ABSTRACT
Chloride reduction in crude palm oil (CPO) of greater than 80% was achieved with water washing conducted at 90°C. Inorganic chloride content in CPO was largely removed through washing, with no significant reduction in the organic chloride. Phosphorous content of CPO reduced by 20%, while trace elements such as calcium, magnesium and iron were also reduced in the washing operation. The 3-MCPDE formed in the refined, bleached and deodorised palm oil displayed (RBDPO) a linear relationship with the chloride level in washed CPO, which could be represented by the equation y = 0.91x, where y is 3-MCPDE and x represents the chloride in RBDPO refined from washed CPO. In plant scale trials using 5% water at 90°C, mild acidification of the wash water at 0.05% reduced chloride by average 76% in washed CPO. Utilising selected bleaching earths, controlled wash water temperature and wash water volume produced low chloride levels in RBDPO. Chloride content less than 1.4 mg kg−1 in plant RBDPO production was achieved, through physical refining of washed CPO containing less than 2 mg kg−1 chloride and would correspond to 3-MCPDE levels of 1.25 mg kg−1 in RBDPO. The 3-MCPDE reduced further to 1.1 mg kg−1 as the chloride level of washed CPO decreased below 1.8 mg kg−1. Chloride has been shown to facilitate the 3-MCPDE formation and its removal in lab scale washing study has yielded lower 3-MCPDE levels formed in RBDPO. In actual plant operations using washed CPO, 3-MCPDE levels below 1.25 mg kg−1 were achieved consistently in RBDPO.
Graphical Abstract
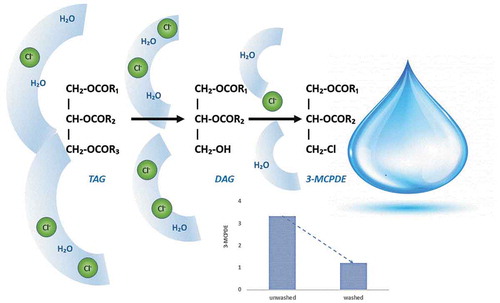
Acknowledgements
The authors thank Malaysian Palm Oil Board for the award of a matching grant for investing in plant scale CPO washing facilities, involving the centrifugal separator and auxiliary equipment. The authors also thank IOI Edible Oils Sdn. Bhd., Sabah, for the resources provided. The authors also wish to thank Alfa Laval for the use of a mill scale centrifugal separator for many months of plant scale trials conducted.