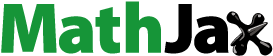
ABSTRACT
The formation of coarse needle-shaped α′-Ti within columnar β-Ti grains in additively manufactured titanium alloy components is nearly unavoidable, and it can lead to unforeseeable service failures. This study employs a multi-component eutectoid alloying strategy, integrating CoCrFeNiMn high-entropy alloy particles within Ti64 alloy. By varying laser parameters, the resulting microstructure transitions from β-dominated to a metastable β + nanoscale α′ microstructure. The coarse needle-shaped α′-Ti and columnar β-Ti grains are significantly refined. Concurrently, the multi-component eutectoid alloying strategy successfully suppresses the formation of detrimental intermetallic compounds by promoting the uniform distribution and solubility of the alloying elements. The Ti64-(4.5%) CoCrFeNiMn alloy demonstrates exceptional mechanical properties, including high tensile strength (1333.8 MPa), uniform elongation (9.3%), and a work-hardening capacity (>390.0 MPa). These are attributed to the continuous variation of Co, Cr, Fe, Ni, and Mn concentrations within the ultrafine α′ and metastable β-phase regions, providing a progressive transformation-induced plasticity effect.
1. Introduction
Incorporating low-density metals into the production of structural components for various industries, including aviation, aerospace, automotive, and lightweight transportation, is a highly promising approach. This technique has the potential to reduce overall weight, enhance energy efficiency, and minimise energy consumption, consequently mitigating carbon emissions and resolving the energy crisis [Citation1]. Among low-density metals, titanium alloys possess significant benefits and are an excellent choice for aerospace structural materials due to their high specific strength and stiffness. These properties make titanium alloys a crucial material for optimising the performance of aerospace and ground systems, while also being extensively used in the cost-sensitive automotive industry. For example, Ti-6Al-4 V (Ti64), an α + β titanium alloy, offers superior strength and toughness, making it suitable for various applications such as medical implants and automotive components operating under moderate temperatures.
Titanium alloys are important structural materials, yet their poor machinability, which includes low thermal conductivity, severe work hardening, and limited plastic deformation, make them less competitive compared to other materials [Citation2]. To reduce production costs, near-net shape manufacturing is an important method. Powder metallurgy (PM) and additive manufacturing (AM) have shown great potential for manufacturing titanium alloys. In particular, laser powder bed fusion (L-PBF) has shown promising results in producing metal alloys with improved mechanical properties [Citation3]. However, large needle-like martensite within detrimental columnar grains, leading to an anisotropic microstructure, resulting in an anisotropic microstructure and poor ductility, fatigue strength, and fracture toughness [Citation4]. This has become a critical challenge that needs to be addressed in the additive manufacturing of titanium alloys [Citation5].
Research on metallic materials suggests that in order to overcome the conflict between their strength and plasticity, three prerequisites must be met: firstly, a uniform strain distribution must be achieved [Citation6]; secondly, an effective plastic deformation mechanism must exist [Citation7]. The third requirement is grain refinement [Citation8]. Inspiration can be drawn from biological materials with spatially distributed local chemical compositions, constituents, and/or nano-structural features [Citation9]. These materials typically exhibit a favourable combination of strength and toughness. In the L-PBF process, due to the short lifespan of the melt pool and fast cooling rate, finer scale (e.g. micron-level) concentration modulation can be achieved through the internal partial compositional homogenisation [Citation10,Citation11]. Such micro-composite materials have been demonstrated to possess extraordinary strain hardening effects that provide a synergistic combination of strength and ductility, such as gradient precipitation microstructure in β-Ti [Citation12] and martensite-austenite heterostructures in steel [Citation13,Citation14], which cannot be achieved in materials with uniform mixed microstructures [Citation15].
Research over the years has further explored the TRIP effect in titanium alloys, continuously revealing remarkable mechanical properties and novel deformation mechanisms [Citation16–19]. The TRIP effect can be achieved by incorporating specific alloying elements, such as Fe. When stress is applied to titanium alloys, the β phase can undergo a phase transformation into the martensite phase (β→α’), thereby enhancing the material’s plasticity. This effect allows the alloy to better absorb and distribute stress when subjected to mechanical loads, thus improving its tensile strength and toughness [Citation20]. However, it is crucial to note that excessively high Fe content may adversely affect the thermal stability of the alloy. The addition of single elements like Cr, Nb, Mo, and Ta as precipitates can effectively stabilise the β phase, thereby enhancing the alloy’s performance [Citation21,Citation22]. Nevertheless, the solid solubility of individual co-precipitating elements has its limitations, as excessive additions may lead to the formation of brittle intermetallic compounds, and the presence of residual precipitates may negatively impact fatigue resistance [Citation23,Citation24]. Recent research suggests that the synergistic co-doping of multiple elements may also have a positive impact on the TRIP effect. This implies that further exploration of element combinations may maximise the potential of the TRIP effect, thereby enhancing the performance of titanium alloys.
To address these limitations and enhance the strength and work hardening behaviour of Ti64 alloy, we designed a strategy to incorporate CoCrFeNiMn high entropy alloy (HEA) as a β stabiliser. By synergistically in situ alloying trace amounts of β-stabilising elements (Fe, Co, Ni, Cr, and Mn) with Ti64 alloy, we can leverage the unique benefits of each element. Fe, Co, Ni, Cr, and Mn are known to be effective grain refining agents and β stabilisers in titanium alloys, with the potential to achieve a fine microstructure.
Furthermore, the addition of HEA elements promotes constitutional supercooling of Ti alloys, thereby enabling the formation of ultrafine grains, which is crucial for microstructure control during additive manufacturing. By comparing the effects of individual elements on titanium alloys (as detailed in Table S1), it is evident that HEAs offer a more balanced and effective enhancement of alloy properties when used as β stabilisers. This comprehensive improvement underscores the significant potential of HEAs in the design of high-performance materials, providing a novel and advanced approach to alloy development that surpasses traditional methods involving single or limited element additions. Finally, by controlling the laser parameters during additive manufacturing, we can regulate the composition and structure of CoCrFeNiMn-reinforced Ti64 alloy, achieving both high strength and a pronounced TRIP effect. This method presents a novel approach for the design and manufacture of high-performance titanium alloys, demonstrating the considerable potential of HEAs as β stabilisers.
2. Thermodynamic calculation.
The Thermo-Calc software, in conjunction with the TCTI1 database, is a commonly utilised tool in the design of composites [Citation10,Citation25]. Based on the phase diagrams of binary alloys of Ti-Co, Ti-Cr, Ti-Fe, Ti-Ni, and Ti-Mn (as depicted in Figure S1), the introduction of small amounts of Co, Cr, Fe, Ni, and Mn elements is capable of significantly broadening the range of solidification temperature (ΔT) in Ti alloys. However, excessive doping is prone to form undesirable second-phase particles (such as TiMn, CoTi2, NiTi2, C14, and C15 Laves phases) due to the relatively low solubility of pure elements in Ti, which typically has adverse effects on the mechanical properties of the alloy. Thus, it is imperative to exercise caution in controlling the content of β-stabilising elements to avoid the formation of unwanted phases.
To simulate the thermodynamics of non-equilibrium processes, we employed the Scheil solidification model to estimate the solidification range and curve of the Ti64-CoCrFeNiMn alloy constructed using L-PBF. As shown in , the addition of a small amount of CoCrFeNiMn (≤4.5 wt%) significantly increased the solidification range of the Ti64-4.5CoCrFeNiMn alloy (about 795°C). However, when the CoCrFeNiMn content exceeds 4.5 wt%, the solidification range hardly changes, because the formation of compounds consumes a large amount of β stabilising elements (Figure S2). The creation of a considerable number of intermetallic compounds poses a grave threat to the mechanical attributes of the alloy. Consequently, we opted for a CoCrFeNiMn content of 4.5 wt%.
3. Material and methods
3.1. Materials
The starting materials used in this study were gas atomised Ti64 and CoCrFeNiMn HEA powders with diameters between 15–53 μm, purchased from Ningbo Zhongyuan Advanced Materials Technologies Co., Ltd. The Ti64 powder particles exhibited a spherical morphology and had a size distribution of D10 = 20.1 µm, D50 = 36.6 µm, and D90 = 58.8 µm. The Ti64 powder composition included Ti (balance), Al (6.06%), V (≤3.96%), Fe (≤0.052%), Y (≤0.001%), O (0.1%), N (≤0.0013%), and C (≤0.016%) in weight percent. On the other hand, the CoCrFeNiMn particles had a size distribution of D10 = 23.1 µm, D50 = 36.8 µm, and D90 = 57.6 µm, and were composed of Co (20%), Cr (20%), Fe (20%), Ni (20%), and Mn (20%) in atomic percent (Figure S3). The Ti64-(4.5%) CoCrFeNiMn mixed powder was prepared by mixing the Ti64 base powder with 4.5 wt% of CoCrFeNiMn particles for 16 h using a 3D dynamic mixer device (ML5, Zhengzhou Kele Machinery Equipment Co., Ltd) to obtain a homogeneous mixture. The scanning electron microscopy (SEM) images of the Ti64-(4.5%) CoCrFeNiMn mixed powder are shown in (a and b).
3.2. Laser-powder bed fusion
The L-PBF is a 3D printing technique that uses a high-powered laser to selectively melt and fuse metallic powders to create complex geometries with high precision. In this study, an L-PBF printer equipped with a 200 W laser of wavelength 1070 nm (AmPro Innovations Pty Ltd.) was used to fabricate the Ti64-(4.5%) CoCrFeNiMn specimens. To ensure a controlled printing environment, the printing chamber was shielded with argon gas, and the oxygen levels were maintained below 200 ppm. The process parameters used for printing the specimens included a laser power of 80 W, a layer thickness of 30 μm, a hatching spacing of 60 μm, and a base temperature of 25 °C. An alternate scanning strategy was used to improve the dimensional accuracy and surface quality of the specimens, with the scanning direction clockwise rotating 66.7° between the two adjacent layers. The scanning speed was varied between 500–800 mm/s to achieve different volume energy densities (VED) in the different specimens, as listed in . Tensile specimens with a gauge length of 16 mm, a width of 3 mm, and a total length of 60 mm were fabricated directly using different processing parameters for tensile testing ((c and d)). Ti64 was fabricated employing the S3 parameters to enable a direct juxtaposition with Ti64-(4.5%) CoCrFeNiMn, utilising identical processing conditions. This comparative analysis is instrumental in elucidating the influence of CoCrFeNiMn on the microstructural features and mechanical properties of the material.
Table 1. Detailed L-PBF processing parameters for the in-situ alloyed Ti64-CoCrFeNiMn samples.
3.3. Characterisation methods
The relative density of the printed specimens was determined using both Archimedes principle and metallographic statistics. The results indicate that the relative density of the specimens surpasses 98.5%, thus demonstrating the ability to produce relatively dense composites through the print parameters utilised in this study (as illustrated in (e)). The phase composition of the specimens subjected to vibratory polishing was identified via X-ray diffraction (XRD, D8 discover, Bruker) with Cu kα monochromatic radiation at a scanning rate of 10°/min. The Rietveld method was applied to calculate the volume fraction of phase β, employing the PDF-#89-4913 (BCC) and PDF-#89-5009 (HCP) databases for phases β and α, correspondingly. The specimens were then sectioned, ground, and polished following standard protocols before being corroded for 10 s using Koller reagent (HF: HNO3: H2O = 1:3:7). The microstructures of the specimens were characterised utilising field emission scanning electron microscopy (FESEM, Sirion, FEI) in the backscattered electron (BSE) mode, in conjunction with an energy dispersive spectrometer (EDS), and Transmission Electron Microscopy (TEM) coupled with selected area electron diffraction (Tecnai, FEI). Additionally, the grain size and texture of the bulk composites were evaluated using electron backscatter diffraction (EBSD) by Oxford Instruments. Subsequently, tensile specimens were subjected to testing at room temperature on a CMT5105 test machine (MTS Industrial Systems, China) at a crosshead speed of 0.5 mm/min. To ensure the reproducibility of the test outcomes, three measurements were taken for each specimen, and the tensile fracture was observed via FE-SEM. The nano-mechanical properties of the alloy were assessed using a Nano Indenter XP with a Berkovich diamond tip (MTS, US). A 10 × 10 array of indents was formed on the polished surface, with a spacing of 20 μm in both the horizontal and vertical directions to mitigate the effects of mutual interaction. The surface approach velocity, depth limit, and surface approach distance were set at 40 nm/s, 1000, and 1000 nm, respectively.
4. Results
4.1. Microstructure analysis
The utilisation of mixed powders in L-PBF for manufacturing differs from conventional printing using pre-alloyed powders because during the melting process, the interactions between mixed powders significantly affect the phase transformation and resulting microstructure. (a) displays the XRD spectrum of the Ti64-(4.5%) CoCrFeNiMn alloy fabricated through L-PBF. The peak of the β-phase was detected in all alloys, which further demonstrated the formation of β-phase in the Ti64-(4.5%) CoCrFeNiMn alloy. Despite the possibility that other phases may exist in the Ti64-(4.5%) CoCrFeNiMn alloy, which we could not detect within the sensitivity range of XRD, if such phases do exist, they do not have a significant impact on the mechanical properties or uniformity. Due to the reinforcement of entropy effects, interactions among elements, and the intricate lattice structure, the multi-element composition in high-entropy alloys enhances the diffusion rate of elements. Simultaneously, the high-entropy elements (Co, Cr, Fe, Ni, and Mn) exhibit atomic sizes and chemical properties similar to those of the Ti matrix, facilitating the uniform distribution and diffusion matching of elements during alloying [Citation26]. Consequently, this improves the diffusion matching between high-entropy particles and the Ti64 matrix, enhancing element compatibility and reducing the likelihood of intermetallic compound formation. High-entropy alloy particles (CoCrFeNiMn) with varied elemental compositions and continuous concentration gradients aid in optimising diffusion matching. In contrast, single-element strengthening particles typically contain only one or a few elements, making it challenging to achieve such refined diffusion matching. Furthermore, they are constrained by solubility limits, which may lead to intermetallic compound formation. Therefore, high-entropy alloy particles excel in enhancing titanium alloys by achieving superior diffusion matching, thereby enhancing alloy performance.
Figure 3. (a)XRD patterns after laser printing in four specimens. (b) Rietveld refinement XRD patterns of Ti64-(4.5%) CoCrFeNiMn samples at different VED.
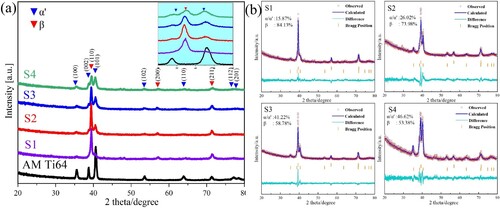
As-printed S1 and S2 were dominated by the β-phase, whereas as-printed S3 and S4 displayed a clear dual-phase microstructures composed of the β-phase and α’ phase. Rietveld refined XRD analysis is a potent method to determine phase composition and content. The Rietveld analysis spectra, shown in (b), presented representative samples of S1, S2, S3, and S4. The observed XRD patterns matched well with the fitting patterns using the Full Prof-Suite software for Rietveld refinement. Meanwhile, according to the calculation of phase content ratio, the β-phase content of the S1 sample prepared under high VED was as high as 84%, whereas that of the as-printed S4 was only 53.38%. Here, we revealed the significant influence of laser parameters on microstructure, further indicating that the synergistic promotion of the in-situ α’ martensite decomposition was achieved by the method of multiphase alloying and adjusting process parameters.
4.2. Micron-scale characteristic microstructures of the L-PBFed specimens
The typical microstructure of the printed Ti64-(4.5%) CoCrFeNiMn alloy is shown in (a), displaying a lava-like microstructure with clear vortex patterns that indicate fluid flow inside the melt pool. Electron microscopy images and EDS results at higher magnification ((a–d)) show that the α′ martensite phase area has much lower CoCrFeNiMn element content than the β phase area. (e) reveals a clear depletion of Ti64 elements (Ti, Al, and V) and an enrichment of CoCrFeNiMn elements (Fe, Co, Ni, Cr, and Mn) within a vortex inside the melt pool. Two distinctly different microstructural features were found in the dark (CoCrFeNiMn element-depleted) and bright (CoCrFeNiMn element-enriched) vortices. The dark vortex is composed of fine needle-like α′ martensite (yellow arrows), while the bright vortex consists of β phase (blue arrows).
Figure 4. (a) BSE images of the as-printed S3, (b) and (c) corresponding EDS results, (d)enlarged view of the as-printed S3 showing the lava-like heterogeneous microstructure with the coexistence of acicular martensite (yellow arrows), β grains (blue arrows), (e) EDS determined elemental distribution.
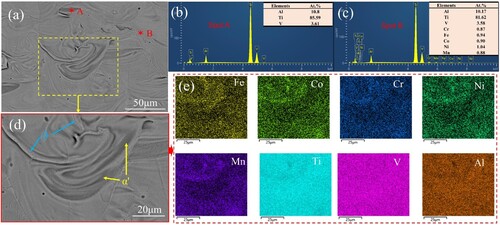
illustrates the BSE micrographs of as-printed S1-S4 after etching. With the increase of energy input, the molten pool depth in S1 is significantly greater than that in S4. Moreover, unlike the traditional large columnar grains observed in AM Ti64 ((e)), bright regions composed of large β grains and dark regions composed of α′ martensite were observed (yellow and blue arrows, respectively) [Citation27]. By adding CoCrFeNiMn, the typical hierarchical coarse needle-like martensite in Ti-based matrix was eliminated, and ultrafine grains were formed throughout the building process ((f and g)). Through proper selection of the composition of β-stabilising elements and control of process parameters, these elements created microscale composition gradients and spatial heterogeneities in the Ti64 matrix.
Figure 5. Microstructures of the cross-sections of specimens printed with different laser parameters. (a-d) BSE micrographs showing different features after etching with Kroll’s reagent. (e) The Ti64 structure has coarse columnar crystals and needle like structures α′.
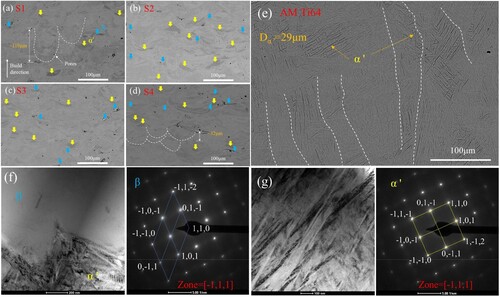
To investigate the crystallographic texture changes in the titanium alloy, EBSD measurements were conducted, which included EBSD inverse pole figure (IPF) orientation maps, EBSD phase maps, and pole figures (PF) of the β phase. These results are summarised in . As the presence of nanoscale ultrafine α’ grains in the sample exceeds the resolution capability of the existing EBSD technique (about 200 nm), we consider the zero-resolution area to also be the α’ phase. The IPF orientation map ((a)) of S1 displays a microstructure predominantly composed of β phase. The EBSD phase map shows that the fraction of β phase in the S1 is 85%, which is almost consistent with the result calculated by Rietveld technology. Unlike the traditional large columnar grains observed along the build direction in AM Ti64, ultrafine grains are present throughout the build process, which is caused by constitutional supercooling resulting from the microstructure [Citation4,Citation5,Citation28,Citation29]. This further indicates that the addition of trace elements Co, Cr, Fe, Ni, and Mn can promote in-situ martensite decomposition and β phase formation. As the VED decreases, the β phase content also decreases. Unlike the large β regions formed in S1 and S2 manufactured with high VED, in S3 and S4 printed with low VED, a large number of ultrafine α’ martensite swirls are dispersed between the β phase swirls, forming a highly heterogeneous and finely modulated β + α’ microstructure.
4.3. Mechanical properties and fracture behaviour
(a and b) presents the tensile mechanical properties of the Ti64-(4.5%) CoCrFeNiMn alloys, with values detailed in . Relative to the Ti64 alloy, the Ti64-(4.5%) CoCrFeNiMn variant shows marked improvements in uniform elongation (εս) and ultimate tensile strength (σUTS). The σUTS initially rises then falls with reduced energy density, peaking at 1333.8 MPa for sample S3. Excluding the as-printed S1, all alloys maintain ductility between 9–10%, double that of Ti64 at 4.8%. The as-printed S3 alloy demonstrates the optimal combination of strength and ductility. (c) shows the work-hardening response relative to the true strain. In the initial stage of plastic deformation, as-printed S3 shows a much higher work-hardening rate than as-printed S2 and S4. As-printed S3 exhibits a higher and gradually decreasing work-hardening rate (∼7.9 GPa) over a larger strain range, which reflects stable and continuous stress-induced β-to-a′ martensitic transformation (SIMT) during the deformation process [Citation10]. In contrast, despite the presence of a high proportion of β phase in S1, most of the β phases in this alloy are excessively stable and unable to transform into martensite during deformation (Figure S4).
Figure 7. (a) Tensile engineering stress – strain curves of as-built specimens printed with different laser parameters, Ti64 was prepared using the same parameters as S2. (b) comparison of the ultimate tensile strength, yield strength and total elongation of different specimens, (c) Work-hardening rate curves, (d) Engineering tensile strength versus uniform elongation of the as-printed Ti64-CoCrFeNiMn alloy as compared with Ti64 alloy produced by different AM methods and conventional technologies: L-PBFed Ti64 [Citation4,Citation10,Citation30–40]; E-PBF Ti64 [Citation30,Citation36–38]; As-casted Ti64 [Citation31,Citation35]; wrought Ti64 [Citation31,Citation34,Citation35,Citation41]; L-PBFed Ti64-(4.5wt.%)316[Citation10]; Ti64-Nb [Citation42]; Ti64-10Mo [Citation43]; Ti5553[Citation44]; Ti64-CoCrNi [Citation44]; Ti64-Fe2O3 [Citation29].
![Figure 7. (a) Tensile engineering stress – strain curves of as-built specimens printed with different laser parameters, Ti64 was prepared using the same parameters as S2. (b) comparison of the ultimate tensile strength, yield strength and total elongation of different specimens, (c) Work-hardening rate curves, (d) Engineering tensile strength versus uniform elongation of the as-printed Ti64-CoCrFeNiMn alloy as compared with Ti64 alloy produced by different AM methods and conventional technologies: L-PBFed Ti64 [Citation4,Citation10,Citation30–40]; E-PBF Ti64 [Citation30,Citation36–38]; As-casted Ti64 [Citation31,Citation35]; wrought Ti64 [Citation31,Citation34,Citation35,Citation41]; L-PBFed Ti64-(4.5wt.%)316[Citation10]; Ti64-Nb [Citation42]; Ti64-10Mo [Citation43]; Ti5553[Citation44]; Ti64-CoCrNi [Citation44]; Ti64-Fe2O3 [Citation29].](/cms/asset/52148d47-9033-4203-9cd8-86546d4ce3b2/nvpp_a_2375106_f0007_oc.jpg)
Table 2. Mechanical properties of the as-printed Ti64-(4.5%) CoCrFeNiMn alloy at different VED.
Compared to titanium alloys manufactured by different AM techniques such as L-PBF, electron beam PBF (E-PBF), and laser direct energy deposition (L-DED) ((d)), the Ti64-(4.5%) CoCrFeNiMn alloy exhibits both higher σUTS and greater εս. These enhanced properties suggest that the alloy could provide significant advantages for structural applications. The excellent work-hardening capability of the alloy (σUTS – σy = 390.8 ± 13 MPa) not only demonstrates its potential for higher performance but also indicates a larger safety margin before fracture. These findings support the notion that the mechanical properties of the Ti64-(4.5%) CoCrFeNiMn alloy manufactured by L-PBF can be further improved by optimising the microstructure.
displays the fracture morphology of the specimens. The fracture surfaces of specimens S1 through S4 exhibit smooth, arc-shaped tear surfaces, which likely indicate the presence of melt pool boundaries. For specimens S2, S3, and S4, the primary features on the fracture surfaces are sub-micron dimples, indicative of a typical ductile fracture mode. In contrast, the fracture surface of specimen S1 is characterised mainly by quasi-cleavage planes and small dimples, revealing a mixed fracture mechanism. Notably, the magnified view in (a) distinctly shows the cellular β-phase features.
Figure 8. Typical SEM fractography under different magnifications of the fractured:(a) S1, (b) S2, (c) S3, (d) S4 stretched at room temperature.
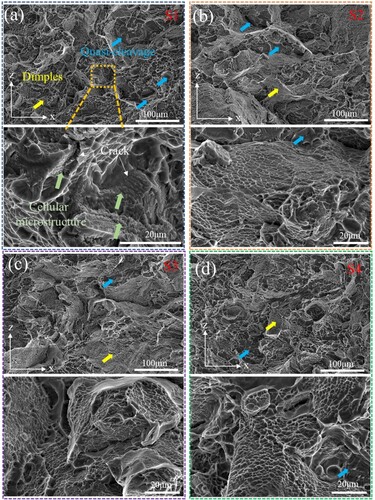
In specimen S1, in addition to the influence of melt pool boundaries, printing defects such as pores or areas of insufficient fusion could also contribute to the occurrence of quasi-cleavage planes. These printing defects create areas of stress concentration within the material, promoting fracture under stress and manifesting as quasi-cleavage fracture characteristics. The prominence of cellular β-phases in specimen S1 may explain its relatively poor mechanical performance. These cellular β-phases form potential weak points in the microstructure, which are prone to fracture under stress, leading to brittle fracture. Furthermore, the cellular microstructure adjacent to the cracks further indicates the presence of brittle fracture, severely limiting the mechanical performance of S1. Overall, the presence of cellular β-phases, combined with printing defects, may be key factors in the inferior mechanical performance of specimen S1. The following section will explore in detail how these microstructural features impact the material’s strengthening and toughening mechanisms.
5. Discussion
As-printed S3 and S4 of Ti64-(4.5%) CoCrFeNiMn, which have a nearly equal proportion of α’ and β phases and have not undergone any post-processing treatments, exhibit enhanced strength and ductility. Conversely, the as-printed specimen S1, comprising a considerable volume of β phase, displays inferior mechanical properties. The observed cellular structure of the oversaturated β phase in S1 forms a continuous network structure with void defects ((a, b)). It has been reported that cellular structures are also formed in high-solute alloys produced by L-PBF, such as 316L stainless steel [Citation45], nickel-based superalloys [Citation46], and Ti-42Nb alloys [Citation47], which are typically associated with micro-segregation of solutes during solidification. Under high VED conditions, such as the parameters used for the S1 sample, the increased thermal input results in the formation of larger melt pools and extends the duration of high-temperature retention. These larger melt pools can retain heat longer before solidifying, thereby reducing the cooling rate. This scenario allows solute elements (such as Co, Cr, Fe, Ni, Mn) within the melt pool sufficient time to redistribute through convection and diffusion, forming supersaturated β phases and promoting grain growth, ultimately yielding a microstructure with larger grains (as illustrated in (a)). During the cooling process, due to local concentration gradients and phase transformation dynamics, these elements readily form cellular enriched regions along the grain boundaries and within the grains. These regions are characterised by highly dispersed and uneven element distribution, manifesting as supersaturated β-rich zones.
Figure 9. (a,) The cellular oversaturated β phase and its mesh-like structure in the S1, (b) The magnified view of the cellular structure and its elemental distribution., (c) crack initiation and propagation under stress state of as-printed S1 sample.
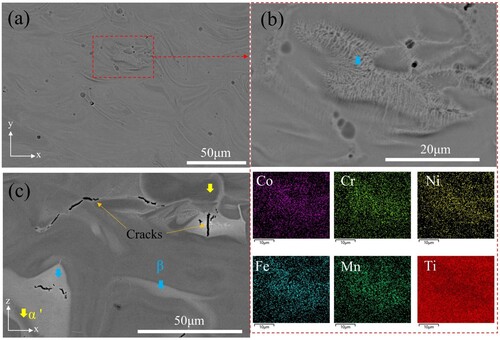
The cellular oversaturated β-enriched regions are often structurally weak and susceptible to the formation of microcracks under stress. Furthermore, the continuous network structure formed by the cellular oversaturated β phase at grain boundaries weakens the mechanical properties at these sites, making them susceptible to tensile fracture. Therefore, when designing and manufacturing titanium alloy parts, it is necessary to consider these cellular oversaturated β-enriched regions to reduce the occurrence of defects and improve material performance and stability. During 3D printing at high energy densities, defects such as gas pores and cracks may occur (refer to (b)), primarily due to an excessively high energy density that leads to deep or wide melt pools. This condition causes overheating, which can result in the material entering a state of over-melting or vaporisation. Additionally, the voids at the cell boundaries could also be caused by the fracture of segregated CoTi2 and NiTi2 intermetallic compounds, as indicated by thermodynamic calculation ((b)). Subsequent tensile deformation often reveals cracks within these cellular, oversaturated β-enriched regions or their network structures in specimen S1 (shown in (c)), clearly illustrating the susceptibility to premature fracture in these areas.
Low VED settings, such as the parameters used for the S4 sample, result in reduced energy input per unit volume, leading to the formation of smaller melt pools. The rapid dissipation of heat induces a higher cooling rate, limiting atomic mobility and reducing the time available for grain growth, thereby promoting the rapid formation of α’ martensite. This rapid cooling generates a fine-grained structure that exhibits enhanced strength and hardness.
It is common knowledge that the chemical composition of printed components may deviate from that of the original powder due to element loss during the printing process. To investigate effect of VED on the chemical composition among as-printed S1-S4, EDS measurements were conducted. The results show that the CoCrFeNiMn content in S3 exceeds that of S1 and S2 by approximately 21% and 14%, while it is around 10% lower than in S4 (as shown in ). The pronounced increase in VED results in a substantially larger melt pool and heat-affected zone, leading to multiple melting and elevated overall temperatures over similar time intervals [Citation48]. This facilitates a higher incidence of splattering, a phenomenon where metal particles are ejected from the melt pool due to intense laser interaction. Splattering is particularly significant at higher energy densities and is a primary contributor to the observed reduction in CoCrFeNiMn content, as it leads to the expulsion of alloying elements from the melt pool.
Table 3. Measured local compositions (wt.%) of the as-printed Ti64-(4.5%) CoCrFeNiMn alloy at different VED.
Furthermore, while the lower melting points of CoCrFeNiMn (1269°C) compared to Ti64 (1669°C) suggest a susceptibility to thermal effects, it does not necessarily indicate volatilisation [Citation49]. Instead, the comparatively lower melting points contribute to the ease with which these elements are expelled during the splattering process. Additionally, the concentration of Al and V in the printed samples is quite similar, with EDS measurements indicating an Al content of approximately 6 wt% and V content of around 4 wt%. Given the pre-alloying of Al and V in Ti64 particles, which helps to stabilise these elements, the impact of vaporisation on their content is minimal. This points to splattering as the predominant mechanism for the loss of elements during the printing process.
With the increase of laser VED in additive manufacturing, the distribution of HEA elements tends to be more homogeneous (). The concentration of HEA elements in micro-areas varies from 1.26 to 13.61 wt% in S3. In the additive manufacturing process, the movement of HEA elements is primarily governed by convective currents within the melt pool and by diffusion, both of which are strongly influenced by the laser parameters and the resultant thermal gradient. Larger VED induces a deeper molten pool in S1, subjecting the material to significantly more melting-solidification cycles. These thermal cycles within the melt pool induce repetitive mixing, ultimately leading to the stabilisation of the β phase within the microstructure, thereby compromising the material’s capacity to exhibit the TRIP effect. Conversely, as VED decreases, the heat-affected zone of the molten pool reduces in size, leading to the local enrichment of HEA elements, thereby affecting the phase stability of metastable β-Ti and reducing the metastable β phase fraction in S2-S4 [Citation10]. Additionally, alterations in the composition of the metastable β phase region may trigger variations in phase stability, resulting in a progressive TRIP effect upon loading. Regardless of whether it is stress-induced α′ martensitic phase transformation or twinning, it involves shearing and rearranging the β lattice, thereby altering the original atomic arrangement. Thus, the greater the susceptibility of the β phase lattice to undergo shear, the more prone it becomes to stress-induced α′ martensitic phase transformation or twinning. Electron concentration and the average atomic radius difference serve as crucial physical quantities characterising the structural stability of the material, employed to gauge the ease of lattice shearing in titanium alloys [Citation50]. For comparative analysis, taking Ti atomic radius as the standard, the calculation involves assessing the alloy’s deviation in average atomic radius from Ti’s atomic radius (average atomic radius difference), providing insights into the extent of increase or decrease in atomic radius post-alloying. The formulas for calculating the average atomic radius difference
and electron concentration (e/a ratio) are as follows:
(1)
(1)
(2)
(2) Where
represents the atomic radius of the i-th element, and
denotes the atomic radius of Ti.
and
correspond to the valence electron number and atomic percentage of element i, respectively. The atomic radius of commonly used alloying elements in titanium alloys and the valence electron numbers of alloying elements are presented in Table S2, while the element concentrations are detailed in Table S3. The computed results are summarised in . According to the reported theory model of valence electron solubility-average atomic radius difference, in the low electron concentration region (such as points A, B, and C where the elemental composition is present), the β phase is relatively unstable, favouring twinning/SIM. The deformation modes transition from twinning/SIMT to slip with the increase in e/a ratio and the decrease in
. This transition is attributed to lattice distortion induced by high-entropy elements, reducing the symmetry and regularity of the β phase lattice [Citation51–53]. This, in turn, increases the resistance to twinning or stress-induced martensitic phase transformation, causing the S1 alloy to undergo plastic deformation in the form of dislocation slip only under higher stress. This elucidates the reason for the high yield strength resulting from the dislocation slip mechanism.
Figure 10. (a-d) Cross-sectional microstructures of samples printed with different laser parameters and EDS maps showing the distribution of Mn element. The rectangular boxes in the images display the overall HEA element content in those regions.
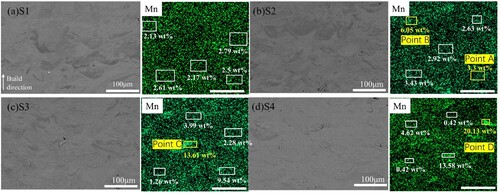
Table 4. Crucial physical quantities for material structural stability.
With the increase in HEA element content within the β phase, lattice distortion becomes more pronounced. The manifestation of lattice distortion (δ) in terms of atomic size differences can be quantified using the mean square deviation of element atomic radii [Citation54]:
(3)
(3)
(4)
(4) The calculated values of δ for different elemental content regions in the alloy are listed in . A threshold value of δ = 6.6, as derived from the mean square deviation of element atomic radii, serves as the boundary for the formation of a solid solution structure in the alloy. When δ < 6.6, the alloy tends to form a disordered solid solution structure, while δ > 6.6 favours the generation of intermetallic compounds. Remarkably, even in the region D with a high concentration of HEA elements (20.13 wt%), the δ value is merely 4.84%, significantly below the threshold for the formation of intermetallic compounds. This implies that the ‘high-entropy effect’ (such as severe lattice distortion and solid solution strengthening) can prevent the formation of brittle intermetallic compounds within the alloy [Citation55].
It is noteworthy that although the Fe, Co, Ni, Cr, and Mn contents in S1 are the lowest, the β content remains at the highest level. This phenomenon could be attributed to the higher energy density, which promotes better uniform mixing of β-stabilising elements within the Ti64 matrix, resulting in a significant increase in the stabilised β fraction after printing. Furthermore, high-VED laser melting may also facilitate the transformation of the β phase in the original titanium alloy matrix, further increasing the β phase content in the alloy [Citation56].
From (c, d), it is evident that there is a distinct layered heterostructure in S3 and S4. As demonstrated in (a, b), nanohardness tests on the S3 alloy reveal that the hardness in the α’ region (indent A) is approximately 10.43 GPa, whereas in the β region (indent B), it is about 5.44 GPa, approximately 2.18 times that of the β region. The high-strength nanoscale α’ phase contrasts sharply with the soft and highly plastic coarse-grain β phase. For convenient measurement and observation of the Hetero-Deformation-Induced (HDI) effect, unload-reload experiments were conducted at every 1% strain interval during the tensile testing of printed titanium alloy. (c) presents the true stress–strain curves for unload-reload cycles of Ti64, S3, and S4, contrasting the as-printed Ti64. S3 and S4 specimens exhibit noticeable hysteresis loops during the unload-reload process, indicating the formation of significant back stresses in the Ti64 + CoCrFeNiMn alloy during deformation. Furthermore, with increasing deformation, the hysteresis loops become more prominent, and the strengthening effect of back stresses correspondingly intensifies ((d)). The back stress value of the S4 specimen is relatively high, providing a crucial guarantee for its high plasticity.
Figure 11. (a) Hysteresis loops of unload-reload tests for printed titanium alloy and the evolution of (b) HDI stress values. (c) Nanohardness mapping in the S3 specimen; (d) Corresponding load-displacement curves at selected positions during nanoindentation tests.
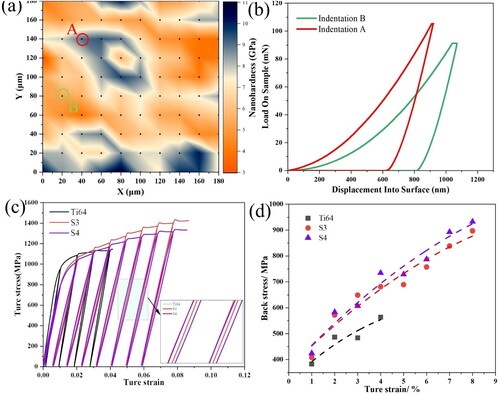
The primary mechanism for the generation of back stresses in heterogeneous titanium alloys is as follows: during plastic deformation, the plastic incompatibility between the soft β phase and the high strength α’ phase primarily occurs at grain boundaries or phase boundaries, leading to strain gradients across these boundaries. Consequently, Geometrically Necessary Dislocations (GNDs) form near these boundaries, providing the possibility of coordinated deformation. In addition to GNDs, ordinary dislocations (such as slip dislocations) also contribute to the internal stress. During the cyclic loading process, these ordinary dislocations accumulate and interact, increasing the material’s internal stress. This combined internal stress from both GNDs and ordinary dislocations is measured as back stress in our experiments.
We have actively utilised the Marangoni effect of L-PBF to achieve a spatially heterogeneous distribution of α’ and metastable β dual-phase microstructure, resembling the microstructure of flowing lava [Citation57,Citation58]. As a result, we have obtained a novel titanium alloy with exceptional mechanical properties, which exhibits superior performance in the following aspects: 1. Enhanced strength of the alloy due to the dispersion of ultra-fine α’ martensite within the metastable β phase region, resulting in the emergence of numerous strengthening dislocations and phase boundaries; Improved toughness of the alloy as the presence of metastable β phase effectively impedes the aggregation of martensite, reducing the formation of brittle regions generated by martensite in the alloy and limiting crack propagation; 2. Through the adjustment of L-PBF process parameters, we have successfully improved the mechanical properties of Ti64-CoCrFeNiMn alloy. Specifically, we selected the representative S3 alloy for tensile testing and found that during deformation, the peak intensity of (110) β at 39.4° continuously decreased (). Additionally, EBSD phase mapping confirmed that the fraction of metastable β phase decreased from 65.9% to 21% after deformation, indicating a continuous deformation-induced phase transformation from the metastable β phase to the α′ martensite phase (). It is worth noting that stress-induced martensite is constrained within the β grains, which results in the reduction of β grain size.
Figure 12. (a) XRD profiles and (b) EBSD analysis of the S3 alloy in as-printed state illustrate the continuous transformation of the β phase to the a′ phase during a tensile test. (c) SIMT was found in the stress concentration area at a strain of 6%.
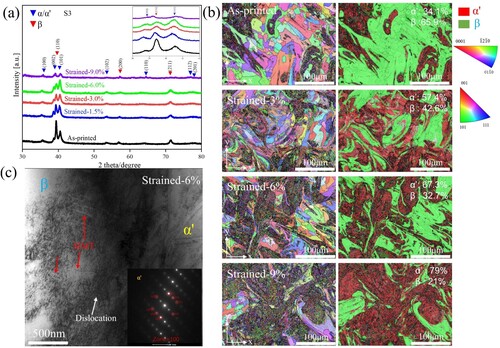
The difference between the preserved β phase in S3 and that in S1 lies in the fact that there are abundant Fe, Co, Cr, Ni, and Mn elements in S3, which is largely metastable and has continuous variations in Co, Cr, Fe, Ni, and Mn concentrations, resulting in changes in its metastability (). The metastable β phase regions with relatively higher concentrations of these elements exhibit higher mechanical stability under load and have higher triggering stress for SIMT, whereas those metastable β phases with relatively lower Co, Cr, Fe, Ni, and Mn concentrations have lower SIMT triggering stress. Therefore, during loading, SIMT starts in the less stable β phase regions first, and then gradually spreads to those more stable β phase regions with increasing load, prolonging the uniform deformation process of the material and delaying the onset of necking ((c)). Figure S5 shows that martensitic transformation of the metastable β phase around the stress field of the crack occurred, which released the compressive stress field that counteracts crack propagation and delayed the formation of cracks.
6. Conclusions
In this work, a novel multi-component eutectoid alloying strategy was employed to in-situ fabricate a Ti64-(4.5%) CoCrFeNiMn alloy with a spatially heterogeneous structure of α′ + β phase microstructure through L-PBF method. The microstructure, mechanical properties and strengthening mechanisms of the Ti64-(4.5%) CoCrFeNiMn alloy were studied. The main conclusions can be summarised as follows:
The addition of CoCrFeNiMn significantly refines the coarse acicular martensite and in situ β columnar crystals of the Ti-6Al-4 V alloy. Concurrently, the multi-component eutectoid alloying strategy successfully suppresses the formation of detrimental intermetallic compounds by promoting uniform distribution and solubility of the alloying elements.
The Ti64-(4.5%) CoCrFeNiMn alloy exhibits a refined α′ + metastable β dual-phase microstructure. This is indicative of synergistic enhancement in the decomposition of in-situ α’ martensite, facilitated by the multi-component eutectoid alloying approach and VED adjustments. The multi-component eutectoid alloying allows for a more homogeneous distribution of alloying elements, which promotes a fine and stable microstructure.
Nanoscale α’ martensite enhances the material’s strength, while the layered heterostructure formed by β phase and α’ phase effectively increases the alloy’s ductility by providing back stress.
Continuous variation in the concentrations of Co, Cr, Fe, Ni, and Mn within the metastable β phase region endows the alloy with a gradient TRIP effect over a wide stress range. Printed samples exhibit a high tensile strength of approximately 1333.8 MPa, a uniform elongation of about 9.3%, and outstanding work-hardening capacity exceeding 390.0 MPa.
This research has successfully developed a titanium alloy with a bimodal (alpha prime and beta phases) microstructure that is strategically distributed to enhance mechanical properties, surpassing those of conventional Ti-6Al-4 V. This demonstrates a promising instance of an additively manufactured titanium alloy, intentionally designed with a heterogeneous microstructure to optimise performance.
Credit author statement
Yifeng Xiong: Investigation, Data curation, Writing – original draft, Writing – review & editing, Validation, Formal analysis.
Faming Zhang: Writing – review & editing, Investigation, Supervision, Funding acquisition.
Yinuo Huang: Investigation, Formal analysis.
Ting Dai: Investigation.
Qifa Wan: Investigation, Formal analysis.
Yan Chen: Investigation, Formal analysis.
Shuo Yin: Writing – review & editing, Investigation, Formal analysis.
Supplemental Material
Download MS Word (921.5 KB)Acknowledgments
The authors gratefully acknowledge the financial supports from National Natural Science Foundation of China (No. 52271129) and Joint Fund of Chinese Ministry of Education for Equipment Pre-research (No.8091B022112), Jiangsu Key Laboratory for Advanced Metallic Materials, Southeast University (No. AMM2023B02), the China Scholarship Council (No. 202306090091).
Disclosure statement
No potential conflict of interest was reported by the author(s).
Additional information
Funding
References
- Zang MC, Niu HZ, Liu S, et al. Achieving highly promising strength-ductility synergy of powder bed fusion additively manufactured titanium alloy components at ultra-low temperatures. Addit Manuf. 2023;65:103444. doi:10.1016/j.addma.2023.103444
- Kaushik HC, Korayem MH, Hadadzadeh A. Determination of α to β phase transformation kinetics in laser-powder bed fused Ti–6Al–2Sn–4Zr–2Mo-0.08 Si and Ti–6Al–4 V alloys. Mater Sci Eng A. 2022;860:144294. doi:10.1016/j.msea.2022.144294
- Liu S, Shin YC. Additive manufacturing of Ti6Al4 V alloy: A review. Mater Des. 2019;164:107552. doi:10.1016/j.matdes.2018.107552
- Todaro CJ, Easton MA, Qiu D, et al. Grain structure control during metal 3D printing by high-intensity ultrasound. Nat Commun. 2020;11(1):142. doi:10.1038/s41467-019-13874-z
- Xiong Y, Zhang F, Dai T, et al. Crystal growth mechanism and mechanical properties of Ti-6Al-4 V alloy during selective laser melting. Mater Charact. 2022;194:112455. doi:10.1016/j.matchar.2022.112455
- Fang TH, Tao NR. Martensitic transformation dominated tensile plastic deformation of nanograins in a gradient nanostructured 316L stainless steel. Acta Mater. 2023;248:118780. doi:10.1016/j.actamat.2023.118780
- Zhang C, Liu S, Zhang J, et al. Trifunctional nanoprecipitates ductilize and toughen a strong laminated metastable titanium alloy. Nat Commun. 2023;14(1):1397. doi:10.1038/s41467-023-37155-y
- Sui S, Chew Y, Weng F, et al. Achieving grain refinement and ultrahigh yield strength in laser aided additive manufacturing of Ti− 6Al− 4 V alloy by trace Ni addition. Virtual Phys Prototyp. 2021;16(4):417–427. doi:10.1080/17452759.2021.1949091
- Lai MJ, Li T, Raabe D. Ω phase acts as a switch between dislocation channeling and joint twinning-and transformation-induced plasticity in a metastable β titanium alloy. Acta Mater. 2018;151:67–77. doi:10.1016/j.actamat.2018.03.053
- Zhang T, Huang Z, Yang T, et al. In situ design of advanced titanium alloy with concentration modulations by additive manufacturing. Science. 2021;374(6566):478–482. doi:10.1126/science.abj3770
- Dong Z, Han C, Zhao Y, et al. Role of heterogenous microstructure and deformation behavior in achieving superior strength-ductility synergy in zinc fabricated via laser powder bed fusion. Int J Extreme Manuf. 2024;6(4):045003. doi:10.1088/2631-7990/ad3929.
- Zhang T, Wang D, Wang Y. Novel transformation pathway and heterogeneous precipitate microstructure in Ti-alloys. Acta Mater. 2020;196:409–417. doi:10.1016/j.actamat.2020.06.048
- Ding R, Yao Y, Sun B, et al. Chemical boundary engineering: A new route toward lean, ultrastrong yet ductile steels. Sci Adv. 2020;6(13):eaay1430. doi:10.1126/sciadv.aay1430
- An XL, Zhang RM, Wu YX, et al. The role of retained austenite on the stress-strain behaviour of chemically patterned steels. Mater Sci Eng A. 2022;831:142286. doi:10.1016/j.msea.2021.142286
- Fan J, Zhu L, Lu J, et al. Theory of designing the gradient microstructured metals for overcoming strength-ductility trade-off. Scr Mater. 2020;184:41–45. doi:10.1016/j.scriptamat.2020.03.045
- Sun F, Zhang J-Y, Marteleur M, et al. A new titanium alloy with a combination of high strength, high strain hardening and improved ductility. Scr Mater. 2015;94:17–20. doi:10.1016/j.scriptamat.2014.09.005
- Ren L, Xiao W, Ma C, et al. Development of a high strength and high ductility near β-Ti alloy with twinning induced plasticity effect. Scr Mater. 2018;156:47–50. doi:10.1016/j.scriptamat.2018.07.012
- Mantri SA, Nartu MSKKY, Dasari S, et al. Suppression and reactivation of transformation and twinning induced plasticity in laser powder bed fusion additively manufactured Ti-10V-2Fe-3Al. Addit Manuf. 2021;48:102406. doi:10.1016/j.addma.2021.102406
- Saito T, Furuta T, Hwang J-H, et al. Multifunctional alloys obtained via a dislocation-free plastic deformation mechanism. Science. 2003;300(5618):464–467. doi:10.1126/science.1081957
- Chen M, Van Petegem S, Zou Z, et al. Microstructural engineering of a dual-phase Ti-Al-V-Fe alloy via in situ alloying during laser powder bed fusion. Addit Manuf. 2022;59:103173. doi:10.1016/j.addma.2022.103173
- Zafari A, Xia K. Superior titanium from hybridised microstructures–A new strategy for future alloys. Scr Mater. 2019;173:61–65. doi:10.1016/j.scriptamat.2019.07.031
- Huber F, Papke T, Scheitler C, et al. In situ formation of a metastable β-Ti alloy by laser powder bed fusion (L-PBF) of vanadium and iron modified Ti-6Al-4 V. Metals. 2018;8(12):1067. doi:10.3390/met8121067
- Vrancken B, Thijs L, Kruth J-P, et al. 2014. Microstructure and mechanical properties of a novel β titanium metallic composite by selective laser melting. Acta Mater 68:150–158. doi:10.1016/j.actamat.2014.01.018
- Nagase T, Hori T, Todai M, et al. Additive manufacturing of dense components in beta-titanium alloys with crystallographic texture from a mixture of pure metallic element powders. Mater Des. 2019;173:107771. doi:10.1016/j.matdes.2019.107771
- Su J, Jiang F, Tan C, et al. Additive manufacturing of fine-grained high-strength titanium alloy via multi-eutectoid elements alloying. Compos Part B: Eng. 2023;249:110399. doi:10.1016/j.compositesb.2022.110399
- Hsu W-L, Tsai C-W, Yeh A-C, et al. Clarifying the four core effects of high-entropy materials. Nature Rev Chem. 2024: 471–485. doi:10.1038/s41570-024-00602-5
- Chen J, Fabijanic D, Zhang T, et al. Deciphering the transformation pathway in laser powder-bed fusion additive manufacturing of Ti-6Al-4 V alloy. Addit Manuf. 2022;58:103041. doi:10.1016/j.addma.2022.103041
- Yang J, Yu H, Yin J, et al. Formation and control of martensite in Ti-6Al-4 V alloy produced by selective laser melting. Mater Des. 2016;108:308–318. doi:10.1016/j.matdes.2016.06.117
- Zhang J, Liu Y, Sha G, et al. Designing against phase and property heterogeneities in additively manufactured titanium alloys. Nat Commun. 2022;13(1):4660. doi:10.1038/s41467-022-32446-2
- Rafi HK, Karthik NV, Gong H, et al. Microstructures and mechanical properties of Ti6Al4 V parts fabricated by selective laser melting and electron beam melting. J Mater Eng Perform. 2013;22:3872–3883. doi:10.1007/s11665-013-0658-0
- Vilaro T, Colin C, Bartout J-D. As-fabricated and heat-treated microstructures of the Ti-6Al-4 V alloy processed by selective laser melting. Metall Mater Transact A. 2011;42(10):3190–3199. doi:10.1007/s11661-011-0731-y
- Xu W, Brandt M, Sun S, et al. Additive manufacturing of strong and ductile Ti–6Al–4 V by selective laser melting via in situ martensite decomposition. Acta Mater. 2015;85:74–84. doi:10.1016/j.actamat.2014.11.028
- Vandenbroucke B, Kruth J. Selective laser melting of biocompatible metals for rapid manufacturing of medical parts. Rapid Prototyp J. 2007;13(4):196–203. doi:10.1108/13552540710776142
- Facchini L, Magalini E, Robotti P, et al. Ductility of a Ti-6Al-4 V alloy produced by selective laser melting of prealloyed powders. Rapid Prototyp J. 2010;16(6):450–459. doi:10.1108/13552541011083371
- Niinomi M. Mechanical properties of biomedical titanium alloys. Mater Sci Eng A. 1998;243(1-2):231–236. doi:10.1016/S0921-5093(97)00806-X
- de Formanoir C, Martin G, Prima F, et al. Micromechanical behavior and thermal stability of a dual-phase α+ α’titanium alloy produced by additive manufacturing. Acta Mater. 2019;162:149–162. doi:10.1016/j.actamat.2018.09.050
- de Formanoir C, Michotte S, Rigo O, et al. Electron beam melted Ti–6Al–4V: microstructure, texture and mechanical behavior of the as-built and heat-treated material. Mater Sci Eng A. 2016;652:105–119. doi:10.1016/j.msea.2015.11.052
- Gong H, Rafi K, Gu H, et al. Influence of defects on mechanical properties of Ti–6Al–4 V components produced by selective laser melting and electron beam melting. Mater Des. 2015;86:545–554. doi:10.1016/j.matdes.2015.07.147
- Edwards P, Ramulu M. Fatigue performance evaluation of selective laser melted Ti–6Al–4 V. Mater Sci Eng A. 2014;598:327–337. doi:10.1016/j.msea.2014.01.041
- Qiu C, Adkins NJ, Attallah MM. Microstructure and tensile properties of selectively laser-melted and of HIPed laser-melted Ti–6Al–4 V. Mater Sci Eng A. 2013;578:230–239. doi:10.1016/j.msea.2013.04.099
- Shunmugavel M, Polishetty A, Littlefair G. Microstructure and mechanical properties of wrought and additive manufactured Ti-6Al-4 V cylindrical bars. Procedia Technol. 2015;20:231–236. doi:10.1016/j.protcy.2015.07.037
- Gou J, Wang Z, Hu S, et al. Effects of trace Nb addition on microstructure and properties of Ti–6Al–4 V thin-wall structure prepared via cold metal transfer additive manufacturing. J Alloys Compd. 2020;829:154481. doi:10.1016/j.jallcom.2020.154481
- Madikizela C, Cornish LA, Chown LH, et al. Microstructure and mechanical properties of selective laser melted Ti-3Al-8V-6Cr-4Zr-4Mo compared to Ti-6Al-4 V. Mater Sci Eng A. 2019;747:225–231. doi:10.1016/j.msea.2018.12.100
- Schwab H, Palm F, Kühn U, et al. Microstructure and mechanical properties of the near-beta titanium alloy Ti-5553 processed by selective laser melting. Mater Des. 2016;105:75–80. doi:10.1016/j.matdes.2016.04.103
- Wang YM, Voisin T, McKeown JT, et al. Additively manufactured hierarchical stainless steels with high strength and ductility. Nat Mater. 2018;17(1):63–71. doi:10.1038/nmat5021
- Keller T, Lindwall G, Ghosh S, et al. Application of finite element, phase-field, and CALPHAD-based methods to additive manufacturing of Ni-based superalloys. Acta Mater. 2017;139:244–253. doi:10.1016/j.actamat.2017.05.003
- Tekumalla S, Seita M, Zaefferer S. Delineating dislocation structures and residual stresses in additively manufactured alloys. Acta Mater. 2024;262:119413. doi:10.1016/j.actamat.2023.119413
- Shoji Aota L, Bajaj P, Sandim HRZ, et al. Laser powder-bed fusion as an alloy development tool: parameter selection for in-situ alloying using elemental powders. Materials. 2020;13(18):3922. doi:10.3390/ma13183922
- Owen LR, Pickering EJ, Playford HY, et al. An assessment of the lattice strain in the CrMnFeCoNi high-entropy alloy. Acta Mater. 2017;122:11–18. doi:10.1016/j.actamat.2016.09.032
- Wang CH, Russell AM, Cao GH. A semi-empirical approach to the prediction of deformation behaviors of β-Ti alloys. Scr Mater. 2019;158:62–65. doi:10.1016/j.scriptamat.2018.08.035
- Wong K-K, Hsu H-C, Wu S-C, et al. A review: design from beta titanium alloys to medium-entropy alloys for biomedical applications. Materials. 2023;16(21):7046. doi:10.3390/ma16217046
- Wang J, Zhang B, Yu Y, et al. Ti content effect on microstructure and mechanical properties of plasma-cladded CoCrFeMnNiTix high-entropy alloy coatings. Surf Topogr: Metrol Proper. 2020;8(1):015004. doi:10.1088/2051-672X/ab615b
- Wang J, Zhang B, Yu Y, et al. Study of high temperature friction and wear performance of (CoCrFeMnNi) 85Ti15 high-entropy alloy coating prepared by plasma cladding. Surf Coat Technol. 2020;384:125337. doi:10.1016/j.surfcoat.2020.125337
- Zhang Y, Zhou YJ, Lin JP, et al. Solid-solution phase formation rules for multi-component alloys. Adv Eng Mater. 2008;10(6):534–538. doi:10.1002/adem.200700240
- Zhang Y, Lu ZP, Ma SG, et al. Guidelines in predicting phase formation of high-entropy alloys. MRS Commun. 2014;4(2):57–62. doi:10.1557/mrc.2014.11
- Ahmed FF, Clark SJ, Leung CLA, et al. Achieving homogeneity in a high-Fe β-Ti alloy laser-printed from blended elemental powders. Mater Des. 2021;210:110072. doi:10.1016/j.matdes.2021.110072
- Zhang T, Li H, Liu S, et al. Evolution of molten pool during selective laser melting of Ti–6Al–4 V. J Phys D: Appl Phys. 2018;52(5):055302. doi:10.1088/1361-6463/aaee04
- Kang N, Lin X, Coddet C, et al. Selective laser melting of low modulus Ti-Mo alloy: α/β heterogeneous conchoidal structure. Mater Lett. 2020;267:127544. doi:10.1016/j.matlet.2020.127544