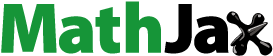
Abstract
High-temperature solid-solution is indispensable for bake-hardenable dilute Mg alloys, which generally induces grain coarsening. Herein, we report extraordinary thermal stability in a bake-hardenable dilute Mg-1.61Zn-0.57Mn-0.54Ca-0.46Al (wt. %, ZMXA2110) alloy, maintaining fine-grained structure at 450 °C. The thermal stability is stemmed from the Zener pinning effect of dense fine (∼15.0 nm) core–shell β-Mn particles and co-segregation of Zn and Ca at grain boundaries. The fine-grained (∼3.2 μm) dilute alloy exhibits high room-temperature formability in solid-solution condition with an Index Erichsen value of ∼6.0 mm, and impressive yield strength of ∼293 MPa with an evident increment of ∼60 MPa by bake-hardening treatment.
GRAPHICAL ABSTRACT

IMPACT STATEMENT
By achieving extraordinary fine-grain thermal stability under high-temperature solid-solution treatment, appreciable bake-hardenability along with fine-grained structure are obtained simultaneously to ensure the development of dilute Mg alloys with high strength.
1. Introduction
Recently, dilute Ca-containing magnesium (Mg) alloy sheets have been gaining extensive attention because of high room-temperature formability and moderate strength [Citation1–4]. However, it is still a great challenge to achieve high yield strength in dilute Mg alloys while maintaining good room-temperature formability, leading to insufficient service performance as compared to 6xxx aluminum (Al) alloys [Citation5–8]. Excitingly, bake-hardening (BH) treatment, usually performed in Al alloys and steels, was proved to further increase the flow stress from ∼198 MPa to ∼238 MPa in a room-temperature formable Mg-1.3Al-0.8Zn-0.7Mn-0.5Ca (wt. %) alloy sheet, which was ascribed to co-segregation of Al, Zn, and Ca at dislocations along with co-clustering of these solutes [Citation9]. Nevertheless, since bake-hardenability strongly depends on the dissolved degree of solutes in matrix, high-temperature solid-solution (T4) treatment is indispensable, which inevitably induces grain coarsening (from ∼3–5 [Citation10] to ∼10–50 μm). The fine-grain strengthening would lose ∼50–90 MPa in Mg alloys (taking the Hall-Petch coefficient as 205 MPa μm0.5 [Citation11,Citation12]), which can be hardly compensated by the limited BH response. In other words, stabilizing a fine-grained structure and meanwhile achieving a significant BH effect would be an efficient alternative to strengthening dilute Mg alloys. Accordingly, high thermal stability of the fine-grained structure is urgently required under high-temperature T4 treatment, e.g. 450∼500 °C.
Recent studies revealed that the enhanced thermal stability of Mg alloys relied on solute segregation at the grain boundary (GB), which could slow down grain migration by reducing GB energy and/or exerting dragging pressure. A successful example was reported in a Mg-6Zn-0.5Zr-0.2Ca (wt. %) alloy [Citation13], wherein co-segregation of Zn and Ca at GBs was demonstrated to enhance thermal stability of grain structure at 400 °C. Nevertheless, when the temperature reaches 450 °C, the driving pressure on GBs exceeds a critical threshold, and thus GBs could break through the segregated solute atmosphere and migrate rapidly, leading to grain instability [Citation14]. Second phase pinning is another effective way to improve thermal stability. There exist some reliable intermetallics, e.g. Al3Sc, to retain the fine-grained structure of Al alloys at 450 °C [Citation15,Citation16], while it is rarely reported in dilute Mg alloys to achieve comparable thermal stability. More strategies of stabilizing fine-grained structure should be proposed in dilute heat-treatable Mg alloys, with the goal of attaining high performance.
In this study, we found extraordinary thermal stability of fine-grained structure in a bake-hardenable Mg-1.61Zn-0.57Mn-0.54Ca-0.46Al (wt. %, ZMXA2110) alloy under T4 treatment at 450 °C, retaining a fine-grained structure of ≤3.4 μm up to 30 min. The dilute alloy exhibits satisfactory room-temperature formability (Index Erichsen ∼6.0 mm) in T4 condition (10 min) and appreciable yield strength (∼293 MPa) after BH treatment. The present work may shed new insight into the development of strong and formable Mg alloy sheets in dilute composition.
2. Materials and methods
The ZMXA2110 alloy was prepared by melting in an electric resistance furnace and casting in the water-chilled copper mold with the cavity dimension of 60 mm75 mm
6 mm. The as-cast slabs were subjected to a multi-stage homogenization treatment (330 °C/60 min + 400 °C/60 min + 450 °C/120 min), followed by water quenching. Afterward, the slabs were machined into samples with a thickness of ∼5 mm and rolled at 300∼325 °C by 5 passes to a final thickness of ∼0.8 mm, with ∼30% reduction per pass. The rolled sheets were T4-treated at 450 °C for 10, 30, 60, and 120 min, respectively. Tensile specimens with a gauge length of 10 mm and a width of 4 mm were cut along the rolling direction (RD). To simulate the BH process, the T4-treated specimens were tensile stretched to the strain of ∼2%, then unloaded and aged at 200 °C for 30 min. The discrepancy between the flow stress at unloading point and the yield strength (YS) after the BH process is defined as the BH response, i.e. bake-hardenability [Citation9]. To obtain a high BH response, the temperature of BH treatment was optimized to be 200 °C, which is in the range of industrial applications, i.e. 150–200 °C [Citation17].
Uniaxial tensile tests were conducted using an AGS-100 kN testing machine at a strain rate of 110−3 s−1. To measure the Index Erichsen (I.E.) value, Erichsen cupping tests were performed on circular samples at room temperature with a hemispherical punch in a diameter of 20 mm. The sample diameter is 50 mm, and Vaseline along with Teflon film are used for lubrication. The punch speed and blank-holder force are 0.1 mm s−1 and 80 kN, respectively. At least three samples were tested to ensure reproducibility of the tensile and cupping test results. The microstructure characterizations were carried out by a Schottky field emission microscope (Zeiss, Sigma 500) equipped with an electron backscatter diffraction (EBSD) detector (Oxford instruments, Symmetry), transmission electron microscopes (TEM, JEM-2100F and JEM-F200) operating at 200 kV and three-dimensional atom probe tomography (3D APT). Transmission Kikuchi diffraction (TKD) analyses were performed on the TEM sample by using Sigma 500 equipment. Thin foils for TEM analyses were prepared by mechanical grinding to a thickness of ∼80 μm, twin-jet electropolishing for perforation, and ion-milling using a Gatan 691 Precision Ion Polishing System (PIPS) with liquid nitrogen cooling. The APT specimen was prepared using the two-stage electro-polishing method and performed on a LEAP 4000X Si under ultraviolet laser pulse mode at a pulse energy of 60 pJ and a pulse rate of 200 Hz.
3. Results and discussion
3.1. Mechanical properties
Figure a shows tensile curves of the ZMXA2110 alloy sheets after T4 (10 min) and BH treatment, respectively. The T4-treated sample exhibits a YS of ∼234 MPa and an ultimate tensile strength (UTS) of ∼288 MPa, along with an elongation to failure (EL) of ∼21%. The Erichsen cupping test indicates that the T4-treated sample possesses a high I.E. value of ∼6.0 mm (inserted in Figure a). Interestingly, the flow stress increases significantly by ∼60 MPa after a short BH treatment, leading to an appreciable YS of ∼293 MPa, even comparable to that of conventional 6xxx Al alloys. Figure b summarizes the YS and I.E. value of various Mg alloy sheets [Citation2,Citation4,Citation9,Citation18,Citation19]. After BH treatment, the ZMXA2110 alloy shows superior strength-formability synergy to the vast majority of other Mg alloy sheets (Figure b). Furthermore, among the Mg alloys with I.E. values exceeding 5 mm, the ZMXA2110 alloy presents a significantly higher YS.
Figure 1. (a) Tensile curves of the ZMXA2110 alloy sheets after T4 treatment at 450 °C for 10 min and BH treatment, along with the Erichsen cupping test result. (b) The YS and I.E. value of various Mg alloy sheets. (c) The EBSD inverse pole figure (IPF) map and (d) corresponding pole figures of the ZMXA2110 alloy after T4 treatment at 450 °C for 10 min.
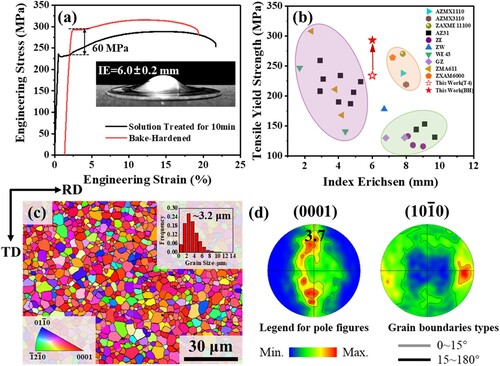
Figure c presents that the ZMXA2110 alloy sheet owns a fine-grained structure with a size of ∼3.2 μm after T4 treatment at 450 °C for 10 min. Meanwhile, the corresponding pole figure reveals a weak texture with a maximum pole intensity of 3.7 mrd (Figure d). Note that the texture here exhibits a ‘quadruple’ characteristic where basal poles are not merely tilted from nominal direction (ND) to RD but also split to transverse direction (TD). Similar textures were also reported in several Mg-Al-Zn-Ca series alloys and are responsible for good room-temperature formability [Citation3,Citation8,Citation19]. However, such kind of texture may lead to the anisotropy of strength, which exists in a few dilute Mg sheet alloys. As shown in Figure S1 (in Supplemental Material), the ZMXA2110 alloy sheet exhibits lower YS of ∼189 MPa and ∼182 MPa along 45° and TD, respectively. Even though a smaller grain size is obtained compared with typical Mg-Al-Zn-Ca series alloys (Table ), the ZMXA2110 alloy sheet shows relatively lower tensile ductility. To uncover the reason of the inferior ductility, SEM analyses were performed before and after the tensile test (Figure S2 in Supplemental Material). Intermetallic compounds Mg2Ca and β-Mn were detected to distribute homogeneously in the ZMXA2110 alloys sample after T4 treatment at 450 °C for 10 min. As shown in Figure S2d–f, the cracking and cavitation of Mg2Ca particles are observed after the tensile test, which is seriously detrimental to the ductility. Therefore, further optimization of alloy chemistry is greatly encouraged for eliminating Mg2Ca particles to enhance ductility and formability.
Table 1. Tensile properties of ZMXA2110 and other Mg alloys (tensile directions are along RD unless otherwise specified).
3.2. Thermal stability of the fine-grained structure
To assess the processing window of the T4 treatment, the microstructure evolution and corresponding mechanical properties of the samples treated at 450 °C from 30 to 120 min were further investigated, as shown in Figure a–c and Table . Surprisingly, as the T4 treatment time increases from 10 (Figure c) to 30 min (Figure a), the grain size remains nearly unchanged. While further extending the time to 60 and 120 min (Figure b and c), the grains grow slowly to the size of ∼4.5 and ∼6.9 μm, respectively.
Figure 2. EBSD IPF maps and inserted grain-size frequency distribution histograms of the ZMXA2110 alloy sheets after T4 treatment at 450 °C for (a) 30 min, (b) 60 min, and (c) 120 min.
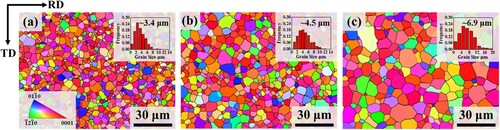
Moreover, during the grain stable stage (10–30 min), the YS of T4-treated and BH samples undergo minor variation from ∼234 to ∼233 MPa and ∼293 to ∼297 MPa (Table ), respectively. After T4 treatment for 60 min, although the YS of the T4-treated sample decreases to ∼220 MPa, the eventual YS only witnesses a slight decline after BH treatment (∼289 MPa) due to the enhanced bake-hardenability (Table ) and strain hardening capacity. As the time further extends to 120 min, the YS of both T4 and BH samples decrease to ∼196 and ∼283 MPa (Table ), respectively. Tensile curves of samples after T4 treatment for different times are provided in Figure S1. Compared with other Mg alloys, whether medium rare-earth containing or dilute ones (Table ), the ZMXA2110 alloy sheet possesses excellent thermal stability during T4 treatment and a wide processing window up to at least 30–60 min.
3.3. Mechanism underlying the thermal stability of fine-grained structure
To uncover the underlying mechanism responsible for the excellent thermal stability, HAADF-STEM analyses were performed on the samples after T4 treatment for 10 and 60 min. As shown in Figure a, dense and homogeneously distributed intermetallic particles with an average size of ∼15.0 nm are present in the sample treated for 10 min. Using TKD and high-resolution transmission electron microscopy (HRTEM) analyses, these particles are confirmed to be β-Mn phases (Figure S3 in Supplemental Material). Clearly in Figure S4a (in Supplemental Material), some particles are located at GBs, implying the effectiveness of the β-Mn particles on pinning the GBs. In addition, the Zn and Ca segregation at GBs was also detected in the sample treated for 10 min, as shown in b and c. Note that similar GB segregation behavior was reported in multiple Mg-Zn-Ca(-Al) series alloys [Citation9,Citation18,Citation24,Citation25]. With T4 treatment time extending to 60 min, β-Mn particles could still impede the motion of GBs effectively (Figure S4b and c), and the mean size of these particles merely increases to ∼17.0 nm. The reasons for such slow grain growth could be: (i) the driving force for grain growth is still larger than the Zener pinning force, and (ii) grain boundary mobility is relatively high at T4 condition. Meanwhile, the distribution of β-Mn particles surrounding GBs becomes quite heterogeneous, exhibiting the particle-free zone (PFZ) (Figure S4b) or sparse distribution (Figure S4c). Generally, as the GB is considered as a high-diffusivity path, particles around GBs show more rapid coarsening kinetics than those in grain interiors, which should be responsible for the heterogeneous distribution. The similar heterogeneous coarsening of particles has been reported by Gao et al. [Citation26], and could also reasonably explain why the grain coarsening occurs in the ZMXA2110 alloy after T4 treatment for 60 min. The GB segregation is extensively observed (e.g. in Figure e and f), which suggests that the GB segregation could impose dragging pressure against the grain growth in the ZMXA2110 alloy sheet [Citation27]. Consequently, the thermal stability of the ZMXA2110 alloy can be ascribed to the β-Mn particles and GB co-segregation.
3.4. Mechanism underlying the thermal stability of β-Mn particles
Note that β-Mn particles in the ZMXA2110 alloy are thermally stable at such a high temperature, which is important for the grain stability. To reveal the mechanism underlying the thermal stability of β-Mn particles, an inspection of solute distribution around β-Mn particles would be necessary. Through high-magnification EDS scanning and APT analyses of β-Mn particles, β-Mn particles are observed with a core–shell structure, i.e. the co-segregation of Zn and Ca at β-Mn/matrix interphase boundaries (Figure ). Solute segregation at interphase boundary has been reported in various alloy systems, e.g. Gd segregation at Zn2Zr/α-Mg interfaces [Citation28] and Sc segregation at Al2Cu/α-Al interfaces [Citation29], which are deemed to inhibit the coarsening of precipitates by alleviating strain, reducing interface energy and/or decelerating diffusion of atoms in precipitates. To verify the effect of the interphase boundary segregation on suppressing coarsening of β-Mn particles, we further prepared a Mg-0.61Mn-0.49Al (wt. %, MA10) alloy under the same fabrication route as that of the ZMXA2110 alloy. Interestingly, the β-Mn particles of the MA10 alloy grow from an average size of ∼21.6 to ∼28.0 nm as the T4 treatment time increases from 10 to 60 min (Figure S5a and b in Supplemental Material), which is larger than that of the ZMXA2110 alloy (Figure S5c). Meanwhile, the grain size of the MA10 alloy increases from ∼5.7 to ∼7.3 μm after T4 treatment at 450 °C from 10 to 60 min (Figure S6 in Supplemental Material), which is much larger than that of the ZMXA2110 alloy (from ∼3.2 to ∼4.5 μm, Figure a and Figure a). As a result, it is concluded that the core–shell structure can effectively suppress the coarsening of β-Mn particles and stabilize fine grain structures in the ZMXA2110 alloy.
Figure 4. HAADF-STEM and APT analyses of the ZMXA2110 alloy sheet after T4 treatment at 450 °C for 10 min: (a) The atomic resolution HAADF-STEM image and corresponding EDS (b–e) mapping and (f) line scanning results; (g) APT maps of Al, Mn, Zn and Ca; (h) The 1D compositional profile along yellow line in (g).
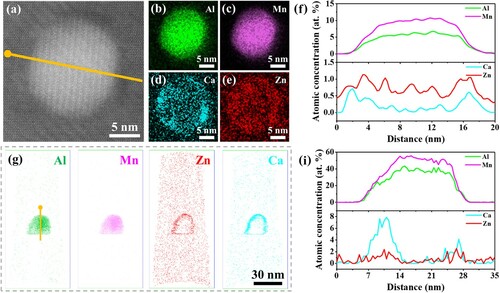
3.5. Origin of the significant BH response
The T4-treated ZMXA2110 alloy sample (450 °C/10 min) is selected to further expound the underlying mechanism of the appreciable BH response. The quasi-in-situ EBSD maps of the sample after T4 treatment for 10 min and subsequent 2% tensile-stretching are shown in Figure a and b, respectively. During tensile stretching, only a small number of tensile twins and
compression twins are observed (see black and white arrows in Figure b), indicating that the dislocation slip should be the dominant deformation mechanism. Further slip trace analysis (Figure c) shows that the 2% tensile-stretching is dominated by the basal <a> slip. After BH treatment, abundant precipitates lying on the basal planes are observed in the microstructure, as shown in Figure d. The continuous streaks in the SAED (Figure e) and characteristics of the precipitates, i.e. atomic column distance of ∼0.47 nm and monoatomic layer structure (Figure f, similarly reported in Ref. [Citation30]), imply that these precipitates are Guinier Preston (G.P.) zones. Assisted by APT analyses, G.P. zones are detected to mainly contain Ca, Zn and Al (Figure i). Besides, G.P. zones have a small diameter of ∼3.6 nm and high number density of ∼9.6×1023 m−3 (Figure g and h). The Zn-Ca and Al-Ca G.P. zones with similar size and number density have also been reported in Mg-Al-Ca-Mn [Citation31,Citation32] and Mg-Zn-Ca-Zr alloys [Citation6], which are responsible for the significant age-hardenability from 40 to 90 MPa. Therefore, we could expect that dispersed G.P. zones play an important role in strengthening the ZMXA2110 alloy sheet after BH treatment. In addition, the yield point phenomenon of the BH sample (Figure a) suggests that solutes may segregate at the residual dislocations during the BH process and hence participate in strengthening, which has been reported by Bian et al. [Citation9].
Figure 5. EBSD IPF maps of the ZMXA2110 alloy sheet after (a) T4 treatment at 450 °C for 10 min and (b) subsequent 2% tensile stretching (black and white arrows indicate tensile twins and
compression twins, respectively). (c) The corresponding forescatter electron image of the black dashed box showing slip traces. (d–i) TEM and APT analyses of the ZMXA2110 alloy sheet after BH treatment: (d) HRTEM image, (e) the corresponding
SAED pattern and (f) high magnification HRTEM image; (g) APT maps of Zn, Ca and Al; (h) The APT map of Mg (dark blue atoms) and 1.0 at. % Ca iso-concentration surface; (i) The concentration proximity histogram of G.P. zones.
![Figure 5. EBSD IPF maps of the ZMXA2110 alloy sheet after (a) T4 treatment at 450 °C for 10 min and (b) subsequent 2% tensile stretching (black and white arrows indicate {101¯2} tensile twins and {101¯1} compression twins, respectively). (c) The corresponding forescatter electron image of the black dashed box showing slip traces. (d–i) TEM and APT analyses of the ZMXA2110 alloy sheet after BH treatment: (d) HRTEM image, (e) the corresponding [1¯100] SAED pattern and (f) high magnification HRTEM image; (g) APT maps of Zn, Ca and Al; (h) The APT map of Mg (dark blue atoms) and 1.0 at. % Ca iso-concentration surface; (i) The concentration proximity histogram of G.P. zones.](/cms/asset/9c27dbf0-ec2a-487f-b624-5ddfa5125662/tmrl_a_2106797_f0005_oc.jpg)
4. Conclusions
In summary, the ZMXA2110 alloy sheet owns extraordinary high-temperature grain stability, retaining a fine-grained structure with the size ≤3.4 μm under T4 treatment at 450 °C up to 30 min. Even though extending the T4 treatment time to 60 min, the grain size merely witnesses a slight increment to ∼4.5 μm. The grain stability is associated with co-segregation of Zn and Ca at GBs and the Zener pinning effect offered by a large number of thermally stable core–shell β-Mn particles in size of ∼15.0 nm. The shell is enriched with segregated Zn and Ca atoms, which is demonstrated to suppress the coarsening of β-Mn particles. Benefiting from the excellent grain stability, fine-grain strengthening and BH are achieved simultaneously. The alloy sheet exhibits high room-temperature formability (I.E. value ∼6.0 mm) in T4 condition (10 min) and high YS of ∼293 MPa after BH treatment. Our finding could shed some light on the development of dilute Mg alloy sheets with the excellent synergy of room-temperature formability and strength.
Supplemental Material
Download Zip (6.3 MB)Acknowledgement
Financial supports from The National Natural Science Foundation of China (Nos. 51625402, U19A2084, and 51801069) are greatly acknowledged. Partial financial support comes from The Science and Technology Development Program of Jilin Province (Nos. 20200201002JC and 20200401025GX).
Disclosure statement
No potential conflict of interest was reported by the author(s).
Additional information
Funding
References
- Chino Y, Huang X, Suzuki K, et al. Enhancement of stretch formability at room temperature by addition of Ca in Mg-Zn alloy. Mater Trans. 2010;51:818–821.
- Suh B-C, Shim M-S, Shin KS, et al. Current issues in magnesium sheet alloys: where do we go from here? Scr Mater. 2014;84-85:1–6.
- Bian MZ, Sasaki TT, Suh BC, et al. A heat-treatable Mg–Al–Ca–Mn–Zn sheet alloy with good room temperature formability. Scr Mater. 2017;138:151–155.
- Nakata T, Xu C, Kamado S. Improving tensile properties of a room-temperature formable and heat-treatable Mg–6Zn-0.2Ca (wt. %) alloy sheet via micro-alloying of Al and Mn. Mater Sci Eng A. 2020;772:138690.
- Joost WJ, Krajewski PE. Towards magnesium alloys for high-volume automotive applications. Scr Mater. 2017;128:107–112.
- Li ZH, Sasaki TT, Shiroyama T, et al. Simultaneous achievement of high thermal conductivity, high strength and formability in Mg-Zn-Ca-Zr sheet alloy. Materials Research Letters. 2020;8:335–340.
- Hua Z-M, Li M-X, Wang C, et al. Pre-strain mediated fast natural aging in a dilute Mg-Zn-Ca-Sn-Mn alloy. Scr Mater. 2021;200:113924.
- Bian M, Huang X, Chino Y. Substantial improvement in cold formability of concentrated Mg–Al–Zn–Ca alloy sheets by high temperature final rolling. Acta Mater. 2021;220:117328.
- Bian MZ, Sasaki TT, Nakata T, et al. Bake-hardenable Mg–Al–Zn–Mn–Ca sheet alloy processed by twin-roll casting. Acta Mater. 2018;158:278–288.
- Zhao L-Q, Wang C, Chen J-C, et al. Development of weak-textured and high-performance Mg–Zn–Ca alloy sheets based on Zn content optimization. J Alloys Compd. 2020;849:156640.
- Stanford N, Barnett MR. Solute strengthening of prismatic slip, basal slip and twinning in Mg and Mg–Zn binary alloys. Int J Plast. 2013;47:165–181.
- Pan H, Kang R, Li J, et al. Mechanistic investigation of a low-alloy Mg–Ca-based extrusion alloy with high strength–ductility synergy. Acta Mater. 2020;186:278–290.
- Kim B, Hong CH, Kim JC, et al. Factors affecting the grain refinement of extruded Mg–6Zn–0.5Zr alloy by Ca addition. Scr Mater. 2020;187:24–29.
- Pei R, Zou Y, Wei D, et al. Grain boundary co-segregation in magnesium alloys with multiple substitutional elements. Acta Mater. 2021;208:116749.
- Marquis EA, Seidman DN. Nanoscale structural evolution of Al3Sc precipitates in Al(Sc) alloys. Acta Mater. 2001;49:1909–1919.
- Komura S, Horita Z, Furukawa M, et al. An evaluation of the flow behavior during high strain rate superplasticity in an Al-Mg-Se alloy. Metall Mater Trans A-Phys Metall Mater Sci. 2001;32:707–716.
- Pereloma E, Timokhina I. Bake hardening of automotive steels. In: R Rana, SB Singh, editors. Automotive steels: Woodhead Publishing; 2017. p. 259–288.
- Trang TTT, Zhang JH, Kim JH, et al. Designing a magnesium alloy with high strength and high formability. Nat Commun. 2018;9:2522.
- Shi R, Miao J, Avey T, et al. A new magnesium sheet alloy with high tensile properties and room-temperature formability. Sci Rep. 2020;10:10044.
- Li ZH, Sasaki TT, Bian MZ, et al. Role of Zn on the room temperature formability and strength in Mg–Al–Ca–Mn sheet alloys. J Alloys Compd. 2020;847:156347.
- Jain V, Mishra RS, Verma R, et al. Superplasticity and microstructural stability in a Mg alloy processed by hot rolling and friction stir processing. Scr Mater. 2013;68:447–450.
- Huang X, Suzuki K, Chino Y. Static recrystallization and mechanical properties of Mg–4Y–3RE magnesium alloy sheet processed by differential speed rolling at 823K. Mater Sci Eng A. 2012;538:281–287.
- Miao Q, Hu L, Wang X, et al. Grain growth kinetics of a fine-grained AZ31 magnesium alloy produced by hot rolling. J Alloys Compd. 2010;493:87–90.
- Zeng ZR, Zhu YM, Xu SW, et al. Texture evolution during static recrystallization of cold-rolled magnesium alloys. Acta Mater. 2016;105:479–494.
- Guan D, Liu X, Gao J, et al. Exploring the mechanism of “rare earth” texture evolution in a lean Mg-Zn-Ca alloy. Sci Rep. 2019;9:7152.
- Gao J, Jiang S, Zhang H, et al. Facile route to bulk ultrafine-grain steels for high strength and ductility. Nature. 2021;590:262–267.
- Humphreys J, Rohrer GS, Rollett A. Recrystallization and related annealing phenomena third ed. Oxford: Elsevier; 2017.
- Li JH, Barrirero J, Sha G, et al. Precipitation hardening of an Mg–5Zn–2Gd–0.4Zr (wt. %) alloy. Acta Mater. 2016;108:207–218.
- Gao YH, Yang C, Zhang JY, et al. Stabilizing nanoprecipitates in Al-Cu alloys for creep resistance at 300°C. Mater Res Lett. 2018;7:18–25.
- Oh-ishi K, Watanabe R, Mendis CL, et al. Age-hardening response of Mg–0.3at.%Ca alloys with different Zn contents. Mater Sci Eng A. 2009;526:177–184.
- Nakata T, Xu C, Ajima R, et al. Strong and ductile age-hardening Mg-Al-Ca-Mn alloy that can be extruded as fast as aluminum alloys. Acta Mater. 2017;130:261–270.
- Bhattacharyya JJ, Sasaki TT, Nakata T, et al. Determining the strength of GP zones in Mg alloy AXM10304, both parallel and perpendicular to the zone. Acta Mater. 2019;171:231–239.