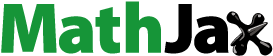
ABSTRACT
In hot regions, the main reason for the consumption of energy arises from cooling the buildings. The intensity of the sunlight also has a direct relation to the use of the cooling systems. In the present work, a humidification system is built with packing made of locally available novel materials, and the performance of the cooling pads has been accessed under both counter flow and cross flow conditions. Coconut coir and wood shaving are used as alternative materials for evaporative cooling, and the experiments are conducted using varied airflow rates and the performance parameters, such as heat flow rate, humidification efficiency, moisture flow rate, coefficient of performance (COP) and specific cooling capacity (SCC) have been tested and compared with the Celdek packing. Results indicated that wood shaving performed better than the coconut coir. Values of COP and SCC are found to be very close to Celdek packing. Humidification efficiency of wood shaving is at par with the Celdek packing with improved quality of indoor air. In addition, results indicated that the counter flow arrangement gave better results compared to cross flow.
1. Introduction
Evaporative cooling technique is one of the unique methods of cooling system where the air gets cooled by the evaporation of water. It can be seen in many household cooling systems due to less operational cost, simple technology and is popular in most of the tropical and developing countries (Jain and Hindoliya Citation2011; Malli et al. Citation2011; Dhamneya, Rajput, and Singh Citation2018). Current AC systems work on vapour compression phenomenon, consume substantial amount of power and is very harmful to the environment causing global warming and ozone layer depletion (Dhamneya, Rajput, and Singh Citation2017). Evaporative cooling system is a good alternative, which consumes less energy and provides the best thermal comfort inside the space (Al-Sulaiman Citation2002; Alam et al. Citation2017). Buildings consume electricity at around 32% in the whole world (Oueslati, Hannachi, and Elmaaoui Citation2015; Doğramacı et al. Citation2019). Air conditioning systems are the biggest electricity consumption sectors worldwide, and they consume around 20% of power. Hence, the evaporative cooling technique can be considered as the best alternative (Nada et al. Citation2019; Patel and Patel, Citation2018). The power consumption of evaporative cooler is very less compared to traditional AC units with the saving of 75% of energy (Cazzaniga, Colombo, and De Antonellis Citation2019). Similarly, in the tropical developing countries, where there is scarcity of electrical energy, evaporative cooling is one of the most important options available for space cooling which also saves substantial amount of energy (Chiranjeevi and Srinivas Citation2017).
Efficiency of evaporative pad is affected by many factors, such as materials selected for absorption and related properties like type of the material, thickness, size of perforation, etc. Humidification is also influenced by surrounding air conditions such as air temperature, relative humidity and the flow rate (Hassabou, Spinnler, and Polifke Citation2014; Kumar et al. Citation2020; Salins et al. Citation2020). The process is also influenced by the water properties like temperature and flow rate. Since it is basically a heat and mass transfer process, the type of the flow between air as well as water also affects the evaporation (Wavdekar et al. Citation2017; Warke and Deshmukh Citation2017). As the water holding and absorbing capacity differs from material to material, selection of the appropriate material becomes very important for the performance of the evaporative cooling. In addition, regular use of the pads deteriorates the performance of the pads (Patel, Patel, and Patel Citation2016; Reddy and Prasanna Citation2015). Various pad materials have been used and tested by different investigators for evaporative cooling (Niyomvas and Potakarat Citation2013; Ndukwu and Manuwa Citation2014; Velasco-Gómez et al. Citation2020). Evaporative pads are made from materials, such as wood, plastic, glass, metal, etc. Commercially available pads are made of cellulose-based materials, and their manufacturing is very expensive and also complicated (Arshad Citation2017; Dhakulkar et al. Citation2018; Kim Citation2017).
Jain and Hindoliya (Citation2011) analysed two cooling pad materials such as Aspen and Khus. These materials were tested along with coconut and Palash fibres. In their experiments, Palash fibres exhibited effectiveness of 13.2% and 26.3% more than Aspen and Khus pads. Khus pads gave less pressure drop, whereas Aspen pads gave highest pressure drop among all four materials. Malli et al. (Citation2011) used two types of cellulose packing 5090 and 7090, which are made from hard corrugated paper and concluded that pressure increase strongly depends on the air velocity. Dhamneya, Rajput, and Singh (Citation2018) used Aspen fibres as packing material and various configurations related to this material and its behaviour patterns were analysed. Results indicated that triangular configuration gave maximum humidification efficiency compared to the other types. Dhamneya, Rajput, and Singh (Citation2017) used five different materials, such as banana tree fibres, sugar cane fibres, coconut fibres, Khus fibres and honeycomb paper. All the fibres were maintained with a fixed density. Results indicated that the cooling efficiency of coconut fibre was higher than others. Al-Sulaiman (Citation2002) obtained an efficiency of 62.1% with jute which was highest among the different materials studied. Oueslati, Hannachi, and Elmaaoui (Citation2015) observed that a slight increase in water temperature yielded increased humidification using Celdek packing as the pad material. Doğramacı et al. (Citation2019) investigated the performance of new type of packing made by eucalyptus fibres for evaporative cooling and obtained satisfactory performance as compared with commercially available Celdek packing. Nada et al. (Citation2019), during his experiments using cellulose packings of different thicknesses, observed that, with the increase in the thickness of pads, there was a rise in the saturation efficiency, energy efficiency and overall efficiency. Citation2018 built two humidifier units: one is a packed bed that is made of honeycomb slated packing material and the other is a bubble column humidifier. Results revealed that slated bed type gave maximum humidification compared to bubble type. Cazzaniga, Colombo, and De Antonellis (Citation2019), worked on an innovative air humidification system where two packed beds were made, one with a packed bed and the other made of sorption material. Results indicated that there was a rise in humidification in packed bed compared to other types. Chiranjeevi and Srinivas (Citation2017) focused on the design and development of air humidifier unit, which was used in desalination unit and also conducted numerical analysis. Results showed that experimental and theoretical results well matched with each other. Hassabou, Spinnler, and Polifke (Citation2014) discussed the role of conductive packing as a heat and mass exchanger. Numerical and experimental investigations were carried out and compared. Wavdekar et al. (Citation2017) worked on cooling and humidification system on the different modes of flow patterns. Warke and Deshmukh (Citation2017) used cellulose packing, which were made up of corrugated paper material. A sonic wind tunnel was built, and the pad area used was 0.35 × 0.35 m2 with the thicknesses of 50, 100 and 150 mm. Pressure drop, evaporation rate and effectiveness increased with increase in the air velocity, whereas humidity variation dropped with the rise in air velocity. It was found that the effectiveness of the cellulose is higher than Aspen and Khus pad. Cellulose pads gave a saturation efficiency of 90.37%, whereas the Aspen packing gave 78.31%. Patel, Patel, and Patel (Citation2016) worked on a humidification dehumidification system used in the small capacity water generation plants. Humidification chamber used a new type of pad called grass pad. The water was sprayed on the pads. Results showed that there is a rise in the humidity by 12%. Rawangkul et al. (Citation2008) worked on two types of coconut coir with different configurations. The air velocity was varied between 1.88 and 2.87 m/s. The average pressure drop was found to be 1.5 and 5.1 Pa, respectively. Results indicated that cooling efficiency of 50% was obtained.
From the literature, it is understood that cellulose paper packing is the material widely used for humidification and dehumidification purposes in various applications including residential and industrial sectors. These pads are fabricated with corrugated papers. They are compact and light in weight, but are costly and uneconomical. Manufacturing of these pads will be difficult and requires a proper technology and skill, which makes them as expensive and locally unavailable (Yash et al. Citation2017; Mehere, Mudafale, and Prayagi Citation2014). In addition, the life span of cellulose pads is limited. As per the literature, some other alternative materials considered in the commercial evaporative coolers are Aspen and Khus pads. The performance of these materials is moderate, and life span is also limited (Inamdar and Akshay Kale Citation2019; Laknizi et al. Citation2019). Hence, it is always desired to investigate alternative locally available materials as packing materials for evaporative cooling giving higher performance in terms of humidification air temperature (Ahmed et al. Citation2011; Roshan and Parashar Citation2015; Vala, Makwana, and Sagarika Citation2019) . In addition, the materials should have a long-life span, possibly biodegradable and economical (Lal Basediya, Samuel, and Beera Citation2013; Chantana Citation2019). In this context, it is required to investigate the performance of alternative materials for evaporative cooling in order to derive with the material, which shows better performance and economical. In order to bridge these research gaps, in the present study, wood shaving and coconut coir have been used as the packing materials, and the experimental investigations have been carried out in a humidification test rig. Experiments have been carried out under both counter flow and cross flow conditions to determine the best possible configuration and material selection for optimum performance, which is the novelty of the present work.
2. Theory background
The main principle involved in the operation of the humidification system is evaporative cooling process. A known velocity of air is blown into the duct, where it is made to interact with the packing or the cooling pads, which are soaked with water sprayed on it. When the air interacts with cooling pads, evaporation of water takes place by absorbing the latent heat of evaporation from air, thereby increasing the humidity of exit air and decreasing its temperature (Haruna et al. Citation2014; Sharma et al. Citation2016).
Knowing the exposed surface area of the pads, heat transfer coefficient and the logarithmic mean temperature difference between air and water, the heat transfer rate can be calculated. EquationEquation (2)(2)
(2) is used to calculate the logarithmic mean temperature difference between the two fluids.
During the humidification process, water receives the latent heat from air and gets evaporated. Evaporation rate provides the total amount of water getting evaporated, and it is a function of mass flow rate of air and the difference in the air-specific humidity values, which can be calculated by using EquationEquation (3)(3)
(3) .
Humidification efficiency refers to the amount of humidity percentage in addition to the regular input air. It is represented by EquationEquation (4)(4)
(4) .
The coefficient of performance refers to the ratio of output cooling effect to the input work done by the blower and pump. EquationEquation (5)(5)
(5) shows the calculation of COP.
where Qc represents to the cooling effect, which can be determined using EquationEquation (6)(6)
(6) .
where Cp and ΔT represent the specific heat at constant pressure and the change in temperature for air.
The specific cooling capacity (SCC) shown in EquationEquation (7)(7)
(7) is determined by the amount of cooling capacity obtained per kg of water evaporated. It is the ratio of the cooling capacity to evaporation rate.
SCC = Cooling capacity/Evaporation rate
Two types of arrangements have been selected in the present study, counter flow and cross flow. In the counter flow type, water and air will be flowing in different directions, whereas, in the cross flow, they move in two mutually perpendicular directions (Sampath, Kumar, and Reddy Citation2020). An experimental setup is built in order to compare different flows, which gives the best humidification efficiency.
3. Experimental setup and methodology
& show the schematic sketch, and show the experimental setup used for counter flow and cross flow humidification system, respectively. It consists of a duct where the air is circulated from the blower at variable velocities. In the counter flow humidifier, air is circulated from the blower interacts with the water dripping from the reservoir in the opposite direction. Interaction of both fluids takes place effectively inside the packing. In cross flow, both the air and the water dripping with gravity interact in perpendicular direction. The direction of water dripping will be maintained constant, whereas air direction is changed to make it as cross and counter flow. A packing or cooling pad element, which has the wettability property to hold the moisture, used at the interface is placed inside the duct having the dimension of 100 mm × 100 mm × 100 mm. Celdek Packing of type 7090 is cut to fit the cross-section of the duct. To hold the coconut coir and wood shaving, a frame with mesh is constructed. Volume of the box for accommodating the pads is 1000 cm3 with a thickness of 2 mm, the density of the wood shaving and coconut coir is calculated, and a uniform value of 200 kg/m3 has been considered as the density for the sake of comparison.
Cellulose pads consist of flutes which are porous and designed to absorb and retain water in order to provide maximum cooling efficiency. Included angles and wettability of the chosen cellulose packing are calculated, and the corresponding values are 45° groove angle and 632 m2/m3, respectively.
Coconut trees are common trees that will be grown in most of the parts of tropical countries. It has a scientific name Cocos nucifera. The coir, which is separated from the coconut, will be the byproduct and is a waste product other than used for firewood applications. This has good water absorbing holding capacity. Similarly, the waste chips that are obtained after the woodwork collectively known as wood shavings are considered as another alternative packing material. Wood shaving material can be used as a packing material, since it has merits such as easily available, water resistance, good strength, free of debris and dirt, good water retention and good evaporation rate. Also, the density of the packing can be varied by appropriate filling of the wood chips given an added advantage of obtaining the best performance depending upon the optimum point. Schematic presentation of commercially available Celdek packing, wood shavings and coconut coir is shown in .
Pump with a capacity of 0.1 horsepower is used to fill the water in the reservoir, and it is made to drip on the packing by gravity. Air is blown at different flow rates supplied by the blower having a capacity of 0.25 HP. When air blows on the packing, there is a surface contact taking place between packing and air, where it will carry the moisture along with it. The outlet air is humidified. The excess water collects in the water collector tank, which is circulated back to the reservoir with the pump. Various inlet parameters considered are air velocity, relative humidity, dry and wet bulb air temperature. Corresponding dry and wet bulb air temperature at the outlet, relative humidity and water temperature at the outlet are noted. The measured values are used to quantify the humidification performance parameters such as coefficient of performance, specific cooling capacity, evaporation rate, humidification efficiency and cooling effect. Digital thermometers are used to measure dry bulb and wet bulb temperatures. The thermometer measuring wet bulb thermometer has wet cloth on the bulb and tip is in contact with water. Hygrometer measures the inlet and outlet humidity and the anemometer measures the air velocity. shows the specifications of the instruments used and their accuracy values.
Table 1. Measuring devices to measure the parameters of humidification
The selected materials have been inserted into a mesh made of polyester. shows the frame/mesh constructed of sheet metal. A wire mesh is used to enclose the surface of the sheet metal and to make the frame intact. A volume of 100 mm × 100 mm × 100 mm is considered. Commercially available Celdek packing is selected such that it exactly fits into the mesh. Initial experiments are performed with changing the various air mass flow rates from 0.062 kg/s to 0.083 kg/s. Later, wood shaving has been filled to the frame with the density as mentioned above, and the humidification experiments have been carried out. Later, the frame is filled with coconut coir with a density of 200 kg/m3 filling the same original volume, and experiments are repeated. All the readings are noted, and the cooling performance is compared with the Celdek packing.
4. Results and discussion
Experiments are conducted by changing the air flow rate from 0.062 kg/s to 0.083 kg/s in increments of 0.00692 kg/s, while keeping the water flow rate constant at 450 litres/hr. The Frontal surface area of the pad of 0.0113 m2 is held constant. Densities of air and water are taken as of 1.225 kg/m3 and 998 kg/m3, respectively. Experiments are repeated for Celdek, wood shaving and coconut fibres. All the above-mentioned input and output parameters are recorded. Using the EquationEquations (1(1)
(1) –Equation7
(7)
(7) ) output parameters are determined.
4.1. Relative humidity
shows the variation of relative humidity (ΔRH) with the mass flow rate. Relative humidity is defined as the ratio of vapour partial pressure of air to partial pressure of saturated air. It is observed that as the mass flow rate of air increases, there is a drop in ΔRH at the outlet for all tested conditions. ΔRH in Cellulose is more compared to wood shaving and coconut coir for both types of flow. Wood shaving provided better results compared to the coconut coir. When wood shavings are in a coiled form, surface area exposed will be higher. In addition to this, its inherent capacity to absorb and hold higher quantity of water will also contribute to the increase in ΔRH for wood shaving. This in turn increases the specific humidity as well as relative humidity values. As the mass flow rate of air is increases, conversion of sensible to latent heat reduces, which leads to a drop in ΔRH. This may be due to the reduced contact time between the water and air for higher mass flow rates of air. Water holding capacity of coconut coir is lower than that of wood shaving, which reduces the ΔRH values. By comparing the two types of flows for all three pads, it is seen that counter flow is performing better than the cross flow. For the maximum mass flow rate of the air, it is observed that for counter flow conditions, ΔRH values are lower by 23% and 40.90% for wood shaving and coconut coir, respectively, as compared to that of Celdek packing. Similarly, for cross flow conditions, these values are 20.05% and 47.36%, respectively.
4.2. Heat transfer rate
Variations in the heat transfer between air and packings for different types of flow conditions and for different pad materials are shown in . Although it is a heat and mas transfer process, with respect to the air, EquationEquation (6)(6)
(6) is used to estimate the heat transfer taking place due to convection. Graphical representation indicates that there is an increase in the heat transfer rate with the increase in mass flow rate of air. It is observed that beyond the optimum value of mass flow rate, heat transfer rate tends to decrease. For the maximum mass flow rate conditions, heat flow difference for wood shaving and coconut coir are 1.6% and 11.7% lesser than the cellulose pad under counter flow conditions. Similarly, in cross flow case, the values are 7.3% and 22% less than cellulose packing. These results show that cellulose pad showing highest values, followed by wood shaving, and coconut coir is the least among them. The heat transfer function is due to the amount of heat absorbed under sensible and latent heat conditions during evaporation. As the water absorbing capacity of wood shaving is higher than that of coconut coir, this shows better results due higher amount of water being evaporated by absorbing higher amount of heat energy. From the results, it can be concluded as wood shaving performs better than coconut coir under both counter and cross flow conditions, and the counter flow case can be preferred over the other because of higher heat transfer rate.
4.3. Humidification efficiency
represents the variation of humidification efficiency with the mass flow rate. Humidification efficiency is defined as the ratio of the temperature difference between inlet and outlet dry bulb temperatures of air to the difference between the inlet dry bulb and wet bulb temperatures of air. The above graph represents humidification efficiency with respect to different packings and flow types. For cellulose, wood shaving and coconut coir type, the fluid flowing in counter flow gives higher efficiency as compared to the cross flow. On considering the different materials, Celdek is showing the peak, followed by the wood shaving and coconut coir being the least. When there is a higher DBT difference between the inlet and the exit air, the humidity efficiency increases. For a fixed mass flow rate, higher temperature difference indicates the increased amount of heat lost by air, which is also characterised by the material properties. Wood shaving can absorb and hold higher amount of water, so that during evaporation, it exchanges higher amount of energy with air than the coconut coir. Hence, there will be a higher air temperature difference, which helps to improve the humidification efficiency. For the counter flow arrangements, for the highest mass flow rate, there is a difference of 12.96% between cellulose and wood shaving, whereas there is a significant difference of 22.64% between wood shaving and coconut coir for the same mass flow rate of air. This shows the better performance of wood shavings compared to that of coconut coir and is at par with cellulose pads. Due to the increasing water absorbing capacity of wood shaving, it absorbs more amount of energy from the air thus dropping the air temperature to a higher value as compared to the coconut. These results again conclude that counter flow conditions are preferred over the cross flow arrangements. As the mass flow rate of air is increased, the humidity efficiency drops for all tested cases. Due to the reduced contact between air and water, DBT drop will be lowered which reduces the efficiency.
4.4. Coefficient of performance
The coefficient of performance is defined as the ratio of the cooling effect to the work done as shown in EquationEquation (5)(5)
(5) . Under similar operating conditions for three different materials, with an increase in the mass flow rate, there is a significant rise in the COP. It can be noticed that cellulose pad having the highest COP followed by wood shaving and coconut, for both types of flows as seen from . Increasing the air velocity, the effective mass transfer coefficient also increases, thereby water evaporation rate increases. This is also influenced by the type of the pad material. The wettability of wood shaving is higher than that of coconut coir. This increases the amount of water exposed to air, and hence the evaporation rate also enhances. For the maximum mass flow rate of air, it is found that COP of the cellulose packing is 34% higher than wood shaving and 45% higher than that of coconut coir under counter flow conditions. Similarly, for cross flow conditions, COP of cellulose is 32% higher than wood shaving and 55% higher than coconut coir. Under counter flow conditions, higher log mean temperature difference between the two fluids will cause higher heat transfer rate, and the results show that counter flow humidifier yields higher COP of 5–7% compared to crossflow for all the type of packing.
4.5. Specific cooling capacity
Cooling capacity and evaporation rate are the two factors affecting the specific cooling capacity. Both are functions of the velocity, and they are directly proportional to each other. Specific cooling capacity (SCC) is defined as the ratio of the cooling effect to the evaporation rate. It represents the cooling performance of different packing materials with respect to change in air velocities. In other words, it is the overall cooling effect for kg of evaporated water. SCC is calculated for three different packing materials and different mass flow rates, as shown in . Cellulose shows the highest value followed by wood shaving and coconut coir, respectively, for both types of flow, showing the advantages of counter flow over cross flow conditions. Wood shaving possesses having higher porosity, high surface area due to its coiled structure and higher water absorbing capacity than the coconut coir. Coconut coir is long extended and tubular structure, and reduced porosity has decreased its water absorbing capacity. Due to this, for a definite quantity of heat lost by air, amount of water evaporated per kg of air for coconut coir is higher than wood shaving. These characteristics have reduced SCC for coconut coir as compared to wood shaving. Further, whenever there is a counter flow arrangement, due to the more uniform temperature difference and reduced thermal stresses, higher heat transfer will occur between the pad material and the air initiating higher SCC as clearly seen in .
4.6. Evaporation rate
Evaporation trend for different mass flow rate is shown in . Evaporation rate is defined as the rate at which material evaporates or vaporises. In other words, it is a change from liquid to vapour phase. Evaporative cooling happens when air encounters the liquid and liquid absorbs the latent heat there by converting into the vapour form. During this time, air temperature drops and hence it gets cooled. indicates that the evaporation rate is directly proportional to the mass flow rate of air. As there is an increase in mass flow rate, there is a rise in evaporation rate. From the experimental results, it is found that the evaporation rate is maximum in the case of coconut coir compared to wood shaving and standard cellulose packing in both counter and cross flow types. Cellulose exhibited the lowest evaporation rate. Inherent characteristics of wood shaving like long coiled porous structure compared to the long fibres with higher water holding capacity have made wood shaving as a better option for evaporative cooling pads. Increases in the evaporation rate with wood shaving and coconut coir are 54% and 47% with respect to Celdek packing under counter flow conditions. Similarly, these values are 63% and 51% higher for cross flow conditions. The low value of evaporation rate yielded high value of specific cooling capacity for cellulose and wood shaving type of packings. These figures will indicate the higher suitability of wood shaving as an alternative pad material in evaporative coolers as compared to Celdek material.
4.7. Pressure variation
shows the variation of pressure with the mass flow rate. It is observed that for all types of packing material and the type of flow, the change in the pressure rises significantly with the increase in the air velocity. As the air velocity increases, it leads to a higher distribution of flow field and offers higher resistance between
Corrugated papers or pad materials. This indicates that with the increase in the thickness of packing material leads to the increase in the pressure drop. The size of the pores plays a major role in the pressure drop. The smaller the pore size increases the contact area and friction, which indirectly increases the pressure drop. In the above figure, standard Celdek material yields higher pressure drop because of neatly arranged layers with compact structure. Wood shaving offered next higher pressure since they are the coils of wood pieces with higher surface area and not as dense as Celdek packing. Coconut coir gave the least pressure drop because it is arranged in the form of stack of strands, which offers low surface contact area and friction. With respect to the different flow conditions, counter flow and cross flow do not show much difference in the pressure drop values.
From the above results, it is clear that counter flow operation is superior to the cross flow pattern for all the three types of materials. The counter flow heat exchanger is compact which yields maximum performance because of increased interaction between air and the water. In the counter flow arrangement, two fluids are flowing in the opposite direction, whereas in case of a cross flow arrangement, two fluids are flowing perpendicular to each other. In the case of either parallel or cross flow, temperature difference at any instant is not effective as that of counter flow arrangement. In a counter flow arrangement, a more uniform temperature difference between the two fluids will be observed over the entire length of the fluid flow. In addition, the thermally induced stresses will be lower. This leads to an increased heat transfer rate and higher temperature drop at the exit. On the other hand, the temperature drop is minimum for across flow type due to the inefficient heat transfer occurring between water and air. Higher drop in temperature is also followed by the higher evaporation of water leading to higher humidity with lower temperature at the exit condition in case of counter flow arrangement.
5. Validation of results
In order to validate the results of the present work for the three types of pads cellulose, wood shaving and coconut coir, they are compared with published literature reports which is shown in . The change in DBT is compared with the work carried out by CitationJain and Hindoliya (Citation2011); Dhamneya, Rajput, and Singh (Citation2018, Citation2017); Al-Sulaiman (Citation2002), where they used straw pads, sliced wood pads and Palash fibres under similar operating conditions and for a mass flow rate 0.06 kg/s. The results showed that cellulose, showing the highest change in DBT followed by wood shaving and ΔDBT for the other pads, is in the order of straw pads, coconut coir, sliced wood and Palash, respectively. These results indicate that wood shaving performs better than many of the packing materials considered.
Similarly, humidification efficiency variation with respect to different materials is compared with the present work reports, which is shown in . The materials considered are Palm, Luffa, Jute and a commercial material from the literature (Jain and Hindoliya Citation2011; Dhamneya, Rajput, and Singh Citation2017; Al-Sulaiman Citation2002). The mass flow rate is fixed at 0.06 kg/s. Results indicate that celdek and wood shaving gave maximum efficiencies of 91% and 86%. The efficiencies of other materials are in the order of coconut coir, jute, luffa, commercially available material and palm, respectively. Both the above results indicate that wood shaving gives better humidification performance compared with other locally available materials. In addition to this, it is very cheap, abundantly available with free of cost, odourless, longer life, easy to fill the pad channel and better water absorbing and holding capacity. It also provides better quality of air as compared to coconut coir. All these factors have made use of wood shaving as one of the potential pad material for future evaporative cooling process.
6. Conclusions
The humidification experiment is carried out by maintaining the same volume and weight of different pad materials like wood shaving and coconut coir and are compared with the commercially available Celdek packing. Tests are conducted by varying the air velocity in both counter and cross flow directions, and the performance parameters are evaluated and tabulated. The performance of the evaporative cooling pads is evaluated and quantified for air humidity rise, air temperature drop, COP, efficiency, cooling effect and specific cooling capacity. From the findings, the following conclusions can be drawn.
The coefficient of performance and cooling effect of the cellulose packing is higher than those of wood shaving and the coconut coir packing. Also, the counterflow humidification system gave better results compared to the cross flow humidification system. When the mass flow rate is small, the difference in counter and cross flow humidifier COP is negligible. The maximum COP obtained for the cellulose, wood shaving and coconut coir are 3.17, 2.08 and 1.41, respectively.
Humidification efficiency of the wood shaving packing is very close to the standard cellulose type of packing, irrespective of the type of flow, whereas for coconut coir it is very low compared to both wood shaving and cellulose packing. Efficiencies of cellulose, wood shaving and coconut coir are 86.15%, 78.33% and 68.40%, respectively, for the highest mass flow rate.
SSC values for wood shaving are higher than coconut coir packing for all mass flow rates of air tested and are marginally less than the commercial Celdek packing. As far as the pressure drop is concerned, Celdek shows the peak values followed by wood shaving, and coconut coir showing the least among them.
Considering the performance parameters among wood shaving and coconut coir materials, wood shaving gave better results, which are very close to the results of cellulose packing material. Hence, the effectiveness of the pads in decreasing order of magnitude is Cellulose>Wood shaving> coconut coir pad.
Counter flow arrangement for the three types of packing gave better results in terms of higher humidification efficiency, higher evaporation rate and higher relative humidity values.
From the above study, it can be concluded that out of the different materials under consideration for evaporative cooling pads, wood shaving is one such alternative that can be substituted for commercially available Celdek cellulose packing, whose performance is comparable to Celdek and with added benefits like reduced price, cheaply available, easy to fill the packing volume and also higher life. In addition, they are locally available, biodegradable materials, which further makes them as cost-effective. They also provide clean air and hence free from environmental pollution.
Hence, the use of wood shaving in evaporative coolers will help to reduce the energy consumption as compared to the normal air conditioning systems for cooling applications, which will indeed contribute to the development of the sustainable energy sources.
Nomenclature
Disclosure statement
No potential conflict of interest was reported by the author(s).
Additional information
Notes on contributors
Sampath Suranjan Salins
Sampath Suranjan Salins is working as Assistant professor (Senior scale) in Mechanical Engineering department in School of Engineering and IT at MAHE Dubai, UAE. His research interests include heat transfer in fins, refrigeration and air conditioning, desiccant based dehumidification and humidification.
S.V. Kota Reddy
S.V. Kota Reddy is working as Professor in Mechanical Engineering department at VIT-AP, Andra Pradesh India. He is also Vice Chancellor of VIT-AP University. His research interests include refrigeration and air conditioning, Humidification and dehumidification, solar air heaters and heat pumps.
Shiva Kumar
Shiva Kumar is an Associate Professor (Senior Scale) in the Department of Mechanical and Manufacturing Engineering, at Manipal Institute of Technology, Manipal Academy of Higher Education, Manipal, India. His research interests include refrigeration and air conditioning, desiccant based dehumidification and humidification, Engine combustion, Alternate fuels, pollution.
References
- Ahmed, E. M., O. Abaas, M. Ahmed, and M. R. Ismail. 2011. “Performance Evaluation of Three Different Types of Local Evaporative Cooling Pads in Greenhouses in Sudan.” Saudi Journal of Biological Sciences 18 (1): 45–51. doi:https://doi.org/10.1016/j.sjbs.2010.09.005.
- Alam, M. F., A. S. Sazidy, A. Kabir, G. Mridha, N. A. Litu, and M. A. Rahman. 2017. “An Experimental Study on the Design, Performance and Suitability of Evaporative Cooling System Using Different Indigenous Materials.” In AIP Conference Proceedings (Vol. 1851, p. 020075). Melville, NY, USA: AIP Publishing LLC. DOI:https://doi.org/10.1063/1.4984704.
- Al-Sulaiman, F. 2002. “Evaluation of the Performance of Local Fibers in Evaporative Cooling.” Energy Conversion and Management 43 (16): 2267–2273. doi:https://doi.org/10.1016/S0196-8904(01)00121-2.
- Arshad, M. O. 2017. “Optimization of Process Parameters of Direct Evaporative Cooling Using Khus Material by Taguchi Method.” In International Research Journal of Engineering and Technology (IRJET) 4: 1508–1511.
- Cazzaniga, E., L. Colombo, and S. De Antonellis. 2019. “Preliminary Experimental and Numerical Analysis of a Silica Gel Packed Bed Humidification System.” In 13th REHVA World Congress, CLIMA 2019 (Vol.111, pp. 1–6). Bucharest, Romania: EDP Sciences. DOI:https://doi.org/10.1051/e3sconf/201911106044.
- Chantana, C. 2019. “A Cooling System for A Mushroom House for Use in the Upper Central Region Climate of Thailand.” Naresuan University Journal: Science and Technology (NUJST) 27 (3): 10–19.
- Chiranjeevi, C., and T. Srinivas. 2017. “November. Design and Development of an Air Humidifier Using Finite Difference Method for a Solar Desalination Plant.” In Materials Science and Engineering Conference Series (Vol. 263, p. 062041), Vellore, India. DOI: https://doi.org/10.1088/1757-899X/263/6/062041.
- Dhakulkar, K. T., M. V. Hinge, M. S. Kolhe, M. R. Chaudhari, and M. S. Mahalle. (2018). “An Experimental Analysis of Direct Evaporative Cooler by Changing Its Cooling Pads.”
- Dhamneya, A. K., S. P. S. Rajput, and A. Singh. 2017. “Experimental Performance Analysis of Alternative Cooling Pad Made by Agricultural Waste for Direct Evaporative Cooling System.” International Journal of Mechanical Engineering and Technology 8: 7.
- Dhamneya, A. K., S. P. S. Rajput, and A. Singh. 2018. “Thermodynamic Performance Analysis of Direct Evaporative Cooling System for Increased Heat and Mass Transfer Area.” Ain Shams Engineering Journal 9 (4): 2951–2960. doi:https://doi.org/10.1016/j.asej.2017.09.008.
- Doğramacı, P. A., S. Riffat, G. Gan, and D. Aydın. 2019. “Experimental Study of the Potential of Eucalyptus Fibres for Evaporative Cooling.” Renewable Energy 131: 250–260. doi:https://doi.org/10.3390/buildings9110224.
- Haruna, I. U., L. L. Akintunji, B. S. Momoh, and M. I. Tikau. 2014. “Theoretical Performance Analysis of Direct Evaporative Cooler in Hot and Dry Climates.” Int. J. Sci. Technol. Res 3 (4): 193–197.
- Hassabou, A., M. Spinnler, and W. Polifke. 2014. “The Role of Conductive Packing in Direct Contact Humidification-dehumidification Regenerators-part I: Theoretical Analysis.” International Journal of Advanced Research in Engineering and Technology (IJARET) 5 (12): 126–138.
- Inamdar, S. J., and J. P. Akshay Kale. 2019. “Performance Enhancement of Evaporative Cooling by Using Bamboo.” In International Journal of Engineering and Advanced Technology (IJEAT) 8: 856–860. doi:https://doi.org/10.35940/ijeat.F1161.0886S19.
- Jain, J. K., and D. A. Hindoliya. 2011. “Experimental Performance of New Evaporative Cooling Pad Materials.” Sustainable Cities and Society 1 (4): 252–256. doi:https://doi.org/10.1016/j.scs.2011.07.005.
- Kim, N. H. 2017. “Moisture Transfer and Pressure Drop of Humidifying Elements Made of Non-woven Fabric (Rayon/pet).” Journal of Mechanical Science and Technology 31 (6): 3075–3082. doi:https://doi.org/10.1007/s12206-017-0551-0.
- Kumar, S., J. Singh, J. Siyag, and S. Rambhatla. 2020. “Potential Alternative Materials Used in Evaporative Coolers for Sustainable Energy Applications: A Review.” International Journal of Air-Conditioning and Refrigeration 2030006. doi:https://doi.org/10.1142/S2010132520300062.
- Laknizi, A., M. Mahdaoui, A. B. Abdellah, K. Anoune, M. Bakhouya, and H. Ezbakhe. 2019. “Performance Analysis and Optimal Parameters of a Direct Evaporative Pad Cooling System under the Climate Conditions of Morocco.” Case Studies in Thermal Engineering 13: 100362. doi:https://doi.org/10.1016/j.csite.2018.11.013.
- Lal Basediya, A., D. V. K. Samuel, and V. Beera. 2013. “Evaporative Cooling System for Storage of Fruits and vegetables - a Review.” Journal of Food Science and Technology 50 (3): 429–442. doi:https://doi.org/10.1007/s13197-011-0311-6.
- Malli, A., H. R. Seyf, M. Layeghi, S. Sharifian, and H. Behravesh. 2011. “Investigating the Performance of Cellulosic Evaporative Cooling Pads.” Energy Conversion and Management 52 (7): 2598–2603. doi:https://doi.org/10.1016/j.enconman.2010.12.015.
- Mehere, S. V., K. P. Mudafale, and S. V. Prayagi. 2014. “Review of Direct Evaporative Cooling System with Its Applications.” International Journal of Engineering Research and General Science 2 (6): 995–999.
- Nada, S. A., A. Fouda, M. A. Mahmoud, and H. F. Elattar. 2019. “Experimental Investigation of Energy and Exergy Performance of a Direct Evaporative Cooler Using a New Pad Type.” Energy and Buildings 203: 109449. doi:https://doi.org/10.1016/j.enbuild.2019.109449.
- Ndukwu, M. C., and S. I. Manuwa. 2014. “Review of Research and Application of Evaporative Cooling in Preservation of Fresh Agricultural Produce.” International Journal of Agricultural and Biological Engineering 7 (5): 85–102.
- Niyomvas, B., and B. Potakarat. 2013. “Performance Study of Cooling Pads.” In Advanced Materials Research (Vol.664, pp. 931–935). Kapellweg, Switzerland: Trans Tech Publications.
- Oueslati, A., A. Hannachi, and M. Elmaaoui. 2015. “Effect of Air Humidification on the Pumping Efficiency of Water in a Packed Column Humidifier.” Energy Procedia 74: 1381–1393. doi:https://doi.org/10.1016/j.egypro.2015.07.784.
- Patel, D. J., and M. J. Patel. 2018. “Review of Design, Development and Performance of Humidification- Dehumidification Desalination System.” In International Journal for Research Trends and Innovation 2 (4): 227–231.
- Patel, P. G., A. R. Patel, and N. D. Patel. 2016. “Patel B I. Development of Humidification Chamber with the Help of Solar Circular Collector for Close Water Open Air System (CWOA) Humidification Dehumidification Process: A Review.” In International Journal of Advance Engineering and Research Development 3: 552–561.
- Rawangkul, R., J. Khedari, J. Hirunlabh, and B. Zeghmati. 2008. “Performance Analysis of a New Sustainable Evaporative Cooling Pad Made from Coconut Coir.” International Journal of Sustainable Engineering 1 (2). doi:https://doi.org/10.1080/19397030802326726.
- Reddy, V. T., and I. Prasanna. 2015. “Design and Working Model of Humidifier with Evaporative Cooling Pads.” In International Journal & Magazine of Engineering, Technology, Management and Research 2: 453–460.
- Roshan, R., and U. Parashar. 2015. “Comparative Analysis of Efficiency of Evaporative Air Cooler with Two Different Cooling Pad Material.” In SSRG International Journal of Thermal Engineering 1: 18–21.
- Salins, S. S., S. Siddiqui, S. K. Reddy, and S. Kumar. 2020. “Parametric Analysis for Varying Packing Materials & Water Temperatures in a Humidifier.” In International Conference on Fluid Flow, Heat and Mass Transfer (pp. 196–197), Niagara Falls, Canada. DOI: https://doi.org/10.11159/ffhmt20.196.
- Sampath, S. S., S. Kumar, and S. K. Reddy. 2020. “Influence of Different Desiccants, Flow Type and Packings on the Liquid Desiccant Dehumidification System: A Review.” International Journal of Air-Conditioning and Refrigeration 28 (1): 2030002. doi:https://doi.org/10.1142/S2010132520300025.
- Sharma, A., M. Kumar, R. Ranjan, and A. A. Krishnan. 2016. “Conversion of Dessert Cooler into Low Cost Air Conditioner Using Peltier Module.” International Journal of Research in Engineering and Technology 5: 347–352.
- Vala, K. V., M. Makwana, and N. Sagarika. 2019. “Validation of Evaporative Cooling System Using CFD Analysis.” In International Journal of Current Microbiology and Applied Sciences 8: 393–399. doi:https://doi.org/10.20546/ijcmas.2019.803.049.
- Velasco-Gómez, E., A. Tejero-González, J. Jorge-Rico, and F. J. Rey-Martínez. 2020. “Experimental Investigation of the Potential of a New Fabric-Based Evaporative Cooling Pad.” Sustainability 12 (17): 7070. doi:https://doi.org/10.3390/su12177070.
- Warke, D. A., and S. J. Deshmukh. 2017. “Experimental Analysis of Cellulose Cooling Pads Used in Evaporative Coolers.” Int. J. Energy Sci. Eng 3 (4): 37–43.
- Wavdekar, R. V., R. Z. Katre, A. Yadav, S. Kulkarni, and M. Sose. 2017. “Experimentation on Cooling Tower: Material Balance.” Efficiency and Packed Height in International Journal of Research and Review 4 (1): 10–13.
- Yash, R., D. Bhosal, G. K. N. Gandhi, and T. S. Gandhi. 2017. “Performance Improvement Techniques for Evaporative Air Cooler - A Review.” In International Journal of Engineering Research & Technology 6: 379–382. doi:https://doi.org/10.17577/IJERTV6IS030367.