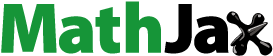
ABSTRACT
Ceramsites have been prepared from iron ore tailings and sludge by controlling the content of the iron ore tailings and sludge, and calcination parameters. Effect of the sintering temperature, duration time and content of the iron ore tailings on the physical properties of the ceramsites have been analysed by X-ray diffraction (XRD) and scanning electron microscopy (SEM). The optimal component of tailings/sludge ceramsites is as follows: Iron ore tailings 90 wt.%, sludge 10 wt.%. The optimal sintering parameters of the ceramsites are 1100°C for 30 min. The cylinder compressive strength of the obtained ceramsites is 10.1 MPa. XRD analysis shows that the ceramsites are composed of CaSiO3, Al2SiO5, MgSiO3, Ca7Si2P2O16, CaAl2Si2O8 and Ca2Fe2O5 phases. SEM observations show that the ceramsites consist of pore structure with a size of less than 50 μm. The volume of the ceramsites shrinks and the density increases, which remarkably increase the cylinder compressive strength with increasing the sintering temperature and duration time.
1 Introduction
Rich mineral resources exist in China which promotes the industrial and social development. Tailings are produced as solid waste during the mineral treatment process and discharged into the soil after crushing. They are secondary resources containing trace minerals, which leads to the complex symbiotic relationship in the form of fine particles and particulate inclusions (Wang et al. Citation2014). The reaction of the sulphide, phosphide and water exposed to the air during the tailings accumulation is the main acid-producing process, which makes the water acidified and eutrophic (Liu, Liu, and Li Citation2011; Choi et al. Citation2009). Tailings can not only cause serious environmental pollution and ecological problems but also bring about industrial accidents and casualties. Therefore, it is an important significance to deal with the tailings for the assurance of the environmental safety and human health (Yue and Chen Citation2013; Yi et al. Citation2009; Li et al. Citation2010).
The tailings contain some extractable metal components and a large number of available silicates and carbonates, which can be used as the raw materials to produce various building materials (Ma et al. Citation2016; Alcalde, Kelm, and Vergara Citation2018; Sang et al. Citation2016). As the construction sand, fine tailing cement is usually used for the underground filling and solidification of dry heap. Tailings are commonly re-selected for recovery of beneficial elements and used as the padding materials and soil amendment (Chen et al. Citation2011; Wang et al. Citation2018; Yang et al. Citation2014). In recent years, various kinds of tailing building materials, such as tailing bricks, tailing ceramsites, tailing ceramics and tailing concrete blocks have been widely investigated exhibiting great application prospect in the construction field (Kim et al. Citation2019; Kinnunen, Ismailov, and Solismaa Citation2018; Zhu et al. Citation2017; Li et al. Citation2017; Ahmari and Zhang Citation2013; Liu et al. Citation2016a).
Ceramsite is a kind of ceramic spheres prepared by the spheronization and calcination of silicate-based raw materials, such as clay and feldspar (Yang et al. Citation2017). Ceramsites have the characteristics of high cylinder compressive strength, low density and good water absorption, which is widely used in the field of flower cultivation and water treatment (Delgado et al. Citation2014). Ceramists, a sort of light aggregate, can partly replace sand and stone to make concrete with the performance of light weight and good adsorption capacity for widely used in architecture field (Cheng et al. Citation2018; Zou and Liu Citation2013). Making use of the tailings, the cost of the products can be significantly decreased and the accumulation of the tailings can be avoided, which is beneficial for the society and environmental safety (He et al. Citation2015).
Sludge is a kind of industrial byproducts with a high organic content and adsorption capacity (Zou and Li Citation2008; Liu et al. Citation2016b). High content of SiO2 and Al2O3 in the sludge makes them suitable as the ceramic skeleton components. The gas, such as H2O, O2, CO2 and SO2 can be generated by the oxidation reaction process (Sun et al. Citation2017; Li, Luo, and Jin Citation2013; Liu et al. Citation2013). Building blocks, cement, concrete and bioplastics have been reported showing good application promising in the fields of construction and plastics industry (Sharma and Joshi Citation2016; Singhal, Tewari, and Prakash Citation2008; Khardenavis et al. Citation2009; Modolo et al. Citation2011; Soucy et al. Citation2014). The high-temperature calcination of the sludge and tailings is a promising method to improve the performance of the ceramsites (Xu, Zou, and Dai Citation2006). Iron ore tailing and sludge ceramsites take the advantages of the products, such as increasing mechanical strength by the component fixation, removal of contaminants by high-temperature organic decomposition and gasification, and stabilisation of harmful metals by the incorporation of phases (Tang, Chan, and Shih Citation2014; Sonowal, Khwairakpam, and Kalamdhad Citation2014; He and Wang Citation2011; Wang et al. Citation2016). In the work, iron ore tailing/sludge ceramsites have been obtained using the iron ore tailings and sludge as the raw materials. The roles of the tailing content and sintering parameters on the performance of the ceramsites have been analysed in detail. The optimal tailing content, sintering temperature and duration time have been determined. The formation of the ceramsites has been investigated by X-ray diffraction (XRD) and scanning electron microscopy (SEM).
2 Experimental
2.1. Raw materials
Iron ore tailings and sludge were used as the raw materials to prepare tailing ceramsites. Iron ore tailings were obtained from Ma’anshan Gushan Mining Co., Ltd of P. R. China. Sludge was obtained from Ma’anshan sewage treatment company. The main composition and content of the raw materials is shown in . The loss on ignition (LOI) value of iron ore tailings and sludge is 10.08 wt.% and 26.28 wt.%, respectively. The particle size distribution of iron ore tailings and sludge is listed in . The maximum size of the 90 wt.% iron ore tailing and 90 wt.% sludge powder are 35.6 μm and 278.4 μm, respectively. The mass percentage of the iron ore tailing and sludge powder with the size of less than 100 μm is 99.9% and 54.8%, respectively.
Table 1. Main composition and content of the raw materials (wt.%)
Table 2. The particle size distribution of the raw materials
2.2. Preparation process of the ceramsites
The water content for the iron ore tailings and sludge raw materials was 40 wt.%. The solid content of the sludge was 27 wt.%. The mass ratio of the tailings in the raw materials for the ceramsites was 80–95%, and the mass ratio of the sludge was 5–20% which was determined on dry basis. lists the ceramists proportioning of the iron ore tailings and dry sludge. The typical preparation process of the ceramsites was as follows: The iron ore tailings and sludge with definite mass ratio were mixed and stirred for 15 min. Then, the water was added into the mixed powder and stirred for 15 min. The mixture was made into raw balls with the diameter of 10–20 mm using 3200 balling machine (Zhengzhou Zhonghou mechanical equipment Co., Ltd.) and placed in drying box and dried at 100°C for 12 h. The dried raw pellets were placed into an SRJX-10-13A furnace (Shanghai SuoYu Test Equipment Co., Ltd.) and calcined at 500°C for 20 min, then heated to 700–1100°C for 10–40 min. The heating rate was 5°C/min, and naturally cooled to room temperature. Finally, the ceramsites were obtained. The effects of the tailing content, sintering temperature and duration time on the properties of the tailing ceramsites were studied in order to determine the optimal sintering parameters.
Table 3. Ceramists proportioning of the iron ore tailings and dry sludge
2.3. Characterisation methods
To analyse the composition of the raw materials, the composition of the tailings and sludge was measured at room temperature by an X-ray fluorescence spectrometer (XRF). XRF spectra of the samples were obtained using ARL Advant’X Intellipower 3600 XRF spectrometer from Thermo Fisher Scientific, Inc. The phases of the raw materials and obtained ceramsites were analysed by a Bruker AXS D8 X-ray diffractometer with a graphite-monochromatized Cu-Kα radiation. The samples were scanned at the 2θ range of 20–80° with a scan rate of 0.05 °s−1. The tailing ceramsites were broken into 5 mm samples and placed on the surface of the conductive adhesive. Gold film was sprayed before SEM observation to increase the conductivity of the samples. SEM observation was performed using a nova nanoSEM FEI 430 SEM with a 15 kV accelerating voltage.
Stacking density referred to the unit volume mass measured by filling the bulk materials in a container freely. Apparent density referred to the ratio of the material mass to the apparent volume. Based on the stacking density and apparent density, the air void could be determined. Water absorption reflected to the density and cylinder compressive strength of the ceramsites. Cylinder compressive strength is the key parameter of the tailing ceramsites. The stacking density, apparent density, water absorption and cylinder compressive strength were determined by the standard of CNS (1998) GB/T 17431.2: Light aggregate and experimental methods, No. 2 part: Experimental methods of the light aggregate, Standard of P. R. China.
3 Results and discussion
The sludge is a complex heterogeneous substance composed of organic matter, bacterial cells, inorganic particles and colloidal substance (Wang et al. Citation2019). The main characteristics of the sludge are high water content, high organic matter content, easy to rot, low density and gelatinous liquid. High organic content of the sludge can promote the calcination of the ceramsites (Dong et al. Citation2013; Asakura et al. Citation2009). Therefore, sludge was added into the iron ore tailings to prepare ceramsites. The optimal tailing content, sintering temperature and duration time of the ceramsites were determined.
3.1. Effect of the tailing content on the properties of the ceramsites
The tailing content was controlled to be 95 wt.%, 90 wt.%, 85 wt.% and 80 wt.%, respectively. The sintering temperature and duration time were 1100°C and 30 min, respectively.
lists the stacking density, apparent density, air void and water absorption of the ceramsites obtained from 1100°C for 30 min. Seen from , the stacking density, apparent density and air void decrease from 1067.63 kg·m−3, 2163.10 kg·m−3, 50.64% to 1002.42 kg·m−3, 1776.02 kg·m−3, 43.56%, respectively, with the tailing content decreasing from 95 wt.% to 80 wt.%. And the water absorption of the ceramsites increases from 7.30% to 12.34%, respectively. Some organic substances exist in the sludge. The content of the organic substances increases with the increase of the sludge content. A large amount of pores exist in the ceramsites owing to the gasification of the organic substance in the sludge. The water absorption of the ceramsites increases obviously as the increase of the sludge content from 5 wt.% to 20%.
Table 4. Stacking density, apparent density, air void and water absorption of the ceramsites obtained from 1100°C for 30 min
shows that the cylinder compressive strength of the ceramsites increases from 4.9 MPa to 10.8 MPa with the tailing content increasing from 80 wt.% to 95 wt.%. The cylinder compressive strength of the ceramsites is 10.1 MPa and 10.8 MPa, respectively, which is similar when the tailing content is 90 wt.% and 95 wt.%. When the tailing content is 90 wt.%, the stacking density and apparent density of the obtained ceramsites are obviously lower than those of 95 wt.%. The results show that the density of the ceramsites is also decreased with decreasing the tailing content. Therefore, the optimal components of the raw materials are as follows: 90 wt.% tailing, 10 wt.% sludge.
3.2. Effect of the duration time on the properties of the ceramsites
The duration time was selected as 10 min, 20 min, 30 min and 40 min, respectively. The sintering temperature was adapted as 1100°C. The effect of the duration time on the properties of ceramsites was investigated and the optimal duration time was determined.
lists the stacking density, apparent density, air void and water absorption of the ceramsites obtained from 1100°C for different duration time. From , it is observed that when the duration time increases from 10 min to 40 min, the stacking density and apparent density increase from 878.99 kg·m−3, 1717.58 kg·m−3 to 1089.67 kg·m−3, 2056.66 kg·m−3, respectively. The air void and water absorption decrease from 48.82%, 9.81% to 46.99%, 7.17%, respectively. As the duration time increases, the sintering of the ceramsites is more sufficient resulting in the increase of the density, decreasing the air void and water absorption of the ceramsites. However, as the duration time increases to 40 min, a large amount of pores are produced in the ceramsites owing to the continuous sintering of the cerasmsites. The amount of the pores in the ceramsites increases resulting in the decrease of the density of the ceramsites.
Table 5. Stacking density, apparent density, air void and water absorption of the ceramsites obtained from 1100°C for different duration time
It can be seen from , the cylinder compressive strength of the ceramsites increases from 3.4 MPa to 10.6 MPa with the increase of duration time at 1100°C. When the duration time is 40 min, the ceramsites have the highest cylinder compressive strength. When the duration time is 30 min and 40 min, the cylinder compressive strength of the obtained ceramsites is 10.1 MPa and 10.8 MPa, respectively, which is similar. Considering the preparation cost, it can be determined that the optimal duration time of the ceramsites at 1100°C is 30 min. The cylinder compressive strength of the ceramsites obtained at 1100°C for 30 min is 10.1 MPa, and the stacking density is 1036.57 kg·m−3.
Figure 2. Relationship curve between the duration time and cylinder compressive strength of the ceramsites obtained from 1100°C for different duration time
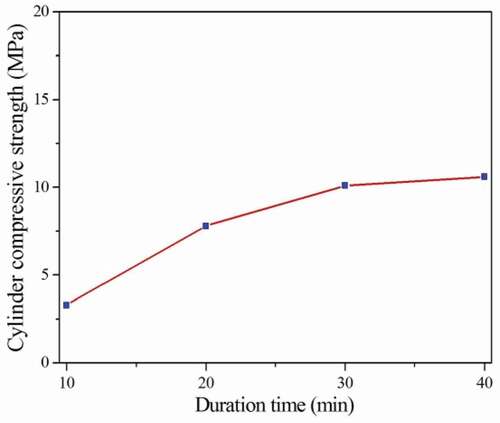
shows the XRD patterns of the ceramsites obtained from 1100°C for different duration times. Seen from , Al2O3, CaCO3 and MgO phases disappear from the ceramsites obtained from 1100°C for 10 min. SiO2, Fe2O3 and Ca3(PO4)2 phases still exist in the ceramsites. The ceramsites mainly consists of monoclinic CaSiO3 (JCPDS card, PDF 27–0088), triclinic Al2SiO5 (JCPDS card, PDF 11–0046), triclinic MgSiO3 (JCPDS card, PDF 18–0778), orthorhombic Ca2Fe2O5 (JCPDS card, PDF 38–0408), hexagonal Ca7Si2P2O16 (JCPDS card, PDF 11–0676) and triclinic CaAl2Si2O8 (JCPDS card, PDF 41–1486). As the duration time increases to 30 min, some diffraction peaks of SiO2, Fe2O3 and Ca3(PO4)2 phases disappear (2θ = 53.48°, 68.38°), and the intensities of other diffraction peaks are remarkably increased (2θ = 21.03°, 42.59°), which is caused by the formation of silicate phases. The intensities of some diffraction peaks decrease, such as 2θ = 36.54°, 62.17° which is caused by the disappearance of SiO2, Fe2O3 and Ca3(PO4)2, and the formation of various species of silicate and ferrite phases. Therefore, as the duration time increases to 30 min, the reaction is relatively complete. The ceramsites are mainly composed of CaSiO3, Al2SiO5, MgSiO3, Ca7Si2P2O16, CaAl2Si2O8 and Ca2Fe2O5 phases. The formation of these phases induces the densification of the ceramsites resulting in the increase of the cylinder compressive strength from 3.4 MPa to 10.6 MPa as the duration time increasing from 10 min to 30 min at 1100°C.
Figure 3. XRD patterns of the ceramsites obtained from 1100°C for different duration time. (a) 10 min, (b) 30 min
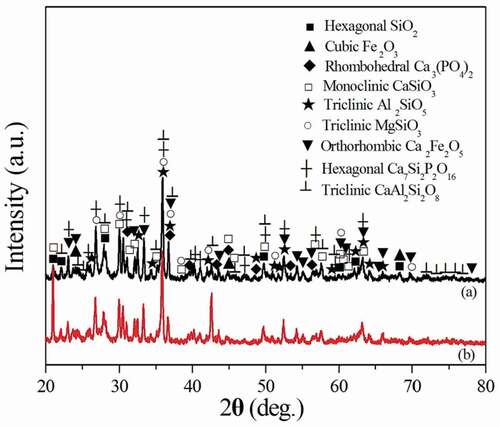
shows SEM images with different magnifications of the ceramsites obtained from 1100°C for different duration time. Seen from , the ceramsites consist of microscale irregular particles with a size of less than 100 μm. Some sub-microscale particles with a size of less than 1 μm also exist in the ceramsites. The irregular particles are loosely dispersed in the ceramsites, and a large amount of pores with the microscale size also exist in the ceramsites. The pores are formed by the gasification of the organic matter at high temperature. When the duration time increases to 30 min at 1100°C, the ceramsites are composed of microscale and sub-microscale particles. Although some pores with the size of less than 50 μm, no loose particles exist in the ceramsites. The density of the ceramsites is significantly improved indicating the formation of ceramsites with high density due to the complete high-temperature solid-phase reaction. According to the XRD diffraction patterns of the ceramsites obtained from 1100°C for different duration time, it is known that CaSiO3, Al2SiO5, MgSiO3, Ca7Si2P2O16, CaAl2Si2O8 and Ca2Fe2O5 phases are formed. The high-temperature solid reaction induces the increase of the relative density of the ceramsites leading to the increase of the cylinder compressive strength of the ceramsites with increasing the duration time.
3.3. Effect of the sintering temperature on the properties of the ceramsites
The sintering temperature was controlled to be 700°C, 800°C, 900°C, 1000°C and 1100°C, respectively, to determine the optimal calcination temperature. The duration time was 30 min.
lists the stacking density, apparent density, air void and water absorption of the ceramsites obtained from different temperatures for 30 min. As seen from , at the sintering temperature of below 1000°C, the stacking density and apparent density are below 760.72 kg·m−3 and 1460.48 kg·m−3. The cylinder compressive strength is less than 1.9 MPa. The water absorption is higher than 25.96%. The ceramsites obtained from below 1000°C have low density, low cylinder compressive strength and high water absorption. The results are caused by the organic matter and low density of the sludge, which has high reaction activity during the calcination process. shows the relationship curve between the sintering temperature and cylinder compressive strength of the ceramsites obtained from different sintering temperatures for 30 min. As the sintering temperature increases to 1100°C, the stacking density, apparent density and cylinder compressive strength increase obviously, reaching 1089.67 kg·m−3, 2056.66 kg·m−3and 10.1 MPa, respectively. And the water absorption of the ceramsites decreases to 8.52%. It can be concluded that the volume of the ceramsites shrinks, the density and cylinder compressive strength increase obviously due to the complete reaction of the compounds in the ceramsites. The optimal sintering parameters of the ceramsites are 1100°C for 30 min.
Table 6. Stacking density, apparent density, air void and water absorption of the ceramsites obtained from different temperatures for 30 min
Figure 5. Relationship curve between the sintering temperature and cylinder compressive strength of the ceramsites obtained from different sintering temperatures for 30 min
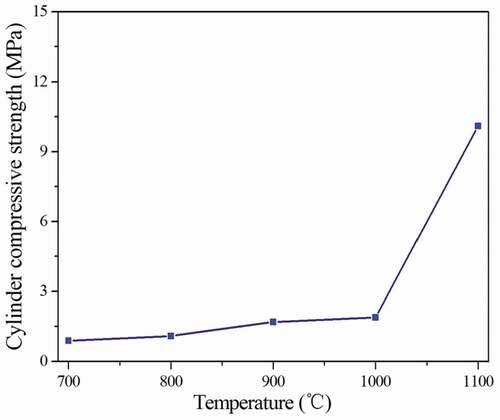
shows the XRD patterns of the tailing powder and ceramsites obtained from different temperatures for 30 min. It is observed that the raw material tailing powder is composed of SiO2, Fe2O3, Al2O3, Ca3(PO4)2, CaCO3 and MgO ()). The ceramsites are composed of CaSiO3, Al2SiO5, MgSiO3, Ca2Fe2O5, Ca7Si2P2O16 and CaAl2Si2O8 phases when the ceramsites are obtained from 700°C ()). As the sintering temperature increases to 900°C, the intensities of the diffraction peaks of the CaSiO3, Al2SiO5, MgSiO3, Ca2Fe2O5, Ca7Si2P2O16 and CaAl2Si2O8 phases increase ()). However, the intensities of the diffraction peaks of SiO2 (2θ = 27.37°, 42.47°), Fe2O3 (2θ = 75.35°), Al2O3 (2θ = 21.91°), Ca3(PO4)2 (2θ = 28.55°, 30.84° and 39.76°), CaCO3 (2θ = 24.95°, 29.39°) and MgO (2θ = 24.95°, 29.39°) decrease, even the diffraction peaks disappear. High temperature induces the reaction of the compounds in the ceramsites and densification of the ceramsites. As the sintering temperature increases to 1100°C, the solid reaction in the ceramsites is complete. The formation of the CaSiO3, Al2SiO5, MgSiO3, Ca7Si2P2O16, CaAl2Si2O8 and Ca2Fe2O5 phases and high relative density of the ceramsites result in the sharp increase of the cylinder compressive strength of the ceramsites with increasing the sintering temperature from 700°C to 1100°C.
Figure 6. XRD patterns of the tailing powder and the ceramsites obtained from different temperatures for 30 min. (a) Tailing powder, (b) 700°C, (c) 900°C
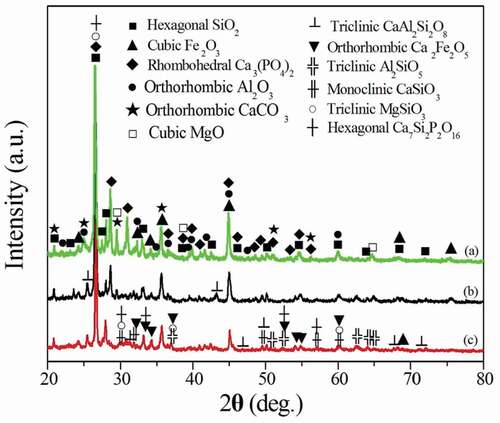
shows the SEM images of the ceramsites obtained from different temperatures for 30 min. The ceramsites are composed of loose irregular particles with microscale size when the sintering temperature is 700°C () and 800°C (), respectively. A large amount of pores also exist in the ceramsites. Therefore, the cylinder compressive strength of the ceramsites is low with the value of 0.9 MPa and 1.1 MPa, respectively, when the sintering temperature is 700°C and 800°C. The SEM images obtained at 700°C and 800°C show little difference. However, as the sintering temperature increases to 900°C () and 1000°C (), the ceramsites still contain irregular particles with the microscale size. The amount of the pores is decreased and the relative density of the ceramsites is improved owing to high-temperature solid densification reaction. Dense irregular particles with the size of several hundred micrometres exist in the ceramsites besides the irregular particles with less than 10 μm. Therefore, the density of the ceramsites is significantly increased. The water absorption decreases, and the cylinder compressive strength increases to 1.5 MPa and 1.9 MPa at 900°C and 1000°C, respectively. The ceramsites react completely when the sintering temperature is 1100°C leading to the increase of the cylinder compressive strength to 10.1 MPa.
3.4. Formation process of the tailing ceramsites
The formation process of the tailing ceramsites can be divided into three processes as follows: The preheating stage, heating stage and sintering stage. From room temperature to 500°C, the preheating stage mainly contains the volatilisation of water, the gathering of solid particles, the shrink of raw material balls, and the increase of the porosity (Wang et al. Citation2013; Lin, Lee, and Hwang Citation2015).
According to , it is known that the sludge and tailing have high LOI value of 26.28% and 10.08%, respectively. The organic matter, CaCO3 and other compounds in the ceramsites undergo the gasification, oxidation and decomposition reaction. At relatively low temperature, such as 600°C, the generated gas escapes to make the ceramsites form a large amount of pores. During the heating period from 500°C to 1100°C, complex chemical reactions occur in the ceramsites as follows:
SiO2 reacts with high-temperature solid phase of CaO, Al2O3, MgO and Ca3(PO4)2 to form CaSiO3, Al2SiO5, MgSiO3, Ca7Si2P2O16 and CaAl2Si2O8. FeO reacts with CaO to form Ca2Fe2O5. High temperature induces the reaction of the compounds in the ceramsites and densification of the ceramsites. As the sintering temperature and duration time increase to 1100°C and 30 min, respectively, the solid reaction in the ceramsites is complete, the shrinkage of the ceramsites increases. The amount of the pores is decreased and the relative density of the ceramsites is improved owing to high-temperature solid densification reaction. Dense irregular particles with the size of several hundred micrometres exist in the ceramsites besides the irregular particles with less than 10 μm. The high-temperature sintering process results in a decrease in the porosity, and an increase in the density and cylinder compressive strength of the ceramsites.
4. Conclusions
In summary, tailing ceramsites have been prepared from iron ore tailings and sludge by the sintering process. The optimal components of the ceramsites are tailing 90 wt.%, sludge 10 wt.%. Stacking density, apparent density and cylinder compressive strength of the ceramsites obtained from 1100°C for 30 min are 1036.57 kg·m−3, 1973.01 kg·m−3 and 10.1 MPa, respectively. The optimal sintering parameters of the ceramsites are 1100°C for 30 min. The obtained ceramsites are mainly composed of CaSiO3, Al2SiO5, MgSiO3, Ca7Si2P2O16, CaAl2Si2O8 and Ca2Fe2O5 phases. The irregular particles are loosely dispersed in the ceramsites, and a large amount of pores with the microscale size exist in the ceramsites when the sintering temperature is lower than 900°C for 10 min. With increasing the sintering temperature and duration time to 1100°C for 30 min, the ceramsites are composed of microscale and sub-microscale particles. Dense irregular large particles with the size of several hundred micrometres exist in the ceramsites besides the irregular particles with the size of less than 10 μm leading to the increase of the cylinder compressive strength of the ceramsites.
Disclosure Statement
No potential conflict of interest was reported by the authors.
Additional information
Funding
Notes on contributors
Z. Wang
Z. Wang has been a postgraduate of College of Materials Science and Engineering, Anhui University of Technology of P. R. China since 2018. He obtained his Bachelor degree from Nanjing University of Technology, P. R. China in 2018. His main research interest is solid waste utilization.
H. J. Chen
H. J. Chen has been a postgraduate of College of Materials Science and Engineering, Anhui University of Technology of P. R. China since 2018. He obtained his Bachelor degree from Huaibei Normal University, P. R. China in 2018. His main research interest is solid waste utilization.
L. Z. Pei
L. Z. Pei has been a professor of College of Materials Science and Engineering, Anhui University of Technology of P. R. China since 2011. He obtained his Ph.D. from Hunan University, P. R. China in 2006 and joined College of Materials Science and Engineering, Anhui University of Technology of P. R. China. His main research interests are solid waste utilization, low-dimensional nanoscale materials, passivation solution and paint. He has published more than 80 papers, reviews and communications in the international journal, such as J. Mater. Chem. A, CrystEngComm,J. Electrochem. Soc., Electrochim. Acta, Phys. Rev. Lett. and Mater. Charact. And he has also more than 10 China patents.
X. Y. Guo
X. Y. Guo has been a postgraduate of College of Materials Science and Engineering, Anhui University of Technology of P. R. China since 2017. He obtained his Bachelor degree from Anhui University of Technology, P. R. China in 2017. His main research interest is solid waste utilization.
C. G. Fan
C. G. Fan has been a professor of College of Materials Science and Engineering, Anhui University of Technology of P. R. China since 2009. He obtained his Ph.D. from University of Science and Technology of China in 2003 and joined College of Materials Science and Engineering, Anhui University of Technology of P. R. China. His main research interests are solid waste utilization and functional ceramics materials. He has published more than 30 papers the international journal, such as Sep. Purif. Technol., J. Membr. Sci.and J. Fuel. Cell Sci. Technol. And he has also more than 20 China patents.
References
- Ahmari, S., and L. Y. Zhang. 2013. “Durability and Leaching Behavior of Mine Tailings-based Geopolymer Bricks.” Construction and Building Materials 44: 743–750. doi:https://doi.org/10.1016/j.conbuildmat.2013.03.075.
- Alcalde, J., U. Kelm, and D. Vergara. 2018. “Historical Assessment of Metal Recovery Potential from Old Mine Tailings: A Study Case for Porphyry Copper Tailings, Chile.” Minerals Engineering 127: 334–338. doi:https://doi.org/10.1016/j.mineng.2018.04.022.
- Asakura, H., K. Endo, M. Yamada, Y. Inoue, and Y. Ono. 2009. “Improvement of Permeability of Waste Sludge by Mixing with Slag or Construction and Demolition Waste.” Waste Management 29 (6): 1877–1884. doi:https://doi.org/10.1016/j.wasman.2008.12.019.
- Chen, Y. L., Y. M. Zhang, T. J. Chen, Y. L. Zhao, and S. X. Bao. 2011. “Preparation of Eco-friendly Construction Bricks from Hematite Tailings.” Construction and Building Materials 25: 2107–2111. doi:https://doi.org/10.1016/j.conbuildmat.2010.11.025.
- Cheng, G., Q. H. Li, Z. Su, S. Sheng, and J. Fu. 2018. “Preparation, Optimization, and Application of Sustainable Ceramsites Substrate from Coal Fly Ash/waterworks Sludge/oyster Shell for Phosphorus Immobilization in Constructed Wetlands.” Journal of Cleaner Production 175: 572–581. doi:https://doi.org/10.1016/j.jclepro.2017.12.102.
- Choi, Y. W., Y. J. Kim, O. Choi, K. M. Lee, and M. Lachemi. 2009. “Utilization of Tailings from Tungsten Mine Waste as a Substitution Material for Cement.” Construction and Building Materials 23 (7): 2481–2486. doi:https://doi.org/10.1016/j.conbuildmat.2009.02.006.
- Delgado, J. A., L. M. Alonso, J. Nacimento, K. P. Macedo, A. Antunes, M. Varella, … M. García-Vallès. 2014. “Sintering Behavior of Nanostructured Hydroxyapatite Ceramics.” Key Engineering Materials 631: 207–211.
- Dong, B., X. G. Liu, L. L. Dai, and X. H. Dai. 2013. “Changes of Heavy Metal Speciation during High-solid Anaerobic Digestion of Sewage Sludge.” Bioresource Technology 131: 152–158. doi:https://doi.org/10.1016/j.biortech.2012.12.112.
- He, H. T., P. Zhao, Q. Y. Yue, B. Y. Gao, D. T. Yue, and Q. Li. 2015. “A Novel Polynary Fatty Acid/sludge Ceramsites Composite Phase Change Materials and Its Applications in Building Energy Conservation.” Renewable Energy 76: 45–52. doi:https://doi.org/10.1016/j.renene.2014.11.001.
- He, J., and Q. S. Wang. 2011. “Technology Research on Waterworks Sludge for Ceramsites.” Advanced Materials Research 383–390: 3352–3355.
- Khardenavis, A. A., A. N. Vaidya, M. S. Kumar, and T. Chakrabarti. 2009. “Utilization of Molasses Spentwash for Production of Bioplastics by Waste Activated Sludge.” Waste Management 29 (9): 2558–2565. doi:https://doi.org/10.1016/j.wasman.2009.04.008.
- Kim, Y., Y. Lee, M. Kim, and P. Hyunsik. 2019. “Preparation of High Porosity Bricks by Utilizing Red Mud and Mine Tailing.” Journal of Cleaner Production 207: 490–497. doi:https://doi.org/10.1016/j.jclepro.2018.10.044.
- Kinnunen, P., A. Ismailov, and S. Solismaa. 2018. “Recycling Mine Tailings in Chemically Bonded ceramics-A Review.” Journal of Cleaner Production 174 (3): 634–649. doi:https://doi.org/10.1016/j.jclepro.2017.10.280.
- Li, C., H. H. Sun, Z. L. Yi, and L. T. Li. 2010. “Innovative Methodology for Comprehensive Utilization of Iron Ore Tailings: Part 2: The Residues after Iron Recovery from Iron Ore Tailings to Prepare Cementitious Material.” Journal of Hazardous Materials 174 (1–3): 78–83. doi:https://doi.org/10.1016/j.jhazmat.2009.09.019.
- Li, C., Q. J. Wen, M. Z. Hong, Z. Y. Liang, Z. Y. Zhuang, and Y. Yu. 2017. “Heavy Metals Leaching in Bricks Made from Lead and Zinc Mine Tailings with Varied Chemical Components.” Construction and Building Materials 134 (12): 443–451. doi:https://doi.org/10.1016/j.conbuildmat.2016.12.076.
- Li, W. F., X. Y. Luo, and X. L. Jin. 2013. “Effect of Acoustic Components on Characteristics of Ceramsites Porous Concrete.” Journal of Building Materials 16 (1): 70–75.
- Lin, K. L., T. C. Lee, and C. L. Hwang. 2015. “Effects of Sintering Temperature on the Characteristics of Solar Panel Waste Glass in the Production of Ceramic Tiles.” Journal of Material Cycles and Waste Managemen 17 (1): 194–200. doi:https://doi.org/10.1007/s10163-014-0240-3.
- Liu, S. J., H. Li, H. J. Liu, J. B. Chen, and F. Q. Zhao. 2013. “Preparation of a New Polymer-modified Adhesive Mortar Using Fine Iron Tailings as Aggregate.” Journal of Adhesion Science and Technology 27 (9): 951–962. doi:https://doi.org/10.1080/01694243.2012.727167.
- Liu, T. Y., Y. Tang, L. Han, J. Song, Z. W. Luo, and A. X. Lu. 2016a. “Recycling of Harmful Waste Lead-zinc Mine Tailings and Fly Ash for Preparation of Inorganic Porous Ceramics.” Ceramics International 43 (6): 4910–4918. doi:https://doi.org/10.1016/j.ceramint.2016.12.142.
- Liu, X., L. Huang, K. L. Guo, X. L. Zhang, H. M. Jiang, and J. F. Zhang. 2016b. “Effect on the Quality of Sandy Fluvo-aquic Soil by Application of Non-hazardous Sewage Sludge with Molybdenum Tailings.” Journal of Agro-Environment Science 35 (12): 2385–2396.
- Liu, Y. Q., H. B. Liu, and G. Li. 2011. “The Experimental Study on Use of Industrial Wastes in Ceramsites for Construction.” Applied Mechanics and Materials 71–78: 1132–1135.
- Ma, B. G., L. X. Cai, X. G. Li, and S. W. Jian. 2016. “Utilization of Iron Tailings as Substitute in Autoclaved Aerated Concrete: Physico-mechanical and Microstructure of Hydration Products.” Journal of Cleaner Production 127: 162–171. doi:https://doi.org/10.1016/j.jclepro.2016.03.172.
- Modolo, R., V. M. Ferreira, L. M. Machalo, M. Rodrigues, and I. Coelho. 2011. “Construction Materials as a Waste Management Solution for Cellulose Sludge.” Waste Management 31: 370–377. doi:https://doi.org/10.1016/j.wasman.2010.09.017.
- Sang, D., A. Wang, D. Sun, and K. Liu. 2016. “Manufacturing Sintering-expanded Ceramsites from Industrial Solid Wastes.” Materials Review 30 (5): 110–114.
- Sharma, P., and H. Joshi. 2016. “Utilization of Electrocoagulation-treated Spent Wash Sludge in Making Building Blocks.” International Journal of Environmental Science and Technology 13 (1): 349–358. doi:https://doi.org/10.1007/s13762-015-0845-7.
- Singhal, A., V. K. Tewari, and S. Prakash. 2008. “Utilization of Treated Spent Liquor Sludge with Fly Ash in Cement and Concrete.” Building and Environment 43 (6): 991–998. doi:https://doi.org/10.1016/j.buildenv.2007.02.002.
- Sonowal, P., M. Khwairakpam, and A. S. Kalamdhad. 2014. “Stability Analysis of Dewatered Sludge of Pulp and Paper Mill during Vermicomposting.” Waste & Biomass Valorization 5 (1): 19–26. doi:https://doi.org/10.1007/s12649-013-9225-z.
- Soucy, J., A. Koubaa, S. Migneault, and B. Riedl. 2014. “The Potential of Paper Mill Sludge for Wood-plastic Composites.” Industrial Crops and Products 54: 248–256.
- Sun, Y. Y., Y. B. Sun, Q. B. Sun, and X. J. Xiao. 2017. “Lightweight Ceramsites Prepared by the Solid Waste of Semiconductor and Textile Dyeing Industry.” International Journal of Modern Physics B 31: 16–19.
- Tang, Y. Y., S. W. Chan, and K. Shih. 2014. “Copper Stabilization in Beneficial Use of Waterworks Sludge and Copper-laden Electroplating Sludge for Ceramic Materials.” Waste Management 34 (6): 1085–1091. doi:https://doi.org/10.1016/j.wasman.2013.07.001.
- Wang, D., J. L. Huang, H. T. Peng, and J. L. Huang. 2014. “Sinterability and Expansion Property of Ceramsites Made with Lead-zinc Mine Tailings.” Applied Mechanics and Materials 551: 23–27.
- Wang, Q., C. B. Zhang, Z. Y. Ding, and L. Jun. 2013. “Study on the Thermal Properties of Paraffin/Ceramsites Phase Change Concrete.” Advanced Materials Research 838–841: 91–95.
- Wang, X. P., R. Yu, Z. H. Shui, Z. M. Zhao, Q. L. Song, B. Yang, and D. Q. Fan. 2018. “Development of a Novel Cleaner Construction Product: Ultra-high Performance Concrete Incorporating Lead-zinc Tailings.” Journal of Cleaner Production 196: 172–182. doi:https://doi.org/10.1016/j.jclepro.2018.06.058.
- Wang, Y. N., J. H. Yang, H. Xu, C. W. Liu, Z. Shen, and K. Hu. 2019. “Preparation of Ceramsite Based on Waterworks Sludge and Its Application as Matrix in Constructed Wetlands.” International Journal of Environmental Research and Public Health 16 (15): 2637. doi:https://doi.org/10.3390/ijerph16152637.
- Wang, Z., M. G. Zhong, J. F. Wan, and G. J. Xu. 2016. “Development of Attapulgite Composite Ceramsites/quartz Sand Double-layer Biofilter for Micropolluted Drinking Source Water Purification.” International Journal of Environmental Science and Technology 13 (3): 825–834. doi:https://doi.org/10.1007/s13762-015-0920-0.
- Xu, G. R., J. L. Zou, and Y. Dai. 2006. “Utilization of Dried Sludge for Making Ceramsites.” Water Science & Technology 54 (9): 69.
- Yang, C. M., C. Cui, J. Qin, and X. Y. Cui. 2014. “Characteristics of the Fired Bricks with Low-silicon Iron Tailings.” Construction and Building Materials 70: 36–42. doi:https://doi.org/10.1016/j.conbuildmat.2014.07.075.
- Yang, Y. H., Z. A. Wei, Y. L. Chen, and Y. J. Li. 2017. “Utilizing Phosphate Mine Tailings to Produce Ceramsites.” Construction and Building Materials 155 (6): 1081–1090. doi:https://doi.org/10.1016/j.conbuildmat.2017.08.070.
- Yi, Z. L., H. H. Sun, X. Q. Wei, and W. C. Li. 2009. “Iron Ore Tailings Used for the Preparation of Cementitious Material by Compound Thermal Activation. International Journal of Minerals.” Metallurgy and Materials 16 (3): 355–358. doi:https://doi.org/10.1016/S1674-4799(09)60064-9.
- Yue, Z. X., and J. N. Chen. 2013. “Study on Preparation of Ceramsites by Kyanite Tailings.” Advanced Materials Research 753–755: 632–636.
- Zhu, M. G., H. Wang, L. L. Liu, R. Ji, and X. D. Wang. 2017. “Preparation and Characterization of Permeable Bricks from Gangue and Tailings.” Construction and Building Materials 148 (2): 484–491. doi:https://doi.org/10.1016/j.conbuildmat.2017.05.096.
- Zou, J. L., and G. B. Li. 2008. “Stabilization of Heavy Metals in Ceramsites Made with Sewage Sludge.” Journal of Hazardous Materials 152 (1): 56–61. doi:https://doi.org/10.1016/j.jhazmat.2007.06.072.
- Zou, Z. Y., and Y. S. Liu. 2013. “Preparation of Non-sintered Ceramsites from Coal Fly Ash and Its Performance on Heavy Metals Removal.” Chinese Journal of Environmental Engineering 7 (10): 4054–4060.