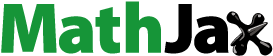
Abstract
Flexible and hierarchical nanostructured Pd/SiO2-TiO2 nanofibrous catalytic membranes were fabricated via combining electrospinning technique and a two-step hydrothermal method. The size and distribution of TiO2 nanorods immobilised on SiO2 nanofibrous membranes can be regulated via adjusting the dosage of TiCl3 solution in the first step hydrothermal process. When using an optimal TiCl3 solution dosage of 0.2 mL, a hierarchical structured Pd/SiO2-TiO2-0.2 nanofibrous catalytic membrane with uniformly dense TiO2 nanorods loaded on SiO2 nanofibers is obtained, and still shows good tensile strength and flexibility. The catalytic activity of Pd/SiO2-TiO2-0.2 increases 5 times as compared to Pd/SiO2-TiO2-0 in the reduction of p-nitrophenol (PNP) to p-aminophenol (PAP). The modification with TiO2 nanorods can provide more surface areas for loading the Pd nanoparticles, thereby increased active sites. The three-dimensional open-cell network stacked and assembled by thousands of SiO2 nanofibers and TiO2 nanorods enhances the contact between the reactants and Pd nanoparticles. Both aspects contribute the superior catalytic activity of Pd/SiO2-TiO2-0.2. Furthermore, a continuous and complete conversion of PNP to PAP can be stably operated over 240 min in a gravity-driven catalytic membrane reactor constructed by Pd/SiO2-TiO2-0.2.
1. Introduction
p-Nitrophenol (PNP), one of the most representative nitroaromatic compounds, is a kind of common organic pollutant [Citation1–3]. As the toxic contaminant in aqueous phase, it is inevitably discharged after industrial use, which is a great threat to human health. From the perspective of environmental protection and human safety, authoritative environmental protection agencies have listed it as a high-level organic harmful substance and strictly restricted its concentration in water bodies [Citation4]. Therefore, how to effectively and completely degrade the pollutant has become a hot issue [Citation5,Citation6]. Traditional physical methods such as adsorption, deposition and filtration cannot fundamentally treat the pollution of PNP [Citation7–9]. Biodegradation not only has little effect, but also may cause the later energy and cost burden [Citation10,Citation11]. It is an effective solution to develop chemical methods such as catalysis for realising the complete conversion of PNP and obtaining high-value products [Citation12]. For instance, sodium borohydride (NaBH4), as a highly efficient reducing agent, can thoroughly convert PNP into p-aminophenol (PAP) in the presence of catalysts under mild conditions. More importantly, PAP plays an important role in the preparation of several drugs (e.g. paracetamol and phenacetin) in modern medicine industry and does little harm to the surroundings [Citation13,Citation14]. Therefore, complete reduction of PNP to PAP via catalysis is a feasible strategy to kill two birds with one stone.
In recent years, the mainly used catalysts are powdered metal-based materials in the catalytic reduction of PNP to PAP [Citation15,Citation16]. However, the powdered catalysts will encounter a series of challenges against uneven dispersion in heterogeneous catalytic reactions and difficult recovery from the reaction mixture, which limits their practical applications [Citation15]. It is urgent to explore more alternative catalytic materials for such reduction. Catalytic membranes prepared via anchoring the catalytic active components on the membrane surface or/and in the membrane pores can provide an efficient solution for the above problems [Citation17]. Furthermore, the PNP reduction can be carried out in a flow through mode, which can dramatically strengthen the mass transfer and completely reduce PNP to PAP [Citation13,Citation18]. Our group has developed sheet and tubular ceramic catalytic membranes for stable and efficient PNP reduction in flow through membrane reactors [Citation13,Citation18,Citation19]. Moreover, the surface modification of the ceramic membranes with functional groups and oxides can significantly improve the Pd content and the interaction between the Pd nanoparticles and ceramic membranes, and then enhance the catalytic activity and stability of the catalytic membranes [Citation13,Citation19,Citation20]. Nevertheless, the current ceramic membranes have some disadvantages, such as low porosity, high mass transfer resistance and small surface area per unit volume, limiting the practical applications of the ceramic catalytic membranes.
The nanofibrous catalytic membranes constructed by nanofibers have high porosity and three-dimensional (3 D) pore structure, which can significantly increase the membrane flux, reduce the transfer resistance and enhance the catalytic efficiency [Citation17,Citation21]. Wang et al. designed a gravity-settlement nanofibrous membrane decorated with polydopamine (PDA) microsphere for continuous reduction of PNP. The PNP conversion remained over 93% after several times of consecutive use [Citation21]. Liu et al. developed a polymer nanofibrous membrane decorated with Ni-P nanoparticles via melt-phase-separated nanofiber-suspension coating and electroless nickel plating. The 100% conversion of PNP was achieved when the Ni-P content was 25 wt.%. This nanofibrous catalytic membrane presented an excellent recycled feature that still kept greater than 98% conversion of PNP after six recycles [Citation17]. Thus, these catalytic membranes with nanofibrous structures are ideal materials for the efficient transformation of PNP to PAP. The current main nanofibrous catalytic membranes for the reduction of PNP are polymer membranes, and the unstable characteristics of polymer under the reaction conditions may limit the further developments [Citation22]. The ceramic nanofibrous catalytic membranes can be the potential candidates.
In this contribution, we reported on a flexible ceramic nanofibrous catalytic membrane (denoted as Pd/SiO2-TiO2) for the reduction of PNP to PAP. SiO2 nanofibrous membranes were first produced by electrospinning, and then TiO2 nanorods were grown on the SiO2 nanofibrous membranes via a two-step hydrothermal method to fabricate the flexible hierarchical SiO2-TiO2 nanofibrous membranes. Finally, Pd/SiO2-TiO2 catalytic membranes were achieved by loading Pd nanoparticles with an impregnation method. The dosage of TiCl3 solution in the first step hydrothermal process was regulated to control the structure and morphology of SiO2-TiO2 nanofibrous membranes, and then their influences on the microstructure and the catalytic performance of Pd/SiO2-TiO2 for the reduction of PNP to PAP were emphatically investigated. Furthermore, a simple gravity-driven membrane reactor was built to realise the stable conversion of PNP to PAP for a long time.
2. Experimental
2.1. Chemicals
Polyvinyl alcohol (PVA, Mw = 77000) was purchased from Macklin Reagent Co., Ltd., China. Tetraethyl orthosilicate (TEOS), polyvinylpyrrolidone (PVP) and phosphoric acid (H3PO4) were purchased from Sinopharm Chemical Reagent Co., Ltd., China. Nitroarenes and titanium chloride solution (TiCl3, 15-20 wt.%) were purchased from Aladdin Industrial Co., Ltd., China. Titanium butoxide (98.0%), sodium borohydride (NaBH4) and concentrated hydrochloric acid (36.5-38 wt.%) were purchased from Shanghai Ling Feng Chemical Reagents Co., Ltd., China. Palladium acetate (Pd(OAc)2) was obtained from Sino-platinum Metals Co., Ltd., China. Ethanol was obtained from Ya sheng Chemical Co., Ltd., China. All chemicals were purchased commercially without further purification.
2.2. Preparation of Pd/SiO2-TiO2 nanofibrous catalytic membranes
The preparation of Pd/SiO2-TiO2 nanofibrous catalytic membranes mainly includes three steps: synthesis of SiO2 nanofibrous membranes, fabrication of SiO2-TiO2 nanofibrous membranes, and loading of Pd nanoparticles, as shown in Scheme 1.
2.2.1. Synthesis of SiO2 nanofibrous membranes
A PVA homogeneous solution with a concentration of 14 wt.% was prepared by dissolving PVA in deionised water with vigorous stirring at 80 °C for 5 h. A solution was prepared by mixing 0.58 mL of deionised water with 198 mL of H3PO4, and 10 mL of the solution was dripped to 11.2 mL of a TEOS aqueous solution (28.4 wt.%) and stirred at 25 °C for 6 h to produce a transparent silica gel by hydrolysis and polycondensation. A precursor solution containing 5 g of PVA solution and 5 g of silica gel was used as the spinning solution. SiO2 precursor nanofibrous membranes were fabricated through electrospinning (ET2535H, Beijing UCALERY Co., Ltd., China) with a feed rate of 1.5 mL/h, a fixed gap between the spinneret and the collector of 18 cm, an applied anode voltage of 17 kV and a rotating speed of 80 rpm. The as-spun hybrid membranes were calcined in air at 700 °C with a heating rate of 5 °C/min.
2.2.2. Fabrication of SiO2-TiO2 nanofibrous membranes TiO2
TiO2 nanorods were grown on SiO2 nanofibrous membranes by a two-step hydrothermal method. First, a sheet of SiO2 nanofibrous membrane was placed vertically in a Teflon-lined stainless steel autoclave containing 40 mL of H2O, 0.1 mL of HCl and an appropriate amount of TiCl3 solution ranging from 0, 0.05, 0.2 to 0.5 mL (the colourless, light white, milky white and purple white of hydrothermal reaction solution, respectively). Afterwards, the first step hydrothermal reaction took place in an oven at 80 °C for 16 h. Then, the membrane was repeatedly cleaned by deionised water and vertically placed in the same stainless steel autoclave containing 20 mL of H2O, 20 mL of HCl and 1 mL of titanium butoxide. The second step hydrothermal reaction was carried out at 150 °C for 4 h, and the membrane was washed repeatedly after taking out. The as-prepared membranes are denoted as SiO2-TiO2-n (n represents that the amount of TiCl3 solution in the first step hydrothermal reaction mixture is n mL).
2.2.3. Synthesis of Pd/SiO2-TiO2 nanofibrous catalytic membranes
The final nanofibrous catalytic membrane was fabricated through impregnating the as-prepared SiO2-TiO2 membrane in 50 mL of 0.005 mol/L Pd colloid in a water bath at 40 °C for 12 h. The Pd colloid was prepared via stirring the mixed solution (0.056 g of Pd(OAc)2, 0.555 g of PVP and 50 mL of ethanol) in a glass round bottom flask at 60 °C for 2 h. The resultant catalytic membranes are marked as Pd/SiO2-TiO2-n.
2.3. Characterisation
The crystal phase structure of the samples was analysed by X-ray powder diffraction (XRD, Miniflex-600). The morphology and composition of the catalytic membranes were examined by field emission scanning electron microscopy (FESEM, S-4800), high-resolution transmission electron microscopy (HRTEM, JEOL JEM-2100), and energy dispersive X-ray spectroscopy (EDS, Horiba Emax). The Pd content was measured by coupled plasma-atomic emission spectroscopy (ICP-AES, Optima 2000 DV). For analysing the element composition and chemical state of the catalytic membranes, X-ray photoelectron spectroscopy (XPS) was performed on a Thermo ESCALAB 250 spectrometer. The specific surface area of the catalytic membranes was determined by the Brunauer-Emmett-Teller (BET) method on a Micromeritics ASAP 2020 analyzer. The pore size distribution was evaluated using a pose-size distribution analyzer (PMI, ipore-1500AEX-clamp). The tensile strength of the catalytic membranes was measured by a tensile tester (XQ-1C).
2.4. Catalytic test
The catalytic reduction of PNP to PAP (Scheme 2) was performed at the temperature of 30 °C in a flow through catalytic membrane reactor system (Scheme 3). The effective membrane area of the samples was 8.04 cm2. In a typical test, 0.05 g (12 mM) of PNP and 0.17 g (150 mM) of NaBH4 were dissolved in 30 mL of a mixture with 5 mL of ethanol and 25 mL of H2O. The mixture solution was pumped through the membrane cyclically and continuously in the help of a peristaltic pump at a rotation speed of 30 rpm. Samples of the reaction mixture were analysed by high-performance liquid chromatography (Agilent 1200 Series) at regular time intervals. The catalytic stability performance during a permeation process driven by gravity at a constant pressure head of 7.5 cm was also conducted through the following procedure: a piece of Pd/SiO2-TiO2-0.2 membrane (diameter of 1.5 cm, membrane area of 1.77 cm2) was fixed between two vertical glass tubes.
2.5. Reaction kinetics
Reaction kinetic expression can provide information about the influences of operating conditions and component concentration on the reaction rate, which helps to determine the control system of catalysts and reactor design [Citation23]. The effect of key reaction conditions on the initial reaction rate of the PNP reduction was investigated by changing several single factors (rotation rate, PNP and NaBH4 concentrations, and reaction temperature). Then the reaction rate of the PNP reduction can be calculated through the power law model (1) and the Arrhenius equation (2):
(1)
(1)
(2)
(2)
where r is the reaction rate (mol·L−1·min−1), k is the rate constant, CA and CB are the concentrations of PNP and NaBH4 (mol·L−1), a and b are the relevant reaction orders, Ea is the activation energy (kJ·mol−1), R is the general gas constant (kJ·mol−1·K−1), k0 is the pre-exponential factor, and T is the reaction temperature (K).
3. Results and discussion
3.1. Synthesis and characterisation of the catalytic membranes
The XRD patterns of the as-synthesised Pd/SiO2-TiO2 catalytic membranes prepared under different TiCl3 dosages in the first step hydrothermal reaction are presented in . The XRD spectrum of the Pd/SiO2-TiO2-0 membrane () shows a broad characteristic peak at about 21.9°, which represents the amorphous phase of SiO2 (JCPDS No. 75-0638) [Citation24]. There are no diffraction peaks of TiO2, which indicates that TiO2 does not grow on the SiO2 nanofibers and the seed coating is necessary for the TiO2 formation. With the increase of TiCl3 dosage in the first step hydrothermal reaction, the characteristic peaks of TiO2 appear and tend to become stronger, but the inherent characteristic peak of SiO2 weakens and finally disappears, because the XRD peaks of high-density TiO2 nanorods cover the peak of SiO2 with low intensity [Citation25]. As shown in d, the obvious TiO2 characteristic peaks are found at 27.4° (main diffraction peak), 41.2° and 44.1°, which represent (110), (111) and (210) crystal faces of rutile-type TiO2 (JCPDS No. 21-1276) [Citation26]. The unobvious TiO2 characteristic peaks at 30.9° and 64.1° represent (121) and (203) crystal faces of brookite-type TiO2 (JCPDS No. 29-1360) [Citation27]. At the peak positions of 25.4°, 36.5°, 37.9°, 54.4°, 56.7°, 62.9°, 68.9° and 69.9° there are characteristic peaks of anatase-type TiO2 corresponding to (101), (103), (004), (105), (211), (204), (116) and (220) crystal faces (JCPDS No. 21-1272) [Citation28]. The appearance of XRD diffraction peaks of these typical TiO2 nanocrystals suggests the successful fabrication of TiO2 on the SiO2 nanofibers. The intensity of TiO2 diffraction peaks of the Pd/SiO2-TiO2-0.2 membrane is the greatest, which may be attributed to higher crystallinity and greater growth density of TiO2 on the membrane under the conditions [Citation29]. There are no characteristic diffraction peaks of metal Pd nanoparticles in the XRD patterns, which can be due to the small size and high dispersion of Pd nanoparticles [Citation13].
Figure 1. XRD patterns of (a) Pd/SiO2-TiO2-0, (b) Pd/SiO2-TiO2-0.05, (c) Pd/SiO2-TiO2-0.2, (d) Pd/SiO2-TiO2-0.5.
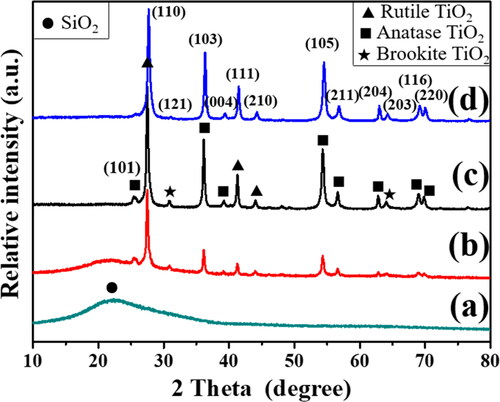
The FESEM images provide overall morphologies of the Pd/SiO2-TiO2 nanofibrous catalytic membranes (). The results indicate that the content of TiCl3 has a great effect on the membrane morphology. No TiO2 nanorods can be found on the SiO2 nanofibers when TiCl3 solution is not used from the low magnification FESEM image (). Compared with Pd/SiO2-TiO2-0, many TiO2 nanorods are coated on the SiO2 nanofibers for other nanofibrous catalytic membranes (). The distribution of TiO2 nanorods on the surface of Pd/SiO2-TiO2-0.2 is rather intensive and uniform. It may be the reason that suitable concentration of TiCl3 precursor solution is conducive to the uniform coverage and growth of seed crystals on the nanofibers, which results in better development of nanorods. Additionally, it can be clearly seen that Pd/SiO2-TiO2-0 exhibits smooth fibre morphology and the average fibre diameter is about 0.3 μm at the high magnification (). When increasing the dosage of TiCl3 solution from 0.05 to 0.5 mL, the size of TiO2 nanorods coated on the SiO2 nanofibers (as shown in ) gradually decreases. The length of nanorods decreases from 1.6 ± 0.2 to 0.72 ± 0.4 μm, and the diameter of nanorods reduces from 210 ± 27 to 90 ± 11 nm. Overall diameters of the as-prepared membrane fibres are about 3.65、2.9 and 2.68 μm due to the TiO2 nanorods with different sizes. The decrease in the size of TiO2 nanorods with increasing the dosage of TiCl3 solution may be related to the growth process. In the present work, TiO2 nanorods were grown on SiO2 nanofibrous membranes using a two-step hydrothermal method by controlling the dosage of TiCl3 solution in the first step hydrothermal reaction. The TiO2 seed crystals formed in the first step hydrothermal process act as the growth points for the formation of TiO2 nanorods. With increasing the dosage of TiCl3 solution, the TiO2 seed crystals become larger, providing more growth points for the formation of TiO2 nanorods and leading to high-density TiO2 nanorods. Thus, the inhibition between each other in the later growth of TiO2 nanorods becomes obvious, resulting in the smaller size of TiO2 nanorods [Citation30,Citation31]. The FESEM characterisation further demonstrates that a large number of TiO2 nanorods are successfully grown on the SiO2 nanofibers and the morphology of the hierarchical membranes can be controlled by tuning the dosage of TiCl3 solution in the first step hydrothermal process.
Figure 2. FESEM images of (a) Pd/SiO2-TiO2-0, (b) Pd/SiO2-TiO2-0.05, (c) Pd/SiO2-TiO2-0.2, (d) Pd/SiO2-TiO2-0.5 with low magnification.
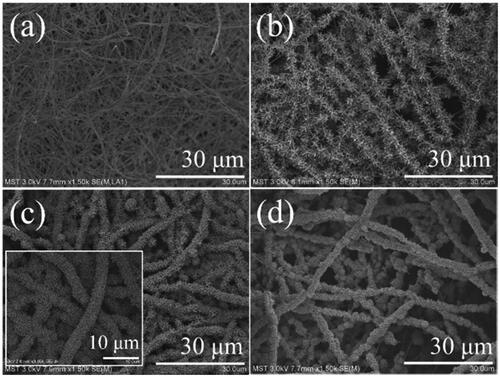
EDS analysis was performed on the four nanofibrous catalytic membranes to identify the distribution of elemental Ti and Pd. Obvious Ti signals are detected except for Pd/SiO2-TiO2-0 ( and ), which indicates that TiO2 nanorods can be covered on the membranes by two-step hydrothermal reaction, and the first step hydrothermal process is the key to the successful growth of TiO2 nanorods. Pd signals are detected on each catalytic membrane, verifying that Pd nanoparticles are loaded successfully. Furthermore, Pd signals of the nanofibrous catalytic membranes with TiO2 nanorods modification (Pd/SiO2-TiO2-0.05, Pd/SiO2-TiO2-0.2 and Pd/SiO2-TiO2-0.5) are stronger than that of Pd/SiO2-TiO2-0, which indicates that TiO2 nanorods are favourable for loading more Pd nanoparticles on the membranes ( and ). The distribution of Pd on Pd/SiO2-TiO2-0.2 is extremely intensive and uniform, illustrating that the modification with TiO2 nanorods provides optimal available surface for loading the Pd nanoparticles owing to excellent growth density and appropriate size of nanorods ().
Figure 3. EDS analysis of the catalytic membranes: (a) Pd/SiO2-TiO2-0.05, (b) Pd/SiO2-TiO2-0.2, (c) Pd/SiO2-TiO2-0.5.
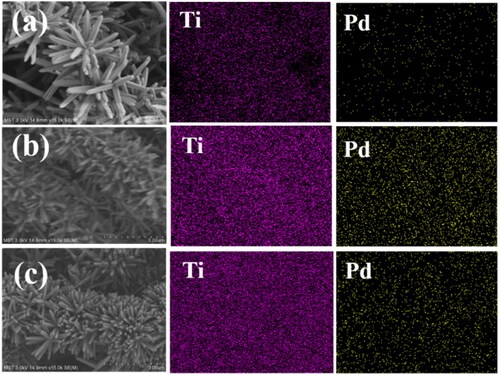
The loading amount of Pd is one of the crucial factors to determine the catalytic activity. The Pd content of the nanofibrous catalytic membranes was evaluated by ICP and the results are displayed in . The actual Pd loadings of the membranes modified with TiO2 nanorods are obviously increased from 4.05 to above 100 mg/m2. The Pd loading of Pd/SiO2-TiO2-0.2 is the highest among all samples. Pd/SiO2-TiO2-0.2 has higher N2 adsorption amount (), specific surface area (25.89 m2/g) and BJH pore volume (0.0471 cm3/g) than other catalytic membranes because of the uniformly dense TiO2 nanorods (), resulting in the increased Pd loading. The above results are well consistent with the EDS characterisation ( and ) [Citation32,Citation33].
Table 1. Pd content and BET analysis of the catalytic membranes.
shows the distribution of Pd nanoparticles in the two typical membranes: Pd/SiO2-TiO2-0 and Pd/SiO2-TiO2-0.2. The HRTEM images of Pd nanoparticles () show well resolved lattice planes of Pd with a spacing of 2.2 Å corresponding to the (111) diffraction plane [Citation34], further confirming the successful loading of Pd nanoparticles. The lattice-spacing value of 3.2 Å in Pd/SiO2-TiO2-0.2 () matches well with the (110) lattice plane of rutile TiO2 [Citation35]. In comparison with Pd/SiO2-TiO2-0, more Pd nanoparticles with an average particle size of 4 nm are uniformly distributed on TiO2 nanorods-modified SiO2 nanofibrous membrane (). The results verify that TiO2 nanorods grown on the SiO2 fibres are conducive to supporting more Pd, in line with the EDS and ICP results ( and S2, ). There is no obvious difference in the Pd particle size distribution for the two catalytic membranes (), which may be related to the preparation process of Pd/SiO2-TiO2. In this study, the Pd colloid was first prepared, and then the Pd/SiO2-TiO2 catalytic membrane was fabricated through impregnating the SiO2-TiO2 membrane in the Pd colloid as presented in Section 2.2. Furthermore, shows that many Pd nanoparticles are immobilised on the trunks of the TiO2 nanorods and SiO2 nanofibers, which can account for the higher Pd content in Pd/SiO2-TiO2-0.2 ( and ).
The XPS survey spectra in show the detailed analysis on the surface elements of Pd/SiO2-TiO2-0 and Pd/SiO2-TiO2-0.2. A Ti 2p peak is observed in the spectrum of Pd/SiO2-TiO2-0.2, further confirming the successful formation of TiO2 nanorods on the SiO2 fibre membrane (). Both of them have Pd characteristic peaks, indicating that Pd nanoparticles are successfully loaded, in agreement with the results of EDS and TEM (). Pd atomic concentrations in the Table in are 0.17% and 5.2% respectively, further illustrating that the TiO2 nanorods can markedly increase the amount of Pd loaded on the nanofibrous membrane. This result is consistent with these obtained in EDS, ICP and TEM (, supplementary material; ) characterisations. The Pd 3d XPS spectra are fitted, as shown in . The peaks at 335.4 eV and 340.5 eV are assigned to zero-valent Pd (Pd0), while the peaks at 337.1 eV and 342.6 eV can be assigned to bivalent Pd (Pd2+) [Citation36]. The existence of Pd2+ may be due to the fact that Pd2+ is not completely reduced in the preparation of PVP-Pd sol or some Pd elements are oxidised [Citation37]. Pd/SiO2-TiO2-0 and Pd/SiO2-TiO2-0.2 have similar Pd0 ratio. However, integrated into the total surface Pd content in , Pd/SiO2-TiO2-0.2 has a higher loading amount of Pd0, which contributes to the increase of catalytic activity. Compared with Pd/SiO2-TiO2-0, besides the Si4+ peak and the Si-O and -OH groups in the high resolution XPS spectra () [Citation38], Pd/SiO2-TiO2-0.2 also exhibits a Ti-O band and a Ti4+ peak [Citation39], further proving the successful formation of TiO2 nanorods.
3.2. Basic properties of nanofibrous catalytic membranes
shows the permeation performance, porosity and pore size of the as-prepared Pd/SiO2-TiO2 catalytic membranes. The pure water flux of Pd/SiO2-TiO2-0 is as high as 487600 L·m−2·h−1·bar−1 due to its super hydrophilicity, high porosity and large pore size. The permeability of the catalytic membranes decreases significantly after the modification with TiO2 nanorods, and the pure water flux of Pd/SiO2-TiO2-0.2 is the lowest, only 62395 L·m−2·h−1·bar−1. The main reason is the reduction of porosity and interconnected pore size formed by stacking thousands of nanofibers [Citation40]. The average pore diameter of Pd/SiO2-TiO2-0 is concentrated and about 1.3 μm (). The pore diameters of the as-prepared Pd/SiO2-TiO2-0.05, Pd/SiO2-TiO2-0.2 and Pd/SiO2-TiO2-0.5 membranes are decreased to about 1.1, 0.48 and 0.75 μm, respectively. High-density TiO2 nanorods can be grown on the SiO2 nanofibrous membrane (), which should be responsible for the decrease in the membrane pore diameter. With the increase of the TiCl3 dosage, the size of TiO2 nanorods coated on the SiO2 nanofibers decreases (), while the number of TiO2 nanorods increases. Under the action of the two factors, Pd/SiO2-TiO2-0.2 has the smallest pore diameter and narrow pore size distribution, resulting in the lowest pure water flux. The results also suggest that it is a feasible strategy to control the pore size of nanofibrous membranes by loading TiO2 nanorods with different sizes.
Figure 7. Basic properties of the catalytic membranes: (a) pure water permeability and porosity, (b) pore size distribution.
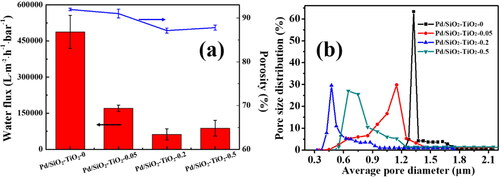
The tensile strength of the catalytic membranes is a key parameter affecting the actual applications. The typical tensile stress-strain curves of the relevant nanofibrous catalytic membranes are presented in . The tensile stress decreases from 4.03 (Pd/SiO2-TiO2-0) to 2.31 MPa (Pd/SiO2-TiO2-0.2) and the elongation at break also reduces from 1.7% to 0.75%, because that the nanostructured TiO2 nanorods filled on the fibre surface or in the gaps block the slippage of fibres during the stretching process [Citation41]. Pd/SiO2-TiO2-0 derived from the stacking of smooth nanofibers shows wonderful deformability (). Pd/SiO2-TiO2-0.2 (width 10 mm and thickness 0.15 mm) also exhibits good flexibility, which can bend and twist without breaking, and easily bear the weight of 100 cN (). Consequently, the as-prepared hierarchical Pd/SiO2-TiO2 nanofibrous catalytic membranes reveal excellent flexibility.
3.3. Catalytic performance of Pd/SiO2-TiO2 nanofibrous catalytic membranes
3.3.1. Catalytic efficiency and kinetics of PNP reduction
A catalytic membrane reactor was built via placing a piece of nanofibrous catalytic membrane in a homemade module, as shown in Scheme 3. The PNP aqueous solution was transported by using a peristaltic pump in a circulation mode. The catalytic properties of the Pd/SiO2-TiO2 catalytic membranes fabricated with different TiCl3 solution dosages were evaluated (). For all Pd/SiO2-TiO2 catalytic membranes, the only product PAP is obtained (data not shown here), in line with the reported results [Citation2,Citation12,Citation13,Citation19]. In each case, the conversion increases rapidly in the early stage of reaction and then gradually becomes stable, possibly because that NaBH4 is gradually hydrolysed as the reaction goes on, resulting in the decrease of the reaction rate [Citation42]. Interestingly, with the increase of TiCl3 solution dosage, the catalytic efficiency first rises, reaches the highest at a dosage of 0.2 mL and reduces. With respect to Pd/SiO2-TiO2-0, the conversion of PNP is only about 17% at 5 min and merely 20% after 60 min. While for Pd/SiO2-TiO2-0.2, the conversion of PNP can reach 67% with 5 min and 100% of conversion at 60 min is achieved. The catalytic activity of Pd/SiO2-TiO2-0.2 increases 5 times as compared to Pd/SiO2-TiO2-0. This can be reasonably explained that the modification with TiO2 nanorods can provide more surface area for loading Pd ( and ), resulting in higher Pd content and catalytic activity ( and ). When further increasing the TiCl3 dosage to 0.5 mL, the catalytic activity slightly decreases, and the PNP conversion is 97% at 60 min. The size reduction of nanorods and inhomogeneous coverage on the SiO2 nanofibrous membrane () lead to the reduction of surface area and Pd loading ( and ), thereby decreased catalytic activity. Unfortunately, it is seen from and , the catalytic activity of Pd/SiO2-TiO2 does not well match with the Pd content, and the increased degree of catalytic activity of Pd/SiO2-TiO2 is significantly lower than that of Pd content. A possible explanation is that some Pd nanoparticles are anchored between the TiO2 nanorods (), and thus some active Pd nanoparticles fail to function [Citation13]. In brief, these aforementioned results highlight that the modification with TiO2 nanorods can significantly promote the PNP reduction to PAP.
Figure 9. Catalytic activities of the Pd/SiO2-TiO2 catalytic membranes in the hydrogenation of PNP (PNP concentration 12 mM, molar ratio of NaBH4 to PNP 12.5, temperature 30 °C, rotation rate 30 rpm).
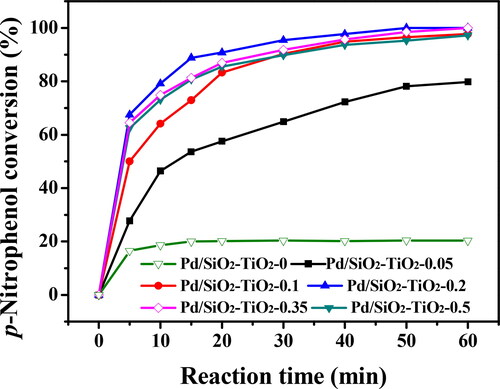
Pd/SiO2-TiO2-0.2 shows outstanding catalytic performance in the PNP hydrogenation, and the reaction kinetics of Pd/SiO2-TiO2-0.2 was further studied in the constructed flow through membrane reactor. The effects of the rotation rate of pump, PNP and NaBH4 concentrations, and reaction temperature on the initial reaction rate were investigated (). The mass transfer resistance should be considered into this typical liquid-solid two-phase reaction. According to the Mears criterion, the internal diffusion of the reaction can be negligible because of the very small size of the Pd nanoparticles (about 4.0 nm, ) [Citation43]. The external diffusion is usually associated with the flow rate of the reaction solution through the catalytic membrane controlled by the rotation rate of pump. The initial reaction rate of PNP almost keeps stable when the rotation rate exceeds 30 rpm (), illustrating that the impact of the external mass transfer resistance can be eliminated at the rotation rate larger than 30 rpm. The initial reaction rate keeps unchanged when the PNP concentration increases in the experimental range. According to the kinetic equation (EquationEq. (1)(1)
(1) ), the plot of lnCA to lnr is a horizontal straight line (), which manifests that the slope of the line is 0, i.e. the order of the reaction to PNP is 0, in line with our previous works [Citation13, Citation19]. The initial reaction rate increases with increasing NaBH4 concentration, and the slope of the linear equation between lnr and lnCB is 0.4, i.e. the reaction order to NaBH4 is 0.4 (). The result is different from some reports [Citation44,Citation45], possibly because the molar ratio of NaBH4 to PNP (just 12.5) is significantly smaller than the values (>100) in literature. As expected, the increase of reaction temperature will speed up the initial reaction rate. The slope of the linear equation between lnk and T−1 is 10.23 kJ/mol (i.e. the activation energy Ea according to the Arrhenius equation (EquationEq. (2)
(2)
(2) ), and the intercept is 11.02 mmol0.6·L−0.6·min−1 (the pre-exponential factor k0). Compared with the reported activation energies (36 kJ/mol [Citation46] and >20 kJ/mol [Citation47]), the activation energy in this work is much lower, which indicates that the PNP hydrogenation is easily to proceed on Pd/SiO2-TiO2-0.2. Smaller Pd nanoparticles () and the flow through operation mode (Scheme 3) can be responsible for the lower activation energy [Citation19].
3.3.2. Stability of the nanofibrous catalytic membrane
A simple catalytic membrane reactor device driven by gravity was constructed to test the catalytic stability of Pd/SiO2-TiO2-0.2. The colour of the reaction solution filtered through the catalytic membrane changes from yellow to transparent, and the catalytic membrane reactor can run stably over 240 min (). The results indicate that PNP can be completely and continuously converted to PAP confirmed by HPLC analysis, and the as-prepared catalytic membrane Pd/SiO2-TiO2-0.2 has an excellent catalytic stability. The recovered Pd/SiO2-TiO2-0.2 after the continuous reduction of PNP was characterised by FESEM and ICP. It is found that the morphology () and the Pd content (349.82 mg/m2) of the recovered Pd/SiO2-TiO2-0.2 are basically similar with the fresh one ( and ), further confirming the good stability of Pd/SiO2-TiO2-0.2. As shown in ,d, the catalytic membrane Pd/SiO2-TiO2-0.2 also exhibits excellent catalytic efficiency for the reduction of other nitroarenes (o-nitrophenol and m-nitrophenol). These results highlight that the as-prepared catalytic membrane Pd/SiO2-TiO2-0.2 has potential application in the conversion of PNP (‘waste’) into PAP (‘valuable’).
Figure 11. Stability of gravity-driven nanofibrous catalytic membrane reactor: (a) reduction efficiency of PNP over Pd/SiO2-TiO2-0.2, the inset is the membrane reactor device driven by gravity; (b) FESEM image of Pd/SiO2-TiO2-0.2 after continuous reaction (Reaction conditions: PNP concentration 1.2 mM, molar ratio of NaBH4 to PNP 50, temperature 25 °C, residence time 3.3 s, permeation flux 153 L·m−2·h−1); and (c, d) reduction efficiency of Pd/SiO2-TiO2-0.2 for o-nitrophenol (ONP) and m-nitrophenol (MNP), the inset shows the change of the reaction solution.
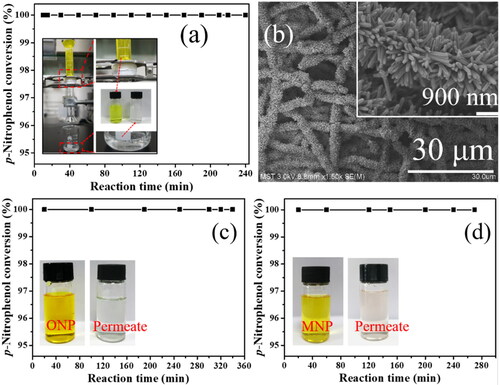
3.4. Mechanism of the p-nitrophenol reduction
Depending on the above investigations and literature [Citation48], the catalytic mechanism can be explained that BH4- and PNP are adsorbed and then promptly diffused on the surface of Pd/SiO2-TiO2 in the initial stage, and then a mass of active H are transmitted to PNP via Pd for completing the hydrogenation of PNP to PAP () [Citation17]. In our work, the conversion of PNP is conducted in a continuous penetration mode driven by gravity, which facilitates the sufficient contact between the reactants and Pd nanoparticles in the pores and enforces rapid mass transfer, leading to higher catalytic efficiency than that in batch reactors [Citation49]. Compared with what are reported in literature (), in this work, a complete transformation of higher concentration of PNP is achieved at a lower molar ratio of NaBH4 to PNP in a shorter reaction time, which may be attributed to higher Pd content () and smaller Pd nanoparticles (4 nm, ). In spite of the small size and higher content of the Pd nanoparticles loaded on the polyethersulfone membrane was obtained [Citation53], it still took a much longer time to achieve the complete conversion of PNP to PAP, which was ascribed to the dense and closed membrane pore structure. On the contrary, in this study, the nanofibrous membranes stacked and assembled by thousands of nanofibers and nanorods form a 3 D open-cell network, which has restrictive effects on the substrate molecules and directly increases their collision frequency with the supported Pd nanoparticles, thereby higher catalytic efficiency.
Table 2. Comparison of p-nitrophenol reduction by catalytic membranes.
4. Conclusions
We successfully fabricated flexible hierarchical TiO2 nanorods-modified SiO2 nanofibrous membranes (SiO2-TiO2) with high membrane porosity and surface area by electrospinning and a two-step hydrothermal method. The smaller size and higher content of Pd nanoparticles could be uniformly anchored on the SiO2-TiO2 nanofibrous membranes to fabricate Pd/SiO2-TiO2 catalytic membranes. In the p-nitrophenol reduction with NaBH4, the prepared Pd/SiO2-TiO2-0.2 nanofibrous catalytic membrane exhibited superior and stable catalytic performance with 100% conversion in the form of the flow through and penetrative operation. This work may provide a new strategy for the design and fabrication of flexible and hierarchical nanostructured inorganic nanofibrous membranes for the remediation of industrial wastewater and other potential applications.
tjen_a_1904137_sm5306.docx
Download MS Word (780.1 KB)Disclosure statement
No potential conflict of interest was reported by the author(s).
Additional information
Funding
References
- Mohsen N, Saeed Y, Foroozan H, et al. Highly efficient catalytic degradation of p-nitrophenol by Mn3O4.CuO nanocomposite as a heterogeneous Fenton-like catalyst. J Exp Nanosci. 2020;15(1):322–336.
- Wang J, Wu Z, Li T, et al. Catalytic PVDF membrane for continuous reduction and separation of p-nitrophenol and methylene blue in emulsified oil solution. Chem Eng J. 2018;334:579–586.
- Shang K, Li W, Wang X, et al. Degradation of p-nitrophenol by DBD plasma/Fe2+/persulfate oxidation process. Sep Purif Technol. 2019;218:106–112.
- Chang W, Liu S, Qileng A, et al. In-situ synthesis of monodispersed Au nanoparticles on eggshell membrane by the extract of Lagerstroemia speciosa leaves for the catalytic reduction of 4-nitrophenol. Mater Res Express. 2018;6(1):015002.
- Zhu X, Lv Z, Feng J, et al. Controlled fabrication of well-dispersed AgPd nanoclusters supported on reduced graphene oxide with highly enhanced catalytic properties towards 4-nitrophenol reduction. J Colloid Interface Sci. 2018;516:355–363.
- Borhamdin S, Shamsuddin M, Alizadeh A. Biostabilised icosahedral gold nanoparticles: synthesis, cyclic voltammetric studies and catalytic activity towards 4-nitrophenol reduction. J Exp Nanosci. 2016;11(7):518–530.
- Sardar R, Funston AM, Mulvaney P, et al. Gold nanoparticles: past, present, and future. Langmuir. 2009;25(24):13840–13851.
- Pradhan A, Gogate P. Degradation of p-nitrophenol using acoustic cavitation and Fenton chemistry. J Hazard Mater. 2010;173(1-3):517–522.
- Koklioti M, Saucedo-Orozco I, Quintana M, et al. Functionalised MoS2 supported core-shell Ag@Au nanoclusters for managing electronic processes in photocatalysis. Mater Res Bull. 2019;114:112–120.
- Yi S, Zhuang W, Wu B, et al. Biodegradation of p-nitrophenol by aerobic granules in a sequencing batch reactor. Environ Sci Technol. 2006;40(7):2396–2401.
- Tomei M, Annesini M. 4-Nitrophenol biodegradation in a sequencing batch reactor operating with aerobic-anoxic cycles. Environ Sci Technol. 2005;39(13):5059–5065.
- Lv J, Wang A, Ma X, et al. One-pot synthesis of porous Pt-Au nanodendrites supported on reduced graphene oxide nanosheets toward catalytic reduction of 4-nitrophenol. J Mater Chem A. 2015;3(1):290–296.
- Miao J, Lu J, Jiang H, et al. Continuous and complete conversion of high concentration p-nitrophenol in a flow-through membrane reactor. AIChE J. 2019;65(9):e16692.
- Wu Y-J, Wen M, Wu Q-S, et al. Ni/graphene nanostructure and its electron-enhanced catalytic action for hydrogenation reaction of nitrophenol. J Phys Chem C. 2014;118(12):6307–6313.
- Wang H, Dong Z, Na C. Hierarchical carbon nanotube membrane-supported gold nanoparticles for rapid catalytic reduction of p-nitrophenol. ACS Sustain Chem Eng. 2013;1(7):746–752.
- Fazzini S, Nanni D, Ballarin B, et al. Straightforward synthesis of gold nanoparticles supported on commercial silica-polyethyleneimine beads. J Phys Chem C. 2012;116(48):25434–25443.
- Liu K, Wang Y, Chen P, et al. Noncrystalline nickel phosphide decorated poly(vinylalcohol-co-ethylene) nanofibrous membrane for catalytic hydrogenation of p-nitrophenol. Appl Catal B–Environ. 2016;196:223–231.
- Miao J, Liu X, Jiang H, et al. Pd nanoparticles immobilized on TiO2 nanotubes-functionalized ceramic membranes for flow-through catalysis. Korean J Chem Eng. 2015;32:1759–1765.
- Liu Y, Peng M, Jiang H, et al. Fabrication of ceramic membrane supported palladium catalyst and its catalytic performance in liquid-phase hydrogenation reaction. Chem Eng J. 2017;313:1556–1566.
- Peng M, Liu Y, Jiang H, et al. Enhanced catalytic properties of Pd nanoparticles by their deposition on ZnO-coated ceramic membranes. RSC Adv. 2016;6(3):2087–2095.
- Wang J, Pei X, Liu G, et al. Gravity-driven catalytic nanofibrous membrane with microsphere and nanofiber coordinated structure for ultrafast continuous reduction of 4-nitrophenol. J Colloid Interface Sci. 2019;538:108–115.
- Yutaka T, Takuya N, Satoshi M, et al. Performance characteristics and internal phenomena of polymer electrolyte membrane fuel cell with porous flow field. J Power Sources. 2013;238:21–28.
- Afrand M, Toghraie D, Ruhani B. Effects of temperature and nanoparticles concentration on rheological behaviour of Fe3O4-Ag/EG hybrid nanofluid: an experimental study. Exp Therm Fluid Sci. 2016;77:38–44.
- Mao X, Si Y, Chen Y, et al. Silica nanofibrous membranes with robust flexibility and thermal stability for high-efficiency fine particulate filtration. RSC Adv. 2012;2(32):12216–12223.
- Zhu Q, Tang X, Feng S, et al. ZIF-8@SiO2 composite nanofiber membrane with bioinspired spider web-like structure for efficient air pollution control. J Membr Sci. 2019;581:252–261.
- Huang H, Pan L, Lim C, et al. Hydrothermal growth of TiO2 nanorod arrays and in situ conversion to nanotube arrays for highly efficient quantum dot-sensitized solar cells. Small. 2013;9(18):3153–3160.
- Wang Q, Ren H, Zhao Y, et al. Facile and mild preparation of brookite-rutile heterophase-junction TiO2 with high photocatalytic activity based on a deep eutectic solvent (DES). J Mater Chem A. 2019;7(24):14613–14619.
- Sun C, Wang N, Zhou S, et al. Preparation of self-supporting hierarchical nanostructured anatase/rutile composite TiO2 film. Chem Commun. 2008;28(28):3293–3295.
- Chen Z, Liu Z, Wei T, et al. Improved epitaxy of AlN film for deep-ultraviolet light-emitting diodes enabled by graphene. Adv Mater. 2019;31(23):1807345.
- Liu Y, Tang A, Zhang Q, et al. Seed-mediated growth of anatase TiO2 nanocrystals with core-antenna structures for enhanced photocatalytic activity. J Am Chem Soc. 2015;137(35):11327–11339.
- Cui Y, Wang W, Li N, et al. Hetero-seed meditated method to synthesize ZnO/TiO2 multipod nanostructures with ultra-high yield for dye-sensitized solar cells. J Alloy Compd. 2019;805:868–872.
- Xu C, Wu J, Desai U, et al. Multilayer assembly of nanowire arrays for dye-sensitized solar cells. J Am Chem Soc. 2011;133(21):8122–8125.
- Dhawale D, Gujar T, Lokhande C. TiO2 nanorods decorated with Pd nanoparticles for enhanced liquefied petroleum gas sensing performance. Anal Chem. 2017;89(16):8531–8537.
- Mansouri A, Semagina N. Enhancement of palladium-catalyzed direct desulfurization by yttrium addition. Appl Catal A. 2017;543:43–50.
- Lv M, Zheng D, Ye M, et al. Densely aligned rutile TiO2 nanorod arrays with high surface area for efficient dye-sensitized solar cells. Nanoscale. 2012;4(19):5872–5879.
- Ao C, Tian P, Ouyang L, et al. Dispersing Pd nanoparticles on N-doped TiO2: a highly selective catalyst for H2O2 synthesis. Catal Sci Technol. 2016;6(13):5060–5068.
- Wang H, Wang Y, Jia A, et al. A novel bifunctional Pd-ZIF-8/rGO catalyst with spatially separated active sites for the tandem knoevenagel condensation-reduction reaction. Catal Sci Technol. 2017;7(23):5572–5584.
- Liu G, Wang G, Hu Z, et al. Ag2O nanoparticles decorated TiO2 nanofibers as a p-n heterojunction for enhanced photocatalytic decomposition of RhB under visible light irradiation. Appl Surf Sci. 2019;465:902–910.
- Bao W, Liang X, Liu Y, et al. Effects of AC and DC corona on the surface properties of silicone rubber: characterization by contact angle measurements and XPS high resolution scan. IEEE Trans Dielect Electr Insul. 2017;24(5):2911–2919.
- Awang C, Dayang N, Ismail A, et al. The influence of alumina particle size on the properties and performance of alumina hollow fiber as support membrane for protein separation. Sep Purif Technol. 2020;250:117147.
- Wang X, Dou L, Yang L, et al. Hierarchical structured MnO2@SiO2 nanofibrous membranes with superb flexibility and enhanced catalytic performance. J Hazard Mater. 2017;324(Pt B):203–212.
- Neal R, Hughes R, Sapkota P, et al. Effect of nanoparticle ligands on 4-nitrophenol reduction: reaction rate, induction time, and ligand desorption. ACS Catal. 2020;10(17):10040–10050.
- Zhan G, Hong Y, Lu F, et al. Kinetics of liquid phase oxidation of benzyl alcohol with hydrogen peroxide over bio-reduced Au/TS-1 catalysts. J Mol Catal A: Chem. 2013;366:215–221.
- Chang Y-C, Chen D-H. Catalytic reduction of 4-nitrophenol by magnetically recoverable Au nanocatalyst. J Hazard Mater. 2009;165(1-3):664–669.
- Feng J, Su L, Ma Y, et al. CuFe2O4 magnetic nanoparticles: A simple and efficient catalyst for the reduction of nitrophenol. Chem Eng J. 2013;221:16–24.
- Wang Z, Chen X, Li K, et al. Preparation and catalytic property of PVDF composite membrane with polymeric spheres decorated by Pd nanoparticles in membrane pores. J Membr Sci. 2015;496:95–107.
- Bi S, Li K, Chen X, et al. Preparation and catalytic properties of composites with palladium nanoparticles and poly(methacrylic acid) microspheres. Polym Compos. 2014;35(11):2251–2260.
- Xia J, He G, Zhang L, et al. Hydrogenation of nitrophenols catalysed by carbon black-supported nickel nanoparticles under mild conditions. Appl Catal B-Environ. 2016;180:408–415.
- Domènech B, Muñoz M, Muraviev D, et al. Catalytic membranes with palladium nanoparticles: from tailored polymer to catalytic applications. Catal Today. 2012;193(1):158–164.
- Emin C, Gu Y, Remigy J, et al. Polyethersulfone hollow fibre modified with poly(styrenesulfonate) and Pd nanoparticles for catalytic reaction. Eur Phys J Spec Top. 2015;224(9):1843–1848.
- Emin C, Remigy J, Lahitte J. Influence of UV grafting conditions and gel formation on the loading and stabilization of palladium nanoparticles in photografted polyethersulfone membrane for catalytic reactions. J Membr Sci. 2014;455:55–63.
- Yin J, Zhan F, Jiao T, et al. Highly efficient catalytic performances of nitro compounds via hierarchical PdNPs-loaded MXene/polymer nanocomposites synthesised through electrospinning strategy for wastewater treatment. Chinese Chem Lett. 2020;31(4):992–995.
- Mahdavi H, Heidari A. Chelated palladium nanoparticles on the surface of plasma-treated polyethersulfone membrane for an efficient catalytic reduction of p-nitrophenol. Polym Adv Technol. 2018;29(2):989–1001.