ABSTRACT
The growing industrial demand for sustainable materials has led to a paradigm shift in the focus from synthetic polymers towards natural fibres. This paper deals with the challenges and opportunities associated with the use of natural fibre-reinforced polymer composites in various industrial applications. Natural fibres being biodegradable, light in weight, cost-effective and environment friendly are good candidate materials for modern industrial applications. Use of natural fibres in various industries with a focus on automotive and furniture industry has been discussed. The commonly used natural fibres in polymer composites including jute, hemp, sisal, kenaf, bamboo, cotton, flax, abaca, coir etc. have been dealt with in this paper. The literature revealed that tensile strength and other mechanical properties of these fibres are comparable to synthetic fibres like glass or carbon fibres. However, the temperature stability of polymers limits their extensive use and remains an issue to be addressed.
1. Introduction
In the last decade, natural fibres are being preferred over synthetic fibres as the reinforcement in polymeric composites due to their environmental and economical benefits. Owing to the global energy crisis and quest for sustainability, the unique features of natural fibres like abundance, non-toxicity, high performance, versatility, easy processing at low cost, no irritation to respiratory system, skin, eyes and non-corrosive nature, natural fibre-reinforced polymer composites (NFPCs) have got more attention as compared to synthetic fibre-reinforced polymeric composites. In addition to this, the energy consumption by natural fibres during their production is only 17% as compared to synthetic fibres like glass fibres (Shalwan and Yousif Citation2013; Holbery and Houston Citation2006; Dhakal, Zhang, and Richardson Citation2007). Use of these composites in different sectors has a great potential to improve the pace of manufacturing and recycling with environmental friendliness (Bledzki and Gassan Citation1999). As suggested by a recent report, NFPC materials market is expected to grow to US$ 531.3 million in the year 2016 from US$ 289.3 million in 2010. The report also revealed that the major increase in the use of NFPC is due to increase of these composites in automotive sector. NFPCs have found considerable applications in the field of automotive and construction due to good specific strength, low density, biodegradability, low density, better tool life and renewability (Caprino et al. Citation2015). NFPCs offer extensive applications in low-cost housing, consumer goods, civil structures, and different other applications (Satyanarayana, Arizaga, and Wypych Citation2009; Pandey, Ahn, and Lee Citation2010). Moreover, NFPCs were found suitable for panelling elements in airplanes and trains (Mohanty, Misra, and Hinrichsen Citation2000).
The most common natural fibres used in industrial applications include flax, kenaf and hemp, because of their better fibre strength properties. In , the tensile strength and elastic modulus of the various natural and synthetic fibres have been provided. A comparison of the specific strength (tensile strength/density) and specific modulus (modulus of elasticity/density) of various natural fibres to E-glass reveals that E-glass-specific strength is superior to all natural fibres, although flax fibre is very competitive (1275 vs. 1000, respectively). However, the specific modulus of kenaf (42.9) and flax (54) exceeds to that of E-glass (28). These values imply that the natural fibre characteristics are comparable or, in some cases, better than those of glass fibres (Holbery and Houston Citation2006). Fowler, Mark Hughes and Elias (Citation2006) and Alix et al. (Citation2008) have opined that cellulose plays a crucial role in strength and durability of fibres, and the percentage of cellulose in fibre directly impacts its strength and durability.
Table 1. Properties of natural and synthetic fibres (Bledzki and Gassan Citation1999; Holbery and Houston Citation2006; Hutchinson Citation2006; Eichhorn et al. Citation2002; George, Sreekala, and Thomas Citation2001; Saheb and Jog Citation1999; Chand and Fahim Citation2008; Hutten Citation2007; Khalil et al. Citation2012; Shinoj et al. Citation2011; Sen and Reddy Citation2011; Xiaobo Li Citation2004; Marrot et al. Citation2013; Mahjoub et al. Citation2014; Udoeyo and Adetifa Citation2012; Ramnath et al. Citation2014; Berger Citation1983; Yusriah et al. Citation2014; Hossain et al. Citation2014; Paturau Citation1987; Pothan, Thomas, and Groeninckx Citation2006; Mwaikambo Citation2006).
1.1. Sources and properties of natural fibres
Based on the source, natural fibres can be classified into bast fibres (jute, flax, hemp, kenaf, ramie etc.), leaf fibres (sisal, palm, manila, caraua etc.), seed fibres (cotton, kapok etc.), fruit fibres (coconut, coir etc.) and stalk fibres (bamboo, wheat, rice, grass, corn etc.). Natural fibres are generally harvested yearly and in some cases like jute, hemp and kenaf can be harvested two to three times yearly. As reported by Holbery and Houston (Citation2006), all the natural fibres have a high CO2 assimilation rate i.e. they consume high amount of CO2, thus helping in reducing the carbon content in atmosphere. The various sources/origin of natural fibres are represented in .
Figure 1. Sources of natural fibres (Conceptualized from Ahmad, Choi, and Park Citation2015; Ashori Citation2008).

The documented literature suggests that natural fibres when used as reinforcements with polymers result in improved mechanical properties and can act as a suitable replacement to the artificial fibres. Generally, the synthetic fibres have much higher strength than the natural fibre but in case of specific modulus most of the natural fibres are far better than the synthetic fibres as shown in . As various mechanical properties of natural fibres like tensile strength (σ), breaking strain (ɛ), Young’s modulus (E) etc. have varying cited values mainly due to non-standard testing conditions. The proper compliance to the testing standards for determination of these properties can further bring more clarity and could pave way for widespread use of NFPCs in structural applications (Symington et al. Citation2009).
Generally, natural fibres are lignocellulosic in nature consisting of cellulose microfibrils in helical form in the matrix of hemicelluloses and lignin (Young Citation1986; Mohanty, Misra, and Drzal Citation2001; Zafeiropoulos et al. Citation2002). presents the different chemical compositions of various natural fibres. Plant fibres are mainly composed of lignin, cellulose, hemicellulose, waxes and some other compounds (Sarkanen and Ludwig Citation1971).
Table 2. Chemical composition of common natural fibres (Hutten Citation2007; Khalil et al. Citation2012; Shinoj et al. Citation2011; Han and Rowell Citation1997; Averous and Le Digabel Citation2006; Wambua, Ivens, and Verpoest Citation2003; Xue Li, Tabil, and Panigrahi Citation2007; Kalia and Sheoran Citation2011; Ramachandra, Kamakshi, and Shruthi Citation2004; Mark Citation1986; Preethi and Balakrishna Murthy Citation2013).
The strength of natural fibres depends mainly on cellulose content, microfibrillar angle and the aspect ratio. More the value of cellulose content, higher will be the strength of fibre and it is opposite in case of microfibrillar angle i.e. lower value of microfibrillar angle provides higher strength to fibre. Normally, fibres are characterised by the aspect ratio (Mallick Citation2010; Saravana Bavan and Mohan Kumar Citation2010). The density of natural fibres has a maximum value of about 1.5 g/cm3. Hollow natural fibres or fibres which are less dense in their natural form like wood can be densified by suitable processing (Saxena et al. Citation2008). The other parameters which influence the physical properties of NFPCs are fibre–matrix adhesion, volume fraction of the fibres in the composite, fibre dispersion, modulus and strength of fibres and toughness of the matrix (Young Citation1986; Giancaspro, Papakonstantinou, and Balaguru Citation2009). The mechanical properties of NFPCs especially the tensile properties improve with the increase in fibre volume fraction (Hull and Clyne Citation1996). shows various types of degradation for natural fibres and factors responsible.
Figure 2. Current scenario for the applications of NFPCs (Conceptualized from Smith and Wolcott Citation2006).
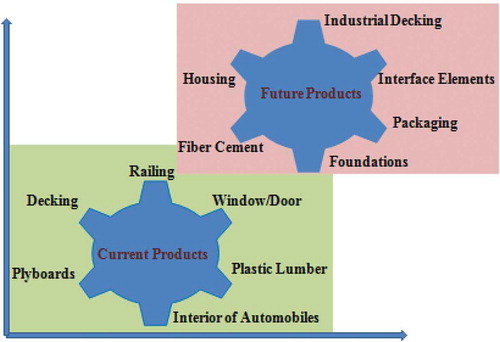
Figure 3. Factors responsible of different types of degradation (Conceptualized from Rowell Citation1998; Amar K Mohanty, Misra, and Hinrichsen Citation2000).
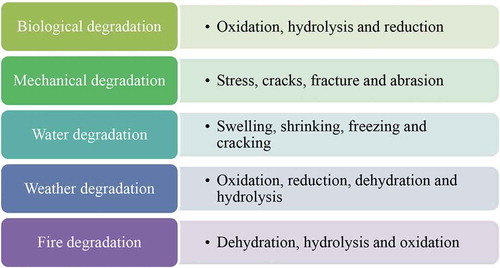
1.2. Polymer and their composites
Polymer plays the crucial role of matrix phase in the NFPCs. Thermosets as well as thermoplastics both can be used as the resin in polymer composites. Thermoplastics are better than thermosets on different parameters like low processing cost, design flexibility, better mechanical properties etc. Polyester, epoxy, polypropylene (PP), poly vinyl chloride, polybutylene succinate (PBS), polyurethane, phenol-formaldehyde, polyethylene (PE) and polystyrene are the major polymers that have been used as matrix phase in polymeric composites. Properties of composites are governed by matrix–fibre interface, fibre properties and aspect ratio of the fibres. Matrix–fibre interface is very crucial in stress transfer from matrix to fibre (Saheb and Jog Citation1999).
Matrix–fibre interface can be improved by various surface treatments/chemical treatments like acetone, silane and alkali treatment etc. An alternate way to improve matrix–fibre interface is the use of coupling agents and grafting. Research studies have revealed maleic anhydride as an effective compatibilizer for better matrix–fibre adhesion (John and Anandjiwala Citation2008; Singha et al. Citation2009; Mohanty et al. Citation2004; Gao and Mäder Citation2006; Samal, Mohanty, and Nayak Citation2009). Natural fibres when used as the reinforcement in the matrix of petroleum-based polymer result in a partially biodegradable composite; however, if the polymer used is biodegradable, then the resulting composite is green composite. When two or more natural fibres are used with the polymer as reinforcement, then the resulting composite is hybrid composite (Bajpai, Singh, and Madaan Citation2014). The hybrid composites offer better mechanical and physical properties in comparison to conventional composites. The properties can be tailored by selecting the orientation of the fibres, length of the fibres, content of each reinforcement and chemical treatment of the fibres (Chaudhary, Bajpai, and Maheshwari Citation2018). Though there are several review articles available on applications of natural fibres, the paper is articulated in a manner to discuss the various industrial applications of NFPCs.
2. Natural fibres in structural automotive applications
With the global trend in the automotive sector towards lightweight materials and with stringent environmental laws, the use of natural fibres is increasingly gaining importance (Anand et al. Citation2017). Amongst the numerous natural fibres, only a few fibres find automotive applications. In the last decade, NFPCs have been used in European automotive sector. The recent legislation passed by European Union that 80% of a vehicle must be recyclable or reused by the end of 2006 and by 2015 it should be 85%. Use of natural fibres in automotive industries has given more impetus to research in the field of NFPCs. The use of polyester and PP-based natural fibre composites to produce different components for automobiles is already in vogue in German automotive industries (Karus and Kaup Citation2002; Silva et al. Citation2006).
Schuh (Citation1999) reported predominant use of natural fibres as reinforcement for door panels, rear parcel shelf, seat coverings and various damping and insulation parts etc. ‘MANACA’ (car panel) banana-reinforced polymer composite was designed and fabricated by Al-Qureshi (Citation1999) who found that fibre and matrix bonding was excellent and there were no clues of debonding or delamination. Davoodi et al. (Citation2010) used Kenaf/glass fibre-reinforced epoxy hybrid composite as structural components in car bumper beams that enhanced the mechanical properties of the said component. Modulus and tensile strength of the hybrid composite were found more than the typical material of car bumper beam and that paved the way for its use as structural components in some car bumper beams.
Alves et al. (Citation2010) used jute fibres as a replacement to glass fibres in frontal bonnet of a vehicle to check on different aspects like environmental, social, technical and economical. Except technical aspect, jute fibres provide better performance than glass fibres in this structural application. Kim et al. (Citation2011) reinforced poly lactic acid (PLA) and PBS (biopolymers) with pineapple and cassava flour to check total volatile organic compound emissions and it was compared with synthetic polymers like PP and PE. Significant reduction in odour emissions was found for pineapple, cassava/PLA, PBS-based composites and this property is very useful in automotive interior components. Ramnath et al. (Citation2014) investigated mechanical properties of abaca, jute and their hybrid composites along with glass fibre in all three cases. The maximum volume fraction of fibres in all three composites was set to 0.4. The study revealed that tensile strength of hybrid composite was much higher than other composites. Moreover, the impact and flexural strength of abaca-based composite as reported by the authors are also higher than that of jute and hybrid composites. The authors also concluded that hybrid composite is good replacement for various application. Moreover, abaca-based composite can be used in cases of higher impact strength requirement. The authors also suggested that abaca and jute fibres can be used as reinforcement in polymeric composites to make automotive components like mudguard and engine cover. Zhong, Lv and Wei (Citation2007) developed sisal/urea-formaldehyde composite through compression moulding technique. The authors investigated the effect of fibre loading on mechanical properties. The researchers have concluded that composites with 30 wt.% sisal fibre exhibited best results for flexural strength and composites with 50 wt.% sisal fibre exhibited maximum impact strength. Abdellaui et al.(Citation2015) studied the effect of number of jute layers on mechanical properties of jute/epoxy laminated composite prepared using compression moulding technique. The researchers observed that a number of fibre layers have a significant effect on the mechanical properties. The study revealed that composites with five layers of fibre exhibited better mechanical properties.
The study carried out by Saxena, Nandan and Ramakrishan (Citation2011) revealed that NFPCs possess significant advantages in various structural applications in Indian railways. In railway industry, floor/roof panels, berths, partitions, modular toilets are made up of NFPCs. Use of natural fibres in railways is critical in achieving high speed, low power consumption, weight reduction, lesser inertia, lower track wear etc. The authors also suggested that sisal fibre is also a potential candidate for these applications.
DaimlerChrysler’s efforts towards sustainability paved the way for technology transfer initiatives which involve use of green materials in South America, Philippines and South Africa. The organisation emphasised upon the use of renewable energy sources over conventional fuels to promote global sustainability network wherein a bio-based automotive supply chain system would be developed which shall start from the farmer and shall end at automotive distributor (Elliott-Sink Citation2005). Presently, almost all the major automotive manufacturers are using NFPCs to make different components as listed in .
Table 3. Automotive parts produced from natural fibres (Pandey, Ahn, and Lee Citation2010; Singh, Verma, and Gupta Citation1998; Das Citation2009; Nakamura et al. Citation2009).
3. Natural fibres in building applications
The use of NFPCs is growing rapidly to meet today’s requirement of the world like low-cost building (Chandramohan and Bharanichandar Citation2013). Lumen/Voids present in the natural fibres helps these composites to have better acoustic and thermal insulation characteristics especially in construction industries (Holbery and Houston Citation2006; Taylor Citation2002). Structural beams and panels were fabricated and tested for NFPCs especially on bio-based polymers (Dweib et al. Citation2004, Citation2006). Saravana and Mohan (Citation2010) reported use of Straw in polymer composites as building material. Literature revealed that straw bales are good candidates for building construction material.
Swamy et al. (Citation2004) investigated use of areca fibre as reinforcement in polymeric composites and found as a good acoustic material for structural applications. Polymeric composites reinforced with jute fibre are used in structural applications like ceiling, window panels, floor and wall partition, mobile or pre-fabricated buildings and panels for partition etc. (Das Citation2009). Li and Matuana (Citation2003) used wood fibre-reinforced polymer composites in making window frames, moulded panel components. Maheswari et al. (Citation2013) suggested that borassus/High Density Poly Ethylene (HDPE) composites can be used as a good packaging material and in various secondary structural applications. Further some researchers have investigated jute/PP composites for structural and manufacturing feasibility for insulated panelised construction, used as skin in the panels (Uddin and Kalyankar Citation2011; Kalyankar and Uddin Citation2012). Moreover, some authors have manufactured cellular beams and plates with jute, hemp and flax fibre-reinforced unsaturated polyester as load bearing structural components, wherein it was revealed that NFPCs can be used as load bearing components with some improvement in their efficiency as structural components by arranging the cellular material (Burgueno et al. Citation2004; Burgueño et al. Citation2005; Burgueno et al. Citation2005a, Citation2005b). Ramnath et al. (Citation2014) found abaca and jute fibre-based composites suitable for housing and packaging industry. Ghavami (Citation2005) has reported the use of bamboo fibre to make structural concrete elements. Green composites have found various applications in building materials like door, bridge, fencing etc. (Golbabaie Citation2006). Some other natural fibres that are used as reinforcement are jute fibre (Chakraborty et al. Citation2013a; Zhou et al. Citation2013; Chakraborty et al. Citation2013b), coir fibre (Ali et al. Citation2012; Ali and Chouw Citation2013; Saravanan and Sivaraja Citation2012), flax fibre (Yan and Chouw Citation2013), corn stalk (Jarabo et al. Citation2013) and hemp fibre (Jarabo et al. Citation2012).
4. Natural fibres in decking/furniture applications
The wood like appearance and minimal maintenance of NFPCs make them a suitable replacement of wood in various applications like window systems and decking. Banana fibre is a potential replacement for wood-based products like plywood and medium density boards (Bavan and Kumar Citation2010). Rethinam and Sivaraman (Citation2001) investigated the acoustic properties of areca fibre and have reported better properties in comparison to wood-based plywood, thereby making it more suitable for various furniture applications. Arecanut-based products can be used in preparation of hardboards and paperboards etc. Das (Citation2009) reported the use of jute/polymer in making of products like tables, chairs, kitchen cabinets etc. Li and Matuana (2013) used wood fibre-reinforced polymer composites to form decks, docks. summarises the various applications of NFPCs.
5. Challenges in using natural fibres
Use of natural fibres in polymeric composites involves various issues related to moisture absorption, durability, weak interfacial adhesion of fibre and matrix and poor mechanical properties etc.(Gassan and Gutowski Citation2000; Hirai, Hamada, and Kim Citation1998; Irfan Ul Haq et al. Citation2018). NFPCs face the critical issue of degradation when exposed to external environment. There are different degradation modes pointed out in . These include biological, mechanical, water, weather and fire degradations. Different degradation reactions are also mentioned in . Biological degradation of NFPCs takes place due to attack by biological organisms. Organisms/Enzymes attack hemicelluloses first and hydrolyse them into digestible units (Rowell Citation1998). This weakens the fibre–matrix interface resulting in lowered strength of composites. Biodegradation also occurs due to oxidation and reduction reactions by enzymes. It can be avoided by using toxic chemicals (Golbabaie Citation2006).
Water degradation is the next challenge associated with these composites. As NFPCs are hydrophilic in nature, therefore, they absorb moisture in outdoor environment. It is governed by void content of natural fibres and content of non-crystalline parts. Rain, sea, dew and ice are the major sources for this absorption. The main constituent of fibre that absorbs moisture is hemicelluloses. The fibre swells due to this and also shrinks when it dries. Those NFPCs which are exposed to water frequently have wetter and drier areas within the composite leading to differential swelling and ultimately cracking (Rowell Citation1998).
Absorbed water bonds with fibre’s hydroxyl group weaken the bonding of fibre and matrix resulting in lesser mechanical strength (Azwa et al. Citation2013). The moisture absorption behaviour of natural fibres limits the outdoor applications of NFPCs. There are several methods like chemical treatment, coupling agents that are used to reduce moisture absorption and enhance mechanical properties (Ahmad, Choi, and Park Citation2015; Saheb and Jog Citation1999; Riccieri, Vázquez, and De Carvalho Citation1999; Luo and Netravali Citation1999). Percentage of moisture absorption is shown in . It can be seen that the lower the moisture content, the better will be the physical and mechanical characteristics of fibres and composites.
Table 4. Moisture absorption by different natural fibres (Bledzki and Gassan Citation1999; Khalil et al. Citation2012; Averous and Le Digabel Citation2006; Wambua, Ivens, and Verpoest Citation2003; Mark Citation1986; Preethi and Balakrishna Murthy Citation2013).
Degradation is also caused by ultraviolet (UV) radiations when these composites are exposed to outdoor environment. Lignin constituent of fibre is responsible for this weather degradation. Fresh layer of lignin is exposed to UV radiations after first layer degradation. This results in significant loss of fibres at the surface of composite. Mechanical degradation of NFPCs is caused by wind, dust, snow and hail etc. leading to stress, fracture, cracks and abrasion.
Another major challenge for the use of NFPCs in various structural applications is their poor fire resistance. Moreover, very less information is available for this behaviour of these composites. NFPCs undergo fire degradation due to pyrolysis reactions (oxidation, hydrolysis, oxidation). These reactions take place as the temperature increases. First, hemicelluloses degrade, then cellulose followed by lignin. The thermal degradation is a two-stage process one starting in the range of 220–280°C and the another starting in the range of 280–300°C. The lower temperature range is linked with the degradation of hemicellulose and the higher range is associated with lignin degradation. Thermal degradation effects colour, odour and also deteriorates mechanical properties of natural fibres (Saheb and Jog Citation1999).
As represented in , there are four degradation reactions which include oxidation, reduction, hydrolysis and dehydration which points to a similar degradation chemistry (Rowell Citation1998).
Fibre consistency/quality throughout the composite is also a big concern. Diameter of fibre is also not constant throughout its length and sometimes, it is not perfectly circular also. Natural fibres have low impact strength and high concentration of fibres cause defects in the composite. Poor matrix–fibre interface is a major challenge in NFPCs. Fibre degradation taking place during the composite processing leads to lower durability which can be improved by the chemical treatment up to a considerable amount.
6. Conclusion and outlook
The stringent environmental regulations and the quest towards sustainable materials have led researchers towards development of eco-friendly materials. NFPCs with outstanding properties have potential applications in the modern industry in general and the automotive industry and civil infrastructure sector in particular. The comparable mechanical properties of natural fibres with synthetic fibres, low production cost, good thermal and acoustic characteristics and eco-friendly processing make them a good alternative as reinforcement in polymeric composites. Owing to the excellent properties, NFPCs have good potential in load bearing applications. There seems a tremendous scope as many of the natural fibres and their polymer blends are unexplored. Additionally, the various indigenous species of a lot of natural fibres also needs to be explored. The hybrid polymer composites and the synergetic effect of various natural fibres are an area towards which future studies could be focused. The issues of thermal stability and the moisture absorption need to be addressed so as to widen the applications of NFPCs. This paper will serve as a catalyst and to initiate further advancements in the field of polymer composites
Disclosure statement
No potential conflict of interest was reported by the authors.
Additional information
Notes on contributors
Rajiv Kumar
Rajiv Kumar is specialized in Industrial and Production. He is currently working as as Assistant Professor at School of Mechanical Engineering, Shri Mata Vaishno Devi University, Katra. He is pursuing his doctoral program in the field of polymer composites.
Mir Irfan Ul Haq
Mir Irfan Ul Haq is specialized in Mechanical System Design. He has worked previously with Mahindra Research Valley, Chennai. He is currently pursuing his Ph.D. in the field of Materials and Tribology. He is currently working as Assistant Professor at School of Mechanical Engineering, Shri Mata Vaishno Devi University, Katra.
Ankush Raina
Ankush Raina is specialized in Mechanical System Design. He is pursuing his doctoral program in the field of lubricating oils used in Mechanical Industry. He is currently working as Assistant Professor at School of Mechanical Engineering, Shri Mata Vaishno Devi University, Katra.
Ankush Anand
Ankush Anand is specialized in the field of sustainability and design . He is currently working as Associate Professor in the School of Mechanical Engineering. He has published numerous articles in journals of high repute. He has guided numerous Masters and PhD candidates. Dr. Anand is also member of various international bodies.
References
- Abdellaoui, H., H. Bensalah, J. Echaabi, R. Bouhfid, and A. Qaiss. 2015. “Fabrication, Characterization and Modelling of Laminated Composites Based on Woven Jute Fibres Reinforced Epoxy Resin.” Materials & Design 68: 104–113. doi:10.1016/j.matdes.2014.11.059.
- Ahmad, F., H. S. Choi, and M. K. Park. 2015. “A Review: Natural Fiber Composites Selection in View of Mechanical, Light Weight, and Economic Properties.” Macromolecular Materials and Engineering 300 (1): 10–24. doi:10.1002/mame.201400089.
- Ali, M., and N. Chouw. 2013. “Experimental Investigations on Coconut-Fibre Rope Tensile Strength and Pullout from Coconut Fibre Reinforced Concrete.” Construction and Building Materials 41: 681–690. doi:10.1016/j.conbuildmat.2012.12.052.
- Ali, M., A. Liu, H. Sou, and N. Chouw. 2012. “Mechanical and Dynamic Properties of Coconut Fibre Reinforced Concrete.” Construction and Building Materials 30: 814–825. doi:10.1016/j.conbuildmat.2011.12.068.
- Alix, S., S. Marais, C. Morvan, and L. Lebrun. 2008. “Biocomposite Materials from Flax Plants: Preparation and Properties.” Composites Part A: Applied Science and Manufacturing 39 (12): 1793–1801. doi:10.1016/j.compositesa.2008.08.008.
- Al-Qureshi, H. A. 1999. “The Use of Banana Fibre Reinforced Composites for the Development of a Truck Body.” In Second International Wood and Natural Fibre Composites Symposium, 1–8. Kassel/Germany.
- Alves, C., A. J. Silva, L. G. Reis, M. Freitas, L. B. Rodrigues, and D. E. Alves. 2010. “Ecodesign of Automotive Components Making Use of Natural Jute Fiber Composites.” Journal of Cleaner Production 18 (4): 313–327. doi:10.1016/j.jclepro.2009.10.022.
- Anand, A., M. Irfan Ul Haq, K. Vohra, A. Raina, and M. F. Wani. 2017. “Role of Green Tribology in Sustainability of Mechanical Systems: A State of the Art Survey.” In Materials Today: Proceedings. Vol. 4(2): 3659-3665. doi:10.1016/j.matpr.2017.02.259.
- Ashori, A. 2008. “Wood–Plastic Composites as Promising Green-Composites for Automotive Industries!” Bioresource Technology 99 (11): 4661–4667. doi:10.1016/j.biortech.2007.09.043.
- Averous, L., and F. Le Digabel. 2006. “Properties of Biocomposites Based on Lignocellulosic Fillers.” Carbohydrate Polymers 66 (4): 480–493. doi:10.1016/j.carbpol.2006.04.004.
- Azwa, Z. N., B. F. Yousif, A. C. Manalo, and W. Karunasena. 2013. “A Review on the Degradability of Polymeric Composites Based on Natural Fibres.” Materials & Design 47: 424–442. doi:10.1016/j.matdes.2012.11.025.
- Bajpai, P. K., I. Singh, and J. Madaan. 2014. “Development and Characterization of PLA-Based Green Composites: A Review.” Journal of Thermoplastic Composite Materials 27 (1): 52–81. doi:10.1177/0892705712439571.
- Berger, K. G. 1983. “Production of Palm Oil from Fruit.” Journal of the American Oil Chemists’ Society 60 (2Part1): 206–210. doi:10.1007/BF02543483.
- Bledzki, A. K., and J. Gassan. 1999. “Composites Reinforced with Cellulose Based Fibres.” Progress in Polymer Science 24 (2): 221–274. doi:10.1016/S0079-6700(98)00018-5.
- Burgueno, R., M. J. Quagliata, G. M. Mehta, A. K. Mohanty, M. Misra, and L. T. Drzal. 2005a. “Sustainable Cellular Biocomposites from Natural Fibers and Unsaturated Polyester Resin for Housing Panel Applications.” Journal of Polymers and the Environment 13 (2): 139–149. doi:10.1007/s10924-005-2945-9.
- Burgueno, R., M. J. Quagliata, A. K. Mohanty, G. Mehta, L. T. Drzal, and M. Misra. 2004. “Load-Bearing Natural Fiber Composite Cellular Beams and Panels.” Composites Part A: Applied Science and Manufacturing 35 (6): 645–656. doi:10.1016/j.compositesa.2004.02.012.
- Burgueno, R., M. J. Quagliata, A. K. Mohanty, G. Mehta, L. T. Drzal, and M. Misra. 2005b. “Hybrid Biofiber-Based Composites for Structural Cellular Plates.” Composites Part A: Applied Science and Manufacturing 36 (5): 581–593. doi:10.1016/j.compositesa.2004.08.004.
- Burgueño, R., M. J. Quagliata, A. K. Mohanty, G. Mehta, L. T. Drzal, and M. Misra. 2005. “Hierarchical Cellular Designs for Load-Bearing Biocomposite Beams and Plates.” Materials Science and Engineering: A 390 (1–2): 178–187. doi:10.1016/j.msea.2004.08.034.
- Caprino, G., L. Carrino, M. Durante, A. Langella, and V. Lopresto. 2015. “Low Impact Behaviour of Hemp Fibre Reinforced Epoxy Composites.” Composite Structures 133: 892–901. doi:10.1016/j.compstruct.2015.08.029.
- Chakraborty, S., S. P. Kundu, A. Roy, B. Adhikari, and S. B. Majumder. 2013a. “Effect of Jute as Fiber Reinforcement Controlling the Hydration Characteristics of Cement Matrix.” Industrial & Engineering Chemistry Research 52 (3): 1252–1260. doi:10.1021/ie300607r.
- Chakraborty, S., S. P. Kundu, A. Roy, R. K. Basak, B. Adhikari, and S. B. Majumder. 2013b. “Improvement of the Mechanical Properties of Jute Fibre Reinforced Cement Mortar: A Statistical Approach.” Construction and Building Materials 38: 776–784. doi:10.1016/j.conbuildmat.2012.09.067.
- Chand, N., and M. Fahim. 2008. Tribology of Natural Fiber Polymer Composites. Cambridge, UK: Elsevier.
- Chandramohan, D., and J. Bharanichandar. 2013. “Natural Fiber Reinforced Polymer Composites for Automobile Accessories.” American Journal of Environmental Sciences 9 (6): 494. doi:10.3844/ajessp.2013.494.504.
- Chaudhary, V., P. K. Bajpai, and S. Maheshwari. 2018. “An Investigation on Wear and Dynamic Mechanical Behavior of Jute/Hemp/Flax Reinforced Composites and Its Hybrids for Tribological Applications.” Fibers and Polymers 19 (2): 403–415. doi:10.1007/s12221-018-7759-6.
- Das, S. 2009. “Jute Composite and Its Applications.” In Das S. Jute composite and its applications. Dhaka, Bangladesh: Proceedings of International Workshop IJSG, Feb 8–9.
- Davoodi, M. M., S. M. Sapuan, D. Ahmad, A. Ali, A. Khalina, and M. Jonoobi. 2010. “Mechanical Properties of Hybrid Kenaf/Glass Reinforced Epoxy Composite for Passenger Car Bumper Beam.” Materials & Design 31 (10): 4927–4932. doi:10.1016/j.matdes.2010.05.021.
- Dhakal, H. N., Z. Y. Zhang, and M. O. W. Richardson. 2007. “Effect of Water Absorption on the Mechanical Properties of Hemp Fibre Reinforced Unsaturated Polyester Composites.” Composites Science and Technology 67 (7–8): 1674–1683. doi:10.1016/j.compscitech.2006.06.019.
- Dweib, M. A., B. Hu, A. O. Donnell, H. W. Shenton, and R. P. Wool. 2004. “All Natural Composite Sandwich Beams for Structural Applications.” Composite Structures 63 (2): 147–157. doi:10.1016/S0263-8223(03)00143-0.
- Dweib, M. A., B. Hu, H. W. Shenton III, and R. P. Wool. 2006. “Bio-Based Composite Roof Structure: Manufacturing and Processing Issues.” Composite Structures 74 (4): 379–388. doi:10.1016/j.compstruct.2005.04.018.
- Eichhorn, S. J., C. A. Baillie, N. Zafeiropoulos, L. Y. Mwaikambo, M. P. Ansell, and A. Dufresne. 2002. “Review-Current International Research into Cellulosic Fibers and Composites.” Journal Mat Sciences 36: 19–26.
- Elliott-Sink, S. 2005. “Special Report: Cars Made of Plants.” From Edumds. Comhttp://www.Edmunds.com/advice/specialreports/articles/105341
- Fowler, P. A., J. Mark Hughes, and R. M. Elias. 2006. “Biocomposites: Technology, Environmental Credentials and Market Forces.” Journal of the Science of Food and Agriculture 86 (12): 1781–1789. doi:10.1002/jsfa.2558.
- Gao, S.-L., and E. Mäder, others. 2006. “Jute/Polypropylene Composites I. Effect of Matrix Modification.” Composites Science and Technology 66 (7–8): 952–963.doi:10.1016/j.compscitech.2005.08.009.
- Gassan, J., and V. S. Gutowski. 2000. “Effects of Corona Discharge and UV Treatment on the Properties of Jute-Fibre Epoxy Composites.” Composites Science and Technology 60 (15): 2857–2863. doi:10.1016/S0266-3538(00)00168-8.
- George, J., M. S. Sreekala, and S. Thomas. 2001. “A Review on Interface Modification and Characterization of Natural Fiber Reinforced Plastic Composites.” Polymer Engineering & Science 41 (9): 1471–1485. doi:10.1002/pen.10846.
- Ghavami, K. 2005. “Bamboo as Reinforcement in Structural Concrete Elements.” Cement and Concrete Composites 27 (6): 637–649. doi:10.1016/j.cemconcomp.2004.06.002.
- Giancaspro, J., C. Papakonstantinou, and P. Balaguru. 2009. “Mechanical Behavior of Fire-Resistant Biocomposite.” Composites Part B: Engineering 40 (3): 206–211. doi:10.1016/j.compositesb.2008.11.008.
- Golbabaie, M. 2006. Applications of Biocomposites in Building Industry. Department of Plant Agriculture, Ontario, Canada: University of Guelph.
- Han, J. S., and J. S. Rowell. 1997. “Chemical Composition of Fibers.” In Paper and Composites from Agro-Based Resources, 83–134. Florida:CRC Press
- Hirai, Y., H. Hamada, and J.-K. Kim. 1998. “Impact Response of Woven Glass-Fabric Composites: Effect of Fibre Surface Treatment.” Composites Science and Technology 58 (1): 91–104. doi:10.1016/S0266-3538(97)00111-5.
- Holbery, J., and D. Houston. 2006. “Natural-Fiber-Reinforced Polymer Composites in Automotive Applications.” JOM Journal of the Minerals, Metals and Materials Society 58 (11): 80–86. doi:10.1007/s11837-006-0234-2.
- Hossain, M. K., M. R. Karim, M. R. Chowdhury, M. A. Imam, M. Hosur, S. Jeelani, and R. Farag. 2014. “Comparative Mechanical and Thermal Study of Chemically Treated and Untreated Single Sugarcane Fiber Bundle.” Industrial Crops and Products 58: 78–90. doi:10.1016/j.indcrop.2014.04.002.
- Hull, D., and T. W. Clyne. 1996. An Introduction to Composite Materials. Cambridge, UK: Cambridge university press.
- Hutchinson, H. 2006. “Easy on the GAS.” Mechanical Engineering Magazine Select Articles 128 (7). American Society of Mechanical Engineers: 26–33.
- Hutten, I. M. 2007. Handbook of Nonwoven Filter Media. UK: Elsevier.
- Irfan Ul, H., M., . A. Raina, K. Vohra, R. Kumar, and A. Anand. 2018. “An Assessment of Tribological Characteristics of Different Materials under Sea Water Environment.” In Materials Today: Proceedings. Vol. 5(2): 3602-3609. doi:10.1016/j.matpr.2017.11.610.
- Jarabo, R., M. Monte, A. Blanco, C. Negro, and J. Tijero. 2012. “Characterisation of Agricultural Residues Used as a Source of Fibres for Fibre-Cement Production.” Industrial Crops and Products 36 (1): 14–21. doi:10.1016/j.indcrop.2011.07.029.
- Jarabo, R., M. C. Monte, E. Fuente, S. F. Santos, and C. Negro. 2013. “Corn Stalk from Agricultural Residue Used as Reinforcement Fiber in Fiber-Cement Production.” Industrial Crops and Products 43: 832–839. doi:10.1016/j.indcrop.2012.08.034.
- John, M. J., and R. D. Anandjiwala. 2008. “Recent Developments in Chemical Modification and Characterization of Natural Fiber-Reinforced Composites.” Polymer Composites 29 (2): 187–207. doi:10.1002/pc.20461.
- Kalia, S., and R. Sheoran. 2011. “Modification of Ramie Fibers Using Microwaveassisted Grafting and Cellulase Enzyme-Assisted Biopolishing: A Comparative Study of Morphology, Thermal Stability, and Crystallinity.” International Journal of Polymer Analysis and Characterization 16 (5): 307–318. doi:10.1080/1023666X.2011.587946.
- Kalyankar, R. R., and N. Uddin. 2012. “Structural Characterization of Natural Fiber Reinforced Polymeric (NFRP) Laminates for Building Construction.” Journal of Polymers and the Environment 20 (1): 224–229. doi:10.1007/s10924-011-0377-2.
- Karus, M., and M. Kaup. 2002. “Natural Fibres in the European Automotive Industry.” Journal of Industrial Hemp 7 (1): 119–131. doi:10.1300/J237v07n01_10.
- Khalil, H. P. S. A., I. U. H. Bhat, M. Jawaid, A. Zaidon, D. Hermawan, and Y. S. Hadi. 2012. “Bamboo Fibre Reinforced Biocomposites: A Review.” Materials & Design 42: 353–368. doi:10.1016/j.matdes.2012.06.015.
- Kim, K.-W., B.-H. Lee, S. Kim, H.-J. Kim, J.-H. Yun, S.-E. Yoo, and J. R. Sohn. 2011. “Reduction of VOC Emission from Natural Flours Filled Biodegradable Bio-Composites for Automobile Interior.” Journal of Hazardous Materials 187 (1–3): 37–43. doi:10.1016/j.jhazmat.2011.01.068.
- Li, Q., and L. M. Matuana. 2003. “Surface of Cellulosic Materials Modified with Functionalized Polyethylene Coupling Agents.” Journal of Applied Polymer Science 88 (2): 278–286. doi:10.1002/app.11681.
- Li, X. 2004. “Physical, Chemical, and Mechanical Properties of Bamboo and Its Utilization Potential for Fiberboard Manufacturing.”
- Li, X., L. G. Tabil, and S. Panigrahi. 2007. “Chemical Treatments of Natural Fiber for Use in Natural Fiber-Reinforced Composites: A Review.” Journal of Polymers and the Environment 15 (1): 25–33. doi:10.1007/s10924-006-0042-3.
- Luo, S., and A. N. Netravali. 1999. “Mechanical and Thermal Properties of Environment-Friendly Green Composites Made from Pineapple Leaf Fibers and Poly (Hydroxybutyrate-Co-Valerate) Resin.” Polymer Composites 20 (3): 367–378. doi:10.1002/pc.10363.
- Maheswari, C. U., K. Obi Reddy, E. Muzenda, M. Shukla, and A. Varada Rajulu. 2013. “A Comparative Study of Modified and Unmodified High-Density Polyethylene/Borassus Fiber Composites.” International Journal of Polymer Analysis and Characterization 18 (6): 439–450. doi:10.1080/1023666X.2013.814027.
- Mahjoub, R., J. M. Yatim, A. R. Mohd Sam, and S. H. Hashemi. 2014. “Tensile Properties of Kenaf Fiber Due to Various Conditions of Chemical Fiber Surface Modifications.” Construction and Building Materials 55: 103–113. doi:10.1016/j.conbuildmat.2014.01.036.
- Mallick, P. K. 2010. Materials, Design and Manufacturing for Lightweight Vehicles. Cambridge, UK: Woodhead Publishing Limited.
- Mark, H. F. 1986. “Fiber Chemistry, Handbook of Fiber Science and Technology: Volume I, Menachem Lewin and Eli M. Pearce, Eds., Marcel Dekker, New York, 1985.” Journal of Polymer Science Part C: Polymer Letters 24 (9): 486–487. doi:10.1002/pol.1986.140240912.
- Marrot, L., A. Lefeuvre, B. Pontoire, A. Bourmaud, and C. Baley. 2013. “Analysis of the Hemp Fiber Mechanical Properties and Their Scattering (Fedora 17).” Industrial Crops and Products 51: 317–327. doi:10.1016/j.indcrop.2013.09.026.
- Mohanty, A. K., M. Misra, and L. T. Drzal. 2001. “Surface Modifications of Natural Fibers and Performance of the Resulting Biocomposites: An Overview.” Composite Interfaces 8 (5): 313–343. doi:10.1163/156855401753255422.
- Mohanty, A. K., M. Misra, and G. Hinrichsen. 2000. “Biofibres, Biodegradable Polymers and Biocomposites: An Overview.” Macromolecular Materials and Engineering 276 (1): 1–24. doi:10.1002/(SICI)1439-2054(20000301)276:1<1::AID-MAME1>3.0.CO;2-W.
- Mohanty, S., S. K. Nayak, S. K. Verma, and S. S. Tripathy. 2004. “Effect of MAPP as a Coupling Agent on the Performance of Jute–PP Composites.” Journal of Reinforced Plastics and Composites 23 ((6).): 625–637. doi:10.1177/0731684404032868.
- Mwaikambo, L. 2006. “Review of the History, Properties and Application of Plant Fibres.” African Journal of Science and Technology 7 (2): 121.
- Nakamura, R., K. Goda, J. Noda, and J. Ohgi. 2009. “High Temperature Tensile Properties and Deep Drawing of Fully Green Composites.” eXPRESS Polymer Letters 3: 1. doi:10.3144/expresspolymlett.2009.4.
- Pandey, J. K., S. H. Ahn, and C. S. Lee. 2010. “Mohanty AK. Misra M.” Recent Advances in the Application of Natural Fiber Based Composites Macromol Mat and Eng 295: 975–989.
- Paturau, J. M. 1987. “ALTERNATIVE USES OP SUGARCANE AND ITS BYPRODUCTS IN AGROINDUSTRIES.”
- Pothan, L. A., S. Thomas, and G. Groeninckx. 2006. “The Role of Fibre/Matrix Interactions on the Dynamic Mechanical Properties of Chemically Modified Banana Fibre/Polyester Composites.” Composites Part A: Applied Science and Manufacturing 37 (9): 1260–1269. doi:10.1016/j.compositesa.2005.09.001.
- Preethi, P., and G. Balakrishna Murthy. 2013. “Physical and Chemical Properties of Banana Fibre Extracted from Commercial Banana Cultivars Grown in Tamilnadu State.” Agrotechnol S11 8 (2): 1-3.
- Ramachandra, T. V., G. Kamakshi, and B. V. Shruthi. 2004. “Bioresource Status in Karnataka.” Renewable and Sustainable Energy Reviews 8 (1): 1–47. doi:10.1016/j.rser.2003.09.001.
- Ramnath, B. V., V. M. Manickavasagam, C. Elanchezhian, C. Vinodh Krishna, S. Karthik, and K. Saravanan. 2014. “Determination of Mechanical Properties of Intra-Layer Abaca–Jute–Glass Fiber Reinforced Composite.” Materials & Design 60: 643–652. doi:10.1016/j.matdes.2014.03.061.
- Rethinam, P., and K. Sivaraman. 2001. “Arecanut (Areca Catechu L). Present Status and Future Strategies.” Indian Journal Arecanut, Spices Medica Plants 3 (2): 35–50.
- Riccieri, J. E., A. Vázquez, and L. H. De Carvalho. 1999. “Interfacial Properties and Initial Step of the Water Sorption in Unidirectional Unsaturated Polyester/Vegetable Fiber Composites.” Polymer Composites 20 (1): 29–37. doi:10.1002/pc.v20:1.
- Rowell, R. M. 1998. “Property Enhanced Natural Fiber Composite Materials Based on Chemical Modification.” In P.N.Prasad, et al. (Eds.), Science and Technology of Polymers and Advanced Materials, 717–732, Plenum Press: New York.
- Saheb, D. N., and J. P. Jog. 1999. “Natural Fiber Polymer Composites: A Review.” Advances in Polymer Technology: Journal of the Polymer Processing Institute 18 (4): 351–363. doi:10.1002/(SICI)1098-2329(199924)18:4<351::AID-ADV6>3.0.CO;2-X.
- Samal, S. K., S. Mohanty, and S. K. Nayak. 2009. “Polypropylene Bamboo/Glass Fiber Hybrid Composites: Fabrication and Analysis of Mechanical, Morphological, Thermal, and Dynamic Mechanical Behavior.” Journal of Reinforced Plastics and Composites 28 (22): 2729–2747. doi:10.1177/0731684408093451.
- Saravana Bavan, D., and G. C. Mohan Kumar. 2010. “Potential Use of Natural Fiber Composite Materials in India.” Journal of Reinforced Plastics and Composites 29 (24): 3600–3613. doi:10.1177/0731684410381151.
- Saravanan, R., and M. Sivaraja. 2012. “Durability Studies on Coir Reinforced Bio-Composite Concrete Panel.” European Journal Sciences Researcher 81 (2): 220–230.
- Sarkanen, K. V., and C. H. Ludwig. 1971. Lignins: Occurrence, Formation, Structure and Reactions, New York: Wiley-Interscience.
- Satyanarayana, K. G., G. G. C. Arizaga, and F. Wypych. 2009. “Biodegradable Composites Based on Lignocellulosic Fibers an Overview.” Progress in Polymer Science 34 (9): 982–1021. doi:10.1016/j.progpolymsci.2008.12.002.
- Saxena, M., R. K. Morchhale, P. Asokan, and B. K. Prasad. 2008. “Plant Fiber Industrial Waste Reinforced Polymer Composites as a Potential Wood Substitute Material.” Journal of Composite Materials 42 (4): 367–384. doi:10.1177/0021998307087014.
- Saxena, M., M. J. Nandan, and N. Ramakrishan. 2011. “Sisal: Potential for Employment Generation and Rural Development.” IOSR Journal of Mechanical and Civil Engineering 8 (6): 1–8.
- Schuh, T. G. 1999. “Renewable Materials for Automotive Applications.” Daimler-Chrysler AG, Stuttgart.
- Sen, T., and H. N. Jagannatha Reddy. 2011. “Various Industrial Applications of Hemp, Kinaf, Flax and Ramie Natural Fibres.” International Journal of Innovation, Management and Technology 2 (3): 192.
- Shalwan, A., and B. F. Yousif. 2013. “In State of Art: Mechanical and Tribological Behaviour of Polymeric Composites Based on Natural Fibres.” Materials & Design 48: 14–24. doi:10.1016/j.matdes.2012.07.014.
- Shinoj, S., R. Visvanathan, S. Panigrahi, and M. Kochubabu. 2011. “Oil Palm Fiber (OPF) and Its Composites: A Review.” Industrial Crops and Products 33 (1): 7–22. doi:10.1016/j.indcrop.2010.09.009.
- Silva, R. V., D. Spinelli, W. W. Bose Filho, S. Claro Neto, G. O. Chierice, and J. R. Tarpani. 2006. “Fracture Toughness of Natural Fibers/Castor Oil Polyurethane Composites.” Composites Science and Technology 66 (10): 1328–1335. doi:10.1016/j.compscitech.2005.10.012.
- Singh, B., A. Verma, and M. Gupta. 1998. “Studies on Adsorptive Interaction between Natural Fiber and Coupling Agents.” Journal of Applied Polymer Science 70 (9): 1847–1858. doi:10.1002/(ISSN)1097-4628.
- Singha, A. S., V. K. Thakur, I. K. Mehta, A. Shama, A. J. Khanna, R. K. Rana, and A. K. Rana. 2009. “Surface-Modified Hibiscus Sabdariffa Fibers: Physicochemical, Thermal, and Morphological Properties Evaluation.” International Journal of Polymer Analysis and Characterization 14 (8): 695–711. doi:10.1080/10236660903325518.
- Smith, P. M., and M. P. Wolcott. 2006. “Opportunities for Wood/Natural Fiber-Plastic Composites in Residential and Industrial Applications.” Forest Products Journal 56 (3): 4.
- Swamy, R. P., G. C. Mohan Kumar, Y. Vrushabhendrappa, and V. Joseph. 2004. “Study of Areca-Reinforced Phenol Formaldehyde Composites.” Journal of Reinforced Plastics and Composites 23 (13): 1373–1382. doi:10.1177/0731684404037049.
- Symington, M. C., W. M. Banks, O. D. West, and R. A. Pethrick. 2009. “Tensile Testing of Cellulose Based Natural Fibers for Structural Composite Applications.” Journal of Composite Materials 43 (9): 1083–1108. doi:10.1177/0021998308097740.
- Taylor, A. 2002. “Case Study on Fibers in Composite Materials, Eg Hemp in Automotive Applications.” In 4th Meeting of Government-Industry Forum on Non-Food Uses of Crops, GIFNFC, Vol. 4 London: DTI Conference Centre.
- Uddin, N., and R. R. Kalyankar. 2011. “Manufacturing and Structural Feasibility of Natural Fiber Reinforced Polymeric Structural Insulated Panels for Panelized Construction.” International Journal of Polymer Science, Vol. 2011.
- Udoeyo, F. F., and A. Adetifa. 2012. “Characteristics of Kenaf Fiber-Reinforced Mortar Composites.” International Journal Researcher Reviews Applications Sciences 12 (1): 339–353.
- Wambua, P., J. Ivens, and I. Verpoest. 2003. “Natural Fibres: Can They Replace Glass in Fibre Reinforced Plastics?” Composites Science and Technology 63 (9): 1259–1264. doi:10.1016/S0266-3538(03)00096-4.
- Yan, L., and N. Chouw. 2013. “Experimental Study of Flax FRP Tube Encased Coir Fibre Reinforced Concrete Composite Column.” Construction and Building Materials 40: 1118–1127. doi:10.1016/j.conbuildmat.2012.11.116.
- Young, R. A. 1986. “Structure, Swelling and Bonding of Cellulose Fibers.” In Cellulose: Structure, Modification and Hydrolysis, 91–128, New York: Wiley and Sons.
- Yusriah, L., S. M. Sapuan, E. S. Zainudin, and M. Mariatti. 2014. “Characterization of Physical, Mechanical, Thermal and Morphological Properties of Agro-Waste Betel Nut (Areca Catechu) Husk Fibre.” Journal of Cleaner Production 72: 174–180. doi:10.1016/j.jclepro.2014.02.025.
- Zafeiropoulos, N. E., D. R. Williams, C. A. Baillie, and F. L. Matthews. 2002. “Engineering and Characterisation of the Interface in Flax Fibre/Polypropylene Composite Materials. Part I. Development and Investigation of Surface Treatments.” Composites Part A: Applied Science and Manufacturing 33 (8): 1083–1093. doi:10.1016/S1359-835X(02)00082-9.
- Zhong, J. B., L. Jian, and C. Wei. 2007. “Mechanical Properties of Sisal Fibre Reinforced Urea Formaldehyde Resin Composites.” Express Polymer Letters 1 (10): 681–687. doi:10.3144/expresspolymlett.2007.93.
- Zhou, X., S. H. Ghaffar, W. Dong, O. Oladiran, and M. Fan. 2013. “Fracture and Impact Properties of Short Discrete Jute Fibre-Reinforced Cementitious Composites.” Materials & Design 49: 35–47. doi:10.1016/j.matdes.2013.01.029.