i.e. flexural strength) for the different ABS samples with and without acetone treatment and with and without CuO coating. In addition, D shows the flexural strength for all samples. In D, the flexural strength of the ABS samples without acetone treatment and with CuO coating for 1 and 2 h increased by 9.45% and 11.35%, respectively, compared to the flexural strength of 40.96 ± 4.80 MPa for the ABS samples without acetone treatment and CuO coating.
Figure 7. The bending test flexural stress-strain curves (A) for the ABS samples without acetone treatment with (1 and 2 h) and without CuO coating, (B) for the ABS samples with 10 s of acetone treatment with (1 and 2 h) and without CuO coating, and (C) for the ABS samples with 20 s of acetone treatment with (1 and 2 h) and without CuO coating. (D) The flexural strength (i.e. stress) for all tested samples.
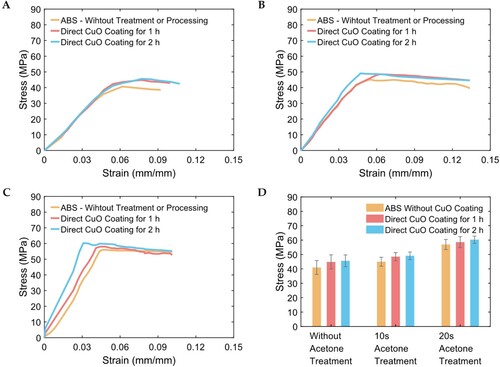
Similarly, the flexural strength of the ABS samples with acetone treatment for 10 s and with CuO coating for 1 and 2 h increased by 7.82% and 9.16%, respectively, compared to the flexural strength of 44.99 ± 3.10 MPa for the ABS samples with acetone treatment for 10 s and without CuO coating.
Likewise, the flexural strength of the ABS samples with acetone treatment for 20 s and with CuO coating for 1 and 2 h increased by 2.90% and 5.86%, respectively, compared to the flexural strength of 56.96 ± 3.50 MPa for the ABS samples with acetone treatment for 20 s and without CuO coating.
Moreover, based on these results, it is evident that the etching effect during the ace-tone treatment process increased the overall flexural strength of ABS. The flexural strength of the ABS samples without CuO coating and with 10 and 20 s of acetone treatment increased by 9.84% and 39.06%, respectively, compared to the flexural strength of 40.96 ± 4.8 MPa for the ABS samples without CuO coating and acetone treatment. This effect can be attributed to the fact that the 3D-printed layers are fused on the surface along the cylinder's height (i.e. length) during the acetone treatment process. This fusion leads to stronger bonds between the different layers that are thin 3D-printed ABS plastic disks stacked over each other [Citation41,Citation46].
Moreover, the CuO coating of the ABS samples enhanced their flexural strength. It is important to note that there is a positive relationship between the duration of the acetone treatment process and the increase in flexural strength. There is a positive relationship between the duration of the CuO coating process and the increase in the flexural strength of the ABS samples.
3.3. Wear test
A wear test on a pin-on-disc apparatus was conducted to extract the coefficient of friction, μ, of the ABS samples. As shown in , the inputs were used in the design of the experiment (DOF) to create a Taguchi design [Citation47]. shows the L9 Taguchi array (i.e. orthogonal array) where 9 represents the number of experiments. Therefore, 27 experiments were performed out of which 9 were divided equally with and without acetone treatment. The values of the coefficient of friction are experimentally determined and listed in .
Table 3. Coefficient of friction and wear rate experimental values with and without acetone treatment.
In addition, ANOVA was conducted, in Minitab (Version 19.1, Minitab, LLC.) to determine the percentage contribution (i.e. degree of influence) of each factor on the coefficient of friction [Citation48]. The percentage contributions of each factor to the coefficient of friction are listed in . For the ABS samples without acetone treatment, the highest contribution was that of the speed with 65.67%. For the ABS samples with 10 and 20 s of acetone treatment, the highest contribution was that of the load with 93.36% and 93.86%, respectively.
Table 4. ANOVA results for the coefficient of friction without acetone treatment.
Table 5. ANOVA results for the coefficient of friction with 10 s of acetone treatment.
Table 6. ANOVA results for the coefficient of friction with 20 s of acetone treatment.
Finally, the wear rate was measured and the data is listed in . The wear rate in this work was computed to understand the material loss during the wear test. From it is evident that the increased duration of acetone treatment leads to a reduction in wear rate due to the change in the surface finish of the ABS samples (i.e. smoother surface).
The normal probability plots for the coefficient of friction for different durations of acetone treatment are shown in , where it is evident that the residuals approach a straight line, therefore, suggesting that the experimental results obtained are normally distributed and dependable. The linear regression models obtained for the coefficient of friction with and without acetone treatment are given by Equations (5)–(7). The coefficient of friction values obtained experimentally were compared with the coefficient of friction values obtained from the regression models (L stands for Load in the equations of the regression models).
Figure 8. The normal probability plot of the coefficient of friction for the different acetone durations of (A) 0 s (i.e. without acetone treatment), (B) 10 s of acetone treatment, and (C) 20 s of acetone treatment.
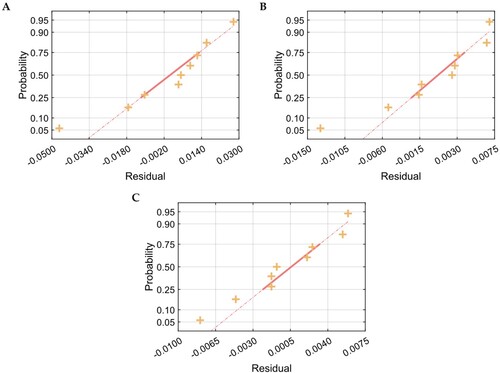
Regression Model 1 (i.e. without acetone treatment):
(5)
(5) Regression Model 2 (i.e. with 10 s of acetone treatment):
(6)
(6)
Regression Model 3 (i.e. with 20 s of acetone treatment):
(7)
(7)
3.4. Optimisation of the coefficient of friction
The Taguchi method produces an optimised value or the best levels of control factors from the analysis. Based on the orthogonal array, these experiments are balanced for all control factors. The results obtained describe the reliability and repeatability of the experimental models. The plots for the main effects of the signal-to-noise (SN) ratios give the optimisation plots for the control factors, as shown in .
Figure 9. The main effects plot of the coefficient of friction (A) without acetone treatment, (B) with 10 s of acetone treatment, (C) and with 20 s of acetone treatment.
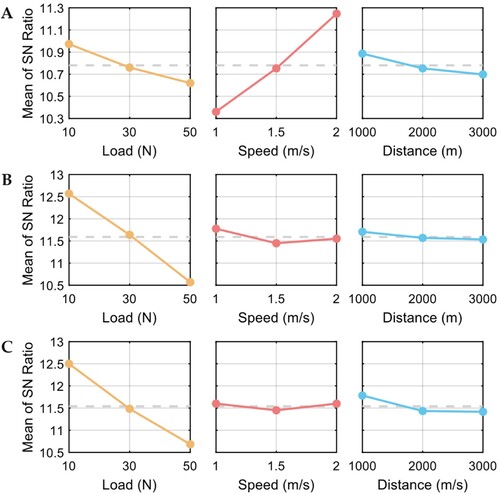
The best levels of control factors or optimisation levels are those that maximise the SN ratios. The corresponding optimum values were taken from the main effects plots, which were used to perform the experimental and theoretical verifications, which is the final step in the Taguchi method and is referred to as the verification experiments. From , it is clear that the acetone treatment affects the friction coefficient of the ABS samples by reducing it compared to the coefficient of friction of the ABS samples without ace-tone treatment.
Table 7. Coefficient of friction experimental data verification.
shows the coefficient of friction for all samples. In , the coefficient of friction of the ABS samples without acetone treatment and with CuO coating for 1 and 2 h decreased by 5.90% and 16.97%, respectively, compared to the coefficient of friction of 0.272 ± 0.019 for the ABS samples without acetone treatment and CuO coating.
Similarly, the coefficient of friction of the ABS samples with acetone treatment for 10 s and with CuO coating for 1 and 2 h decreased by 9.09% and 15.28%, respectively, compared to the coefficient of friction of 0.242 ± 0.009 for the ABS samples with acetone treatment for 10 s and without CuO coating.
Likewise, the coefficient of friction of the ABS samples with acetone treatment for 20 s and with CuO coating for 1 and 2 h decreased by 6.92% and 16.88%, respectively, compared to the coefficient of friction of 0.231 ± 0.010 for the ABS samples with acetone treatment for 20 s and without CuO coating.
In addition, based on these results, it is evident that the etching effect during the ace-tone treatment process decreased the coefficient of friction of ABS. The coefficient of friction of the ABS samples without CuO coating and with 10 and 20 s of acetone treatment decreased by 11.02% and 15.07%, respectively, compared to the coefficient of friction of 0.272 ± 0.019 for the ABS samples without CuO coating and acetone treatment.
Moreover, the CuO coating of the ABS samples decreased the friction coefficient. It is important to note that there is a positive relationship between the duration of the acetone treatment process and the decrease in the coefficient of friction. Similarly, there is a positive relationship between the duration of the CuO coating process and the decrease in the coefficient of friction for the ABS samples.
3.5. Worn-out surface analysis
In A, the microscopic image illustrates the worn-out surfaces of a 3D-printed cylindrical ABS sample with 10 s of acetone treatment. The image illustrates that the wear track of the sample appears to be free of contaminants, displaying a rather clean surface. Applying acetone treatment to the sample can modify the surface of the polymer by eliminating contaminants and enhancing surface wettability and lubrication. The microstructural image of the worn-out surface clearly shows that the acetone-treated surface was free of any surface contaminants. Specifically, the wear track on the coated ABS exhibits typical features of adhesive wear, marked by microcracks and grooves.
Figure 11. Worn-out surface analysis of (a) a cylindrical ABS sample with 10 s of acetone treatment, (B) a cylindrical ABS sample with 20 s of acetone treatment, (C) a cylindrical ABS sample with CuO coating and without acetone treatment, (D) a cylindrical ABS sample with CuO coating and with 10 s of acetone treatment, and (e) a cylindrical ABS sample with CuO coating and with 20 s of acetone treatment.
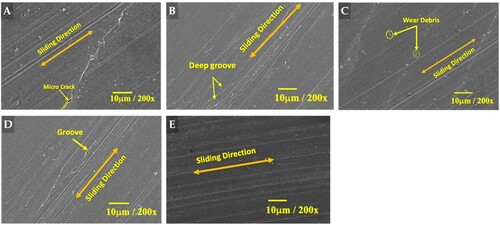
The cylindrical ABS sample with 20 s of acetone treatment (B), revealed an enhanced wear surface characterised by the absence of microcracks. However, the presence of deep grooves suggests an adhesive wear form. Additionally, it is noticeable that more wear debris and surface contaminants were eliminated compared to the previous sample shown in A.
The CuO-coated cylindrical ABS sample displayed a microstructural image (C) superior to the samples treated only with acetone. The CuO coating is expected to enhance the wear resistance of ABS by providing a protective layer on the surface. Copper oxide is recognised for its hardness and its ability to serve as a protective barrier against wear. Also, multiple wear scars were evident along the sliding direction, suggesting an abrasive wear form. D depicts a cylindrical ABS sample coated with CuO and with 10 s of acetone treatment. The adhesion between the CuO coating and the ABS substrate is vital for ensuring the overall effectiveness of the coating. Effective adhesion is essential for maintaining the integrity of the coating under wear conditions.
The compatibility between acetone-treated ABS and the CuO coating holds significance. The acetone treatment demonstrates the capability to enhance the adhesion of the coating. Consequently, the enhanced adhesion of the surface and CuO coating achieved through acetone treatment has elevated the wear resistance of the sample. The sample treated with acetone for 20 s and coated with CuO (E), demonstrated an improved wear sample with minimal signs of wear. The CuO coating provides a protective layer between the wear pin and the contact surface, enhancing wear resistance.
As shown in , the mapping analysis confirmed the presence of CuO coating, indicating its role as a protective layer against wear and a strength-enhancing factor, rendering the material suitable for diverse applications. The adhesive characteristics of the acetone treatment play a crucial role in bonding the ABS substrate and the coating together. Consequently, a noticeable and substantial improvement in wear resistance is attributed to acetone treatment and CuO coating. These results agree with the literature that CuO coating improves the wear resistance of polymers [Citation49–51] and the friction properties between lubricated surfaces by decreasing the effective friction coefficient between them [Citation52].
4. Discussion
For the tensile strength of ABS, it was evident that CuO coating improves it. The highest tensile strength obtained without acetone treatment and CuO coating is 34.6 ± 5.20 MPa, dramatically increasing with CuO coating for 2 h to 40.52 ± 3.20 MPa. Even when the tensile strength decreased with acetone treatment, it increased again when the acetone-treated ABS samples were coated with CuO.
Savvakis et al. [Citation53], for example, conducted a study to extract the tensile strength of FDM 3D-printed ABS and ABS plus samples, resulting in a maximum tensile strength of 20.64 MPa. Wu et al. [Citation54] analyzed the influence of layer thickness and raster angle on the mechanical properties of FDM 3D-printed ABS and reported a maximum tensile strength of 37 MPa. Jayanth et al. showed that the tensile strength of 36.75 MPa for FDM 3D-printed ABS samples can be decreased to 26.74 and 20.29 MPa by immersing the samples for 3 and 7 min, respectively, in an acetone solution [Citation55]. Torres et al. determined that annealing ABS samples at 100°C for 60 min enhanced their tensile properties, and vapour smoothing the ABS samples with 20 mL of acetone for 15 min improved their surface roughness [Citation56].
Therefore, the results of this study are comparable with the literature and suggest that the tensile strength of ABS can be dramatically improved with CuO coating. In addition, the tensile strength of ABS can be tuned (i.e. increased or decreased) by using acetone treatment and CuO coating.
For the flexural strength of ABS, it was evident that it could be dramatically increased through acetone treatment and CuO coating. These results suggest that any of the two processes can be used to tune the bending performance of ABS structures. It is possible to use the processes together to achieve the desired flexural strength that is impossible with one process. In addition, the flexural strength values obtained in this work are comparable with the literature. For example, Wu et al. [Citation54] reported a maximum flexural strength of 56.10 MPa for ABS samples that are 3D-printed with a 300 µm resolution using FDM. This work obtained a higher maximum flexural strength of 60.30 ± 2.50 MPa with acetone treatment and CuO coating. Gurg et al. found that acetone treatment reduces the flexural strength of ABS samples from 55 MPa to 49 MPa [Citation57]. However, Wu et al. [Citation58], found that through the ultrasonic strengthening of 3D-printed structures, the flexural strength of ABS samples can be increased up to 69.26 MPa.
Similarly, to the tensile strength results, acetone treatment decreased the coefficient of friction, and CuO coating increased it. Treating ABS with acetone smoothens the outer surface of the samples, and therefore, a decrease in the coefficient of friction is expected. However, CuO coating increases the coefficient of friction since the surface of the samples will be rough due to the presence of the CuO thin film on the surface of the ABS samples. Omar et al. [Citation59] showed that layer thickness, air gap, raster angle, and build orientation are the most influential factors affecting the friction performance of FDM-manufactured polycarbonate-ABS structures and that such parameters can be used to obtain coefficients of friction up to 0.728.
Aravind et al. [Citation60] reported a lowest coefficient of friction of 0.280 at a speed of 4 m/s for glass fibre/ABS and carbon fibre-reinforced/ABS. In this work, the highest coefficient of friction obtained for untreated ABS is 0.308 ± 0.018. The lowest coefficient friction obtained is 0.192 ± 0.021 for the ABS samples with 10 s of acetone treatment and 2 h of CuO coating. provides a summary of the overall results.
Table 8. Summary of results for the tensile strength, flexural strength, and coefficient of friction.
6. Conclusion
This work reported on the effect of acetone treatment and CuO coating on the mechanical and wear properties of FDM 3D-printed ABS. ABS samples were tested with and without acetone treatment and with and without CuO coating. The acetone treatment process was conducted using two durations of 10 and 20 s. In addition, the CuO coating process was conducted using two durations of 1 and 2 h. The tensile strength, flexural strength, and coefficient of friction, of the ABS samples were extracted experimentally to assess the influence of the acetone treatment process and CuO coating process on them. Some significant key findings of this work are as follows:
Two hours of CuO coating significantly enhances tensile strength by 17.12% of 3D-printed ABS structures without acetone treatment.
A remarkable 10% increase in the tensile strength of ABS is achieved when coated with CuO for 1 h without acetone treatment.
Although acetone treatment reduces the tensile strength (16.04% reduction for 10 s of acetone treatment and 20.38% reduction for 20 s of acetone treatment compared to 34.60 MPa for the samples without acetone treatment and CuO Coating) of ABS, CuO coating can increase it again which means the tensile strength of ABS structures can be tuned for specific applications by using the two processes of acetone treatment and CuO coating.
Acetone treatment and CuO coating improve the flexural strength of 3D-printed ABS structures. Combining the two processes results in higher flexural strength than the flexural strength obtained from each process individually. The flexural strength increased from 40.96 MPa for the ABS samples without acetone treatment and CuO coating to 60.0 MPa for the ABS samples with 20 s of acetone treatment and 2 h of CuO coating. This is a remarkable 47.22% increase in the flexural strength of the ABS samples.
Although acetone treatment decreases the coefficient of friction, also CuO coating quantitatively decreases it, which is attributed to the reduction in roughness of ABS structures due to the deposited thin metalling film during the coating process.
Wear analysis was conducted on the fabricated sample and observed a combination of adhesion and abrasive mechanism.
This study showed that such mechanical and wear properties can be tuned (i.e. increased or decreased) using acetone treatment, CuO coating, or a combination of both processes. Therefore, the mechanical and wear properties of FDM 3D-printed ABS structures can be tuned to meet certain requirements for a specific application in different fields, such as robotics and biomedical engineering.
Disclosure statement
No potential conflict of interest was reported by the author(s).
Data availability statement
Data is available on request from the authors.
References
- Louda P. Applications of thin coatings in automotive industry. J Achievements Mater Manuf Eng. 2007;24(1):51–56.
- Wang Z, Wang J, Li M, et al. Three-dimensional printed acrylonitrile butadiene styrene framework coated with Cu-BTC metal-organic frameworks for the removal of methylene blue. Sci Rep. 2014;4(1):5939. doi:10.1038/srep05939
- Park S-S, Lee Y-S, Lee S-W, et al. Facile surface treatment of 3D-printed PLA filter for enhanced graphene oxide doping and effective removal of cationic dyes. Polymers. 2023;15(2):269. doi:10.3390/polym15020269
- Galeja M, Hejna A, Kosmela P, et al. Static and dynamic mechanical properties of 3D printed ABS as a function of raster angle. Materials. 2020;13(2):297. doi:10.3390/ma13020297
- Yang S, Kang Z, Guo T. Preparation and conductive property of Cu coatings and Cu-graphene composite coatings on ABS substrate. Nanotechnology. 2020;31(19):195710. doi:10.1088/1361-6528/ab703e
- Gui-Xiang W, Ning L, Hui-Li H, et al. Process of direct copper plating on ABS plastics. Appl Surf Sci. 2006;253(2):480–484. doi:10.1016/j.apsusc.2005.12.106
- Tang X, Cao M, Bi C, et al. Research on a new surface activation process for electroless plating on ABS plastic. Mater Lett. 2008;62(6-7):1089–1091. doi:10.1016/j.matlet.2007.07.055
- Nigam S, Patel SK, Mahapatra SS. Copper plating On Abs plastic By thermal spray. Int J Mech Prod Eng. 2015;3(6):115–119.
- Zhang H, Kang Z, Sang J, et al. Surface metallization of ABS plastics for nickel plating by molecules grafted method. Surf Coat Technol. 2018;340:8–16. doi:10.1016/j.surfcoat.2018.02.005
- Khan M, Mishra S, Kumar MA, et al. Optimizing surface texture and coating thickness of nickel coated ABS-3D parts. Mater Today Proc. 2018;5(9):19011–19018. doi:10.1016/j.matpr.2018.06.252
- Bazzaoui M, Martins J, Bazzaoui E, et al. Environmentally friendly process for nickel electroplating of ABS. Appl Surf Sci. 2012;258(20):7968–7975. doi:10.1016/j.apsusc.2012.04.146
- Sudagar J, Lian J, Sha W. Electroless nickel, alloy, composite and nano coatings–A critical review. J Alloys Compd. 2013;571:183–204. doi:10.1016/j.jallcom.2013.03.107
- Li J, Zhou G, Jin X, et al. Direct activation of copper electroplating on conductive composite of polythiophene surface-coated with nickel nanoparticles. Compos Part B: Eng. 2018 2018/12/01/;154:257–262. doi:10.1016/j.compositesb.2018.08.019
- Di Bari GA. Electrodeposition of nickel. Mod Electroplating. 2010: 79–114. doi:10.1002/9780470602638.ch3
- Kumar SSA, Bashir S, Ramesh K, et al. A comprehensive review: super hydrophobic graphene nanocomposite coatings for underwater and wet applications to enhance corrosion resistance. FlatChem. 2022;31:100326. doi:10.1016/j.flatc.2021.100326
- Nasir S, Shuaib N, Shayfull Z, et al. Warpage analyses on thin plate by Taguchi Method and Analysis of Variance(ANOVA) for PC, PC/ABS and ABS materials. Int Rev Mech Eng. 2011;5(6):1125–1131.
- Hwang T, Oh JS, Hong J-P, et al. One-step metal electroplating and patterning on a plastic substrate using an electrically-conductive layer of few-layer graphene. Carbon. 2012;50(2):612–621. doi:10.1016/j.carbon.2011.09.020
- Augustyn P, Rytlewski P, Moraczewski K, et al. A review on the direct electroplating of polymeric materials. JMatS. 2021;56(27):14881–14899.
- Huener B, Demir N, Kaya MF. Electrodeposition of NiCu bimetal on 3D printed electrodes for hydrogen evolution reactions in alkaline media. Int J Hydrogen Energy. 2022;47(24):12136–12146. doi:10.1016/j.ijhydene.2021.10.009
- Olivera S, Muralidhara HB, Venkatesh K, et al. Plating on acrylonitrile–butadiene–styrene (ABS) plastic: a review. JMatS. 2016;51:3657–3674.
- Kulkarni MV, Elangovan K, Hemachandra RK. Effects of electroplating on the mechanical properties of injection molded thermoplastics. Int J Plast Technol. 2013;17(2):163–170. doi:10.1007/s12588-013-9056-6
- Demircali AA, Yilmaz D, Yilmaz A, et al. Enhancing mechanical properties and surface quality of FDM-printed ABS: A comprehensive study on cold acetone vapor treatment. Int J Adv Manuf Tech. 2024;130(7):4027–4039. doi:10.1007/s00170-023-12929-2
- Mohd Yusoff NH, Chong CH, Wan YK, et al. Optimization strategies and emerging application of functionalized 3D-printed materials in water treatment: A review. J Water Proc Eng. 2023;51:103410. doi:10.1016/j.jwpe.2022.103410
- Bragaglia M, Pascale V, Rinaldi M, et al. Silver electroless plating on 3D printed resins via stereolithography: A sustainable solution. Thin Solid Films. 2022;757:139417. doi:10.1016/j.tsf.2022.139417
- Dizon JRC, Gache CCL, Cascolan HMS, et al. Post-processing of 3D-printed polymers. Technologies. 2021;9(3):61. doi:10.3390/technologies9030061
- Wickramasinghe S, Do T, Tran P. FDM-based 3D printing of polymer and associated composite: A review on mechanical properties, defects and treatments. Polymers. 2020;12(7):1529. doi:10.3390/polym12071529
- Tamburrino F, Barone S, Paoli A, et al. Post-processing treatments to enhance additively manufactured polymeric parts: A review. Virtual Phys Prototyp. 2021;16(2):221–254. doi:10.1080/17452759.2021.1917039
- Alhamad RK, Hussein AK, Abbas LK. Improved acrylonitrile-butadiene-styrene surface properties via electroless (NiP-SiC) nanocomposite coating. Chem Phys Impact. 2023;7:100375. doi:10.1016/j.chphi.2023.100375
- Ponnamma D, Yin Y, Salim N, et al. Recent progress and multifunctional applications of 3D printed graphene nanocomposites. Compos Part B: Eng. 2021;204:108493. doi:10.1016/j.compositesb.2020.108493
- Perera A, Song K, Umezu S, et al. Recent progress in functionalized plastic 3D printing in creation of metallized architectures. Mater Des. 2023: 112044. doi:10.1016/j.matdes.2023.112044
- Gackowski BM, Goh GD, Sharma M, et al. Additive manufacturing of nylon composites with embedded multi-material piezoresistive strain sensors for structural health monitoring. Compos Part B: Eng. 2023;261:110796. doi:10.1016/j.compositesb.2023.110796
- Tran TQ, Sarmah A, Dasari SS, et al. Enhanced transverse strength of 3D printed acrylonitrile butadiene styrene parts by carbon fiber/epoxy pin insertion. Addit Manuf. 2024;79:103952. doi:10.1016/j.addma.2023.103952
- Demarbaix A, Ochana I, Levrie J, et al. Additively manufactured multifunctional composite parts with the help of coextrusion continuous carbon fiber: study of feasibility to print self-sensing without doped raw material. J Compos Sci. 2023;7(9):355. doi:10.3390/jcs7090355
- Aberoumand M, Soltanmohammadi K, Rahmatabadi D, et al. 4D printing of polyvinyl chloride (PVC): A detailed analysis of microstructure, programming, and shape memory performance. Macromol Mater Eng. 2023: 2200677. doi:10.1002/mame.202200677
- Soleyman E, Rahmatabadi D, Soltanmohammadi K, et al. Shape memory performance of PETG 4D printed parts under compression in cold, warm, and hot programming. Smart Mater Struct. 2022;31(8):085002. doi:10.1088/1361-665X/ac77cb
- Rahmatabadi D, Aberoumand M, Soltanmohammadi K, et al. A new strategy for achieving shape memory effects in 4D printed two-layer composite structures. Polymers (Basel). 2022;14(24):5446. doi:10.3390/polym14245446
- Abeykoon C, Sri-Amphorn P, Fernando A. Optimization of fused deposition modeling parameters for improved PLA and ABS 3D printed structures. Int J Lightweight Mater Manuf. 2020;3(3):284–297. doi:10.1016/j.ijlmm.2020.03.003
- Akhil VM, Aravind SL, Kiran R, et al. Experimental investigations on the effect of infill patterns on PLA for structural applications. Mater Today Proc. 2023;76:636–639. doi:10.1016/j.matpr.2022.10.292
- Riva L, Fiorentino A, Ceretti E. Characterization of the chemical finishing process with a cold acetone bath of ABS parts fabricated by FFF. Sel Top Manuf: AITeM Young Res Award 2021. 2022: 77–89. doi:10.1007/978-3-030-82627-7_5
- Bokov D, Turki Jalil A, Chupradit S, et al. Nanomaterial by sol-gel method: synthesis and application. Adv Mater Sci Eng. 2021;2021:1–21. doi:10.1155/2021/5102014
- Aegerter MA, Mennig M. Sol-gel technologies for glass producers and users. New York (NY): Springer 2013.
- Joseph A, Mohan S, Sujith Kumar CS, et al. An experimental investigation on pool boiling heat transfer enhancement using sol-gel derived nano-CuO porous coating. Exp Therm Fluid Sci. 2019;103:37–50. doi:10.1016/j.expthermflusci.2018.12.033
- Armelao L, Barreca D, Bertapelle M, et al. A sol–gel approach to nanophasic copper oxide thin films. Thin Solid Films. 2003;442(1):48–52. doi:10.1016/S0040-6090(03)00940-4
- Bortoleto EM, Rovani AC, Seriacopi V, et al. Experimental and numerical analysis of dry contact in the pin on disc test. Wear. 2013;301(1):19–26. doi:10.1016/j.wear.2012.12.005
- Kulkarni MV, Elangovan K, Reddy KH, et al. Tribological behaviours of abs and pa6 polymer-metal sliding combinations under dry friction, water absorbed and electroplated conditions. J Eng Sci Technol. 2016;11:68–84.
- Popescu D, Zapciu A, Amza C, et al. FDM process parameters influence over the mechanical properties of polymer specimens: A review. Polym Test. 2018;69:157–166. doi:10.1016/j.polymertesting.2018.05.020
- Sudeepan J, Kumar K, Barman T, et al. Study of friction and wear of ABS/Zno polymer composite using taguchi technique. Procedia Mater Sci. 2014;6:391–400. doi:10.1016/j.mspro.2014.07.050
- Rahmatabadi D, Soltanmohammadi K, Pahlavani M, et al. Shape memory performance assessment of FDM 3D printed PLA-TPU composites by box-Behnken response surface methodology. Int J Adv Manuf Technol. 2023;127:1–16.
- Wu L, Zhang Z, Yang M, et al. Facile synthesis of CuO/g-C3N4 hybrids for enhancing the wear resistance of polyimide composite. Eur Polym J. 2019;116:463–470. doi:10.1016/j.eurpolymj.2019.04.041
- Wu J, Huang X, Berglund K, et al. Cuo nanosheets produced in graphene oxide solution: An excellent anti-wear additive for self-lubricating polymer composites. Compos Sci Technol. 2018;162:86–92. doi:10.1016/j.compscitech.2018.04.020
- Larsen TØ, Andersen TL, Thorning B, et al. Changes in the tribological behavior of an epoxy resin by incorporating CuO nanoparticles and PTFE microparticles. Wear. 2008;265(1):203–213. doi:10.1016/j.wear.2007.10.003
- Jatti VS, Singh TP. Copper oxide nano-particles as friction-reduction and anti-wear additives in lubricating oil. J Mech Sci Technol. 2015;29(2):793–798. doi:10.1007/s12206-015-0141-y
- Savvakis K, Petousis M, Vairis A, et al., editors. Experimental determination of the tensile strength of fused deposition modeling parts. ASME international mechanical engineering congress and exposition. Montreal (QC): American Society of Mechanical Engineers; 2014. p. V014T11A022.
- Wu W, Geng P, Li G, et al. Influence of layer thickness and raster angle on the mechanical properties of 3D-printed PEEK and a comparative mechanical study between PEEK and ABS. Materials. 2015;8(9):5834–5846. doi:10.3390/ma8095271
- Jayanth N, Senthil P, Prakash C. Effect of chemical treatment on tensile strength and surface roughness of 3D-printed ABS using the FDM process. Virtual Phys Prototyp. 2018;13(3):155–163. doi:10.1080/17452759.2018.1449565
- Torres J, Abo E, Sugar AJ. Effects of annealing and acetone vapor smoothing on the tensile properties and surface roughness of FDM printed ABS components. Rapid Prototyp J. 2023;29(5):921–934. doi:10.1108/RPJ-03-2022-0088
- Garg A, Bhattacharya A, Batish A. Chemical vapor treatment of ABS parts built by FDM: analysis of surface finish and mechanical strength. The International Journal of Advanced Manufacturing Technology. 2017;89:2175–2191. doi:10.1007/s00170-016-9257-1
- Wu W, Jiang J, Jiang H, et al. Improving bending and dynamic mechanics performance of 3D printing through ultrasonic strengthening. Mater Lett. 2018;220:317–320. doi:10.1016/j.matlet.2018.03.048
- Mohamed OA, Masood SH, Bhowmik JL. A parametric investigation of the friction performance of PC-ABS parts processed by FDM additive manufacturing process. Polym Adv Technol. 2017;28(12):1911–1918. doi:10.1002/pat.4080
- Dhandapani A, Krishnasamy S, Nagarajan R, et al. Investigation of wear behavior in self-lubricating ABS polymer composites reinforced with glass fiber/ABS and glass fiber/carbon fiber/ABS hybrid. Lubricants. 2023;11(3):131. doi:10.3390/lubricants11030131