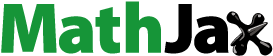
Abstract
This study represents the evaluation of energy efficiency improvement using combination of natural gas, solar energy and flue gases heat recovery in polyester production. The analyzed energy sources are used for dry saturated steam generation. The energy consumption for combined system on location (φ = 45°49′) with collector field of 23.23 × 103 m2, was investigated. The hybrid system was calculated for four variants: (1) solarized process without flue gases heat recovery, (2) solarized processes with heat contend in flue gases using economizer, (3) solarized processes with heat contend in flue gases using an air preheater and (4) solarized processes with heat contend in flue gases using economizer and air preheater. The best method among presented sources is solution using economizer and the air preheater with natural gas, solar energy and flue gases heat recovery. The natural gas consumption is reduced for 67.82% which indicates that this solution is the optimal one. At the same time the volume of exhaust flue gases is diminished from 4947.1 to 1430.4 /h while simultaneously decreasing outlet temperature of 172.85°. Together with considerable energy savings, this hybrid system is sustainable and environmentally acceptable.
Public Interest Statement
The main novelty in this paper are extensive energy efficiency improvements in polyester production when applying hybrid system combining solar energy together with flue gases heat recovery for dry saturated steam generation. The utilization of presented energetic system could have the advantages of sustainability of environmental acceptability and availability in industrial production process. The hybrid system development is shown for four options. The environmental analysis showed reduction of natural gas consumption and diminishing of flue gases exhaust temperature and volume. The results show that energy consumption using solarized process without flue gases heat recovery saves natural gas for 60.98%. The natural gas savings becomes 67.1% when combining solarized process with flue gases heat recovery using economizer. Combustion air preheating, using solar radiation and flue gases results with fuel savings of 65.54%, while combining solarized process with flue gases heat recovery using both economizer and air preheater showed reduction of natural gas consumption for 67.82%.
1. Introduction
Polyethylene terephthalate (PET) also named polyester is the most common thermoplastic polymer (https://en.wikipedia.org/wiki/Polyethylene_terephthalate). This synthetic noncellulosic organic manmade fibers are very long threadlike molecules collected of hundreds of thousands of atoms strung together in chains (https://www.referenceforbusiness.com/industries/Chemicals-Allied/Organic-Fibers-Noncellulosic.html). Polymer is made up of polymerized units of the monomer ethylene terephthalate. Earliest polyester production was based on dimethyl ester polymerization (Mihelić-Bogdanić & Budin, Citation2009). Nowadays, about 70% of widely used terephthalic acid applied in polyester manufacturing is produced by the oxidation process of paraxilene in nitric acid (Mohd Fadzil, Ab. Rahim, & Maniam, Citation2014).
Polyester is an excellent water and moisture barrier material with very good properties like heat stability, resistant to wrinkling. It has great durability and therefore takes a central position under engineering plastic with commercial use. This thermoplastic polymer is used in fibers for clothing in textile industry, containers for liquids and foods, thermoforming for manufacturing and in combination with glass fiber for engineering resins. Also it is used as a substrate in thin film solar cells (https://en.wikipedia.org/wiki/Polyethylene_terephthalate). As many others thermoplastics polyester can be recycled and then prime applied for fiber, strapping and etc. (https://plastics.americanchemistry.com/Plastic-Resin-Codes-PDF/).
The polymerizations process of polyester is a continuous process including many series actions, where a significant quantity of heat energy produced employing high grade fossil fuel, electrical energy and water is consumed (Smith, Citation1990). Now, in this process a great amount of hot condensate as well as flue gases are rejected to the surrounding. In order to reduce heat wastes and at the same time to be environmentally friendly with lowest losses, this process should be optimized. The high temperature of flue gases shows an indicative potential for energy conservation. The implementation of flue gases heat recovery for air and feed water preheating as well as combination of both can improve the technological process (Mihelić-Bogdanić, Budin, & Sutlović, Citation2000; Thumann, Citation2002).
Although renewable energy has received a good treat of attention for power generation i.e. their use in industrial applications has received less interest (Renewable Energy in Industrial Applications, Citation2010). The presented analyses are focused on the potential of solar energy sources for process heat in polyester manufacturing sector. Solar energy is the world’s most abundant permanent source of energy (Goswami & Kreith, Citation2016). The implementation of solar energy depends on yearly solar radiation. Most applications require backup energy source to ensure that the requirements of industry are met even on days with less solar radiation (Mihelić-Bogdanić & Budin, Citation2009). Process with solar heat is based by relevant solar data for selected location in Croatia. The combination of solar generated steam and flue gases heat recovery technique show the reducing fuel consumption as well as the temperature of exhaust flue gases (Afsar & Akin, Citation2016; Karagiorgas, Botzios, & Tsoutsos, Citation2001), which shows positive impact on the environment. This hybrid powered system will be outlined and discussed. The objective of this paper is to find energy reduction and improvements using the combination of different energy sources. The assumption is that hybrid system using the combination of natural gas, solar energy and flue gases heat recovery provides the greatest energy savings in polyester production.
2. Polyester fibres process flow
Manmade polyester fibres offer substitute for many natural fibres (cotton, wool, etc.) and has become the most widely used polymer in nonwovens industry (https://en.wikipedia.org/wiki/Polyethylene_terephthalate). Polyethylene terephthalate is a condensation polymer industrially fabricated by either dimethyl terephthalate with ethylene glycol or at present by the most widely used terephthalic acid process. This is based on oxidation of paraxilene conducted with a cobalt catalyst in nitric acid (Hedge et al., Citation2004; Rodriguez, Cohen, Ober, & Archer, Citation2015; Stevens, Citation1999). The typical industrial sequences for continuous polymerization process include many relevant operations requiring a significant amount of electrical, thermal energy and water (Mohd Fadzil et al., Citation2014). The manufacture of polyester is shown in Figure .
This research analyses energy consumption in polyester manufacturing at rate DPET = 45 t/day by yearly operation time of τ = 7,272 h i.e. 303 days. The plant is closed for two months yearly (Mihelić-Bogdanić & Budin, Citation2006, Citation2014). This technology consists of following procedures: in autoclave reactor, filters, dryers, esterification reactor, crystallizer, melter, rollers, transesterification reactor, polymerizer, polymer melt, tow drawing, crimper, cutter and baler.
Electrical energy in amount of ee = 1.432 kWhe/kgPET is distributed to the following units: filters, esterification reactor, crystallizer, rollers, transesterification reactor, polymerizer, tow drawing, crimper and cutter with baler, as seen in Table .
Table 1. Electrical energy consumption in polyester manufacturing
Cold water in mass is used in autoclave reactor (
) and in crystallizer (
).
The natural gas fuel has the ultimate analysis by volume (Potter & Somerton, Citation1993; Požar, Citation1992):(1)
(1)
The lower heating value becomes HL = 35,513 kJ/m calculated earlier (https://plastics.americanchemistry.com/Plastic-Resin-Codes-PDF/). The natural gas consumption is VF = 387.7 m
/h = 9,034.8 m
/day or with yearly operating time VF, Y = 2.82 × 106 m
/year (Mihelić-Bogdanić & Budin, Citation2014).
Feed water enters the boiler at temperature, tB = 298.15 K (25°C). The dry saturated steam (p = 3 bar) in amount of dS = 2.3 kgS/kgPET is generated in a natural gas fuelled boiler with efficiency ηB = 82% and is transferred to the autoclave reactor where terephthalic acid is produced. Steam production is: Ds = 103,500 kgS/day = 4,312.5 kgS/h while the heat transferred to the steam generator is: QB = 270.96 × 106 kJ/day = 82.1 × 109 kJ/year.
The air requiring for fuel combustion enters firebox with temperature, ta = 298.15 K (25°C)
The exhaust flue gases temperature is tFG = 477.15 K (204°C) and the volume with α = 25% of excess air becomes: VFG = 12.76 m/m
. In this process exhaust flue gases in quantity of VFG,PET = 4,947.1 m
/h = 35.97 × 106m
/year are rejected to the environment and are analysed in formerly article (Mihelić-Bogdanić & Budin, Citation2014). The daily consumptions in polyester production are shown in Table .
Table 2. Daily resources consumption in polyester production
The novelty of this study is the impact of hybrid system in polyester production which combines natural gas together with solar energy , flue gases heat recovery for dry saturated steam generation. The environmental analysis showed reduction of natural gas consumption while simultaneously diminishing the flue gases exhaust temperature and volume when using both economizer and air preheater (Eastop & Croft, Citation1995). The presented combination of sources provides greater efficiency improvements in polyester production and is also environmentally acceptable.
3. Flue gases heat recovery
The goal of the process, which includes flue gases heat recovery is to create maximum reduction in energy consumption with a minimum investment. In all thermal processes exist very large heat losses and it is important to evaluate the quantity of that (Demirel, Citation2012). In industrial production plant the heat losses from natural gas fired boiler comes from the hot exhaust flue gases and are primary wasted through chimney. The recovered heat of the flue gases could be used for better utilization of fuel resulting with higher overall efficiency. The assignment is to take out from the hot flue gases as much as possible (Bloom, Citation2009).
The flue gases heat recovery systems offer significant possibilities of improving the efficiency with simultaneous reduction of the waste heat discard to the atmosphere (Demirel, Citation2012). The energy contained in the natural gas savings system reclaims the waste heat from the exhaust gases. This presented flue gases are used in the boiler to preheat feed water as well as combustion air or both. Flue gases heat recovery evaluate the existing heat potential (Flue Gas Heat Recovery, Citation2012).
3.1. Feed water preheating in economizer
The economizer (ECO) (Turner, Citation2012) is gas to liquid water heat exchanger using process thermal energy from hot flue gases. In presented process feed water at the temperature tEi = tB = 298.15 K (25°C) passes the economizer with efficiency ηE = 85%. Feed water is preheated using recovered flue gases with inlet temperature tFG, Ei = 477.15 K (204°C) in amount of VFG = 12.76 m/m
. After leaving economizer water achieved temperature of tE0 = 355.85 K (82.7°C).
The process steam production is Ds = 4,312.5 kgS/h. In presented case the natural gas consumption becomes VF, E = 351.96 m/h or 8,447.21 m
/day or yearly VF,E,Y = 2.56 × 106m
/year (Mihelić-Bogdanić & Budin, Citation2014).
The heat calculation for dry saturated steam production is (Budin & Mihelić-Bogdanić, Citation2013):(2)
(2)
In presented case the flue gases volume is lowered 9.2%, while the hot exhaust gases are cooled from 477.15 K (204°C) to 324.95 K (51.8°C) (Mihelić-Bogdanić & Budin, Citation2014).
3.2. Combustion air preheating in air preheater
The air preheater (AP) has the function to preheat the combustion air before entering the boiler. The energy required for this purpose is supplied to the heat exchanger (Flue Gas Heat Recovery, Citation2012). The high temperature of boiler exhaust gases is a problem of clean energy generation. Flue gases temperature can be lowered using air preheater system. Such a procedure should result in smaller fuel consumption and diminished flue gases outlet temperature.
In the process of polyester production flue gases in volume of VFG = 12.76 m/m
have temperature tFG,Ai = 477.15 K (204°C). These gases enter the air preheater with efficiency ηA = 90%. The ambient air temperature at tAi = ta = 298.15 K (25°C) and in volume
passes through air preheater where they are heated by flue gases to temperature of 322.34 K = 49.19°C.
The natural gas consumption is or with yearly operating time
becomes,
.
The heat consumption for dry saturated steam production becomes is (Budin & Mihelić-Bogdanić, Citation2013):(3)
(3)
In this process volume of flue gases are diminished for 7% while the flue gases outlet temperature is lowered from 477.15 K (204°C) to 337.55 K (64.4°C). Here presented results are calculated and published (Mihelić-Bogdanić & Budin, Citation2014).
3.3. Combustion air and feed water preheating
In a plant with heat recovery a part of flue gases energy from the natural gas fueled boiler could be transferred by an air preheater passing through an economizer. It is used for combustion air and feed water preheating (Figure ) (Flue Gas Heat Recovery, Citation2012).
Applying presented method, the flue gases are cooled what caused increasing of combustion air as well as boiler feed water temperature. These approaches with air preheater and economizer by using heat of flue gases are attractive in polyester production. Previously calculated values indicated that the volume of flue gases have an economizer outlet temperature
which is at the same time flue gases air preheater inlet temperature
. Atmospheric air with volume
and at the temperature of
enters the air preheater.
The fuel consumption is or yearly
.
Taking into account boiler efficiency ηB = 82% and lower heating value of natural gas calculating earlier (Mihelić-Bogdanić & Budin, Citation2014), the heat consumption for dry saturated steam is assembled as is (Budin & Mihelić-Bogdanić, Citation2013):
(4)
(4)
The flue gases emission declined to the surrounding is reduced by 10.15% while the exhaust flue gases temperature is lowered from 477.15 K (204°C) to 304.30 K (31.15°C). These values are estimated in formally paper (Mihelić-Bogdanić & Budin, Citation2014).
4. Solar system design
Although the residential sector offers a huge potential for solar thermal applications, the industrial sector shows a remarkable relevance, covering about 28% of the total primary energy consumption and a significant share of the heat consumed in the industrial sector is in the low and medium temperature range (Vannoni, Battisti, & Drigo, Citation2008). The presented analysis discussed the potential for solar energy use and technologies in the industrial manufacturing sector, separately in here presented polyester production. Solar energy has an unlimited resource potential and the sun is the most reliable and abundant source of energy (Ataei, Hemmatabady, & Nobakhtand, Citation2016). Solar thermal energy generation concentrates the light from the sun to produce heat.
The application of solar energy, as a partial substitution for natural gas fuel in polyester production process, can reduce significantly the total energy consumption (Mihelić-Bogdanić, Budin, & Filipan, Citation1999; Mihelić-Bogdanić et al., Citation2000). The utilization of this friendly available and environmentally benign source depends on location of the plant, the insolation rate what means on latitude and climatologically conditions (Weiss & Biermayr, Citation2010). The solar system analysed here is proposed to be installed on (φ =45°49′). Data for monthly average daily radiation (Qr) on horizontal area were calculated from global daily hourly radiate on measurements (Croatian Meteorological Bulletin Climatic Data, Citation1997) and are presented in Figure .
The useful solar radiation (Qu) depending on monthly average daily radiation (Qr) and collector area (A) which defer from 65% in summer, 50% in transition to 25% in winter period (ASHRAE Standard 93, Citation1986) is expressed as is (Budin & Mihelić-Bogdanić, Citation2013):(5)
(5)
The area needed for solar collector can be formulated as is (Budin & Mihelić-Bogdanić, Citation2013):(6)
(6)
where F = 1.25 is the security factor for large collector installation (ASHRAE Standard 93, Citation1986) and is the previously calculated daily heat input to the boiler in the plant. Heat of boiler flue gases are used in air preheater and also in economizer.
Flat plate collectors (Goswami, Citation2015) are the cheapest technology but they can be used to heat loads between 323.15 K and 353.15 K (50 and 80°C) (Kalogirou, Citation2009). The mean flat plate collector area (Table ) is calculated on the basis of average values area for summer period i.e. June, July, August and becomes is (Budin & Mihelić-Bogdanić, Citation2013):(7)
(7)
Table 3. The mean flat plate collector area calculation
Calculation of monthly useful solar energy with mean collector area can be obtained using following equation is (Budin & Mihelić-Bogdanić, Citation2013):(8)
(8)
where dm are days in a month.
Two months i.e. January and December are omitted because the plant is closed in this period. The results of useful daily radiation (Qu), collector area (A), monthly useful solar energy (Qm) are shown in Table .
The total useful yearly radiation becomes is (Budin & Mihelić-Bogdanić, Citation2013)(9)
(9)
5. Solar system combined with flue gases heat recovery
Optimum design of the combined solar collector and flue gases heat recovery is studied (Ataei et al., Citation2016; Kalogirou, Citation2009; Vineetha & Babu, Citation2016). Such a combination applied in polyester production is illustrated in Figure . This concept is characterized by collector fields, heat exchanger, steam generator, air preheater, economizer, waste heat recovery system and industrial process.
Figure 4. Optimum design of the combined solar collector and flue gases heat recovery in polyester production.
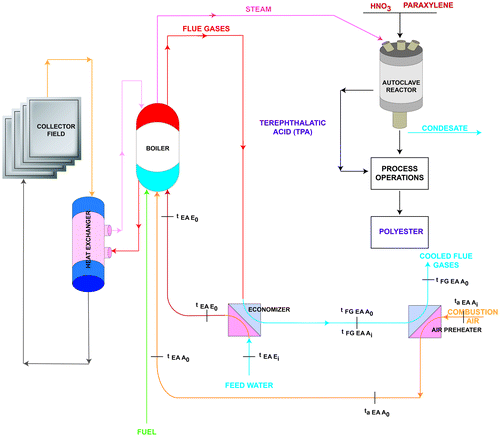
Steam generator, where dry saturated steam is produced, is heated by energy from collector fields, natural gas and exhaust flue gases. Combustion air, as well as feed water, are preheated with waste heat of flue gases. In this hybrid system, natural gas fuel consumption and energy savings in process without flue gases recovery will be analysed. Also processes with flue gases heat recovery using economizer, air preheater as well as the combination of both are presented. The volume of exhaust flue gases that will be rejected to the atmosphere in all cases are computed.
Relevant calculated values for solarized process are shown as follows:
1. | Process without flue gases heat recovery |
Natural gas consumption is (Budin & Mihelić-Bogdanić, Citation2013):(10)
(10)
and fuel savings becomes (Budin & Mihelić-Bogdanić, Citation2013):(11)
(11)
The volume of exhaust flue gases is (Budin & Mihelić-Bogdanić, Citation2013):(12)
(12)
2. | Process with flue gases heat recovery using economizer |
Natural gas consumption is (Budin & Mihelić-Bogdanić, Citation2013):(13)
(13)
and fuel savings becomes (Budin & Mihelić-Bogdanić, Citation2013):(14)
(14)
The volume of exhaust flue gases is (Budin & Mihelić-Bogdanić, Citation2013):(15)
(15)
3. | Process with flue gases heat recovery using air preheater |
Natural gas consumption is (Budin & Mihelić-Bogdanić, Citation2013):(16)
(16)
and fuel savings becomes (Budin & Mihelić-Bogdanić, Citation2013):(17)
(17)
The volume of exhaust flue gases is (Budin & Mihelić-Bogdanić, Citation2013):(18)
(18)
4. | Process with flue gases heat recovery using economizer and air preheater |
Natural gas consumption is (Budin & Mihelić-Bogdanić, Citation2013):(19)
(19)
and fuel savings becomes (Budin & Mihelić-Bogdanić, Citation2013):(20)
(20)
The volume of exhaust flue gases is (Budin & Mihelić-Bogdanić, Citation2013):(21)
(21)
The results of proposed optimization from energy point of view shows the best values when applying natural gas and the solar system combined with flue gases heat recovery, Table . This option use economizer and air preheater in polyester production for selected location. Such a technology shows natural gas savings in amount 67.82% compared with process without solar energy and flue gases recovery. At the same time volume of exhaust flue gases diminished from 4947.1 m to 1430.4 m
what makes the positive impact on the environment. Such hybrid system is claimed to be not only energy efficient but economical and environmentally responsible (Mihelić-Bogdanić, Budin, & Sutlović, Citation2002) because of the role of new energy technologies, which include both different renewable energy sources and efficient energy end-use technologies, and their contribution to the emission reductions required could come up to even 70–75%. The rapid growth of new renewables such as wind and solar power as a result of both public support schemes and price reductions matches well with their perceived future role in the mitigation measures (Lund, Citation2016).
Table 4. Consumption comparison in different processes
6. Conclusion
The main novelty in this paper are extensive energy efficiency improvements in polyester production when applying hybrid system combining solar energy together with flue gases heat recovery for dry saturated steam generation. The environmental analysis showed reduction of natural gas consumption while simultaneously diminishing the flue gases exhaust temperature and volume.
The results are based on the calculated natural gas requirements and the measured data for solar radiation in polyester production. In order to save natural gas energy for feed water and combustion air preheating with solar energy and heat of exhaust gases are presented. This calculation includes data for selected location (φ = 45°49′) using collector field of 23.24 × 103 m2.
The results show that energy consumption using solarized process without flue gases heat recovery saves natural gas for 60.98%. The volume of flue gases diminished from to
with exhaust temperature of 477,15 K (204°C).
The combined solarized process with flue gases heat recovery using economizer for feed water preheating shows the natural gas savings up to 67.1%. The volume of flue gases is simultaneously reduced to . The temperature of flue gases is lowered from 477.15 K (204°C) to 324.95 K (51.8°C).
Combustion air preheating, using solar radiation and flue gases heat recovery results with fuel savings of 65.54%. The flue gases volume decrease to while the outlet temperature becomes 337.19 K (64.04°C).
The greatest energy savings where shown when combining all four energy source together, i.e. solarized process with flue gases heat recovery using both economizer and air preheater. The environmental analysis showed the greatest reduction of natural gas consumption up to 67.82%. The flue gases emission is reduced by 71.1% with flue gases exhaust temperature diminishing from 477.15 K (204°C) to 304.30 K (31.15°C).
The utilization of presented energetic system could have the advantages of sustainability of environmental acceptability and availability in industrial production process.
Funding
This work was supported by Croatian Science Foundation under the project [grant number IP-2016-06-5278] and Ministarstvo Znanosti, Obrazovanja i Sporta [grant number 25-1951390-3000].
Cover image
Source: Authors.
Additional information
Notes on contributors
Alka Mihelić-Bogdanić
Alka Mihelić-Bogdanić, PhD was born in Zagreb and works as full professor at the University of Zagreb, Faculty of Textile Technology. She received her bachelor's degree in the year 1972, her master's degree in the year 1975 and her doctor's degree in the year 1977 from Zagreb University, Faculty of Technology. Her research activities are in the field of chemical engineering, textile technology and energetics. The areas of special research interest are: Energetics, Technical thermodynamics, Energy management in industry and New and renewable energy sources.
From 1984 to 2000, she has performed the collaboration with the Institute for Thermodynamic at the Technical University Graz and with the Institute for Physics at the Karl Franz University Graz, in the field of alternative energy sources as well as Stirling engine. She has published over 121 scientific papers with international reviews and 13 professional papers.
References
- Afsar, C., & Akin, S. (2016). Solar generated steam injection in heavy oil reservoirs: A case study. Renewable Energy, 91, 83–89.10.1016/j.renene.2016.01.047
- ASHRAE Standard 93. (1986). Methods of testing to determine the thermal performance of solar collectors. New York, NY: ASHRAE Publications.
- Ataei, A., Hemmatabady, H., & Nobakhtand, S. Y. (2016). Hybrid thermal seasonal storage and solar assisted geothermal heat pump systems for greenhouses. Advances in Energy Research, 4, 87–106.10.12989/eri.2016.4.1.087
- Bloom, A. (2009). Investigating in Industrial Heat Recovery. Flue gas cooling. Booklet Investigating in industrial heat recovery. Retrieved from https://www.procesvarme.dk/heatrecovery/Booklet_Waste_Heat_Recovery.pdf
- Budin, R., & Mihelić-Bogdanić, A. (2013). Sources and energy management in industry. Zagreb: Element. ISBN 9789531976725.
- Croatian Meteorological Bulletin Climatic Data. (1997). Zagreb: Geophysical Institute.
- Demirel, Y. (2012). Energy production, conversion, storage, conservation, and coupling. Chapter 9. In Energy. Series: Green Energy and Technology (pp. 229–303). London: Springer. ISBN: 978-1-4471-2371-2.
- Eastop, T. D., & Croft, D. R. (Eds.). (1995). Energy efficiency for engineers and technologists (2nd ed.). Longman Group Ltd. ISBN 0582031842.
- Flue Gas Heat Recovery. (2012). Power Systems by Babcock Borsig Steinmüller GmbH. Brochure. Retrieved from https://www.bbs.bilfinger.com/fileadmin/power_steinmuller/Mediathek/Broschuere_Rauchgasw_rmenutzung_BBS_web_E.pdf
- Goswami, D. Y. (Ed.). (2015). Principles of solar engineering (3rd ed.). Taylor & Francis group LLC. ISBN 9781466563797.
- Goswami, D. Y., & Kreith, F. (Eds.). (2016). Energy efficiency and renewable energy handbook (2nd ed.). Taylor & Francis group LLC. ISBN 9781466585096
- Hegde, R. R., Dahiya, A., Kamath, M. G., Kotra, R., & Gao, X. (2004). Polyester fibers. University of Tennessee. Retrieved from https://www.engr.utk.edu/mse/Textiles/Polyester%20fiber.htm
- Kalogirou, S. (Ed.). (2009). Solar energy engineering: Processes and systems. Elsevier. ISBN 978-0-12-374501-9.
- Karagiorgas, M., Botzios, A., & Tsoutsos, T. (2001). Industrial solar thermal applications in Greece: Economic evaluation; quality requirements and case studies. Renewable and Sustainable Energy Reviews, 5, 157–173.10.1016/S1364-0321(00)00012-5
- Lund, P. D. (2016). Clean energy systems as mainstream energy options. International Journal of Energy Research, 40, 4–12.10.1002/er.3283
- Mihelić-Bogdanić, A., & Budin, R. (2006). Energy effective polyester production. In Katalinic, B. (Eds.), DAAAM International Scientific Book 2006 (pp. 075–080). Viena: DAAAM International.
- Mihelić-Bogdanić, A., & Budin, R. (2009). Impact of heat recovery and resource diversification in industrial process. In B. Katalinić (Ed.), Chapter 12. In DAAAM International Scientific Book (pp. 107–116). Vienna: DAAAM International. ISBN 978-3-901509-69-8.
- Mihelić-Bogdanić, A., & Budin, R. (2014). Boiler flue gases as secondary source in polyester production. International Journal of Energy Engineering, 4, 83–88.
- Mihelić-Bogdanić, A., Budin, R., & Filipan, V. (1999). Heat recovery and solar energy in polyester production. Renewable Energy, 16, 2154–2157.
- Mihelić-Bogdanić, A., Budin, R., & Sutlović, I. (2000). Solar energy system and waste heat recovery in industrial process. In A. A. M. Sayigh (Eds.), Proceedings of World Renewable Energy Congress VI (WREC2000) (pp. 1094–1098). Brighton.
- Mihelić-Bogdanić, A., Budin, R., & Sutlović, I. (2002). Solar energy application in termoplastics production. In Proceedings of the World Renewable Energy Congress (388/1–5). Koln.
- Mohd Fadzil, N. A., Ab. Rahim, M. H., & Maniam, G. P. (2014). A brief review of para-xylene oxidation to terephthalic acid as a model of primary C-H bond activation. Chinese Journal of Catalysis, 35, 1641–1652.10.1016/S1872-2067(14)60193-5
- Potter, M. C., & Somerton, C. V. (1993). Schaum’s outline of theory and problems of engineering thermodynamics. New York, NY: McGrow–Hill. ISBN 0070506167.
- Požar, H. (1992). Fundamentals of energetics (in Croatian). Zagreb: Školska knjiga. ISBN 8603991650.
- Renewable Energy in Industrial Applications. (2010). An assessment of the 2050 potential (Technical paper). Vienna: United Nations Industrial Development Organization.
- Rodriguez, F., Cohen, C., Ober, C. K., & Archer, L. (2015). Principles of polymer systems (6th ed.). Boca Raton, FL: CRC Press, Taylor & Francis Group.
- Smith, W. F. (1990). Principles of materials science and engineering (2nd ed.). New York, NY: McGraw–Hill.
- Stevens, M. P. (1999). Polymer chemistry. An introduction. (3rd ed.). Oxford: Oxford University Press.
- Thumann, A. (2002). Plant engineers & managers; Guide to energy conservation (8th ed.). Lilburn, GA: The Fairmont Press.
- Turner, W. C. (Ed.). (2012). Energy management handbook (8th ed.). Fairmont Press. ISBN 9781466578289.
- Vannoni, C., Battisti, R., & Drigo, S. (2008). Potential for solar heat in industrial processes. Madrid: CIEMAT.
- Vineetha, C. P., & Babu, C. A. (2016). Optimal unidirectional grid tied hybrid power system for peak demand management. Advances in Energy Research, 4, 47–68.10.12989/eri.2016.4.1.047
- Weiss, W., & Biermayr, P. (2010). Potential of solar thermal in Europe. European Solar Thermal Industry Federation. Retrieved from www.estif.org