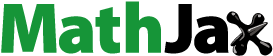
Abstract
The paper seeks to address issues that arise during the drilling and fixation of bones in orthopedic, orthodontic and implant surgeries. Thermal necrosis is one of the widespread problems that occurs during bone/tooth drilling and which can lead to implant failures. The highest registered temperature during drilling is 86°C. However, when the temperature is increased beyond 47° C during the drilling process, it can often lead to osteonecrosis. The possibility of thermal necrosis can be minimized by controlling the drilling parameters. However, optimal parameter values identified by various researchers have not been complied so far, primarily because of the effects of multifactorial constraints. Overall, the drilling bore speed and the feed rate are found to be the most influential parameters in triggering thermal injuries in the course of time. The drilling speed is also more important to the feed rate. In addition, osteological location also increases the probability of necrosis by multiple means in terms of anatomy. A thermocouple is used to evaluate in vivo temperature conditions during the drilling process. However, given the uncertainty and the practical errors that occur during the experimental measurements, the finite-element analysis (FEA) is proposed in most studies. This paper explores the existing state of literature and summarizes various drilling methods and assess the related parameters using FEA. It also describes the impact of various constraints in detail to explore the optimum drilling parameters in order to minimize the danger of thermal necrosis.
PUBLIC INTEREST STATEMENT
Thermal necrosis is one of the widespread problems that occurs during bone/tooth drilling and which can lead to implant failures. The highest registered temperature during drilling is 86°C. However, when the temperature is increased beyond 47°C during the drilling process can lead to osteonecrosis. The possibility of thermal necrosis can be minimized by controlling the drilling parameters. Overall, the drilling bore speed and the feed rate are found to be the most influential parameters in triggering thermal injuries in the course of time. The drilling speed is also more important to the feed rate. Osteological location also increases the probability of necrosis by multiple means in terms of anatomy. A thermocouple is used to evaluate in vivo temperature conditions during the drilling process. However, given the uncertainty and the practical errors that occur during the experimental measurements, the finite-element analysis (FEA) is proposed in most studies.
1. Introduction
Orthopedic, Orthodontic and Implant surgeries involve drilling holes in bones and teeth to mount screws for anchor plates and prosthetic devices, or fix bone fractures. Most importantly in bone and tooth drilling are mechanical and thermal damages (Thermal Necrosis) that occur to the subject by drilling tools. The quality of the drilling procedure is crucial to the success of the process. Although the reliability of the tooth implant is significantly high, reported at 93.9–98.7% (Higuchi et al., Citation1995; W. Li et al., Citation2009; Mazzocchi et al., Citation2007), the assessment of causes for failure plays a crucial role to improve the success rate associated procedures. Implant failures are classified either early failure or late failure. Early failure occurs between the first and second stages. of the surgery while all other failures, caused by subsequent surgeries, are delayed failures (Buser et al., Citation1991). Thermal necrosis is one of the early-stage failures. Penetrating the bone contains gentle use of drills so as not to affect many structures neighboring the bone (W. Li et al., Citation2009). Several attempts have been made to determine the critical threshold temperature value of the drilling process (Eriksson & Albrektsson, Citation1984; A. R. Eriksson & Albrektsson, Citation1983) as bone tissues are very receptive to heat. The osteotomy temperature is 44°C-47°C when drilling for 1 minute (Sezek et al., Citation2012) and over and above this, drilling injuries to the bone tissue can occur. Previous studies point out that peak bone temperature ranging 56°C–70°C could be detrimental to the bone tissues, as at this temperature the alkaline phosphate undergoes a notable changea (Berman et al., Citation1984; Ludewig, Citation1972; Matthews & Hirsch, Citation1972; Rhinelander et al., Citation1979). However, heat generation owing to the frictional forces and shearing between tool bit and bone result in thermal injuries (Thermal Necrosis) to the vicinity of the drilling bone areas (Bachus et al., Citation2000; Eriksson et al., Citation1984). The most probable cause of implant failure is thermally induced bone necrosis (Jo et al., Citation2011).
The considerable clinical occurrence of thermal necrosis and implant failures has motivated researchers (Nam et al., Citation2006; Sezek et al., Citation2012; Sharawy et al., Citation2002) to probe the relationship between temperature and the drilling parameters to understand the cause of heat generation and how it can be controlled to prevent thermal necrosis and its consequences, and thereby, ensure a highly successful surgery rate. The degree of bone cell destructions is interdependent on the magnitude of temperature elevation and the drilling duration. In addition, when a certain temperature is reached, the width of the necrotized zone becomes directly proportional to the heat generated during the drilling procedure (Weinlaender, Citation1991). Some studies have shown that high-speed drilling with high forces (Bachus et al., Citation2000) can control the temperature rise in the nearby bone areas (Abouzgia & James, Citation1995). However, on the other hand, the sustained drill feed rate, the increase in drilling diameter and the increase in drilling speed lead to an increase in cortical bone temperature (Augustin et al., Citation2008). The change in heat is greatly influenced by drill feed rate, relative to drilling speed and torque. Thus, it mainly affects the surface area and force applied for drilling process (Wiggins & Malkin, Citation1976). To minimize on-site temperature, it is essential to optimize drilling parameters to minimize thermal damage and thereby prevent inadvertent loosening. Significant studies have examined the effects of the drilling conditions (Abouzgia & James, Citation1997; Augustin et al., Citation2008; Matthews et al., Citation1984; Toews et al., Citation1999), bone type, density (Eriksson et al., Citation1984; Toews et al., Citation1999), drill bit geometry (Abouzgia & James, Citation1997; Augustin et al., Citation2008; Matthews et al., Citation1984), irrigation presence (Augustin et al., Citation2008; Eriksson et al., Citation1984; Matthews et al., Citation1984), peak temperatures and exposure times, with a view to reducing the risk of thermal osteonecrosis. Necrotized cells may cause unpremeditated loosening of bone-anchored devices and post-operative difficulties (Christie, Citation1981). It is therefore quite essential to measure the temperature in order to ascertain the parameters tied with thermal necrosis.
Temperature measurement using thermocouple is most prevalent in practice. Because of low heat conductivity, the heat generation cannot be easily swept away from the drilling point. The temperature measurement obtained from the thermocouples cannot offer the precise surface temperature value approximately at the drilling point. Due to this deficiency, many researchers have lately begun to use the finite-element (FE) technique to simulate the drilling process (Davidson & James, Citation2003; Guo & Dornfeld, Citation2000). However, there are hardly any studies that have been tried to measure temperature distribution. Previous studies have only explored the heat reaction of the subjective bone utilizing the two-dimensional FE method (Alam et al., Citation2009, Citation2010; Tu et al., Citation2008). A recent study has focused (Tu et al., Citation2013) on three-dimensional modeling using the bone analog to investigate temperature distribution and has set a trend to use three-dimensional modelling in FE methods to analyze the temperature during the drilling process.
The major part of orthopedic, orthodontic and implant surgery involves drilling holes in the bones and teeth to mount screws. Various osseous models have been used to record implant drilling temperatures, including dead specimens, live animals, and humans; however, most of the available studies have been conducted upon dead specimens (in vitro), which cast shadow on the accuracy of the study results. There is a considerable difference between dead and living bones based on their density and cellularity (Haider et al., Citation1993), water content, fluid content and movements (Berman et al., Citation1984; Rogers et al., Citation1952) and, therefore, their electrical thermal conductivity (Vachoy, Citation1967). This difference may insinuate a slight diffraction on the anticipated results. However, it has been shown that there is no significant temperature difference between in vitro and in vivo studies (Matthews & Hirsch, Citation1972). Hence, the testing of dead specimens is advantageous in terms of applying pressure and testing the other mechanical properties of drilling. The aim of this review article is to critically evaluate drilling parameters to minimize the risk of thermal necrosis and to justify the parameters using the FE method, which often threaten the successful implementation.
2. Background
2.1. Search strategy
A systematic literature review was conducted according to the Preferred Reporting Items for Systematic Reviews and Meta-analysis (PRISMA) guidelines to identify all potential relevant studies using the PubMed®, Springer®, MEDLINE®, Scopus®, Web of Science® and Inspec® databases for reporting evaluation of thermal necrosis. Peer-reviewed journals were prioritized for data collection. The keywords searched were Thermal necrosis, optimal bone-drilling parameters, implant osteotomy, implant necrosis, FE modelling of bone drilling, and heat generation during drilling as shown in . Besides, the keywords were also combined for search, for example, thermal necrosis in dental implants, thermal necrosis in bone drilling, FE modelling in thermal necrosis, heat generated by implant drills, and effects of heat in bone drilling. The search strategy blends techniques of systematic, retrospective, citation, and targeted review.
2.2. Selection strategy
Some of the articles we found based on our keywords deviated from our context and so we had to sieve through them to retain the ones that were relevant. The articles related to heat generation during bone drilling, thermal injuries, FE simulation of tooth drilling and drilling parameters were included. Articles that did not comply with the keywords considered or those on the restoration of implants regardless of thermal injury were excluded as shown in . A systematic strategy was followed to accumulate journals that are informative of the drilling parameters including external and internal irrigation, effects of the drilling environment, type of bone structure, heat generation, method of heat measurement, and FE methods regardless of age, type of bone, and gender of the subject. The flow chart of study selection process is shown in . This review article outlines the parameters used to minimize thermal necrosis.
Table 1. Inclusion and exclusion criteria considered in present study
Figure 3. (a)Thermo-mechanically coupled model (Alam et al., Citation2014) (b) idealized mandible model (Fonseca et al., Citation2013)
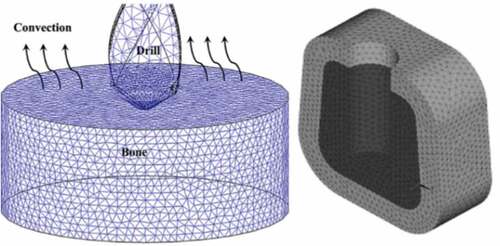
The summary of the recent research articles on drilling process optimization and FE methods considered in the study are presented in .
Table 2. Summary of the recent research articles on drilling process optimization and finite-element methods
3. Drilling parameters: osteology
3.1. Bone mineral density (BMD) and Bone sex
Successful implants are highly dependent on the location of the osteotomy (Watanabe et al., Citation1992; Yacker & Klein, Citation1996). The density of the bone varies greatly from individual to individual, even maxilla to mandible. The cortical bone is dense, because of which thermo-conductivity is relatively high and heat conduction from the pilot hole is agile. The cancellous bone is formed of lettuce-like structure and filled with water and lipids, making the heat produced hard enough to reach the bone surface. Bone architecture and vascularization show a vital part in the heat response of the exposed bone. Haider (Haider et al., Citation1993) finds that heat is better tolerated by spongy bones. Huiskes R (Huiskes, Citation1980) finds that resorption in cortical bone (with up to 550 μm) is higher than soft bone structures (maximum 180 μm). Yacker et al. (Yacker & Klein, Citation1996) based on their study conclude that the rise in temperature between compact bones and cancellous bones varies significantly regardless of the drill’s depth, a fact which is testified by G. Pearce (Pearce et al., Citation2005). These researchers tested for the density of the bone model after alternating the initial temperature. Results show that temperature elevation in high-density bones is higher than in low-density bone structures.
Besides, Sezek et al. (Sezek et al., Citation2012) conduct a study on six different bone mineral densities (BMD) exposed to drilling to conduct analytical studies. Compared to the experiment outcomes, analytical drilling analysis later disclosed that nearly 20% differences were observed. In their studies, they concluded that BMD should be at 2.4 g/cm2 in order to carry a procedure below the critical point in a safe zone. Most of the experiments were examined in various drilling materials such as rabbit mandible (Iyer et al., Citation1997), rabbit tibia (Cavalcante Gomes de Souza Carvalho et al., Citation2011), pig maxilla and mandible (Sharawy et al., Citation2002), pig rib (Watanabe et al., Citation1992), sheep tibia (Bachus et al., Citation2000; Buser et al., Citation1991), bovine cortical/medullary bone (Allsobrook et al., Citation2011; Brisman, Citation1996; Chacon et al., Citation2006; Cordioli & Majzoub, Citation1997; Yacker & Klein, Citation1996) and polymeric material (Harris & Kohles, Citation2001). To simulate live maxillofacial bone as drilled substance Acetal homopolymer was used (Harris & Kohles, Citation2001), but most studies were performed in death samples (In-vitro). However, Matthews et al. (Matthews & Hirsch, Citation1972) in their studies find no changes in in-vitro or in-vivo temperatures.
3.2. Drilling force
The amount of frictional force is directly proportional to the force applied to the drilling tool, the shape of the drilling tool, and the period of drilling. Matthews and Hirsch (Matthews & Hirsch, Citation1972) conduct a study using different drilling pressure and drilling speed. They find that the temperature rise is inversely proportional to the pressure forces. Brisman (Citation1996) confirms this statement using bovine femoral bone. Drilling forces and drilling torque are two different parameters. The factors influencing the insertion torque are mainly the bone density and hardness, non-standard drills, and tapered implant designs. Considerable amounts of studies show the methods to optimize the maximum and minimum drilling torque values for over-compression and so on. Neugebauer et al. (Citation2006) deem 50 Ncm drilling torque to be the upper limit, which should not be surpassed, while 35Ncm is optimal for the instant load protocol. On the other hand, Ottoni et al. (Citation2005) state that osseointegration of the implant requires a minimum of 32Ncm. Whereupon, Duyck et al. (Kilpatrick, Citation1958) assert that peri-implantitis is clearly caused by drilling torque greater than 50Ncm.
3.3. Drill speed, drilling depth, drilling method and drilling diameter
The results of research experiments conducted to assess the effect of drilling speed on thermal necrosis (Boyne, Citation1966; Calderwood et al., Citation1964; Kilpatrick, Citation1958; Pal & Saha, Citation1981) show that slow rotational speed controls the rise in frictional temperature in bone drilling (R. Anderson & Finlayson, Citation1943; Horner, Citation1961; Lentrodt & Bull, Citation1976; Manson & Dolan, Citation1966; PETERSON, Citation1952). Thompson (Manson & Dolan, Citation1966) focusses on the mechanical effects of the drilling to study the thermal changes at different speeds from 125 to 2000 rpm. Pallan (Citation1960) and Costich et al. (Citation1964) confirm that by not using a coolant, the temperature ranges from 38.3°C to 65.5°C with an upswing in the drill speed. The evidence-based recommendation by Eriksson et al. (Eriksson & Adell, Citation1986) demonstrated that the hand pieces for implant bed preparation should be of operating in range of 1500 to 2000 rpm and with high torque rating. Further, the effect of drilling depth has also been parameterized in some studies (Haider et al., Citation1993; Kay et al., Citation1991). Cordioli et al. (Cordioli & Majzoub, Citation1997) record that there is considerable amount of temperature rise at 8 mm versus 4 mm despite the drill diameter. Augustin et al., (Citation2008) experiment with drill diameters of 2.5, 3.2 and 4.5 mm; drill speed of 188, 462, 1,140 and 1,820 rpm; feed-rate of 24, 56, 84 and 196 mm/min; and drill point angle of 80°, 100° and 120°, and with external irrigation of water at 26°C. The study observed that, there were no significant changes in temperature with a drill point angle, but at a high feed rate and a high drill speed, the temperature elevations were magnificent. Researchers have also focused on the effect of drilling diameter and have thus concluded that drill speed has a higher impact on bone temperature increase than the drill diameter (Tehemar, Citation1999).
3.4. Temperature measurement
Measurement of rise in temperature shall be recorded either by direct method, for instance, thermocouple (Eriksson & Adell, Citation1986; Yacker & Klein, Citation1996) or indirect methods, including infrared thermography (Benington et al., Citation1996; Watanabe et al., Citation1992), mathematical calculation (Hültenschmidt, Citation1986), or by measuring the electrical power supply to the drill (Hültenschmidt, Citation1986). Accordingly, some studies focused on measuring temperature distribution have opted for thermocouple as a practice of choice for bone drilling (Augustin et al., Citation2008; Bachus et al., Citation2000; Brisman, Citation1996; Eriksson & Adell, Citation1986; Eriksson et al., Citation1984; Hillery & Shuaib, Citation1999; Matthews et al., Citation1984; Matthews & Hirsch, Citation1972; Yacker & Klein, Citation1996). However, thermocouples are not closer than 0.5 mm from the osteotomy site. Some researchers feel that the accuracy of the measuring values depends heavily on multiple factors. Thermocouples are considered to measure the spot temperatures above the massive average temperature (Cordioli & Majzoub, Citation1997).
3.5. Cooling methods
An irrigation system is always sought by the workers or researchers in heat-producing experiments. Two types of irrigation methods are used in osteological surgery; internal and external irrigation. However, studies show that internal irrigation has some advantages over external irrigation. In 1974, Huhule (Kirschner, Citation1975) demonstrated the internal method of cooling by improvising on the removal of the bone chip to ensure that no clogging occurred during the procedure. The effectiveness could also be enhanced irrespective of the cavity (Kirschner, Citation1975; Koch, Citation1976). Goran Augustin (Augustin et al., Citation2008) stated that in the drilling processes, it is mandatory to use at least external irrigation to prevent thermal necrosis and damage. However, Sener (Sener et al., Citation2009) concludes that external irrigation at room temperature is enough to cool throughout drilling that internal cooling is rather complicated and expensive (Möhlhenrich et al., Citation2015). Furthermore, Sezek et al., (Citation2012) prove that a tiny amount of cooling is usually achieved with natural moisture present in bones or due to saliva. They conducted the FEA, as well as other experimental studies and found that the temperature rise in experimental results was lagging by some degrees.
3.6. Drilling parameter-dentistry
Although drilling sampling is mostly done with bone elements and the studies on the effect of drilling in the oral cavity are rare, it is inevitable to investigate and validate the effect of thermal necrosis in dental implantations. The Ph level varies with time in the oral cavity; hence, these physical changes in the region of the oral cavity result in physical after-effects. It is therefore essential to generalize the factors that trigger thermal necrosis in dental implantation during bone structures. A disturbance in equilibrium, mainly because of the bacterial existence in nature, may be the cause of the pathological changes. So, the underlying thermal necrosis during drilling should be evaluated in the oral cavity as well. Thermal fluctuations, owing to the consumption of supreme or lower food temperatures, and thermal shocks due to dental treatment (Bjørndal, Citation2002; Piperno et al., Citation1982; Silvestri et al., Citation1977; Zach & Cohen, Citation1965), which may lead to thermal necrosis in tooth tissue. The heat transmitted depends on type of bur, cooling technique and rotational speed of drill.
3.7. Food consumption
The consumption of food may cause the rise and fall in temperature in the oral cavity, which may lead to thermal ratcheting (and if the missing tooth is replaced with metal implants). The temperature of the food varies from 70°C to 75°C, causing temperature changes in the oral cavity in the range of 5°C to 48°C. Due to this thermal change in the tooth environment, the teeth and the implants undergo thermal stress (Brown et al., Citation1972; Ting, Citation1970)
3.8. Thermal fatigue in teeth
Brown et al. (Brown et al., Citation1972) conducted a clear thermocycling study with extracted human and bovine teeth, which presents the results of experimental studies conducted with animal organisms to justify the likelihood and dissimilarity of animal teeth to human organisms in the scope. The teeth were subjected to the thermal cycling process at 90°F (32.23°C) −140 F (60°C). The same condition can be analogous to the ingestion of food and the following thermal fluctuations. When the tooth is exposed to lower temperatures, the enamel is subjected to contraction. However, dentin, which has the lower thermal diffusivity, retains its shape. This may induce tensile forces in enamel, resulting in surface cracks. On the other hand, when the temperature reaches a high level, the enamel develops compressive stress (Brown et al., Citation1972). Therefore, this temperature cycling can be mimicked by the thermocycling process in the laboratories for experimental processes. Brown developed a thermal cycling machine in his laboratory to examine six different types of teeth at different temperatures and at different times.
3.9. Cooling by coolant
The coolant protects the tooth from thermal shocks and thermal stress during the drilling process. In their paper, Carson et al. (Möhlhenrich et al., Citation2015) compare water-air coolant and air coolant using thermography. Due to the evaporative effects of the liquid around the teeth environment, the natural cooling is facilitated in the oral cavity area. Zach and Cohen (Citation1962) address a peculiar means of cooling, known as the “washed-field technique”. Alfred Schuchard (Schuchard & Watkins, Citation1961) addresses the possibility of providing air, water–air combination, and water steam to regulate the temperature in the oral cavity. He finds that no specific method of cooling is universally applicable in implant treatment. Thus, the part where the surgical method is performed, is very decisive. The most appropriate technique of irrigation is therefore, chosen accordingly. Lloyd et al. (Citation1978) discuss a set of cooling techniques and their efficacy while preparing teeth for implantation. For four cooling methods, comparisons are provided: Only air stream, spray of air and water, only water from a syringe, and water through hollow bur.
3.10. Rotational speed
The temperature in the pulp cavity kept as low as possible with improved rotating speeds and quick elimination of tooth structures. However, an uncertain conclusion has been drawn regarding temperature changes with increased rotational speeds (D. Anderson & Van Praagh, Citation1942; Lloyd et al., Citation1978; Walsh & Symmons, Citation1972). Temperature changes may differ from a few degrees to some hundred (D. Anderson & Van Praagh, Citation1942; Lloyd et al., Citation1978).
3.11. Temperature measurement
Temperature distribution during tooth clinical operative procedures has most commonly been analyzed with thermocouples (Dachi & Stigers, Citation1968; Fonseca et al., Citation2013). But, it is also reported that the source of error (Dansgaard & Jarby, Citation1958) could be mainly due to the use of thermocouple and that needs to be assessed or correlated with the point of measurements.
3.12. Finite-element methods
FE is an analytical method used to perform various biomechanical analyses in bone implants and see the drilling effect on success of implant. Many practical instances have been governed by multifactorial parameters. It is difficult to evaluate the performance of a single parameter, a combination of parameters or their interdependencies. FE simulations on the validated models possibly decrease the experimental efforts on drilling techniques. Several investigators have therefore advised to use FE methods to simulate the drilling procedure (Davidson & James, Citation2003; Guo & Dornfeld, Citation2000). Still, very limited studies investigated the highest temperature near drilled hole. Few studies have inspected the thermal reaction of bone during drilling using 2D FE models (Alam et al., Citation2010; Tu et al., Citation2013, Citation2008). In a latest study (Weinlaender, Citation1991), FEs based on a bone analog were used to model a three-dimensional bone-drilling process. Currently, most researchers are relying on elastic-plastic models to perform FEA (Sezek et al., Citation2012), using different software platforms, such as Ansys (Fonseca et al., Citation2013; Vathsala et al., Citation2019), MSC Marc (Alam et al., Citation2014; Davidson & James, Citation2003; Sezek et al., Citation2012) Pro/Engineer 2000i (Sevimay et al., Citation2005) and so on. As the real bone/tooth is sensible to heat and mechanical forces, the FE techniques utilize the thermo-mechanically coupled FE Model (Alam et al., Citation2014). Several studies only consider the mechanical analysis (Davidson & James, Citation2003; Sezek et al., Citation2012) and evaluate the Von mises stress components, due to relatively low anisotropic nature of cortical bone behavior (S. Li et al., Citation2013) and relatively smaller dimensions (compared to those in the model) of the bone constituents, the anisotropic and heterogeneous structure was approximated as a homogenous isotropic equivalent content. The material properties generally considered in the FE studies are given in . Alam et al. (Citation2014) describe the equation to calculate the elastic moduli of structures to utilize it in the FE model, such that the model can mimic the actual bone/tooth substance, and lead to results that are more accurate.
Table 3. Material properties used in FE Simulations
Researchers have not considered any restrictions on the development of models in any form. They have mostly used model-like cylindrical and square designs, to replicate the actual bone/tooth elements, the development of the models may require a lot of time and resources. The Johnson–Cook (JC) material model uses EquationEquation (1)(1)
(1) in the FE model to represent the thermal and mechanical behavior of bones/teeth and incorporates strain-rate dependent materials (Alam et al., Citation2014). The JC models have been used even in two-dimensional FE models (Alam et al., Citation2009, Citation2010)
where A, B, C and n are constants and ε, ε., ε.0 are the plastic strain, effective plastic strain rate, and reference strain rate, respectively. The effects of temperature in the equation are neglected in the FE models for drilling, as no data is available on the temperature-dependent plasticity. A, B, C and n constraints are obtained from previous studies (Alam et al., Citation2009; Davidson & James, Citation2003). If the FE models are used with the JC model, the results will be tested for different strain rates according to EquationEquation (1)(1)
(1) .
4. Discussion
4.1. Osteology
The atraumatic surgical procedure is important when placing the implants in the bone. The main cause of implant failure is heat generation and surgical trauma (Mediouni et al., Citation2017). Therefore, implant failure studies to prevent thermal necrosis seem to be specific to preventing implant surgical failure. Earlier studies were mostly associated with in vitro experimental studies (Augustin et al., Citation2008; Pearce et al., Citation2005) while the recent studies mostly depend on computational analysis and experiments (Mediouni et al., Citation2017). Computational Analysis provides greater scope for assessing the salient parameters that can be used to prevent thermal necrosis. Most studies have found that Drilling Speed, Drilling Feed, Drilling Diameter, and Drilling Forces are the main parameters for the operator to control thermal necrosis. Pearce et al. (Citation2005) investigated thermal bone damage or necrosis associated with orthopedic surgical procedures. During their studies on pig bones, they found that thermal necrosis could lead to infection and the inadvertent loosening of the implant subjects. It has been reported that if the bone is subjected to 56°C temperature for over 10s, necrosis appears. However, they did not compare or validate the results with the human bone model where drilling is done using K-wires, following micro examination using the scanning electron microscope (SEM). In their research, they used the drill with 656, 1180 and 2000 rpm speed, and discovered that reduced drilling speeds caused the greatest temperature rise. The temperature rise for 656 rpm was approximately twice that of 2000 rpm. The drilling speed of 1180 rpm appears to be the optimum for keeping the temperature low at both insertion speeds. The study also found that larger the drilling diameter, the higher the peak temperature. However, the authors have not discussed the effect of the increase in density during the k-wire drilling (due to the absence of a screw thread).
Inversely, Mohamed Mediouni et al. conducted a study in 3D simulation (Mediouni et al., Citation2017; Tu et al., Citation2013) by means of computational analysis. Their in-depth assessment was based on the known data points for bone (drill bit and bone) and their findings demonstrate the stress and the temperature produced when drilling cortical at a steady rotation of 600 rpm. Drilling 3 mm deep and feeding 1 mm/sec produced an axial force acting on a drill of about 50–80 Newton (N) and a temperature of 75°C. Once the feed rate was reduced to 0.1 mm/sec at the same rotational speed, the temperature was increased to 85°C. When the speed was up to 300 rpm, the temperature came down to 39°C. The findings, the depth of the drilling and the speed played an essential role in regulating the drilling temperature. Even though the above FEM studies provide an apparent insight into the force and temperature dynamics involved in bone drilling, it is still not enough to reveal the real-time data analysis. The set of known data points were used instead of parameter evaluation to support the argument of FEM with experiment results. An experiment was conducted by Tu et al., (Citation2013) using FEA to discuss the effect of the drilling speed on bone temperature distribution, the results showed that the higher the drill bit rotation, the higher the heat generation at the drilling pilot hole and the higher the thermally affected zone at constant feed rates. The numerical results were discussed with experiment results. The maximum difference in temperature predicted by the proposed equation in the numerical model is less than 3.5% (Abouzgia & James, Citation1997; Augustin et al., Citation2008; Brisman, Citation1996; Christie, Citation1981; Hillery & Shuaib, Citation1999; Matthews et al., Citation1984; Matthews & Hirsch, Citation1972).
Further, the set of simulations were carried out to investigate the rise of bone temperature corresponding to drilling speeds of n = 600, 800, and 1200 rpm. The experiments once again confirmed that the higher drilling speed generates a higher temperature rise. The peak temperature increases approximately by 92°C as the drilling speed is increased from 600 to 1200 rpm. After 4.3, 5.8 and 6.6 s, maximum temperatures are reached at drilling speeds of 600, 800 and 1200 rpm. The lower drill rate increases both the average bone temperature and the time to drill to the peak temperature (Davidson & James, Citation2003) (Reilly & Burstein, Citation1974). Matthews and Hirsch (Citation1972) have conducted similar experiments with nearly the same results. So, at peak temperatures, as classified by the drilling speed, higher speed causes higher temperatures rise.
Alam et al., (Citation2014) performed a virtual application of the saline cooling using the FE Method. The numerical results were almost the same as the experimental results, the study proves that higher drilling speed and the presence of cooling dramatically reduce the temperature distribution in the drilling vicinity area. The maximum temperature increase was 86 °C at 4000 rpm without saline cooling (irrigation). The cooling by saline solution was recorded to reach a 49°C maximum temperature. The temperature drop for the same drilling speeds was not reported when cooled with air. The temperature threshold for the thermal necrosis was below 1500 rpm; however, the highest possible temperature in drilling was lower in the presence of saline above 2500 rpm.
4.2. Dentistry
Since the thermocycling of the teeth surroundings can trigger stresses of tooth fatigue, implant failures, and post-operative pathological conditions, it is vital to differentiate the parameters in an elaborate manner in order to prevent these circumstances. However, some factors cannot be suppressed because they all belong to the behavioral, congenital aspects of the patient. These factors include food consumption, oral cavity PH, etc. Nevertheless, some of the underlying surgical factors could be controlled. Although the type of bur, the cooling methods and the speed of the instruments are important factors in the generation of heat, adequate irrigation of the surgical area is even more important. The “washed-field technique” discussed by Zach & Cohen (Zach & Cohen, Citation1962) in their studies has been shown to be an effective cooling procedure. Lloyd (Lloyd et al., Citation1978) and Schuchard (Dachi & Stigers, Citation1968) show that wet cooling techniques provide better temperature control than air-cooling and improve the rate of chips removal from drilling. They confirm that without the cooling method, a considerable amount of heat is deposited by bur in the tooth, resulting in an excessive temperature increase (Christensen, Citation1973; Langeland & Langeland, Citation1968; Peyton, Citation1955, Citation1958) leading to mechanical damage to the tooth structure due to thermal stress.
Langeland (Langeland, K., & Langeland, L. K., 1968) argues that water-cooling is best done even for a short time in natural contact, but, on the other hand, Schuchard (Schuchard & Watkins, 1965), Stigers (Dachi & Stigers, 1968), Carlton (Carlton & Dorman, 1969) argue that air-cooling is sufficient. However, this statement is numerically justified by Carlton and Dorman (Fonseca et al., Citation2013) who report dentin temperatures of 267 °F (130.6°C) and pulp temperatures of 140 °F in the presence of air coolant, while the respective temperatures are 257 °F (125°C) and 79.9 °F (26°C) in case of water spray. Typically, in water-spray cooling systems, the flow rate is maintained between 30 and 50 ml/minute; and the air-water technique is enough if it is maintained between 35 and 50 ml/minute (Lloyd et al., Citation1978). Using a handheld syringe, rather than other methods, has some negative effects mainly due to the inaccurate focusing on the water stream. Schuchard and Watkins (Citation1961) discuss that the causes of errors in temperature measurements are (a) Thermo-metric lag, (b) the lag of the measuring instrument, (c) current leakage, (d) sensitivity bulb size, and (e) heat loss in the conducting wires in contrast to the mercury thermometer. Thermal conductivity of the enamel dentine pulp is relatively small compared to metal. Even more, heat dissipation from the surface is higher than into the dentine, as it is the poor conductor (Dachi & Stigers, Citation1968). The thermal stress may lead to the impairments among enamel and dentin contacts (Manson & Dolan, Citation1966). Brown et al. (Brown et al., Citation1972) show that bovine teeth are more prone to thermal necrosis than human teeth and that the dryness of the teeth is a serious cause of cracking, which occurs due to shrinking. Such a declaration questions the conformity of the assessed parameters in drilling with animal organisms in vitro studies. Not many studies have investigated this issue; rather they have been exclusively concerned with the assessment of the drilling parameter. Bovine teeth have two-thirds of the ultimate tensile strength of human teeth (Jo et al., Citation2011). Yet the tensile strength of both teeth in the axial direction is three times higher than their transverse tensile strength. As suggested in Osteology, most researchers recommend FEA for a precise point-oriented analysis. Fonseca et al. (Citation2013) use the Pork Mandible to evaluate the FE model and carry out the numerical analysis with the transient heat conduction by modeling the heat flux from the drilling process. In this process, the FE mesh is dissolved by cortical and trabecular bones and the drilling hole is the same as the cylindrical portion of the drill hole. Twenty nodes with a mesh size of 0.5 mm were considered in their research model. They simulated the study with an original temperature of 750 rpm and 20°C. For experimental validation, four idealized cross-sections of the mandible were used. Cortical bone of 2 mm with medium density, low-density trabecular bone, cortical bone of 1 mm thickness with medium density, and low-density trabecular bone were tested to compare the results.
5. Conclusion
Drilling in bone structures generates heat, which sometimes leads to thermal Necrosis. It is found that temperature ranging between 44°C and 47°C is the threshold value after which thermal injuries occur. A temperature range of 700°C-750°C is regarded as the non-reversible cell death drilling point. Drilling chamber heat generation relies primarily on drill speed, feed rate, feed depth, irrigation, and drill diameter. Drill speed and drill depths make a substantial contribution to heat generation. No significant changes in temperature increase are reported with drill angles. An increase in drill speeds produces more heat and generally, 150–2500 rpm is considered the medium drill speed. Few studies have conducted tests with higher rotational speeds such as 160,000 rpm and 290,000 rpm. External irrigation is most often preferred over medium rotational speeds. Although internal irrigation methods provide better cooling and material removal, they are complex and costly. Air-cooling does not provide the required cooling and water-related cooling techniques are used noticeably. It is even obvious that wet drilling improves quality, reduces the temperature induced and increases the removal rate of the material. Using a hand-held syringe during dental implantation fills the fundamental requirements despite the inappropriate focus on the water stream. The injection of water through the hollow bur increases the cooling effect, reduces water permits, and improves the visibility of the drill point and the patient’s convenience. The optimal parameter for the reduction of thermal necrosis cannot be justified precisely because the tests are conducted in a controlled way. Multifactorial analysis can be assessed using FE modeling. Thermocouples are used in many cases to explore near-end temperature distributions. Thermal cycling in the tooth reverses the stress distribution in all directions and trigger fatigue failure, that tends to deteriorate the teeth and implants. Clinically observed 500°C temperature difference at higher stress levels leads to cracking and sometimes implant failure. Very few papers have investigated the likelihood of differences in outcomes between in vitro animal samples and human samples. Notable deviations were observed in some animal and human model samples. The review clearly indicates that more histological, vitality tests to be carried out considering the circumstances of multiple factors to assess the selection of optimum parameters.
Additional information
Funding
Notes on contributors
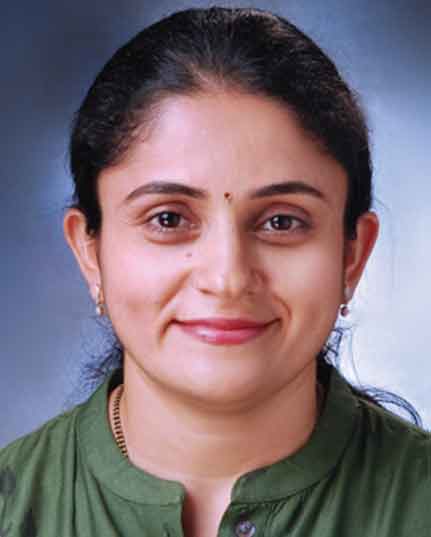
Nayana Prabhu
Dr. Nayana Prabhu is an Associate Professor in the Department of Prosthodontics and Crown & Bridge and Coordinator of Manipal Implant Program at Manipal College of Dental Sciences, Manipal. She has received her Master’s degree from Manipal Academy of Higher Education, in 2006. She has more than 18 years of teaching experience in Dentistry. Her research interest includes the development of Implant surfaces, Dental Materials and Maxillofacial Prosthodontics. She is involved in the academic activities of the Undergraduate and Postgraduate students like Seminars, Journal Club discussions, Case discussions, etc., and guide for Postgraduate dissertation studies. She has guided many Undergraduate and Postgraduate students in research and project works. She has published several research articles in National and International Journals of repute.
References
- Abouzgia, M. B., & James, D. F. (1995). Measurements of shaft speed while drilling through bone. Journal of Oral and Maxillofacial Surgery, 53(11), 1308–19. https://doi.org/10.1016/0278-2391(95)90590-1
- Abouzgia, M. B., & James, D. F. (1997). Temperature rise during drilling through bone. The International journal of oral & maxillofacial implants, 12(3), 342–353.
- Alam, K., Khan, M., & Silberschmidt, V. V. (2014). 3D finite-element modelling of drilling cortical bone: Temperature analysis. Journal of Medical and Biological Engineering, 34(6), 618–623. DOI: 10.5405/jmbe.1585
- Alam, K., Mitrofanov, A. V., & Silberschmidt, V. V. (2009). Finite element analysis of forces of plane cutting of cortical bone. Computational Materials Science, 46(3), 738–743. https://doi.org/10.1016/j.commatsci.2009.04.035
- Alam, K., Mitrofanov, A. V., & Silberschmidt, V. V. (2010). Thermal analysis of orthogonal cutting of cortical bone using finite element simulations. International Journal of Experimental and Computational Biomechanics, 1(3), 236. https://doi.org/10.1504/IJECB.2010.035259
- Allsobrook, O. F., Leichter, J., Holborow, D., & Swain, M. (2011). Descriptive study of the longevity of dental implant surgery drills. Clinical Implant Dentistry and Related Research, 13(3), 244–254. https://doi.org/10.1111/j.1708-8208.2009.00205.x
- Anderson, D. J., & Van Praagh, G. (1942). Preliminary investigation of the temperature produced in Burring. Brit. Dent J, 73, 62–64.
- Anderson, R., & Finlayson, B. L. (1943). Sequelae of transfixation of bone. Surgery, 13(1), 46–54. https://doi.org/10.5555/uri:pii:S0039606043903939
- Augustin, G., Davila, S., Mihoci, K., Udiljak, T., Vedrina, D. S., & Antabak, A. (2008). Thermal osteonecrosis and bone drilling parameters revisited. Archives of Orthopaedic and Trauma Surgery, 128(1), 71–77. https://doi.org/10.1007/s00402-007-0427-3
- Bachus, K. N., Rondina, M. T., & Hutchinson, D. T. (2000). The effects of drilling force on cortical temperatures and their duration: An in vitro study. Medical Engineering & Physics, 22(10), 685–691. https://doi.org/10.1016/S1350-4533(01)00016-9
- Benington, I. C., Biagioni, P. A., Crossey, P. J., Hussey, D. L., Sheridan, S., & Lamey, P. J. (1996). Temperature changes in bovine mandibular bone during implant site preparation: An assessment using infra-red thermography. Journal of Dentistry, 24(4), 263–267. https://doi.org/10.1016/0300-5712(95)00072-0
- Berman, A. T., Reid, J. S., Yanicko, J. D., Sih, G. C., & Zimmerman, M. R. (1984). Thermally induced bone necrosis in rabbits. Relation to implant failure in humans. Clinical Orthopaedics and Related Research, (186), 284–292. https://journals.lww.com/clinorthop/Abstract/1984/06000/Thermally_Induced_Bone_Necrosis_in_Rabbits_.44.aspx
- Bjørndal, L. (2002). Dentin and pulp reactions to caries and operative treatment: Biological variables affecting treatment outcome. Endodontic Topics, 2(1), 10–23. https://doi.org/10.1034/j.1601-1546.2002.20102.x
- Boyne, P. J. (1966). Histologic response of bone to sectioning by high-speed rotary instruments. Journal of Dental Research, 45(2), 270–276. https://doi.org/10.1177/00220345660450020901
- Brisman, D. L. (1996). The effect of speed, pressure, and time on bone temperature during the drilling of implant sites. International Journal of Oral & Maxillofacial Implants, 11, 1. PMID: 8820120
- Brown, W. S., Jacobs, H. R., & Thompson, R. E. (1972). Thermal fatigue in teeth. Journal of Dental Research, 51(2), 461–467. https://doi.org/10.1177/00220345720510023601
- Buser, D., Schenk, R. K., Steinemann, S., Fiorellini, J. P., Fox, C. H., & Stich, H. (1991). Influence of surface characteristics on bone integration of titanium implants. A histomorphometric study in miniature pigs. Journal of Biomedical Materials Research, 25(7), 889–902. https://doi.org/10.1002/jbm.820250708
- Calderwood, R. G., Hera, S. S., Davis, J. R., & Waite, D. E. (1964). A comparison of the healing rate of bone after the production of defects by various rotary instruments. Journal of Dental Research, 43(2), 207–216. https://doi.org/10.1177/00220345640430020701
- Carlton, M. L., Jr, & Dorman, H. L. (1969). Comparison of dentin and pulp temperatures during cavity preparation. Texas Dental Journal, 87(5), 7. PMID: 5253214
- Cavalcante Gomes de Souza Carvalho, A., Pereira Queiroz, T., Okamoto, R., Margonar, R., Rangel Garcia, I., & Magro Filho, O. (2011). Evaluation of bone heating, immediate bone cell viability, and wear of high-resistance drills after the creation of implant osteotomies in rabbit tibias. International Journal of Oral & Maxillofacial Implants, 26(6), 1193–1201. PMID: 22167423
- Chacon, G. E., Bower, D. L., Larsen, P. E., McGlumphy, E. A., & Beck, F. M. (2006). Heat production by 3 implant drill systems after repeated drilling and sterilization. Journal of oral and maxillofacial surgery : official journal of the American Association of Oral and Maxillofacial Surgeons, 64(2), 265–269. https://doi.org/10.1016/j.joms.2005.10.011
- Christensen, D. O. (1973). Temperature and stress profiles in teeth during cavity preparation [Thesis]. Salt Lake City: University of utah.
- Christie, J. (1981). Surgical heat injury of bone. Injury, 13(3), 188–190. https://doi.org/10.1016/0020-1383(81)90236-9
- Cordioli, G., & Majzoub, Z. (1997). Heat generation during implant site preparation: An in vitro study. International Journal of Oral & Maxillofacial Implants, 12(2), 186–193. PMID: 9109268
- Costich, E. R., Youngblood, P. J., & Walden, J. M. (1964). A study of the effects of high-speed rotary instruments on bone repair in dogs. Oral Surgery, Oral Medicine, Oral Pathology, 17(5), 563–571. https://doi.org/10.1016/0030-4220(64)90359-7
- Dachi, S. F., & Stigers, R. W. (1968). Pulpal effects of water and air coolants used in high-speed cavity preparations. The Journal of the American Dental Association, 76(1), 95–98. https://doi.org/10.14219/jada.archive.1968.0025
- Dansgaard, W., & Jarby, S. (1958). Measurement of Non-stationary Temperatures in Small Bodies. Odont. Tskr, 66, 474–502.
- Davidson, S. R., & James, D. F. (2003). Drilling in bone: Modeling heat generation and temperature distribution. Journal of Biomechanical Engineering, 125(3), 305–314. https://doi.org/10.1115/1.1535190
- Eriksson, A. R., & Albrektsson, T. (1983). Temperature threshold levels for heat-induced bone tissue injury: A vital-microscopic study in the rabbit. Journal of Prosthetic Dentistry, 50(1), 101–107. https://doi.org/10.1016/0022-3913(83)90174-9
- Eriksson, A. R., Albrektsson, T., & Albrektsson, B. (1984). Heat caused by drilling cortical bone: Temperature measured in vivo in patients and animals. Acta orthopaedica Scandinavica, 55(6), 629–631. https://doi.org/10.3109/17453678408992410
- Eriksson, R. A., & Adell, R. (1986). Temperatures during drilling for the placement of implants using the osseointegration technique. Journal of Oral and Maxillofacial Surgery, 44(1), 4–7. https://doi.org/10.1016/0278-2391(86)90006-6
- Eriksson, R. A., & Albrektsson, T. (1984). The effect of heat on bone regeneration: An experimental study in the rabbit using the bone growth chamber. Journal of Oral and Maxillofacial Surgery, 42(11), 705–711. https://doi.org/10.1016/0278-2391(84)90417-8
- Fonseca, E. M., Magalhães, K., Fernandes, M. G. A., Barbosa, M. P., & Sousa, G. (2013, November). Numerical model of thermal necrosis due a dental drilling process. In II International Conference on Biodental Engineering, J. Natal et al ( Ed.), Taylor & francis group, London, CRC Press(pp. 69–73). https://www.taylorfrancis.com/chapters/numerical-model-thermal-necrosis-due-dental-drilling-process-fonseca-magalh%C3%A3es-fernandes-barbosa-sousa/e/10.1201/b15986-19?context=ubx&refId=dae7452d-da51-4b16-b8d2-70bf6cff5a1d
- Guo, Y. B., & Dornfeld, D. A. (2000). Finite element modeling of burr formation process in drilling 304 stainless steel. Journal of Manufacturing Science and Engineering, 122(4), 612–619. https://doi.org/10.1115/1.1285885
- Haider, R., Watzek, G., & Plenk, J. H. (1993). Effects of drill cooling and bone structure on IMZ implant fixation. International Journal of Oral & Maxillofacial Implants, 8(1), 83–91. PMID: 8468088
- Harris, B. H., & Kohles, S. S. (2001). Effects of mechanical and thermal fatigue on dental drill performance. International Journal of Oral & Maxillofacial Implants, 16(6), 819–826. https://pubmed.ncbi.nlm.nih.gov/11769832/
- Higuchi, K. W., Folmer, T., & Kultje, C. (1995). Implant survival rates in partially edentulous patients: A 3-year prospective multicenter study. Journal of Oral and Maxillofacial Surgery, 53(3), 264–268. https://doi.org/10.1016/0278-2391(95)90222-8
- Hillery, M. T., & Shuaib, I. (1999). Temperature effects in the drilling of human and bovine bone. Journal of Materials Processing Technology, 92, 302–308. https://doi.org/10.1016/S0924-0136(99)00155-7
- Horner, D. B. (1961). A self-powered low-speed surgical drill: Prevention of thermal necrosis. Am. J. Orthop, 3, 278–283.
- Huiskes, R. (1980). Some fundamental aspects of human joint replacement: Analyses of stresses and heat conduction in bone-prosthesis structures. Acta orthopaedica Scandinavica, 51(sup185), 3–208. https://doi.org/10.3109/ort.1980.51.suppl-185.01
- Hültenschmidt, D. (1986). Das Temperaturverhalten bei der Bearbeitung von Knochen, ein Vergleich verschiedener Sägeverfahren (Doctoral dissertation, Verlag nicht ermittelbar).
- Iyer, S., Weiss, C., & Mehta, A. (1997). Effects of drill speed on heat production and the rate and quality of bone formation in dental implant osteotomies. Part I: Relationship between drill speed and heat production. International Journal of Prosthodontics, 10(5), 536–540. https://pubmed.ncbi.nlm.nih.gov/9495174/
- Jo, K. H., Yoon, K. H., Park, K. S., Bae, J. H., You, K. H., Han, J. H., … Cheong, J. K. (2011). Thermally induced bone necrosis during implant surgery: 3 case reports. Journal of the Korean Association of Oral and Maxillofacial Surgeons, 37(5), 406–414. https://doi.org/10.5125/jkaoms.2011.37.5.406
- Kay, J. F., Gilman, L., & May, T. C. (1991). The tri-spade drill for endosseous dental implant installation. The Journal of Oral Implantology, 17(4), 424–428. https://pubmed.ncbi.nlm.nih.gov/1813652/
- Kilpatrick, H. C. (1958). Removal of impacted third molars utilizing speeds up to 200,000 RPM. Oral Surgery, Oral Medicine, Oral Pathology and Oral Radiology, 11(4), 364–369. https://doi.org/10.1016/0030-4220(58)90073-2
- Kirschner, V. H. (1975). Entwicklung einer Innenkuhlung fur chirugische Bohrer. Dtsch. Zahnarztl Z., 30, 436–438.
- Koch, W. L. (1976). Die zweiphasige enossale Implantation von intramobilen Zylinderimplantaten-IMZ. Quintessenz, 27(3), 21–27. https://pubmed.ncbi.nlm.nih.gov/1072103/
- Langeland, K., & Langeland, L. K. (1968). Cutting procedures with minimized trauma. The Journal of the American Dental Association, 76(5), 991–1005. https://doi.org/10.14219/jada.archive.1968.0181
- Lentrodt, J., & Bull, H. G. (1976). Tierexperimentelle Untersuchungen zur Frage der Knochenregeneration nach Bohrvongangen im Knochen. Deutsche zahnarztliche Zeitschrift, 31(2), 115. https://pubmed.ncbi.nlm.nih.gov/56259/
- Li, S., Demirci, E., & Silberschmidt, V. V. (2013). Variability and anisotropy of mechanical behavior of cortical bone in tension and compression. Journal of the Mechanical Behavior of Biomedical Materials, 21, 109–120. https://doi.org/10.1016/j.jmbbm.2013.02.021
- Li, W., Chow, J., Hui, E., Lee, P. K. M., & Chow, R. (2009). Retrospective study on immediate functional loading of edentulous maxillas and mandibles with 690 implants, up to 71 months of follow-up. Journal of Oral and Maxillofacial Surgery, 67(12), 2653–2662. https://doi.org/10.1016/j.joms.2009.07.015
- Lloyd, B. A., Rich, J. A., & Brown, W. S. Effect of cooling techniques on temperature control and cutting rate for high-speed dental drills. (1978). Journal of Dental Research, 57(5–6), 675–684. HUDSON, D.C., and SWEENEY, W.T.: Temperature developed in rotating Dental Cutting Instruments, JADA 48: 127-133, 1954.. https://doi.org/10.1177/00220345780570050201
- Ludewig, R. (1972). Temperaturmessungen beim Knochensagen [thesis]. Gissen: Univ. of Gissen.
- Manson, S. S., & Dolan, T. J. (1966). Thermal stress and low cycle fatigue.
- Matthews, L. S., Green, C. A., & Goldstein, S. A. (1984). The thermal effects of skeletal fixation-pin insertion in bone. JBJS, 66(7), 1077–1083. https://doi.org/10.2106/00004623-198466070-00015
- Matthews, L. S., & Hirsch, C. (1972). Temperatures measured in human cortical bone when drilling. JBJS, 54(2), 297–308. https://doi.org/10.2106/00004623-197254020-00008
- Mazzocchi, A., Passi, L., & Moretti, R. (2007). Retrospective analysis of 736 implants inserted without antibiotic therapy. Journal of Oral and Maxillofacial Surgery, 65(11), 2321–2323. https://doi.org/10.1016/j.joms.2007.06.620
- Mediouni, M., Schlatterer, D. R., Khoury, A., Von Bergen, T., Shetty, S. H., Arora, M., … Volosnikov, A. (2017). Optimal parameters to avoid thermal necrosis during bone drilling: A finite element analysis. Journal of Orthopaedic Research, 35(11), 2386–2391. https://doi.org/10.1002/jor.23542
- Möhlhenrich, S. C., Modabber, A., Steiner, T., Mitchell, D. A., & Hölzle, F. (2015). Heat generation and drill wear during dental implant site preparation: Systematic review. British Journal of Oral and Maxillofacial Surgery, 53(8), 679–689. https://doi.org/10.1016/j.bjoms.2015.05.004
- Nam, O., Yu, W., Choi, M. Y., & Kyung, H. M. (2006). Monitoring of bone temperature during osseous preparation for orthodontic micro-screw implants: Effect of motor speed and ressure. In Key Engineering Materials (Vol. 321, pp. 1044–1047)., Trans Tech Publications.
- Neugebauer, J., Traini, T., Thams, U., Piattelli, A., & Zöller, J. E. (2006). Peri‐implant bone organization under immediate loading state. Circularly polarized light analyses: A minipig study. Journal of Periodontology, 77(2), 152–160. https://doi.org/10.1902/jop.2006.040360
- Ottoni, J. M. P., Oliveira, Z. F. L., Mansini, R., & Cabral, A. M. (2005). Correlation between placement torque and survival of single-tooth implants. International Journal of Oral & Maxillofacial Implants, 20, 5. http://www.quintpub.com/journals/omi/abstract.php?article_id=1973#.YA2FP-gzbIU
- Pal, S., & Saha, S. (1981). Effect of cutting speeds on temperature during drilling of bone. Proc Am Coll Eng Med Biol, 23, 289.
- Pallan, F. G. (1960). Histological changes in bone after insertdon of skeletal fixation pins. Journal of Oral Surgery, Anesthesia, and Hospital Dental Service, 18, 400. https://pubmed.ncbi.nlm.nih.gov/14429940/
- Pearce, G., Bainbridge, C., Patrick, J., Lenz, M., & Jones, G. (2005). An investigation into thermal necrosis of bone associated with surgical procedures. WIT Transactions on Biomedicine and Health, 8. https://www.witpress.com/elibrary/wit-transactions-on-biomedicine-and-health/8/15491
- PETERSON, L. T. (1952). Principles of internal fixation with plates and screws. A.M.A. Archives of Surgery, 64(3), 345–354. https://doi.org/10.1001/archsurg.1952.01260010359009
- Peyton, F. A. (1955). Temperature rise in teeth developed by rotating instruments. The Journal of the American Dental Association, 50(6), 629–632. https://doi.org/10.14219/jada.archive.1955.0117
- Peyton, F. A. (1958). Effectiveness of water coolants with rotary cutting instruments. The Journal of the American Dental Association, 56(5), 664–675. https://doi.org/10.14219/jada.archive.1958.0099
- Piperno, S., Barouch, E., Hirsch, S. M., & Kaim, J. M. (1982). Thermal discomfort of teeth related to presence or absence of cement bases under amalgam restorations. Operative Dentistry, 7(3), 92.
- Reilly, D. T., & Burstein, A. H. (1974). The mechanical properties of cortical bone. JBJS, 56(5), 1001–1022. https://doi.org/10.2106/00004623-197456050-00012
- Rhinelander, F. W., Nelson, C. L., Stewart, R. D., & Stewart, C. L. (1979). Experimental reaming of the proximal femur and acrylic cement implantation: Vascular and histologic effects. Clinical Orthopaedics and Related Research, (141), 74–89. https://journals.lww.com/clinorthop/Citation/1979/06000/Experimental_Reaming_of_the_Proximal_Femur_and.9.aspx
- Rogers, H. J., Weidmann, S. M., & Parkinson, A. (1952). Studies on the skeletal tissues. 2. The collagen content of bones from rabbits, oxen and humans. Biochemical Journal, 50(4), 537. https://doi.org/10.1042/bj0500537
- Schuchard, A., & Watkins, C. (1961). Temperature response to increased rotational speeds. Journal of Prosthetic Dentistry, 11(2), 313–317. https://doi.org/10.1016/0022-3913(61)90207-4
- Schuchard, A., & Watkins, C. E. (1965). Thermal and histologic response to high-speed and ultrahigh speed cutting in tooth structure. The Journal of the American Dental Association, 71(6), 1451–1458. https://doi.org/10.14219/jada.archive.1965.0009
- Sener, B. C., Dergin, G., Gursoy, B., Kelesoglu, E., & Slih, I. (2009). Effects of irrigation temperature on heat control in vitro at different drilling depths. Clinical Oral Implants Research, 20(3), 294–298. https://doi.org/10.1111/j.1600-0501.2008.01643.x
- Sevimay, M., Turhan, F., Kiliçarslan, M. A., & Eskitascioglu, G. (2005). Three-dimensional finite element analysis of the effect of different bone quality on stress distribution in an implant-supported crown. The Journal of Prosthetic Dentistry, 93(3), 227–234. https://doi.org/10.1016/j.prosdent.2004.12.019
- Sezek, S., Aksakal, B., & Karaca, F. (2012). Influence of drill parameters on bone temperature and necrosis: A FEM modelling and in vitro experiments. Computational Materials Science, 60, 13–18. https://doi.org/10.1016/j.commatsci.2012.03.012
- Sharawy, M., Misch, C. E., Weller, N., & Tehemar, S. (2002). Heat generation during implant drilling: The significance of motor speed. Journal of Oral and Maxillofacial Surgery, 60(10), 1160–1169. https://doi.org/10.1053/joms.2002.34992
- Silvestri, J. A., Cohen, S. H., & Wetz, J. H. (1977). Character and frequency of discomfort immediately following restorative procedures. Journal of the American Dental Association (1939), 95(1), 85–89. https://doi.org/10.14219/jada.archive.1977.0546
- Tehemar, S. H. (1999). Factors affecting heat generation during implant site preparation: A review of biologic observations and future considerations. The International Journal of Oral & Maxillofacial Implants, 14(1), 127–136.
- Ting, V. C. (1970). Numerical Analysis of Transient Temperature and Thermal Stresses in Dental Teeth (Doctoral dissertation, Department of Mechanical Engineering, University of Utah.).
- Toews, A. R., Bailey, J. V., Townsend, H. G., & Barber, S. M. (1999). Effect of feed rate and drill speed on temperatures in equine cortical bone. American Journal of Veterinary Research, 60(8), 942–944. https://pubmed.ncbi.nlm.nih.gov/10451201/
- Tu, Y. K., Chen, L. W., Ciou, J. S., Hsiao, C. K., & Chen, Y. C. (2013). Finite element simulations of bone temperature rise during bone drilling based on a bone analog. Journal of Medical and Biological Engineering, 33(3), 269–274. https://doi.org/10.5405/jmbe.1366
- Tu, Y. K., Chen, L. W., Huang, C. C., Chen, Y. C., Tsai, H. H., & Lin, L. C. (2008, May). Finite element simulation of drill bit and bone thermal contact during drilling. In 2008 2nd International Conference on Bioinformatics and Biomedical Engineering, (pp. 1268–1271). IEEE.
- Vachoy, R. I. (1967). In vivo determination of thermal conductivity of bone using the thermal comparator technique. In Digest of the Seventh International Conference of Medical and Biological Engineering. Stockholm, Sweden; 1967 (Vol. 502).
- Vathsala, P., Noronha, D. J., Nithesh, N., & Manjunath, S. (2019). A comparative study on the effect of stress in dental implant structure using finite element analysis. International Journal of Mechanical and Production Engineering Research and Development, 9(2), 709–717.
- Walsh, J. P., & Symmons, H. F. (1972). A comparison of the heat production and mechanical efficiency of diamond instruments, stones, and burs at 3000 and 60,000 rpm. The New Zealand Dental Journal, 68(311), 58–64. https://pubmed.ncbi.nlm.nih.gov/4567495/
- Watanabe, F., Tawada, Y., Komatsu, S., & Hata, Y. (1992). Heat distribution in bone during preparation of implant sites: Heat analysis by real-time thermography. International Journal of Oral & Maxillofacial Implants, 7(2), 212–219. https://www.ngt.ndu.ac.jp/cb/research/achieve/paper/040-1992.htm
- Weinlaender, M. (1991). Bone growth around dental implants. Dental Clinics of North America, 35(3), 585–601. https://pubmed.ncbi.nlm.nih.gov/1879579/
- Wiggins, K. L., & Malkin, S. (1976). Drilling of bone. Journal of Biomechanics, 9(9), 553–559. https://doi.org/10.1016/0021-9290(76)90095–6
- Yacker, M. J., & Klein, M. (1996). The effect of irrigation on osteotomy depth and bur diameter. International Journal of Oral & Maxillofacial Implants, 11(5), 634–638.PMID: 8908862
- Zach, L., & Cohen, G. (1962). Thermogenesis in operative techniques: Comparison of four methods. Journal of Prosthetic Dentistry, 12(5), 977–984. https://doi.org/10.1016/0022-3913(62)90051-3
- Zach, L., & Cohen, G. (1965). Pulp response to externally applied heat. Oral Surgery, Oral Medicine, Oral Pathology, 19(4), 515–530. https://doi.org/10.1016/0030-4220(65)90015-0