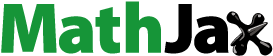
Abstract
Achieving appreciable strain-aging hardening coupling with fine-grain strengthening remains a critical challenge in dilute Mg alloys, as high-temperature solid-solution, utilized to impart high-level solutes for strain-aging, inevitably causes grain coarsening and great strength loss. Herein, we report a rapid dislocation-mediated solute repartitioning behavior upon aging in a low-temperature annealed Mg–1.0Zn–0.45Ca–0.33Sn–0.2Mn (wt.%) alloy. Thereby, appreciable strain-aging hardening (YS increment of ∼30 MPa) coupling with fine-grain (grain size of ∼2.5 µm) strengthening accounts for a high yield strength (∼297 MPa) and ductility (∼20%). It suggests a feasible avenue to develop strong dilute Mg alloys by combining strain-aging hardening and fine-grain strengthening.
GRAPHICAL ABSTRACT
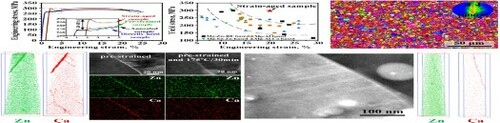
IMPACT STATEMENT
By manipulating solute distribution while keeping a fine-grain structure, appreciable strain-aging hardening response coupling with fine-grain strengthening guarantees the development of strong dilute Mg alloy.
Introduction
Simultaneous high formability and strength are required for magnesium (Mg) alloys if they are to be more competitive as lightweight structural materials [Citation1,Citation2]. Reducing the alloying addition content improves the formability considerably, however, the strength of low-alloyed Mg alloys is usually inadequate for applications [Citation3,Citation4]. Due to the low alloy content and the lack of precipitates, solute strengthening and precipitation hardening are insufficient in dilute Mg alloys [Citation3]. Introducing a high density of dislocations can increase the strength, but subsequent plastic deformation capability is considerably deteriorated. Among classical strengthening methods, grain refinement is considered as the most important way to strengthen dilute Mg alloys [Citation5,Citation6]. Numerous efforts have been devoted to reducing the grain size of dilute Mg alloys to sub-micro scale [Citation7–9], but the minimum grain size achieved by conventional processing (e.g. rolling and extrusion) techniques is typically around several to ten microns [Citation10,Citation11], which leads to a yield strength (YS) limited to ∼200 MPa.
Alternatively, strain-aging hardening, taking advantage of the interaction between solute atoms and dislocations, has been utilized to further enhance the strength of aluminum (Al) alloys in automobile industry [Citation12,Citation13]. The hardening response is intimately related to the solute atoms dissolved in the matrix [Citation13,Citation14], and thus high-temperature solid-solution treatment is needed to provide a relatively high solute concentration. However, due to the scarce of segregated solute atoms and/or thermal stable particles at grain boundaries (GBs) in dilute Mg alloys, high-temperature heat treatment would cause a significant grain growth (with final average grain size ranging from ∼8.5 to ∼40 µm) before strain-aging treatment [Citation15–17]. Compared with Al alloys, the strength loss due to grain coarsening in Mg alloys is hard to be compensated by subsequent strain-aging treatment, due to the inherent large Hall-Petch coefficient [Citation6], limiting the development of strong dilute Mg alloys. In the present study, we found an unexpected strain-aging hardening response (YS increment of ∼30 MPa) in a low-temperature annealed Mg–1.0Zn–0.45Ca–0.33Sn–0.2Mn (wt.%, ZXTM1000) alloy, and the internal mechanisms are revealed based on multi-scale microstructure characterizations. The findings of this work provide a novel strategy to achieve strain-aging hardening and fine-grain strengthening simultaneously in dilute Mg alloys.
Materials and methods
As-cast ZXTM1000 alloy was homogenized at 415°C for 24 h and then extruded at 430°C with an extrusion ratio of ∼35. Before hot rolling, the extruded ZXTM1000 plates were homogenized at 480°C for 3 h followed by water-quenching. The rolling process was conducted at 300°C by five passes, with a total thickness reduction of ∼80% and a similar thickness reduction of ∼30% per pass. Before each pass, the plates were pre-heated at 300°C for 10 min. Afterwards, the rolled plates were annealed at 300°C for 7 min. Subsequent strain-aging treatment, i.e. a slight pre-strain of ∼2% followed by aging at 175°C for 30 min, was employed in the annealed ZXTM1000 alloy. Note that the aging parameters in the present study (i.e. 175°C/30 min) were determined to meet the industrial application requirements of bake hardening, where the pre-strained samples are usually aged at 150–200°C for 20–30 min to enhance the strength of alloys [Citation18].
Tensile specimens with a gauge dimension of 10 × 4 × 0.8 mm were cut along the rolling direction, and the tensile tests were carried out at 1 × 10−3 s−1 by an AGS-100 kN machine equipped with a video extensometer. After ∼2% pre-strain, the sizes of tensile samples with and without aging treatment were re-measured before reloading. At least three samples for each condition were tested to ensure data reliability. The microstructure was characterized by EBSD (FE-SEM (Zeiss, Sigma 500) equipped with an Oxford instruments Symmetry EBSD detector), TEM (JEM-2100F and FEI Talos F200X, operating at an accelerating voltage of 200 kV), and three-dimensional atom probe tomography (3D APT). The APT specimen was prepared using the two-stage electro-polishing method and performed on a LEAP 4000X Si under ultraviolet laser pulse mode at a pulse energy of 60 pJ and a pulse rate of 200 Hz. For in-situ heating TEM observations, the sample was prepared by FEI Helios UX G5 dual-beam focused-ion-beam (FIB) system. Annular FIB milling was performed using an acceleration voltage of 30 kV with polishing at 5 kV and 2 kV. After milling, the sample was welded on the chip of in-situ heating station. The sample was first heated to 50°C with a heating rate of ∼0.5°C/s, and then heated to 175°C with a heating rate of ∼0.7°C/s. The temperature error did not exceed 0.2°C during the subsequent aging process. After aging for 30 min, the sample was cooled down to chamber temperature and stabilized for ∼20 min. To examine the GB segregation levels before and after aging, STEM-EDS mapping was conducted on the conditions of identical STEM magnification, screen current, and time consumption.
Results and discussion
The annealed ZXTM1000 alloy shows a yield strength of , accompanied by a high elongation to failure of
% (Figure (a)). Typical IPF image and corresponding grain size distribution show a fine-grained (∼2.5 µm) microstructure with a TD-split micro-texture (Supplementary Figure S1 (a,b)). TEM characterizations reveal the existence of residual dislocations and four types of precipitates, i.e. Mg2Ca, Ca2Mg6Zn3, α-Mn and MgSnCa phases (Supplementary Figure S1 (c–h)). After strain-aging treatment, the flow stress witnesses an appreciable increment of ∼30 MPa (Figure (a)), leading to a high YS of
. Due to the collective effects originated from appreciable strain-aging hardening and fine-grained microstructure, the strain-aged ZXTM1000 alloy exhibits a superior strength-ductility combination to other wrought Mg alloys either with a high or low alloying content (Figure (b)) [Citation4,Citation9,Citation19–27], including extruded Mg–9.8Sn–1.2Zn–1.0Al (wt.%) alloy [Citation23] and peak-aged Mg–8.8Sn–4.0Zn–0.9Al–0.3Na (wt.%) [Citation25] and Mg–1.6Zn–0.5Ca–0.4Zr (wt.%) [Citation24] alloys. For comparison, the tensile curves of directly aged ZXTM1000 alloy without pre-strain treatment and pre-strained ZXTM1000 alloy without aging treatment are also presented. The YS of directly aged and pre-strained ZXTM1000 alloys is ∼5 MPa lower or higher than that of the annealed sample, respectively, which is far lower than the YS increment of ∼30 MPa in the strain-aged sample (Figure (a)). It further reflects that both the pre-strain and aging processes are necessary to impart the additional strengthening for developing strong dilute ZXTM1000 alloy.
Figure 1. (a) Tensile engineering stress-strain curves of annealed, directly aged, pre-strained and strain-aged ZXTM1000 alloys. (b) YS as a function of elongation for various rolled and extruded Mg alloys [Citation4,Citation9,Citation19–27].
![Figure 1. (a) Tensile engineering stress-strain curves of annealed, directly aged, pre-strained and strain-aged ZXTM1000 alloys. (b) YS as a function of elongation for various rolled and extruded Mg alloys [Citation4,Citation9,Citation19–27].](/cms/asset/5d2b57d7-94b1-4cdf-b8fc-69525984c49f/tmrl_a_2009585_f0001_oc.jpg)
To explore the origin of additional strengthening effect, quasi-in-situ EBSD was utilized to track the microstructure evolution upon ∼2% pre-strain. After ∼2% pre-strain treatment, no evident change in the grain-orientation occurs (Figure (a,b)). Subsequent GB misorientation distribution shows a slightly increased fraction of misorientation angle peak of ∼86° (indicated by black arrow in Figure (c)), suggesting that only a few tensile twins formed, as further confirmed by comparing the GBs superimposed with twin boundaries maps of annealed and pre-strained samples (Figure (d,e)). Note that the fraction of boundaries with misorientation angles between 2° and 15° increases significantly after pre-strain treatment (indicated by red arrow in Figure (c)), and thus dislocation slip is expected to be the dominant deformation mechanism. Two typical grains, showing evident slip traces, are presented in Figure (f,g), where the corresponding IPF maps, orientations and theoretical slip trace directions are also included. Based on the EBSD-assisted slip trace analysis results, it is concluded that the pre-strain process is mainly accommodated by basal<a> slip. The kernel average misorientation (KAM) maps (Figure (h,i)) reveal a heterogeneous orientation gradient after pre-strain process, with a higher value in the regions close to GBs (indicated by the white arrows in Figure (i)). The higher local orientation gradient might be caused by a higher dislocation density near GBs. Further TEM analysis was employed to investigate the dislocations introduced during ∼2% pre-strain. Based on the
invisible criterion [Citation15], dislocations are invisible under the condition of
(Figure (j)), and therefore the dislocations observed under the condition of
(Figure (k)) are <a>-type dislocations. In addition, almost all dislocations are parallel to basal plane, further indicating that these dislocations belong to basal <a> type. Compared with the grain center region, a higher dislocation density is observed around GBs (indicated by red arrows in Figure (k)), which is consistent with the KAM results (Figure (i)).
Figure 2. (a, b) IPF, (d, e) GB superimposed with twin boundaries and (h, i) KAM images of (a, d, h) annealed and (b, e, i) pre-strained ZXTM1000 alloys. The boundaries with misorientation angles between 2° and 15° are indicated by gray lines, the boundaries with misorientation angles above 15° are indicated by black lines and the
twin boundaries are indicated by red lines in (d, e). (c) GB misorientation distribution of the annealed and pre-strained ZXTM1000 alloys. (f, g) Typical slip trace analysis results in the pre-strained ZXTM1000 alloy. The calculated slip trace directions for basal <a> slip, prismatic <a> slip, and pyramidal II <c + a> slip are indicated by 1–3, 4–6, and 7–12, respectively. (j, k) Two-beam central dark-field images taken under the conditions of (j)
, (k)
.
![Figure 2. (a, b) IPF, (d, e) GB superimposed with { 101¯2} twin boundaries and (h, i) KAM images of (a, d, h) annealed and (b, e, i) pre-strained ZXTM1000 alloys. The boundaries with misorientation angles between 2° and 15° are indicated by gray lines, the boundaries with misorientation angles above 15° are indicated by black lines and the { 101¯2} twin boundaries are indicated by red lines in (d, e). (c) GB misorientation distribution of the annealed and pre-strained ZXTM1000 alloys. (f, g) Typical slip trace analysis results in the pre-strained ZXTM1000 alloy. The calculated slip trace directions for basal <a> slip, prismatic <a> slip, and pyramidal II <c + a> slip are indicated by 1–3, 4–6, and 7–12, respectively. (j, k) Two-beam central dark-field images taken under the conditions of (j) g=[0002], (k) g=[12¯10].](/cms/asset/7aa42472-3e02-43f9-9201-28e911a91805/tmrl_a_2009585_f0002_oc.jpg)
After aging treatment, profuse basal <a> dislocations are still observed (Figure (a)), and HAADF-STEM (Figure (b,c)) images show that solute aggregation occurs at the dislocations both within grain interior and along grain boundaries. The APT results (Figure (d)) reveal a strong Zn and Ca co-segregation at a dislocation segment, with the concentration of ∼2.0 at.% for Ca and ∼2.5 at.% for Zn, respectively (Figure (e)). A smaller volume (i.e. 20 20
60 nm3) of the matrix extracted from Figure (d) shows no evident solute cluster, which is further demonstrated by the count distribution of 1st nearest neighbor (1NN) distance for Zn element. The BF-TEM image and corresponding select area electron diffraction (SAED) patterns suggest that neither precipitates nor G.P. zones are found in the strain-aged ZXTM1000 alloy (Figure (g,h)). The HRTEM image (Figure (i)) further confirms the absence of G.P. zones. Consequently, the YS increment of ∼30 MPa is originated from pinned basal <a> dislocations movement by Zn and Ca solute atoms, which is also reflected by the discontinuous yielding flow associated with a yield drop phenomenon (Figure (a)).
Figure 3. (a) BF-STEM image of the strain-aged ZXTM1000 alloy. (b, c) HAADF-STEM images corresponding to region I and region II in (a). (d) APT maps of Zn, Ca, Sn, Mn in strain-aged ZXTM1000 alloy. (e) 1D compositional profiles along cylinder 1 in (d). (f) An enlarged volume (20 20
60 nm3) extracted from (d), and the count distribution of 1NN distance for Zn element. (g) BF-TEM and (i) HRTEM images of the strain-aged ZXTM1000 alloy. (h) SAEDs corresponding to the matrix.
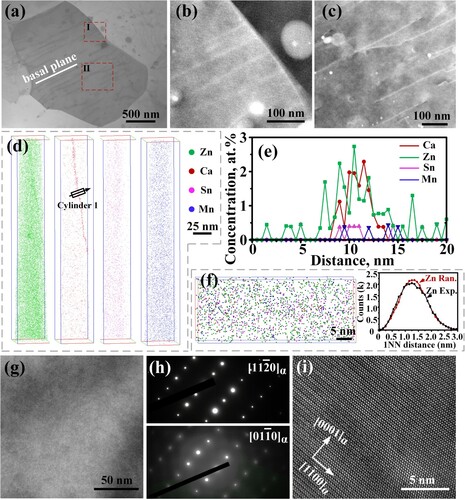
Previous study [Citation28] also reported an enhanced YS by strain-aging treatment in an extruded Mg–12.6Gd–1.3Y–0.9Zn–0.5Mn (wt.%) alloy. Note that a high large pre-strain (i.e. ∼10% cold rolling and ∼2% tensile pre-strain) and a long aging time (i.e. 200°C for 32 h) were utilized to achieve the high strength (YS of 543 MPa) in the RE-containing Mg alloy. Actually, the intrinsic high solid solubility of rare-earth elements (e.g. ∼9.41 wt.% for Gd at 370°C [Citation29]) enables strain-aging hardening in the Mg–12.6Gd–1.3Y–0.9Zn–0.5Mn (wt.%) alloy.
In contrast, a lean addition of alloying elements, with a total concentration of ∼2 wt.%, was adopted in the present annealed ZXTM1000 alloy. Moreover, although a slight pre-deformation (i.e. ∼2% tensile pre-strain) was applied, an unusually rapid (i.e. 175°C for 30 min) strain-aging hardening effect was achieved. It suggests that the solute atoms aggregated at dislocations may not solely originate from the matrix as in previous studies [Citation15,Citation17,Citation28], considering that a short annealing time (i.e. 7 min) at a relatively low temperature (i.e. 300°C), in general, cannot provide sufficient dissolution of Zn and Ca atoms.
APT was employed to reveal solute distributions in the annealed and strain-aged ZXTM1000 alloys. The GB segments of both tips show localized aggregation of Zn and Ca atoms (Figure (a,b)). The concentrations of Ca and Zn solute atoms at the GB are ∼4.40 and ∼3.40 at.%, respectively, in the annealed ZXTM1000 alloy (Figure (c)), which decrease to ∼1.06 and ∼1.68 at.% in the strain-aged sample (Figure (d)). The calculated Gibbsian interfacial excess (GIE) values of Zn and Ca atoms in the annealed sample (Figure (e)) are 3.06 ± 0.12 and 3.20 ± 0.12, while those for the strain-aged sample are 2.16 ± 0.10 and 1.65 ± 0.09, respectively. Apart from solute aggregation at the GB, the solute segregation along dislocations are also detected in the annealed alloy (Figure (a)), with the concentrations of ∼5.0 at.% for Ca and ∼2.8 at.% for Zn (Figure (f)).
Figure 4. (a, b) APT maps of Zn, Ca, Sn, Mn in (a) annealed ZXTM1000 and (b) strain-aged ZXTM1000. The rightmost map in (a) is plotted with 0.55 at.% Ca iso-surfaces. (c, d, f) 1D compositional profiles along (c) cylinder 1, (d) cylinder 2, and (f) cylinder 3. (e) Gibbsian interfacial excess of Zn and Ca atoms for the detected two GBs.

As revealed by APT analysis of the annealed and strain-aged samples (Figure ), the concentrations of Zn and Ca atoms at detected GBs are considerably reduced after strain-aging treatment. It suggests that the pre-segregated solute atoms have escaped from GBs upon the strain-aging process. To reveal the correlation between strain-aging treatment and solute repartitioning behavior, in-situ TEM of a GB with high density dislocations attached (confirmed by Supplementary Figure 2(a)) was conducted on the pre-strained sample. Figure shows the snapshots taken in situ in the HAADF-STEM scan mode at different heating stages for the pre-strained ZXTM1000 alloy. As illustrated by Figure (a), the GB exhibits evident bright contrast, showing strong segregation of Zn and Ca atoms. A precipitate enriched in Ga element appears at the GB when the temperature reaches 175°C (Figure (b), Supplementary Figure S2(b–h)), which should be implanted during sample preparation. Note that during aging process, the GB brightness contrast dims gradually, while the dislocations brightness contrast gradually brightens (indicated by red arrows in Figure (e)). The results indicate a decreased concentration of both Zn and Ca atoms at GB, accompanied by an enhanced solute concentration at dislocations. The decreased GB solute concentration has been confirmed by comparing the mapping results before (Figure (f)) and after aging (Figure (g)) as well as line scanning results (Figure (h)). To alleviate the possible influence of long-time electron beam irradiation on the solute repartitioning behavior, another GB decorated by a lower density of dislocations (Supplementary Figure S3(a)) was only characterized before and after heating without video recording. HAADF-STEM (Supplementary Figure S3(c)) image shows strong segregation of solute atoms at the GB. As the mapping (Supplementary Figure S3(b, d)) and line scanning (Supplementary Figure S3(g)) results are almost identical, the influence of electron beam irradiation during the energy spectrum data acquisition process can be ignored. After the aging process, although the HAADF-STEM image (Supplementary Figure S3(e)) reveals a segregation of solute atoms, a similar declining trend of Zn and Ca concentration is also detected in this GB in terms of the mapping and line scanning results (Supplementary Figure S3(d, f, g)). Considering the absence of precipitates or G.P. zones (Figure ), it can be concluded that the pre-segregated Zn and Ca atoms at GBs can migrate into the matrix facilitated by pre-induced dislocations during the aging process.
Figure 5. (a–e) HAADF-STEM images of pre-strained ZXTM1000 alloy during in-situ heating. (a) before heating, (b) reaching at 175°C, (c) 175°C for 10 min, (d) 175°C for 20 min, (e) 175°C for 30 min. (f, g) STEM-EDS mapping results of (f) before and (g) after heating. (h) Line scanning results extracted from the EDS mapping data, corresponding to the specific regions in (a) and (e).
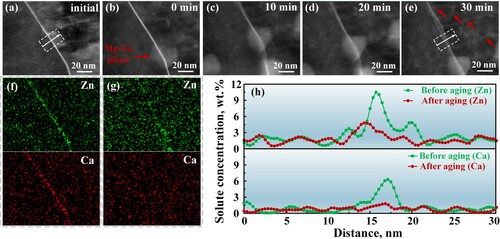
Furthermore, the solute atoms within grain interior are also important for the formation of solute segregation at dislocations in the strain-aged ZXTM1000 alloy. The 1D compositional profiles in Figure (c) show that although Zn and Ca atoms are strongly aggregated at the GB in the annealed sample, the solute concentrations within grain interior are still at a non-neglected level, especially for Zn element (i.e. 0–0.12 at.% for Ca and 0.1–0.47 at.% for Zn). During pre-strain process, basal <a> dislocations were introduced in the annealed ZXTM1000 alloy within grain interior and along GBs (Figure (k)). The dislocations are expected to change the energetic states due to lattice distortion around the dislocation core. Previous study [Citation15] showed that the co-segregation of Zn and Ca atoms at dislocations, with smaller Zn atoms (0.134 < 0.160 nm (Mg)) segregated at the compressive region and larger Ca atoms (0.197 nm) segregated at the tensile region, is expected to alleviate the elastic strain around the dislocation core. Therefore, the Zn and Ca atoms (supersaturated at GBs and dissolved in the matrix) would diffuse toward basal <a> dislocations during the aging process for energy minimization, achieving strain-aging hardening in the fine-grained ZXTM1000 alloy.
Conclusions
In summary, appreciable strain-aging hardening response has been achieved in a low-temperature annealed ZXTM1000 alloy, which breaks a previous cognition that high-temperature solid-solution for ensuring solute concentration is needed before strain-aging treatment. By optimizing alloy composition and annealing parameters, a considerable amount of Zn and Ca solute atoms segregate at GBs and dissolve in the matrix. Moreover, facilitated by pre-strain-induced dislocations, the pre-segregated Zn and Ca atoms diffuse toward the matrix during the subsequent short-time aging process, pinning the dislocation movement and leading to an unusually rapid strain-aging hardening response. The synergetic effects of fine-grain strengthening and strain-aging hardening guarantee high yield strength (∼297 MPa) and ductility (∼20%) in the dilute ZXTM1000 alloy. The present work sheds a new insight to develop dilute Mg alloys with high strength-ductility synergy by manipulating solute partitioning behavior while keeping a fine-grained microstructure.
Supplemental Material
Download MS Word (1.2 MB)Disclosure statement
No potential conflict of interest was reported by the authors.
Additional information
Funding
Reference
- Pollock TM. Weight loss with magnesium alloys. Science. 2010;328:986–987.
- Kim NJ. Critical assessment 6: magnesium sheet alloys: viable alternatives to steels? Mater Sci Technol. 2014;30:1925–1928.
- Cihova M, Schäublin R, Hauser LB, et al. Rational design of a lean magnesium-based alloy with high age-hardening response. Acta Mater. 2018;158:214–229.
- Nakata T, Xu C, Ajima R, et al. Strong and ductile age-hardening Mg-Al-Ca-Mn alloy that can be extruded as fast as aluminum alloys. Acta Mater. 2017;130:261–270.
- Zheng R, Bhattacharjee T, Shibata A, et al. Simultaneously enhanced strength and ductility of Mg-Zn-Zr-Ca alloy with fully recrystallized ultrafine grained structures. Scr Mater. 2017;131:1–5.
- Razavi SM, Foley DC, Karaman I, et al. Effect of grain size on prismatic slip in Mg–3Al–1Zn alloy. Scr Mater. 2012;67:439–442.
- Zeng ZR, Zhu YM, Liu RL, et al. Achieving exceptionally high strength in Mg 3Al 1Zn-0.3Mn extrusions via suppressing intergranular deformation. Acta Mater. 2018;160:97–108.
- Pan H, Qin G, Huang Y, et al. Development of low-alloyed and rare-earth-free magnesium alloys having ultra-high strength. Acta Mater. 2018;149:350–363.
- Pan H, Xie D, Li J, et al. Development of novel lightweight and cost-effective Mg–Ce–Al wrought alloy with high strength. Mater Res Lett. 2021;9:329–335.
- Wang J, Zhu G, Wang L, et al. Origins of high ductility exhibited by an extruded magnesium alloy Mg-1.8Zn-0.2Ca: experiments and crystal plasticity modeling. J Mater Sci Technol. 2021;84:27–42.
- Zha M, Zhang H-M, Wang C, et al. Prominent role of a high volume fraction of Mg17Al12 particles on tensile behaviors of rolled Mg–Al–Zn alloys. J Alloys Compd. 2017;728:682–693.
- Birol Y, Karlik M. The interaction of natural ageing with straining in a twin-roll cast AlMgSi automotive sheet. Scr Mater. 2006;55:625–628.
- Li H, Yan Z, Cao L. Bake hardening behavior and precipitation kinetic of a novel Al-Mg-Si-Cu aluminum alloy for lightweight automotive body. Mater Sci Eng A. 2018;728:88–94.
- Marioara CD, Andersen SJ, Jansen J, et al. The influence of temperature and storage time at RT on nucleation of the β″ phase in a 6082 Al–Mg–Si alloy. Acta Mater. 2003;51:789–796.
- Bian MZ, Sasaki TT, Nakata T, et al. Bake-hardenable Mg–Al–Zn–Mn–Ca sheet alloy processed by twin-roll casting. Acta Mater. 2018;158:278–288.
- Wang Q, Liu L, Jiang B, et al. Twin nucleation, twin growth and their effects on annealing strengths of Mg–Al–Zn–Mn sheets experienced different pre-compressive strains. J Alloys Compd. 2020;815:152310.
- Zeng ZR, Zhu YM, Bian MZ, et al. Annealing strengthening in a dilute Mg–Zn–Ca sheet alloy. Scr Mater. 2015;107:127–130.
- Dehghani K. Bake hardening of nanograin AA7075 aluminum alloy. Mater Sci Eng A. 2011;530:618–623.
- Suh B-C, Shim M-S, Shin KS, et al. Current issues in magnesium sheet alloys: where do we go from here? Scr. Mater. 2014; 84–85:1-6.
- Mendis CL, Bae JH, Kim NJ, et al. Microstructures and tensile properties of a twin roll cast and heat-treated Mg–2.4Zn–0.1Ag–0.1Ca–0.1Zr alloy. Scr Mater. 2011;64:335–338.
- Nakata T, Xu C, Suzawa K, et al. Enhancing mechanical properties of rolled Mg-Al-Ca-Mn alloy sheet by Zn addition. Mater Sci Eng A. 2018;737:223–229.
- Li ZH, Sasaki TT, Bian MZ, et al. Role of Zn on the room temperature formability and strength in Mg–Al–Ca–Mn sheet alloys. J Alloys Compd. 2020;847:156347.
- Sasaki TT, Yamamoto K, Honma T, et al. A high-strength Mg–Sn–Zn–Al alloy extruded at low temperature. Scr Mater. 2008;59:1111–1114.
- Li ZH, Sasaki TT, Shiroyama T, et al. Simultaneous achievement of high thermal conductivity, high strength and formability in Mg-Zn-Ca-Zr sheet alloy. Mater Res Lett. 2020;8:335–340.
- Davis AE, Robson JD, Turski M. The effect of multiple precipitate types and texture on yield asymmetry in Mg-Sn-Zn(-Al-Na-Ca) alloys. Acta Mater. 2018;158:1–12.
- Bhattacharjee T, Suh BC, Sasaki TT, et al. High strength and formable Mg–6.2Zn–0.5Zr–0.2Ca alloy sheet processed by twin roll casting. Mater Sci Eng A. 2014;609:154–160.
- Zhao L-Q, Wang C, Chen J-C, et al. Development of weak-textured and high-performance Mg–Zn–Ca alloy sheets based on Zn content optimization. J Alloys Compd. 2020;849:156640.
- Heng X, Zhang Y, Rong W, et al. A super high-strength Mg-Gd-Y-Zn-Mn alloy fabricated by hot extrusion and strain aging. Mater Des. 2019;169:107666.
- Si H, Jiang Y, Tang Y, et al. Stable and metastable phase equilibria in binary Mg-Gd system: a comprehensive understanding aided by CALPHAD modeling. J MagnesAlloys. 2019;7:501–513.