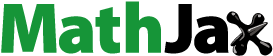
Abstract
This research paper explains the impact of dynamics viscosity of carbon nanotubes (CNTs) water base nanofluid for different parameter for both velocity and temperature profile. Similarity transformation is used to convert the partial differential equation to nonlinear ordinary differential equation. The solution of the problem is obtained using the optimal homotopy analysis method. The stability of the problems is also obtained up to the 30th order approximation using the BVPh 2.0 package. The outputs are displayed and discussed. The effects of various parameters on the skin friction coefficient and Nusselt number coefficient of single and multi-walled CNTs are displayed and discussed.
PUBLIC INTEREST STATEMENT
The flow of CNTs over a stretching surface is directly connected with industrial and engineering due to this flow heat transfer produced and heat transfer plays an important role in almost every industry because heat generation from power generation required high amount of cooling. The heat generated in our vehicle and air conditioning system require as well. Heat transfer also play a serious role in other industries such as food industries and micro sized application. So we use CNTs nanofluid in our research because CNTs is one of the most effective nanoparticle, the small concentration of CNTs having very high thermal conductivity. Thus, the public interest of this research is the study of thermo physical and heat transfer enhancement for the benefit of industries and engineering.
1. Introduction
Laminar flow is one of the most important problems in fluid dynamics. The problem is called blasius problem when the free stream appears to be parallel to the surface and fluid velocity behave as constant, and the problem is called wedge flow problem if the surface makes angle with the free stream. Due to the wide range of application in geothermal system, crude oil extraction, aerodynamics, heat exchangers, polymer processing chemical engineering processing wedge flow problem is more important area for the researchers. Falkner & Skan (Citation1931) are the first to work on this sector, they investigate wedge problem by using viscous incompressible two-dimensional fluid flows using similarity transformation and converting nonlinear partial differential equation to ordinary differential equation. Yih (Citation1998) investigates forced convection boundary layer flow over a wedge by using suction and injection. Watanabe (Citation1990) and Rajagopal et al. (Citation1983) used second-grade fluid to discuss wedge problem. Na (Citation1979) introduced group of transformation to transformed Falkner equation to two initial value problems and solved by forward integration scheme. Asaithambi (Citation1998) used finite difference scheme to solve Falkner and Skan equation. The nanofluid is defined as homogeneous mixture of nanosize fractional and base fluid. The base fluid such as oil ethylene and water having very poor thermal conductivity. To improve the thermal conductivity and heat transfer rate, we adding nanoparticle in the base fluid, so it will improve the thermal conductivity and heat transfer rate. To increase the thermal conductivity by this parses needs an undesirable increase in the size of thermal running system. So by taking into interpretation the rising weights of present technology covering chemical production, power stations and microelectronics, there is a need to recommend new types of fluids that are more active with respect to heat exchange working. For this reason nanofluids are composed to guarantee operative thermal conductivity developments and to achieve the uprising weights of cooling/heating and other requirements.
Nanofluid is a spreading consisting of nanometer-sized particles, called nanoparticles. The carbon nanotube (CNT) is the most popular class of carbon family for the enhancement of heat transfer devices. This class is further divided into subclasses known as single and multiple wall carbon nanotubes (SWCNTs/MWCNTs), respectively. The CNTs are widely used in the engineering application like fluidization reactor and heat-exchange cooling industry. Iijima (Citation1991) in 1991 discovers the CNTs. Iijima inspected first time the MWCNTs using Krastschmer and Huddman technique (Iijima, Citation1991). Later on, in 1993 Donald Bethune inspected SWCNTs (Ajayan & Iijima, Citation1993). SWCNTs are a rolled sheet of graphene in a tube or cylinder shape with diameter range to
and thickness is about
(To, Citation2006). While MWCNTs consist of 2 to 50 coaxial nanotubes with
layer spacing and diameter range is from
to
(Dresselhaus et al., Citation1995). Hone (Citation2004) has identified that the thermal conductivity is achieved up to
for SWCNTs and
for MWCNTs at room temperature. Haq et al. (Citation2015) described the comparison of engine oil base CNTs has greater value of skin friction as well as heat transfer rate of simple water and kerosene oil base CNTs. Khan et al. (Citation2014) have discussed the thermal conductivity and Navier slip boundary condition for the flow of both CNTs along a plate. Kamali & Binesh (Citation2010) studied the model of power law and convective heat analysis using CNTs base nanofluid with constant heat flux. Liu et al. (Citation2005) examined CNTs in the presence of engine oil and ethylene glycol as ordinary liquid. They disclosed the fact that the thermal efficiency of CNTs in engine oil nanofluid has higher than without CNTs and alike result was obtained in case of ethylene glycol. At 0.02 volume fraction, the thermal efficiency of engine oil is increased by 30%, while CNTs ethylene glycol-based nanofluid of 0.01 volume fraction increased by 12.4%. In another study, the efficiency of coolant water base nanofluid CNTs has been reported by Halelfadi et al. (Citation2014).
The role of stretched surface is very important in industrial processes, for example, the cooling of metallic sheet due to stretched surface, paper, glass, and fiber are produced with the help of stretched surface. In all the above industrial processes, cooling play the key role and the stretched surface produced cooling and boundary layer flow. Crane (Citation1970) investigated two-dimensional steady Newtonian fluids over a moving surface. After this investigation, the flow over a moving surface becomes an important area for the researcher. Dandapat & Gupta (Citation1989) used viscoelastic fluid to discuss heat transfer by using stretching surface. Wang (Citation1990) used for the first time dependent stretching surface to discuss finite liquid. Rehman et al. (Citation2019a) used stretching cylinder to discuss Marangoni convection of thin film spray of CNT nanofluids.Rehman et al. (Citation2019b) discussed the impact of magnetic field and viscous dissipation on the thin film unsteady flow of GO-EG/GO-W nanofluids.
Due to the important use of the above investigation, the present research article deal with the impact of dynamic viscosity properties (wedge problem) with stretching surface using MWCNTs and SWCNTs water-based nanofluid. The similarity transformation is used to convert the partial differential equation to nonlinear ordinary differential equation. The solution to the problem is obtained using the optimal homotopy analysis method (OHAM). The stability of the problems is also obtained up to the 30th order approximation using the BVPh 2.0 package. The outputs are displayed and discussed.
Most of the mathematical problems are complicated in their nature and we cannot find its exact solution. To find the solution of such problem we use two methods, one is numerical method and the other is analytical method to find approximate solution of such problem. One of the analytical methods is OHAM. The key point is that with the help of this method, we solve nonlinear differential equation. This method is rapidly convergent and gives series solution. Liao (Citation2010) used this method for the first time to solve nonlinear differential equation.
2. Mathematical Formulation
Consider the laminar boundary layer flow of water base MWCNT and SWCNT nanofluids on a moveable stretching sheet. Figure above shows the geometry of the flow problem. The lower surface is stretching surface and the upper surface is free surface where the lower surface is moving with velocity known as stretching velocity. The temperature on the lower surface is a variable. We consider the coordinate axis in such a way the -axis is aligned vertically upwards direction. Also, due to the moveable stretching sheet two equal and opposite forces are produced. The sheet is stretching with velocity
and
is the temperature of the moving surface, where
and
are constants. Throughout this paper, all other assumptions are selected as (Rashidi et al., Citation2016), so the resulting equations of continuity, motion and heat are
Boundary conditions are
The velocity component along -axis is
and along
-axis is
, the gravitational acceleration is
, nanofluid temperature and away from the wall is
, respectively. Here dynamic density represented by
, the heat capacitance by
and the thermal expansion coefficient
of the nanofluid, the thermal conductivities by
and
of CNTs nanoparticles, base fluid and nanofluid, respectively,
is the solid volume fraction of nanofluid and the dynamic viscosity of the nanofluid is given by
2.1. Similarity Transformation
Applying the following similarity factors
The resulting equations (2) and (3) take the following non-dimensional form
Transform boundary conditions are
The energy equation take the following form
with boundary conditions
2.2. Important Physical Parameter
The mathematical form of skin friction and Nusselt number are
3. Method of Solution
The OHAM method has been used for the solution of the problem in Eqs. (7, 9). Trial solution is obtained from the auxiliary linear operators and is defined as
with constant properties
where
are the arbitrary constant which is included in general solution.
3.1. Total Square Residual Error
In this section, we have displayed the total square residual error 30th in the form of . Here in current work the outputs of the optimal convergence controlling constraints
and
have been attained from the 30th order OHAM approximation for both cases of velocity and temperature distribution.
4. Result and Discussion
The main objective of this section is to study the effect of various model factors like (nanoparticle volume fraction, mixed convection, dynamic viscosity, Prandtl number, Eckert number) on velocity and temperature distribution. In Tables and , the numeric results illustrate the impacts of different model factors on the skin friction coefficient and Nusselt number of both single and MWCNTs. The effect of different parameters on local skin friction coefficient is shown in Table . The table depicts that the skin friction coefficient enhances in the case of SWCNT and reduces in the case of MWCNT for the increasing values of both dynamic viscosity
and mixed convection parameter
. Whereas, Table shows the Nusselt number coefficient decline in the case of both SWCNT and MWCNT for rising magnitude of Prandtl number. While for increasing values of Eckert number, the Nusselt number coefficient increases in SWCNT and in the case of MWCNT decreases. Similarly, for increasing values of dynamic viscosity
the Nusselt number coefficient increases for both SWCNT and MWCNT. The convergence of the CNTs nanofluid has been obtained up to the 25th iteration for the SWCNTs and MWCNTs nanofluid in Table , one-to-one. Tables and show that increasing the number of iteration reduces the order of residual error and strong convergence attained.
Table 1. Effect of dynamic viscosity and mixed convection parameter on skin friction coefficient
Table 2. Effect of and
on Nusselt number
Table 3. The convergence of OHAM, the error is decreasing after each iteration for the SWCNTs when
Table 4. The convergence of OHAM, the error is decreasing after each iteration for the MWCNTs when
Figure shows the impact of the nanoparticles volume fraction versus the velocity field. The relation between and
is inverse relation. For the growing magnitude of
, decrease the
as displayed in Figure . Relatively this effect is strong in the SWCNTs as equated to MWCNTs. Figure shows the effect of the mixed convection parameter
against the
. The relation between
and
is inverse relation. By increasing the magnitude of
, decreasing the
as displayed in Figure . Relatively this effect is strong in the SWCNTs. Figure shows the effect of the dynamic viscosity against the velocity field. The relation between velocity field
and dynamic viscosity
is inverse relation. The increasing values of the dynamic viscosity
decrease the velocity field
as displayed in Figure . Physically, increasing dynamic viscosity produced resistant forces due to which fluid particles does not move easily, so velocity field is decreasing by increasing dynamic viscosity
. Relatively this effect is strong in the SWCNTs.
Similarly, Figure displays the effect of the against the
temperature field. From the figure we observe that the relation between temperature field and
is inverse relation. So, by increasing values of the
decreasing the
temperature field as displayed in Figure . Relatively this effect is strong in the SWCNTs. Figure shows the effect of the
against the
temperature field. The relation between temperature field and
is inverse relation, so enhancing the
decreases the temperature profile as displayed in Figure . In fact, the thickness of the momentum boundary layer to be larger than that of the thermal boundary layer, or that the viscous diffusion is larger than the thermal diffusion and therefore, the larger amount of the
reduces the thermal boundary layer. Relatively this effect is strong in the SWCNTs. Figure shows the impact of
, Eckert number versus the temperature field. From the figure we notice that the relation between temperature field and
is direct relation, that is increasing the
increases the temperature profile as displayed in Figure . In fact, the thickness of the momentum boundary layer to be small than that of the thermal boundary layer, or that the viscous diffusion is less than the thermal diffusion and therefore, the larger amount of the
increase the thermal boundary layer. Relatively this effect is strong in the SWCNTs. Figure displays the impact of the dynamic viscosity
versus the temperature field. The relation between temperature field and dynamic viscosity
is inverse relation. So, the increasing values of the
decline the temperature field as shown in Figure . Physically, by increasing the
(dynamic viscosity) produced resistant forces due to which fluid particles does not move easily, so they cannot collect with each other, therefore the temperature field is decreasing by increasing dynamic viscosity. Relatively this effect is strong in the SWCNTs as compared to MWCNTs.
5. Conclusion
In this research work Laminar (wedge flow problem) flow of water based CNTs nanofluid over the stretching surfaces with dynamic viscosity has been examined. The two sorts SWCNTs/MWCNTs of water base CNTs has been used for the impact of dynamic viscosity. The result of model problem has been calculated by OHAM. Moreover, the outcome convergence of the (OHAM) has been calculated up to 25th iteration for both SWCNT and MWCNT. The effect of skin friction coefficient and Nusselt number are plotted and discussed. The effect of different parameter have been discussed and plotted. The main conclusions drawn from the present analysis are as follow:
The velocity distribution enhances via
.
High estimation of dynamics viscosity
, reduces the velocity field.
The larger estimation
, increases the velocity field.
By increasing the value of Eckert number, increases the temperature profile.
Temperature profile decays for higher magnitude of Prandtl number.
Nomenclatures
= | Acceleration due to gravity | |
= | Dynamic viscosity of the nanofluids axial directions, | |
= | Density of the nanofluids | |
= | Eckert number | |
= | Heat generation/absorption parameter | |
= | Kinematic viscosity of the nanofluids | |
= | Local Temperature | |
= | Suction, Injection velocity | |
= | Local Temperature | |
= | Mean absorption coefficient | |
= | Non-dimensional thickness of the liquid film | |
= | Nusselt number | |
= | Prandtl number | |
= | Specific heat | |
= | Stretching velocity | |
= | Thermal expansion coefficient of solid particles | |
= | Similarity variable | |
= | Solid particle volume fraction | |
= | Stefan-Boltzman constant | |
= | Skin friction | |
= | Thickness of the liquid film | |
= | Temperature at the free surface | |
= | Thermal radiative heat flux | |
= | Thermal conductivity of the nano particles | |
= | Velocity components |
Additional information
Funding
Notes on contributors
Ali Rehman
Ali Rehman obtained under graduate degree from Islami Collage University Peshawar. He start PhD in Applied Mathematics from Universiti Malaysia Terengganu under the supervision of Professor Dr. Zabidin Salleh. He actively involved in the research to model and solve nonlinear differential equation. He used the analytical method to find the approximate solution of the nonlinear problem and discuss the effect of different parameters for both velocity and temperature profiles. The key focus of his research is heat transfer which play an important role in industrial product development process.
Zabidin Salleh
Zabidin Salleh obtained a PhD degree in Topology from the Universiti Putra Malaysia in 2008. He then worked as a Senior Lecturer at the Department of Mathematics, Universiti Malaysia Terengganu from 2008 till date. He actively involved in the research related to topology, dynamical systems and optimization. Currently, his research interest are in dynamical systems and fluid dynamics, working on carbon nanotubes nanofluid.
References
- Ajayan, P. M., & Iijima, S. (1993). Capillarity-induced filling of carbon nanotubes. Nature, 361(6410), 333–13. https://doi.org/10.1038/361333a0
- Asaithambi, A. (1998). A finite difference method for the Falkner and Skan equation. Applied Mathematics and Computation, 92(2–3),135–141. https://doi.org/10.1016/S0096-3003(97)10042-X
- Crane, L. J. (1970). Flow past a stretching plate. Angrew Mathematics and Physics, 21(4), 645–647. https://doi.org/10.1007/BF01587695
- Dandapat, B. S., & Gupta, A. S. (1989). Flow and heat transfer in a viscoelastic fluid over a stretching sheet. International Journal of Non-Linear Mechanics, 24(3), 215–219. https://doi.org/10.1016/0020-7462(89)90040-1
- Dresselhaus, M. S., Dresselhaus, G., & Saito, R. (1995). Physics of carbon nanotubes. Carbon, 33(7), 883–891. https://doi.org/10.1016/0008-6223(95)00017-8
- Falkner, V. M., & Skan, S. W. (1931). LXXXV. Solutions of the boundary-layer equations. Philosophical Magazine, 12(80), 865–896. https://doi.org/10.1080/14786443109461870
- Halelfadi, S., Mare, T., & Estelle, P. (2014). Efficiency of carbon nanotubes water based nanofluids as coolants. Experimental Thermal and Fluid Science, 53, 104–110. https://doi.org/10.1016/j.expthermflusci.2013.11.010
- Haq, R. U., Nadeem, S., Khan, Z. H., & Noor, N. F. M. (2015). Convective heat transfer in MHD slip flow over a stretching surface in the presence of carbon nanotubes. Physica B: Condensed Matter, 457, 40–47. https://doi.org/10.1016/j.physb.2014.09.031
- Hone, J. (2004). Carbon nanotubes: Thermal properties. Dekker Encyclopedia of Nanoscience and Nanotechnology, 7, 603–610. New York, NY: Marcel Dekker.
- Iijima, S. (1991). Helical microtubules of graphitic carbon. Nature, 354(6348), 56–58. https://doi.org/10.1038/354056a0
- Kamali, R., & Binesh, A. R. (2010). Numerical investigation of heat transfer enhancement using carbon nanotube-based non-Newtonian nanofluids. International Communications in Heat and Mass Transfer, 37(8), 1153–1157. https://doi.org/10.1016/j.icheatmasstransfer.2010.06.001
- Khan, W. A., Khan, Z. H., & Rahi, M. (2014). Fluid flow and heat transfer of carbon nanotubes along a flat plate with Navier slip boundary. Applied Nanoscience, 4(5), 633–641. https://doi.org/10.1007/s13204-013-0242-9
- Liao, S. (2010), An optimal homotopy-analysis approach for strongly nonlinear differential equations, Communication in Nonlinear Science and Numerical Simulation 15(8),2003-2016. https://doi.org/10.1016/j.cnsns.2009.09.002
- Liu, M. S., Lin, M. C. C., Te, H. I., & Wang, C. C. (2005). Enhancement of thermal conductivity with carbon nanotube for nanofluids. International Communications in Heat and Mass Transfer, 32(9), 1202–1210. https://doi.org/10.1016/j.icheatmasstransfer.2005.05.005
- Malvandi, A., & Ganji, D. D. (2014). Magnetic field effect on nanoparticles migration and heat transfer of water/alumina nanofluid in a channel. Journal of Magnetism and Magnetic Materials, 362(362), 172–179. https://doi.org/10.1016/j.jmmm.2014.03.014
- Na, T. Y. (1979). Computational methods in engineering boundary value problems. Academic, New York.
- Rajagopal, K. R., Gupta, A. S., & Na, T. Y. (1983). A note on Falkner and Skan flows of a non-newtonian fluid. International Journal of Non-Linear Mechanics, 18(4), 313–320. https://doi.org/10.1016/0020-7462(83)90028-8
- Rashidi, M. M., Ganesh, N. V., Hakeem, A. A., Ganga, B., & Lorenzini, G. (2016). Influences of an effective Prandtl number model on nano boundary layer flow of γ Al2O3-H2O and γ Al2O3-C2H6O2 over a vertical stretching sheet. International Journal of Heat and Mass Transfer, 98, 616–623. https://doi.org/10.1016/j.ijheatmasstransfer.2016.03.006
- Rehman, A., Gul, T., Salleh, Z., Mukhtar, S., Hussain, F., Nisar, K. S., & Kumam, P. (2019a). Effect of the Marangoni convection in the unsteady thin film spray of CNT nanofluids. Processes, 7(6), 392. https://doi.org/10.3390/pr7060392
- Rehman, A., Salleh, Z., Gul, T., & Zaheer, Z. (2019b). The impact of viscous dissipation on the thin film unsteady flow of GO-EG/GO-W nanofluids. Mathematics, 7(7), 653. https://doi.org/10.3390/math7070653
- To, C. W. S. (2006). Bending and shear moduli of single-walled carbon nanotubes. Finite Elements in Analysis and Design, 42(5), 404–413. https://doi.org/10.1016/j.finel.2005.08.004
- Ullah, I., Khan, I., & Shafie., S. (2016). MHD natural convection flow of casson nanofluid over nonlinearly stretching sheet through porous medium with chemical reaction and thermal radiation. Nanoscale Research Letters, 1(1), 527. https://doi.org/10.1186/s11671-016-1745-6
- Wang, C. Y. (1990). Liquid film on an unsteady stretching surface. Quarterly of Applied Mathematics, 48(4), 601–610. https://doi.org/10.1090/qam/1079908
- Watanabe, T. (1990). Thermal boundary layers over a wedge with uniform suction or injection in forced flow. Acta Mechanica, 83(3–4), 119–126. https://doi.org/10.1007/BF01172973
- Yih, K. A. (1998). Uniform suction/blowing on forced convection about a wedge: Uniform heat flux. Acta Mechanica, 128(3–4), 173–181. https://doi.org/10.1007/BF01251888