ABSTRACT
As a pivotal component of robotic systems and wearable devices, flexible actuators play a significant role; while it remains a challenge to achieve intelligent applications due to complex high-degree-of-freedom deformation control and insufficient functionality. Here, inspired by the leaf structure of Ficus benjamina 'Barok', a new type of programmable flexible actuator (PFA) prototype that can be 4D printed is designed, featuring a liquid metal-spidroin-liquid crystal elastomer composite printing functional structure and microstructure substrate, which achieves selective actuation and integrates sensing functions through differentiated manufacturing and pattern design. The interior of PFA is composed of functional masks with photothermal effects and differentiated photopolymerization mesogen structures. The microscopic rearrangement of asymmetric structures at different positions makes remote control of programming deformation convenient. Furthermore, benefiting from the integration of material properties, PFA can sense strain through resistive changes and connect to intelligent devices to transmit signals. The motion support and sensing performance of PFA have the potential to be applied to advanced robotics and human-machine interfaces.
1. Introduction
Robotic systems have been widely used in various industries such as manufacturing, service, and healthcare as automation tools to assist human work [Citation1–3]. However, the application of traditional robots is limited because these systems cannot provide safe interactions with humans and lack high degrees of freedom and precise processing methods when facing fine objects [Citation4,Citation5]. Compared with traditional robots, soft robotics systems with shapes similar to those of biological muscles have significant advantages in solving these problems, especially in medical fields that require fine-grained operations [Citation6–8]. Flexible actuators can be seen as simplified soft robotics systems that provide motion from multiple angles and achieve high compliance to adapt to complex environments and human-machine interactions [Citation9–11]. In the actuation design of flexible actuators, deformation actuation based on intelligent materials that can respond to different stimuli is currently an important strategy [Citation12]. Compared with traditional robots, this method can provide safety and certain actuation capabilities, greatly improving the accuracy and degrees of freedom. In addition to smart material actuation, the use of external power devices connected to cables for actuation and fluid pressure for actuation has also been widely applied [Citation13,Citation14]. Although flexible actuators provide a new approach for robotic systems, they still have limitations. An increase in the deformation degree of freedom necessitates more precise shape control, and flexible actuators with integrated sensing monitoring and selective actuation can play an important role in control schemes [Citation15,Citation16]. Most related research has focused on exploring combinations of functional composite materials [Citation17,Citation18]. Although composite materials integrate driving and sensing functions, the complexity and low controllability of degree of freedom control schemes hinder their application [Citation19]. Therefore, designing a highly controllable and convenient selective actuator scheme based on functional materials is still needed.
In this article, inspired by the structure of Ficus benjamina 'Barok', we propose a novel programmable flexible actuator composite material design scheme. The system has a biomimetic mesogen microstructure, spidroin, and photothermal actuator fillers, which can achieve significant deformation and selective actuation through differentiated manufacturing and can be intelligently applied, as shown in . Ficus benjamina 'Barok' is a potted plant with distinct structures on both sides of its leaves that continuously curl inward during growth. Due to their unique leaf morphology, banyan trees have attracted widespread attention in various fields in terms of structural design. It is worth noting that film-like actuators have undergone an integrated material combination and unique manufacturing procedures, and internal structural differences have been constructed to programmatically monitor the actuation mode. In addition, these different mesogen structures alter the single contraction-induced mode of liquid crystal elastomers, significantly increasing the deformation amplitude [Citation20]. Therefore, utilising asymmetric manufactured blade-like structures can become an effective strategy for achieving flexible actuator actuation mode setting and deformation degree of freedom control.
Figure 1. Schematic diagram of the PFA with programmable deformation and motion sensing signals. PFA is composed of an internal asymmetric structure inspired by Ficus benjamina 'Barok', and this differential construction is based on material properties and manufacturing modes, with the addition of microneedle patches.

Herein, we designed a PFA composed of spidroin, photothermal functional masks, and an internally asymmetric mesogen structure, which was manufactured using 4D printing and differential photopolymerization methods. When PFA is irradiated with near-infrared light, the temperature of the PFA increases, and the mesogen transitions from anisotropic to isotropic. Notably, asymmetric structural rearrangement leads to unidirectional bending of PFA toward the photopolymerization surface, which is achieved based on the material properties and manufacturing methods, improving the controllability of the actuator. Moreover, differentiated printing pattern layout can control the deformation position of the actuator. As a proof of concept, we designed a biomimetic soft robotics system and intelligent gripper using PFA to provide directional motion support for the entire system. Research has shown that the PFA prepared in the present study can undergo significant selective actuation, demonstrating the advantage of high controllability in flexible actuator applications. In addition, due to the integration of functional materials, the shape of the PFA can be reflected by changes in the resistance. Therefore, a gesture recognition device was designed to transmit sensing signals to intelligent devices for analysis and machine learning recognition. Furthermore, due to the selectivity and integration of functions, intelligent bandages were assembled based on PFA as a physical therapy method to accelerate wound recovery, which was validated through experiments in a mouse wound model. Therefore, this new type of flexible actuator has shown effective capabilities in intelligent applications, indicating its enormous potential in the fields of robotics motion systems and wearable devices.
2. Materials and methods
2.1. Materials
A eutectic gallium−indium liquid alloy (EGaIn, 75 wt% Ga and 25% wt%) was purchased from Shenyang Baijujie Co., Ltd. Spidroin was prepared in the laboratory. The liquid crystal monomer (1,4bis-[4-(3-acryloyloxypropypropyloxy)benzoyloxy]-2-methylbenzene (RM257)) was purchased from Yesheng Chemical Technology Co., Ltd. and used without further purification. Pentaerythritol tetrakis(3mercaptopropionate) (PETMP), 2,2-(ethylenedioxy)diethanethiol (EDDET), 2-hydroxy-4′-(2-hydroxyethoxy)-2-methylpropiophenone (HHMP), dipropylamine (DPA), and toluene were purchased from Aladdin. Polyurethane (PU) was purchased from JITIAN CHEMICAL Co., Ltd. (Shenzhen, China). All animal experiments were performed in strict accordance with the Guide for the Care and Use of Laboratory Animals and received approval from the Animal Investigation Ethics Committee of Nanjing Tech University.
2.2. Synthesis of liquid crystal materials
In a typical synthesis, the diacrylate mesogen RM257 (2.0 g) and the HHMP photoinitiator (0.014 g) were dissolved in 1.0 mL of toluene at 80 °C for 20 min. After cooling to room temperature, 0.144 g of PETMP (a tetrafunctional thiol cross-linking monomer) and 0.431 g of EDDET (a flexible dithiol monomer) were added.
2.3. Preparation of spider silk solution
Using the diploid repeat sequence of chimeric spidroin MaSp1 on the cloning vector pUC57 as the template, a single point mutation was used to achieve site-directed mutation by designing appropriate primers for PCR, resulting in the positions of the diploid repeat sequence GGX of spidroin MaSp1. Mutation sites were involved in this mutation, so the required octaploid mutation sequence was obtained by successive primer mutagenesis. A single colony of E. coli transformed with a chimeric spidroin plasmid was cultured in TB media at 37 °C on an orbital shaker. The culture was then used to inoculate fresh TB medium, which was allowed to grow to an OD600 of 3−5. The culture was then induced by the addition of 1 mM IPTG and continued to grow at 30 °C for 24 h. The cells were then pelleted by centrifugation, and the cell pellets were stored at −80 °C until use. The recombinant spidroin was purified by Ni-column affirmation chirography. The cell pellets were lysed in buffer A (6 M guanidine hydrochloride, 300 mM NaCl, 50 mM K2HPO4, pH = 8.0) for 12 h at 4 °C under constant stirring, followed by centrifugation. The supernatant was loaded onto a Ni-NTA column and washed with buffer B (300 mL of NaCl, 50 mM K2HPO4, 8 M urea, pH = 8.0) with 0, 20 and 50 mM imidazole in advance. Spidroin was then eluted with buffer B containing 300 mM imidazole. All SDS–PAGE gels were 1 mm thick and discontinuous, with a 4% stacking gel on the top and the indicated percentages of separation gels on the bottom. Samples were prepared in 4× protein sample buffer (60 mM Tris pH 6.8, 10% glycerol, 2% SDS, 0.01% bromophenol blue, 100 μM DTT). The gels were run on Mini-PROTEAN Tetra Cells (Bio-Rad) in 1× Tris−glycine SDS buffer (25 mM Tris base, 250 mM glycine, 0.1% w/v SDS). The protein expression level was estimated by integrating the intensity of the product band over the sum of all protein bands on the gel.
2.4. Preparation of the liquid metal-spidroin composite materials
300 μL of EGaIn was added to 700 μL of ethanol, and 100 μL of spidroin was added. The mixture was ultrasonicated for 30 min. During this period, the solution was removed every 10 min and shaken for 5 min.
2.5. Manufacturing of programmable flexible actuators
Programmable flexible actuator thin films were prepared by modifying the reported methods. The DPA catalyst (0.284 g, diluted in toluene at a ratio of 1:50) and liquid metal-spidroin composite material were added to the liquid crystal material for vortex mixing. After degassing in the vacuum chamber, the mixture was subjected to 4D printing, followed by a 12-hour reaction and heating at 80 °C in a vacuum oven for 24 h to evaporate the solvent in the composite material. After pouring polyurethane into the mold for curing and demolding, the next step is to uniaxial stretch the film (300% strain) to orient the mesogen structure to a temporary monodomain state. Then, single-sided photopolymerization is carried out to form cross-links between excess mesogens to stabilise the monodomain state.
2.6. Photothermal response performance testing of programmable flexible actuators
The photothermal response of programmable flexible actuators (size: 10 × 3 × 1.5 mm) under irradiation with an 808 nm laser beam (power density: 2 W cm−2) was studied. During the irradiation process, the distance between the laser and the flexible actuator was always 20 cm. The deformation status of programmable flexible actuators is recorded in real time through a digital camera. Real-time recording of temperature changes and corresponding thermal images of programmable flexible actuators and liquid crystal elastomers through infrared thermal imaging cameras.
2.7. Characterisation and measurements
The microstructure of the programmable flexible actuators was observed by a field mission scanning electron microscope (ZEISS Gemini 300, Germany). A spectrometer (Thermo Scientific Nicolet iS20, USA) was used to obtain the Fourier transform infrared (FTIR) spectra of the programmable flexible actuators and liquid crystalline elastomer in the spectral range of 500–4000 cm−1. An electronic spectrometer (Thermo Scientific Nexsa, USA) was used to perform X-ray photoelectron spectroscopy (XPS) of the programmable flexible actuators. The Raman spectra of the programmable flexible actuators were measured using a Raman spectrometer (Renishaw inVia, British). Stretch-and-recovery tests of the microneedles were performed with a single-column material testing machine (HP-10K, HANDPI). Optical microscope images were acquired by an optical microscope (SJ-U500, SAGA). The thermal images were recorded by an infrared thermal imaging camera (HIKVISION, H10). Electromechanical measurements of the electrical resistance were taken with a true RMS multimeter (UT71D, UNI-T). The relative change in resistance is estimated as follows: Δ R/R0 = (R-R0)/R0 × 100%, where R0 is the original resistance and R is the real-time resistance after applying strain. Images of H&E-, IHC-, and MT-stained sections were captured with a biological inverted microscope (Olympus, BX63).
2.8. Wound treatment experiment
After a circular wound with a diameter of 1 cm was cut on the back, the mice were randomly divided into four groups. Different treatment strategies were applied to the wounds of the four mouse models, namely, the control group, blank intelligent bandage group, VEGF group, and VEGF + intelligent bandage group. The control group did not undergo any treatment procedures. For the other three groups, different strategies were used to treat the wounds on the back of each mouse: blank intelligent bandages without any medication (blank intelligent bandage group), ordinary bandages loaded with mupirocin and VEGF (VEGF group), and intelligent bandages loaded with mupirocin and VEGF (VEGF + intelligent bandage group). These intelligent bandages are replaced with new bandages every day. Digital images of the wound status were taken at predetermined daily intervals (at 0, 3, 6, 9, and 12 days). In addition, epidermal tissue samples were collected and immersed in a 10% paraformaldehyde solution. Subsequently, the tissue samples were dehydrated and embedded in paraffin to prepare 5 mm thick slices. Finally, H&E staining, Masson staining, and TNF staining were performed on these slices.α Immunohistochemical staining of IL-6 was performed.
2.9. Statistical analysis
All the statistical data are expressed as the means ± SDs, with n = 6 for each group. All the results were analysed by Origin 2023.
3. Results and discussion
3.1. Design and manufacturing of the PFA
In a typical experiment, a programmable flexible actuator is composed of an asymmetric polymeric liquid crystal elastomer containing liquid metal and spidroin, which can be printed on a substrate film with a microneedle structure design. As shown in a, we used laser engraving to create a microneedle mold on a polydimethylsiloxane (PDMS) mold and continuously printed multiple layers of liquid metal-spidroin-liquid crystal elastomer (LM-SP-LCE) composite material as functional structures on the mold. Then, polyurethane was used as the microneedle substrate material for casting. Finally, the mold was demolded, longitudinally stretched and photopolymerized on one side. Programmable actuation modes were manufactured in a convenient and digital way, with a short response time. Asymmetric flexible actuators with strong deformability can be remotely controlled through simple means. The combination of composite materials for PFA manufacturing was determined based on their functionality and manufacturability [Citation21]. Unlike traditional LCE actuators, PFA combines functional materials directly with elastic substrates. Due to the viscosity of LM and SP, LCE can effectively disperse them internally. The built-in actuation factor makes the deformation function more stable, and the dispersion of LM within the LCE can reduce the maximum temperature of the entire actuator during the deformation process while also increasing the sensing function to a certain extent. Moreover, an asymmetric structure was designed through manufacturing methods within the LCE, which allows the direction of deformation to be preset, and the programming of deformation is achieved through structural design. By printing, PFA can be arranged on a substrate according to certain requirements, causing the entire system to bend in a predetermined direction at a fixed position. The dispersed layout can reduce the heating of the actuation response. Furthermore, the addition of a microneedle structure enhances the friction force of the actuation system, and combined with the deformation programming mode, this can enable PFA to crawl in a directional manner.
Figure 2. Manufacturing and characterisation of PFA. (a) Schematic diagram of PFA 4D printing: laser engraving was performed on PDMS molds, and then a flexible actuator with an LM-SP-LCE composite material printing function structure and microneedle array was prepared on the mold; (b) Composite material function with printed patterns; i) Composite material functional structure-printed microfluidic channel patterns. Scale bar: 5 mm. ii) Spiral linear patterns printed on composite material functional strips. Scale bar: 5 mm. iii) Composite material function with printed chessboard patterns. Scale bar: 5 mm. (c) Physical structure of PFA. i) Digital images of the PFA entity structure. Scale bar: 5 mm. ii) Deformation actuation based on asymmetric structure and printed pattern programming. Scale bar: 5 mm. iii) Digital images of microneedle substrates. Scale bar: 1 mm. (d) Scanning electron microscopy (SEM) images of LM-SP-LCE composite materials. i) Surface image. Scale bar: 2 μm. ii) Cross-sectional images. Scale bar: 2 μm. iii) Energy-sensitive X-ray spectroscopy (EDS) analysis of gallium. Scale bar: 50 μm. iv) Energy-sensitive X-ray spectroscopy (EDS) analysis of indium. Scale bar: 50 μm. (e) Fourier transform infrared (FTIR) spectra of the LCE and LM-SP-LCE composite materials; (f) X-ray photoelectron spectroscopy (XPS) spectrum of the LM-SP-LCE composite material; (g) Raman spectra of the LCE and LM-SP-LCE composite materials; (h) The load capacity of PFA. i) Characterisation of the mechanical properties of PFA; ii) Deformation parameters of PFA during a temperature increase; iii) The load force generated by PFA during deformation process.
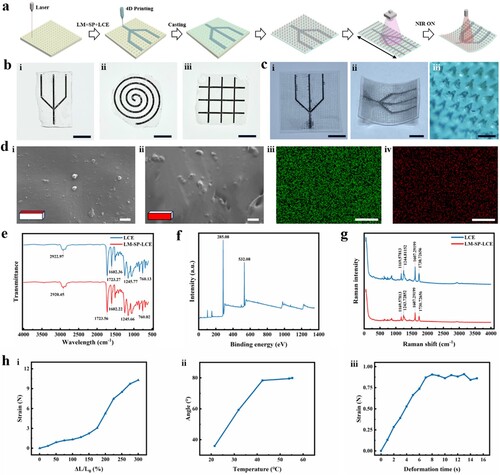
The design of PFAs is different from that of traditional flexible actuators. The programming deformation ability of PFA is based on material characteristics and asymmetric manufacturing, which improves the degree of freedom control and response ability. It does not require complex operational steps and can generate significant deformation in the preset direction through remote near-infrared lighting control. This selective actuation can adapt to a wider range of application scenarios. Similar to the implementation of the programming deformation capability, the integration of other functions of PFA composite materials also needs to be achieved based on manufacturing methods and material characteristics. As a fast and controllable manufacturing technology, additive manufacturing can play a crucial role in the construction of PFA entities because of the manufacturability of PFA composite materials. The uncured PFA composite material has good stability and viscoelasticity, and can be used as an ink material for additive manufacturing. Moreover, after printing, the material can maintain its shape and solidify, making it suitable for additive manufacturing. Based on the physical printability of PFA composite materials, various digital models with functional structures were designed. Construct printing patterns with asymmetric structures on a microneedle substrate to achieve programmable actuation modes, as shown in b. Moreover, the printing of functional strips can accurately display digital models, with the potential to carry complex designs. The printed solid structure is tightly integrated with the transparent substrate, which can drive the substrate to undergo a deformation response as a whole. Similar to the assembly method of transparent substrates, substrates with microneedle structures can also be connected to composite functional structures through 4D printing. To further enhance the functionality of PFA, the composite functional structures were combined with microneedle substrates through 4D printing (c). The microneedle substrate can provide a unique structure, and the design of this microstructure can effectively enhance the performance of PFA. The tightly arranged prismatic microneedles can not only increase the specific surface area of the contact between the composite functional structure and the substrate but also increase the friction force on the surface of the PFA. The microneedle substrate used for PFA is made of polyurethane, which can provide hardness and damage resistance for microneedles. In addition to manufacturing methods, the functionality of PFA is also influenced by the combination of composite materials. First, 1,4-bis-[4-(3-acyloxypropyloxy) benzoyloxy]-2-methylbenzene (RM257) was chosen as the liquid crystal monomer because the LCE based on this monomer is easy to prepare, exhibits excellent mechanical properties after the addition of SP, and has good compatibility with other functional materials. As an amorphous and flowable LM, LM can be added to LCEs. Not only can it improve the electrical properties of composite materials and increase the photothermal effect, but it can also maintain the original soft elasticity of the elastomer so that while the deformation response ability is enhanced, the limitations of deformation resistance and degrees of freedom are not increased, and the stress generated by deformation can be maximised [Citation22,Citation23]. At present, EGaIn has been widely used in the biomedical field and in the manufacturing of various instruments and equipment. LMs based on gallium have good biocompatibility in most applications. Compared to mercury, which is toxic, EGaIn is not volatile and has advantages as a nontoxic and intelligent material in contact with organisms [Citation24]. Many materials that can be used in contact with living organisms, such as metals, ceramics, and some polymers, cannot adapt to complex and ever-changing working environments. Compared with these solid fillers, liquid metals have excellent deformability and can adapt to various potential morphological changes while maintaining stability. This shape variability can also further combine with spider silk protein to improve the toughness of composite materials. The viscosity of EGaIn allows liquid metal to be mixed with LCE as a functional filler and used for further printing and mold casting [Citation25]. In addition, EGaIn not only has excellent photothermal performance but also has good thermal conductivity and heat dissipation ability. The temperature of PFA filled with EGaIn as the internal filler rapidly increased to a certain extent after near-infrared light irradiation and gradually decreased to the initial temperature after the near-infrared light was turned off. This allows the LCE matrix to immediately respond to temperature changes and produce deformation and can return to its initial state. The scanning electron microscopy (SEM) results showed that the surface of the PFA was smooth, and gallium and indium were evenly distributed inside. The size and distribution of LM particles could be well controlled by ultrasound (d). Due to the viscosity of the composite material, LM cannot be completely deposited, resulting in a relatively uniform distribution of large LM particles inside, and there are more large LM particles in the cross-section than on the surface. The Fourier transform infrared (FTIR) spectra of PFA and the LCEs are shown in e, indicating a high degree of similarity between the two materials. Next, X-ray photoelectron spectroscopy (XPS) was used to study PFA (f). The relative content of gallium and indium in PFA was relatively low, which can prevent photothermal effects leading to high PFA temperatures. In addition, the Raman spectra of PFA and the LCEs were measured as supplements to the FTIR spectra, and the study showed that the addition of LM and SP did not have a significant effect on the polymerisation of the LCEs (g). Furthermore, due to the addition of SP, the mechanical properties of PFA were optimised. SP is a special type of fibrin, and the internal methionine is tightly connected to the sericin protein [Citation26]. The structural characteristics determine that SP has the characteristics of high strength and toughness. Adding it to composite materials can significantly enhance the mechanical properties of the entire system, and this biomaterial can also provide biocompatibility. The addition of SP enhances the toughness of PFA. After testing, under the condition of 300 % tensile strain, the tensile force acting on PFA can reach about 10 N, as shown in h. Only when the PFA is subjected to a tensile strain exceeding the 300 % limit for a long period of time, will the overall system be completely damaged, causing the printed structure to fracture and detach from the substrate. This proves that PFA can easily withstand the deformation state generated by signal response and can resist significant damage. Due to structural reasons, multi-layer flexible actuators may experience separation between different layers due to stress changes during the deformation process of receiving stimulus signals, thereby affecting the working effect of the entire actuator. Unlike multi-layer flexible actuators, PFA is composed of a printed structure of composite materials and a micro needle functional layer based on polyurethane. Although asymmetric parts are constructed inside the composite material, they still belong to the same whole. In PFA, the printing structure provides actuation and sensing functions internally, reinforced by a microneedle substrate. By printing PFA on microneedle molds and directly pouring polyurethane for casting after initial curing, the composite material is integrated with the substrate, and even multiple large deformations cannot cause the printing structure to detach from the substrate. Toughness and stability can enable PFA to adapt to multiple cyclic deformations, demonstrating its excellent damage resistance and making sustainable deformation applications possible.
PFA undergoes deformation through internal photothermal effects, and the deformation angle is positively correlated with temperature. The printing speed often affects the deformation characteristics of materials, which requires studying the parameters of thermal mechanical behaviour [Citation27,Citation28]. Because the viscosity of LM and SP can be uniformly combined with that of LCE, PFA composite materials have internal stability. After testing at different speeds, it was found that the printing speed only affects the printing volume of PFA and has no significant effect on temperature-induced deformation under photothermal effects. The trend of the deformation angle of PFA with increasing temperature is shown in h. The temperature variation range of PFA is 20 to 60 °C, with a maximum angle of about 80 ° from the horizontal plane. The size of the included angle is limited by the PFA deformation mode. When the deformation angle reaches about 80 °, the internal temperature also reaches its maximum value. At this point, the PFA will curl towards the inner side of the bend, and the maximum deformation load can exceed the circular closed loop at both ends of the actuator bend and extend inward. Although flexible actuators based on smart materials have the advantages of simple response, facilitating functional integration, and convenient application. However, compared to its own weight, the small deformation response generated by stimulation usually cannot provide sufficient force efficiency. In order to improve work efficiency, it is necessary to enhance the deformation state of the actuator. The differentiated programming design of actuators can significantly enhance their deformation ability, thereby optimising the efficiency of force generation during the deformation process. In order to make the experimental results clearer and more accurate, the PFA film was cut into dimensions of 3 cm × 0.5 cm × 0.1 cm, and stimulus signals were provided to test the load-bearing capacity of PFA during deformation. Place PFA on the platform of the universal testing machine, and deform the actuator by near-infrared light irradiation. Test the load-bearing capacity generated during the deformation process using a force sensor. The load capacity change of PFA during the deformation process is shown in h. The temperature of PFA will continue to increase with irradiation time, and when it reaches the highest temperature, it will stop rising. At this time, the generated force will also tend to stabilise. The force that PFA can generate varies under different deformation conditions. PFA with a size of 3 cm × 0.5 cm × 0.1 cm can generate a load force of about 0.9 N when reaching the maximum temperature, which is the maximum deformation angle.
Based on material characteristics and asymmetric manufacturing methods, combined with additive manufacturing technology, PFA can be manufactured with preset actuation modes, strong response capabilities, and simple and unconstrained control methods. Moreover, the manufacturing of PFAs has the advantages of simplicity, speed, and high-precision digital design. It is not limited to fixed proportions and structures and can be designed and manufactured according to specific application scenarios. Compared to traditional rigid robots, the resource consumption of soft robot systems is minimal, and the manufacturing cost is mainly focused on material related aspects. In the manufacturing of PFA, the required materials mainly include EGaIn, SP, LCE, and PU. Manufacturing cost accounting was conducted on a single actuator sample with dimensions of 3 cm × 1 cm × 0.1 cm for the required materials, as shown in . Although a combination of composite materials is used, the usage of each material is very small, and the manufacturing cost of PFA is very cheap. In the manufacturing process of PFA, the first step is to cure and shape the composite material. Due to the ability to cycle multiple times and produce in large quantities, mold casting is often applied in the customisation of composite material structures. However, due to the need for personalised structural design based on application scenarios for programming the actuation mode of PFA, it requires a significant amount of cost to customise the mold, which is not conducive to sustainable soft robot applications based on PFA. Sustainable applications require stable functionality, fast and low-cost structural shaping, which requires a convenient manufacturing method that can adapt to diverse designs. 4D printing provides manufacturing conditions for the formation of composite materials. Through 4D printing, the functional structure of composite materials can be quickly constructed, stable PFA systems can be manufactured, and deformation and recovery can be programmed multiple times to achieve sustainable applications in personalised application scenarios. Integrating additive manufacturing technology into soft robot design helps to customise the functionality of the entire system by selectively placing functional materials in positions that traditional manufacturing methods cannot reach [Citation29]. Additive manufacturing technology, due to its scalability and designability, is often used to build equipment based on sustainable biomaterial, and this technology has significant advantages in the field of composite material manufacturing [Citation30,Citation31]. In addition, to achieve sustainable applications, composite materials need to be environmentally friendly and biocompatible. The composite materials used for PFA manufacturing can come into contact with living organisms, and the addition of biomaterial SP further enhances the biocompatibility of the composite materials. The biosafety and stability of PFA based on material design enable PFA to adapt to the needs of sustainable applications. In order to improve the sustainable application capability of PFA, it is necessary to further enhance the biocompatibility and functional stability of composite materials.
Table 1. The cost of materials for fabricating one actuator.
3.2. Actuation performance of the PFA
LCEs can shrink in response to temperature changes through microstructural rearrangement of the mesogen transition from anisotropic to isotropic states, and this deformation is reversible. However, the single simple actuation mode and the uncertainty of actuation control limit the application of LCEs in the field of flexible actuators [Citation32]. As a potted plant, Ficus benjamina 'Barok' has attracted widespread interest among researchers due to its unique leaf shape. As shown in a, due to the different internal structures on both sides of the leaves, the leaves of these plants curl continuously during growth. This difference can be applied to the design of deformation modes for flexible actuators, thus overcoming the difficulties in the application of LCEs in the field of flexible actuators. Based on the biological insight obtained from the leaf structure of Ficus benjamina 'Barok', through differentiated design and manufacturing, not only can the deformation mode of the actuator be programmed, but differentiation can also be enhanced to improve the deformation ability. In the design of PFA, an asymmetric mask structure was artificially constructed through the single-sided manufacturing method of composite material photopolymerization, and this difference was further fixed by the stretching of PFA during single-sided photopolymerization treatment.
Figure 3. Performance testing of PFA actuation. (a) Biomimetic image of PFA. i) The source of biological inspiration comes from optical images of Ficus benjamina 'Barok'; ii) The biomimetic curling deformation mode of PFA. Scale bar: 5 mm. (b) The influence of printing structure layout on driving deformation. i) Deformation of vertical printing layout. Scale bar: 5 mm. ii) Deformation of horizontal printing layout. Scale bar: 5 mm. (c) Directional bending mechanism for single-sided photopolymerization manufacturing of flexible actuators. i) Schematic diagram of the internal structure of single-sided photopolymerization of PFA; ii) Thin films made from LM-SP-LCE composite materials. Scale bar: 5 mm. (d) Actuation response characteristics of the PFA ultraviolet polymerisation side. i) Conceptual diagram of PFA UV polymerisation side deformation under near-infrared illumination; ii) Optical images of the PFA ultraviolet polymerisation side subjected to near-infrared light irradiation deformation. Scale bar: 5 mm. iii) Finite element simulation of the relative displacement of the PFA ultraviolet polymerisation side after short-term near-infrared light irradiation; (e) Actuation response characteristics of the PFA non-ultraviolet photopolymerization side; i) Conceptual diagram of the deformation of the PFA non-ultraviolet polymerisation side under near-infrared illumination; ii) Optical images of the PFA non-ultraviolet polymerisation side subjected to near-infrared illumination deformation. Scale bar: 5 mm. iii) Finite element simulation of relative displacement on the non-ultraviolet polymerisation side of PFA after short-term near-infrared light irradiation; (f) Infrared images of changes in PFA temperature. i) Infrared images of temperature changes in PFA under near-infrared illumination; ii) Infrared images of temperature changes in LCEs after exposure to near-infrared light; (g) Line graph of temperature over time after exposure to near-infrared light. i) Line graph of the temperature variation in PFA over time after exposure to near-infrared light; ii) Line graph of the temperature variation in LCEs over time after exposure to near-infrared light; (h) The bending angle of PFA deformation. i) Schematic diagram of the PFA deformation and bending angle; ii) Line chart of the PFA bending angle over time.
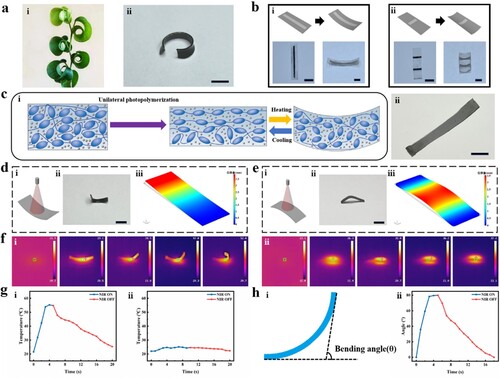
Based on the internal asymmetric structural design, after being irradiated by near-infrared light, the PFA will bends toward the side that is subjected to light aggregation during the manufacturing process. This programmable deformation method guided by asymmetric structural design with preset directions is inspired by Ficus benjamina 'Barok', whose leaves continuously curl inward during growth due to the influence of internal asymmetric structures. In addition to the deformation modes influenced by asymmetric structures, the shape of deformation is also influenced by this type of blade. As shown in a, for PFA, as the near-infrared light irradiation time increased, the temperature continued to increase until reaching its highest point. Under the influence of temperature, the film bends and gradually curls inward, and this trend further strengthens and is maintained with increasing near-infrared light irradiation time. In addition to achieving programmed deformation through single-sided light aggregation to construct internal differences, PFA can also programme the joint positions that generate deformation through the design of printing structures, thus adapting to complex application scenarios. Based on the flexible design and diverse programming of actuation modes, when PFA is combined with the substrate film, the deformation mode can be controlled by arranging composite materials with asymmetric internal structures at different positions, allowing the entire system to bend in diversity at different positions and in different directions. The differences in the layout structure of composite materials can cause overall deformation from different directions, as shown in b. Drawing digital models can accurately design the layout and structure of composite materials on the substrate, and further use additive manufacturing technology to quickly construct entities. Through digitalisation and intelligent manufacturing, systematic customisation of PFA can be achieved. In addition, due to the increase in temperature of the composite material during PFA deformation, this may pose a threat to the substrate material. Dispersing functional units based on composite materials through printing can reduce the negative impact of temperature. Moreover, the physical printing of different digital models has verified that the composite materials used in PFA have excellent plasticity and can be used to construct specific structures according to application requirements. This demonstrates the potential of composite materials for rapid prototyping and sustainable manufacturing, which can be further developed and applied. To highlight the actuation performance of composite materials and optimise the observation effect of the functional structure of composite materials, thin film structure PFA was used in some of the experiments involved in the study. A simple mixture of SP, LM, and LCE was used to directly produce a thin film structure of PFA. The solid structure of the PFA film and the asymmetric internal structure after single-sided photopolymerization are shown in c. During the manufacturing process of PFA, due to the dispersion of LM nanoparticles, the mask is constructed to reduce the transparency of LCE. During photopolymerization, ultraviolet light cannot fully penetrate the PFA film, resulting in different microstructures of the mesogens on both sides of the film. This difference increases with the thickness of the composite material. To avoid differential construction caused by the alignment of the mesoporous structure due to the shear stress of the printing nozzle, multilayer PFA composite materials were continuously printed at the same position. Within the PFA, a local orientation is programmed, and the closer the orientation is to the photopolymerization side, the greater the anisotropy of the mesogen microstructure. In contrast, the anisotropy of the mesogen microstructure on the back side near the photopolymerization side is weaker. Therefore, a temperature gradient with orientation is constructed, which results in differences in the response of the PFA to temperature changes, thus achieving selective actuation. A temperature change is achieved by the photothermal effect of the internal LM, and near-infrared irradiation can increase the temperature of the LM. This internal temperature change allows the PFA to be remotely controlled without the need for cables. Based on the internal asymmetric structure, when responding to photothermal effects, the PFA film bends significantly toward only the photopolymerization side, and this deformation mode is not affected by the direction of near-infrared illumination. As shown in d, near-infrared light illuminates the flexible actuator from the photopolymerization side, and one end of the flexible actuator can be flipped upward. The deformation effect of near-infrared light illuminating the flexible actuator from the nonphotopolymerization side is shown in e. The flexible actuator bends inward, allowing the entire actuator to be supported. The internal asymmetric structure constructed during the manufacturing process can be programmed with specific actuation modes, causing PFA to deform only in a specific direction towards the side subjected to photopolymerization. For this deformation mode, different deformations can be observed by using near-infrared light from different directions. Finite element simulations were conducted on the relative displacement trends of two different deformation states, simplifying PFA to an internally uniform distribution and using a standard finer and denser triangular mesh. For two different deformation states, when PFA is bent upwards, the short section at one end is selected as the fixed boundary and relative displacement reference. When PFA is bent downwards, select the short cross-section at both ends as the fixed boundary and relative displacement reference. Resolve the thermal strain of PFA as ϵ = α ΔT. ϵ represents thermal strain, α represents the coefficient of thermal expansion, ΔT is the amount of temperature change. To demonstrate the relative displacement trend more clearly, the ΔT is fixed at 10 °C. Furthermore, obtaining an analysis of thermal stress σ = ϵ E. E is the Young's modulus. Applying the analysed thermal stress to a PFA model with dimensions of 3 cm × 0.5 cm × 0.1 cm can obtain the displacement boundary affected by temperature. The displacement boundary of PFA bending upwards is 0 to 3.56 mm. Due to the downward bending that requires bearing its own weight, the displacement boundary is slightly smaller, ranging from 0 to 3.5 mm. Subsequently, the photothermal effect of the LM in PFA was evaluated, as shown in f. The temperature of the flexible actuator rapidly increased after exposure to near-infrared light and stabilised after a period of time. Unlike PFA, LCEs without LM exhibit almost no temperature change after irradiation with near-infrared light. This indicates that LM has photothermal effects. Within one deformation cycle after being exposed to near-infrared light, as shown in g, the temperature of the PFA first rapidly increased. The sudden change in temperature gives the PFA the ability to quickly respond and produce deformation. When the temperature reaches a certain level, it stabilises and no longer increases. Moreover, the deformation amplitude of the PFA reaches its maximum. After turning off the near-infrared light, the temperature gradually decreased, and at this point, the deformation of the PFA began to slowly recover. LCEs without added LM cannot generate photothermal effects. After irradiation by near-infrared light, the temperature fluctuates between 20 and 25 °C and cannot reach the transition temperature of LCEs, which is not enough to cause them to shrink. The response of PFA to stimulus signals and deformation is a continuous process, and the programmed actuation mode gradually bends towards the preset direction. In order to determine the degree of freedom of PFA deformation, the PFA film is placed on a horizontal plane, and deformation is generated by near-infrared light irradiation stimulation. The angle of the tangent extending from the farthest distance between the two ends of the PFA deformation distance is taken as the deformation angle, as shown in h. The magnitude of the angle increased with increasing PFA deformation amplitude. Within a deformation cycle, the deformation angle is similar in magnitude to the temperature change, and the deformation angle can reach 80 °. The programmable deformation capability of the designed PFA is achieved by material properties and asymmetric manufacturing. This simple process-based mode not only allows the flexible actuator to bend in the preset direction, achieving remote selective actuation but also enhances the deformation response ability of the flexible actuator, changing the single deformation mode of the LCE and providing a simplified working scheme for the controllable high-degree-of-freedom deformation of the flexible actuator.
3.3. Design of PFA-based directional crawling soft robotics and grippers
In nature, although the measuring worm is a creature that relies on multiple short distance displacements for crawling, it can flexibly adapt to various complex terrains through the bending and stretching of its body, thus moving on uneven or vertical surfaces (a). Therefore, the geometrid has become an important source of biological inspiration for building flexible soft robotics [Citation33]. However, due to the high degree of freedom of motion, directional motion control of a geometrid, such as that used in soft robotics, requires complex steps. To simplify the motion programming problem from a high-degree-of-freedom perspective, based on the characteristics of the PFA instant response and directional deformation, flexible actuator films, microneedle substrates, and polyimide films were assembled to design geometrically inspired and directional crawling soft robotics, as shown in b. The motion direction was controlled through a simple asymmetric structural design. The physical structure of the assembled soft robotics is shown in c. PFA serves as the main component of soft robotics; the microneedle base is assembled at one end on the inner side of the PFA bend, and the polyimide film is assembled at the other end on the outer side of the PFA bend. PFA serves as an interlayer separating the polyimide film and the microneedle base, and the polyimide film and microneedle base are located at two ends on different sides of the PFA. Based on this asymmetric structure, soft robotics are placed on a horizontal desktop, with one side of the microneedle base in contact with the horizontal desktop. Soft robotics can continuously crawl toward one end of a polyimide film. During the deformation process of soft robotics, due to the very low thermal expansion coefficient of the polyimide film, the thermal expansion coefficient generally ranges from 2 × 10−5/°C to 3 × 10−5/°C. However, at the liquid crystal phase transition temperature (65–80 °C), the thermal shrinkage deformation rate of the LCE film exceeds 10%, and the difference in the temperature response between the polyimide film and PFA can significantly increase the degree of photothermal deformation bending. The degree of bending of the overlapping part of the polyimide film and PFA is greater than that of the single PFA part. During deformation, the bending of the soft machine will face the end with a polyimide film, which can provide a strain force biased toward one end. After programming and design, the actuation mode of PFA is a reciprocating bending towards the preset direction. In this mode, homogeneous structures are difficult to achieve selective motion, and further improvement and optimisation of the actuation state are needed. At present, the common method is to improve simple bending deformation into controllable directional displacement motion by attaching a fixed direction of friction force under specific conditions [Citation34,Citation35]. To further optimise the adaptability of soft robots to complex environments and enable PFA based soft robot systems to achieve directional movement in various environments, the deformation direction of the actuator is first determined based on programming design. A micro needle structure is integrated at one end on the inner side of the deformation to construct a differentiated friction force distribution during the deformation process. This causes the entire system to generate friction force in the direction of movement during the deformation recovery process. Then, a polyimide film is integrated on the outer side of the other end to move the deformation position of the actuator forward and enhance the bending state, preventing the two opposing frictional forces generated during the initial deformation and deformation recovery from cancelling each other out, reducing the negative impact of frictional forces, and constructing a unidirectional frictional force to assist in achieving directional motion. The microneedle structure located in contact with the horizontal desktop at the rear can increase the frictional force of the soft machine during deformation recovery, effectively preventing the reverse sliding of the soft machine during movement and improving the displacement efficiency of forward crawling. The main force characteristics of the soft robotics during crawling are shown in d. Through asymmetric manufacturing and preprogrammed bending of flexible actuators, soft robotics deform in a predetermined actuation mode and undergo directional displacement during repeated deformation and recovery cycles. By programming the actuation mode, directional crawling can be achieved via simple steps. As in the case of crawling a geometrid, the motion cycle of soft robotics includes a period from significant bending and contraction to recovery and extension, as shown in e. Through continuous contraction and extension, soft robotics can achieve directional crawling in repeated motion cycles. The motion of the soft machine is shown in f. After multiple deformations, the soft robotics advanced a certain distance from their original position toward the specified direction, as shown in g. The directionality and displacement of this motion trend are obvious. Soft robotics can complete their preset motion cycle and achieve directional displacement while maintaining stable crawling.
Figure 4. Actuation application of the PFA. (a) Digital image of a measuring worm; (b) Conceptual diagram of soft robotics assembled based on PFA; (c) The structure of a soft robotics assembled based on PFA. i) Digital image of the top of the soft robotics. Scale bar: 5 mm. ii) Digital image of the bottom of the soft robotics. Scale bar: 5 mm. (d) Analysis of the main force characteristics of soft robotics; (e) The crawling cycle of soft robotics; (f) Digital images of the crawling process of soft robotics. Scale bar: 5 mm. (g) Crawling displacement of soft robotics. Scale bar: 5 mm. (h) A schematic diagram of the grasping process and details of a soft robotics gripper assembled based on the PFA. Scale bar: 2 cm.
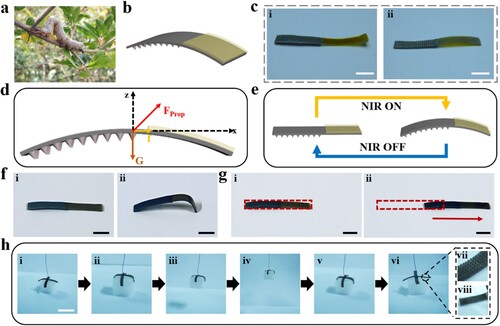
Based on the programming deformation characteristics of flexible actuators, we designed a soft robotics gripper composed of two flexible actuator films. A microstructure was added inside the gripper to increase the friction between the gripper and the object being grasped, achieving more reliable grasping. As shown in h, the soft robotics gripper can grasp objects on a desktop computer. After coming into contact with the object, the gripper can quickly deform inward, tightly wrap the grasped object, and pick up the object to a certain height. During this process, the object is always tightly controlled by the gripper. Finally, the gripper placed the object on the desktop under control and released it, achieving stable grasping and a complete workflow. Compared with flexible actuators with complex deformation control methods, our designed PFA actuation mode provides a new approach for simplifying the degree of freedom motion control and intelligent auxiliary work applications. LCE actuators can respond to changes in external temperature and generate deformation through overall contraction [Citation36]. To further control the deformation mode of the LCE actuator, the actuator was optimised and designed. The built-in actuation factor can quickly respond to near-infrared light irradiation, causing significant deformation of the PFA. Based on the unique internal asymmetric structure and printing layout design, PFA can achieve a directional programming deformation mode, bending in a predetermined direction at a fixed position [Citation37,Citation38]. Due to the flexible deformation mode, the application of flexible actuators in directional control is achieved through external conditions support. Based on the needs of lightweight and integration, targeted structural design was carried out for PFA to support its application in controllable systems. By improving the preset deformation mode and incorporating micro needle structure design, PFA can not only achieve tight grip, but also serve as a directional motion system.
3.4. The sensing performance and intelligent application of the PFA
The role of human skin in perceiving motion changes and transmitting perception signals is irreplaceable [Citation39]. Similarly, the perception and feedback of actuator deformation also play crucial roles in intelligent applications. Based on the functionality of the composite materials, PFA can not only respond to stimuli to achieve deformation actuation but also perceive changes based on the deformation state. However, due to the electrostatic repulsion of natural oxides on LM particles, the resistance of PFA composite films is usually high, resulting in unstable sensing performance [Citation40]. By printing MXene-based circuits on the surface of PFA, this instability can be significantly improved, enabling wearable motion monitoring or self-sensing of deformation [Citation41]. MXene, a conductive inorganic material with a two-dimensional multilayer nanosheet structure, has excellent conductivity and stability, especially for TiC2Tx-MXene. Printing and drying TiC2Tx-MXene on PFA can enhance the sensing performance, and the perception of deformation is represented by relative resistance changes. Based on the combined effect of internal LM functional fillers and surface MXene coatings, PFA can reflect the deformation state in real time through changes in its own resistance signal. The sensing performance of PFA comes from the degree of change in the internal resistance signal. Due to the uncertainty of the application environment, there may be errors in the sensing data. In order to accurately define the sensing performance of PFA, the PFA is first connected to a resistance measurement device, and stable initial resistance data is tested in an invisibly variable horizontal state, recorded as R0. Then install the PFA on a fixed angle bending device and apply deformation signals under stable bending conditions of 30, 60, and 90 °. Measure the changes in output resistance data multiple times and record them as R. Subtract the initial resistance in the intangible deformation state from the resistance in the deformation state to obtain the change in resistance, and record it as ΔR. The change in resistance directly reflects the deformation state of PFA. The larger the value of resistance change, the greater the deformation angle of PFA, and there is a positive correlation between the two parameters. The resistance data of PFA in different states needs to be measured multiple times to determine the average value of the data and reduce the error of the sensing function. The resistance data may vary between different PFAs due to differences in the manufacturing process. To ensure the accuracy of the sensing function, it is necessary to measure the resistance data of multiple PFAs separately. Compared with the average data, PFA with significant errors can adjust its sensing performance by adding or scraping off some surface conductive coatings, thereby achieving sensing calibration under unified standards and ensuring that the sensing signal data accurately reflects the deformation state of PFA.
Due to the incomplete connection of the internal liquid metal after dispersion, the sensing function of PFA is not stable, and the sensing signal may suddenly disappear during the deformation process, making it difficult to detect small deformations. By adding MXene circuits to the surface of PFA to optimise the overall sensing performance, stable sensing data can be obtained by combining internal functional fillers with external coatings. By assembling MXene on the surface, the continuous deformation and small deformation of PFA can be stably monitored. The external MXene circuit does not exist as an independent sensing device. The purpose of the coating is to further enhance the sensing performance of PFA and increase the sensing sensitivity. In addition, a single MXene circuit cannot monitor itself, and when combined with PFA, it can reflect the deformation status of the entire system in real time through changes in resistance signals. The high sensitivity to deformation perception endows PFA with the ability to monitor human motion in real time and provide feedback on deformation status, enabling PFA to be further applied as a wearable device. For example, the relative resistance change in PFA can be used to monitor the movement status of the wound area as a wearable device for wound treatment. Due to the possibility of tearing the wound and causing secondary injury during intense exercise, which increases recovery time, it is possible to avoid excessive exercise or evaluate injury conditions based on the sensing signals of wearable devices. To study the sensing performance of PFA, a composite film was directly adhered to the fingers, wrists, and elbow joints, and the change in resistance of PFA was recorded in real time, as shown in b to d. The change in resistance signal reflects the amplitude of motion, and the larger the amplitude of motion, the greater the rate of signal change. The high-sensitivity sensing characteristics of the PFA composite film can also be demonstrated through deformation feedback. When PFA undergoes deformation under photothermal stimulation, the actuator bends inward, causing the external MXene coating to extend and the resistance signal to change, providing feedback on the deformation state, as shown in e. Moreover, due to the high contact resistance of double-layer PFA during deformation contact, the contact resistance decreases sharply after deformation recovery, and the change in the microstructure can significantly increase the specific surface area of PFA, increasing the sensitivity of the contact between the two layers of PFA and the microstructure to resistance changes and enhancing the sensing signal. As shown in f, at the same deformation angle, the signal response of the double-layer microstructure of PFA is more pronounced than that of the single-layer PFA. However, unstable functional integration solutions may constrain the application of the entire system. Although both actuation and sensing functions are integrated, the efficiency of various PFA functions has not been weakened due to this integration. This also confirms the potential of PFA for integration, high efficiency, and miniaturisation. The combined effect of internal LM functional filler and surface MXene coating enables PFA to produce significant directional deformation while also possessing excellent sensing ability. The sensitivity of this sensing performance is reflected by response time. Record the time when PFA begins to deform, and then record the time it takes for the resistance signal to reach a stable value of 70 % in the deformation state, in order to obtain the response time for PFA deformation perception. Based on existing sensing data, the response time of PFA was observed to be between 700 to 900 ms. Further test results indicate that after 200 cycles of significant deformation and recovery, PFA can still maintain stable sensing function, and there is no significant difference in resistance signal changes. This proves that PFA has excellent fatigue resistance and sustainable application potential. The sensing signal changes of PFA during the cycle are shown in g. The sensing experiment has verified the high sensitivity of PFA with the potential to monitor human motion and self-induced deformation.
Figure 5. Wearable sensing application of PFA. (a) Schematic diagram of the wearable sensing application of PFA; (b) Resistance changes in PFA during finger bending at 30°, 60°, and 90°; (c) Resistance change in PFA during wrist bending deformation; (d) Resistance change in PFA during elbow bending deformation; (e) Resistance changes caused by PFA-induced deformation; (f) Sensing signal of PFA with/without microneedle structure design for finger bending 90° deformation; (g) Changes in resistance signal of PFA during 200 cycles of significant deformation and recovery.
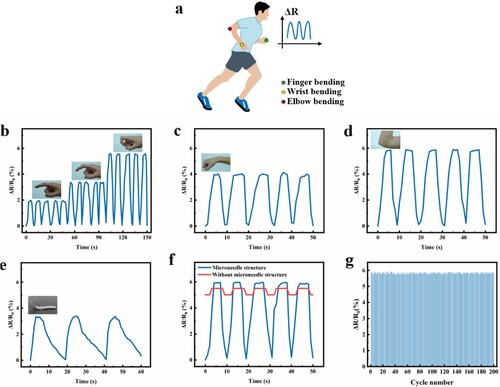
Based on its high-sensitivity sensing ability, PFA can serve as a wearable device for collecting strain signals through deformation. It can not only monitor and provide real-time feedback on motion status but also serve as a human–computer interaction interface to connect intelligent devices, thereby analysing and identifying motion postures and understanding user intentions. Unlike the exchange of information between individuals through language, body movements can convey abstract or metaphorical information [Citation42]. Based on the simulation of gesture changes, certain meanings or words can be defined, and information exchange can be completed through action changes [Citation43]. To convert human motion signals into information that can be used for human–computer interaction, a wearable gesture recognition system was designed to improve the interactivity of signals. The workflow of the system is shown in a. The wearable gesture recognition system includes intelligent sensing gloves, electrical signal monitoring devices, and a computer for recognition. As shown in b, the main components of the intelligent sensing glove are assembled based on a PFA located on five different fingers, which can fit the finger joints in both the extended and bent states. A monitoring device is used to convert the finger movement status collected by the intelligent sensing glove into electrical signals, and the computer is subsequently connected to transmit the signals for recognition. In this system, PFA serves as a sensing device that can monitor the bending activity of different fingers separately. After the user forms sign language-based gestures, the sensing system bends as the fingers bend. Moreover, the electrical signal monitoring device receives real-time resistance changes from intelligent sensing gloves, and the resistance signal is transmitted to the computer system through connected cables. A computer is used to output letters corresponding to gestures based on the changing trend of signals from different fingers. To improve the working accuracy of the gesture recognition system, machine learning was used to train the system. A simplified schematic diagram is shown in c, which shows the construction of a neural network that includes input layers, multiple hidden layers, and output layers. This method uses a mechanism completely different from traditional information processing techniques and can overcome the shortcomings of traditional artificial intelligence in processing complex information [Citation44]. Different combinations of gesture signals are transmitted and recognised, and motion signals are converted and output. When users complete different gestures, they can clearly observe the signal changes in the corresponding finger combinations, as shown in d. After multiple training sessions, the wearable gesture recognition system successfully recognised various gestures, and the recognition results are shown in e. The design of a gesture recognition system involves the conversion of human motion signals into human–computer interaction information and further expands the application of the PFA in the field of wearable devices. Based on the advantages of safety, compliance, and functional integration, flexible robot systems have been widely applied in the field of human–computer interaction. Flexible robot systems have the potential as human-machine interaction interfaces, and through intelligent and personalised settings, they can adapt to different work needs. Due to the integration of sensing and actuation functions in flexible robot systems, human-machine interaction can transmit signals for intelligent control, converting perception signals into physical motion. Furthermore, the addition of artificial intelligence and machine learning can further enhance the intelligence level of interactive systems. Flexible modules based on artificial intelligence convert physical interactions into specific signals through material properties, which are transmitted between humans and machines to achieve secure information exchange [Citation45]. In addition to functionality, artificial intelligence and machine learning can also improve and optimise the manufacturing process of soft robot systems. One of the promising research directions in the future is to continuously simulate and optimise the application of soft robot systems in work scenarios through machine learning, thereby improving structural design and functionality, using printing technology for intelligent manufacturing, and constructing solid structures [Citation46,Citation47].
Figure 6. PFA-based machine learning-optimised gesture recognition system. (a) Schematic diagram of the gesture recognition system based on the PFA; (b) Physical optical images of intelligent sensing gloves. Scale bar: 3 cm. (c) Neural network processing flowchart for sensing signals; (d) Optical images of 9 gestures and their corresponding five-finger signal curves; (e) Confusion matrix for gesture recognition results.
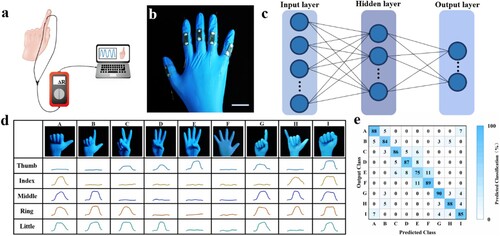
3.5. Intelligent bandages based on PFA for wound treatment
To explore the potential application of PFA in the field of wearable devices, we designed an intelligent bandage for biomedical applications based on the directional bending characteristics of PFA, as shown in a. This intelligent bandage consists of a flexible actuator layer, a divider layer, and a drug therapy layer. Due to the asymmetric structural design, the PFA bends to one side. Intelligent bandages based on the PFA design can tightly wrap the wound through this deformation method, effectively reducing the area of wound cracking. Due to the possibility of wounds appearing in different body parts, smart bandages for wounds in different locations require the targeted design of coverage modes. The arrangement and layout of the PFA affect the deformation direction at the base of the bandage. By adjusting the direction of the PFA, it can adapt to the bandage coverage requirements at various positions. The arrangement of PFA on the bandage base can be achieved by printing patterns designed according to work requirements, which is a very convenient manufacturing method. By using deformation wrapping, the drugs carried on the bandage can be fixed in contact with the wound, improving drug delivery efficiency and accelerating wound recovery. In addition, the design of microneedle structures on smart bandages can increase friction and prevent the bandage from falling off. To evaluate the practical effect of intelligent bandages in wound treatment and healing, we used mice with a circular incision on the back with a diameter of 1 cm as the epidermal wound model. In the experiment, all the mice were randomly divided into four groups and treated with different strategies. First, an experimental group without any treatment measures was used as the control group. The remaining three groups were treated with intelligent bandages without drugs, ordinary bandages with vascular endothelial growth factor (VEGF) drugs, or intelligent bandages with VEGF drugs, the intelligent bandage group, the VEGF group, and the VEGF + intelligent bandage group, respectively. Images of the wound healing process in each group were taken on days 0, 3, 6, 9, and 12, and optical images are shown in b. Beginning on the 6th day of treatment, the wound recovery rates of the VEGF group and the VEGF + intelligent bandage group were significantly greater than those of the control group and the blank intelligent bandage group. During the treatment process, the wound recovery rate in the VEGF + intelligent bandage group was the fastest, while the wound recovery rate in the VEGF group was slightly faster than that in the blank intelligent bandage group. The wound recovery rate of the control group was the slowest throughout the entire process. These findings confirmed that the synergistic effect of intelligent bandages and VEGF drugs significantly enhances the recovery efficiency of wounds, which is beneficial for wound treatment. The deformation of PFA can fully wrap around the wound, reduce the area of cracking, and apply intelligent bandages loaded with drugs to the wound area. The wrapping effect of the deformation can fully contact the wound, improving the efficiency of drug delivery. Through the deformation and collaborative drug delivery of intelligent bandages, the wounds in the VEGF + intelligent bandage group almost fully recovered on the 12th day, significantly faster than those in the other three groups, indicating that intelligent bandages loaded with drugs can be used for wound treatment and can accelerate wound healing. In addition, the recovery rate of mice following circular incisions on the back was quantified and analysed, as shown in c.
Figure 7. Treatment of epidermal incisions with intelligent bandages based on PFA. a) Schematic diagram of the structure of intelligent bandages and their attachment to mice. b) 12-day optical images and 12-day morphological changes in wounds in different groups (control, intelligent bandage, VEGF, VEGF + intelligent bandage). Scale bar: 5 mm. c) Recovery rate of the circular incision (%) (mean ± standard deviation; n = 6); d) H&E staining of tissue slices around the wound; e) Masson staining of tissue slices around the wound; f) TNF-α immunohistochemical staining; g) IL-6 immunohistochemical staining.
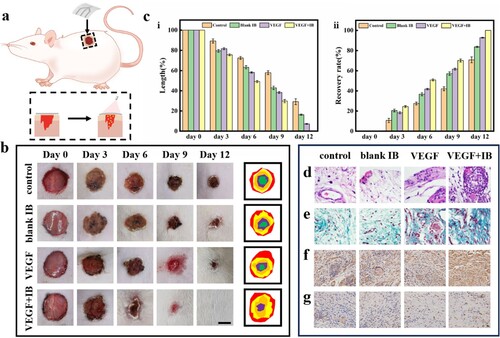
Furthermore, different staining methods were used to treat the epidermal wound model, and the recovery status was evaluated based on histological analysis of the wound [Citation48]. The early recovery of wounds often accompanies the growth of granulation tissue [Citation49]. As one of the most widely used staining strategies, hematoxylin and eosin (H&E) staining can be used to evaluate the growth status of granulation tissue. As shown in d, the granulation tissue growth in the VEGF + intelligent bandage group and VEGF group was relatively dense, and the granulation tissue growth in the VEGF + intelligent bandage group was denser than that in the VEGF group. The granulation tissue growth in the control group and blank intelligent bandage group was relatively sparse, which is consistent with the recovery status of the wound model. The deformation of the intelligent bandage increased the efficiency of drug treatment for wounds, creating a stable recovery environment for the wound. As the wound recovers, the blood and fibrinogen oozing from the wound further coagulate, and fibrosis is a part of the normal wound healing process. The growth of fibrous tissue can be visualised by Masson staining. According to the Masson staining results shown in e, the VEGF + intelligent bandage group had the highest degree of fibrinogen coagulation in the wound area, indicating a significant improvement in wound recovery. Compared with those in the VEGF + intelligent bandage group, the patients in the VEGF group not wearing intelligent bandages to promote drug delivery had a lower degree of fibrinogen coagulation. Due to the lack of effective drug treatment, the fibrinogen coagulation status of the control group and the blank intelligent bandage group was poor, and there was a significant difference in wound recovery compared to that of the VEGF + intelligent bandage group. In addition to the degree of tissue growth and fibrinogen coagulation, the wound recovery status can also be evaluated by the degree of wound infection. The levels of inflammatory factors, including interleukin-6 (IL-6) and tumour necrosis factor-α (TNF-α), are important indicators of the degree of wound infection. IL-6 and TNF are two typical cytokines secreted by immune cells to eliminate wound infections-α, and the secretion of these cytokines decreases as the degree of wound infection decreases. By analysing IL-6 and TNF-α, we observed and evaluated the degree of wound recovery, as shown in f and g. For the VEGF + intelligent bandage group, the expression of the intelligent bandage was significantly lower than that of the other groups, confirming that the intelligent bandage can effectively accelerate wound healing by reducing wound cracking and improving drug release efficiency. Therefore, intelligent bandages loaded with drugs can effectively accelerate the recovery speed of wounds and have potential applications in the field of wound treatment.
4. Conclusion
We have developed a new type of programmable flexible actuator (PFA), which is a differentiated manufacturing functional structure that can be 4D printed on a microneedle substrate for soft robotics directional movement and intelligent wearable devices. Through 4D printing, the composite material is effectively combined with the microneedle substrate, and the functionality of PFA is significantly enhanced. Due to the photothermal effect, the mesogen structure is rapidly rearranged, and the microneedle substrate is immediately driven to produce large-scale deformation. Moreover, the asymmetric mesogen structure causes PFA programming deformation, further increasing the deformation amplitude. Due to these obvious advantages, the PFA can serve as a motion support device for the directional motion of soft robotics, effectively improving the displacement capability. Research has shown that the designed PFA can quickly and easily achieve selective actuation, which can improve the controllability of soft machine deformation modes. In addition, PFA can integrate sensing functions, reflect morphological changes through resistance signals, and be further assembled into wearable devices for gesture recognition and wound management. This study is expected to provide new ideas for the control optimisation of the selective actuation of flexible actuators, demonstrating enormous potential in intelligent applications.
Credit authorship contribution statement
Bingyi Wang: Conceptualization, Writing-original draft preparation, Literature search, Figures. Suwen Cao: Conceptualization, Data collection. Senhao Jiang: Study design, Data collection. Bingbing Gao: Project administration, Study design, Data collection, Funding acquisition. Biao Ma: Methodology, Validation.
Disclosure statement
No potential conflict of interest was reported by the author(s).
Data availability statement
The data that support the findings of this study are available from the corresponding author upon reasonable request.
Additional information
Funding
References
- Maddikunta PKR, Pham QV, Prabadevi B, et al. Industry 5.0: a survey on enabling technologies and potential applications. J Ind Inf Integr. 2022;26:100257.
- Ng KKH, Chen CH, Lee CKM, et al. A systematic literature review on intelligent automation: aligning concepts from theory,: practice, and future perspectives. Adv Eng Inf. 2021;47:101246.
- Barricelli BR, Casiraghi E, Fogli D. A survey on digital twin: definitions,: characteristics, applications, and design implications. Ieee Access. 2019;7:167653–167671. doi:10.1109/ACCESS.2019.2953499
- Bi ZM, Luo CM, Miao ZH, et al. Safety assurance mechanisms of collaborative robotic systems in manufacturing. Robot Comput Integr Manuf. 2021;67:102022.
- Bauer S, Bauer-Gogonea S, Graz I, et al. 25th anniversary article: a soft future: from robots and sensor skin to energy harvesters. Adv Mater. 2014;26(1):149–162. doi:10.1002/adma.201303349
- Wang D, Wang JQ, Shen ZQ, et al. Soft actuators and robots enabled by additive manufacturing. Annu Rev Control Rob Auton Syst. 2023;6:31–63. doi:10.1146/annurev-control-061022-012035
- Wang BY, Zhou S, Jiang SH, et al. Personalized medical devices connect monitoring and assistance: emerging wearable soft robotics. Anal Chem. 2023;95(22):8395–8410. doi:10.1021/acs.analchem.3c00950
- Xu JJ, Song AG. A miniature multiaxis force/torque sensor for acupuncture. IEEE Sensors J. 2023;23(7):6660–6671. doi:10.1109/JSEN.2023.3248640
- Xiong JQ, Chen J, Lee PS. Functional fibers and fabrics for soft robotics, wearables, and human-robot interface. Adv Mater. 2021;33(19). doi:10.1002/adma.202002640
- Rus D, Tolley MT. Design, fabrication and control of soft robots. Nature. 2015;521(7553):467–475. doi:10.1038/nature14543
- Wang JX, Gao DC, Lee PS. Recent progress in artificial muscles for interactive soft robotics. Adv Mater. 2021;33(19):2003088.
- Apsite I, Salehi S, Ionov L. Materials for smart soft actuator systems. Chem Rev. 2022;122(1):1349–1415. doi:10.1021/acs.chemrev.1c00453
- Mosadegh B, Polygerinos P, Keplinger C, et al. Pneumatic networks for soft robotics that actuate rapidly. Adv Funct Mater. 2014;24(15):2163–2170. doi:10.1002/adfm.201303288
- Sanchez V, Mahadevan K, Ohlson G, et al. 3D knitting for pneumatic soft robotics. Adv Funct Mater. 2023;33(26):2212541.
- Hegde C, Su JT, Tan JMR, et al. Sensing in soft robotics. ACS Nano. 2023;17(16):15277–15307. doi:10.1021/acsnano.3c04089
- Jiao DJ, Zhu QL, Li CY, et al. Programmable morphing hydrogels for soft actuators and robots: from structure designs to active functions. Acc Chem Res. 2022;55(11):1533–1545. doi:10.1021/acs.accounts.2c00046
- Gao D, Lin MF, Xiong JQ, et al. Photothermal actuated origamis based on graphene oxide-cellulose programmable bilayers. Nanoscale Horiz. 2020;5(4):730–738. doi:10.1039/C9NH00719A
- Maurin V, Chang YL, Ze QJ, et al. Liquid crystal elastomer-liquid metal composite: ultrafast, untethered, and programmable actuation by induction heating. Adv Mater. 2023;2302765.
- Kalashnikov N, Moraes C. Morphodynamic tissues via integrated programmable shape memory actuators. Adv Funct Mater. 2019;29(34). doi:10.1002/adfm.201903327
- Kotikian A, Truby RL, Boley JW, et al. 3D printing of liquid crystal elastomeric actuators with spatially programed nematic order. Adv Mater. 2018;30(10):1706164.
- Ford MJ, Ambulo CP, Kent TA, et al. A multifunctional shape-morphing elastomer with liquid metal inclusions. Proc Natl Acad Sci U S A. 2019;116(43):21438–21444. doi:10.1073/pnas.1911021116
- Ambulo CP, Ford MJ, Searles K, et al. 4D-Printable liquid metal-liquid crystal elastomer composites. ACS Appl Mater Interfaces. 2021;13(11):12805–12813. doi:10.1021/acsami.0c19051
- Ma B, Xu CT, Cui LS, et al. Magnetic printing of liquid metal for perceptive soft actuators with embodied intelligence. ACS Appl Mater Interfaces. 2021;13(4):5574–5582. doi:10.1021/acsami.0c20418
- Chen S, Zhao RQ, Sun XY, et al. Toxicity and biocompatibility of liquid metals. Adv Healthcare Mater. 2023;12(3):2201924.
- Zhao ZB, Soni S, Lee T, et al. Smart eutectic gallium-indium: from properties to applications. Adv Mater. 2023;35(1):2203391.
- Liu X, Shi LX, Wan XZ, et al. Recent progress of spider-silk-inspired adhesive materials. ACS Mater Lett. 2021;3(10):1453–1467. doi:10.1021/acsmaterialslett.1c00378
- Bodaghi M, Noroozi R, Zolfagharian A, et al. 4D printing self-morphing structures. Materials. 2019;12(8). doi:10.3390/ma12081353
- Bodaghi M, Damanpack AR, Liao WH. Adaptive metamaterials by functionally graded 4D printing. Mater Des. 2017;135:26–36. doi:10.1016/j.matdes.2017.08.069
- Zolfagharian A, Kaynak A, Kouzani A. Closed-loop 4D-printed soft robots. Mater Des. 2020;188:108411. doi:10.1016/j.matdes.2019.108411
- Soleimanzadeh H, Rolfe B, Bodaghi M, et al. Sustainable robots 4D printing. Adv Sustainable Syst. 2023;7(12):2300289.
- Mohammadi M, Kouzani AZ, Bodaghi M, et al. Sustainable robotic joints 4D printing with variable stiffness using reinforcement learning. Robot Comput Integr Manuf. 2024;85. doi:10.1016/j.rcim.2023.102636
- Zhang C, Lu XL, Fei GX, et al. 4D printing of a liquid crystal elastomer with a controllable orientation gradient. ACS Appl Mater Interfaces. 2019;11(47):44774–44782. doi:10.1021/acsami.9b18037
- Ze QJ, Wu S, Nishikawa J, et al. Soft robotic origami crawler. Sci Adv. 2022;8(13):eabm7834.
- Zhang H, Yang X, Valenzuela C, et al. Wireless power transfer to electrothermal liquid crystal elastomer actuators. ACS Appl Mater Interfaces. 2023;15(22):27195–27205. doi:10.1021/acsami.3c03817
- Vinciguerra MR, Patel DK, Zu W, et al. Multimaterial printing of liquid crystal elastomers with integrated stretchable electronics. ACS Appl Mater Interfaces. 2023;15(20):24777–24787. doi:10.1021/acsami.2c23028
- Dong LL, Zhao Y. Photothermally driven liquid crystal polymer actuators. Mater Chem Front. 2018;2(11):1932–1943. doi:10.1039/C8QM00363G
- Liu ZS, Zhang R, Xiao YC, et al. Somatosensitive film soft crawling robots driven by artificial muscle for load carrying and multi-terrain locomotion. Mater Horiz. 2021;8(6):1783–1794. doi:10.1039/D1MH00457C
- Ye J, Yao YC, Gao JY, et al. LM-Jelly: liquid metal enabled biomimetic robotic jellyfish. Soft Robotics. 2022;9(6):1098–1107. doi:10.1089/soro.2021.0055
- Shen ZQ, Zhu XY, Majidi C, et al. Cutaneous ionogel mechanoreceptors for soft machines, physiological sensing, and amputee prostheses. Adv Mater. 2021;33(38):2102069.
- Lee W, Kim H, Kang I, et al. Universal assembly of liquid metal particles in polymers enables elastic printed circuit board. Science. 2022;378(6620):637–641. doi:10.1126/science.abo6631
- Wang YQ, Gao BB, He BF. Toward efficient wound management: bioinspired microfluidic and microneedle patch. Small. 2023;19(3):2206270.
- Ma YH, Zhang DZ, Wang ZH, et al. Self-Adhesive, anti-freezing MXene-based hydrogel strain sensor for motion monitoring and handwriting recognition with deep learning. ACS Appl Mater Interfaces. 2023;15(24):29413–29424. doi:10.1021/acsami.3c02014
- Li TL, Wang QA, Su YF, et al. AI-Assisted Disease monitoring using stretchable polymer-based sensors. ACS Appl Mater Interfaces. 2023;15(25):30924–30934. doi:10.1021/acsami.3c01970
- Zhang J, Wu JY, Qiu YY, et al. Intelligent speech technologies for transcription, disease diagnosis, and medical equipment interactive control in smart hospitals: A review. Comput Biol Med. 2023;153:106517.
- Zolfagharian A, Khosravani MR, Vu HD, et al. AI-Based Soft module for safe human-robot interaction towards 4D printing. Polymers. 2022;14(16). doi:10.3390/polym14163302
- Zolfagharian A, Jarrah HR, Bodaghi M. 4D printing classroom in modern interactive learning environments. Bioprinting. 2021;24:e00169. doi:10.1016/j.bprint.2021.e00169
- Zolfagharian A, Durran L, Gharaie S, et al. 4D printing soft robots guided by machine learning and finite element models. Sens Actuators, A. 2021;328:112774. doi:10.1016/j.sna.2021.112774
- Chen GP, Yu YR, Wu XW, et al. Bioinspired multifunctional hybrid hydrogel promotes wound healing. Adv Funct Mater. 2018;28(33):1801386.
- Chi JJ, Zhang XX, Chen CW, et al. Antibacterial and angiogenic chitosan microneedle array patch for promoting wound healing. Bioact Mater. 2020;5(2):253–259. doi:10.1016/j.bioactmat.2020.02.004