ABSTRACT
The gas–solid separation has several industrial applications in engineering process. The collection efficiency and the energy consumption are critical variables in particles separation process. In this study, a non-linear programming problem is proposed to maximise the cyclone efficiency in a 34,560.0 ton/year particles separation–classification plant. A new process integration scheme is proposed to energy consumption minimisation. The units included in the model are a powder feeder, a high efficiency cyclone, a bag filter and a blower. Stairmand and Swift’s high efficiency cyclones models are evaluated and compared. Four particulate materials are considered: limestone, dolomite, sawdust and toner. The particles diameters range studied is 0.1–1000 m. Mass and energy balances are solved with an initial solid concentration of 500 g/m
. Stairmand’s cyclone proved to be more efficient than Swift for all materials analysed. The highest cyclone efficiency is achieved for sawdust (
99%). The cyclone separates more than 34,000 ton/year of particles
m. The energy integration scheme consumes 43% less energy than the basic one for all cases studied. The proposed optimisation model results a valuable tool for optimal process design, reducing the environment process impact and adaptable to operate at high temperatures values with different materials.
1. Introduction
The demand for particulate materials follows closely the business cycle, and grows in the industrialised and industrializing countries. Industries such as plastics, rubber, paper, paints, cement-based, ceramic and aliphatic materials are some classic examples of industrial requirement of fine powders. These materials are expensive due to the sophistication involved in the particles separation and classification process. Equipments modelling and optimisation constitute a present objective in the gas–solid separation field. Cyclones are the most popular particles separators. They are simple and robust units, with low operation cost. For air purification process, the conventional cyclones are commonly used, while for particulate material of a specific size, it is more appropriate to use high efficiency cyclones. In the cement industry, to achieve high resistance concrete using crushed rocks wastes, it is necessary to control specifically the particles distribution size and shape. Concrete production required particles sizes that are generally not satisfied by conventional milling processes. In general, there is an abundance of coarse particles and lack of essential material, i.e. of particles in the range of 4–150 m-diameter, Stone (Citation2012) and Pettingell (Citation2008).
Several studies have recently explored the simulation and optimisation of cyclone separators, Zou et al. (Citation2015), Elsayed (Citation2015), Sgrott et al. (Citation2015) and Shaaban (Citation2011). A high efficiency stairmand cyclone was designed by Fathizadeh et al. (Citation2015) to separate the black powder from natural gas. Funk et al. (Citation2015) proposed a energy saving reducing the pressure drop and the inlet velocity in the cyclone, but they do not report energy savings values. Zhang et al. (Citation2014) proposed a cascade of cyclonic pre-heaters to energy optimise cement kilns; and Elsayed and Lacor (Citation2010) deeply studied the optimisation of cyclone dimensions through computational fluid dynamics. However, is not found in the literature energy integration reports for particles separations process. The development of integrated mathematical models that optimise the separation–classification process and consider energy integration is an uncompleted issue in the area.
In this study, an energy efficiency approach is proposed through a new process scheme for particles separation. The formulation of a non-linear mathematical problem is introduced to optimal process design. The cyclone efficiency is selected as the objective function to maximise. Mass and energy balances, equations for the design of high efficiency cyclones, filters equations designs, pressure drops restrictions and operating conditions are included as linear and non-linear constraints in the optimisation model. The problem is solved for four solid materials, two cyclones models and two process schemes. The paper is structured as follows. Section 2 describes the materials properties and the particles size distributions. Special description of the cyclone main dimensions is explained. Basic and energy integrations process schemes are presented and analysed. Mass and energy balances are listed in Section 3, including the enthalpies calculations. The models considered for the design of high efficiency cyclones and the optimisation problem solved by the algorithm implemented on CONOPT are also described in Section 3. Section 4 summarises the model results and discussions. Finally, conclusions are presented in Section 5.
2. Material and methods
2.1. Materials properties
Four different particulate materials are considered: dolomite, limestone, sawdust and toner. The particle size distributions are analysed by laser diffraction (Analyser Malvern, Mastersizer 2000E, dry dispersion module Sirocco 2000M). shows the particles distributions obtained, and the accumulate distributions. Limestone 1 and 2 distinguishes between two different grinding times for the same material. To evaluate the molecular weights, dolomite is considered as a mineral composed of calcium and magnesium carbonate (); limestone is considered as
; toner is 50% butyl acrylate and 50% iron oxide; and sawdust is considered as oak from bolivia (cerejeira) 48.9% C, 44.5% O and 6.6% H, Himmelblau (Citation1997), Jiménez, Baquero, and Diaz (Citation2006), XEROX (Citation2002) and Gupta (Citation2011).
Table 1. Materials properties.
summarises the materials properties. For air, dolomite and limestone, the specific heat is computed as a temperature function; for sawdust and toner a mean value is used.
2.2. Separation–classification process
Dust separators are the classical equipments to obtain particulate material. Technological developments in cyclone separators permit its use as classifiers with a good particles separation performance up to 5 m-diameter. When industry requirements involve even smaller sizes, the use of more complex equipment is needed to obtain the desired separation. In these cases, bag filters are generally used. The optimal combination cyclone-filter allows to separate particles up to 0.01
m-diameter, yielding technical and economic advantages for the entire separation–classification process, Hoffmann and Stein (Citation2008). The process considered in this work consists of a powder feeder that provides the solid material, a high efficiency cyclone where the main separation of particles occurs, a filter for collecting small particles and a blower device as a flow driver. The materials to be separated and classified may contain moisture initially. To avoid problems in the operation of the equipments due to the presence of water, the air entering the process is preheated in a heat exchanger. shows a Basic Scheme (BS) of the separation–classification process.
and
are the control volumes were energy consumption evaluation are performed. The powder feeder is used to regulate the solid input to the process. These types of units consist of electric motors, solenoids, pneumatic cylinders and regulators. To achieve a proper dosage is necessary to control the material input to the unit and ensure a homogeneous mix of the output material. Depending on variables such as nature and characteristics of the solid material, dynamics required for the discharge and desired accuracy, the feeders are commonly classified into volumetric and gravimetric, Baxter and Prescott (Citation2009). For the process studied in this work the selection of a gravimetric feeder is preferred due to the precision required.
Figure 3. Basic scheme for particles separation–classification process (BS). HE: heat exchanger; PF: powder feeder; CY: cyclone; FI: filter; BL: blower; F: process streams.
and
: control volumes for energy purpose.
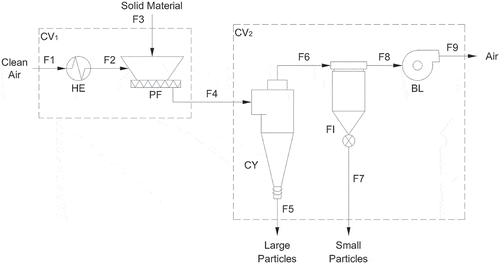
The cyclone is the most important process equipment, where the separation of the larger fraction of particles occurs. Cyclones are robust units, easy handling and low maintenance costs. shows the main dimensions of a tangential input cyclone.
Figure 4. Cyclone main dimensions. Tangential input. a: input height; b: input width; Dc: diameter; B: bottom outlet diameter, Ds: top outlet diameter; S: output height; h: cylindrical height; z: conical height, H: total height.

Filters are commonly used for the separation of fine powders. A common filter type consists of closed metal structures with textile filtering elements arranged vertically. According to the filter design, the elements can be tubular or rectangular known as sleeves or bags, respectively. Filtration occurs as a result of the formation of a primary powder layer on the surface of the sleeves and a subsequent accumulation of dust. This accumulated material forms a ‘cake’ on the sleeves. Once formed the primary layer, the filtration occurs by sieving. Sleeve filters are highly efficient, they can reach efficiencies of for particles of 0.5 microns, and even acceptable values for particles under 0.01 microns in size. The blower is the process flow driver. It is responsible for the whole movement of air and particles from the powder feeder to the cyclone and filter. The location of the blower is at the end of the process, sucking air. This arrangement is convenient because the unit operates with lower dust density, reducing pressure drop and increasing its useful life.
Figure 5. Energy integration scheme (EI). Mix: mixer; SP1: splitter 1; SP2: splitter 2; F: process streams.
and
: control volumes for energy purpose.
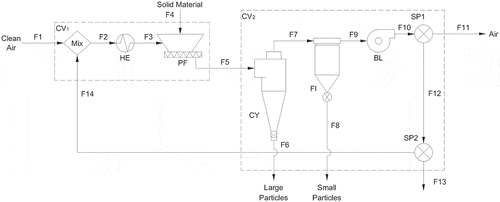
To recover the heat loss in the process, a recirculation of air is proposed us a new energy integration scheme (EI). The air and a few particles that are not separated by the combination cyclone-filter are recirculated to the mixer joining the input of clean air. shows the energy integration scheme. A purge is necessary (stream 13), to prevent the accumulation of fine particles in the process. and
are the control volumes to evaluate process energy balances.
3. Calculation
3.1. Mass and energy balances
Global and component mass balances are formulated for both, the basic and the energy integration schemes. For process analysis, the index i indicates the numbering of the mass flow in each process. That is, the subscript i indicates the number of each stream in the process, I= [1,2,3, ldots, 9]; I
= [1,2,3, ldots, 14], according to Figures and .
The index j indicates the chemical component, either air ( ‘air’) or the solid material to be separated (
‘particles’). The optimisation program does not run for all components simultaneously, for each material the non-linear programming problem was coded. In each program the set ‘particles’ correspond to ‘limestone 1’, ‘limestone 2’, ‘dolomite’, ‘sawdust’ or ‘toner’.
The set of equations relating each component flow f(i,j), with total flow F(i) and the mass fractions x(i,j) are expressed as:
Considering e process units, E = [powder feeder, heat exchanger, cyclone, filter, blower, splitter 1, splitter 2], global and component mass balances are performed. For the whole process the balances are also added:
Mass fractions are calculated for each stream considering cyclone and filter efficiencies. shows the values obtained and the final expressions for x(i,j). The corresponding equations are incorporated to the mathematical model as non-linear constraints.
Table 2. Mass fractions x(i,j) for BS and EI process streams.
The enthalpies values for each stream are expressed as:
T is the reference temperature adopted (293K). The Cp
(T) [J/gmol K] are the expressions listed in for each material. For air, limestone and dolomite the integrated expressions for enthalpies evaluations [J/kg] are:
For sawdust and toner the integrated enthalpies [J/kg] are evaluated as:
Energy balances were evaluated over the control volumes ( and
), using the enthalpies expression developed before and the component flow streams (fc(i,j)). The balances for the BS scheme are:
The corresponding energy balances for EI scheme are:
The process energy consumption are represented by the [J/s] values, while
[J/s] represents the energy losses.
3.2. Models for the design of high efficiency cyclones
The cyclone efficiency is defined as the mass percentage of incoming particles that are separated or retained at the bottom of the cyclone. There is not a simple theoretical method for its calculation, so different theories have been developed based on experimental approaches, Dirgo and Leith (Citation1985), Leith and Licht (Citation1972) and Gil, Romeo, and Corts (Citation2002). These theories establish different relations between variables such as cyclone efficiency, particles size, geometric ratios, gas flow rate and operating temperatures. The particle removal efficiency is based on the number of turns or external vortices that the gas stream takes inside the cyclone. One of the relationship between cyclone fractional efficiency and some parameters and operating conditions is given by:
where N is the number of turns or vortices, the particle density (kg/m
),
the particle diameter (m),
the air inlet velocity (m/s) and
the viscosity of air (Pa
s). The number of turns or vortices N, is defined as the turns present in the gas stream inside the cyclone. This parameter can be estimated from the dimensions of the cyclone as follows:
Equation 17 provides the cyclone efficiency for a given particle size k. To obtain the global cyclone efficiency the particles distributions () and the specific cutting size must be considered. A reasonable value for the cutting size is 10 m-diameter, meaning that at least 50% of the particles greater than this value will be retained in the cyclone. The overall efficiency of the cyclone is expressed as:
where m(k) is the mass percentage of particles of size k according to the corresponding particle distribution (). This efficiency is valid for low solids contents, because ignores the particle–particle interaction and should be used for dust concentrations not exceeding 2 g/m (C1), Hoffmann and Stein (Citation2008), Gil, Romeo, and Corts (Citation2002) and Echeverri Londoño (Citation2006). Previous work showed that the cyclone separation efficiency increases with the initial powder concentration, Paulo, Diaz, and Barbosa (Citation2013); Trefz and Muschelknautz (Citation1993).The highest solid concentration tested on Paulo, Diaz, and Barbosa (Citation2013) is considered for this paper
. This operating value is an equality constraints in the mathematical model. To correct the cyclone efficiency for higher particle concentrations (C2) the Smolik relation is necessary, Hoffmann and Stein (Citation2008), Svarovsky (Citation1981) and Gil, Romeo, and Corts (Citation2002):
Temperature changes affect the gas density and viscosity. These changes also affect the cyclone efficiency, Echeverri Londoño (Citation2006), Gimbun et al. (Citation2005), Magwai and Bosman (Citation2008), Chuah, Gimbun, and Choong (Citation2006) and Bohnet (Citation1995). The corrections are expressed between the reference temperature T and the cyclone inlet temperature
(363K):
where is the air density evaluated at the cyclone temperature, and
is the air density evaluated at the reference temperature.
The air input velocity is a critical variable. Low values can produce sedimentation of larger particles, whereas large velocities can re-suspend the collected material. The second situation decreases the operation cyclone efficiency. This phenomenon is considered by the saltation velocity (Vs). A semiempirical expression for this variable is considered, Kalen and Zenz (Citation1974), Berezowski and Warmuziski (Citation1993) and Chen and Chen (Citation1995):
where . W is the equivalent velocity, parameter that depends on the fluid and the particle properties:
Experimental correlations show that for maximum cyclone efficiency the gas inlet velocity should be 1.25 times the saltation velocity, this limit can be extended up to 1.35 to avoid re-suspension of collected particles, Salcedo and Cándido (Citation2001):
The heat exchanger preheats the air entering the process to reach a temperature of 363K at the entrance of the cyclone. The flow rate input to the process is constant .
Diverse models to estimate cyclones pressure drops are available in literature. These models involve different degrees of complexity and vary in terms of the aspects that they account for. In this study, the task is to estimate the pressure drop in a smooth-walled cyclone operation at low solids loading, so the simple empirical model of Shepherd–Lapple is consider. Hoffmann and Stein (Citation2008) listed the models than can be used when the cyclone has rough walls, e.g. due to refractory lining, or is operating at high loading. In these more complex cases the models of Barth, Casal-Martinez, Muschelknautz or Stairmand would be more appropriate, Shepherd and Lapple (Citation1939), Hoffmann and Stein (Citation2008) and Cortés and Gil (Citation2007).
The pressure drop in the cyclone studied is evaluated by Shepherd–Lapple model:
where is the pressure drop in pascals and NH the number of speed heads at the cyclone inlet:
where K is a constant, equal to 16 for tangential entries cyclones.
Table 3. Geometric constraints for different cyclones models.
Different models of high efficiency cyclones are analysed and compared. Stairmand (ST) and Swift (SW) models are tested in this paper regarding previous results, Paulo, Diaz, and Barbosa (Citation2013). shows the different geometric ratios. They are included into the non-linear model as design constraints.
Table 4. Optimal process variables for BS scheme. C2:500 g/m.
Table 5. Energy consumptions for different process schemes and materials.
3.3. Optimisation algorithm
Considering the equations and constraints presented in the previous sections the following non-linear optimisation problem (NLP) is formulated for maximizing the cyclone efficiency.
The cyclone efficiency is selected as the objective variable. The independent variables in the model are the cyclone diameter (Dc), the inlet gas velocity (Ve), and the stream flows (fc(i,j)). More than hundred dependent variables are necessary depending on the process scheme. Air and solid process input are kept as constant. Some operating conditions, such as the cyclone inlet temperature, are added as equality constraints. A maximum pressure drop restriction is added (2,488.2 Pa). Lower and upper variable bounds are included as inequality constraints. The purpose is to find the optimal flux distributions, the energy consumptions and the design variables that maximise the cyclone efficiency.
Twenty cases are solved, varying the solids materials, the cyclone models, and the process schemes. For the BS, each NLP includes 188 equations and 167 variables. For the EI, the problems solved include 246 equations and 211 variables. The non lineal programming problems are solved through the Generalised Reduced Gradient Method, implemented in CONOPT, GAMS (Brooke, Kendrick, and Meeraus Citation2005; Edgar, Himmelblau, and Lasdon Citation2001). The gradients of the constraints and the objective function are employed in the non-linear problem to determine the search direction in the space of variables to estimate (cyclone diameter, height and width of the tangential inlet, input velocity, streams flows, etc.).
4. Results and discussions
shows the key process variables obtained for the basic scheme.
The highest cyclone efficiency is achieved for sawdust (99%), and the lowest for toner (78%). These results are consistent and concordant with , showing that sawdust has the largest particles, and toner has the lowest particle diameters. For limestone-1 and limestone-2 high efficiencies values are achieved (
90%), whereas for dolomite an acceptable efficiency value is obtained (86%). ST cyclone model is slightly more efficient than SW model, being the difference much appreciable for toner. The results for the principal cyclone dimensions are consistent for each model. ST cyclones have a mean diameter value of 0.97 m over the materials studied, and 1.06 m for SW models. The total mean cyclone height is 3.86 m for ST and 4.12 m for SW. These results can project the use of the same cyclone size for the different materials, providing versatility to the process. The ST cyclone result more efficient and smaller than the SW model.
For all the cases studied, the combination cyclone-filter proved to be highly efficient to classify particulate matter, achieving a final purity of air 99.5% at the end of the process. Figures and present the optimal stream flows obtained for sawdust for BS and EI schemes.
The flow of air to the process is 68,548.9 ton/year, and the input of solid material is 34,560.0 ton/year for both schemes. The plant is considered continuous, operating 8,000.0 h per year. The cyclone separates 34,527.1 ton/year of large particles for the BS scheme, and 34,367.3 ton/year for the EI scheme. The difference is 0.5%. The savings in the clean air stream between the BS and EI schemes is greater than 99%. The filter separates 31.3 ton/year of small particles for the BS scheme. For the EI scheme, the filter is six time more efficient and separates 192.7 ton/year.
shows the result of the energy balances and the cost estimation of the energy savings. The values listed correspond to ST model cyclone. The plant energy consumptions (Q) and energy losses (Q
) are represented in MWh, while the energy savings values are expressed in MWh and US$/h. For the energy cost evaluations, the considered industrial electricity tariff is 800 US$/MWh, supplied by a local cement plant.
In all cases studied, EI scheme consumes 43% less energy than the BS scheme. The energy savings are calculated comparing the consumptions () between BS and EI schemes. A mean energy saving of 393 US$/h is obtained for limestone 1 and 2, dolomite and toner. For the same materials, the energy losses (
) remain constant between BS and EI schemes (130–142 MWh). It is important to note that sawdust has a better performance compared with the others materials. Its energy saving value is substantially higher (8,508 US$/h), and its energy losses are reduced a 49% comparing the EI and BS schemes.
5. Conclusions
A non-linear programming problem is developed to optimise the efficiency collection in a 34,560.0 ton/year particles separation–classification plant. The generalised reduced gradient method, is used to find the optimal process design variables. Four different materials with a wide diameters range are studied (0.1–1000 m). A high process particle loading is used (500 g/m3). The objective function is defined to maximise the cyclone collection efficiency. Six operation and geometric variables are selected as manipulated variables. Stairmand’s cyclone proved to be more efficient than Swift, for all materials studied. The highest cyclone efficiency is achieved for sawdust ( 99%). The cyclone separates more than 34,000 ton/year of particles
10
m which represent and overall process efficiency superior to 99.9%. The integration scheme consumes 43% less energy than the basic scheme for all cases studied, reducing the environment process impact. Future extension of this work includes a computational fluid dynamics simulation to correlate the numerical model results.
Notes on contributors
C. I. Paulois currently working as an assistant research in CIFICEN-CONICET and teaching at Department of Chemical Engineering at UNCPBA University. The author’s research interests include modeling and optimisation of process systems, and the study of particle separation equipment.
E. Borsais a PhD student at UNCPBA University, and teacher at Department of Mathematics. The author’s research interest includes the microscopic study of particulate matter and its relationship with the macroscopic aspect of separation process.
M. R. Barbosais a Professor in Transport Phenomena at UNCPBA University, currently retired. The author’s research interests include fluid mechanics, corrosion and solid separation equiment.
Additional information
Funding
Notes
No potential conflict of interest was reported by the authors.
References
- Baxter, Thomas, and James Prescott. 2009. “Chapter 28 - Process Development, Optimization, and Scale-up: Powder Handling and Segregation Concerns.” In Developing Solid Oral Dosage Forms, edited by Yihong Qiu, Yisheng Chen, Geoff G.Z. Zhang, Lirong Liu, and William R. Porter, 637–665. San Diego: Academic Press. http://www.sciencedirect.com/science/article/pii/B978044453242800028X
- Berezowski, Marek, and Krzysztof Warmuziski. 1993. “Gas Recycling as a means of Controlling the Operation of Cyclones.” Chemical Engineering and Processing: Process Intensification 32 (6): 345–347. http://www.sciencedirect.com/science/article/pii/0255270193800229
- Bohnet, Matthias. 1995. “Influence of the Gas Temperature on the Separation Efficiency of Aerocyclones.” Chemical Engineering and Processing: Process Intensification 34 (3): 151–156. http://www.sciencedirect.com/science/article/pii/025527019404001X
- Brooke, A., D. Kendrick, A. Meeraus, R. Raman, and R. E. Rosenthal. 2005. GAMS: A Users Guide. Washington, DC: GAMS Development Corporation.
- Chen, X. Dong, and John J. J. Chen. 1995. “On Gas Recycling as a means of Improving the Operation of Cyclones.” Chemical Engineering and Processing: Process Intensification 34 (4): 379–383. http://www.sciencedirect.com/science/article/pii/0255270194005516
- Chuah, T. G., Jolius Gimbun, and Thomas S. Y. Choong. 2006. “A {CFD} Study of the Effect of Cone Dimensions on Sampling Aerocyclones Performance and Hydrodynamics.” Powder Technology 162 (2): 126–132. http://www.sciencedirect.com/science/article/pii/S0032591005005498
- Cortés, C., and A. Gil. 2007. “Modeling the Gas and Particle Flow inside Cyclone Separators.” Progress in Energy and Combustion Science 33 (5): 409–452. Cited By 0. http://www.scopus.com/inward/record.url?eid=2-s2.0-34250839553\&partnerID=40\&md5=8bcc4b50cb427450d3ce76329d074a67
- Dirgo, John, and David Leith. 1985. “Performance of Theoretically Optimised Cyclones.” Filtration and Separation 22 (2): 119–125. Cited By 23. http://www.scopus.com/inward/record.url?eid=2-s2.0-0022024772\&partnerID=40\&md5=8412e321058f3267ee249937670fda55
- Echeverri Londoño, C. A. 2006. “Diseo óptimo de ciclones.” Revista Ingenierías Universidad de Medellín 5: 123–139.
- Edgar, Thomas F., David M. Himmelblau, and Leon S. Lasdon. 2001. Optimization of Chemical Processes. 2nd ed. New York: McGraw-Hill. Includes bibliographical references and indexes.
- Elsayed, Khairy. 2015. “Design of a Novel Gas Cyclone Vortex Finder Using the Adjoint Method.” Separation and Purification Technology 142: 274–286. http://www.sciencedirect.com/science/article/pii/S1383586615000398
- Elsayed, Khairy, and Chris Lacor. 2010. “Optimization of the Cyclone Separator Geometry for Minimum Pressure Drop Using Mathematical Models and {CFD} Simulations.” Chemical Engineering Science 65 (22): 6048–6058. http://www.sciencedirect.com/science/article/pii/S0009250910005245
- Fathizadeh, Nadimeh, Ali Mohebbi, Saeid Soltaninejad, and Masoud Iranmanesh. 2015. ““Design and Simulation of High Pressure Cyclones for a Gas City Gate Station Using Semi-empirical Models, Genetic Algorithm and Computational Fluid Dynamics.” Journal of Natural Gas Science and Engineering 26: 313–329. http://www.sciencedirect.com/science/article/pii/S1875510015002759
- Funk, P. A., K. Elsayed, K. M. Yeater, G. A. Holt, and D. P. Whitelock. 2015. “Could Cyclone Performance Improve with Reduced Inlet Velocity?” Powder Technology 280: 211–218. http://www.sciencedirect.com/science/article/pii/S0032591015003009
- Gil, A., L. M. Romeo, and C. Corts. 2002. “Effect of the Solid Loading on a Pressurized Fluidized Bed Combustors Cyclone with Pneumatic Extraction of Solids.” Chemical Engineering and Technology 25 (4): 407–415. Cited By 0. http://www.scopus.com/inward/record.url?eid=2-s2.0-0036537642\&partnerID=40\&md5=1a0cbcfc3e14f4c5b3568bff31cee58f
- Gimbun, J., T. G. Chuah, A. Fakhru’l-Razi, and T. S. Y. Choong. 2005. “The Influence of Temperature and Inlet Velocity on Cyclone Pressure Drop. A CFD Study.” Chemical Engineering and Processing: Process Intensification 44 (1): 7–12. Cited By 0. http://www.scopus.com/inward/record.url?eid=2-s2.0-4744372573\&partnerID=40\&md5=82149f257d29b2cf81a00da54ae99d8a
- Gupta, Harsh. 2011. “Encyclopedia of Solid Earth.” Geophysics 1: 1539.
- Himmelblau, D. M. 1997. “Principios básicos y cálculos en ingeniería química.” Pearson Educación. https://books.google.com.ar/books?id=JgysV9f1HmEC
- Hoffmann, A. C., and L. E. Stein. 2008. “Gas Cyclones and Swirl Tubes.” Principles, Design and Operation 2: 422.
- Jiménez, L. F., M. C. Baquero, and J. J. Diaz. 2006. ““Carbonizados de Origen Vegetal (COV) Para la Generación de Antroposoles Obtención y Caracterización Fisicoquímica.” Revista Colombiana de Química 35 (2): 177–190. http://www.redalyc.org/articulo.oa?id=309026669001
- Kalen, B., and F. A. Zenz. 1974. “Theoretical Empirical Approach to Saltation Velocity in Cyclone Design [Recent Advances in Air Pollution Control].” American Institute of Chemical Engineering Progress Symposium Series 70 (137): 388–396. Cited By 0. http://www.scopus.com/inward/record.url?eid=2-s2.0-0016308967\&partnerID=40\&md5=a7d2a57f54b168eaf91043b22317b6e0
- Leith, D., and W. Licht. 1972. “The Collection Efficiency of Cyclone Type Particle Collectors-a New Theoretical Approach.” American Institute of Chemical Engineers (AIChE) Symposium Series\#126 68: 196–206.
- Magwai, M. K., and J. Bosman. 2008. “The Effect of Cyclone Geometry and Operating Conditions on Spigot Capacity of Dense Medium Cyclones.” International Journal of Mineral Processing 86 (1–4): 94–103. Cited By 0. http://www.scopus.com/inward/record.url?eid=2-s2.0-39649088669\&partnerID=40\&md5=b1f8ad4b1af83ef00ab84662cc2384a8
- Paulo, C. I., M. S. Diaz, and M. R. Barbosa. 2013. Diseño Óptimo de un Proceso de Separación de Partículas Finas. Proceedings of VII CAIQ 2013 y 2das JASP, Rosario-Patio de la Madera-Argentina.
- Pettingell, Hugo. 2008. “An Effective Dry Sand Manufacturing Process from Japan Potential to Replace Natural Sand Entirely in Concrete.” Quarry Management Magazine 1: 1–6.
- Salcedo, R. L. R., and M. G. Cándido. 2001. “Global Optimization of Reverse-flow Gas Cyclones: Application to Small-scale Cyclone Design.” Separation Science and Technology 36 (12): 2707–2731. doi:10.1081/SS-100107221.
- Sgrott, O. L., D. Noriler, V. R. Wiggers, and H. F. Meier. 2015. “Cyclone Optimization by COMPLEX Method and CFD Simulation.” Powder Technology 277: 11–21. http://www.scopus.com/inward/record.url?eid=2-s2.0-84924705786\&partnerID=40\&md5=40327a3ed3d01bb3b6e1a3761045ffbe
- Shaaban, S. 2011. “Numerical Optimization and Experimental Investigation of the Aerodynamic Performance of a Three-stage Gas-solid Separator.” Chemical Engineering Research and Design 89 (1): 29–38. http://www.sciencedirect.com/science/article/pii/S0263876210001243
- Shepherd, C. B., and C. E. Lapple. 1939. Air Pollution Control: A Design Approach. 2nd ed. Wove Land Press Inc..
- Stone, Luck. 2012. “Corporation.” Dry Engineered Sand Solutions. https://www.agg-net.com/files/aggnet/attachments/articles/dry_engineered_sand_solutions.pdf
- Svarovsky, L. 1981. “Preface.” In Solid-Gas Separation, Vol. vii Vol. 3 of Handbook of Powder Technology, edited by Ladislav Svarovsky. Elsevier Science BV. http://www.sciencedirect.com/science/article/pii/B9781483256672500051
- Trefz, Michael, and Edgar Muschelknautz. 1993. “Extended Cyclone Theory for Gas Flows with High Solids Concentrations.” Chemical Engineering and Technology 16 (3): 153–160. Cited By 0. http://www.scopus.com/inward/record.url?eid=2-s2.0-0027611254\&partnerID=40\&md5=d29e61f189de114f75db6f3dbff3c4ea
- XEROX. 2002. Ficha de Seguridad. Technical Report. España: XEROX.
- Zhang, H., R. Dewil, J. Degrve, and J. Baeyens. 2014. “The Design of Cyclonic Pre-heaters in Suspension Cement Kilns.” International Journal of Sustainable Engineering 7 (4): 307–312. Cited By 1. https://www.scopus.com/inward/record.uri?eid=2-s2.0-84911994250\&partnerID=40\&md5=0999c5b54935606da1310696754814b4
- Zou, K., Z.-J. Ai, K. Hu, H.-J. Qian, and B.-W. Fu. 2015. “Performance Optimization of Cyclone Separator based on the Wear Structure.” Guocheng Gongcheng Xuebao/The Chinese Journal of Process Engineering 15 (1): 9–15. Cited By 0. http://www.scopus.com/inward/record.url?eid=2-s2.0-84925611485\&partnerID=40\&md5=86d168c4fbb73a1a9958f5e29c029c92