Abstract
We investigate the tensile deformation behavior and mechanism of nickel-based superalloy CM247LC, which has been subjected to various ageing treatment schemes, but possesses almost the same γ′ particle size, at 600°C. It is found that the transition in the deformation mode from particle shearing plus microtwinning to particle shearing accounts for the decrease in the work-hardening rate and tensile strength with ageing temperature. Our study provides a new strategy to design the heat treatment schedule to achieve a good compromise between the strength and plasticity for superalloys by tunning the operative deformation and fracture mechanisms.
IMPACT STATEMENT
The work provides new insights into understanding the influence of ageing heat treatment or microstructural features on the mechanical properties and corresponding deformation and fracture mechanisms of precipitate-hardened superalloys.
1. Introduction
As the key high-temperature structural materials, directionally solidified (DS)/single-crystal (SC) nickel-based superalloys, hardened by a high volume fraction of finely dispersed γ′ precipitates (Ni3(Al, Ti, Ta), L12-ordered structure), have a wide application in industrial gas turbines ascribed to their superior mechanical properties and corrosion resistance at high temperatures [Citation1–5]. Whereas, during the casting process, a coarse, less homogeneous precipitation of γ′ precipitates as well as large clusters of γ/γ′ eutectics usually formed, thereby conferring the relatively lower strength to these alloys [Citation1,Citation2,Citation5]. Thus, in order to exploit the maximum potential of these alloys to adopt the increasingly severe service conditions, establishing the optimum relationship between the heat treatment scheme, microstructural features and mechanical properties becomes an indispensable task for a given superalloy.
Great efforts have been paid to clarify the impact of the ageing treatment on the microstructures and mechanical properties of [001]-orientated SC nickel-based superalloys [Citation6–15]. These studies disclosed that the heat treatments, which gave rise to a homogeneous distribution of cuboidal γ′ particles of 300–500 nm, imparted the optimum high-temperature mechanical properties to these alloys with the absolute value of the γ/γ′ lattice misfit, 0.1–0.5%, since the microstructure facilitated the glide of perfect dislocations in the matrix channels and then contributed to the rapid and uniform strain hardening or the formation of regular perfect γ/γ′ lamellar in the initial stage of creep [Citation6,Citation8,Citation12–15]. Whereas, it is worth mentioning that, apart from the particle size, other microstructural features also vary significantly in accompany with changing the heat treatments. For this reason, it is difficult to ascertain unambiguously which factor dictates the mechanical response. On the other hand, although considerable experimental results are available, systematic research of the effect of the ageing temperature on the tensile properties and deformation mechanisms of nickel-based superalloys has hitherto been relatively scarce. It was therefore decided to investigate the tensile behavior and corresponding deformation mode of the DS nickel-based superalloy CM247LC which has suffered various ageing treatments, but possesses almost the same γ′ particle size.
2. Materials and methods
The superalloy CM247LC studied in this work has the following chemical composition (wt.%): 9.4W, 0.5Mo, 3.2Ta, 0.015B, 9.2Co, 5.6Al, 1.4Hf, 0.07C, 8.0Cr, 0.7Ti, 0.017Zr with balanced Ni. Master ingots of the alloy were remelted and then directionally solidified into slabs of dimensions 21 cm by 6 cm by 2.4 cm with columnar grains along the <001 > direction at a constant withdrawal rate of 42 mm h-1 using an ALD Vacuum Technologies furnace. Typical dendritic microstructures are visible in the as-cast specimens (see Supplementary Figure S-1(a) and (b)). Whereas, after a three-step high-temperature solution heat treatment, 1232°C/2 h + 1243°C/2 h + 1252°C/6 h/air cooling (AC), the γ/γ′ eutectic pools are rarely observed, and the γ′ precipitates display a unimodal distribution (see Supplementary Figure S1(c,d)). Subsequently, these bars are subjected to four different heat treatments, which are named as HT1–HT4, respectively (see Table ).
Table 1. Heat treatment schedules investigated in this study for the experimental alloy CM247LC.
Rods were sectioned from the slabs along the direction parallel to the growth direction using a wire-cut electric discharge machine. After the heat treatments, threaded tensile specimens, 4 mm in diameter and 20 mm in gauge length were prepared. Tensile tests were carried out in air and at an engineering strain rate of 3.0 × 10−4 s-1 on a Zwick Z1200 testing machine at 600°C. At least three specimens were tested for each ageing condition. Most of these specimens were stretched to fracture, but a few tests were interrupted at around 1.0% plastic strain to unveil the deformation mode at the initial stage of plastic deformation using transmission electron microscope (TEM). These specimens were forced air cooled from the test temperature to room temperature to preserve the dislocation structures.
Thin slices were sectioned from the middle regions of the slightly deformed samples at around 25° with respect to the loading axis. Whereas, in regard to the fracture specimens, slices were cut from the gauge section at a minimum distance of 5 mm away from the fracture surface. After mechanically thinned to around 70 μm, discs were electrolytically polished in an electrolyte of 440 ml ethanol, 50 ml perchloric acid and 10 ml ethylene glycol at around −30∼−25°C and 35∼40 V. The thin foils were examined in a JEM-2100Plus TEM equipped with a double-tilt goniometer operated at 200 kV.
3. Results and discussion
Figure (a–d) shows the typical γ/γ′ microstructures in CM247LC after the heat treatments HT1–HT4. Evidently, the γ′ precipitates show a unimodal distribution of γ′ precipitates in the alloy subjected to HT2 and HT3, whereas a bimodal distribution of γ′ precipitates is obtained for the other two heat treatments. The formation of the tertiary γ′ precipitates in the latter two heat treatments is associated with the supersaturation of the γ′-forming elements in the matrix [Citation16–18]. After thermal ageing at 1080 °C for 4 h, there still exists a large supersaturation of the γ′-forming elements in the matrix. Thus, tertiary γ′ particles precipitate within the matrix channels during air cooling or low-temperature thermal ageing. Using a line intersect method, the average sizes of coarse γ′ precipitates in these specimens are determined to 256 ± 72, 317 ± 62, 283 ± 62 and 303 ± 72 nm, respectively (see Supplementary Figures S-2 and S-3). The equilibrium phase diagram of CM247LC is calculated using the software Thermo-Calc, together with TCNI 11 database. We found that the equilibrium volume fractions of γ′ precipitates in CM247LC are 0.437, 0.584, 0.640 and 0.687 at 1080, 980, 930 and 870°C, respectively. On the other hand, the carbides in these specimens were also observed. As shown in Supplementary Figures S-4-S-6, no significant differences can be found in the microstructural features of these carbides, and the volume fractions of the carbides in all these specimens are around 1.0%. Thus, the carbides would not have a prominent influence on the tensile deformation behavior and mechanisms and are therefore not discussed in detail in the following sections.
Figure 1. The γ/γ′ microstructures (a–d) in CM247LC and corresponding tensile properties at 600°C (e,) after various heat treatments; (a) HT1; (b) HT2; (c) HT3; (d) HT4; (e) engineering stress-strain curves; (f) work-hardening rate plotted vs true strain.
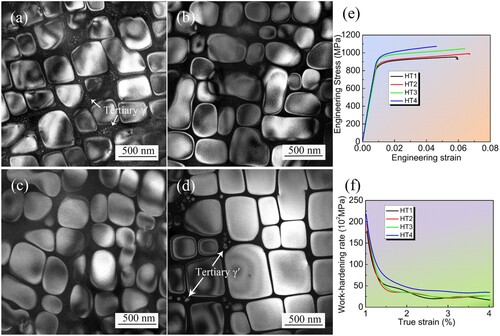
Figure (e) displays the engineering stress–strain curves of CM247LC with various heat treatments at 600°C. Evidently, the alloy subjected to HT3 has the largest yield strength and the second best plasticity. With respect to HT4, the yield strength of the alloy is comparable to that of the specimen with HT3, but the elongation to fracture is the minimum among the four heat treatments. Whereas, for HT1 and HT2, the intermediate values are obtained in terms of strength and plasticity. These results are in strong contrast to those reported in Refs. [Citation14,Citation19–21], which showed that the alloy owning a bimodal distribution of γ′ precipitates exhibited a better tensile plasticity at low and intermediate temperatures. These differences are ascribed to the operation of different deformation mechanisms in the experimental alloy, and subsequently this will be discussed detailly. It is also apparent from this figure that the tensile stress of the specimen subjected to HT4 increases more rapidly with proceeding plastic deformation, and the curves display a slightly sharper bend than those in the other three specimens, so that the work-hardening rates for these specimens are in order: HT1 < HT2 < HT3 < HT4, up to strain of around 1.5%. Beyond this strain, the work-hardening rates of the former three samples approach to each other, although the work-hardening rate of the specimen subjected to HT4 is still larger, as illustrated in Figure (f).
Figure (a) and (b) show the typical dislocation structures in the experimental alloy after HT1 and HT2 as well as around 1.0% plastic strain. Although the initial heat treatments are different, the same predominant deformation mode operates. Numerous dislocation pairs, which are separated by anti-phase boundary (APB), are produced, suggesting that APB shearing controls the plastic deformation of the experimental alloy with HT1 and HT2. This result is similar to those found in other nickel-based superalloys after plastic deformation at low temperatures [Citation22–27], but is different from that found in the same alloy with HT4 after compressive deformation at 600°C [Citation24], which showed that particle shearing was frequently achieved by the <112>111 slip systems. Generally, tensile/compressive plastic deformation of nickel-based superalloys was inhomogeneous at low temperatures [Citation7,Citation26,Citation28,Citation29], and the deformation mechanisms in nickel-based superalloys could evolve with proceeding plastic deformation [Citation30–33]. Whereas, as shown in Figure (c) and (d), the main deformation mode does not change obviously with plastic strain, and the main deformation patterns in the fracture specimens are still constricted a/2 < 011 > dislocation pairs coupled by APB, hence precluding the above contention.
Figure 2. Deformed patterns in CM247LC after HT1 and HT2 as well as around 1.0% plastic strain and fracture at 600°C: (a,b) HT1; (c,d) HT2; (a) and (c) 1.0% plastic strain; (b) and (d) fracture.
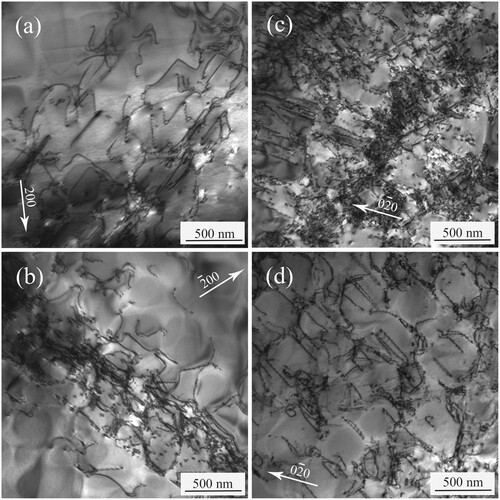
It is argued that the operative deformation mechanisms in nickel-based superalloys were sensitive to the sign of the applied stress, and shearing of γ′ precipitates by partial dislocations causing the production of stacking faults and microtwins (MTs) was easier to occur during compressive deformation [Citation33–35]. Then, after 1.0% plastic strain and fracture, the deformation microstructures in the specimens with HT4 are examined. As illustrated in Figure , it is interesting to note that APB-coupled dislocation pairs, isolated superlattice stacking faults (SSFs), extended stacking faults (ESFs) and MTs are frequently observed in the slightly deformed and fracture specimens, in accordance with the results found in CM247LC after compressive deformation [Citation24]. These results suggest that for the experimental alloy, the operative deformation mechanisms might not be associated with the sign of the applied stress, but be sensitive to the ageing temperature. With respect to the formation mechanisms of these planar faults, these have been discussed detailly in Refs. [Citation24,Citation36], and will be described only briefly herein. That is, the Shockley partial dislocations, which were dissociated from single matrix a/2 < 110 > dislocations, glided on single as well as neighboring 111 planes, finally resulting in the formation of these planar faults.
On the other hand, we also investigate the microstructures in the experimental alloy subjected to HT3 as well as tensile deformation. After around 1.0% plastic strain and fracture, the three typical deformation patterns mentioned above are also visible, analogous to those found in the experimental alloy subjected to HT4. However, comparing with the deformation microstructures in the experimental alloy suffered to HT4 (see Figures and ), one can get that the densities of stacking faults and MTs are much lower, although the experimental alloy with HT3 has a larger fracture strain and therefore has suffered a severer plastic deformation. Someone might argue that these planar faults have been created in the experimental alloy after HT3 and HT4. However, as shown in Figure and Figure S-7 in the Supplementary Materials, these planar faults are invisible in these specimens, hence precluding the statement. Meanwhile, these results further demonstrate that the operative deformation mechanisms in CM247LC can be tailored by adjusting the ageing temperature. On the other hand, given these results together with those stated above, one can also obtain that the present results are in strong contrast to those reported for other SC nickel-based superalloys during plastic deformation at intermediate temperatures in Refs. [Citation10,Citation37,Citation38], where reported that the cooperative precipitate shearing involved the formation of stacking faults and MTs was easier to occur in the specimens with the smaller irregularly shaped γ′ particles.
Figure 3. Deformed patterns in CM247LC after HT4 as well as around 1.0% plastic strain and fracture at 600°C: (a–c) 1.0% plastic strain; (d–f) fracture; (a) and (d) dislocation pairs and isolated SSFs; (b) and (e) isolated SSFs and ESFs; (c) and (f) MTs, the arrowheads indicate the spots of MTs.
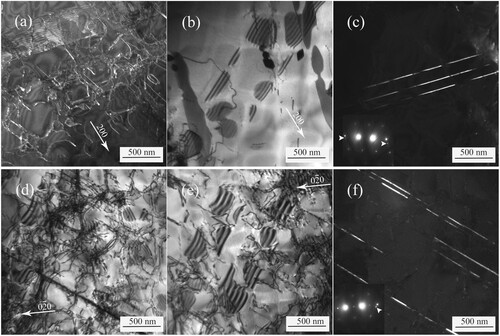
Figure 4. Deformed patterns in CM247LC after HT3 as well as around 1.0% plastic strain and fracture at 600°C: (a–c) 1.0% plastic strain; (d–f) fracture; (a) and (d) dislocation pairs; (b) and (e) isolated SSFs; (c) and (f) MTs, the arrowheads indicate the spots of MTs.
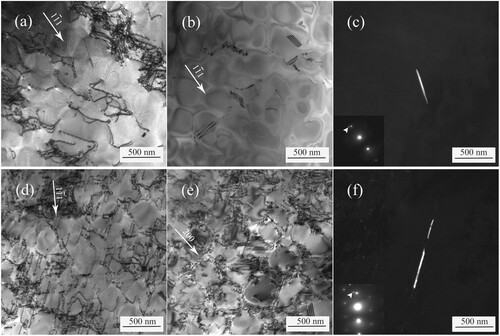
A question has arisen as to why the deformation mechanism in CM247LC changes with the ageing temperature. It is well-known that whether particle shearing is accomplished by APB-coupled dislocation pairs or partial dislocations is associated with the size and distribution of γ′ precipitates [Citation38–40]. For example, Sinharoy et al. [Citation38] reported that as the precipitate size increased, the dominant deformation mechanism changed from stacking fault shearing to APB shearing in the nickel-based superalloy KM4, and the fine, tertiary γ′ precipitates located between the large ones could facilitate the formation of SFs. This proposal has some consent in the community [Citation14,Citation41–44]. Whereas, as shown in Figure , SFs and MTs are invisible in the specimens subjected to HT1 and tensile deformation, and the coarse γ′ precipitates in the specimens with HT2–HT4 are approached to each other. This suggests that the γ′ particle size and precipitation of fine tertiary γ′ particles do not play a vital role in determining the initiation of the shearing process for CM247LC. It is also widely reported that which shearing process dominated the plastic deformation was intimately connected with the APB energy (APBE) and intrinsic stacking fault energy (ISFE) of the γ′ phase, and a larger ratio between the APBE and the ISFE promoted the activation of stacking fault shearing and microtwinning [Citation45–47]. So, variations of the APBE with the ageing temperature are calculated using the software Thermo-Calc. It reveals that the APBE decreases with raising the ageing temperature (see Supplementary Figure S-8(a)). At 870°C, the APBE of the γ′ phase is 0.219 J/m2. Whereas, this value is only about 0.179 J/m2 at 1080°C. With respect to the changes in the ISFE of the γ′ phase with temperature, it is unclear up to now. Whereas, the ISFE of the γ′ phase is dependent on its chemical compositions. So, changes in the chemical composition of the γ′ phase with temperature are calculated (see Supplementary Figure S-8(c)). It is found that the content of Co element increases with decreasing temperature, whereas the other elements remain almost unchanged with temperature, thus resulting in reducing the ISFE according to previous results [Citation18,Citation48–51]. On the other hand, the chemical compositions of the γ phase at various temperatures were also obtained (see Supplementary Figure S-8(b)). We found the amounts of Cr and Co elements also increase with decreasing temperature. This would cause a decrease in the stacking fault energy and therefore trigger the formation of SFs and MTs [Citation18,Citation47,Citation49,Citation51]. Thus, it can be concluded that the increase in the stacking fault energies of the γ and γ′ phases and the decrease in the APBE with increasing the ageing temperature mainly account for the transition in the deformation mechanism with temperature. These results also provide new explanations for variations in the tensile/compressive deformation mechanisms with the tested temperature. It is also argued that the operation of deformation mechanisms in nickel-based superalloys were intimately associated with the γ/γ′ lattice misfit [Citation30,Citation48]. Whereas, previous research revealed that the γ/γ′ lattice misfit of CM247LC fell into the range of 0.04–0.06% between 600°C and 1000°C [Citation52]. Thus, it is believed that the changes in the lattice misfit with temperature are not one of the main factors causing the transition in the deformation modes for the experimental alloy.
As shown in Figure (e), the experimental alloy subjected to HT4 has the second largest yield strength, but the largest ultimate tensile strength, although the γ′ volume fraction is the largest. The phenomenon can be rationalized in terms of the operative deformation mechanisms. Generally, as the initiation of stacking fault shearing and microtwinning needs a smaller shear stress as compared to APB shearing, the frequent operation of stacking fault shearing and microtwinning would decrease the yield strength at the very beginning stage of plastic deformation [Citation53–55]. Whereas, as the plastic deformation proceeds, multiple slip operates simultaneously (see Figures ). So, SSFs and MTs created after slight plastic deformation can act as obstacles to the glide of moving dislocations from other slip systems, thereby resulting in a higher work-hardening rate as compared to that due to interactions between dislocations on different slip systems [Citation40,Citation56,Citation57]. Consequently, the fastest increase in the flow stress with increasing plastic strain can be expected for HT4 with proceeding plastic deformation. With respect to the tensile plasticity, the minimum elongation to fracture for the experimental alloy after HT4 can also be understood in light of the operative deformation mechanisms. As shown in Figure , stacking fault shearing and microtwinning occur frequently in the experimental alloy with HT4. The extended characteristic of the fault configurations, which prevents dislocations from leaving their slip planes by cross-slip or climb, easily promotes the planar slip and then leads to heterogeneous deformation [Citation10,Citation58]. If the localized plastic deformation operates frequently, the glide plane decohesion would operate frequently (see Supplementary Figure S-9), finally causing the premature fracture at a low stress level [Citation10,Citation27,Citation59,Citation60]. Thus, only limited plastic strain can only be obtained.
4. Conclusion
In summary, this study explicitly discloses that the tensile properties and deformation mechanism of the nickel-based superalloy CM247LC at 600°C can be tailored by adjusting the ageing temperature, but keeping the γ′ precipitate size almost the same. As the ageing temperature increases, the predominant deformation mode changes from APB shearing plus stacking faulting shearing and microtwinning to APB shearing due to the decrease in the APBE of the γ′ phase as well as the increases in the SFE of the γ and γ′ phases with temperature. The transition in the deformation mechanism accounts for the decrease in the work-hardening rate and increase in the tensile plasticity with ageing temperature. The relatively low yield strength and high ultimate tensile strength arise from the activation of <112>111 slip systems.
Supplemental Material
Download ()Disclosure statement
No potential conflict of interest was reported by the author(s).
Additional information
Funding
Reference
- Sims CT, Stoloff NS, Hagel WC. Superalloys II. New York: John Wiley & Sons; 1987.
- Fuchs GE. Solution heat treatment response of a third generation single crystal Ni-base superalloy. Mater Sci Eng A. 2001;300:52–60. doi:10.1016/S0921-5093(00)01776-7
- Li X, Liu Y, Zhao Y, et al. Oxygen changes crack modes of Ni-based single crystal superalloy. Mater Res Letts. 2021;9:531–539. doi:10.1080/21663831.2021.1993367
- Ru Y, Hu B, Zhao W, et al. Topologically inverse microstructure in single-crystal superalloys: microstructural stability and properties at ultrahigh temperature. Mater Res Letts. 2021;9:497–506. doi:10.1080/21663831.2021.1982785
- Cailletaud G, Cormier J, Eggeler G, et al. Nickel base single crystals across length scales. Amsterdam: Elsevier; 2022.
- Khan T, Caron P. Effect of processing conditions and heat treatments on mechanical properties of single-crystal superalloy CMSX-2. Mater Sci Technol. 1986;2:486–492. doi:10.1179/mst.1986.2.5.486
- Hopgood AA, Martin JW. The effect of aging on the yield stress of a single-crystal superalloy. Mater Sci Eng. 1987;91:105–110. doi:10.1016/0025-5416(87)90288-6
- Nathal MV. Effect of initial gamma prime size on the elevated temperature creep properties of single crystal nickel base superalloys. Metall Trans A. 1987;18:1961–1970. doi:10.1007/BF02647026
- Caron P, Henderson PJ, Khan T, et al. On the effects of heat treatments on the creep behaviour of a single crystal superalloy. Scripta Metall. 1986;20:875–880. doi:10.1016/0036-9748(86)90458-8
- Caron P, Khan T. Effect of heat treatments on the anisotropic creep behaviour and deformation modes in a nickel-based single crystal superalloy. In: PO Kettunen, TK Leposto, editors. Proceedings of the 8th international conference on the strength of metals and alloys. Tampere: Pergamon; 1989. p. 893–898.
- Kim IS, Choi BG, Seo SM, et al. Influence of heat treatment on microstructure and tensile properties of conventionally cast and directionally solidified superalloy CM247LC. Mater Letts. 2008;62:1110–1113. doi:10.1016/j.matlet.2007.07.058
- Sun N, Zhang L, Li Z, et al. Effect of heat-treatment on microstructure and high-temperature deformation behavior of a low rhenium-containing single crystal nickel-based superalloy. Mater Sci Eng A. 2014;606:417–425. doi:10.1016/j.msea.2014.03.093
- Sun N, Zhang L, Li Z, et al. The effect of microstructure on the creep behavior of a low rhenium-containing single crystal nickel-based superalloy. Mater Sci Eng A. 2014;606:175–186. doi:10.1016/j.msea.2014.03.074
- Rame J, Eyidi D, Joulain A, et al. Creep and tensile behavior of a nickel-based single crystal superalloy with a bimodal γ′ precipitation. Metall Mater Trans A. 2023;54:1496–1508. doi:10.1007/s11661-023-07022-y
- Xu J, Zhao X, Li W, et al. Aging process design based on the morphological evolution of γ′ precipitates in a 4th generation nickel-based single crystal superalloy. J Mater Sci Technol. 2023;147:176–188. doi:10.1016/j.jmst.2022.10.072
- Durand-Charre M. The microstructure of superalloys. Amsterdam: Gordon and Breach Science; 1997.
- Jackson MP, Reed RC. Heat treatment of UDIMET 720Li: the effect of microstructure on properties. Mater Sci Eng A. 1999;259:85–97. doi:10.1016/S0921-5093(98)00867-3
- Tian C, Han G, Cui C, et al. Effects of Co content on tensile properties and deformation behaviors of Ni-based disk superalloys at different temperatures. Mater Des. 2015;88:123–131. doi:10.1016/j.matdes.2015.08.114
- Collins DM, Stone HJ. A modelling approach to yield strength optimisation in a nickel-base superalloy. Int J Plast. 2014;54:96–112. doi:10.1016/j.ijplas.2013.08.009
- Preuss M, JQd F, Grant BMB, et al. The effect of γ’ particle size on the deformation mechanism in an advanced polycrystalline nickel-base superalloy. In: in Reed RC, Green KA, Caron P, Gabb TP, Fahrmann MG, editors. Proceeding of the 11th International Symposium on Superalloys. Champion, PA: AIME; 2008 Sep 14–18. p. 405–414.
- Sun B, Zhang T, Song L, et al. Correlation between secondary γ′ and high-temperature tensile behavior of a powder metallurgy nickel-based superalloy EP962NP. Mater Sci Eng A. 2023;866:144687. doi:10.1016/j.msea.2023.144687
- Feller-Kniepmeier M, Link T, Poschmann I, et al. Temperature dependence of deformation mechanisms in a single crystal nickel-base alloy with high volume fraction of γ′ phase. Acta Mater. 1996;44:2397–2407. doi:10.1016/1359-6454(95)00354-1
- Rai RK, Sahu JK, Jena PSM, et al. Micromechanism of high-temperature tensile deformation behavior of a directionally solidified nickel base superalloy. J Mater Eng Perform. 2018;27:659–665. doi:10.1007/s11665-018-3176-2
- Zhang P, Yuan Y, Gao ZH, et al. Strain-rate insensitive yield strength and deformation mechanisms of Ni-base superalloy CM247LC at 600 °C. J Alloys Compds. 2021;862:158478. doi:10.1016/j.jallcom.2020.158478
- Lv P, Liu L, Zhao G, et al. Temperature effects on tensile behaviors and relevant deformation mechanisms of a low-cost nickel-based single crystal superalloy containing 1.5% Re. J Alloys Compds. 2022;926:166819. doi:10.1016/j.jallcom.2022.166819
- Zhang P, Ma L, Yang G, et al. Extraordinary plastic behaviour of the γ′ precipitate in a directionally solidified nickel-based superalloy. Phil Mag Letts. 2016;96:19–26. doi:10.1080/09500839.2015.1134832
- Bettge D, Österle W, Ziebs J. Temperature dependence of yield strength and elongation of the nickel-base superalloy IN 738 LC and the corresponding microstructural evolution. Inter J Mater Res. 1995;86:190–197. doi:10.1515/ijmr-1995-860309
- Westbrooke EF, Forero LE, Ebrahimi F. Slip analysis in a Ni-base superalloy. Acta Mater. 2005;53:2137–2147. doi:10.1016/j.actamat.2005.01.025
- Grant BMB, Francis EM, Quinta da Fonseca J, et al. Deformation behaviour of an advanced nickel-based superalloy studied by neutron diffraction and electron microscopy. Acta Mater. 2012;60:6829–6841. doi:10.1016/j.actamat.2012.09.005
- Link T, Feller-Kniepmeier M. Shear mechanisms of the γ′ phase in single-crystal superalloys and their relation to creep. Metall Trans A. 1992;23:99–105. doi:10.1007/BF02660857
- Tang Y, Huang M, Xiong J, et al. Evolution of superdislocation structures during tertiary creep of a nickel-based single-crystal superalloy at high temperature and low stress. Acta Mater. 2017;126:336–345. doi:10.1016/j.actamat.2016.12.072
- Zhang P, Yuan Y, Gao Z, et al. Plastic deformation mechanisms in a new Ni-base single crystal superalloy at room temperature. J Micro. 2017;268:186–192. doi:10.1111/jmi.12597
- Zhang P, Li J, Yuan Y, et al. Correlation the<112>111 slip with high-temperature tension/compression asymmetry in the single-crystal nickel-based superalloy PWA1483. Mater Res Letts. 2023;11:399–406. doi:10.1080/21663831.2023.2166432
- Yamashita M, Kakehi K. Tension/compression asymmetry in yield and creep strengths of Ni-based superalloy with a high amount of tantalum. Scripta Mater. 2006;55:139–142. doi:10.1016/j.scriptamat.2006.03.048
- Tsuno N, Shimabayashi S, Kakehi K, et al. Tension/compression asymmetry in yield and creep strengths of Ni-based superalloys. In: in Reed RC, Green KA, Caron P, Gabb TP, Fahrmann MG, editors. Proceeding of the 11th international symposium on superalloys. Champion, PA: AIME; 2008 Sep 14–18. p. 433–442.
- Zhang P, Yuan Y, Shi XB, et al. Extraordinary deformation modes in Ni-base superalloy CM247LC at room temperature. Metall Mater Trans. 2021;52:3699–3705. doi:10.1007/s11661-021-06370-x
- Caron P, Khan T, Veyssière P. On precipitate shearing by superlattice stacking faults in superalloys. Phil Mag A. 1988;57:859–875. doi:10.1080/01418618808204522
- Sinharoy S, Virro-Nic P, Milligan WW. Deformation and strength behavior of two nickel-base turbine disk alloys at 650 °C. Metall Mater Trans A. 2001;32:2021–2032. doi:10.1007/s11661-001-0014-0
- Viswanathan GB, Sarosi PM, Henry MF, et al. Investigation of creep deformation mechanisms at intermediate temperatures in René 88 DT. Acta Mater. 2005;53:3041–3057. doi:10.1016/j.actamat.2005.03.017
- Zhang P, Yuan Y, Li B, et al. Tensile deformation behavior of a new Ni-base superalloy at room temperature. Mater Sci Eng A. 2016;655:152–159. doi:10.1016/j.msea.2015.12.089
- Décamps B, Raujol S, Coujou A, et al. On the shearing mechanism of γ′ precipitates by a single (a/6) <112> Shockley partial in Ni-based superalloys. Phil Mag. 2004;84:91–107. doi:10.1080/14786430310001621472
- Douin J, Pettinari-Sturmel F, Coujou A. Dissociated dislocations in confined plasticity. Acta Mater. 2007;55:6453–6458. doi:10.1016/j.actamat.2007.08.006
- Kovarik L, Unocic RR, Li J, et al. Microtwinning and other shearing mechanisms at intermediate temperatures in Ni-based superalloys. Pro Mater Sci. 2009;54:839–873. doi:10.1016/j.pmatsci.2009.03.010
- Unocic RR, Zhou N, Kovarik L, et al. Dislocation decorrelation and relationship to deformation microtwins during creep of a γ′ precipitate strengthened Ni-based superalloy. Acta Mater. 2011;59:7325–7339. doi:10.1016/j.actamat.2011.07.069
- Suzuki K, Ichihara M, Takeuchi S. Dissociated structure of superlattice dislocations in Ni3Ga with the L12 structure. Acta Metall. 1979;27:193–200. doi:10.1016/0001-6160(79)90096-8
- Milligan WW, Antolovich SD. The mechanisms and temperature dependence of superlattice stacking fault formation in the single-crystal superalloy PWA 1480. Metall Trans. A. 1991;22:2309–2318. doi:10.1007/BF02664997
- Zhang P, Yuan Y, Li J, et al. Microtwinning in single-crystal nickel-based superalloys during compressive deformation at 1000°C. Metall Mater Trans A. 2023;54:1484–1495. doi:10.1007/s11661-022-06944-3
- Zhang YH, Chen QZ, Knowles DM. Mechanism of dislocation shearing of gamma in fine precipitate strengthened superalloy. Mater Sci Technol. 2001;17:1551–1555. doi:10.1179/026708301101509818
- Cui CY, Gu YF, Yuan Y, et al. Dynamic strain aging in a new Ni–Co base superalloy. Scripta Mater. 2011;64:502–505. doi:10.1016/j.scriptamat.2010.11.025
- Crudden DJ, Mottura A, Warnken N, et al. Modelling of the influence of alloy composition on flow stress in high-strength nickel-based superalloys. Acta Mater. 2014;75:356–370. doi:10.1016/j.actamat.2014.04.075
- Dodaran M, Ettefagh AH, Guo SM, et al. Effect of alloying elements on the γ’ antiphase boundary energy in Ni-base superalloys. Intermetallics. 2020;117:106670. doi:10.1016/j.intermet.2019.106670
- Chang KM, Srivastava SK, Bain DUF, et al. Advanced technology for superalloy affordability. Warrendale: TMS; 2000.
- Sass V, Glatzel U, Feller-Kniepmeier M. Anisotropic creep properties of the nickel-base superalloy CMSX-4. Acta Mater. 1996;44:1967–1977. doi:10.1016/1359-6454(95)00315-0
- Barba D, Egan A, Gong Y, et al. Rationalisation of the micromechanisms behind the high-temperature strength limit in single-crystal nickel-based superalloys. In: Tin S, Hardy M, Clews J, Cormier J, Feng Q, Marcin J, O'Brien C, Suzuki A, editors. Proceedings of the 14th international symposium on superalloys. Cham: Spinger; 2021 Sep 13–16. p. 260–272.
- Zhang P, Yuan Y, Gao ZH, et al. Microtwinning in the nickel-based superalloy CM247LC during compression tests. Phil Maga. 2022;102:2235–2255. doi:10.1080/14786435.2022.2108155
- Lenz M, Eggeler YM, Müller J, et al. Tension/compression asymmetry of a creep deformed single crystal Co-base superalloy. Acta Mater. 2019;166:597–610. doi:10.1016/j.actamat.2018.12.053
- Pandey P, Heczko M, Khatavkar N, et al. On the faulting and twinning mediated strengthening and plasticity in a γ′ strengthened CoNi-based superalloy at room temperature. Acta Mater. 2023;252:118928. doi:10.1016/j.actamat.2023.118928
- Kear BH. The influence of ordering on the engineering properties of two phase alloys part I: mechanical mroperties of γ’ precipitation hardened nickel-base superalloys. In: H Warlimont, editor. Order-Disorder transformations in alloys. New York: Springer-Verlag; 1974. p. 440–474.
- Duan P, Zhang P, Li J, et al. Intermediate temperature brittleness in a directionally solidified nickel-based superalloy M4706. Mater Sci Eng A. 2019;759:530–536. doi:10.1016/j.msea.2019.05.037
- Jensen RR, Tien JK. Temperature and strain rate dependence of stress-strain behavior in a nickel-base superalloy. Metall Trans A. 1985;16:1049–1068. doi:10.1007/BF02811675