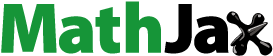
ABSTRACT
Herein, hybrid triply periodic minimal surfaces (TPMS) metamaterials were structurally designed and additively manufactured via 4D printing using a biomass-derived shape memory polymer. Two TPMS topologies including gyroid and diamond with homogeneous and graded structures were separately generated by adjusting the C parameter. The mechanical performance and deformation behaviour between the uniform and graded structures were compared, and the compressive shaping-recovery cycles were conducted. The results showed that the gyroid (C:0.7→0.4) and diamond (C:0.7→0.4) samples exhibited superior reusability to the uniform counterparts. Subsequently, heterogeneous metamaterials assembled by gyroid and diamond subsections were established and 4D-printed. It was observed that both the yielding and shape recovery were preferred occurring in the gyroid part, while the diamond subsection played a stronger supporting effect. Therefore, the compressive performance and deformation mode could be feasibly tuned by the hybridisation of TPMS, which broadened the functional and sustainable applications in energy absorption, intelligent protection and medical implants.
Highlights
Biomass-derived shape memory polyesters with excellent 4D printability and high shape recovery capacity.
Heterogeneous TPMS with graded substructures were designed, constructed and successfully 4D-printed.
Tuneable mechanical properties and deformation behaviour could be achieved by TPMS hybridizations.
Good reusability of load-bearing and energy absorption could be achieved by 4D-printed heterogeneous metamaterials.
1. Introduction
The rapid development of 3D/4D printing manufacturing techniques has enabled the integration of the material and structure with multifunction, which provides a new strategy to produce high-performance and multifunctional engineered components [Citation1–3]. Over the last decades, the structural design of components has been considered a significant factor in realizing and ensuring high-performance components [Citation4–6]. Metamaterials are artificial microstructural materials with high specific strength, energy storage, acoustic absorption, vibration reduction and extraordinary lightweight effects [Citation7–10]. The triply periodic minimal surface (TPMS), a class of metamaterials, is consisted of a smooth and continuous structural surface, whose cellular structure could be created and tailored by the mathematical equation. The unique interconnected and regular porosity are suitable to facilitate body fluid and nutrition exchange, which enables cell proliferation [Citation11–17]. On the other hand, the load-carrying and energy absorption capacity of TPMS metamaterials makes them excellent candidates for lightweight energy absorbers [Citation18]. Therefore, their remarkable properties make them attractive in aerospace, medical and protection fields.
Considerable research has been dedicated to improve TPMS performance by studying the influence of geometric parameters and cellular configuration on mechanical performance [Citation15,Citation16,Citation19–22]. TPMS metamaterials exhibit promising crashworthiness properties, bio-inspired structure, lightweight effect and excellent energy absorption capacity. Each class of TPMS structure possessed unique load-bearing, energy absorption, shape deformation modes as well as fluid transmission capacity. The experimental test and numerical modelling were applied to reveal the deformation behaviour and failure mode based on both metal and polymeric materials. TPMS has been designed into graded structures with gradient relative density, and the graded samples showed a controllable deformation mode and compressive performance.
Most recently, hybridisation of TPMS lattices was also proposed to achieve designable properties [Citation23–28]. For the newly proposed structures, heterogeneous TPMS structures may provide a means to achieve integrated properties, which could fully utilise the advantage of the multi-characteristics in comparison with a single TPMS type. More importantly, inspired by the repeatability of shaping and recovery cycles, TPMS structures using 4D printing technology bring promising reusability into these architected metamaterials [Citation29–31]. Consequently, inspired by the energy reusability, 4D printing of SMP combined with heterogeneous structural design showed great potential as bone implants, energy absorbers, intelligent aircraft skin, dynamic impact armour, etc (as illustrated in ) [Citation32,Citation33]. By utilising the proposed hybrid lattices and shape memory materials, the biomimetic design, smart-stimulus response and excellent lightweight could be ideally realised. For instance, the heterogeneous structure was able to realise a loose to dense transition, which exactly mimicked the cortical-trabecular bone structure. When used as vehicle energy absorbers, the gyroid with lower relative density well-protected the pedestrian and the diamond with higher relative density support collision safety. On the other hand, the 4D printing of smart material endowed shape recovery behaviour as deployable-foldable intelligent components. Therefore, the 4D printing of heterogeneous metamaterials with tuneable mechanical performance and reusability significantly broadened the rapid prototyping applications.
As the 4D printing feedstock, shape memory polymers (SMP) are a new type of intelligent materials that can maintain temporary shape and then recover to their original shape by an external stimulus such as temperature, light, electricity or magnetic field. Accordingly, 3D/4D printing of SMPs has become a hotspot in fabricating smart and functional components [Citation34–37]. The advancement of 4D printing technology using SMPs allows the fabrication of reusable and mechanical metamaterials, which is beyond the capacity of traditional lattice structures [Citation38]. Consequently, the mechanical properties of 4D-printed metamaterials are not only determined by the unit cell topology but also greatly depended on the material properties. Polymeric materials such as polylactic acid (PLA), thermoplastic polyurethanes (TPU) and PETG have been proven to be a novel and excellent SMP [Citation39,Citation40]. In previous work, a new kind of biomass-derived polyester poly (trimethylene furanoate) (PTF) showed comparable mechanical properties with traditional PLA, but a faster shape recovery rate and higher shape recovery ratio [Citation41,Citation42]. Moreover, PTF also exhibited excellent 4D printability, which could fabricate complex components and lattice samples.
With the inspiration of integrating 4D printing with TPMS, novel architected metamaterials were structurally designed and then 4D-printed using PTF feedstock in the current work. Firstly, two types of TPMS surfaces including gyroid (G) and diamond (D) were selected, and the impact of gradient pattern and hybridisation of two surfaces on the mechanical performance and energy absorption were explored. After that, the compression-shaping-restoration cycles were performed to assess the reusability of the graded TPMS surfaces. Then, the heterogeneous structures consisting of gyroid and diamond subsection with tuneable mechanical performance were fabricated and assessed. The shape fixing and recovery behaviour during repeatable cycles were revealed, and the possible deformation mechanism and energy reusability were assessed. Overall, the current work provides insights into the multi-functionally graded and hybrid designs of 4D printing metamaterials.
2. Materials and methods
2.1. Conception and structural design of heterogeneous metamaterials
In the current work, the generation of the heterogeneous metamaterials were structurally designed and generated based on subsection of gradient gyroid and diamond TPMS ().
Figure 2. Generation of the heterogeneous TPMS metamaterials based on gradient gyroid and diamond surfaces.
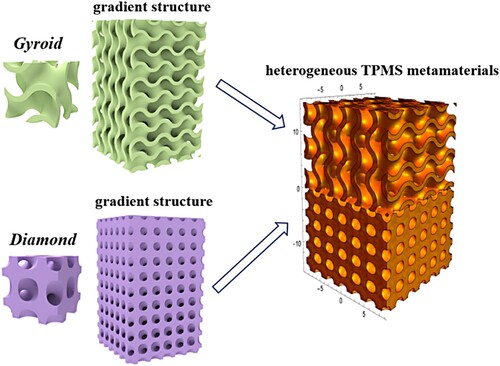
2.1.1. Design of graded TPMS structures
The sheet-network 3D surfaces are constructed by using the following level-set equations Q(x, y, z). Q is in order to divide space into solid and void regions, where Q(x,y,z) > 0 represents the solids, and Q(x,y,z) < 0 represents the pores [Citation43].
The typical equation of gyroid (G) surfaces:
(1)
(1)
The diamond (D) surfaces:
(2)
(2) when
, the typical equation could be specified as a Linear graded lattice. Moreover, the direction of the C value changes is along the z-axis. The parameters including a, b and c are constants that control the size of the cytosol in the x, y and z directions, respectively. C is the level-set constant of the minimal surface, which influences the relative density, thickness and porosity of the minimal surface. A and B are the slopes and intercepts of the linear variation of the C value along the z-axis, which directly affect the extent of the variation of the C value along the z direction.
The constructed model for graded gyroid and diamond surfaces is shown in . It was shown that the variation of C values could change the cell wall thickness and, therefore, realised the graded in thickness and relative density. The C values were changed from 0.7 to 0.4 for graded gyroid surface, whereas the C value = 0.55 for homogeneous structure was set as control. In detail, the variation C values were set as 0.7→0.4, 0.7→0.4→0.7 and 0.7→0.625→0.55→0.475→0.4 (abbreviated as 0.7∼→0.4) from the bottom to up for both surfaces.
Figure 3. Structural design of two types of TPMS: (a) homogenous and gradient C regions of gyroid and (b) homogeneous and gradient C regions of diamond. The variation of C values is illustrated in the figure.
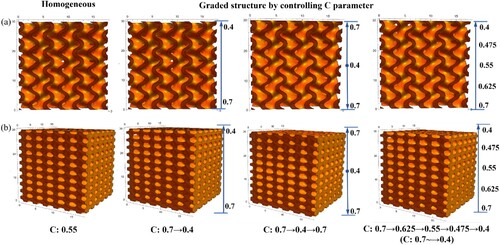
The relative density (ρ*) of the structural entity of the minimal surface greatly determines the mechanical properties and energy absorption capacity, which has a close relationship with the volume fraction. Therefore, the relative density is defined as the ratio of the equivalent density of the minimal surface to the density of the base material [Citation44]:
(3)
(3) where
is the density of the matrix material,
is the equivalent density of the minimal surface structure,
is the volume of the minimal surface minimum envelope cube and
is the volume of the minimal surface structure with thickness.
The relative density corresponded to the C value is shown in . It could be seen that the same C values corresponded to ρ* for gyroid and diamond were different. At the same C value, diamond structure possessed higher ρ* with lower porosity. To assess the influence of C value on the mechanical behaviour of graded samples, both the graded and homogeneous TPMS samples were kept the same relative densities.
Table 1. C values versus relative density of gyroid and diamond surfaces.
After the multipoint calculations, there was a positive and linear relationship between the C values and the theoretical relative density of TPMS cells. As shown in , the fitted equation was ρ*(G) = 1.20057C–0.00946 for gyroid structure, whereas that for diamond surface was ρ*(D) = 0.66236C–0.00547. Therefore, by adjusting the C values in equations, the relative density in the three-dimensional structure of TPMS could be easily controlled.
2.1.2. Design of heterogeneous gyroid/diamond metamaterials
The heterogeneous structure was designed on the basis of graded gyroid and diamond surfaces. In the process of establishing heterogeneous TPMS structures, Voronoi diagram and minimal surface are combined. Voronoi diagram is a geometric data structure that forms continuous polygons by connecting the perpendicular bisectors of the lines connecting adjacent points. It is used to divide geometric space into multiple convex polygons or polyhedrons. In Euclidean space, the Voronoi diagram is defined based on a given set and a set of points, with the formula as follows:
(4)
(4) where
represents the i-th Voronoi cell,
stands for the i-th Voronoi site, and
denotes the Euclidean distance from a given point to point R.
The construction of heterogeneous TPMS structures is based on Voronoi diagram. First, n Voronoi sites are determined to divide the space into n sub-regions, with each sub-region containing only one Voronoi site. The boundary of each sub-region is formed by the perpendicular bisector of adjacent points. Then, graded minimal surface functions are assigned to the sub-regions, and the substructure functions of the minimal surface are connected by a transition function to form a heterogeneous structure. The purpose of using the Voronoi diagram is to automatically generate sub-spaces based on arbitrary Voronoi sites.
The subspace into which the whole space is divided by the Voronoi sites can be defined as
(5)
(5) where
where the Voronoi site is the centre of the i-th subspace. The entire space is partitioned into n Voronoi cells using an equal number of Voronoi sites. These Voronoi cells are then populated with numerous substructures, and a specialised function is employed to connect them.
A heterogeneous lattice structure could be constructed by the inequality as follows [Citation20]:
(6)
(6) and
(7)
(7) The functions
represent the weights assigned to each structure within the heterogeneous lattice structure. Functions need to fulfil a certain condition for every Voronoi site:
(8)
(8) and
(9)
(9) The substructure is comprehensively arranged within the subspace, and the transition gradients are achieved through the manipulation of the control parameter
. When building heterogeneous structures, Voronoi cells can be populated with graded structures that correspond to a given Voronoi site
. This process naturally incorporates graded TPMS
into each Voronoi cell. After completion, the entire heterogeneous structures can be constructed and a smooth transformation of substructures can be realised using the above method [Citation31,Citation45].
For a heterogeneous structure consisting of only two substructures gyroid and diamond, the equations are as follows:
(10)
(10)
is assigned to the weight function, which is specified as
(11)
(11)
In Equation (7), the k value determines the degree of the transition of the two substructures in the transition region, and the larger the value of k, the sharper the transition is, and the smaller the value of k, the smoother the transition realises. Therefore, concerning the transition region of the heterogeneous structures, the influence of relative density of the transition region on the mechanical performance were further investigated. By regulating the transition region in combination with the Vino diagram, the relative density of the transition region could be freely designed to realise the thickening and thinning, as shown in . The detailed cross-sectional views were provided to visualise the changes in the transition region.
2.2. 4D printing of heterogeneous metamaterials
A biomass-derived polyester, PTF (Zhongke Guosheng Technology Co., Ltd, China) filament with a diameter of 1.75 ± 0.10 mm was selected. The glass transition temperature (Tg) of PTF was 53°C with a good shape memory effect. In the current work, the geometric models graded, and heterogeneous TPMS structures were established by Mathematica software. The models were exported as STL files and then sliced in by using software in FFF 3D printer, with processing parameters as follows: the nozzle temperature was 200°C, the nozzle diameter was 0.4 mm, the layer thickness was 0.15 mm, the printing speed was 20 mm/s and the infill density was 100% [Citation41]. The tensile strength and Young’s modulus of PTF were 63.8 MPa and 1.6 GPa, respectively. Samples for TPMS were 3 × 3 × 5 unit cells with a dimension of 18 mm × 18 mm × 30 mm.
2.3. Characterisations
2.3.1. Internal structure of heterogeneous metamaterials
The internal structure of a 4D-printed heterogeneous gyroid/diamond sample was scanned using a micro-computer tomography (CT) scanner (Zeiss Xradia, 610 Versa). The scanning power and voltage were 8.5 W and 70 kV. Three-dimensional (3D) slice image was collected every 30 μm and then reconstructed into 3D models by using dragonfly software (ZEISS).
2.3.2. Compression performance of graded and heterogeneous metamaterials
For the graded gyroid and diamond, the variation in thickness and type of metamaterial showed a great impact on the mechanical performance. The 4D-printed TPMS samples were performed by the quasi-static compression tests using a universal mechanical testing machine (TSE105D, Shenzhen Wance Testing Machine Co., LTD). Three samples were compressed at a loading rate of 2 mm/min up to a strain of 70%, and each design was tested to ensure repeatability. After the displacement reached to 70% original height of the sample, the pressing load was maintained for 300 s to fix the deformed shape. Then, the compression load was released until the force decreased to zero. The load–displacement data were recorded, and the deformation process was recorded by a real-time CCD camera.
2.4. Shape memory effect and reusability of 4D-printed metamaterials
2.4.1. Shape recovery behaviour
The deformed metamaterials with fixed shapes were recovered to their original shape (as printed) by placing them in an air-circulating oven at a temperature of 75°C. The total recovery times for gyroid, diamond and heterogeneous structures are 390, 510 and 450 s, respectively. The restoration process was recorded by a camera out of the oven window. Since the compressive tests were conducted at room temperature instead of heating conditions, the shape fixing was also called a ‘cold-programme’ shaping. The compressive shaping and recovery process was defined as a shape memory cycle. The shape fixity ratio (Rf) and shape recovery ratio (Rr) were assessed by height changing according to our previous work. The calculation formula was set as follows:
(12)
(12)
(13)
(13) where Ho is the initial height as 4D-printed, Hmax is the height at the end of compression, Hf is the height after the pressing load is released and Hr is the height after the 4D-printed sample is recovered.
2.4.2. Reusability of 4D-printed metamaterials
In order to evaluate the load-carrying and energy absorption reusability of the proposed metamaterials, two additional cycles were further conducted. For each cycle, the yielding strength, elastic modulus and specific energy absorption (SEA) were calculated and analysed. The yielding strength was assigned to the first peak value of the stress and the modulus was the slope of the initial rising stage in the compressive stress–strain curves. The energy absorption (EA) was calculated by the enclosed area between the compressive stress–strain curve and the x axil. The SEA referred the amount of energy absorbed by a structural unit mass as follows [Citation46]:
(14)
(14) where m is the weight of printed sample.
3. Results and discussion
The uniform and graded gyroid and diamond metamaterials were successfully 4D-printed by using PTF filaments. As shown in , all metamaterials were smoothly and fine printed, suggesting a good printability of PTF-based complex structure. All kinds of metamaterials with gradient C intervals exhibited a golden brown colour with high printing quality. Different C values corresponded to different relative densities and the weight of 4D-printed gyroid and diamond samples are listed in and . Although the C values were varied, both the graded and uniform TPMS samples possessed the same relative density (ρ*) of each type of TPMS. Since the density of PTF was 1.27 g/cm3, the theoretical volumes of gyroid and diamond were 3.50 and 6.32 cm3, and thus, the theoretical mass was 4.45 and 8.03 g, respectively. It could be seen that the error percentages between the actual and design mass were less than 6%, suggesting a high feasibility and producibility of TPMS 4D printing. The golden colour of uniform and graded gyroid samples did not greatly vary due to a smaller difference between the relative density. On the other hand, the relative density for diamond sample was larger, which caused different shades of golden and brown colours. High relative density meant thicker wall thickness and smaller volume fraction.
Figure 6. 4D-printed uniform and graded (a) gyroid and (b) diamond surfaces with different gradient C intervals, the sample size was 18 × 18 × 30 mm3
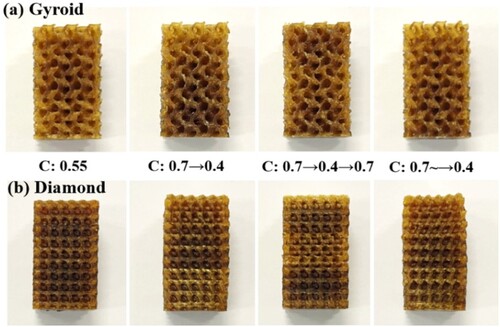
Table. 2. Design mass and the actual mass of the gyroid and diamond with varying C values.
3.1. Effect of gyroid parameters on compressive performance and shape memory behaviour
The compressive stress–strain curves of graded gyroid metamaterials with varying C intervals are plotted in . As structurally designed, the relative density of homogenous structure (C:0.55) was equal to those of the graded gyroid ones (C:0.7→0.4, C:0.7→0.4→0.7, C:0.7∼→0.4). It can be seen that all gyroid samples exhibited typical curve pattern, including an initial elastic stage, plateau and densification stage [Citation47]. However, different elastic strength, plateau strength and elastic modulus were obtained for homogeneous and graded gyroid metamaterials. In the first half compression process (marked blue region), the homogeneous sample exhibited superior compressive property to the graded ones, whereas the varying trend was opposite in the second half (orange region). This phenomenon was greatly determined by varied C values corresponded to different relative densities.
Figure 7. (a) Compressive stress–strain curves and the deformation process of 4D-printed gyriod metamaterials with different C values, (b) C:0.55, (c) C:0.7→0.4, (d) C:0.7→0.4→0.7 and (e) C:0.7∼→0.4.
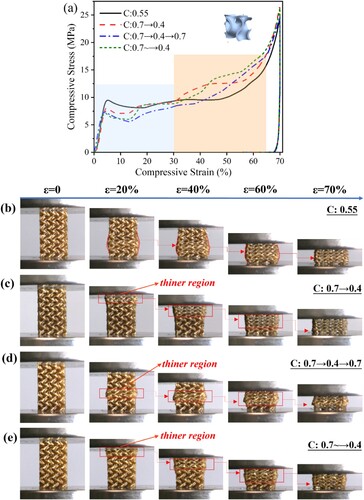
The corresponding compressive process is also simultaneously recorded in (b–e). For homogeneous gyroid sample with C value of 0.55, an overall bulky deformation was observed, which displayed a continuously increasing trend, indicating a stable supporting effect. For graded G samples, different collapsing regions were detected. It can be observed that the buckled initially occurred in the low relative density (thinner) region. For example, the loading displacement firstly deformed in the middle region of the gyroid (C:0.7→0.4→0.7), which possessed thinner wall thickness. Therefore, the yielding preferentially happened in the low-density local region and then deformed in the high relative density part, which was also shown with a higher plateau in the curves. Although the stress of the homogeneous structure (C: 0.55) was flatter, the stress of the gradient structure presented a multilevel buffer behaviour, and the stress growth would also be larger than the homogeneous counterparts in the latter stage, and thus, the overall energy absorption achieved higher. behaviourMeanwhile, the multilevel buffer effect with a reduced initial stress also contributed to a certain collision protection capacity for gradient structures.
The reusability of 4D-printed gyroid with different C values were further evaluated. An external load-shaping and thermally-activated restoration cycle were conducted [Citation48,Citation49]. The gyroid was firstly compressive loaded, then the force released and the fixing shape was obtained. During the compression, the sample exhibited good load-carrying and energy-absorbing capacity. After that, the shape restoration was stimulated by placing the sample in an air-circulating oven at a temperature of 75°C. Three repeated compression-shaping-recovery processes are conducted and presented in (a). To compare the initial and the recovered height, the shaping fixing ratio (Rf) maintained high values above 96% after three cycles (). Therefore, the excellent shape memory effect for PTF metamaterial might provide a satisfied reusability for engineering applications.
Figure 8. (a) Cold-programmed shaping-restoration process for a 4D-printed gyroid sample and (b) the shape fixing ratio after load released.
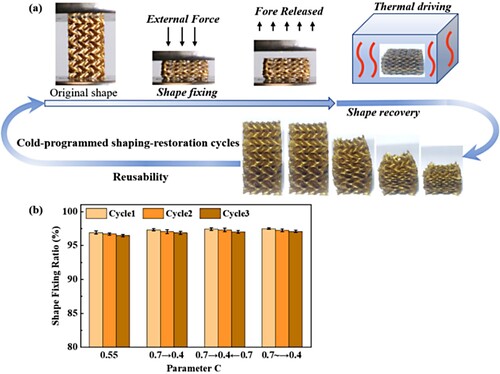
The compressive stress–strain curves during the three cycles of 4D-printed gyroid samples are shown in , and the yielding strength and elastic modulus are listed in . It was clearly shown that both the compressive strength and modulus became decreased as well as the declined densification after the first cycle. For gyroid (C:0.55) in the 1st cycle, the compressive modulus and strength were 306.6 ± 22.1 and 9.5 ± 0.9 MPa, then decreased to 198.0 ± 18.3 and 9.4 ± 1.5 MPa for the 2nd cycle, and 173.3 ± 19.6 and 9.1 ± 0.9 MPa for the 3rd cycle, respectively. For the graded ones, gyroid (C:0.7→0.4) exhibited higher initial elastic modulus and yielding strength were 281.9 ± 19.7 and 8.1 ± 0.9 MPa, which was superior to those of gyroid (C:0.7→0.4→0.7) and gyroid (C:0.7∼→0.4). Although the compressive property decreased after three cycles, the elastic modulus and yielding strength of G structure (C:0.55) still maintained a retention ratio of 56% and 96%, respectively. Meanwhile, higher retention ratios of 59% and 90% for modulus and strength were also achieved for the graded gyroid (C:0.7→0.4) sample.
Figure 9. Compressive stress–strain curves of 4D-printed gyroid for three cycles, (a) C: 0.55, (b) C: 0.7→0.4, (c) C: 0.7→0.4→0.7 and (d) C: 0.7∼→0.4.
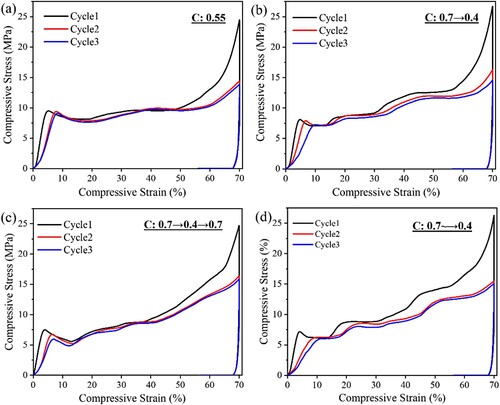
Table 3. Elastic modulus, yielding strength and shape fixing ratio of the 4D-printed homogenous and graded gyroid samples during three shaping-recovery cycles.
During the compression–restoration cycles, the entire absorbed energy, reduced energy, SME-restored energy and stored energy from the stress–strain curves were achieved. To better evaluate the energy absorption capacity and reusable energy of 4D-printed TPMS, the SEA was calculate covering the whole compressive strain to evaluate the overall energy absorption under compression and the reusable energy during shape recovery over a large deformation including the densification stage. The calculation method for each kind of energy is illustrated in (a,b). During the two loading process, the area enclosed by the first and the second loading curves represented the reduced energy (marked purple), which could not be utilised for the shape recovery. The area between the unloading curve and axis encircles was assigned to the stored energy (marked blue), which provides the rebound energy once the indenter lifted after compression. The stored energy is less related to the TPMS reusability in the current work. The area enclosed by the second loading curve, the first unloading curve and the x axis were assigned to the SME-restored energy (marked green). It represented the absorbed energy that could be reused by the thermally stimulated shape memory during the cycle loading, which was a key parameter to evaluate the reusability and energy absorption capacity of the TPMS structures.
Figure 10. (a) SEA achieved from the stress–strain curve, (b) illustration of each kind of energy and the energies of gyroid metamaterials under each compression-shape memory cycle, (c) C: 0.55, (d) C: 0.7→0.4, (e) C: 0.7→0.4→0.7 and (f) C: 0.7∼→0.4.
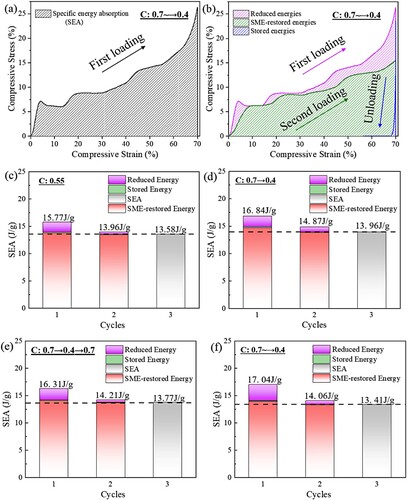
So, the reduced energy, stored energy, SEA and SME-restored energy are plotted in (c–f). These specific energies indicated the reusability of the 4D-printed gyroid samples. To calculate the SEA during the compression process (strain: 0→70%), all graded samples achieved higher values than the uniform one (as shown in (a) for Cycle 1). In detail, the values were 16.84, 16.31 and 17.04 J/g for gyroid 0.7→0.4, 0.7→0.4→0.7 and 0.7∼→0.4, respectively, in contrast with uniform samples with 15.71 J/g. This was due to the linear relative density in the gradient structure contributed to varying energy absorption. The graded structural designS allowed better absorb and consume the impact energy, reducing the damage caused by energy transfer and reflection. Therefore, the graded gyroid (C:0.7→0.4) achieved the best energy absorption capacity among the homogeneous and the other two graded samples. Furthermore, the uniform sample exhibited an overall buckling whereas the yielding of the graded sample tended to occur in the low relative density region (C value). Accordingly, the deformation of gradient structure could be realised and predictable by graded structural design. To achieve a balanced load-carrying capacity and energy reusability, the graded gyroid (0.7→0.4) sample exhibited comparable yielding strength, controllable deformation mode and higher absorbed energy.
3.2. Effect of diamond parameters on compressive performance and shape memory behaviour
In this section, the influence of C values on the compressive performance of the diamond TPMS structure was further investigated. Although the C variation intervals for diamond were the same as gyroid, different relative density was achieved for each type of TPMS (as shown in ). The compressive stress–strain curves and the deformation process of diamond samples are presented in . As presented in the curves, the homogeneous diamond exhibited higher yielding strength than that of the graded ones before the compressive strain of 27% but inferior performance as the strain ranged from 28% to 70%. Similarly, as shown in (b–d), the deformation was preferentially yielded in the thinner region, which was corresponded to the lower C value region. Therefore, the initial yielding region for the TPMS structure could be tuned by adjusting lower C values.
Figure 11. (a) Compressive stress–strain curves and the deformation process of 4D-printed diamond metamaterials with different C values, (b) C:0.55, (c) C:0.7→0.4, (d) C:0.7→0.4→0.7 and (e) C:0.7∼→0.4.
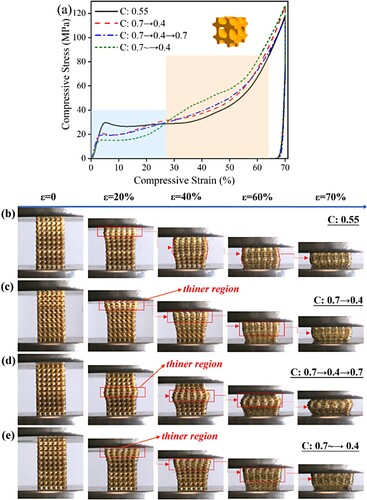
Furthermore, the shape recovery process for the homogeneous and graded diamond samples after compressive shaping are recorded and presented in . The entire shape recovery period was set at 510 s, and the recovered shape at each time point was recorded. Despite the local buckling, the shape restoration behaviour displayed a similar mode and recovery time. The whole recovery process suggested an efficient shape memory effect for PTF materials. In addition, although the 4D-printed diamond structures experienced large deformation, the samples were restored to the original height and no obvious fracture or distortion was observed, which indicated an excellent shape memory effect for the proposed TPMS samples.
Figure 12. Recovered process of 4D-printed diamond structures with different C values, (a) C:0.55, (b) C:0.7→0.4, (c) C:0.7→0.4→0.7 and (d) C:0.7∼→0.4.
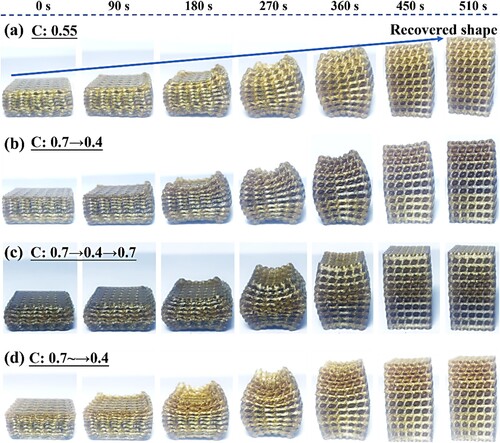
The compressive stress–strain of 4D-printed diamond during the three repeated shaping-recovery cycles is presented in and . For both homogeneous and graded samples, the initial elastic modulus and yielding strength of the diamond were above 733 and 15.4 MPa, respectively, which was higher than those of gyroid sample. The differentiated mechanical performance was determined by the TPMS type and the relative densities. The diamond samples played a supporting role, while the gyroid exhibited a more ductile deformation. For stress–strain curves ((a–d)), the plateau and densification stages continuously increased for graded diamond. However, the elastic modulus and initial yielding strength of graded samples were lower than those of uniform one, which showed similar patterns as gyroid. As the cycle progressed, the elastic modulus attenuated to the 50%∼60% initial values for diamond (C:0.55, 0.7→0.4, 0.7→0.4→0.7), whereas the yielding strength only slightly decreased. Therefore, both the retention rate of graded samples was greater than the uniform one. The compressive properties were followed as: (C:055) > (C:0.7→0.4) > (C:0.7→0.4→0.7)> (C:0.7∼→0.4). Meanwhile, the shape fixing rations for all kinds of diamond samples were all above 96%, demonstrating good shape memory behaviour for diamond metamaterials.
Figure 13. Compressive stress–strain curves of 4D-printed diamond for three cycles, (a) C:0.55, (b) C:0.7→0.4, (c) C:0.7→0.4→0.7, (d) C:0.7∼→0.4, (e) the elastic modulus and (f) the compressive strength.
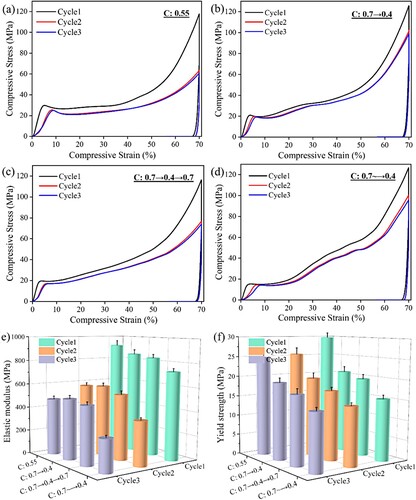
Table 4. Elastic modulus, yielding strength, shape fixing ratio and shape recovery ratio of the 4D-printed homogenous and graded diamond samples during three shaping-recovery cycles.
With the same relative densities, the reduced energy, SME-restored energy and absorbed energy of 4D-printed diamond samples are analysed in . It was notable that the overall energy absorption of diamond was twice as much as gyroid sample, suggesting a better energy absorption capacity. Nevertheless, the high relative density and low volume fraction of diamond structure might be not suitable for biomedical porous implants. When subjected to the first compression test, the reduced energy of the homogeneous sample was larger than the graded ones, suggesting a greater dissipated energy during the compression. Meanwhile, the overall energy absorptions of graded samples for each cycle were all higher than the homogeneous control. Especially, diamond (C:0.7→0.4) achieved the maximum overall energy and the fewest reduced energy. However, the higher SME-restored energy indicated that higher energy may be required for shape recovery. Considering the compressive indicators, energy absorption and reusability, diamond (C:0.55) and gyroid (C:0.7→0.4) samples exhibited considerable compressive performance.
3.3. Compressive performance and reusability of heterogeneous gyroid/diamond structures
After studying the compressive performance and shape memory reusability, the heterogeneous structures consisted of graded gyroid and diamond substructure were newly proposed and established. As shown in (a), the G/D volume ratio was set as 1:1, and three assembling patterns were designed in this section. Due to the good performance of graded gyroid (C:0.7→0.4) and diamond (C:0.7→0.4) samples, two kinds of heterogeneous samples including (GC0.7→0.4/DC0.55) and (GC0.7→0.4/DC0.4→0.7) were fabricated, and (GC0.55/DC0.55) sample were set as control. The hybrid lattice samples were then 4D-printed, which was agreed with the established model. Furthermore, the micro-CT scan was utilised to examine the whole internals structural configuration. From the inside out, the smooth transition was observed at hybrid region, no printing defect was observed and the hybrid region was smoothly transited in the 4D-printed sample. In the x–z section, gyroid and diamond geometry were detected, and the gradient thickness and varied porosity were clearly shown, which was well-verified with the established model. Therefore, the heterogeneous G/D structure was successfully designed and additively manufactured [Citation42].
Figure 15. (a) Structural design of heterogeneous TPMS including (GC0.55/DC0.55), (GC0.7→0.4/DC0.55) and (GC0.7→0.4/DC0.4→0.7) and (b) representative 4D-printed GC0.7→0.4/DC0.4→0.7 sample and the 3D reconstituted micro-CT models.
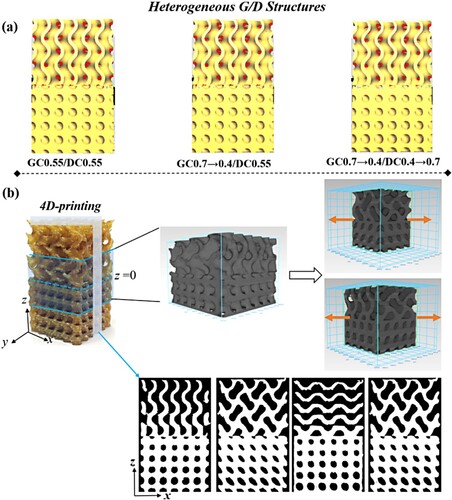
The compressive stress–strain curves of heterogeneous samples are presented in . It can be observed that all samples exhibited similar pattern, which showed two distinct stages. Each stage consisted of an initial yielding and plateau, which was assigned to the two substructures. The first stage was assigned to the deformation of gyroid substructure with a yielding strength of ∼10 MPa, which was in agreement with the results in (a). The second stage reached the yielding strength of 30 MPa, which was also matched with the diamond supporting effect in (a). Therefore, it could be inferred that the yielding was firstly occurred in the G substructure and then the D substructure when subjected to the compression load. Among the three kinds of hybrid lattices, the graded gyroid (C:0.7→0.4) substructure exhibited higher plateau values in the first half during the compression, whereas the uniform diamond (C:0.55) substructure was superior in the second half curves. Overall, the hybrid sample with (GC0.7→0.4/DC0.55) pattern achieved superior load-carrying and energy absorption capacity in contrast with the rest of the two samples.
Figure 16. (a) Compressive stress–strain curves and (b–d) the deformation process of 4D-printed heterogeneous TPMS structures including (GC0.55/DC0.55), (GC0.7→0.4/DC0.55) and (GC0.7→0.4/DC0.4→0.7).
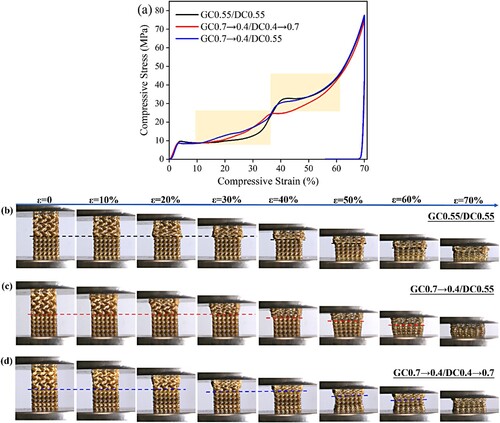
Then, the deformation of hybrid lattices is specially focused in (b–d). Different from the single TPMS sample, a sequential deformation trend which was dependent on the TPMS type was observed. Within a lower compressive strain of 30%, the gyroid subsection suffered continuously deformation and the height of the diamond subsection was nearly unchanged. This phenomenon was consistent with the stress–strain curves, demonstrating that the yielding initially happened in the substructure with a weaker supporting effect. When the compressive strain was above 30%, the diamond subsection began to buckle, and the gyroid subsection continuously compressed till the densification stage. Therefore, two defensing stages with different protective capacity were fabricated by means of heterogeneous structures, including the compressive parameters and deformation mode.
The shape-recovered process of heterogeneous structures is further observed in , and the shape recovery period was set for 450 s. It should be noted that the recovery also first occurred in the gyroid subsection under thermal conditions, which was mainly attributed to lower relative density of gyroid structure. Then, both the gyroid and diamond subsection gradually restored to their original shape. It was found that the shape recovery was reversible with the compression-shaping process, which suggested a good shape memory effect with PTF-based heterogeneous samples.
Figure 17. Recovered process of 4D-printed heterogenous structures with different C values, (a) GC0.55/DC0.55, (b) GC0.7→0.4/DC0.55, (c) GC0.7→0.4/DC0.4→0.7.
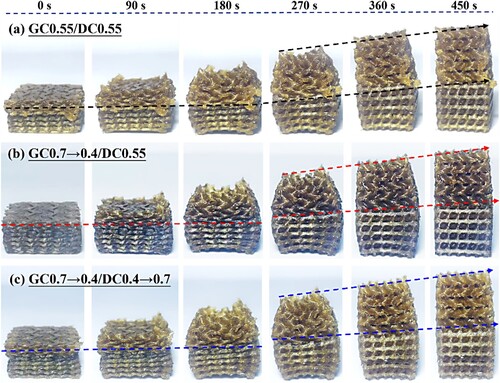
The stress–strain curves and energy absorption values are analysed in , and the compressive parameters are listed in . It was shown that the first yielding strengths of all three hybrid lattices were well-maintained, which was mainly attributed to the deformation of the gyroid subsection. Then, the second stages were assigned to the yielding of the diamond substructure, which exhibited an evident reduced energy and compressive strength. For all three heterogeneous structures, the elastic modulus was found to sharpy decrease but had a high reservation of compressive strength. After three shaping-recovery cycles, the elastic modulus decreased to 25∼30% of initial values, while the yielding strength maintained >89%. Therefore, the initial yielding region, the strength/stiffness variation and the overall energy absorption could be tuned by the G/D structurally design. While the gyroid subsection provided a large deformation and relatively long plateau, the diamond subsection greatly enhanced the load-carrying capacity. These reusable hybrid substructures would be beneficial for hierarchical protection when subjected to the dynamic impact state.
Figure 18. Compressive stress–strain curves and energy absorption of heterogeneous metamaterials under each compression-shape memory cycle, (a,d) GC0.55/DC0.55, (GC0.7→0.4/DC0.4→0.7), (b,e) GC0.7→0.4/DC0.55 and (c,f) GC0.7→0.4/DC0.4→0.7.
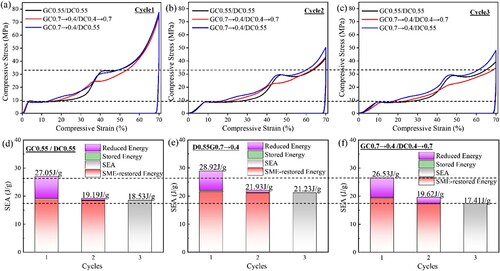
Table 5. Elastic modulus, yielding strength, shape fixing ratio and recovery ratios of the 4D-printed heterogeneous gyroid/diamond samples during three shaping-recovery cycles.
Then, the influence of the transition region of the heterogeneous metamaterials on the mechanical behaviour was further investigated. To eliminate the interference of gradient structure, the hybrid lattice was set as GC0.55/DC0.55. A fixed transition region was selected and three models including thinning, regular and thickening models were established according to and then 3D-printed. From the compressive stress–strain curves (), it was obvious that the transition region had an impact on the mechanical properties. Heterogeneous metamaterials with a thicken transition region exhibited a better load-carrying the energy absorption capacity, which provided another strategy to further improve the mechanical performance of the components with the infilled hybrid lattices. Consequently, the design of thinning, regular and thickening of transition regions could be realised, which could effectively prevent the potential weakness of the transition region of the heterogeneous metamaterials in engineering applications.
4. Conclusion
In summary, a structural design method by adjusting geometric parameters was proposed for substantially tuning the mechanical properties of heterogeneous TPMS metamaterials. Single TPMS structures including gyroid and diamond and assembled gyroid/diamond heterogeneous surfaces were established and fabricated via 4D printing technology. By adjusting C value with three different intervals, uniform and graded gyroid and diamond samples were fabricated. The mechanical performance and deformation behaviour were revealed, and the reusability of lattice structures was realised by compression-shaping and thermal-activated restoration.
In the first section, the compressive properties of uniform and graded gyroid and diamond were separated investigated, and the reusable energy absorption and load-carrying capacity were assessed through compression-shaping and recovery cycles. For each single TPMS type, the results showed that the 4D-printed gyroid (C:0.7→0.4) and diamond (C:0.7→0.4) samples exhibited superior reusability, while the elastic modulus and yielding strength were close to those of uniform counterparts. It could be observed that the buckling initially occurred in the region of lower relative density region and then deformed in the thicker region. The gradient TPMS structure not only exhibited an enhanced load-carrying and energy absorption capacity but also deformed in a predictable failure mode.
Subsequently, the heterogeneous metamaterials assembled by gyroid and diamond subsections were generated and additively manufactured. The stress distribution and failure pattern were consisted of two distinct yielding stages, which were assigned to subsections. It could be observed that both the yielding and shape recovery were preferred occurred in gyroid part due to a lower relative density, while the diamond subsection played a stronger supporting effect. The thickening design of transition region between the two substructures could further improve the mechanical properties of heterogeneous metamaterials. As a result, the proposed design method can be considered as a reference to achieve tuneable compressive performance and excellent reusability, which provided new ideas in the research on TPMS metamaterials.
Data availability statement
Data is available on request from the authors. The data that support the findings of this study are available from the corresponding author upon reasonable request.
Additional information
Funding
References
- Kang YW, Wu LL, Tian XY, et al. 4D printed thermally tunable metasurface with continuous carbon fibre. Virtual Phys Prototy. 2023;18:2224298, doi: 10.1080/17452759.2023.2224298.
- Wan MQ, Yu KQ, Gu JP, et al. 4D printed TMP origami metamaterials with programmable mechanical properties. Int J Mech Sci. 2023;250:108275, doi:10.1016/j.ijmecsci.2023.108275
- Roach DJ, Sun XH, Peng XR, et al. 4D printed multifunctional composites with cooling-rate mediated tunable shape morphing. Adv Funct Mater. 2022;32:2203236, doi:10.1002/adfm.202203236
- Maskery I, Aboulkhair NT, Aremu AO, et al. Compressive failure modes and energy absorption in additively manufactured double gyroid lattices. Addit Manuf. 2017;16:24–29. doi:10.1016/j.addma.2017.04.003
- Liu B, Feng JW, Lin ZW, et al. Controllable three-dimension auxetic structure design strategies based on triply periodic minimal surfaces and the application in hip implant. Virtual Phys Prototy. 2023;18:e2170890, doi: 10.1080/17452759.2023.2170890.
- Wallat L, Selzer M, Wasmuth U, et al. Energy absorption capability of graded and non-graded sheet-based gyroid structures fabricated by microcast processing. J Mater Res Technol. 2022;21:1798–1810. doi:10.1016/j.jmrt.2022.09.093
- Wong M, Owen I, Sutcliffe CJ, et al. Convective heat transfer and pressure losses across novel heat sinks fabricated by selective laser melting. Int J Heat Mass Transfer. 2009;52:281–288. doi:10.1016/j.ijheatmasstransfer.2008.06.002
- Li ZD, Li XW, Chua JW, et al. Architected lightweight, sound-absorbing, and mechanically efficient microlattice metamaterials by digital light processing 3D printing. Virtual Phys Prototy. 2023;18:e2166851, doi: 10.1080/17452759.2023.2166851.
- Kirsch KL, Thole KA. Pressure loss and heat transfer performance for additively and conventionally manufactured pin fin arrays. Int J Heat Mass Transfer. 2017;108:2502–2513. doi:10.1016/j.ijheatmasstransfer.2017.01.095
- William Isaac C, Duddeck F. Current trends in additively manufactured (3D printed) energy absorbing structures for crashworthiness application – a review. Virtual Phys Prototyp. 2022;17:1058–1101. doi: 10.1080/17452759.2022.2074698.
- Wang X, Zhang P, Ludwick S, et al. Natural frequency optimization of 3D printed variable-density honeycomb structure via a homogenization-based approach. Addit Manuf. 2018;20:189–198. doi:10.1016/j.addma.2017.10.001
- Zhou Y, Yang QD, Wei K. Additively manufactured multi-functional metamaterials: low coefficient of thermal expansion and programmable poisson’s ratio. Virtual Phys Prototy. 2024;19:e2303714, doi: 10.1080/17452759.2024.2303714.
- Abueidda DW, Dalaq AS, Abu Al-Rub RK, et al. Micromechanical finite element predictions of a reduced coefficient of thermal expansion for 3D periodic architectured interpenetrating phase composites. Compos Struct. 2015;133:85–97. doi:10.1016/j.compstruct.2015.06.082
- Tsai YY, Chang SW. Pullout strength of triply periodic minimal surface-structured bone implants. Int J Mech Sci. 2023;237:107795, doi:10.1016/j.ijmecsci.2022.107795
- Novak N, Al-Ketan O, Krstulovic-Opara L, et al. Quasi-static and dynamic compressive behaviour of sheet TPMS cellular structures. Compos Struct. 2021;266:113801, doi:10.1016/j.compstruct.2021.113801
- Yang Z, Liang QX, Duan YB, et al. An ultrabroadband metamaterial absorber based on remarkable magnetic coupling via constructing conductive composite resonators and magnetic gradient gyroid structure. Virtual Phys Prototy. 2023;18:e2262445, doi: 10.1080/17452759.2023.2262445.
- Kolken HMA, Janbaz S, Leeflang SMA, et al. Rationally designed meta-implants: a combination of auxetic and conventional meta-biomaterials. Mater Horiz. 2018;5:28–35. doi:10.1039/C7MH00699C
- Mohsenizadeh M, Gasbarri F, Munther M, et al. Additively-manufactured lightweight metamaterials for energy absorption. Mater Des. 2018;139:521–530. doi:10.1016/j.matdes.2017.11.037
- Sadeghi F, Baniassadi M, Shahidi A, et al. TPMS metamaterial structures based on shape memory polymers: mechanical, thermal and thermomechanical assessment. J Mater Res Technol. 2023;23:3726–3743. doi:10.1016/j.jmrt.2023.02.014
- Yang N, Song Y, Huang H, et al. Combinational design of heterogeneous lattices with hybrid region stiffness tuning for additive manufacturing. Mater Des. 2021;209:109955, doi:10.1016/j.matdes.2021.109955
- Wang WW, Jin Y, Mu YR, et al. A novel tubular structure with negative poisson’s ratio based on gyroid-type triply periodic minimal surfaces. Virtual Phys Prototy. 2023;18:e2203701, doi: 10.1080/17452759.2023.2203701.
- Lei H, Li C, Zhang X, et al. Deformation behavior of heterogeneous multi-morphology lattice core hybrid structures. Addit Manuf. 2021;37:101674, doi:10.1016/j.addma.2020.101674
- Jiang W, Liao W, Liu T, et al. A voxel-based method of multiscale mechanical property optimization for the design of graded TPMS structures. Mater Des. 2021;204:109655, doi:10.1016/j.matdes.2021.109655
- Lv Y, Wang B, Liu G, et al. Design of bone-like continuous gradient porous scaffold based on triply periodic minimal surfaces. J Mater Res Technol. 2022;21:3650–3665. doi:10.1016/j.jmrt.2022.10.160
- Fan XJ, Tang Q, Feng QX, et al. Design, mechanical properties and energy absorption capability of graded-thickness triply periodic minimal surface structures fabricated by selective laser melting. Int J Mech Sci. 2021;204:106586, doi:10.1016/j.ijmecsci.2021.106586
- Feng J, Fu J, Shang C, et al. Efficient generation strategy for hierarchical porous scaffolds with freeform external geometries. Addit Manuf. 2020;31:100943, doi: 10.1016/j.addma.2019.100943.
- Perez-Boerema F, Barzegari M, Geris L. A flexible and easy-to-use open-source tool for designing functionally graded 3D porous structures. Virtual Phys Prototy. 2022;17:682–699. doi: 10.1080/17452759.2022.2048956.
- Yu S, Sun J, Bai J. Investigation of functionally graded TPMS structures fabricated by additive manufacturing. Mater Des. 2019;182:108021, doi:10.1016/j.matdes.2019.108021
- Huang XY, Panahi-Sarmad M, Dong K, et al. 4D printed TPU/PLA/CNT wave structural composite with intelligent thermal-induced shape memory effect and synergistically enhanced mechanical properties. Compos Part A Appl Sci Manuf. 2022;158:106946, doi:10.1016/j.compositesa.2022.106946
- Zeng CJ, Liu LW, Bian WF, et al. 4D printed electro-induced continuous carbon fiber reinforced shape memory polymer composites with excellent bending resistance. Compos B Eng. 2020;194:108034, doi:10.1016/j.compositesb.2020.108034
- Dong K, Wang YH, Wang ZH, et al. Reusability and energy absorption behavior of 4D printed continuous fiber-reinforced auxetic composite structures. Compos Part A-Appl Sci Manuf. 2023;169:107529, doi:10.1016/j.compositesa.2023.107529
- Cuan-Urquizo E, Guerra Silva R. Fused filament fabrication of cellular, lattice and porous mechanical metamaterials: a review. Virtual Phys Prototy. 2023;18:e2224300, doi: 10.1080/17452759.2023.2224300.
- Maskery I, Aremu AO, Parry L, et al. Effective design and simulation of surface-based lattice structures featuring volume fraction and cell type grading. Mater Des. 2018;160:106–107. doi:10.1016/j.matdes.2018.09.007
- Zou Y, Guo W, Lu X, et al. A novel water-induced two-way shape memory polymer based on poly (L-lactic acid)/silk fibroin composites. Compos Commun. 2024;46:101822, doi:10.1016/j.coco.2024.101822
- Zeng C, Liu L, Xin X, et al. 4D printed bio-inspired mesh composite materials with high stretchability and reconfigurability. Compos Sci Technol. 2024;249:110503, doi:10.1016/j.compscitech.2024.110503
- Günther F, Hirsch F, Pilz S, et al. Structure-property relationships of imperfect additively manufactured lattices based on triply periodic minimal surfaces. Mater Des. 2022;222:111036, doi:10.1016/j.matdes.2022.111036
- Lin C, Xin XZ, Tian LF, et al. Thermal-, magnetic-, and light-responsive 4D printed SMP composites with multiple shape memory effects and their promising applications. Compos Part B Eng. 2024;274:111257, doi:10.1016/j.compositesb.2024.111257
- Zeng C, Liu L, Du Y, et al. A shape-memory deployable subsystem with a large folding ratio in China’s tianwen-1 Mars exploration mission. Engineering. 2023;28:49–57. doi:10.1016/j.eng.2023.01.005
- Feng P, Zhao RY, Yang F, et al. Co-continuous structure enhanced magnetic responsive shape memory PLLA/TPU blend fabricated by 4D printing. Virtual Phys Prototy. 2024;19:e2290186, doi: 10.1080/17452759.2023.2290186.
- Kuang TR, Zhang ML, Chen F, et al. Creating poly(lactic acid)/carbon nanotubes/carbon black nanocomposites with high electrical conductivity and good mechanical properties by constructing a segregated double network with a low content of hybrid nanofiller. Adv Compos Hybrid Mater. 2023;6:48, doi:10.1007/s42114-022-00622-z
- Wang B, Wu WY, Liu H, et al. 3D-printing of biomass furan-based polyesters with robust mechanical performance and shape memory property. Int J Biol Macromol. 2024;254:127701, doi:10.1016/j.ijbiomac.2023.127701
- Sang L, Wu WY, Sun ZQ, et al. Reusability and energy absorption behavior of 4D-printed heterogeneous lattice structures based on biomass shape memory polyester. J Mater Res Technol. 2023;27:1563–1578. doi:10.1016/j.jmrt.2023.09.323
- Zhao M, Zhang DZ, Liu F, et al. Mechanical and energy absorption characteristics of additively manufactured functionally graded sheet lattice structures with minimal surfaces. Int J Mech Sci. 2020;167:105262, doi:10.1016/j.ijmecsci.2019.105262
- Liang YJ, He HY, Yin J, et al. Energy absorption of gradient triply periodic minimal surface structure manufactured by stereolithography. Rev Adv Mater Sci. 2024;63:20230185, doi:10.1515/rams-2023-0185
- Al-Ketan O, Abu Al-Rub RK. Multifunctional mechanical metamaterials based on triply periodic minimal surface lattices. Adv Eng Mater. 2019;21:1900524, doi:10.1002/adem.201900524
- Hou WB, He P, Yang Y, et al. Crashworthiness optimization of crash box with 3D-printed lattice structures. Int J Mech Sci. 2023;247:108198, doi:10.1016/j.ijmecsci.2023.108198
- Zhang H, Guo ZC, Zhang ZH, et al. Biomimetic design and fabrication of PEEK and PEEK/CF cage with minimal surface structures by fused filament fabrication. J Mater Res Technol. 2023;26:5001–5015. doi:10.1016/j.jmrt.2023.08.236.
- Yue L, Sun XH, Yu LX, et al. Cold-programmed shape-morphing structures based on grayscale digital light processing 4D printing. Nat Commun. 2023;14:5519, doi:10.1038/s41467-023-41170-4
- Soleyman E, Rahmatabadi D, Soltanmohammadi K, et al. Shape memory performance of PETG 4D printed parts under compression in cold, warm, and hot programming. Smart Mater Struct. 2022;31:085002, doi:10.1088/1361-665X/ac77cb