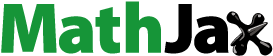
ABSTRACT
WC-Al2O3-graphene composite powder was synthesized by ultrasonic treatment and ball milling, then consolidated by hot pressing sintering (HPS). For potential applications, the friction coefficient and wear resistance of the sintered bulks at different temperatures (room temperature, 200, 400, and 600°C) were investigated. The wear tracks were characterized by scanning electron microscope, energy dispersive spectroscopy and Raman spectroscopy, X-ray photoelectron spectroscopy, respectively. The results show that the friction coefficient decreases and the wear rate increases with the increase of temperature, mainly because oxidization wear occurs on the wear surface of WC-Al2O3-graphene composite under high temperature. The main wear mechanism is the destruction and formation of tribochemical compacted layer. Graphene reduces the wear rate of WC-Al2O3-graphene composite under high tampere. The reason is that graphene reduces oxidation wear by blocking or absorbing oxygen; moreover, graphene reduces the cycle frequency of damage and reconstruction of tribochemical compacted layer by reducing the peeling of it.
GRAPHICAL ABSTRACT
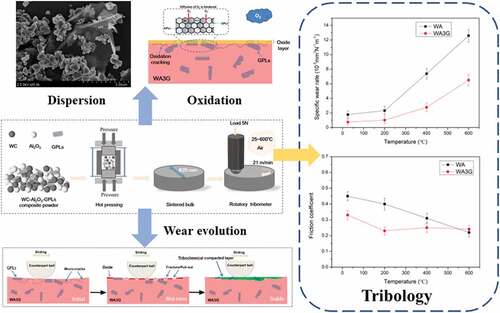
1. Introduction
WC-based composites toughened by ceramic phases (such as MgO [Citation1], Al2O3 [Citation2], ZrO2 [Citation3]) without metallic binder are developed with a very recent surge of interest due to their excellent hardness and wear resistance for promising use in many demanding applications [Citation4]. Many researchers [Citation5–7] consider that without soft and oxidizable cobalt metal, the wear resistances of these materials are better than that of conventional WC-Co cemented carbides. In these materials, WC-Al2O3 composite may be a feasible approach to eliminating the negative influence on hardness, oxidation and corrosion resistance with metallic binder addition [Citation8]. Luo [Citation9] and Su [Citation10] found that the wear resistance of WC-Al2O3 composite at ambient temperature was better than that of conventional WC-Co cemented carbide indeed. However, when at elevated temperatures, the wear resistance of WC-Al2O3 composite and WC-Co cemented carbide was just the opposite. The reason was that the oxidation of tungsten carbide matrix in WC-Al2O3 composite led to the change of wear mechanism from abrasive wear to oxidative wear, which greatly increased the wear rate of this material at elevated temperatures. While in WC-Co cemented carbide, the prior cobalt oxides inhibited WC from serious oxidation under the same conditions, resulting in a lower wear rate.
Over the past two decades, graphene as an outstanding carbon nanomaterial has attracted great interest in using it as toughening and self-lubricating fillers for ceramic materials serving in severe tribological conditions [Citation11,Citation12]. For example, the reduction of friction coefficient and wear rate due to the incorporation of graphene were widely reported in Si3N4 [Citation13–16], Al2O3 [Citation17–20], SiC [Citation21,Citation22] ceramics, etc. For binderless WC-Al2O3 composite, the added graphene may eliminate the deficiency of unsatisfactory toughness. Using WC-Al2O3-graphene composite as a tool material, it may be especially suitable for processing some difficult-to-machine materials such as titanium/titanium alloy [Citation6]. The early proposed mechanisms for enhanced tribological properties of these ceramics/graphene composites were the formation of graphene lubricating film during the friction and the improvement of the mechanical properties due to the addition of graphene. However, the majority of these studies were based on the condition of ambient temperatures. There are few reports [Citation23] describing wear properties of ceramics/graphene composites at higher temperatures.
The effect of added graphene on other properties of ceramics at high temperatures has been studied by researchers. Rutkowski et al. [Citation24] reported that alumina ceramic with up to 2 mass% of graphene could be used as working parts in air at high temperatures (>1000°C), while higher additions of graphene decreased the working temperatures to ~550°C. Li et al. [Citation25] reported that the introduction of graphene in SiBCN ceramics significantly improved the ablation resistance, because graphene provided superior thermal conductivity and ‘three-dimensional structure’ in matrix. Nieto et al. [Citation26] investigated the oxidation behavior of TaC ceramics reinforced by graphene nanoplatelets (GNPs) and found the addition of GNP could suppress the formation of the oxide layer by up to 60%, due to the high thermal conductivity of GNP. In addition, they found GNPs could seal oxide grain boundaries, hinder the further influx of oxygen and provide nano-sized carbon needed to induce the localized reduction of Ta2O5 to TaC. From these references, it can be inferred that graphene in ceramics affects the oxidation process of the matrix at high temperatures, which will eventually affect the friction and wear properties.
In present study, we focused on the tribological behavior of WC-Al2O3-graphene composite at different temperatures. Whether graphene fillers can lubricate the friction and reduce the wear rate of sintered WC-Al2O3-graphene composite at high temperatures were explored. The morphology of wear track was investigated and the wear mechanism of WC-Al2O3-graphene composite at different temperatures was discussed.
2. Experimental procedures
2.1 Preparation methods
The preparation process and wear test of WC-Al2O3 composite reinforced by graphene platelets are schematically shown in . In order to study the effect of graphene on the friction and wear properties of WC-Al2O3 composite at different temperatures, two composites with and without 0.3 wt% graphene (namely, WA3G and WA, respectively) were prepared. The choice of WA3G was based on the previous reference [Citation27], where it was found that WA3G had the highest wear resistance in all specimens with different content of graphene at room temperature. Therefore, WA3G was naturally chosen to investigate whether it also has excellent wear resistance at higher temperatures.
WC powder with a particle size of 74 μm and Al2O3 powder with a particle size of 150 μm were used as the raw ceramic powders (purchased from Sinopharm Chemical Reagent Co., Ltd.). Graphene platelets (GPLs) with a level dimension of 5–10 μm and a thickness of 3–10 nm were used as the raw graphene material (purchased from Nanjing XFNANO Material Tech Co., Ltd).
The GPLs were ultrasonic processed for 4 h in ethanol mixed with 10 vol.% polyethylene glycol. When adding graphene to the solution, the concentration was set at ~1 mg/mL. The temperature of the ultrasonic treatment was 40°C, the power was 150 w, and the frequency was 40 kHz. Before mixing with GPLs, WC and Al2O3 powders were mixed to obtain fine composite powder using the dry ball-milling process. The volume ratio of Al2O3 in WC-Al2O3 composite was 40 vol.%. In this milling process, the duration, rotating speed, and ball-to-material ratio were set at 50 h, 350 rpm, and 10/1, respectively. At last, the GPLs dispersion was added into WC-Al2O3 composite powders and ball-milled for another 4 h using the same process parameters. The obtained slurry was poured into a plate and dried in a vacuum oven until the powder was fully dried, and the drying temperature was set at 70°C. The dried powder was then sieved with an 80-mesh sieve to obtain WC-Al2O3-GPLs composite powder. After that, the WC-Al2O3-GPLs composite powders were sintered by hot pressing (HPS) in vacuum (ZT-40-20YB, Shanghai Chen Hua Electric Furnace Co., China). The sintering parameters were selected and shown in based on the previous reference [Citation28].
Table 1. Sintering parameters of WC-Al2O3-GPLs composite powders.
2.2 Characterization methods
The characterization methods of the powders and sintered bulks were selected according to the previous references [Citation27,Citation29]. Before microscopic observation, the specimens were polished by the diamond paste. The relative density was measured using Archimedes rule. The microstructure was obtained by Quanta 250 scanning electron microscope (SEM) manufactured by FEI Co., USA. The radial size and thickness of GPLs were measured by MFP-3D Atomic Force Microscope (AFM) manufactured by Asylum research Co., USA. The AFM measurement methods and conditions can be described as following. The original graphene powder was added into anhydrous ethanol, and then ultrasonically dispersed for 20 minutes until the dispersion was transparent. The dispersion was dropped onto the mica and then the ethanol dispersant was dried. Graphene was tested at room temperature using tapping mode. The GPLs and ceramics powders were characterized by an S-4800 SEM manufactured by Hitachi Co., Japan.
The sintered specimens were ground and polished before the performance measurements and microstructure characters. The WC grain size was measured by line intercept method on the metallographic SEM photos. Vickers hardness was measured by the indenter method (HVS-50Z, Shanghai Taiming Optical Instrument Co.). The indentation method is carried out under the load of 30 Kg (294.3 N) and time of 15s. For each sample, an average hardness value of 10 indentations was obtained. Due to the limitation of specimen size, the fracture toughness KIC (MPa·m1/2) of composites was determined by indentation cracking. The indentation fracture toughness was calculated from Eq. (1) [Citation30]:
where HV is Vickers hardness, P is the load, is the mean length of crack.
The high-temperature (200, 400, 600°C) hardness of samples was tested using the indenter (FH330, Feitai Co.). The Rockwell Superficial hardness was tested with the indentation load of 30 N.
Wear test was conducted in a rotatory ball-on-flat high-temperature tribometer (HT-1000, Lanzhou zhongke kaihua Tech. Co., China). The balls were WC-6 wt.%Co cemented carbide (YG6, Zhuzhou Cemented Carbide Co., China). The WC-6Co hard-metal balls (6 mm in diameter) were used in the as-received condition with a highly polished surface. The flat surfaces of disks were polished to a roughness of ~0.1 μm Ra using the diamond paste. The polished flats and the balls were ultrasonically cleaned in acetone for 5 min and this step was repeated 4 times. The experiments were conducted at a speed of 21 m/min and a rotating radius of 8 mm was used in all the tests. The normal load was set at 5 N, and the temperature was set at 25°C (room temperature), 200°C, 400°C, and 600°C, respectively. The maximum temperature (600°C) was selected according to the reference [Citation31], where the friction coefficient and wear rate of pure WC bulk proved to be difficult to be accurately measured when the temperature exceeds 600°C. The tests were conducted for a duration of 1.5 h (1890 m sliding distance) in laboratory air with a relative humidity ranging from 40% to 50%. The surface profile traces were obtained using a stylus profiler (JB-4C, Shanghai Taiming Optical Instrument, China). The cross-sectional area of wear tracks was calculated by definite integral method. These data were then used to calculate the specific wear rate according to Eq. (2) [Citation32].
where W refers to specific wear rate, L refers to sliding distance (1890 m), F refers to applied load (5 N), and V refers to wear volume.
The worn surfaces and cross-sections were characterized by SEM (quanta 250, FEI Co., USA) and energy-dispersive spectroscopy (EDS, Aztec X-MAX 20, Oxford Co., UK). Raman spectroscopy (inVia-Reflex, Renishaw Co., UK) was used to analyze the structural integrity of graphene on the worn surface.
To simulate the oxidation behavior at high temperatures separately, the thermogravimetry (TG) and differential scanning calorimetry (DSC) curves of the specimens were measured by synchronous thermal analyzer (STA 449F3, Netzsch, Germany). In this simulated oxidation experiment, the simulated air (80 vol.% N2 + 20 vol.% O2) was used as oxidation atmosphere, and the specimens were heated from room temperature to 800°C with a heating rate of 20°C/min and then kept for 1 h. In order to quantitatively compare the oxidation behavior of WA and WA3G, the specimens were cut into cubes with the same volume (3 × 3 × 4 mm3) and each specimen surface was polished before the test.
3. Results and discussion
3.1. Microstructure and mechanical properties
shows the AFM image of GPLs and the height profile at three sections after ultrasonic processing for 4 h. It can be seen that the radial size of dispersed graphene is about 9.5 μm, which is basically consistent with the nominal size. The thickness is about 5 nm, which is slightly smaller than the nominal size. These indicate that the GPLs do not break radially but exfoliate between layers after ultrasonic processing for 4 h.
Figure 2. AFM image of GPLs by height sensor, and the corresponding profile of height along the straight lines.
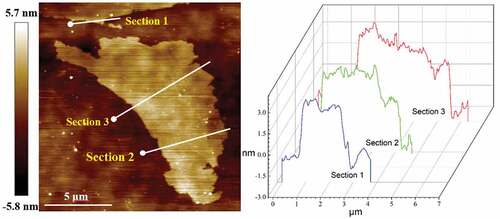
The SEM and EDS images of the WC-Al2O3 composite powder after ball milling for 50 h are shown in . It can be seen that the WC-Al2O3 composite powders are uniformly mixed and most of the powder particle size is less than 1 μm after ball milling.
Figure 3. SEM image of WC and Al2O3 powders after ball milling for 50 h and their EDS mapping images.
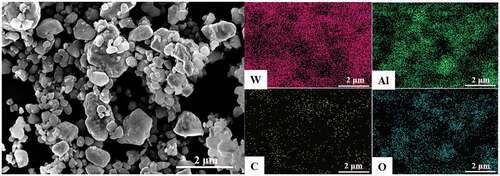
shows the SEM image of WC-Al2O3-GPLs composite powder after ultrasonic treatment and ball milling. It can be seen that the edge of GPLs is curled, and the GPLs show the thin morphological feature, which is distributed among the fine WC-Al2O3 particles. shows the Raman spectra of GPLs before ball milling and WC-Al2O3-GPLs composite powder after ball milling. The peak intensity ratio (ID/IG) between D peak (~1317 cm−1) and G peak (~1581 cm−1) was calculated. The ID/IG values of GPLs before ball milling and WC-Al2O3-GPLs composite powder after ball milling were 0.107 and 0.204, respectively. This indicates that the structure of graphene is damaged to some extent after ball milling, because the ID/IG value reflects the defect (disorder) degree of graphene structure [Citation33,Citation34].
Figure 4. SEM image (a) of WC-Al2O3 composite powders with 0.3 wt% GPLs after sonication and ball-milling, Raman spectra (b) for GPLs and mixed powder of GPLs, WC and Al2O3.
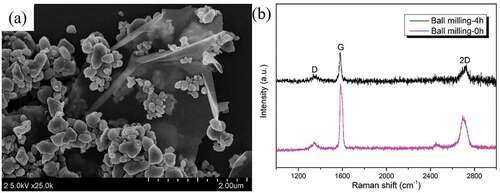
shows the microstructure (SEM in BSE mode of polished surface) and phase (corresponding XRD spectrum) of WA and WA3G composite respectively. The XRD spectra (Fig. 5a1 and b1) show that the two specimens are mainly composed of WC and Al2O3 phase, and WAG contains a small number of GPLs. Generally, elements with higher atomic numbers have brighter colors in BSE mode. Moreover, it can be seen from the EDS mapping ( c1~ c4) of WA that the content of W element in the brighter phase is high, while the content of Al element in the darker phase is high. Therefore, it can be seen from a and b, where white phase corresponds to WC phase while black phase corresponds to Al2O3 phase, respectively. It can be seen from that the WC grain size of WA (~3.05 μm) is larger than that of WA3G (~2.67 μm). However, some obvious holes can be seen in WA3G (shown by the circle in ). WA3G is superior to WA in mechanical properties due to the grain refinement and toughening of graphene [Citation27,Citation29], although the relative density (98.1%) of WA3G is lower than that (99.2%) of WA. The hardness and fracture toughness of WA are 16.18 GPa and 8.08 MPa·m1/2, while the hardness and fracture toughness of WA3G are 18.34 GPa and 11.02 MPa·m1/2, respectively.
3.2. Friction and wear properties
shows the average values of coefficient of friction for WA and WA3G at all experimental temperatures. It can be seen that the friction coefficient of WA and WA3G decreases with the increase of temperature. The friction coefficient of WA decreased more than that of WA3G. The friction coefficient of WA is higher than that of WA3G at room temperature, 200°C and 400°C. However, the friction coefficient of WA and WA3G is not much different at 600°C.
Figure 6. Average values of coefficient of friction for the two specimens at different experimental temperatures.
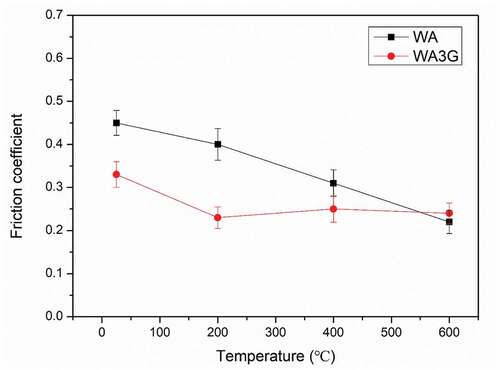
It can be seen from the that the fine grain (WA3G) corresponds to a lower friction coefficient when the temperature is less than 600°C. Generally, the friction force between the friction pair mainly depends on the state of the contact surface, because the friction force is caused by the relative motion between the micro rough peaks on each pair. During the friction period, the micro rough peaks of fine-grained samples correspond to the lower micro peak indentation depth, which leads to a lower resistance. On the other hand, the micro peaks of the fine-grained samples produce small abrasive particles during running-in period. The furrow effect of the small abrasive particles is lower, resulting in lower friction. Therefore, the fine grain corresponds to smaller friction force and friction coefficient. However, when the temperature reaches 600°C, WO3 film is distributed on the wear surface, so the friction coefficient is mainly determined by the amount of WO3 film. The friction coefficient of WA is even lower than that of WA3G because WA produces more WO3 films.
show the optical images of WA and WA3G wear tracks at different temperatures respectively. It can be seen that the wear track width of WA and WA3G increases with the increase of temperature.
Figure 7. Optical images of wear tracks for WA at room temperature (a), 200°C(b), 400°C(c) and 600°C(d).
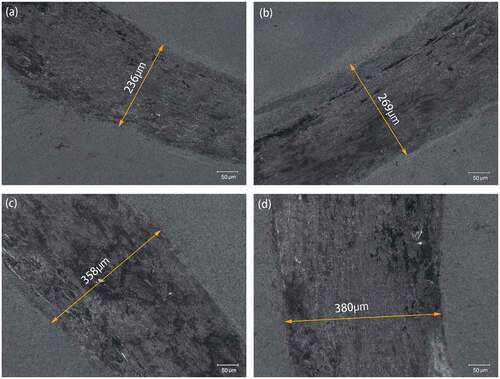
Figure 8. Optical images of wear tracks for WA3G at room temperature (a), 200°C(b), 400°C(c) and 600°C(d).
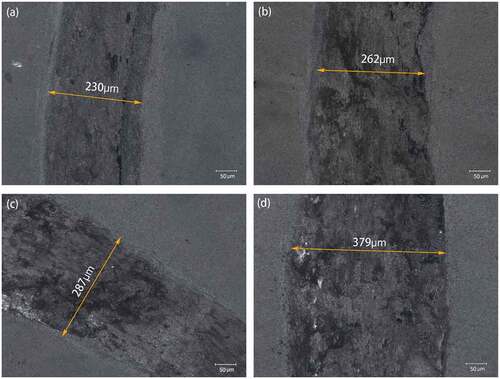
shows the profile of WA and WA3G wear tracks at different temperatures. It can be seen that the cross-sectional area of wear tracks of WA and WA3G gradually increase with the increase of temperature. The cross-sectional area of WA and WA3G at different temperatures can be calculated by using the profile data. The cross-sectional area and experimental parameters are substituted into Eq. (1) to calculate the wear rate.
Figure 9. Cross sectional profiles of wear tracks for WA (a) and WA3G (b) at different temperatures.
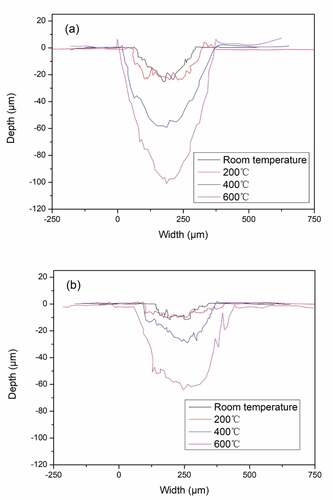
shows the specific wear rates of WA and WA3G at different experimental temperatures. It can be seen that the wear rate of WA and WA3G increases with the increase of temperature. From room temperature to 200°C, the wear rate of WA and WA3G increases slowly. From 200°C to 600°C, the wear rate of WA and WA3G increases relatively quickly. However, the wear rate of WA3G is lower than that of WA at all temperatures. This may be related to the corresponding grain size, because the wear rate is also affected by the grain size. The number of grain boundaries of fine-grained sample is more than that of coarse-grained sample. Therefore, the wear damage stress essential for causing grain boundaries micro-fracture in fine grained WA3G is higher than that in coarse grained WA. In other words, the fine grain WA3G may suffer grain boundary crushing more difficulty compared with the coarse grain WA under the same sliding conditions. Therefore, the wear resistance of fine-grained WA3G is higher than that of WA.
3.3. Wear surface morphology and structure
show the SEM image of the wear track morphology of WA and WA3G at different temperatures. It can be seen that WA3G has the same wear mechanism with WA. At room temperature, there are two kinds of morphologies in WA and WA3G wear tracks, i.e. the grain fragmentation and compacted layer. The grain fragmentation demonstrates that micro fracture occurs on the surface during sliding. Some of the wear debris form the compacted layer. The difference is that the degree of the grain fragmentation of WA3G is much weaker because WA3G has a higher toughness than that of WA. Therefore, the wear surface roughness of WA3G may be much lower, leading to a lower friction coefficient. Under the condition of 200°C, 400°C and 600°C, the compacted layer on the surface is composed of long cylindrical oxide particles along the sliding direction, which are the tribochemical reaction production [Citation23]. The corresponding EDS surface scanning maps of are shown in b1-b4) and b1-b4), respectively. It can be seen from the figures that the compacted layer formed on WA and WA3G at 200°C is composed of uniformly distributed W, Al, O and C elements. At 600°C, part of the compacted layer of WA has been peeled off. The difference is that the compacted layer on the WA3G wear surface peels off less.
Figure 11. SEM images (yellow two-way arrows showing sliding direction) of wear tracks for WA at room temperature (a), 200°C(b), 400°C(c) and 600°C(d); EDS mappings of wear tracks for WA at 200°C, including (b1) W, (b2) Al, (b3) O, (b4) C.
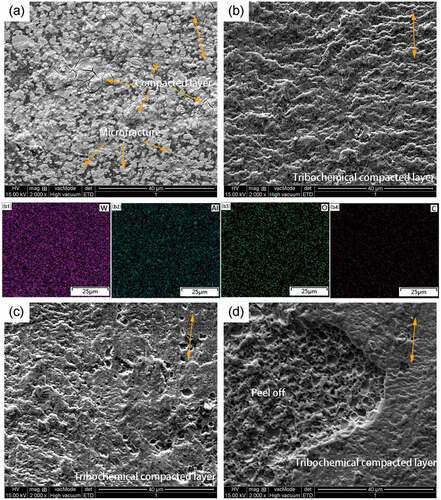
Figure 12. SEM images (yellow two-way arrows showing sliding direction) of wear tracks for WA3G at room temperature (a), 200°C(b), 400°C(c) and 600°C(d); EDS mappings of wear tracks for WA3G at 200°C, including (b1)W, (b2)Al, (b3)O, (b4)C.
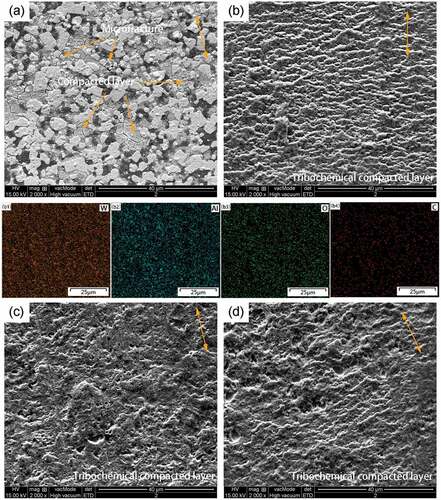
In order to further analyze the effect of graphene on wear resistance at different temperatures, Raman tests were carried out on the worn surface. shows the Raman spectra of wear tracks of WA3G at different temperatures. It can be seen from the figure that D peak and G peak appear on the worn surface of WA3G at different temperatures, indicating that the graphene material exists on the wear surface. However, all the ID/IG values are higher than that (0.204) of the composite powder. ID/IG values at room temperature, 200, 400, 600°C are 0.882, 0.651, 0.945, 1.742, respectively. The increase in the ID/IG value confirms the damage to graphene during the wear testing [Citation35]. Moreover, extra fragmented graphene flakes may form during the wear testing, because the increased D peaks intensity is related to the numbers of edges [Citation36]. Although the structure of graphene has been damaged to some extent in the wear testing, graphene can still play a role of partial lubrication and anti-wear [Citation37].
Figure 13. Raman spectra of wear tracks for WA3G at room temperature (a), 200°C(b), 400°C(c) and 600°C(d).
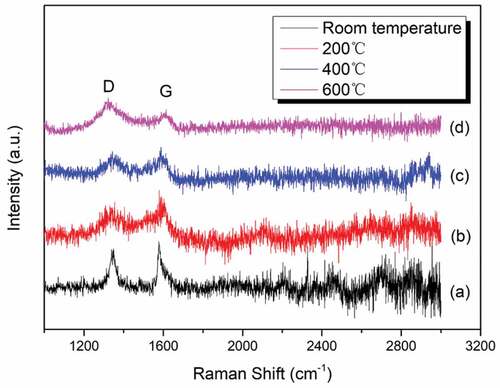
In order to further study the compacted layer on the worn surface, the worn surface of WA and WA3G composites was analyzed perpendicular to the sliding direction. a and b show the SEM images of wear track section of WA and WA3G after test at 600°C. EDS mapping images are also shown in . It can be seen from a and b that both WA and WA3G wear track surfaces are covered by a compacted layer with about 2 μm thickness. According to , WA3G compacted layer is composed of W, C, Al and O elements, which is consistent with the test results in . The red arrow in shows a platelet in compacted layer of WA3G. EDS () shows that the platelet is carbon rich material, and it is speculated to be the graphene material, i.e. the graphene material exists in WA3G compacted layer. This is consistent with the results of Raman (). Graphene material existing in the compacted layer is beneficial to the friction and wear properties of WA3G.
Figure 14. SEM images of sectional wear tracks for WA (a), WA3G and its EDS mappings at 600°C(b), EDS spectrum (c) of the flake (red arrow) in WA3G.
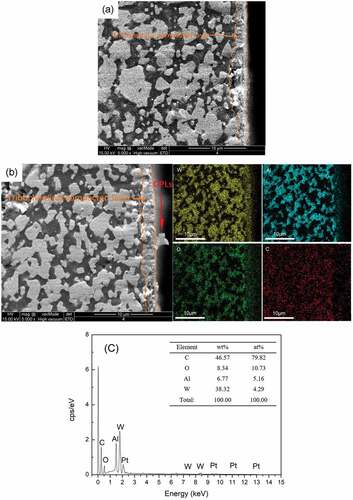
shows the high resolution XPS spectra of the worn surfaces of WA and WA3G at 600°C. Both the W 4 f peaks exhibit four components, which are attributed to the existence of WC 4 f 7/2, WC 4 f 7/2, WO3 4 f 7/2 and WO3 4 f 5/2 on the worn surfaces. It can be seen from the two XPS patterns that WC and WO3 appear on the worn surface of WA and WA3G at 600°C. On WA, the WC peaks are weaker while the WO3 peaks are stronger. This indicates that the oxidation degree of WC of WA is higher than that of WA3G. This may be due to the role of graphene in isolating air or inhibiting oxidation. On the other hand, the worn surface may have more WO3 layers.
In order to study the oxidation behavior of WA and WA3G in the tribological process at 600°C, the thermal and weight dynamic curves of WA and WA3G in simulated air (80 vol.% N2 + 20 vol.% O2) were tested and shown in . Considering the heating effect of friction itself, holding temperature was set at 800°C. It can be seen that the time of obvious weight gain and the corresponding DSC peak shape and peak position of WA and WA3G are consistent, indicating that the oxidation weight gain reaction mechanism of WA and WA3G is consistent. During the heat preservation process, the weight gain of WA3G was significantly lower than that of WA, indicating that the oxidation degree of WA3G was lower than that of WA.
Figure 16. Mass gain curve (a) and DSC curve (b) of WA and WA3G in simulated air under same conditions.
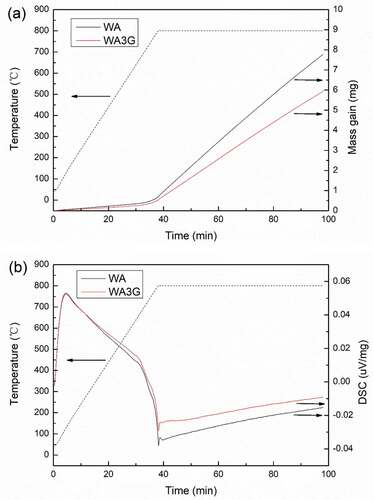
In order to find out the mechanism of graphene reducing the oxidation degree of WC-Al2O3 composite and whether graphene can inhibit the oxidation of WC, the possible chemical reactions between WA3G and O2 are counted as following [Citation38]:
The Gibbs free energy corresponding to above chemical reactions from 0 to 1000°C is calculated in . It can be seen that the Gibbs free energy change values (ΔG) of the above four reactions at 600°C are less than 0, indicating that the reactions can spontaneously proceed to the positive direction. However, the ΔG of reaction (3) is significantly lower than that of the other three reactions, so WC will react with O2 first. Combined with the analysis of , it can be considered that the main reaction at this time is reaction (3). That is to say, graphene (C) cannot inhibit the oxidation of WC.
Based on the above analysis, it can be inferred that the mechanism of graphene reducing the oxidation degree of WC-Al2O3 composite is that graphene partly prevents contact between WC and air (O2). The schematic diagram describing the mechanism is shown in . Graphene nanosheets with large specific surface area are uniformly distributed in WA3G, which play a role of partial isolation between WC and O2. The outermost layer of WA3G contacts with O2 first, so graphene first reduces the oxidation degree of the outermost layer of WA3G. With the further increase of oxidation degree, WO3 formed by WC and O2 will gradually expand, which makes the outermost layer of cracks and induces O2 to gradually enter the interior of WA3G. Then graphene distributed in the interior will continue to reduce the oxidation degree of WA3G. Nieto et al. [Citation26] studied the oxidation behavior of TaC ceramics reinforced by graphene, where they also found that graphene can improve the oxidation resistance of the materials. Due to the high thermal conductivity of graphene, the thickness of the oxide layer can be reduced by 60%. In addition, they found that graphene could seal the oxide grain boundaries and prevent further flow of oxygen.
3.4. Discussion
At higher temperatures, the friction and wear process of WA and WA3G are complex and affected by many factors. Among them, the superposition of environmental temperature and friction heat will have a greater impact on the friction and wear properties. It is reported in ref [Citation39]. that WC-Co cemented carbide will undergo chemical reaction (3) at high temperatures. With the increase of temperature, the activation energy required for this chemical reaction is fully replenished, so the reaction speed is greatly improved. Therefore, the content of WO3 increased with the increase of temperature. It is reported in ref [Citation40]. that the carbide ceramics will form oxide layers on the wear surface at high temperatures, which plays a role of self-lubrication. Therefore, with the increase of temperature, the number of the lubricating layers increases, and friction coefficients of WA and WA3G gradually decrease. Although WO3 layers have self-lubricating effect, their mechanical properties are low and their coefficients of thermal expansion is not consistent with that of ceramic matrix, which makes them easy to fall off and aggravate the wear of the material.
At higher temperatures, the mechanical properties of most materials will change. For example, the hardness of the material at high temperatures is lower than that at room temperature [Citation41,Citation42], which leads to the increase of wear rate with the increase of temperature. Similarly, the hardness (HR30N) of WA at 200°C, 400°C, 600°C was 79.2, 75.6 and 59.5 respectively, while that of WA3G at 200°C, 400°C, 600°C was 83.7, 77.3 and 63.7 respectively. For WA and WA3G, with the increase of testing temperature, the hardness of the material decreases gradually, resulting in the increase of wear rate. Especially at 600°C, the wear rate increases obviously.
However, the wear rate of WA is higher than that of WA3G at all testing temperatures. At room temperature, main wear mechanisms of WA and WA3G are microcrack, fracture and pull-out. With the wear process continuing, the compacted layer is formed on the surface of the material. According to the analysis in previous study [Citation27], the wear rate of WA3G at room temperature is lower than that of WA because WA3G has better mechanical properties, smaller grain size, and the self-lubricating effect of graphene.
At higher temperature, there are D and G peaks in the compacted layer according to the Raman spectrum in , indicating that graphene still exists in the compacted layer though it suffers oxidation and damage. also confirms the existence of graphene in the compacted layer. To explain the improvement principle of graphene on the wear resistance of WC-Al2O3 composite, the evolution of wear mechanism of WA and WA3G at higher temperatures is described as . In this figure, we divided the wear process into three stages: the initial stage, the mid-term stage, and the stable stage.
Figure 19. Wear evolution mechanisms of WA (a) and WA3G (b) at higher temperatures, showing the effect of GPLs on the wear rate.
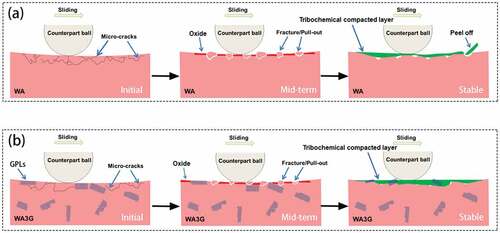
Under the combined action of friction and high temperature, besides the main mechanism of micro fracture and compacted layer, oxidation gradually occur on the surface of these two materials, and finally a thick tribochemical compacted layer is formed. With the increase of test temperature, the mechanical properties decrease, and the oxidation degree of WC matrix increases gradually, resulting in the increase of wear rate of WA and WA3G (). The difference is that graphene in WA3G can delay the oxidation process of WC matrix due to isolating WC from O2. Moreover, the oxidation of graphene will partially absorb oxygen and indirectly delay the oxidation of WC matrix. Another interpretation could be that graphene reduce the peel-off of the tribochemical compacted layer.
According to the ref. [Citation9], the oxidation reaction of WC-Al2O3 composite occurs during sliding, resulting in the coating of oxide film on the surface, which makes the substrate bear load during friction, while friction is carried out on the oxide film. Because the elastic modulus and hardness of WO3 (the oxidation product of WC), are lower than that of the substrate, it is easy to cause the oxide film attached to the substrate to be damaged. After the destruction, the new matrix exposed in the air interacts with the surrounding environment to form a new oxide film. This cycle of destruction and formation causes the surface wear of the sample to intensify, and the wear amount (wear rate) increases with the increase of temperature. Therefore, on the one hand, graphene reduces the degree of oxidative wear of WA3G. On the other hand, even in the case of oxidative wear, graphene will weaken the peeling of the tribochemical compacted layer of WA3G. For the above two reasons, the wear rate of WA3G is lower than that of WA at higher temperature.
4. Conclusions
In this study, the tribological behavior and wear mechanisms of WC-Al2O3-graphene composite were investigated at different temperatures. It is found that the friction coefficient decreases while the wear rate increases with the increase of temperature. The wear resistance of WC-Al2O3-graphene composite is improved by adding graphene under both room and high temperature. At high temperature, WC-Al2O3-graphene composite mainly undergoes oxidation wear during dry sliding. WC matrix tends to react to generate WO3 and result in the tribochemical compacted layer under the function of normal and shear stress along with the high temperature. The tribochemical compacted layer as a role of self-lubrication on the wear surface at high temperatures, result in the decrease of friction coefficient gradually with the increase of temperature, while the cycle of destruction and formation of the tribochemical compacted layer result in the increase of wear rate gradually with the increase of temperature. Graphene reduces the wear rate of WC-Al2O3-graphene composite for two reasons. On the one hand, graphene reduces oxidative wear by blocking or absorbing oxygen, and on the other hand, graphene reduces the cycle frequency of damage and reconstruction of tribochemical compacted layer by reducing the peeling of it.
Acknowledgments
This work was supported by Natural Science Foundation of the Higher Education Institutions of Jiangsu Province (Grant No. 22KJB460038) and Suqian Sci&Tech Program (Grant No. K202138).
Disclosure statement
No potential conflict of interest was reported by the author(s).
Additional information
Funding
References
- Radajewski M, Schimpf C, Krüger L. Study of processing routes for WC-MgO composites with varying MgO contents consolidated by FAST/SPS. J Eur Ceram Soc. 2017;37(5):2031–2037.
- Oh S-J, Kim B-S, Yoon J-K, et al. Enhanced mechanical properties and consolidation of the ultra-fine WC–Al2O3 composites using pulsed current activated heating. Ceram Int. 2016;42(7):9304–9310.
- Zheng D, Li X, Li Y, et al. Zirconia-toughened WC with/without VC and Cr3C2. Ceram Int. 2014;40(1, Part B):2011–2016.
- Mukhopadhyay A, Basu B. Recent developments on WC-based bulk composites. J Mater Sci. 2010;46(3):571–589.
- Sun J, Zhao J, Chen M, et al. Determination of microstructure and mechanical properties of VC/Cr3C2 reinforced functionally graded WC-TiC-Al2O3 micro-nano composite tool materials via two-step sintering. J Alloys Compd. 2017;709:197–205.
- Sun J, Zhao J, Chen M, et al. Determination of microstructure and mechanical properties of functionally graded WC-TiC-Al2O3-GNPs micro-nano composite tool materials via two-step sintering. Ceram Int. 2017;43(12):9276–9284.
- Tang W, Zhang L, Zhu J-F, et al. Effect of direct current patterns on densification and mechanical properties of binderless tungsten carbides fabricated by the spark plasma sintering system. Int J Refract Metals Hard Mater. 2017;64:90–97.
- Sun J, Zhao J, Chen M, et al. Multilayer graphene reinforced functionally graded tungsten carbide nano-composites. Mater Des. 2017;134:171–180.
- Luo Y, Liu X, Weiwei Dong SZ. Friction and wear properties of WC-Al_2O_3 composite. Acta Materiae Compositae Sinica. 2016;33(11):2584–2590.
- Su Q, Zhu S, Ding H, et al. Comparison of the wear behaviors of advanced and conventional cemented tungsten carbides. Int J Refract Metals Hard Mater. 2019;79:18–22.
- Zhai W, Srikanth N, Kong LB, et al. Carbon nanomaterials in tribology. Carbon. 2017;119:150–171.
- Miranzo P, Belmonte M, Osendi MI. From bulk to cellular structures: a review on ceramic/graphene filler composites. J Eur Ceram Soc. 2017;37(12):3649–3672.
- Llorente J, Ramírez C, Belmonte M. High graphene fillers content for improving the tribological performance of silicon nitride-based ceramics. Wear. 2019;430-431:183–190.
- Tapasztó O, Balko J, Puchy V, et al. Highly wear-resistant and low-friction Si3N4 composites by addition of graphene nanoplatelets approaching the 2D limit. Sci Rep. 2017;7(1):10087.
- Belmonte M, Ramírez C, González-Julián J, et al. The beneficial effect of graphene nanofillers on the tribological performance of ceramics. Carbon. 2013;61:431–435.
- Maros M, B AKN, Károly Z, et al. Tribological characterisation of silicon nitride/multilayer graphene nanocomposites produced by Hip and SPS technology. Tribol Int. 2016;93:269–281.
- Ahmad I, Anwar S, Xu F, et al. Tribological investigation of multilayer graphene reinforced alumina ceramic nanocomposites. J Tribol. 2018;141(2):022002.
- Gutiérrez-Mora F, Cano-Crespo R, Rincón A, et al. Friction and wear behavior of alumina-based graphene and CNFs composites. J Eur Ceram Soc. 2017;37(12):3805–3812.
- Cheng Z, Andy N, Arvind A. Ultrathin graphene tribofilm formation during wear of Al2O3–graphene composites. Nanomater Nanotechnol. 2016;5(1):1–9.
- Wozniak J, Cygan T, Petrus M, et al. Tribological performance of alumina matrix composites reinforced with nickel-coated graphene. Ceram Int. 2018;44(8):9728–9732.
- Llorente J, Belmonte M. Friction and wear behaviour of silicon carbide/graphene composites under isooctane lubrication. J Eur Ceram Soc. 2018;38(10):3441–3446.
- Llorente J, Román-Manso B, Miranzo P, et al. Tribological performance under dry sliding conditions of graphene/silicon carbide composites. J Eur Ceram Soc. 2016;36(3):429–435.
- Balko J, Hvizdoš P, Dusza J, et al. Wear damage of Si3N4-graphene nanocomposites at room and elevated temperatures. J Eur Ceram Soc. 2014;34(14):3309–3317.
- Rutkowski P, Klimczyk P, Jaworska L, et al. Thermal properties of pressure sintered alumina–graphene composites. J Therm Anal Calorim. 2015;122(1):105–114.
- Li D, Yang Z, Jia D, et al. Ablation behavior of graphene reinforced SiBCN ceramics in an oxyacetylene combustion flame. Corros Sci. 2015;100:85–100.
- Nieto A, Kumar A, Lahiri D, et al. Oxidation behavior of graphene nanoplatelet reinforced tantalum carbide composites in high temperature plasma flow. Carbon. 2014;67:398–408.
- Zhang X, Zhu S, Shi T, et al. Preparation, mechanical and tribological properties of WC-Al2O3 composite doped with graphene platelets. Ceram Int. 2020;46(8, Part A):10457–10468.
- Qu H, Zhu S, Li Q, et al. Influence of sintering temperature and holding time on the densification, phase transformation, microstructure and properties of hot pressing WC–40vol.%Al2O3 composites. Ceram Int. 2012;38(2):1371–1380.
- Zhang X, Zhu S, Ding H, et al. Fabrication and properties of hot-pressing sintered WC-Al2O3 composites reinforced by graphene platelets. Int J Refract Metals Hard Mater. 2019;82:81–90.
- Shetty DK, Wright IG, Mincer PN, et al. Indentation fracture of WC-Co cermets. J Mater Sci. 1985;20(5):1873–1882.
- Liu Y, Wang Z, Sun Q, et al. Tribological behavior and wear mechanism of pure WC at wide range temperature from 25 to 800°C in vacuum and air environment. Int J Refract Metals Hard Mater. 2018;71:160–166.
- De Portu G, Guicciardi S. 2.14 - wear of hard ceramics [M]//V. K. Sarin. Comprehensive hard materials. Oxford: Elsevier; 2014. p. 385–412.
- Centeno A, Rocha VG, Alonso B, et al. Graphene for tough and electroconductive alumina ceramics. J Eur Ceram Soc. 2013;33(15–16):3201–3210.
- Stankovich S, Dikin DA, Piner RD, et al. Synthesis of graphene-based nanosheets via chemical reduction of exfoliated graphite oxide. Carbon. 2007;45(7):1558–1565.
- Porwal H, Tatarko P, Saggar R, et al. Tribological properties of silica–graphene nano-platelet composites. Ceram Int. 2014;40(8, Part A):12067–12074.
- Yazdani B, Xu F, Ahmad I, et al. Tribological performance of graphene/carbon nanotube hybrid reinforced Al2O3 composites. Sci Rep. 2015;5(1):11579.
- Ranjan S, Mukherjee B, Islam A, et al. Microstructure, mechanical and high temperature tribological behaviour of graphene nanoplatelets reinforced plasma sprayed titanium nitride coating. J Eur Ceram Soc. 2020;40(3):660–671.
- Ma J, Zhu SG. Direct solid-state synthesis of tungsten carbide nanoparticles from mechanically activated tungsten oxide and graphite. Int J Refract Metals Hard Mater. 2010;28(5):623–627.
- Chen L, Yi D, Wang B, et al. Mechanism of the early stages of oxidation of WC–Co cemented carbides. Corros Sci. 2016;103:75–87.
- Zhang W, Yamashita S, Kita H. Self lubrication of pressureless sintered SiC ceramics. J Mater Res Technol. 2020;9(6):12880–12888.
- Milman YV, Chugunova S, Goncharuck V, et al. Low and high temperature hardness of WC-6 wt%Co alloys. Int J Refract Metals Hard Mater. 1997;15(1):97–101.
- De Luca F, Zhang H, Mingard K, et al. Nanomechanical behaviour of individual phases in WC-Co cemented carbides, from ambient to high temperature. Materialia. 2020;12:100713.