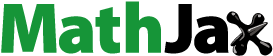
Abstract
This paper deals with automatic generation control of multi area power system using a Fuzzy PID controller. The controller parameters are optimized by Grey Wolf Optimizer (GWO) algorithm. Initially, Hydro-Thermal-Gas two area power systems is considered and superiority of the proposed controller is verified by comparing the results with GWO optimized classical PID controller as well as recently published optimal controller, such as DE-PID and TLBO-PID controllers. The proposed methodology is also verified with a modified power system with a nuclear plant and HVDC link and reveals better performance when compared with sliding mode controller tuned by TLBO algorithm. The proposed controller is designed to stabilize the frequency deviations of nonlinear power system considering FACTS devices and SMES. The results reveal that IPFC seems to be a promising alternative for frequency and tie-line power stabilization. Also the proposed controller is robust and satisfactory towards random step and sinusoidal load patterns.
Public Interest Statement
Automatic generation control (AGC) plays an important role to maintain a desired operating point. In an interconnected system, the function of AGC is to exchange and regulate power produced from various power generation units in each area so that the system frequency and the tie-line power interchanges between different control areas are maintained at their scheduled values. With the passage of time new ideas are emerging for the design of AGC controller to improve the system dynamics under the occurrence of the load perturbation. Flexible AC Transmission Systems (FACTS) are capable of enhancing power system stability by controlling the power flow in an interconnected power system. Further, improvement of system dynamics have been revealed with inclusion of storage devices along with FACTS based controller. A comparative study of FACTS devices on AGC have been analyzed in coordination with SMES, which further enhances system dynamics performance to a large extent.
1. Introduction
In a large interconnected power system, the generation of power is normally done by hydro, thermal and nuclear power plants. However, gas power generation is a small percentage of the total power generation which is suitable to meet the varying load demand. In the field of power system operation and control, automatic generation control (AGC) plays an important role in order to maintain a desired operating level characterized by nominal frequency, voltage profile and load flows in power system. In multi area interconnected power system all the generating units are connected together synchronously and work with the same frequency. A small load perturbation in the system will cause the deviations of frequencies of the areas and tie line power deviations from their nominal values (Elgerd, Citation2008). Therefore, the function of AGC is to exchange and regulate power produced from various sources in each area so that the system frequency and the tie-line power interchanges between different control areas are maintained at their scheduled values (Bevrani, Citation2009; Elgerd, Citation2008; Kothari & Nagrath, Citation2011). Initially, Elgerd and Fosha have done the pioneering works on AGC for solving regulator design problem (Elgerd & Fosha, Citation1970a, Citation1970b). By the passage of time, various controllers such as classical control (Das, Nanda, Kothari, & Kothari, Citation1990), optimal control (Bhatti, Citation2014; Elgerd & Fosha, Citation1970a; Yamashita & Taniguchi, Citation1986; Yazdizadeh, Ramezani, & Hamedrahmat, Citation2012), adaptive controls (Oysal, Yilmaz, & Koklukaya, Citation2005; Pan & Liaw, Citation1989; Rubaai & Udo, Citation1994) and robust control (Azzam & Mohamed, Citation2002; Toulabi, Shiroei, & Ranjbar, Citation2014; Wang, Zhou, & Wen, Citation1993) are proposed in AGC study. Though, significant improvements of new controllers in recent years, Proportional Integral Derivative (PID) controller is still an attractive and simple option in AGC. Hence, PID controller is most widely employed in many power industries (Bevrani & Hiyama, Citation2008; Yu & Tomsovic, Citation2004). In past decades following the advent of modern intelligent techniques such as Genetic Algorithm (GA), Particle Swarm Optimization (PSO), Fuzzy Logic (FL) and Artificial Neural Network (ANN), new ideas have been emerged for the design of AGC controller to improve the system dynamics under the occurrence of the load perturbation. The gains of PI and PID controllers are optimized through real coded genetic algorithm in a two area power system (Pingkang, Hengjun, & Yuyun, Citation2002). A PSO based controller parameter tuning of interconnected reheat thermal system is proposed for AGC in Abdel-Magid and Abido (Citation2003). Artificial Bee Colony (ABC) algorithm has been proposed to tune PI and PID controller’s parameters for interconnected reheat thermal power system and its superiority is tested by comparing the dynamic performance of the system having PSO tuned controllers (Gozde, Taplamacioglu, & Kocaarslan, Citation2012). The optimal output feedback controller is proposed to the multi-source multi area power system having thermal, hydro and gas power plant in each area (Parmar, Majhi, & Kothari, Citation2012). Similarly, Teaching Learning Based Optimization (TLBO) algorithm is proposed for the same system for AGC in (Barisal, Citation2015) and the potential and effectiveness is compared with that of Differential Evolution (DE) and optimal output feedback controller proposed in (Mohanty, Panda, & Hota, Citation2014; Parmar et al., Citation2012). Few authors proposed hybrid intelligent techniques such as hybrid Bacterial Foraging Optimization Algorithm—PSO (hBFOA-PSO), hybrid Firefly Algorithm—Pattern Search (hFA-PS), hPSO-PS and hDE-PSO for the study of AGC and achieved excellent dynamic performance of the system (Panda, Mohanty, & Hota, Citation2013; Sahu, Panda, & Padhan, Citation2015; Sahu, Panda, & Sekhar, Citation2015; Sahu, Pati, & Panda, Citation2014). The success of fuzzy logic controllers for AGC of nonlinear power system are reported by many researchers. A self tuning fuzzy PID type controller for AGC of two area interconnected power system is proposed by Yeşil, Güzelkaya, and Eksin (Citation2004). Various heuristic optimization techniques have been incorporated successfully for tuning of fuzzy PID controllers (Sahu, Panda, & Padhan, Citation2015; Sahu, Panda, & Sekhar, Citation2015). Similarly, variable structure fuzzy gain scheduling based controller tuned by GA is reported for multi source two area hydro thermal system (Chandrakala, Balamurugan, & Sankaranarayanan, Citation2013) and output feedback sliding mode controller (SMC) tuned by TLBO algorithm is proposed for multi source two area hydro thermal system with addition of gas plant in one area and nuclear plant in other area (Mohanty, Citation2015). Distributed optimization and control methods have been applied for economic load dispatch in smart grid (Li, Yu, Yu, Chen, & Wang, Citation2017; Li, Yu, Yu, Huang, & Liu, Citation2016). Remodeling of demand side management and development of bidirectional framework for quickly solving problem and getting customers best response is quite encouraging. Due to quite popularity, distributed optimization and control methods are emerging techniques for solving LFC problem. Different level of coordinated communications may be established between the different controllers. This will lead to establish distributed control mechanism of interconnected realistic power system, which tackles GRC, GDB and load reference set-point constraints.
Further, improvement of system dynamics have been revealed with inclusion of Flexible AC Transmission Systems (FACTS) based controller. These FACTS devices are capable of enhancing power system stability by controlling the power flow in an interconnected power system (Hingorani & Gyugyi, Citation2000). Several FACTS devices, such as Thyristor Controlled Phase Shifter (TCPS), Static Synchronous Series Compensator (SSSC), Thyristor Controlled Series Compensator (TCSC), Unified Power Flow Controller (UPFC) and Interline Power Flow Controller (IPFC), have been developed and proposed for AGC (Abraham, Das, & Patra, Citation2007; Chidambaram & Paramasivam, Citation2012; Lal, Barisal, & Tripathy, Citation2016; Ngamroo, Taeratanachai, Dechanupaprittha, & Mitani, Citation2007; Padhan, Sahu, & Panda, Citation2014; Ponnusamy, Banakara, Dash, & Veerasamy, Citation2015; Pradhan, Sahu, & Panda, Citation2016; Shankar, Bhushan, & Chatterjee, Citation2016; Zare, Hagh, & Morsali, Citation2015). Energy storage devices have been widely accepted by many researchers for AGC in coordination with FACTS devices. The control performance enhancement of two areas multiple unit power system in coordination with Redox Flow Battery (RFB) and IPFC have been introduced in (Chidambaram & Paramasivam, Citation2012). Bhatt, Roy, and Ghoshal (Citation2011) compared and described the performance of SMES-SMES, TCPS-SMES and SSSC-SMES controllers in AGC for a two area interconnected power system. The system dynamics in coordination with SSSC and TCPS for two area power system has been studied (Subbaramaiah, Citation2011).
The literature review reveals that the performance of the power systems not only depend on various controllers but also on the intelligent techniques used for controller parameters optimization. Also the improvements of system dynamics have been achieved with inclusion of FACTS and energy storage devices. In perspective of the above, the ongoing work proposes Fuzzy PID controller for AGC. The controller parameters have been optimized by recently developed powerful optimization technique i.e. Grey Wolf Optimizer (GWO) algorithm (Mirjalili, Mirjalili, & Lewis, Citation2014). The main advantages of selecting GWO algorithm in the present work is that, the algorithm provides very promising results in various engineering optimization problems. It may be noted that the GWO algorithm requires least number of controlling parameter, which make it simple concept for implementation, effective, faster convergence due to inherent randomness for optimum global solutions. Also, Guha, Roy, and Banerjee (Citation2016) tested the superiority and effectiveness of the GWO algorithm by optimizing the classical controllers such as PI/PID controllers for AGC and compared transient responses of the power system with GA, DE, BFOA, hBFOA-PSO, FA and TLBO optimized classical controllers. Also the comparisons have been done with hPSO-PS and hFA-PS optimized Fuzzy PID controllers.
The motivation behind the present work is that efficient AGC of a complex interconnected power system with FACTS devices coordinated with storage facility greatly improves the dynamic stability of the system when subjected to small load perturbation. In the present work the GWO optimized Fuzzy PID controller is proposed on a two area multi-source interconnected power system and its performance is compared with recently published results such as TLBO-PID, DE-PID and optimal controller for the same power system. Furthermore, proposed controller performance is compared in the modified power system having the output feedback sliding mode controller (SMC) (Mohanty, Citation2015). Finally, the present work is extended with inclusion of several FACTS devices for AGC and a comparative performance of the system have been analyzed in coordination with SMES. Furthermore, three unequal area thermal power system has been considered to verify the potential of FACTS based controller with the proposed algorithm.
In view of the above discussion, the following are the main objectives of the present work:
(I) | Initially, the work is started with AGC of multi-area multi-source hydro-thermal-gas power system to investigate the superiority of the proposed GWO optimized Fuzzy PID control technique. Then, the work is extended to hydro-thermal-gas in one area and hydro-thermal-nuclear in another area with Super Conducting Magnetic Energy Storage (SMES). Also, to make the system more realistic nonlinearities like Generation Rate Constraint (GRC) and Governor Dead Band (GDB) is considered for analysis. | ||||
(II) | To incorporate different types of FACTS devices for AGC of power system and compare their effectiveness to system performance. | ||||
(III) | To check the stability of different power system models as proposed in this paper, Eigen value analysis has been done. | ||||
(IV) | To conduct sensitivity analysis for the proposed GWO optimized Fuzzy PID controller for the proposed model and to investigate its robustness to wide changes in loading patterns. |
2. Modeling of the interconnected power system
The system under study is a two area multi source interconnected power system. First the power system model taken into consideration for dynamic behaviour study includes reheat thermal, hydro and gas generating units in each area. Subsequently the study is extended to power system model which includes reheat thermal, hydro and gas generating units in one area. The other area consists of reheat thermal, hydro and nuclear units. The non-linearity such as GRC and GDB is included in the system to make it more realistic power system. The transfer function model of the proposed system is shown in Figure for simulation and AGC study. The system parameters are given in Appendix A.
3. Modeling of FACTS devices
FACTS devices are one aspect of the power electronics revolution that is taking place in all areas of electric energy. The principal role is to enhance controllability and power transfer capability in ac system. In this section modeling of the FACTS devices are presented for AGC study.
3.1. Modeling of SSSC for AGC
The SSSC belongs to the family of FACTS devices. It is installed in series with the transmission lines. It has the capability to shift its reactance characteristic from capacitive to inductive and effectively control the power flow. The SSSC is implemented by a voltage sourced converter operated as a synchronous voltage source and to provide effective voltage and power flow control in an independent way by internally generated series reactive compensation. It is installed in series with the tie-line for frequency stabilization of interconnected power system. The schematic diagram of SSSC connected in series with the tie-line is shown in Figure .
The controller to change the SSSC voltage can be expressed as (Ngamroo et al., Citation2007; Ponnusamy et al., Citation2015; Pradhan et al., Citation2016):(1)
(1)
If the frequency deviation ΔF1(s) is sensed, it can be used as the control signal (i.e. ΔError = ΔF1(s)) to the SSSC unit to control Vs which will alter the tie-line power flow between two areas and assist in stabilizing the frequency oscillation. Thus:(2)
(2)
(3)
(3)
where, KSSSC = K1K2(4)
(4)
(5)
(5)
The detailed structure of SSSC in series with tie line is provided in Figure . The input signal of SSSC controller is the frequency deviation p.u. Hz in Area 1. The structure of SSSC frequency stabilizers consists of the stabilization gain (KSSSC) block and the phase compensation block with time constants T1, T2, T3 and T4 which provides the appropriate phase-lead characteristics to compensate the lag between input and the output signals.
3.2. Modeling of the TCPS for AGC
The TCPS is a device that changes the relative phase angle between the system voltages. Therefore, the real power flow can be controlled to mitigate the frequency oscillations and improve power system stability (Abraham et al., Citation2007). A schematic of the two area interconnected power system with TCPS in series with the tie-line is shown in Figure . TCPS is placed near Area 1. Resistance of the tie-line is neglected. Without TCPS, the incremental tie-line power flow from Area 1 to Area 2 can be expressed as:(6)
(6)
Figure 4. A schematic diagram of a two area interconnected power system with TCPS in series with tie-line.

where is the synchronizing constant without TCPS and Δf1 and Δf2 are frequency deviations of Area 1 and Area 2 respectively. The detail derivations are presented in Abraham et al. (Citation2007).
The phase shifter angle with inclusion of TCPS can be represented as:
(7)
(7)
where Kϕ and TPS are the gain and time constant of the TCPS. Now the tie-line power flow deviation can be written as:(8)
(8)
If the frequency deviation is sensed and used as the control signal to the TCPS unit to control the TCPS phase angle which in turn, control the tie-line power flow, then Equation (7) becomes:
(9)
(9)
Also the tie-line power flow becomes:(10)
(10)
(11)
(11)
where,
The structure of TCPS as a frequency stabilizer is shown in Figure . The gain Kϕ and time constant TPS of the TCPS are optimized using the proposed algorithm.
3.3. Modeling of UPFC for AGC
The Unified Power Flow Controller (UPFC) belongs to an important member in the FACTS family. It has the capability to control, at the same time or specifically every one of the parameters such as voltage, impedance and phase angle which are affecting power flow in the transmission line. In other words, it can independently control both the real and reactive power flow in the line (Hingorani & Gyugyi, Citation2000). The UPFC consists of two back to back voltage sourced converters as shown in Figure . These consecutive converters are worked from a common dc link provided by a dc storage capacitor. Based on the concept on reactive shunt compensation, series compensation and phase angle regulation of power transmission line, the UPFC fulfill all these functions and thereby meet multiple control objectives.
The detail derivations of UPFC based controller for AGC study is given in (Shankar et al., Citation2016). Thus the UPFC based controller can be represented as follows.(12)
(12)
where TUPFC is a time constant of UPFC.
The structure of UPFC as frequency stabilizer is shown in Figure .
3.4. Modeling of IPFC for AGC
The IPFC provides a path for the cost-effective utilization of individual transmission lines by encouraging the autonomous control of both the real and reactive power flow. The IPFC which belongs to FACTS family proposed by Gyugyi with Sen and Schauder in 1998 provides attractive option for compensation and power flow management of multiple transmission lines at a given substation (Hingorani & Gyugyi, Citation2000). The IPFC employs a number of dc-to-ac converters and each provides series compensation for a different line. The schematic of IPFC is shown in Figure . It facilitates not only compensation of each transmission line separately but also provides compensation of all at the same time. The IPFC not only provides independent control of reactive series compensation of each individual line, but also provides a capability to directly transfer of real power between the compensated lines through dc link. In this way it controls both the real and reactive power transfer through the common dc link from over-loaded lines to under-loaded lines. To understand the impact of IPFC in the power system during the steady state the mathematical derivation is presented in Chidambaram and Paramasivam (Citation2012). The IPFC based controller can be represented in AGC as:(13)
(13)
and(14)
(14)
where TIPFC is a time constant of IPFC.
The structure of IPFC as a frequency controller is shown in Figure .
4. Modeling of the SMES system for AGC
Figure shows the basic transfer function model of SMES unit in power system. An SMES unit has high efficiency and fast response. An SMES unit is designed to store electric power in the low loss superconducting magnetic coil. Its storage capability in addition to kinetic energy of the generator rotor enhances the damping of the electromechanical oscillation in power system. In view of the above, two SMES units are incorporated in Area 1 and Area 2 in order to stabilize frequency oscillations as shown in Figure .
The structure for SMES as frequency stabilizer is modeled as the second order lead-lag compensator as shown in Figure . The input signals of the SMES units are p.u. frequency deviations in respective areas where those are connected. The parameters of SMES frequency stabilizers in each area such as, the stabilization gain KSMES and time constants T1, T2, T3 and T4 are to be optimized for optimal design of SMES frequency stabilizer.
5. Controller structure and objective function
The structure of the Fuzzy PID controller is shown in Figure (Sahu et al., Citation2014; Yeşil et al., Citation2004). An identical controller is employed in each area. The error inputs to the controllers are the respective area control error (ACE). For the two areas interconnected power system, the ACE signal made by frequency and tie-line power deviations is represented by Equations (15) and (16),(15)
(15)
(16)
(16)
Fuzzy controller uses error(e) and derivative of error as input signals. The outputs of the Fuzzy controllers UT, UH and UG are the control inputs of the generating units. Fuzzy PID controller is a combination of fuzzy proportion-integral (PI) and fuzzy proportional-derivative (PD) controllers. The input scaling factors are K1and K2 and the output scaling factors are K3 and K4. Triangular membership functions are used with five fuzzy linguistic variables such as NB (negative big), NS (negative small), Z (zero), PS (positive small) and PB (positive big) for both the inputs and the output. Membership functions for error, error derivative and FLC output are shown in Figure . Mamdani fuzzy inference engine is selected for the present work. The two-dimensional rule base for error, error derivative and FLC output are given in Table .
Figure 13. Membership function for the two inputs and two outputs with gains of −1 to 1 and −10 to 10, respectively.

Table 1. Fuzzy rules for the inputs and outputs
In the selection process of the controller parameters, the objective function is first defined based on the desired specifications and constraints. The output specifications in time domain are peak overshooting, rise time, settling time and steady state errors. In Integral of Time Multiplied Absolute Error (ITAE), time is multiplied with the absolute value of errors so that oscillations die out quickly and results in minimum of settling time (Ogata, Citation2010). Therefore, it is used as objective function for controller parameters tuning. The objective function J for controller parameters optimization of the interconnected power system is depicted below.(17)
(17)
where, ΔF1 and ΔF2 are the frequency deviations in Area 1 and Area 2 respectively; ΔPTie is the incremental change in tie line power; tsim is the time range of simulation. The problem constraints are the minimum and maximum limits of Fuzzy PID controllers scaling factors K1, K2 K3 and K4. Thus, the design problem can be formulated as follows:(18)
(18)
Subject to:(19)
(19)
6. Grey Wolf Optimizer algorithm
The meta-heuristic optimization techniques have been successfully implemented in many engineering fields. Those have produced excellent results and have many advantages over conventional methods such as simplicity, flexibility, derivative free mechanism and local optima avoidance (Mirjalili et al., Citation2014). The Grey Wolf Optimizer (GWO) algorithm is one of the meta-heuristic algorithms inspired by grey wolves (Canis lupus) (Mirjalili et al., Citation2014). Grey wolf, also known as timber wolf or western wolf belongs to Canidae family.
The advantage of GWO algorithm over most of the optimization algorithm is that the algorithm requires no specific input parameters. Also, it is straightforward and free from computational complexity. The flowchart of GWO algorithm is presented in Figure .
The group hunting is an important social behaviour apart from the surviving and living in a pack. The main phases of group hunting are as follows:
(i) | Tracking, chasing and approaching the prey. | ||||
(ii) | Pursuing, encircling and harassing the prey until it stops moving. | ||||
(iii) | Attack towards the prey. |
The mathematical model of social hierarchy of wolves, tracking, encircling and attacking prey are given in Mirjalili et al. (Citation2014).
Finally, the steps of GWO algorithm may be summarized as follows (Guha et al., Citation2016):
(a) | The search process is started with random initialization of candidate solutions (wolves) in the search space. | ||||
(b) | Alpha, beta and delta wolves are estimated based on the position of prey. | ||||
(c) | To find the optimum location of prey, each wolf updates its position. | ||||
(d) | A control parameter | ||||
(e) | Candidate solutions tend to diverge and at the end the optimum solution is stored. |
7. Results and discussion of the simulated test system
7.1. Two area test system
The simulation of system under study has been done in MATLAB/Simulink environment and GWO algorithm has been written in (.m file). The developed model is simulated using initial gain scheduling parameters considering an 1% step load perturbation (SLP) in Area 1 at time t = 0 s. The objective function is calculated in .m file and used in optimization algorithm for tuning the gains of Fuzzy PID controller for power system. Series of experiments were conducted to choose the appropriate controller parameters. The simulation was repeated for 30 times and the best final solution among the 30 runs is selected as proposed controller parameters. The best final solutions obtained in the 30 runs are considered as optimal solution shown in Table for the system under study.
Table 2. GWO optimized Fuzzy PID controller parameters of power system-1 without physical constraints
The predominance of the proposed GWO optimized Fuzzy PID controller is verified in Figure (a)–(c), when compared with optimal controller, DE-PID controller, TLBO-PID controller and GWO optimized PID controller for the multi-source two area power system having Hydro-Thermal-Gas in each area considering a 1% SLP in Area 1 at time, t = 0 s. The controller parameters values are given in Table . Then, a gas unit in Area 2 is replaced by nuclear unit along with HVDC link, GRC and reheat turbine in each area. The model is simulated with the proposed controller and controller parameters are optimized. Results in terms of frequency deviations in each area and tie-line power deviation are shown in Figure (a)–(c) by comparing with recently published paper on TLBO optimized output feedback sliding mode controller (SMC). The optimized values for the proposed controllers are presented in Table . The performance index values in terms of maximum undershoot (MUS), maximum overshoot (MOS), settling time with 2% tolerance band and different errors are shown in Table . The present work is extended considering GDB with GRC and reheat turbine with inclusion of SMES units in both areas. The comparative analysis of the considered system with proposed controller is done with and without SMES units in each area. It is clear from Figure (a)–(c) that system performance further improves with SMES units. Also the Eigen values and minimum damping ratio (MDR) are presented in Table . As we know the closed loop system is said to be stable if all the eigen values are located to the left half of the s-plane. From Table , it is clear that all eigen values are lying in the left half of s-plane for which the system is stable. The MDR value with SMES and proposed controller is found to be higher than without SMES. The settling time, maximum overshoot (MOS) and minimum undershoot (MUS) are better with SMES as shown in Table .
Figure 15. (a) Frequency deviation in Area 1 subjected to a step load change of 0.01 p.u. in Area 1, (b) Frequency deviation in Area 2 subjected to a step load change of 0.01 p.u. in Area 1 and (c) Tie-line power flow deviation subjected to a step load change of 0.01 p.u. in Area 1.
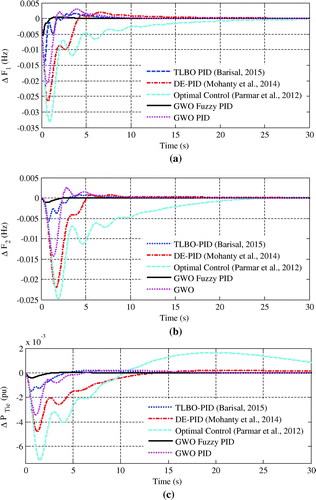
Figure 16. (a) Frequency deviation in Area 1 subjected to a step load change of 0.01 p.u. in Area 1 and their comparison for proposed GWO optimized Fuzzy PID control scheme with TLBO optimized Output feedback SMC scheme, (b) Frequency deviation in Area 2 subjected to a step load change of 0.01 p.u. in Area 1 and their comparison for proposed GWO optimized Fuzzy PID control scheme with TLBO optimized Output feedback SMC scheme and (c) Tie-line power flow deviation subjected to a step load change of 0.01 p.u. in Area 1 and their comparison for proposed GWO optimized Fuzzy PID control scheme with TLBO optimized Output feedback SMC scheme.
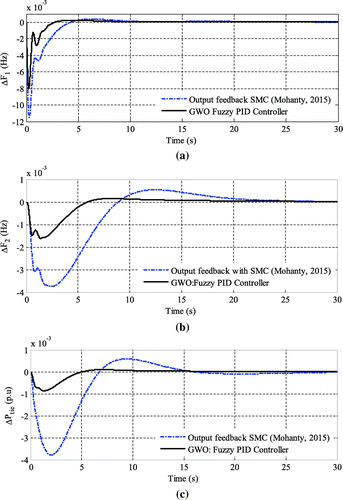
Table 3. GWO optimized Fuzzy PID controllers parameters of power system-2 with HVDC link, GRC and reheat turbine
Table 4. Performance evaluation of proposed GWO optimized Fuzzy PID controller by settling time, minimum undershoot and maximum overshoot
Figure 17. (a) Frequency deviation of Area 1 without and with SMES subjected to load change of 0.01 p.u. in Area 1, (b) Frequency deviation of Area 2 without and with SMES subjected to load change of 0.01 p.u. in Area 1 and (c) Tie-line power flow deviation without and with SMES subjected to load change of 0.01 p.u. in Area 1.
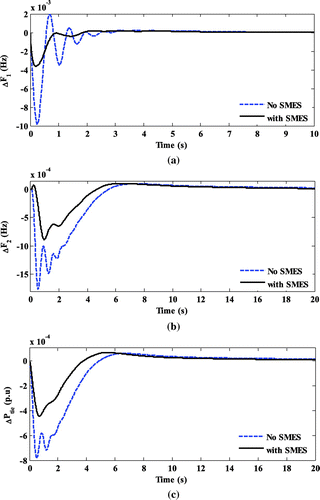
Table 5. System modes, minimum damping ratio, for multi-source multi area power system with HVDC link, GDB, GRC and Reheat turbine without and with SMES
Table 6. Performance evaluation of proposed GWO optimized Fuzzy PID controller by settling time, minimum undershoot and maximum overshoot of multi-source multi area nonlinear power system without and with SMES
Further the present work is extended to verify the improvements in system performance with incorporation of different FACTS devices such as SSSC, TCPS, UPFC and IPFC along with SMES units as shown in Figure . The optimal gains of the proposed GWO based Fuzzy PID controller with FACTS devices are reported in Table . The comparison of the performance of the system with different FACTS devices are shown in Figure (a)–(c). It is clear from Figure (a)–(c) that UPFC and IPFC providing good results. If only frequency deviation of Area 1 is considered UPFC performs better than IPFC. But IPFC performs better than UPFC when frequency deviation in Area 2 and tie-line power deviations are also considered. The performance of IPFC is dominating to all FACTS members considered. The performance index values with different FACTS devices are given in Table . The overall performance of IPFC is found to be better than others. The eigen values evaluated for the system with coordinated operation of different FACTS devices with an SLP of 1% in Area 1 are presented in Table . All eigen values are lying in the left half of s-plane, because of which the system is stable. The MDR value of IPFC based controller is found to be 0.5881, which is higher than others. To approve the adequacy of the proposed approach the analysis is carried out for the system subjected to different load patterns such as random step load and sinusoidal load. A random step load pattern is presented in Figure and is applied in Area 1. The system responses are given in Figure (a)–(c).
Table 7. Optimal gains of controller for different FACTS devices
Figure 18. (a) Frequency deviation of Area 1 with SMES and FACTS subjected to a step load change of 0.01 p.u. in Area 1, (b) Frequency deviation of Area 2 with SMES and FACTS subjected to a step load change of 0.01 p.u. in Area 1 and (c) Tie-line power flow deviation with SMES and FACTS subjected to a step load change of 0.01 p.u. in Area 1.
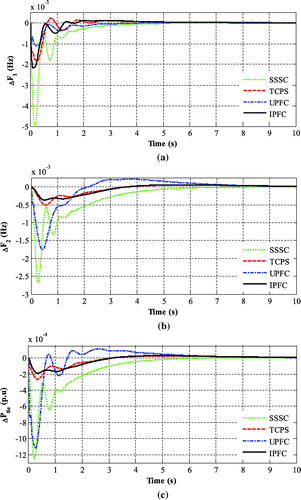
Table 8. Performance criteria for multi-source multi area nonlinear power system with SMES and FACTS
Table 9. System modes, minimum damping ratio, for multi-source multi area nonlinear power system with SMES and FACTS
Figure 20. (a) Frequency deviation in Area 1 subjected to random load in Area 1 with GWO optimized Fuzzy PID controller, (b) Frequency deviation in Area 2 subjected to random load in Area 1 with GWO optimized Fuzzy PID controller and (c) Tie line power deviation obtained subjected to random load in Area 1 with GWO optimized Fuzzy PID controller.
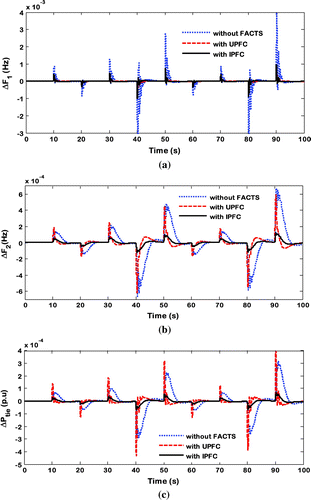
The sinusoidal load perturbation represented by Equation (20) with varying amplitude as shown in Figure is applied in Area 1. The expression for sinusoidal load change is as follows:(20)
(20)
Figure (a)–(c) show the system response subjected to sinusoidal varying load in Area 1.
Figure 22. (a) Frequency deviation in Area 1 subjected to sinusoidal load pattern in Area 1 with GWO optimized Fuzzy PID controller with and without FACTS, (b) Frequency deviation in Area 2 subjected to sinusoidal load pattern in Area 1 with GWO optimized Fuzzy PID controller with and without FACTS and (c) Tie line power deviation subjected to sinusoidal load pattern in Area 1 with GWO optimized Fuzzy PID controller with and without FACTS.
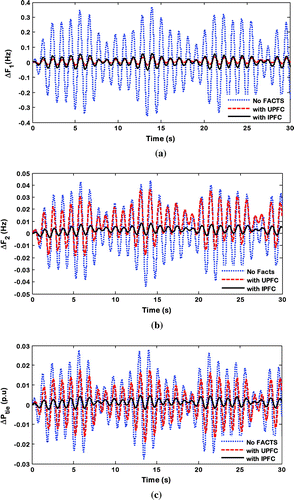
It is clear from Figures (a)–(c) and (a)–(c) that the system oscillation greatly decreased with incorporation of FACTS controller. It is proved that the IPFC performs better among all FACTS devices for the considered power system.
7.2. Three unequal area thermal power system
The system considered is a three unequal area thermal system. Each area of power system consists of speed governor, single stage reheat turbine and generation rate constraint (GRC) of 3%/min. The capacities of different control areas are in the ratio of 2:5:8. The nominal system parameters are presented in Appendix B. The transfer function model of the considered system is shown in Figure .
It is concluded from the discussion as presented in Section 7.1 that, overall performance of UPFC and IPFC are superior among others FACTS devices for improvement of power system dynamic performance. In order to verify the potential of the UPFC and IPFC based controller, a three area power system is considered in present study. The Structure of UPFC and IPFC as frequency stabilizers for three area power system are shown in Figures and , respectively. The system dynamic responses are evaluated and analyzed with 1% SLP in Area 1. The optimal gains of controllers for different FACTS devices are given in Table . The frequency deviations in Area 1, Area 2 and Area 3 are shown in Figure (a)–(c) respectively, subjected to SLP of 1% in Area 1 with GWO optimized Fuzzy PID controller with and without FACTS devices. The IPFC is once again exhibiting greater flexibility as far as the dynamics of the system is considered.
Table 10. Optimal gains of controller for different FACTS devices for three area thermal power system
Figure 26. (a) Frequency deviation in Area 1 subjected to SLP of 1% in Area 1 with GWO optimized Fuzzy PID controller with and without FACTS, (b) Frequency deviation in Area 2 subjected to SLP of 1% in Area 1 with GWO optimized Fuzzy PID controller with and without FACTS and (c) Frequency deviation in Area 3 subjected to SLP of 1% in Area 1 with GWO optimized Fuzzy PID controller with and without FACTS.
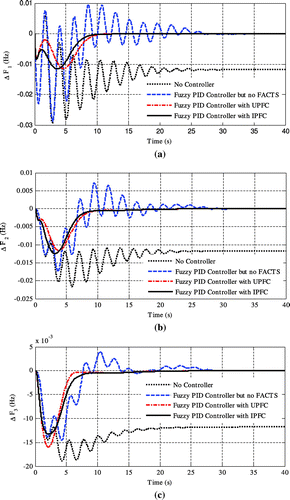
8. Conclusion
This paper presents the design and implementation of GWO optimized Fuzzy PID controller in power systems. At first multi-source two area power system having Hydro-Thermal-Gas in each area is considered and the effectiveness and superiority of the proposed GWO optimized Fuzzy PID controller for the power system is verified by comparing the results with GWO optimized classical PID controller as well as recently published optimal controller, DE-PID and TLBO-PID controllers. Then the considered power system model is modified and a gas unit in Area 2 is replaced by nuclear unit along with HVDC link, GRC and reheat turbine in each area. The comparison is made between GWO optimized Fuzzy PID controller and TLBO optimized output feedback with SMC for the same power system. The study reveals that the dynamic performance of the system improves largely with the proposed controller as compared to TLBO optimized output feedback SMC. Then work is extended considering GDB with GRC and reheat turbine with inclusion of SMES units in both areas. The system dynamics is significantly improved in presence of SMES. A comparative study is also presented with coordinated operation of different FACTS controllers for AGC with the proposed controller. Finally sensitivity analysis is carried out to determine the robustness of the system with proposed controller at different load perturbation like random step load and sinusoidal load in Area 1.
Additional information
Funding
Notes on contributors
Deepak Kumar Lal
Deepak Kumar Lal born in 1984 and received the BTech Degree from the BPUT, Rourkela, Odisha, in 2008 and MTech degree in power system engineering in Electrical Engineering Department, National Institute of Technology, Jamshedpur, India in 2010. Since 2011, he is working as Assistant professor in the Department of Electrical Engineering, Veer Surendra Sai University of Technology, Burla, Odisha, India. His research interests include automatic generation control, economic load dispatch, renewable energy integration and power quality.
A.K. Barisal
A.K. Barisal is an associate professor in the Department of Electrical Engineering, Veer Surendra Sai University of Technology, Burla, Odisha, India since 2006. He received the “Odisha Young Scientist award - 2010”, IEI Young Engineers award - 2010” and “Union Ministry of Power, Department of power prize - 2010” for his outstanding contribution to Engineering and Technology research. His research interests include economic load dispatch, Hydrothermal Scheduling and soft computing applications to power system.
References
- Abdel-Magid, Y.L., & Abido, A.A. (2003). AGC tuning of interconnected reheat thermal systems with particle swarm optimization. 10th IEEE International Conference on Electronics, Circuits and Systems, Proceedings of the ICECS, 1, 376–379.
- Abraham, R. J., Das, D., & Patra, A. (2007). Effect of TCPS on oscillations in tie-power and area frequencies in an interconnected hydrothermal power system. IET Generation, Transmission & Distribution, 1, 632–639.10.1049/iet-gtd:20060361
- Azzam, M., & Mohamed, Y. S. (2002). Robust controller design for automatic generation control based on Q-parameterization. Energy Conversion and Management, 43, 1663–1673.10.1016/S0196-8904(01)00118-2
- Barisal, A. K. (2015). Comparative performance analysis of teaching learning based optimization for automatic load frequency control of multi-source power systems. International Journal of Electrical Power & Energy Systems, 66, 67–77.10.1016/j.ijepes.2014.10.019
- Bevrani, H. (2009). Robust power system frequency control. New York, NY: Springer.10.1007/978-0-387-84878-5
- Bevrani, H., & Hiyama, T. (2008). Robust decentralised PI based LFC design for time delay power systems. Energy Conversion and Management, 49, 193–204.10.1016/j.enconman.2007.06.021
- Bhatt, P., Roy, R., & Ghoshal, S. P. (2011). Comparative performance evaluation of SMES–SMES, TCPS–SMES and SSSC–SMES controllers in automatic generation control for a two-area hydro–hydro system. International Journal of Electrical Power & Energy Systems, 33, 1585–1597.10.1016/j.ijepes.2010.12.015
- Bhatti, T. S. (2014). AGC of two area power system interconnected by AC/DC links with diverse sources in each area. International Journal of Electrical Power & Energy Systems, 55, 297–304.
- Chandrakala, K. R. M. V., Balamurugan, S., & Sankaranarayanan, K. (2013). Variable structure fuzzy gain scheduling based load frequency controller for multi source multi area hydro thermal system. International Journal of Electrical Power & Energy Systems, 53, 375–381.10.1016/j.ijepes.2013.05.009
- Chidambaram, I. A., & Paramasivam, B. (2012). Control performance standards based load-frequency controller considering redox flow batteries coordinate with interline power flow controller. Journal of Power Sources, 219, 292–304.10.1016/j.jpowsour.2012.06.048
- Das, D., Nanda, J., Kothari, M. L., & Kothari, D. P. (1990). Automatic generation control of a hydro thermal system with new area control error considering generation rate constraint. Electric Machines & Power Systems, 18, 461–471.10.1080/07313569008909490
- Elgerd, O. I. (2008). Electric energy system theory: An introduction (2nd ed.). McGraw Hill.
- Elgerd, O. I., & Fosha, C. E. (1970a). Optimum megawatt-frequency control of multiarea electric energy systems. IEEE Transactions on Power Apparatus and Systems, PAS-89, 556–563.10.1109/TPAS.1970.292602
- Elgerd, O. I., & Fosha, C. E. (1970b). The megawatt-frequency control problem: A new approach via optimal control theory. IEEE Trans Power Apparatus System, PAS-89, 563–577.
- Gozde, H., Taplamacioglu, M. C., & Kocaarslan, İ. (2012). Comparative performance analysis of artificial bee colony algorithm in automatic generation control for interconnected reheat thermal power system. International Journal of Electrical Power & Energy Systems, 42, 167–178.10.1016/j.ijepes.2012.03.039
- Guha, D., Roy, P. K., & Banerjee, S. (2016). Load frequency control of interconnected power system using grey wolf optimization. Swarm and Evolutionary Computation, 27, 97–115.10.1016/j.swevo.2015.10.004
- Hingorani, N. G., & Gyugyi, L. (2000). Understanding FACTS: Concepts and technology of FACTS. New York, NY: IEEE Press.
- Kothari, D. P., & Nagrath, I. J. (2011). Modern power system analysis. New Delhi: McGraw Hill.
- Lal, D. K., Barisal, A. K., & Tripathy, M. (2016). Grey wolf optimizer algorithm based fuzzy PID controller for AGC of multi-area power system with TCPS. Procedia Computer Science, 92, 99–105.10.1016/j.procs.2016.07.329
- Li, C., Yu, X., Yu, W., Chen, G., & Wang, J. (2017). Efficient computation for sparse load shifting in demand side management. IEEE Transactions on Smart Grid, 8, 250–261.10.1109/TSG.2016.2521377
- Li, C., Yu, X., Yu, W., Huang, T., & Liu, Z. W. (2016). Distributed event-triggered scheme for economic dispatch in smart grids. IEEE Transactions on Industrial Informatics, 12, 1175–1785.
- Mirjalili, S., Mirjalili, S. M., & Lewis, A. (2014). Grey wolf optimizer. Advances in Engineering Software, 69, 46–61.10.1016/j.advengsoft.2013.12.007
- Mohanty, B. (2015). TLBO optimized sliding mode controller for multi-area multi-source nonlinear interconnected AGC system. International Journal of Electrical Power & Energy Systems, 73, 872–881.10.1016/j.ijepes.2015.06.013
- Mohanty, B., Panda, S., & Hota, P. K. (2014). Controller parameters tuning of differential evolution algorithm and its application to load frequency control of multi-source power system. International Journal of Electrical Power & Energy Systems, 54, 77–85.10.1016/j.ijepes.2013.06.029
- Ngamroo, I., Taeratanachai, C., Dechanupaprittha, S., & Mitani, Y. (2007). Enhancement of load frequency stabilization effect of superconducting magnetic energy storage by static synchronous series compensator based on H∞ control. Energy Conversion and Management, 48, 1302–1312.10.1016/j.enconman.2006.09.017
- Ogata, K. (2010). Modern control engineering (5th ed.). New Delhi: Prentice Hall.
- Oysal, Y., Yilmaz, A. S., & Koklukaya, E. (2005). A dynamic wavelet network based adaptive load frequency control in power systems. International Journal of Electrical Power & Energy Systems, 27, 21–29.10.1016/S0142-0615(04)00099-7
- Padhan, S., Sahu, R. K., & Panda, S. (2014). Automatic generation control with thyristor controlled series compensator including superconducting magnetic energy storage units. Ain Shams Engineering Journal, 5, 759–774.10.1016/j.asej.2014.03.011
- Pan, C. T., & Liaw, C. M. (1989). An adaptive controller for power system load-frequency control. IEEE Transactions on Power Systems, 4, 122–128.10.1109/59.32469
- Panda, S., Mohanty, B., & Hota, P. K. (2013). Hybrid BFOA–PSO algorithm for automatic generation control of linear and nonlinear interconnected power systems. Applied Soft Computing, 13, 4718–4730.10.1016/j.asoc.2013.07.021
- Parmar, K. P. S., Majhi, S., & Kothari, D. P. (2012). Improvement of dynamic performance of LFC of the two area power system: An analysis using MATLAB. International Journal of Computer Application, 40, 28–32.
- Pingkang, L., Hengjun, Z., & Yuyun, L. (2002). Genetic algorithm optimization for AGC of multi-area power systems. TENCON’02 Proceedings, 2002 IEEE Region 10 Conference on Computers, Communications, Control and Power Engineering, 3, 1818–1821.
- Ponnusamy, M., Banakara, B., Dash, S. S., & Veerasamy, M. (2015). Design of integral controller for load frequency control of static synchronous series compensator and capacitive energy source based multi area system consisting of diverse sources of generation employing Imperialistic Competition Algorithm. International Journal of Electrical Power & Energy Systems, 73, 863–871.10.1016/j.ijepes.2015.06.019
- Pradhan, P. C., Sahu, R. K., & Panda, S. (2016). Firefly algorithm optimized fuzzy PID controller for AGC of multi-area multi-source power systems with UPFC and SMES. Engineering Science and Technology, an International Journal, 19, 338–354.10.1016/j.jestch.2015.08.007
- Raju, M., Saikia, L. C., & Sinha, N. (2016). Automatic generation control of a multi-area system using ant lion optimizer algorithm based PID plus second order derivative controller. International Journal of Electrical Power & Energy Systems, 80, 52–63.10.1016/j.ijepes.2016.01.037
- Rubaai, A., & Udo, V. (1994). Self-tuning load frequency control: Multilevel adaptive approach. IEE Proceedings Generation, Transmission and Distribution, 141, 285–290.10.1049/ip-gtd:19949964
- Sahu, B. K., Pati, S., & Panda, S. (2014). Hybrid differential evolution particle swarm optimisation optimised fuzzy proportional–integral derivative controller for automatic generation control of interconnected power system. IET Generation, Transmission & Distribution, 8, 1789–1800.10.1049/iet-gtd.2014.0097
- Sahu, R. K., Panda, S., & Padhan, S. (2015). A hybrid firefly algorithm and pattern search technique for automatic generation control of multi area power systems. International Journal of Electrical Power & Energy Systems, 64, 9–23.10.1016/j.ijepes.2014.07.013
- Sahu, R. K., Panda, S., & Sekhar, G. T. C. (2015). A novel hybrid PSO-PS optimized fuzzy PI controller for AGC in multi area interconnected power systems. International Journal of Electrical Power & Energy Systems, 64, 880–893.10.1016/j.ijepes.2014.08.021
- Shankar, R., Bhushan, R., & Chatterjee, K. (2016). Small-signal stability analysis for two-area interconnected power system with load frequency controller in coordination with FACTS and energy storage device. Ain Shams Engineering Journal, 7, 603–612.10.1016/j.asej.2015.06.009
- Subbaramaiah, K. (2011). Improvement of dynamic performance of SSSC and TCPS based hydrothermal system under deregulated scenario employing PSO based dual mode controller. European Journal of Scientific Research, 57, 230–243.
- Toulabi, M. R., Shiroei, M., & Ranjbar, A. M. (2014). Robust analysis and design of power system load frequency control using the Kharitonov’s theorem. International Journal of Electrical Power & Energy Systems, 55, 51–58.10.1016/j.ijepes.2013.08.014
- Wang, Y., Zhou, R., & Wen, C. (1993). Robust load-frequency controller design for power systems. IEE Proceedings C Generation, Transmission and Distribution, 140, 11–16.10.1049/ip-c.1993.0003
- Yamashita, K., & Taniguchi, T. (1986). Optimal observer design for load-frequency control. International Journal of Electrical Power & Energy Systems, 8, 93–100.10.1016/0142-0615(86)90003-7
- Yazdizadeh, A., Ramezani, M. H., & Hamedrahmat, E. (2012). Decentralized load frequency control using a new robust optimal MISO PID controller. International Journal of Electrical Power & Energy Systems, 35, 57–65.10.1016/j.ijepes.2011.09.007
- Yeşil, E., Güzelkaya, M., & Eksin, İ. (2004). Self tuning fuzzy PID type load and frequency controller. Energy Conversion and Management, 45, 377–390.10.1016/S0196-8904(03)00149-3
- Yu, X., & Tomsovic, K. (2004). Application of linear matrix inequalities for load frequency control with communication delays. IEEE Transactions on Power Systems, 19, 1508–1515.10.1109/TPWRS.2004.831670
- Zare, K., Hagh, M. T., & Morsali, J. (2015). Effective oscillation damping of an interconnected multi-source power system with automatic generation control and TCSC. International Journal of Electrical Power & Energy Systems, 65, 220–230.10.1016/j.ijepes.2014.10.009
Appendix
The typical values of system under study are given below:
A.1. Power system-1 (Barisal, Citation2015; Mohanty et al., Citation2014; Parmar et al., Citation2012)
f = 60 Hz; B1 = B2 = 0.425 p.u. MW/Hz; PR = 2,000 MW (rating), PL = 1,740 MW (nominal loading); R1 = R2 = R3 = 2.4 Hz/p.u. MW; pf11 = pf21 = 0.46966; pf12 = pf22 = 0.37814; pf13 = pf23 = 0.1522; Tps = 11.49 s; Kps = 68.9566 Hz/p.u. MW; T12 = 0.0433 p.u.; a12 = −1.
Thermal: Tg1 = Tg2 = 0.08 s; Tr1 = Tr2 = 10 s; Kr1 = Kr2 = 0.3; Tt1 = Tt2 = 0.3 s.
Hydro: Trh1 = Trh2 = 28.75 s; TR1 = TR2 = 5 s; Tgh1 = Tgh2 = 0.2 s; Tw1 = Tw2 = 1 s.
Gas: b1 = b2 = 0.5; c1 = c2 = 1; Xc1 = Xc2 = 0.6 s; Yc1 = Yc2 = 1 s; Tcr1 = Tcr2 = 0.03 s; Tf1 = Tf2 = 0.23 s; Tcd1 = Tcd2 = 0.2 s.
A.2. Power system-2 (Mohanty, Citation2015)
This is the modified system of power system1 with physical constraints, HVDC link, nuclear power plant in Area 2 are given below:
f = 60 Hz; B1 = B2 = 0.4312 p.u. MW/Hz; PR = 2,000 MW (rating), PL = 1,740 MW (nominal loading); R1 = R2 = R3 = 2.4 Hz/p.u. MW; KT = 0.543478; KH = 0.326084; KN = 0.130438; T12 = 0.545 p.u.; a12 = − 1.
HVDC: Tdc = 0.2 s; Kdc = 1.
Nuclear: KHI = 2; KR1 = 0.3; TT1 = 0.5 s; TRH1 = 7 s; TRH2 = 9 s.
GRC of thermal 3% per minute.
GRC of hydro 360% up and 240% down per minute.
B. Power system-3 (Raju, Saikia, & Sinha, Citation2016)
f = 60 Hz, Tgi = 0.08 s, Tti = 0.3 s, Tri = 10 s, Kri = 0.5, KPi = 120 Hz/p.u. MW, TPi = 20 s, Hi = 5 s, Di = 8.33 × 10−3 p.u. MW/Hz, Ri = 2.4 Hz/p.u. MW, T12 = 0.0866 p.u. MW/rad, Bi = 0.425 p.u. MW/Hz, Loading = 50%, GRC = 3 min in each area, capacities of different areas are 2:5:8 and SLP = 1 in Area 1.