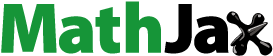
ABSTRACT
The beneficiation of agricultural waste is a topical issue in the field of sustainable and renewable energy production. This review focuses on recent methods applied to extract silica and silicon (Si), a major semiconductor material, from different agricultural waste ashes and their application in solar cell nanotechnology. Specific attention is given to such methods as relating to sugarcane bagasse ash, a waste product from the sugarcane processing industry. Also reviewed is the current carbothermal process through which pure silicon is obtained from an inorganic source, quartz. The review also highlights current challenges and opportunities associated with present technologies, and aims to create awareness and provoke the thoughts of researchers, scientists and stakeholders in the energy sector in this area.
Introduction
Globally, the daily energy demand is increasing with the increase in population. The estimated number of people who do not have access to electricity worldwide is 1.1 billion and about 84% of them live in the rural communities and 95% of them are in countries in Sub-Saharan Africa and developing Asia (International Energy Agency Citation2017). Meanwhile, the number of people in the rural areas who depend on traditional biomass fuel is projected to increase from the current 2.7 billion to 2.8 billion by 2030 (Kaygusuz Citation2012). However, there are different energy systems and sources from which energy could be produced for the use of mankind. Different sources of energy production and methods of extraction of the energy are presented in .
Table 1. Renewable energy resources and their application (Panda, Glaspell, and El-Shall Citation2006)
Solar photovoltaics have vast potentials as the clean, abundant and economical energy source. Armaroli and Balzani (Citation2007) reported a conversion efficiency range of between 17% and 25% for silicon-based solar cells. A later report by VonderHaar (Citation2017) places the conversion efficiency of silicon-based single-crystalline solar cells above 25% and that of multi-crystalline solar cells above 20%. He et al. (Citation2019) states that the theoretical power conversion efficiency can improve to above 29% for thin crystalline Si solar cells if surface passivation and light-harvesting can both approach their ideal limits. Silicon solar cells have higher photo-conversion efficiency due to the excellent quality of material utilised. Silicon solar cells have major advantages relevant for photovoltaic applications, such as low toxicity, abundant raw material, scalable solar cell fabrication processes (Yoshikawa et al. Citation2017). Peng et al. (Citation2010) reported that research is currently focused on new photovoltaic systems that incorporate optically active nanostructures such as nanoparticles, quantum dots, nanotubes, nanorods and nanowires, which offer substantial potential for new device structures. Silicon solar cell power performance improved by 60% in the ultraviolet range of the electromagnetic spectrum by integrating high film of silicon nanoparticles directly onto the solar cell (Nayfeh, Younis, and Abdel-Rahman Citation2007). Silicon nanoparticles are promising materials that can be incorporated into solar cells and possess competitive advantages such as flexibility in shape, easy to instal, the use of print-like manufacturing process to improve the conversion efficiency (Ludwig et al. Citation2004). According to (Klafehn Citation2016), the main interest in silicon nanoparticles (SiNPs) arises from the unique effect that quantum confinement has on silicon, for instance, the bandgap possessed by silicon is normally 1.12 eV, allowing it to collect light with energy above the bandgap efficiency. However, as the size of SiNPs decrease below 10 nm in diameter, its bandgap increases to 1.8 eV, allowing for the efficient collection of higher energy wavelength without significant loss in energy as heat.
Silicon (Si) is the second-most abundant element after oxygen in the earth’s crust (Matichenkov and Calvert Citation2002). The element is a valuable metalloid and is the primary component of high-speed optical fibres, semiconductors, photovoltaic cells, thin-film transistors, silicon carbide and silicon nitride, among many other applications (Gupta and Gupta Citation2016). Silicon is produced by carbothermic reduction of quartz sand at 1900°C as shown in EquationEquation (1)(1)
(1) (Bernardis Citation2012):
Metallurgical grade silicon (MG-Si) is produced and is approximately 99% pure and the energy input for this process is about 50 kWh/kg (Tao Citation2008). The current global production of MG-Si is approximately 600 000 tones/year, and the production process releases a million tons of greenhouse gases into the atmosphere (Tao 2008). About 5% of the 600 000 tons of (MG-Si) is further purified to produce electronic-grade silicon (EG-Si) for the semiconductor industry. The purity of EG-Si is above 99.99999%. For solar-grade silicon (SG-Si), the required impurity level is below ~0.001% (Tao 2008). A schematic representation of the production of silicon solar cells from quartz/sand as the source of silicon is summarised in .
The electric arc furnace requires approximately 1900 °C to melt sand which translates to 50 kWh of energy to melt a kilogram of sand. Since 600 00 tons of MG-Si is estimated to be produced annually, the approximated energy required could be 30TWh. It is obvious that the process described above is energy-intensive as well as environmentally unsustainable. Based on these findings it is worth to investigate other alternative sources for silicon for solar cell production. Thus, this review specifically concentrates on methods of extracting silica from the agro-waste ashes, methods of converting the extracted silica to silicon and the application of the produced silicon in solar cells. In addition, the review highlights current challenges in the field and proffers suggestions to overcome the challenges as a way of provoking the thoughts of researchers, scientists and stakeholders in the energy sectors.
Overview of agricultural waste and disposal techniques
Disposal of agro-waste
The system of disposal of agricultural waste is dependent on the chemical and physical properties of the agro-waste materials generated. It is pertinent to point out that waste disposal and pollution are inextricably related (Duhan et al. Citation2017). Under this context, the attention of the world focuses on how best the wastes generated can be disposed of such that they will not pose any threat to the environment. Currently, different environmental protection laws and regulations have been enacted to guide various systems of waste or agricultural waste disposals. Momentarily, some of the disposal systems are practised more than the others, and this may be attributed to certain factors including cost of disposal, environmental friendliness, properties of the waste, basic needs for the future utilisation of the waste and many other factors. However, presents the various systems that can be applied to agricultural waste disposal.
It can be observed that land-filling of agro-waste is considered a cheap technique of agro-waste disposal; however, there are environmental challenges associated with this. The most common challenge is groundwater pollution. Although combustion is categorised under incineration, the process takes a small area which is an advantage, but it requires expensive equipment however, results in serious air pollution (Drosg et al. Citation2015). Composting is another option of agro-waste disposal, it involves microbial action that enhances the soil nutrient and preferable to inorganic methods of disposing waste. Recycling is the current topical issue worldwide. Agro-waste recycling is an attractive strategy for waste disposal because useful materials can be recovered (Duhan et al. Citation2017).
Agro-waste availability
Agricultural waste is referred to as a waste generated because of various agricultural activities (Iacovidou et al. Citation2018; Yadav and Samadder Citation2018; Murillo and Cristina Citation2014; Drosg et al. Citation2015). However, there is a need to comprehensively characterise the wastes by investigating the physical and chemical properties of these residues before their utilisation (Adriano et al. Citation1980). The availability of agricultural residues determines their reuse or utilisation. The major drawback in the utilisation of these residues is limited information concerning fuel feeding, combustion and emission characteristics (Werther et al. Citation2000).
The chemical composition of selected main crop residues is shown in . Meanwhile, understanding the chemical constituents of crop residues or wastes will enhance their selectivity and utilisation for fuel or energy production. Most agricultural wastes are considered suitable and favourable for energy production depending on their availability and chemical compositions.
Table 2. Chemical composition of some selected agricultural waste
Several researchers have reported various compositions of agro-waste as depicted in . It is seen that rice straw has a high ash content of 12.7% and, is in affirmation with the high silica content in rice. However, Georgieva, Mikkelsen, and Ahring Citation2008 reported 2.4% ash content in sugarcane bagasse. The various bio-waste materials have different silica contents (Demirbas Citation2011). Similarly, some authors have equally worked on characterisation of the ash contents of agro-waste materials, and their findings are presented in .
Figure 3. Percentage of silica in selected biowaste ashes (Kazmi et al. Citation2016, Bhagiyalakshmi et al. Citation2010, Frías et al. Citation2007, Binod et al. Citation2010, Adesanya and Raheem Citation2009, Purnomo et al. Citation2012, Villar-Cociña et al. Citation2011, Lanning et al. Citation1958)
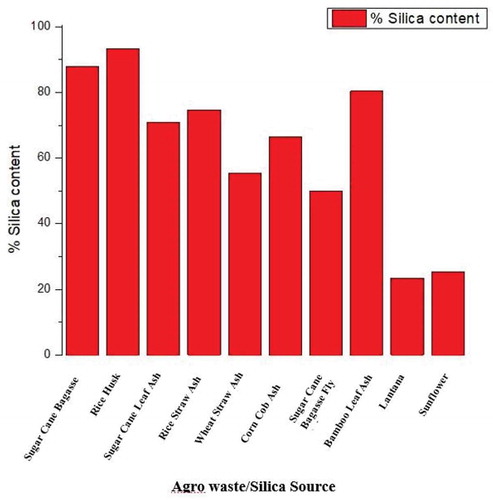
Agro-waste sources for nano-silica and silicon
In recent years, agricultural waste products have gained recognition as a potential raw material for preparing silicon composites. Agricultural waste is one of the cheapest sources of silica production (Zhang, Xu, and Champagne Citation2010). Natural silica has many benefits including; safe to handle and cost-effective (Norsuraya, Fazlena, and Norhasyimi Citation2016). Several potential methods and reasons for the use agro-wastes to generate silica have been offered by numerous authors (Adebisi et al. Citation2017; Falk et al. Citation2019; Mor et al. Citation2017; Patel, Shettigar, and Misra Citation2017; Zamani, Marjani, and Mousavi Citation2019). The reasons include (i) cheap cost of raw materials; (iii) high percentage silica content in the agricultural waste; (iii) comparable silica quality; (iv) the fine size of the amorphous material; (v) high energy content; and (vi) low energy consumption. It can be recalled from and that rice husks have the highest silica content from the physio-chemical analysis of the samples. Under this context, authors have carried out studies for the agro-waste materials, but the current paper focuses also on wheat straw, corn cob and sugarcane bagasse ashes, because they are the core global agro-waste that attracts the highest disposal challenge.
Rice husk ash
Rice Husk Ash is one of the most abundant natural resources rich in silica (SiO2). It is one of the agricultural by-products from rice milling industries. Rice husk ash consists of more than 90% amorphous silica (Li et al. Citation2011). To produce Nano-silicon crystalline particles from rice husk ash a magnesiothermic reduction method which involves the activation of the ash with an alkali, sodium hydroxide solution is applied. The process involves boiling the mixture for an hour to yield a sodium silicate solution (Na2SiO3). The Nano silica was then precipitated by sulphuric acid. Vacuum filtration was done in conjunction with hydrofluoric acid and distilled water washing to obtain solid Nano-silicon particles and remove other impurities as a waste filtrate. Washing of the Nano silicon for many times yielded the solid silicon, and it was followed by the drying of the solid Nano-silicon particles at 110°C (Venkateswaran, Yuvakkumar, and Rajendran Citation2013).
Liou and Yang (Citation2011) reported an alkali-leaching method for the extraction of Nano silica from rice husk ash. Rice husk samples were treated with hot hydrochloric acid to remove metallic impurities, the samples were washed with distilled water and dried. The dried samples were placed in a muffle furnace to eliminate the organic matter. The ash was then mixed with 1.5 M NaOH solution and boiled at 100°C with stirring for 1 h to produce sodium silicate solution. Nano silica was then produced by neutralising sodium silicate solution with hydrochloric acid, sulphuric acid, citric acid and oxalic acid to ascertain the best performing acid in the precipitation process. Carmona et al. Citation2013, extracted Nano silica from rice husk ash by acid leaching method and subsequently the ash was subjected to thermal treatment (Lee et al. Citation2017), carried out a series of experiments each with sulphuric acid, hydrochloric acid, oxalic acid and an ionic liquid. The workers investigated the possibility of enhancing the purity of silica from rice husk. After the chemical treatments, the residue was pyrolysed at 800°C in a muffle furnace for 48 h the resulting product was Nano silica. Mor et al. (Citation2017) produced Nano-silica particles by hydrothermal activation of rice husk ash (RHA) in 2 M NaOH. Product was a supernatant solution which was sodium silicate.
Corn cob ash
Another agricultural waste for the production of Nano silica is corn cob ash. Globally, a large amount of corn cob ash is generated after eating the corn annually. Many of the rural communities consume the corn and burn the cobs into ashes usually found in heaps or mounds. Several articles have been published on the utilisation of corn cob ash for Nano-silica production. Okoronkwo, Imoisili, and Olusunle (Citation2013) and Venkateswaran, Yuvakkumar, and Rajendran (Citation2013) used corn cob ash to produce Nano silica. The reaction was carried out using 1 M NaOH solution as an activating agent, after thermal treatment of corn cob at 650°C treatment for 3 h. The ash was cooled and treated with 1 M sodium hydroxide to produce sodium silicate solution this was titrated with 3 M HCl with stirring until pH of 7. The precipitate was washed and dried. Shim, Velmurugan, and Oh (Citation2015) reported the extraction of Nano silica from corn cob ash at variable pH conditions via sol-gel method. Okoronkwo, Imoisili, and Olusunle (Citation2013) reported again synthesis of Nano silica by sol-gel method and nanostructured with templating concept. The Hexadecyltrimethyly ammonium bromide (CTAB) was dissolved in distilled water and stirred for 5 min to obtain a homogeneous transparent solution. With continuous stirring ammonium hydroxide was added with continuous stirring, the extracted silica was then added slowly with stirring and was left to age for 20 h. Nano silica was then washed and dried. The Nano silica was then calcined in a muffle furnace at 550°C.
Wheat straw ash
Wheat straw is another abundant agro-waste which has been explored by several authors because of its high silica content. Globally, over 500 million tons of wheat straw is produced. Most of this wheat straw is burnt in the field causing significant environmental and health hazards and traffic accidents (YaNing, Ghaly, and BingXi Citation2012). About 2.45 billion people approximately 35% of the world rely on wheat as their staple food. Chen et al. (Citation2010), extracted Nano silica from wheat straw by two methods, namely, combustion and acid leaching. With combustion washed clean wheat straw was combusted in a muffle furnace at 500°C for 8 h. The ash obtained was cooled and it was silica. Acid treatment involved mixing of 10 g wheat straw at 60°C to 70°C for 24 h in 100 ml 4:1 concentrated HNO3 and H2SO4 aqueous solution followed by centrifugation and washing for several times. The powder obtained was dried. summarises other various methods for the synthesis of Nano silica and Nano silicon from selected agro-waste sources.
Table 3. Synthesis of nanoparticles from selected agro-waste sources using various processing routes
Table 4. Physicochemical composition of sugarcane bagasse ash from different countries sugarcane bagasse ash analysis: countries and authors
Sugarcane bagasse ash
Another interesting agro-waste material in this study is sugarcane bagasse a waste product from sugar milling and ethanol industries. It has been reported that agricultural activities reduce silicon from the soil due to its utilisation by plants (Savant et al. Citation1999). For instance, sugarcane is known to absorb more silicon than any other mineral nutrient from the soil in the form of silicic acid (H4SiO4), accumulating approximately 380 kg/ha of Silicon (Si), in a 12-month-old crop plantation period (Savant et al. Citation1999). Sugarcane Bagasse Ash (SCBA) is a waste from sugar and bioethanol industries, potentially used as the cheap source of natural silica. Researchers worldwide have dedicated effort to investigate potential applications of silica from bio-waste including sugarcane bagasse ash (Ferreira-Leitão et al. Citation2010). However, the silica content in sugarcane bagasse ash is highly dependent on the geographical location and the environment where the sugarcane is grown as well as the farming practices. From a study that was conducted by (Du Preez Citation1970) in South Africa, on the treatment of soil with silicate-containing fertilisers, there was an increase in cane yield with an increase in the silica concentration in the plant. Sugarcane in Hawaii is normally a two-year crop while in most countries it is a one-year crop (Fox et al. Citation1969).
Sugarcane bagasse ash has good pozzolanic properties and could be used in place of cement but to around 10% to retain the desired strength and increase the characteristics of the concrete (Maheswari, Ahamed, and Duraisamy Citation2017). Several authors have demonstrated a successful use of sugarcane bagasse ash as a partial substrate in the concrete formulation (Srinivasan and Sathiya Citation2010; Abdulkadir, Oyejobi, and Lawal Citation2014). The chemical composition of sugarcane bagasse ash and specifically the level of silica in the ash plays a major role in concrete formulations. This is because it determines the quality of the concrete.
The chemical compositions of a typical sugarcane bagasse ash with reference to geographical locations are shown in Table 54, while the diffeent methods of producing silicon nanoparticles via different precursors is depicted in . From Table 54, it can be observed that the silica content and other compositions of the ash vary in accordance with the geographical locations.
Table 5. Methods of producing silicon nanoparticles starting with different precursors
Researchers have indicated the use of sugarcane bagasse ash (SCBA) in different applications, and equally specifically investigated the influence of SCBA on the surface characteristics of silica for silicon production. Sol-gel and bio-digestion methods could be used to produce the Nano silica. Similarly, Vaibhav, Vijayalakshmi, and Roopan Citation2015 demonstrated in their work a successful production of silicon nanoparticles using precipitation technique and silica extracted from sugarcane bagasse, groundnut shell, rice husk and bamboo leaves.
Demerit of bio-sourced ash from biomass-firing heaters
Despite the potential applications of ash sourced from combustion of agro-waste, there are significant process challenges that result from the firing of biomass prior to the extraction of silicon. Several researchers have reported on the negative impacts of bio-sourced ashes from fuel-feeding on process equipment and complications related to their deposition into the environment. In a study by Yao et al. (Citation2020) on co-firing anthracitic coal with woody biomass (pine sawdust), it was observed that mitigating slagging and fouling tendencies of ash which related to the ash fusion temperature (AFT) requires careful temperature control. Yao et al. (Citation2019) found that there were less acidic oxides and amphoteric oxides
in soybean straw compared to coal while basic oxides were much higher. The higher basic oxides resulted in lower AFT, thus requiring that the process operates at lower temperatures. An advantage of the co-firing strategy is the reduction in ash volume per unit volume of fuel-feed due to the presence of less inorganic materials in the biomass component.
The challenge with utilising biomass fuels lies in the abundance of alkali/alkaline earth metals (K, Na and Ca) and chlorine (Cl) and low sulphur content compared thermal coal which has been proven to adversely impact combustion and significantly alter the properties of the ash product (Shao et al. Citation2012). Due to the high activity of the alkali/alkaline earth metals present, particularly the readily volatilised forms of K in biomass, vapour phase compounds and ions of chlorine are formed. Because of low melting temperatures (<800°C) of the vapour phase compounds and ions of chloride, deposits form adhesive layers on heat transfer surfaces. This problem is more complex in agro-waste with an abundance of silica combined with alkali/alkaline earth metals (rice husk, sugarcane bagasse, etc.) which readily cause slag and fouling within the temperature range 800–900°C, the normal temperature ranges for biomass-firing boilers. Therefore, co-deposition of alkali silicates and alkali chlorides resulting in corrosion/fouling is difficult to avoid at a low AFT (typically <700°C) (Shao et al. Citation2012).
Despite the low-S content of biomass fuels or co-firing fuels which significantly reduces the emission of gases, ash deposition is negatively affected particularly due to the high Cl content of biomass. The work of Nielsen et al. (Citation2000a) and Yao et al. (Citation2019) concurred that intense volatilisation of sylvinite, KCl, a typical fluxing agent, which happens between 750°C and 900°C is responsible for ash fusion and agglomeration. Sulphur is known to reduce corrosion and such challenges related to chloride deposits through the following sulphation mechanism (Nielsen et al. Citation2000b):
Therefore, due to low-S, combustion of biomass of co-fired fuels can lead to increased Cl-related deposition and corrosion problems. In spite of the focus on the process challenges concomitant with biomass-firing, challenges are the environmental penalties of chlorine-bearing ash deposits to the company. is the schematic representation of the ash formation deposition mechanisms on a superheater tube surface.
Figure 4. Schematic of mechanisms of ash formation and deposition on a superheater tube adapted from (Shao et al. Citation2012)
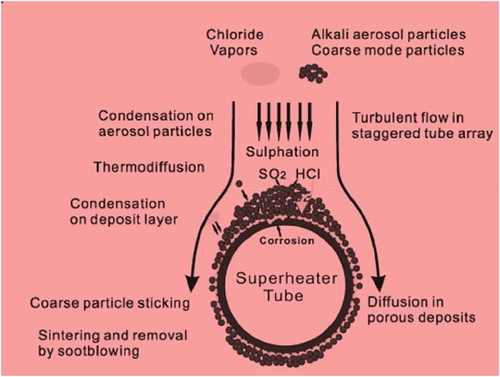
Since the global community moves towards emission-free society, thus it becomes more pertinent that more-sustainable approaches to the harvesting of silica from agro-waste be investigated. However, the use of bio-sourced ash finds its significance not as a long-term method for extraction of silica but a mitigating method to reduce the environmental impact of ash deposits from biomass-firing activities.
Production of silicon nanoparticles
Nanoparticles are fundamental building blocks of nanotechnology (Nagarajan Citation2008). Their synthesis often follows a bottom-up or top-down approach (Kulkarni et al. Citation2010; Overney and Jeanneret Citation2010; Yadav and Samadder Citation2018) and it is dependent on whether the materials are made from elemental basis via chemical processes or reduced from the bulk state via mechanical milling or chemical attrition processes. Nanotechnology has improved the manufacturing of various products with higher efficiency because of improved material properties. Bottom-up synthesis of nanoparticles is achieved through pyrolysis, hydro (solvo) thermal reaction, inert gas condensation, sol-gel fabrication and structured media methods whereas; top-down methods are largely achieved by milling and attrition (Overney and Jeanneret Citation2010). There are various methods for the preparation of nano silicon such as laser-assisted electrochemical etching, pulsed laser deposition, electron beam evaporation, combustion synthesis and plasma-enhanced chemical vapour deposition (Eisenhawer et al. Citation2011). These synthesis methods are not cost effective. The chemical synthesis method has the advantage of size and shape control, as well as purity improvement. Nano-silicon produced from silica can be used for several applications such as biological, industrial, electronics. In electronics applications, it is used for fabrication of transistors, solar cells, semiconductor detectors. Solar modules made from high-quality thin films crystalline silicon layers on glass substrates have the potential of making photovoltaic electricity substantially cheap (Venkateswaran, Yuvakkumar, and Rajendran Citation2013). Solar energy exploitation has spurred research and scientific attention in renewable alternative energy primarily to address energy shortages, and on the grounds of these energy shortages, silicon Nanoparticles for solar cell applications have become a promising option, globally (Huan and Shu-Qing Citation2014).
Production of silicon nanoparticles based on synthetic and analytical size-selected techniques offers a comprehensive understanding of the properties, morphologies and dimensions of silicon nanoparticles (SiNPs). There are quite a few routes for the synthesis of SiNPs such as pulsed laser ablation, heating degradation and ball milling, chemical and electrochemical etching syntheses. The guiding strategies will include the understanding of the surface chemistry, size distribution and dimensions of particles, and its scalability. The basic and model strategies for the synthesis are explained below;
Pulsed laser ablation (PLA)
Pulsed laser ablation (PLA) which uses PLA vaporisation of the greater amount of the metal in a pulsed supersonic nozzle to render ultra-cold metal cluster of copper (Cu2) (Powers et al. Citation1982) and high-melting molybdenum (MO2) (Hopkins et al. Citation1983). This method is most advanced for semiconductors such as SiNPs. Production is facilitated by the application of Argon fluoride (ArF) excimer laser ablation at constant helium (He) gas atmosphere as demonstrated by (Yoshida et al. Citation1996). The authors correlated a relationship indicating that the increase in helium (He) pressure from the kinetic energy of the material which collided with that of the surrounding gas particles has a link with the cohesive energy as shown in EquationEquation (2)(2)
(2) :
Where p the diameter of the ultrafine crystallite,
is the ambient pressure and
is the density of the surrounding gas.
Heating degradation
Thermal decomposition has extensively been used to produce SiNPs using silane as starting materials. For example, Ho, Coltrin, and Breiland Citation1994 have shown the possibility of producing the elemental Silicon (Si) atom by chemical decomposition via two chemical equations coupled to a rotating chemical vapour deposition (CVD). Further work by (Swihart and Girshick Citation1999) resulted in a plausible yield of more 20 Silicon atoms and rendering a kinetic mechanism for the formation of silicon hydride. These earlier works have garnered more inspiration for more researchers including (English et al. Citation2002) proposing production of sterically stabilised silicon nanostructures thereby enthroning the freedom of environmental contamination using heating and pressurised solvents in an elevated temperature greater than their critical points (400–500°C) for decomposition of Organosilane feedstock. However, Shafeev, Freysz, and Bozon-Verduraz Citation2004 have demonstrated that microwave-assisted thermal decomposition can affect Organosilane precursors at certain microwave powers. In another effort, Knipping et al. Citation2004 achieved Si single crystals ranging from 6 to 11 nm through microwave-induced decomposition of silane. This result has shown that the particle size was proportional to the precursor concentration whereas, the gas pressure proved an inverse relationship with the microwave power. The use of thermal degradation in Si nanostructures is currently applied in SiNPs featuring blue emission, great PL yield, high pH stability and favourable size with the use of a facile one-pot aqueous production technique (He et al. Citation2009; Panda, Glaspell, and El-Shall Citation2006). This process shows that the use of microwave supported the nucleation or Oswald ripening (He et al. Citation2009). There are a few advantages which microwave has over the thermal decomposition, among them are uniform heating of solvents, greater selective heating of reactants, and short residence time of reaction due to efficient absorption of microwaves thereby increasing reaction rate (Atkins et al. Citation2011).
Ball milling
Nano-crystalline materials can be successfully produced from ball-milling experiments and this method is popular because of its simplicity, relatively inexpensive equipment and can take on a wide range of other materials. (Lam et al. Citation2000) used ball milling to synthesise large-scale ultrafine SiNPs with dimension 5 nm using solid graphite (C) in conjunction with silicon dioxide (SiO2) in a planetary ball miller for 7–10 days. 1:1 graphite-SiO2 molar ratio was applied and the mixture was loaded into a stainless-steel vial together with stainless-steel balls (7.5 mm in diameter). The content was sealed with a Viton O-ring. However, before sealing, argon was passed through the vial to repel other gases while the remaining argon was set at atmospheric pressure. After 7–10 days, respectively, the milled powders were annealed in a hydraulic press for 48 h at 150°C under a loading of 30 kgf/mm2. After this, the annealed powders were put back into the vial and milled for another 2 h to break up the pressed tablet into powder form.
The resulting NPs were covered with an amorphous SiO2 layer 1nm in thickness and this produced a multi-peak PL spectrum due to the wide range of particle sizes. Apart from the size distribution, another issue arises from the aggregation which presented a complex and coarse shape. This tends to limit the ball milling synthetic strategy despite its convenience and inexpensiveness.
Physicochemical methods
In this category of silicon nanoparticle production technique, photothermic aerosol synthesis is popular. This utilises a laser-induced decomposition of gas-phase materials and is carried out in three stages. At the onset, the silicon powders are synthesised by CO2 laser-induced heating of silane followed by H2 and a photosensitiser (e.g. sulphur hexafluoride) to a degree that can be effectively dissociated. The product of this synthesis is in the range of SiNPs from 5 nm to 10 nm or even larger than 10 nm (Ehbrecht and Huisken Citation1999) which cannot manifest serious size confinement effect, implying that they have much lower PL efficiency. This, therefore, calls for a post-treatment for size selection and to reduce particle dimension as required. However, it was of importance to select the neutral clusters using cluster size, slotted molecular beam chopper wheel based on the correlation suggested by (Ehbrecht and Huisken Citation1999). Etching of the obtained SiNPs by chemical etching with HF/HNO3 would induce bright visible luminescence (Li et al. Citation2003; Erogbogbo et al. Citation2010).
A physical route to SiNPs production usually encounters low product yield, but in this case, gram scale yield of Si QDs is obtained (Zhang et al. Citation2007a) resulting in non-aggregation, well-controlled nanoparticle size, and incidentally deposited on the desired substrate or liquid medium. Huisken et al. (Citation2002) demonstrated a successful particle injection through a nozzle into a high vacuum device and then deposited a molecular beam of Si clusters on a suitable substrate.
Chemical techniques
Production of SiNPs takes on the solution phase synthesis which received plausible efforts (JR Heath Citation1992). The starting materials were silicon halides. These were systematically reduced by sodium naphthalenide (Baldwin et al. Citation2002; Heath Citation1992; Zou et al. Citation2006), lithium naphthalenide (Kornowski et al. Citation1993), lithium aluminium hydride (Hapala et al. Citation2013; Sudeep, Page, and Emrick Citation2008) or zinc salts (Bley and Kauzlarich Citation1996) These reactions were carried out in a variety of surfactant solvent environments resulting in small-sized, free-standing SiNPs which were hydrogen capped (Hapala et al. Citation2013; Wilcoxon, Samara, and Provencio Citation1999). Recently, Chang and Sun Citation2014 used allyltrichlorosilane as both the surfactant and the functionalization reagent and silicon tetrachloride in a ratio of 1:3, to explore a simple approach to the synthesis of morphology-controlled hexagonal silicon nanocrystals modified with allyl in the range of 20–50 nm.
The Si-Cl bonds were reduced by lithium tetra hydridoaluminate to Si-Si which promotes the growth of Si crystals (Chang and Sun Citation2014). To control the size dispersion, Tilley et al. Citation2005 found that the narrow size distribution could be obtained by using powerful hydride reducing agents and selective surfactants in micelles, which termed, ‘micro-emulsion synthesis’. In this process, the surfactant plays a critical role in restricting the core growth and finally resulted in uniform particle dimensions.
Chang and Sun (Citation2014) have successfully demonstrated a one-step technique to produce highly monodispersed, alkyl-capped, brightly luminescent nanocrystals using hexyltrichlorosilane as both surfactant and the reactant. When the hexyltrichlorosilane was not used, the product of reaction showed smaller Si QDs with diameters 2 ± 0.5 nm implying a narrow size distribution and excitation wavelength-dependent PL performance. The PL was shown to peak-range from 350 to 450 nm as the excitation state wavelength red-shifted (Wang et al. Citation2011). Several authors including (McMillan et al. Citation2005; Zhang et al. Citation2007b) have utilised different precursors to synthesise silicon nanoparticles. For example, zinc salt was used with ammonium bromide, nanoparticles with bright blue emission in the size range of 3.9 ± 1.3 nm could be obtained with resultant by-products such as ammonia, hydrogen and sodium bromide.
Electrochemical techniques
This method appears to be one of the versatile approaches to SiNPs synthesis when looking at it from the fundamental perspectives, for example, the synthesis of porous silicon (PSi) otherwise known as silicon nanocrystal thin film that transcended photoluminescent SiNPs was developed from galvanostatic anodisation. Traditionally, its preparation involved the filling of a Teflon cell with a blend of aqueous HF and ethanol followed by etching a silicon wafer under steady current supply. A fracturing treatment is carried out on the fleshly etched PSi layer for sonication in order to achieve quantum-confined colloidal silicon nanoparticles (SiNPs) (Ahire et al. Citation2012). It should be noted that electrolyte composition, etching time, silicon dopant type and dopant concentration (Bley and Kauzlarich Citation1996) exert irreversible effect on the surface morphology and properties of the PSi thin-film whereas the ethanol has an advantage of preventing bubble break up and annulment of the hydrophobicity leading to effective pore formation (Sailor and Wu Citation2009) and consequently, more uniform hydrogen-terminated silicon nanocrystals result.
Surface modification
This method of synthesis of SiNPs is achievable through understanding the surface chemistry of the nanoparticles, for example, from the fact that chemical reactions take place at the surface much higher than they do at the bulk mass, pristine Si nanocrystals with hydrogen termination show meta-stability due to its surface hydrophobicity to oxygen and water. This shows that surface modification of Si nanocrystals which have functional molecules would significantly improve their stability as well as their optical performance (Sato and Swihart Citation2006; Zhu et al. Citation2005) and solubility in some solvents.
Some authors (Bent Citation2002; Duke Citation1996; Neergaard Waltenburg and Yates Citation1995) have suggested the existence of dangling bonds on the surface of SiNPs which enhance chemical reactivity at the surfaces with other organic molecules. There are one instead of two spin-paired electrons responsible for the tendency of minimising the free energy that removes the dangling bonds. The resulting energy minimisation was a trade-off between that gained in forming new local bonds and the energy lost during bond strain from its new configuration. The result is a complex reconstruction of the surface that leads into termination with certain molecules. Presently, different types of water-soluble SiNPs with bioconjugation are available in the areas of in vivo and in vitro applications. In Si-H bonding, it can easily be oxidised while Si-Si linkage produces a weaker bond. However, in order to avoid surface oxidation (Ruizendaal et al. Citation2011), an inert atmosphere had been incorporated.
The seemingly chemically stable Si-C bond emerges as a suitable medium for further chemical compound passivation such as acrylic acid, octylamine (Zhang et al. Citation2007a), 4-bromo-1-butene (Ruizendaal et al. Citation2011), epoxide, 1-heptene (Tilley et al. Citation2005). This is so because the Si-C has low polarity and high bond strength through hydrosilylation, and if a further modification was necessary, the small organic molecules with a C = C end group would produce hydrophobic and hydrophilic SiNPs (Ahire et al. Citation2012; Tilley and Yamamoto Citation2006).
Polarisation effect (Hu et al. Citation2009) had been investigated on the scale of in-situ oxidation under high temperature yielding SiO2 that aided particle to become water-soluble for easy surface functionalization. The commonly used approaches these days to achieve hydrosilylation of silicon nanocrystals are metallic catalysis, UV irradiation, heating treatment and microwave-assisted functionalization.
Drawbacks and benefits of different methods
Physical methods of SiNPs generally have the capacity to achieve size controllability of the synthesised SiNPs. Their major disadvantage is that production is not scalable, and the Si QDs must be stabilised. Under mild conditions (Hapala et al. Citation2013; Zou et al. Citation2006), chemical synthesis techniques of Si-NPs have been shown to achieve surface modification and controllable particle size distribution of Si QDs, but the question of contamination of the residual side products which are reducing agents are compromised. High yield (Ahire et al. 2012b) and uniformity in essential properties (Wilson, Szajowski, and Brus Citation1993) have attracted much research attention focusing on the porous silicon as a source of Si QDs using electrochemical technique under certain conditions. There is a further need for this method to separate the final products as there is an apparent lack of particle size control, shape and size distribution. Many methods had been applied by several researchers to study the production of nanoparticles using different feedstocks. presents some of the methods used by different authors in the production of silicon nanoparticles.
Table 6. XRF analysis of nano silicon at different temperatures (Venkateswaram et al. 2012)
Basically, the silicon nanoparticles have high physical characteristics, active surface state, outstanding photoluminescence and biocompatibility thus, making the material to be very attractive (Chang and Sun Citation2014) in solar cell fabrication.
Methods of characterisation of silicon nanoparticles
In the production of silicon nanoparticles, different characterisation techniques are applied to allow for a proper understanding of the nature of the Nano-material produced. If the properties of the materials are identified, it will be possible to project the material for a suitable application. (Cho et al. Citation2013) studied the synthesis of luminescent silicon nanoparticles from the reaction of magnesium silicide and ethylene diammonium chloride in a low-temperature condition. Two important parameters; the amount of reducing agent and reaction time on the synthesis process were investigated.
The nanoparticles were optically characterised using UV-Vis absorption spectrophotometer, Fourier Transform Infrared (FT-IR), Photoluminescence Spectroscopy. Similarly,Odo et al. Citation2012 investigated the production of silicon nanoparticles from single-crystalline silicon wafers and polycrystalline bulk using a vibrating disc mill in a top-down synthesis route. The authors applied Microscopy including Scanning Electron Microscopy (SEM) and Transmission Electron Microscopy (TEM), and the Energy Dispersive X-ray Spectroscopy (EDX) to study the elemental composition and morphology of the silicon-particles produced, whereas, the structural characteristics of the particles were studied using XRD (X-ray-diffraction, Raman and Electron Diffraction technology. On the other hand, the silicon nanoparticles synthesised from a thin section of porous silicon in an organic solvent was characterised by (Bley and Kauzlarich Citation1996) using High-Resolution Transition Electron Microscopy (HRTEM) and Fourier Transform Infrared. HRTEM and FTIR were used to determine the mono-dispersion and the composition of the amorphous surface layer of the nanoparticles, respectively. The authors stated that the average particle diameter, size distribution and the charge of the nanoparticles influences both the in-vivo distribution and physical balance of the nano-material. Many authors including Bhatia Citation2016; Pal et al. Citation2011; Patra and Baek Citation2015; Polakovič et al. Citation1999 have reported about nano-particles characterisation. A schematic representation of the methods of characterising silicon nanoparticles is shown in .
Characterisation of Si-NPs: case study 1
In this study, the work of Venkateswaram et al. (Citation2013) is used as a case study to describe the characterisation of silicon nanoparticles (SiNPs) produced using magnesiothermic reduction method (MRM) for solar cell fabrication. The MRM according to the authors is a cost-effective method used for SiNPs production. The work was chosen because it was a comprehensive characterisation, and the characterisation techniques employed include XRD, Particle Size Analyser (PSA), FT-IR, TEM, UV-Vis and. displayed the XRD, PSA, FT-IR, TEM, UV-Vis results of the characterisation, respectively, while the XRF result is presented in .
Figure 6. XRD Patterns of nano silicon at different sintering temperatures (Venkateswaram et al. 2012)
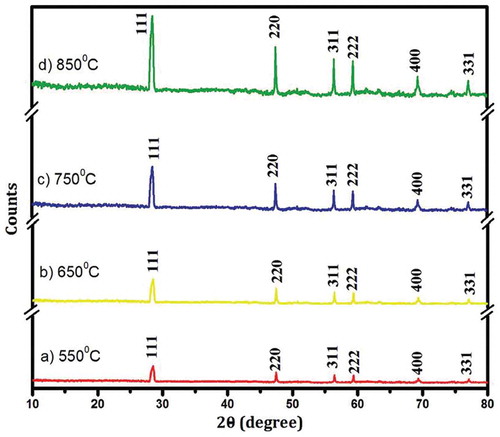
Figure 7. Particle size distribution of nano silicon at different sintering temperatures (Venkateswaram et al. 2012)
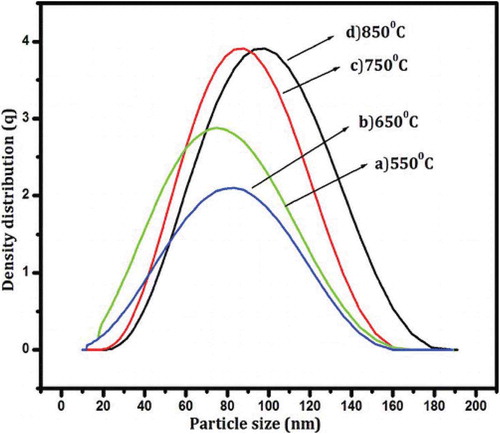
Figure 8. FTIR spectrum of nano silicon at different sintering temperatures (Adapted from Venkateswaram et al. 2012)
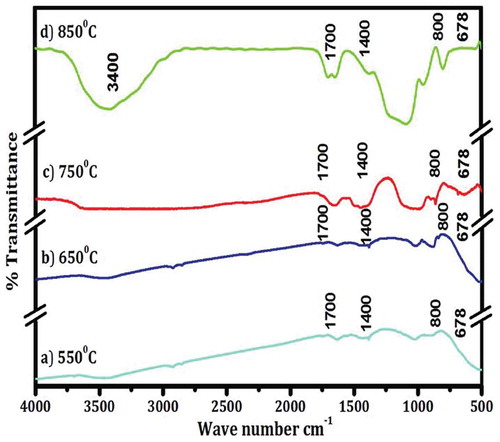
Figure 9. TEM images of nano silicon at different sintering temperatures (Adapted from Venkateswaram et al. 2012)
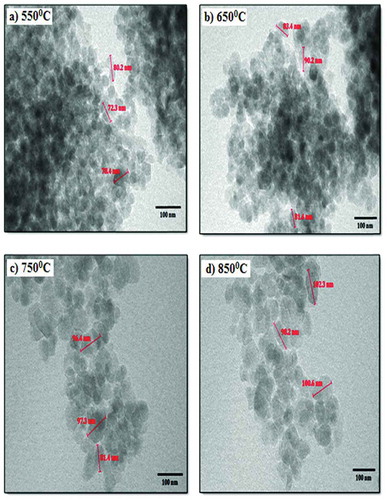
Figure 10. UV–Vis absorption spectra of nano silicon at different sintering temperatures (Adapted from Venkateswaram et al. 2012)
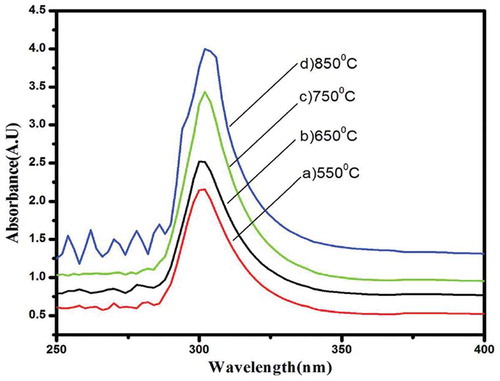
From , sharp well-oriented crystalline peaks (111, 220, 311, 222, 400 and 331) were obtained for 550°C, 650°C, 750°C and 850°C and it was an indication of crystalline silicon formation. The average crystallite sizes were 42.60, 47.24, 54.38, 56.21, 59.47 and 63.18 nm and the sharp peaks were a revelation of face-centred cubic structure formation and the reduction in the Si-NPs size was achieved by lowering the sintering temperature. According to Venkateswaram et al. (2012), Si-NPs obtained at a temperature of 850°C is suitable for solar cell fabrication. The temperature condition used for the XRD analysis was also applied for the particle size analysis (PSA). , the PSA of the Si-NPs was in the range of 40–125, 48–104, 55–119, 60–134 nm for 550°C, 650°C, 750°C and 750 °C, respectively. The maximum distribution particle size was 72 ± 3, 80 ± 3, 84 ± 3 and 94 ± 3 nm for the above-mentioned temperature conditions, respectively, and the size of the Si-NPs increased with an increase in temperature.
From , a strong absorption band was obtained at 800 cm-1 at low sample product pressure and it corresponded to the Si-H2 bending mode. Secondly, a 1400 cm-1 and 1700 cm−1 absorption bands were present, while the peaks seen at 678 cm−1was an indication of Si-Si stretching mode. The presence of CH2 stretching band was found at 3400 cm−1. From , all the temperatures studied has an agglomeration spherical morphology at a particle size of between 70 and 100 nm, but the agglomeration morphology obtained at 850O°C was higher than the morphology obtained from every other temperature studied. The UV-Vis analysis displayed in confirmed that the absorption peaks and wavelength of around 300–310 nm were present at 850°C and it was better than other temperatures investigated. In this case, the silicon powder has pure phase formation, high purity and good absorption peaks and can be employed for solar cell fabrication. The XRF result shown in equally affirms the potentials of Si-NPs for solar cell fabrication.
However, Venkateswaram et al. (2012) and his co-workers affirmed that MRM was very attractive for Si-NPs production due to its cost effectiveness, but according to Ahire et al. (Citation2012), the chemical synthesis technique is more attractive because of the possibility of surface modification and control of Si particle size distribution, but contamination of residual side products may be a setback.
Solar cell technologies
Solar Cell Technology involves the harnessing of incident optical energy from the sun. The most widely used semiconductor material in conventional solar cells is silicon (Si) (Ghahremanirad, Olyaee, and Chizari Citation2016). This material is widely used in photovoltaic industry and more than 90% of the PV market is dominated by silicon solar cells (Mutlugun, Soganci, and Demir Citation2008; Sampaio and González Citation2017). However, the solar conversion efficiency and photovoltaic device parameters are very low due to the intrinsic properties of silicon. In the ultraviolet (UV) spectrum, silicon has a high absorption coefficient which results in short absorption length. It is difficult to collect the photo-generated carriers across silicon solar cell and the electrical energy generated under UV illumination is very low. The high refractive index of silicon is more than 30%, and incident radiation is reflected back hence low conversion efficiency (Prevo, Hon, and Velev Citation2007).
shows the working mechanism of a solar cell. Basically, a photovoltaic solar cell is a thin wafer which consists of a very thin layer of phosphorous doped (n-type) silicon on top of a thicker layer of boron-doped (p-type) silicon. An electrical field is created near the top surface of the cell where the two materials meet (the P-N junction). The photovoltaic effect is created when sunlight hits the semiconductor surface, thus exciting an electron which is attracted towards the n-type semiconductor material and resulting in generation of current. Current generated by a photovoltaic (PV) solar cell is dependent on its efficiency, size (surface area) and intensity of sunlight hitting the surface (Kumar Moluguri, Murthy, and Harshavardhan Citation2016). illustrates the progress in solar cell efficiency from 1993–2017.
Figure 11. Solar cell working mechanism (Adapted from Kumar Moluguri, Murthy, and Harshavardhan Citation2016)
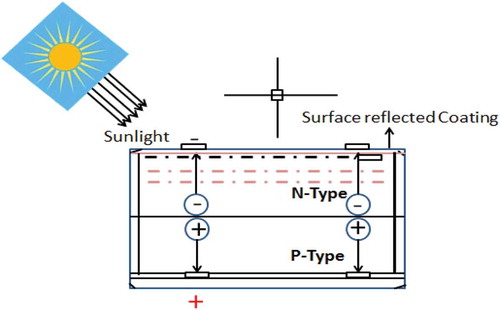
Figure 12. Progress in the Efficiency of Solar Cells from 1993–2017 (Ghahremanirad, Olyaee, and Chizari Citation2016)
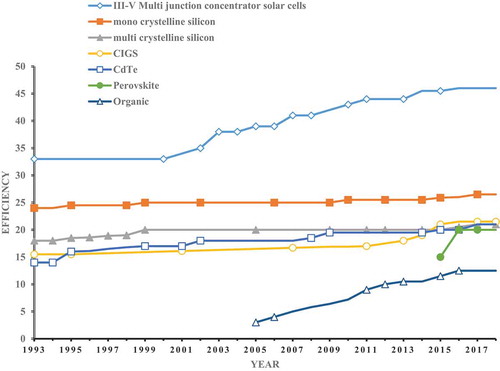
The recent researches on thin films photovoltaic technologies have been appreciated to have a high potential for cost-cutting which is the main issue of thin-film silicon PV technologies (Martin et al. Citation2004). The major advantage of these technologies is that there is a material reduction as compared to silicon wafers (Sopori Citation2007). With evolving technology and research, solar cells which make use of a thin layer of active materials are proposed. However, they have a challenge of absorbing long-wavelength light as it passes through the thin layer of active material without being absorbed hence the use of light-trapping structures (LTS) is applied to improve absorption in the active layer (Ghahremanirad, Olyaee, and Chizari Citation2016). The cost reduction, adaptability and high efficiency of thin-film solar cells lead to their use in power generation mobile devices and building-integrated photovoltaics. The fabrication of these cells is however complex and challenging since there is a contradictory interchange between their optical and electrical properties (van Dijk et al. Citation2016). For excellent optical performance, the photovoltaic solar cell should be thicker while for best electrical performance and reduction in cost, a thin photovoltaic solar cell is considered the best. This can be efficiently achieved by the improvement of the diffusion length of charge carriers (van Dijk et al. Citation2016). For commercialisation purposes, thin-film silicon solar cell technology requires its energy conversion efficiency values to be increased with a technique commensurate with low cost of fabrication.
Current trends in solar cell technology
Razykov et al. (Citation2011), reported that the current solar photovoltaic market was growing annually at a rate of 35–40%, and photovoltaic production was at 10.66 GW in 2009. The crystalline silicon and polycrystalline silicon wafer technologies dominate more than 80% of the global PV industries. Gallium Arsenide and single junction crystalline solar cells are almost reaching their maximum theoretical maximum efficiency, whereas; thin-film solar cells have promising efficiency results (Razykov et al. Citation2011) and the efficiencies are highlighted in .
Table 7. Conversion efficiency of selected thin-film solar cells
Razykov et al. (Citation2011) concluded that continuous research and development (R&D) is biased towards increasing the efficiency of thin-film solar cells and nano-PV devices. They also highlighted that emphasis should be on the development of cost-effective manufacturing technologies that will lower the solar module production cost.
Solar photovoltaics are proving to be a promising opportunity for power generation and business Devabhaktuni et al. (Citation2013). There is a remarkable improvement by international, governmental and non-governmental organisations in supporting solar technology uptake in different nations. The progress has improved the quality of living to those who were once lacking modern energy. Developing societies will benefit from a rise in solar PV system installation. These authors concluded that due to intervention by more organisations volunteering their financial, technical and professional services, solar photovoltaic technology is becoming cost-effective. The current efforts by industry leaders and researchers have also reduced the costs and improved the efficiencies, hence, increasing the demand for solar PV technologies. There is a speculation that in the next decade’s solar power will be the primary, integrated and cost-effective power source that reduces environmental impact and increase energy security (Devabhaktuni et al. Citation2013)
The Photovoltaics PV cell technologies can be divided into three generations which are 1st, 2nd and 3rd Generation PVs. The overall efficiency and performance of these PV generations vary due to types of semiconductor materials used. The more commercially mature generations are the 1st and 2nd Generations while 3rd Generation is in R&D phase and premature (Gangopadhyay, Jana, and Das Citation2013; Khan and Arsalan Citation2016)
Methods of solar cell fabrication
The most common solar cell technologies are monocrystalline, polycrystalline and amorphous. Monocrystalline silicon cells are produced from pure silicon (single crystal) wafers. The wafer substrates are cut from column ingots grown by the Czochralski (CZ) process (Goetzberger, Hebling, and Schock Citation2003; Miles Citation2006). Single-crystal solar cells are cut from pieces of unbroken silicon crystals. The crystals are shaped as cylinders and sliced into circular disks. These slices can be cut into other shapes such as rectangular or square to optimise the space to be occupied by cells on the module.
Polycrystalline solar cells are made from silicon substrates cut from polycrystalline ingots formed by melting and pouring silicon into a mould. The mound forms a squared cross-section. Thin slices are cut from the block. There is no material loss on the fact that the discs are square shaped in nature. As the material cools down it crystallises in an imperfect manner causing the polycrystalline cells to have a somewhat lower energy conversion efficiency compared to the single-crystalline cells. The polycrystalline cells are slightly larger in size per gained watt than the monocrystalline cells (Nordtröm Citation2012). The methods used to make polycrystalline cells include the heat exchange method (HEM), electromagnetic casting (EMC) and directional solidification system (DSS) with DSS being the most common method (Miles Citation2006). Basically, the chemical route is used to produce polycrystalline cells while the metallurgical route is used to produce monocrystalline cells (Xakalashe and Tangstad Citation2012) as shown in . The production of monocrystalline solar cells is more complex compared to the production of polycrystalline or multi-crystalline solar cells, and both monocrystalline and polycrystalline cells are then polished and treated to repair potential damages that could have occurred during slicing.
Figure 13. Stages to produce crystalline silicon solar cells from quartz (Goetzberger, Hebling, and Schock Citation2003)
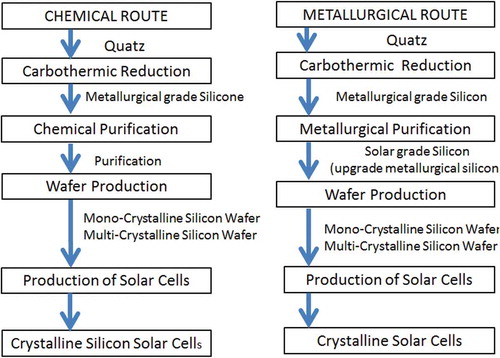
Meanwhile, the amorphous silicon cells are produced by depositing a silicon film on the substrate like a glass plate. This can be done by plasma-enhanced chemical vapour deposition, hot-wire catalytic deposition, Very High Frequency (VHF) glow discharge deposition, indirect microwave deposition and hot-wire glow discharge deposition.
Nano photovoltaics
According to PV Magazine USA: 2017, European researchers have become the first to successfully integrate a nanophotonic structure into a crystalline silicon solar cell, boosting its light absorption and greatly reducing silicon use. This breakthrough, the researchers say, sets a pathway for scaling down the texture of crystalline solar cells from the micro to the nano-scale.
Silicon nanoparticles in solar cells
The use of silicon nanoparticles in solar cell production not only saves material but also improves the efficiency of the solar cell device (Barcaro et al. Citation2017). Recently the use of self-organised plasmonic nanoparticle layers within the device window layer or back reflector using the deposition and subsequent annealing of thin metal films has been explored (Chen et al. Citation2013). The accurate tailoring of periodic nanoparticle arrays to the absorption characteristics of the amorphous silicon material is expected to yield an increase in performance compared to randomised particles (Crudgington, Rahman, and Boden Citation2017). In photovoltaic cells, it is regarded that the purity of silicon (Si) needs to be above 99.9999% (wt%) (Six nines) to enable long carrier diffusion length. Silicon (Si) nanowires and nanoparticles can provide the following advantages: absorption enhancement, efficient carrier extraction and reduced requirements for material quality in solar photovoltaics (Zong et al. Citation2015). shows silicon nanoparticles incorporated in a solar cell to enhance solar cell performance.
Figure 14. Quantum-Confined SiNPs can be used as a high bandgap layer in lieu of other materials allowing for a multi-bandgap solar cell composed entirely of Silicon (Adapted from Klafehn Citation2016)
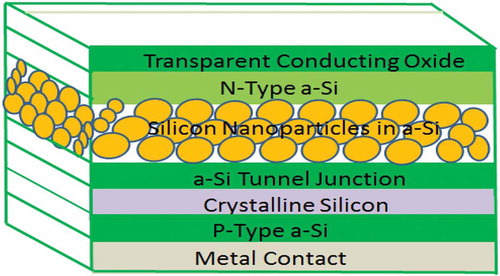
Nanocrystalline silicon has been proven to be a viable material for use in Photovoltaics. The growth process for traditional nanocrystalline silicon involves hydrogen dilution, which harms the amorphous material’s performance or post-process annealing, which adds another step to the growth process. Decoupling the growth of a-Si and SiNPs solves this problem (Klafehn Citation2016).
Challenges in the valorisation of agricultural waste into nano silicon
The effects of exposure to engineered nanoparticles may be different from the effects caused by naturally occurring nanoparticles. Engineered nanoparticles may be better to evade the body’s defences because of their size or protective coatings. Moreover, the health and environmental risks raised due to the exposure to engineered nanoparticles need further study (Prasad, Kumar, and Prasad Citation2014). Water availability is the most critical aspect in the valorisation of agricultural waste as it is a requirement in growing the crops until the use of the produced waste. Water scarcity may also become a challenge in the production of bio wastes. Genuine progress in the valorisation of agricultural waste requires a close partnership between chemists and engineers to enable new ideas from chemists can quickly be transformed to meet the needs of global increasing population. Most researchers are still having silo mentality in working together and this challenge the progress in this field (Tuck, Pérez, Horváth, Sheldon, and Poliakoff Citation2012).
Nanoparticles are generally synthesised using a bottom-top or top-bottom approach based on whether a chemical process was used to produce the materials or the material is produced through size reduction from its bulk state through chemical attrition or physical milling processes (Adebisi et al. Citation2017). In the bottom-top approach, nanoparticles can be synthesised using chemical and biological methods by self-assembly of atoms to new nuclei which grow into a particle of nanoscale size while in the top-bottom approach, suitable bulk material is broken down into fine particles by size reduction using various lithographic techniques e.g. grinding, milling, sputtering and thermal/laser ablation. Most of these methods for the synthesis of nanoparticles are very expensive (Kharissova, Dias, Kharisov, Pérez, and Pérez Citation2013). The challenges in the field are outweighed by the benefits of nanotechnology to research.
Conclusions and outlook
This review demonstrated that the production of nano-silicon particles from bio-waste ashes had attracted researchers’ growing interests in the last decades as a beneficial waste management and safe environmentally effective approach. The various routes for which SiNPs had been produced from bio-wastes and their production technologies featured processes such as pyrolysis, leaching, sol-gel, reduction, acid pretreatment, combustion, precipitation, supercritical CO2-drying, biotransformation, calcination and magnesiothermic reduction from different source materials to demonstrate diverse sources of bio-waste derived SiNPs. However, Venkateswaram et al. (2012) and his co-workers affirmed that MRM was very attractive for Si-NPs production due to its cost effectiveness, but according to Ahire et al. (2012), the chemical synthesis technique is more attractive because of the possibility of surface modification and control of Si particle size distribution, but contamination of residual side products may be a setback.
The current study, however, outlined different characterisation methods to update on the current and effective techniques for an understanding of the nature of the nano-materials produced. This will project the material for a suitable application. To date, major characterisation techniques include XRD, UV-Vis Absorption, SEM, TEM, FTIR, AFM, HRTEM and Raman Spectroscopy.
For the past 20 years, researchers have focused on different feedstocks mainly silane, silica, SiO2, SiCl4, bamboo, sugar cane bagasse, rice husk, groundnut shell, coffee husk and had applied ultra-sonification, microwave-induced decomposition, PLA, low-temperature solution route, plasma-enhanced chemical vapour deposition (PECVD), spark discharge process, metallothermic process and hydrometallurgical.
More so, the production of SiNPs using combustion, vacuum directional solidification, halidothermic reduction, pyro-chemical process and vermicomposting with annelid technologies proved attractive because, the processes enhance the SiNPs high active surface state, physical characteristics, outstanding photoluminescence and biocompatibility in solar cell fabrication. The review, however, indicated that the conversion efficiency in existing solar cell applications remains very low (ranging from 17% to 25%). The efficiency of photovoltaic solar cells depends on the size (surface area) and the intensity of sunlight hitting the surface. For over 20 years, latest research efforts had recorded photovoltaic efficiency of over 45% in 2016, using multi-junction solar cells whereas in 2004 below 5% conversion efficiency was achieved on the application of organic solar cell technology.
The review shows that there is still more research work required in the production of silicon nanoparticles to fully support solar cell technology and to reduce environmental challenges posed by bio waste.
Acknowledgments
The authors wish to acknowledge the University of Witwatersrand Post Graduate Merit Award, Wise Petroleum for the Finances. The following institutions supported this work Bindura University of Science Education, Green Fuel Private Limited and Scientific and Industrial Research and Development Centre.
Disclosure statement
No potential conflict of interest was reported by the authors.
Additional information
Notes on contributors
Fortunate Farirai
Fortunate Farirai is a PhD candidate in the School of Chemical and Metallurgical Engineering, Faculty of Engineering and the Built Environment, University of Witwatersrand, Johannesburg, South Africa. She holds MSc Renewable Energy and BSc Chemical Technology from University of Zimbabwe and Midlands State University,respectively. Her area of interests includes and not limited to renewable energy research, empowering women and girls in science.
Maxwell Ozonoh
Maxwell Ozonoh is a PhD research student in the School of Chemical and Metallurgical Faculty of Engineering and the Built Environment, University of the Witwatersrand Johannesburg, South Africa. His research interest is on Waste-to- Energy conversion.
Thomas Chinedu Aniokete
Thomas Chinedu Aniokete is a PhD candidate in the School of Chemical and Metallurgical Engineering, University of Witwatersrand, Johannesburg South Africa. His research is on the development of heterogeneous catalysts for biodiesel production.
Orevaoghene Eterigho-Ikelegbe
Orevaoghene Eterigho-Ikelegbe completed his MSc in the School of Chemical and Metallurgical Engineering, University of the Witwatersrand, South Africa. He also received his B.Sc. in Chemical Engineering from the Obafemi Awolowo University, Nigeria. His research interest is in nanoparticles/nanoporous materials, zeolites, membrane gas separation and clean coal technologies.
Mathew Mupa
Dr Mathew Mupa is a Senior lecturer, at Bindura University of Science Education’s Department of Chemistry. He holds a master’s degree in industrial processing chemistry, from Technical University of Carl Schorlemmer, Merseburg, former Germany Democtratic Republic and a PhD in Analytical and Polymer Chemistry from Innsbruck University’s Institute of Analytical Chemistry and Radiochemistry, Austria. Dr Mupa has also worked as a senior scientist with the Scientific and Industrial Research and Development Centre, Harare, Zimbabwe. His research interest is in separation sciences with focus on solid phase extraction, liquid chromatographic techniques and adsorption science.
Benson Zeyi
Benson Zeyi is a Programme Officer responsible for Sub-Saharan Africa at the International Renewable Energy Agency (IRENA) since December 2018. He possesses an MSc in Renewable Energy, BSc in Applied Physics and several professional certificates in Renewable Energy and Energy Efficiency. He is a Certified Energy Manager and Certified Measurement and Verification Professional. Previously, Benson was an energy expert at the Scientific & Industrial Research and Development Centre in Harare, Zimbabwe where implemented projects in renewable energy and energy efficiency. Some of the projects implemented include conducting the national energy efficiency audit for Zimbabwe, development of the NDC implementation framework for Zimbabwe and preparation of the national GHG inventory in the energy sector for Zimbabwe.
Michael Olawale Daramola
Michael Olawale Daramola primary research is within chemical and bioprocess engineering, but with main activities in nanomaterials and bioresource engineering. In the area of nanomaterials, his interest is in the development of nanoparticles, nanocomposite materials and their applications. In the area of bioresource engineering, he applies chemical and biotechnology concepts to develop chemical/biochemical/biotechnological strategies/processes for treatment and valorisation of waste materials into value-added products.
References
- Abbasi, A., and A. Zargar. 2013. “Using Baggase Ash in Concrete as Pozzolan.” Middle-East Journal of Scientific Research 13: 716–719.
- Abdulkadir, T. S., D. O. Oyejobi, and A. A. Lawal. 2014. “Evaluation of Sugarcane Bagasse Ash as a Replacement for Cement in Concrete Works.” Acta Technica Corviniensis - Bulletin of Engineering Hunedoara 7: 71–76.
- Aboyade, A. O., T. J. Hugo, M. Carrier, E. L. Meyer, R. Stahl, J. H. Knoetze, and J. F. Görgens. 2011. “Non-isothermal Kinetic Analysis of the Devolatilization of Corn Cobs and Sugar Cane Bagasse in an Inert Atmosphere.” Thermochimica Acta 517: 81–89. doi:10.1016/j.tca.2011.01.035.
- Adebisi, J., J. Agunsoye, S. Bello, I. Ahmed, O. Ojo, and S. Hassan. 2017. “Potential of Producing Solar Grade Silicon Nanoparticles from Selected Agro-wastes: A Review.” Solar Energy 142: 68–86. doi:10.1016/j.solener.2016.12.001.
- Adebisi, J. A., J. O. Agunsoye, S. A. Bello, M. Haris, M. M. Ramakokovhu, M. O. Daramola, and S. B. Hassan. 2019. “Green Production of Silica Nanoparticles from Maize Stalk.” Particulate Science and Technology 1–9. doi:10.1080/02726351.2019.1578845.
- Adesanya, D. A., and A. A. Raheem. 2009. “Development Of Corn Cob Ash Blended Cement.” Construction and Building Materials 23 (1): 347–52. doi: 10.1016/j.conbuildmat.2007.11.013.
- Adriano, D. C., A. L. Page, A. A. Elseewi, A. C. Chang, and I. Straughan. 1980. “Utilization and Disposal of Fly Ash and Other Coal Residues in Terrestrial Ecosystems: A Review 1.” Journal of Environmental Quality 9: 333–344. doi:10.2134/jeq1980.00472425000900030001x.
- Agunsoye, J., J. Adebisi, S. Bello, M. Haris, J. Agboola, and S. Hassan. 2018. “Synthesis of Silicon Nanoparticles from Cassava Periderm by Reduction Method.” MS&T18, 701–709.
- Ahire, J. H., Q. Wang, P. R. Coxon, G. Malhotra, R. Brydson, R. Chen, and Y. Chao. 2012. “Highly Luminescent and Nontoxic Amine-Capped Nanoparticles from Porous Silicon: Synthesis and Their Use in Biomedical Imaging.” ACS Applied Materials & Interfaces 4: 3285–3292. doi:10.1021/am300642m.
- Armaroli, N., and V. Balzani. 2007. “The Future of Energy Supply: Challenges and Opportunities.” Angewandte Chemie International Edition 46: 52–66. doi:10.1002/(ISSN)1521-3773.
- Atkins, T. M., A. Thibert, D. S. Larsen, S. Dey, N. D. Browning, and S. M. Kauzlarich. 2011. “Femtosecond Ligand/Core Dynamics of Microwave-Assisted Synthesized Silicon Quantum Dots in Aqueous Solution.” Journal of the American Chemical Society 133: 20664–20667. doi:10.1021/ja207344u.
- Baldwin, R. K., K. A. Pettigrew, E. Ratai, M. P. Augustine, and S. Kauzlarich. 2002. “Solution Reduction Synthesis of Surface Stabilized Silicon Nanoparticles.” Chemical Communications 1822–1823. doi:10.1039/b205301b.
- Bao, Z., M. R. Weatherspoon, S. Shian, Y. Cai, P. D. Graham, S. M. Allan, G. Ahmad, et al. 2007. “Chemical Reduction of Three-dimensional Silica Micro-assemblies into Microporous Silicon Replicas.” Nature 446: 172–175. doi:10.1038/nature05570.
- Barcaro, G., S. Monti, L. Sementa, and V. Carravetta. 2017. “Atomistic Modelling of Si Nanoparticles Synthesis.” Crystals 7: 54. doi:10.3390/cryst7020054.
- Barth, S., F. Hernandez-Ramirez, J. D. Holmes, and A. Romano-Rodriguez. 2010. “Synthesis and Applications of One-dimensional Semiconductors.” Progress in Materials Science 55: 563–627. doi:10.1016/j.pmatsci.2010.02.001.
- Basika, E., J. Kigozi, and N. Kiggundu. 2015. “Investigation of Sugar Cane Bagasse Ash as a Binding Material for the Construction Industry.” Journal of Global Ecology and Environment 2: 205–208.
- Belomoin, G., J. Therrien, A. Smith, S. Rao, R. Twesten, S. Chaieb, M. H. Nayfeh, L. Wagner, and L. Mitas. 2002. “Observation of a Magic Discrete Family of Ultrabright Si Nanoparticles.” Applied Physics Letters 80: 841–843. doi:10.1063/1.1435802.
- Bent, S. F. 2002. “Organic Functionalization of Group IV Semiconductor Surfaces: Principles, Examples, Applications, and Prospects.” Surface Science 500: 879–903. doi:10.1016/S0039-6028(01)01553-9.
- Bernardis, S. 2012. “Engineering Impurity Behavior on the Micron-scale in Metallurgical-grade Silicon Production”. Massachusetts Institute of Technology. https://dspace.mit.edu/handle/1721.1/101457.
- Bhagiyalakshmi, M, L. J. Yun, R. Anuradha, and H. T. Jang. 2010. “Utilization Of Rice Husk Ash as Silica Source for The Synthesis Of Mesoporous Silicas and Their Application to Co2 Adsorption Through Tren/tepa Grafting.” Journal Of Hazardous Materials 175 (1): 928–38. doi: 10.1016/j.jhazmat.2009.10.097.
- Bhatia, S. 2016. “Nanoparticles Types, Classification, Characterization, Fabrication Methods and Drug Delivery Applications.” In Natural Polymer Drug Delivery Systems: Nanoparticles, Plants, and Algae, edited by S. Bhatia, 33–93. Cham: Springer International Publishing.
- Binod, P., R. Sindhu, R. Rani Singhania, S. Vikram, L. Devi, S. Nagalakshmi, N. Kurien, R. K. Sukumaran, and A. Pandey. 2010. “Bioethanol Production from Rice Straw: an Overview.” Bioresource Technology, Special Issue on Lignocellulosic Bioethanol: Current Status and Perspectives 101 (13): 4767–74. doi: 10.1016/j.biortech.2009.10.079.
- Bley, R. A., and S. M. Kauzlarich. 1996. “A Low-Temperature Solution Phase Route for the Synthesis of Silicon Nanoclusters.” Journal of the American Chemical Society 118: 12461–12462. doi:10.1021/ja962787s.
- Boulos, M. I., P. Fauchais, and E. Pfender. 2013. Thermal Plasmas: Fundamentals and Applications. Springer Science & Business Media.
- Carmona, V. B., R. M. Oliveira, W. T. L. Silva, L. H. C. Mattoso, and J. M. Marconcini. 2013. “Nanosilica from Rice Husk: Extraction and Characterization.” Industrial Crops and Products 43: 291–296. doi:10.1016/j.indcrop.2012.06.050.
- Castaldelli, V. N., J. L. Akasaki, J. L. P. Melges, M. M. Tashima, L. Soriano, M. V. Borrachero, J. Monzó, and J. Payá. 2013. “Use of Slag/Sugar Cane Bagasse Ash (SCBA) Blends in the Production of Alkali-Activated Materials.” Materials 6: 3108–3127. doi:10.3390/ma6083108.
- Chang, H., and S.-Q. Sun. 2014. “Silicon Nanoparticles: Preparation, Properties, and Applications.” Chinese Physics B 23: 088102. doi:10.1088/1674-1056/23/8/088102.
- Chen, H., F. Wang, C. Zhang, Y. Shi, G. Jin, and S. Yuan. 2010. “Preparation of Nano-silica Materials: The Concept from Wheat Straw.” Journal of Non-Crystalline Solids 356: 2781–2785. doi:10.1016/j.jnoncrysol.2010.09.051.
- Chen, X., B. Jia, Y. Zhang, and M. Gu. 2013. “Exceeding the Limit of Plasmonic Light Trapping in Textured Screen-printed Solar Cells Using Al Nanoparticles and Wrinkle-like Graphene Sheets.” Light: Science & Applications (London) 2: e92. doi:10.1038/lsa.2013.48.
- Cho, B., S.-G. Lee, H.-G. Woo, and H. Sohn. 2013. “Synthesis and Optical Characterization of Silicon Nanoparticles.” Journal of Nanoscience and Nanotechnology 13: 384–387. doi:10.1166/jnn.2013.6949.
- Crudgington, L. J., T. Rahman, and S. A. Boden. 2017. “Development of Amorphous Silicon Solar Cells with Plasmonic Light Scattering.” Vacuum 139: 164–172. doi:10.1016/j.vacuum.2016.12.026.
- Demirbas, A. 2011. “Waste Management, Waste Resource Facilities and Waste Conversion Processes.” Energy Conversion and Management 52: 1280–1287. doi:10.1016/j.enconman.2010.09.025.
- Devabhaktuni, V., M. Alam, S. S. R. Depuru, R. C. Green, D. Nims, and C. Near. 2013. “Solar Energy: Trends and Enabling Technologies.” Renewable and Sustainable Energy Reviews 19: 555–564. doi:10.1016/j.rser.2012.11.024.
- Drosg, B., W. Fuchs, T. A. Seadi, M. Madsen, and B. Linke. 2015. “Nutrient Recovery by Biogas Digestate Processing”. IEA Bioenergy Dublin.Vol. 40.
- Du Preez, P., and others. 1970. “The Effect of Silica on Cane Growth.” In Proceedings of the South African Sugar Technologists’ Association, 44: 183–188.
- Duhan, J. S., R. Kumar, N. Kumar, P. Kaur, K. Nehra, and S. Duhan. 2017. “Nanotechnology: The New Perspective in Precision Agriculture.” Biotechnology Reports 15: 11–23. doi:10.1016/j.btre.2017.03.002.
- Duke, C. B. 1996. “Semiconductor Surface Reconstruction: The Structural Chemistry of Two-Dimensional Surface Compounds.” Chemical Reviews 96: 1237–1260. doi:10.1021/cr950212s.
- Ehbrecht, M., and F. Huisken. 1999. “Gas-phase Characterization of Silicon Nanoclusters Produced by Laser Pyrolysis of Silane.” Physical Review B 59: 2975–2985. doi:10.1103/PhysRevB.59.2975.
- Eisenhawer, B., D. Zhang, R. Clavel, A. Berger, J. Michler, and S. Christiansen. 2011. “Growth of Doped Silicon Nanowires by Pulsed Laser Deposition and Their Analysis by Electron Beam Induced Current Imaging.” Nanotechnology 22: 705–706. doi:10.1088/0957-4484/22/7/075706.
- English, D. S., L. E. Pell, Z. Yu, P. F. Barbara, and B. A. Korgel. 2002. “Size Tunable Visible Luminescence from Individual Organic Monolayer Stabilized Silicon Nanocrystal Quantum Dots.” Nano Letters 2: 681–685. doi:10.1021/nl025538c.
- Erogbogbo, F., K.-T. Yong, R. Hu, W.-C. Law, H. Ding, C.-W. Chang, P. N. Prasad, and M. T. Swihart. 2010. “Biocompatible Magnetofluorescent Probes: Luminescent Silicon Quantum Dots Coupled with Superparamagnetic Iron(III) Oxide.” ACS Nano 4: 5131–5138. doi:10.1021/nn101016f.
- Espíndola-Gonzalez, A., A. Martínez-Hernández, C. Angeles-Chávez, V. Castaño, and C. Velasco-Santos. 2010. “Novel Crystalline SiO2 Nanoparticles via Annelids Bioprocessing of Agro-Industrial Wastes.” Nanoscale Research Letters 5: 1408. doi:10.1007/s11671-010-9654-6.
- Falk, G., G. Shinhe, L. Teixeira, E. Moraes, and A. N. de Oliveira. 2019. “Synthesis of Silica Nanoparticles from Sugarcane Bagasse Ash and Nano-silicon via Magnesiothermic Reactions.” Ceramics International 45: 21618–21624. doi:10.1016/j.ceramint.2019.07.157.
- Ferreira-Leitão, V., L. M. F. Gottschalk, M. A. Ferrara, A. L. Nepomuceno, H. B. C. Molinari, and E. P. S. Bon. 2010. “Biomass Residues in Brazil: Availability and Potential Uses.” Waste Biomass Valorization 1: 65–76. doi:10.1007/s12649-010-9008-8.
- Fox, R. L., J. A. Silva, D. L. Plucknett, and D. Y. Teranishi. 1969. “Soluble and Total Silicon in Sugar Cane.” Plant and Soil 30: 81–92. doi:10.1007/BF01885263.
- Frías, M., E. Villar-Cociña, and E. Valencia-Morales. 2007. “Characterisation Of Sugar Cane Straw Waste as Pozzolanic Material for Construction: Calcining Temperature and Kinetic Parameters.” Waste Management 27 (4): 533–38. doi: 10.1016/j.wasman.2006.02.017.
- Gangopadhyay, U., S. Jana, and S. Das. 2013. “State of Art of Solar Photovoltaic Technology.” In Conference Papers in Science, Hindawi. doi:10.1155/2013/764132.
- Georgieva, T. I., M. J. Mikkelsen, and B. K. Ahring. 2008. “Ethanol Production from Wet-exploded Wheat Straw Hydrolysate by Thermophilic Anaerobic Bacterium Thermoanaerobacter BG1L1 in a Continuous Immobilized Reactor.” Applied Biochemistry and Biotechnology 145: 99–110. doi:10.1007/s12010-007-8014-1.
- Ghahremanirad, E., S. Olyaee, and A. Chizari. 2016. “Nano-plasmonic Thin-film Solar Cell Receiver in Visible Light Communication.” In 2016 10th International Symposium on Communication Systems, Networks and Digital Signal Processing (CSNDSP), 1–5.IEEE.
- Goetzberger, A., C. Hebling, and H.-W. Schock. 2003. “Photovoltaic Materials, History, Status and Outlook.” Materials Science and Engineering: R: Reports 40: 1–46. doi:10.1016/S0927-796X(02)00092-X.
- Gupta, K., and N. Gupta. 2016. “Semiconductor Materials: Their Properties, Applications, and Recent Advances.” In Advanced Semiconducting Materials and Devices, 3–40. Engineering Materials. Cham: Springer International Publishing. https://doi.org/10.1007/978-3-319-19758-6_1.
- Hapala, P., K. Kůsová, I. Pelant, and P. Jelínek. 2013. “Theoretical Analysis of Electronic Band Structure of 2- to 3-nm Si Nanocrystals.” Physical Review B 87: 195420. doi:10.1103/PhysRevB.87.195420.
- Hariharan, V., M. Shanmugam, K. Amutha, and G. Sivakumar. 2014. “Preparation and Characterization of Ceramic Products Using Sugarcane Bagasse Ash Waste.” Research Journal of Recent Sciences 2277: 2502.
- He, J., M. A. Hossain, H. Lin, W. Wang, S. K. Karuturi, B. Hoex, J. Ye, P. Gao, J. Bullock, and Y. Wan. 2019. “15% Efficiency Ultrathin Silicon Solar Cells with Fluorine-Doped Titanium Oxide and Chemically Tailored Poly (3, 4-ethylenedioxythiophene): Poly (Styrenesulfonate) as Asymmetric Heterocontact.” ACS Nano 3: 6356–6362. doi:10.1021/acsnano.9b01754.
- He, Y., Z.-H. Kang, Q.-S. Li, C. H. A. Tsang, C.-H. Fan, and S.-T. Lee. 2009. “Ultrastable, Highly Fluorescent, and Water-Dispersed Silicon-Based Nanospheres as Cellular Probes.” Angewandte Chemie 121: 134–138. doi:10.1002/ange.200802230.
- Heath, J. R. 1992. “A Liquid-Solution-Phase Synthesis of Crystalline Silicon.” Science Wash 258: 1131. doi:10.1126/science.258.5085.1131.
- Ho, P., M. E. Coltrin, and W. G. Breiland. 1994. “Laser-Induced Fluorescence Measurements and Kinetic Analysis of Si Atom Formation in a Rotating Disk Chemical Vapor Deposition Reactor.” The Journal of Physical Chemistry 98: 10138–10147. doi:10.1021/j100091a032.
- Hopkins, J. B., P. R. R. Langridge‐Smith, M. D. Morse, and R. E. Smalley. 1983. “Supersonic Metal Cluster Beams of Refractory Metals: Spectral Investigations of Ultracold Mo2.” The Journal of Chemical Physics 78: 1627–1637. doi:10.1063/1.444961.
- Hu, S.-K., G.-H. Cheng, M.-Y. Cheng, B.-J. Hwang, and R. Santhanam. 2009. “Cycle Life Improvement of ZrO2-coated Spherical LiNi1/3Co1/3Mn1/3O2 Cathode Material for Lithium Ion Batteries.” Journal of Power Sources 188: 564–569. doi:10.1016/j.jpowsour.2008.11.113.
- Huan, C., and S. Shu-Qing. 2014. “Silicon Nanoparticles: Preparation, Properties, and Applications.” Chinese Physics B 23: 088102. doi:10.1088/1674-1056/23/8/088102.
- Huisken, F., G. Ledoux, O. Guillois, and C. Reynaud. 2002. “Light-Emitting Silicon Nanocrystals from Laser Pyrolysis.” Advanced Materials 14: 1861–1865. doi:10.1002/adma.200290021.
- Hussein, A. A. E., N. Shafiq, M. F. Nuruddin, and F. A. Memon. 2014. “Compressive Strength and Microstructure of Sugar Cane Bagasse Ash Concrete.” Research Journal of Applied Sciences, Engineering and Technology 7: 2569–2577. doi:10.19026/rjaset.7.569.
- Iacovidou, E., J. Hahladakis, I. Deans, C. Velis, and P. Purnell. 2018. “Technical Properties of Biomass and Solid Recovered Fuel (SRF) Co-fired with Coal: Impact on Multi-dimensional Resource Recovery Value.” Waste Management 73: 535–545. doi:10.1016/j.wasman.2017.07.001.
- International Energy Agency. 2017. “Energy Access Outlook 2017: From Poverty to Prosperity, Special Report.”OECD/IEA, Paris.
- Izdebska, J., and S. Thomas. 2015. Printing on Polymers: Fundamentals and Applications. Elsevier, Waltham .
- Kabel, M. A., G. Bos, J. Zeevalking, A. G. J. Voragen, and H. A. Schols. 2007. “Effect of Pretreatment Severity on Xylan Solubility and Enzymatic Breakdown of the Remaining Cellulose from Wheat Straw.” Bioresource Technology 98: 2034–2042. doi:10.1016/j.biortech.2006.08.006.
- Kauldhar, B. S., and S. K. Yadav. 2018. “Turning Waste to Wealth: A Direct Process for Recovery of Nano-silica and Lignin from Paddy Straw Agro-waste.” Journal of Cleaner Production 194: 158–166. doi:10.1016/j.jclepro.2018.05.136.
- Kawade, U. R., V. R. Rathi, and M. V. D. Girge. 2013. “Effect of Use of Bagasse Ash on Strength of Concrete.” International Journal of Innovative Science Engineering and Technology 2: 2997–3000.
- Kaygusuz, K. 2012. “Energy for Sustainable Development: A Case of Developing Countries.” Renewable and Sustainable Energy Reviews 16: 1116–1126. doi:10.1016/j.rser.2011.11.013.
- Kazmi, Syed M. S., S Abbas, M. A. Saleem, M. J. Munir, and A. Khitab. 2016. “Manufacturing of Sustainable Clay Bricks: Utilization of Waste Sugarcane Bagasse and Rice Husk Ashes.” Construction and Building Materials 120 (September): 29–41. doi:10.1016/j.conbuildmat.2016.05.084.
- Khan, J., and M. H. Arsalan. 2016. “Solar Power Technologies for Sustainable Electricity Generation – A Review.” Renewable and Sustainable Energy Reviews 55: 414–425. doi:10.1016/j.rser.2015.10.135.
- Kharissova, O. V., H. V. R. Dias, B. I. Kharisov, B. O. Pérez, and V M. J. Pérez. 2013. “The Greener Synthesis Of Nanoparticles.” Trends in Biotechnology 31 (4): 240–48. doi: 10.1016/j.tibtech.2013.01.003.
- Kim, D.-H., N. Lu, R. Ma, Y.-S. Kim, R.-H. Kim, S. Wang, J. Wu, et al. 2011. “Epidermal Electronics.” Science 333: 838–843. doi:10.1126/science.1206157.
- Klafehn, G. W. 2016. “Silicon Nanoparticle Optimization and Integration into Amorphous Silicon via PECVD for Use in Photovoltaics.” PhD, Colorado School of Mines.
- Knipping, J., H. Wiggers, B. Rellinghaus, P. Roth, D. Konjhodzic, and C. Meier. 2004. “Synthesis of High Purity Silicon Nanoparticles in a Low Pressure Microwave Reactor.” Journal of Nanoscience and Nanotechnology 4: 1039–1044. doi:10.1166/jnn.2004.149.
- Kornowski, A., M. Giersig, R. Vogel, A. Chemseddine, and H. Weller. 1993. “Nanometer-sized Colloidal Germanium Particles: Wet-chemical Synthesis, Laser-induced Crystallization and Particle Growth.” Advanced Materials 5: 634–636. doi:10.1002/(ISSN)1521-4095.
- Kulkarni, A. P., K. M. Noone, K. Munechika, S. R. Guyer, and D. S. Ginger. 2010. “Plasmon-Enhanced Charge Carrier Generation in Organic Photovoltaic Films Using Silver Nanoprisms.” Nano Letters 10: 1501–1505. doi:10.1021/nl100615e.
- Kumar Moluguri, N., C. R. Murthy, and V. Harshavardhan. 2016. “Solar Energy System and Design - Review.” Materials Today: Proceedings 3: 3637–3645. doi:10.1016/j.matpr.2016.11.007.
- Lam, C., Y. F. Zhang, Y. H. Tang, C. S. Lee, I. Bello, and S. T. Lee. 2000. “Large-scale Synthesis of Ultrafine Si Nanoparticles by Ball Milling.” Journal of Crystal Growth 220: 466–470. doi:10.1016/S0022-0248(00)00882-4.
- Lanning, F. C., B. W. X. Ponnaiya, and C. F. Crumpton. 1958. “The Chemical Nature Of Silica in Plants. 1.” Plant Physiology 33 (5): 339–43. doi:10.1104/pp.33.5.339.
- Lee, J. H., J. H. Kwon, J.-W. Lee, H. Lee, J. H. Chang, and B.-I. Sang. 2017. “Preparation of High Purity Silica Originated from Rice Husks by Chemically Removing Metallic Impurities.” Journal of Industrial and Engineering Chemistry 50: 79–85. doi:10.1016/j.jiec.2017.01.033.
- Li, X., Y. He, S. S. Talukdar, and M. T. Swihart. 2003. “Process for Preparing Macroscopic Quantities of Brightly Photoluminescent Silicon Nanoparticles with Emission Spanning the Visible Spectrum.” Langmuir 19: 8490–8496. doi:10.1021/la034487b.
- Li, Y., X. Ding, Y. Guo, C. Rong, L. Wang, Y. Qu, X. Ma, and Z. Wang. 2011. “A New Method of Comprehensive Utilization of Rice Husk.” Journal of Hazardous Materials 186: 2151–2156. doi:10.1016/j.jhazmat.2011.01.013.
- Liou, T.-H., and -C.-C. Yang. 2011. “Synthesis and Surface Characteristics of Nanosilica Produced from Alkali-extracted Rice Husk Ash.” Materials Science and Engineering: B 176: 521–529. doi:10.1016/j.mseb.2011.01.007.
- Ludwig, W., O. Strunk, R. Westram, L. Richter, H. Meier, A. Yadhukumar, Buchner, T. Lai, et al. 2004. “ARB: A Software Environment for Sequence Data.” Nucleic Acids Research 32: 1363–1371. doi:10.1093/nar/gkh293.
- Maheswari, T. L., M. S. I. Ahamed, and S. Duraisamy. 2017. “Quality Assessment System for Object Oriented Structure.” Journal of Computational and Theoretical Nanoscience 14: 1993–2014. doi:10.1166/jctn.2017.6533.
- Martin, C. A., J. K. W. Sandler, M. S. P. Shaffer, M.-K. Schwarz, W. Bauhofer, K. Schulte, and A. H. Windle. 2004. “Formation of Percolating Networks in Multi-wall Carbon-nanotube–epoxy Composites.” Composites Science and Technology 64: 2309–2316. doi:10.1016/j.compscitech.2004.01.025.
- Matichenkov, V. V., and D. V. Calvert. 2002. “Silicon as a Beneficial Element for Sugarcane.” JASST 22: 21–29.
- McMillan, P. F., J. Gryko, C. Bull, R. Arledge, A. J. Kenyon, and B. A. Cressey. 2005. “Amorphous and Nanocrystalline Luminescent Si and Ge Obtained via a Solid-state Chemical Metathesis Synthesis Route.” Journal of Solid State Chemistry 178: 937–949. doi:10.1016/j.jssc.2004.12.040.
- Mercaldo, L. V., M. L. Addonizio, M. D. Noce, P. D. Veneri, A. Scognamiglio, and C. Privato. 2009. “Thin Film Silicon Photovoltaics: Architectural Perspectives and Technological Issues.” Applied Energy 86: 1836–1844. doi:10.1016/j.apenergy.2008.11.034.
- Miles, R. W. 2006. “Photovoltaic Solar Cells: Choice of Materials and Production Methods.” Vacuum 80: 1090–1097. doi:10.1016/j.vacuum.2006.01.006.
- Modani, P. O., and M. R. Vyawahare. 2013. “Utilization of Bagasse Ash as a Partial Replacement of Fine Aggregate in Concrete.” Procedia Engineering 51: 25–29. doi:10.1016/j.proeng.2013.01.007.
- Mohanraj, K., S. Kannan, S. Barathan, and G. Sivakumar. 2012. “Preparation and Characterization of Nano SiO2 from Corn Cob Ash by Precipitation Method.” Optoelectronics and Advanced Materials - Rapid Communications 6: 394–97.
- Mor, S., C. K. Manchanda, S. K. Kansal, and K. Ravindra. 2017. “Nanosilica Extraction from Processed Agricultural Residue Using Green Technology.” Journal of Cleaner Production 143: 1284–1290. doi:10.1016/j.jclepro.2016.11.142.
- Murillo, A., and A. Cristina. 2014. “A Decision Support Model for the Assessment of Bio-resource Management Systems.” Thesis.
- Mutlugun, E., I. M. Soganci, and H. V. Demir. 2008. “Photovoltaic Nanocrystal Scintillators Hybridized on Si Solar Cells for Enhanced Conversion Efficiency in UV.” Optics Express 16: 3537–3545. doi:10.1364/OE.16.003537.
- Nagai, T., H. Sasaki, and M. Maeda. 2012. “Thermodynamic Study for Removal of Phosphorus from Molten Silicon.” In TT Chen Honorary Symposium on Hydrometallurgy, Electrometallurgy and Materials Characterization. Hoboken, NJ, USA: John Wiley & Sons, 431–435. doi:10.1093/rpd/ncs123.
- Nagarajan, R. 2008. “Nanoparticles: Building Blocks for Nanotechnology.” In Nanoparticles: Synthesis, Stabilization, Passivation, and Functionalization, ACS Symposium Series 996. American Chemical Society 996:2–14. doi:10.1021/bk-2008-0996.ch001.
- Nayfeh, A. H., M. I. Younis, and E. M. Abdel-Rahman. 2007. “Dynamic Pull-in Phenomenon in MEMS Resonators.” Nonlinear Dynamics 48: 153–163. doi:10.1007/s11071-006-9079-z.
- Neergaard Waltenburg, H., and J. T. Yates. 1995. “Surface Chemistry of Silicon.” Chemical Reviews 95: 1589–1673. doi:10.1021/cr00037a600.
- Neiner, D., H. W. Chiu, and S. M. Kauzlarich. 2006. “Low-Temperature Solution Route to Macroscopic Amounts of Hydrogen Terminated Silicon Nanoparticles.” Journal of the American Chemical Society 128: 11016–11017. doi:10.1021/ja064177q.
- Nielsen, H., L. Baxter, G. Sclippab, C. Morey, F. Frandsen, and K. Dam-Johansen. 2000a. “Deposition of Potassium Salts on Heat Transfer Surfaces in Straw-Fired Boilers: A Pilot-Scale Study.” Fuel 79: 131–139. doi:10.1016/S0016-2361(99)00090-3.
- Nielsen, H. P., F. Frandsen, K. Dam-Johansen, and L. Baxter. 2000b. “The Implications of Chlorine-Associated Corrosion on the Operation of Biomass-Fired Boilers.” Progress in Energy and Combustion Science 26: 283–298. doi:10.1016/S0360-1285(00)00003-4.
- Nordtröm, E. 2012. Design and Development Process of Solar Panels. KTH, School of Industrial Engineering and Management. http://urn.kb.se/resolve?urn=urn:nbn:se:kth:diva-176847.
- Norsuraya, S., H. Fazlena, and R. Norhasyimi. 2016. “Sugarcane Bagasse as a Renewable Source of Silica to Synthesize Santa Barbara Amorphous-15 (SBA-15).” Procedia Engineering 148: 839–846. doi:10.1016/j.proeng.2016.06.627.
- Odo, E. A., D. T. Britton, G. G. Gonfa, and M. Harting. 2012. “Structure and Characterization of Silicon Nanoparticles Produced Using a Vibratory Disc Mill.” African Review of Physics 7:45-56.
- Okoronkwo, E. A., P. E. Imoisili, and S. O. O. Olusunle. 2013. “Extraction and Characterization of Amorphous Silica from Corn Cob Ash by Sol-Gel Method.” 3: 6.Chemistry and Materials Research 3 (4): 68–72.
- Otoko, G. R. 2014. “Use of Bagasse Ash as Partial Replacement of Cement in Concrete.” International Journal of Innovative Research and Development 3: 285–289.
- Overney, F., and B. Jeanneret. 2010. “Realization of an Inductance Scale Traceable to the Quantum Hall Effect Using an Automated Synchronous Sampling System.” Metrologia 47: 690–698. doi:10.1088/0026-1394/47/6/008.
- Pal, S. L., U. Jana, P. K. Manna, G. P. Mohanta, and R. Manavalan. 2011. “Nanoparticle: An Overview of Preparation and Characterization.” Journal of Applied Pharmaceutical Science 1: 228–234.
- Panda, A. B., G. Glaspell, and M. S. El-Shall. 2006. “Microwave Synthesis of Highly Aligned Ultra Narrow Semiconductor Rods and Wires.” Journal of the American Chemical Society 128: 2790–2791. doi:10.1021/ja058148b.
- Patel, K. G., R. R. Shettigar, and N. M. Misra. 2017. “Recent Advance in Silica Production Technologies from Agricultural Waste Stream–.” Journal of Advanced Agricultural Technologies (3): 274–79. https://doi.org/10.18178/joaat.4.3.274-279.
- Patra, J. K., and K.-H. Baek. 2015. “Green Nanobiotechnology: Factors Affecting Synthesis and Characterization Techniques.” Journal of Nanomaterials 2014: 219.
- Peng, K.-Q., X. Wang, L. Li, X.-L. Wu, and S.-T. Lee. 2010. High-Performance Silicon Nanohole Solar Cells. Journal of the American Chemical Society 132(20): 6872-73. https://doi.org/10.1021/ja910082y
- Pi, X. D., O. H. Y. Zalloum, A. P. Knights, P. Mascher, and P. J. Simpson. 2006. “Electrical Conduction of Silicon Oxide Containing Silicon Quantum Dots.” Journal of Physics: Condensed Matter 18: 9943–9950. doi:10.1088/0953-8984/18/43/016.
- Polakovič, M., T. Görner, R. Gref, and E. Dellacherie. 1999. “Lidocaine Loaded Biodegradable Nanospheres: II. Modelling of Drug Release.” Journal of Controlled Release 60: 169–177. doi:10.1016/S0168-3659(99)00012-7.
- Powers, D. E., S. G. Hansen, M. E. Geusic, A. C. Puiu, J. B. Hopkins, T. G. Dietz, M. A. Duncan, P. R. R. Langridge-Smith, and R. E. Smalley. 1982. “Supersonic Metal Cluster Beams: Laser Photoionization Studies of Copper Cluster (Cu2).” The Journal of Physical Chemistry 86: 2556–2560. doi:10.1021/j100211a002.
- Prasad, R. 2014. “Nanotechnology in Sustainable Agriculture: Present Concerns and Future Aspects.” African Journal Of Biotechnology 13 (6): 705–713.
- Prevo, B. G., E. W. Hon, and O. D. Velev. 2007. “Assembly and Characterization of Colloid-based Antireflective Coatings on Multicrystalline Silicon Solar Cells.” Journal of Materials Chemistry 17: 791–799. doi:10.1039/B612734G.
- Purnomo, C. W., C. Salim, and H. Hinode. 2012. “Synthesis Of Pure Na–x and Na–a Zeolite from Bagasse Fly Ash.” Microporous and Mesoporous Materials 162: 6–13. doi: 10.1016/j.micromeso.2012.06.007.
- Rafiee, E., S. Shahebrahimi, M. Feyzi, and M. Shaterzadeh. 2012. “Optimization of Synthesis and Characterization of Nanosilica Produced from Rice Husk (A Common Waste Material).” International Nano Letters 2: 29. doi:10.1186/2228-5326-2-29.
- Razykov, T. M., C. S. Ferekides, D. Morel, E. Stefanakos, H. S. Ullal, and H. M. Upadhyaya. 2011. “Solar Photovoltaic Electricity: Current Status and Future Prospects.” Solar Energy 85: 1580–1608. doi:10.1016/j.solener.2010.12.002.
- Ruizendaal, L., S. P. Pujari, V. Gevaerts, J. M. J. Paulusse, and H. Zuilhof. 2011. “Biofunctional Silicon Nanoparticles by Means of Thiol-Ene Click Chemistry.” Chemistry: An Asian Journal 6: 2776–2786. doi:10.1002/asia.201100375.
- Saha, B. C., and M. A. Cotta. 2006. “Ethanol Production from Alkaline Peroxide Pretreated Enzymatically Saccharified Wheat Straw.” Biotechnology Progress 22: 449–453. doi:10.1021/bp050310r.
- Sailor, M. J., and E. C. Wu. 2009. “Photoluminescence-Based Sensing with Porous Silicon Films, Microparticles, and Nanoparticles.” Advanced Functional Materials 19: 3195–3208. doi:10.1002/adfm.v19:20.
- Sales, A., and S. A. Lima. 2010. “Use of Brazilian Sugarcane Bagasse Ash in Concrete as Sand Replacement.” Waste Management 30: 1114–1122. doi:10.1016/j.wasman.2010.01.026.
- Sampaio, P. G. V., and M. O. A. González. 2017. “Photovoltaic Solar Energy: Conceptual Framework.” Renewable and Sustainable Energy Reviews 74: 590–601. doi:10.1016/j.rser.2017.02.081.
- Sato, S., and M. T. Swihart. 2006. “Propionic-Acid-Terminated Silicon Nanoparticles: Synthesis and Optical Characterization.” Chemistry of Materials 18: 4083–4088. doi:10.1021/cm060750t.
- Savant, N. K., G. H. Korndörfer, L. E. Datnoff, and G. H. Snyder. 1999. “Silicon Nutrition and Sugarcane Production: A Review.” Journal of Plant Nutrition 22: 1853–1903. doi:10.1080/01904169909365761.
- Shafeev, G. A., E. Freysz, and F. Bozon-Verduraz. 2004. “Self-influence of a Femtosecond Laser Beam upon Ablation of Ag in Liquids.” Applied Physics A 78: 307–309. doi:10.1007/s00339-003-2357-4.
- Shao, Y., J. Wang, F. Preto, J. Zhu, and C. Xu. 2012. “Ash Deposition in Biomass Combustion or Co-Firing for Power/Heat Generation.” Energies 5: 5171–5189. doi:10.3390/en5125171.
- Shim, J., P. Velmurugan, and B.-T. Oh. 2015. “Extraction and Physical Characterization of Amorphous Silica Made from Corn Cob Ash at Variable pH Conditions via Sol Gel Processing.” Journal of Industrial and Engineering Chemistry 30: 249–253. doi:10.1016/j.jiec.2015.05.029.
- Sopori, B. 2007. National Solar Technology Roadmap: Wafer-silicon PV. Washington, DC, USA: EERE Publication and Product Library.
- Srinivasan, R., and K. Sathiya. 2010. “Experimental Study on Bagasse Ash in Concrete.” The International Journal for Service Learning in Engineering, Humanitarian Engineering and Social Entrepreneurship 5: 60–66.
- Sudeep, P. K., Z. Page, and T. Emrick. 2008. “PEGylated Silicon Nanoparticles : Synthesis and Characterization.” Chemical Communications 6126–6127. doi:10.1039/b813025f.
- Swihart, M. T., and S. L. Girshick. 1999. “Thermochemistry and Kinetics of Silicon Hydride Cluster Formation during Thermal Decomposition of Silane.” The Journal of Physical Chemistry B 103: 64–76. doi:10.1021/jp983358e.
- Tang, Q., and T. Wang. 2005. “Preparation of Silica Aerogel from Rice Hull Ash by Supercritical Carbon Dioxide Drying.” The Journal of Supercritical Fluids 35: 91–94. doi:10.1016/j.supflu.2004.12.003.
- Tao, M. 2008. “Inorganic Photovoltaic Solar Cells: Silicon and beyond.” Electrochemical Society Interface 17 (4): 30–35.
- Teghammar, A., K. Karimi, I. Sárvári Horváth, and M. J. Taherzadeh. 2012. “Enhanced Biogas Production from Rice Straw, Triticale Straw and Softwood Spruce by NMMO Pretreatment.” Biomass & Bioenergy 36: 116–120. doi:10.1016/j.biombioe.2011.10.019.
- Tilley, R. D., J. H. Warner, K. Yamamoto, I. Matsui, and H. Fujimori. 2005. “Micro-emulsion Synthesis of Monodisperse Surface Stabilized Silicon Nanocrystals.” Chemical Communications: 1833–1835. doi:10.1039/b416069j.
- Tilley, R. D., and K. Yamamoto. 2006. “The Microemulsion Synthesis of Hydrophobic and Hydrophilic Silicon Nanocrystals.” Advanced Materials 18: 2053–2056. doi:10.1002/(ISSN)1521-4095.
- Torres Agredo, J., R. Mejía de Gutiérrez, C. E. Escandón Giraldo, and L. O. González Salcedo. 2014. “Characterization of Sugar Cane Bagasse Ash as Supplementary Material for Portland Cement.” Ingeniería e Investigación 34: 5–10. doi:10.15446/ing.investig.v34n1.42787.
- Tuck, C. O., E. Pérez, I. T. Horvath, R. A. Sheldon, and M. Poliakoff. 2012. “Valorization Of Biomass: Deriving More Value from Waste.” Science 337 (6095): 695–99. doi: 10.1126/science.1218930.
- Vaibhav, V., U. Vijayalakshmi, and S. M. Roopan. 2015. “Agricultural Waste as a Source for the Production of Silica Nanoparticles.” Spectrochimica Acta, Part A: Molecular and Biomolecular Spectroscopy 139: 515–520. doi:10.1016/j.saa.2014.12.083.
- van Dijk, L., J. van de Groep, L. W. Veldhuizen, M. Di Vece, A. Polman, and R. E. I. Schropp. 2016. “Plasmonic Scattering Back Reflector for Light Trapping in Flat Nano-Crystalline Silicon Solar Cells.” ACS Photonics 3: 685–691. doi:10.1021/acsphotonics.6b00070.
- Venkateswaran, S., R. Yuvakkumar, and V. Rajendran. 2013. “Nano Silicon from Nano Silica Using Natural Resource (Rha) for Solar Cell Fabrication.” Phosphorus, Sulfur, and Silicon and the Related Elements 188: 1178–1193. doi:10.1080/10426507.2012.740106.
- Venkateswaran, S., R. Yuvakkumar, and V. Rajendran. 2013. “Nano Silicon from Nano Silica Using Natural Resource (Rha) for Solar Cell Fabrication.” Phosphorus, Sulfur, and Silicon and The Related Elements 188 (9): 1178–93. doi: 10.1080/10426507.2012.740106.
- Villar-Cociña, E., E. V. Morales, S. F. Santos, H. Savastano, and M. Frías. 2011. “Pozzolanic Behavior Of Bamboo Leaf Ash: Characterization and Determination Of The Kinetic Parameters.” Cement and Concrete Composites 33 (1): 68–73. doi: 10.1016/j.cemconcomp.2010.09.003.
- VonderHaar, G. 2017. “Efficiency of Solar Cell Design and Materials.” Missouri S&T’s Peer Peer 1: 7.
- Wang, J., S. Sun, F. Peng, L. Cao, and L. Sun. 2011. “Efficient One-pot Synthesis of Highly Photoluminescent Alkyl-functionalised Silicon Nanocrystals.” Chemical Communications 47: 4941–4943. doi:10.1039/c1cc10573f.
- Werther, J., M. Saenger, E.-U. Hartge, T. Ogada, and Z. Siagi. 2000. “Combustion of Agricultural Residues.” Progress in Energy and Combustion Science 26: 1–27. doi:10.1016/S0360-1285(99)00005-2.
- Wilcoxon, J. P., G. A. Samara, and P. N. Provencio. 1999. “Optical and Electronic Properties of Si Nanoclusters Synthesized in Inverse Micelles.” Physical Review B 60: 2704–2714. doi:10.1103/PhysRevB.60.2704.
- Wilson, W. L., P. F. Szajowski, and L. E. Brus. 1993. “Quantum Confinement in Size-Selected, Surface-Oxidized Silicon Nanocrystals.” Science 262: 1242–1244. doi:10.1126/science.262.5137.1242.
- Won, C. W., H. H. Nersisyan, and H. I. Won. 2011. “Solar-grade Silicon Powder Prepared by Combining Combustion Synthesis with Hydrometallurgy.” Solar Energy Materials and Solar Cells 95: 745–750. doi:10.1016/j.solmat.2010.10.016.
- Xakalashe, B. S., and M. Tangstad. 2012. “Silicon Processing: From Quartz to Crystalline Silicon Solar Cells.” Chemical Technology March: 6–9.
- Yadav, P., and S. R. Samadder. 2018. “A Critical Review of the Life Cycle Assessment Studies on Solid Waste Management in Asian Countries.” Journal of Cleaner Production 185: 492–515. doi:10.1016/j.jclepro.2018.02.298.
- Yang, X., W. Ma, G. Lv, K. Wei, T. Luo, and D. Chen. 2014. “A Modified Vacuum Directional Solidification System of Multicrystalline Silicon Based on Optimizing for Heat Transfer.” Journal of Crystal Growth 400: 7–14. doi:10.1016/j.jcrysgro.2014.04.025.
- YaNing, Z., A. E. Ghaly, and L. BingXi. 2012. “Physical Properties of Rice Residues as Affected by Variety and Climatic and Cultivation Conditions in Three Continents.” American Journal of Applied Sciences 9: 1757–1768. doi:10.3844/ajassp.2012.1757.1768.
- Yao, X., H. Zhou, K. Xu, Q. Xu, and L. Li. 2019. “Evaluation of the Fusion and Agglomeration Properties of Ashes from Combustion of Biomass, Coal and Their Mixtures and the Effects of K2co3 Additives.” Fuel 255: 115829. doi:10.1016/j.fuel.2019.115829.
- Yao, X., H. Zhou, K. Xu, Q. Xu, and L. Li. 2020. “Investigation on the Fusion Characterization and Melting Kinetics of Ashes from Co-Firing of Anthracite and Pine Sawdust.” Renewable Energy 145: 835–846. doi:10.1016/j.renene.2019.06.087.
- Yermekova, Z., Z. Mansurov, and A. S. Mukasyan. 2010. “Combustion Synthesis of Silicon Nanopowders.” International Journal of Self-Propagating High-Temperature Synthesis 19: 94–101. doi:10.3103/S1061386210020032.
- Yoshida, T., S. Takeyama, Y. Yamada, and K. Mutoh. 1996. “Nanometer‐sized Silicon Crystallites Prepared by Excimer Laser Ablation in Constant Pressure Inert Gas.” Applied Physics Letters 68: 1772–1774. doi:10.1063/1.116662.
- Yoshikawa, K., H. Kawasaki, W. Yoshida, T. Irie, K. Konishi, K. Nakano, T. Uto, et al. 2017. “Silicon Heterojunction Solar Cell with Interdigitated Back Contacts for a Photoconversion Efficiency over 26%.” Nature Energy 2: 17032. doi:10.1038/nenergy.2017.32.
- Zamani, A., A. P. Marjani, and Z. Mousavi. 2019. “Agricultural Waste Biomass-Assisted Nanostructures: Synthesis and Application.” Green Processing and Synthesis 8: 421–429. doi:10.1515/gps-2019-0010.
- Zemnukhova, L. A., T. A. Babushkina, T. P. Klimova, A. M. Ziatdinov, and A. N. Kholomeiydik. 2012. “Structural Features of Amorphous Silica from Plants.” Applied Magnetic Resonance 42: 577–584. doi:10.1007/s00723-012-0332-y.
- Zhang, L., C. C. Xu, and P. Champagne. 2010. “Overview of Recent Advances in Thermo-chemical Conversion of Biomass.” Energy Conversion and Management 51: 969–982. doi:10.1016/j.enconman.2009.11.038.
- Zhang, X., D. Neiner, S. Wang, A. Y. Louie, and S. M. Kauzlarich. 2007a. “A New Solution Route to Hydrogen-terminated Silicon Nanoparticles: Synthesis, Functionalization and Water Stability.” Nanotechnology 18: 095601. doi:10.1088/0957-4484/18/9/095601.
- Zhang, X., M. Brynda, R. D. Britt, E. C. Carroll, D. S. Larsen, A. Y. Louie, and S. M. Kauzlarich. 2007b. “Synthesis and Characterization of Manganese-Doped Silicon Nanoparticles: Bifunctional Paramagnetic-Optical Nanomaterial.” Journal of the American Chemical Society 129: 10668–10669. doi:10.1021/ja074144q.
- Zhu, X. P., T. Yukawa, T. Kishi, M. Hirai, H. Suematsu, W. Jiang, and K. Yatsui. 2005. “Synthesis of Light-emitting Silicon Nanoparticles by Intense Pulsed Ion-beam Evaporation.” Journal of Nanoparticle Research 7: 669–673.
- Zong, L., B. Zhu, Z. Lu, Y. Tan, Y. Jin, N. Liu, Y. Hu, S. Gu, J. Zhu, and Y. Cui. 2015. “Nanopurification of Silicon from 84% to 99.999% Purity with a Simple and Scalable Process.” Proceedings of the National Academy of Sciences 112: 13473–13477. doi:10.1073/pnas.1513012112.
- Zou, J., P. Sanelle, K. A. Pettigrew, and S. M. Kauzlarich. 2006. “Size and Spectroscopy of Silicon Nanoparticles Prepared via Reduction of SiCl4.” Journal of Cluster Science 17: 565–578. doi:10.1007/s10876-006-0082-9.