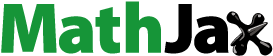
ABSTRACT
In the present research work, the performance, combustion and emission characteristics of compression ignition engine fuelled 22 different biodiesels categorised as (first, second, third generation, waste oil, and animal oil) biodiesel (B100) are evaluated numerically and compared with diesel fuel. Diesel-RK, a full-thermodynamic cycle engine analysis tool was used to carry out the numerical analysis. The engine power, fuel consumption, ignition delay, maximum cylinder pressure, oxides of nitrogen (NOx), and carbon dioxide (CO2) emission were investigated at four different engine operating loads. Power output was observed to be higher for Corn oil biodiesel, while Jatropha oil biodiesel produced lower fuel consumption among all other biodiesel. 9.1% increase in-cylinder peak pressure was found for waste transformer oil biodiesel than diesel, while ignition delay was found to be lowest for Rapeseed oil BD, Rice bran oil BD among all other biodiesel. The NOx emissions were higher for biodiesel by 30–32%, while CO2 emissions were reduced by 10–12% compared to diesel. The physicochemical properties of biodiesel were responsible for the diverse characteristics of the engine.
KEYWORDS:
1. Introduction
The demand for liquid energy sources, especially petroleum fuels, is high due to rapid development and progress in the industry and automobile sector. Diesel and gasoline are the most widely used fuels in the transportation sector (Covert, Greenstone, and Knittel Citation2016). However, large-scale consumption of these fuels has caused severe environmental issues, such as climate change and global warming (Outlook Citation2012). There has been increased interest in renewable and cleaner sources of energy for the transportation sector to tackle these issues. This critical phenomenon enforces scientists, researchers, policymakers, and engineers to accelerate and emphasise their efforts to search for alternative and renewable fuels. As a result, many leading-edge studies reported on several forms of fuel sources and their usage. Research and development are being carried out worldwide to develop alternative fuels for the compression ignition engines that can deliver the same performance vis-à-vis diesel fuels while bringing down the tailpipe emissions.
One such alternative for the conventional diesel fuel is biodiesel, a renewable fuel that can meet engine power requirements and reduce emissions. Biodiesel has attained considerable attention as an alternative renewable fuel for compression ignition. From the 1980s the biodiesel has been brought into usage in diesel engines as a green fuel. Biodiesel, knows as fatty acid methyl ester (FAME), is produced from any sources which have oil content in it. Biodiesel is generally classified according to the feedstocks used for its production, viz. first generation, second generation, third generation (Naik et al. Citation2010; Ben Hassen Trabelsi et al. Citation2018; Nautiyal, Subramanian, and Dastidar Citation2014). The first generation consists of feedstocks, such as edible oil and food crops, such as soyabean oil, peanut oil, rapeseed oil, etc. The second-generation consists of feedstocks or seeds which are non-edible, such as Karanja oil, Jatropha oil, etc. The third generation is the latest biodiesel feedstock generation, which includes algae, biomass as a feedstock for biodiesel production. At present, most biodiesel is produced from the waste cooking oil collected from restaurants or households; waste cooking (Wu et al. Citation2009) is currently the potential feedstock for biodiesel production due to availability on a large scale.
Studies have proved that biodiesel has excellent emission-reducing quality due to its superior chemical composition vis-à-vis diesel fuel (Yilmaz and Morton Citation2011). Biodiesel properties such as oxygen content, high cetane number, and flash point make biodiesel a suitable alternative to conventional diesel. Biodiesel is also known to provide better thermal efficiency than diesel fuel (Agarwal and Dhar Citation2013). Biodiesel, which is index as ‘B,’ can be used in pure form (B100) or blended with diesel. The fuel properties such as higher cetane number, additional oxygen content, and lower Sulphur describe biodegradable, cleaner combusting, and relatively less exhaust emission profiles of biodiesel.
The engine’s experimental testing is time-consuming and expensive due to its fuel usage, technical requirement, and workforce. Numerical modelling of engines to predict its performance is an effective method that can give insights into various factors that govern the engine performance, combustion, and emissions characteristics. Attempts have been made to investigate the performance, emissions, and combustion characteristics numerically. (Al-Dawody and Bhatti Citation2013) analysed the NOx formation for soyabean oil methyl ester in and CIDI diesel engine using numerically using simulation software Diesel-RK. The numerical and experimental had a good correlation with each other. A similar simulation tool was used by (Rajak and Verma Citation2018) to study engine combustion and performance characteristics numerically by varying compression ratio. Various other researchers have tried to simulate the engine characteristics numerically for different biofuels (Yilmaz Citation2012; Paul, Datta, and Mandal Citation2014).
Many literatures are available, which signifies the engine characteristics fuelled with biodiesel studied experimentally and numerically, which emphases primarily on available fuel from any generation of biodiesel, that is, first, second or third. The aim of the present study is to evaluate the performance, combustion and emission characteristics of compression ignition engine fuelled with diesel and biodiesels (B100) (1st, 2nd, 3rd generations, waste oils and animal oils) produced from different generations. Diesel-RK, the full thermodynamic engine analysis numerical tool, is used to analyse the engine characteristics. Engine characteristics such as power output, fuel consumption, maximum cylinder pressure, ignition delay period, NOx and CO2 emission were compared for biodiesel and diesel fuels.
2. Biodiesel properties and numerical tool
In the present study, the performance, combustion, and emission characteristics of compression ignition diesel engine fuelled with 22 different biodiesels (B100) are evaluated numerically. According to its feedstock, these 22 different biodiesels are categorised as first-generation biodiesel, second-generation biodiesel, third-generation biodiesel, biodiesel from waste oils, and biodiesel from animal oils for biodiesel production. The properties of conventional diesel fuel are measured as per ASTM D6751 standards. The physicochemical properties of this biodiesel were referred to from previous works and are summarised in the below. All the biodiesel are produced using transesterification reaction (Aransiola et al. Citation2014), the popular biodiesel production method. The properties of biodiesel vary depending upon the raw oil or feedstocks. The biodiesels are made up of triglycerides with complex and branched molecular structure. As a result of this the biodiesels have high viscosity. Biodiesels have oxygen molecule in their structure and hence this improves the combustion efficiency of biodiesel as compared to diesel. However, the additional presence of oxygen causes the reduction in calorific value. Biodiesel fuels consist of five major fatty acid methyl ester which are, palmitic (C16:0), stearic (C18:0) which are saturated fatty acids and oleic (C18:1), linoleic (C18:2) and linolenic (C18:3). The fatty acid composition of biodiesel varies depending upon the feedstock used for production. The fatty acid composition has significant effect of various properties of biodiesel and effect the engine performance and emission levels. The fatty acid composition of biodiesel used in present study is tabulated in .
Table 1. Properties of first, second, third generation, waste oils and animal oil biodiesels
Table 2. Fatty acid composition of first, second, third generation, waste oils and animal oil biodiesels
The cetane number of biodiesels depends upon the feedstock used, however, the fatty acid composition also contributes to the ignition quality of biodiesel. Increase in unsaturated fatty acid compounds such as linoleic (C18:2) and linolenic (C18:3) acids decrease the cetane number of fuels which results in poor combustion. Biodiesel with high saturated fatty acids such as palmitic and stearic acids have high cetane number. It is reported that the cetane number increase with increase in chain length and decreases with increase in number of double bonds (Kathirvelu et al. Citation2017). The cetane number of oleic acid (C18:1) is observed to be higher than linoleic acid (C18:2) which causes reduced ignition delay. The calorific value of the biodiesel is also related to the fatty acid composition. The calorific value of biodiesel increases with increase in chain length, but decreases with increase in unsaturation fatty acid compounds. The oleic acid (C18:1) fatty compounds have higher calorific value than linoleic (C18:2) and linolenic (C18:3) compounds. Again, the calorific value increases with increasing the carbon number in ester molecule. The density of biodiesel is also function of fatty acid composition. The decreases with decreasing chain length and increasing double bonds. Viscosity of biodiesel increase with increasing the unsaturation of fatty acid compounds and is also related to the configuration of the chain structure and double bonds. Biodiesel with less branching strucutre has lower viscosity which limits the interaction of carbon chains.
Thus, biodiesel with high saturation compounds shortens the ignition delay time; however, highly saturated compounds like palmitic (C16:0), stearic (C18:0) and oleic (C18:1) increases the viscosity which results in poor air-fuel mixing and hence the combustion efficiency. While linoleic (C18:2) and linolenic (C18:3) favours better air-fuel mixing but can lead to high NOx levels (Graboski and McCormick Citation1998). Thus, balance of fatty acid compounds is essential for superior engine performance and emissions.
The oxidation stability (hrs) represents the resistance of material to the oxidation reaction when it comes in contact with air or other materials. The oxidation of biodiesel is one of the major issues for automotive application. The oxidation of biodiesel depends upon its fatty acid composition. The oxidation rate of biodiesel is dependent on the number and position of the double bonds of fatty acids. The oxidation ability is inversely proportional to the molecular weight and number of carbon double bonds. The allylic position equivalents (APE) and bis-allylic position (BAPE) in fatty acids are susceptible to oxidation. The oxidation stability was predicted from fatty acid composition. It is seen that oxidation stability of biodiesel from animal oils are higher than first and second biodiesel. Since first and second generation biodiesel contains a greater number of double bonds, they are likely to oxidise at faster rate.
2.1 Diesel-RK
Open-source code Diesel-RK, a full-cycle thermodynamic simulation tool designed for engine analysis, is used to analyse the engine performance, emission, and combustion. Diesel-RK operates on a multi-zone model. It is accompanied by an advanced mixture and combustion model, along with multi-parameter optimisation (Kuleshov Citation2006). It also considers the various fuel injection characteristics, such as spray, dispersion, spray formation, interaction, swirl, and orientation. The initial boundary conditions used in the numerical analysis are given in the . Detailed kinetic mechanism and Zeldovich’s mechanism are used to evaluate the nitrogen and other emissions given in . The fuel spray model and its characteristics zone considered in Diesel-RK are shown in the . A specific condition is defined for each zone to capture the evaporation and burning of fuel.
Table 3. Initial and boundary conditions
Table 4. Numerical models used in Diesel-RK (Kuleshov Citation2007)
2.2 Diesel-RK tool validation
The numerical results from Diesel-RK software are validated with the experimental results of (Gnanasekaran, Saravanan, and Ilangkumaran Citation2016) and (Rajak and Verma Citation2019). The engine parameters and engine operating conditions used in the numerical study were similar to those used in the experimental study and are given in the . The engine testing was carried out as per IS:10,000 standards for engine testing (Indian standard IS: 10,000, 1980). The engine speed, injection timing, and nozzle diameter were set to 1500 rpm, 23°bTDC, and 0.25 mm for validation purposes. In-cylinder pressure, BTE, EGT, and MRPR were validated with those obtained in the experimental study shown in the . The numerical results show good agreement with experimental results. The percentage error for BTE, EGT, and MRPR emissions at 100% engine load were 4.16%, 1.83%, and 6.69% compared to experimental results. In-cylinder pressure also shows reasonable agreement with numerical and experimental data. Thus, Diesel-RK can be used as numerical tool for the performance analysis of diesel engine fuelled with biodiesels. Experimentation involves use of different instruments to quantify different parameters. The measurement accuracy and performance may vary depending on the experimental and operating environment which may lead to uncertainity due to random or fixed error. The uncertainity associated with the various parameters are represented in .
Table 5. Engine parameters
Table 6. Uncertainity associated with experimental parameters
3. Results and discussion
3.1 Engine power
represents the engine power output for different biodiesels. The power output increases with increase in load due to the increased fuel supply for all the biodiesel. Also, amongst all the test fuels, diesel’s power output was maximum due to its superior combustion properties vis-à-vis biodiesels. The power generated for first-generation biodiesel at 100% load was 3.545, 4.209, 3.91, 4.162, 4.398, 3.836, and 3.936 kW for Coconut oil BD, Corn oil BD, Palm oil BD, Soyabean oil BD, Sunflower oil BD, Rapeseed oil BD, Rice bran oil BD, respectively, while that for diesel it was 4.416 kW. Engine power output was maximum for biodiesel made from corn oil, followed by sunflower oil and soyabean oil, due to its excellent heating value compared to other first-generation biodiesels.
The biodiesel from second-generation feedstocks resulted in maximum power output amongst all the other biodiesel under study. The power output for second-generation biodiesel feedstocks at 100% load was 4.23, 3.17, 3.74, 4.268, 4.20, 3.42 kW for Jatropha oil BD, Karanja oil BD, Castor oil BD, Mahua Indica oil BD, Jojoba oil BD, and Tamarind seed oil BD. Biodiesel from Jatropha oil showed maximum power at all the engine operating loads. A marginal decrease of 4% in power output was found for Jatropha oil biodiesel. For the third-generation feedstock, the power output was 4.01 kW, and 3.00 kW for algae oil BD and waste coffee beans oil BD at 100% engine load.
Even though the calorific value of waste coffee bean oil (5.16cSt) BD was superior to algae oil BD (2.95 cSt), the higher viscosity lead to poor spray, which resulted in improper combustion hampering the power output. The higher calorific values of the waste oil biodiesel aided in increase combustion temperature and pressure, thereby giving higher power output. At 100% engine load, the power output was observed to be 4.23 kW, 4.36 kW, and 4.31 kW for waste cooking oil BD, waste transformer oil BD, and soyabean acidic oil BD, respectively. The engine output power for animal oil biodiesel was found to be 3.69, 3.775, 4.21, 4.09 kW for Lard oil BD, Chicken fat oil BD, Fish oil BD, and beef fat oil BD.
3.2 Specific fuel consumption
Engine fuel consumption is an essential parameter in engine testing because it is employed as a direct measure of volumetric fuel savings. The shows the fuel consumption for the different generations of biodiesel. The fuel consumption for diesel was found to be less compared to all other biodiesel under study. The higher consumption of fuel in the case of biodiesels is owing to its enhanced viscosities and densities (Yilmaz Citation2011). Many studies have reported that to produce an equivalent amount of heat during the combustion vis-à-vis diesel fuel, the extra quantity of biodiesel must be supplied in the combustion chamber, increasing fuel consumption. Among the first-generation biodiesel, the sunflower oil BD showed the least fuel consumption, followed by the corn oil and Palm oil. At 100% engine load, the values of fuel consumption in were 0.301, 0.266, 0.298, 0.289, 0.260, 0.320, and 0.296 kg/kWh for Coconut oil BD, Corn Oil BD, Palm Oil BD, Soyabean Oil BD, Sunflower oil BD, Rapeseed oil BD, Rice bran oil BD, respectively, while that for diesel it was 0.241 kg/kWh. Thus, the lower heating value, higher density, and viscosity have a primary effect on engine fuel consumption. For the second-generation biodiesel, Jatropha oil BD showed lesser fuel consumption than the other biodiesel. At 100% load, the fuel consumption was 0.243, 0.269, 0.334, 0.310, 0.279, and 0.334 kg/kWh for Jatropha oil BD, Karanja oil BD, Castor oil BD, Mahua Indica oil BD, Jojoba oil BD and Tamarind seed oil BD. This variation in consumption of fuel for different biodiesel may be attributed to the different carbon-chain lengths or the process used to produce biodiesel, which impacts fuel consumption. The fuel consumption for the third-generation biodiesel at 100% engine load was found to be 0.305 kg/kWh and 0.312 kg/kWh. The higher viscosity (5.16csT) of waste coffee bean oil was the reason for the higher fuel consumption.
Biodiesel production from waste transformer oil showed lower fuel consumption vis-à-vis waste cooking oil and soyabean acidic oil. Since the fuel injection pump metres, the fuel on a volumetric basis, the denser biodiesel showed increased fuel consumption. The fuel consumption was 0.274, 0.246, and 0.266 kg/kWh for waste cooking oil BD, Waste transformer oil, and soyabean acidic oil, respectively. Biodiesel made from animal oils has higher densities, resulting in increased fuel consumption compared to all other biodiesel. Lard oil BD had the highest fuel consumption of 0.313 kg/kWh at 100% engine load, while Chicken fat oil BD, Fish oil BD, and beef fat oil BD showed fuel consumption of 0.306, 0.274, and 0.282 kg/kWh at 100% engine load.
3.3 Maximum cylinder pressure
represents the MCP for different biodiesel. The first generation of biodiesel had comparable maximum cylinder pressure with diesel. The MCP increased with an increase in engine load for all the biodiesels. The viscosity and surface tension of biodiesel impact droplet formation, increasing its overall size. The MCP was found to be 78.92, 81.50, 72.11, 76.58, 77.31, 65.42 and 65.98 bars for Coconut oil BD, Corn oil BD, Palm oil BD, Soyabean oil BD, Sunflower oil BD, Rapeseed oil BD, Rice bran oil BD respectively at 100% of engine load. Jatropha BD showed higher cylinder pressure compared to other second-generation biodiesel. Karanja and Mahua Indica BD showed near about MCP vis-à-vis diesel. The peak pressure at 100% engine load was found to be 80.11, 79.74, 70.63, 77.92, 79.44 and 74.4 bars for Jatropha oil BD, Karanja oil BD, Castor oil BD, Mahua Indica oil BD, Jojoba oil BD and Tamarind seed oil BD. The higher ignition delay in biodiesel also reduces combustion pressure by delaying the combustion of the accumulated fuel in the cylinder. The third-generation biodiesel, algae oil BD, and waste coffee beans oil BD showed 8% and 16.24% lesser MCP vis-à-vis diesel at 100% engine load.
One of the striking findings was the 9.1% increase in MCP for waste transformer oil BD than diesel, due to its high calorific value and lesser density. The peak cylinder pressure was found to be 76.31, 89.20 and 84.67 bars for waste cooking oil BD, waste transformer oil BD, and Soyabean acidic oil BD at 100% engine load. Among the animal oil biodiesel, fish oil resulted in higher cylinder pressures than other animal oil biodiesel. The peak pressure values were 71.35, 72.08, 76.46 and 72.09 bars for lard oil BD, chicken fat oil BD, fish oil BD, and beef fat oil BD at 100% engine load.
3.4 Ignition delay period
The represents the ignition delay period for different biodiesel. The ignition delay in a diesel engine is the time difference between the start of injection and the start of combustion. The ignition delay period is the strong function of the fuel’s cetane number. Fuel with a lower cetane number has a more extended ignition delay period, which increases the overall time required for fuel combustion. The ignition delay period for all the biodiesel decreased with an increase in load, due to the higher gas temperatures in the cylinder at higher loads reducing the physical delay period. All the first-generation biodiesel except corn oil BD showed a lower ignition delay period vis-à-vis diesel. The biodiesel’s lower compressibility can be the reason for it, which causes shorter ignition delay. The ignition delay period was 12.50°, 15.44°, 8.02°, 11.52°, 13.07°, 3.66°, 3.04° for Coconut oil BD, Corn Oil BD, Palm Oil BD, Soyabean Oil BD, Sunflower oil BD, Rapeseed oil BD, Rice bran oil BD at 100% engine load while that of diesel it was 14.29°. Biodiesel contains a smaller fraction of diglycerides with high boiling points compared to diesel. But chemical reactions occur during the injection of biodiesel at high temperatures, breakdown the high molecular esters, forming the gases of lower molecular weight. This low molecular gas causes quick gasification of the lighter oil in the periphery of the spray, resulting in a jet that spreads out. Due to this, biodiesel’s volatile compounds ignite earlier and reduce the ignition delay period (Shahabuddin et al. Citation2013; Aldhaidhawi, Chiriac, and Badescu Citation2017). The ignition delay period in second-generation biodiesel was observed to be 11.21°, 12.07°, 14.31°, 13.31°, 9.21°, 12.95° at 100% engine load. The additional oxygen content in biodiesel was also the reason for the shorter ignition delay period of biodiesel. Third-generation biodiesel algae oil BD and waste coffee bean oil BD showed a higher ignition delay period vis-à-vis diesel at a lower engine load of 25%. This may be due to the increase in fuel viscosity resulting in poor mixing and atomisation.
The waste oil biodiesel showed the ignition delay period of 13.52°, 12.38°, 15.78° for waste cooking oil BD, waste transformer oil BD, and soyabean acidic oil BD at 100% engine operating load. All the animal oil biodiesel showed shorter ignition delay at all the engine loads compared to diesel. The cetane number, inferior compressibility, and fatty acid structure were accountable for the shorter ignition delay for animal oil biodiesels. The ignition delay period was 10.94°, 12.72°, 12.95°, 10.25° for lard oil BD, chicken fat oil BD, fish oil BD, and beef fat oil BD, respectively, at full load.
3.5 NOx emissions
Out of total engine exhaust emissions, NO2 accounts for 10–30% of total oxides of nitrogen emissions. The mechanism responsible for NOx formation is known as Zeldovich mechanism. During the combustion nitrogen enters the combustion chamber via. air intake and becomes the major source of NOX emissions, which is also known as thermal NOX. The atmospheric nitrogen which is triple bonded acts as inert gas but during the presence of high temperature the triple bond splits and undergo series of chemical reaction with oxygen and forms NO2. The high temperature due to combustion of fuel in cylinder of engine favours the N2 and O2 chemical reactions such as:
The formation and propagation of thermal NOX depends upon the various factors:
Combustion temperature.
The air-fuel equivalence ratio as it controls the oxygen presence in combustion chamber. A low air-fuel ratio is known to produce less NOx emissions
The retention time or the duration of reacting gases in combustion chamber. Shorter retention time lesser is the NOx generation.
Amount of oxygen present in fuel
represents NOx emissions for different biodiesels. For first-generation biodiesel, the NOx emissions were higher for corn oil BD, followed by soyabean oil BD and Palm oil BD. The NOx emission values at 100% engine load were found to be 5.45 g/kWh for diesel while it was 9.47, 9.61, 8.49, 7.80, 5.21, 7.97 and 6.20 g/kWh for Coconut oil BD, Corn Oil BD, Palm Oil BD, Soyabean Oil BD, Sunflower oil BD, Rapeseed oil BD, Rice bran oil BD, respectively. Even though a single factor cannot quantify the rise in NOx emissions for biodiesel, the increase in combustion temperature, and longer combustion duration are likely reasons that boost the NOx formation (Xue and Grift Citation2011). The second-generation biodiesels showed higher NOx emissions than all other biodiesel. The additional oxygen content may promote the combustion, and with an additional quantity of fuel, there may be an enhancement in the air–fuel ratio that might augment the flame temperatures, leading to magnifying the NOx formation. The NOx emissions were 5.45, 12.34, 14.34, 12.87, 15.72, 17.78, and 17.32 g/kWh for Jatropha oil BD, Karanja oil BD, Castor oil BD, Mahua Indica oil BD, Jojoba oil BD, and Tamarind seed oil BD at 100% load on the engine. Algae oil BD and waste coffee oil BD had the NOx emission lower than first-generation biodiesel.
Waste coffee beans oil BD showed 8–9% lesser emission than algae oil biodiesel. The values of NOx emission for algae oil BD and waste coffee beans oil BD were 11.40 g/kWh and 10.74 g/kWh at 100% engine load. The biodiesel with a higher cetane number deteriorates the combustion by shorter ignition delay and lower combustion temperature, thereby decreasing the NOx formation. Waste cooking oil BD showed almost a 50% reduction in NOx emission compared to waste transformer oil BD and soybean acidic oil BD, which was remarkable. This may be associated with the higher viscosity of the waste transformer oil BD and soyabean acidic oil BD. Fuels with higher viscosity influence the spray formation due to larger droplets, poor atomisation, and poor combustion. The NOx emissions for a waste cooking oil BD, waste acidic oil BD and soyabean acidic oil BD were found to be 6.84, 15.11 and 11.82 g/kWh at 100% engine operating load. The NOx emissions for animal oil biodiesel were the least compared to all other biodiesel due to the high amount of saturated fatty acids. The iodine value of fuel also affects the NOx formation, the biodiesel derived from oil seeds or fishery oils was found to have higher iodine content, and hence NOx emissions were higher for such biodiesels. The higher the iodine index, the higher the number of bonds suitable for hydroperoxide reaction (Hoekman and Robbins Citation2012). The NOx values for lard oil BD, chicken fat oil BD, fish oil BD and beef fat oil BD were 2.68, 2.91, 5.92 and 5.42 g/kWh at 100% engine load.
Several techniques are adopted to mitigate the NOx emission with biodiesel as fuel, such as modifications in the fuel injection timings and exhaust gas recirculation, after exhaust systems being the popular ones. Apart from engine modifications and calibrations, various studies have reported using additives or fuel property improvers to reduce NOx emissions. However, long-term study is warranted to ensure biodiesel’s practical use as an engine fuel without harming the environment.
3.6 CO2 emissions
Detailed analysis of emissions from biodiesel was carried out by the EPA, in which it is conveyed that the carbon emissions reduced by 50% for biodiesel (B100) compared to diesel fuel. A general decreasing trend of carbon emission was observed for biodiesel in the present work, as shown in the . The carbon development in diesel engines is primarily controlled by the air-fuel equivalence ratio (Teoh et al. Citation2014). The additional oxygen present in biodiesel reduces the fuel-air mixture ratio, which lowers carbon emissions. In current work, the carbon emission reduced with an increase in engine operating load; this behaviour may be due to an increase in availability of oxygen at higher loads, which encouraged the complete combustion of biodiesel. The specific carbon dioxide emission at 100% engine load for Coconut oil BD, Corn Oil BD, Palm Oil BD, Soyabean Oil BD, Sunflower oil BD, Rapeseed oil BD, Rice bran oil BD were found to be 971.7, 760.66, 850.38, 824.93, 642.94, 913.88, and 801.25 g/kWh. Sunflower oil BD showed lower carbon dioxide emissions than all other first-generation biodiesel with a 20% reduction in emission vis-à-vis diesel fuel. Jatropha oil BD showed a 20% reduction in carbon emission, while Karanja oil BD and Castor oil BD reduced the carbon dioxide emission by 15% compared to diesel. Tamarind seed oil BD had a 26% reduction in carbon emission, while mahua indica oil BD and jojoba oil biodiesel had comparable diesel emissions. Algae oil BD and waste coffee beans oil BD had carbon dioxide emissions of 897.85 g/kWh and 841.34 g/kWh at 100% engine load. The formation of carbon emission is also related to the fuel density; the denser is the fuel higher is the carbon content; hence higher carbon emissions are observed. The biodiesel from waste oils showed comparable carbon emissions to diesel. The carbon dioxide emission was 732.06, 701.65 and 760.9 g/kWh for waste cooking oil BD, and waste acidic oil BD, and soyabean acidic oil BD, respectively, at 100% engine load.
A similar trend was observed for animal oil biodiesel, which showed an average of 8–10% reduction in carbon emission than diesel. The carbon emission values were 893.41, 873.74, 781.64 and 805.9 g/kWh for lard oil BD, chicken fat oil BD, fish oil BD, and beef fat oil BD at 100% engine load. Overall, the carbon emission is lower for biodiesel in context to conventional diesel fuel. However, the degree of emission reduction largely depends upon the types of feedstock, physiochemical properties of biodiesel, and the engine operating and calibration parameters.
4. Conclusion
Engine performance, combustion, and emission were evaluated for 22 different biodiesels by Diesel-RK numerical tool. The numerical results were validated with experimental findings from literature and were in good agreement with each other. The important conclusion drawn from the present work are as follows:
Biodiesel’s properties such as viscosity, density, calorific value and also fatty acid composition had significant effect on engine performance and emission levels.
An average drop of 5–10% was observed in engine power output when operated with biodiesel. Corn oil BD (4.209 kW), Jatropha oil BD (4.23 kW), algae oil BD (4.01), waste transformer oil BD (4.21 kW) and Fish oil BD (4.36 kW) resulted in maximum power output at 100% load.
The fuel consumption was slightly high for all the biodiesels at all the engine loads vis-à-vis diesel. Sunflower oil BD (0.260 kg/kWh), Jatropha oil BD (0.243 kg/kWh), algae oil BD (0.305 kg/kWh), waste transformer oil BD (0.246 kg/kWh) and fish oil BD (0.274 kg/kWh) resulted in lower fuel consumption.
Peak cylinder pressures for biodiesel were lower compared to diesel. Both viscosity and surface tension are co-related to fuel atomisation and combustion and reduce the in-cylinder pressure. An 9.1% increase in peak pressure was observed for waste transformer oil BD.
Almost all the biodiesels showed shorter ignition delays due to their higher cetane number than diesel.
An 30–32% enhancement in NOx emissions was observed for all the tested biodiesels vis-à-vis diesel due to its poor spray characteristics affecting the atomisation and combustion.
The overall, the carbon dioxide emission for all the biodiesel reduced by 10–12% in context to diesel fuel.
Based on the findings it is evident that engine performance and emission characteristics are greatly influenced by the feedstock used for biodiesel production. However, further research should address the techniques to reduce the engine NOx emissions when fuelled with biodiesel. Also, engine durability and lubricating oil degradation are the important aspects to be considered as a part of further research.
Disclosure of potential conflicts of interest
No potential conflict of interest was reported by the author(s).
Additional information
Notes on contributors
Vishal Sharad Kumbhar
Vishal Kumbhar is research scholar at symbiosis international university, Pune. His research area includes alternative fuels, IC engines and tribology.
Anand Pandey
Dr. Anand Pandey is working as a professor and head at the Mechanical Engineering Department, Symbiosis Institute of Technology, Symbiosis International Deemed University, Pune, Maharashtra, India. He has 25 years of research experience. He has a keen research interest in military equipment design and military vehicle performance enhancements, and he is associated with the defense research field for the last 20 years. His current research includes experimental as well as a numerical simulation on internal combustion engines, alternative fuels, and very large power (1000 HP) engines.
Anil Varghese
Anil Varghese is doctoral research scholar at symbiosis international university, Pune. His research area includes alternative fuels, multifuel engines.
Virendra Patil
Virendra Patil is doctoral research scholar at Savitribai Phule Pune University. His research area includes alternative fuels and IC engines.
References
- Agarwal, A. K., and A. Dhar. 2013. “Experimental Investigations of Performance, Emission and Combustion Characteristics of Karanja Oil Blends Fuelled DICI Engine.” Renewable Energy 52: 283–291. doi:https://doi.org/10.1016/j.renene.2012.10.015.
- Al-Dawody, M. F., and S. K. Bhatti. 2013. “Optimization Strategies to Reduce the Biodiesel NOx Effect in Diesel Engine with Experimental Verification.” Energy Conversion and Management 68: 96–104. doi:https://doi.org/10.1016/j.enconman.2012.12.025.
- Aldhaidhawi, M., R. Chiriac, and V. Badescu. 2017. “Ignition Delay, Combustion and Emission Characteristics of Diesel Engine Fueled with Rapeseed Biodiesel – A Literature Review.” Renewable and Sustainable Energy Reviews 73: 178–186. doi:https://doi.org/10.1016/j.rser.2017.01.129.
- Alves, S. M., F. K. Dutra-pereira, and T. C. Bicudo. 2019. “Influence of Stainless Stzeel Corrosion on Biodiesel Oxidative Stability during Storage.” Fuel 249: 73–79. doi:https://doi.org/10.1016/j.fuel.2019.03.097.
- Aransiola, E. F., T. V. Ojumu, O. O. Oyekola, T. F. Madzimbamuto, and D. I. O. Ikhu-Omoregbe. 2014. “A Review of Current Technology for Biodiesel Production: State of the Art.” Biomass & Bioenergy 61: 276–297. doi:https://doi.org/10.1016/j.biombioe.2013.11.014.
- Ben Hassen Trabelsi, A., K. Zaafouri, W. Baghdadi, S. Naoui, and A. Ouerghi. 2018. “Second Generation Biofuels Production from Waste Cooking Oil via Pyrolysis Process.” Renewable Energy 126: 888–896. doi:https://doi.org/10.1016/j.renene.2018.04.002.
- Covert, T., M. Greenstone, and C. R. Knittel. 2016. “Will We Ever Stop Using Fossil Fuels?” Journal of Economic Perspectives 30 (1): 117–138. doi:https://doi.org/10.1257/jep.30.1.117.
- Cunha, A., V. Feddern, M. C. De Prá, M. M. Higarashi, P. G. De Abreu, and A. Coldebella. 2013. “Synthesis and Characterization of Ethylic Biodiesel from Animal Fat Wastes.” Fuel 105: 228–234. doi:https://doi.org/10.1016/j.fuel.2012.06.020.
- Dhana Raju, V., P. S. Kishore, K. Nanthagopal, and B. Ashok. Conversion and Management 2014. “An Experimental Study on the Effect of Nanoparticles with Novel Tamarind Seed Methyl Ester for Diesel Engine Applications.” Energy 61: 276–297. doi:https://doi.org/10.1016/j.biombioe.2013.11.014.
- Dias, J. M., A.-F. MCM, and M. F. Almeida. 2009. “Production of Biodiesel from Acid Waste Lard.” Bioresource Technology 100 (24): 6355–6361. doi:https://doi.org/10.1016/j.biortech.2009.07.025.
- Ezekannagha, C. B., C. N. Ude, and O. D. Onukwuli. 2017. “Optimization of the Methanolysis of Lard Oil in the Production of Biodiesel with Response Surface Methodology.” Egyptian Journal of Petroleum 26 (4): 1001–1011. doi:https://doi.org/10.1016/j.ejpe.2016.12.004.
- Fadhil, A. B. 2013. “Biodiesel Production from Beef Tallow Using Alkali-Catalyzed Transesterification.” Arabian Journal for Science and Engineering 38 (1): 41–47. doi:https://doi.org/10.1007/s13369-012-0418-8.
- Gharehghani, A., M. Mirsalim, and R. Hosseini. 2017. “Effects of Waste Fish Oil Biodiesel on Diesel Engine Combustion Characteristics and Emission.” Renewable Energy 101: 930–936. doi:https://doi.org/10.1016/j.renene.2016.09.045.
- Gnanasekaran, S., N. Saravanan, and M. Ilangkumaran. 2016. “Influence of Injection Timing on Performance, Emission and Combustion Characteristics of a DI Diesel Engine Running on Fish Oil Biodiesel.” Energy 116: 1218–1229. doi:https://doi.org/10.1016/j.energy.2016.10.039.
- Graboski, M. S., and R. L. McCormick. 1998. “Combustion of Fat and Vegetable Oil Derived Fuels in Diesel Engines.” Progress in Energy and Combustion Science 24 (2): 125–164. doi:https://doi.org/10.1016/S0360-1285(97)00034-8.
- Haas, M. J., P. J. Michalski, S. Runyon, A. Nunez, and K. M. Scott. 2003. “Production of FAME from Acid Oil, a By-product of Vegetable Oil Refining.” Journal of the American Oil Chemists’ Society 80 (1): 97–102. doi:https://doi.org/10.1007/s11746-003-0658-4.
- Hoekman, S. K., and C. Robbins. 2012. “Review of the Effects of Biodiesel on NOx Emissions.” Fuel Processing Technology 96: 237–249. doi:https://doi.org/10.1016/j.fuproc.2011.12.036.
- Hoque, M. E., A. Singh, and Y. L. Chuan. 2011. “Biodiesel from Low Cost Feedstocks: The Effects of Process Parameters on the Biodiesel Yield.” Biomass & Bioenergy 35 (4): 1582–1587. doi:https://doi.org/10.1016/j.biombioe.2010.12.024.
- Kathirvelu, B., S. Subramanian, N. Govindan, and S. Santhanam. 2017. “Emission Characteristics of Biodiesel Obtained from Jatropha Seeds and Fish Wastes in a Diesel Engine.” Sustainable Environment Research 27 (6): 283–290. doi:https://doi.org/10.1016/j.serj.2017.06.004.
- Kirubakaran, M. 2018. “Arul Mozhi Selvan V. A Comprehensive Review of Low Cost Biodiesel Production from Waste Chicken Fat.” Renewable and Sustainable Energy Reviews 82: 390–401. doi:https://doi.org/10.1016/j.rser.2017.09.039.
- Kuleshov, A. S. “Use of Multi-zone DI Diesel Spray Combustion Model for Simulation and Optimization of Performance and Emissions of Engines with Multiple Injection.” SAE Tech. Pap., SAE International; 2006. doi: https://doi.org/10.4271/2006-01-1385.
- Kuleshov, A. S. “Multi-zone Di Diesel Spray Combustion Model and Its Application for Matching the Injector Design with Piston Bowl Shape.” SAE Tech. Pap., SAE International; 2007. doi: https://doi.org/10.4271/2007-01-1908.
- Kumar, A. N., P. S. Kishore, K. B. Raju, and N. Kasianantham “Engine Parameter Optimization of Palm Oil Biodiesel as Alternate Fuel in CI Engine.” 2019.
- Kumbhar, V., A. Pandey, A. Varghese, and S. Wanjari. 2020a. “An Overview of Production, Properties and Prospects of Tamarind Seed Oil Biodiesel as an Engine Fuel.” International Journal of Ambient Energy 1–9. doi:https://doi.org/10.1080/01430750.2020.1824946.
- Kumbhar, V., A. K. Pandey, A. Varghese, and S. Wanjari. 2020b. “Application of Biodiesel for 12-cylinder, Supercharged Military Combat Vehicle.” International Journal of Ambient Energy 1–7. doi:https://doi.org/10.1080/01430750.2020.1725632.
- Manigandan, S., P. Gunasekar, J. Devipriya, and S. Nithya. 2019. “Emission and Injection Characteristics of Corn Biodiesel Blends in Diesel Engine.” Fuel 235: 723–735. doi:https://doi.org/10.1016/j.fuel.2018.08.071.
- Mn, N., A. Ms, and M. A. Rahman “Waste Transformer Oil as an Alternative Fuel for Diesel Engine.” Procedia Eng., vol. 56, Dhaka, Bangladesh: Elsevier; 2013, p. 401–406. https://doi.org/https://doi.org/10.1016/j.proeng.2013.03.139.
- Mueanmas, C., and R. Nikhom. n.d. Energy AP-R, 2019 Undefined. Extraction and Esterification of Waste Coffee Grounds Oil as Non-edible Feedstock for Biodiesel Production. Elsevier.
- Naik, S. N., V. V. Goud, P. K. Rout, and A. K. Dalai. 2010. “Production of First and Second Generation Biofuels: A Comprehensive Review.” Renewable and Sustainable Energy Reviews 14 (2): 578–597. doi:https://doi.org/10.1016/j.rser.2009.10.003.
- Nakpong, P., and S. Wootthikanokkhan. 2010. “High Free Fatty Acid Coconut Oil as a Potential Feedstock for Biodiesel Production in Thailand.” Renewable Energy 35 (8): 1682–1687. doi:https://doi.org/10.1016/j.renene.2009.12.004.
- Nautiyal, P., K. A. Subramanian, and M. G. Dastidar. 2014. “Production and Characterization of Biodiesel from Algae.” Fuel Processing Technology 120: 79–88. doi:https://doi.org/10.1016/j.fuproc.2013.12.003.
- Outlook, B. “Energy Outlook 2030.” 2012.
- Pandey, A. K., and M. R. Nandgaonkar. 2011. “Experimental Investigation of the Effect of Esterified Karanja Oil Biodiesel on Performance, Emission and Engine Wear of a Military 160hp Turbocharged CIDI Engine.” Proceedings of World Congress Engineering 2011 WCE 2011. 3: 2075–2079. (Accessed 2 Dec 2020) https://doi.org/https://doi.org/10.4271/2010-01-1521
- Paul, G., A. Datta, and B. K. Mandal. 2014. “An Experimental and Numerical Investigation of the Performance, Combustion and Emission Characteristics of a Diesel Engine Fueled with Jatropha Biodiesel.” Energy Procedia 54, Elsevier Ltd, 455–467. doi:https://doi.org/10.1016/j.egypro.2014.07.288.
- Prasanna Raj Yadav, S., S. Cg, R. Vallinayagam, S. Vedharaj, and W. L. Roberts. 2015. “Fuel and Engine Characterization Study of Catalytically Cracked Waste Transformer Oil.” Energy Conversion and Management 96: 490–498. doi:https://doi.org/10.1016/j.enconman.2015.02.051.
- Puhan, S., N. Vedaraman, B. V. B. Ram, G. Sankarnarayanan, and K. Jeychandran. 2005. “Mahua Oil (Madhuca Indica Seed Oil) Methyl Ester as Biodiesel-preparation and Emission Characterstics.” Biomass & Bioenergy 28 (1): 87–93. doi:https://doi.org/10.1016/j.biombioe.2004.06.002.
- Rajak, U., and T. N. Verma. 2018. “Effect of Emission from Ethylic Biodiesel of Edible and Non-edible Vegetable Oil, Animal Fats, Waste Oil and Alcohol in CI Engine.” Energy Conversion and Management 166: 704–718. doi:https://doi.org/10.1016/j.enconman.2018.04.070.
- Rajak, U., and T. N. Verma. 2019. “Influence of Combustion and Emission Characteristics on a Compression Ignition Engine from a Different Generation of Biodiesel.” Engineering Science and Technology and International Journal 23 (1): 10–20. doi:https://doi.org/10.1016/j.jestch.2019.04.003.
- Raman, L. A., B. Deepanraj, S. Rajakumar, and V. Sivasubramanian. 2019. “Experimental Investigation on Performance, Combustion and Emission Analysis of a Direct Injection Diesel Engine Fuelled with Rapeseed Oil Biodiesel.” Fuel 246: 69–74. doi:https://doi.org/10.1016/j.fuel.2019.02.106.
- Saydut, A., S. Erdogan, A. Beycar, C. Kaya, and F. Aydin. 2016. “Process Optimization for Production of Biodiesel from Hazelnut Oil, Sunflower Oil and Their Hybrid Feedstock.” Fuel 183: 512–517. doi:https://doi.org/10.1016/j.fuel.2016.06.114.
- Shahabuddin, M., A. M. Liaquat, H. H. Masjuki, M. A. Kalam, and M. Mofijur. 2013. “Ignition Delay, Combustion and Emission Characteristics of Diesel Engine Fueled with Biodiesel.” Renewable and Sustainable Energy Reviews 21: 623–632. doi:https://doi.org/10.1016/j.rser.2013.01.019.
- Shameer, P. M., and K. Ramesh. 2017. “Experimental Evaluation on Performance, Combustion Behavior and Influence of In-cylinder Temperature on NOx Emission in a D.I Diesel Engine Using Thermal Imager for Various Alternate Fuel Blends.” Energy 118: 1334–1344. doi:https://doi.org/10.1016/j.energy.2016.11.017.
- Sharma, A., Y. Singh, N. K. Singh, and A. Singla. 2019. “Sustainability of Jojoba Biodiesel/diesel Blends for DI Diesel Engine Applications- Taguchi and Response Surface Methodology Concept.” Industrial Crops and Products 139: 111587. doi:https://doi.org/10.1016/j.indcrop.2019.111587.
- Sinha, S., and A. K. Agarwal “Performance Evaluation of a Biodiesel (Rice Bran Oil Methyl Ester) Fuelled Performance Evaluation of a Biodiesel (Rice Bran Oil Methyl Ester) Fuelled Transport Diesel Engine.” 2005. doi: https://doi.org/10.4271/2005-01-1730.
- Sinha, S., A. K. Agarwal, and S. Garg “Biodiesel Development from Rice Bran Oil : Transesterification Process Optimization and Fuel Characterization.” 2008;49:1248–1257. doi: https://doi.org/10.1016/j.enconman.2007.08.010.
- Teoh, Y. H., H. H. Masjuki, M. A. Kalam, M. A. Amalina, and H. G. How. 2014. “Effects of Jatropha Biodiesel on the Performance, Emissions, and Combustion of a Converted Common-rail Diesel Engine.” RSC Adv 4 (92): 50739–50751. doi:https://doi.org/10.1039/c4ra08464k.
- Tongcumpou, C., P. Usapein, and N. Tuntiwiwattanapun. 2019. “Complete Utilization of Wet Spent Coffee Grounds Waste as a Novel Feedstock for Antioxidant, Biodiesel, and Bio-char Production.” Industrial Crops and Products 138. doi:https://doi.org/10.1016/j.indcrop.2019.111484.
- Tripathi, S., and K. A. Subramanian. 2017. “Experimental Investigation of Utilization of Soya Soap Stock Based Acid Oil Biodiesel in an Automotive Compression Ignition Engine.” Applied Energy 198: 332–346. doi:https://doi.org/10.1016/j.apenergy.2017.02.057.
- Uslu, S., and M. Ayd “Eff Ect of Operating Parameters on Performance and Emissions of a Diesel Engine Fueled with Ternary Blends of Palm Oil Biodiesel/diethyl Ether/diesel by Taguchi Method” 2020;275. doi: https://doi.org/10.1016/j.fuel.2020.117978.
- Vellaiyan, S. 2020. “Combustion, Performance and Emission Evaluation of a Diesel Engine Fueled with Soybean Biodiesel and Its Water Blends.” Energy 201: 117633. doi:https://doi.org/10.1016/j.energy.2020.117633.
- Wu, F., J. Wang, W. Chen, and S. Shuai. 2009. “A Study on Emission Performance of A Diesel Engine Fueled with Five Typical Methyl Ester Biodiesels.” Atmospheric Environment 43 (7): 1481–1485. doi:https://doi.org/10.1016/j.atmosenv.2008.12.007.
- Xue, J., and T. E. H. A. Grift. 2011. “Effect of Biodiesel on Engine Performances and Emissions.” Renewable and Sustainable Energy Reviews 15 (2): 1098–1116. doi:https://doi.org/10.1016/j.rser.2010.11.016.
- Yilmaz, N. 2011. “Temperature-dependent Viscosity Correlations of Vegetable Oils and Biofuel-diesel Mixtures.” Biomass & Bioenergy 35 (7): 2936–2938. doi:https://doi.org/10.1016/j.biombioe.2011.03.026.
- Yilmaz, N. 2012. “Effects of Intake Air Preheat and Fuel Blend Ratio on a Diesel Engine Operating on Biodiesel-methanol Blends.” Fuel 94: 444–447. doi:https://doi.org/10.1016/j.fuel.2011.10.050.
- Yilmaz, N., and B. Morton. 2011. “Effects of Preheating Vegetable Oils on Performance and Emission Characteristics of Two Diesel Engines.” Biomass & Bioenergy 35 (5): 2028–2033. doi:https://doi.org/10.1016/j.biombioe.2011.01.052.
- Zareh, P., A. A. Zare, and B. Ghobadian. 2017. “Comparative Assessment of Performance and Emission Characteristics of Castor, Coconut and Waste Cooking Based Biodiesel as Fuel in a Diesel Engine.” Energy 139: 883–894. doi:https://doi.org/10.1016/j.energy.2017.08.040.