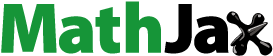
Abstract
To increase the productivity in machining industries demand for better surface finish and accuracy has been increasing rapidly in recent years. Therefore, this paper focus on an effective approach for the optimization of process parameters in Minimum Quantity Lubrication (MQL) turning of AISI 4340 with nano fluid by using Grey Relational Analysis (GRA). Sixty experimental trials based on full factorial design matrix were carried on CNC turning lathe machine to optimize best level. Analysis of experimental results for response variable such as surface roughness and cutting force was performed using Grey Relational Grade (GRG). From GRA the optimal conditions are obtained as cutting speed (75 m/min), Feed (0.04 mm/rev), Depth of cut (0.5 mm) and Tool nose radius (0.8 mm) for optimal response variable surface roughness (1.26 μm) and cutting force (7.69 kgf). The Signal to Noise ratio plot for GRA shows similar optimum condition therefore the results obtained from ANOVA are closely matching to the results of GRA. Improvement in GRG is near about 4.32%. By analysing the GRG, it is observed that the cutting performance in MQL turning of AISI 4340 under MQL mode can be improved.
Public Interest Statement
Industries are looking for ways to reduce the amount of lubricants in metal removing operations due to ecological, economical and environmental impact. During turning operation high temperature is produced such high temperature leads to several problems like large heat affected zone, high tool wear, change in hardness and microstructure of the work piece, burning and micro crack etc. To reduce above problem minimum quantity lubrication is convenient method in order to achieve good surface roughness and reduce tool wears. Also the advanced heat transfer and tribological properties of nano fluids can provide better cooling and lubricating in the MQL machining process, and make it production-feasible. With proper selection of the MQL system and the cutting parameters, it is possible for MQL machining with minimum cost and less quantity of coolant to obtain better conditions, in terms of lubricity, tool life, cutting temperature and surface finish and optimization of cutting parameters.
1. Introduction
Nowadays, modern machining industries are trying to achieve high quality, dimensional accuracy, surface finish, high production rate and cost saving along with reduced environmental impact (Narana Rao & Satyanarayana, Citation2011). Turning is the commonly carried out operation in the machining process. It can be carried out on different machines like conventional lathe, CNC machine and special purpose lathe machine (Shaw, Citation2005). The quality of turning is measured in terms of tolerances and roughness of surface. Surface finish is a quality specified by customer for machined parts (Suhail & Ismail, Citation2010). In turning operation, parameters such as cutting speed, depth of cut, feed rate and tool nose radius have great impact on the surface finish. The turning operation seems very simple; through high speed turning of steel inherently generates high cutting zone temperature. Such high temperature causes dimensional deviation and premature failure of cutting tools. It also impairs the surface integrity of the product by inducing tensile residual stresses and surface and subsurface micro cracks in addition to rapid oxidation and corrosion (Dhar, Islam, & Kamruzzaman, Citation2007). However, in high speed machining the conventional cutting fluid application fails to carry away the heat effectively (Lohar & Nanavte, Citation2013). Therefore, the recent development of nano fluids provides alterative cutting fluids which can be used in MQL machining (Tasdelen, Thordenberg, & Olofsson, Citation2008). The tribological and advanced heat transfer properties of nano fluids can provide better lubricating and cooling in the MQL machining process, and make it production-feasible. With proper selection of the cutting parameters and the MQL system, it is possible for MQL machining with minimum cost and less quantity of coolant to obtain better conditions, in terms of lubricity, tool life, cutting temperature, surface finish and optimisation of cutting parameters (Shen, Citation2008). To improve the surface characteristics from micro level to nano level, nano fluids are useful in the machining process (Prabhu & Vinayagam, Citation2011). Taguchi and Analysis of Variance (ANOVA) can conveniently optimize the cutting parameters with designed experimental trials. Taguchi design optimizes the parameters and reduces the sensitivity of the system performance (Berger & Maurer, Citation2002). This study describes the how to select process parameters which can minimize the effect of nuisance factor. Also this paper deals with the experimental investigation on effect of cutting parameters and optimization of cutting parameters in MQL turning of AISI 4340 with nano fluid for surface roughness and cutting force using Grey Relational Analysis (GRA).
2. Experimental set up and procedure
2.1. Preparation of nano fluid
Nano fluid is a new class of fluids engineered by dispersing nano meter-size solid particles into base fluids such as water, ethylene glycol, lubrication oils, and synthetic oil etc. (Shen, Citation2008). The Multi Walled Carbon Nano Tube (MWCNT 15 nm in diameter and 30 μm in length) particle is mixed with cutting fluid. The cutting fluid is a base fluid such as ethylene glycol in the proportion of the MWCNT is mixed in the concentration of 0.2%. The nano cutting fluid is prepared for 2 litres. The mass of the MWCNT nano particle required for the preparation of nano fluid is calculated as follows
The mass of the MWCNT required for the preparation of nano fluid is 8.4 gm. This nano particle is mixed with the cutting fluid using “Ultrasonic Vibrator” and “Magnetic Stirrer” in the Nano Science Laboratory. The alloy steel AISI 4340 is widely used for gears, shafts, couplings and other parts. Therefore the nano cutting fluid having better heat carrying capacity it results in better surface finish, maintain degree of cutting temperature and cutting force hence tool life increases so that it is used as the coolant for the turning operation of AISI 4340 under MQL mode.
2.2. Experimental procedure
To verify the grade of particular material chemical composition test is carried out. The chemical composition of work piece material in percentage is shown in Table .
Table 1. Chemical composition
According to design of experiment principles the factors and levels are selected for experimentation. The design matrix is (31 × 51 × 22) (Montgomery, Citation2001). Such as, three values of depth of cut, five values of feed rate, two values of cutting speed and tool nose radius respectively. Therefore, No. of sets of experiment = 31 × 51 × 22 = 60 sets. Whereas the air pressure 5 bar and fluid flow rate, 140 ml/h. are optimized value selected for experimental work. The input parameters and their levels are shown in Table .
Table 2. Input parameters and their levels
The experimental trials were conducted on the high speed precision MAXTURN++ (MTAB) CNC lathe machine (Speed 50–4,000 rpm, motor 7 KW). The alloy steel AISI 4340 used as a work piece material having diameter 24 mm, 100 mm length and BHN 217. Tungsten Carbide coated inserts with specification CCMT 090308 are used in MQL turning of AISI 4340 with nano fluid and different cutting parameters with their levels are shown in Table . For experimental work MWCNT is mixed in the cutting fluid used as a coolant because it is having better heat carrying capacity. In this research work, the surface roughness of the turned work piece was measured with Mitutoyo make surface roughness tester (SJ-201P). All measurements were repeated three times and the average value was taken as the final value. The cutting forces measured with the help of Kistler Dynamometer, a charge amplifier and PC software. Therefore surface roughness and cutting force are selected as response parameters whereas cutting force is a nuisance factor it affects by controlled as well as uncontrolled parameters so it is need to study the effect of cutting parameters on cutting force to improve the cutting performance under MQL condition with nano fluid. Figures – shows Experimental set up, MQL set up and Machined work piece respectively.
3. Results and discussion
The sixty experimental trials were carried out under MQL mode with nano fluid to optimize process parameters (cutting speed, depth of cut, feed rate and tool nose radius) on the output response variable such as cutting force and surface roughness. Full factorial orthogonal array was used for designing the experiments. The measured values of cutting force and surface roughness for the machined surfaces corresponding to all the experimental trials are shown in Table .
Table 3. Experimental results
3.1. Analysis of variance
ANOVA is a computational technique that enables the estimation of the contribution of the control factors to the overall measured response. Therefore, the statistical analysis of the experimental results can be processed by using Analysis of Variance (ANOVA) (Singh & Rao, Citation2007). The design of matrix has a major effect on the number of experiments needed. Therefore it is essential to have a proper design of experiments. In present work, the experimental results were analysed with Analysis of Variance which is used for identifying the factors affecting on the surface roughness and cutting force shown in Tables and . In this research work, by using full factorial matrix design sixty experimental trials were carried out in MQL turning of AISI 4340 with nano fluid. The results were analysed by using MINITAB statistical software. The response variable surface roughness and cutting force whose lower value is desirable related to machining performance. From Table and Figure it is seen that feed rate and cutting speed having maximum percentage contribution i.e. 38.94 and 22.87 respectively. Also it is observed that from Table feed rate and cutting speed had strongest influence on surface roughness followed by nose radius and depth of cut. Similarly from Table depth of cut had strongest influence on cutting force followed by feed rate and last by nose radius whereas cutting speed is a non significant factor. From Table it can be concluded that depth of cut and feed rate had maximum percentage contribution i.e. 65.27 and 34.12% respectively.
Table 4. ANOVA results for surface roughness
Table 5. ANOVA results for cutting force
Analysis of influence of each control factor speed, feed, depth of cut and tool nose radius on the surface roughness and cutting force has been performed with signal to noise ratio response table. The influence of each parameter can be clearly shown by response graphs. The response graphs of mentioned control parameters are shown in Figures and for surface roughness and cutting force respectively. The slope of the line clearly shows the power of influence of each control factor. From Figure it is seen that the optimum conditions for surface roughness are cutting speed 75 m/min, Feed rate 0.04 mm/rev. Depth of cut 1 mm and Tool nose radius 0.8 mm. From Figure it is observed that the optimum conditions for cutting force are cutting speed 90 m/min, Feed rate 0.04 mm/rev, Depth of cut 0.5 mm and Tool nose radius 0.4 mm.
3.2. Grey Relational Analysis
This analysis can be used to represent the grade of correlation between two sequences so that the distance of two factors can be measured discretely (Ulas & Ahmet, Citation2008). When the experimental method cannot be carried out exactly, grey analysis helps to compensate for the shortcoming in statistical regression (Lin & Ho, Citation2003). GRA can analyse many factors that can overcome the disadvantages of statistical method (Chang, Tsai, & Chen, Citation2003). Grey relational coefficients, grade and order of the measured values of surface roughness and cutting force for the machined surfaces corresponding to all the experimental trials are shown in Table . Table shows that experiment No. 3 has the highest Grey Relational Grade (GRG) (Appendix A). The response variables in this experiment are surface roughness (1.26 μm) and cutting force (7.69 kgf).
Table 6. Grey relational coefficients (GRC), grade and order
To calculate Average GRG for each factor level Taguchi method was employed. In orthogonal array average the GRG by factor level for each column (Fung, Citation2003). The mean of GRGs of all parameters at different levels and the difference between the maximum and minimum value of GRG for cutting parameters are shown in Table . The (Max-Min) the value of GRG shows the importance of individual parameter in MQL turning of AISI 4340 with nano fluid. From Table , it is observed that the difference between maximum and minimum value of GRG for parameter feed rate is higher than that of spindle speed, depth of cut and tool nose radius parameters. It indicates that feed rate has stronger effect on the multi performance characteristics than other parameters. Table indicates that the highest GRG of each parameter shows optimal level of parameter. The optimised parameters are as Feed rate1, Depth of cut 1, Cutting speed 1 and Tool nose radius 2. Therefore the optimized parameters are as cutting speed (75 m/min), Feed rate (0.04 mm/rev), Depth of cut (0.5 mm) and Tool nose radius (0.8 mm).
Table 7. Response table for grey relational grade
From Table it is seen that, feed rate is a most significant factor and also observed that the obtained results are statistically significant as probability of significance (p-value) is less than 0.05. The Signal to Noise ratio (S/N) is calculated by using MINITAB software. Signal represents desirable value whereas noise represents undesirable value for the output characteristics (Rao, Ramji, & Satyanarayna, Citation2010). The S/N ratio plot for GRA (Figure ) shows similar optimum condition i.e. cutting speed (75 m/min), feed rate (0.04 mm/rev), depth of cut (0.5 mm) and tool nose radius (0.8 mm). It means that the results obtained from ANOVA are closely matching to the results of GRA.
Table 8. ANOVA results for GRG
The validation of optimal level of cutting parameters is evaluated by using GRG. Table shows GRG improvement with optimised parameters. A good improvement with optimised parameters is 4.32%.
Table 9. GRG improvement with optimized parameters
Figure shows GRG vs. experimental trial. According to conducted full factorial experimental design, it is clearly seen that from Table and Figure that the process parameters setting of experiment No. 3 has the highest GRG. Thus, the third experiment gives the best multi performance characteristics among the sixty experiments.
3.3. Comparative analysis
The experimental runs were carried out on CNC turning lathe machine at different levels of process parameters to evaluate the effect of cutting parameters such as depth of cut and feed rate on surface roughness at different conditions such as—MQL1 (MWCNT nano particles mixed with ethylene as a base fluid), MQL2 (MWCNT nano particles mixed with water as a base fluid), Flooded and Dry. Figure shows surface roughness v/s feed rate at 0.5 mm depth of cut for MQL1, MQL2, Flooded and Dry lubrication systems. From Figure , it is observed that among the four lubrication systems, MQL1 with nano fluid gives better values of surface roughness. It is observed from Figures , as feed rate increases surface roughness value increases. Hence, it can be seen that from the lower surface roughness values that nano fluid has better heat carrying capacity with MQL1 as compared to other lubrication conditions.
3.4. Regression analysis
The regression model is mostly used to predict the responses is an algebraic representation of the regression line and is used to built up the relationship between the response and predictor parameters Montgomery (Citation2001), Patel et al.,(Citation2015).(1)
(1)
Regression analysis was implemented to develop prediction model using the predictors such as feed, speed, depth of cut and tool nose radius in CNC turning of AISI 4340 under MQL mode with nano fluid. The Minitab software was used for the analysis of experimental work and to develop the predictive model for the GRG of surface roughness and cutting force. Therefore the regression equation obtained is(2)
(2)
The quantity R2 called as coefficient of determination is used to judge the adequacy of regression model developed. The higher of R2 indicates the better fitting of the model with the data (Mandal, Doloi, & Mondal, Citation2011). In this model the adjusted R2 value is nearly closer to the predicted R2. To test the statistical significance of model, analysis of variance table is constructed and shown in Table for GRG. F-ratio is also the important factor to check the adequacy of model where F-table value should be smaller than the F-calculated value (Hwang & Lee, Citation2010). From Table it is seen that model is to be statistically significant as probability of significance (p-value) is less than 0.05 and F-calculated value is greater than F-table value (5.14). It is observed that the parameters mentioned in the model have significant effect on the response. Also, at optimum condition actual value (0.87) and predicted value (0.85) for response are very close to each other showing the significance of model developed.
Table 10. Summary of the model
Table 11. Analysis of variance for GRG model
4. Conclusion
By using GRA, the process parameters in MQL turning of AISI 4340 with nano fluid are optimized such as cutting speed (75 m/min), feed rate (0.04 mm/rev), depth of cut (0.5 mm) and tool nose radius (0.8 mm). From result analysis it is observed that, feed rate is a most significant factor. The optimum response variable obtained as surface roughness 1.26 μm and cutting force 7.69 kgf. From Figure it is also seen that the experiment No. 3 has highest GRG. Improvement in GRG is near about 4.32%. Table shows optimised parameter value. From comparative analysis it is observed that, MQL1 gives better surface roughness value as compared to other lubrication systems.
Table 12. Optimised parameters
To achieve the desire quality more focus should be on right selection of machining parameters. Therefore, the regression model would be helpful in selecting cutting conditions for required response characteristics. It may be helpful in optimising machining parameters to obtain desired value of GRG of surface roughness and cutting force under Minimum Quantity Lubrication turning of alloy steel with nano fluid.
Abbreviations | ||
MQL | = | Minimum Quantity Lubrication |
MWCNT | = | Multi Walled Carbon Nano Tube |
FR | = | Feed rate |
CS | = | Cutting speed |
DOC | = | Depth of cut |
NR | = | Nose radius |
Ra | = | Surface roughness |
Funding
The authors received no direct funding for this research.
Acknowledgement
The authors would like to express their appreciation to Mechanical Department of WCE, Sangli for their support of this research work.
Additional information
Notes on contributors
P.B. Patole
P.B. Patole is presently working as Assistant Professor in Department of Mechanical Engineering at Bharati Vidyapeeth’s College of Engineering, Kolhapur. He is pursuing PhD in Mechanical Engineering Department by Shivaji Universitty, Kolhapur, India. He received his BE from RIT Islampur, India and ME from K.I.T. Kollhapur, India. He has guided 06 PG students. His area of research includes Metal cutting theory, Advanced machining, Design of experiment, Optimization techniques.
References
- Berger, P. D., & Maurer, R. E. (2002). Experimental design with applications in management, engineering and the sciences (1st ed., p. 496). Pacific Grove, CA: Duxbury Press. ISBN 10: 0534358225.
- Chang, C. L., Tsai, C. H., & Chen, L. (2003). Applying grey relational analysis to the decathlon evaluation model. International Journal of the Computer, the Internet and Management, 11, 54–62.
- Dhar, N. R., Islam, S., & Kamruzzaman, M. (2007). Effect of minimum quantity lubrication (MQL) on tool wear, surface roughness and dimensional deviation in turning AISI-4340 steel. Gazi University Journal of Science, 20, 23–32.
- Fung, C. P. (2003). Manufacturing process optimization for wear property of fiber-reinforced polybutylene terephthalate composites with grey relational analysis. Wear, 254, 298–306.
- Hwang, Y. K., & Lee, C. M. (2010). Surface roughness and cutting force prediction in MQL and wet turning process of AISI 1045 using design of experiments. Journal of Mechanical Science and Technology, 24, 1669–1677.10.1007/s12206-010-0522-1
- Lin, Z. C., & Ho, C. Y. (2003). Analysis and application of grey relation and ANOVA in chemical-mechanical polishing process parameters. International Journal of Advanced Manufacturing Technology, 24, 10–14.
- Lohar, D. V., & Nanavte, C. R. (2013). Performance evaluation of minimum quantity lubrication (MQL) Using CBN tool during hard turning of AISI 4340 and its comparison with dry and wet turning. International Journal of Industrial Engineering and Management Science, 3, 102.
- Mandal, N., Doloi, B. M., & Mondal, B. (2011). Optimization of flank wear using Zirconia Toughened Alumina (ZTA) cutting tool: Taguchi method and regression analysis. Measurement, 44, 2149–2155.10.1016/j.measurement.2011.07.022
- Montgomery, D. C. (2001). Design and analysis of experiments (p. 17). John Wiley and Sons.
- Narana Rao, S., & Satyanarayana, B. S. (2011). Experimental estimation of tool wear and cutting temperatures in MQL using cutting fluids with CNT inclusion. International Journal of Industrial Engineering Science and Technology. ISSN: 0975-5462.
- Patel, P., Modi, B. S., Sheth, S., & Patel, T. (2015). Experimental investigation, modelling and comparison of Kerfwidth in laser cutting of laser cutting of GFRP. Bonfring International Journal of Industrial Engineering and Management Science, 5, 55–62.10.9756/BIJIEMS
- Prabhu, S., & Vinayagam, B. K. (2011). Fractal dimensional surface analysis of AISI D2 Tool steel material with nanofluids in grinding process using atomic force microscopy. Journal of the Brazilian Society of Mechanical Sciences and Engineering, 33, 459–466.10.1590/S1678-58782011000400009
- Rao, P. S., Ramji, K., & Satyanarayna, B. (2010). Perdiction of material removal rate for aluminium BIS-24345 alloy in wire cut EDM. International Journal of Engineering Science and Technology, 2, 7729–7739.
- Shaw, M. C. (2005). Metal cutting principles. New York, NY: Oxford University Press.
- Shen, B. (2008). Minimum quantity lubrication grinding using nano fluids (A Dissertation Submitted in Partial Fulfilment of the Requirements for the Degree of Doctor of Philosophy (Mechanical Engineering) in the University of Michigan, Michigan).
- Singh, D., & Rao, P. V. (2007). A surface roughness prediction model for hard turning process. The International Journal of Advanced Manufacturing Technology, 32, 1115–1124.10.1007/s00170-006-0429-2
- Suhil, A. H., & Ismail, N. (2010). Optimization of cutting parameters based on surface roughness and assistance of workpiece surface temperature in turning process. American Journal of Engineering and Applied Sciences, 3, 102–108.10.3844/ajeassp.2010.102.108
- Tasdelen, B., Thordenberg, H., & Olofsson, D. (2008). An experimental investigation on contact length during minimum quantity lubrication (MQL) machining. Journal of Materials Processing Technology, 203, 221–231.10.1016/j.jmatprotec.2007.10.027
- Ulas, C., & Ahmet, H. (2008). Use of the grey relational analysis to determine optimum laser cutting parameters with multi-performance characteristics. Elsevier, Optics and Laser Technology, 40, 987–994.
Appendix A
For experimental No. 3
(1) | Normalisation of Ra | ||||
(2) | Deviation sequence of Ra | ||||
(3) | Grey Relational Coefficient (GRC) of Ra | ||||
(4) | Grey Relational Grade of Ra |