Abstract
The intent of the present research work is to explore the prospect of replacing natural soil used in brick making by some extent with industrial waste, that is, lime mud, as obtained from paper mill waste. Extensive adoption of this mill waste as a brick making material will deter the environmental effects of this waste disposal. Moreover, its adoption will not only solve the problem of stocked waste piles but also scale down the usage of natural soil as a brick making material. In consideration of the central intend of this study to utilize industrial waste as an alternate raw material, yet another industrial waste—fly ash, has also been blended to the mix to manufacture unburnt bricks, such that, it may produce cementitious compounds with lime mud. So, the materials used for brick making in this study are: lime mud, collected from the dumping site of M/s Hindustan Paper Corporation Limited, Jagiroad, Assam, India; soil, collected from a brick manufacturing unit also near Jagiroad; and fly ash, collected from National Thermal Power Station, Badarpur, Delhi, India. The materials have been characterized with respect to their chemical and geotechnical properties. Then, experiments have been conducted on hand-moulded bricks of aforementioned mix in distinct proportions. In this study, all the bricks have been dried in the natural condition and then tested for compressive strength conforming to International standards. It has been duly noted that none of the treated unburnt bricks satisfies the requirements of standard codes. Nonetheless, in case of burnt bricks, the compressive strength satisfies the requirements of International standard codes wherein lime mud has been added up to a certain percentage (=20%) in soil-lime mud mix.
Public Interest Statement
Due to ever-increasing problem of pollution, there is an immediate need for the communities and industries to come up with radical measures such as strict environmental regulations, and cleaner waste disposal technologies. The intent of the present research work is to explore the prospect of replacing natural soil used in brick making by some extent with industrial waste, that is, lime mud, as obtained from paper mill waste. Extensive adoption of this mill waste as a brick making material will deter the environmental effects of this waste disposal. Moreover, its adoption will not only solve the problem of stocked waste piles but also scale down the usage of natural soil as a brick making material.
1. Introduction
The ever-increasing environmental pollution causing grave and irreparable damage to mother Earth is one of the momentous dilemmas that the world is facing today. There is an immediate need for the communities and industries to come up with radical measures such as strict environmental regulations, and cleaner waste disposal technologies. Waste handling is also a burning issue in all industrial plants as well as in pulp and paper industries. One such prompt measure for waste management is re-using and recycling generated industrial waste for applications such as building material and construction processes. The re-use of waste is meaningful from a variety of viewpoints such as: to save and sustain the natural building material resources; to mitigate the pollution caused by stocked waste piles; and to save utilized energy in production processes (Hassani, Ganjidoust, & Maghanaki, Citation2005; Rocha & John, Citation2003). The productive re-use of waste material represents a way of solving the major concern of solid waste management (Davis & Cornweel, Citation1998). This is so because, suitable waste disposal landfill sites are becoming more and more difficult to locate due to expanding urbanisation, poor landfill capacity and unsuitable buffer zones (Ngoc & Schnitzer, Citation2009). Therefore, industrial waste and by-products could be valuable alternative resources for building construction and other applications (van Beers, Bossilkov, & Lund, Citation2009). Numerous attempts have been made to incorporate industrial waste in the production of bricks, for illustration, the usage of textile effluent treatment plant sludge, cotton waste, rice husk ash, granulated blast furnace slag, processed waste tea, petroleum effluent treatment plant sludge, craft pulp production residue and waste paper pulp (Balasubramanian, Sabumon, John, & Ilangovan, Citation2006; Demir, Citation2006; Demir, Serhat, & Mehmet, Citation2005; Halil & Turgut, Citation2008; Malhotra & Tehri, Citation1996; Rahman, Citation1987; Raut, Sedmake, Dhunde, Ralegaonkar, & Mandavgane, Citation2012; Sengupta, Saikia, & Borthakur, Citation2002). The committals to conserve traditional building materials that may face depletion have compelled engineers to unearth cheaper alternative materials (Abang & Chandra, Citation1977). Recycling of such industrial wastes by blending them into building materials is a proficient solution to the pollution problem (Raut et al., Citation2012). This especially holds true for the paper and brick manufacturing units in Assam, India. Stimulating cooperation between these two large scaled production sectors can be a good scheme in terms of waste management (Modolo, Senff, Labrincha, Ferreira, & Tarelho, Citation2014). The Paper industry in Jagiroad is large tonnage one and is characterized by high energy consumption with subsequent generation of substantial quantities of waste of organic and inorganic origin. The primary disposal routes for paper sludge are: land-spreading as an agricultural fertilizer; combined incineration at heat and power plants at the paper mill; production of paper sludge ash; and disposal in a landfill site. Because of so many paper industries in Jagiroad, an even larger quantity of waste is generated. Paper fibres can be recycled or re-used only a finite number of times before they tend to become too weak or short to make high quality paper. This results in separation of broken, low-quality fibres as waste sludge. All the inks, pigments, dyes, staples, coatings and treatment by-products are also washed off along with recycled fibres to generate waste solids of paper and pulp industry (Bajpai, Citation2014). These paper mill sludges are eating-up a large percentage of local landfill space each year. Due to land spreading of waste on cropland as a disposal technique, there is a rising worriment of contaminants building up in soil or running off into area lakes and streams. Worse yet, some companies burn their sludge in incinerators, contributing significantly towards serious air pollution problems, including the release of dioxin.
Lime, either alone or in combination with other materials, can be used to treat wide spectrum of soil types. The mineralogical properties of soils determine their degree of reactivity with lime and the ultimate strength that the stabilized soil layers will develop (Sarkar, Abbas, & Shahu, Citation2012). In general, fine-grained clayey soils are considered good for stabilization with lime as a geotechnical admixture. Soils containing significant amount of organic materials (greater than about 1%) or sulphates (greater than 0.3%) may require additional lime and/or special constructional considerations. Stocked lime-mud waste from disposal site of Hindustan Paper Corporation Limited, Jagiroad Paper Mill, Dist.-Morigaon, Assam, India, may be used as an alternative cheaper source of geotechnical admixture such that bonding properties of soil used for brick making can be enhanced. This will not only destock the existing waste but also reduce the volume of natural soil currently used for brick making. Lime sludge waste as obtained from the dumping site of pulp and paper craft chemical units has no toxic substances, rather it contains about 66.2% calcium carbonate (refer Table ). Moreover, the heavy metals found in the lime mud are also below the set permissible level (Deka & Yasmin, Citation2006; Siqueira & Holanda, Citation2013). Henceforth, this lime sludge waste will cause no adverse effect to mortal-beings when used as one of the brick constructing material. Also, fly ash is a pozzolan which may be used along with lime to stabilize soils. Keeping this point in mind, an approach has been made for brick making wherein fly ash has been mixed with lime mud and soil.
Table 1. Chemical properties of lime mud from Jagiroad paper mill and marketed lime in India
Existing know-how illustrate that most soils can be satisfactorily stabilized with cement-lime. It is, however, necessary to conduct comprehensive tests on soils in laboratory in order to determine their optimum requirements for the specified properties. While in general building construction, soil based blocks may be used as a substitute for bricks, however, their usage should be avoided in the case of isolated load bearing columns, piers or such other heavily loaded structures (Indian Standard: 1725, Citation1997).
2. Types of waste produced
The amount/type of waste generated during paper production varies remarkably from mill to mill, because of adopted different recycling rates. However, in Jagiroad Paper Mill, following different types of solid wastes and sludge are produced. They are chiefly generated during wastewater treatment, pulping and deinking processes.
2.1. Wastewater treatment sludge
This sludge is produced from the treatment of wastewater via on-site (e.g. septic tank) and off-site (e.g. activated sludge) systems. This is inherently in such wise because principal objective of the treatment is to remove solids from the wastewater.
2.2. Lime mud
Lime mud is a by-product produced in pulp mills as part of the process that turns bamboo and wood chips into pulp for paper. Basically, pulp mill cooks bamboo and wood chips with sodium hydroxide (NaOH) to extract the bamboo and wood fiber, pre-requisites for paper manufacturing, from the lignin that binds the bamboo or wood together. During this process, sodium hydroxide (NaOH) is converted to sodium carbonate (Na2CO3). The pulp mill then adds calcium oxide (CaO), also known as quicklime, to convert the sodium carbonate (Na2CO3) back to sodium hydroxide (NaOH) such that it can be re-utilized. On account of this process, calcium carbonate (CaCO3) is generated.
Most of the generated waste is lime mud, which is about 40% to a unit of produced paper (Hynninen, Citation1998). The moisture content can be typically as high as 40%. The material so produced is highly viscous, sticky, difficult to dry and can vary in viscosity and lumpiness (Gendebien et al., Citation2001).
2.3. Grits
Grits are formed chiefly by chunks of calcium carbonate (CaCO3) and calcium oxide (CaO) which did not react in the slaker. Slaker is a set-up where the reaction between sodium carbonate (Na2CO3), present in green liquor clarifier; calcium oxide (CaO), lime coming from lime oven; and Water (H2O) occurs, giving sodium hydroxide (NaOH) plus calcium carbonate (CaCO3), which constitutes the lime sludge that will be filtered and re-cycled to lime oven for calcinations (Modolo, Benta, Ferreira, & Machado, Citation2010).
3. Materials used
All the materials have been collected personally, stored properly and procured freshly at the beginning of the study. The materials have been characterized in the Geotechnical Laboratory of Delhi Technological University as well as in Assam Engineering College for assurance. Whereas, environmental engineering laboratory of Delhi Technological University was used to determine chemical properties of lime mud and fly ash.
3.1. Characterization of lime mud
The lime mud has been tested as per the provisions of Indian standards (Indian Standard: 6932, Citation1973). The particle size distribution analysis, inclusive of both sieves and hydrometer analyses (Indian Standard: 2720 - (Part IV), Citation1985) has pointed out that the lime mud consists of around 66% silt-sized particles and 34% clay-sized particles (Figure ). The optimum moisture content (OMC) and maximum dry density (MDD) (Indian Standard: 2720 - (Part VII), Citation1980) have also been ascertained as 52.1% and 11.8 kN/m3, respectively. The chemical properties of lime mud from Jagiroad paper mill and marketed lime are mentioned in Table .
The morphological aspect of the waste particles has also been observed as depicted in scanning electron micrographs shown in Figures and . The lime mud powder consists of smooth, irregular-shaped particles typical of calcium carbonate. Tests have also been tried to determine the plastic properties of collected the waste sample. However, the non-cohesive nature of this solid waste material jeopardized the realization of these evaluations. Thus, the waste material can be classified as a non-plastic material in terms of geotechnical properties (Table ). The lime mud also shows slight electrical conductivity (4.37 mS/cm); thus, it can be classified as a non-pozzolanic material (Luxán, Madruga, & Saavedra, Citation1989).
3.2. Characterization of fly ash
The fly ash used in present investigation has been procured from Badarpur Thermal Power Plant, New Delhi, India. Chemical properties of Fly ash are listed in Table . The specific gravity of fly ash is 2.07 and is non-plastic in nature. The optimum moisture content (OMC) and maximum dry density (MDD) have also been ascertained as 32% and 12.2 kN/m3, respectively. The few geotechnical properties are mentioned in Table .
Table 2. Chemical properties of Badarpur fly ash
Table 3. Few geotechnical properties of lime mud, fly ash and soil
3.3. Characterization of soil
The soil available in the brick kiln near Jagiroad has been taken and tested as per the provisions contained in Indian standards (Indian Standard: 2720 - (Part IV), Citation1985; Indian Standard: 2720 - (Part V), Citation1985; Indian Standard: 2720 - (Part VII), Citation1980). The specific gravity of the soil is 2.64. Its liquid limit (LL), plastic limit (PL), and plasticity index (PI) are 37.2, 23.1, and 14.1% respectively. The value of OMC and MDD are listed in Table . A pictorial view of various materials used in this study is given in Figures –.
4. Methodology
Paper mill waste has been obtained from M/s Hindustan Paper Corporation Limited (HPCL), Jagiroad, Assam, India. The lime mud thus obtained from these wastes has been used for making bricks by mixing in different weight proportions with another industrial waste: fly ash; obtained from National Thermal Power Station, Badarpur, Delhi, India. The composed mixtures have been adjudged in accordance to Indian Standards (Indian Standard: 1725, Citation1997).
4.1. Fabrication of unburnt bricks
The brick samples of size 190 × 90 × 90 mm (Indian Standard: 12894, Citation2002) have been casted in Soil Mechanics laboratory of Delhi Technological University by blending lime mud and soil in 15:85, 20:80, 25:75, 30:70, 35:65 and 40:60 ratios respectively by dry weight. Modular bricks made of lime mud, fly ash and soil have also been casted in ratios of 15:10:75, 20:10:70, 25:10:65, 30:10:60, 35:10:55 and 40:10:50 respectively. The blended samples have been mixed with sufficient quantity of water to obtain working consistency for moulding. The clean mould has been filled with the above mix without allowing any air bubble. The surplus mix has then been removed such that top surface of the mould can be levelled. Since the bricks have been cast by hand, so no pressure has been applied on the mould. The moulded brick has then been allowed to dry for two days in such a manner that there is no direct contact with sun light. After that, the specimens are sun dried for two days and are kept in room temperature for 28 days. Fly ash and cement mixed bricks have been cured by moist jute bags for 7 and 28 days respectively. All bricks are then tested after 28 days for compressive strength as per the provisions of Indian standards (Indian Standard: 3495 (Part 1), Citation1992). Before testing, the frogs and voids of the specimen have been filled up. A pictorial view of the casted bricks is shown in Figure .
4.2. Fabrication of burnt bricks
The non-modular brick samples of size 230 × 110 × 70 mm (Indian Standard: 1077, Citation1997) have been casted using lime-mud and soil in ratios of 0:100, 5:95, 10:90, 15:85, 20:80, 25:75, 30:70, respectively by volume, at the brick manufacturing site of M/s Sri Bajrang Brick Manufacturing Company, Jagiroad; just 4 km away from the dumping site of M/s HPCL, Jagiroad Paper Mill. Since the prime motive of the present study is to maximise the usage of lime mud waste as a brick making resource, henceforth, fly ash and cement has been avoided in the soil—lime mud mix for the burnt bricks. The aforementioned blended samples have been mixed with sufficient quantity of water to obtain working consistency for moulding. The clean mould has been filled with the above mix without allowing any air bubble. The surplus mix has then been removed such that top surface of the mould can be levelled. Since the bricks have been cast by hand, so no pressure has been applied on the mould as depicted in Figures –. The moulded brick are dried as per the conventional method as shown in Figure for a week after which the dry bricks have been placed in kiln for burning. All the burnt bricks have been tested for compressive strength and water absorption as per the provisions of Indian standards (Indian Standard: 3495 (Part 1), Citation1992), respectively. Before testing, the frogs and voids of the specimen have been filled up.
5. Results and discussion
5.1. Unburnt bricks
The results of the present investigation are presented in Figures and . Figure shows the variation of compressive strength with percentage of lime mud. It has been discerned that with the increase of percentage of lime mud in soil-lime mud mix for brick manufacturing, the compressive strength of bricks also increases. The compressive strength is 1.18, 1.22, 1.30, 1.38, 1.41, 1.53, and 1.61 N/mm2 when the percentage of lime mud in the mix is 10, 15, 20, 25, 30, 35, and 40, respectively.
Similarly, Figure shows the variation of compressive strength with percentage of lime mud mixed with fly ash (10%). It has also been observed that with the increase of percentage of lime mud in soil–lime mud–fly ash (10%) mix, the compressive strength of bricks increases up till 30% and decreases thereafter. The compressive strength is 1.51, 1.56, 1.60, 1.64, 1.68, 1.67, and 1.66 N/mm2 when the percentage of lime mud in the mix is 10, 15, 20, 25, 30, 35, and 40, respectively.
Soil strength enhancement can be accomplished by blending good admixture such as cement or quicklime to soil (Van Inpe, Citation1989). In cohesive soils such as clay and heavy loam, improvements can be gained by adding quicklime during surface compaction. Figure shows the principle of soil stability with unslaked lime. From Figure , it can be observed that with the addition of lime mud in the mix, the compressive strength increases which bolsters the above statement.
Figure 18. Principle of soil stability with unslaked lime (Van Inpe, Citation1989).
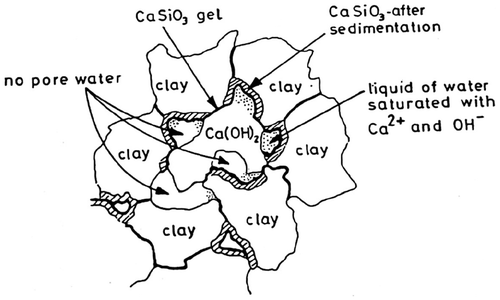
The behaviour of lime shows that strength shall increase up to a certain limit of lime (=8%) (Sarkar et al., Citation2012) and decrease thereafter. The increase in the strength due to lime stabilization confirms the pozzolanic nature of the fly ash, and thus its capability to react with lime and develop substantial strength. As stated earlier, further addition of lime in the fly ash beyond 8% decreases the compressive strength; possibly due to the fact that the silica present in the finer particles of fly ash is completely exhausted up to this value and addition of more lime actually becomes counterproductive thenceforth (Hausmann, Citation1990). From Figure , it can be observed that with the addition of lime mud in the mix of soil and fly ash (10%), the compressive strength increases up till 30% of lime mud and then decreases. The percentage addition of lime mud is almost four times of that quick lime, probably due to lower valuation of calcium carbonate and chloride content in lime mud as to marketed lime (Table ).
5.2. Burnt bricks
5.2.1. Compressive strength
The variation of compressive strength of burnt brick with percentage of lime mud is shown in Figure . The compressive strength is 3.61, 3.57, 3.54, 3.52, 3.46, and 3.33 N/mm2 when the percentage of lime mud in the mix is 0, 5, 10, 15, 20, and 25, respectively. The compressive strength of bricks casted by 30% lime mud could not be determined since various cracks have been seen in the surface of the bricks.
From Figure , it is noted that with the increase in percentage of lime mud in soil-lime mud mix for brick manufacturing, the compressive strength of burnt bricks decreases. It is established that during the firing, the bricks receive their strength. In the presence of high heat, the alkalis in the clay together with small amounts of oxides of iron and other metals are joined in chemical union with the alumina and silica of clay to form a dense and durable mass. As mentioned above, when lime is used for soil stabilization, the lime reacts with the clay minerals, creating a gel of calcium silicate which is insoluble in water and binding the soil particles together. But during the process of heating of bricks, perhaps the gel loses its strength and thus decreases the compressive strength of the bricks.
5.2.2. Water absorption
In case of ordinary bricks, when tested in accordance with the procedure laid down in (Indian Standard: 3495 (Part 2), Citation1992) after immersion in cold water for 24 h, water absorption shall not be more than 20%. But in the present case the range of water absorption of bricks lies between 22–27% in all composition of soil–lime mud bricks.
6. Conclusions
This paper presents the details of feasibility of replacing natural soil used in brick making by some extent with lime mud waste, as obtained from dumping site of a paper mill in Assam, India. Laboratory tests have been conducted on the hand-moulded bricks composed of varied weighted proportions. Based on the study presented in previous sections, following site-specific conclusions may be drawn:
(1) | Lime mud is a low-cost, calcium carbonate rich material that can be used as a binder cum inert filler material to improve the packing and densification of soil based bricks. | ||||
(2) | Since lime mud is a waste material and can be utilise free of cost for brick making, so brick manufacturing by using it is economical, beneficial to society, and environmentally friendly. | ||||
(3) | The compressive strength of unburnt bricks increases with lime mud proportion. | ||||
(4) | The compressive strength of bricks increases to a certain limit (=30%) with the addition of lime mud in fly ash (10%)—soil mix. | ||||
(5) | The compressive strength of unburnt bricks increases with addition of cement in the lime mud (30%)—fly ash (10%)—soil mix. | ||||
(6) | In the present study, the compressive strength of unburnt bricks in all the trials is found to be less than 2 N/mm2 which does not fulfil the criteria of minimum compressive strength of bricks as per (Indian Standard: 1725, Citation1997). | ||||
(7) | As per (Indian Standard: 1077, Citation1997), the minimum compressive strength of common burnt clay bricks should be 3.5 N/mm2. Whereas in the present study, the burnt bricks possessed compressive strength of 3.46 N/mm2 (≈3.5 N/mm2) when soil is mixed with up to 20% lime mud, by volume. |
List of abbreviations | ||
Al2O3 | = | Aluminium Oxide |
Ca | = | Calcium |
Ca2+ | = | Calcium Ion |
CaCO3 | = | Calcium Carbonate |
CaO | = | Calcium Oxide (Lime) |
Ca(OH)2 | = | Calcium Hydroxide |
CaSiO3 | = | Calcium Silicate |
CBR | = | California Bearing Ratio |
Fe2O3 | = | Ferric Oxide |
HPCL | = | Hindustan Paper Corporation Limited |
H2O | = | Water |
LOI | = | Loss on Ignition |
LL | = | Liquid Limit |
MgO | = | Magnesium Oxide |
MDD | = | Maximum Dry Density |
Na2CO3 | = | Sodium Carbonate |
NaOH | = | Sodium Hydroxide |
NTPC | = | National Thermal Power Corporation |
OH− | = | Hydroxide ion |
OMC | = | Optimum Moisture Content |
PCBA | = | Pollution Control Board, Assam |
PI | = | Plasticity Index |
PL | = | Plastic Limit |
SiO2 | = | Silica |
Funding
This work was supported by Pollution Control Board, Govt. of Assam, India [grant number WB/Z-I/T-1014/AIR/03-04/314].
Additional information
Notes on contributors
Raju Sarkar
The first author Dr Raju Sarkar is a civil engineer at the College of Science and Technology, Royal University of Bhutan with interests in earthquake and environmental geotechnology, soil-structure interaction, vulnerability and risk assessment, and disaster management education. He heads the University’s Disaster Risk Reduction and Community Development Studies Centre and led a research team that retrofitted a multi-storey building in Kathmandu after the 2015 Gorkha earthquake. In Bhutan, he currently works on vulnerability and risk assessment of traditional buildings within the country.
References
- Abang, A. A., & Chandra, S. (1977). Waste materials used in concrete manufacturing. Westwood, NJ: Noyes Publications.
- Bajpai, P. (2014). Generation of waste in pulp and paper mills. Management of pulp and paper mill waste (1st ed.). New York, NY: Springer.
- Balasubramanian, J., Sabumon, P. C., John, U., & Ilangovan, R. (2006). Reuse of textile effluent treatment plant sludge in building materials. Waste Management, 26(1), 22–28.
- Davis, M. L., & Cornweel, D. A. (1998). Introduction to environmental engineering (3rd ed.). New York, NY: WCB McGraw-Hill.
- Deka, S., & Yasmin, S. (2006). Utilization of lime sludge waste from paper mills for fish culture. Current Science, 90(8), 1126–1129.
- Demir, I. (2006). An investigation on the production of construction brick with processed waste tea. Building and Environment, 41(9), 1274–1278.
- Demir, I., Serhat, M., & Mehmet, O. (2005). Utilization of kraft pulp production residues in clay brick production. Building and Environment, 40(11), 1533–1537.
- Gendebien, A., Ferguson, R., Brink, J., Horth, H., Sullivan, M., & Davis, R. (2001). Survey of wastes spread on land—Final report. Study contract B4-3040/99/110194/MAR/E3. Luxembourg: European Commission Directorate General for Environment. ISBN 92-894-1732-3.
- Halil, M. A., & Turgut, P. (2008). Cotton and limestone powder waste as brick material. Construction and Building Material, 22, 1074–1080. S0950061807000736.
- Hassani, A., Ganjidoust, H., & Maghanaki, A. A. (2005). Use of plastic waste (poly-ethylene terephthalate) in asphalt concrete mixture as aggregate replacement. Waste Management and Research, 23(4), 322–327. doi:10.1177/0734242X05056739
- Hausmann, M. R. (1990). Physical and chemical modification. Engineering principles of ground modification (Part-IV). Singapore: McGraw Hill.
- Hynninen, P. (1998). Environmental control. Papermaking science and technology (Vol. 19). Helsinki: FapetOy. ISBN 9525216195.
- Indian Standard: 1077. (1997). Common burnt clay building bricks- specification. New Delhi: Bureau of Indian Standards.
- Indian Standard: 12894. (2002). Specification for pulverized fuel ash-lime bricks. New Delhi: Bureau of Indian Standards.
- Indian Standard: 1725. (1997). Specification for soil based blocks used in general building construction. New Delhi: Bureau of Indian Standards.
- Indian Standard: 2720 - (Part IV). (1985). Methods of test for soils: Determination of grain size analysis. New Delhi: Bureau of Indian Standards.
- Indian Standard: 2720 - (Part V). (1985). Methods of test for soils: Determination of liquid and plastic limit. New Delhi: Bureau of Indian Standards.
- Indian Standard: 2720 - (Part VII). (1980). Methods of test for soils: Determination of water content-dry density relation using light compaction. New Delhi: Bureau of Indian Standards.
- Indian Standard: 3495 (Part 1). (1992). Methods of tests of burnt clay building bricks: Part 1: Determination of compressive strength. New Delhi: Bureau of Indian Standards.
- Indian Standard: 3495 (Part 2). (1992). Methods of tests of burnt clay building bricks: Part 2: Determination of water absorption. New Delhi: Bureau of Indian Standards.
- Indian Standard: 6932. (1973). Methods of tests for building limes. New Delhi: Bureau of Indian Standards.
- Luxán, M. P., Madruga, F., & Saavedra, J. (1989). Rapid evaluation of pozzolanic activity of natural products by conductivity measurement. Cement and Concrete Research, 19(1), 63–68. doi:10.1016/0008-8846(89)90066-5
- Malhotra, S. K., & Tehri, S. P. (1996). Development of bricks from granulated blast furnace slag. Construction and Building Materials, 10(3), 191–193.
- Modolo, R., Benta, A., Ferreira, V. M., & Machado, L. M. (2010). Pulp and paper plant wastes valorisation in bituminous mixes. Waste Management, 30(4), 685–696. doi:10.1016/j.wasman.2009.11.005
- Modolo, R. C. E., Senff, L., Labrincha, J. A., Ferreira, V. M., & Tarelho, L. A. C. (2014). Lime mud from cellulose industry as raw materials in cement mortars. Construction Material, 64(316), 1–9. doi:10.3989/mc.2014.00214
- Ngoc, U. N., & Schnitzer, H. (2009). Sustainable solutions for solid waste management in Southeast Asian countries. Waste Management, 29(6), 1982–1995.
- Rahman, M. A. (1987). Properties of clay-sand-rice husk ash mixed bricks. International Journal of Cement Composites and Lightweight Concrete, 9(2), 105–108.
- Raut, S. P., Sedmake, R., Dhunde, S., Ralegaonkar, R. V., & Mandavgane, S. A. (2012). Reuse of recycle paper mill waste in energy absorbing light weight bricks. Construction and Building Materials, 27(1), 247–251. S0950061811004077.
- Rocha, J. C., & John, M. W. (2003). Use of residues in housing construction. Porto Alegre: Coletânea Habitare.
- Sarkar, R., Abbas, S. M., & Shahu, J. T. (2012). A Comparative study of geotechnical behaviour of lime stabilized pond ashes from Delhi region. International Journal of Geomate, 3(1), 273–279.
- Sengupta, P., Saikia, N., & Borthakur, P. C. (2002). Bricks from petroleum effluent treatment plant sludge: Properties and environmental characteristics. Journal of Environmental Engineering, 128(11), 1090–1094.
- Siqueira, F. B., & Holanda, J. N. F. (2013). Reuse of grits waste for the production of soil–cement bricks. Journal of Environmental Management, 131, 1–6. S0301479713006403.
- van Beers, D., Bossilkov, A., & Lund, C. (2009). Development of large scale reuses of inorganic by-products in Australia: The case study of Kwinana, Western Australia. Resources Conservation and Recycling, 53(7), 365–378.
- Van Inpe, W. F. (1989). Lime and cement stabilization for surface compaction. Principles of ground modification. Netherlands: McGraw Hill.