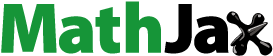
ABSTRACT
Due to the increasing interest in reducing the usage of metals in the construction sector, birch plywood has shown good potential in structural engineering and timber connections as a substitute for the more conventional slotted-in metal plate solutions. However, a proper way of bonding birch plywood with other timber parts that results in adequate connection strength has not been fully investigated. In this paper, experimental studies were carried out to investigate the proper workflow when manufacturing bonded connections made of birch plywood and spruce glulam beams. Tensile shear mechanical tests were then conducted on produced bonded joints to evaluate the bond strength. Three adhesives, i.e. melamine-urea-formaldehyde (MUF), phenol–resorcinol–formaldehyde (PRF), and two-component polyurethane (2C PUR) were evaluated in dry and moist conditions. The influence of three pressing methods, i.e. (a) screw-gluing, (b) clamping by means of clamps, and (c) clamping by application of weight loads, on the bonding strength was investigated. The bonding strength was thereafter compared with the shear strength of spruce glulam and the wood failure percentage was also examined in this study.
Introduction
In large-scale timber structures, dowel-type connections with slotted-in steel plates have been widely used (Yurrita et al. Citation2019). Comprehensive analyzes have been conducted during the last few decades for the investigation of this technique with the utilization of different timber or bamboo materials (Leng et al. Citation2020), for possible ductile or brittle failure modes (Rossi et al. Citation2016, Xu et al. Citation2021), regarding fire safety issues (Erchinger et al. Citation2010), etc. (Sandhaas Citation2012).
Recently, more interests have been raised to investigate timber-based panels as a potential alternative to the steel plates due to the growing concern in terms of the environmental impacts and economy (del Coz Díaz et al. Citation2013, Furuheim and Nesse Citation2020, Hedlund and Persson Citation2021). Moreover, when comparing the timber-to-timber and steel-to-timber bonded joints, the significant discrepancies in thermal and hygroscopical properties between timber and steel make the adoption of bonded steel-to-timber connections only feasible for relatively small bonded areas, thus with limited load-bearing capacity. Among the timber-based plates, birch (Betula pendula) plywood exhibits the combined advantages of superior mechanical properties compared to softwood species and the cross-lamination configuration, thus suitable to be applied as gusset plate in the connection system in, e.g. truss structures and moment-resisting applications (Wang et al. Citation2022a). Besides, this hardwood species is also highly resourced on the Eurasian continent (Hynynen et al. Citation2010).
When plywood plates are properly bonded to the timber parts of a joint, it would be possible to achieve higher values of both stiffness and load-bearing capacity than the mechanical connections with dowel-type fasteners (Thelandersson and Larsen Citation2003). However, the bonded joints are more difficult to be assembled on-site where the ambient conditions cannot be controlled. Currently, one potential proposal is to adhesively connect as many timber components as possible in the factory with the rest parts mechanically assembled on-site. A prototype demonstrating this hybrid concept is presented in .
Figure 1. Illustration of the hybrid concept that assembling the bonded joints in the factory and the mechanical ones on-site (Säfwe and Wåhlander Citation2021).
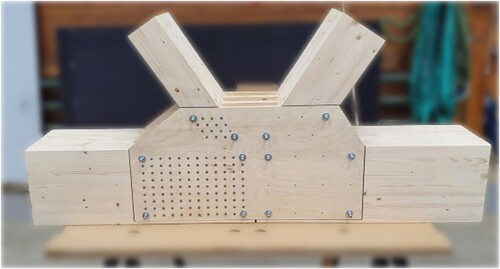
Investigations on the mechanical connection solutions have been initiated. Wang et al. (Citation2023) studied the stress distribution and failure mechanism of birch plywood when it was used as the gusset plate in timber-timber mechanical connections and proposed the spreading angle theory for the design of the gusset plate. On the other hand, the bonded joints are lack of research, in particular when it comes to how to bond spruce (Picea abies) glulam and birch plywood. The research questions, including which type of adhesive should be used and what bonding procedure should be adopted, ought to be studied in the first place on the research level.
Based on a comprehensive literature study, three types of adhesives, i.e. melamine-urea-formaldehyde (MUF), phenol–resorcinol–formaldehyde (PRF), and two-component polyurethane (2C PUR), were selected in this paper.
Choi et al. (Citation2020) carried out block shear tests to examine the bonding strength and failure mode between hardwood (mixed light hardwood) plywood and softwood (larch (Larix kaempferi) and Douglas fir (Pseudotsuga menziesii)) lamina by using polyvinyl acetate (PVAc) and PRF. Nearly 100% wood failure was observed on both PVAc and PRF specimens. It is known that PVAc cannot be introduced for structural purposes owing to its thermoplastic characteristic. On the other hand, PRF, with its thermosetting property, outstanding fire and moisture resistance, was a conventional choice for spruce glulam production in Sweden (Crocetti et al. Citation2011). Additionally, PRF is also employed to bond acetylated birch veneers to manufacture plywood (Wang et al. Citation2022b).
In recent years, MUF takes a considerable hold in the glulam industry with an esthetic advantage compared to PRF (Crocetti et al. Citation2011, Blaß and Sandhaas Citation2017, Martins et al. Citation2019). Only few studies have been found on the gluability of spruce glulam and birch plywood. In the studies of Furuheim and Nesse (Citation2020) and Hedlund and Persson (Citation2021), birch plywood gusset plates were glued to spruce glulam by using MUF. Both studies aimed to investigate the failure mechanism of birch plywood in the connection system. Therefore, the specimens were designed in such a way that failure of birch plywood would take place prior to bond line failure. See the frame tested by Hedlund and Persson (Citation2021) in . However, premature failure in the bond line occurred in some specimens with a small part of wood fiber remaining and with the average bonding stress less than 2 MPa (Hedlund and Persson Citation2021). This relatively low value of shear strength and low wood failure percentage (WFP) might be attributed primarily to the low temperature during assembly (approximately 10-15°C) and some other factors. It is worth noting that the bonding performance is strongly dependent on adhesive types and process-related parameters (Marra Citation1992, Bastani et al. Citation2016, Gavrilović-Grmuša et al. Citation2016, Alade et al. Citation2022, Hänsel et al. Citation2022, Slabohm and Militz Citation2022), e.g. mixing ratio, the surrounding environment during and after assembly, assembly time, and pressing methods, etc. Consequently, the premature failure in the bond line not necessarily indicated that the MUF adhesive system could not work.
Figure 2. Bonded joints in the tested specimen (Hedlund and Persson Citation2021).
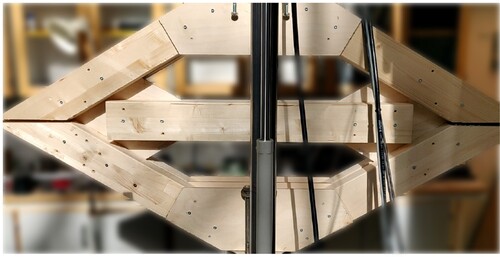
A few researchers (Boruszewski et al. Citation2011, Morin-Bernard et al. Citation2020) have investigated the bonding strength of solid birch timber (Betula pubescens, Betula alleghaniensis, and Betula papyrifera) by using 2C PUR. They found that solid birch could be effectively bonded with 2C PUR adhesive.
Kilde et al. (Citation2006) examined the bonding quality of birch timber by using different types of adhesives. It was found that the test series using one-component polyurethane (1C PUR) did not achieve as good results as the others using MUF, PRF, emulsion polymer isocyanate (EPI), and epoxy, with lower bonding strength, lower wood failure percentage, and higher variations. Hence, 1C PUR was not selected in this study.
The possibilities of bonding softwood and hardwood laminations into hybrid glulam beams or cross-laminated timber panels were investigated by some researchers (Aicher et al. Citation2016, Sciomenta et al. Citation2022). The primary bonding in these engineered wood products is normally formed by hydraulic, pneumatic, or vacuum pressing methods (Aicher et al. Citation2021).
However, for the bonded joints in timber connections (see and ), especially for large-scale timber structures, the screw press gluing method is a simpler pressing method (Schiere et al. Citation2018). In order to investigate how the pressing methods influence the bonding quality, two other pressing methods, namely, clamping by means of clamps and application of loads, were adopted.
The aim of this work is to investigate the structural performance of adhesively bonded joints between spruce glulam and birch plywood by conducting longitudinal tensile shear tests. Different parameters in the workflow when manufacturing the adhesive connections were investigated. Three types of adhesives and three pressing methods were evaluated by checking the bonding strength and wood failure percentage. Each type of adhesive was tested in both dry and moist conditions after the gluing was completed in the dry state. At the end of the study, the authors presented an insight into the adhesively bonding solutions.
Materials and methods
Materials
Timber materials
Spruce glulam beams GL28cs (EN 14080 Citation2013) with cross-sectional dimensions of 42 mm × 180 mm were produced by Moelven (Töreboda, Sweden) and used for the experiments. Then they were resawn for the preparation of the specimens.
The utilized birch plywood consists of 11 veneers with a nominal total thickness of 15 mm. The inner 9 veneers have identical thicknesses while the face veneers are slightly thinner due to the sanding process in the production line. Phenol formaldehyde resin was used between each veneer for the production of plywood by Koskisen (Järvelä, Finland).
Adhesives
Three types of adhesives with associated hardeners were evaluated in this paper:
MUF (Prefere 4546/5022) (Dynea, Lillestrøm, Norway)
PRF (Aerodux 185/ HRP 155) (Dynea, Lillestrøm, Norway)
2C PUR (Aro-Bond 925) (Ureka, Bristol, UK)
It is noted that the selected MUF and PRF adhesive systems are approved for structural purposes (Materialprüfungsanstalt, Otto-Graf-Institut (MPA) Citation2023) in Europe while the last 2C PUR adhesive system has not been specifically approved for load-bearing constructions. Nevertheless, this 2C PUR system exhibited satisfying performance in the preliminary test campaign. Considering that the studies in this paper are on the research level, it is of secondary importance in terms of the approval of the adhesive system.
illustrates the mixing ratio, solid content, application amount, assembly time, pressing temperature, and pressing time based on the technical data sheet and the results from a preliminary test campaign. The parameters optimized after performing the preliminary test series are underlined in . The open assembly time refers to the time from glue application until the assembly and the close assembly time indicates the time from assembly until pressure is established.
Table 1. Adhesive and process-related parameters.
The mixing ratio between the adhesive and the hardener for MUF ranges from 10:1 pbw to 1:1 pbw in the technical data sheet. It was found from the preliminary test campaign that the specimen with the ratio of 10:1 pbw showed cohesion failure in adhesive or adhesion failure at the adhesive-birch plywood interphase while the one with the ratio of 1:1 pbw possessed more wood failure and remarkably higher bonding strength. Consequently, MUF was mixed with the ratio of 1:1 pbw in the formal test campaign. All types of adhesives were applied to both glulam and plywood surfaces with an application amount of 400 g/m2 on each surface. The application amount was controlled by measuring the mass of each part of timber before and after the adhesive application. The open assembly time was kept as short as possible. The close assembly time was 20 and 50 min for MUF and PRF respectively, optimized from the preliminary test campaign. The close assembly time allows water to absorb into the wood for better adhesion. No close assembly time was set for 2C PUR specimens, however, 2C PUR was applied 10 min after mixing the two components so as to increase the viscosity for the help of the adhesive transfer and penetration in the bonded area (Frihart and Hunt Citation2010). According to the preliminary test results, this would be beneficial compared to applying 2C PUR immediately after mixing in terms of both bonding strength and wood failure percentage. For the screw-gluing method, screws were not withdrawn since it would be the same case in practical applications. Thus, the pressing time for the screw-glued specimens is not listed in .
Pressing apparatus
Three pressing methods were assessed for each type of adhesive, i.e. screw-gluing, clamping by means of clamps, and application of weight loads.
The specifications with regard to the screw-gluing pressing method are described in the German standard DIN Citation1052–Citation10 (Citation2012) and the Austrian standard ÖNORM B Citation1995-Citation1-Citation1 (Citation2019). It is recommended to use partially threaded counter head or washer head screws. No thread should be within the added material (birch plywood in this case). An alternative could be the fully threaded screw with different thread angles. In this study, 50 mm-long partially threaded counter head screws with milling and drilling ribs were used. The threaded length is 30 mm and the outer diameter is 4 mm. Before inserting the screws, the specimens were predrilled with a diameter of 2.8 mm. Given that the screw head is too small to generate sufficient pressure on the whole bonding area, i.e. 40 mm × 40 mm, an extra washer with an outer diameter of 30 mm was positioned beneath the screw head to spread the pressure. The screwdriver (DeWALT DCD790, USA) with the maximum torque of 60 Nm was switched to the drill mode and setting 1 (low speed/high torque) when tightening the screw. Moreover, the same type of clamp (Luna, Sweden) with the maximum force of 1500 N was used.
Although the pressure from screw-gluing and clamping by clamps are not straightforwardly quantified, it is expected that the clamping by applying weight loads created the lowest pressure. The steel block with a mass of 1.8 kg was put on the top of the bonding area, creating a pressure of around 0.01 MPa. This method is referred to as ‘steel block’ for short in the following text. See for the pressure establishment on specimens with three types of adhesives.
Specimen preparation
Before applying the adhesive, the bonded surfaces were sanded. Moisture content (MC) was measured on glulam and plywood pieces from the same batch by using the oven-dry method described in EN Citation322 (Citation1993). The mean MC during assembly was determined to be 10.2% and 9.6% for spruce glulam and birch plywood, respectively.
After the assembly, all the specimens were conditioned in a climate room with the temperature (T) of 20°C and the relative humidity (RH) of 65% for two weeks. The specimens tested in this condition were denoted as ‘dry condition’ specimens. As a comparison, the ‘moist condition’ specimens were furthermore conditioned in another room (T = 20°C and RH = 95%) for five days before testing. Density and MC measured on ‘dry condition’ specimens are respectively 492.0 kg/m3 and 11.8% for spruce glulam, and 682.9 kg/m3 and 10.5% for birch plywood. MC of ‘moist condition’ specimens was 18.0% for both spruce glulam and birch plywood. It is worth noting that the pre-treatment method utilized in this paper to examine the adhesive performance in the moist condition corresponds to the service class 2 in EN Citation1995-Citation1-Citation1 (Eurocode Citation5 (Citation2004)) where the average MC of most softwoods will not exceed 20%. It is considered to be adequate as the bonded joints are planned to be used in potential indoor applications, where the bond line would not be soaked into water but is likely to be exposed to high humidity.
Moreover, based on the results from the preliminary test campaign, most wood failures were observed in spruce glulam rather than in birch plywood. Thus, the shear strength of spruce glulam should be determined as a reference value for the strength of the adhesively bonded specimens. The characteristic shear strength of spruce glulam GL28cs is reported in the handbook (Crocetti et al. Citation2011), which is 3.5 MPa. However, the shear strength with the same cross-section as the bonded ones (40 mm × 40 mm) might be higher than the reported value due to the size effect. Accordingly, the shear strength of glulam was experimentally evaluated. Glulam specimens were tested in both ‘dry condition’ and ‘moist condition’. See for detailed information regarding the test series and replicates.
Table 2. Information regarding the test series and replicates.
Test method
Several standards, e.g. EN 14080 (Citation2013), ASTM D4680 (Citation2017), and ASTM D905 (Citation2021), describe the test method for determining the strength properties of adhesive bonds in shear. A single lap joint is suggested in these standards with the bonding area varying from 200 mm2 to approximately 2000 mm2. The specimens are loaded either in compression or in tension. In this study, the bonding area of 1600 mm2 (40 mm× 40 mm) was chosen and the longitudinal tensile shear test was conducted. The loading axis is parallel to both glulam grain direction and plywood face grain direction. See for the adhesive test setup and configuration.
As displayed in , the upper part of the glulam was fixed onto a steel fixture on the test machine, and the lower part of birch plywood was gripped. It is noted that, neither the test setup adopted in this study nor the ones suggested in the testing standards could exclude the tensile peeling stress, i.e. the tensile stress perpendicular to the bonded surface because there is always an eccentricity between the bond line and the load application plane. However, how the peeling stress would affect the estimation of the bonding strength in pure shear is uncertain. In this specific study, one screw was inserted in the center of the bonding area in each specimen totake the potential peeling stress during the load as its axial stiffness is remarkably higher than the stiffness of the adhesive bonding in the normal direction of the bonded surface (Serrano Citation2000, Larsson et al. Citation2016, Shi et al. Citation2020). For the screw-glued specimens, screws were simply not withdrawn before the tests; for the specimens with other pressing methods, screws were inserted right before the tests. The influence of the screw on the tested bonding strength was further discussed in the section ‘Results and discussion’.
The glulam shear test setup and configuration are shown in .
All the tests were carried out on the MTS 810 universal testing machine with a constant loading head motion of 2 mm/min. The bonding strength () is defined as the maximum force () during the load divided by the bonding area (
). Wood failure percentage was assessed through visual inspection to the nearest 10% for each specimen according to EN Citation314-Citation1 (Citation2004). The shear strength (
) of the spruce glulam is defined similar to the bonding strength, i.e. the maximum force divided by the shearing area.
In order to evaluate the influence of the adhesive types and the pressing methods on the bonding strength, a two-way analysis of variance (ANOVA) was employed. The significance level was set at 0.05. If the p-value (probability value) of the statistical test is lower than the significance level, it can be concluded that the influence is statistically significant. On this basis, the Tukey post-hoc test was further conducted to specify which group is significantly different from other groups.
Results and discussion
Bonding strength
To study the structural performance of adhesively bonded joints between spruce glulam and birch plywood, the tensile shear tests were performed with three types of adhesives (MUF, PRF, and 2C PUR) and three pressing methods (screw-gluing, clamping, and steel block) in both dry and moist conditions. See for the bonding strengths in the dry condition (T = 20°C and RH = 65%), with the shear strength of spruce glulam as a reference.
Figure 6. Bonding strengths with three types of adhesives and pressing methods in the dry condition. The error bars denote the standard deviation.
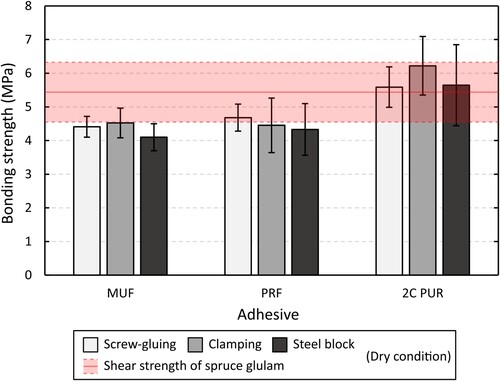
As shown in , regardless of the pressing methods, the specimens bonded with 2C PUR exhibit the highest bonding strength, over 5 MPa, while the ones with MUF and PRF possess lower but similar bonding strength properties (4-5 MPa). Moreover, the mean longitudinal shear strength of spruce glulam was experimentally evaluated to be 5.4 MPa, with the standard deviation of 0.9 MPa. It is found that all the bonding strengths are within or close to the pink region representing the mean shear strength of spruce glulam one standard deviation.
Two-way analysis of variance (ANOVA) reveals that the bonding strength has significant difference in terms of the adhesive types (p < 0.001) but the influence of the pressing methods (p = 0.353) or the interaction between the adhesive types and the pressing methods (p = 0.739) is not significant. According to the Tukey post-hoc test results, the specimens bonded with 2C PUR has significantly higher bonding strength than the ones bonded with MUF and PRF (p < 0.001). The bonding strengths with MUF and PRF show no significant difference between each other (p = 0.841).
The higher bonding strength with 2C PUR could be possibly explained by a more even shear stress distribution along the bond line. A few researchers commented that PRF and MUF are stiffer than PUR (one component or two components) (Müller et al. Citation2005, Lehringer and Gabriel Citation2014, Vallée et al. Citation2017, Bockel et al. Citation2020). The adhesives with high shear modulus tend to exhibit shear stress concentration at the end of the bond line; the shear stress distribution is, however, more homogenous for less stiff adhesives (Gustafsson Citation2002, Müller et al. Citation2005). The non-uniform stress distribution would result in the underestimation of the bonding strength (Serrano Citation2004), which might be the cause for the lower bonding strength with MUF and PRF in this study.
It is aforementioned that the pressing method is not a significant factor for the bonding strength between birch plywood and spruce glulam. Nevertheless, there is no doubt that screw-gluing is more suitable for structural applications due to its ease of operation.
As noted in the section ‘Materials and methods’, a screw was inserted in the specimen to take the potential peeling stress. The influence of the screw on the bonding strength was investigated by conducting supplementary tests. In the supplementary tests, the specimens were bonded by using PRF and screw-gluing pressing method. Then, the screw was withdrawn before loading. It was found that the bonding strength with or without the screw showed no significant difference at the significant level of 0.05. This might be attributed to: firstly, the slip modulus of a single screw (4 mm outer diameter) is much lower than the shear stiffness of a large bonded area of 1600 mm2. The force in the loading direction was thus mostly taken by the bonded connection instead of the screw; secondly, the peeling stress is usually high close to the edge and low in the center area of the bond line (Thelandersson and Larsen Citation2003, Serrano Citation2004). In this study, the screw was inserted in the center of the bonded area since it also served the purpose of applying pressure during assembly. Consequently, the peeling stress taken by the screw might be negligible. Therefore, the influence of the screw in the bonded area could be neglected in this context. Besides, the bonding shear strength of the specimens without the screw is also within the range of the glulam shear strength. It indicates that the interaction effect between the peeling stress and bonding shear stress is not pronounced in this test.
Moreover, test results in the moist condition are presented and compared to the bonding test results in the dry condition in . Although the mean shear strength of spruce glulam in the moist condition (3.8 MPa) is 30% lower than its shear strength in the dry condition, the bonding strengths in the moist condition only decrease 6.4%, 4.4%, and 6.2% for the MUF, PRF, and 2C PUR specimens, respectively. Slabohm and Militz (Citation2022) compared the bonding shear strength of untreated beech LVL in dry condition and wet condition (after 24 h immersing in water). Slight difference was also found when commercial PRF adhesives were used. Satisfactory bonding performance is unveiled for all the adhesives tested in the context of this paper. The slight reduction also implies the effectiveness of the adhesives to be applied in indoor structures.
Wood failure percentage
The mean wood failure percentage (WFP) of each test series is listed in . Nearly 100% total WFP was observed for the specimens bonded with PRF. It is noticed that all the test series in the dry condition show at least 75% total WFP except the MUF and 2C PUR ones pressed by the steel block (52% and 36%).
Table 3. Mean wood failure percentage of each test series.
Furthermore, the difference of the WFP between the dry and moist specimens was also analyzed. For the specimens bonded with MUF, the ‘moist’ ones show a certain reduction of the total WFP (46%) from the ones in the dry condition (78%). The rest area without the wood failure in the ‘moist’ specimens showed the adhesion failure between MUF and birch plywood. The total WFP of the ‘moist’ specimens bonded with PRF is not reduced; however, more failure was observed in the second veneer of the birch plywood. Lastly, for the specimens bonded with 2C PUR, the WFP difference is rather limited between the dry and moist specimens. Considering that the reduction of the bonding strength in the moist condition is similar between the three adhesives, the adhesion failure in MUF specimens is thus negligible and the slight reduction of the bonding strength in the moist condition is mainly attributed to the reduced shear strength of the wood adherents.
As shown in , the total WFP can be subdivided into glulam failure and birch plywood failure. See examples of WFP evaluation to the nearest 10% in . Despite the major wood failure in glulam, a small percentage of wood failure occurred in birch plywood. Failure in both face veneer and the second veneer was observed in birch plywood (see (b)). In the longitudinal direction, the shear strength of the birch veneer (the face veneer) should be higher than that of spruce glulam due to the higher density of birch. However, the second veneer was subjected to rolling shear. The rolling shear strength of birch plywood is considerably lower than its longitudinal shear strength and even lower than the shear strength of spruce glulam. According to the handbook of birch plywood, the characteristic rolling shear strength of birch plywood in the direction parallel to the face grain is 2.62 MPa (Finnish Forest Industries Federation Citation2002). Thus, the face veneer and the second veneer of birch plywood, as the wood adherent, were involved but played different roles in resisting the tensile shear stress.
In this study, glulam and birch plywood had their grain and face grain directions parallel to the loading axis. In practical situations, e.g. in glulam truss connections, birch plywood gusset plates would connect the glulam truss elements in different directions (see and ). The bonding performance might be influenced by the face grain angle of birch plywood as the role of the face veneer and the second veneer is different from the case studied herein, which is worth investigating in the future.
Conclusions
In this paper, the possibility of adhesively bonding spruce glulam and birch plywood has been experimentally studied. The tensile shear test results indicate that the specimens bonded with 2C PUR exhibit the highest bonding strength (over 5 MPa), higher than the ones bonded with MUF and PRF (4-5 MPa) regardless of the pressing methods, which might be attributed to the more even shear stress distribution along the bond line for the less stiff 2C PUR. A two-way analysis of variance reveals that the influence of the pressing methods on the bonding strength is not significant. However, screw-gluing is recommended due to the ease of operation in the potential structural uses. All three types of adhesives show satisfactory bonding performance in the moist condition.
It is found that the bonding strength is close to the shear strength of spruce glulam and most wood failure occurred in glulam. This finding only holds true in this study when the grain of glulam and the face grain of birch plywood are parallel to the loading axis. How the face veneer and the second veneer contribute with the change of load-to-face grain angles is the next research question to be studied. In addition, the bonding strength is also highly related to the bonded size. Experimental studies should be carried out in the future to study the size effect of the bonding strength by varying the bonded area from small (e.g. the size adopted in this paper) to large (e.g. the size in large-scale timber structures).
Undoubtedly, the properties tested herein, i.e. bonding strength and wood failure percentage, are essential factors if one would like to choose one type of adhesive for structural purposes; but they are not the only decisive ones. Other factors, e.g. fire resistance, gap-filling property, formaldehyde emissions, and economy, etc., should also be taken into consideration.
Acknowledgements
The authors wish to gratefully acknowledge China Scholarship Council, Svenskt Trä, Vinnova project 2017-02712 “Outdoor load-bearing timber structures” within the BioInnovation program and Vinnova project 2021-03681 “Rational building systems for medium to long-span timber structures” within the strategic innovation program for Production2030 for the financial support. Dynea is sincerely acknowledged for supplying the MUF and PRF adhesives. Koskisen is thanked for supplying the birch plywood materials and Moelven is acknowledged for supplying the glulam materials. CBI Betonginstitutet AB is thanked for the sample conditioning in the climate rooms.
Data availability statement
The data that support the findings of this study are available from the corresponding author upon request.
Disclosure statement
No potential conflict of interest was reported by the author(s).
Additional information
Funding
References
- Aicher, S., Hirsch, M. and Christian, Z. (2016) Hybrid cross-laminated timber plates with beech wood cross-layers. Construction and Building Materials, 124, 1007–1018. doi:10.1016/j.conbuildmat.2016.08.051
- Aicher, S., Zisi, N. and Simon, K. (2021) Screw-gluing of ribbed timber elements – effects of screw spacing and plate stiffness on bond line cramping pressure. Otto-Graf-Journal, 20, 9–38.
- Alade, A. A., Naghizadeh, Z., Wessels, C. B., Stolze, H. and Militz, H. (2022) Adhesion performance of melamine-urea–formaldehyde joints of copper azole-treated Eucalyptus grandis at varied bonding process conditions. Construction and Building Materials, 314, 125682. doi:10.1016/j.conbuildmat.2021.125682
- ASTM D4680-98 (2017) Standard Test Method for Creep and Time to Failure of Adhesives in Static Shear by Compression Loading (Wood-to-Wood) (West Conshohocken, PA: ASTM International).
- ASTM D905-08 (2021) Standard Test Method for Strength Properties of Adhesive Bonds in Shear by Compression Loading (West Conshohocken, PA: ASTM International).
- Bastani, A., Militz, H., Adamopoulos, S. and Rohumaa, A. (2016) Development of bonding strength of modified birch veneers during adhesive curing. Wood Research, 61(2), 205–214.
- Blaß, H. J. and Sandhaas, C. (2017) Timber Engineering-Principles for Design (Karlsruhe: KIT Scientific Publishing).
- Bockel, S., Harling, S., Konnerth, J., Niemz, P., Weiland, G., Hogger, E. and Pichelin, F. (2020) Modifying elastic modulus of two-component polyurethane adhesive for structural hardwood bonding. Journal of Wood Science, 66(1), 1–10. doi:10.1186/s10086-020-01917-9
- Boruszewski, P. J., Borysiuk, P., Mamiński, MŁ and Grześkiewicz, M. (2011) Gluability of thermally modified beech (Fagus silvatica L.) and birch (Betula pubescens Ehrh.) wood. Wood Material Science and Engineering, 6(4), 185–189. doi:10.1080/17480272.2011.598239
- Choi, G. W., Yang, S. M., Lee, H. J., Kim, J. H., Choi, K. H. and Kang, S. G. (2020) A study on the block shear strength according to the layer composition of and adhesive type of ply-lam CLT. Journal of the Korean Wood Science and Technology, 48(6), 791–806. doi:10.5658/WOOD.2020.48.6.791
- Crocetti, R., Johansson, M., Johnsson, H., Kliger, R., Mårtensson, A., Norlin, B., Pousette, A. and Thelandersson, S. (2011) Design of timber structures.
- del Coz Díaz, J. J., Nieto, P. G., Martínez-Luengas, A. L., Domínguez, F. S. and Hernández, J. D. (2013) Non-linear numerical analysis of plywood board timber connections by DOE-FEM and full-scale experimental validation. Engineering Structures, 49, 76–90. doi:10.1016/j.engstruct.2012.11.003
- DIN 1052-10 (2012) Design of Timber Structures – Part 10: Additional Provisions (Berlin: German Institute for Standardization (DIN)).
- EN 14080 (2013) Timber Structures – Glued Laminated Timber and Glued Solid Timber – Requirements (Brussels: European Committee for Standardization (CEN)).
- EN 1995-1-1 (2004) +A1:2008 Eurocode 5: Design of Timber Structures - Part 1-1: General - Common Rules and Rules for Buildings (Brussels: European Committee for Standardization (CEN)).
- EN 314-1 (2004) Plywood - Bonding Quality - Part 1: Test Methods (Brussels: European Committee for Standardization (CEN)).
- EN 322 (1993) Wood-Based Panels – Determination of Moisture Content (Brussels: European Committee for Standardization (CEN)).
- Erchinger, C., Frangi, A. and Fontana, M. (2010) Fire design of steel-to-timber dowelled connections. Engineering Structures, 32(2), 580–589. doi:10.1016/j.engstruct.2009.11.004
- Finnish Forest Industries Federation (2002) Handbook of Finnish plywood. https://www.koskisen.com/file/handbook-of-finnish-plywood/.
- Frihart, C. R. and Hunt, C. G. (2010) Adhesives with wood materials: bond formation and performance. Wood handbook: wood as an engineering material: chapter 10. Centennial ed. General Technical Report FPL; GTR-190. Madison, WI: US Dept. of Agriculture, Forest Service, Forest Products Laboratory, 2010: p. 10.1-10.24, 190, 10-1.
- Furuheim, E. F. and Nesse, P. M. (2020) Beam-column Connections in Glulam Structures, with Gusset Plates of Birch Plywood and Self-Tapping Screws. Master Thesis (Ås, Norway: Norwegian University of Life Sciences).
- Gavrilović-Grmuša, I., Dunky, M., Djiporović-Momčilović, M., Popović, M. and Popović, J. (2016) Influence of pressure on the radial and tangential penetration of adhesive resin into poplar wood and on the shear strength of adhesive joints. Bioresources, 11(1), 2238–2255. doi:10.15376/biores.11.1.2238-2255
- Gustafsson, P. J. (2002) Adhesive joints. Cost Action E13–Wood Adhesion and Glued Products, COST, 79-122.
- Hänsel, A., Sandak, J., Sandak, A., Mai, J. and Niemz, P. (2022) Selected previous findings on the factors influencing the gluing quality of solid wood products in timber construction and possible developments: A review. Wood Material Science & Engineering, 17(3), 230–241. doi:10.1080/17480272.2021.1925963
- Hedlund, P. and Persson, P. (2021) Complex Stress States In Structural Birch Plywood: An Experimental Study on the Behavior of Birch Plywood in Structural Applications. Master Thesis (Stockholm, Sweden: KTH Royal Institute of Technology).
- Hynynen, J., Niemistö, P., Viherä-Aarnio, A., Brunner, A., Hein, S. and Velling, P. (2010) Silviculture of birch (Betula pendula Roth and Betula pubescens Ehrh.) in northern Europe. Forestry, 83(1), 103–119. doi:10.1093/forestry/cpp035
- Kilde, V., Solli, K. H., Pitzner, B., Lind, P. and Bramming, J. (2006) Bjørk i Synlige Konstruksjoner (Oslo, Norway: Norsk Treteknisk Institutt).
- Larsson, G., Gustafsson, P. J., Serrano, E. and Crocetti, R. (2016) Bond line models of glued wood-to-steel plate joints. Engineering Structures, 121, 160–169. doi:10.1016/j.engstruct.2016.04.053
- Lehringer, C. and Gabriel, J. (2014) Review of recent research activities on one-component PUR-adhesives for engineered wood products. Materials and joints in timber structures, 405-420.
- Leng, Y., Xu, Q., Harries, K. A., Chen, L., Liu, K. and Chen, X. (2020) Experimental study on mechanical properties of laminated bamboo beam-to-column connections. Engineering Structures, 210, 110305. doi:10.1016/j.engstruct.2020.110305
- Marra, A. A. (1992) Technology on Wood Bonding: Principles in Practice (New York: Van Norstrand Reinhold).
- Martins, C., Dias, A. M. and Cruz, H. (2019) Bonding performance of Portuguese Maritime pine glued laminated timber. Construction and Building Materials, 223, 520–529. doi:10.1016/j.conbuildmat.2019.06.143
- Materialprüfungsanstalt, Otto-Graf-Institut (MPA) (2023) Klebstoffliste I der MPA Universität Stuttgart Betreffend Geprüfte Klebstoffe im Geltungsbereich der DIN 1052-10 und mit Allgemeiner Bauaufsichtlicher Zulassung (Stuttgart).
- Morin-Bernard, A., Blanchet, P., Dagenais, C. and Achim, A. (2020) Use of northern hardwoods in glued-laminated timber: A study of bondline shear strength and resistance to moisture. European Journal of Wood and Wood Products, 78(5), 891–903. doi:10.1007/s00107-020-01572-3
- Müller, U., Sretenovic, A., Vincenti, A. and Gindl, W. (2005) Direct measurement of strain distribution along a wood bond line. Part 1: shear strain concentration in a lap joint specimen by means of electronic speckle pattern interferometry. Holzforschung, 59, 300–306. doi:10.1515/HF.2005.050
- ÖNORM B 1995-1-1 (2019) Eurocode 5: Design of timber structures - Part 1-1: General - Common rules and rules for buildings - Consolidated version with national specifications, national comments and national supplements for the implementation of ÖNORM EN 1995-1-1. Austrian Standards International, Vienna.
- Rossi, S., Crocetti, R., Honfi, D. and Hansson, E. F. (2016) Load-bearing capacity of ductile multiple shear steel-to-timber connections. In World Conference on Timber Engineering (WCTE 2016), August 22–25, 2016, Vienna, Austria, pp. 195–203.
- Säfwe, G. and Wåhlander, R. (2021) Monteringsstudie av Träfackverk med Förband av Björkplywood. Bachelor Thesis (Stockholm, Sweden: KTH Royal Institute of Technology).
- Sandhaas, C. (2012) Mechanical Behaviour of Timber Joints with Slotted-in Steel Plates. Doctoral Dissertation (Delft: Delft University of Technology).
- Schiere, M., Franke, S., Franke, B. and Müller, A. (2018) Investigation and Analysis of Press Glued Connections for Timber Structures (Bern: Bern University of Applied Sciences, Institute for Timber Construction, Structures and Architecture).
- Sciomenta, M., Spera, L., Peditto, A., Ciuffetelli, E., Savini, F., Bedon, C., Romagnoli, M., Nocetti, M., Brunetti, M. and Fragiacomo, M. (2022) Mechanical characterization of homogeneous and hybrid beech-Corsican pine glue-laminated timber beams. Engineering Structures, 264, 114450. doi:10.1016/j.engstruct.2022.114450
- Serrano, E. (2000) Adhesive Joints in Timber Engineering. Modelling and Testing of Fracture Properties. Doctoral Dissertation (Lund: Lund University).
- Serrano, E. (2004) A numerical study of the shear-strength-predicting capabilities of test specimens for wood–adhesive bonds. International Journal of Adhesion and Adhesives, 24(1), 23–35. doi:10.1016/S0143-7496(03)00096-4
- Shi, B., Yang, H., Liu, J., Crocetti, R. and Liu, W. (2020) Short-and long-term performance of bonding steel-plate joints for timber structures. Construction and Building Materials, 240, 117945. doi:10.1016/j.conbuildmat.2019.117945
- Slabohm, M. and Militz, H. (2022) Bonding performance of hot-bonded acetylated beech (fagus sylvatica L.) laminated veneer lumber (LVL). Wood Material Science & Engineering, doi:10.1080/17480272.2022.2124544
- Thelandersson, S. and Larsen, H. J. (eds.). (2003) Timber Engineering (John Wiley & Sons).
- Vallée, T., Tannert, T. and Fecht, S. (2017) Adhesively bonded connections in the context of timber engineering–A review. The Journal of Adhesion, 93(4), 257–287. doi:10.1080/00218464.2015.1071255
- Wang, T., Wang, Y., Crocetti, R. and Wålinder, M. (2022a) In-plane mechanical properties of birch plywood. Construction and Building Materials, 340, 127852. doi:10.1016/j.conbuildmat.2022.127852
- Wang, Y., Wang, T., Crocetti, R. and Wålinder, M. (2022b) Experimental investigation on mechanical properties of acetylated birch plywood and its angle-dependence. Construction and Building Materials, 344, 128277. doi:10.1016/j.conbuildmat.2022.128277
- Wang, Y., Wang, T., Persson, P., Hedlund, P., Crocetti, R. and Wålinder, M. (2023) Birch plywood as gusset plates in glulam frame via mechanical connectors: A combined experimental and numerical study. Journal of Building Engineering, 65, 105744. doi:10.1016/j.jobe.2022.105744
- Xu, M., Cui, Z., Lam, F., Xu, Q. and Chen, Z. (2021) Splitting load-carrying capacity of steel-to-laminated bamboo dowel connections with slotted-in steel plates. Journal of Building Engineering, 42, 102805. doi:10.1016/j.jobe.2021.102805
- Yurrita, M., Cabrero, J. M. and Quenneville, P. (2019) Brittle failure in the parallel-to-grain direction of multiple shear softwood timber connections with slotted-in steel plates and dowel-type fasteners. Construction and Building Materials, 216, 296–313. doi:10.1016/j.conbuildmat.2019.04.100