Abstract
A grain structure tailoring strategy was implemented by powder assembly & alloying in carbon nanotube reinforced Al-Cu-Mg composites. Tensile tests revealed that composites with trimodal grain structure had an outstanding combination of strength and ductility, surpassing that of composites with simpler grain structures (e.g. bimodal and unimodal structure). An in-situ tracking of the strain distributions and computational simulations were jointly employed to provide insight into the underlying mechanisms. The results unravel that the trimodal grain structure is more prone to facilitate strain hardening and alleviate strain/stress concentrations, thereby rendering the composites high yield strength and large tensile ductility.
IMPACT STATEMENT
A novel trimodal grain structure was designed for the first time to achieve an excellent strength-ductility combination in CNT/Al-Cu-Mg composites.
GRAPHICAL ABSTRACT
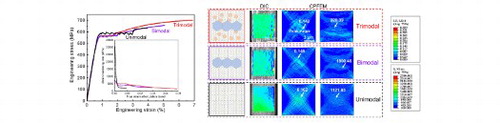
It was known that carbon nanotubes (CNTs), which possess excellent mechanical properties as well as appealing functional attributes, are ideal reinforcements for metals [Citation1,Citation2]. Although the incorporation of CNTs into Al alloys can achieve Al matrix composites with outstanding strengths, a general trend for this strength enhancement is often accompanied by ductility degradation, i.e. strength-ductility ‘trade-off’ [Citation3–5]. For example, 2024Al alloy reinforced with 3 vol.% of CNTs demonstrated an unprecedented yield strength of 780 MPa, overwhelming many high-strength Al alloys (e.g. ∼600 MPa for 7075Al alloy [Citation6]) and nanocrystalline Al, but the ductility of the composites was very limited (∼2%) [Citation4]. This conflict between strength and ductility has become an ‘Achilles’ heel’ for high-strength CNT/Al alloys, hindering their extensive engineering applications. Despite the fact that the ductility reductions in CNT/Al alloy composites are mainly interpreted from CNTs agglomerations and low interfacial strengths [Citation7,Citation8], the dominating factor may be associated with the ultrafine Al grain sizes in these high-strength composites [Citation9]. There are substantial evidences suggesting that the strain hardening capacity, thereby the uniform tensile elongation, of an ultrafine-grained (UFG) metal/alloy is dramatically reduced as a result of the extensive dislocation dynamic recovery (or sinking) at grain boundaries [Citation10]. Therefore, the rejuvenation of the strain hardening ability is critical to overcoming the low ductility problem in high-strength CNT/Al alloys.
The strategy of designing heterogeneous grain structure has emerged as a mighty new tool in improving the tensile ductility of high-strength CNT/Al alloys, among which the bimodal structure has been widely adopted owning to its simplicity and ease of control. This kind of heterogonous grain structure is beneficial to introduce an extra ‘back-stress’ hardening upon deformation, leading to improvements in dislocation storage and tensile ductility [Citation11–13]. For instance, CNT-Al and CNT/2009Al composites with bimodal Al grain structures were fabricated via high-energy ball-milling, and the tensile ductility of the composites was significantly improved [Citation14,Citation15]. Considering the fact that a more hierarchical grain structure, such as gradient and multimodal structure, enables metals/alloys to possess more balanced mechanical properties [Citation16,Citation17], one natural question is whether or not the strength-ductility combinations of CNT/Al alloys could be optimized with more complicated grain structures (e.g. trimodal grain structure)? And if it could, what is the physics behind the property enhancement? To this end, we developed a novel powder assembly & alloying approach to tailor grain structures in CNT/Al alloy composites. This fabrication strategy relies on the assembly of metallic powder building blocks (Al, Cu, Mg …), with subsequent diffusion-assisted alloying, by which the CNT/Al alloy composites with designable Al grain structures (unimodal, bimodal and trimodal) can be readily fabricated. We here employed high-strength CNT/Al-Cu-Mg composites as a prototype because of the wide applications of 2xxx Al alloys. This work aims to demonstrate that a more complex trimodal grain structure of the composites leads to better strength-ductility combinations than the other two grain structures (unimodal and bimodal). It’s worth noting the fabrication strategies and the underlying strengthening/hardening mechanisms are readily extendable for other alloy systems (e.g. 7xxx alloy). We will focus on the creation of other high-strength, heterogeneous metallic materials in our future investigations. We utilized digital image correlation analysis and crystal plasticity finite element modeling to interpret the underlying mechanisms, manifesting that trimodal grain structure is superior in promoting strain hardening and alleviating strain concentrations, thereby leading to the enhanced tensile ductility. This work is instrumental for a better understanding of the grain structure design in high-strength CNT/Al composites, and may provide useful benchmarks for the future development of high-performance metal matrix composites.
CNT/Al-Cu-Mg composites with trimodal grain structures were fabricated by powder assembly & alloying approach based on the technical route of flake powder metallurgy [Citation9]. First, the powders with different grain structures were obtained by ball milling. Pure Al powders (∼30 µm in diameter), 25 wt.% 2024Al powders (∼30 µm in diameter), 1.875 wt.% multi-walled CNTs (30–50 nm in diameter, ∼5 µm in length) and elemental powders (Cu and Mg) were ball milled together at 135 rpm for 12 h and 270 rpm for 1 h, obtaining the cold-welded particles, then mixed with another 20 wt.% pure Al powders. For comparison, composite powders for unimodal grain structure were obtained only by ball milling pure Al powders, CNTs and elemental powders under the same condition, while for bimodal structure, composites powders were acquired by mixing the unimodal powders and another 20 wt.% pure Al powders. Subsequently, the composite powders were pressed into Φ 40 mm columns under the pressure of 500 MPa, sintered at 570°C for 2 h and hot extruded into rods at 450°C with an extrusion ratio of 25:1. The alloying process could be fully completed during the sintering process [Citation9]. The composition of all the matrix is designed as Al-4Cu-1.5Mg and the CNT content is also identical (1.5 wt.%) for composites with different grain structures. The as-extruded rods were solid solution treated at 495°C for 3 h, and then artificial aged at 130°C for 20 h after water quenched.
We employed scanning electron microscopy (SEM, MIRA3, Tescan) equipped with electron backscattered diffraction (EBSD, NordlysMax3, Oxford) to probe the grain and fracture morphologies of the composites. Transmission electron microscopy (TEM, Talos F200X, Thermal fisher) attached with energy-dispersive X-ray spectroscopy (EDS), operated at the voltage of 200 kV, was also used to investigate grain and interfacial structures. Dog-bone shaped specimens with 10 mm gauge length, 2 mm width, and 1 mm thickness were machined from the as-extruded rods with the tensile axis parallel to the extrusion direction. Tensile tests and loading-unloading-reloading tests were conducted in the Instron 3344 universal testing machine with a strain rate of 5 × 10−4 s−1 at room temperature. Three specimens were tested for each sample to get the statistics. We also performed an in-situ tensile test under the optical microscope, in combination with the digital image correlation (DIC) analysis, to enable a direct assessment of strain distributions in different sets of composite samples. Crystal plasticity finite element models were set based on the ABAQUS platform for our composites with different grain morphologies to pinpoint the role of heterogeneous grain structure in tailoring stress/strain distributions during the tensile testing.
Figure a and b display the EBSD and TEM images of the trimodal CNT/Al-Cu-Mg composites respectively, from which a three-level grain structure can be clearly observed: Level 1 mainly consists of coarse grains (CG, area percentage of 31%), whose grain size ranges from 2 to 20 µm, with a mean size of 7.8 µm. Level 2 contains grains with grain size between 500 nm and 2 µm, with a mean value of 785 nm and an area fraction of 26%. The grains in Level 3 (area percentage: 43%) can only be recognized by TEM observations, whose grain sizes are below 500 nm with an average grain size of 207 nm. After examining the TEM images of grains in Level 3 more carefully, we found that CNTs were mainly distributed along the grain boundaries (Figure c). This distribution state of CNTs is beneficial to promote the Zener pinning of grain boundaries, stabilizing the ultrafine-grained region [Citation18]. High-resolution TEM (HRTEM) image (Figure d), in collaboration with EDS maps (Figure e), reveals a well-bonded CNT/Al interface, with no visible reactions between Al matrix and CNTs. A summary of the grain size distributions of composites with different grain structures, i.e. unimodal, bimodal and trimodal structures, was shown in Figure f. The grain size distribution in bimodal samples (grain structure: Level 1 + Level 3) was deliberately designed to ensure a similar CG percentage (33%) with that of trimodal structure.
Figure 1. Typical microstructures of CNT/Al-Cu-Mg composites with the trimodal grain structure. (a) IPF map showing three level grain structures. (b) Dark-field TEM image showing level 2 and level 3 grain structures. (c) Bright-field TEM image of Level 3. (d) HRTEM image of the interface-contained region in Level 3, which was indicated by the black box in (c). (e) Al and C EDX maps of the marked blue region in (c). (f) Grain size distribution of composites with deliberately controlled grain structures. The data were statistically estimated by integrating TEM and EBSD analyses.
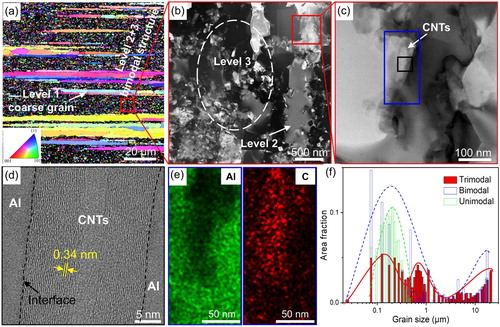
The representative tensile stress-strain curves of CNT/Al-Cu-Mg composites with different grain structures were shown in Figure a (see Fig. S1 for statistical results). As expected, unimodal composites possess the highest yield strength (YS) of 586 ± 2 MPa, but the lowest ductility (3.0 ± 0.3%). The incorporation of CG in bimodal samples slightly improves the tensile ductility to 4.1 ± 0.1%, with a compromise of YS (reduced to 559 ± 4 MPa). This is understandable, as the softer and more ductile phase provides an extra room for strain hardening, thereby avoiding easy strain localization in fine-grained unimodal samples and enhancing ductility. Remarkably, trimodal composites demonstrate a considerably higher tensile elongation (5.5 ± 0.4%), 34% improvement over bimodal samples, and at the same time, keep a high yield strength of 560 ± 3 MPa, comparable to that of the bimodal composites. That is to say, the trimodal grain structure can facilitate a better yield strength-tensile ductility combination than that of the bimodal structure. We note here that Lüders elongation was clearly observed in all of these samples, and more interestingly, it showed strong grain structure dependence, i.e. Lüders elongation increases with decreasing average grain size. The unimodal composites that have the smallest grain sizes (Figure f) showed a Lüders elongation of 2.09 ± 0.19%, significantly higher than that of the bimodal (1.22 ± 0.02%) and trimodal (0.98 ± 0.11%) composites. It was generally believed that the Lüders elongation in alloys is mainly associated with dislocation de-pinning from solute atoms (e.g. Mg atoms in the Al-Cu-Mg system that studied here) [Citation19]. On the contrary, Lüders deformation was also observed in pure metals with UFG structure and was mainly interpreted from dislocation sinking at the grain boundaries [Citation20]. In this regard, although the most significant feature of trimodal composites is manifested in the enhanced ductility, a fundamental understanding of the origin of the Lüders elongation in this work as well as its grain size dependence are worthy topics of further study.
Figure 2. (a) Representative engineering stress-strain curves of CNT/Al-Cu-Mg composites with different grain structures. (b) Strain hardening rate vs. true strain curves after Lüders deformation (the serrated region in tensile stress-strain curves) for composites with different grain structures. Insets show their corresponding fracture surfaces.
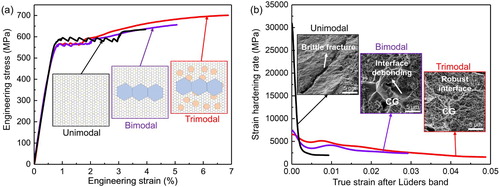
To investigate the underlying mechanisms of the ductility improvement, we compared the strain hardening behaviors after Lüders deformation of the composites with different grain structures. Figure b shows the strain hardening rate (Θ = dσ/dϵ, where σ and ϵ are true stress and true strain, respectively) vs. true strain curves of these composites. Notably, the trimodal composite possesses the highest Θ for the entire plastic deformation, followed by composite with the bimodal and unimodal structures. This observation demonstrates the validity of grain structure regulation in regaining strain hardening capacity, and the trimodal grain structure is more beneficial in promoting dislocation storage. Apart from the strain hardening differences, insets in Figure b illustrated the representative fracture surfaces, from which a dramatic difference in fracture attributes can be observed. Unimodal composites displayed obvious brittle fracture and large cracks were frequently seen in the fracture surfaces. On the contrary, composites with bimodal grain structure revealed typical ductile fracture morphologies, where well-defined dimples were present in the primary CG regions, suggestive of the large plastic deformation undertaken by the CGs. However, unexpectedly, interfacial delamination between CG and ultrafine-grained regions (i.e. Level 1 and Level 3) was generally seen, which phenomenon could be induced by the sharp transition of mechanical properties and the associated strong strain gradient at Level 1/Level 3 interfaces. The existence of intense stress and strain concentration at soft/hard phase interfaces had also been demonstrated in the previous studies on bimodal metals or composites [Citation21–23]. Surprisingly, we found the CG/UFG interfaces stay intact in the trimodal composites, even the total elongation surpassed that of unimodal or bimodal samples, suggesting that strain incompatibility between hard/soft regions alleviates after the Level 2 incorporation. Therefore, our strategy of employing trimodal grain structure combines two of the most important features in enhancing ductility; that is, a significantly improved strain hardening capacity to retard strain localization, and strong suppression of interfacial fracture between soft/hard regions. The result is that our trimodal composites demonstrate an excellent combination of strength and ductility.
We employed loading-unloading-reloading (LUR) tensile tests to probe the origin of high strain hardening in the trimodal composites (Fig. S2). It was known that the LUR test is an effective method to evaluate the long-range internal stress (or back-stress) in metallic materials with heterogeneous microstructures [Citation24–26], and this heterogeneous deformation-induced (HDI) stress provides extra hardening in high-strength metals and leads to improved tensile ductility. Fig. S2b displays the evolution of HDI stresses as a function strain in different samples. HDI stresses in trimodal samples are very high (larger than 360 MPa), remarkably higher than those in bimodal structures. More importantly, HDI stresses increase consistently with straining, and the hardening rate is unparalleled for both unimodal and bimodal samples. These observations indicate that the more hierarchical trimodal grain structure not only renders strong back-stress to improve yield strength, but also facilitates the continuous accumulation of geometrically necessary dislocations (GNDs) for hardening. We propose that the enhanced HDI strengthening and hardening mechanisms may be originated from extensive GNDs distributions as a result of the heterogeneous grain structure. This mechanism had been elaborated in gradient nanotwinned Cu system [Citation27] and could be hinted by our post-mortem EBSD characterizations (Fig. S3).
We further investigated the grain structure dependence of deformation/fracture mechanisms of the composites by tracking the in-situ strain distributions with DIC analysis (Figure ). We found that, for unimodal composites, significant strain localization appeared when the strain was larger than 0.035 (Figure b), and this strain concentration intensified with applied strain without any strain-delocalization phenomenon (Figure c), which could lead to a low tensile ductility and brittle fracture. For bimodal composites, however, the dimensions of the strain localization regions were much smaller and dispersive (Figure d-f). In particular, in stark contrast to the unimodal samples where strain concentration moves collectively, we found strain concentration gradually and discretely appeared in the low strain concentration region (left part in Figure e), implying an obvious strain-delocalization behavior. This remarkably different deformation behavior should be attributed to the CG-assisted strain hardening in bimodal samples. The strain localization was further reduced for trimodal composites (Figure g-i). At an applied strain of 4%, very limited strain localization regions were identified, and these regions were sparsely distributed without forming large-scale strain localization, which greatly facilitates the retarding of the sudden failure at the intrinsic ‘weak-points’ of the composites (e.g. interfaces between hard/soft regions). Therefore, it’s notable that the incorporation of Level 2 grain structure effectively tempers strain localization, enabling the full display of the strain hardening capacity of the composites.
Figure 3. The evolution of strain distributions in CNTs/Al-Cu-Mg composites with different grain structures during tensile deformation, as measured by DIC tests. (a)-(c) Composites with unimodal grain structure. (d)-(f) Composites with bimodal grain structure. (g)-(i) Composites with trimodal grain structure.
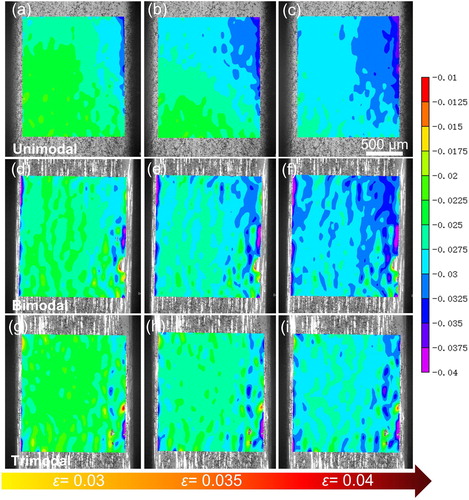
The advantage of trimodal grain structure in relieving strain/stress concentrations can be further demonstrated by Crystal plasticity finite element modeling. The representative volume element (RVE) models of the composites with unimodal, bimodal and trimodal structures were shown in Figure a, 4b and 4c, respectively. The simulated strain distributions of three composites, at an applied tensile strain of 3.5%, were shown in Figure d-4f. The modeling results show similarities with those experimentally observed ones (Figure ): Unimodal composite exhibited the most severe strain localization, followed by the bimodal and trimodal composite. This general trend could be more intuitively revealed by the peak strain values of the deformed samples, which were indicated in Figure d-4f. Moreover, stress concentration can also be alleviated in trimodal composite, as demonstrated by the smaller peak stress value compared to that of unimodal or bimodal composites (Figure g-4i), ensuring the robust combination between hard and soft regions during deformation. To sum, our in-situ tracking of the deformation behaviors and computational simulations together suggest that trimodal grain structure is predominant in mitigating strain/stress concentrations in our high-strength CNT/Al-Cu-Mg composites, thereby contributing to the enhanced tensile ductility.
Figure 4. Crystal plasticity finite element modeling of the deformation process of composites with different grain structures. (a), (b) and (c) are RVE model of composites with unimodal, bimodal and trimodal grain structures, respectively. (d)-(f), (g)-(i) are strain and stress mapping of composites with various grain structures, at a tensile strain of 3.5%. The maximum strain (or stress) magnitude in each case was indicated.
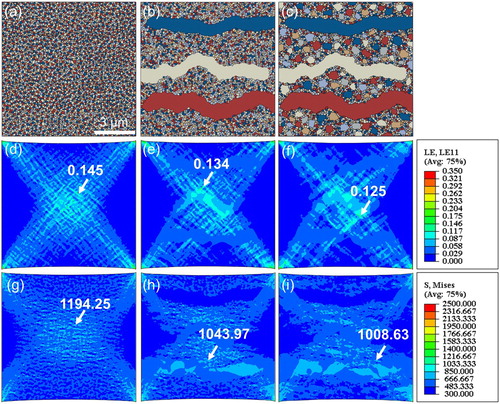
We developed a powder assembly & alloying fabrication strategy to fabricate CNT/Al-Cu-Mg composites with tailored grain structures. Their mechanical properties show strong grain structure dependence, where the tensile property of the most heterogonous grain structure (i.e. trimodal grain structure) achieved a superior strength-ductility combination. This outstanding mechanical property is mainly interpreted from the improved strain hardening capacity and compatible deformation between the hard/soft regions in the complex trimodal grain structure, as manifested by both experimental and modeling results. Our results offer a concrete strategy to design and fabricate high-strength Al matrix composites with excellent strength-ductility combinations.
Supplemental Material
Download MS Word (879.4 KB)Acknowledgements
This work was supported by the National Key R&D Program of China (No. 2016YFB1200506), the National Natural Science Foundation of China (Nos. 51671130, 51871149, 51801120, 51971206), Science and Technology Commission of Shanghai Municipality (No. 19ZR1474900), and Aeronautical Science Foundation of China (No. 2017ZF57023). We also thank the financial supports from the Administrative Committee of Maanshan Economic and Technological Development Zone.
Disclosure statement
No potential conflict of interest was reported by the author(s).
Additional information
Funding
References
- Tjong SC. Recent progress in the development and properties of novel metal matrix nanocomposites reinforced with carbon nanotubes and graphene nanosheets. Mater Sci Eng R Rep. 2013;74(10):281–350. doi: 10.1016/j.mser.2013.08.001
- Chen B, Shen J, Ye X, et al. Length effect of carbon nanotubes on the strengthening mechanisms in metal matrix composites. Acta Mater. 2017;140:317–325. doi: 10.1016/j.actamat.2017.08.048
- Wei H, Li Z, Xiong D-B, et al. Towards strong and stiff carbon nanotube-reinforced high-strength aluminum alloy composites through a microlaminated architecture design. Scr Mater. 2014;75:30–33. doi: 10.1016/j.scriptamat.2013.11.014
- Choi HJ, Min BH, Shin JH, et al. Strengthening in nanostructured 2024 aluminum alloy and its composites containing carbon nanotubes. Compos A: Appl Sci Manuf. 2011;42(10):1438–1444. doi: 10.1016/j.compositesa.2011.06.008
- Jagannatham M, Chandran P, Sankaran S, et al. Tensile properties of carbon nanotubes reinforced aluminum matrix composites: A review. Carbon N Y. 2020;160:14–44. doi: 10.1016/j.carbon.2020.01.007
- Ma K, Wen H, Hu T, et al. Mechanical behavior and strengthening mechanisms in ultrafine grain precipitation-strengthened aluminum alloy. Acta Mater. 2014;62:141–155. doi: 10.1016/j.actamat.2013.09.042
- Jiang L, Li Z, Fan G, et al. The use of flake powder metallurgy to produce carbon nanotube (CNT)/aluminum composites with a homogenous CNT distribution. Carbon N Y. 2012;50(5):1993–1998. doi: 10.1016/j.carbon.2011.12.057
- He T, He X, Tang P, et al. The use of cryogenic milling to prepare high performance Al2009 matrix composites with dispersive carbon nanotubes. Mater Des. 2017;114:373–382. doi: 10.1016/j.matdes.2016.11.008
- Xu R, Tan Z, Fan G, et al. High-strength CNT/Al-Zn-Mg-Cu composites with improved ductility achieved by flake powder metallurgy via elemental alloying. Compos A: Appl Sci Manuf. 2018;111:1–11. doi: 10.1016/j.compositesa.2018.05.012
- Ovid'ko IA, Valiev RZ, Zhu YT. Review on superior strength and enhanced ductility of metallic nanomaterials. Prog Mater Sci. 2018;94:462–540. doi: 10.1016/j.pmatsci.2018.02.002
- Yang M, Yan D, Yuan F, et al. Dynamically reinforced heterogeneous grain structure prolongs ductility in a medium-entropy alloy with gigapascal yield strength. Proc Natl Acad Sci USA. 2018;115(28):7224–7229. doi: 10.1073/pnas.1807817115
- Park HK, Ameyama K, Yoo J, et al. Additional hardening in harmonic structured materials by strain partitioning and back stress. Mater Res Lett. 2018;6(5):261–267. doi: 10.1080/21663831.2018.1439115
- Wu X, Yang M, Yuan F, et al. Heterogeneous lamella structure unites ultrafine-grain strength with coarse-grain ductility. Proc Natl Acad Sci USA. 2015;112(47):14501–14505. doi: 10.1073/pnas.1517193112
- Liu ZY, Ma K, Fan GH, et al. Enhancement of the strength-ductility relationship for carbon nanotube/Al–Cu–Mg nanocomposites by material parameter optimisation. Carbon N Y. 2020;157:602–613. doi: 10.1016/j.carbon.2019.10.080
- Salama EI, Abbas A, Esawi AMK. Preparation and properties of dual-matrix carbon nanotube-reinforced aluminum composites. Compos A: Appl Sci Manuf. 2017;99:84–93. doi: 10.1016/j.compositesa.2017.04.002
- Lu K. Making strong nanomaterials ductile with gradients. Science. 2014;345(6203):1455–1456. doi: 10.1126/science.1255940
- Zhao Y, Topping T, Bingert JF, et al. High tensile ductility and strength in bulk nanostructured nickel. Adv Mater. 2008;20(16):3028–3033. doi: 10.1002/adma.200800214
- Liu ZY, Xiao BL, Wang WG, et al. Modelling of carbon nanotube dispersion and strengthening mechanisms in Al matrix composites prepared by high energy ball milling-powder metallurgy method. Compos A: Appl Sci Manuf. 2017;94:189–198. doi: 10.1016/j.compositesa.2016.11.029
- Ebenberger P, Uggowitzer PJ, Kirnstötter S, et al. Processing-controlled suppression of Lüders elongation in AlMgMn alloys. Scr Mater. 2019;166:64–67. doi: 10.1016/j.scriptamat.2019.02.047
- Yu CY, Kao PW, Chang CP. Transition of tensile deformation behaviors in ultrafine-grained aluminum. Acta Mater. 2005;53(15):4019–4028. doi: 10.1016/j.actamat.2005.05.005
- Zhang Z, Topping T, Li Y, et al. Mechanical behavior of ultrafine-grained Al composites reinforced with B4C nanoparticles. Scr Mater. 2011;65(8):652–655. doi: 10.1016/j.scriptamat.2011.06.037
- Zan YN, Zhou YT, Liu ZY, et al. Enhancing strength and ductility synergy through heterogeneous structure design in nanoscale Al2O3 particulate reinforced Al composites. Mater Des. 2019;166:107629. doi: 10.1016/j.matdes.2019.107629
- Han B, Lavernia E, Lee Z, et al. Deformation behavior of bimodal nanostructured 5083 Al alloys. Metall Mater Trans A. 2005;36(4):957–965. doi: 10.1007/s11661-005-0289-7
- Zhu Y, Wu X. Perspective on hetero-deformation induced (HDI) hardening and back stress. Mater Res Lett. 2019;7(10):393–398. doi: 10.1080/21663831.2019.1616331
- Wu X, Zhu Y. Heterogeneous materials: a new class of materials with unprecedented mechanical properties. Mater Res Lett. 2017;5(8):527–532. doi: 10.1080/21663831.2017.1343208
- Yang M, Pan Y, Yuan F, et al. Back stress strengthening and strain hardening in gradient structure. Mater Res Lett. 2016;4(3):145–151. doi: 10.1080/21663831.2016.1153004
- Cheng Z, Zhou H, Lu Q, et al. Extra strengthening and work hardening in gradient nanotwinned metals. Science. 2018;362(6414):eaau1925. doi: 10.1126/science.aau1925