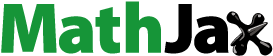
Abstract
Chemically complex MAX phase-based ceramics in the (Ti,Zr,Hf,V,Nb)-(Al,Sn)-C system were synthesised by reactive hot pressing for 30 min at 1250–1450°C under a load of 30 MPa for the first time in this work. The dense bulk ceramics contained chemically complex double solid solution MAX phases, each comprising five M-elements and two A-elements. The predominant 211 (Ti0.23,Zr0.18,Hf0.20,V0.11,Nb0.28)2(Al0.42,Sn0.58)C MAX phase characterised all ceramics, while the 312 (Ti0.23,Zr0.31,Hf0.31,V0.08,Nb0.08)3(Al0.36,Sn0.64)C2 and 211 (Ti0.26,Zr0.07,Hf0.07,V0.47,Nb0.13)2(Al0.66,Sn0.34)C MAX phases were only present in the ceramics sintered at 1350–1450°C. A limited amount (4–5 vol%) of parasitic phases (mainly, binary intermetallics) was found in the pseudo-binary carbide-free ceramics sintered at 1350–1450°C.
GRAPHICAL ABSTRACT
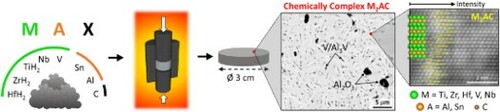
IMPACT STATEMENT
Chemically complex 211 & 312 double solid solution MAX phase-based ceramics with a MAX phase content up to 96 vol% were synthesised in the (Ti,Zr,Hf,V,Nb)-(Al,Sn)-C system for the first time.
Introduction
The MAX phases are ternary carbides or nitrides with the Mn+1AXn stoichiometry, where M is an early transition metal, A is an A-group element (mainly groups 13–16 in the periodic table), X is C or N, and n = 1, 2 or 3 (corresponding to the 211, 312, or 413 sub-groups, respectively). Their nanolaminated unit cell, consisting of M6X ceramic blocks separated by metallic A-layers, imparts to this family of materials a unique set of properties, some characteristic of metals and some of ceramics. Their compatibility with inherently corrosive reactor coolants [Citation1] and their radiation tolerance [Citation2] makes the MAX phases promising candidate materials for advanced nuclear systems. However, the properties of the MAX phases are compound-specific; for example, Zr2AlC interacts with liquid lead and lead-bismuth eutectic [Citation3] even though most MAX phases are characterised by complete immunity to liquid metal corrosion attack. On the other hand, the commonly observed stability under ion irradiation is not observed in Cr2AlC, which tends to amorphize [Citation4]. Synthesising solid solutions on the M-, A- and/or X-site improved the oxidation resistance [Citation5–7], fracture toughness [Citation8,Citation9], strength [Citation6,Citation8], and/or phase purity [Citation10,Citation11] of various ternary MAX phases. 211 MAX phase-based ceramics with increased phase purity were experimentally synthesised by using elements with similar average atomic radii to produce double solid solutions on both M- and A-sites [Citation10,Citation11].
Alloying is commonly used to improve material properties and produce single-phase concentrated solid solutions, such as high-entropy alloys (HEAs) characterised by high strength-to-weight ratios, thermal stability, hardness, high-temperature strength, fatigue and corrosion resistance [Citation12,Citation13], as well as radiation tolerance [Citation14–17]. Typically, HEAs contain at least five principal elements with 5–35 at% each.
Designing radiation-tolerant materials typically strives for materials with (1) numerous point defect sinks or recombination centres, (2) limited point defect mobility, and/or (3) intrinsically low defect accumulation [Citation17]. The A-layers in the MAX phases act as sinks for radiation-induced point defects, inherently satisfying the first condition [Citation18]. On the other hand, the enhanced chemical complexity of HEAs is responsible for high stresses on the atomic scale, reducing defect mobility and promoting point defect recombination [Citation19]. Moreover, a number of HEAs investigated for nuclear applications were found to possess appealing properties, such as significantly reduced radiation swelling, low neutron cross-section, reduced activation, high-temperature strength and oxidation resistance [Citation19–23]. Similarly, high-entropy (HE) ceramics show higher hardness [Citation24], oxidation resistance [Citation25], and radiation tolerance [Citation26] as compared to ZrC, a candidate material for Gen-IV fission reactors [Citation26].
In light of these advances, a chemically complex, high-entropy MAX phase material concept is very appealing for nuclear applications, therefore, its study was recommended as a promising future research path [Citation27]. To our knowledge, the few prior studies on multi-elemental MAX phases were associated with V2(Ax,Sn1-x)C with A = Fe, Co, Ni, Mn or binary/ternary/quaternary combinations thereof [Citation28], ‘high-entropy’ M2AlC-MC composite (M = Ti, Zr, Hf, Nb, Ta) [Citation29], ‘medium-entropy’ (Ti,Zr,Hf)2SC MAX phase (90 wt.% phase purity) [Citation30], and ‘compositionally complex’ (Ti,Nb,Ta)4AlC3 and (Ti,Nb,Ta,V)4AlC3 MAX phases [Citation31]. Inspired by previous success in synthesising high-purity double solid solution MAX phases by adding Sn and carefully adjusting the relative atomic radii of the M- and A-elements in order to minimise crystal lattice distortions [Citation10,Citation11], this work synthesised chemically complex MAX phases with five M-elements and two A-elements in the (Ti,Zr,Hf,V,Nb)-(Al,Sn)-C system.
Materials and methods
HfH2, ZrH2, Nb, V, TiH2, Sn, Al, and C raw powders (Table ) were mixed at an M:A:C ratio of 2:1.1:0.95 with equiatomic fractions of M-elements (Hf, Zr, Nb, V, Ti; 20 at% each) and A-elements (Al, Sn; 50 at% each). The powders were dry-mixed on a multidirectional Turbula mixer for 24 h in argon, and the powder mixtures were reactively hot pressed (RHP; W100/150-2200-50LAX, FCT System) in a graphite die (Ø 30 mm) under 30 MPa, for 30 min at 1250°C, 1350°C, or 1450°C (heating rate: 20°C/min).
Table 1. Starting powders used for the synthesis of the RHP MAX phase ceramics.
Density was measured by the Archimedes’ method and residual porosity was calculated from the theoretical density obtained by X-ray diffraction (XRD) and Rietveld refinement. Vickers hardness (Model FV700, Future Tech) was measured using an indentation load of 3 kg for 15 s. Scanning electron microscopy (SEM; Nova NanoSEM 450, FEI) was employed for microstructural imaging, both in the secondary electron (SE) and backscattered electron (BSE) modes, in conjunction with energy dispersive X-ray spectroscopy (EDS) for compositional analysis (reported results: averages of five-point analyses). Elemental mapping of chemically complex regions was done by electron probe microanalysis (EPMA; JXA-8530F, Jeol). XRD (D2 Phaser, Bruker) used Cu Kα radiation at 40 kV and 30 mA to collect patterns in the 5–75° 2θ range, in steps of 0.01°, at 0.2 s per step. Simulated powder XRD patterns were calculated by the VESTA version 3 software [Citation32], while the Materials Analysis Using Diffraction (MAUD) software was used for Rietveld refinement of the XRD patterns [Citation33]. Ternary MAX phase crystal structure (P63/mmc) input files were modified to include 5 elements on the M- and 2 elements on the A-site, assuming a random distribution. MAX phase compounds with distinctly different compositions were identified by EDS inspection and introduced to the Rietveld refinement software. The elemental occupancies of each site in the MAX phase structure were determined using elemental ratios measured by SEM/EDS, however, these occupancies were not refined further due to the high chemical complexity of the solid solutions. Thin foils made by focused ion beam (FIB; Nova NanoLab 600 DualBeam, FEI) were studied by Cs-corrected scanning transmission electron microscopy (S/TEM, ARM200F JEOL) at 200 kV, using selected area diffraction (SAED), bright field and high-angle annular dark field (HAADF) STEM imaging, and EDS mapping. Selected area quantification of STEM/EDS elemental maps was used to determine individual grain compositions and averages over 18 grains. The average grain size was determined by measuring the width and length of ∼270 MAX phase laths using the ImageJ software [Citation34].
Results and discussion
The density of the produced ceramics was 6.43 g/cm3 (RHP 1250°C), 7.19 g/cm3 (RHP 1350°C), and 7.23 g/cm3 (RHP 1450°C), i.e. the highest amount of residual porosity (3%; see Table ) characterised the material that was sintered at the lowest temperature. BSE microstructural overview images of the produced ceramics are provided in Figure (a-c). RHP 1250°C consisted of a matrix of sub-micrometre 211 MAX phase grains, MC grains with varying composition (some V-rich, some (Zr,Hf)-rich), and dark alumina (Al2O3) grains (Figure (g, h)). This ceramic also contained large (≤ 40 µm) ‘islands’ of intermetallic compounds (IMCs) with Nb2Al cores (Figure (a), point-II) and Al3Nb rims (Figure (a), point-I); the Al3Nb rims contained traces of undissolved Sn, while Sn dissolved in the Nb2Al cores. The binary-carbide-free RHP 1350°C and RHP 1450°C featured a dual microstructure made of two distinct regions, herein referred to as ‘single-phase’ (Figure (d, i)) and ‘dual-phase’ (Figure (d, j)). The ‘single-phase’ regions consisted of elongated MAX phase grains with similar compositions, while the ‘dual-phase’ regions comprised two MAX phases with different compositions. The MAX phase in the ‘single-phase’ regions is named ‘single-phase 211’ (SP211), whereas the two MAX phases in the ‘dual-phase’ regions are named ‘dual-phase 312’ (DP312) and ‘dual-phase 211’ (DP211), based on their M/A ratios (2.6 and 2.0, respectively). The compositions of the different regions were determined by SEM/EDS and are reported in Table . Grain size measurements (in μm) in ‘single-phase’ SP211 regions yielded average length/width ratios of (2.39 ± 1.70)/(0.57 ± 0.24) and (4.28 ± 2.82)/(0.98 ± 0.50) for RHP 1350°C and RHP 1450°C, respectively. In both cases, this aspect ratio was around 4.2–4.35, interestingly similar to the SP211 lattice parameter ratio (c/a ≈ 4.4), suggesting a correlation between crystal habit and crystal structure.
Figure 1. BSE microstructural overview images of (a) RHP 1250°C, (b) RHP 1350°C, and (c) RHP 1450°C. (d) Dual microstructure of RHP 1350°C. SE images of Vickers indentation corners in (e) ‘single-phase’ and (f) ‘dual-phase’ regions in RHP 1350°C. BSE images of the 211 MAX phase matrix in RHP 1250°C: detail (g) and overview (h). BSE images of the ‘single-phase’ (i) and ‘dual-phase’ (j) regions in RHP 1350°C.
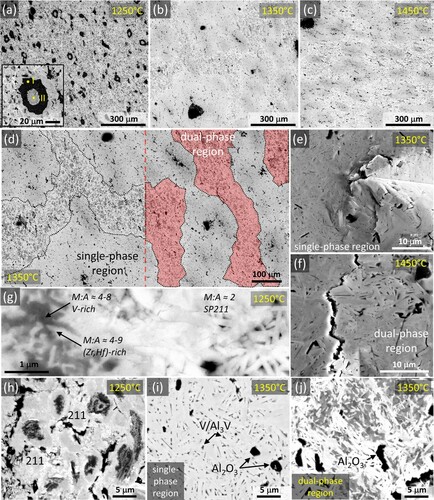
Table 2. Phase assembly (vol%), chemical composition, lattice parameters (Å), density (g/cm3), porosity (%), hardness (GPa), and grain size in length/width (both in μm) of the produced ceramics. Uncertainties: ∼1 for vol%, ∼10−3 Å for lattice parameters and z. SP and DP stand for ‘single-phase’ and ‘dual-phase’. Numbers in parenthesis indicate uncertainties in the last digit.
The XRD patterns were characterised by broad MAX phase (hkl) peaks, possibly due to peak overlap of MAX phase grains/clusters with slightly inhomogeneous distributions of elements leading to lattice variations. In contrast to the broad MAX phase peaks, the IMC peaks in RHP 1250°C are sharp (Figure (a)). Broad peaks of pseudo-binary MC (M = Ti, Zr, Hf, V, Nb) were also observed in the XRD pattern of RHP 1250°C (Figure (a)), possibly due to the presence of different MC compositions with varying lattice parameters, some of which were V-rich and some (Hf,Zr)-rich according to EDS. With increasing sintering temperature, the MAX phase peaks became sharper (Figure (b, c)). Although not visible in the XRD patterns due to its low fraction and peak overlap with other phases, Al2O3 was invariably present in the produced ceramics due to the aluminothermal reduction of Nb2O5 in the Nb raw powder and the possible oxygen contamination of the other powders [Citation10]. peaks belonging to MAX phase compounds had particularly low intensity, as also seen in the simulated powder XRD peak intensities of the SP211 phase (Figure (d)). Rietveld refinement of XRD data from the produced ceramics (RHP 1250/1350/1450°C) and SEM/EDS findings showed the presence of a predominant (71–76 vol%) SP211 phase with the (Zr0.16–0.21,Hf0.17–0.22,Ti0.22–0.24,Nb0.25–0.30,V0.10–0.14)2(Al0.33–0.50,Sn0.50–0.67)C general composition. Within this phase, the largest deviations from the composition of the initial powder mixture among M-elements were observed for Nb and V. The higher Nb content in SP211 could be associated with a reduced Nb content in the main (18 vol%) MC secondary phase in RHP 1250°C. Although the exact MC phase compositions are not reported here due to their complexity, the Nb content of MC phases was invariably small (almost zero in V-rich carbides, <10 at% in (Hf,Zr)-rich carbides). The rate-limiting factor for the formation of high-entropy carbides is the M-element diffusivity, which is proportional to the ease of M-site vacancy formation in MC carbides [Citation35]. Since Nb has the lowest vacancy formation energy on the M-site among MC carbides (Nb < V < Ti < Hf < Zr [Citation36]), NbC is likely to become the preferred ‘host compound’ for the easy inward diffusion of other M-elements. Such NbC-based, chemically complex ‘host’ carbides could aid the nucleation of SP211, explaining the formation of the Nb-rich MAX phase. The reduced V incorporation in SP211 is discussed further in the text. Considering the fractions of DP312 and DP211 MAX phases in the ‘dual-phase’ regions, the overall MAX phase content increased to 95–96 vol% in RHP 1350°C and RHP 1450°C. While SP211 formed at 1250°C, the disappearance of IMC ‘islands’ and MC carbides, along with the formation of ‘dual-phase’ MAX phase regions at higher temperatures (1350–1450°C), suggest a MAX phase synthesis route that involves reactions between pseudo-binary carbides and IMCs. Likewise, the presence of IMCs and MC carbides indicate an incomplete MAX phase formation reaction at 1250°C. SEM/EDS compositions and refined lattice parameters of the constituent phases, along with density and hardness values, are given in Table .
Figure 2. Rietveld refined XRD patterns for (a) RHP 1250°C, (b) RHP 1350°C, and (c) RHP 1450°C. Experimentally measured (black) and calculated (red for full patterns, other colours for individual phases) patterns and their differences (black; shown at the bottom of each pattern). (d) Simulated powder XRD pattern for SP211 in RHP 1350°C.

Figure (e) shows plastic deformation without crack formation at the corner of a Vickers indentation in the ‘single-phase’ region of RHP 1350°C. On the other hand, Figure (f) shows strong intergranular crack deflection, indicative of high fracture toughness, at the corner of an indentation in the ‘dual-phase’ region of RHP 1450°C. The hardness of the produced ceramics falls within the 2–8 GPa range, typical for the MAX phases [Citation37]. The slightly more porous RHP 1250°C (3% porosity) was substantially softer (3.6 ± 0.5 GPa) than RHP 1350°C and RHP 1450°C (7.1 ± 0.4 and 6.8 ± 0.2 GPa, respectively), even though it contained 9 vol% of the harder Al3Nb IMC (∼6 GPa) and 27 vol% pseudo-binary MC carbides (Table ). The hardness of ternary MAX phases comprising elements used in this work varied between 2.5 GPa for V2AlC [Citation38] and 6.5 GPa for Nb2AlC [Citation39]. (Zr,Ti)2(Al0.5,Sn0.5)C quinary compounds were harder ( 5.9 GPa) than the related Zr2(Al0.5,Sn0.5)C (5.3 GPa) and Ti2(Al0.5,Sn0.5)C (3.7 GPa) quaternary compounds, a fact that was tentatively attributed to solid solution hardening [Citation11]. Similarly, the (Ti,Zr,Hf,V,Nb)n+1(Al,Sn)Cn MAX phase double solid solutions were harder than all known ternary, quaternary, and quinary MAX phase solid solutions made of the same elements [Citation11,Citation38,Citation39].
The chemical composition of the ‘dual-phase’ region in RHP 1350°C was determined by both SEM/EDS and EPMA (Figure ), indicating high Zr/Hf/Sn contents in DP312 (Ti0.24,Zr0.33,Hf0.35,V0.05,Nb0.03)3(Al0.33,Sn0.67)C2 and high V/Nb/Ti/Al contents in DP211 (Ti0.28,Zr0.05,Hf0.06,V0.49,Nb0.12)2(Al0.67,Sn0.33)C. It is likely that DP312 contains mixed 312 & 211 stackings (not proven by TEM here), as the elemental ratio M:A was ∼2.6 instead of the expected 3.0. Supported by XRD analysis, DP312 was identified and refined as a 312 MAX phase. It is worthwhile noticing that the Al/Sn ratio on the A-site of each MAX phase self-adjusts to accommodate larger (Zr, Hf) or smaller (V) M-elements, in accordance with the similar M- and A-site atomic radii principle published earlier [Citation10]. The formation of DP312 and DP211 at higher temperatures in ceramics with similar SP211 contents suggests that a transformation/decomposition of SP211 is not really responsible for the nucleation of these MAX phases. In fact, the disappearance of the (Hf,Zr)-rich and V-rich MC carbides detected at 1250°C and the concurrent formation of (Hf,Zr)-rich (DP312) and V-rich (DP211) MAX phases indicate that reactions between pre-existing MCs and IMCs form MAX phases with compositions similar to those of the ‘precursor’ MC phases.
Figure 3. EPMA elemental maps of the ‘dual-phase’ region in RHP 1350°C. The ‘level’ values in the colour legends represent the intensity of the detected elements.
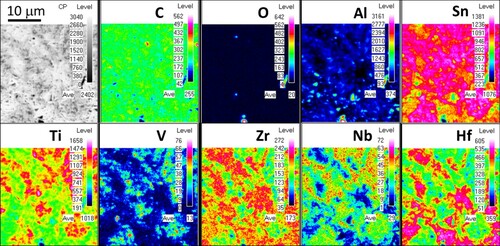
The dominant SP211 phase in RHP 1350°C was studied in-depth by TEM/STEM/EDS. Figure presents STEM/EDS data collected from an SP211 ‘single-phase’ region with uniform chemical composition. In alignment with XRD results, the identified secondary phases in this region were metallic V (bcc) with some dissolved Al, and Al3V IMC in triple junctions and grain boundaries. The presence of V-rich secondary phases agrees with the reduced V content of the dominant SP211 phase, which might possibly reflect a low V solid solubility in the MAX phase lattice at 1350°C. Moreover, some of the added V resided in sporadic, large (∼500 µm) V-rich and Al-containing areas (not shown here) that presumably resulted from non-optimal raw powder mixing.
TEM confirmed that the chemically complex 211 MAX phases have the typical MAX phase crystal structure, space group P63/mmc, as proven by the SAED patterns of the [] and [
] zone axes, Z.A., in Figure (d-e). Figure (f-g) show SAED and Fast Fourier Transformation (FFT) patterns belonging to the V and Al3V secondary phases. Figure (b-c) are high-resolution (HR) HAADF-STEM images of a SP211 grain with slightly brighter single-atom rows (A) between double-atom rows (M) (Figure (c)). The Z (atomic number) contrast induced by HAADF-STEM imaging is difficult to observe, likely due to similar average Z values in the M (41 ± 1) and A (39 ± 1) layers of SP211, and an intensity profile is overlaid with the HRSTEM image for confirmation (Figure (c)). Even though STEM/EDS results from a small area (Figure (j)) are slightly different from SEM/EDS results from a large area (Table ), they are probably more representative of the examined region due to the higher spatial resolution of STEM/EDS. Based on the SAED pattern of Figure (d), the SP211 lattice parameters were a ≈ 3.20 Å and c ≈ 14.85 Å, differing from the values obtained by XRD Rietveld refinement. Although XRD typically yields accurate lattice parameter data, the lattice parameter values derived by SAED might be more representative for the specific SP211 grains, as the XRD values are affected by the overlap of multiple phases, peak broadening, and chemical complexity.
Figure 4. STEM/EDS maps for (a) Al, (b) Sn, (c) C, (d) Ti, (e) Zr, (f) Hf, (g) Nb and (h) V of the ‘single-phase’ region in RHP 1350°C with corresponding HAADF/STEM image (i). (j) STEM/EDS spectrum of the area within the yellow frame in (i).
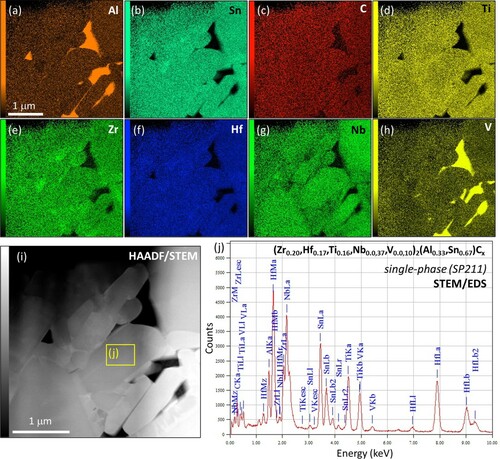
Figure 5. (a) HAADF-STEM overview image of the ‘single-phase’ region in RHP 1350°C. (b-c) HR HAADF-STEM images and FFT of the [] Z.A. of the SP211 grain circled in (a). (d,e) SAED patterns of the SP211 [
] and [
] Z.A., respectively. (f) SAED pattern of the [
] Z.A. of the V-based secondary phase. (g) HRTEM image and FFT of the [
] Z.A. of the Al3V IMC.
![Figure 5. (a) HAADF-STEM overview image of the ‘single-phase’ region in RHP 1350°C. (b-c) HR HAADF-STEM images and FFT of the [211¯0] Z.A. of the SP211 grain circled in (a). (d,e) SAED patterns of the SP211 [211¯0] and [11¯00] Z.A., respectively. (f) SAED pattern of the [100] Z.A. of the V-based secondary phase. (g) HRTEM image and FFT of the [100] Z.A. of the Al3V IMC.](/cms/asset/5a70d351-d133-4db6-a023-0b339175361a/tmrl_a_2017043_f0005_oc.jpg)
Conclusions
Fine-grained (<5 µm) MAX phase ceramics were produced in the (Ti,Zr,Hf,V,Nb)-(Al,Sn)-C system by reactive hot pressing of transition metal hydride and elemental powders at 1250–1450°C for 30 min under a load of 30 MPa. All ceramics contained chemically complex double solid solution MAX phases, each comprising five M- and two A-elements. All produced ceramics contained a predominant 211 phase with the (Ti0.23,Zr0.18,Hf0.20,V0.11,Nb0.28)2(Al0.42,Sn0.58)C average composition. The binary-carbide-free ceramics sintered at 1350–1450°C contained two more chemically complex MAX phases, i.e. a 312 phase with the (Ti0.23,Zr0.31,Hf0.31,V0.08,Nb0.08)3(Al0.36,Sn0.64)C2 average composition and a 211 phase with the (Ti0.26,Zr0.07,Hf0.07,V0.47,Nb0.13)2(Al0.66,Sn0.34)C average composition. This work demonstrates that ultra-pure, dense, chemically complex MAX phase ceramics can be synthesised in the (Ti,Zr,Hf,V,Nb)-(Al,Sn)-C system via the double solid solution approach. Considering the inherent radiation tolerance of the nanolaminated MAX phases and the expected reduction in defect mobility due to the high chemical complexity, these materials are promising candidates for nuclear applications close to the reactor core (e.g. fuel cladding applications).
Acknowledgements
The authors gratefully acknowledge FWO-Vlaanderen (Hercules project AKUL/1319) and financial support from the Euratom research and training programme 2014–2018 under Grant Agreement No. 740415 (H2020 IL TROVATORE). N. Goossens acknowledges FWO fundamental research grant 1118120N. Special thanks to P.O.Å. Persson for valuable discussions on TEM results, and V. Naenen, S. Navarini, L. Snels, and T. Van Hout for launching this study during their P&O project at the Dept. of Materials Engineering of the KU Leuven.
Disclosure statement
No potential conflict of interest was reported by the author(s).
Additional information
Funding
References
- Heinzel A, Müller G, Weisenburger A. Compatibility of Ti3SiC2 with liquid Pb and PbBi containing oxygen. J Nucl Mater 2009;392:255–258.
- Tunes MA, Harrison RW, Donnelly SE, et al. A transmission electron microscopy study of the neutron-irradiation response of Ti-based MAX phases at high temperatures. Acta Mater 2019;169:237–247. https://www.sciencedirect.com/science/article/pii/S1359645419301326.
- Lapauw T, Tunca B, Joris J, et al. Interaction of Mn+1AXn phases with oxygen-poor, static and fast-flowing liquid lead-bismuth eutectic. J Nucl Mater 2019;520:258–272. doi:https://doi.org/10.1016/j.jnucmat.2019.04.010.
- Wang C, Yang T, Xiao J, et al. Structural transitions induced by Ion irradiation in V2AlC and Cr2AlC. J Am Ceram Soc. 2016;99:1769–1777.
- Salama I, El-Raghy T, Barsoum MW. Oxidation of Nb2AlC and (Ti,Nb)2AlC in Air. J Electrochem Soc 2003;150:C152–C158–C158. doi:https://doi.org/10.1149/1.1545461.
- Gu J, Pan L, Yang J, et al. Mechanical properties and oxidation behavior of Ti-doped Nb4AlC3. J Eur Ceram Soc. 2016;36:1001–1008.
- Kalidindi SR, Zhen T, Barsoum MW. Macroscale constitutive modeling of kinking nonlinear elastic solids. Mater Sci Eng A 2006;418:95–98.
- Yu W, Li S, Sloof WG. Microstructure and mechanical properties of a Cr2Al(Si)C solid solution. Mater Sci Eng A 2010;527:5997–6001. doi:https://doi.org/10.1016/j.msea.2010.05.093.
- Lapauw T, Tytko D, Vanmeensel K, et al. (Nbx,Zr1– x)4AlC3 MAX phase solid solutions: processing, mechanical properties, and density functional theory calculations. Inorg Chem. 2016;55:5445–5452. http://pubs.acs.org/doi/abs/10.1021/acs.inorgchem.6b00484.
- Lapauw T, Tunca B, Potashnikov D, et al. The double solid solution (Zr,Nb)2(Al,Sn)C MAX phase: a steric stability approach. Sci Rep 2018;8:1–13. doi:https://doi.org/10.1038/s41598-018-31271-2.
- Tunca B, Lapauw T, Delville R, et al. Synthesis and characterization of double solid solution (Zr,Ti)2(Al,Sn)C MAX phase ceramics. Inorg Chem 2019;58:6669–6683.
- Gludovatz B, Hohenwareter A, Catoor D, et al. A fracture-resistant high-entropy alloy for cryogenic applications. Science. 2014;345:1153–1158. http://www.ncbi.nlm.nih.gov/pubmed/17840151.
- Senkov ON, Wilks GB, Scott JM, et al. Mechanical properties of Nb25Mo25Ta25W25 and V20Nb20Mo20Ta20W20 refractory high entropy alloys. Intermetallics 2011;19:698–706. https://www.sciencedirect.com/science/article/pii/S0966979511000185.
- Xia S, Wang Z, Yang T, et al. Irradiation behavior in high entropy alloys. J Iron Steel Res Int 2015;22:879–884. doi:https://doi.org/10.1016/S1006-706X(15)30084-4.
- Yeh JW, Lin SJ. Breakthrough applications of high-entropy materials. J Mater Res. 2018;33:3129–3137.
- Kumar NAPK, Li C, Leonard KJ, et al. Microstructural stability and mechanical behavior of FeNiMnCr high entropy alloy under ion irradiation. Acta Mater 2016;113:230–244.
- Zinkle SJ. Advanced irradiation-resistant materials for Generation IV nuclear reactors. In: Yvon P., editor. Structural materials for Generation IV nuclear reactors. Cambridge: Woodhead Publishing, 2017. p. 569–594. doi:https://doi.org/10.1016/B978-0-08-100906-2.00016-1.
- Tallman DJ, He L, Gan J, et al. Effects of neutron irradiation of Ti3SiC2 and Ti3AlC2 in the 121–1085 °C temperature range. J Nucl Mater 2017;484:120–134. doi:https://doi.org/10.1016/j.jnucmat.2016.11.016.
- Lu C, Niu L, Chen N, et al. Enhancing radiation tolerance by controlling defect mobility and migration pathways in multicomponent single-phase alloys. Nat Commun. 2016;7:1–8. http://www.nature.com/articles/ncomms13564.
- Kareer A, Waite JC, Li B, et al. Short communication: ‘Low activation, refractory, high entropy alloys for nuclear applications.’. J Nucl Mater 2019;526:0–5.
- King DJM, Cheung STY, Humphry-Baker SA, et al. High temperature, low neutron cross-section high-entropy alloys in the Nb-Ti-V-Zr system. Acta Mater. 2019;166:435–446. doi:https://doi.org/10.1016/j.actamat.2019.01.006.
- Ayyagari A, Salloom R, Muskeri S, et al. Low activation high entropy alloys for next generation nuclear applications. Materialia. 2018;4:99–103. doi:https://doi.org/10.1016/j.mtla.2018.09.014.
- He MR, Wang S, Jin K, et al. Enhanced damage resistance and novel defect structure of CrFeCoNi under in situ electron irradiation. Scr Mater 2016;125:5–9. doi:https://doi.org/10.1016/j.scriptamat.2016.07.023.
- Sarker P, Harrington T, Toher C, et al. High-entropy high-hardness metal carbides discovered by entropy descriptors. Nat Commun 2018;9:1–10. doi:https://doi.org/10.1038/s41467-018-07160-7.
- Tan Y, Chen C, Li S, et al. Oxidation behaviours of high-entropy transition metal carbides in 1200 °C water vapor. J Alloys Compd 2020;816:1–6. doi:https://doi.org/10.1016/j.jallcom.2019.152523.
- Wang F, Yan X, Wang T, et al. Irradiation damage in (Zr0.25Ta0.25Nb0.25Ti0.25)C high-entropy carbide ceramics. Acta Mater 2020;195:739–749.
- Moghaddam AO, Cabot A, Trofimov EA. Does the pathway for development of next generation nuclear materials straightly go through high-entropy materials? Int J Refract Met Hard Mater 2021;97:1–7. doi:https://doi.org/10.1016/j.ijrmhm.2021.105504.
- Li Y, Lu J, Li M, et al. Multielemental single–atom-thick A layers in nanolaminated V2(Sn,A)C (A = Fe, Co, Ni, Mn) for tailoring magnetic properties. Proc Natl Acad Sci 2020;117:820–825. https://www.pnas.org/content/117/2/820.
- Bao W, Wang XG, Ding H, et al. High-entropy M2AlC-MC (M = Ti, Zr, Hf, Nb, Ta) composite: synthesis and microstructures. Scr Mater. 2020;183:33–38. doi:https://doi.org/10.1016/j.scriptamat.2020.03.015.
- Chen K, Chen Y, Zhang J, et al. Medium-entropy (Ti,Zr,Hf)2SC MAX phase. Ceram Int. 2020;47(6):7582–7587. doi:https://doi.org/10.1016/j.ceramint.2020.11.096.
- Tan Y, Xia Y, Teng Z, et al. Synthesis and enhanced mechanical properties of compositionally complex MAX phases. J Eur Ceram Soc. 2021;41:4658–4665. doi:https://doi.org/10.1016/j.jeurceramsoc.2021.03.027.
- Momma K, Izumi F. VESTA 3 for three-dimensional visualization of crystal, volumetric and morphology data. J Appl Crystallogr. 2011;44:1272–1276.
- Lutterotti L, Matthies S, Wenk H. MAUD: a friendly Java program for material analysis using diffraction. CPD Newsl. 1999;21:14–15.
- Schindelin J, Arganda-Carreras I, Frise E, et al. Fiji: An open-source platform for biological-image analysis. Nat Methods. 2012;9:676–682.
- Castle E, Csanádi T, Grasso S, et al. Processing and properties of high-entropy ultra-high temperature carbides. Sci Rep. 2018;8:1–12.
- Yu XX, Thompson GB, Weinberger CR. Influence of carbon vacancy formation on the elastic constants and hardening mechanisms in transition metal carbides. J Eur Ceram Soc. 2015;35:95–103. doi:https://doi.org/10.1016/j.jeurceramsoc.2014.08.021.
- Barsoum MW. MAX phases properties of machinable ternary carbides and nitrides. Weinheim, Germany: WILEY-VCH Verlag GmbH & Co. KGaA; 2013.
- Hu C, He L, Liu M, et al. In situ reaction synthesis and mechanical properties of V2AlC. J Am Ceram Soc. 2008;91:4029–4035.
- Salama I, El-Raghy T, Barsoum MW. Synthesis and mechanical properties of Nb2AlC and (Ti,Nb)2AlC. J Alloys Compd. 2002;347:271–278.