Abstract
The cement industry is one of the most energy-intensive industries consuming 4 GJ/ton of cement, i.e. 12–15% of the energy use in total industry. Energy cost accounts for 30% of the total cost of cement production. Seventy-five per cent of this energy is due to the thermal energy for clinker production. It is also found that 35% of this supplied thermal energy is lost in flue gas streams. Most modern kilns use pet coke or coal as their primary fuel. Instead, the municipal waste in landfills offer a cheap source of energy and reduce the environmental effects of dumping solid waste. The calcination and drying processes and the kiln need large quantities of thermal energy. About 40% of the total energy input is lost in the hot flue gases and cooling the stack plus the kiln shell. Hence, it is suitable to use an organic Rankine cycle (ORC) to recover the exhaust energy from the kiln. Alternatively, a 15 MW gas turbine engine combined with a steam turbine could be utilized. It was found that ORC produces 5 MW with a capital cost recovery period of 1.26 years. However, the gas turbine combined system produces 21.45 MW with a maximum recovery period of 2.66 years.
1. Introduction
1.1. Energy conservation
Cement production is one of the most energy-intensive industries. It consumes 12–15% of the total energy consumption in various industries. Energy consumption involves 50–60% of the direct production cost of cement (Engin and Ari Citation2005). Calcination and drying processes plus the kiln requires large quantities of thermal energy. The grinding mills, fans and other motor-driven equipment need large amount of electric energy (Eugeniusz and Bochen-czyk Citation2002). About 40% of the total input energy is lost in hot flue gases, cooling the stack and kiln shell (Figure ) (Trezza and Scian Citation2005). Hence, heat recovery and utilization is essential to improve the whole process (Madlool et al. Citation2013).
The rotary kilns one of the most effective types of incinerators (Figure ) (Kuntz Citation2001), capable of handling both liquefied and solid waste (Nielsan Citation1994; Rugenberger Citation1998; Jormana, Kojo, and Astrom Citation1993; Schneider et al. Citation2011; Darley and Bowell Citation2001; Terasawa et al. Citation2001). The kiln is of a rotating refractory-lined cylinder that is mounted in a slant. The pre-processed waste is fed into the kiln via a burner. The waste then reacts with the hot air coming from the clinker cooler and combust directly (Kira et al. Citation2001; Pirson and Bracker Citation1994). The high temperatures and supply of fresh air within the kiln ensures that there is a complete combustion of the waste. Due to its inclination, any ash that is produced as a by-product of the combustion process falls to the floor of the kiln, combines with the raw material and travels down the kiln due to its rotation and exits as clinker (Khurana, Banerjee, and Gaitonde Citation2002; Caribbean Cement Company Log sheet, Kiln5.19). Hence, recuperators can be used for waste-heat recovery from such rotary kilns (Karamarkovic et al. Citation2013).
Figure 1 Main energy flow in a cement production process. Adapted from Bell (Citation2007).
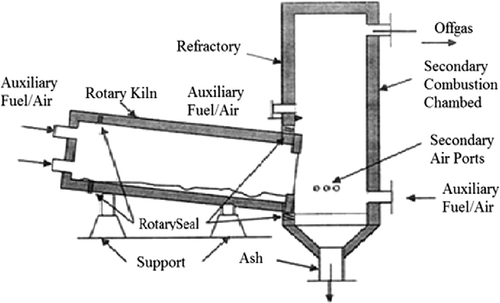
The spray tower is a device designed to remove heat from the flue gas before it enters the bag house (Figure ). By spraying water into this gas stream, the temperature of the flue gas is brought down from 350°C to 105°C to enter into the bag house. This is just above the dew point of air at atmospheric pressure. This use of water to bring down the temperature shows a significant loss of available energy and water (Lukaski Citation1999).
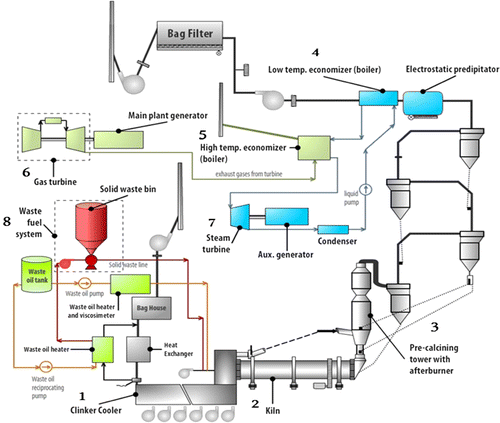
Utility is usually the main source of power supply. In this work, it is suggested that the heat in the exhaust gases of the kiln could be utilized in an organic Rankine cycle (ORC) to provide part of the electrical power supply. Energy efficiency could be improved by different methods, among which are waste-heat recovery (Akyurt et al. Citation1995), combined cycles (Najjar and Akyurt Citation1994) and energy storage for peak shaving and load levelling (Najjar and Jubeh Citation2006). Widening the range of fuel specifications also improves thermo economics (Najjar Citation1982). All these processes contribute towards green technology in industry.
One megawatt of electric power per kiloton of clinker could be produced from waste-heat recovery of the exhaust gas. This constitutes a significant energy saving about 33% for the plant. Alternatively, the power from the grid could be totally dispensed with by installing a 15 MW gas turbine running on natural gas or diesel. Utilizing its exhaust energy in raising steam in a heat recovery boiler runs a steam turbine in a combined cycle. The exhaust energy from the kiln is then used to boost the steam production for running the steam turbine that produces 6.45 MW. This power could be sold to the grid, as shown in Figure (Najjar and Jubeh Citation2006; Najjar Citation1982).
The main objectives of this work are
To design a waste-heat recovery system using the available heat in the exhaust of the cement kiln in ORC or alternatively using a gas turbine in a combined system with steam turbine power plant.
To provide the cement plant with a means of improving its economic set-up, by selling electricity produced from the waste heat that would have been dumped into the atmosphere.
1.2. Waste utilization
An incinerator is a device that is used to dispose waste products through burning (Rueth Citation1977; Taplin Citation1991; Allen Citation1993; Isles Citation1993). However, due to revised environmental laws with respect to the disposal of solid waste, the use of incinerators has increased significantly (Salvador, Kara, and Commander Citation2006; Valenti and Trash Citation1999). The types of waste sent to incinerators are those with high-heating values that burn easily. By using waste in cement kilns as their source of energy, governments can reduce the degradation of their natural environment due to the reduced need for landfills (Pleunneke Citation1988; Kuntz Citation2001).
Most cement plants focus on waste with high-heating value. This includes the burning of automobile tires, plastics, carpets and refuse oil from power generation plants, auto repair centres and restaurants (Kaantee et al. Citation2002; Kumar Citation2005; Ewall and Nicholson Citation2003; Utlu et al. Citation2006; Doheim and Sayed Citation1987). Municipal waste requires extensive preprocessing. Tires and solid wastes must be dehydrated and shredded into small pellets to improve their burning. Likewise, liquidized waste must be properly mixed into a homogeneous liquid to avoid multi-stage flames in the kiln. The liquid should also be kept at a temperature below its ignition point, hence allowing for recirculation and the removal of water (Cohen, Rogers, and Saravanamuttoo Citation2001; Engin and Ari Citation2005; Wiekmeijer Citation1990; Scuibba Citation1986; Korobitsyn, Jellema, and Hirs Citation1999; Wang, Dai, and Gao Citation2009).
The use of waste-derived fuel in cement kilns saves over 300,000 ton of fossil fuel per year in France alone. Recovering the energy contained in industrial and domestic waste therefore leads to considerable conservation of fossil fuels (fuel oil, petroleum products and coal). In addition to energy recovery, there is also a corresponding saving relevant to CO2 emissions released into the atmosphere which accounts for about 7% of the total worldwide CO2 emissions.
Waste must be exposed to a temperature exceeding 850°C for at least 2 s for the incineration of non-chlorinated hazardous waste (Lukaski Citation1999). In a cement kiln, the temperatures exceed 1400°C within its burning zone, and gases stay at temperatures exceeding 1200°C throughout the process for 5–6 s to ensure the resulting clinker quality (Noor et al. Citation2013).
Incineration in cement kilns has provided municipalities with a viable option that leaves the government, cement producers and the environment in a win–win situation where the waste can be easily disposed by using it as fuel for cement kilns (Wang, Dai, and Gao Citation2009). Thus, with proper regulations, cement kiln incineration can dispense with the use of landfills. When eliminated, the governments only have to worry about the disposal of hazardous waste that would be harmful to the environment if burnt.
To encourage cement plants to burn waste material as fuel, many governments have introduced a concept of “environmental dollars” where cement plants are literally paid to use municipal waste as their fuel. This payment may come in the form of budgetary support or tax reliefs.
There is no significant increase in greenhouse gases through the use of cement kilns as incinerators. Also, there is no liquid or solid residue to contend with, after the combustion process. As a result, the process is clean and good for the environment.
From calculations, it was found that up to a total of 166,000 ton of municipal waste can be burnt in the kiln per day at a rate of 20.96 ton/h to achieve the same temperature profile as when the plant operates on petcoke (Table ).
Table 1 Conversion rates from petcoke to municipal waste.
Additional benefits from using the municipal waste could be:
The amount of nitrogen released into the air can be reduced from 4% with the use of pet coke to 0.3% due to the change in composition of the fuel.
The release of harmful chemicals such as NOx and SOx is reduced due to the containment of the highest temperatures within the burning zone at the front section of the kiln. By the time these gases get to the back of the kiln, the temperature falls to 900°C where these gases return to a state that does not harm the environment.
2. Theoretical analysis
For plants that must utilize power supply from the national grid, the cost of electricity can be an overbearing factor on their cost of operation culminating up to 50% of production cost. However, with an investment of just under $3 million, these plants can reduce their cost of electricity from the grid by up to 33%.
2.1. Using ORC
ORC is used to capture heat from the exhaust gases of both the calcination tower and clinker cooler and convert this usually wasted energy to electricity.
Industrial installations such as those existing in cement plants where the temperature of exhaust gases exceeds 350°C, indirect ORC systems are generally employed (Lukaski Citation1999). Thermo oil is used as an intermediate fluid to transfer the heat from the exhaust gases to the low temperature organic fluid that operates within a Rankine cycle. Figure shows a schematic of ORC (Leibowitz Citation1983) and Figure shows the layout (Lukaski Citation1999).
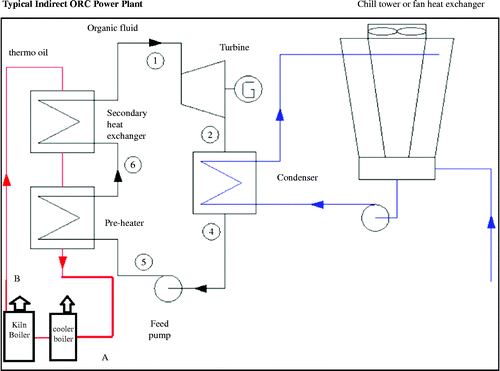
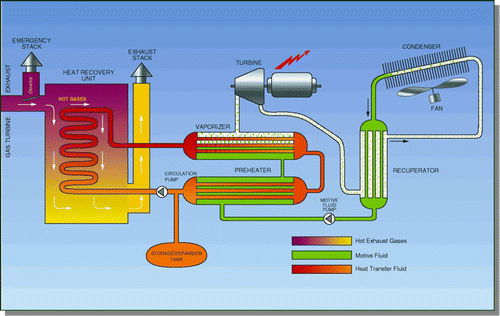
2.2. Typical indirect ORC power plant
Based on the typical operating temperatures, ORC power plants utilized in cement plants are capable of producing 1 MW/kiloton (Scuibba Citation1986) of clinker produced. Therefore, in this work an existing plant of 210 ton/h (5040 ton/day) was selected, with a 5 MW gas turbine plant to be added. This will in turn reduce the plant electricity bill between 16% and 33% depending on the operating conditions. At a rate of $70 per MWh (using grid power), the plant reduces the overall electricity bill by $2.77 million per year (Lukaski Citation1999).
2.3. Using combined system of gas and steam turbines
1 GJ = 4184 kcal
Fuel rate: The rate of fuel fired to the kiln is based on normal operation standards of 7.2 ton/h petcoke to the riser duct and 4.7 ton/h petcoke to the kiln.
Fuel sharing: Fuel mass flow can be combined based on availability and determined as follows:
2.3.1. Gas turbine
Assumptions
Compression ratio = 12
Turbine inlet temperature is limited to 1200°C (1473 K)
Compressor efficiency = 80%
Turbine efficiency = 80%
Combustor efficiency = 95%
2.3.2. Thermal efficiency (ηth)
2.3.3. Steam plant
2.3.3.1. Boiler 1
Kiln air mass flow (kg/s) was calculated to be 71.25 kgair/s (Figure ).
Energy balance
whereis the kiln air mass flow (kg/s),
is the feed water mass flow (kg/s) and Qin boiler 1 is the energy supplied to boiler 1 (kg/s).
Heat
2.3.3.2. Boiler 2
Mass flow of turbine exhaust (
) = 50.22 kg/s.
From energy balance
whereis the gas turbine air mass flow (kg/s),
is the feed water mass flow (kg/s) and Qin boiler 2 is the energy supplied to boiler 2 (kJ/s).
Heat recovery from gas turbine = 50.22 × 1.21 × (694–320) = 22726.6 kJ/s.
3. Discussion of results
The computations during this work were based on the following assumptions:
The cement plant rate is 210 ton of clinker/h, i.e. 1.663 Mt/year. Assume a 5-day break each 2 months for dust removal, hence 330 effective days/year (7920 h/year). The corresponding petcoke consumption is 12 ton/h, i.e. 290 ton/day. At a price of $100/ton, the petcoke cost becomes $9.57 million. Thus, when using municipal waste, a 15.5% of clinker production could be produced considering the international price of clinker as $37/ton.
Using the ORC to produce 1 MW/1000 ton of clinker, the whole plant produces 5 MW power, thereby reducing the electricity bill by 33%. At an electricity price of $70/MWh, the reduction in electricity bill amounts to $2.77 million/year.
If both gas turbine (15 MW equivalent to grid power supply, with exhaust gases about 600°C down to 320°C) and kiln gases (355°C down to 120°C) are utilized, then the steam generated could run a steam turbine (of 65% efficiency) to produce 6.45 MW power. This is equivalent to 43% of the plant need. This amounts to $3.576 million/year reduction in the electricity bill. If the steam plant and the relevant ducts and auxiliaries are assumed to cost $6.5 million, then this may be recovered in about 2 years of effective operation.
Table shows these particulars in details. Annual savings for the gas turbine is $2.821 million/year hence the recovery period is 2.66 years. The steam and ORC plants are based on the selling cost of electricity to the grid at $0.05/kWh while the operating cost is $0.01/kW. The recovery period becomes 1.27 and 1.262 years, respectively.
Table 2 Overview of different plant configurations.
4. Conclusions
When using municipal waste, a 15.5% of clinker production could be obtained considering the international price of clinker as $37/ton. Using the ORC to produce 1 MW/1000 ton of clinker, the whole plant produces 5 MW power, thereby reducing the electricity bill by 33%. At $70/MWh electricity price, this amounts to $2.77 million saving/year and recovery period of 1.262 years.
When using the gas turbine, savings per year is $2.821 million; hence, the recovery period is 2.66 years. Savings from the steam and ORC plants are based on the selling cost of electricity to the grid being $0.05/kWh while the operating cost is $0.01/kW. The recovery period becomes 2 and 1.262 years, respectively.
For a typical cement plant capacity of 210 ton/h, up to a total of 166,000 tons of municipal waste can be burnt in the kiln per day at a rate of 20.96 ton/h to achieve the same temperature profile as when the plant operates on petcoke.
By using municipal waste, the amount of nitrogen released into the air can be reduced from 4% with the use of petcoke to 0.3% due to the change in composition of the fuel.
The release of harmful chemicals such as NOx and SOx is reduced due to the containment of the highest temperatures within the burning zone at the front section of the kiln.
References
- Akyurt, M., N. J. Lamfon, Y. S. H. Najjar, M. H. Habeebullah, and T. Y. Alp. 1995. “Modeling of Waste Heat Recovery by Looped Water-in-Steel Heat Pipes.” The International Journal of Heat and Fluid Flow 16 (4): 263–271.
- Allen, W. H. 1993. “Poultry Power Scores One in the Eye.” Modern Power Systems 57–61.
- Bell, J. 2007. “Concrete Energy Saving-On–Site Power for the World's Cement Industry.” http://www.cospp.com/articles/print/volume-8/issue-3/features/concrete-energy-savings-on-site-power-for-the-worldrsquos-cement-industry.html.
- Cohen, H., G. Rogers, and H. I. H. Saravanamuttoo. 2001. Gas Turbine Theory. 5th ed. London: Longman.
- Darley, P., and R. Bowell. 2001. “CHP From Municipal Refuse: Learning From Operating Experience.” Modern Power Systems 37–39.
- Doheim, M. A., and S. A. Sayed. 1987. “Analysis of Waste Heat and its Recovery in a Cement Factory.” Heat Recovery Systems and CHP 7 (5): 441–444.
- Engin, T., and V. Ari. 2005. “Energy Auditing and Recovery for Dry Type Cement Rotary Kiln Systems – A Case Study.” Energy Conversion and Management 46: 551–562.
- Eugeniusz, M., and A. U. Bochen-czyk. 2002. “Alternative Fuels for the Cement Industry.” Applied Energy 74 (1–2): 95–100.
- Ewall, M., and K. Nicholson. 2003. “Hazardous Waste and Tire Incineration in US and Mexican Cement Industries.” Energy Justice Network. www.energyjustice.net/cementkilns.
- Isles, J. 1993. “Waste Incineration Turns to Cogeneration.” Modern Power System 51–55.
- Jormana, M., K. Kojo, and L. Astrom. 1993. “Making the Most of Waste.” MPS Review 19–21.
- Kaantee, U., R. Zenenhoven, R. Backman, and M. Hupa. 2002. “Cement Manufacturing Using Alternative Fuels and the Advantages of Process Modeling.” . Presented at R2002 Recovery, Recycling, Re-integration, February 12–15, Geneva (Switzerland). www.R2002.com.
- Karamarkovic, V., M. Marasevic, R. Karamakovic, and M. Kramakovic. 2013. “Recuperator for Waste Heat Recovery From Rotary Kilns.” Applied Thermal Engineering 54: 470–480.
- Khurana, S., R. Banerjee, and U. Gaitonde. 2002. “Energy Balance and Cogeneration for Cement Plant.” Applied Thermal Engineering 22 (5): 485–494.
- Kira, M., T. Doi, S. Tsuneizumi, M. Takuma, and T. Kitta. 2001. “Development of New Stoker Incinerator for Municipal Solid Wastes Using Oxygen Enrichment.” Technical Review 38 (2)
- Korobitsyn, M. A., P. Jellema, and G. G. Hirs. 1999. “Possibilities for Gas Turbine and Waste Incinerator Integration.” Energy 783–793.
- Kumar, P. 2005. “Cogeneration of Power Through Waste Heat Recovery in Cement Plants – Overview and Prospects.” EMT India. http://www.emtindia.net/Presentations/3L_CHP/05NewDelhi/01Cogenerationofpower-NCCBM.pdf.
- Kuntz, F. J. 2001. “Incinerator Systems.” International Conference on Incineration and Thermal Treatment Technologies, Philadelphia, PA.
- Leibowitz, H. M. 1983. “Electric Power from Waste Heat Using ORC Technology.” Ormat Industrial Company. www.ormat.com/…/e008778b83b2bdbf3a8033b23928b234.pdf.
- Lukaski, M. 1999. “Design and Optimization of Standard Organic Rankine Cycle Power Plant for European Conditions.” www.skemman.is/stream/get/1946/7113/17787/1/Maciej_Lukawski.pdf.
- Madlool, N. A., R. Saidur, N. A. Rahim, and M. Kamalisarvestani. 2013. “An Overview of Energy Savings Measures for Cement Industry.” Renewable and Sustainable Energy Reviews 29: 18–29.
- Najjar, Y. S. H. 1982. “Some Performance Characteristics of the Gas Turbine Combustor Using Heavy Fuels.” Journal of the Institute of Energy LV (425): 187–194.
- Najjar, Y. S. H., and M. Akyurt. 1994. “Combined Cycles with Gas Turbine Engines.” Journal of Heat Recovery Systems & CHP 14 (2): 93–103.
- Najjar, Y. S. H., and N. Jubeh. 2006. “Comparison of Performance of Compressed-Air Energy–Storage Plant (CAES) with Compressed-Air Storage with Humidification (CASH).” Proceedings of the Institution of Mechanical Engineers (IMechE) 220, Part A. Journal of Power and Energy 581–588.
- Nielsan, C. R. 1994. “Sonderborgchp Plant Burns Gas and Refuse.” Modern Power Systems 47–51.
- Noor, Z. Z., R. O. Yusuf, A. H. Abba, and M. A. Hassan. 2013. “An Overview for Energy Recovery From Municipal Solid Waste (MSW) in Malaysia Scenario.” Renewable and Sustainable Energy Reviews 20: 378–384.
- Pirson, R., and G. P. Bracker. 1994. “The Gavi Wijster 735 000 t/a Waste to Energy Plant.” Modern Power Systems 57–64.
- Pleunneke, K. A. 1988. “Thermal Destruction of Hazardous Wastes.” Mechanical Engineering 55–57.
- Rueth, N. 1977. Energy and Materials from Garbage. New York: Mechanical Engineering Magazine.
- Rugenberger, M. 1998. “Putting an End to Landfill.” Modern Power Systems 36–39.
- Salvador, S., Y. Kara, and J. M. Commander. 2006. “Factors Influencing Pollutant Gas Emissions of VOC Recuperative Incinerators: Large-Scale Parametric Study.” Applied Thermal Engineering 26: 1640–1651.
- Schneider, M., M. Romer, M. Tschudin, and H. Bolio. 2011. “Sustainable Cement Production – Present and Future.” Cement and Concrete Research 41: 642–650.
- Scuibba, E. 1986. “Steam Plant for Electricity Generation From Solid Urban Refuse with Gas-Turbine Blown Pressurized Fluidized Bed Combustion.” International Gas Turbine Conference and Exhibit Dusseldorf 1–11.
- Taplin, B. 1991. “100 MWe From Proposed Refuse-Burning Plant.” Modern Power Systems 65–69.
- Terasawa, Y., H. Yasuda, H. Horizoe, J. Sato, and Y. Gotou. 2001. “Commercialization of MSW Incineration System with Direct Ash Melting by Thermal Cracking for High Efficient Generation of Electricity.” Technical Review 38 (2)
- Trezza, M. A., and A. N. Scian. 2005. “Waste Fuels: Their Effect on Portland Cement Clinker.” Cement and Concrete Research 35 (3): 438–444.
- Utlu, Z., Z. Sogut, M. Hepbasli, and Z. Oktay. 2006. “Energy and Exergy Analyses of a Raw Mill in a Cement Production.” Applied Thermal Engineering 26: 2479–2489.
- Valenti, M., and S. Trash. 1999. “Heat and Ash.” Mechanical Engineering 44–47.
- Wang, J., Y. Dai, and L. Gao. 2009. “Exergy Analyses and Parametric Optimizations for Different Cogeneration Power Plants in Cement Industry.” Applied Energy 86: 941–948.
- Wiekmeijer, I. R. 1990. “Improvements in Incinerators by Means of Gas Turbine Based Cogen Systems.” Gas Turbine and Aero-Engine Congress and Exposition 1–6.