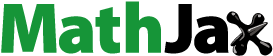
Abstract
In this paper, the role of nickel-20 chromium and TiO2 nanoparticles additions for enhancement of corrosion resistance and microhardness of organic zinc-rich coatings were investigated. Three coating samples were prepared by the new additions in different amounts that were experimentally predicted. Particle sizes and coatings micrographs were examined by scanning electron microscope (SEM) and chemical composition was analyzed by energy dispersive spectroscopy (EDS) technique. The corrosion behavior was conducted in 8% concentration HCl by potentiodynamic polarization test and corrosion parameters extracted through Tafel Extrapolation from polarization curves. Microhardness test employed for evaluation the hardness of all obtained coating samples. Results showed that diffusion and dispersion the added nanoparticles through zinc-rich coating (ZRC) improved the hardness of coating significantly. Furthermore, adding nickel-20 chromium nanoparticles to ZRC and incorporation of TiO2 with it, has been shown an enhancement in corrosion resistance by a percentage of 88.7% and 99.8%, respectively.
PUBLIC INTEREST STATEMENT
Zinc-rich coating (ZRC) is a coating consisting of zinc dust embedded in a binding material. This coating has been widely used for protecting steel structures from rust. Zinc-rich coating provides a protective layer that is not hard enough, which makes it unsuitable in certain applications where high scratch and wear resistance are demanded. Furthermore, in some media especially these contain chlorides this coating layer loses the function of protection and deteriorates as a result of the high affinity of zinc particles. In this paper, an attempt is made to enhance the properties of ZRC under the above severe conditions by mixing it with nano-particles of TiO2 and nickel-20 chromium.
1. Introduction
Protective coatings are considered one of the most convenient mean for mitigating metal deterioration and easier for application. For some applications, the need for corrosion protection and resistance to abrasion is necessary and the metallic coating is the suitable solution. Zinc rich coatings (ZRC) are one of the metallic coating forms which also called “cold galvanizing” that give a cathodic protection to steel and hard surface to resist scratches and wear. They are categorized to organic and inorganic types when high content of zinc dust mixed with organic or inorganic binders a shielding shall be formed when applied to steel surfaces and extending their lives (Gergely et al., Citation2015). ZRC can easily applied, either by spry, brush or roll, which can be used for in situ or in service equipment. Just like zinc, those coatings exhibit an excellent works in marine environments and a poor resistance to some acids (Zheng, Citation2020). Applying films of ZRC will work as a barrier to protect steel against corrosion in 3% NaCl (Hammouda et al., Citation2011). The electrochemical response of steel painted with ZRC in (0.5 M and 1 M) of NaCl solution will slightly different with the increases of coating thickness and zinc contents (Bin Sofian, Citation2015). The anticorrosive behavior of a zinc-rich epoxy coating containing sulfonated polyaniline in 3.5% NaCl solution was studied; the passive film formed on the metal surfaces owing to the excellent reversible redox performance and nanofiber addition which evidently enhance effective utilization of zinc powder and decrease the coating porosity (Yang et al., Citation2018). The electrochemical investigation of the corrosion behavior of epoxy modified silicate zinc-rich coatings in 3.5% NaCl solution leads to the impedance value of the zinc-rich coating increase with the increasing the epoxy content which indicates that the ability of the coating to resist corrosive media is enhanced especially in hydrochloric acid which is considered one of the most difficult corrosives due to chlorides attack (Wang et al., Citation2020).
Some nano—powders may be added to ZRC in different amount to improve specific characteristics of the ZRC. Nickel alloys nanoparticles added to improve the general resistance to chlorides attack while chromium powder promote resistance to oxidizing in aqueous media by raising the passive range to higher potentials and to protect the metal from oxidation in air at high temperatures by selective oxidation yielding a surface of chromium oxide Cr2O3 (David, Citation2018). Titanium can enhance the resistance in dilute solutions of non-oxidizing inorganic acids especially sulfuric, phosphoric, hydrochloric, and hydrofluoric acids because the redox potentials of the corroding systems are below the appropriate passivating potentials (ASM Handbook, Citation2005). Researches have proved that the electrochemical behavior of ZRC can be modified by different additions. In the present study, ZRC with the addition of some Titanium Oxide and Nick-chromium nanoparticles in various percentages was prepared. The electrochemical behavior of the coating was investigated in the acidic solution of 8% HCl.
2. Experimental work
2.1. Substrate
ASTM A 516 Gr.70 (ASTM, Citation2015a) steel plate was used as a substrate for this work which is used for welded vessels. The chemical composition analysis was carried out according to the procedure of ASTM A 751(ASTM, Citation2015b) by using OES, SPECTRO device. The measured and standard chemical composition values are shown in .
Table 1. Chemical composition for steel substrate
The plate was cut to several substrates and their surfaces was cleaned and sand blasted to a degree SA 2.5 according to SSPC-SP6 (SSPC, Citation2016) before application of the coating.
2.2. Zinc-Rich Coating (ZRC), nano-coating preparation, and application
Zinc-rich coating (ZRC) gray in color brand ZINGA which was supplied from the local market with 96% of zinc dust, purity of 99.999%. The zinc dust pigment embedded in a binder of epoxy resin and solved by aromatic hydrocarbon to comply with the composition of ASTM D520 Type II (ASTM, Citation2015b). Three nano-coating samples were formulated by adding specific amounts of nano-materials (TiO2 and Nickel-20 chromium) to zinc-rich coating (ZRC). shows details of the quantity of nano-materials that mixed for each system. All quantities that represented in this table were weighted with accuracy 0.1 mg. After the addition, an electrical stirrer was used to guarantee a uniform nanoparticle distribution, mixing with the zinc-rich coating (ZRC) and solvent, and to overcome any agglomerate that may be existing in the added nano-materials. An air gun with 2 mm nozzle diameter connected to a pressure vessel with high pressure 4 bar was used for application of the nano-coating perpendicularly to the substrate.
Table 2. Mixing weights for coating samples
Coated samples were left to solidify and cure for 48 hours in laboratory conditions (30 ± 1 ͦ C and 25% RH).
2.3. Coating characterization and particle size determination
The surface morphology of coating after application on the substrate was characterized through cell phone photos with a magnification of 5X. To give more insight, microstructure, and elemental analysis for coating after application were conducted using the scanning electron microscope model (NOVA NANOSEM 450) with operating voltage 10 kV equipped with an electron dispersive spectroscopy (EDS) according to ASTM E 1508 (ASTM, Citation2019). Moreover, the same scanning electron microscope was employed to determine the particle size of zinc dust and the added nano-materials before mixing and application on the substrate.
2.4. Corrosion test
Open circuit potential (OCP) and potentiodynamic polarization tests were used to characterize the electrochemical behavior of bare and coated samples in media of diluted hydraulic acid with 8% concentration at room temperature. Specimens were cut from coated steel substrate in dimensions (1 cm x1cm). Three electrodes corrosion cell connected to a potentiostat model MLab was used to achieve this work. The specimens were acted as the working electrode in the system and Calomel electrode was the reference electrode while the platinized Titanium performed the auxiliary electrode. The tests were started with OCP measurements at room temperature for a time of 100 minutes for each sample. After that, potentiodynamic polarization was carried out with a scan rate (1.0 mV/s). The anodic and cathodic slops, Ecorr, and were extracted using MLab software by TAFEL EXTRAPOLATION and the polarization resistance (Rp) was calculated depending on Stern-Geary constant from the formulas below. All measurements were done according to ASTM G5 and ASTM G 102 (ASTM, Citation2014; ASTM, Citation2015b).
Where:
B: Stern-Geary constants (V)
: slope of the anodic Tafel reaction (V/Dec)
: slope of the cathodic Tafel reaction (V/Dec)
: corrosion current density (A/cm2)
2.5. Hardness measurements
Coated samples hardness was evaluated by vickers microhardness (HV) tester model (vhs-30b) with an applied load of 100 g and an indentation time of 30 s. Five readings were determined for each sample and the mean value was taken. The micro-indentation test was done in compliance with ASTM E384 (ASTM, Citation2015b).
3. Results and discussion
3.1. Coating characterization and particle size determination
SEM micrographs of zinc-rich coating (ZRC) before application and mixing with nano-particles are shown in . The coating shows an attractive structure of small and semi-sphere agglomerated zinc particles. It also appears that the zinc particles are different in grain sizes in the range (241.3 - 249.4 nm) and are bonded together due to the presence of the binder.
clarifies the SEM micrographs of TiO2 nano-particles before mixing with ZRC. It obvious from this figure that the particle sizes of the added nano-materials in range sizes from (30.58 - 62.95 nm). A very adorable structure of the added nano-materials as found in the SEM micrographs of nickel-20 chromium particles that are depicted in . Small and agglomerated nickel particles with range sizes (23.20 - 77.70 nm). These small nickel particles cover and distribute among large chromium particles as indicated in the SEM micrograph.
The surface morphology of the coating after mixing and application on the substrate is shown in .Visually, the zinc coating by spraying process produced a cohesive and pores-free coating layer. As shown in this labeled images, there is a contrast in color in the applied coating where the sample 1 (i.e. zinc only) exhibits light gray compared to the sample 2 that exhibits a gradation in color between white and gray as a result of adding the nanomaterial that was white (i.e., TiO2).
On the other hand, the samples (3&4) had shown a gray color similar to the first sample, but darker due to the addition of nanomaterial (i.e. Nickel-20 chromium) that was gray.
SEM micrographs and EDS analysis for coating samples (1,2,3, and 4) after application on the steel substrate can be observed in , ,, and ) respectively. Furthermore, summarizes the EDS analysis values for all coating samples in weight percentage. The structure of zinc particles embedded in a film of aromatic hydro-carbonic binder (i.e., sample 1) that keeps particles bonded together when the film of the dry coating had produced is quite obvious in . EDS analysis confirms that the constituents of coating are mainly zinc element with a very little percentage of calcium element that appeared fortuitously as an impurity with a constant value in all coating samples. For sample (2), a slight change had occurred in the microstructure of ZRC after incorporation TiO2 nano-material, referring to . The small TiO2 particles had interfered with zinc particles and the binder, provided a coherent, non-porous, and homogenous coating as reported by Praveen and Venkatesha (Praveen & Venkatesha, Citation2008). The appearance of titanium and oxygen peaks through elemental analysis confirms the existence of TiO2 in the surface layer of the coating. On the other hand, a clear change had occurred for microstructure of samples 3 and sample 4 after addition as shown in and , respectively, where it was noticed that the clustered nature of the surface had disappeared. Additionally, EDS analysis for both surface layer of these samples had confirmed the incorporation of Ni and Cr particles with ZRC, thus TiO2 particles in sample 4.
Table 3. Chemical compositions for coatings by EDS in weight percentage
It is observed that there are slight differences in zinc weight percentage and the other incorporated elements that are associated with EDS analysis and this may be attributed to some errors as a result of average values had obtained. Based on the pervious result, it is worth mentioning that the incorporation of TiO2 and nickel-20 chromium nano-materials had carried out successfully and this gave to the process of coating application by spraying the validity to use for production the nano-coating.
3.2. Corrosion test
The OCP measurements and polarization curves for coated samples and control in 8 % HCl solution at room temperature are represented in and respectively. For OCP results, all samples showed approximately constant behavior during the whole test period. The control sample (i.e. uncoated) started with −309 mV and reached −209 mV at a maximum time of test. This slight shifting toward the positive part is attributed to forming an oxide layer on the surface. A clear shifting of potential of coated samples to more negative values and this action is normal due to the change of the sample surface material and the nature of reaction with test solution. Additionally, incorporation TiO2 nano particles with ZRC did not change the state of sample 1 (i.e., zinc only) a lot, where exhibited potential ranges from the starting time of test to end (−1023 to −1029 mV) and (−1036 to −1029 mV) for sample 1 and sample 2, respectively. Otherwise, incorporation nickel-20 chromium with ZRC had shifted the potential to more positive value obviously as seen for sample 3 and sample 4 where they showed potential ranges (−947 to −946) and (−918 to 922) respectively.
Regarding polarization results, and introduce a comparison for corrosion potential and corrosion current density values extracted by extrapolation of coated samples and uncoated in 8% HCl solution, respectively. Thus, summarizes the anodic and cathodic constant as well as the calculated polarization resistance for each sample.
Table 4. Potentiodynamic polarization data of coated samples and control
The uncoated sample (i.e., control) showed Ecorr value lower than the values that exhibited by coated samples and the as result the new surface layer has come into contact with the corrosive solution. Furthermore, the change in the corrosion potential Ecorr value of the coated samples itself between down and up and this is naturally attributable to the incorporation of nanomaterials with ZRC. It should be noted that Ecorr is not a kinetic property and this could not give a correct evaluation for the coating integrity. Therefore, the integrity of coating can be evaluated easily through corrosion current icorr because it is directly related to corrosion rate and polarization resistance Rp.
A high affinity of zinc for reaction with dilute HCl as observed in sample 1 that exhibited the highest corrosion current icorr and lowest polarization resistance compared with all other samples. A subtle change of icorr and Rp after incorporation TiO2 with zinc (i.e., sample 2) (Praveen & Venkatesha, Citation2008; Yılmaz et al., Citation2014). On the other hand, an obvious change for these values associated with sample 3 and sample 4 where showed an improvement in corrosion resistance compared with the uncoated sample by a percentage of 88.7 and 99.8%, respectively. This gives proof that the incorporation of nickel-20 chromium nano-material with ZRC had offered an efficient physical barrier to resist the chloride-rich medium (Lotfi et al., Citation2018).
The low corrosion current values accompanied by high polarization resistance values presented by sample 4 give an excellent indication of the integrity of the coating from porosity in addition to the strong bonding between the coating and the metallic substrate. This beneficial effect of incorporation of nickel-20 chromium nano-material as well as TiO2 nanoparticles with ZRC it may be attributed to powerful affinity and activity of these added materials with ZRC and provide a synergistic effect for enhancement the surface layer of coated samples (Fayomi & Popoola, Citation2015). It is important to note that the addition of these particles had increased the contact between zinc particles themselves and/or zinc particles and steel substrate interface region, thus it achieved full protection of corrosive medium (Schaefer & Miszczyk, Citation2013).
3.3. Microhardness test
Hardness measurements for coated samples are presented in . An obvious change of hardness values had observed after incorporation nanomaterials.Adding TiO2 to ZRC (i.e., sample 2) increased the hardness pronouncedly because these fine and hard TiO2 particles had dispersed into the zinc matrix and caused a mechanical obstacle for indentation (Shao et al., Citation2012). For the same reason, as well as the small nanoparticle size of nickel particles compared to TiO2 had facilitated interference and spread these particles between zinc particles and thus the hardness of sample 3 had little increased. The effect of double addition of TiO2 and nickel-20 chromium nano-material has increased the hardness of sample 4 significantly.
4. 4. Conclusion
An attempt to produce a nano-coating that is resistant to a medium rich in chlorides by spraying process has been successfully completed. Based on morphological and microstructural characterization, a cohesive, pores-free, and rich in added nano-elements coating has been obtained. Furthermore, the electrochemical measurements had shown an enhancement in the corrosion behavior of ZRC after nanoparticle addition. It has been found incorporation nickel-20chromium nanoparticles with ZRC had enhanced the corrosion resistance by 88.7% while the combined addition of TiO2 and nickel-20chromium improved it by 99.8%. Otherwise, adding TiO2 alone to ZRC didn’t enhance the corrosion behavior considerably. For microhardness test, results obtained from nickel-20chromium and TiO2 addition were relatively high compared to nickel-20chromium addition only and lateral was higher than TiO2 addition and in general, all nano additions enhanced ZRC microhardness values.
Disclosure statement
The authors declare no financial or commercial conflict of interest.
Additional information
Funding
Notes on contributors
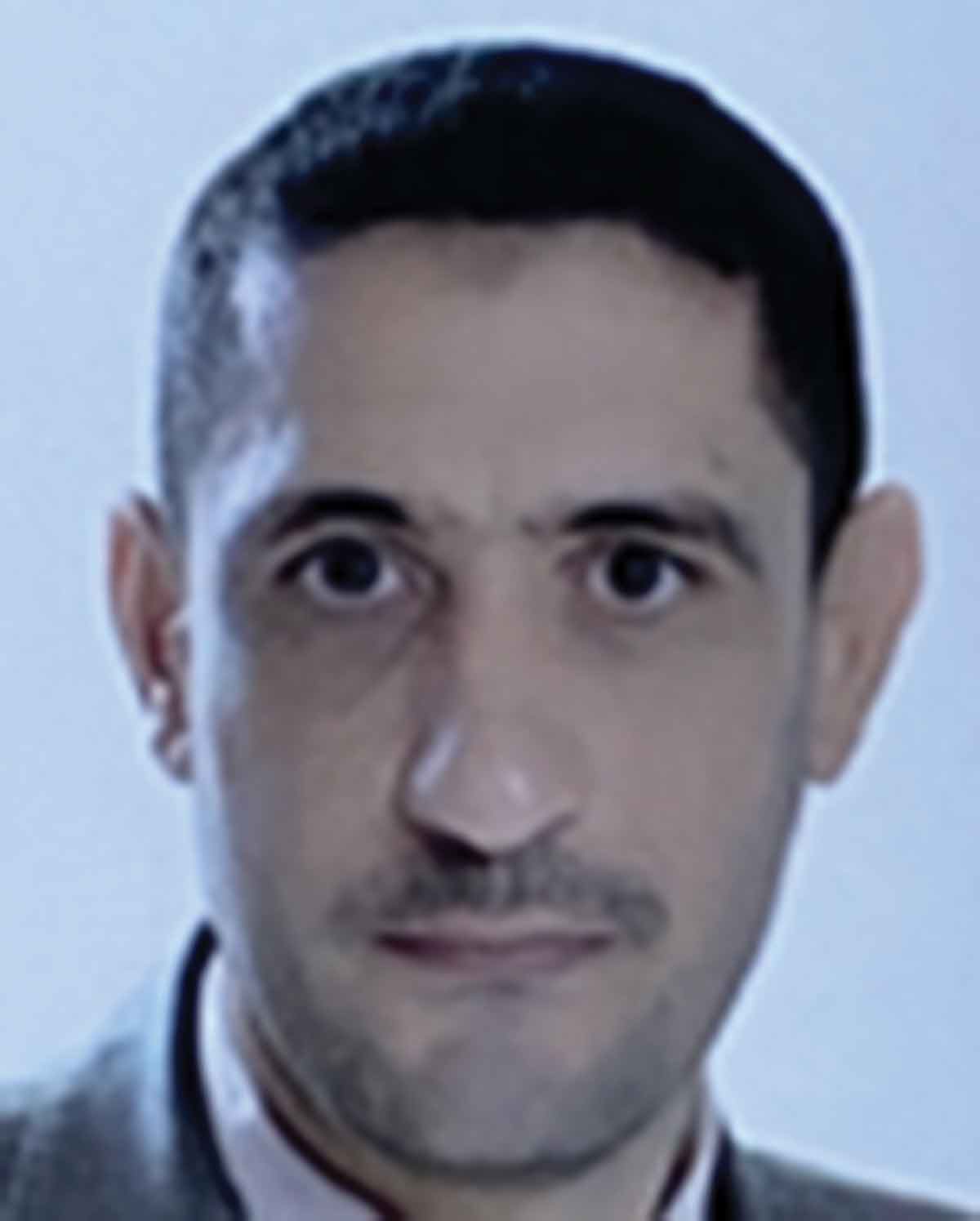
Murtadha Abbas Jabbar
Murtadha Abbas Jabbar was born in Basrah, Iraq, in 1975. He received his B.Sc. degree and M.Sc. degree, respectively, in mechanical engineering from College of Engineering, University of Basrah, Basrah, Iraq. He made the experimental part of his Ph.D. dissertation at the University of Iowa, Iowa, the USA as a visiting scholar in 2009. He was awarded his Ph. D. degree in Mechanical Engineering from the University of Basrah in 2010, Basrah, Iraq. He is a lecturer of engineering material, materials selection, and engineering metallurgy in College of Engineering, University of Basrah, Basrah, Iraq with about 18 years of experience in teaching. His area of expertise is Heat Treatments, Corrosion, Smart Materials, Nanomaterials, and Failure analysis. He has several publications to his credit some of them in Scopus indexed journals. He working as a supervisor, materials inspector, and consulting engineer for several projects.
References
- ASM Handbook. (2005). Corrosion (Vol. 13B). ASM International.
- ASTM. (2014). Standard reference test method for making potentiodynamic anodic polarization measurements. In Annual Book of ASTM Standard, G5-14.
- ASTM. (2015a). Standard specification for pressure vessel plates carbon steel for moderate- and low-temperature service. In Annual Book of ASTM standard A516.
- ASTM. (2015b). Zinc dust pigment. In Annual Book of ASTM standard D520.
- ASTM. (2019). Standard guide for quantitative analysis by energy-dispersive spectroscopy. Annual Book of ASTM standard E1508-12a.
- Bin Sofian, A. H. Corrosion Protection of Zinc Rich Paint Coating on Steels, PhD. Thesis. A Publication of the University of Miskolc. 2015.
- David, E. J. (2018). Talbot, James D.R. Talbot (Eds.), Corrosion science and technology (pp. 97-107). CRC Press. https://doi.org/10.1201/9781351259910
- Fayomi, O. S. I., & Popoola, A. P. I. (2015). Anti-corrosion properties and structural characteristics of fabricated ternary coatings. Surf. Engin. Appl. Electrochem, 51(1), 76–11. https://doi.org/10.3103/s1068375515010068
- Gergely, A., Pászti, Z., Bertóti, I., Mihály, J., Drotár, E., & Török, T. (2015). Hybrid zinc-rich paint coatings. Intelligent coatings for corrosion control (pp. 195–249). Elsevier. https://doi.org/10.1016/b978-0-12-411467-8.00006-4
- Hammouda, N., Chadli, H., Guillemot, G., & Belmokre, K. (2011). The corrosion protection behaviour of zinc rich epoxy paint in 3% NaCl solution. ACES, 01(2), 51–60. https://doi.org/10.4236/aces.2011.12009
- Lotfi, N., Aliofkhazraei, M., Rahmani, H., & Darband, G. B. (2018). Zinc–nickel alloy electrodeposition: characterization, properties, multilayers and composites. Prot Met Phys Chem Surf, 54(6), 1102–1140. https://doi.org/10.1134/s2070205118060187
- Praveen, B. M., & Venkatesha, T. V. (2008). Electrodeposition and properties of Zn-nanosized TiO2 composite coatings. Applied Surface Science, 254(8), 2418–2424. https://doi.org/10.1016/j.apsusc.2007.09.047
- Schaefer, K., & Miszczyk, A. (2013). Improvement of electrochemical action of zinc-rich paints by addition of nanoparticulate zinc. Corrosion Science, 66, 380–391. https://doi.org/10.1016/j.corsci.2012.10.004
- Shao, W., Nabb, D., Renevier, N., Sherrington, I., Fu, Y., & Luo, J. (2012). Mechanical and anti-corrosion properties of TiO2 nanoparticle reinforced Ni coating by electrodeposition. J. Electrochem. Soc, 159(11), 671–676. https://doi.org/10.1149/2.065211jes
- SSPC. (2016). Commercial blast cleaning. Surface Protective Coating SSPC –SP6.
- Wang, J., Qi, Y., Zhao, X., & Zhang, Z. (2020). electrochemical investigation of corrosion behavior of epoxy modified silicate zinc-rich coatings in 3.5% NaCl solution. Coatings, 10(5), 444. https://doi.org/10.3390/coatings10050444
- Yang, F., Liu, T., Li, J., Qiu, S., & Zhao, H. (2018). Anticorrosive behavior of a zinc-rich epoxy coating containing sulfonated polyaniline in 3.5% NaCl solution. RSC Advances, 8(24), 13237–13247. https://doi.org/10.1039/c8ra00845k
- Yılmaz, G., Hapçı, G., & Orhan, G. (2014). Properties of Ni/Nano-TiO2 composite coatings prepared by direct and pulse current electroplating. J. Of Materi Eng and Perform, 24(2), 709–720. https://doi.org/10.1007/s11665-014-1346-4
- Zheng, S. X. (2020). Principles of organic coatings and finishing. (pp. 1–5). Cambridge Scholars Publishing.