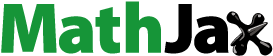
Abstract
In the field of nano-composites, hybrid nano-fluids have noteworthy applications in aerospace, energy materials, thermal sensors, antifouling, etc. because of their ability to produce higher thermal conductivity than conventional nanofluids. Different combinations of nanocomposites have been found in the literature to develop the suitable hybrid-mixture, but no study has been found yet about the combined influence of ceria and zinc-oxide nanocomposites in the host liquid. In this article, unsteady 3 D transport of water driven hybrid nano-fluid with the consequences of brick shaped nanocomposites (ceria; and zinc oxide;
) has deliberated with the thermal link of heat source/sink. Variable thermal conditions have been supplied at the surface with the effect of a magnetic environment. Similarity relations have been used to articulate the transport equations into solvable forms and then solved numerically via Keller-Box method. Nusselt number and skin-friction coefficients have also plotted with the wide ranges of involved parameters. Thermal setup has also briefly been discussed with the non-uniformity of surface temperature. Rate of heat transfer has significantly improved with the amounts of ceria (1 wt% to 10 wt%) and zinc-oxide (1 wt% to 10 wt%) nanocomposites. The Nusselt number is reported in the range of 4.0 to 4.8 with the increasing amount of
from −0.6 to −0.2, whereas it is reported in the range of 3.1 to 3.9 with the varying amount of
from 0.2 to 0.6. Rate of heat transfer is observed higher for zinc-oxide nanoparticles as compared to ceria nanoparticles.
Graphical Abstract
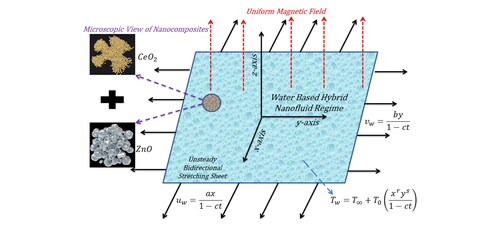
1. Introduction
The extension of nano-fluid with the composition of two or more different nanocomposites dissolves in the host liquid having higher thermal conductivity is termed as a hybrid nano-fluid. Hybrid nano-fluids are extensively applied in various fields of heat transfer such as coolant in machining, transformer and electronic cooling, drug reduction, biomedical and refrigeration, etc. with superior proficiency as compared to conventional nano-fluids. Waini et al. [Citation1] incorporated heat transference and unsteady flow over elongating sheet in hybrid nano-fluid and elaborated that for a certain choice of unsteadiness constraint, dual solutions may exists. To determine stability of dual solutions, temporal stability analysis is performed and elaborated that one is stable and other is unstable. Abbasi and Farooq [Citation2] glimpsed numerical simulation for transportation of hybrid nano-fluid in non-uniform vertical channel and deduced that current study is helpful in nano-medical technologies. Babazadeh et al. [Citation3] analyzed the behavior of hybrid nano-fluid including radiation effects and Lorentz force within a porous cavity and depicted that higher values of Hartman factor enhances the conduction mode. Pourrajab et al. [Citation4] experimentally deliberated collaborative effects of improvement in thermal conductivity of water driven hybrid nano-fluid containing and
nanocomposites. It was perceived that the hybrid nano-fluid’s thermal conductivity having 0.16 vol%
and 0.04 vol%
nanocomposites was collectively improved by 47.3% in comparison with thermal conductivity of the water driven liquid. Shah et al. [Citation5] reported the CFD simulation of water driven hybrid nano-fluid with nanocomposites (
using free convection in permeable media and deduced that by enlargement of Hartmann number, temperature of heat source is diminished. Malika and Sonawane [Citation6] disclosed consequences of nanocomposites mixed ratio on stability and thermo-physical characteristics of
water-driven hybrid nano-fluid. Size, shape and morphology of nanocomposites were characterized using DLS and Zeta analysis. Investigation of the properties of concentrated water driven
binary hybrid nano-fluid in heat pipe was presented by Çiftçi [Citation7]. Properties of water driven graphene-silver (
) hybrid nano-fluid in recharging micro-channel (RMC) with temperature dependent properties numerically explored by Samal and Moharana [Citation8] and deduced that use of RMC is advantageous for high heat flux. When pumping water is not constraint then utilization of water driven (
) hybrid nano-fluid has various advantageous. Tiwari et al. [Citation9] experimentally investigated the influence of stabilization procedures on thermal conductivity and stability of
water driven hybrid nano-fluid. Thermal conductivity of
and
and their hybrid via ratio (50:50) by volume based deionized water nano-fluid experimentally incorporated by Kamel et al. [Citation10]. Lahari et al. [Citation11] examined heat transference characteristics of water driven
nano-fluids.
and
nano-fluids prepared at 0.5%, 1.5% and 2.0% volume concentration and temperature range of
It was noticed that substantial augmentation of both heat transfer rate and efficiency of heat exchanger with
nano-fluids at 2.0% volume concentration and 1.5% volume concentration of
hybrid nano-fluids were achieved. Bhattad [Citation12] inquired experimentally energy of plate heat exchanger via energy linked performance features like, coolant energy rate, coolant outlet temperature, non-dimensional energy, irreversibility rate, and second law efficiency. Coolant energy rate, coolant outlet temperature, non-dimensional energy and irreversibility rate increases by 2.5 wt%, 4.8 wt%, 7.5 wt% and 3.5 wt%, respectively, whereas the second law efficiency reduces using nanocomposites and increasing flow rate and decreases with the coolant inlet temperature. Yadav et al. [Citation13] experimentally scrutinized rheological comportment of 13 nm
25 nm
and the hybrid mixture
–
(in 50:50 volume)/
over volumetric concentrations 0.05–1 vol% and temperature of 30–90 °C. It was concluded that performance of the hybrid mixture is similar to
which makes it advantageous in anti-freezing applications. Nano-structures of
with concrete based Jaffrey nano-fluid presented by Sheikh et al. [Citation14] and conferred its applications in cement and concrete industry. Nfawa et al. [Citation15] reported the use of tiny-particle
for augmenting thermal conductivity of
-water nanofluid and used two-step method for synthesis of
-water hybrid nano-fluid. Some recent explorations related with the investigation of hybrid nanofluid in the view of various geometries are discussed via Refs. [Citation16–19].
The nanocomposites shapes may have a significant effect on thermo-physical characteristics of the nano-fluids. Various experimental and numerical studies have been allocated to nanocomposites shapes effects. Saba et al. [Citation20] analyzed water driven hybrid nano-fluid with different shapes and concluded that platelet shape nanocomposites offer better heat transference ability in comparison with other shapes. Convective heat transferal in horizontal pipe of hybrid nano-fluid considering different shapes effects were numerically studied by Benkhedda et al. [Citation21] and revealed the idea that for platelet shaped nanocomposites, maximum value of friction factor has registered. Some more extraordinary considerations concerning the impact of nanocomposites shapes of various substances are discussed by the researchers via Refs. [Citation22–28].
Magneto-hydro-dynamics (MHD) has gained extensive applications in the manufacturing and engineering industries such as crystal growth in liquid, cooling of nuclear reactor, food processing, electronic package, underground heat pumps, and solar technology. Mabood et al. [Citation29] reported 3 D unsteady MHD flow of /graphene-water hybrid non-fluid with non-linear radiation effects. Non-Newtonian Casson hybrid nano-fluid with MHD mixed convection flow in stagnation link was investigated by Zahar et al. [Citation30]. Sulochana and Apama [Citation31] analyzed mass and heat transference mechanism of unsteady MHD thin film stream of
–
hybrid nano-fluid subject to electromagnetic waves. Afterwards, numerous authors via Refs. [Citation32, Citation33] exploited the magnetic effect on the flow of nanofluids passed/touching the various geometries. Heat transference can be controlled by external magnetic field which has several applications in different fields such as thermal engineering, aero-scope and electronic packing. Gorla et al. [Citation34] explored numerically MHD effects of heat transferal on hybrid nano-fluid in square porous cavity. MHD mixed convection flow of
hybrid nano-fluid with impact of heat transferal near stagnation point is revealed by Jamaludin et al. [Citation35] over moveable surface. Armaghani et al. [Citation36] addressed the mixed convection of
hybrid nano-fluid by considering a heat source/sink for L-shaped cavity. Moreover, researchers [Citation37–41] have been performed some novel studies about hybrid nano-fluid with heat source/sink.
Prescribed surface temperature and heat flux have plentiful applications in industrial and metallurgical processes such as glass fiber and paper production, wire drawing, extrusion of polymer sheets and drawing of plastic films etc. Shehzad et al. [Citation42] provided the exact solution of Maxwell fluid over bidirectional elongating sheet with both VST and VHF cases. Hayat et al. [Citation43] carried out the study of 3 D flow of an Oldroyd-B fluid over bi-directional enlarging surface with VST and VHF. Furthermore, Waini et al. [Citation44] depicted permanence of flow and heat transferal over a stirring needle with VHF thermal supply. Natural convection mass and heat transferal of nano-fluids over vertical plate surrounded in a saturated Darcy porous medium subjected to VST and VHF was numerically deliberated by Noghrehabadi et al. [Citation45]. Some latest contributions about the VST and VHF cases have been found in the Refs. [Citation46–48].
From published literature, it is concluded that not much attention is given to the dynamics of hybrid nano-fluid with the effects of brick shaped nanocomposites. The objective of present study is to deliberate the unsteady 3 D magnetic transference of water driven hybrid nano-fluid containing brick shaped nanocomposites (ceria and zinc-oxide
) with heat source/sink. Thermophysical properties of ceria and zinc-oxide nanocomposites have been used to model the problem with the fluid properties of water. Hamilton-Crosser model has been used for composition and shape of the dispersed nanoparticles. The thermal supply is examined under the environment of VST and VHF modes. An innovative numerical approach, namely, Keller-Box method [Citation49–52] is selected to solve the flow problem. Graphical illustrations are made to inspect the rate of heat transference, temperature fluctuation for VST and temperature fluctuation for VHF under the control of emerging involved parameters. To the best of our knowledge, no such contribution has been made in literature yet.
2. Mathematical formulation
Cartesian configuration is opted to enlighten the unsteady mathematical model for bidirectional dynamics of water-driven hybrid nano-fluid containing brick shaped nanocomposites (ceria; and zinc oxide;
) with heat source/sink. This combination of ceria and zinc oxide nanocomposites is not previously considered by any researcher. The distinctive property of ceria is its reversible conversation to a non-stoichiometric oxide and it has vast applications in the purification of elements as well as in the polishing processes. The distinctive property of zinc-oxide is its good transparency. Zinc-oxide has variety of applications in heat protecting windows, thin film transistors, light emitting diode, liquid crystal display, etc. To scrutinize the MHD (magneto hydrodynamics) effects with uniform strength
mathematical relation with the deficiency of electric force is utilized. The considered nanocomposites are kept in thermal equilibrium. To keep the flow incompressible as well as laminar, the no-slip phenomenon is considered at the surface. The disturbance in the rest position of the nanofluid is observed by displacing the stretching device with velocity
along
- axis and with velocity
along
- axis, however, the region covered by the hybrid nano-fluid is denoted by
Two types of thermal conditions, namely, VST and VHF are applied to provide a variable temperature environment at the surface. The graphical abstract of the mathematical modeling is included in the report via . is constructed to summarize the thermo-physical appearances of
and
Table 1. Thermophysical properties of ceria and zinc oxide with water as host liquid [Citation9–11].
By keeping above mentioned measures in contact, the transport rheology of hybrid-powder along with boundary layer concept is established as [Citation29, Citation46, Citation48]:
(1)
(1)
(2)
(2)
(3)
(3)
(4)
(4)
The geometrical conditions for present circumstances are [Citation42, Citation43, Citation46]
(5)
(5)
(6)
(6)
(7)
(7)
Here, indicates the heat source/sink (
represents source, whereas
represents sink),
entitles the specific heat capacity,
is chosen to label the density of the hybrid material,
characterizes the temperature at the surface,
and
are dimensional constants,
entitles velocity components along
-,
- and
- directions, respectively,
are the indices that are used to control the heat distribution at the surface, time is suggested by
whereas,
and
are labeled to describe the effective viscosity, thermal conductivity, thermal diffusivity and influence of electrical conductivity of the hybrid nano-powder.
To familiarize brick-shaped nanocomposites, the mathematical relations for present development of hybrid nano-powder are communicated as [Citation22]:
(8)
(8)
(9)
(9)
(10)
(10)
(11)
(11)
(12)
(12)
(13)
(13)
(14)
(14)
(15)
(15)
(16)
(16)
Here, quantities of ceria and zinc oxide are expressed through and
respectively. The set of equations used to non-dimensionlize the above formulation are written as [Citation50]:
(17)
(17)
(18)
(18)
With the involvement of EquationEqs. (19)(19)
(19) and Equation(20)
(20)
(20) , the transport equations take the following forms
(19)
(19)
(20)
(20)
(21)
(21)
(22)
(22)
with geometrical conditions
(23)
(23)
(24)
(24)
Here, indicates the heat source
or heat sink
and
indicate the Hartman number and unsteady factor, respectively, elongation ratio is conveyed by
Prandtl factor is specified by
and
are the relations related with the inclusion of nanocomposites and these are mathematically conveyed as:
(25)
(25)
(26)
(26)
(27)
(27)
(28)
(28)
Reduced Nusselt number and skin-friction coefficients are the most remarkable quantities for thermal and mechanical processes, respectively, and are incorporated here in the forms of Reynolds’s numbers
as:
(29)
(29)
3. Keller-Box simulation
In the current era, researchers are interested to find the numerical solutions of the modeled problems because these solutions take the less computational time. Various numerical methods, namely, shooting method, RK-method, RKF-method, finite difference method and their combinations have been tested to solve the engineering problems. Among them the best method is implicit finite difference scheme, namely, Keller-Box method. In this method, higher order differential system is firstly transfigured into the first order differential system and then reduced differential system is reformed into a difference system by opting central difference approximations in the computed domain. The system of difference equations are then linearized along with boundary conditions by using the well-known Newton-Raphson method. The linearized system is then shaped into the matrix-vector form with tri-diagonal matrix as a coefficient of unknown vector. LU-decomposition scheme is opted to solve the formulated matrix-vector problem. The value of unknown vector will be the first approximation of the solution. The further approximations of the solutions are obtained by varying the numbers of grid-points The final value of unknown vector is further used for graphics purpose as well as for the computation of heat transaction rate.
provides the solution of the formulated problem by using the above mentioned steps of Keller-Box method. While obtaining the solution, the initial value of (say
) is opted zero and then increased gradually to obtain the final value of
(i.e.
). The further increment in the value of
did not affect the solution of the problem. The first approximation of the Keller-Box solution is obtained by considering
with step-size
and then the value of
is increased gradually up-to 6500 in order to attain the convergent and stable numerical solution of the physical problem with accuracy
. It is inferred through that five-hundred grid points are enough to obtain the convergent value of
fifteen-hundred grid points are necessary to get the convergent amount of
six-thousand grid points are enough to attain the convergence of
for VST case and convergence of
for VHF case as well. These values of
that provide the convergent solution are further used for heat transfer analysis.
Table 2. Convergence of the Keller-Box simulation under the control of parameters
4. Results and discussion
The effects of involved parameters on temperature distributions, reduced Nusselt numbers and skin-friction coefficients are evaluated and discussed in this section via and . Effect of heat source/sink factor on heat distribution
for VST state is assessed via and concluded that varying amount of
enhances the heat distribution
because of the reduction in the value of specific heat produced by water. explores the information about the effect of
on
for VHF state and it is assessed that higher estimation of
develops the heat distribution
because of the enhancement in the amount of heat source/sink connection
The fluctuation in heat distributions is observed lower for heat sink state as compared to heat source state because of the transmission of heat from hotter region to colder region. Moreover, the width of thermal layer is compressed with the downfall in the amount of
and it is upgraded with the progression in the amount of
Furthermore, the temperature for VHF state is observed less than the surface temperature because a huge amount of heat flux is produced at the stretchy surface.
Figure 2. (a, b). Heat estimations with the influence of for VST state (pattern a) and for VHF state (pattern b).
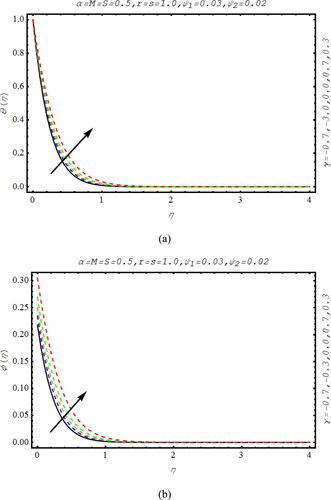
Figure 3. (a, b). Heat estimations with the influence of for VST state (pattern a) and for VHF state (pattern b).
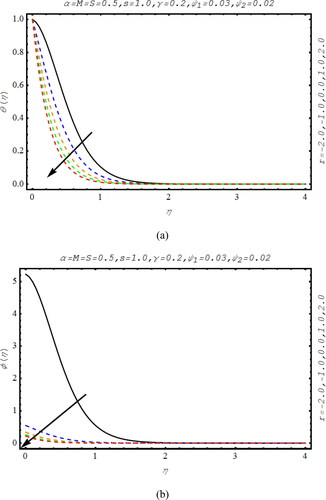
Figure 4. (a, b). Heat estimations with the influence of for VST state (pattern a) and for VHF state (pattern b).
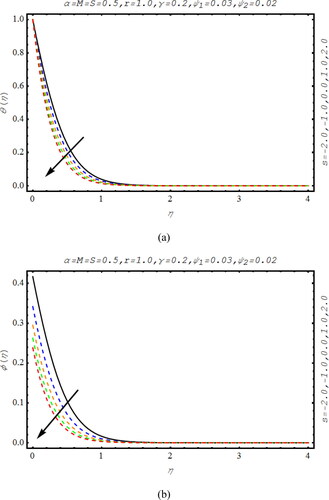
Figure 5. (a-c). Nusselt number estimations with the pairs (a): (ceria) versus
(b):
(zinc-oxide) versus
(ceria) for heat sink situation, and
(ceria) versus
(zinc-oxide) for heat source situation.
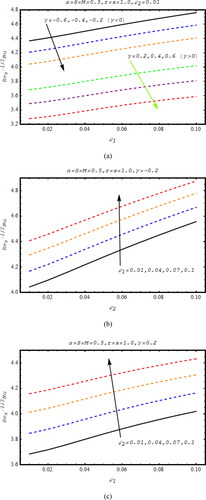
Figure 6. (a-c). Skin-friction coefficients for ceria nanocomposites with the pairs (a): versus
(b):
versus
and (c):
versus
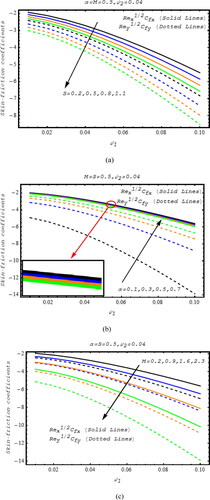
Figure 7. Comparison between rate of heat transfer by ceria and rate of heat transfer by zinc-oxide
against the wide range of unsteady stretching parameter
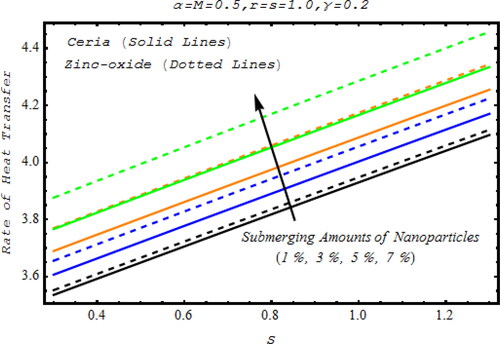
Table 3. Calculation of Nusselt number for solid volume fractions (ceria) and
(zinc-oxide) with
explores the influence of non-uniformity of the surface temperature along - direction for VST state when the temperature along
- direction is fixed (i.e.
) and explains the role of the non-uniformity of the surface temperature along
- direction for VHF state when the temperature along
- direction is fixed (i.e.
). The heat distribution is reduced with the upraising value of
for both the VST and VHF states. The width of thermal layer is also reduced with the higher estimation of
because surface temperature is improved with the growth in the choice of
The temperature is higher than the surface temperature for
in the state of VHF and it is lower than the surface temperature for the values of
greater than
because of huge heat flux production at the surface. The thermal space between the uppermost curve and the blue curve is very high because in between
and
the heat flux rate dominates in this region.
summaries the influence of non-uniformity of surface temperature along - direction for VST state when the temperature along
- direction is kept fixed but non-uniform (i.e.
) and demonstrates the control of the non-uniformity of surface temperature along
- direction for VHF state when the temperature value along
- direction is kept constant but non-uniform (i.e.
). Here, we see that the width of the thermal layer is attained the identical behaviour with the progression of
for VST state, whereas for VHF state it is initially developed and then comes to a uniform width for VHF state because a higher rate of heat flux is produced for this situation.
describes the graphical explanation of reduced Nusslet number for the ceria nanocomposites with varying choice of It is shown that higher loading of ceria nanocomposites develops a rate of heat transaction for both positive and negative values of gamma but the rate of heat transaction is higher for negative value of gamma than positive value of gamma. Physically, a negative value of gamma reduces the heat conduction process and positive value of gamma enhances the heat conduction process. Moreover, rate of heat transaction is reduced with the uprising in the amount of gamma. The higher rate of heat transaction is achieved for
and lower rate of heat transaction is attained for
in the selected range of gamma. explains the behaviour of reduced Nusslet number for the zinc-oxide nanocomposites with various loading percentages of ceria nanocomposites. The rate of heat transaction is highly improved with the higher loading percentages of zinc-oxide nanocomposites. Moreover, Nusslet number is also improved with the various loading percentages of ceria nanocomposites. The higher loading percentages of ceria nanocomposites with the combination of zinc-oxide nanocomposites develop the Nusslet number because the thermal conductivity of zinc-oxide is almost triple to the thermal conductivity of ceria. enlightens the combined influence of nanocomposites (i.e. ceria and zinc-oxide) on the rate of heat transaction. It is worth to noticed that rate of heat transaction is dramatically improved with the combined influence of these nanocomposites. The smallest value of Nusslet number is achieved for 1 wt% inclusion of ceria nanocomposites with the 1 wt% inclusion of zinc-oxide nanocomposites and the highest value of Nusslet number is attained for 10 wt% ceria nanocomposites with the 10 wt% of zinc-oxide nanocomposites for the adopted percentages of nanocomposites.
communicates the influence of unsteady stretching factor on skin-friction coefficients
(represented by solid lines) and
(represented by dotted lines) with different amounts of ceria when the amount of zinc-oxide is kept constant (i.e. 4 wt%). Escalation in the choice of
from 0.2 to 1.1 reduces the skin-friction coefficients because a higher rate of unsteady expansion is produced with the uprising of
Also, the value of
is higher than
because positive disturbance in the value of
reduces the value of expansion rate
along
- direction and hence expansion ratio
is improved. Mathematically,
is involved in the numerator of EquationEq. (29)
(29)
(29) with negative exponent and hence
must be less than
as observed through the .
highlights the influence of from 0.1 to 0.7 on skin-friction coefficients
(denoted by solid lines) and
(denoted by dashed lines). It is deduced that escalation in the choice of
reduces the worth of
and enhances the net worth of
because the expansion rate
is improved with the escalation of
Moreover, the enhancement in the value of
increases the flow rate of the hybrid nanofluid at the surface and hence the combined influence of
is improved. The equality between skin-friction coefficients exists when
(i.e. axisymmetric case) as the dotted curves and dashed curves are being closer to each other when
Furthermore, higher percentage involvement of ceria nanocomposites diminishes the skin-friction coefficients because the specific heat of ceria is lower than the specific heat of zinc-oxide, whereas the density of ceria is higher than the density of zinc-oxide. describes the impact of Hartman number
on skin-friction coefficients with the varying amounts of ceria and fixed amount of zinc-oxide (i.e. 4 wt%). It is summarized that higher choice of
diminishes the skin-friction coefficients as the electrical conductivity of the host liquid is much less than the density of the host liquid. Moreover, the higher estimation of
produces a strong Lorentz force and hence a reduction in the skin-friction coefficient is obtained.
constructs the comparison between the rate of heat transaction by ceria (1 wt%, 3 wt%, 5 wt% and 7 wt%) represented by solid lines and the rate of heat transaction by zinc-oxide (1 wt%, 3 wt%, 5 wt% and 7 wt%) represented by dotted lines. declares that the rate of heat transaction by zinc-oxide is higher than the rate of heat transaction by ceria and the difference between their rates of heat transaction is lower for smaller amounts of nanocomposites than higher contents of nanoparticles. Physically, the thermal conductivity of zinc-oxide is almost triple the thermal conductivity of ceria and the above spectacular outcomes are achieved.
addresses the Nusslet number for both the VST and VHF states against the different amounts of nanocomposites (ceria and zinc-oxide) for constant choices of other involved parameters. The results obtained through Keller-Box method (KBM) are also compared with the homotopy analysis method (HAM) for the validity of the numerical code. The value of Nusslet number is tremendously improved with the increasing nanocomposite contents i.e. 3 wt%, 6 wt% and 9 wt%. The Nusslet number for both thermal conditions is similar as the relation for Nusslet number for VST state via EquationEq. (29)(29)
(29) differs from the Nusslet number for VHF state by the factor
which has been adjusted in the thermal boundary condition i.e.
Mathematically, for the present heat transfer problem the temperature distribution remained different for VST and VHF states whereas the rate of heat transfer is remained the same for both the thermal states because EquationEq. (21)
(21)
(21) and EquationEq. (22)
(22)
(22) are the same for both the thermal cases but boundary conditions are slightly different.
5. Conclusions
A mathematical solution for unsteady bidirectional dynamics of water driven hybrid nano-fluid (i.e. the combination of nanocomposites ceria and zinc-oxide
having brick shapes) with VST and VHF thermal conditions has been reported. The magnetic impact and internal heat source/sink impact have also incorporated in the momentum balance and energy balance equations, respectively. The heat fluctuation was reduced with the higher estimations of heat controlling indices along
- and
- directions, whereas it is significantly improved with the increasing of heat source/sink factor
Increasing amounts of ceria and zinc-oxide developed the rate of heat transaction, whereas skin-friction coefficients were slightly reduced with the positive tendencies in these percentage amounts. The amount of reduced Nusslet number doubled for zinc-oxide nanocomposites compared to ceria nanocomposites. It is hoped that the present heat transport model will not only contribute to the development of nanocomposites but also will set a new roadmap for researchers working in this field.
Acknowledgments
We are grateful to honorable Editor-in-Chief and worthy reviewers for their useful recommendations which helped us in order to improve the manuscript.
Disclosure statement
No potential conflict of interest was reported by the authors.
Additional information
Notes on contributors
Iftikhar Ahmad
Iftikhar Ahmad currently working as a professor in the Department of Mathematics at Azad Jammu and Kashmir University, Muzaffarabad, Pakistan. He completed his PhD in mathematics from Quaid-i-Azam University, Islamabad, Pakistan. His research is in the field of fluid dynamics focusing on heat and mass transfer problems. Other research areas address modeling of engineering problems, solution of differential equations, numerical analysis, etc.
Muhammad Faisal
Muhammad Faisal is a Faculty Member in the Department of Mathematics, Faculty of Science, Azad Jammu & Kashmir University, Muzaffarabad, Pakistan. He received his PhD, MPhil and MSc degrees from Department of Mathematics UAJK in 2021, 2013 and 2010, respectively. His research is in the field of computational fluid dynamics, thermal engineering, engineering mathematics and physics, nanocomposites, computational methods, nanofluids, hybrid nanofluids, etc.
Qazi Zan-Ul-Abadin
Qazi Zan-Ul-Abadin is a PhD scholar at the Department of Mathematics, Faculty of Science, Azad Jammu & Kashmir University, Muzaffarabad, Pakistan. He received his MSc and MPhil degrees from Department of Mathematics UAJK in 2013 and 2016, respectively. He is working in the field of nanocomposites and hybrid nanofluids.
Tariq Javed
Tariq Javed is currently working as a professor in the Department of Mathematics and Statistics at International Islamic University, Islamabad, Pakistan. He completed his PhD in mathematics from Quaid-i-Azam University, Islamabad, Pakistan. His research is in the field of computational fluid dynamics focusing on cavity flow problems. Other research areas address modeling of engineering problems, solution of differential equations, numerical analysis, boundary layer flows, stagnation point flows, etc.
K. Loganathan
K. Loganathan is currently working as researcher in the Department of Mathematics and Statistics at Manipal University Jaipur, Rajasthan, India. He received MSc and MPhil degrees in 2014 and 2016, respectively. His areas of interest are fluid dynamics, CFD, convective heat and mass transfer, nanofluids, bioconvection, microorganisms, porous media, etc.
References
- Waini I, Ishak A, Pop I. Unsteady flow and heat transfer past a stretching/shrinking sheet in a hybrid nanofluid. Int J Heat Mass Transf. 2019;136:288–297.
- Abbasi A, Farooq W. A numerical simulation for transport of hybrid nanofluid. Arab J Sci Eng. 2020;45(11):9249–9265.
- Babazadeh H, Shah Z, Ullah I, et al. Analysis of hybrid nanofluid behavior within a porous cavity including Lorentz forces and radiation impacts. J Therm Anal Calorim. 2021;143(2):1129–1137.
- Pourrajab R, Noghrehabadi A, Behbahani M, et al. An efficient enhancement in thermal conductivity of water-based hybrid nanofluid containing MWCNTs-COOH and Ag nanoparticles: experimental study. J Therm Anal Calorim. 2021;143(5):3331–3343.
- Shah Z, Sheikholeslami M, Kumam P, et al. CFD simulation of water-based hybrid nanofluid inside a porous enclosure employing Lorentz forces. IEEE Access. 2019;7:177177–177186.
- Malika M, Sonawane SS. Effect of nanoparticle mixed ratio on stability and thermo-physical properties of CuO-ZnO/water-based hybrid nanofluid. J Indian Chem Soc. 2020;97(3):414–419.
- Çiftçi E. Distilled water-based AlN + ZnO binary hybrid nanofluid utilization in a heat pipe and investigation of its effects on performance. Int J Thermophys. 2021;42(3):1–21.
- Samal SK, Moharana MK. Thermo-hydraulic and entropy generation analysis of recharging microchannel using water-based graphene–silver hybrid nanofluid. J Therm Anal Calorim. 2021;143(6):4131–4148.
- Tiwari AK, Pandya NS, Said Z, et al. 4S consideration (synthesis, sonication, surfactant, stability) for the thermal conductivity of CeO2 with MWCNT and water based hybrid nanofluid: an experimental assessment. Colloids Surf, A. 2021;610:125918.
- Kamel MS, Al-Oran O, Lezsovits F. Thermal conductivity of Al2O3 and CeO2 nanoparticles and their hybrid based water nanofluids: an experimental study. Period Polytech Chem Eng. 2020;65(1):50–60.
- Lahari MC, Sai PST, Swamy KN, et al. 2018. Investigation on heat transfer properties of water based TiO2-ZnO nanofluids. In IOP conference series: materials science and engineering (Vol. 455, No. 1, p. 012092). IOP Publishing.
- Bhattad A. Exergy analysis of plate heat exchanger with graphene alumina hybrid nanofluid: experimentation. IJEX. 2020;33(3):254–262.
- Yadav D, Kumar R, Tiwary B, et al. Rheological characteristics of CeO2, Al2O3 and their hybrid mixture in ethylene glycol base fluid in the wide range of temperature and concentration. J Therm Anal Calorim. 2021;143(2):1003–1019.
- Sheikh NA, Chuan Ching DL, Khan I, et al. Concrete based Jeffrey nanofluid containing zinc oxide nanostructures: application in cement industry. Symmetry. 2020;12(6):1037.
- Nfawa SR, Abu Talib AR, Basri AA, et al. Novel use of MgO nanoparticle additive for enhancing the thermal conductivity of CuO/water nanofluid. Case Stud Therm Eng. 2021;27:101279.
- Acharya N, Bag R, Kundu PK. Influence of hall current on radiative nanofluid flow over a spinning disk: a hybrid approach. Physica E. 2019;111:103–112.
- Acharya N. On the flow patterns and thermal behaviour of hybrid nanofluid flow inside a microchannel in presence of radiative solar energy. J Therm Anal Calorim. 2020;141(4):1425–1442.
- Acharya N, Maity S, Kundu PK. Influence of inclined magnetic field on the flow of condensed nanomaterial over a slippery surface: the hybrid visualization. Appl Nanosci. 2020;10(2):633–647.
- Acharya N. Spectral quasi linearization simulation on the hydrothermal behavior of hybrid nanofluid spraying on an inclined spinning disk. Partial Differential Equations in Appl Math. 2021;4:100094.
- Saba F, Ahmed N, Khan U, et al. Thermophysical analysis of water based (Cu–Al2O3) hybrid nanofluid in an asymmetric channel with dilating/squeezing walls considering different shapes of nanoparticles. Appl Sci. 2018;8(9):1549.
- Benkhedda M, Boufendi T, Tayebi T, et al. Convective heat transfer performance of hybrid nanofluid in a horizontal pipe considering nanoparticles shapes effect. J Therm Anal Calorim. 2020;140(1):411–425.
- Hosseinzadeh K, Roghani S, Asadi A, et al. Investigation of micropolar hybrid ferrofluid flow over a vertical plate by considering various base fluid and nanoparticle shape factor. HFF. 2021;31(1):402–417.
- Sowmya G, Gireesha BJ, Prasannakumara BC. Scrutinization of different shaped nanoparticle of molybdenum disulfide suspended nanofluid flow over a radial porous fin. Int J Numer Methods Heat & Fluid Flow. 2019;30(7):3685–3699.
- Acharya N. On the flow patterns and thermal control of radiative natural convective hybrid nanofluid flow inside a square enclosure having various shaped multiple heated obstacles. Eur Phys J Plus. 2021;136(8):1–29.
- Sahoo RR. Effect of various shape and nanoparticle concentration based ternary hybrid nanofluid coolant on the thermal performance for automotive radiator. Heat Mass Transf. 2021;57(5):873–887.
- Anshori I, Nuraviana Rizalputri L, Rona Althof R, et al. Functionalized multi-walled carbon nanotube/silver nanoparticle (f-MWCNT/Ag NP) nanocomposites as non-enzymatic electrochemical biosensors for dopamine detection. Nanocomposites. 2021;7(1):97–108.
- Chester G, Skinner A, Villa-Garcia A, et al. Iron nanoparticle surface treatment of carbon nanotubes to increase fatigue strength of steel composites. Nanocomposites. 2021;7(1):132–140.
- Safaei-Ghomi J, Kareem Abbas A, Shahpiri M. Synthesis of imidazoles promoted by H3PW12O40-amino-functionalized CdFe12O19@ SiO2 nanocomposite. Nanocomposites. 2020;6(4):149–157.
- Mabood F, Ashwinkumar GP, Sandeep N. Effect of nonlinear radiation on 3D unsteady MHD stagnancy flow of Fe3O4/graphene–water hybrid nanofluid. Int J Ambient Energy. 2020:1–11.DOI: 10.1080/01430750.2020.1831593.
- El-Zahar ER, Mahdy AEN, Rashad AM, et al. Unsteady MHD mixed convection flow of Non-Newtonian Casson hybrid nanofluid in the stagnation zone of sphere spinning impulsively. Fluids. 2021;6(6):197.
- Sulochana C, Aparna SR. Unsteady magnetohydrodynamic radiative liquid thin film flow of hybrid nanofluid with thermophoresis and brownian motion. MMMS. 2019;16(4):811–834.
- Subhani M, Nadeem S. Numerical investigation into unsteady magnetohydrodynamics flow of micropolar hybrid nanofluid in porous medium. Phys Scr. 2019;94(10):105220.
- Krishna MV, Ahammad NA, Chamkha AJ. Radiative MHD flow of Casson hybrid nanofluid over an infinite exponentially accelerated vertical porous surface. Case Stud Therm Eng. 2021;27:101229.
- Gorla RSR, Siddiqa S, Mansour MA, et al. Heat source/sink effects on a hybrid nanofluid-filled porous cavity. J Thermophys Heat Transfer. 2017;31(4):847–857.
- Jamaludin A, Naganthran K, Nazar R, et al. MHD mixed convection stagnation-point flow of Cu-Al2O3/water hybrid nanofluid over a permeable stretching/shrinking surface with heat source/sink. Eur J Mech B/Fluids. 2020;84:71–80.
- Armaghani T, Sadeghi MS, Rashad AM, et al. MHD mixed convection of localized heat source/sink in an Al2O3-Cu/water hybrid nanofluid in L-shaped cavity. Alexandria Engin J. 2021;60(3):2947–2962.
- Acharya N, Mabood F. On the hydrothermal features of radiative Fe3O 4–graphene hybrid nanofluid flow over a slippery bended surface with heat source/sink. J Therm Anal Calorim. 2021;143(2):1273–1289.
- Chamkha AJ, Yassen R, Ismael MA, et al. MHD free convection of localized heat source/sink in hybrid nanofluid-filled square cavity. J Nanofluids. 2020;9(1):1–12.
- Faizal NFA, Ariffin NM, Rahim YF, et al. MHD and slip effect in micropolar hybrid nanofluid and heat transfer over a stretching sheet with thermal radiation and non-uniform heat source/sink. CFDL. 2020;12(11):121–130.
- Jino L, Kumar AV. Natural convection of water-cu nanofluid in a porous cavity with two pairs of heat source-sink and magnetic effect. Int J Mech Prod Engin Res Devel. 2020;10(3):14481–14492.
- Irfan M, Khan M, Khan WA. Numerical analysis of unsteady 3D flow of Carreau nanofluid with variable thermal conductivity and heat source/sink. Results Phys. 2017;7:3315–3324.
- Shehzad SA, Alsaedi A, Hayat T. Hydromagnetic steady flow of Maxwell fluid over a bidirectional stretching surface with prescribed surface temperature and prescribed surface heat flux. PLoS One. 2013;8(7):e68139.
- Hayat T, Shehzad SA, Al-Mezel S, et al. Three-dimensional flow of an Oldroyd-B fluid over a bidirectional stretching surface with prescribed surface temperature and prescribed surface heat flux. J Hydrol Hydromech. 2014;62(2):117–125.
- Waini I, Ishak A, Pop I. On the stability of the flow and heat transfer over a moving thin needle with prescribed surface heat flux. Chin J Phys. 2019;60:651–658.
- Noghrehabadi A, Behseresht A, Ghalambaz M. Natural convection of nanofluid over vertical plate embedded in porous medium: prescribed surface heat flux. Appl Math Mech-Engl Ed. 2013;34(6):669–686.
- Ahmad I, Faisal M, Javed T. Dynamics of copper–water nanofluid with the significance of prescribed thermal conditions. Heat Transfer. 2021;50(5):4248–4263.
- Faisal M, Ahmad I, Javed T. Dynamics of MHD tangent hyperbolic nanofluid with prescribed thermal conditions, random motion and thermo-migration of nanoparticles. J Dispersion Sci Technol. 2021:1–15. DOI: 10.1080/01932691.2021.1931291.
- Ishak A, Nazar R, Pop I. Heat transfer over an unsteady stretching permeable surface with prescribed wall temperature. Nonlinear Anal Real World Appl. 2009;10(5):2909–2913.
- Faisal M, Ahmad I, Javed T. Keller–box simulation for nonzero and zero mass fluxes of nanofluid flow impinging over a bi-directional stretching sheet: an unsteady mathematical model. Int J Mod Phys C. 2021;32(04):2150052.
- Javed T, Faisal M, Ahmad I. Dynamisms of solar radiation and prescribed heat sources on bidirectional flow of magnetized Eyring-Powell nanofluid. Case Stud Therm Eng. 2020;21:100689.
- Ahmad I, Faisal M, Javed T, et al. Numerical investigation for mixed convective 3D radiative flow of chemically reactive Williamson nanofluid with power law heat/mass fluxes. Ain Shams Eng J. 2021. DOI: 10.1016/j.asej.2021.05.022.
- Ahmad I, Faisal M, Javed T, et al. Insight into the relationship between unsteady Cattaneo-Christov double diffusion, random motion and thermo-migration of tiny particles. Ain Shams Eng J. 2021. DOI: 10.1016/j.asej.2021.05.008.