Abstract
Renewable and alternative fuels have numerous advantages compared with fossil fuels as they are renewable and biodegradable and provide food and energy security and foreign exchange savings besides addressing environmental concerns and socio-economic issues (Yaliwal et al. 2013. International Journal of Sustainable Engineering, doi:10.1080/19397038.2013.801530. Zhu et al. 2011a, Applied Thermal Engineering 31 (14–15): 2271–2278; Zhu et al. 2011b, Fuel 90: 1743-1750; Banapurmath, Tewari, and Hosmath 2008, Renewable Energy 33: 2007-2018; Banapurmath 2009, “Performance, Combustion and Emission Characteristics of a Single Cylinder Direct Injection CI Engine Operated on Dual Fuel Mode Using Honge Oil and Producer Gas.” PhD thesis, 1–195; Banapurmath et al. 2011, Waste and Biomass Valorization 2: 1–11). In this context, the main objective of the present work is to study methods of biofuel production such as Honge oil methyl ester (HOME) using a conventional transesterification process and bioethanol from the Calliandra calothyrsus shrub using a new pretreatment method known as hydrothermal explosion. Further, experimental investigations were carried out on a single-cylinder, four-stroke, direct-injection stationary diesel engine operating in a dual-fuel mode using HOME, bioethanol and producer gas combinations to determine its performance, combustion and emission characteristics. The performance of the dual-fuel engine was analyzed at optimized engine conditions. HOME-Bioethanol (BE) blends such as HOME+ 5% bioethanol (BE5), HOME+ 10% bioethanol (BE10) and HOME+ 15% bioethanol (BE15) were prepared by adding bioethanol to HOME (on volume basis) in different proportions ranging from 5 to 15% with an increment of 5%. In this present work, the effect of different BE blends on the performance of producer gas fuelled dual fuel engine was studied. Experimental investigation on dual fuel engine using BE5-Producer gas operation resulted in up to 4–9% increased brake thermal efficiency with decreased hydrocarbon (HC), carbon monoxide (CO) and marginally increased nitric oxide (NOx) emission levels compared to HOME-Producer gas, BE10-producer gas and BE15-producer gas mode of operation. However, it was observed that, the overall performance of BE-producer gas operation was found to be lower compared to diesel-producer gas operation.
1. Introduction
India consists of approximately 638,588 villages and 70% of the population in rural areas depends upon agriculture for their livelihood. India has a huge potential for biomass and agricultural residues, and it has been estimated that approximately 620 million tonnes of biomass reserves were available in the country during 2004–2005 and the total biomass reserve was expected to be a little more than 700 million tonnes during 2010–2011, with the possibility of 1127 million tonnes in 2024–2025. Different woody biomass and agricultural residues corresponding to a potential of about 18,000 MW and the total installed capacity of biomass-based power in India have been estimated to be 2559 MW. The country has a potential to generate an additional 20 GW of electricity from biomass residues. Owing to shortage in crude oil supply, India is still dependent on non-commercial fuel sources such as cow dung, firewood, agricultural waste and biofuels to the extent of 30–35% (Deepak and Kumar Citation2007; Scholl and Sorenson Citation1993; Nwafor Citation2003, Citation2000). India is experiencing high and volatile energy prices as well as issues related to national security for energy, and hence power generated from biomass sources is becoming increasingly important. Benefits of biomass power generation include local communities, national economy and environment pollution control, savings in foreign exchange, favourable payback periods, lower operating costs compared to diesel engine operating on fossil fuels. Therefore, the use of renewable and alternative fuels in internal combustion engines is essential. In this context, biofuels such as biodiesels and producer gas derived from different biomass feedstock can be conveniently used in a diesel engine operating in a dual-fuel mode.
Biodiesels derived from vegetable oils give slightly lower performance with reduced emission levels (Deepak and Kumar Citation2007; Scholl and Sorenson Citation1993; Nwafor Citation2003, Citation2000; Banapurmath and Tewari Citation2008; Banapurmath, Tewari, and Hosmath Citation2008). The effects of different engine parameters on the performance and emission levels of a single-cylinder diesel engine operating using biodiesel and blends with diesel fuel were investigated (Sridhar et al. Citation2005; Raheman and Ghadge Citation2008; Muralidharan and Vasudevan Citation2011; Sayin and Gumus Citation2011; Samir, Lalit, and Shashikant Citation2008). Increased brake thermal efficiency with reduced exhaust emission levels at higher compression ratio and advanced injection timing were reported in the literature for producer gas fuelled dual fuel engine (Samir, Lalit, and Shashikant Citation2008; Ramadas, Jayaraj, and Muraleedharan Citation2006; Banapurmath, Tewari, and Hosmath Citation2008; Sahoo et al. 2009; Roy et al. Citation2009). For a producer gas fuelled dual fuel engine and at fixed injection timing and compression ratio, higher exhaust gas temperature (EGT) was reported. The hydrogen content in a producer gas improves the performance of the dual-fuel operation because of its higher flame velocity and calorific value (Ramadas, Jayaraj, and Muraleedharan Citation2006, Citation2008; Singh, Singh, and Pathak Citation2007a, Citation2007b; Zhu et al. Citation2011a, Citation2011b; Roy et al. Citation2009; Sahoo, Sahoo, and Saha Citation2009). Recognizing the energy needs of the rural population, India has launched several programmes on biomass gasifier-based power plants with MW level grid connected systems, exclusively that are operating on a dual-fuel engine or 100% producer gas-fuelled spark ignition (SI) engine. In view of this, the promotion of biomass-based power generation is being encouraged in the country. Dual-fuel technology offers number of potential benefits such as fuel flexibility, lower emission levels, higher compression ratio, better thermal efficiency and easy conversion of existing diesel engines without major hardware modifications (Singh, Singh, and Pathak Citation2007a, Citation2007b; Banapurmath et al. Citation2011). Producer gas can act as a promising alternative fuel, especially for diesel engines, by substituting a considerable amount of liquid fuel. However, diesel engines cannot be operated using a producer gas without the injection of a small amount of liquid fuel because the producer gas will not ignite under the prevailing conditions of temperature and pressure. The major problem associated with producer gas-operated engines is power derating. Diesel savings up to 70–90% have been reported for dual fuelling (Sridhar et al. Citation2005; Muralidharan and Vasudevan Citation2011; Sayin and Gumus Citation2011; Samir, Lalit, and Shashikant Citation2008; Ramadas, Jayaraj, and Muraleedharan Citation2006; Banapurmath, Tewari, and Hosmath Citation2008; Banapurmath et al. Citation2011; Sahoo et al. 2009; Singh, Singh, and Pathak Citation2007a, Citation2007b). In the case of producer-gas dual fuelling, a suitable carburettor was used. An ideal carburettor can provide a mixture of appropriate pre-defined air-to-fuel (A/F) ratio to the engine over entire load range of its operation (Banapurmath, Tewari, and Hosmath Citation2008; Banapurmath et al. Citation2011; Anil et al. Citation2006; Sridhar et al. Citation2005). The use of bioethanol in biodiesel blends improves combustion behaviour and reduces emission levels significantly. Bioethanol has a much lower flash point. The mixing of ethanol in a biodiesel lowers viscosity and improves volatility. From the point of view of engine durability, blends of 15% (by vol.) bioethanol in diesel/biodiesel can be considered relatively safe (Banapurmath Citation2009). The cold flow properties will be improved when bioethanol proportion is increased in the blend of biodiesel (Shropshire and Goering Citation1982; Sayin and Gumus Citation2011; Likos, Callahan, and Moses Citation1982; Park et al. Citation2008; Meiring et al. Citation1983; Meiring, Allan, and Hansen Citation1983; Singh and Singh Citation2010).
1.1 Use of bioethanol in the compression ignition engine
Bioethanol is extracted from biomass and has a good CO2 emission balance. A diesel–bioethanol blend improves the performance of the diesel engine and lowers smoke and particulate emission levels (Likos, Callahan, and Moses Citation1982; Park et al. Citation2008). Various methods have been developed for employing the bioethanol–diesel dual-fuel operation, which can be grouped into the following three types: (1) bioethanol fumigation method (Hayes et al. Citation1988; Meiring et al. Citation1983; Meiring, Allan, and Hansen Citation1983; Park et al. Citation2008); (2) dual injection system method – this method is not considered very practical – (3) blends or emulsions of bioethanol and diesel/biodiesel using an emulsifier to mix the two fuels in order to prevent separation (Hayes et al. Citation1988; Noguchi, Terao, and Sakata Citation1996; Park et al. Citation2008). Properties of bioethanol in terms of flame velocity allow a large improvement in engine performance. Bioethanol has a very low cetane number and reduces the cetane level of diesel/biodiesel–bioethanol blends, and therefore requires the use of cetane-enhancing additives (Xingcai et al. Citation2004). Additives improve ignition delay and mitigate cycle irregularity (Chen, Shuai, and Wang Citation2007). Bioethanol has a much higher flame velocity and lower flash point than diesel fuel, requiring great precautions for handling these blends (Banapurmath and Tewari Citation2010). Anhydrous bioethanol (200 proof) does not require an emulsifying agent, whereas lower-proof bioethanol requires an emulsifying agent to form an opaque macro-emulsion. However, there is a possibility of separation of the blends into two phases when they are allowed to stagnate for a longer period (Hansen, Zhang, and Lyne Citation2005; Statge de Caro et al. Citation2001). From the point of view of engine durability, blends with up to 15% (by vol.) bioethanol in diesel/biodiesel fuel can be considered relatively safe. The cold flow properties will be improved when bioethanol proportion is increased in the blend of biodiesel–bioethanol (Muralidharan et al. Citation2004). However, the bioethanol content in fuel flow lines and engine causes corrosion-related problems because bioethanol can react with Al, brass and Cu and rubber materials and create a jam in the fuel pipe lines. Therefore, a suitable pipe made of fluorocarbon rubber is used instead of other rubber types (Hansen, Zhang, and Lyne Citation2005).
The majority of the research work is focused on the utilization of diesel/biodiesel–bioethanol blends in diesel engines. Biodiesel and bioethanol production has been investigated by many researchers (Singh and Singh Citation2010; Syed et al. Citation2009; Demirbas Citation2005; Carmen, Vinatoru, and Maeda Citation2007; Yaliwal et al. Citation2010; Marichetti, Miguel, and Errazu Citation2007; Leung, Wu, and Leung Citation2010; Furuta, Matsuhashi, and Arata Citation2006; Keskin, Guru, and Altiparmak Citation2007; Bjerre et al. Citation1996; Dien et al. Citation2006; Holtzapple et al. Citation1991; Laser et al. Citation2002; Liu and Wyman Citation2005; Mosier et al. Citation2005; Pérez et al. Citation2008). However, bioethanol production from Calliandra calothyrsus and the use of the biodiesel–bioethanol–producer gas combination in diesel engines need more detailed studies, as this area has been less investigated. Literature reviews have suggested that the combustion characteristics of producer gas-operated engines need extensive research for a long-term use in dual fuel engines. Based on the literature, it has been found that fuel properties, engine operation and design parameters play a vital role in achieving higher performance with reduced emission levels.
In the present study, an effort has been made to evaluate the feasibility of alternative renewable fuels in the form of mixed fuels [Honge oil methyl ester (HOME)–bioethanol blend and producer gas] as a complete replacement for fossil fuels. In the first phase of the study, bioethanol production was carried out by using the hydrothermal explosion of C. calothyrsus biomass. In the second phase of the study, experiments have been conducted on a single-cylinder, four-stroke, water-cooled, direct-injection compression ignition (CI) engine operated in dual-fuel mode using three types of mixed fuel combinations, namely HOME–5% bioethanol–producer gas (BE5–producer gas), HOME–10% bioethanol–producer gas (BE10–producer gas) and HOME–15% bioethanol–producer gas (BE15–producer gas). The optimum parameters for the operation of a dual-fuel engine were kept constant (Banapurmath, Tewari, and Hosmath Citation2008; Banapurmath Citation2009; Banapurmath et al. Citation2011).
2. Production of biodiesel and bioethanol for dual-fuel engine applications
HOME was produced using a conventional transesterification process. It is a standard and well-established process used to produce biodiesel. Biodiesel has properties comparable to diesel. The performance of the engine fuelled with biodiesel is lower when compared with that operated using diesel with acceptable emission levels. The performance of the engine fuelled with biodiesel is comparable to that of diesel operation with reduced emission levels. The optimum parameters for biodiesel production and better yield have been reported in the literature (Noureddini and Zhu Citation1997; Basha, Raja Gopal, and Jebaraj Citation2009; Leung, Wu, and Leung Citation2010; Vivek and Guptha Citation2004; Meher, Naik, and Das 2004). Bioethanol was produced by the hydrothermal explosion of the C. calothyrsus shrub. The optimum parameters for bioethanol production have been reported in the literature (Yaliwal et al. Citation2013). The experimental method for bioethanol production involves hydrothermal explosion, acid hydrolysis, fermentation and distillation. The stems were collected, dried and reduced to a size of 3 mm. Then, the biomass was pretreated with water in a 5-litre capacity hydrothermal unit and exploded by depressurizing the content at 5 bar after 30 min of retention time. Solids were then separated, washed, dried and stored. The solids were delignified using 10% NaOH for 2 h, followed by hydrolysis with 2% HCl at 100°C for 80 min. After filtration, the solid residue was discarded, and the liquid filtrate was neutralized with calcium carbonate and then treated with activated charcoal (1:40, w/v) for the removal of any degraded compounds (furfurals) formed. Later, glucose was quantitatively estimated using the deoxyribonucleic acid method. The medium prepared was added to the sugar solution, and 5% yeast (Saccharomyces cerevisiae) was inoculated to the hydrolysate and kept for fermentation at 35°C for 3 days in the rotary incubator at a speed of 200 rpm. After fermentation, the broth was centrifuged to separate the solid biomass from the supernatant, which was later distilled at 78°C to separate bioethanol. The properties and distillation parameters have been reported in the literature (Li et al. Citation2005; Huang, Mao, and Zhu Citation1999; Banat and Simandl Citation1999; O'Brien and Craig Citation1996). Figure shows the block diagram of bioethanol production from C. calothyrsus biomass.
2.1 HOME–bioethanol blends
If bioethanol proportion in HOME is higher than 15%, then it results in turbidity. This is affected by the water content and room temperature. In the present study, 5–15% bioethanol was mixed in the known volume of HOME. The homogeneity of the HOME and bioethanol mixture was ensured by placing the test tube containing the mixture above a black paper, and the solution without any turbidity indicated good miscibility of bioethanol in HOME (Anand, Sharma, and Mehta Citation2011). In addition, a mechanical stirrer was also used to mix HOME and bioethanol blends, as shown in Figure , to ensure further homogeneity. The fuel blends were prepared just before the commencement of the experiment to ensure that the fuel mixture is homogeneous. A solubility test was conducted at a room temperature of about 32°C. In the present study, bioethanol proportion up to 15% in HOME did not show any phase difference.
2.2 Characterization of the fuels used
Honge oil is also called Karanja oil. Its botanical name is Pongamia pinnata L., belonging to the family Leguminaceae or Papilionaceae. This tree attains a height of about 18 m and a trunk diameter of more than 50 cm. It can grow on most soil types, ranging from stony to sandy to clay. This tree bears green pods that after 10–11 months get matured and change to a tan colour in the month of May–June. The pods are elliptical, with 4–7.5 cm long. The seeds are usually elliptical, with 1.7–2 cm long and 1.2–1.8 cm broad, wrinkled with a reddish brown, leathery testa. The tree starts bearing at the age of 4–7 years, and the pods come to maturity at different periods of the year in different parts of the country, but the harvest season extends from November–December to May–June. Seed yield ranges from 9 to 90 kg/tree.
C. calothyrsus is one of the promising cellulosic feedstock for bioethanol production due to its high cellulosic content. C. calothyrsus is a small, perennial, thornless, multi-stemmed shrub, which grows 3–15 m with a trunk diameter of 0.25–0.40 m, belonging to the family Fabaceae. C. calothyrsus is naturally found abundantly in many tropical regions and can be used as fuel wood, plantation shade and reforestation. It grows on all soil types and sandy clays. The cellulose of C.calothyrsus can be harnessed for bioethanol production. The composition of the raw material was determined at our college laboratory. Cellulose and hemicellulose were determined according to the procedures of Goering and Van Soest (1970), and Klason lignin, ethanol–benzene soluble contents and ash content were determined using TAPPI Standard Test Methods T 222 om-06, T 204 cm-07, T 413 om-06, respectively. All calculations were made on an oven-dried basis, which are shown in Table .
Table 1 Composition of the C. calothyrsus shrub.
The properties of HOME and bioethanol were determined. The properties of biodiesel and bioethanol such as acid value, methanol content, distillation parameters, cetane number and cetane index have been reported in the literature (Aldo et al. Citation2012; Yaliwal et al. Citation2010; Bobade and Khyade Citation2012; Thiruvengadaravi et al. Citation2012; Khayoon, Olutoye, and Hameed Citation2012; Leung, Wu, and Leung Citation2010; Vivek and Guptha Citation2004; Meher, Naik, and Das 2004). The properties of the tested fuels are listed in Table . Table gives the typical composition of the producer gas obtained from gasification on a volumetric basis.
Table 2 Properties of the tested fuels.
Table 3 Composition of the producer gas.
3. Experimental set-up
The experiments were conducted on a Kirloskar TV1-type, four-stroke, single-cylinder, water-cooled diesel engine test rig. Figure shows the schematic of the experimental set-up. An eddy current dynamometer was used for loading the engine. The specifications of the CI engine and downdraft gasifier are given in Tables and , respectively. The engine was operated at a rated constant speed of 1500 rev/min. The engine speed was kept constant by adjusting the governor lever so that the quantity of the injected liquid fuel varied depending on the engine load, and the flow rate of the producer gas was kept nearly constant. The mass flow rates of the fuels used in the present study were measured appropriately. The downdraft gasifier was suitably connected to the engine with a filter and cooling and cleaning system. EnginSoft is a software that evaluates power, efficiencies, fuel consumption and heat release and pressure–crank angle diagram. A parallel-flow (90°) gas entry carburettor was used to maintain the air-gas mixture at nearly stoichiometric ratio. Hartridge Smoke Meter was used to measure the exhaust smoke density. The smoke meter works on the principle of comparative basis. A DELTA 1600 S Exhaust Gas Analyser was used to measure HC, CO and NOx emission levels. Tables and show the specifications of the exhaust gas analyser and smoke meter, respectively. It uses a non-dispersive infrared technology for measuring exhaust emission levels. It consists of different sensors for measuring an individual gas and pyroelectric detectors. Then, the detector output is sent to an analog-to-digital converter (ADC), and the microprocessor samples the ADC and thus provides the data.
Table 4 Specifications of the engine.
Table 5 Specifications of the downdraft gasifier.
Table 6 Specifications of the exhaust gas analyser.
Table 7 Specifications of the smoke meter.
In the present study, diesel, HOME, bioethanol and HOME–bioethanol (BE) blends were used as injected liquid fuels, and the producer gas was derived from the babul wood and used as an inducted gaseous fuel.
4. Results and discussion
The present study mainly focuses on the evaluation of the performance of a HOME–producer gas-operated dual-fuel engine. Also, the present work compares the performance of dual fuel engine operated on HOME + bioethanol–producer gas operation with HOME - producer gas and diesel-producer gas operations. The tests were conducted with different load conditions. The maximum bioethanol proportion was limited to 15% (by vol.) in steps of five. Throughout the experiment, the engine speed was kept constant. The injection timing, injection pressure and compression ratio were kept constant at 27° before top dead center, 230 bar HOME–producer gas combinations and 17.5, respectively. However, for the engine operation using diesel–producer gas, the injection pressure was varied to 205 bar. Babul wood was used as a fuel for the gasifier, and the parallel-flow (90°), gas entry carburettor was used to maintain the air–gas mixture at a stoichiometric ratio.
4.1 Performance characteristics
Figure shows the variation in brake thermal efficiency (BTE) with brake power for the diesel–producer gas and mixed fuel combinations. It was observed that over the entire power range, the HOME–producer gas combination operated at a lower BTE compared with the diesel–producer gas combination. The producer gas being common, the properties of the injected fuel had a major effect on engine performance. The lower calorific value and higher viscosity of HOME in the presence of the slow-burning producer gas resulted in a lower BTE. These results are in close agreement with those published in the literature (Parikh et al. Citation1989; Sahoo, Sahoo, and Saha Citation2009; Banapurmath, Tewari, and Hosmath Citation2008; Banapurmath Citation2009; Banapurmath et al. Citation2011).
The addition of bioethanol to HOME improved the efficiency of the dual-fuel engine. The producer gas being common, the addition of bioethanol to HOME lowered viscosity and increased volatility as well (Lapuerta, Armas, and Herreros Citation2008; Banapurmath Citation2009). This led to a more complete combustion in the fuel-rich zone due to the oxygen present in bioethanol-blended fuels. Hence, it resulted in enhanced combustion efficiency and decreased heat losses in the cylinder due to the lower flame temperature of bioethanol-blended fuels than of HOME. However, the engine operation using BE5–producer gas resulted in a slightly higher BTE than that using the BE10–producer gas and BE15–producer gas combinations. This could be attributed to the combined effect of the reduced energy content of HOME with a higher content of the bioethanol and producer gas combination. A higher latent heat of vaporization of bioethanol has a more dominating effect and leads to a more cooling effect with a higher bioethanol content compared with that of the BE5–producer gas combination. The difference in the fuel's input chemical availability might also be the reason for this observed trend. This in turn results incomplete combustion of the gaseous fuel along with HOME and excess bioethanol. It was observed that the BE15–producer gas combination resulted in a marginally similar effect to that of the HOME–producer gas combination. Therefore, a higher percentage of bioethanol addition to HOME during the dual-fuel mode of operation did not show any positive effect on engine performance. The BTE values for diesel–producer gas, HOME–producer gas, BE15–producer gas, BE10–producer gas and BE5–producer gas were found to be 18.65%, 16.12%, 15.25%, 16.89% and 17.89%, respectively, for the 80% load condition.
Figure shows the variation in EGT for the diesel–producer gas and mixed fuel combinations at all load conditions. The EGT for the diesel–producer gas combination under the dual-fuel mode was found to be lower than that for the HOME–producer gas combination. This could be attributed to the better combustion of the diesel–producer gas combination in the premixed combustion phase, leading to an enhanced BTE (Parikh et al. Citation1989; Ramadas, Jayaraj, and Muraleedharan Citation2008; Banapurmath, Tewari, and Hosmath Citation2008; Sahoo, Sahoo, and Saha Citation2009).
The addition of bioethanol to HOME improves the combustion in a dual-fuel engine. The producer gas being common, the addition of bioethanol to HOME lowers the viscosity of the blend and increases volatility as well. The addition of bioethanol to HOME biodiesel increases flame velocity and enhances oxygen in the air–fuel mixture. However, the BE10–producer gas and BE15–producer gas combinations resulted in a higher EGT compared with the BE5–producer gas combination. This could be attributed to the inadequate combustion of the gaseous fuels in the presence of a higher percentage of bioethanol in HOME under the dual-fuel mode of operation. The EGT values for the diesel–producer gas, HOME–producer gas, BE15–producer gas, BE10–producer gas and BE5–producer gas combinations were found to be 385, 498, 470, 445 and 425°C, respectively, for the 80% load conditions.
4.2 Emission characteristics
Emission characteristics of an engine are important as far as environmental aspects are concerned. Combustion quality can be represented on the basis of emission levels from the engine. The emissions from the dual-fuel engine are due to the variation in the composition of the producer gas, the type of the liquid fuel used, engine design and operating parameters. The different emission parameters during the dual-fuel mode of operation with different fuel combinations are discussed below.
Figure shows the variation in smoke opacity for the diesel–producer gas and mixed fuel combinations at all load conditions. Smoke opacity for the HOME–producer gas combination under the dual-fuel mode of operation was found to be higher compared with that for the diesel–producer gas combination. This could be attributed to the lower calorific value, improper spray pattern due to a higher viscosity of HOME in the presence of the slow-burning producer gas and free fatty acids with a heavier molecular structure compared with diesel, resulting in higher smoke emission levels. These results are similar to those published in the literature (Parikh et al. Citation1989; Banapurmath, Tewari, and Hosmath Citation2008; Banapurmath Citation2009; Sahoo, Sahoo, and Saha Citation2009; Ramadas, Jayaraj, and Muraleedharan Citation2008). It can also be due to the insufficient availability of oxygen for combustion and the high temperature of the producer gas reduces the density, which in turn reduces the quantity of the air required for the complete combustion of the fuel combination. The producer gas being common, the addition of bioethanol to HOME lowers the viscosity of the blend and increases volatility as well. The addition of bioethanol to HOME reduces the smoke emission levels of the dual-fuel engine. This is due to the fact that the presence of a bonded oxygen reduces the probability of the formation of soot nuclei in locally rich zones (Banapurmath, Tewari, and Hosmath Citation2008). The enrichment of the oxygen content in the fuel due to the addition of oxygen by both HOME and bioethanol results in a slightly better combustion compared with HOME–producer gas alone. The main reason for reduced smoke emission levels is the improved spray characteristics of the mixed fuels. It was observed that the BE5–producer gas combination resulted in lower smoke emission levels compared with the other fuel combinations. The increased smoke emission levels were observed for both BE10-producer gas and BE15-producer gas operations. It could be attributed to incomplete combustion due to reduced energy content and improper mixing of air-producer gas combination with HOME and bioethanol blend. The smoke emission level values for the diesel–producer gas, HOME–producer gas, BE15–producer gas, BE10–producer gas and BE5–producer gas combinations were found to be 32, 66, 51, 56 and 48 HSU, respectively, for the 80% load conditions.
Figures and show the variation in hydrocarbon (HC) and carbon monoxide (CO) emission levels, respectively, for the diesel–producer gas and other mixed fuel combinations at all load conditions. Both the HC and CO emission levels were higher for the HOME–producer gas combination compared with that for the diesel–producer gas combination. This could be due to the incomplete combustion of the HOME–producer gas mixture. In the case of the dual-fuel mode of operation, the incomplete combustion is due to the presence of free fatty acids in HOME and the insufficient availability of oxygen for combustion. Also, the lower calorific value of HOME and producer gas, the lower adiabatic flame temperature and higher viscosity of HOME and the lower mean effective pressure are also responsible for higher HC and CO emission levels (Parikh et al. Citation1989; Singh, Singh, and Pathak Citation2007a, Citation2007b; Ramadas, Jayaraj, and Muraleedharan Citation2008; Banapurmath, Tewari, and Hosmath Citation2008; Sahoo, Sahoo, and Saha Citation2009).
However, the addition of bioethanol to HOME reduces both the HC and CO emission levels compared with the HOME–producer gas combination. The addition of bioethanol to HOME increases the oxygen content in the fuel combination resulting slightly improved combustion. (Likos, Callahan, and Moses Citation1982; Meiring et al. Citation1983; Meiring, Allan, and Hansen Citation1983; Park et al. Citation2008; Banapurmath Citation2009). The producer gas being common, the addition of bioethanol to HOME lowers the viscosity of the blend and increases volatility as well. In addition, studies have indicated that ethanol molecules are polar, which cannot be absorbed easily by non-polar molecules in the lubricating oil layer and therefore ethanol blending in a HOME can lower the production of HC emission levels in the engine exhaust (Statge de Caro et al. Citation2001; Wyman Citation2003). It was observed that both the HC and CO emission levels were reduced upon addition of a lower content of ethanol in the blend due to the reduced viscosity and increased volatility of the fuel blend. The addition of a lower percentage of bioethanol to HOME resulted in a positive effect on combustion. This could be due to a slightly better combustion in the oxygen-rich region, resulting in slightly reduced HC and CO emission levels. However, the addition of a higher percentage of bioethanol to HOME slightly increased both the HC and CO emission levels, resulting in a marginally similar effect to that of the HOME–producer gas combination. The reason is that the cooling effect due to a higher latent heat of vaporization of bioethanol dominates the combustion.
The HC emission level values for the diesel–producer gas, HOME–producer gas, BE15–producer gas, BE10–producer gas and BE5–producer gas combinations were found to be 38, 54, 52, 48 and 44 ppm, respectively, for the 80% load condition. The CO emission level values for the diesel–producer gas, HOME–producer gas, BE15–producer gas, BE10–producer gas and BE5–producer gas combinations were found to be 0.31%, 0.47%, 0.46%, 0.45% and 0.39%, respectively, for the 80% load condition.
The NOx emission levels were found to be higher for the diesel–producer gas combination under the dual-fuel mode of operation compared with those for mixed fuel combinations over the entire load range (Figure ). This is due to the fact that a higher heat release rate during the premixed combustion phase occurs for the diesel–producer gas combination compared with that for the other fuel combinations (Singh, Singh, and Pathak Citation2007a, Citation2007b; Banapurmath, Tewari, and Hosmath Citation2008; Ramadas, Jayaraj, and Muraleedharan Citation2008; Sahoo, Sahoo, and Saha Citation2009). Compared with the HOME–producer combination, the HOME+bioethanol–producer gas combination resulted in slightly higher NOx emission levels. This could be due to a slightly better combustion that occurs in the oxygen-rich region, resulting in slightly higher NOx emission levels for the bioethanol-blended dual-fuel operation. However, the HOME–producer gas combination resulted in lower NOx emission levels compared with mixed fuel combinations. This is mainly due to the combined effect of incomplete combustion due to the higher viscosity and lower energy density of HOME along with the slow-burning nature of the producer gas. However, the BE10–producer gas and BE15–producer gas combinations resulted in a marginally similar effect to that of the HOME–producer gas combination. The NOx emission level values for the diesel–producer gas, HOME–producer gas, BE15–producer gas, BE10–producer gas and BE5–producer gas combinations were found to be 108, 84, 68, 75 and 92 ppm, respectively, at the 80% load condition.
4.3 Fuel substitution
Figure presents the fuel substitution for the dual-fuel operation at different load conditions. Fuel substitution depends on the fuels used. The results indicated that higher bioethanol blending increases fuel substitution and specific fuel consumption. This means that less fuel is consumed for the lower addition of bioethanol. The liquid fuel substitution for the diesel–producer gas operation is lower compared with that for the HOME+bioethanol–producer gas operation, which could be due to the lower cetane number and calorific value of the HOME–bioethanol blends tested. The fuel substitution values for the diesel–producer gas, HOME–producer gas, BE15–producer gas, BE10–producer gas and BE5–producer gas were found to be 60%, 57%, 52%, 53% and 56%, respectively, at the 80% load condition.
4.4 Combustion analysis
The effect of brake power on ignition delay is shown in Figure . The ignition delay is calculated based on the static injection timing. The HOME–producer gas and HOME+bioethanol–producer gas combinations show a longer ignition delay compared with the diesel–producer gas combination. This could be due to the reduced cetane number, and the presence of oxygen in the blends leads to the difference in the A/F ratio and the improper mixing of the fuel combinations used. A higher viscosity and density of HOME and the poor mixing of the fuel combinations are also responsible for this observed trend. However, the BE5 and HOME blend operation with the producer gas resulted in a lower ignition delay compared with the HOME+bioethanol blends tested. This could be attributed to better spray characteristics due to slightly reduced viscosity and improved chemical kinetics. The ignition delay values were found to be 18.44°, 17.4°, 16.88° and 15.89° CA for the HOME–producer gas, BE15–producer gas, BE10–producer gas and BE5–producer gas combinations, respectively, compared with 14.9° CA for the diesel–producer gas combination at the 80% load condition.
The combustion duration, shown in Figure , was calculated based on the duration between the start of combustion and 90% cumulative heat release. It increases with an increase in the power output for all the fuel combinations. This is due to the increase in the quantity of the fuel injected. A higher combustion duration is observed for the HOME–producer gas and HOME+bioethanol–producer gas combinations compared with the diesel–producer gas combination. This could be due to the improper mixing of the air and liquid fuel used and the reduced heat release rate obtained for the HOME–producer gas and HOME+bioethanol blends–producer gas combinations. Also, the rapid combustion phase was considerably higher for the BE5-producer gas combination compared to HOME-producer gas and other BE-producer gas combinations under the dual-fuel mode of operation. This could be attributed to the better spray characteristics of BE5 due to the reduced viscosity of HOME and improved air–fuel mixing rates along with the slow-burning nature of the producer gas. Significantly higher combustion rates during the later stages for the HOME–producer gas and HOME+bioethanol–producer gas combinations lead to higher exhaust temperatures and lower thermal efficiency. The engine operation with BE5–producer gas showed improvement in heat release rate compared with that using the HOME–producer gas and other BE–producer gas combinations. The combustion duration values were found to be 40°, 40.51°, 39.89° and 38° CA for the HOME+producer gas, BE15–producer gas, BE10–producer gas and BE5–producer gas combinations, respectively, compared with 36° CA for the diesel+producer gas combination at the 80% load condition.
Figure shows in-cylinder pressure versus crank angle for the diesel–producer gas, HOME–producer gas and HOME+bioethanol–producer gas combinations at the 80% load condition. The pressure inside the engine cylinder depends on the combustion rate, the type of the fuel combinations used and how much the fuel is taking part during the rapid combustion period. The uncontrolled combustion phase is governed by the ignition delay period and by mixture preparation during the delay period. A lower cylinder pressure was observed for the HOME–producer gas and HOME+bioethanol–producer gas combinations compared with that for the diesel–producer gas combination. This could be attributed to the combined effect of the lower calorific value of the blends and producer gas and the longer ignition delay due to improper mixing along with the slow-burning nature of the producer gas. However, a slightly higher in-cylinder pressure was observed for the BE5–producer gas combination compared with that for the HOME–producer gas, BE10–producer gas and BE15–producer gas combinations. This could be due to the improved spray characteristics of the blend BE5. Also, the lower energy content of both HOME and bioethanol is responsible for this observed trend. However, a higher blending of bioethanol with HOME lowers the energy content and dual-fuel operation in the presence of the producer gas, resulting in the observed trend. The results indicated that the peak pressure value for the diesel–producer gas combination was about 61.52 bar and for the HOME–producer gas combination was 49.2 bar, and the values for the HOME–producer gas combination with 5%, 10% and 15% bioethanol were found to be 58.1, 55.12 and 53.15 bar, respectively.
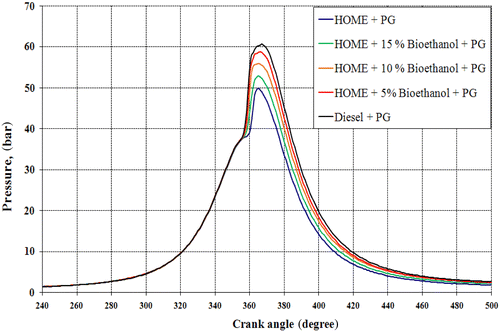
Figure shows the rate of heat release versus crank angle for the diesel–producer gas and HOME–bioethanol–producer gas combinations at the 80% load condition. It was observed that the diesel–producer gas operation resulted in a higher heat release rate compared with the HOME–producer gas and bioethanol combinations. This could be due to the differences in the combustion rate taking place during the premixed combustion phase resulting in the differences in the energy content of the fuel combinations used, and are also attributed mainly to the changes in the oxygen concentration of the charge and the chemical kinetic processes. The addition of 5% bioethanol to HOME resulted in higher heat release rates compared with the HOME–producer gas, BE10–producer gas and BE15–producer gas combinations. This may be due to the fact that the changes in fuel properties dominated during the premixed combustion phase for the BE5–producer gas operation.
5. Conclusions
From the exhaustive experiment conducted on the dual-fuel engine operated with different fuel combinations, the following conclusions were drawn:
Phase separation was not a major issue when using the lower content of bioethanol (5–15%) in biodiesel. However, beyond 15% bioethanol in biodiesel may require suitable additives to minimize turbidity. Also, the higher content of bioethanol in the HOME–producer gas operation is not suitable as the calorific value of the blend reduced with a higher latent heat of vaporization of bioethanol.
Biodiesel–producer gas operation resulted in slightly inferior performance to its counterpart diesel–producer gas combination.
BTE was decreased by 1.41%, 1.85% and 3.45% for the BE5–producer gas, BE10–producer gas and BE15–producer gas combinations compared with that for the diesel–producer gas combination. For all the BE–producer gas combinations under the dual-fuel mode of operation, emission levels such as HC, CO and smoke were reduced compared with those for the HOME–producer gas combination. However, NOx emission levels were increased considerably for the BE–producer gas combination.
Increased bioethanol percentage for the HOME–producer gas combination retarded the combustion. Maximum heat release rates for the premixed combustion and in-cylinder peak pressure were observed for 5% bioethanol and HOME-blended fuels with producer gas operation.
Notes
1. Email: [email protected]
References
- Aldo, Okullo, A. K.Temu, P.Ogwok, and J. W.Ntalikwa. 2012. “Physico-Chemical Properties of Biodiesel from Jatropha and Castor Oils.” International Journal of Renewable Energy Research2 (1): 44–52.
- Anand, K., R. P.Sharma, and P. S.Mehta. 2011. “Experimental Investigations on Combustion, Performance and Emissions Characteristics of Neat Karanji Biodiesel and Its Methanol Blend in a Diesel Engine.” Biomass and Bioenergy35: 533–541.
- Anil, T. R., S. D. Ravi, M. Shashikanth, N. K. S. Rajan, and P. G. Tewari. 2006. “CFD Analysis of a Mixture Flow in a Producer Gas Carburetor.” International Conference On Computational Fluid Dynamics, Acoustics, Heat Transfer and Electromagnetics, CFEMATCON-06, July 24–25, 2006, Andhra University, Visakhapatnam, India, 1–6.
- Banapurmath, N. R., and P. G.Tewari. 2008. “Combustion and Emission Characteristics of a Direct Injection CI Engine When Operated on Honge Oil, Honge Oil Methyl Ester (HOME) and Blends of Honge Oil Methyl Ester (HOME) and Diesel.” International Journal of Sustainable Energy1 (2): 80–93.
- Banapurmath, N. R.2009. “Performance, Combustion and Emission Characteristics of a Single Cylinder Direct Injection CI Engine operated on Dual Fuel Mode Using Honge Oil and Producer Gas.” PhD thesis1–195.
- Banapurmath, N. R., and P. G.Tewari. 2010. “Performance, Combustion, and Emissions Characteristics of a Single-Cylinder Compression Ignition Engine Operated on Ethanol–Biodiesel Blended Fuels.” Proceedings of the Institution of Mechanical Engineers, Part A: Journal of Power and Energy224: 533–543.
- Banapurmath, N. R., P. G.Tewari, and R. S.Hosmath. 2008. “Experimental Investigations of a Four-Stroke Single Cylinder Direct Injection Diesel Engine Operated on Dual Fuel Mode with Producer Gas as Inducted Fuel and Honge Oil and Its Methyl Ester (HOME) as Injected Fuels.” Renewable Energy33: 2007–2018.
- Banapurmath, N. R., V. S.Yaliwal, SatishKambalimath, A. M.Hunashyal, and P. G.Tewari. 2011. “Effect of Wood Type and Carburetor on the Performance of Producer Gas-Biodiesel Operated Dual Fuel Engines.” Waste and Biomass Valorization2 (4) : 403–413. ISSN 1877-2641.
- Banat, Fawzi A., and JanaSimandl. 1999. “Membrane Distillation for Dilute Ethanol: Separation from Aqueous Streams.” Journal of Membrane Science163 (2): 333–348.
- Bjerre, A. B., A. B.Olesen, T.Fernqvist, A.Ploger, and A. S.Schmidt. 1996. “Pretreatment of Wheat Straw Using Combined Wet Oxidation and Alkaline Hydrolysis Resulting in Convertible Cellulose and Hemicelluloses.” Biotechnology and Bioenergy49 (5): 568–577.
- Bobade, S. N., and V. B.Khyade. 2012. “Detail Study on the Properties of Pongamia Pinnata (Karanja) for the Production of Biofuel.” Research Journal of Chemical Sciences2 (7): 16–20. ISSN 2231-606X.
- Carmen, S., M.Vinatoru, and Y.Maeda. 2007. “Aspects of Ultrasonically Assisted Transesterification of Various Vegetable Oils with Methanol.” Ultrasonic Sonochemistry14: 380–386.
- Chen, H., S.Shuai, and J.Wang. 2007. “Study on Combustion Characteristics and PM Emission of Diesel Engines Using Ester–Ethanol–Diesel Blended Fuels.” Proceedings of Combustion Institute31: 2981–2989.
- Deepak, A., and A. A.Kumar. 2007. “Performance and Emission Characteristics of a Jatropha Oil (Preheated and Blends) in a Direct Injection Compression Ignition Engine.” Applied Thermal Engineering27: 2314–2323.
- Demirbas, A.2005. “Biodiesel Production from Vegetable Oils via Catalytic and Non-Catalytic Supercritical Methanol Transesterification Methods.” Progress in Energy Combustion Science31: 446–487.
- Dien, B. S., X.-L.Li, L. B.Iten, D. B.Jordan, N. N.Nichols, P. J.O'Bryan, and M. A.Cotta. 2006. “Enzymatic Saccharification of Hot-Water Pretreated Corn Fiber for Production of Monosaccharides.” Enzyme and Microbial Technology39: 1137–1144.
- Furuta, Satoshi, HiromiMatsuhashi, and KazushiArata. 2006. “Biodiesel Fuel Production with Solid Amorphous-Zirconia Catalysis in Fixed Bed Reactor.” Biomass and Bioenergy30 (10): 870–873.
- Goering, H. K., and P. J. Van Soest. 1970. “Forage Fiber Analysis (Apparatus, Reagents, Prosedures and some Applications).” Department of Agriculture (USDA), Agricultural Hand book No. 379: 1–20.
- Hansen, A. C., Q.Zhang, and P. W. L.Lyne. 2005. “Ethanol–Diesel Fuel Blends – A Review.” Bioresource Technology96: 277–285.
- Hayes, T. K., L. D. Savage, R. A. White, and S. C. Sorenson. 1988. “The Effect of Fumigation of Different Ethanol Proofs on a Turbocharged Diesel Engine.” Society of Automotive Engineers Paper No.: 880497.
- Holtzapple, M. T., J. H.Jun, G.Ashok, S. L.Patibandla, and B. E.Dale. 1991. “The Ammonia Freeze Explosion (AFEX) Process – A Practical Lignocellulose Pretreatment.” Applied Biochemistry and Biotechnology28/29: 59–74.
- Huang, J. B., M.Mao, and B. Y.Zhu. 1999. “The Surface Physico-Chemical Properties of Surfactants in Ethanol–Water Mixtures.” Colloids and Surfaces155: 339–348.
- Keskin, Ali, MetinGuru, and DuranAltiparmak. 2007. “Biodiesel Production from Tall Oil with Synthesized Mn and Ni Based Additives; Effects of the Additives on Fuel Consumptions and Emissions.” Fuel86: 1139–1143.
- Khayoon, M. S., M. A.Olutoye, and B. H.Hameed. 2012. “Utilization of Crude Karanj (Pongamia Pinnata) Oil as a Potential Feedstock for the Synthesis of Fatty Acid Methyl Esters.” Bioresource Technology111: 175–179.
- Lapuerta, Magín, OctavioArmas, and JoséM.Herreros. 2008. “Emissions from a Diesel–Bioethanol Blend in an Automotive Diesel Engine.” Fuel87: 25–31.
- Laser, M., D.Schulman, S. G.Allen, J.Lichwa, M. J.Antal, and L. R.Lynd. 2002. “A Comparison of Liquid Hot Water and Steam Pretreatments of Sugar Cane Bagasse for Bioconversion to Ethanol.” Bioresource Technology81 (1): 33–44.
- Leung, Dennis Y. C., XuanWu, and M. K. H.Leung. 2010. “A Review on Biodiesel Production Using Catalyzed Transesterification.” Applied Energy87 (4): 1083–1109.
- Likos, B., T. J. Callahan, and C. A. Moses. 1982. “Performance and Emissions of Ethanol and Ethanol-Diesel Blends in Direct-Injected and Pre-Chamber Diesel Engines.” Society of Automotive Engineers Paper No.: 821039.
- Li, De-gang, HuangZhen, XingcaiLu, Wu-gaoZhang, and Jian-guangYang. 2005. “Physico-Chemical Properties of Ethanol–Diesel Blend Fuel and Its Effect on Performance and Emissions of Diesel Engines.” Renewable Energy30: 967–976.
- Liu, C., and C. E.Wyman. 2005. “Partial Flow of Compressed-Hot Water Through Corn Stover to Enhance Hemicellulose Sugar Recovery and Enzymatic Digestibility of Cellulose.” Bioresource Technology96: 1978–1985.
- Marichetti, J. M., V. U.Miguel, and A. F.Errazu. 2007. “Possible Methods for Biodiesel Production.” Renewable and Sustainable Energy Reviews11: 1300–1311.
- Meher L. C., S. N. Naik, and L. M. Das. 2004. “Methorolysis of Pangamia pinnata(Karanjo) Oil for Production of Biodiesel.” Journal of Scientific and Industrial Research 63: 913–918.
- Meiring, P., R. S.Allan, and A. C.Hansen, and P. W. L.Lyne. 1983. “Tractor Performance and Durability with Ethanol-Diesel Fuel.” Transactions of the American Society of Agricultural Engineers26 (1): 59–62.
- Meiring, P., A. C.Hansen, A. P.Vosloo, and P. W. L.Lyne. 1983. “High Concentration Ethanol–Diesel Blends for Compression–Ignition Engines.” Society of Automotive Engineers. Paper No.: 831360.
- Mosier, N., C.Wyman, B.Dale, R.Elander, Y.Lee, M.Holtzapple, and M.Ladisch. 2005. “Features of Promising Technologies for Pretreatment of Lignocellulosic Biomass.” Bioresource Technology96 (6): 673–685.
- Muralidharan, K., and D.Vasudevan. 2011. “Performance, Emission and Combustion Characteristics of a Variable Compression Ratio Engine Using Methyl Esters of Waste Cooking Oil and Diesel Blends.” Applied Energy88 (11): 3959–3968.
- Muralidharan, M., P. T.Mathew, S.Roy, J. P.Subrahmanyam, and P. M. V.Subbarao. 2004. “Use of Pongamia Biodiesel in CI Engines for Rural Application.” Society of Automotive Engineers, Paper No.: 2004-28-0030.
- Noguchi, N., H.Terao, and C.Sakata. 1996. “Performance Improvement by Control of Flow Rates and Diesel Injection Timing on Dual-Fuel Engine with Ethanol.” Bio-resource Technology56: 35–39.
- Noureddini, H., and D.Zhu. 1997. “Kinetics of Transesterification of Soyabean Oil.” Journal of the American Oil Chemists Society (JAOCS)74 (11): 1457–1463.
- Nwafor, O. M. I.2000. “Effect of Advanced Injection Timing on the Performance of Rape Seed Oil in Diesel Engines.” Renewable Energy21: 433–444.
- Nwafor, O. M. I.2003. “The Effect of Elevated Fuel Inlet Temperature on Performance of Diesel Engine Running on Neat Vegetable Oil at Constant Speed Conditions.” Renewable Energy28: 171–181.
- O'Brien, D. J., and J. C.CraigJr.. 1996. “Ethanol Production in a Continuous Fermentation/Membrane Pervaporation System.” Applied Microbiology and Biotechnology44 (6): 699–704.
- Parikh, P. P., A. G.Bhave, D. V.Kapse, and Shashikantha. 1989. “Study of Thermal and Emission Performance of Small Gasifier-Dual-Fuel Engine Systems.” Biomass19: 75–97.
- Park, S. H., S. H.Yoon, H. K.Suh, and C. S.Lee. 2008. “Effect of Temperature Variation on Properties of Biodiesel and Biodiesel–Ethanol Blends Fuels.” Oil & Gas Science Technology – Rev. IFP63 (6): 737–745.
- Pérez, J. A., I.Ballesteros, M.Ballesteros, F.Saez, M. J.Negro, and P.Manzanares. 2008. “Optimizing Liquid Hot Water Pretreatment Conditions to Enhance Sugar Recovery from Wheat Straw for Fuel-Ethanol Production.” Fuel87: 3640–3647.
- Raheman, H., and S. V.Ghadge. 2008. “Performance of Diesel Engine with Biodiesel at Varying Compression Ratio and Ignition Timing.” Fuel87: 2659–2666.
- Ramadas, A. S., S.Jayaraj, and C.Muraleedharan. 2006. “Power Generation Using Coir Pith and Wood Derived Producer Gas in a Diesel Engine.” Fuel Processing Technology87: 849–853.
- Ramadas, A. S., S.Jayaraj, and C.Muraleedharan. 2008. “Dual Fuel Mode Operation in Diesel Engines Using Renewable Fuels; Rubber Seed Oil and Coir Pith Producer Gas.” Renewable Energy339: 2077–2083.
- Roy, Murari Mohon, EijiTomita, NobuyukiKawahara, YujiHarada, and AtsushiSakane. 2009. “Performance and Emission Comparison of a Supercharged Dual-Fuel Engine Fueled by Producer Gases with Varying Hydrogen Content.” International Journal of Hydrogen Energy34: 7811–7822.
- Sahoo, B. B., N.Sahoo, and U. K.Saha. 2009. “Effect of Engine Parameters and Type of Gaseous Fuel on the Performance of Dual-Fuel Gas Diesel Engines – A Critical Review.” Renewable and Sustainable Energy Reviews13: 1151–1184.
- Samir, J. D., B. B.Lalit, and B. T.Shashikant. 2008. “Investigation on Performance and Emission Characteristics of CI Engine Fuelled with Producer Gas and Esters of Hingan (Balanites) Oil in Dual Fuel Mode.” International Journal of Mechanical Systems Science and Engineering2 (3): 148–153.
- Sayin, Cenk, and MetinGumus. 2011. “Impact of Compression Ratio and Injection Parameters on the Performance and Emissions of a DI Diesel Engine Fueled With Biodiesel-Blended Diesel Fuel.” Applied Thermal Engineering31 (6): 3182–3188.
- Scholl, K. W., and S. C.Sorenson. 1993. “Combustion Analysis of Soyabean Oil Methyl Ester in a Direct Injection Diesel Engine.” Society of Automotive Engineers. Paper No: 930934.
- Shropshire, G. J., and C. E.Goering. 1982. “Ethanol Injection into a Diesel Engine.” Transactions of the American Society of Agricultural Engineers25 (3): 570–575.
- Singh, R. N., S. P.Singh, and B. S.Pathak. 2007a. “Investigations on Operation of CI Engine Using Producer Gas and Rice Bran Oil in Mixed Fuel Mode.” Renewable Energy32: 1565–1580.
- Singh, R. N., S. P.Singh, and B. S.Pathak. 2007b. “Extent of Replacement of Methyl Ester of Rice Bran Oil by Producer Gas in CI Engine.” Energy Resource Wiley Inter Science31: 1545–1555.
- Singh, S. P., and DiptiSingh. 2010. “Biodiesel Production Through the Use of Different Sources and Characterization of Oils and Their Esters as the Substitute of Diesel: A Review.” Renewable and Sustainable Energy Reviews14: 200–216.
- Sridhar, G., H. V.Sridhar, S.Dasappa, P. J.Paul, N. K. S.Rajan, and H. S.Mukunda. 2005. “Development of Producer Gas Engines.” Proceedings of the Institution of Mechanical Engineers, Part A: Journal of Power and Energy, Part D219: 423–438.
- Statge de Caro, P., Z.Mouloungui, G.Vaitilingom, and J. Ch.Berge. 2001. “Interest of Combining an Additive with Diesel–Ethanol Blends for Use in Diesel Engines.” Fuel80: 565–574.
- Syed, Ameer Basha, K.Raja Gopal, and S.Jebaraj. 2009. “A Review on Biodiesel Production, Combustion, Emissions and Performance.” Renewable and Sustainable Energy Reviews13 (6–7): 1628–1634.
- Thiruvengadaravi, K. V., J.Nandagopal, P.Baskaralingam, V.Sathya Selva Bala, and S.Sivanesan. 2012. “Acid-Catalyzed Esterification of Karanja (Pongamia Pinnata) Oil with High Free Fatty Acids for Biodiesel Production.” Fuel98: 1–4.
- Vivek, and A. K.Guptha. 2004. “Biodiesel from Karanja Oil.” Journal of Scientific and Industrial Research63: 39–47.
- Wyman, C. E.2003. “Potential Synergies and Challenges in Refining Cellulosic Biomass to Fuels, Chemicals, and Power.” Biotechnology Progress19: 254–262.
- Xingcai, L., Y.Jianguang, Z.Wugao, and H.Zhen. 2004. “Effect of Cetane Number Improver on Heat Release Rate and Emissions of High Speed Diesel Engine Fuelled with Ethanol Diesel Blend Fuel.” Fuel83: 2013–2020.
- Yaliwal, V. S., S. R.Daboji, N. R.Banapurmath, and P. G.Tewari. 2010. “Production and Utilization of Renewable Liquid Fuel in a Single Cylinder Four Stroke Direct Injection Compression Ignition Engine.” International Journal of Engineering Science and Technology2: 5888–5899.
- Yaliwal, V. S., S. Y.Adaganti, B. M.Kulkarni, and G. P.Desai. 2013. “Production of Renewable and Sustainable Fuel from Calliandra calothyrsus and its Utilization in Compression Ignition Engines.” International Journal of Sustainable Engineering. 10.1080/19397038.2013.801530.
- Zhu, Lei, C. S.Cheung, W. G.Zhang, and ZhenHuang. 2011a. “Effect of Charge Dilution on Gaseous and Particulate Emissions from a Diesel Engine Fueled with Biodiesel and Biodiesel Blended with Methanol and Ethanol.” Applied Thermal Engineering31 (14–15): 2271–2278.
- Zhu, Lei, C. S.Cheung, W. G.Zhang, and ZhenHuang. 2011b. “Combustion, Performance and Emission Characteristics of a DI Diesel Engine Fueled with Ethanol–Biodiesel Blends.” Fuel90: 1743–1750.