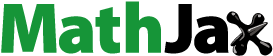
Abstract
Food, pharmaceutical, mineral and petroleum industries often use fluidized bed dryers for the drying process. In the present study, fluidized bed dryers in the tea processing industry is of particular interest. The main aim of this work is to investigate the effect of on the static bed height on the the coefficient of heat transfer in the fluidized bed dryer. In addition, the effect of particle size variations on the bed pressure drop in a fluidized bed dryer is also explored based on the computational fluid dynamics (CFD) approach. The multiphase, solid, and gas Eulerian-Eulerian models are employed to investigate the behavior of the fluidized bed dryers. The solid gas interphase interactions is predicted by the Syamlal O’Brien and Gidaspow drag models. To get more accurate results, a 3D fluidized bed model is applied. The analysis is performed by varying the particle sizes and the static bed heights. The simulation results show that the pressure drop increases with the increase in the particle size in the fluidized bed dryer. In addition, the effect of bed height variations on the coefficient of the heat transfer is also quite significant. The difference in the coefficient of the heat transfer values for each height of the static bed is highlighted. It is also found that when the height of the bed is higher, the efficiency of air to particle heat transfer becomes lower.
PUBLIC INTEREST STATEMENT
The industrial use of dryers is widely used and is continuously being developed to meet the needs of more and more varied products. One commonly used dryer is the fluidized bed dryer because of its effectiveness. A fluidized bed dryer is a tool that uses warm air to reduce water content and humidity from the product. Fluidized bed dryer performance includes pressure drop and coefficient heat transfer. There are many characteristics and operational parameters that influence fluidized bed dryer performance. The present study analyzed the effects of particle diameter and bed height on a bed dryer using the CFD method. Numerical results show that the increase in particle diameter and bed height can improve the drying process.
1. Introduction
Tea is one product that is often consumed and is also the main export commodity in several developing countries in the tropics (Onduru et al., Citation2012). Indonesia is one of the tea exporting countries and is ranked eighth in the world in 2017 (Kementan, 2017). Tea is a very important commodity. However, the tea sector faces many challenges such as high production costs, poor processing and poor processing management, high additional expenditure costs, low employee productivity, climate change, and poor infrastructure. Also, many tea fields are converted for cocoa, palm oil, coffee, and other horticultural crops because they have a higher selling price. In the last two decades, tea has experienced a price decline of around 35%. Tea quality improvement must meet the standards of Good Agriculture Practice (GAP); Good Manufacture Process (GMP), and product quality standards as required by ISO (Ahmed & Stepp, Citation2016).
There are several processes in processing tea, especially the drying process. The drying process is useful for stopping fermentation and reducing water content in tea leaves. For tea leaves which do not dry or even burn, the drying process must be monitored properly. There are two types of drying techniques commonly used, namely conventional drying techniques and fluidization. Traditional drying techniques use the heat generated from burning wood. Consequently, carcinogenic substances resulted from burning logs can reduce the quality of the tea leaves because of the reduced content of polyphenols, which are antitumor substances (Kim et al., Citation2007). Also, pollution caused by the combustion process endangers the health of workers and consumers. Smoke from burning wood (organic material) triggers and raises levels of Polycyclic Aromatic Hydrocarbon (PAH) in tea. These Polycyclic Aromatic Hydrocarbon (PAH) substances are carcinogenic and mutagenic, these properties are believed to contribute to the formation of cancer cells (Syahrul et al., Citation2002; Engelman et al.,Citation2007). Fluidization is a drying technique that reduces or eliminates moisture in wet particles/solids and converts the moisture into gas (evaporation). This technique is called convective drying. The fluidization technique uses a fluidized bed dryer as the drying medium. Fluidized bed dryers are generally used for drying processes on solid objects because they have significant mass and heat transfer rates, so they can cut drying time (Yohana et al., Citation2018). The working principle of a fluidized bed dryer is to blow hot air into the reservoir so that the particles in the reservoir can float (Bodhanwalla & Manickam, Citation2017).
Recently, with the rapid development of hardware and computer technology, many researchers employed computational fluid dynamics (CFD) codes for studying the fluidized bed dryers. Abdelmotalib et al. (Citation2016) analyzed the wall-to-bed flow characteristics and heat transfer in a conical fluidized bed combustor. They found that the heat transfer coefficient and pressure drop increase with increasing gas velocity. Heat transfer from the walls heated in the fluidized bed Eulerian-Eulerian approach was also carried out by Armstrong, Gu and Luo in 2010. Simulations were carried out using CFD to capture the characteristics of heat transfer in the downers. Simulations were carried out to determine the effect of constant air property, friction between particles, heat transfer between particles, and different granular kinetic theory flow. In 2005, Chiesa et al. numerically examined the flow behaviour of laboratory scale fluidized beds and compared their results with the experiment. The results showed that the simulation data tends to have the same flow pattern as the experimental data when the Eulerian and Lagrangian approaches were applied.
There are two approaches applied in modelling gas and solid phases in fluidized bed dryers, namely the Eulerian-Lagrangian model and the Eulerian-Eulerian model. In the Eulerian-Lagrangian method, gas and solid phases are treated continuously and undergo discretization. This model is solved using Newton’s second law of motion, because the particle collisions and forces act on gas phase particles. The Eulerian-Eulerian model is a model commonly used in the simulation of gas and solid phases in a fluidized bed dryer. With this approach, the solid-gas phase is treated as continuous with a balance of continuity and momentum. The thermal energy equation is applied to both phases with appropriate boundary conditions (Askaripour & Dehkordi, Citation2015).
Various studies have implemented a Two-Fluid Model (TFM) to simulate fluidized bed dryers. Conservation of mass and the balance of momentum for solid and gas phases are applied in hydrodynamic simulations of the bubbling phenomenon in fluidized beds. Kinetic theory of granular flow (KTGF) is used in TFM to describe collisions between particles. Also, Kinetic theory of granular flow (KTGF) can analyze the flow phenomena in fluidized bed dryers and predict particle pressures using turbulent models (Enwald & Almstedt, Citation1999). Extending the main frame of the advantage of the fluidized bed dryers, it is necessary to simulate the effect of variations in particle size and the effect of bed height variations on heat transfer in the fluidized bed dryer using computational fluid dyanamics (CFD) approach. A three-dimensional (3D) models are employed in this study to get more accurate results.
2. Methodology
2.1. General equations
The Eulerian-Eulerian model is used to model the interaction between gas and solids in a fluidized bed dryer. Interactions between the two phases are solved using mass and momentum conservation equations. Multiphasic mass conservation equations for incompressible fluid flows are shown in EquationEquations (1)(1)
(1) and (Equation2
(2)
(2) ) below (Ngoh & Lim, Citation2016).
where ε is the volume fraction, ρ is the density of tea particles, and v is the velocity, while subscripts g and s denote gas and solid, respectively.
EquationEquation (3)(3)
(3) is the conservation of momentum in a multiphase gas-solid case (Ngoh & Lim, Citation2016).
where K is thermal conductivity, τ is Reynold’s tensor voltage, and g is the gravitational acceleration.
Multiphase energy equation as shown in EquationEquation (5)(5)
(5) reads: (Abdelmotalib et al., Citation2016)
The Reynolds number is the ratio between the force of inertia to the viscous force which quantifies the relationship of the two forces with a particular flow source. For particles (i.e. solid), Reynolds number is shown in EquationEquation (7)(7)
(7) (Cengel & Cimbala, Citation2018):
In the Reynold number equation, is the air flow viscosity and
is the particle diameter. The Prandtl number is a comparison between momentum diffusivity and thermal diffusion. EquationEquation (8)
(8)
(8) is a Prandtl number (Cengel & Cimbala, Citation2018):
The Nusselt number is a dimensionless value that determines heat transfer in the flow. The Nusselt number used in this flow is shown in EquationEquation (9)(9)
(9) (Abdelmotalib et al., Citation2016):
where is the volume of air fraction and
is convection heat transfer.
The turbulent K-ε model is commonly used to solve several equations in turbulent applications. The model can be written as in EquationEquation (10)(10)
(10) and EquationEquation (11)
(11)
(11) (Jones & Lauder, Citation1972)
For K:
For :
k is turbulent kinetic energy and is the rate of turbulent energy dissipation.
where
The most fundamental characteristic of a fluidized bed dryer is the relationship between pressure drop and gas velocity (superficial gas velocity).The flow of gas that moves up and down the material grains creates a drag force (Fd) and buoyancy force (buoyancy force) on the particle. In the physical model adopted here, the air flow that passes through solid objects (i.e. particles) will have the drag force. External flow is influenced by fluid flow and the geometry of the object. The relative air velocity in objects that are enveloped in air flow and moving away from objects (outside the boundary layer) is called free stream velocity (Cengel & Cimbala, Citation2018). Increasing the speed of gas entering the fluidized bed causes an increase in pressure drop (∆P) and drag force on the particles. When drag force and buoyancy force generated by the velocity of gas entering pounding particles is balanced, the gravitational force (Fg), or the weight of the static bed, will experience a fluidization phenomenon. Figure shows the balance of forces acting when particles have a substantial impact on the air flow.
2.2. CFD model
Computational fluid dynamics, commonly called CFD, is a tool that can analyze fluid flow, heat transfer, and phenomena related to chemical reactions. This study uses a design from Ngoh and Lim (Citation2016) as seen in Figure ). The inlet, outlet, and wall geometry boundary conditions in the fluidized bed dryer are shown in Figure ). The dimensions of the fluidized bed dryer are shown in Table . ANSYS Fluid Flow (FLUENT) is used to solve the equations displayed on turbulent models. The volume control method is used to discretize three-dimensional Navier-Stokes equations. The SIMPLE scheme is used to make it easier to reach convergence. The solver uses the pressure-based method for incompressible flow. There are types of multiphase flow models used to determine inter-phase interactions. The approache of the Eulerian-Lagrangian model is used (Yohana et al., Citation2018). In this study, the Eulerian-Eulerian approach is employed to analyze the characteristics of hydrodynamics and heat transfer in the fluidized bed dryer. This approach only focuses on the control volume of particles not every single particle. Solid and gas phases in this model are described as converging continuously where the gas phase is the primary phase and the solid phase is the secondary phase. The use of kinetic temperature granular force (KTGF) aims to describe the viscous force, pressure, and collision between particles as a function of granular temperature which facilitates analysis of heat transfer and hydrodynamics (Moukalled et al., Citation2016). On completion of momentum, the scheme used is the QUICK scheme (Abdelmotalib et al., Citation2016; Inc. ANSYS, Citation2013). The second-order upwind scheme is used to determine the discretization of kinetic energy and the rate of dissipation equation (Abdelmotalib et al., Citation2016).
Table 1. Dimension of fluidized bed dryer
2.3. Boundary conditions and operating conditions
The boundary conditions and operating conditions are chosen based on the the material properties and air flow rates. This study uses two main phases, i.e. solid and gas, in which their properties are shown in Table . The air phase boundary conditions have a velocity value of 0.6 m/s with a temperature of 403 K, while for the solid phase, the velocity is assumed to be 0 m/s with a temperature of 298. In the present study, the particle size are varied from 360 µm, 450 µm, and 570 µm. The height of the bed particles are varied from 0.147 m, 0.158 m, 0.166 m and 0.175 m. The following assumptions are used, i.e.
There is no chemical reaction during the drying process
Gas—solid are well mixed
No slip conditions are assumed
The moisture is not considered
Tea particle size is kept constant during drying process
Table 2. Values of the operating conditions
A pressure outlet is a result of defining the outlet side to be simulated, where the pressure coming out is equal to the amount of atmospheric pressure so that the gauge pressure is zero for the air and solid phases. There is no heating on the wall and stationary wall. Wall boundary conditions are divided into two phases, namely the air phase and solid. Gas and solid particle are well mixed. The air wall phase is defined as no slip and the solid wall phase is defined as a specularity coefficient with a value of 0.5. In this study, the control method used was a discretization model of second order upwind, quick volume fraction, implicit second order, and simple for pressure-velocity coupling so that the calculations carried out in the simulation process will be more detailed.
2.4. Grid generation
Grid size will affect the accuracy of a CFD analysis. The smaller grid size, the more results are obtained, but it requires computing power and a longer time than the bigger size grid (Yohana, Citation2018). To get the grid results that are appropriate but do not depend on size, a calculation of the number of elements is done so that the number of elements is relevant. The number of rejected elements is shown in Table . From Table it can be seen that the number of elements, as many as 65,000, has an error value of 0.74% from the overall simulation results. The mesh size of the grid generation has min size 1.4 x e−3 mm, max size 5.4 mm and max face size 1.9 mm. The box used in this study is a hexahedral box with an element number of 68,950 and mesh size is. The grid generation is shown in Figure .
Table 3. Independent grid results
3. Results and discussion
The results of the simulation series that have been carried out show a pressure drop graph that is influenced by variations in solid particle size in the fluidized bed dryer. Particle size variations were 360 µm, 450 µm, and 570 µm with air velocities of 0.92 m/s. Bed particle height varied by 0.147 m, 0.158 m, 0.166 m, and 0.175 m. The fluidized bed dryer was heated by flowing hot air constantly at 130°C from the initial particle temperature of 25°C. Analysis was carried out on solid volume fraction profiles and temperature profiles to explain the heat transfer that occurred.
3.1. Validation
Numerical simulation results must be verified through validation with experimental data in the same conditions. The simulation results in this study are compared with the results of experimental studies conducted by Abdelmotalib et al. (Citation2016). Validation is done by comparing the pressure drop that occurs. Pressure drop is obtained from the difference in static pressure in the inlet and outlet parts (). Figure shows a comparison of the simulation results and experimental results. The comparison results obtained an average error of 1.388%, with the highest error of 3.25% and the lowest of 0.51%. Data from the validation results are shown in Table .
Table 4. Perhitungan validasi pressure drop
3.2. Effect of particle size and bed height on fluidized bed dryer
Simulations are carried out repeatedly by varying the bed height and particle size in tea particles to maintain operating parameters and material properties. Heat transfer between tea and air occurs because of the coveted heat transfer coefficient. Hot air will flow to the fluidized bed with a temperature of 130 °C from the initial temperature of the particles 25 °C. The particle sizes used were 360 μm, 450 μm, and 570 μm. Bed height was 0.147 m, 0.158 m, 0.166 m, 0.175 m and the air velocity used was 0.92 m/s.
The analysis was carried out on a solid volume fraction profile to explain the heat transfer that occurred. Figure shows the contour of solid volume fraction (solid volume fraction) at a speed of 0.92 m/s.
Figure 5. The contour of solid volume fraction at 360 µm particle size with bed height 0.147 m at a speed of 0.92 m/s
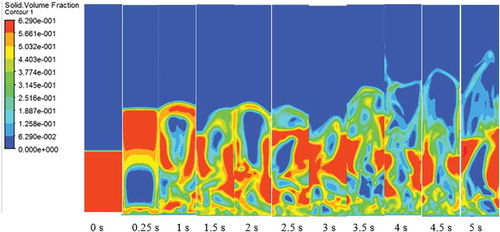
Figures – shows the contours of the solid volume fraction from seconds to 0.25 s-5 s. At 0.25 s the exhaled air lifts the particles uniformly. After the air is exhaled continuously, it will spread to the fluidized bed as seen in the 1 s to 5 s seconds contours. The distribution of particles to all fluidized bed space is shown in red.
Figure 6. Contours of solid volume fraction at particle size 450 µm with bed height 0.147 m at a speed of 0.92 m/s
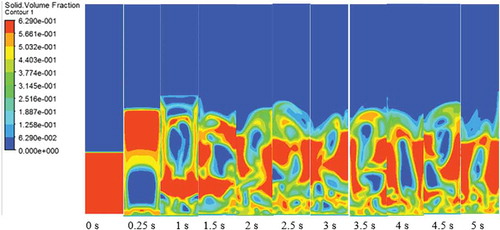
Figure 7. Contours of solid volume fraction at particle size 570 µm with bed height 0.147 m at a speed of 0.92 m/s
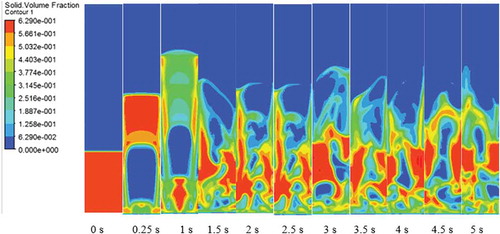
Figures – show that the particle concentration at the bottom tends to be lifted uniformly. This indicates that the air entering the fluidized bed dryer has a uniform velocity distribution. The flow of gas that enters the material grains creates a drag force (Fd) and buoyancy force (buoyancy force) on the particle, increasing the speed of air entering the fluidized bed causing a pressure drop (∆P) and the raising the drag force. When air is exhaled from the bottom of the fluidized bed, the particles will move in various directions. The movement of particles in various directions causes convection heat transfer. Heat transfer in a fluidized bed occurs in two conditions, namely between particles with walls and particles of tea and air. The characteristics of heat transfer can be seen from the value of the heat transfer coefficient. The method used to estimate the heat transfer coefficient in this study is the Gunn thermal method (Gunn, Citation1978). The results of the analysis of the heat transfer coefficient are shown in Figure .
Figure 8. The effect of bed height on the coefficient of heat transfer varying the particle sizes. (note: the velocity = 0.92 m/s)
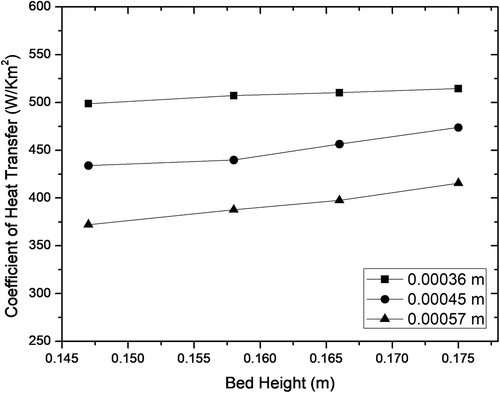
Regarding with the coefficient of the heat transfer studied here, based on Figure , there are several interesting features can be drawn. It should be noted that in the present study, the heat transfer coefficent was obtained from the numerical calculation by solving EquationEquations (8(7)
(7) –Equation9
(8)
(8) ). First, dealing with the effect of particle size, it can be found that a smaller particle size leads to the increase in the coefficient of heat transfer. And as a result, the heat transfer occurs more easily. The reason behind this is that smaller particles size will be more easily disposed in hot air compared to that with larger size. On the other words, exhaled air will envelop the particles leading to the acceleration of the heat transfer. In addition, small particles will more easily absorb hot air than large particles. Second, regarding with the effect of the height of the bed, it is can be revealed that increasing height of the bed makes the heat transfer become easier and consequently, the coefficient of heat transfer increases. Other interesting finding based on Figure is the fact that the increase in the coefficient of the heat transfer for the case with smaller particles size is not as high as the case with large particle size. This is because the distance of the particles from the heat source is growing while the heat distribution is lessening which makes the coefficient of heat transfer be smaller.
3.3. Effect of particle size on pressure drop in fluidized bed dryers
Tea particle size affects the value of the pressure drop fluidized bed dryer. Figure . shows that the pressure drop at each particle size fluctuates in 0–5 seconds. Fluctuations in pressure drop indicate that the fluidized bed dryer bubbles continuously. The graph shows that the larger the particle size, the higher the pressure drop. Bubble air pressure around the particles has a lower level than atmospheric pressure. It is because when the air is exhaled, the particles will float high and cause small bubbles to form, and the bubbles will fuse into more substantial bubbles, as seen in Figures –. All particles will float, and bubbles form evenly to meet fluidized beds over time.
The increase in pressure drop in each particle size also occurs at the height of the bed at 0.158 m, 0.166 m, 0.175 m, as shown in Figures –.
Figures –1 reveal that there is a correlation between the particle size and the pressure drop in the fluidized beds. The larger the particle sizes, the higher the pressure drop in the fluidized bed. Based on these figures, it can be found that when the particle size is small, the lower pressure drop is always observed as the time is increased. The most possible explanation is the fact that the small particles only require less pressure to lift. This result matches well with the work of Hamzehei (Citation2011). The highest values of the pressure drop are 3411.64 Pa, 2261.02 Pa, 2566.28 Pa, and 2521.35 Pa for each bed height for the case of the particle size of 570 µm.
The solid volume fraction contour for each particle size at 0.25 s is shown in Figure . Based on Figure , it can be shown that when the particle size increases, the elevation of the particles raises. Consequently, the higher pressure drop value in the fluidized bed dryer is generated. It leads to the increase in the number of floating particles. On the other words, based on Figure , the larger the particle size, the lower the particle can float.
4. Conclusion
In this study, 3D gas and a solid fluidized bed dryer were analyzed using the CFD method. Multiphase flow analysis uses the Eulerian-Eulerian model because it is more suitable with industrial scale fluidized bed dryer models. The system for reducing equations is solved using the finite volume method that applies the Semi implicit Method for Pressure-Linked Equations (SIMPLE) algorithm. Validation of the CFD method is used to ensure the method is used appropriately. Simulation results and literature indicate compliance.
Variations in the height of the bed particles affect the value of the heat transfer coefficient. The higher the particle bed height and the lower the particle size, the higher the heat transfer coefficient because when air scatters the particles, particles that have a smaller size will be easier to spread and absorb heat (with the particle heat transfer coefficient at an altitude of 0.147 m at 372.21 W/Km2, 433.98 W/Km2, and 498.64 W/Km2).
The effect of variations in particle size on pressure drop shows that the larger the particle size, the pressure drop will increase. When the particle size is small, the value of the pressure drop is less so that the collection of particles in the floating bed is higher compared to the size of the large particle.
The research also concluded that heat transfer is not affected by particle size, but a high coefficient of heat will cause a faster tea drying process which results in the increasingly minimal costs required for drying tea.
Nomenclature
= | Drag coefficient | |
= | Specific heat capacity | |
= | Reynolds number | |
= | Particle diameter | |
= | Solid restitution coefficient | |
= | Gravitational acceleration | |
= | Bed static height | |
= | convection heat tranfer coefficient | |
= | Gas-solid momentum exchange coefficient | |
= | conduction heat transfer coefficient | |
= | Lenght of Characteristic Geometry | |
= | Solid volume fraction | |
= | Fraction of Void (Air) | |
= | Density | |
= | Rate of conduction heat transfer | |
= | Rate of convection heat transfer | |
Nu | = | Nusselt number |
Pr | = | Prandtl number |
= | Surface Temperature | |
= | Temperature of Surrounding Fluid | |
= | Time | |
= | Superficial gas velocity | |
= | Superficial velocity for minimum fluidization | |
= | Upstream velocity | |
= | Kinematic viscosity of fluid | |
= | Thermal diffusivity | |
= | Dynamic viscosity of fluid | |
= | Velocity of Void (Air) | |
= | Roundness of particle | |
= | Pressure drop | |
= | Particle mass |
Additional information
Funding
Notes on contributors
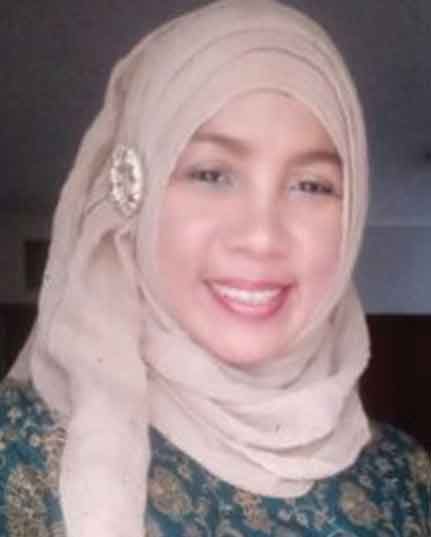
Eflita Yohana
Eflita Yohana received Doctoral degree in Mechanical Engineering from Pukyong National University, South Korea.
Muchammad
Muchammad received his Masters Degree in Mechanical Engineering from Gadjah Mada University.
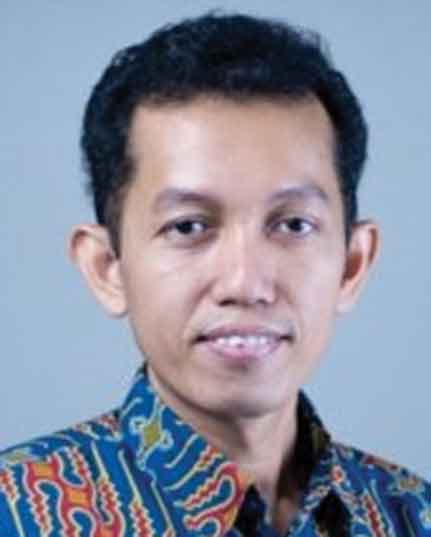
Mohammad Tauviqirrahman
Mohammad Tauviqirrahman is Head of Laboratory for Engineering Design and Tribology, Diponegoro University. He received his BEng in Mechanical Engineering from Diponegoro University in 2003, his Masters Degree (2006) in Mechanical Engineering from Institute of Technology Bandung, and his Doctorate (2013) in Laboratory for Surface Technology and Tribology, University of Twente, the Netherlands. His research interest is Computational Fluid Dynamics (CFD); both the fundamental basis and applications.
Awallina Ani Sayekti
Awallina Ani Sayekti received her Bachelor of Science in Mechanical Engineering from Diponegoro University, Indonesia.
Kwang-Hwan Choi
Kwang-Hwan Choi is a professor in the Departement of Refrigeration and Air Conditioning Engineering Pukyong National University, South Korea.
Vita Paramita
Vita Paramita her Doctorate from Laboratory of Food Engineering, Engineering Faculty from Tottori University, Japan.
References
- Abdelmotalib, H. M., Youssef, M. A. M., Hassa, A. A., Youn, S. B., Youn, S. B., & Im, I. T. (2016). Numerical study on heat transfer in a conical fluidized bed combustor considering particle elasticity. International Journal of Heat and Mass Transfer, 92, 236–16. https://doi.org/10.1016/j.ijheatmasstransfer.2015.08.069
- Ahmed, S., & Stepp, J. R. (2016). Beyond yields: Climate change effects on specialty crop quality and agroecological management. Elementa: Science of the Anthropocene, 4, 000092. http://doi.org/10.12952/journal.elementa.000092
- Armstrong, L. M., Gu, S., & Luo, K. H. (2010). Study of wall-to-bed heat transfer in a bubbling fluidised bed using the kinetic theory of granular flow. International Journal of Heat and Mass Transfer, 53(21–22), 4949–4959. https://doi.org/10.1016/j.ijheatmasstransfer.2010.05.047.
- Askaripour, H., & Dehkordi, A. M. (2015). Effects of initial static bed height on fractional conversion and bed pressure drop in tapered-in and tapered-out fluidized bed reactors. International Journal of Multiphase Flow, 79, 50–61. https://doi.org/10.1016/j.ijmultiphaseflow.2015.08.006
- Bodhanwalla, H., & Manickam, R. (2017). Parameters affecting the fluidized bed performance : A review parameters affecting the fluidized bed performance : A review. REST Journal on Emerging Trends in Modelling and Manufacturing, 3(1), 17–21.
- Cengel, Y. A., & Cimbala, J. M. (2018). Fluid mechanics (4th ed.). McGraw-Hill Education.
- Chiesa, M., Mathiesen, V., Melheim, J. A., & Halvorsen, B. (2005). Numerical simulation of particulate flow by the eulerian–lagrangian and the eulerian–eulerian approach with application to a fluidized bed. Computers & Chemical Engineering, 29(2), 291–304. https://doi.org/10.1016/j.compchemeng.2004.09.002
- Engelman, J. A., Zejnullahu, K., Mitsudomi, T., Song, Y., Hyland, C., Park, J. O., Lindeman, N., Gale, C. M., Zhao, X., Christensen, J., Kosaka, T., Holmes, A. J., Rogers, A. M., Cappuzzo, F., Mok, T., Lee, C., Johnson, B. E., Cantley, L. C., & Jänne, P. A. (2007). MET amplification leads to gefitinib resistance in lung cancer by activating ERBB3 signaling. Science, 316(5827), 1039–1043.
- Enwald, H., & Almstedt, A. E. (1999). Fluid dynamics of a pressurized fluidized bed: Comparison between numerical solutions from two-fluid models and experimental results. Chemical Engineering Science, 54(3), 329–342. http://dx.doi.org/10.1016/S0009-2509(98)00187-0
- Gunn, D. J. (1978). Transfer of heat or mass to particles in fixed and fluidised beds. International Journal of Heat and Mass Transfer, 21(4), 467–476. http://dx.doi.org/10.1016/0017-9310(78)90080-7
- Hamzehei, M. (2011). CFD modeling and simulation of hydrodynamics in a fluidized bed dryer with experimental validation. ISRN Mechanical Engineering, 131087, 9. http://dx.doi.org/10.5402/2011/131087
- Inc. ANSYS. (2013). ANSYS FLUENT theory guide, release 18.2.
- Jones, W. P., & Lauder, B. (1972). The prediction of laminarization with two equation model of turbulence’. Heat MassTransfer, 15, 302–314.
- Kim, J. S. et al. (2007) ‘antimicrobial effects of silver nanoparticles’, nanomedicine: nanotechnology, biology, and medicine, 3 (1),pp. 95–101. doi:10.1016/j.nano.2006.12.001
- Moukalled, F., Mangani, L., & Darwish, M. (2016). the finite volume method in computational fluid dynamics - an advanced introduction with openFOAM and MATLAB. Springer International Publishing.
- Ngoh, J., & Lim, E. W. C. (2016). Effects of particle size and bubbling behavior on heat transfer in gas fluidized beds. Applied Thermal Engineering, 105, 225–242. http://dx.doi.org/10.1016/j.applthermaleng.2016.05.165
- Onduru, D. D., De Jager, A., Hiller, S., & Van den Bosch, R. (2012). Sustainability of smallholder tea production in developing countries : Learning experiences from farmer field schools in Kenya. International Journal of Development and Sustainability, 1(3), 1–29. https://pdfs.semanticscholar.org/fa7e/a6a351b6b7823dec6be721e150387dc97b53.pdf
- Syahrul, S., Hamdullahpur, F., & Dincer, I. (2002). Exergy analysis of fluidized bed drying of moist particles. Exergy, An International Journal, 2(2), 87–98. http://dx.doi.org/10.1016/s1164-0235(01)00044-9
- Teaters, L., (2012). A Computational study of the hydrodynamics of gas-solid fluidized beds. Master Thesis, Faculty of the Virginia Polytechnic Institute and State University, https://doi.org/10.1094/PDIS-11-11-0999-PDN
- Yohana, E., Nugraha, A. P., Diana, A. E., Mahawan, I., & Nugroho, S. (2018). CFD analysis to calculate the optimal air velocity in drying green tea process using fluidized bed dryer. E3S Web of Conferences, 31, 01009. https://doi.org/10.1051/e3sconf/20183101009