ABSTRACT
Three-dimensional (3D) printing has been profoundly changing the production mode of traditional industries. However, this technique is usually limited to metre-scale fabrication, which prevents large-scale 3D printing (LS3DP) applications such as the manufacturing of buildings, aircraft, ships, and rockets. LS3DP faces great challenges, particularly, it not only requires confronting problems not yet solved by conventional 3D printing, such as the inability to print functional structures due to limitations by single-material manufacturing, but also needs to overcome the size effect limitation of large-scale printing. Here, we systematically review the state of the art in the integration of materials and technologies in LS3DP. We also demonstrate some disruptive engineering cases of LS3DP in the field of construction. The challenges and strategies for overcoming size constraints to achieve LS3DP of functional structures are discussed, including multifunctional 3D printing processes from nano- to large-scale and large-scale 4D printing processes, diverse printable materials and sustainable structures, horizontal and vertical size-independent printers, collaborative and intelligent control of the entire process, and extreme environment printing. These strategies can provide tremendous opportunities for the fully automated, intelligent, and unmanned production of these different material megastructures and internal multiscale multifunctional components such as buildings/structures, aerospace vehicles, and marine equipment.
1. Introduction
Additive manufacturing (AM), or 3D printing, is a disruptive and sustainable digital technology that can automatically produce 3D complex physical objects that are indistinguishable from their target objects directly from 3D digital models, without human intervention in the printing process [Citation1–3]. Herewith, AM is about to change the business models, design methods, production methods and industrial chains of traditional industries [Citation4,Citation5]. Compared to traditional manufacturing methods, the significant advantages of 3D printing can provide extraordinary freedom to achieve controlled composition, geometry, complexity and functionality [Citation6]. Specifically, with its high degree of mechanisation and fully automated manufacturing, this technology improves production efficiency, safety and product quality, reduces resource waste [Citation7], minimises the use of labour [Citation8], and lowers production costs [Citation9,Citation10]. In addition, 3D printing offers the opportunity to digitally and flexibly manufacture complex structures that can be customised [Citation3,Citation11], and can be optimised to improve designs for better performance and functionality [Citation12], while saving materials and even creating new structures that were previously unattainable. These advantages have made 3D printing a practical technology that is beginning to be used in many different industries [Citation13] and is gradually expanding [Citation14].
For example, this fully automated digital technology has already been widely used in end-use production for consumers (smartphone assemblies [Citation15], wearable electronics [Citation16], food [Citation17], robot parts [Citation18], etc.), electronic information (Li-ion battery architectures [Citation19], piezoresistors [Citation20], microelectrodes [Citation21], capacitors [Citation22], organic electronic devices [Citation23], etc.), biomedical applications (medical equipment components [Citation24], scaffolds [Citation25], tissues [Citation26], artificial organs [Citation27], medicines [Citation28], bacterial communities [Citation29], etc.), and chemical industry applications (catalysts [Citation30], desalination spacers [Citation31], etc.). Collectively, these applications of traditional 3D printing tend to be concentrated at the desktop scale [Citation6], which has mostly been limited to the micrometer to decimetre scale, except for a few nanoscale applications.
To extend the benefits of this automated digital technology beyond small-scale 3D printing, a large-scale 3D printing (LS3DP) for the automated AM of huge structures has been developed as a solution to overcome manufacturing size limitations. Huge structures [Citation2] here are usually larger than 1 m in size and specifically include buildings/structures/space bases, automobiles, aircraft, rockets, high-speed trains and ships. As one of the representative LS3DP technologies, construction 3D printing (C3DP), has been developed for automated AM of buildings/structures (also infrastructure, space bases, etc.), aiming to change the way of production in the construction industry.
Several pioneers have initiated the research and applications of LS3DP. For example, a large format polymer 3D printing was pioneered by ORNL in 2013 [Citation32] and later commercialised by Cincinnati Incorporated. Afterwards, some 3D printers with a working range of more than 1 m (Voxeljet [Citation33], mobile printers [Citation34], KamerMaker [Citation35], SLA machines [Citation3], etc.) have been invented. A large-format 45-degree printing has been introduced by Thermwood and Ingersoll Machine Tool as ways to make LS3DP larger. This automated LS3DP technology has been used to print metallic components for aircraft with lighter weight, higher performance [Citation36,Citation37]. Furthermore, the technology has been used to print plastic components or metal parts for cars [Citation1,Citation38,Citation39] and customised car bodies (e.g. the Strati car was printed by Local Motors), metal thrusters and stainless steel engine components for rockets [Citation1,Citation40], metal propellers for ships [Citation41], stellarators and ceramic structures for nuclear industrial equipment [Citation42,Citation43], alloy steel core parts for high-speed trains [Citation44], complex concrete components for buildings [Citation3,Citation45–47], entire houses (e.g. some bio-based houses were printed by University of Maine), etc. In addition, the development of plastic and metal large format 3D printers from Ingersoll system, WIRE-ARC AM metal 3D printers from AML3D, additive and subtractive hybrid 3D-printers from Big Metal Additive, robotic arc welding 3D printers from Wolf Robotics and laser metal deposition with wire 3D-printing technology from GKN Aerospace offer possibilities for LS3DP applications. In fact, the advantages of LS3DP have been demonstrated in construction and nuclear industry applications. In particular, LS3DP can fundamentally change the high risk, harsh operating environment, labour intensity, and environmental pollution [Citation48,Citation49] in these industries.
As these industries continue to benefit from LS3DP in terms of freedom of design and smart manufacturing [Citation50,Citation51], one potentially revolutionary step in the transition of LS3DP is to achieve full-size automated printing of mega-structures and their functions [Citation52]. However, it is undeniable that this highly interdisciplinary research effort is still in its infancy [Citation53,Citation54] and that the application of LS3DP technology is mostly limited to the metre scale fabrication [Citation2,Citation11]. Moreover, unlike conventional 3D printing, LS3DP faces greater challenges due to size effects, notably to a necessary compromise between accuracy and efficiency [Citation2]. That is, the size effects dramatically magnify the requirements for various processes, material performance, equipment configurations, and 3D spatial control involved in LS3DP. This would result in printed products that exhibit dispersion and uncertainty in shape, accuracy, quality and performance [Citation2]. Even worse, printing large structures cannot omit challenges in small and conventional scale 3D printing, as printing at this scale still faces some limitations. Specifically, only a single material structure or part can usually be printed using the same printer [Citation1], while most printers cannot print multifunctional components or structures.
Here, we systematically report current the state of the art in the integration of materials and technologies in LS3DP represented by C3DP, including feasible printing processes, available printing materials and their property space maps, general printing equipment, and core printing controls. We also demonstrate some disruptive cases of LS3DP represented by C3DP, such as a 6 m high 3D printed habitable and deliverable two-story building and a 21.6 m long 3D printed bridge. In parallel, we analyze the relationship between C3DP and LS3DP. On this basis, we finally describe the challenges and strategies for overcoming size constraints to achieve LS3DP of functional structures.
2. LS3DP materials and technologies
2.1. 3D printing processes
Unlike traditional subtractive manufacturing, the cornerstone of 3D printing is a digital process to layer-by-layer fabrication, which allows manufacturing flexibility by optimising the process balance supply process [Citation55,Citation56]. The International Organization for Standardization Technical Committee on Additive Manufacturing (ISO/TC 261) and the American Society for Testing and Materials Technical Committee on 3D Printing (ASTM/F42) have defined seven basic 3D printing processes ((A)), including binder jetting (BJT), vat photopolymerization (VPP), powder bed fusion (PBF), material extrusion (MEX), material jetting (MJ), sheet lamination (SHL), and direct energy deposition (DED) [Citation1,Citation57]. Each of the basic 3D printing processes has produced some representative commercial technologies [Citation58], e.g. the representative processes for MEX are fused filament fabrication (FFF) and fused deposition modelling (FDM).
Figure 1. Evolution of the LS3DP process and its feasible processes for LS3DP represented by C3DP. (A) Classification of 3D printing processes and their representative processes. (B) Feasible LS3DP processes represented by C3DP and their respective percentages. (3DP: 3D printing; SLA: stereolithography apparatus; DLP: digital light processing; 3SP: scan-spin-selective photocure; CLIP: continuous liquid interface production; SLS: selective laser sintering; DMLS: direct metal laser sintering; SLM: selective laser melting; EBM: electron beam melting; SHS: selective heat sintering; MJF: multijet fusion; FFF: fused filament fabrication; FDM: fused deposition modelling; SCP: smooth curvature printing; MJM: multijet modelling; LOM: laminated object manufacture; SDL: selective deposition lamination; UAM: ultrasonic additive manufacturing; LMD: laser metal deposition; LENS: laser engineered net shaping; DMD: direct metal deposition; GMAW: gas metal arc welding; Respective percentages: statistical results of the use of 3D printing processes by institutions or research groups in the field of construction, percentage using MEX, BJT and DED) [Citation1,Citation57].
![Figure 1. Evolution of the LS3DP process and its feasible processes for LS3DP represented by C3DP. (A) Classification of 3D printing processes and their representative processes. (B) Feasible LS3DP processes represented by C3DP and their respective percentages. (3DP: 3D printing; SLA: stereolithography apparatus; DLP: digital light processing; 3SP: scan-spin-selective photocure; CLIP: continuous liquid interface production; SLS: selective laser sintering; DMLS: direct metal laser sintering; SLM: selective laser melting; EBM: electron beam melting; SHS: selective heat sintering; MJF: multijet fusion; FFF: fused filament fabrication; FDM: fused deposition modelling; SCP: smooth curvature printing; MJM: multijet modelling; LOM: laminated object manufacture; SDL: selective deposition lamination; UAM: ultrasonic additive manufacturing; LMD: laser metal deposition; LENS: laser engineered net shaping; DMD: direct metal deposition; GMAW: gas metal arc welding; Respective percentages: statistical results of the use of 3D printing processes by institutions or research groups in the field of construction, percentage using MEX, BJT and DED) [Citation1,Citation57].](/cms/asset/ea013c1f-47fa-48cc-9d9f-969b6e854ecf/nvpp_a_2346821_f0001_oc.jpg)
Current LS3DP processes have evolved from 7 basic 3D printing processes based on traditional industrial materials. For instance, the evolutionary processes of material extrusion have generally been applied to 3D printed buildings, and the derivative processes of powder bed fusion, direct energy deposition and sheet lamination are normally used for 3D printed aerospace components. To meet the increasing requirements of printing structure functions, and make it possible to print large-scale structures, the LS3DP process represented by C3DP has been investigated. Various new LS3DP processes ((B)) have been enriched and developed based on these original basic 3D printing processes. Based on our preliminary statistical work [Citation59], we further estimate that 3D printing processes have been used by a large number of institutions or research groups around the world in the field of construction. We found that all these processes have evolved from basic 3D printing processes and that the original basic 3D printing processes used were MEX, BJT, and DED, which accounted for 95.2%, 2.4%, and 2.4% of the total, respectively. Two types of LS3DP processes, unheated extrusion and heated extrusion, were developed based on the MEX process, accounting for 83.0% and 12.2% of the statistics, respectively. The LS3DP processes for unheated extrusion included contour crafting (CC) [Citation60,Citation61], concrete printing (CP) [Citation62–64], etc. The CC process extrudes cement-based material while smoothing the printed layers using a printing head with trowels, prints layer by layer to form a contoured hollow wall, places reinforcement inside the hollow structure and fills it with the same material as the printed structure [Citation60,Citation61]. The CP process forms a print layer by continuously extruding high-performance concrete (HPC) [Citation62,Citation63] or ultrahigh-performance concrete (UHPC) [Citation64], lays a reinforcement mesh on the surface of the printed layer, and repeats the extrusion until the printing structure is complete and the reinforcement is implanted. The LS3DP processes for heated extrusion were developed mainly based on the FDM for the MEX process. For example, we developed a full-size 3D printing polymer material process based on the FDM-like process [Citation52], which heats and melts the polymer material through the nozzle of the ultra-large 3D printing equipment, continuously extrudes and stacks, synchronously and dynamically compacts the printing layer, and solidifies to form a large structure. Based on the BJT process, LS3DP processes were developed, such as the D-shape process [Citation65]. Based on the DED process, some LS3DP processes, such as MX3D, have been explored [Citation66].
In fact, the LS3DP process described above has proven to be capable of printing fairly large buildings and structural components (10 m class) [Citation3], with great potential to facilitate the automated construction of entire structures as well as large-scale components. However, it should be added that there are many LS3DP processes that can evolve from 7 basic 3D printing processes, and in the evolution and development of LS3DP processes represented by C3DP, most of them chose the above three basic processes, especially the MEX process, which occupied an overwhelming proportion. The main reason for this is that researchers and practitioners continue to use similar construction mode of plain concrete and reinforced concrete in C3DP and that the inherent characteristics of those materials used limit the process choice. That is, concrete exhibits inhomogeneity and anisotropy, which implies that one will not be able to achieve rapid printing of complex structures if other processes are chosen [Citation67].
Similarly, in addition to C3DP, current LS3DP processes continue to evolve from 7 basic 3D printing processes based on traditional industrial materials. For instance, the derivative processes of BJT, DED and SHL are normally used for 3D printed aerospace components. Therefore, it is necessary to break through the traditional production methods based on the characteristics and advantages of AM, and develop innovative processes suitable for LS3DP according to different needs.
2.2. 3D printing materials
In addition to the approach of print layer deposition, one of the most important factors in determining the type of LS3DP process is the ink used (i.e. the 3D printing material). For example, the most widely used LS3DP processes, i.e. CP, D-Shape and MX3D, use different materials, namely, cement-based, granular and metallic materials, respectively. For LS3DP, the fundamental principle that makes AM possible is the ability to selectively control material deposition or material phase transition [Citation5]. The base material used determines the performance and mechanical behaviour of the printed structure and affects the function of the manufactured part [Citation9], so materials are critical to LS3DP. Moreover, LS3DP has extremely high requirements for the safety of the structure, and the performance of the formed structure obtained by printing and stacking layer by layer must not differ too much from those of the original base material, otherwise the safety of the structure will be compromised. Several comparative experimental studies of scaled printed specimens of LS3DP have been conducted [Citation4,Citation66,Citation68–70], and microscopic observations have revealed that there are differences in the microstructure between the 3D printed structure and the basic material. The printed structures using different materials have different levels of layered or long-grained microstructures, and the structures present a certain anisotropy. However, the mechanical properties and failure characteristics of the printed structures were tested extensively, and the results show that the mechanical properties of the printed structures are not significantly weakened [Citation66,Citation68,Citation69]. Therefore, the safety performance of printed structures for LS3DP still depends on the choice of their base printing material.
According to the physical state of the materials before deposition [Citation71], 3D printing materials can be classified as liquid materials, powder materials, viscous materials, solid materials, etc., while according to the chemical properties of the materials, they can be divided into polymer-like materials, metalic materials, inorganic nonmetallic materials and their composite materials. We counted the 3D printing materials available for LS3DP, and their property space map is shown in . The available 3D printing materials mainly include cement-based materials, granular materials, metallic materials, wood-based materials, polymers, ceramics, and regolith. When the Young's modulus and strength values of the LS3DP available materials are compared with their densities of approximately 230-7980 kg/m3, a spatial map of material properties can be obtained and easily analyzed.
Figure 2. Available printing materials and their property space maps for LS3DP. (A) Young's modulus versus density. (B) Strength versus density.
Note: the strength of the cement-based, granular, ceramic, regolish material and metallic, wood-based and polymer materials are the compressive strength and tensile strength.
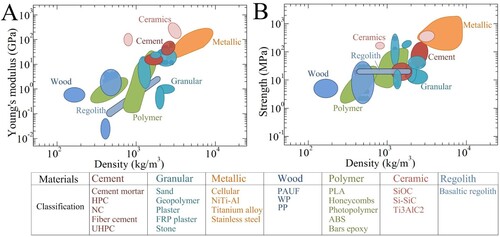
Cement-based materials (Cement in ) are the most commonly used materials for LS3DP in the field of construction due to their high modulus of elasticity and compressive strength. Specifically, cement-based materials have evolved from cement mortars without coarse aggregates and fibre-reinforced cements [Citation72–75] to normal concrete (NC) [Citation76–78], high-performance concrete (HPC) [Citation79], and ultrahigh-performance concrete (UHPC) [Citation64]. Importantly, the performance of cement-based materials can be improved by adding reinforcing materials, including the fibres of photopolymer, polymer-based resin, polyvinyl alcohol, polypropylene (PP), hydroxypropyl methyl, polyethylene, plant (sisal, bamboo), basalt, glass, steel, titanium alloy, and carbon. Granular materials (Granular in ) are also among the materials commonly used for LS3DP in the construction field. These materials typically consist of a mixture of powder and binder (Plaster in ) [Citation69], sand and binder [Citation8], geopolymer-based materials (Geopolymer in ) [Citation80–82] plaster reinforced with high-strength fibre-reinforced polymers (FRP plaster in ) [Citation83] and stone powder (Stone in ) [Citation65]. These granular materials have a wide range of densities, Young's modulus and compressive strengths depending on the powder, binder and reinforcing material. Metallic materials (Metallic in ) have high strength and high stiffness [Citation83], so they can be used for manufacturing large complex structures using LS3DP. These structures are made of titanium alloys [Citation84,Citation85], metal matrix composites (nickel-titanium-aluminum, NiTi-Al) [Citation86], stainless steel material (Stainless steel in ) [Citation66,Citation87,Citation88], aluminum alloys [Citation89,Citation90], copper, gold, magnesium, nickel-base alloys [Citation91], tungsten, metallic cellular materials (Cellular in ) [Citation92], etc. Wood-based materials (Wood in ), as an environmentally friendly organic material, with better properties (e.g. low density of 140–550 kg/m3 [Citation93]), selectively bonded by appropriate binders, can be another ideal material [Citation94,Citation95] for LS3DP to manufacture large scale components of almost any desired shape [Citation96]. Some binders such as polylactic acid (PLA) [Citation97], polyvinyl acetate and urea–formaldehyde (PAUF in ) [Citation95] as well as PP [Citation98], were chosen to improve the mechanical properties of the wood powder (WP in ). Polymers (Polymer in ), as one of the most widely used and mature traditional 3D printing materials, can also be used for LS3DP (such as printed moulds or formworks). These polymers include acrylonitrile butadiene–styrene (ABS) [Citation99–101], photopolymer [Citation102,Citation103] and PLA [Citation104]. 3D printed cellular composites (Bars epoxy and honeycombs in ) [Citation105] yield polymers with low density (less than 200 kg/m3), high specific stiffness and tensile strength. Ceramic materials (Ceramic in ) have impressive properties including high temperature capability, environmental resistance and high strength, and can be used to print large core components [Citation106,Citation107]. Various ceramic compositions, such as SiOC [Citation108], Ti3AlC2 [Citation109], Si-SiC [Citation110] and CMCs (ceramic matrix composites) [Citation111], can be processed with 3D printing and postprocessing. In addition, the readily availability of basaltic regolith, its high compressive strength and the relatively high tensile strength for terrestrial basalt indicate that cast basalt may be an ideal material for the LS3DP of manned outposts (space bases) on the Moon for space exploration [Citation65,Citation112]. Some materials such as glass, soil and bio-based materials can also be used for LS3DP.
Currently, the materials used in LS3DP mimic those available in conventional manufacturing [Citation2]. For example, 3D-printed buildings/structures usually employ concrete materials or wood-based materials. 3D-printed parts for aircraft and rockets typically use alloys or metallic materials. For LS3DP, on the one hand, testing by means of scaled-down printed specimens no longer fully reflects the true performance of large printed structures. On the other hand, the bonding between large printed layers, material defects (cracks, residual stresses) and various anisotropies can no longer be overlooked. Therefore, the materials developed and adopted for LS3DP not only have to fulfil the printable properties of the layer-by-layer AM process, but also need to overcome printed layer defects to ensure that the final printed structure meets the design requirements.
2.3. 3D printing equipment
The fundamental method and direct execution tool to build structures automatically layer by layer is 3D printing equipment (also known as 3D printers). This equipment usually consists mainly of a printing head for delivering material, a frame system equipped with the printing head and a control system, which allows the printing head to move at a predetermined position and deliver material. The 3D printing equipment ((A)) of LS3DP that has been invented and commonly used in the field of construction can be divided into four types according to their main structural forms and degrees of freedom (DOFs) of motion, namely, gantry [Citation113,Citation114], truss [Citation65], robotic arm [Citation66,Citation115], and tower [Citation116,Citation117]. We analyzed these four types of equipment, which accounted for 36.6%, 26.8%, 31.7% and 4.9% of the statistics, respectively, with more applications of truss and robotic arm equipment. The gantry equipment has a large self-weight and cannot be moved after installation. This equipment is more suitable for indoor printing (i.e. printing components indoors and assembling them on site) large-scale structures, with extremely high positioning accuracy due to its high rigidity. The robotic arm itself can be moved or moved by lifting, which is suitable for printing small structures on site or indoors, or adding rails or positioning devices for printing large structures with high positioning accuracy. The tower equipment can be moved by lifting, which is more suitable for on-site printing. However, the weight and deflection of the cantilever structure limits the ability to print structures that are too large, and the positioning accuracy is not high. DOF is normally important when a multi-orientation of material building is concerned. Positioners may be used to facilitate AM flexibility and create a dexterous workspace. This is related to the complexity of the printed object. Both the gantry and truss equipment usually have only 3 DOFs of motion, which are suitable for printing structures with relatively simple shapes, while the robotic arm and the tower equipment usually have 6 and 4 DOFs of motion, which are suitable for printing structures with relatively complex shapes. Based on this equipment, several more complete system ((B)) with 6 DOFs of motion, such as vehicle robotic arms [Citation112], cable-positioning systems (i.e. line-driven printers or hang printers) [Citation118–120] and truss robotic arms [Citation121,Citation122], were developed to accommodate the printing of more complex and larger structures.
Figure 3. Classification of 3D printing equipment and their core printing actuator for LS3DP represented by C3DP. (A) 3D printing equipment commonly used for construction and their respective percentages (gantry, truss, robotic arm and tower, usually with 3, 3, 6 and 4 DOFs respectively). (B) Specific 3D printing equipment for construction (vehicle robotic arm, cable-positioning and truss robotic arm, usually with 6, 6 and 6 DOFs respectively). (C) Classification of printing heads for the LS3DP equipment for construction (heating extrusion, pressure extrusion, screw extrusion and welding deposition).
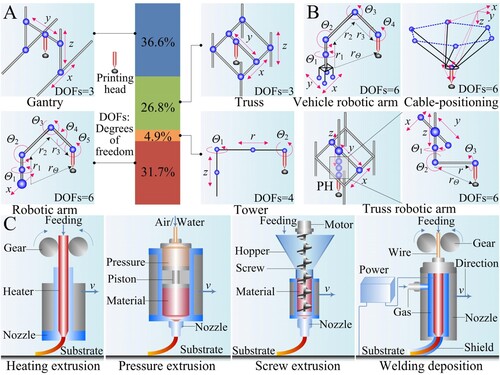
The type of the main structure of the equipment proved to be important, but it does not determine the type of 3D printing process. For example, D-shape and CP are two different printing processes that usually use the same type of equipment (e.g. a truss-based equipment), while on the other hand all four types of equipment can be used for the same process (e.g. the MEX process). In addition, the structural performance of LS3DP equipment for construction needs to be significantly improved compared to traditional 3D printing. For example, LS3DP equipment may be heavy and long-range due to its increased size, which means stiffness is a critical factor. Vibrations may be generated during motion and propagate from the base to the end-effector, affecting manufacturing accuracy. Additionally, with SLM, the roller may damage the deformed part (the wrapping border) during interlayer time. These are typical equipment issues that should be addressed. However, this is not the main obstacle. The most critical part of 3D printing equipment is the core printing actuator, i.e. the printing head system, which needs to be compatible with the corresponding printing process and material. Depending on the principle of deposition, printing heads for LS3DP equipment are usually classified into four categories ((C)): heating extrusion [Citation123–125], pressure extrusion [Citation123,Citation124,Citation126], screw extrusion [Citation123,Citation124], and welding deposition [Citation127,Citation128]. In a sense, the printing head serves to eject droplets of adhesive, or liquid-to-solid compounds, which form a layer of the rapid prototyping structure [Citation55], and can even visually represent the printing process. For example, one printing process that carries a screw extrusion printing head that extrudes material through a compound nozzle assembly and smooths the printed layers by using trowels is the CC process [Citation113,Citation114]. The most significant feature of the D-shape process is that its printing head consists of a set of pressure extrusion spraying nozzles [Citation65]. Extruding material through a pump-mounted screw extrusion printing head is one of the main features of the CP process [Citation62,Citation129]. Deposition material with one welding deposition printing head based on GMAW is a unique feature of MX3D [Citation66,Citation115]. Furthermore, we invented the polymer super LS3DP equipment that carries a heating extrusion printing head called SCG-FDM [Citation52]. It should be noted that although the main structure of the 3D printing equipment does not determine the type of 3D printing process, the LS3DP equipment needs to choose the appropriate main structure according to the different printing objects and printing heads (type, weight, etc.). For example, gantry and tower equipment is usually chosen for MEX processes with a single heavy-duty printing head. Robotic arm equipment is typically used for DED printing processes with a single printing head. Truss equipment is usually chosen for printing processes with multiple printing heads (e.g. BJT process) or array lasers (e.g. SLM process).
2.4. 3D printing controls
Another key requirement that makes AM possible at a large scale is the ability to control the printing operations efficiently and precisely while ensuring the safety of the printing process as well as the performance and quality of the printed structures. Taking the CC process of LS3DP in the construction field as an example, we demonstrate the core control technologies () involved in the full process of these printing operations. Typically, these core technologies include material control (M), 3D spatial control (S), printing control (P) and deviation control (D).
Figure 4. Core control technologies and their control equations for LS3DP represented by C3DP. (X: Shape of the printed layer or structure; f: Printing control equation for LS3DP; P: Printing control; S: 3D Spatial control; M: Printing control; X0: Other factors affecting the shape of the printed layer or structure; Δ: Deviation control; H: Scale of printing structure; V: Speed of movement for printing head; W: Angular speed of rotation for printing head; R: Nozzle diameter; F: Extrusion pressure; v: Extrusion speed; D: Standoff distance; u: Flow rate; tg: Time gap; T: Extrusion temperature; TA: Ambient temperature; h: Layer resolution; w: Extrusion width; h0: other factors that affect the h; w0: other factors that affect the w; hs: Layer resolution set by software; ws: Extrusion width set by software; Vx: Speed of movement in the x direction for printing head; Vy: Speed of movement in the y direction for printing head; Vz: Speed of movement in the z direction for printing head; ρ: Density of the material using LS3DP; E: Elastic modulus of the material using LS3DP; C: Compressive strength of the material using LS3DP; Δp: Path deviation; Δs: Shape deviation).
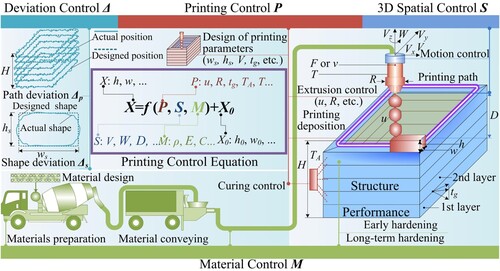
Material control, as defined here, mainly includes material design (e.g. setting time, and properties), material preparation (e.g. mixing), material conveying (or pumping), early curing and hardening of the printed layer, and long-term hardening of the printed structure. This should satisfy pumpability, extrudability and buildability during printing [Citation130] and achieve the desired mechanical properties (density ρ, elastic modulus E, compressive strength C, etc.) after printing and hardening, as well as satisfy long-term structural performance (cracking, shrinkage, durability, etc.) [Citation129].
3D spatial control mainly includes the movement and rotation motion control of the printing head [Citation5] and the distance control between the printing head nozzle and the printing layer. Specifically, the control parameters are the speed of movement for the printing head (V), the angular speed of rotation for the printing head (W) and the standoff distance (D). For efficient 3D spatial control, it is necessary to study reasonable path planning algorithms [Citation113] to optimise the printing path based on simulation before printing and achieve effective control of the position of the printing head during the printing process.
Printing control, as defined here, mainly includes the design of the printing parameters (extrusion width w, layer resolution h, printing head speed of movement V, time gap tg, etc.), extrusion control (flow rate u, nozzle diameter R, extrusion temperature T, nozzle shape, etc.), printing deposition (i.e. geometry control of printing layer) [Citation131] and curing control (curing temperature Tc, etc.), which aims to build the same structure as the designed 3D digital model and meet the shape, performance and functional requirements.
Deviation control mainly includes the control of path deviation Δp (i.e. position deviation) and shape deviation Δs (i.e. geometric deviation). In the absence of monitoring and regulation, it consists of equipment errors and printing deviations. The deviation control [Citation67] finally makes the deviation of the printed structure from the design model within the allowed error range.
Material control, 3D spatial control, and print control are not separate aspects but are mutually adaptive and coordinated, and must be considered in synergy with the material scale, printing path scale, and global shape scale [Citation1,Citation64] both temporally and spatially. In fact, for LS3DP processes (such as the CC process), these factors seem to be difficult to control except for the print path scale, and the control process requires not only controlling the rheology of the extruded material but also the solidification kinetics of the material in interaction with the continuous printing path and the overall shape of the printed structure [Citation64]. In addition, material control involves materials in a time-varying printing process, and 3D spatial control and printing control are the processes that control the dynamic forming of materials. In contrast, the extrudability and buildability of time-varying materials affect and restrict each other [Citation130] and are affected by external environmental conditions such as Tc, which also brings challenges to the control of LS3DP. Therefore, to quantitatively perform LS3DP control, to obtain the desired shape of the printed layer or structure and to obtain accurate geometric dimensions (e.g. h, w), the most central task is to establish the printing control equation () between X and P, S and M. Specifically, the factors affecting the final printing geometric size should be identified through a series of parameter sensitivity tests and simulation analyses before printing, and the quantitative relationship between each factor parameter and the printing geometric size should be established [Citation52]. Using the CC process as an example, these factor parameters typically include V, D, R, u, tg, E, but also dynamic yield stress σD [Citation132], static yield stress σS, etc. Obviously, it is important to note that the printing control equations are different for different printing processes [Citation128]. In the case of printing metallic materials using the DED process, for example, although the objects of control are still X, P, S and M, there are significant differences specifically compared to printing non-metallic materials (e.g. cement-based materials) using the CC process. In terms of material control, printing metallic materials does not require material mixing and pumping, and there is no long-term hardening process, so the mechanical parameters of the material in the print control equations are different. In terms of 3D spatial control, there is not much difference between printing metallic and non-metallic materials. In terms of printing control, the printing parameters involved vary greatly, except for w and h. In terms of deviation control, differences in the materials used can lead to changes in the core control parameters, e.g. printing metallic materials is more concerned with residual stress control.
Another challenge for the control of LS3DP is the size effect, i.e. the conflict between accuracy and efficiency. Suppose a printing scale (H) of 100 m for a high-rise building needs to be constructed with LS3DP. If h and w are set to the mm level in pursuit of higher printing accuracy, then the number of printing layers is 105 (i.e. the ratio of printing structure scale to printing accuracy is equal to 105), and the printing time required (t) is unimaginable. If in pursuit of higher construction speed, h and w are increased to the dm level, and the number of printed layers is 103, then the printing efficiency is increased, but this makes the deviation larger; thus, the printing accuracy cannot be guaranteed. Suppose a component with a small scale of 0.01 m is printed, and the h and w are set to a higher printing resolution (0.1 mm) than that of the high-rise building. However, the ratio of printing structure scale to printing accuracy is only 102. The contradiction between the efficiency and accuracy of large-scale 3D printing [Citation9] is more prominent than that of traditional small-scale 3D printing. To improve the control of materials, geometry and functionality [Citation1] of LS3DP, further research into control techniques is necessary to achieve an optimal balance of efficiency and accuracy [Citation67]. These control techniques, such as path planning, are critical for optimising the 3D printing process, especially in achieving efficient and precise printing of complex structures. It involves volume decomposition and slicing techniques, path generation methods, and joint trajectory planning software [Citation133]. For LS3DP, adaptive methods and algorithms need to be investigated, such as a top k% path planning method for multi-robot cooperative wire arc AM of large-scale metal parts [Citation134], a modified genetic algorithm for resource-constrained scheduling of multi-robot cooperative 3D printing [Citation135] and an optimised scheduling algorithm of the multi-robot printing platform based on efficiency egalitarianism [Citation136].
This means that high-precision and high-efficiency control of LS3DP is not impossible if the conflict between accuracy and efficiency is effectively resolved, and reasonable printing control equations are established.
3. LS3DP applications
3.1. Manufacturing/construction approaches
To overcome the limitation of printing size, there are two approaches to fabricate/construction large structures for LS3DP applications [Citation2]. The first is a manufacturing method based on spatial dimension (i.e. prefabricated 3D printing). Large structures are divided into suitable small components, which are printed, and these small printed components are then assembled by hand or by machine through reliable connectors. The second is a manufacturing method based on temporal dimension (i.e. overall 3D printing). Large structures are divided into small layers with suitable thickness and the large structures are then printed layer by layer based on this thickness. Currently, most LS3DP application cases still use the prefabricated 3D printing approach.
3.2. LS3DP statistics and disruptive cases
Due to the research and development of the above 3D printing technologies, LS3DP has been gradually applied to the field of construction worldwide, including printing non-load-bearing structures [Citation137,Citation138] such as decorations, landscapes, complex nodes and shaped formwork, printing horizontal and vertical lightweight load-bearing structures [Citation139,Citation140], and printing buildings and structures [Citation141].
We statistically analyzed key quantitative indicators of LS3DP, as shown in (A). LS3DP key quantitative indicators mainly include the largest printed structure VL, total printing volume VT and volumetric printing rate RV. VL, VT and RV reflect the maximum volume of the printed structure or the assembled structure of the printed components, the maximum printing volume of the 3D printing equipment, and the maximum printing rate, respectively (see the detailed definitions of quantitative indicators in the literature [Citation142]). Statistics show that VL is approximately between 0.14 and 6080 m3, with an average of approximately 472 m3. VT is approximately between 2 and 9000 m3, with an average of approximately 1016 m3. RV is approximately between 0.0006 and 3.6 m3/h, with an average of approximately 0.452 m3/h.
Figure 5. Statistical analysis and disruptive cases of LS3DP for construction. (A) Statistical analysis of the construction mode of LS3DP and its quantitative indicators (the construction mode includes printed components + assembly and on-site printing; quantitative indicators include VL, VT and RV; most quantitative indicator data are not directly available, but are approximations obtained through estimation, which can be estimated by referring to the method in the literature [Citation142]). (B) China's first polymer 3D printed bridge, the Shanghai Putuo Bridge (the length, width and height of the 3D printed bridge are 15.3, 3.8 and 1.2 m respectively). (C) Quanzhou 3D printing bridge (the length, width and height of the 3D-printed bridge are 17.5, 3.2 and 3.2 m respectively). (D) World's longest polymer 3D printed bridge, Chengdu Bridge (the total length of the bridge is 66.8 m, of which the 3D printed part is 21.6 m long, the widest section is 8 m and the highest section is 2.7 m). (E) The largest single-story 3D printed building in China, the Visitor Service Center of Nanjing Jiangbei New Area Civic Center (the building area is 286 m2 and the height is 5.2 m). (F) A single-story 3D printed building in China, the 3D Daichuang Activity Center of Nanjing (the building area is 98.5 m2 and the height is 5.6 m). (G, H and I) China's first integrated 3D printed habitable and deliverable two-story building (the building area is 52.8 m2 and the height is 6 m [Citation143]). (Here, the data are based on the statistics of application projects, the same project can be completed by multiple organisations, and the same organisation can also adopt different application modes. Projects using the first application mode can be printed as a whole and then assembled on site; projects using the second application mode are not always printed in whole on site; there are also partial components that are printed on-site or indoors and then assembled. CI: Cincinnati Incorporated; ORNL: Oak Ridge National Laboratory; TJU: Tongji University; SCG: Shanghai Construction Group; SCR: Shanghai Coin Robotics; MB: Mighty building; RO: ROYAL3D; TU/e: Eindhoven University of Technology; LU: Loughborough University; USC: University of Southern California; UGent: Ghent University; TUD: TU Dresden; ETH: ETH Zurich; Winsun: Yingchuang Building Technique; LAG: Liaoning Architecture GreenPrint; NJK: Nanjing Kenyo; SEU: Southeast University; HSG: Henan Space Grey; HEBUT: Hebei University of Technology; CSCEC: China State Construction Engineering Corporation; JTT: Jianyanhua testing (Hangzhou) Technology; ZHA: Zaha Hadid Architects; SMC: Shimizu Corporation; MIT: Massachusetts Institute of Technology; AIS: AI SpaceFactory; BHLT: Beijng Huashang Luhai Technology; THU: Tsinghua University; CIIC: CIIC (Tianjin) Technology; TAM: Twente Additive Manufacturing; B3D: BUILDERA 3D; MU: Monolite UK/ D-shape).
![Figure 5. Statistical analysis and disruptive cases of LS3DP for construction. (A) Statistical analysis of the construction mode of LS3DP and its quantitative indicators (the construction mode includes printed components + assembly and on-site printing; quantitative indicators include VL, VT and RV; most quantitative indicator data are not directly available, but are approximations obtained through estimation, which can be estimated by referring to the method in the literature [Citation142]). (B) China's first polymer 3D printed bridge, the Shanghai Putuo Bridge (the length, width and height of the 3D printed bridge are 15.3, 3.8 and 1.2 m respectively). (C) Quanzhou 3D printing bridge (the length, width and height of the 3D-printed bridge are 17.5, 3.2 and 3.2 m respectively). (D) World's longest polymer 3D printed bridge, Chengdu Bridge (the total length of the bridge is 66.8 m, of which the 3D printed part is 21.6 m long, the widest section is 8 m and the highest section is 2.7 m). (E) The largest single-story 3D printed building in China, the Visitor Service Center of Nanjing Jiangbei New Area Civic Center (the building area is 286 m2 and the height is 5.2 m). (F) A single-story 3D printed building in China, the 3D Daichuang Activity Center of Nanjing (the building area is 98.5 m2 and the height is 5.6 m). (G, H and I) China's first integrated 3D printed habitable and deliverable two-story building (the building area is 52.8 m2 and the height is 6 m [Citation143]). (Here, the data are based on the statistics of application projects, the same project can be completed by multiple organisations, and the same organisation can also adopt different application modes. Projects using the first application mode can be printed as a whole and then assembled on site; projects using the second application mode are not always printed in whole on site; there are also partial components that are printed on-site or indoors and then assembled. CI: Cincinnati Incorporated; ORNL: Oak Ridge National Laboratory; TJU: Tongji University; SCG: Shanghai Construction Group; SCR: Shanghai Coin Robotics; MB: Mighty building; RO: ROYAL3D; TU/e: Eindhoven University of Technology; LU: Loughborough University; USC: University of Southern California; UGent: Ghent University; TUD: TU Dresden; ETH: ETH Zurich; Winsun: Yingchuang Building Technique; LAG: Liaoning Architecture GreenPrint; NJK: Nanjing Kenyo; SEU: Southeast University; HSG: Henan Space Grey; HEBUT: Hebei University of Technology; CSCEC: China State Construction Engineering Corporation; JTT: Jianyanhua testing (Hangzhou) Technology; ZHA: Zaha Hadid Architects; SMC: Shimizu Corporation; MIT: Massachusetts Institute of Technology; AIS: AI SpaceFactory; BHLT: Beijng Huashang Luhai Technology; THU: Tsinghua University; CIIC: CIIC (Tianjin) Technology; TAM: Twente Additive Manufacturing; B3D: BUILDERA 3D; MU: Monolite UK/ D-shape).](/cms/asset/d23557fd-8b06-4a94-b01d-5de534151342/nvpp_a_2346821_f0005_oc.jpg)
To further illustrate the buildability of the existing LS3DP technologies, we demonstrate some disruptive cases of LS3DP for the construction field in . China's first polymer 3D printed bridge, the Shanghai Putuo Bridge ((B)), was successfully built by SCG and SCR in January 2019. The length, width and height of the 3D printed bridge are 15.3, 3.8 and 1.2 m, respectively. The bridge was constructed using the construction model of indoor full-scale printing plus an on-site installation, and its 3D printing process was an FDM-like process. The 3D printing material used was a polymer material, namely, a glass fibre reinforced acrylonitrile styrene acrylate copolymer, with a density of 1200 kg/m3, an elastic modulus of approximately 5.5 GPa, and a bending yield strength of approximately 50 MPa. The printing material used in the entire printed bridge weighed approximately 6 tons. The equipment was an internally developed five-axis gantry-type ultra-large high-stiffness 3D printer. The length of the equipment was 25 m, the width was 4 m, the height was 2.5 m, the printing accuracy was approximately 1 mm, the RV was approximately 0.007 m3/h, and the time to print the entire bridge was approximately 4.5 weeks. In the same year, the Quanzhou 3D printing bridge ((C)) was also built by SCG and SCR. The length, width and height of the 3D printed bridge are 17.5 m, 3.2 m and 3.2 m respectively, and the printing material used in the entire printed bridge weighed approximately 12 tons. The bridge was divided into 16 sections, and the construction mode of printing components plus assembly was used. The components were printed indoors and then assembled, after which the whole bridge was transported to the site for installation. The 3D printing process, equipment and materials for the Quanzhou 3D printing bridge were the same as those for the Shanghai Putuo 3D printing bridge, and the RV increased to 0.008 m3/h. The printing of this complex special-shaped bridge took approximately 1 month. The world's longest polymer 3D printed bridge, the Chengdu Bridge ((D)) was successfully built by SCG and SCR in 2021 [Citation144]. The total length of the bridge is 66.8 m, of which the 3D printed part is 21.6 m long, the widest section is 8 m and the highest section is 2.7 m. The printing material used in the entire printed bridge weighed approximately 12 tons. The bridge was divided into 16 sections, and the construction mode was based on indoor printing of the components plus on-site assembly. The 3D printing process and materials for this bridge were the same as those for the Quanzhou 3D printing bridge. The 3D printing equipment was improved to realise the integration of 3D printing and five-axis CNC machining, and the entire printing process of the bridge achieved 7×24 h of uninterrupted printing, which took approximately 35 days. This construction model of indoor printing components plus on-site assembly was used, and the largest single-story 3D printed building in China, named the Visitor Service Center of Nanjing Jiangbei New Area Civic Center ((E)), was built by Nanjing Kenyo and SEU in 2020. The building area is 286 m2, and the height is 5.2 m. The building used a reinforced concrete frame structure, and the height range of the external wavy wall was completed by 3D printing technology. The entire height of the 3D printing wall components are in 10 separate layers, and the number of printed components is 96. Steel trusses were placed during the printing of the walls and the interior was filled with expanded polystyrene insulation after printing was completed. The 3D printing process, materials and equipment adopted were the CP process, PP fibre reinforced concrete and a frame type 3D printing equipment. The density of the 3D printing material used [Citation141] is 2350 kg/m3, the compressive strength is approximately 44.6 MPa, and the flexural strength is approximately 7.4 MPa. The length, width and height of the printing equipment are 3×3×3 m. Based on the same construction model, a single-story 3D printed building in China, named the 3D Daichuang Activity Center of Nanjing ((F)), was built by Nanjing Kenyo and SEU in 2021. The building area is 98.5 m2, and the height is 5.6 m (from outdoor ground to sloped roof). The building also used a reinforced concrete frame structure, but a wood structure was chosen for the roof. The wall was completed by indoor printing components plus on-site assembly. The 3D printing process, equipment and materials for the building were the same as those for the Visitor Service Center of Nanjing Jiangbei New Area Civic Center, while the number of printed components was 16.
Using a construction model based on on-site printing and supplemented by other methods, China's first integrated 3D printed habitable and deliverable two-story building ((G–I), see video [Citation143] for details) was successfully built by SCG, Nanjing Kenyo and SEU in August 2022. The building area is 52.8 m2, and the height is 6 m. This 3D printed building is also called the 3D Printing Science and Technology Demonstration Building Project of SCG [Citation145]. Frame-masonry-laminated slab structures that meet the current Chinese standards were developed and adopted, which created important conditions for the delivery and use of the buildings. The 3D printing process used the CP process, and the 3D printing materials were PP fibre-reinforced concrete materials with and without coarse aggregate, with approximate densities of 2400 kg/m3 and 2300 kg/m3, compressive strengths of approximately 54 MPa and 49 MPa, respectively. A gantry-type mega in-situ 3D printing equipment was developed and used, with a length of 24 m, a width of 8.5 m, a height of 6 m, and an RV of approximately 1.1 m3/h. The effective printing time of the entire building was approximately 50 h. Notably, these 3D printed bridges and buildings mentioned are typically designed to last up to 30 years and 50 years, respectively.
3.3 Relationship between C3DP and LS3DP
LS3DP has been applied not only in the field of construction but also in other fields, for example, it was used to print the wing rib of the Comac C919 aircraft [Citation37], the size of the printed component is 3 m, where the 3D printing process, material and equipment were DMD/laser solid forming, titanium alloy and truss-type equipment, respectively. It was also used to print the 7.6-m-long 3Dirigo2 ship, using the FDM 3D printing process and polymer materials. Moreover, LS3DP was used to print the Relativity Space Terran 1 rocket (33.5 metres high), of which 85% of the rocket body was printed, with the 3D printing process, materials and equipment being DED, alloys and robotic arm plus orbital equipment, respectively.
From these applications mentioned above, we can see that C3DP has learned these processes suitable for LS3DP from other fields (aerospace, automotive, rail transportation, etc.) that use 3D printing. However, C3DP faces greater challenges than other fields due to the more prominent size effects [Citation67] of the time-varying concrete and reinforced multi-material (a habitable building encompasses the vast majority of materials used in almost every other industries) LS3DP processes. Conversely, as the more difficult C3DP processes are researched and developed, other industries can learn from the construction when it comes to large scale.
4. Discussion: challenges and strategies for overcoming size constraints
4.1. Multifunctional 3D printing processes from nano- to large-scale
Although there are many 3D printing processes available for LS3DP, in fact, 3D printing technology can only manufacture an object shell or render a basic shape or a part of an object. It is not even possible to print a truly multifunctional object using 3D printing alone. Broadly, multifunctionality [Citation3] can be interpreted as the introduction of any additional functionality beyond rendering a basic shape (or structure) and the materials it uses. Narrowly, it includes basic shape functions, thermal management, soundproofing, energy storage [Citation64], sensing, transducing, electromagnetic, propulsion utility, etc. [Citation1]. For example, smart structures based on the Internet of Things (IOT) could be printed with LS3DP, which increases the functionality of basic structures by printing the main structure while embedding advanced functional electronic and sensing systems inside [Citation146]. This enables complete interaction between humans and products through monitoring and controlling the basic structure [Citation147]. To achieve multifunctionality in LS3DP, the current limitations implied single-scale, single-material and single-process 3D printing need to be overcome.
4.1.1. Multiscale 3D printing
To achieve multifunctionality for printing structures, LS3DP first requires multiscale 3D printing capabilities (from nano- to large-scale). One large-scale 3D printer is equipped with different-scale printing heads ((A)) [Citation148], or multiple printers carry different scale printing heads for cooperative printing. In addition, this co-printing equipment can either manufacture an object shell (such as a rocket outboard) with large-scale devices or functional components (such as an engine) with macroscale devices. This means that LS3DP is inseparable from conventional, small and nanoscale 3D printing technology [Citation149].
Figure 6. Multifunctional 3D printing processes for LS3DP. (A) Multiscale 3D printing. (B) Multimaterial 3D printing. (C) Multiprocess (or hybrid) 3D printing.
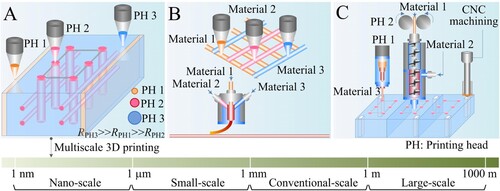
First, it is necessary to further study the technology of conventional scale 3D printing to enable the manufacturing functional components such as generators [Citation150]. Thus, research on small-scale 3D printing is needed, so the resolution of 3D printing can reach submillimeter accuracy. This technique can embed the printed sensor directly into the printed structure during printing [Citation7] or essentially print the entire sensor into the structure. These printed sensors include vibration sensors [Citation151], strain sensors (rigid [Citation152] or flexible [Citation153]), pressure sensors [Citation154], flow sensors [Citation155], acceleration sensors, tactile sensors, environmental sensors, and hybrid sensors [Citation156]. Furthermore, this small-scale 3D printing technology can realise the manufacture of magnets [Citation157], capacitors [Citation158], fuel cells [Citation159], actuators [Citation160], electrodes [Citation161] and electronics circuits [Citation16].
In addition, there is a need to effectively address nanoscale 3D printing technologies to achieve the multifunctionality of objects [Citation162], such as chips at several nanometres [Citation163]. Based on solving the above problems, technologies matching multiscale 3D printing processes should also be developed to achieve synergy between large-scale 3D printing and conventional, small-scale and nanoscale 3D printing.
4.1.2. Multimaterial 3D printing
To achieve the overall 3D printing of a complete functional product, multimaterial 3D printing ((B)) capabilities are needed. Printing a cell phone [Citation164] can be taken as an example, which includes up to 14 types of rigid to flexible materials such as plastic shells, metal and electronics and glass screens. As another example, printing a complex building structure requires a variety of materials such as metallic materials (steel bearing structure), cement-based materials (reinforced concrete, building envelope), granular materials (internal partitions, wall cladding, ceilings), wood-based materials (floors, walls, roofs), glass (glass curtain wall), and polymers (various pipes and cables integrated in the wall). Therefore, to achieve the multifunctionality of printing large structures, the second need for LS3DP is to carry out research on multimaterial 3D printing processes, with possible technical routes including the same printing equipment with a single printing head adapted to serial printing of different materials [Citation165]; the same printing equipment with a single printing head multinozzle adapted to parallel printing of different materials [Citation166]; the same printing equipment carrying multimaterial hybrid printing head for printing [Citation121,Citation167]; the same printing equipment carrying multicolour material printing heads for printing [Citation168]; the same printing equipment carrying different material printing heads [Citation169,Citation170] for seamless, parallel [Citation171] or alternate synergistic printing [Citation148] of different material structures; or different equipment carrying different material printing heads for collaborative printing of different materials. These studies are expected to realise the printing of multiple material functional structures with different properties.
4.1.3. Multiprocess 3D printing
To achieve multifunctionality for printing structures, the third need for LS3DP requires multiprocess or hybrid ((C)) capabilities. For example, when an aircraft is manufactured, different printing processes, materials, and scales of 3D printing equipment are needed to realise the printing of the aircraft fuselage, engines, internal electronic devices and circuits. The possible technical routes for the research and development of multiprocess 3D printing include the following: the same printing equipment carries different printing process printing heads for printing [Citation148]; different equipment carries different printing process printing heads [Citation172] for collaborative printing; integration of the 3D printing process and equal-material manufacturing (e.g. casting [Citation173], robocasting [Citation174], intelligent dynamic slipforming processes [Citation175], automated filling [Citation176]), subtractive manufacturing [Citation177], and complementary processes [Citation1], parallel combinations or switching between them; and the research and development of new multiprocess 3D printing processes. The integration of 3D printing and subtractive manufacturing here has greater potential in multiprocess 3D printing applications, such as the integration process of CNC milling with FDM [Citation178] and arc welding units [Citation179] and the integration process of CNC machining with LMD [Citation180], FFF [Citation181], and DED [Citation182]. This is because it can make full use of the combined advantages of each, while minimising the disadvantages of each process applied separately. The complementary processes include robotic placement [Citation1] during printing, automatic embedding [Citation1,Citation7], automatic implantation [Citation183], simultaneous deployment [Citation122], automatic pick and place [Citation184,Citation185], and automated assembly [Citation186]. The novel multiprocess 3D printing includes the integrated process of printing and electrophoretic deposition [Citation187], the integrated process of printing and automatic weaving [Citation188], and the 3D printing process combining laser-induced forward transfer and photochemical reaction [Citation189]. Furthermore, multifunctional 3D printing allows for the fabrication of multifunctional functional structures [Citation1] using a unified, tool-free and multiprocess printing environment to provide or improve the spatial control of materials, geometry, and function [Citation1]. It is even possible to achieve gradient printing [Citation64], that is, the ability to create a continuous gradient of material properties in the printed material, such as printing seismic dampers directly into building structures [Citation1].
4.1.4. Large-scale 4D printing
On the basis of multiscale, multimaterial and multiprocess 3D printing, the next generation LS3DP process will be further expanded toward more advanced large-scale 4D printing (LS4DP) to further realise the multifunctionality of printed structures. LS4DP is the process by which LS3DP structures using responsive material [Citation190] are dynamically changed [Citation191] in an expected way [Citation192] by external stimuli [Citation193] (or programmed process control [Citation194]).
First, LS4DP requires controllable and programmable responsive materials (or smart materials [Citation194]), including thermally responsive materials, mechanically responsive materials, magnetically responsive materials, light responsive materials, electrically responsive materials, chemically responsive materials, etc. [Citation190]. The representative materials of LS4DP are shape memory polymers, shape memory alloys, shape memory hydrogels, shape memory composites, shape memory ceramics, magnetostrictive materials, light-driven polymers, electroactive polymers, and piezoelectric materials [Citation195]. Second, LS4DP requires external stimuli, including heat, light, electricity, force, water, sound, magnetic fields, solvents, biological stimuli (e.g. pH, temperature, and biomolecular signalling [Citation148]) [Citation193,Citation196], or a combination of these stimuli [Citation190]. Moreover, LS4DP requires theoretical models and design methods to accurately predict and control the expected dynamic change [Citation190,Citation197]. For LS4DP there is also a need to overcome new challenges of size, such as the degradation problem of self-recovery of the original state of the structure after multiple cyclic changes [Citation198]. Dynamic changes here include changes in shape, properties (physical or chemical), and function [Citation190,Citation198,Citation199]. Typical shape changes are self-bending, self-folding, self-twisting, and self-expansion or self-shrinkage [Citation190]. LS4DP creates the conditions for more advanced and controllable [Citation199] dynamic intelligent multifunctional structures [Citation148], which enable complex 3D structures [Citation198] that are self-evolving [Citation200], adaptive, self-assembling, memorable, multifunctional and self-recovering [Citation2]. 4D printing can be used to design and fabricate deformable lattice structure materials [Citation201], adaptive metamaterials [Citation202] and fibre-reinforced shape memory composites [Citation203], create high-resolution complex 3D reprogrammable structures [Citation194], custom shape-changing autonomous robots [Citation204], closed-loop soft robots [Citation205] and multifunctional translational robots (crawling, rolling, jumping, capturing) [Citation206], and develop flexible wings for new unmanned aerial vehicles [Citation207]. LS4DP opens up new ways to create shape self-changing 3D structures for high performance engineering [Citation208], with potential applications in aerospace and intelligent architecture. For example, self-unfolding structures for the International Space Station, solar panels for space vehicles [Citation196], self-sustaining artificial ecosystems in space, foldable and unfoldable antennas for space probes, and self-maintaining satellites [Citation209] have great potential to be manufactured by LS4DP. By LS4DP design and construction of self-assembling building components embedded with smart elements [Citation198], climate-adaptive intelligent wall structures [Citation210], parametric thermally responsive self-shaping building facade skins, and climate-adaptive dynamic buildings [Citation211], the shape of the building has a high potential to change adaptively in response to changes in external humidity [Citation210], temperature [Citation212] and other changes, thereby improving the comfort of building occupants and reducing energy consumption [Citation210] and carbon emissions.
4.2. Diverse printable materials and sustainable structures
Although research on LS3DP materials has given us enough confidence, due to the scale effect, the requirements for materials are more stringent than those for traditional scale 3D printing. To achieve multifunctionality and application for LS3DP, these material issues need to be addressed, including enhancing the performance of printable materials, expanding the range of printable materials and breaking through the differences in material and structure.
4.2.1. Material and structure enhancements
The functional requirements of 3D printed products mainly depend on the properties of the hardened printing-material and the effective mechanical properties of the structural geometry [Citation3]. Since the principle of the 3D printing process is a layer-by-layer stacking process without formwork and vibration, the spatial layout and morphology of the interfaces between the combined layers have an impact on the quality, early and long-term performance, and overall properties of the printed structure [Citation64]. For LS3DP, this impact can no longer be overlooked. Additionally, there are differences in the performance of structures obtained by 3D printing and conventional manufacturing methods in the case of using the same material. Moreover, the strength of 3D printed single materials is often not guaranteed, and taking 3D printed concrete structures as an example, because the tensile strength of the structure without steel reinforcement is not sufficient, several printable materials and structural enhancement techniques ((A)) that need to be researched are as follows.
Figure 7. Multiscale multifunctional ink and sustainable materials for LS3DP. (A) Directions for material and structure enhancements. (B) Routes to expanding the printable materials space. (C) Methods for integrated design and printing of materials and structures. (D) Pathways for the development of sustainable materials and structures.
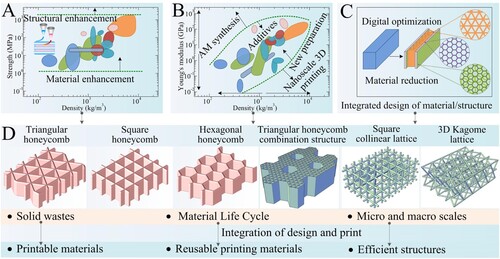
(i) For the microstructure of printable materials, it is necessary to further study the differences in the structures obtained by 3D printing and traditional manufacturing methods to achieve quantifiable differences. It is necessary to optimise the particle size, shape, and structure of raw materials, and precisely control the selective deposition or phase change in materials, which enables the quantification of instantaneous and long-term strength of materials [Citation121]. (ii) In order to reduce the influence of layer-by-layer texture on the surface of the printed structure, it is necessary to study the modification of printable materials. For example, physical polishing, 3D chemical treatment, polishing and painting treatment [Citation86,Citation90], dry powder treatment [Citation213], subtractive manufacturing [Citation4,Citation99] and texture-compatible path planning can be used to improve the surface flatness of the printed structure. Through heat treatment [Citation76,Citation87,Citation108] and ultrasonic strengthening [Citation214] of 3D printed metal structures, fibre-reinforced, self-compacting (self-healing) 3D printing cement-based materials can be developed, where various anomalies of 3D printed structures [Citation148] are expected to improve. By ultraviolet irradiation of 3D printed ceramic structures [Citation108] and adding additive inoculants [Citation215] to 3D printed alloy materials, problems such as cracks in printed structures are expected to be solved. According to the size, shape, distribution, location and formation mechanism of various printing defects, the corresponding defect control methods need to be studied and adopted [Citation216]. (iii) For 3D printing interlayer interfaces [Citation77] of new and old printing materials as well as different materials, it is necessary to carry out research on interlayer bonding and structural enhancement. For example, with the injection of reinforcing materials [Citation217] into 3D printed metallic materials, various material anomalies are reduced. Multimaterial printing is recommended, including simultaneous printing of compressive and tensile materials, printing of materials with different strengths, and synchronous printing of primary materials and bonding layers. Taking cement-based, granular, wood, and polymer materials as examples, printing ceramic materials at the location of compressive members to increase compressive properties, and printing metal materials at the location of tensile members to increase tensile strength, material interface properties are improved, and mechanical properties of the structure [Citation1,Citation148] are enhanced. When multiprocess printing is adopted, including 3D printing synchronised with automatic compaction [Citation183], external printing of formwork and internal pouring of concrete [Citation176], external vibration while printing [Citation76], printing concrete while weaving metal wire [Citation7,Citation122,Citation218] or carbon fibre wire [Citation188], and printing and then inserting or laying reinforcing structures [Citation183], the enhancement of the 3D printed structure is achieved. Printed structure enhancement can also be achieved by path planning [Citation219]. (iv) It is necessary to further conduct research on materials theory, and on the performance of 3D printing structures, related to durability, corrosion resistance, chemical properties [Citation68,Citation73], fatigue resistance [Citation215] and their monitoring [Citation68,Citation73], to support the design, automated preparation and optimisation of a variety of different materials.
4.2.2. Expanding the printable material space
To realise the different scales and functionalities of the LS3DP, it was necessary to investigate expanding the range of materials suitable for automatic printing. The main technical routes ((B)) include: (i) research on new printable materials [Citation64] and the automated preparation and delivery technologies that meet the requirements of 3D printing work and structural properties, which helps to realise the diversity of available printing materials; (ii) research on new additives [Citation118] or preparation processes [Citation220] to meet printability criteria (the rheology, the wetting behaviour, etc.), which promote the transformation of nonprintable materials to printable materials; (iii) research and design of flexible, thermally conductive and electrically conductive 3D printing functional materials [Citation1], which promote the production of multifunctional materials; (iv) research on material preparation techniques suitable for in-situ 3D printing, which realise the utilisation of in-situ materials, e.g. clay [Citation221] and slurries [Citation222]; v) research on technologies for the preparation of renewable and recyclable 3D printing materials [Citation223], which achieves sustainable use of materials; research on innovative 3D printing materials that exhibit good combinations of properties of existing basic materials, e.g. metamaterials [Citation15,Citation224] and smart materials [Citation194,Citation225]; and (vi) research on 3D printing materials and technologies based on the AM synthesis, e.g. creating macro–micro model-driven material design methods and AM processing to produce materials with properties that cannot be achieved with conventional material preparation [Citation226], synthesising established performance printable materials by nanoscale 3D printing [Citation227], preparing functional heterogeneous materials with exquisite microstructural characteristics by multimaterial magnetic-assisted 3D printing [Citation228], and creating functional gradient materials and even materials that cannot be achieved in nature through 3D printing [Citation229]. This opens up new paths for the preparation of new 3D printing materials.
4.2.3. Breaking the boundaries between materials and structures
3D printing will gradually enable the manufacturing of multiscale complex materials [Citation230] and structures, and the essential distinction between materials and structures, design and construction will eventually disappear [Citation64]. This provides a whole new way of thinking for engineering design and optimisation.
It is necessary to study the integrated design technology of 3D printing materials and structures ((C)), change the traditional design concept, and carry out the design of material structures at multiple scales based on the free design of material microstructure ((D)) by making full use of them. Thus, this provides structural effects at the material level. The macrostructure [Citation78] is improved [Citation13]. The weight reduction of the structure and the maximisation of the utilisation of material resources are realised. This provides a new way to highly optimise the composition, strength, stiffness and toughness of LS3DP structures. Some representative microstructures include honeycomb [Citation108,Citation231], triangular honeycomb [Citation6], square honeycomb [Citation6,Citation232], hexagonal honeycomb [Citation6,Citation232] and triangular honeycomb combination structures (also named hierarchical honeycomb) [Citation233]; cellular structures with variable stiffness [Citation234], topology cellular structures [Citation31,Citation235], and multimaterial 3D periodic cellular structures [Citation236]; tetrahedral structures [Citation11], sandwich structures [Citation13], microlattices [Citation108,Citation237], microtrusses [Citation103], lattice structures [Citation13], lattice truss core structures [Citation238], square collinear lattices [Citation11], 3D Kagome lattices [Citation13] and graded lattices [Citation239]; porous structures [Citation240], porous carbon structures [Citation241], and 3D graphene structures [Citation242]; and biomimetic structures [Citation243], spider web structures [Citation244], and reproduction structures inspired by natural materials [Citation227]. Some of the representative macrostructures are the Voronoi structure for the lunar habitat [Citation245], the closed foam topology structures of building components for the lunar outpost [Citation65], and the mesopore structure of artificial photosynthesis for CO2 photoreduction [Citation246].
It is necessary to study material-structure-performance integrated 3D printing technology [Citation247], which creates conditions for the fabrication of high-performance and multifunctional structures in extremely harsh service environments. Furthermore, it is important to study digital design methods and computational optimisation tools (e.g. topology optimisation) suitable for multiscale 3D printing materials and structures, and study the equipment and technologies that integrate the design and construction of 3D printing structures, so that the structuring of matter can be realised from the microstructural scale to the structural element scale [Citation64]. In addition, it is necessary to investigate the standard system for the integration of 3D printing materials, structural design and construction. Taking C3DP as an example, it is essential to study the printing materials and structural design concepts and methods that break the traditional steel plus concrete and steel structures [Citation59], and carry out research on new building structures and standard systems suitable for 3D printing of low-rise, multistory, high-rise and super high-rise buildings.
4.2.4. Sustainable materials and structures
Large structures consume huge amounts of materials and resources due to their size, which is much higher than traditional scale structures. Moreover, these large structures consume large amounts of energy in their use. Therefore, we must consider the sustainability of materials and structures for LS3DP. This requires a shift in the traditional concept of material design and preparation, with the main line of development being the integrated design and printing of materials and structures based on multiscale 3D printing. The specific pathways ((D)) are [Citation2]: (i) research on material preparation technologies for transforming various types of solid wastes into printable materials; (ii) research on reusable 3D printing materials and automated preparation technologies from the perspective of the entire life cycle of materials; and (iii) research and development of design and printing technologies for optimised and efficient structures on both micro- and macro-scales. The development of these technologies could reduce the use of materials for large structures and lower carbon emissions.
4.3. Printing equipment for breaking size constraints
The development of LS3DP equipment () first needs to meet the basic conditions of matching 3D printing processes (multiscale, multimaterial, multiprocess) and compatibility with 3D printing materials, thus enabling multifunctional printing. Second, unlike small-scale 3D printing, one of the greatest challenges of LS3DP is that the equipment requires greater flexibility and scalability while still meeting the safety, stiffness, and stability requirements. Finally, in complete contrast to small-scale printing, the equipment needs to be adapted to the scale and shape of the large-scale structure to be printed to break through the limitations of the printing size.
Figure 8. LS3DP equipment for breaking size constraints. (A, B, C and I) Flexible and scalable 3D printing equipment (gantry equipped with robotic arm 3D printing equipment, modular 3-axis adaptive scalable mobile 3D printing equipment [Citation59], mobile swarm [Citation248] collaborative 3D printing robot, and containerised on-site 3D printing mobile factory [Citation59]). (D and E) Horizontal structure 3D printing equipment (horizontal structure multimaterial 3D printing equipment and horizontal structure 3D printing equipment based on printing with follower support via collaborative formwork). (F, G and H) High-rise structure 3D printing equipment (high-rise structure 3D printing equipment with alternate climbing attached to printed structures [Citation59], self-climbing high-rise structure 3D printing equipment [Citation59] and multiple unmanned aerial vehicles carrying cable drive aerial 3D printing robots). (J, K and L) Flexible and multifunctional printing head (the printing head for printing and simultaneous laying of steel reinforcement, the printing head for printing and simultaneous vibrations, and the printing head for printing and external simultaneous compaction).
![Figure 8. LS3DP equipment for breaking size constraints. (A, B, C and I) Flexible and scalable 3D printing equipment (gantry equipped with robotic arm 3D printing equipment, modular 3-axis adaptive scalable mobile 3D printing equipment [Citation59], mobile swarm [Citation248] collaborative 3D printing robot, and containerised on-site 3D printing mobile factory [Citation59]). (D and E) Horizontal structure 3D printing equipment (horizontal structure multimaterial 3D printing equipment and horizontal structure 3D printing equipment based on printing with follower support via collaborative formwork). (F, G and H) High-rise structure 3D printing equipment (high-rise structure 3D printing equipment with alternate climbing attached to printed structures [Citation59], self-climbing high-rise structure 3D printing equipment [Citation59] and multiple unmanned aerial vehicles carrying cable drive aerial 3D printing robots). (J, K and L) Flexible and multifunctional printing head (the printing head for printing and simultaneous laying of steel reinforcement, the printing head for printing and simultaneous vibrations, and the printing head for printing and external simultaneous compaction).](/cms/asset/2f746efb-2c34-406d-8110-28481d96525b/nvpp_a_2346821_f0008_oc.jpg)
4.3.1. Flexible and scalable 3D printing
The limited size of existing LS3DP equipment dictates that the structure to be printed cannot exceed its operating range, which makes it difficult to completely break the size constraints of LS3DP. This requires the next generation of LS3DP equipment to be more flexible and scalable in the print range. (i) Development of more flexible mounting systems and printing heads. For example, through the combination of several existing pieces of equipment, a gantry-mounted robotic arm 3D printing robot equipment ((A)) is developed, and a 6-axis robotic arm support system [Citation142] is fabricated. The mounting systems are equipped with curved rotatable printing heads, and the printing heads are even equipped with printing and synchronous vibration devices ((K)) and printing and synchronous compaction devices ((L)), which achieve more flexible printing. (ii) Development of modular 3-axis adaptive scalable mobile 3D printing equipment ((B)) [Citation59] or rail plus lift structure plus robotic arm 3D printing equipment [Citation249], which enables extended printing in horizontal and vertical directions. (iii) Development of foldable self-assembling 3D printing equipment [Citation250], modular self-replicating hybrid 3D printing equipment [Citation177,Citation251], and programmable intelligent 3D printing equipment [Citation193], which realises a high adaptation of equipment to environmental printing. (iv) Development of mobile 3D printing equipment. For example, vehicle-mounted 3D printing equipment [Citation118] and mobile robot 3D printing equipment [Citation252] were developed to solve the limitation of the printing size being larger than the equipment [Citation142]. (v) Development of a containerised on-site 3D printing mobile factory ((I)) [Citation58] carrying a printing and layout steel bar integrated system ((J)), which is suitable for printing in complex and difficult working field environments. (vi) Development of 3D printing equipment for multirobot collaborative operation ((C)). The larger the equipment is, the lower the printing accuracy [Citation253], which determines that the equipment can not be infinitely large. To solve this problem, swarms of 3D printing mobile robots [Citation247] (similar to termite or bee colonies performing tasks [Citation254]) for large complex structures are proposed to enable the printing of objects larger than the equipment itself [Citation1]. For example, a team of mobile robots [Citation34] was developed to print large-scale concrete structures, and LS3DP equipment called BAAM [Citation247] was proposed to manufacture aerospace components with a 30 m length. However, the future development of such equipment needs to address core technology issues such as environmental sensing and positioning, collaborative operation and material delivery.
4.3.2. 3D printing of horizontal structures
In the absence of a support skeleton or formwork at the bottom, it is not easy for LS3DP to complete the printing of horizontal structures (In fact, is relatively easy to fabricate horizontal structures in small-scale 3D printing applications). In particular, it is difficult for C3DP using concrete material to break through the limits of their own gravity in suspended or cantilevered horizontal structures, so it is impractical to achieve the overall 3D printing of horizontal structures. To solve this problem, possible development routes for the next generation of 3D printing equipment include the following: (i) Development of construction equipment for 3D printing components plus assembly. At present, the most widely used horizontal structure for C3DP is the process of 3D printing components plus manual assembly [Citation52]. For example, through the process of topology design, 3D printing components, nonautomated assembly and prestressed tensioning, several large horizontal bridges [Citation139,Citation255,Citation256] were printed and built. However, this late manual assembly mode has a low degree of automation and poor customisability. Therefore, future equipment will be developed toward 3D printing modular components [Citation257], robotic automated assembly [Citation186], and automated tensioning. (ii) Research and design of self-supporting horizontal structures matched with 3D printing equipment. For instance, inspired by the AM of masonry, horizontal structures with self-supporting capabilities and their printing paths were designed to enable the printing of horizontal structures [Citation258]. (iii) Development of multimaterial horizontal structure 3D printing equipment ((D)). For example, easily removable supports are printed with one printing head, and horizontal structures are printed on top of the support by another printing head [Citation259]. Alternatively, horizontal support rails can be printed via a printing head. The equipment traverses the printed support rails, and the horizontal structures are printed with another printing head. (iv) Development of horizontal structure 3D printing equipment based on printing via collaborative formwork ((E)). That is, the support rails are printed by the support 3D printing system, the printing equipment traverses the printed support rails, the horizontal main structure is printed by using the horizontal structure 3D printing system, and the collaborative formwork that follows along with the printing provides support for printing the horizontal structure [Citation2].
4.3.3 3D printing of high-rise structures
The existing LS3DP equipment is hardly applicable to the construction of high-rise structures such as skyscrapers, bridge towers and rockets, so it is necessary to carry out research on 3D printing equipment for high-rise structures. Taking 3D printing equipment for high-rise and super high-rise buildings as an example, possible technical routes include: (i) integration of a 3D printer with existing building construction equipment [Citation59], such as integration of a 3D printing head with a concrete pump truck extension boom [Citation260], integration of a 3D printing head with a self-climbing tower crane boom, and integration of existing 3D printing equipment with a climbing or floor-mounted high-rise building machine. (ii) Development of 3D printing for crawling robots [Citation2], i.e. 3D printing head crawling robots climbing and printing on printed layers [Citation251,Citation261]. (iii) Development of 3D printing equipment for high-rise structures with an alternate climbing system attached to printed structures ((F)); i.e. frame system carrying printing heads can automatically climb along the printed structure, and the climbing system is similar to that of the high-rise building machine [Citation262]. (iv) Development of self-climbing high-rise structure 3D printing equipment ((G)) [Citation59], which can climb along the vertical direction to extend printing by adding standard sections of the frame system of the printing equipment. (v) Development of aerial 3D printing equipment ((H)), by a single [Citation263], multiple [Citation264] unmanned aerial vehicle 3D printing robots, or by multiple unmanned aerial vehicles carrying cable drive aerial 3D printing robots, which overcomes printing height limitations. (vi) Development of integrated 3D printing equipment, which can achieve the integrated 3D printing construction of super high-rise structures and their underground structures [Citation265].
4.4. Co-printing and feedback control
The core task of LS3DP control () is to establish printing control equations matched with different 3D printing processes (multiscale, multimaterial, multiprocess) [Citation2], various materials and various equipment, as well as to solve the contradiction between accuracy and efficiency. On this basis, LS3DP control needs to achieve collaborative control in the whole life cycle of printing, virtual printing and accurate simulation prediction before printing, as well as monitoring, detection and dynamic adjustment control of the whole printing process.
Figure 9. Co-printing and feedback control for LS3DP. The core task of LS3DP control is to break through the challenges faced by conventional scale 3D printing and solve the size effect limitations that come with large scale printing. Specifically, it includes the establishment of printing control equations matched with different 3D printing processes, various materials and various equipment, solving the contradiction between accuracy and efficiency, the study of remote collaborative control technology in the whole life cycle of printing, the study of virtual printing and accurate simulation prediction before printing, and the study of monitoring, detection and intelligent control of the whole printing process. With the resolution of these technologies, LS3DP's business model is expected to transform into a global digital cloud 3D printing model, achieving high-precision, high-quality, safe, remote, and fully automated printing.
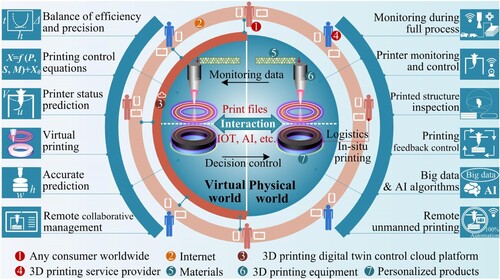
4.4.1. 3D printing remote collaboration control
The next generation of LS3DP control requires remote collaborative management and control of the whole life cycle of printing. The key to development of the control is to develop a reliable and fault-tolerant [Citation266] 3D printing digital twin control cloud platform around the concept of internet-based design and IoT-based printing construction. 3D printing service providers have service capabilities such as cloud manufacturing services, cloud computing services, equipment services, internet services and logistics services [Citation267]. The business model through this platform is as follows:
(i) Consumers communicate with 3D printing service providers through an online internet cloud platform to design and build a digital twin model of the customised product.
(ii) 3D printing service providers remotely process and control (process 3D printing models, transfer processed files to cloud terminals, set parameters and control printing remotely) flexible intelligent equipment or factories at the consumer's location to the product through the online Internet platform [Citation2].
(iii) Consumers receive on-demand customised complex functional products at a relatively low cost.
The novel cloud 3D printing service business model [Citation268] enables mass customisation, design [Citation269], remote printing, and multitask management [Citation270]. With the development of next-generation artificial intelligence (AI) technologies [Citation271], this business model is expected to transform and develop into a global digital cloud [Citation272] 3D printing business model.
4.4.2. Virtual printing and accurate simulation forecasting
The next generation of LS3DP control needs to realise virtual printing before actual printing and accurate simulation predictions of the whole printing process, the core of which is to study the basic theory of LS3DP control, establish the digital twin model of LS3DP [Citation273] and the intelligent algorithm of path optimisation, as well as break through the corresponding printing control equations and motion and printing control algorithms. Through generative AI design and parametric modelling, pre-printing and multiscale [Citation64], multimaterial [374] and multiprocess virtual printing, changes in large-scale printing structures and equipment are adapted, which achieves the optimisation of printing parameters and paths [Citation119].
For accurate simulation prediction, LS3DP control requires the following studies: establish an LS3DP full process [Citation275] dynamic action control model and mechanical behaviour [Citation274] quantitative prediction method [Citation276] considering the influences of the external environment, multiphysics, size effect, printing parameters (time interval, etc.); study the numerical simulation method of the LS3DP structure based on inversion analysis; study the multiscale printing structure simulation prediction method based on microscopic test results [Citation38]; and study the simulation and prediction method of the printing equipment operation state based on machine learning [Citation276] and intelligent algorithms [Citation277]. Another reason to conduct these studies is to optimise the printing structure design [Citation276], pre-evaluate the printing equipment status [Citation278], and accurately predict and control the printing process [Citation277] deviations and printing forming structure [Citation279] deviations. This lays the theoretical foundation for the design, construction and engineering applications of LS3DP intelligent construction. The deviations include dimensional deviations, performance deviations [Citation64] and state deviations [Citation280] of materials and structures.
4.4.3. 3D printing monitoring inspection and intelligent control
The long-term process of the LS3DP must be reliable, stable and repeatable, otherwise failures and quality problems may occur. Therefore, the next generation of LS3DP control also needs to realise the monitoring, detection and intelligent control of the whole printing process. The basis for the development of LS3DP control is the research and development of IoT monitoring hardware and feedback control platform systems suitable for LS3DP state sensing and quality detection, and a breakthrough in deviation quantitative identification and precise control technology. Real-time monitoring of the operation status and printing path of 3D printing equipment [Citation136] needs to be conducted through sensors [Citation281] and visual recording devices installed in the body of the equipment. Real-time monitoring of printing extrusion and dynamic forming processes must be conducted by optical and thermal imaging [Citation4], high-speed cameras [Citation282], and deep learning image recognition [Citation283]. Anomalies in the printing process also need to be detected [Citation284] or monitored using machine learning [Citation285] and deep neural networks [Citation286]. To introduce nondestructive ultrasonic methods [Citation287], wireless monitoring and sensing [Citation261] and other technologies, real-time monitoring devices and systems for early maintenance [Citation288] and long-term hardening [Citation289] processes of printed forming structures need to be developed. The surface quality of printed structures should be inspected and evaluated by 3D imaging, optical/laser imaging, laser Doppler velocimetry (LDV) and particle image velocimetry (PIV) [Citation290], computer vision [Citation291] and other technologies. Contact measurement, 3D laser scanning [Citation52], a mass measurement programme [Citation292] and 3D CT [Citation293] can be used to detect the geometric deviation of the printed structure. Based on these detection data, methods such as machine learning can be introduced to analyze and predict the quality of printed structures [Citation294]. The LS3DP process feedback control [Citation1,Citation281] system and big data management and control cloud platform need to be developed based on IOT real-time online monitoring [Citation295], self-diagnosis, self-detection and deviation analysis [Citation186]. By conducting these studies, it is hoped that high-precision, high-quality [Citation13], safe, and remotely unmanned 3D printing can be achieved. With the application of a large number of printing projects and the accumulation of big data, 3D printing control is expected to achieve the development of self-learning, self-adaptive, self-processing, self-organising, self-coordinating, and intelligent control [Citation296].
4.5. LS3DP for specific conditions or extreme environments
LS3DP has more urgent application needs and better application prospects under specific conditions or extreme environments because of its high degree of automation and can be combined with AI [Citation297] and robotics. Specific conditions or extreme environments mean very challenging, dangerous [Citation263] or very difficult work locations, requiring few or no people. For example, those working on construction sites face high temperatures, rainfall and other weather conditions. In the future, the construction site may not require high-intensity workers, so the use of in-situ monolithic 3D printing can free the high-intensity workers from working in extreme environments and can reduce the cost of prefabricated construction and transportation [Citation248] while saving human resources for on-site assembly. Furthermore, on-site 3D printing equipment should be further investigated to ensure that it is unaffected by weather conditions. On the other hand, since underground engineering construction faces high risks, it is necessary to develop multiprocess 3D printing equipment and technology for exploration, excavation and printing suitable for foundation pit construction [Citation264]. In addition, 3D printing equipment and technology for tunnel construction that combines additive and subtractive manufacturing [Citation298] should be established. The demolition and renovation construction of super high-rise structures faces high risk, so it is necessary to develop equipment and technology suitable for super high-rise demolition and 3D printing construction. Marine, near-coast and other underwater engineering construction face high risks and challenges, so it is critical to develop 3D printing equipment and technology suitable for underwater construction [Citation299] and materials to meet underwater construction requirements. Also, post-disaster conditions face great uncertainty and danger [Citation300]; thus, the development of 3D printing equipment and technology for rapid reconstruction after disasters [Citation262,Citation268] is crucial. Nuclear power plants and other nuclear engineering construction, especially repair, face high risk, so it is necessary to develop the corresponding construction and repair 3D printing equipment and technology. Finally, regarding the construction of space bases on the Moon and Mars, this objective is difficult for humans to attain. But also the construction materials are difficult to obtain [Citation301] and the environment is very extreme (extreme weather temperature and humidity, microgravity, high radiation), so remote, unmanned, in situ construction is required. Therefore, it is necessary to develop LS3DP technology suitable for this extreme environment, including building structures suitable for living in extreme environments [Citation302], in situ material extraction [Citation303] and material preparation technologies [Citation301], lightweight in-situ construction equipment [Citation303], and remote construction processes [Citation304]. Furthermore, it needs to be compatible with the energy and power required for the continuous operation of each piece of construction equipment. For example, the energy required to implement printing for the robots can choose microwave, laser or concentrated sunlight, and the energy needs for other equipment are met by solar arrays or photovoltaic power systems.
In summary, there are three key requirements for adapting the LS3DP to extreme environments. The first is to enable remote or autonomous unmanned control of the entire process of the 3D printer. This requires remote or unmanned operation for ‘transferring processed files to printer terminals’, ‘setting parameters and controlling printing’ and ‘monitoring and controlling the printing process’. The second is develop 3D printers that are adapted to the field environment. The third is the development of materials and structures adapted to the extreme environment. The development of these 3D printing technologies can help humans explore other planets in the future.
4.6. The future of LS3DP and implications for industries
The digital control concept of LS3DP is fundamentally different from traditional production methods. Materials, processes and equipment are closely linked in the form of digital flow through the control or programming, and the 3D digital model is automatically transformed into a physical object through a printer. This control mode of LS3DP determines that we can no longer separate material, process, equipment and structural performance. The manufacturing mode of LS3DP will move toward the integration of material and structure, design and construction, and software and hardware. On the basis of the digital optimisation design of material-structure-equipment-process-performance integration from microscopic to macroscopic, on-demand printing [Citation2] (according to different locations, independently selecting appropriate processes, scales and materials for printing) is realised through the integrated hardware and software equipment (equipment that carries the material, and printing according to a certain process through the control software). We believe that for a long time to come, many industries will develop this digital and intelligent manufacturing mode similar to LS3DP () from digital models (input) to integrated hardware and software equipment and then to physical objects (output), and realise the transformation and upgrading of industries.
Figure 10. Overall direction of LS3DP. LS3DP can no longer separate material, process, equipment and structural performance, and will develop toward the integration of material and structure, design and construction, and software and hardware.
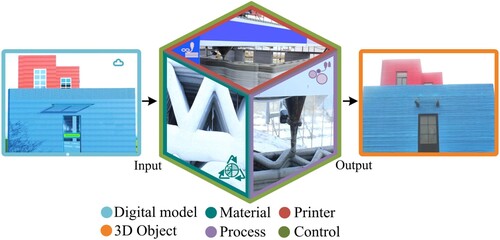
LS3DP is a highly interdisciplinary [Citation64] and multiresearch field integrated [Citation305] technology that will undoubtedly become a link between various disciplines. It includes common core technologies involving disciplines such as materials science [Citation306], mechanical engineering, computer science and electrical engineering, and electronic communication engineering [Citation54] as well as special supplementary disciplines of the printing process. These complementary disciplines may include civil engineering, traffic transportation engineering, ocean engineering (or marine engineering), nuclear engineering, aerospace engineering, etc. LS3DP is expected to break the boundaries of disciplines and industries, and it is not difficult to imagine that in the future, the technology presented in this paper can be used to produce not only buildings (or structures), but also customised cars, aircraft, rockets, high-speed trains, ships and marine equipment, submarine tunnels, nuclear industry equipment, space bases, etc., with the help of 3D printing robots.
5. Conclusions
With the continuous development and enhancement of 3D printing, it is expected to revolutionise the production model of traditional industries, which can completely liberate people from labour-intensive, dangerous and difficult jobs, and hazardous environments, with unlimited possibilities. However, LS3DP must not only overcome the challenges faced by conventional scale 3D printing, which usually cannot achieve multifunctional structure printing and other problems, but also address the limitations of size effects that come with large-scale printing. We systematically reviewed the current state of the LS3DP and applications in terms of printing processes, materials, equipment, and controls. We also illustrated a number of disruptive cases and quantitative indicators of LS3DP in the construction field. Finally, we discussed the challenges and strategies for overcoming size limitations to achieve full-scale printing of large-scale functional structures, mainly as follows:
LS3DP is a technology for the automated AM of huge structures (typically larger than 1 m in scale) such as buildings, aircraft and rockets, where it is necessary to print not only the body of the giant structure, but also the internal functional components. Therefore, the process requires the development of multifunctional 3D printing processes (multi-process, multi-scale, multi-material 3D printing processes) from nano to large scales.
To achieve multifunctionality and application for LS3DP, these material issues need to be addressed, including enhancing the performance of printable materials, expanding the range of printable materials and breaking the boundaries between materials and structures. Moreover, large-scale 3D printed structures consume a lot of materials and resources due to their large size, which requires sustainable materials and structures, with the development of integrated design and printing of materials and structures based on multi-scale 3D printing.
To break through the limitations of the printing size, LS3DP equipment needs to fulfil the basic conditions of matching printing processes (multiscale, multimaterial, multiprocess) and compatibility with materials. It also needs to be more flexibility and scalability while meeting the safety, stiffness and stability requirements. More importantly, there is a need to develop 3D printers for horizontal and high-rise structures.
The control mode of LS3DP determines that we can no longer separate material, process, equipment and structural performance. The core task of LS3DP control is to establish printing control equations matched with different 3D printing processes, various materials and various equipment, as well as to solve the contradiction between accuracy and efficiency. On this basis, LS3DP control needs to achieve collaborative control in the whole life cycle of printing, virtual printing and accurate simulation prediction before printing, as well as monitoring, detection and dynamic adjustment control of the whole printing process.
By reinventing the new design and construction mode of ‘digital twin model - smart equipment – multifunctional products’, the next generation of LS3DP is expected to overcome the challenges faced by conventional scale 3D printing and break through size limitations. Our proposed strategies can provide tremendous opportunities for the automated, intelligent, and unmanned production of different material megastructures and internal multiscale multifunctional components. Specifically, it will be able not only realize the fully automated construction of the arbitrarily shaped giant structure body, but also achieve the full-scale automatic printing of its internal functional components and electrical circuits with the help of 3D printing robots on the same equipment and provide previously impossible functions and performance, which are smarter, greener and more sustainable.
The research insights presented in this paper can be used as a reference for automated, intelligent, and unmanned 3D printing construction of complex, personalised, green, and large-scale buildings (or structures), vehicles, aerospace vehicles, ships and marine equipment, nuclear industry equipment, and space bases.
Acknowledgements
This work is supported by the National Key R&D Program of China (No. 2018YFC0705800), National Natural Science Foundation of China (52025094) and the Science and Technology Commission of Shanghai Municipality (No. 19QB1403300). The authors acknowledge Y. Ma of Winsun, Y. Zhang of SCR, J. Wu of BHLT, S. Du of LAG, E. Dini of MU, and G. van der Velden of MX3D for their help during the survey research and statistical analysis phase. The authors thank M. Gong and C. Lu of SCG, and H. Wang and C. Gao of NJK for their help in preparing the figures.
Data availability statement
Data available on request from the authors.
Disclosure statement
No potential conflict of interest was reported by the author(s).
Additional information
Funding
References
- MacDonald E, Wicker R. Multiprocess 3D printing for increasing component functionality. Science. 2016;353(6307). doi:10.1126/science.aaf2093
- Zuo Z, De Corte W, Huang Y, et al. Propelling the widespread adoption of large-scale 3D printing. Nat Rev Mater. 2023. doi:10.1038/s41578-023-00626-1
- Lim S, Buswell RA, Le TT, et al. Developments in construction-scale additive manufacturing processes. Autom Constr. 2012;21:262–268. doi:10.1016/j.autcon.2011.06.010
- Das S, Bourell DL, Babu SS. Metallic materials for 3D printing. MRS Bull. 2016;41(10):729–741. doi:10.1557/mrs.2016.217
- Buswell RA, Thorpe A, Soar RC, et al. Design,: data and process issues for mega-scale rapid manufacturing machines used for construction. Autom Constr. 2008;17(8):923–929. doi:10.1016/j.autcon.2008.03.001
- Compton BG, Lewis JA. 3D-printing of lightweight cellular composites. Adv Mater. 2014;26(34):5930–5935. doi:10.1002/adma.201401804
- Tay YW, Panda B, Paul SC, et al. 3D printing trends in building and construction industry: a review. Virtual Phys Prototyp. 2017;12(3):261–276. doi:10.1080/17452759.2017.1326724
- Pegna J. Exploratory investigation of solid freeform construction. Autom Constr. 1997;5(5):427–437. doi:10.1016/S0926-5805(96)00166-5
- Buswell RA, Soar RC, Gibb AGF, et al. Freeform construction: mega-scale rapid manufacturing for construction. Autom Constr. 2007;16(2):224–231. doi:10.1016/j.autcon.2006.05.002
- Lu B, Li D, Tian X. Development trends in additive manufacturing and 3D printing. Engineering. 2015;1(1):085–089. doi:10.15302/J-ENG-2015012
- Schaedler TA, Carter WB. Architected cellular materials. Annu Rev Mater Res. 2016;46(1):187–210. doi:10.1146/annurev-matsci-070115-031624
- Kumar S, Wardle BL, Arif MF. Strength and performance enhancement of bonded joints by spatial tailoring of adhesive compliance via 3D printing. ACS Appl Mater Interfaces. 2017;9(1):884–891. doi:10.1021/acsami.6b13038
- Tumbleston JR, Shirvanyants D, Ermoshkin N, et al. Continuous liquid interface production of 3D objects. Science. 2015;347(6228):1349–1352. doi:10.1126/science.aaa2397
- Choong YY, Tan HW, Patel DC, et al. The global rise of 3D printing during the COVID-19 pandemic. Nat Rev Mater. 2020;5(9):637–639. doi:10.1038/s41578-020-00234-3
- Chen Y, Fu Q, Li D, et al. A smartphone colorimetric reader integrated with an ambient light sensor and a 3D printed attachment for on-site detection of Zearalenone. Anal Bioanal Chem. 2017;409(28):6567–6574. doi:10.1007/s00216-017-0605-2
- Tan HW, Choong YYC, Kuo CN, et al. 3D printed electronics: processes,: materials and future trends. Prog Mater Sci. 2022;127:100945. doi:10.1016/j.pmatsci.2022.100945
- Holland S, Foster T, MacNaughtan W, et al. Design and characterisation of food grade powders and inks for microstructure control using 3D printing. J Food Eng. 2018;220:12–19. doi:10.1016/j.jfoodeng.2017.06.008
- Tian L, Magnenat Thalmann N, Thalmann D, et al. The making of a 3D-printed,: cable-driven, single-model, lightweight humanoid robotic hand. Front Robot AI. 2017;4. doi:10.3389/frobt.2017.00065
- Wei TS, Ahn BY, Grotto J, et al. 3D printing of customized li-ion batteries with thick electrodes. Adv Mater. 2018;30(16):1703027. doi:10.1002/adma.201703027
- Li Z, Wang Z, Gan X, et al. Selective laser sintering 3D printing: a way to construct 3D electrically conductive segregated network in polymer matrix. Macromol Mater Eng. 2017;302(11):1700211. doi:10.1002/mame.201700211
- Ahn BY, Duoss EB, Motala MJ, et al. Omnidirectional printing of flexible,: stretchable, and spanning silver microelectrodes. Science. 2009;323(5921):1590–1593. doi:10.1126/science.1168375
- Ahn SH, Yoon HS, Jang KH, et al. Nanoscale 3D printing process using aerodynamically focused nanoparticle (AFN) printing,: micro-machining, and focused ion beam (FIB). CIRP Ann. 2015;64(1):523–526. doi:10.1016/j.cirp.2015.03.007
- Chen J, Leblanc V, Kang SH, et al. High definition digital fabrication of active organic devices by molecular jet printing. Adv Funct Mater. 2007;17(15):2722–2727. doi:10.1002/adfm.200601144
- Kadimisetty K, Song J, Doto AM, et al. Fully 3D printed integrated reactor array for point-of-care molecular diagnostics. Biosens Bioelectron. 2018;109:156–163. doi:10.1016/j.bios.2018.03.009
- Bose S, Vahabzadeh S, Bandyopadhyay A. Bone tissue engineering using 3D printing. Mater Today. 2013;16(12):496–504. doi:10.1016/j.mattod.2013.11.017
- Kolesky DB, Truby RL, Gladman AS, et al. 3D bioprinting of vascularized,: heterogeneous cell-laden tissue constructs. Adv Mater. 2014;26(19):3124–3130. doi:10.1002/adma.201305506
- Mironov V, Boland T, Trusk T, et al. Organ printing: computer-aided jet-based 3D tissue engineering. Trends Biotechnol. 2003;21(4):157–161. doi:10.1016/S0167-7799(03)00033-7
- Sun Y, Soh S. Printing tablets with fully customizable release profiles for personalized medicine. Adv Mater. 2015;27(47):7847–7853. doi:10.1002/adma.201504122
- Connell JL, Kim J, Shear JB, et al. Real-time monitoring of quorum sensing in 3D-printed bacterial aggregates using scanning electrochemical microscopy. Proc Natl Acad Sci USA. 2014;111(51):18255–18260. doi:10.1073/pnas.1421211111
- Díaz-Marta AS, Tubío CR, Carbajales C, et al. Three-dimensional printing in catalysis: combining 3D heterogeneous copper and palladium catalysts for multicatalytic multicomponent reactions. ACS Catal. 2018;8(1):392–404. doi:10.1021/acscatal.7b02592
- Sreedhar N, Thomas N, Al-Ketan O, et al. 3D printed feed spacers based on triply periodic minimal surfaces for flux enhancement and biofouling mitigation in RO and UF. Desalination. 2018;425:12–21. doi:10.1016/j.desal.2017.10.010
- Dinwiddie R, Love L, Rowe J. Real-time process monitoring and temperature mapping of a 3D polymer printing process. Proceedings of SPIE; 2013 May 22. doi:10.1117/12.1518454
- Almaghariz ES, Conner BP, Lenner L, et al. Quantifying the role of part design complexity in using 3D sand printing for molds and cores. Int J Metalcast. 2016;10(3):240–252. doi:10.1007/s40962-016-0027-5
- Zhang X, Li M, Lim JH, et al. Large-scale 3D printing by a team of mobile robots. Autom Constr. 2018;95:98–106. doi:10.1016/j.autcon.2018.08.004
- Rutkin A. Watch as the world’s first 3D-printed house goes up. New Sci. 2014;221(2960):24. doi:10.1016/s0262-4079(14)60529-7
- Wang H. Materials’ fundamental issues of laser additive manufacturing for high-performance large metallic components. Acta Aeronaut Astronaut Sin. 2014;35:2690–2698. doi:10.7527/S1000-6893.2014.0174
- Lin X, Huang W. Laser additive manufacturing of high-performance metal components. Sci Sin Inform. 2015;45(9):1111–1126. doi:10.1360/n112014-00245
- Talagani MR, Dormohammadi S, Dutton R, et al. Numerical simulation of big area additive manufacturing (3D printing) of a full size car. SAMPE J. 2015;51(4):27–36.
- Ruiz LE, Pinho AC, Resende DN. 3D printing as a disruptive technology for the circular economy of plastic components of end-of-life vehicles: a Systematic Review. Sustainability. 2022;14(20):13256. doi:10.3390/su142013256
- Thomas DJ. Advanced active-gas 3D printing of 436 stainless steel for future rocket engine structure manufacture. J Manuf Process. 2022;74:256–265. doi:10.1016/j.jmapro.2021.12.037
- He T, Yu S, Shi Y, et al. Forming and mechanical properties of wire arc additive manufacture for marine propeller bracket. J Manuf Process. 2020;52:96–105. doi:10.1016/j.jmapro.2020.01.053
- Queral V. Concept,: production and validation of a 3D-printed coil frame for the UST_2 modular stellarator. Fusion Eng Des. 2014;89(9-10):2145–2149. doi:10.1016/j.fusengdes.2014.04.055
- Liu Y, Chen Z, Li J, et al. 3D printing of ceramic cellular structures for potential nuclear fusion application. Addit Manuf. 2020;35:101348. doi:10.1016/j.addma.2020.101348
- Liu J, Dong S, Jin X, et al. Quality control of large-sized alloy steel parts fabricated by multi-laser selective laser melting (ML-SLM). Mater Des. 2022;223:111209. doi:10.1016/j.matdes.2022.111209
- De Schutter G, Lesage K, Mechtcherine V, et al. Vision of 3D printing with concrete — Technical, economic and environmental potentials. Cem Concr Res. 2018;112:25–36. doi:10.1016/j.cemconres.2018.06.001
- Ngo TD, Kashani A, Imbalzano G, et al. Additive manufacturing (3D printing): a review of materials,: methods, applications and challenges. Composites Part B. 2018;143:172–196. doi:10.1016/j.compositesb.2018.02.012
- Ma G, Li Z, Wang L. Printable properties of cementitious material containing copper tailings for extrusion based 3D printing. Constr Build Mater. 2018;162:613–627. doi:10.1016/j.conbuildmat.2017.12.051
- Alhumayani H, Gomaa M, Soebarto V, et al. Environmental assessment of large-scale 3D printing in construction: a comparative study between cob and concrete. J Cleaner Prod. 2020;270:122463. doi:10.1016/j.jclepro.2020.122463
- He Y, Zhang Y, Zhang C, et al. Energy-saving potential of 3D printed concrete building with integrated living wall. Energy Build. 2020;222:110110. doi:10.1016/j.enbuild.2020.110110
- Bak D. Rapid prototyping or rapid production? 3D printing processes move industry towards the latter. Assem Autom. 2003;23(4):340–345. doi:10.1108/01445150310501190
- Mami F, Revéret J-P, Fallaha S, et al. Evaluating eco-efficiency of 3D printing in the aeronautic industry. J Ind Ecol. 2017;21(S1):S37–S48. doi:10.1111/jiec.12693
- Zuo Z, Gong J, Huang Y, et al. Experimental research on transition from scale 3D printing to full-size printing in construction. Constr Build Mater. 2019;208:350–360. doi:10.1016/j.conbuildmat.2019.02.171
- Bos FP, Menna C, Pradena M, et al. The realities of additively manufactured concrete structures in practice. Cem Concr Res. 2022;156:106746. doi:10.1016/j.cemconres.2022.106746
- Wüst S, Müller R, Hofmann S. Controlled positioning of cells in biomaterials—approaches towards 3D tissue printing. J Funct Biomater. 2011;2(3):119–154. doi:10.3390/jfb2030119
- Dimitrov D, Schreve K, de Beer N. Advances in three dimensional printing – state of the art and future perspectives. Rapid Prototyp J. 2006;12(3):136–147. doi:10.1108/13552540610670717
- Stansbury JW, Idacavage MJ. 3D printing with polymers: challenges among expanding options and opportunities. Dent Mater. 2016;32(1):54–64. doi:10.1016/j.dental.2015.09.018
- ISO/TC 261, & ASTM F42. (2021). Additive manufacturing – General principles – Fundamentals and vocabulary (ISO/ASTM 52900: 2021). Available from: https://www.iso.org/obp/ui/#iso:std:iso-astm:52900:ed-2:v1:en
- Vithani K, Goyanes A, Jannin V, et al. An Overview of 3D printing technologies for soft materials and potential opportunities for lipid-based drug delivery systems. Pharm Res. 2018;36(1). doi:10.1007/s11095-018-2531-1
- Zuo Z, Huang Y, Zhang L, et al. 3D printing technology and feasibility analysis of its application in super high-rise buildings. Build Struct. 2022;52(12):95–101. doi:10.19701/j.jzjg.SHJG2109
- Khoshnevis B, Bukkapatnam S, Kwon H, et al. Experimental investigation of contour crafting using ceramics materials. Rapid Prototyp J. 2001;7(1):32–42. doi:10.1108/13552540110365144
- Khoshnevis B, Hwang D, Yao KT, et al. Mega-scale fabrication by Contour Crafting. Int J Ind Syst Eng. 2006;1(3):301. doi:10.1504/IJISE.2006.009791
- Lim S, Le T, Webster J, et al. Fabricating construction components using layer manufacturing technology. Glob Innov Constr Conf. 2009;2009(GICC’09):13–16.
- Soar R, Andreen D. The role of additive manufacturing and physiomimetic computational design for digital construction. Archit Design. 2012;82(2):126–135. doi:10.1002/ad.1389
- Gosselin C, Duballet R, Roux P, et al. Large-scale 3D printing of ultra-high performance concrete – a new processing route for architects and builders. Mater Des. 2016;100:102–109. doi:10.1016/j.matdes.2016.03.097
- Cesaretti G, Dini E, De Kestelier X, et al. Building components for an outpost on the Lunar soil by means of a novel 3D printing technology. Acta Astronaut. 2014;93:430–450. doi:10.1016/j.actaastro.2013.07.034
- Joosten SK. Printing a stainless steel bridge: an exploration of structural properties of stainless steel additive manufactures for civil engineering purposes [MA thesis]; 2015.
- Zuo Z, Gong J, Huang Y. Performance of 3D printing in construction by using computer control technology. The 7th International Conference on Computer Engineering and Networks (CENet2017). 2017;299:371–377. doi:10.22323/1.299.0048
- Farina I, Fabbrocino F, Colangelo F, et al. Surface roughness effects on the reinforcement of cement mortars through 3D printed metallic fibers. Composites Part B. 2016;99:305–311. doi:10.1016/j.compositesb.2016.05.055
- Feng P, Meng X, Chen J-F, et al. Mechanical properties of structures 3D printed with cementitious powders. Constr Build Mater. 2015;93:486–497. doi:10.1016/j.conbuildmat.2015.05.132
- Raney JR, Lewis JA. Printing mesoscale architectures. MRS Bull. 2015;40(11):943–950. doi:10.1557/mrs.2015.235
- Kuo CN, Chua CK, Peng PC, et al. Microstructure evolution and mechanical property response via 3D printing parameter development of Al–Sc alloy. Virtual Phys Prototyp. 2020;15(1):120–129. doi:10.1080/17452759.2019.1698967
- Gibbons GJ, Williams R, Purnell P, et al. 3D Printing of cement composites. Adv Appl Ceram. 2010;109(5):287–290. doi:10.1179/174367509(12472364600878
- Farina I, Fabbrocino F, Carpentieri G, et al. On the reinforcement of cement mortars through 3D printed polymeric and metallic fibers. Composites Part B. 2016;90:76–85. doi:10.1016/j.compositesb.2015.12.006
- Kazemian A, Yuan X, Cochran E, et al. Cementitious materials for construction-scale 3D printing: laboratory testing of fresh printing mixture. Constr Build Mater. 2017;145:639–647. doi:10.1016/j.conbuildmat.2017.04.015
- Panda B, Chandra Paul S, Jen Tan M. Anisotropic mechanical performance of 3D printed fiber reinforced sustainable construction material. Mater Lett. 2017;209:146–149. doi:10.1016/j.matlet.2017.07.123
- Malaeb Z, Hachem H, Tourbah A, et al. 3D concrete printing: machine and mix design. Int J Civ Eng Technol. 2015;6(6):14–22.
- Zareiyan B, Khoshnevis B. Interlayer adhesion and strength of structures in Contour Crafting - effects of aggregate size,: extrusion rate, and layer thickness. Autom Constr. 2017;81:112–121. doi:10.1016/j.autcon.2017.06.013
- Zareiyan B, Khoshnevis B. Effects of interlocking on interlayer adhesion and strength of structures in 3D printing of concrete. Autom Constr. 2017b;83:212–221. doi:10.1016/j.autcon.2017.08.019
- Le TT, Austin SA, Lim S, et al. Hardened properties of high-performance printing concrete. Cem Concr Res. 2012;42(3):558–566. doi:10.1016/j.cemconres.2011.12.003
- Xia M, Sanjayan J. Method of formulating geopolymer for 3D printing for construction applications. Mater Des. 2016;110:382–390. doi:10.1016/j.matdes.2016.07.136
- Panda B, Paul SC, Mohamed NAN, et al. Measurement of tensile bond strength of 3D printed geopolymer mortar. Measurement (Mahwah NJ). 2018;113:108–116. doi:10.1016/j.measurement.2017.08.051
- Zhong J, Zhou G-X, He P-G, et al. 3D printing strong and conductive geo-polymer nanocomposite structures modified by graphene oxide. Carbon N Y. 2017;117:421–426. doi:10.1016/j.carbon.2017.02.102
- Feng P, Meng X, Zhang H. Mechanical behavior of FRP sheets reinforced 3D elements printed with cementitious materials. Compos Struct. 2015;134:331–342. doi:10.1016/j.compstruct.2015.08.079
- Frazier WE. Metal additive manufacturing: a review. J Mater Eng Perform. 2014;23(6):1917–1928. doi:10.1007/s11665-014-0958-z
- Fraternali F, Hernández-Nava E, Goodall R, et al. On the additive manufacturing,: post-tensioning and testing of bi-material tensegrity structures. Compos Struct. 2015;131:66–71. doi:10.1016/j.compstruct.2015.04.038
- Hehr A, Dapino MJ. Interfacial shear strength estimates of NiTi–Al matrix composites fabricated via ultrasonic additive manufacturing. Composites Part B. 2015;77:199–208. doi:10.1016/j.compositesb.2015.03.005
- Buchanan C, Matilainen V-P, Salminen A, et al. Structural performance of additive manufactured metallic material and cross-sections. J Constr Steel Res. 2017;136:35–48. doi:10.1016/j.jcsr.2017.05.002
- Gutmann B, Köckinger M, Glotz G, et al. Design and 3D printing of a stainless steel reactor for continuous difluoromethylations using fluoroform. React Chem Eng. 2017;2(6):919–927. doi:10.1039/C7RE00176B
- Dai D, Gu D, Poprawe R, et al. Influence of additive multilayer feature on thermodynamics,: stress and microstructure development during laser 3D printing of aluminum-based material. Sci Bull. 2017;62(11):779–787. doi:10.1016/j.scib.2017.05.007
- Martin JH, Yahata BD, Hundley JM, et al. 3D printing of high-strength aluminium alloys. Nature. 2017;549(7672):365–369. doi:10.1038/nature23894
- Xia M, Gu D, Yu G, et al. Selective laser melting 3D printing of Ni-based superalloy: understanding thermodynamic mechanisms. Sci Bull. 2016;61(13):1013–1022. doi:10.1007/s11434-016-1098-7
- Snelling D, Li Q, Meisel N, et al. Lightweight metal cellular structures fabricated via 3D printing of sand cast molds. Adv Eng Mater. 2015;17(7):923–932. doi:10.1002/adem.201400524
- Gardan J, Nguyen DC, Roucoules L, et al. Characterization of wood filament in additive deposition to study the mechanical behavior of reconstituted wood products. J Eng Fibers Fabr. 2016;11(4):155892501601100. doi:10.1177/155892501601100408
- Henke K, Treml S. Wood based bulk material in 3D printing processes for applications in construction. Eur J Wood Wood Prod. 2012;71(1):139–141. doi:10.1007/s00107-012-0658-z
- Kariz M, Sernek M, Kuzman MK. Use of wood powder and adhesive as a mixture for 3D printing. Eur J Wood Wood Prod. 2015;74(1):123–126. doi:10.1007/s00107-015-0987-9
- Kam D, Layani M, BarkaiMinerbi S, et al. Additive manufacturing of 3D structures composed of wood materials. Adv Mater Technol. 2019;4(9):1900158. doi:10.1002/admt.201900158
- Tao Y, Wang H, Li Z, et al. Development and application of wood flour-filled polylactic acid composite filament for 3D printing. Materials (Basel). 2017;10(4):339. doi:10.3390/ma10040339
- Le Duigou A, Castro M, Bevan R, et al. 3D printing of wood fibre biocomposites: from mechanical to actuation functionality. Mater Des. 2016;96:106–114. doi:10.1016/j.matdes.2016.02.018
- Takagishi K, Umezu S. Development of the improving process for the 3D printed structure. Sci Rep. 2017;7(1). doi:10.1038/srep39852
- Ning F, Cong W, Qiu J, et al. Additive manufacturing of carbon fiber reinforced thermoplastic composites using fused deposition modeling. Composites Part B. 2015;80:369–378. doi:10.1016/j.compositesb.2015.06.013
- Dakhli Z, Lafhaj Z. Experimental and numerical prototyping of a complex cement column formwork for construction. Archit Eng Design Manage. 2016;13(2):147–165. doi:10.1080/17452007.2016.1226745
- Yang H, Lim JC, Liu Y, et al. Performance evaluation of ProJet multi-material jetting 3D printer. Virtual Phys Prototyp. 2017;12(1):95–103. doi:10.1080/17452759.2016.1242915
- Lausic A, Bird A, Steeves CA, et al. Scale-dependent failure of stereolithographic polymer microtrusses in three-point bending. J Compos Mater. 2016;50:1739–1749. doi:10.1177/0021998315596369
- Giordano RA, Wu BM, Borland SW, et al. Mechanical properties of dense polylactic acid structures fabricated by three dimensional printing. J Biomater Sci Polym Ed. 1997;8(1):63–75. doi:10.1163/156856297(00588
- Malek S, Raney JR, Lewis JA, et al. Lightweight 3D cellular composites inspired by balsa. Bioinspir Biomim. 2017;12(2):026014. doi:10.1088/1748-3190/aa6028
- Maurath J, Willenbacher N. 3D printing of open-porous cellular ceramics with high specific strength. J Eur Ceram Soc. 2017;37(15):4833–4842. doi:10.1016/j.jeurceramsoc.2017.06.001
- Hwa LC, Rajoo S, Noor AM, et al. Recent advances in 3D printing of porous ceramics: a review. Curr Opin Solid State Mater Sci. 2017;21(6):323–347. doi:10.1016/j.cossms.2017.08.002
- Eckel ZC, Zhou C, Martin JH, et al. Additive manufacturing of polymer-derived ceramics. Science. 2016;351(6268):58–62. doi:10.1126/science.aad2688
- Yin X, Travitzky N, Greil P. Three-dimensional printing of nanolaminated Ti3AlC2 toughened TiAl3-Al2O3 composites. J Am Ceram Soc. 2007;90(7):2128–2134. doi:10.1111/j.1551-2916.2007.01668.x
- Haussener S, D’Angelo C, Gianella S, et al. Cellular ceramics produced by rapid prototyping and replication. Mater Lett. 2012;80:95–98. doi:10.1016/j.matlet.2012.04.050
- Wang W, Gao X, Zhang L, et al. Large-scale material extrusion-based additive manufacturing of short carbon fibre-reinforced silicon carbide ceramic matrix composite preforms. Virtual Phys Prototyp. 2023;18(1). doi:10.1080/17452759.2023.2245801
- Wilhelm S, Curbach M. Review of possible mineral materials and production techniques for a building material on the moon. Struct Concr. 2014;15(3):419–428. doi:10.1002/suco.201300088
- Zhang J, Khoshnevis B. Optimal machine operation planning for construction by Contour Crafting. Autom Constr. 2013;29:50–67. doi:10.1016/j.autcon.2012.08.006
- Hwang D, Khoshnevis B. An innovative construction process-contour crafting (CC). Proceedings of the 22nd International Symposium on Automation and Robotics in Construction; 2005. doi:10.22260/isarc2005/0004
- Gardner L, Kyvelou P, Herbert G, et al. Testing and initial verification of the world’s first metal 3D printed bridge. J Constr Steel Res. 2020;172:106233. doi:10.1016/j.jcsr.2020.106233
- Gammon K. Why 3-D printed homes may save lives as well as the environment. NBC News. 2017 Mar 9. Available from: https://www.nbcnews.com/mach/innovation/why-3-d-printed-homes-may-save-lives-well-environment-n730606
- Huang S, Xu W, Li Y. The impacts of fabrication systems on 3D concrete printing building forms. Front Archit Res. 2022;11:653–669. doi:10.1016/j.foar.2022.03.004
- Labonnote N, Rønnquist A, Manum B, et al. Additive construction: state-of-the-art,: challenges and opportunities. Autom Constr. 2016;72:347–366. doi:10.1016/j.autcon.2016.08.026
- Barnett E, Gosselin C. Large-scale 3D printing with a cable-suspended robot. Addit Manuf. 2015;7:27–44. doi:10.1016/j.addma.2015.05.001
- Bosscher P, Williams RL, Bryson LS, et al. Cable-suspended robotic contour crafting system. Autom Constr. 2007;17(1):45–55. doi:10.1016/j.autcon.2007.02.011
- Bos F, Wolfs R, Ahmed Z, et al. Additive manufacturing of concrete in construction: potentials and challenges of 3D concrete printing. Virtual Phys Prototyp. 2016;11(3):209–225. doi:10.1080/17452759.2016.1209867
- Bos F, Ahmed Z, Jutinov E, et al. Experimental exploration of metal cable as reinforcement in 3D printed concrete. Materials (Basel). 2017;10(11):1314. doi:10.3390/ma10111314
- Diagne M, Bekiaris-Liberis N, Krstic M. Time- and state-dependent input delay-compensated bang-bang control of a screw extruder for 3D printing. Int J Robust Nonlinear Control. 2017;27(17):3727–3757. doi:10.1002/rnc.3761
- Valkenaers H, Vogeler F, Ferraris E, et al. A novel approach to additive manufacturing: Screw extrusion 3D-printing. Proceedings of the 10th International Conference on Multi-Material Micro Manufacture; 2013; San Sebastian, Spain. doi:10.3850/978-981-07-7247-5-359
- Zein I, Hutmacher DW, Tan KC, et al. Fused deposition modeling of novel scaffold architectures for tissue engineering applications. Biomaterials. 2002;23(4):1169–1185. doi:10.1016/s0142-9612(01)00232-0
- Huang W, Zhang X, Wu Q, et al. Fabrication of HA/β-TCP scaffolds based on micro-syringe extrusion system. Rapid Prototyp J. 2013;19(5):319–326. doi:10.1108/rpj-01-2012-0004
- Bekker ACM, Verlinden JC. Life cycle assessment of wire + arc additive manufacturing compared to green sand casting and CNC milling in stainless steel. J Cleaner Prod. 2018;177:438–447. doi:10.1016/j.jclepro.2017.12.148
- Busachi A, Erkoyuncu J, Colegrove P, et al. Designing a waam based manufacturing system for defence applications. Procedia CIRP. 2015;37:48–53. doi:10.1016/j.procir.2015.08.085
- Le TT, Austin SA, Lim S, et al. Mix design and fresh properties for high-performance printing concrete. Mater Struct. 2012;45(8):1221–1232. doi:10.1617/s11527-012-9828-z
- Zhang C, Nerella VN, Krishna A, et al. Mix design concepts for 3D printable concrete: a review. Cem Concr Compos. 2021;122:104155. doi:10.1016/j.cemconcomp.2021.104155
- Hager I, Golonka A, Putanowicz R. 3D printing of buildings and building components as the future of sustainable construction? Procedia Eng. 2016;151:292–299. doi:10.1016/j.proeng.2016.07.357
- Lao W, Li M, Wong TN, et al. Improving surface finish quality in extrusion-based 3D concrete printing using machine learning-based extrudate geometry control. Virtual Phys Prototyp. 2020;15(2):178–193. doi:10.1080/17452759.2020.1713580
- Lehmann T, Rose D, Ranjbar E, et al. Large-scale metal additive manufacturing: a holistic review of the state of the art and challenges. Int Mater Rev. 2021;67(4):410–459. doi:10.1080/09506608.2021.1971427
- Li Y, Meng L, Li M, et al. Allocation and scheduling of deposition paths in a layer for multi-robot coordinated wire and arc additive manufacturing of large-scale parts. Virtual Phys Prototyp. 2024;19(1):e2300680. doi:10.1080/17452759.2023.2300680
- Poudel L, Zhou W, Sha Z. Resource-constrained scheduling for multi-robot cooperative three-dimensional printing. J Mech Des. 2021;143(7):072002. doi:10.1115/1.4050380
- Shen H, Pan L, Qian J. Research on large-scale additive manufacturing based on multi-robot collaboration technology. Addit Manuf. 2019;30:100906. doi:10.1016/j.addma.2019.100906
- Buchanan C, Gardner L. Metal 3D printing in construction: a review of methods,: research, applications, opportunities and challenges. Eng Struct. 2019;180:332–348. doi:10.1016/j.engstruct.2018.11.045
- Burger J, Huber T, Lloret-Fritschi E, et al. Design and fabrication of optimised ribbed concrete floor slabs using large scale 3D printed formwork. Autom Constr. 2022;144:104599. doi:10.1016/j.autcon.2022.104599
- Vantyghem G, De Corte W, Shakour E, et al. 3D printing of a post-tensioned concrete girder designed by topology optimization. Autom Constr. 2020;112:103084. doi:10.1016/j.autcon.2020.103084
- Anton A, Reiter L, Wangler T, et al. A 3D concrete printing prefabrication platform for bespoke columns. Autom Constr. 2021;122:103467. doi:10.1016/j.autcon.2020.103467
- Xiao J, Ji G, Zhang Y, et al. Large-scale 3D printing concrete technology: Current status and future opportunities. Cem Concr Compos. 2021;122:104115. doi:10.1016/j.cemconcomp.2021.104115
- Keating SJ, Leland JC, Cai L, et al. Toward site-specific and self-sufficient robotic fabrication on architectural scales. Sci Rob. 2017;2(5):eaam8986. doi:10.1126/scirobotics.aam8986
- Chen S, Zuo Z. Shanghai Construction Group builds China’s first on-site 3D printed habitable and deliverable two-story building, which is a national key R&D program demonstration project. Weixin Official Acc Platform. 2022 Aug 22. Available from: https://mp.weixin.qq.com/s/7jGrrEZMYm0dD0k3iuoCRA
- Chen X, Lu C, Gong M, et al. Research and application of 3D printing technology for super large-scale polymer composite material. Constr Technol. 2021;50(21):41–45, 63. doi:10.7672/sgjs2021210041
- Pan D, Zhu Y. China’s first on-site 3D printing deliverable two-story building - National project demonstration project. Sohu; Jiangsu City Channel. 2022 Aug 11. Available from: https://www.sohu.com/a/575952916_120144890
- Ota H, Emaminejad S, Gao Y, et al. Application of 3D printing for smart objects with embedded electronic sensors and systems. Adv Mater Technol. 2016;1(1):1600013. doi:10.1002/admt.201600013
- Leigh SJ, Bradley RJ, Purssell CP, et al. A simple,: low-cost conductive composite material for 3D printing of electronic sensors. PLoS One. 2012;7(11):e49365. doi:10.1371/journal.pone.0049365
- Kong Y, Gupta MK, Johnson BW, et al. 3D printed bionic nanodevices. Nano Today. 2016;11(3):330–350. doi:10.1016/j.nantod.2016.04.007
- Li Q, Kulikowski J, Doan D, et al. Mechanical nanolattices printed using nanocluster-based photoresists. Science. 2022;378(6621):768–773. doi:10.1126/science.abo6997
- Kim F, Kwon B, Eom Y, et al. 3D printing of shape-conformable thermoelectric materials using all-inorganic Bi2Te3-based inks. Nat Energy. 2018;3:301–309. doi:10.1038/s41560-017-0071-2
- Song JH, Kim Y-T, Cho S, et al. Surface-embedded stretchable electrodes by direct printing and their uses to fabricate ultrathin vibration sensors and circuits for 3D structures. Adv Mater. 2017;29(43):1702625. doi:10.1002/adma.201702625
- Rahman MT, Moser R, Zbib HM, et al. 3D printed high performance strain sensors for high temperature applications. J Appl Phys. 2018;123(2):024501. doi:10.1063/1.4999076
- Muth JT, Vogt DM, Truby RL, et al. Embedded 3D printing of strain sensors within highly stretchable elastomers. Adv Mater. 2014;26(36):6307–6312. doi:10.1002/adma.201400334
- Wallin TJ, Pikul J, Shepherd RF. 3D printing of soft robotic systems. Nat Rev Mater. 2018;3(6):84–100. doi:10.1038/s41578-018-0002-2
- Miner GL, Ham JM, Kluitenberg GJ. A heat-pulse method for measuring sap flow in corn and sunflower using 3D-printed sensor bodies and low-cost electronics. Agric For Meteorol. 2017;246:86–97. doi:10.1016/j.agrformet.2017.06.012
- Khosravani MR, Reinicke T. 3D-printed sensors: current progress and future challenges. Sens Actuators, A. 2020;305:111916. doi:10.1016/j.sna.2020.111916
- Windl R, Abert C, Bruckner F, et al. Contactless and absolute linear displacement detection based upon 3D printed magnets combined with passive radio-frequency identification. AIP Adv. 2017;7(11):115121. doi:10.1063/1.5004499
- Areir M, Xu Y, Harrison D, et al. 3D printing of highly flexible supercapacitor designed for wearable energy storage. Mater Sci Eng B. 2017;226:29–38. doi:10.1016/j.mseb.2017.09.004
- Ruiz-Morales JC, Hernández-Rodríguez EM, Acosta-Mora P, et al. Prospective use of the 3D printing technology for the microstructural engineering of Solid Oxide Fuel Cell components. Bol Soc Esp Ceram Vidrio. 2014;53(5):213–216. doi:10.3989/cyv.252014
- McCoul D, Rosset S, Schlatter S, et al. Inkjet 3D printing of UV and thermal cure silicone elastomers for dielectric elastomer actuators. Smart Mater Struct. 2017;26(12):125022. doi:10.1088/1361-665X/aa9695
- Lee CS, Taylor A, Beirne S, et al. 3D-Printed conical arrays of TiO2 electrodes for enhanced photoelectrochemical water splitting. Adv Energy Mater. 2017;7(21):1701060–1701060. doi:10.1002/aenm.201701060
- Garra P, Graff B, Morlet-Savary F, et al. Charge transfer complexes as pan-scaled photoinitiating systems: from 50 μm 3D printed polymers at 405 nm to extremely deep photopolymerization (31 cm). Macromolecules. 2018;51(1):57–70. doi:10.1021/acs.macromol.7b02185
- Weisgrab G, Ovsianikov A, Costa PF. Functional 3D printing for microfluidic chips. Adv Mater Technol. 2019;4:1900275. doi:10.1002/admt.201900275
- Bartlett NW, Tolley MT, Overvelde JTB, et al. A 3D-printed, functionally graded soft robot powered by combustion. Science. 2015;349(6244):161–165. doi:10.1126/science.aab0129
- Carrico JD, Traeden NW, Aureli M, et al. Fused filament 3D printing of ionic polymer-metal composites (IPMCs). Smart Mater Struct. 2015;24:125021. doi:10.1088/0964-1726/24/12/125021
- Larson NM, Mueller J, Chortos A, et al. Rotational multimaterial printing of filaments with subvoxel control. Nature. 2023;613(7945):682–688. doi:10.1038/s41586-022-05490-7
- Mueller J, Raney JR, Shea K, et al. Architected lattices with high stiffness and toughness via multicore-shell 3D printing. Adv Mater. 2018;30(12):1705001. doi:10.1002/adma.201705001
- Hergel J, Lefebvre S. Clean color: improving multi-filament 3D prints. Comput Graph Forum. 2014;33(2):469–478. doi:10.1111/cgf.12318
- Liu X, Yuk H, Lin S, et al. 3D Printing of living responsive materials and devices. Adv Mater. 2017;30(4):1704821. doi:10.1002/adma.201704821
- Truby RL, Lewis JA. Printing soft matter in three dimensions. Nature. 2016;540(7633):371–378. doi:10.1038/nature21003
- Skylar-Scott MA, Mueller J, Visser CW, et al. Voxelated soft matter via multimaterial multinozzle 3D printing. Nature. 2019;575(7782):330–335. doi:10.1038/s41586-019-1736-8
- Jeong H, Cui Y, Tentzeris MM, et al. Hybrid (3D and inkjet) printed electromagnetic pressure sensor using metamaterial absorber. Addit Manuf. 2020;35:101405. doi:10.1016/j.addma.2020.101405
- Shangguan H, Kang J, Deng C, et al. 3D-printed shell-truss sand mold for aluminum castings. J Mater Process Technol. 2017;250:247–253. doi:10.1016/j.jmatprotec.2017.05.010
- Anelli S, Rosa M, Baiutti F, et al. Hybrid-3D printing of symmetric solid oxide cells by inkjet printing and robocasting. Addit Manuf. 2022;51:102636. doi:10.1016/j.addma.2022.102636
- Lloret E, Shahab AR, Linus M, et al. Complex concrete structures: merging existing casting techniques with digital fabrication. Comput Aided Des. 2015;60:40–49. doi:10.1016/j.cad.2014.02.011
- Furet B, Poullain P, Garnier S. 3D printing for construction based on a complex wall of polymer-foam and concrete. Addit Manuf. 2019;28:58–64. doi:10.1016/j.addma.2019.04.002
- Kostakis V, Papachristou M. Commons-based peer production and digital fabrication: the case of a RepRap-based, lego-built 3D printing-milling machine. Telemat Inform. 2014;31(3):434–443. doi:10.1016/j.tele.2013.09.006
- Li L, Haghighi A, Yang Y. A novel 6-axis hybrid additive-subtractive manufacturing process: design and case studies. J Manuf Process. 2018;33:150–160. doi:10.1016/j.jmapro.2018.05.008
- Karunakaran KP, Suryakumar S, Pushpa V, et al. Low cost integration of additive and subtractive processes for hybrid layered manufacturing. Robot Comput Integr Manuf. 2010;26(5):490–499. doi:10.1016/j.rcim.2010.03.008
- Karunakaran KP, Bernard A, Suryakumar S, et al. Rapid manufacturing of metallic objects. Rapid Prototyp J. 2012;18(4):264–280. doi:10.1108/13552541211231644
- Newman ST, Zhu Z, Dhokia V, et al. Process planning for additive and subtractive manufacturing technologies. CIRP Ann. 2015;64(1):467–470. doi:10.1016/j.cirp.2015.04.109
- Flynn JM, Shokrani A, Newman ST, et al. Hybrid additive and subtractive machine tools – Research and industrial developments. Int J Mach Tools Manuf. 2016;101:79–101. doi:10.1016/j.ijmachtools.2015.11.007
- Marchment T, Sanjayan J. Mesh reinforcing method for 3D Concrete Printing. Autom Constr. 2020;109:102992. doi:10.1016/j.autcon.2019.102992
- Valentine AD, Busbee TA, Boley JW, et al. Hybrid 3D printing of soft electronics. Adv Mater. 2017;29(40):1703817. doi:10.1002/adma.201703817
- Macdonald E, Salas R, Espalin D, et al. 3D Printing for the rapid prototyping of structural electronics. IEEE Access. 2014;2:234–242. doi:10.1109/ACCESS.2014.2311810
- Giftthaler M, Sandy T, Dörfler K, et al. Mobile robotic fabrication at 1:1 scale: the In situ Fabricator. Constr Rob. 2017;1:3–14. doi:10.1007/s41693-017-0003-5
- Sullivan KT, Zhu C, Duoss EB, et al. Controlling material reactivity using architecture. Adv Mater. 2016;28(10):1934–1939. doi:10.1002/adma.201504286
- Mechtcherine V, Michel A, Liebscher M, et al. Mineral-impregnated carbon fiber composites as novel reinforcement for concrete construction: material and automation perspectives. Autom Constr. 2020;110:103002. doi:10.1016/j.autcon.2019.103002
- Yung WKC, Sun B, Meng Z, et al. Additive and photochemical manufacturing of copper. Sci Rep. 2016;6; doi:10.1038/srep39584
- González-Henríquez CM, Sarabia-Vallejos MA, Rodriguez-Hernandez J. Polymers for additive manufacturing and 4D-printing: materials,: methodologies, and biomedical applications. Prog Polym Sci. 2019;94:57–116. doi:10.1016/j.progpolymsci.2019.03.001
- Tibbits S. 4D printing: multi-material shape change. Archit Des. 2014;84(1):116–121. doi:10.1002/ad.1710
- Khoo ZX, Teoh JEM, Liu Y, et al. 3D printing of smart materials: a review on recent progresses in 4D printing. Virtual Phys Prototyp. 2015;10(3):103–122. doi:10.1080/17452759.2015.1097054
- Lee J, Kim H-C, Choi J-W, et al. A review on 3D printed smart devices for 4D printing. Int J Precis Eng Manuf Green Technol. 2017;4(3):373–383. doi:10.1007/s40684-017-0042-x
- Ding Z, Yuan C, Peng X, et al. Direct 4D printing via active composite materials. Sci Adv. 2017;3(4):e1602890. doi:10.1126/sciadv.1602890
- Zafar MQ, Zhao H. 4D printing: future insight in additive manufacturing. Met Mater Int. 2019;26:564–585. doi:10.1007/s12540-019-00441-w
- Leist SK, Zhou J. Current status of 4D printing technology and the potential of light-reactive smart materials as 4D printable materials. Virtual Phys Prototyp. 2016;11(4):249–262. doi:10.1080/17452759.2016.1198630
- Kuang X, Roach DJ, Wu J, et al. Advances in 4D printing: materials and applications. Adv Funct Mater. 2018;29(2):1805290. doi:10.1002/adfm.201805290
- Momeni F, Mehdi Hassani M, N S, et al. A review of 4D printing. Mater Des. 2017;122:42–79. doi:10.1016/j.matdes.2017.02.068
- Benyahia K, Seriket H, Prod’hon R, et al. A computational design approach for multi-material 4D printing based on interlocking blocks assembly. Addit Manuf. 2022;58:102993. doi:10.1016/j.addma.2022.102993
- Yuan C, Wang F, Ge Q. Multimaterial direct 4D printing of high stiffness structures with large bending curvature. Extreme Mech Lett. 2021;42:101122. doi:10.1016/j.eml.2020.101122
- Boley JW, van Rees WM, Lissandrello C, et al. Shape-shifting structured lattices via multimaterial 4D printing. Proc Natl Acad Sci USA. 2019;116(42):20856–20862. doi:10.1073/pnas.1908806116
- Bodaghi M, Damanpack AR, Liao WH. Adaptive metamaterials by functionally graded 4D printing. Mater Des. 2017;135:26–36. doi:10.1016/j.matdes.2017.08.069
- Zeng C, Liu L, Bian W, et al. 4D printed electro-induced continuous carbon fiber reinforced shape memory polymer composites with excellent bending resistance. Composites Part B. 2020;194:108034. doi:10.1016/j.compositesb.2020.108034
- Sydney Gladman A, Matsumoto EA, Nuzzo RG, et al. Biomimetic 4D printing. Nat Mater. 2016;15(4):413–418. doi:10.1038/nmat4544
- Zolfagharian A, Kaynak A, Kouzani A. Closed-loop 4D-printed soft robots. Mater Des. 2020;188:108411. doi:10.1016/j.matdes.2019.108411
- Kim Y, Yuk H, Zhao R, et al. Printing ferromagnetic domains for untethered fast-transforming soft materials. Nature. 2018;558(7709):274–279. doi:10.1038/s41586-018-0185-0
- Hoa S, Abdali M, Jasmin A, et al. Development of a new flexible wing concept for Unmanned Aerial Vehicle using corrugated core made by 4D printing of composites. Compos Struct. 2022;290:115444. doi:10.1016/j.compstruct.2022.115444
- Wu W, Zhou Y, Liu Q, et al. Metallic 4D printing of laser stimulation. Adv Sci. 2023;10(12):2206486–2206486. doi:10.1002/advs.202206486
- Mitchell A, Lafont U, Hołyńska M, et al. Additive manufacturing — a review of 4D printing and future applications. Addit Manuf. 2018;24:606–626. doi:10.1016/j.addma.2018.10.038
- Tahouni Y, Cheng T, Lajewski S, et al. Codesign of biobased cellulose-filled filaments and mesostructures for 4D printing humidity responsive smart structures. 3D Printing Addit Manuf. 2022;10(1). doi:10.1089/3dp.2022.0061
- Yi H. 4D-printed parametric façade in architecture: prototyping a self-shaping skin using programmable two-way shape memory composite (TWSMC). Eng Constr Archit Manage. 2021;29(10):4132–4152. doi:10.1108/ecam-05-2021-0428
- Yi H, Kim Y. Prototyping of 4D-printed self-shaping building skin in architecture: design,: fabrication, and investigation of a two-way shape memory composite (TWSMC) façade panel. J Building Eng. 2021;43:103076. doi:10.1016/j.jobe.2021.103076
- Lanzetta M, Sachs E. Improved surface finish in 3D printing using bimodal powder distribution. Rapid Prototyp J. 2003;9(3):157–166. doi:10.1108/13552540310477463
- Wu W, Jiang J, Jiang H, et al. Improving bending and dynamic mechanics performance of 3D printing through ultrasonic strengthening. Mater Lett. 2018;220:317–320. doi:10.1016/j.matlet.2018.03.048
- Todd I. No more tears for metal 3D printing. Nature. 2017;549(7672):342–343. doi:10.1038/549342a
- Zhang K, Meng Q, Qu Z, et al. A review of defects in vat photopolymerization additive-manufactured ceramics: characterization,: control, and challenges. J Eur Ceram Soc. 2024;44(3):1361–1384. doi:10.1016/j.jeurceramsoc.2023.10.067
- Feng X, Yang Z, Rostom SSH, et al. Reinforcing 3D printed acrylonitrile butadiene styrene by impregnation of methacrylate resin and cellulose nanocrystal mixture: Structural effects and homogeneous properties. Mater Des. 2018;138:62–70. doi:10.1016/j.matdes.2017.10.050
- Li Z, Wang L, Ma G. Mechanical improvement of continuous steel microcable reinforced geopolymer composites for 3D printing subjected to different loading conditions. Composites Part B. 2020;187:107796. doi:10.1016/j.compositesb.2020.107796
- Breseghello L, Naboni R. Toolpath-based design for 3D concrete printing of carbon-efficient architectural structures. Addit Manuf. 2022;56:102872. doi:10.1016/j.addma.2022.102872
- Ladd C, So J-H, Muth J, et al. 3D Printing of free standing liquid metal microstructures. Adv Mater. 2013;25(36):5081–5085. doi:10.1002/adma.201301400
- Karl D, Duminy T, Lima P, et al. Clay in situ resource utilization with Mars global simulant slurries for additive manufacturing and traditional shaping of unfired green bodies. Acta Astronaut. 2020;174:241–253. doi:10.1016/j.actaastro.2020.04.064
- Tang S, Yang L, Li G, et al. 3D printing of highly-loaded slurries via layered extrusion forming: parameters optimization and control. Addit Manuf. 2019;28:546–553. doi:10.1016/j.addma.2019.05.034
- Calneryte D, Barauskas R, Milasiene D, et al. Multi-scale finite element modeling of 3D printed structures subjected to mechanical loads. Rapid Prototyp J. 2018;24(1):177–187. doi:10.1108/RPJ-05-2016-0074
- Chanda D, Shigeta K, Gupta S, et al. Large-area flexible 3D optical negative index metamaterial formed by nanotransfer printing. Nat Nanotechnol. 2011;6(7):402–407. doi:10.1038/nnano.2011.82
- Yang H, Leow WR, Wang T, et al. 3D printed photoresponsive devices based on shape memory composites. Adv Mater. 2017;29(33):1701627. doi:10.1002/adma.201701627
- Smith TM, Kantzos CA, Zarkevich NA, et al. A 3D printable alloy designed for extreme environments. Nature. 2023: 1–6. doi:10.1038/s41586-023-05893-0
- Dimas LS, Bratzel GH, Eylon I, et al. Tough composites inspired by mineralized natural materials: computation, 3D printing, and Testing. Adv Funct Mater. 2013;23(36):4629–4638. doi:10.1002/adfm.201300215
- Kokkinis D, Schaffner M, Studart AR. Multimaterial magnetically assisted 3D printing of composite materials. Nat Commun. 2015;6(1). doi:10.1038/ncomms9643
- Gu D. Materials creation adds new dimensions to 3D printing. Sci Bull. 2016;61(22):1718–1722. doi:10.1007/s11434-016-1191-y
- Bates SRG, Farrow IR, Trask RS. 3D printed polyurethane honeycombs for repeated tailored energy absorption. Mater Des. 2016;112:172–183. doi:10.1016/j.matdes.2016.08.062
- Berger JB, Wadley HNG, McMeeking RM. Mechanical metamaterials at the theoretical limit of isotropic elastic stiffness. Nature. 2017;543(7646):533–537. doi:10.1038/nature21075
- Chen Y, Li T, Jia Z, et al. 3D printed hierarchical honeycombs with shape integrity under large compressive deformations. Mater Des. 2018;137:226–234. doi:10.1016/j.matdes.2017.10.028
- Lipton JI, Lipson H. 3D printing variable stiffness foams using viscous thread instability. Sci Rep. 2016;6:29996. doi:10.1038/srep29996
- Wadley HNG. Multifunctional periodic cellular metals. Philos Trans R Soc A. 2005;364(1838):31–68. doi:10.1098/rsta.2005.1697
- Mansouri MR, Montazerian H, Schmauder S, et al. 3D-printed multimaterial composites tailored for compliancy and strain recovery. Compos Struct. 2018;184:11–17. doi:10.1016/j.compstruct.2017.09.049
- Jiang Z, Diggle B, Tan ML, et al. Extrusion 3D printing of polymeric materials with advanced properties. Adv Sci. 2020;7(17):2001379. doi:10.1002/advs.202001379
- Saleh MS, Hu C, Panat R. Three-dimensional microarchitected materials and devices using nanoparticle assembly by pointwise spatial printing. Sci Adv. 2017;3(3):e1601986. doi:10.1126/sciadv.1601986
- Wang Y, Zhang L, Daynes S, et al. Design of graded lattice structure with optimized mesostructures for additive manufacturing. Mater Des. 2018;142:114–123. doi:10.1016/j.matdes.2018.01.011
- Fee C, Nawada S, Dimartino S. 3D printed porous media columns with fine control of column packing morphology. J Chromatogr, A. 2014;1333:18–24. doi:10.1016/j.chroma.2014.01.043
- Bian B, Shi D, Cai X, et al. 3D printed porous carbon anode for enhanced power generation in microbial fuel cell. Nano Energy. 2018;44:174–180. doi:10.1016/j.nanoen.2017.11.070
- Qin Z, Jung GS, Kang MJ, et al. The mechanics and design of a lightweight three-dimensional graphene assembly. Sci Adv. 2017;3(1):e1601536. doi:10.1126/sciadv.1601536
- Yang Y, Chen Z, Song X, et al. Biomimetic anisotropic reinforcement architectures by electrically assisted nanocomposite 3D printing. Adv Mater. 2017;29(11):1605750–1605750. doi:10.1002/adma.201605750
- Qin Z, Compton BG, Lewis JA, et al. Structural optimization of 3D-printed synthetic spider webs for high strength. Nat Commun. 2015;6:1. doi:10.1038/ncomms8038
- Juračka D, Katzer J, Kobaka J, et al. Concept of a 3D-printed voronoi egg-shaped habitat for permanent lunar outpost. Appl Sci. 2023;13(2):1153–1153. doi:10.3390/app13021153
- Chen L, Tang X, Xie P, et al. 3D printing of artificial leaf with tunable hierarchical porosity for CO2 photoreduction. Chem Mater. 2018;30(3):799–806. doi:10.1021/acs.chemmater.7b04313
- Gu D, Shi X, Poprawe R, et al. Material-structure-performance integrated laser-metal additive manufacturing. Science. 2021;372(6545). doi:10.1126/science.abg1487
- Holshouser C, Newell C, Palas S, et al. Out of bounds additive manufacturing. Adv Mater Process. 2013;171(3):15–19.
- Xu W, Huang S, Han D, et al. Toward automated construction: the design-to-printing workflow for a robotic in-situ 3D printed house. Case Stud Constr Mater. 2022;17:e01442. doi:10.1016/j.cscm.2022.e01442
- Ge Q, Qi HJ, Dunn ML. Active materials by four-dimension printing. Appl Phys Lett. 2013;103(13):131901. doi:10.1063/1.4819837
- Pearce JM. Building research equipment with free,: open-source hardware. Science. 2012;337(6100):1303–1304. doi:10.1126/science.1228183
- Dörfler K, Dielemans G, Lachmayer L, et al. Additive manufacturing using mobile robots: opportunities and challenges for building construction. Cem Concr Res. 2022;158:106772. doi:10.1016/j.cemconres.2022.106772
- Keating S, Oxman N. Compound fabrication: a multi-functional robotic platform for digital design and fabrication. Robot Comput Integr Manuf. 2013;29(6):439–448. doi:10.1016/j.rcim.2013.05.001
- Khoshnevis B, Yuan X, Zahiri B, et al. Construction by Contour Crafting using sulfur concrete with planetary applications. Rapid Prototyp J. 2016;22(5):848–856. doi:10.1108/RPJ-11-2015-0165
- Gong J, Zuo Z, et al. Three-demensional scanning digital construction. Beijing: China Architecture & Building Press; 2020, pp. 1–207.
- Salet TAM, Ahmed ZY, Bos FP, et al. Design of a 3D printed concrete bridge by testing. Virtual Phys Prototyp. 2018;13(3):222–236. doi:10.1080/17452759.2018.1476064
- Duballet R, Baverel O, Dirrenberger J. Classification of building systems for concrete 3D printing. Autom Constr. 2017;83:247–258. doi:10.1016/j.autcon.2017.08.018
- Carneau P, Mesnil R, Roussel N, et al. Additive manufacturing of cantilever – from masonry to concrete 3D printing. Autom Constr. 2020;116:103184. doi:10.1016/j.autcon.2020.103184
- Hildreth OJ, Nassar AR, Chasse KR, et al. Dissolvable metal supports for 3D direct metal printing. 3D Printing Addit Manuf. 2016;3(2):90–97. doi:10.1089/3dp.2016.0013
- Mechtcherine V, Nerella VN, Will F, et al. Large-scale digital concrete construction – CONPrint3D concept for on-site,: monolithic 3D-printing. Autom Constr. 2019;107:102933. doi:10.1016/j.autcon.2019.102933
- Nan IC, Patterson C, Pedreschi R. Digital materialization: additive and robotical manufacturing with clay and silicone. 34th ECAADe Conference (ECAADe); 2016. doi:10.52842/conf.ecaade.2016.1.345
- Zuo Z, Huang Y, Pan X, et al. Experimental research on remote real-time monitoring of concrete strength for highrise building machine during construction. Measurement (Mahwah NJ). 2021;178:109430. doi:10.1016/j.measurement.2021.109430
- Hunt, G., Mitzalis, F., Alhinai, T., Hooper, P. A., & Kovac, M. 3D printing with flying robots. 2014 IEEE International Conference on Robotics and Automation (ICRA); 2014; Hong-Kong: China. p. 4493–4499. doi:10.1109/ICRA.2014.6907515
- Zhang K, Chermprayong P, Xiao F, et al. Aerial additive manufacturing with multiple autonomous robots. Nature. 2022;609(7928):709–717. doi:10.1038/s41586-022-04988-4
- Zuo Z, Gong J, Huang Y, et al. Application of 3D laser scanning and printing in geotechnical construction. The 1st International Symposium on Soil Dynamics and Geotechnical Sustainability; 2016; ISBN: 978-988-14032-4-7.
- Kim D, Gil J-M. Reliable and fault-tolerant software-defined network operations scheme for remote 3D printing. J Electron Mater. 2015;44(3):804–814. doi:10.1007/s11664-014-3548-9
- Luo X, Zhang L, Ren L, et al. A dynamic and static data based matching method for cloud 3D printing. Robot Comput Integr Manuf. 2020;61:101858–101858. doi:10.1016/j.rcim.2019.101858
- Cui J, Ren L, Mai J, et al. 3D Printing in the context of cloud manufacturing. Robot Comput Integr Manuf. 2022;74:102256. doi:10.1016/j.rcim.2021.102256
- Bazli M, Ashrafi H, Rajabipour A, et al. 3D printing for remote housing: benefits and challenges. Autom Constr. 2023;148:104772. doi:10.1016/j.autcon.2023.104772
- Wu Q, Xie N, Zheng S, et al. Online order scheduling of multi 3D printing tasks based on the additive manufacturing cloud platform. J Manuf Syst. 2022;63:23–34. doi:10.1016/j.jmsy.2022.02.007
- Vaswani A, Shazeer N, Parmar N, et al. Attention is all you need. Proceedings of the 31st International Conference on Neural Information Processing Systems (NIPS); 2017; Long Beach, CA, USA. p. 6000–6010. ISBN: 9781510860964.
- Bouncken R, Barwinski R. Shared digital identity and rich knowledge ties in global 3D printing—A drizzle in the clouds? Global Strategy J. 2020;11(1). doi:10.1002/gsj.1370
- Debroy T, Zhang W, Turner J, et al. Building digital twins of 3D printing machines. Scr Mater. 2017;135:119–124. doi:10.1016/j.scriptamat.2016.12.005
- Perrot A, Pierre A, Nerella VN, et al. From analytical methods to numerical simulations: a process engineering toolbox for 3D concrete printing. Cem Concr Compos. 2021;122:104164. doi:10.1016/j.cemconcomp.2021.104164
- Bader C, Kolb D, Weaver JC, et al. Making data matter: voxel printing for the digital fabrication of data across scales and domains. Sci Adv. 2018;4(5). doi:10.1126/sciadv.aas8652
- Nerella VN, Näther M, Iqbal A, et al. Inline quantification of extrudability of cementitious materials for digital construction. Cem Concr Compos. 2019;95:260–270. doi:10.1016/j.cemconcomp.2018.09.015
- Nguyen-Van V, Li S, Liu J, et al. Modelling of 3D concrete printing process: a perspective on material and structural simulations. Addit Manuf. 2023;61:103333. doi:10.1016/j.addma.2022.103333
- Garg A, Lam JSL, Savalani MM. A new computational intelligence approach in formulation of functional relationship of open porosity of the additive manufacturing process. Int J Adv Manuf Technol. 2015;80:555–565. doi:10.1007/s00170-015-6989-2
- Bukkapatnam S, Clark B. Dynamic modeling and monitoring of contour crafting—an extrusion-based layered manufacturing process. J Manuf Sci Eng. 2007;129(1):135–142. doi:10.1115/1.2375137
- van den Heever M, Bester F, Kruger J, et al. Numerical modelling strategies for reinforced 3D concrete printed elements. Addit Manuf. 2022;50:102569. doi:10.1016/j.addma.2021.102569
- Gannarapu A, Dutta P, Gozen BA. Prediction of steady-state freeze front position during 3D printing of microstructures. Int J Heat Mass Transfer. 2017;115:743–753. doi:10.1016/j.ijheatmasstransfer.2017.07.092
- DebRoy T, Wei HL, Zuback JS, et al. Additive manufacturing of metallic components – Process, structure and properties. Prog Mater Sci. 2018;92:112–224. doi:10.1016/j.pmatsci.2017.10.001
- Xia M, Nematollahi B, Sanjayan J. Printability, accuracy and strength of geopolymer made using powder-based 3D printing for construction applications. Autom Constr. 2019;101:179–189. doi:10.1016/j.autcon.2019.01.013
- Davtalab O, Kazemian A, Yuan X, et al. Automated inspection in robotic additive manufacturing using deep learning for layer deformation detection. J Intell Manuf. 2020;33. doi:10.1007/s10845-020-01684-w
- Petsiuk A, Pearce JM. Towards smart monitored AM: Open source in-situ layer-wise 3D printing image anomaly detection using histograms of oriented gradients and a physics-based rendering engine. Addit Manuf. 2022;52:102690. doi:10.1016/j.addma.2022.102690
- Goh GD, Hamzah NMB, Yeong WY. Anomaly detection in fused filament fabrication using machine learning. 3D Printing Addit Manuf. 2022;10(3):428–437. doi:10.1089/3dp.2021.0231
- Jin Z, Zhang Z, Shao X, et al. Monitoring anomalies in 3D bioprinting with deep neural networks. ACS Biomater Sci Eng. 2021;9(7):3945–3952. doi:10.1021/acsbiomaterials.0c01761
- Ma G, Wang L. A critical review of preparation design and workability measurement of concrete material for largescale 3D printing. Front Struct Civ Eng. 2017;12(3):382–400. doi:10.1007/s11709-017-0430-x
- Wolfs RJM, Bos FP, Salet TAM. Correlation between destructive compression tests and non-destructive ultrasonic measurements on early age 3D printed concrete. Constr Build Mater. 2018b;181:447–454. doi:10.1016/j.conbuildmat.2018.06.060
- Hou S, Duan Z, Xiao J, et al. A review of 3D printed concrete: performance requirements, testing measurements and mix design. Constr Build Mater. 2021;273:121745. doi:10.1016/j.conbuildmat.2020.121745
- Aycock KI, Hariharan P, Craven BA. Particle image velocimetry measurements in an anatomical vascular model fabricated using inkjet 3D printing. Exp Fluids. 2017;58(11). doi:10.1007/s00348-017-2403-1
- Kazemian A, Yuan X, Davtalab O, et al. Computer vision for real-time extrusion quality monitoring and control in robotic construction. Autom Constr. 2019;101:92–98. doi:10.1016/j.autcon.2019.01.022
- Santana L, Lino Alves J, da Costa Sabino Netto A. A study of parametric calibration for low cost 3D printing: seeking improvement in dimensional quality. Mater Des. 2017;135:159–172. doi:10.1016/j.matdes.2017.09.020
- Silva DN, Gerhardt de Oliveira M, Meurer E, et al. Dimensional error in selective laser sintering and 3D-printing of models for craniomaxillary anatomy reconstruction. J Cranio Maxillofac Surg. 2008;36(8):443–449. doi:10.1016/j.jcms.2008.04.003
- Parsazadeh M, Sharma S, Dahotre N. Towards the next generation of machine learning models in additive manufacturing: a review of process dependent material evolution. Prog Mater Sci. 2023;135:101102–101102. doi:10.1016/j.pmatsci.2023.101102
- Qi X, Chen G, Li Y, et al. Applying neural-network-based machine learning to additive manufacturing: current applications, challenges, and future perspectives. Engineering. 2019;5(4):721–729. doi:10.1016/j.eng.2019.04.012
- Werfel J, Petersen K, Nagpal R. Designing collective behavior in a termite-inspired robot construction team. Science. 2014;343(6172):754–758. doi:10.1126/science.1245842
- Zhu Z, Ng DWH, Park HS, et al. 3D-printed multifunctional materials enabled by artificial-intelligence-assisted fabrication technologies. Nat Rev Mater. 2021;6:27–47. doi:10.1038/s41578-020-00235-2
- Tao Y, Ren Q, Vantyghem G, et al. Extending 3D concrete printing to hard rock tunnel linings: Adhesion of fresh cementitious materials for different surface inclinations. Autom Constr. 2023;149:104787–104787. doi:10.1016/j.autcon.2023.104787
- Mazhoud B, Perrot A, Picandet V, et al. Underwater 3D printing of cement-based mortar. Constr Build Mater. 2019;214:458–467. doi:10.1016/j.conbuildmat.2019.04.134
- Tönissen DD, Schlicher L. Using 3D-printing in disaster response: the two-stage stochastic 3D-printing knapsack problem. Comput Oper Res. 2021;133:105356. doi:10.1016/j.cor.2021.105356
- Isachenkov M, Chugunov S, Akhatov I, et al. Regolith-based additive manufacturing for sustainable development of lunar infrastructure – An overview. Acta Astronaut. 2021;180:650–678. doi:10.1016/j.actaastro.2021.01.005
- Yashar M, Michealsen P, Hammond B, et al. Building information modeling (BIM) workflows for construction sequencing and 4D-planning of 3D-printed ISRU surface habitats. 17th Biennial International Conference on Engineering,: Science, Construction, and Operations in Challenging Environments; 2021. doi:10.1061/9780784483374.128
- Troemner M, Ramyar E, Meehan J, et al. A 3D-printing centered approach to mars habitat architecture and fabrication. J Aerosp Eng. 2022;35(1):04021109. doi:10.1061/(ASCE)AS.1943-5525.0001359
- Li H, Meng H, Lan M, et al. Development of a novel material and casting method for in situ construction on Mars. Powder Technol. 2021;390:219–229. doi:10.1016/j.powtec.2021.05.054
- Wu W, Geng P, Li G, et al. Influence of layer thickness and raster angle on the mechanical properties of 3D-printed peek and a comparative mechanical study between PEEK and ABS. Materials (Basel). 2015;8(9):5834–5846. doi:10.3390/ma8095271
- Zhang Y, Zhang F, Yan Z, et al. Printing,: folding and assembly methods for forming 3D mesostructures in advanced materials. Nat Rev Mater. 2017;2. doi:10.1038/natrevmats.2017.19
- Liu S, Li Y, Li N. A novel free-hanging 3D printing method for continuous carbon fiber reinforced thermoplastic lattice truss core structures. Mater Des. 2018;137:235–244. doi:10.1016/j.matdes.2017.10.007
- Wolfs RJM, Bos FP, Salet TAM. Early age mechanical behaviour of 3D printed concrete: numerical modelling and experimental testing. Cem Concr Res. 2018;106:103–116. doi:10.1016/j.cemconres.2018.02.001