ABSTRACT
Fracture in the hip joint is a major and quite common health issue, particularly for the elderly. The loads exploited by the lower limbs are very acute and severe; in the femur, they can be several folds higher than the whole weight of the body. Nanotechnology and nanocomposites offer great potential in biomedical applications. The organic materials are more biocompatible. Mechanical properties like strength and hardness are challenging parameters which control the selection of a joint. HDPE in its pure form has been successfully used as a prosthetic foot (external) but failed as an implant material due to limited mechanical properties. High-density polyethylene thermoplastic polymer (HDPE) and multi-walled carbon nanotubes (MWCNT)/Nano-Alumina is selected as a potential material for a biomedical implant and its mechanical properties and biocompatibility have been discussed. HDPE/MWCNT/Alumina (Al2O3) nanocomposites have not been explored yet for prosthetic implants. These nanocomposites were prepared in this investigation in different compositions. Prepared material has been physiochemically characterized to check the morphology and the structure. MWCNTs enhanced hardness and elastic modulus of the HDPE. Optimization of the material composition revealed that hybrid composite with structure (2.4% Al2O3 and 0.6% MWCNT) exhibits better mechanical properties compared to other ratios with 3% MWCNTs and 5% MWCNTs. Thermal gravimetric analysis (TGA) dedicates that the percentage of crystallization has been increased to 6% after adding MWCNT to HDPE. The moisture absorption decreased to 90% with 5% MWCNT. Experimental results of Colorimetric assay (MTT) of a normal human epithelial cell line (1- BJ1) over Al2O3/MWCNT@HDPE showed <20% cytotoxic activity, proving its acceptance for medical use. HDPE/MWCNT/Al2O3 nanocomposites emerged as a candidate material for artificial joints.
1. Introduction
Hip joint represents pose a major health challenge to medical fraternity nowadays. The hip prosthesis is a key factor in the selection of biomaterials and the fabrication of replacement joints to meet the requirements of arthroplasty. Massive loads experienced by the limbs pose another challenge. Abnormal combinations of mechanical and physical characteristics are the main parameters that control the quality and feasibility of the hip joint. While joint replacement represents attractive cases in the specialization of orthopedic surgery but maintaining the design and structure for a long time is still a big challenge. The mean half-life time of the hip joint is usually among the range of 15–20 years. High strength, toughness, tailored stiffness, resistance to impact and corrosion, and biocompatibility are critical for tissue substitute structures. Widely used prosthetic materials include ceramics and metals. The metals and alloys are typically used for fracture support, facial and dental restoration, and stents. The biomedical-grade Ti alloys are widely preferred as a load-bearing implant material. The Ti-alloys exhibit excellent tribological properties but they have certain drawbacks such as high cost and weight. There are several other low-cost metals and alloys, which are also used as implant materials [Citation1]. These metals release some toxins over a period questioning their biocompatibility [Citation2]. The ions and the debris generated from metallic materials during bio-tribocorrosion are hazardous for the health of the patient. The mechanical wear and high chemical activity resulting in corrosion, are responsible for producing hazardous debris [Citation3]. The ceramic materials are typically used in orthopedic and dental reconstruction as well as making synthetic valves. Among inorganic implant materials for hip joint replacement, a combination of alumina and silicon nitride exhibited less wear for physically challenging gait requirements [Citation4]. Poor ductility and high brittleness is a limiting factor in the application of ceramic materials in the prosthetic application.
Organic materials, largely polymers are now preferred for such applications due to a wide classification of chemical compositions, characteristics, feasibility, and biocompatibility [Citation5–Citation7]. While polymers are typically used for grafts, catheters, tendons, and softer tissue restoration. In recent times, the less weight and biocompatibility of polymers have led to their use in prosthetic applications but their low strength has been a limiting factor. Among polymers, ultra-high molecular weight polyethylene (UHMWPE) and its composites were successfully used as a prosthetic hip joint material. UHMWPE exhibits acceptable cytocompatibility, mechanical and tribological properties [Citation2]. Hydroxyapatite (Ca5(OH)(PO4)3) known as HA, constitutes 70% of human bones. It is a primary mineral present in bones and teeth. The HA nanorods and nanoplates were recommended for the biomedical applications [Citation8]. HDPE exhibits good mechanical behavior includes high strength to density ratio, lightweight, and chemical resistance. However, it possesses low hardness and is unfit for prolonged use [Citation9–Citation13]. A few studies attempted to improve the properties of HDPE by adding various types of fillers such are talc, nano-hydroxyapatite, and nano aluminum oxide [Citation14,Citation15]. The results displayed an initial increase in the degree of crystallinity and modulus of the composites, followed by a decrease at higher ratios [Citation16,Citation17]. Also, the friction coefficient of composites reduced, and the hardness increased with the increment of carbon fibers [Citation18,Citation19]. HDPE/Hydroxyapatite (HA) composites have been assembled and commercialized under the name of HAPEX™, showing very promising mechanical properties alike human bone [Citation20,Citation21]. It was observed that by replacing the HA content with alumina, the tribological characteristics of HAPEX™ improved significantly [Citation22,Citation23]. The HDPE was used as a total hip joint replacement material. The clinical observations showed that the joint loosened over long-term use and resulted in the ultimate failure of the arthroplasty. Thus, HDPE in its pure form was not recommended for hip joint implants requiring challenging gait necessities [Citation24]. However, HDPE has been used for the prosthetic foot, fixed externally with performance conformance of 94%, and the patient satisfaction of 85% [Citation25] .
Since the great discovery of polymer composites by the Toyota research group [Citation26], a new track of research has flourished in the field of joint replacement. Previously, researchers used to apply inorganic nanomaterials as load-bearing components in the preparation of composites with very high processing and manufacturing costs [Citation27]. Furthermore, preparing composites based on inorganic compounds may produce toxic materials, which are not suitable for medical use. Nanotechnology provides a new opportunity to improve the performance of the composites together with the carbon compounds because of the unique characteristics of the nanoparticles. Nanocarbon materials like fullerene, carbon nanofibers and carbon nanotubes have earned great attention in polymer science. Carbon nanotubes or single layers of graphene rolled into a cylinder shape, have been commonly applied and evolved into diverse research directions including medical applications. CNT usually exists in 2 phases, single-walled and multiwalled, with different characteristics properties [Citation28–Citation33]. There are different types of techniques that have been improved for synthesizing CNT which mainly involve vapor phase routes. Commonly, CNTs are produced by chemical vapor deposition, laser ablation, and carbon arc-discharge processes [Citation34]. The amalgamation of carbon nanostructures and polymer matrices were widely studied to adjust the mechanical properties and to extend their applications [Citation35,Citation36]. Recently, carbon nanotubes and graphite were excessively used to develop composites for different applications [Citation37–Citation48]. MWCNT have truly superior mechanical, electrical properties. For example, they are stronger then steal, much better conductors then copper. Their Young’s modulus is over 1 TPa and their tensile strength is estimated to be 10–60 GPa so by adding MWCNTs will affect the mechanical properties and improve the hardness as reported in many articles [Citation49–Citation52].
The exploration of HDPE as a potential substrate for nanocoating is a possibility that might be studied. But the basic requirement of a sustainable load-bearing joint includes its properties from the core and its biocompatibility. The science and technology is ever aspiring to explore superior materials with lesser liabilities.
The HDPE is light in weight than most metallic and ceramic implants but it is not suitable in its pure form for a load-bearing prosthetic implant. Alumina has been successfully used as a constituent of the ceramic implant. The present prosthetic implant materials offer a solution but come with side effects and limitations. After the successful application of UHMWPE for prosthetic implants and HDPE for external prosthetic limbs and the fact that the metallic implants have their own hazardous and the ceramic implants have limitations, it is worth investigating to explore the possibility of HDPE based nanocomposites for the prosthetic implants. The research design of the present study includes the preparation of an HDPE based nanocomposite, which includes the preparation of the nanocomposite with a limited amount of MWCNT and alumina and their characterization. The cytotoxicity of the selected nanocomposites has been studied to determine their biocompatibility. Such nanocomposites are expected to provide a low cost and lightweight nontoxic alternative to the conventional hip joint materials for challenging gait requirements. This research focuses mainly on studying the effect of impeding MWCNT inside the pores as well as over the surface of HDPE polymer. In this research work, different ratios of MWCNT were incorporated inside the matrix of HDPE to improve the hardness and other mechanical properties of polymer from the perspective of hip joint application. Al2O3/MWCNT@HDPE nanocomposite was prepared by the wet chemical method. The nanocomposite was characterized to examine the structure and morphology. MWCNT act as solid lubricants and are used in wear-resistant applications such as bearing materials. The same properties of MWCNT were exploited in this study to improve the overall mechanical properties of HDPE. Also, the influence of adding MWCNT over the normal cell (Cytotoxic activity test) was studied to determine its feasibility for medical applications.
2. Materials and methods
High-density polyethylene (tensile strength-27.5 MPa and density-0.944 g/cm3) was purchased from Nanotech company. MWCNTs and nano alumina (Al₂O₃) used in this research were purchased from Middle east company for the petrochemical industry. The MWCNT had 8–13 nm diameter, 3–15 μm length, and 99.87% purity. The physical properties of nano-Al₂O₃ are density at RT 3.9 g/cm3, particle size 20–30 nm, and 99.95% purity.
The formation of a prosthetic hip joint is presented in ). The major components of a prosthetic hip joint are acetabular cup, femoral head ball, and femoral stem. A liner is also used sometimes between the acetabular cup and the femoral head. The first composition of MWCNT@ HDPE and the second composition of Al2O3/MWCNT@ HDPE composite were prepared by wet chemical approach as presented in (b).
In particular uniform and reproducible dispersion in liquid phases considered one of the most important challenges in developing polymer nanocomposite applications. The dispersion process was done in the presence of organic solvent ethanol (absolute C2H2OH). Polymer nanocomposite dispersed with ethanol was sonicating using digital Ultrasonic cleaning which utilizes cavitation bubbles incited by high recurrence (sound) waves to shake a fluid. The tumult creates the clinging of contaminants to the substrates. The sonicating time was fixed at 35 min. The composites were stirred using MS300HS hot stirrer. The time for stirring was fixed at 15 min [Citation53,Citation54]. The composites were dried using Dreier (Heraeus UT 6050) recirculated drying oven at a constant temperature to 250 °C for 45 min to evaporate the organic solvent (ethanol) [Citation55,Citation56].
Thermally conductive nano composites were manufactured by mixing MWCNT and HDPE using internal mixing (Melt blinding process). The mixing chamber contains two cylindrical screw rollers for melting and mixing. The internal mixer can rotate up to 2500 rpm powered by a motor of 7.5 hp. The polymer nano composite were melted in the internal mixer at a temperature of 185°C for about 20 min. The weight concentration of the MWCNT in the polymer matrix was initially 0, 1, 2, 3, and 5 %. Following the extraction of HDPE/MWCNT composite from the inward blender, hot pressing was done to transform the specimen into the desired shape. The dog bone type ASTMD-638-IV specimen were employed using two types of molds for the thermal conductivity and tensile strength tests, respectively. This process was done at a temperature of 190°C and a pressure of 150 bar. The total pressing time of specimen was about 45 min including time for holding the sample to cool them for 15 min. The specimens were cooled to the room temperature to enable crystallization and prevent the reappearance of the amorphous phase. HDPE/Al2O3/MWCNTS were produced by the same process as above.
Figure 1. (a) Formation of a hip joint, 1-acetabular cup, 2-femoral head ball, 3-femoral stem, 4-assembled hip joint. (b) Schematic diagram of HDPE/MWCNT/Al2O3 manufacturing process.
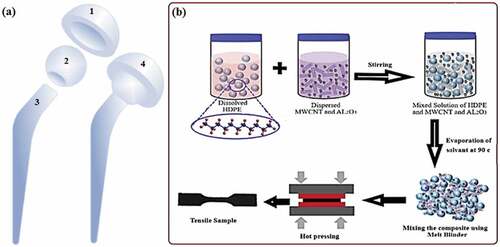
Then the composite was stirred for 1 hour. Thereafter, the powder was separated and dried to remove the excess ethanol and the surfactant by maintaining a temperature of 185°C for about 120 min. Following the extraction of Al2O3/MWCNT@HDPE nanocomposite from the inward blender, hot pressing was done to obtain the desired shape of the specimens. Then, the specimens cooled rapidly to room temperature.
2.1. Material characterization
X-ray diffraction (XRD) technique was utilized to check the composition of phase material and the crystallinity of the prepared material [Citation57]. The XRD measurement was performed using (Siemens XRD D5000) and a copper X-ray source within the range from 0° to 70°. The voltage and current were adjusted at 40 kV and 50 mA, respectively. The morphology and microstructure characterization of Al2O3/MWCNT@HDPE hybrid composites were studied using SEM and TEM systems [Citation58–Citation60].
Mechanical testing is applied to examine the characteristics like hardness, modulus, fracture toughness, and yield strength, etc. Uniaxial compression and tensile testing are typically measured to investigate the acquired elastic modulus [Citation61]. The hardness test employs an indenter probe that is located over a surface under a specific weight load. Usually, the size of the indentation is calculated to determine hardness. Microhardness testing is considered as an acceptable industry standard for quality control for hardness data [Citation62]. The Vickers microhardness tests were conducted to investigate the influence of MWCNTs. The total load is normally applied between 10 and 15 seconds. The zone of the slanting surfaces of the indentation was investigated and the Vickers hardness which is calculated by dividing the weight load (kg) with the area of indentation (mm2) [Citation63]. Tensile measurements were performed on a universal testing machine with a speed of 5 mm/min. Percentages of the MWCNT were maintained between 1–5%. All samples were tested in the same environmental conditions.
Thermal gravimetric analysis (TGA) test estimates the weight change of a material, either as an element of expanding temperature, or isothermally as a function of time in the environment of nitrogen or helium. The degeneration behavior of polymers and their hybrid composites is usually determined by 3 parameters: the temperature at which the framework starts to debase, the degradation temperature Td, and the degradation rate Dr, which is found in the subsidiary weight reduction as an element of temperature curve [Citation64,Citation65]. TGA analysis was performed using (DTG −60 SIMULTANEOUSDTG- TG SHIIMAADZU, JAPAN) for each sample and HDPE/MWCNT/Al2O3 nanocomposite. The specimens were heated from 25°C to 750°C at a rate of 10°C/min in a nitrogen atmosphere. Flexural and mechanical characteristics usually decrease as the water absorption ratio increases. Tensile modulus was found to decrease at a higher level of water absorption, which is considered as a sensitive property. Therefore, it is important to investigate the effect of adding MWCNT over the moisture absorption of HDPE.
Water absorption examination (ASTM D750-95) has been carried out by a total inundation of 5 samples in distilled water at room temperature for 72 h. The water absorption was calculated by weighing the samples at time intervals. Since this application is intended for medical use, it is very important to check whether the material is feasible to be used inside the human body. Cell viability test was dedicated by the mitochondrial-dependent reduction of yellow MTT (3-(4,5-dimethylthiazol-2-yl)-2,5-diphenyl tetrazolium bromide) or MTT essay to magenta formazan [Citation66].
All measurements were done in an antiseptic zone applying a laminar flux cabinet conforming to the biosafety class II level (Baker, SG403INT, Sanford, ME, USA). Cells were suspended in dulbecco’s modified eagle medium (DMEM-F12) with 1% antibiotic-antimycotic mixture (10,000 U/ml Potassium Penicillin, 10,000 µg/ml Streptomycin Sulfate and 25 µg/ml Amphotericin B) and 1% L-glutamine at 37°C under 5% CO2. Cells were refined for 5 days and then implanted at a concentration of 10*103 cells/well in unprecedented plenary outgrowth medium, in 96-well microtiter plastic plates. After 48 h of incubation, the medium was aspirated, 40 ul MTT salt (2.5 μg/ml) was added to each well and hatched for further four hours at the same conditions [Citation67,Citation68]. Absorbance was estimated using a microplate multi-well reader (Bio-Rad Laboratories Inc., model 3350, Hercules, California, USA) at 595 nm at a reference wavelength of 620 nm.
3. Results and discussion
3.1. Characterization
The HDPE/MWCNT nanocomposites have been fabricated and characterized by X-ray diffraction, scanning electron microscope (SEM), and Transmission electron microscopy (TEM). dedicates the XRD diffraction pattern of HDPE, MWCNT, and HDPE/MWCNT hybrid nanocomposite. HDPE presented with two characteristic peaks at 21.4° and 23.2°. These peaks were also detected in the hybrid nanocomposite. The intensity of the peaks in the hybrid nanocomposite is greater ascribed to the increase in crystallinity. This could happen as a result of the interaction and crystallization behavior of MWCNT with HDPE during the blending process. The XRD pattern of MWCNTs is shown as well in . MWCNT exhibits 2 peaks at around 2θ = 26° and other broad peak centered at 2θ = 43° corresponding to the (002) and (100) Bragg reflection planes having the interlayer spacing of 3.213 and 2.012 Å respectively [Citation69]. The presence of MWCNT is acknowledged by the XRD diffraction pattern.
The images obtained from the transmission and scanning electron microscopes to explore the nanocomposite structure and the matrix distribution are shown in . Scanning electron pictures (a) of the nanocomposite samples clearly show the MWCNT among the polymer matrix. In the processing of HDPE and MWCNT blends by the melt blinder, the polymer chains of HDPE are overlapped with each other as observed in the SEM figures. The TEM images are shown in (b) confirm the MWCNT structure and the nano-scaled design of the material. The uniform dispersion of MWCNT in a polymer matrix is a cumbersome task. The fairly homogenous distribution of the MWCNT over the whole matrix can be also observed indicating satisfactory suspension of the MWCNT in the HDPE. Hence the wet chemical synthesis of HDPE/MWCNT nanocomposites has been successfully achieved.
3.2. Mechanical properties
) presents the stress-strain curve for HDPE/MWCNT/Al2O3 nanocomposite. It may be seen that the composite specimen exhibits the highest ultimate tensile stress at 0.3 MPa. The stress, as well as the strain of the nanocomposites with higher concentration of MWCNT, is more than the ones with lower concentrations. Higher stress may be attributed to the reinforcement of the polymer matrix and the exhibition of higher strain is complemented with the increase in ductility in the nanocomposites () with high MWCNT content. This strain behavior is ascribed to the longitudinal orientation and the thread-like formation of the MWCNT, observed in the TEM pictures in (b), which facilitates the effective transfer of stress from the matrix to the MWCNT [Citation13,Citation15,Citation30]. High ductility coupled with higher stress () has resulted in a higher strain. As examined from (b,c), the Vicker’s hardness increases up to 37% with increasing the addition of MWCNTs compared to pure HDPE. The bulk hardness increases consistently with the addition of the MWCNTs. On closer examination of the stress-strain curve (a), the elastic modulus of HDPE is more than 1% and 2% MWCNTs however, as the percentage of MWCNT is increased beyond 2%, the elastic modulus improves and exhibits higher value than HDPE. This might be credited to the narrowing of the interspaces between molecules and reducing their mobility. One of the best ways to reinforce mechanisms in polymer matrices is to transfer the shear stresses in the nanoparticle-matrix interface and to nucleate a 3D nanostructured network. It reduces the mobility of the polymer bonds, thus leading to changes in the elastic modulus of the nanocomposite [Citation70,Citation71].
Table 1. Mechanical properties of HDPE/MWCNT nanocomposite.
illustrates the mechanical properties of HDPE and nanocomposites i.e. elastic modulus, ultimate tensile stress (UTS), elongation, toughness, and hardness. The maximum value of elastic modulus reaches up to 1.02 GPa with 5% MWCNT, higher by 37%, compared with the pure HDPE. The 3% MWCNT nanocomposite exhibit higher elastic modulus than the pure HDPE while it is of the same order for 1% and 2% nanocomposite. The UTS first decreases up to 2% of MWCNT and then increases. The ductility also displays a consistent increase with the addition of MWCNTs. The toughness has been calculated from the area under the load stroke curve, the toughness of the pure polymer was about 160 MJm−3 which is less when 1% MWCNT was impeded into the polymer. However, the toughness decreased sharply with the increase of CNTs in the HDPE matrix probably due to the agglomeration of MWCNT in the HDPE matrix with increasing condensation of filler content. The hardness exhibits a consistent increase with the addition of the MWCNT.
Figure 4. (a) Stress-strain curve for HDPE/MWCNT nanocomposite, (b) Hardness of hybrid Nanocomposite and (c) Linear equation of micro vickers hardness.
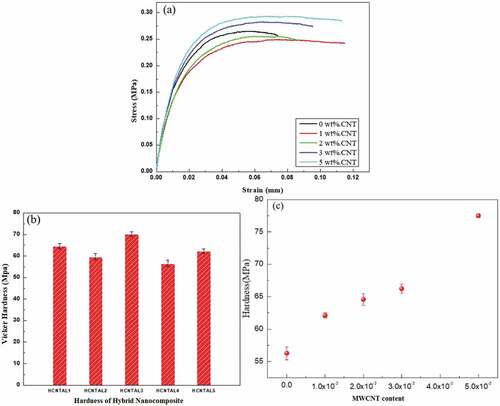
Apart from the toughness, the other mechanical properties have marked improvement ascribed to reasonably good dispersion of MWCNT in HDPE polymer, evident from the SEM and TEM figures. According to recent research work, MWCNTs reinforcement mostly provides strength refinement, furthermore, it can also transfer their strength to composite materials by taking over the load applied to the matrix material. It has been confirmed that MWCNTs prohibit the propagation of cracks in the matrix during erosion situations through their foaming motion. This case is also confirmed by the literature. However, the strengthening can vary according to the reinforcement material but the MWCNTs generally give positive results toward the improvement of mechanical properties [Citation72,Citation73]. The mechanical properties of HDPE/MWCNT nanocomposites are enhanced due to effective CNTs reinforcement in the composites. The good dispensability of the MWCNT in the HDPE is a key factor for increasing the yield strength, ductility, and impact strength. The transfer of stress from the matrix to the reinforcement depends on the interfacial interaction, which was sound owing to the uniform dispersion. Nevertheless, the optimal MWCNT content in the HDPE matrix is important for maximizing the mechanical properties. As the amount of MWCNT increases beyond a certain value, the nanotubes tend to accumulate into clusters compromising the mechanical properties. The thread-like architecture of the MWCNT CNTs may develop a network-like structure by interweaving among themselves and forming Vander Waal and π bonds [Citation74].
The mechanical properties of the composite strengthened with MWCNT along with nano Al2O3 According to the results also it has been found that the addition of alumina linearly increases the hardness particles are given in . The elastic modulus first increases and then reduces indicating that the nano alumina has a positive impact on elastic modulus but as the MWCNT increases, the combined effect of these reinforcements together doesn’t affect the elastic modulus. The maximum elastic modulus is displayed by 0.6 wt%CNT-2.4 wt%Al2O3/HDPE nanocomposite (1 ± 0.073 GPa). The same observation is recorded for UTS, it first improves slightly and then becomes stagnant. The maximum hardness is exhibited by 1.2 wt%CNT-1.8 wt%Al2O3/HDPE nanocomposite. It records a hardness of 70.20 ± 1.3 MPa marking an increase of 6% compared to 3 wt%MWCNT. Toughness and UTS of the composites containing 0.6 wt%CNT-2.4 wt%Al2O3 increased by 2.35 times and 2.9% compared to 3 wt%MWCNT. It is interesting to note that the improvement in ductility in the hybrid nanocomposites is much better than that in MWCNT nanocomposites. The presence of nano alumina particles may have reduced the agglomeration of the MWCNT in the polymer matrix, increasing ductility. For composites containing 1.8 wt%CNT-1.2 wt%Al2O3, the ductility increased by 145% and 141% compared with 3 wt% and 5 wt%MWCNT nanocomposites respectively.
Table 2. Mechanical properties of hybrid Al2O3/HDPE/MWCNT nano composite.
It has been found that adding aluminum oxide besides MWCNTs marked impressive improvements in mechanical properties, compared with 3/5 wt% MWCNTs/HDPE nanocomposites. The possible reason behind this observation is the homogenous dispersion of nanotubes into the polymer matrix in the presence of nano alumina particles. The addition of very small particles (nano Alumina) leads to the segregation of the particles in the polymer matrix. To retard the agglomeration of the particles, the capping agent (TWEEN) was used [Citation75]. The addition of MWCNT and nano alumina produced fine nanocomposites. Usually, the interface between the matrix and the filler is the weakest link in the composite influencing the mechanical properties. The capping agent has helped to secure a strong linkage between the nano alumina and the HDPE matrix [Citation76]. The hybrid nanofillers have resulted in better mechanical properties and supplemented better dispersion of each in the matrix.
3.3. TGA analysis of HDPE/MWCNT composites
TGA curves exhibit onset temperature dwindling with the addition of chemically treated MWCNT due to the presence of amorphous carbon in the MWCNTs. Mass loss degradation temperature of the nanocomposite increases as the MWCNTs ratio increases according to the TGA data as shown in (a). This observation may be ascribed to the strengthening of the HDPE matrix by MWCNT, which has higher thermal conductivity and a favorable effect on the stability of nanocomposites [Citation77].
Figure 5. (a) TGA curves of MWCNT/HDPE nanocomposites and (b) DrTGA curve of MWCNT/HDPE nanocomposite.

The curves of all the materials exhibit similar shape ascribed to the same matrix material (HDPE). The lowest weight loss percentage is obtained for 3% and 5% MWCNTs/HDPE nanocomposites signifying that the mass loss melting speed rate decreases with increasing MWCNTs weight ratio and the melting point temperature increases as shown in (b). The zigzag variation of the weight loss/temperature curve may be credited to the anisotropy of the material. As the content of MWCNT increased in the HDPE matrix, the anisotropy also increased, consequentially increasing the variation of the curve. The presence of MWCNT in the HDPE matrix has led to the non-homogenous distribution of the nanotubes in longitudinal and transverse directions, hence this anisotropy. Irrespective of the content of MWCNT, the weight loss curves of nanocomposites exhibit a similar trend, appearing above the HDPE due to the increased thermal conductivity.
3.4. Water absorption
One of the most important parameters for polymer nanocomposite is water absorption because it affects their life cycle [Citation78,Citation79]. The idea that cellulosic fibers easily absorb water is a major reason for fiber surface treatments. The particles treated by graphite fibers and its derivatives may absorb less amount of moisture, and thus support adhesion to the polymer matrix, which results in better performance in a humid environment. The high-water absorption of the polymer nanocomposite may cause difficulties during processing as well as in service. This can be due to partial curing of the thermosetting matrices, the presence of gaps or cracks, or even poor matrix–fiber adhesion [Citation80]. It was observed that MWCNT/HDPE nanocomposites display less water absorption compared to that of pure HDPE, as shown in . The inclusion of MWCNTs facilitated the crystallization of HDPE and therefore led to higher crystallinity in HDPE nanocomposites making it difficult for water to diffuse into the HDPE matrix.
3.5. Cytotoxic activity of Al2O3/HDPE/MWCNT composites
The in-vitro cytotoxicity tests of HDPE/1.2 wt%MWCNT/1.8 wt%Al2O3 nanocomposites over human normal epithelial cell line 1- BJ1 (normal Skin fibroblast) are given in . The test solution was prepared by using the hybrid composite with concentrations between 100 to 0.78 µg/ml and 100–75PPM MTT in separate iterations. This method is reliable and has good reproducibility [Citation81]. The normal cells are very sensitive to any foreign material. The MTT assay probing system detected cell viability. During the initial (lower) concentration of the nanocomposites (<10 µg/ml) the cell viability varied between 79–90% as this concentration was not sufficient to provide exposure to the broader human cell sample. As the concentration of the nanocomposites increased beyond 10% and more, the cell viability stabilized around 83%. Higher the concentration of the nanocomposites, the better was the cell viability. According to the results, the majority of cells remains safe and viable under all concentration. The minimum cell viability was around 80%, which is considered as biocompatible.
For hip joint implants, the metallic and ceramic materials have been explicitly used but with limitations and a few hazards. A few polymers such as UHMWPE [Citation2] and HA [Citation8] have been tried with promising results. The HDPE in its pure form was not as successful as a potential material [Citation24]. In the present study, the HDPE-MWCNT/Alumina nanocomposites have been developed and characterized for mechanical properties and cytocompatibility and the results are encouraging. These composites have emerged as a potential prosthetic implant material with less weight, less cost, and satisfactory biocompatibility. HDPE is a promising material; its nanocomposite has not been evaluated for prosthetic implants to date.
4. Conclusions
The metallic and ceramic materials have several disadvantages. Polymers in their pure form are not suitable for prosthetic implants. Nanotechnology and nanocomposites offer great potential in biomedical applications. The organic materials are more biocompatible. HDPE in its pure form has been successfully used as a prosthetic foot (external) but failed as an implant material due to limited mechanical properties. Alumina and MWCNT have been used as property enhancing fillers in certain biomedical nanocomposites. Hence an organic nanocomposite with HDPE and MWCNT/Nano-Alumina is selected as a potential material for a biomedical implant and its mechanical properties and biocompatibility have been discussed. HDPE/MWCNT-Alumina nanocomposites have not been explored for prosthetic implants. The HDPE polymer reinforced with MWCNTs and alumina by using a wet chemical approach to develop hybrid nanocomposites. Structure and morphology of the material have been characterized using SEM, TEM, and XRD. It has also been reported that there is a weak interface between 1, 2%wt MWCNT particles with the polymeric HDPE material, however good physical bonding of MWCNTs was observed when the ratio becomes 5%. Improvement in the mechanical properties of the material after incorporation of the MWCNT particularly with a ratio of 5%. The hybrid nanocomposites displayed better mechanical properties than the MWCNT/HDPE. TGA characterization of the prepared composite exhibits that mass loss melting speed rate decreases with increasing MWCNTs weight ratio and melting point temperature increases. The improvement in ductility in the hybrid nanocomposites is much better than that in HDPE/MWCNT nanocomposite. The water absorption studies displayed good performance with the lowest absorption (<0.1%) for 5% MWCNT compared to other ratios. As this work is going to be applied for medical applications, it is important to determine the biocompatibility of the hybrid nanocomposites. Cytotoxicity or cell cycle study of the normal cells has been done for this purpose and it shows low toxicity (<20%) against human normal cells. The results show that these composites are strong enough to bear the gait requirements of the hip joint and their cytocompatibility is satisfactory. According to these results, we can conclude that HDPE/MWCNTs/Al2O3 nanocomposite could be a good and promising candidate material for the total joint replacement and other structural biomedical applications. The authors suggest further studies on the tribological performance of the HDPE/MWCNTs/Al2O3 hybrid nanocomposites to characterize them comprehensively and approve them for biomedical implant material.
Highlights
Hip joint is a major load bearing joint and its deterioration is a common health issue.
Metals, ceramics and polymers have limitations as prosthetic hip-joint material.
HDPE/MWCNT/Al2O3 nanocomposites were explored for prosthetic hip-joint material.
The nanocomposites exhibited better mechanical properties and biocompatibility.
HDPE/0.6% MWCNT/2.4% Al2O3 emerged as the optimum composition.
Acknowledgment
Authors thankfully acknowledge the funding provided by the Scientific Research Deanship, King Khalid University, Kingdom of Saudi Arabia for the Small Research Group, under the grant number R.G.P1./96/40.
Disclosure statement
No potential conflict of interest was reported by the authors.
Additional information
Funding
References
- Luo Y, Yang L, Tian M Application of biomedical-grade titanium alloys in trabecular bone and artificial joints. In: Biomaterials and medical tribology. Elsevier; 2013. p. 181–216.
- Patil NA, Njuguna J, Kandasubramanian B. UHMWPE for biomedical applications: performance and functionalization. Eur Polym J. 2020;125:109529.
- Wang Z, Yan Y, Wang Y, et al. Lifecycle of cobalt-based alloy for artificial joints: from bulk material to nanoparticles and ions due to bio-tribocorrosion. J Mater Sci Technol. 2020;46:98–106.
- Shankar S, Nithyaprakash R, Sugunesh AP, et al. Experimental and finite element wear study of silicon nitride against alumina for hip implants with bio-lubricant for various gait activities. Silicon; 2020. p. 1–12.
- Ramakrishna S, Mayer J, Wintermantel E, et al. Biomedical applications of polymer-composite materials: a review. Compos Sci Technol. 2001;61(9):1189–1224.
- Kirillova A, Ionov L. Shape-changing polymers for biomedical applications. J Mat Chem B. 2019;7(10):1597–1624.
- Backes EH, Pires LDN, Beatrice CAG, et al. Fabrication of biocompatible composites of poly (lactic acid)/hydroxyapatite envisioning medical applications. Polymer Engineering & Science.
- Elbasuney S. Green synthesis of hydroxyapatite nanoparticles with controlled morphologies and surface properties toward biomedical applications. J Inorg Organomet Polym Mater. 2020;30(3):899–906.
- Wu X, Zhang J, Wu C, et al. Study on tribological properties of UHMWPE irradiated by electron beam with TMPTMA and TPGDA as crosslinking agents. Wear. 2013;297(1–2):742–751. .
- Schwartz CJ, Bahadur S, Mallapragada SK. Effect of crosslinking and Pt–Zr quasicrystal fillers on the mechanical properties and wear resistance of UHMWPE for use in artificial joints. Wear. 2007;263(7–12):1072–1080.
- Kilgour A, Elfick A. Influence of crosslinked polyethylene structure on wear of joint replacements. Tribol Int. 2009;42(11–12):1582–1594.
- Wang L, Chen G. Dramatic improvement in mechanical properties of GNs‐reinforced HDPE nanocomposites. J Appl Polym Sci. 2010;116(4):2029–2034.
- Mohammed MT. Nanocomposites in total hip joint replacements. In: Applications of nanocomposite materials in orthopedics. Elsevier; 2019. p. 221–252.
- Gupta A, Tripathi G, Lahiri D, et al. Compression molded ultra high molecular weight polyethylene–hydroxyapatite–aluminum oxide–carbon nanotube hybrid composites for hard tissue replacement. J Mater Sci Technol. 2013;29(6):514–522.
- Xue Y, Wu W, Jacobs O, et al. Tribological behaviour of UHMWPE/HDPE blends reinforced with multi-wall carbon nanotubes. Polym Test. 2006;25(2):221–229.
- Dangsheng X. Friction and wear properties of UHMWPE composites reinforced with carbon fiber. Mater Lett. 2005;59(2–3):175–179.
- Arash B, Park HS, Rabczuk T. Mechanical properties of carbon nanotube reinforced polymer nanocomposites: A coarse-grained model. Compos Part B Eng. 2015;80:92–100.
- Liu Y, Sinha SK. Wear performances and wear mechanism study of bulk UHMWPE composites with nacre and CNT fillers and PFPE overcoat. Wear. 2013;300(1–2):44–54.
- Rahman M, Hoque MA, Rahman GT, et al. Evaluation of thermal, mechanical, electrical and optical properties of metal-oxide dispersed HDPE nanocomposites. Mater Res Express. 2019;6(8):085092. .
- Wang M, Ladizesky NH, Tanner KE, et al. Hydrostatically extruded HAPEX™. J Mater Sci. 2000;35(4):1023–1030.
- Hermán V, González G, Noris-Suárez K, et al. Biocompatibility studies of HDPE–HA composites with different HA content. Polym Bull. 2015;72(12):3083–3095.
- Nath S, Bodhak S, Basu B. Tribological investigation of novel HDPE‐HAp‐Al2O3 hybrid biocomposites against steel under dry and simulated body fluid condition. J Biomed Mater Res A. 2007;83(1):191–208.
- De Santis R, Gloria A, Ambrosio L Composite materials for hip joint prostheses. In: Biomedical composites. Elsevier; 2017. p. 237–259.
- Wroblewski B. Wear of the high-density polyethylene socket in total hip arthroplasty and its role in endosteal cavitation. Proc Inst Mech Eng H. 1997;211(1):109–118.
- Jensen J, Craig JG, Mtalo LB, et al. Clinical field follow-up of high density polyethylene (HDPE)-Jaipur prosthetic technology for trans-femoral amputees. Prosthet Orthot Int. 2004;28(2):152–166. .
- Simon GP. Polymer blends and alloys. Routledge; 2019.
- Park HJ, Badakhsh A, Im IT, et al. Experimental study on the thermal and mechanical properties of MWCNT/polymer and Cu/polymer composites. Appl Therm Eng. 2016;107:907–917.
- Thirumalai J. Hydroxyapatite: advances in composite nanomaterials, biomedical applications and its technological facets. BoD–Books on Demand; 2018.
- Gopanna A, et al. Polyethylene and polypropylene matrix composites for biomedical applications. In: Materials for biomedical engineering. Elsevier; 2019. p. 175–216.
- Parwez K, Budihal SV. Carbon nanotubes reinforced hydroxyapatite composite for biomedical application. J Bionanosci. 2014;8(1):61–65.
- Zhong YL, Tian Z, Simon GP, et al. Scalable production of graphene via wet chemistry: progress and challenges. Mater Today. 2015;18(2):73–78.
- Liang W, Wang F, Tay TE, et al. Experimental and analytical investigation of epoxy/MWCNT nanocomposites: electrical, thermal properties, and electric heating behavior. Polymer Engineering & Science; 2019.
- Arslan M, Dönmez G, Ergün A, et al. Preparation, characterization, and separation performances of novel surface modified LbL composite membranes from polyelectrolyte blends and MWCNT. Polymer Engineering & Science; 2019.
- Janas D, Koziol K. A review of production methods of carbon nanotube and graphene thin films for electrothermal applications. Nanoscale. 2014;6(6):3037–3045.
- Armentano I, Fortunati E, Gigli M, et al. Effect of SWCNT introduction in random copolymers on material properties and fibroblast long term culture stability. Polym Degrad Stab. 2016;132:220–230.
- Morena F, Armentano I, Montanucci P, et al. Design of a nanocomposite substrate inducing adult stem cell assembly and progression toward an epiblast-like or primitive endoderm-like phenotype via mechanotransduction. Biomaterials. 2017;144:211–229.
- Armentano I, Dottori M, Fortunati E, et al. Biodegradable polymer matrix nanocomposites for tissue engineering: a review. Polym Degrad Stab. 2010;95(11):2126–2146.
- Peponi L, Puglia D, Torre L, et al. Processing of nanostructured polymers and advanced polymeric based nanocomposites. Mater Sci Eng R Rep. 2014;85:1–46.
- Fortunati E, Puglia D, Armentano I, et al. Food Preservation. In: Multifunctional antimicrobial nanocomposites for food packaging applications. Elsevier, 2017. p. 265–303.
- Bari SS, Chatterjee A, Mishra S. Biodegradable polymer nanocomposites: an overview. Polymer Rev. 2016;56(2):287–328.
- Rouf TB, Kokini JL Natural biopolymer-based nanocomposite films for packaging applications. In: Bionanocomposites for packaging applications. Springer; 2018. p. 149–177.
- Tripathy J Polymer nanocomposites for biomedical and biotechnology applications. In: Properties and applications of polymer nanocomposites. Springer; 2017. p. 57–76.
- Kuilla T, Bhadra S, Yao D, et al. Recent advances in graphene based polymer composites. Prog Polym Sci. 2010;35(11):1350–1375.
- Hu K, Kulkarni DD, Choi I, et al. Graphene-polymer nanocomposites for structural and functional applications. Prog Polym Sci. 2014;39(11):1934–1972.
- Mittal G, Dhand V, Rhee KY, et al. A review on carbon nanotubes and graphene as fillers in reinforced polymer nanocomposites. J Ind Eng Chem. 2015;21:11–25.
- Potts JR, Dreyer DR, Bielawski CW, et al. Graphene-based polymer nanocomposites. Polymer. 2011;52(1):5–25.
- Du J, Cheng HM. The fabrication, properties, and uses of graphene/polymer composites. Macromol Chem Phys. 2012;213(1011):1060–1077.
- Fazli A, Moosaei R, Sharif M, et al. Developments of graphene-based polymer composites processing based on novel methods for innovative applications in newborn technologies. Indian J Sci Technol. 2015;8(S9):38–44.
- Zayed AS, Kamel BM, Abdelsadek Osman T, et al. Experimental study of tribological and mechanical properties of aluminum matrix reinforced by Al2O3 /CNTs. Fuller Nanotub Car Nanostruct. 2019;27(7):538–544.
- Shirasu K, Yamamoto G, Nelias D, et al. Mechanical and fracture properties of carbon nanotubes. In: Carbon nanotubes-recent progress. IntechOpen; 2017.
- Shrivastava P, Alam SN, Panda D, et al. Effect of addition of multiwalled carbon nanotube/graphite nanoplatelets hybrid on the mechanical properties of aluminium. Diam Relat Mater. 2020;104:107715.
- Thomas S, Tom P, Umasankar V. Effect of MWCNT concentration on microstructures, mechanical properties and sintering behaviour of spark plasma sintered AA2219-MWCNT composites. Mater Today Proc. 2020;22:1424–1432.
- Takenaka Y, Okuda A, Tojo T, et al., Stirring method. Google Patents; 2017.
- Hirayama S, Hayasaki T, Okano R, et al. Preparation of polymer‐based nanocomposites composed of sustainable organo‐modified needlelike nanoparticles and their particle dispersion states in the matrix. Polymer Engineering & Science; 2019.
- Li S, Zhang X, Zhao J, et al. Enhancement of carbon nanotube fibres using different solvents and polymers. Compos Sci Technol. 2012;72(12):1402–1407.
- Rahman MA, Agha H, Truong T-K, et al. Incorporation and orientational order of aligned carbon nanotube sheets on polymer films for liquid crystal-aligning transparent electrodes. J Mol Liq. 2018;267:363–366.
- Rehani BR, Joshi PB, Lad KN, et al. Crystallite size estimation of elemental and composite silver nano-powders using XRD principles; 2006.
- Saif MJ, Naveed M, Asif HM, et al. Irradiation applications for polymer nano-composites: A state-of-the-art review. J Ind Eng Chem. 2018;60:218–236.
- Kong Q, Wu T, Zhang J, et al. Simultaneously improving flame retardancy and dynamic mechanical properties of epoxy resin nanocomposites through layered copper phenylphosphate. Compos Sci Technol. 2018;154:136–144.
- Xu K, ZhouH, Hu Q, et al. Molecular insights into chain length effects of hindered phenol on the molecular interactions and damping properties of polymer‐based hybrid materials. Polymer Engineering & Science; 2019.
- Kutuk M, Oguz Z. A research on effect of sewage sludge ash on the mechanical properties of composite material. In: World congress on civil, struct., and environment engineering (CSEE’16); 2016.
- He X, Zhuang ZC, Cao T, et al. Relationship analysis between vickers hardness and yield stress of structure material. J Xi’an Uni Sci Technol. 2017;37(2):274–279.
- Lee G, Choi H. Study on interfacial transition zone properties of recycled aggregate by micro-hardness test. Constr Build Mater. 2013;40:455–460.
- Vyazovkin S, Koga N, Schick C. Handbook of thermal analysis and calorimetry: recent advances, techniques and applications. Vol. 6. Elsevier; 2018.
- Guo Y, Xu G, Yang X, et al. Significantly enhanced and precisely modeled thermal conductivity in polyimide nanocomposites with chemically modified graphene via in situ polymerization and electrospinning-hot press technology. J Mater Chem C. 2018;6(12):3004–3015.
- Mosmann T. Rapid colorimetric assay for cellular growth and survival: application to proliferation and cytotoxicity assays. J Immunol Methods. 1983;65(1–2):55–63.
- Thabrew MI, HUGHES RD, MCFARLANE IG. Screening of hepatoprotective plant components using a HepG2 cell cytotoxicity assay. J Pharm Pharmacol. 1997;49(11):1132–1135.
- El-Menshawi BS, Fayad W, Mahmoud K, et al. Screening of natural products for therapeutic activity against solid tumors; Indian J Exp Biol. 201048(3):258–264.
- Patel AK, Trivedi P, Balani K. Processing and mechanical characterization of compression-molded ultrahigh molecular weight polyethylene biocomposite reinforced with aluminum oxide. J NanoSci NanoEng Appl. 2014;4(3):1–11.
- Wang Y-H, Wang W-H, Zhang Z, et al. Study of the glass transition temperature and the mechanical properties of PET/modified silica nanocomposite by molecular dynamics simulation. Eur Polym J. 2016;75:36–45.
- Saba N, Jawaid M, Alothman OY, et al. A review on dynamic mechanical properties of natural fibre reinforced polymer composites. Constr Build Mater. 2016;106:149–159.
- Jin-hua T, Guo-qin L, Huang C, et al. Mechanical properties and thermal behaviour of LLDPE/MWNTs nanocomposites. Mater Res. 2012;15(6):1050–1056.
- Kanagaraj S, Varanda FR, Zhil’tsova TV, et al. Mechanical properties of high density polyethylene/carbon nanotube composites. Compos Sci Technol. 2007;67(15–16):3071–3077. .
- Dai L, Sun J. Mechanical properties of carbon nanotubes-polymer composites. In: Carbon nanotubes–current progress of their polymer composites. InTechOpen; 2016. p. 155–194.
- Pramanik N, Tarafdar A, Pramanik P. Capping agent-assisted synthesis of nanosized hydroxyapatite: comparative studies of their physicochemical properties. J Mater Process Technol. 2007;184(1–3):131–138.
- Akmil N, Luqman C, Ahmad M, et al. Improved mechanical properties of HDPE/nano-alumina composite through silane coupling agent. In: AIP Conference Proceedings. American Institute of Physics; 2012.
- Lozovyi F, Ivanenko K, Nedilko S, et al. Thermal analysis of polyethylene+ X% carbon nanotubes. Nanoscale Res Lett. 2016;11(1):1–7.
- Guedes RM. Creep and fatigue in polymer matrix composites. Woodhead Publishing; 2019.
- Lofrano G, Carotenuto M, Libralato G, et al. Polymer functionalized nanocomposites for metals removal from water and wastewater: an overview. Water Res. 2016;92:22–37.
- Ghasemi E, Kord B. Long-term water absorption behaviour of polypropylene/wood flour/organoclay hybrid nanocomposite. 2009.
- Aslantürk ÖS. In vitro cytotoxicity and cell viability assays: principles, advantages, and disadvantages. Vol. 2. InTech; 2018.