Abstract
Sugar industries require a large amount of water for processing, and also generate large amounts of high-degree polluted wastewater. To maintain the water balance in the industry, it is imperative that effective treatment methods need to be devised to treat the wastewaters. The main aim of the present work is to treat the sugar industry wastewater by combined thermal and electro-oxidation methods with a metal and a catalyst based on ferrous material. Results showed a reduction of 75.6% of COD and 79.2% of colour content with thermal treatment, and 97.8% of COD and 99.7% of colour with combined thermal and electrocoagulation treatments under optimum conditions. These reduction levels are adequate for recycling limits.
1. Introduction
India is one of the largest producer and consumer of sugar in the world with an annual production of 27 metric million tons of sugar and 351metric million tons of sugarcane (Aradhey Citation2014). Sugar industries in general generate about 1,000 L of wastewater for one ton of sugar cane processed (Hampannavar and Shivayogimath Citation2010; Kushwaha 2015). Volume of effluent generated depends on the cane crushing capacity of industry and management of water utilisation (Ingaramo et al. Citation2009). Untreated wastewater has significant impact on human health, plant growth and flora and fauna (Sahu and Chaudhari Citation2015). The characteristics of effluents vary from mill to mill and from time to time, which contains high organic pollutants which make it necessary to go for various types of treatments viz., physical, chemical, combination of physical and chemical, biological and Advanced Oxidation Processes (AOP) (Rao et al. Citation2012). The choice of the methods depends upon type of industry, the extent of sophisticated treatment required and the purpose for which the treated water is used. Generally, physic-chemical and biological treatment methods are used to treat the sugar industry wastewaters (Sharma and Kumar Citation2015). Most of the major industries have treatment facilities for industrial effluents. But this is not the case with small-scale industries, which cannot afford enormous investments in pollution-control equipment as their profit margin is very slender (Siddiqui and Waseem Citation2012). Additionally, increasing environmental awareness coupled with more stringent regulatory standards has triggered various industries to orient themselves in seeking appropriate wastewater treatment technologies (Teh et al. Citation2016). Various economical alternatives like thermolysis, electrolysis, etc. are available in literature to treat the effluent and bring up to dischargeable norms (Sahu Citation2016).
Thermolytic catalysis treatment is categorised under the advance treatment methods, and involves in chemical decomposition caused by heat in the presence of a metal catalyst such as iron, copper, aluminium, etc. (Chaudhari et al. Citation2010). The effects of temperature, pH and autogenous pressure were found to be the key parameters affecting the thermolysis, and the settling and filtration characteristics of the precipitates. Literature reports also indicated with reference to high strength organic wastewaters like that emanating from pulp and paper mills (Garg et al. Citation2005), alcohol distilleries (Chaudhari et al. Citation2007), textile industry (Kumar et al. Citation2008), petrochemical (Verma et al. Citation2011), etc. Electrolysis is also a highly efficient treatment process (Asaithambi et al. Citation2016; Kobya et al. 2016), and was used to treat the wastewaters coming from textile industries (Deokate Citation2015), Bilge wastewater (Ulucan et al. Citation2014), Agro-industry wastewaters (Kim et al. Citation2013), etc. In the present work, an attempt was made to treat the sugar industry wastewater by combination of thermal and electrocoagulation processes. The effect of initial pH and mass loading has been discussed in detail. The physicochemical characteristics of sludge and slurry generated after treatment have also been analysed.
2. Material and methods
2.1. Material
AR grade chemicals were used for experimental work and analysis. The wastewater was procured from Bhoramdev Sugar Industry Ltd. Kavardha (C.G.) India. The physicochemical characteristics of effluent are mentioned in Table .
Table 1. Characteristic of SIWW before and after treatment.
2.2. Experimental methods
The experimental set-up for the thermal experiments consists of a three-necked borosil glass reactor of spherical shape (capacity 0.5 dm3) with a magnetic stirrer, a condenser, thermometer and an opening to draw the sample. A sample of 300 ml of wastewater was used in each experiment; and temperatures were maintained between 55 to 95 °C. The characteristics of the catalyst used in each experiment were shown in Table .
Table 2. Different catalyst used in thermal treatment.
Electrocoagulation was carried out in an electrochemical reactor made of plexi-glass. The dimensions of the reactor are given in Table . Two pairs of electrodes were inserted into the reactor with parallel arrangement. The electrodes were connected with DC power supply (ECR). Current flow through the cell and the voltage across the electrodes were measured with an ammeter and a voltmeter, respectively.
Table 3. Dimension of electrochemical reactor.
The initial pH of the wastewater was varied between 2 to 10 using either 0.1 N HCl or 1 M NaOH. Samples were drawn from AGR and ECR (supernatant liquid). Final COD of each sample was measured. The percentage COD removal was calculated using the following relationship:(1)
where, CODo is the initial COD (mg/l) and CODt is the COD after t (min) of electrolysis time (mg/l). The colour of the wastewater samples was before and after the EC by a UV–vis spectrophotometer (Model Lambda 35, Perkin-Elmer Instruments, Switzerland). The percentage of colour removal was calculated from the difference in absorbance values before and after treatment.
2.3. Analytical procedure
All the physico-chemical parameters like COD, colour, total solids, total dissolved solids, total suspended solids, reduced carbohydrate, sulphate, chloride, etc., were determined as per standard methods of analysis (APHA 1989). The colour of the sample was measured in terms of the absorbance at λ = 420 nm using a UV–vis spectrophotometer. After the completion of experiments, the samples were settled in a 500 ml measuring cylinder. Later the contents were filtered using Buechner funnel and What’s man No. 42 filter paper. Thermal analysis (TGA/DTGA/DTA) of the sludge was made using a TG analyser (Pyris Diamond, Perkin-Elmer) after the treatment of SIWW with iron electrode.
3. Result and discussion
3.1. Treatment with catalyst
3.1.1. Effect of pH
The effect of initial pH on thermolysis of the wastewater with ferrous sulphate (FeSO4), ferric chloride (FeCl3), copper sulphate (CuSO4), aluminium sulphate (Al2(SO4)3) and without catalyst (WC) was studied in the AGR at atmospheric pressure and at 95 °C. The results were shown in Figures (a) and (b). All the experiments were carried out for a treatment time of 4 h with the initial COD of 3682 mg/l, colour of 350PCU and the catalyst mass loading (Cw) of 3 kg/m3. The initial pH was varied during the experiments in the range of 2–10. It was generally observed that the per cent reductions reached two maxima, one in acidic region and the other in alkaline region. The maximum COD reduction of 52.7% and colour removal of 55.8% were observed when ferrous sulphate was used at pH of 10. This was followed by aluminium sulphate (pH 8)50.8% COD and 53.9% colour, copper sulphate (pH 8) 45.5% COD and 48.1 colour, ferric chloride (pH 10) 42.8% COD and 45.8% colour removal, respectively. When wastewater treated without catalysis maximum 35.1% COD and 36.5% colour removal was found at pH 7. This may be attributed to dominance of compounds having positive charges (Chaudhari et al. Citation2008). Complexation of the organics with ferrous salts makes them insoluble and thereby precipitates the organics, which could play a major role in COD and colour reduction (Kumar et al. Citation2008).
3.1.2. Effect of mass loading of catalyst
The effect of ferrous sulphate mass loading on the COD and colour reduction of SIWW was studied in range of 1.5 to 7.5 kg/m3 at an optimum of pH 10 and 95 °C for 4hours (shown in Figure ). It was noticed that the COD and colour reduction increased linearly with increase in catalyst dosage from 1.5 to 6 kg/m3. The COD 44.1%, 52.7%, 62.5% 75.6% and colour removal 48.2%, 56.8%, 67.8, 79.2% was found for 1.5 kg/m3, 3 kg/m3, 4.5 kg/m3, 6 kg/m3, respectively. The rising trend, however, did not continue beyond 6 kg/m3. Later the trend got plateaued with COD reduction stabilised at 63.7% and colour removal at 68.5% for the ferrous catalyst loading of 7.5 kg/m3. This catalyst mass loading is termed as the critical chemical concentration (CCC) at which the precipitation just starts. The final pH of the treated wastewater increased from its initial value. In some catalysts, the final pH of the treated wastewater decreased from its initial value. This trend may be attributed to the enhanced formation of functional group (Garg et al. Citation2005). It was also found that the efficiency of COD reduction due to thermochemical precipitation increased as the initial COD of the effluent increased with optimum chemical mass loading (Verma et al. Citation2011).
3.2. Electrocoagulation (EC) process
3.2.1. Effect on initial pH
The experimental initial pH (pHi) for treatment of wastewater was found to have a significant effect on the efficiency of the EC process. Therefore, its effect in the range of pH 2–0 with a current density (CD) of 78 A/m2, electrode distance of 20 mm and treatment time of 120 min. was investigated for iron, aluminium and copper plate. The results of COD and colour reduction are presented in Figure . It can be observed that maximum 71% COD and 74.5% colour removal at pH 7 by aluminium electrode. Copper electrode shows 67.5% COD and 70.8% colour removal at pH 6 and iron electrode shows 60.5% COD and 65.2% colour removal at pH 6, respectively. The effect may be attributed to metal ions which are found in different forms and phases, depending on the pH and chemical characteristics of the solution (Drogui et al. Citation2008). Depending on the pH of the electrolyte, metal ion undergoes spontaneous reactions to produce corresponding hydroxides and/or polyhydroxides. The hydroxide formed remains in the aqueous stream as a gelatinous suspension, which can remove the pollutants from wastewater either by complexation or by electrostatic attraction followed by coagulation (Naje et al. Citation2015).
3.2.2. Effect of current density
Current density is one of the important parameters that influence the pollutant removal. It not only varies the dosages rate of metal cations but also the bubble production rate, size and the floc’s growth, which all can influence the efficiency of electrocoagulation treatment. Effect of current density on removal efficiency was studied for iron electrode the use of which is economical as compared to aluminium electrode. The current density varied from 39A/m2 to 195A/m2 (1 to 5A) at optimum initial pH of 6 and electrode distance of 20 mm. The results as COD and colour reduction are presented in Figure . Figure shows COD removal efficiencies of 55.4%, 60.5%, 75.2%, 84.4% 76.4% and colour removal efficiencies of 61.2%, 65.2%, 78.4%, 89.7%, 80.1% at CD 39, 78, 117, 156 and 195 A/m2, respectively. The results ascertained increase in the removal efficiency with applied current density. The rate of anodic dissolution of metal increased at higher current densities which resulted in a greater amount of coagulant and precipitant production. Consequently, this resulted in a higher removal efficiency of organics. Apart from this, increase in smaller sized bubbles at high CD results in a higher removal efficiency of organics via H2 flotation, in addition to the effect of coagulation (Song et al. Citation2008). The excess formation of iron and its hydroxide cations at CD = 195 A/m2 resulted in restabilisation of colloids, which reduced COD reduction (76.4%) as compared to 84.4% COD reduction at 156A/m2 . It was also observed that the anode loss was less (0.82 g) at 156A/m2 as compared to 0.85 g at 195A/m2.
3.3. Thermolysis followed by electrocoagulation
The effect of time for the COD and colour reduction of electrochemically treated and thermally treated wastewater was shown in Figure . It was observed that electrochemically treated wastewater showed a COD reduction of 574.39 mg/l (84.4%) and colour reduction 36.05CPU (89.7%) in 2 h of treatment at 156 A/m2 current density, 20 mm electrode distance and 0.82 g anode losses (1.5L). Similarly thermally treated wastewater showed 898.40 mg/l (75.6%) COD and 72.80CPU (79.2%) colour removal in 4 h treatment time at 95 °C temperature and 4 kg/m3 catalyst mass loading. The supernatant obtained after catalytic thermolysis was treated by electrochemical method at optimum conditions showed a better effect in treating the effluent than the individual processes (Figure ). The figures demonstrated that a reaction time of 15 min was adequate to achieve the 97.8% (81 mg/l) of COD reduction and 99.7% (1.05CPU) of colour removal.
3.4. Physicochemical analysis of solid and liquid
3.4.1. Settling
Settling is one of the economical processes used to separate solid and liquid of slurry or suspension. Using the batch sedimentation data, a continuous thickener may be designed (Richardson et al. Citation2003; Rao Citation2010). Figure presents a sedimentation test for solid-liquid interface. The height of the interface in terms of dimensionless height (H/Hi) as a function of settling time for various treatments (thermal treatment, electrocoagulation treatment and combined treatment. The batch sedimentation data were collected in a 100 ml measuring jar. Initially, a steady decrease in the solid/liquid interface was seen, which is called regime of zone settling. Thereafter, transition settling occurred. In third stage, compression of settling solids took place. Overall in the present study, the settling rate was in order of thermal treated > electrochemical treated > combined treated. Results indicated settling at thermal treatment at optimum conditions was better. It may be probably due to the bigger size and more compact aggregated flocs formed in thermally treated SIWW. Analysis of residue after treatment is presented in Table .
Figure 7. Settling of slurry after thermal, electrochemical and combined treatment of sugar industry wastewater.
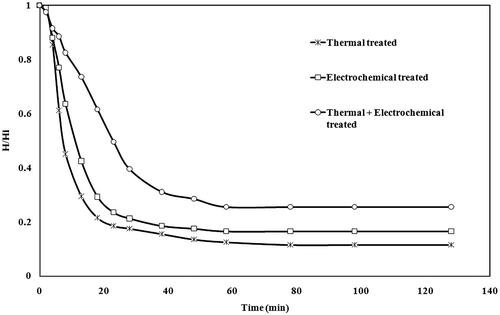
Table 4. Analysis of residue obtained after treatment at optimum parameters.
3.4.2. Filtration
Filtration is one of the steps used to clarify the treated effluent, and it is also important to decide upon the optimal treatment process parameters. The gravity filtration of the slurry was carried out at room temperature using an ordinary filter paper supported on a Buchner funnel, under constant pressure. The filtrate volume obtained as a function of time was observed and a plot between ∆t/∆V and V was drawn for the effluents treated at different pH. The plot in Figure shows a linear relationship. The filtration resistances for the filter media as well as the filter cake were obtained using the filtration equation (McCabe et al. Citation2001):(2)
Figure 8. Filterability of slurry after thermal, electrochemical and combined treatment of sugar industry wastewater.
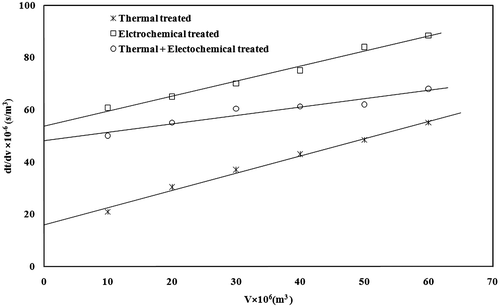
where, Δt is the time interval of filtration, ΔV is the filtrate volume collected up to that time interval, C is the solids concentration in the slurry, V is the total liquid filtrate volume collected up to the time interval t, μ is the viscosity of the liquid filtrate, ΔP is the pressure drop across the filter = ρgh, A is the filtration area, Rm is the resistance of the filter medium, α is the specific cake resistance to filtration. After recording the experimental data on volume of the filtrate as a function of time, a plot of Δt/ΔV versus V was drawn. It is a straight line plot. The values of Rm and α was evaluated from the slope and the intercept of plot and presented in Table . The values of α 0.393 × 10−14, 0.605 × 10−14, 0.679 × 10−14 m/kg and Rm 0.172 × 10−12, 5.012 × 10−12, 6.77 × 10−12 were found for electrochemical treated, combined treated and thermal-treated wastewater. Specific cake resistance values have been reported by Barnes et al. (Citation1981). These values are 4–12 × 1013 m/kg for activated sludge and 3–30 m/kg for digested sludge. Our values are in the range of 2–8 × 1013 m/kg. Similar filtration studies have also been reported by other investigators for treatment of pulp and paper mill effluent (Mahesh et al. Citation2006) and distillery effluent (Chaudhari et al. Citation2007).
Table 5. Filterability of the treated waste water.
3.4.3. Thermal analysis
The TGA, differential thermal analysis (DTA) and differential thermal gravimetery (DTG) curves of the thermally treated and combined treated sludge in oxidising atmosphere is shown in Figures (a) and (b), respectively. The DTA trace shows dehydration and volatilisation (removal of volatiles) of the sample up to 300 °C losing weight of 21.84% for thermal treated and 31.19% for combined treated (CT) sludge. The results indicated that less volatile materials were present in settled sludge. The peak rate of weight loss 0.62 mg/min was seen at temperature Tmax of 254 °C for thermal treated and 0.92 mg at Tmax 162 °C for combined treated sludge. Oxidation of solids was found exothermic; the heat of evolution for thermally treated sludge was 792 J/g and for combined treated sludge was 1250 J/g. Oxidation seems to be completed at 700 °C for thermally treated sludge and 600 °C for combined treated sludge. In 1000 °C, the 79.44% weight of thermal treated and 49.20% weight of combined treated settled sludge as ash found to remain. Thus, sludge of combined treated experiments contained less inorganic material as compare to the thermally treated sludge. Hence, the calorific value of thermally treated sludge is expected to be higher than that of the combined treated sludge. The initial weight loss could be associated with the release of light volatiles (Shak and Wu Citation2015) and absorbed species such as water (Subramonian et al. Citation2014) due to evaporation process.
4. Conclusion
Sugar industries wastewaters were treated for the reduction of COD and colour using catalytic thermal treatment (thermolysis) with/without electrocoagulation. During thermolysis of the fresh effluent, ferrous sulphate was found to be the best catalyst giving 75.6% COD as well as 79.2% colour reduction, respectively, with a catalyst concentration of 6 kg/m3 at pH 10 and 95 °C temperature. The combined experiment of ferrous sulphate catalyst and electrodes gave 97.8% COD reduction and 99.7% colour removal at pH 6, current density 156Am−2, electrode distance 20 mm and treatment time 15 min. The settling rate of the thermal-treated effluent is 80% settle in 25 min of settling time. The specific cake resistance (0.605 × 10−14 m/kg) and filter medium résistance (5.012 × 10−12) of combined treated sludge is less as compared to thermally treated sugar industry wastewater. The residual iron concentration after combined treatment can be utilised as a catalyst in the secondary treatment, e.g. in coagulation. The sludge obtained after combined treatment has a high heating value and hence may find use as a fuel.
Disclosure statement
No potential conflict of interest was reported by the authors.
Notes on contributors
Omprakash Sahu, PhD, is working as an assistant professor in School of Chemical and Food Engineering, BiT Bahir Dar University, Bahir Dar Ethiopia. His main research interests are in Industrial waste water treatment process, waste minimization and recovery. His previous publication includes Sahu OP, and Chaudhari PK, (2014) Removal of color and chemical oxygen demand from sugar industry wastewater using thermolysis processes. Desalination and Water Treatment, 1–10.
Dubasi Govardhana Rao, PhD, is working as a professor in School of Chemical and Food Engineering, BiT Bahir Dar University, Bahir Dar Ethiopia. His main research interests in Biochemical Engineering and wastewater treatment. His previous publication include Rao et al., 2012 wrote book on “Wastewater treatment: advanced processes and technologies”, CRC Press. United States of America.
Arun Thangavel, PhD, is working as an assistant professor in School of Chemical and Food Engineering, BiT Bahir Dar University, Bahir Dar Ethiopia. His main research interest is in Food and industrial microbiology.
Saravanan Ponnappan, PhD, is as an assistant professor in School of Chemical and Food Engineering, BiT Bahir Dar University, Bahir Dar Ethiopia. His main research interest is in Food science and nutrition.
References
- Aradhey A. 2015. “Sugar Annual Report: Global Agricultural Information Report.” GAIN Report Number: IN4029.
- Asaithambi, P., A. R. Aziz, and Wan Mohd Ashri Bin Wan Daud. 2016. “Integrated Ozone—Electrocoagulation Process for the Removal of Pollutant from Industrial Effluent: Optimization through Response Surface Methodology.” Chemical Engineering and Processing: Process Intensification 105: 92–102.10.1016/j.cep.2016.03.013
- Barnes, D., P. J. Bliss, B. W. Gould, and B. W. Vallentine. 1981. Water Wastewater Engineering Systems. New York: Pitman Publishing Inc.
- Chaudhari, P. K., I. M. Mishra, and S. Chand. 2007. “Decolourization and Removal of Chemical Oxygen Demand (COD) with Energy Recovery: Treatment of Biodigester Effluent of a Molasses-Based Alcohol Distillery Using Inorganic Coagulants.” Colloids and Surfaces A: Physicochemical and Engineering Aspects 296 (1): 238–247.
- Chaudhari, P. K., I. M. Mishra, and S. Chand. 2008. “Effluent Treatment for Alcohol Distillery: Catalytic Thermal Pretreatment (catalytic thermolysis) with Energy Recovery.” Chemical Engineering Journal 136 (1): 14–24.
- Chaudhari, P. K., R. Singh, I. M. Mishra, and S. Chand. 2010. “Kinetics of Catalytic Thermal Pretreatment (Catalytic Thermolysis) of Distillery Wastewater and Bio-Digester Effluent of Alcohol Production Plant at Atmospheric Pressure.” International Journal of Chemical Reactor Engineering 8 (1).
- Deokate, A. 2015. “Development of Textile Waste Water Treatment Reactor to Obtain Drinking Water by Solar Powered Electro-Coagulation Technique.” International Journal of Research in Environmental Science and Technology 5 (1): 29–34.
- Drogui, Patrick, Mélanie Asselin, Satinder K. Brar, Hamel Benmoussa, and Jean-François Blais. 2008. “Electrochemical Removal of Pollutants from Agro-Industry Wastewaters.” Separation and Purification Technology 61 (3): 301–310.10.1016/j.seppur.2007.10.013
- Garg, A., I. M. Mishra, and S. Chand. 2005. “Thermochemical Precipitation as a Pretreatment Step for the Chemical Oxygen Demand and Color Removal from Pulp and Paper Mill Effluent.” Industrial & Engineering Chemistry Research 44 (7): 2016–2026.10.1021/ie048990a
- Hampannavar, U. S., and C. B. Shivayogimath. 2010. “Anaerobic Treatment of Sugar Industry Wastewater by Upflow Anaerobic Sludge Blanket Reactor at Ambient Temperature.” International Journal of Environmental Sciences 1 (4): 631.
- Ingaramo, Alejandra, Humberto Heluane, Mauricio Colombo, and Mario Cesca. 2009. “Water and Wastewater Eco-Efficiency Indicators for the Sugar Cane Industry.” Journal of Cleaner Production 17 (4): 487–495.10.1016/j.jclepro.2008.08.018
- Kim, Dae Gun, Woo Yeol Kim, D. ChanYoung Yun, Duk Chang Son, Hyung Suk Bae, Yong Hyun Lee, Young Sunwoo, and Ki Ho Hong. 2013. “Agro-Industrial Wastewater Treatment by Electrolysis Technology.” International Journal of Electrochemical Science 8: 9835–9850.
- Kumar, Pradeep, B. Prasad, I. M. Mishra, and Shri Chand. 2008. “Decolorization and COD Reduction of Dyeing Wastewater from a Cotton Textile Mill Using Thermolysis and Coagulation.” Journal of Hazardous Materials 153 (1-2): 635–645.10.1016/j.jhazmat.2007.09.007
- McCabe, Warren Lee, Julian Cleveland Smith, and Peter Harriott. 2001. Unit Operations of Chemical Engineering. 5th ed. New York: McGraw-Hill.
- Mahesh, S., B. Prasad, I. D. Mall, and I. M. Mishra. 2006. “Electrochemical Degradation of Pulp and Paper Mill Wastewater. Part 1. COD and Color Removal.” Industrial & Engineering Chemistry Research 45 (8): 2830–2839.10.1021/ie0514096
- Naje, Ahmed Samir, Shreeshivadasan Chelliapan, Zuriati Zakaria, and Saad A. Abbas. 2015. “Enhancement of an Electrocoagulation Process for the Treatment of Textile Wastewater under Combined Electrical Connections Using Titanium Plates.” International. Journal of Electrochemical Science. 10: 4495–4512.
- Rao, D. G. 2010. Fundamentals of Food Engineering, 432–439. New Delhi: PHI Learning.
- Rao, Dubasi Govardhana, R. Senthilkumar, J. Anthony Byrne, and S. Feroz. 2012. Wastewater treatment: advanced processes and technologies. United States of America: CRC Press.10.1201/b12172
- Richardson, J.F., J. H. Harker, and J. R. Backhurst. 2003. Coulson and Richardson’s Chemical Engineering, Particle Technology and Separation Processes. Vol. 2. 5th ed. Chennai: Elsevier, a Division of Reed Elsevier India Pvt. Ltd.
- Sahu, Om Prakash, and Parmesh Kumar Chaudhari. 2015. “The Characteristics, Effects, and Treatment of Wastewater in Sugarcane Industry.” Water Quality, Exposure and Health 7 (3): 435–444.10.1007/s12403-015-0158-6
- Sahu, Omprakash. 2016. “Treatment of Agro-Based Industry Wastewater by the Electro-Oxidation Method: Comparative Results from Iron and Aluminum Metal Plate.” Environmental Quality Management 25 (4): 85–106.10.1002/tqem.2016.25.issue-4
- Shak, Katrina Pui Yee, and Ta Wu. 2015. “Optimized Use of Alum Together with Unmodified Cassia Obtusifolia Seed Gum as a Coagulant Aid in Treatment of Palm Oil Mill Effluent under Natural PH of Wastewater.” Industrial Crops and Products 76: 1169–1178.10.1016/j.indcrop.2015.07.072
- Sharma, C., and V. Kumar. 2015. “Analysis of the Volume of the Main Water and Wastewater in a Sugar Manufacturing Process Followed by the Suggestion regarding the Reutilization of the Waste Water.” International Journal of Current Engineering and Technology 5 (3): 01–05.
- Siddiqui, W. A., and M. Waseem. 2012. “A Comparative Study of Sugar Mill Treated and Untreated Effluent- a Case Study.” Oriental Journal of Chemistry 28 (4): 1899–1904.10.13005/ojc/280451
- Song, Shuang, Jie Yao, Zhiqiao He, Jianping Qiu, and Jianmeng Chen. 2008. “Effect of Operational Parameters on the Decolorization of C.I. Reactive Blue 19 in Aqueous Solution by Ozone-Enhanced Electrocoagulation.” Journal of Hazardous Materials 152 (1): 204–210.10.1016/j.jhazmat.2007.06.104
- Subramonian, Wennie, Ta Yeong Wu, and Siang-Piao Chai. 2014. “A Comprehensive Study on Coagulant Performance and Floc Characterization of Natural Cassia Obtusifolia Seed Gum in Treatment of Raw Pulp and Paper Mill Effluent.” Industrial Crops and Products 61: 317–324.10.1016/j.indcrop.2014.06.055
- Teh, Chee Yang, Pretty Mori Budiman, Katrina Pui Yee Shak, and Ta Yeong Wu. 2016. “Recent Advancement of Coagulation–Flocculation and Its Application in Wastewater Treatment.” Industrial & Engineering Chemistry Research 55 (16): 4363–4389.10.1021/acs.iecr.5b04703
- Ulucan, K., H. A. Kabuk, F. Ilhan, and U. Kurt. 2014. “Electrocoagulation Process Application in Bilge Water Treatment Using Response Surface Methodology.” International Journal of Electrochemical Science 9: 2316–2326.
- Verma, S., B. Prasad, and I. M. Mishra. 2011. “Thermochemical Treatment (Thermolysis) of Petrochemical Wastewater: COD Removal Mechanism and Floc Formation.” Industrial & Engineering Chemistry Research 50 (9): 5352–5359.10.1021/ie102576w