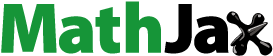
ABSTRACT
The cost of construction has intensified very significantly in recent years, which is a great area of concern for all the stakeholders. Production of conventional bricks causes substantial depletion of natural resources and creates environmental pollution, which have led the researchers to find a more sustainable solution. Foamed concrete is such an innovative and versatile material, which consists of a cement-based mortar having minimum 20% of volume filled with air. Researches are progressing with post-consumer wastes and industrial by-products such as fly ash, quarry dust, slags, etc. for the production of alternate building blocks. The utilisation of industrial waste materials in concrete compensates the lack of natural resources, solving the disposal issues of waste and to find an alternative technique to safeguard nature. Foamed Concrete has become quite popular in the construction industry because of its light weight and thermal insulation properties. This is an attempt to focus the attention to discuss at length concerned with the utilisation of industrial wastes in foamed concrete construction. This paper discusses the use of Ground Granulated Blast Furnace Slag (GGBFS) in the manufacture of building blocks using foamed concrete. It has been observed that there is an increase in compressive strength by the addition of GGBFS up to 20% and then decreases when 40% GGBFS was added.
1. Introduction
Concrete is a versatile building material which can be very easily moulded into any shape. Foamed Concrete (FC) is a novel type of lightweight concrete in which stable foam is used as one of the ingredients. The main peculiarity of this concrete is that it totally avoids the use of coarse aggregate. Foamed concrete usually contains minimum 20% volume of foam entrained into the plastic mortar, with density varying from 400 kg/m3 to 1800 kg/m3 (Kearsley and Wainwright Citation2001, Citation2002; Jones and Mc Carthy Citation2005). While adding stable foam into the prepared cement mortar, it sets around the foam bubbles and when the foam begins to degenerate, the paste will have sufficient strength to maintain its shape around the voids. (Nambiar and Ramamurthy Citation2006).
It has been observed by Kearsley and Mostert (Citation2005) that foamed concrete is more sensitive to water demand than normal concrete. If water added is too less, it may cause rapid degeneration of foam due to the lack of water for initial hydration. At the same time, if water added is too much, it may lead to segregation causing variation in density. They also observed that coarse aggregate being absent in foamed concrete makes it to have more drying shrinkage value, which has been confirmed by Jones and McCarthy (Citation2005). It has also been established that shrinkage of foamed concrete generally occurs within 20 days of casting. Pulverised sand finer than 300 microns has been used as the fine aggregate in the above study. Nambiar and Ramamurthy (Citation2006) also inferred that lower consistency of foamed concrete makes the density ratio, which is the ratio of fresh density to design density, higher than unity. Mix with fine sand and of required consistency resulted in compressive strength higher than that of mix with coarse sand. This is attributed to the uniform distribution of pores in foamed concrete with fine sand (Nambiar and Ramamurthy Citation2007, Citation2008). It is corroborated that, the pozzolanic waste materials such as fly ash and GGBFS, when used as a cement replacement can render sustainable concrete (Chore and Joshia Citation2015).
Substantially, GGBFS concrete at high replacement ratio enhanced the service life due to combination of dense pore structure and enhanced chloride binding capacity (Hong and Ann Citation2017). It has been observed that by keeping the water cement ratio as low as 0.35, concrete containing GGBFS up to 50% can achieve high early-age strength (Samad, Shah, and Limbachiya Citation2017). Later, a study conducted by Jang, Karthick, and Kwon (Citation2017) revealed that better durability performance for chloride environment is obtained in HPC containing GGBFS and FA compared to a control mix. In a study conducted by Muhammad et al. (Citation2017), it has been proved that GGBFS can be very effectively used for the production of geopolymer concrete. Also, it has been reported by Saranya, Nagarajan, and Shashikala (Citation2018) that around 40–45% of cement can be very effectively replaced by GGBFS for making concrete with similar strength as that of control mix. Mohd et al. (Citation2013) observed that GGBFS along with palm oil fuel ash can come out with fruitful results, while making lightweight concrete.
A state-of-the-art review on the characteristics of surfactants and foam done by Sahu, Gandhi, and Khwairakpam (Citation2018), suggests that the selection of surfactant and foam prediction parameters play a vital role in the properties of foam, which in turn affects the properties of FC. Role of foaming agent in FC is to create small enclosed air bubbles by reducing the surface tension of the solution, which facilitates the formation of stable air bubbles. The protein type foaming agent was found to result in smaller isolated air bubbles than the synthetic type foaming agent (Panesar Citation2013; Richard and Ramli Citation2013). Selection of surfactant and foam prediction parameters influences the properties of foam, which in turn affects the properties of foamed concrete (Sahu, Gandhi, and Khwairakpam Citation2018). Promising results were obtained during the experiment with GGBFS replacing 50% of cement without compromising its properties (Zhao et al. Citation2015). For concrete designed for nuclear structures, up to 20% GGBFS could be suitably used (Siddique and Kaur Citation2012), and the best overall performance of GGBFS was reported for 30% addition (Osake Citation2017; Awang and Alijoumaily Citation2017).
From the above investigations, the following observations are made. (1) All the previous studies were focussed on the characterisation of FC as a structural material. But as per the suggestions laid down by Jones and McCarthy (Citation2005), higher drying shrinkage and low tensile strength and stiffness performance limit the straight substitution of foamed concrete for normal weight concrete. (2) But, as a material with reasonably good compressive strength at a low dry density makes foamed concrete blocks a viable substitute for conventional bricks or solid/hollow concrete blocks, which are presently available in densities ranging from 1800 kg/m3 to 2400 kg/m3. Very few works are noted on the viability of FC as a material for the manufacture of load bearing and non-load bearing building units. (3) Possibility of incorporation of high volumes of industrial wastes in the production of masonry blocks will contribute to a sustainable construction practice.
Also, nowadays in all the construction works, manufactured sand is being used instead of river sand due to its depletion. Hence, a study on FC exclusively using manufactured sand is inevitable. Studies on the utilisation of GGBFS for foamed concrete production are not much investigated. Hence, the present study is oriented towards the influence of GGBFS, a waste material, which is found to exhibit pozzolanic properties causing the strength development of FC. An analytical model is developed for predicting the compressive strength and density of FC with powder sand ratio, water powder ratio (powder is cement and GGBFS mixture), foam volume and GGBFS content as variables, which will help the practising engineers to develop a design methodology for commercial production of foamed concrete using GGBFS.
2. Experimental investigations
2.1. Materials
Fifty-three grade Ordinary Portland Cement (OPC) having specific gravity 3.15 conforming to IS: 12269–1987 has been used as the major binder material. Manufactured Sand of specific gravity 2.53 and fineness modulus 2.34 with particle size belonging to zone 4 of IS:383-Citation1970 has been used as fine aggregate. GGBFS of specific gravity 2.9 has been used as a substitute for cement to minimise the cost of construction and to minimise environmental pollution due to its excessive dumping on bare lands. Synthetic-based foaming agent of specific gravity 1.02 and pH 6.7 has been used for the production of stable foam. Mix proportions of FC were arrived as per ASTM C796/97- Citation1997.
2.2. Characterisation of materials
The characteristics of manufactured sand and the particle size variation of GGBFS are presented in . The physical characteristics and the chemical constituents of GGBFS are presented in .
Table 1. Characteristics of manufactured sand
Table 2. Particle size variation of GGBFS
Table 3. Physical characteristics of GGBFS
Table 4. Chemical constituents of GGBFS
2.3. Casting and testing of specimen
In order to economise the production of FC, powder (mix of cement and GGBFS together) to sand proportion has been selected as 1:3 and 1:4. Various mixes in these proportions were prepared with water powder ratios 0.50, 0.55 and 0.60. Volume of stable foam to be added for each mix are selected as 20%, 30% and 40% for the expected densities 1800 kg/m3, 1600 kg/m3 and 1400 kg/m3. The final aim of the research is to produce FC blocks of various sizes, having low densities and comparable strength as that of the existing one and thus to replace them. Hence, the experiment has been limited to only three densities as mentioned above. It has been noticed that water powder ratio less than 0.50 requires the use of super plasticisers to acquire sufficient consistency and required workability and hence the above three water powder ratios were selected for the present study. The details of the mixes are presented in . The stable foam has been mixed thoroughly and uniformly with the already prepared base mix using foam concrete mixer as shown in . It is a horizontal type concrete mixer having a mixing speed of 60 rpm and the mixing time required is less than 5 minutes. Stable foam produced through the foam generator has to be fed into the mixer as shown in , to get FC of required stability as well as consistency. The wet density has to be checked and compared with the design density, during the preparation of each mix, to verify the density ratio (ratio of wet density to design density) to be nearly unity (Nambiar and Ramamurthy Citation2006; Amarnath and Ramachandrudu Citation2013). The cube specimens of size 100 × 100 × 100 mm were cast to conduct various tests. In order to fill the cube moulds with foamed concrete does not require any compaction, as it is freely flowing. The specimens were de-moulded after 24 hours and were kept in water for curing. Fifty-four design mixes were prepared and 810 cubes were cast and tested for the analysis. Fifteen cube specimens were cast from each mix for the various tests. Three cubes each were selected for conducting the tests such as 28 days compressive strength, dry density, water absorption and thermal conductivity as per IS: Citation2185(Part 3) − 1984. For the determination of thermal conductivity, holes are to be made with a minimum depth of 10 cm for inserting the thermal probe. Hence, 150 × 150 × 150 mm cube specimens also were prepared. All these specimens were kept in hot air oven at 110°C until they attained constant mass for the determination of dry density, water absorption and thermal conductivity.
Table 5. Details of mixture composition of some of the mixes with mix ID
3. Results and discussion
The results for compressive strength, dry density, water absorption and thermal conductivity by testing 810 cubes out of the 54 mixes are tabulated in . The variation of compressive strength with foam volume, water powder ratio and fly ash content are shown in –,,. It can be observed that the compressive strength of foam concrete, in almost all the mixes, increases with 20% addition of GGBFS and beyond that the compressive strength decreases. The decrease in compressive strength and dry density is because of the increase in foam volume in the mix resulting in an increase in air voids. This can also be attributed to the merging of foam bubbles resulting in large voids, which in turn leads to the reduction in strength. There is a considerable increase in the compressive strength of FC by the addition of GGBFS and found that it is decreasing after the addition of it by 20%. The increase in strength may be due to the fineness of GGBFS and also its highly pozzolanic nature. The development of strength of foamed concrete is due to the strong interring particle bond between GGBFS particles and the gel matrix. This is also related to the hydration mechanism of the binary cementitious system. Furthermore, due to the pozzolanic reaction and filler characteristics of slag, the density of microstructures in the foamed concrete is increased. But at the same time, the increase in quantity cannot achieve the cementing property and hence there is decrease in strength. It is more interesting to observe that the compressive strength of FC increases marginally with increase in water content in contrast to ordinary concrete. This may be due to the fact that less foam is required at a higher water powder ratio to reach the same target density. An appropriate quantity of water enhances the consistency and stability of the mix and thus plays a key role in the production of FC of required density. There is a maximum increment in compressive strength by 24.48% with the addition of 20% GGBFS and 40% foam volume into foamed concrete.
Table 6. Compressive strength and dry density for FC in 1:3 mix
Table 7. Compressive strength and dry density for FC in 1:4 mix
Water absorption is seen to increase steadily with an increase in foam volume and GGBFS content, but is seen to reduce marginally with increase in water powder ratio. But in all cases, the percentage of water absorption is much lower than burnt bricks of equal strength. Thermal conductivity of normal type FC (control mix) ranges between 0.40 and 0.50 W/mK (Watts per metre Kelvin). But in the present study, it has been observed that the values are decreasing by the addition of GGBFS. The maximum percentage reduction is observed to be 31.25% for foamed concrete with the addition of 40% GGBFS as replacement of cement and 20% foam volume. Hence, it can be inferred that foamed concrete, prepared with GGBFS, replacing cement, possesses better thermal insulation properties.
Here in the figure 20GFC 0 represents Ground granulated foamed concrete with 20% FV and 0% GGBFS.
4. Analytical model for compressive strength and dry density
An analytical model has been developed for 28th day compressive strength (f28) and dry density (D) in terms of sand powder ratio (s/p), water powder ratio (w/p), foam volume (fv) and GGBFS (gg) and are represented in Equations (1) and (2).
where
f 28 = 28 days compressive strength
w/p = water powder ratio
D = Dry density
s/p = sand powder ratio
fv = foam volume in %
gg = GGBFS content in %
4.1. Validation of the proposed model
The experimental results have been compared with the proposed model. The experimental and analytical results are almost similar for both compressive strength and dry density. The analytical results are higher than the experimental results for 50% to 60% for both compressive strength and density. The variation of experimental and analytical results of FC prepared with w/p ratio 0.50, 0.55 and 0.60, respectively, are graphically represented in . The proposed model has been validated with a limited number of results available in the literature and is presented in . Even though many studies are made on FC, the parameters considered in these studies vary from the present investigation. It may also be noted that manufactured sand was used instead of river sand, GGBFS was used to replace cement and foaming agent different from previous studies was used in the present study. In almost all the cases, the variation was very low except in the case of FC with 70% addition of GGBFS, which showed an error of 24.74%.
Table 8. Validation of the model for compressive strength
Table 9. Validation of the model for dry density
5. Cost analysis
Analysis has been carried out to compare the cost of 1 cubic metre of normal concrete and foamed concrete with GGBFS replacing cement and is presented in . It has been understood that there is considerable reduction in the cost of production of foamed concrete, leading to economy in construction.
Table 10. Cost analysis of normal concrete and foamed concrete per cubic metre
6. Conclusions
Based on the study conducted on foamed concrete using GGBFS, the following conclusions can be made.
Foamed concrete blocks of the required quality for both load bearing and non-load bearing types of construction can be developed at low density with the help of a suitable foaming agent. The use of such blocks will reduce the dead load on the structure, which in turn leads to slender sections with savings in reinforced cement concrete, steel reinforcement, plastering, etc. for multi-storeyed framed structures.
The compressive strength is reduced by increasing GGBFS content. But by 20% replacement of cement by GGBFS, the compressive strength is found to increase marginally. Maximum increment in compressive strength of foamed concrete is 24.48% with the addition of 20% GGBFS as a replacement to cement and 40% foam volume.
Thermal conductivity of foamed concrete is reduced by increase in GGBFS content. Maximum percentage reduction is observed to be 31.25% for foamed concrete with the addition of 40% GGBFS as replacement of cement and 20% foam volume.
Best quality construction blocks can be developed using GGBFS, thereby a substantial amount of cement can be saved in large-scale production of foamed concrete, which ensures the environmentally friendly disposal of such waste materials.
An analytical model is developed for 28th day compressive strength and dry density with percentage foam volume, GGBFS percentage, sand powder ratio and water powder ratio as variables. The use of such model enables practising engineers to design and develop construction blocks of sufficient compressive strength and density ensuring sustainable construction practices.
Disclosure statement
There is no conflict of interest in this research.
Additional information
Funding
Notes on contributors
Sajan K. Jose
Sajan K. Jose, M-Tech, currently working as Associate Professor in the Department of Civil Engineering of LBS Institute of Technology for Women, Poojappura, Trivandrum, Kerala, India.
Mini Soman
Dr. Mini Soman PhD, currently working as Professor & Head, Department of Civil Engineering, College of Engineering Trivandrum, Kerala, India.
Sheela Evangeline Y
Dr. Sheela Evangeline Y PhD, Professor, Department of Civil Engineering, College of Engineering Trivandrum, Kerala, India.
References
- Amarnath, Y., and C. Ramachandrudu. 2013. “Production and Properties of Foamed Concrete.” Proceedings of the International Conference & Exhibition on Lightweight Construction, Pune, India, February.
- ASTM C 796-97 Standard Test Method for Foaming Agents for Use in Producing Cellular Concrete Using Preformed Foam. 1997.
- Awang, H., and Z. S. Alijoumaily. 2017. “Influence of Ground Granulated Blast Furnace Slag on Mechanical Properties of Foam Concrete.” Cognent Engineering, Civil & Environmental Engineering 4 (1). doi:https://doi.org/10.1080/23311916.2017.1409853.
- Chore, H. S., and M. P. Joshia. 2015. “Strength Evaluation of Concrete with Fly Ash and GGBFS as Cement Replacing Materials.” Advances in Concrete Construction 3 (3): 223–236. doi:https://doi.org/10.12989/acc.2015.3.3.223.
- Hong, S. I., and K. Y. Ann. 2017. “Estimation of Corrosion-Free Life for Concrete Containing Ground Granulated Blast-Furnace Slag under a Chloride-Bearing Environment.” Hindawi, Advances in Materials Science and Engineering 2017: 10. Article ID 3186371. doi:https://doi.org/10.1155/2017/3186371.
- IS: 2185 (Part3) − 1984 Indian Standard Specification for Concrete Masonry Units PART 3 Autoclaved Cellular (Aerated) Concrete Blocks. Bureau of Indian Standards, 1985, Manak Bhavan, 9 Baiiadur Shah Marg, New Delhi.
- IS:383-1970 Indian Standard Specification for Coarse and Fine Aggregates from Natural Sources for Concrete. Second Revision ed. Bureau of Indian Standards, 1971, Manak Bhavan, 9 Baiiadur Shah Marg, New Delhi.
- Jang, S.-Y., S. Karthick, and S.-J. Kwon. 2017. “Investigation on Durability Performance in Early Aged High-Performance Concrete Containing GGBFS and FA.” Advances in Materials and Engineering 2017: 1–11. doi:https://doi.org/10.1155/2017/3214696.
- Jones, M. R., and A. McCarthy. 2005. “Preliminary Views on the Potential of Foamed Concrete as a Structural Material.” Magazine of Concrete Research 57 (1): 21–31. doi:https://doi.org/10.1680/macr.2005.57.1.21.
- Kearsley, E. P., and H. F. Mostert. 2005. “Designing Mix Composition of Foamed Concrete with High Fly Ash Contents.” Proceedings of the International Conference, Scotland, UK: University of Dundee. August.
- Kearsley, E. P., and P. J. Wainwright. 2001. “Porosity and Permeability of Foamed Concrete.” Cement and Concrete Research 31 (5): 805–812. doi:https://doi.org/10.1016/S0008-8846(01)00490-2.
- Kearsley, E. P., and P. J. Wainwright. 2002. “Ash Content for Optimum Strength of Foamed Concrete.” Cement and Concrete Research 32: 241–246. doi:https://doi.org/10.1016/S0008-8846(01)00666-4.
- Mohd, P. S., Z. J. Hilmi, B. U. Mahmud, and J. Alengaram. 2013. “Oil Palm Shell Lightweight Concrete Containing High Volume Ground Granulated Blast Furnace Slag.” Construction and Building Materials 40: 231–238. doi:https://doi.org/10.1016/j.conbuildmat.2012.10.007.
- Muhammad, N., S. Hadi, N. Farhan, and M. Neaz Sheikh. 2017. “Design of Geopolymer Concrete with GGBFS at Ambient Curing Condition Using Taguchi Method.” Construction and Building Materials 140: 424–431. doi:https://doi.org/10.1016/j.conbuildmat.2017.02.131.
- Nambiar, E. K. K., and K. Ramamurthy. 2006. “Influence of Filler Type on the Properties of Foam Concrete.” Cement and Concrete Composites 28 (5): 475–480. doi:https://doi.org/10.1016/j.cemconcomp.2005.12.001.
- Nambiar, E. K. K., and K. Ramamurthy. 2007. “Sorption Characteristics of Foam Concrete.” Cement and Concrete Research 37 (9): 1341–1347. doi:https://doi.org/10.1016/j.cemconres.2007.05.010.
- Nambiar, E. K. K., and K. Ramamurthy. 2008. “Models for Strength Prediction of Foam Concrete.” Materials and Structures 41: 247–254. doi:https://doi.org/10.16117/s11527-007-9234-0.
- Osake, F. I. 2017. “Durability of Concrete Incorporating Ground Granulated Blast Furnace Slag for Water Infrastructures.” Nigerian Journal of Scientific Research 16 (3): 258–263. www.researchgate. net/publication/327321456.
- Panesar, D. K. 2013. “ Cellular concrete properties and the effect of synthetic and protein foaming agents.“Construction and building materials 44 (2013): 575–584.
- Richard, A. O., and M. Ramli. 2013.“Experimental production of sustainable lightweight foamed concrete. “Current Journal of Applied Science & Technology (2013): 994–1005.
- Sahu, S. S., I. S. R. Gandhi, and S. Khwairakpam. 2018. “State of the Art Review on the Characteristics of Surfactants and Foam from Foam Concrete Perspective.” Journal of Institution of Engineers India 99 (2): 391–405. doi:https://doi.org/10.1007/s40030-018-0288-5.
- Samad, S., A. Shah, and M. C. Limbachiya. 2017. “Strength Development Characteristics of Concrete Produced with Blended Cement Using Ground Granulated Blast Furnace Slag (GGBS) under Various Curing Conditions.” Sadhana 42 (7): 1203–1213. July. doi:https://doi.org/10.1007/s12046-017-0667-z.
- Saranya, P., P. Nagarajan, and A. P. Shashikala. 2018. “Eco-friendly GGBS Concrete: A State-of-The-Art Review.” Materials Science and Engineering 330: 012057. doi:https://doi.org/10.1088/1757-899X/330/1/012057.
- Siddique, R., and D. Kaur. 2012. “Properties of Ground Granulated Blast Furnace Slag (GGBFS) at Elevated Temperatures.” Journal of Advanced Research 3 (1): 45–51. doi:https://doi.org/10.1016/j.jare.2011.03.004.
- Zhao, X., S. K. Lim, C. S. Tan, B. Li, T. C. Ling, R. Huang, and Q. Wang. 2015. “Properties of Foamed Mortar Prepared with Granulated Blast-Furnace Slag.” Materials 8 (2): 462–473. doi:https://doi.org/10.3390/ma8020462.