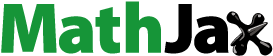
Abstract
The current study’s objective is to investigate the impact of nanoclay on the tensile and wear properties of glass fiber-epoxy-nanoclay ternary nanocomposite. Three types of composites are produced by hand lay-up process and compression molding. Tensile and wear tests are executed according to ASTM standards. The findings disclosed that nanoclay enhanced the tensile properties of glass fiber-epoxy-nanoclay ternary nanocomposite. The causes for the failure under tensile load are revealed by SEM micrographs. Response surface methodology (RSM) is applied to analyse the wear loss of nanocomposite. The “Box–Behnken method” is employed for experimental design to establish the main and interaction effects among factors comprising nanoclay (NC), load, and sliding distance in three levels (0, 2, and 4 wt.% for nanoclay; 1, 3, and 5 kg for load; and 300, 600, and 900 rpm for sliding distance). The RSM offers a strong confidence model for each response. Also, RSM models are often used to estimate the optimum case with the minimum mass loss. The optimum results are estimated for the combination of 4 wt.% nanoclay, 1 kg load, and 300 rpm for sliding distance. Experimental test results revealed an agreement with the predicted values.
PUBLIC INTEREST STATEMENT
In various applications, there is a growing market for the use of exceptional functioning and lightweight composites to replace conventional metals. In many applications, polymer matrix composites (PMC) are commonly used as structural materials. In recent days, nanoparticles and inorganic fillers have been used progressively in PMCs to boost their performance and applications in many fields. In this article, research is carried out on the effect of nanoclay on the tensile and wear properties of ternary nanocomposite glass fiber-epoxy-nanoclay.
1. Introduction
There is a growing market for the usage of exceptional functioning and light-weight composites to substitute traditional metals in different applications (Rajak et al., Citation2019). Polymer matrix composites (PMC) are generally used as structural materials in many applications. Some examples of PMCs’ applications are sand and sludge transporting pipelines, helicopter rotor blades, automobile body parts, and airplane body parts. Resistance to particle erosion (wear) is an essential property in aforesaid applications since these parts are frequently operated in surroundings with abrasive (sand) particles (Chawla, Citation2012; Patnaik et al., Citation2010; Thomas et al., Citation2016).
One of the alternatives suggested to polymers is to introduce reinforcement to boost the mechanical, wear, and thermal properties (Shettar, Kini et al., Citation2020). The reinforcements used to improve the composite’s aforesaid properties are distinguished as whiskers, fibers, micro, and nanoparticles. Nanoparticles and inorganic fillers have been gradually being used in PMCs in current days to enhance their performance (Friedrich, Citation2018). Owed to the higher area of the surface and great aspect ratio of nanoparticles, the load is passed on to nanoparticles from the matrix, and the matrix properties could be enhanced (Fu et al., Citation2019; Islam et al., Citation2013). Nanoparticles display different properties compared to their bigger counterparts. Nanoparticles tender higher reinforcing competence owing to their higher aspect ratios (Shettar, Achutha Kini et al., Citation2017). The degree of mixing (uniformity) and particle size have a substantial effect on the nanocomposite properties. The deciding factors, including the kinds of nanoparticles and its volume percentage, resins, and preparation procedure, significantly impact the properties of end products (Müller et al., Citation2017; Sahoo & Tripathy, Citation2017). Carbon nanofibers, nanotubes, and nanoclays are optimum contenders for such reinforcements, with respect to their load-bearing abilities.
Nanoclay is the utmost frequently employed and widely explored nanoparticles with polymer nanocomposites. Due to its easiness in usage, ecological usefulness, and thorough chemistry, nanoclay has earned importance over other nanoparticles (Shettar et al., Citation2017; Shettar et al., Citation2019a; Shettar et al., Citation2019b). Montmorillonite (MMT) nanoclay is one of the most widely used types of nanoclay. MMT has a strong elastic modulus, less expensive, lower density, lower coefficient of thermal expansion, and relatively higher surface area (Bhattacharya, Citation2016). Aforesaid features considerably increase the strength, fracture toughness, and wear properties of nanoclay-reinforced polymer composites. The literature exposes that a substantial quantity of studies are performed on the influence of nanoclay on the mechanical and wear properties of nanocomposites (Domun et al., Citation2015; Jumahat et al., Citation2016; Krushnamurty et al., Citation2015; Mohan & Kanny, Citation2017; Nanda et al., Citation2019; Withers et al., Citation2015; Zade et al., Citation2018).
“Design of experiments” is a tool that could be applied to minimize the total experiments (numbers). The “response surface methodology” (RSM) could offer a predicted model comprising of several factors at different levels and scrutinize the main and interaction effects. Multi-response optimisation of material properties may be derived from the predicted model’s desirability feature. Several researchers effectively used the RSM to optimize the mechanical properties for various materials (Bagheri et al., Citation2018; Kunnan Singh et al., Citation2018; Moghri et al., Citation2015).
This work aims to investigate the influence of nanoclay addition on the tensile properties of glass fiber-epoxy composite. Furthermore, this work emphasizes the analysis of each factor’s effect on the wear property of glass fiber-epoxy-nanoclay ternary nanocomposite using RSM.
2. Methodology
2.1. Materials
The epoxy resin (L-12) and hardener (K-6) are delivered by “Atul Polymers,” woven E-glass fiber mat is delivered by “Yuje Enterprises Bengaluru”, and nanoclay (“Surface modified contains 25–30 wt.% trimethyl stearyl ammonium”) is delivered by “Sigma Aldrich” are used.
2.2. Sample preparation
demonstrates a detailed composite specimen preparation process. Nanocomposites are produced by hand lay-up process and compression molding. Nanoclay with differing weight percentages () is added in epoxy resin using a stirrer and sonicator to produce the glass fiber-epoxy-nanoclay ternary nanocomposite. The nanoclay-epoxy blend and hardener are carefully blended and applied to both sides of the glass fiber mat. Totally the coated mats are piled collectively and constantly pressed in the middle of two metal sheets, then placed for 24 hours of curing.
Table 1. Composition of glass fiber-epoxy-nanoclay ternary nanocomposite
2.3. Tensile test
Tensile tests are executed as per the ASTM D3039 standard (Specimen dimensions—250 X 25 × 3 mm3) utilizing “Computerized Universal Testing Machine (UTM) (ZWICK-ROELL Z020, LOADCELL 20 kN)”. A minimum of five specimens for each type is tested to minimize error.
2.4. Wear test
A three-body abrasive wear test () is carried out for all the nanocomposites as per ASTM G 65–04. The abrasive particles (silica sand of size ≤250 μm) are fed at the interface of the rotating “chlorobutyl rubber wheel” and the nanocomposite specimen. The specimen is cleaned and weighed initially using a high precision digital weighing apparatus before it is fixed in the specimen holder. The test specimen is pressed at a defined load against the rotating wheel, put in by the lever arm, whereas a regulated flow of abrasives abrades the test surface. The abrasive wheel’s contact face moves into the path of abrasive flow. The lever arm’s pivot axis resides inside a line that is nearly tangent to the surface of the wheel. After the completion of the test, the specimen is finally removed, cleaned properly, and weighed again (final weight). A minimum of three tests are carried out on each condition, and the average values are recorded.
2.5. Design of experiments
In the present analysis, the “Box—Behnken experimental design” of the RSM is applied in order to lessen the number of wear tests, expenses, and time, in addition, to determine the effect of individual factors (at various levels) independently and concurrently on the wear property of glass fiber-epoxy-nanoclay ternary nanocomposite. RSM will obtain the optimal solution by having an estimated function to predict the wear property, i.e., mass loss (responses in this work), and assess the effect of each factor (nanoclay, load, and sliding distance).
Minitab® 19 software is employed to generate the matrix design and analyse the experimental data. Three levels of each factor, viz., nanoclay, load, and sliding distance, are considered as represented in . A sum of 15 experiments is acquired from the “Box–Behnken experimental design,” comprising three centre points for three factors, as presented in .
Table 2. Factors in Box–Behnken experimental design
Table 3. Box–Behnken experimental design with factors and levels
3. Results and discussion
3.1. Tensile properties
As presented in , the nanoclay (2NCGE and 4NCGE) has enhanced the tensile properties compared to GE composites. In glass fiber-epoxy-nanoclay ternary nanocomposite, nanoclay is not the main load-bearing constituent; still, the nanoclay enhances the tensile strength and modulus by 6 and 7% at 2 wt.% nanoclay and 12 and 14% at 4 wt.% nanoclay, respectively. The percentages of increase in tensile strength and modulus are compared with the available literature, which is adjacent to each other and presented in . The results might be attributed to the following reasons: 1) nanoclay platelets enact as interlocking agents among the fiber and epoxy, that could enhance their interfacial bonding (Withers et al., Citation2015); 2) nanoclay addition in epoxy can increase the mechanical properties of the epoxy (Wang et al., Citation2019); 3) nanoclay enhances the epoxy properties, which will strengthen the load taking ability of the epoxy, leading to decrease in the stress intensity on the glass fibers (Feiz & Khosravi, Citation2019). Also, some literature reports that crack pinning and bifurcation, etc., are a few of the strengthening mechanisms witnessed to increase nanocomposites’ strength (Bashar et al., Citation2014; Basturk & Celik Erbas, Citation2018). As presented in , tensile strain (%) is decreased for 2NCGE and 4 NCGE compared to GE composite due to the improved stiffness of glass fiber-epoxy-nanoclay ternary nanocomposite.
Table 4. Tensile properties of glass fiber-epoxy-nanoclay ternary nanocomposite
Table 5. Comparison of present work data with literature data
3.1.1. SEM analysis
displays the SEM images of the fractured specimen. ) illustrates the woven bi-directional fiber mat arrangement. ) displays the specimen failure under tensile load due to glass fiber pull out. The fibers look clean and no residue matrix. (c) displays pulled out fibers exposing the de-bonding between fiber and matrix.
(d-f) shows that nanoclay addition improved the interfacial bonding among fiber and matrix, which is evidence for an increase in tensile properties. The existence of large clusters of resin is apparent in nanocomposite micrographs, demonstrating strong adhesion to fibers by matrix. Well, after the fracture, a minimal amount of relative de-bonding is observed among the glass fibers and epoxy. This specifies the existence of a robust bond because of nanoclay addition in the nanocomposite at the interface of fiber and matrix. Also, the addition of nanoclay helps in crack arresting and diversion of crack propagation in glass fiber-epoxy-nanoclay ternary nanocomposite (U A et al., Citation2018; Kini et al., Citation2019).
3.2. Wear property
3.2.1. ANOVA
The RSM is analysed using Minitab® 19 software. For the response variable and input factors, the analysis presented the “analyses of variance” (ANOVA) table. The ANOVA is a statistical technique that is employed to evaluate statistical hypotheses. For all the particulars provided in the ANOVA table, the researcher’s primary attention would most definitely be centered on “P-Value” column. Since the value is typically set at 0.05, any value lower than 0.05 will contribute to significant effects, whereas the value higher than 0.05 would result in a non-significant effect. The ANOVA results for the mass loss are presented in .
Table 6. ANOVA results for mass loss
The quadratic model for the “mass loss” in terms of input factor by excluding non-significant factors is given by EquationEquation 1(1)
(1) :
As presented in Equationequation 1(1)
(1) , plus (+) and minus (-) signs indicate the positive and negative influence on mass loss, respectively. All factors influence mass loss, where nanoclay (NC) has a negative effect; load and sliding distance have a positive effect. Out of all the factors, load has the most influence on the mass loss as per its uppermost coefficient in the equation, even though the influence is antagonistic. The main effects and 2-way interaction effects of individual factors are shown in .
3.2.2. Main effects plots
shows that the slope of the load is extremely sharp, which impacts the maximum on mass loss, followed by sliding distance and nanoclay (NC). Load vs. mass loss and sliding distance vs. mass loss curves are stepping up, indicating that increase in load and sliding distance escalate the mass loss under wear test. Simultaneously, the nanoclay vs. mass loss curve is stepping down, which suggests increasing the wt.% of nanoclay declines the mass loss. Higher mass loss is observed with increasing load and sliding distance because of increased friction between the rubber wheel and specimen, leading to deeper grooving on the composite surface. The nanoclay addition to the composite has declined the mass loss. Nanoclay enhances the load-carrying ability and stiffness of the matrix, resulting in lower mass loss (Bagci et al., Citation2020; Rashmi et al., Citation2011; Shettaret al., Citation2020).
3.2.3. Interaction effects plots
presents the 2-way interaction effects plots. Line parallel to each other indicates no interaction among the factors. All the lines presented between 2 factors do not interact for the given levels. The lines between NC*Load and NC*Sliding distance are not parallel to each other, which means at higher levels lines might interact, and P-value for the same in confirms it. But, the lines between Load*Sliding distance are parallel to each other, indicating there is no interaction effect, as could be established from its P-value in .
3.2.4. Surface plots
The graphical 3D responses of mass loss according to Equationequation 1(1)
(1) , against the factors, are presented in (a-c). For individual Figure, one factor is kept uniform (at mid-level), and the vertical axis presented as response, i.e., mass loss and horizontal axis presented the other two factors. portrays the mass loss vs. NC and load by keeping the sliding distance at 600 rpm. The surface plot can be learned in that the mass loss is maximum at 0 wt.% of NC and 5 kg load and minimum at 4 wt.% of NC and 1 kg load. The mass loss is increased with increasing the load when nanoclay (NC) wt.% is constant. Also, the addition of nanoclay decreased the mass loss in all the loads. shows mass loss vs. NC and sliding distance by keeping the load at 3 kg. Similarly, it can be established from the surface plot in that the mass loss is maximum at 0 wt.% of NC and 900 rpm sliding distance and minimum at 4 wt.% of NC and 300 rpm sliding distance. The mass loss is increased with increasing the sliding distance when nanoclay (NC) wt.% is constant. Also, the addition of nanoclay decreased the mass loss in all the sliding distances. indicates the effect of load and sliding distance on mass loss by keeping nanoclay at 2 wt.%. The mass loss is maximum at 5 kg load and 900 rpm sliding distance and minimum at 1 kg load and 300 rpm sliding distance. The mass loss is increased by increasing the load and sliding distance when either one is constant.
3.2.5. Prediction of optimal condition
In the present work, the optimization of mass loss is performed by Minitab® 19 software. The result of predicting optimal conditions is presented in . As can be observed in this Figure, to minimize the mass loss, the factor levels should be set at the values: nanoclay at 4 wt.%; load at 1 kg; sliding distance at 300 rpm.
The experiment’s RSM design predicted the minimum mass loss is 1.8887 mg, according to the optimal levels of factors mentioned above. As can also be seen from , the desirability (d) is 1, which means the settings seemed to accomplish favorable for the response.
3.2.6. Confirmation test
In this analysis, after optimization, an experimental test is carried out using the optimal factor’s levels (NC (4 wt.%), load (1 kg), Sliding Distance (300 rpm)). represents the predicted and experimental value of the mass loss. According to , the confirmation test’s mass loss is close enough to the predicted value.
Table 7. Result of the confirmation test
4. Conclusions
Addition of nanoclay enhances the tensile strength and modulus of glass fiber-epoxy-nanoclay ternary nanocomposite, whereas tensile strain is decreased.
SEM images under tensile load disclosed that the addition of nanoclay helps in crack arresting and diversion of crack propagation in glass fiber-epoxy-nanoclay ternary nanocomposite.
ANOVA and main effect plots disclose that all factors viz., nanoclay, load, sliding distance have an influence on mass loss, where nanoclay (NC) decreases the mass loss whereas load and sliding distance increases the mass loss.
2-way interaction effects plots revealed that there is no interaction among the factors.
Surface plots disclosed that the mass loss is increased by increasing the load and sliding distance when either one is constant.
RSM estimated optimal conditions as 4 wt.% nanoclay, 1 kg load, and 300 rpm for sliding distance. The mass loss obtained from the confirmation test is close enough to the desirability optimization data.
Additional information
Funding
Notes on contributors
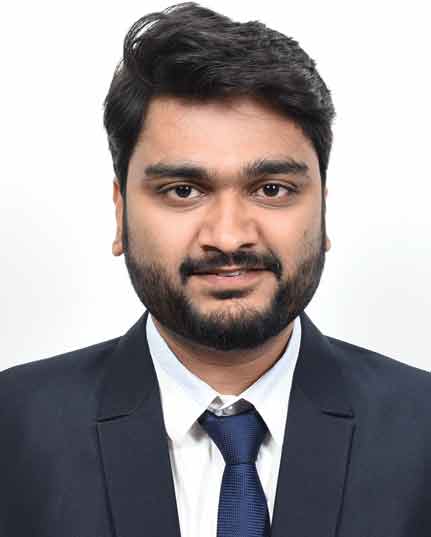
Pavan Hiremath
Mr. Pavan Hiremath, Dr. U Achutha Kini, Dr. Manjunath Shettar, Dr. Sathyashankara Sharma, and Dr. Jayashree P K are the faculty members in the Department of Mechanical and Manufacturing Engineering, Manipal Institute of Technology, Manipal Academy of Higher Education, Manipal, Karnataka, India. The authors’ areas of interest are polymer matrix composites’ characterization, hygrothermal aging behavior of polymer nanocomposites, heat treatment of metals and alloys, etc. In this manuscript, the authors found the influence of process parameters on composite specimens using Response Surface Methodology.
References
- Bagci, M., Demirci, M., Sukur, E. F., & Kaybal, H. B. (2020). The effect of nanoclay particles on the incubation period in solid particle erosion of glass fibre/epoxy nanocomposites. Wear, 444-445, 203159. https://doi.org/10.1016/j.wear.2019.203159
- Bagheri, M. S., Ashenai Ghasemi, F., Ghasemi, I., & Saberian, M. H. (2018). Analysis of the Young’s modulus and impact strength of A-glass/epoxy/nano-silica ternary nano-composites using surface response methodology. Journal of Failure Analysis and Prevention, 18(6), 1472–14. https://doi.org/10.1007/s11668-018-0544-z
- Bashar, M., Mertiny, P., & Sundararaj, U. (2014). Effect of nanocomposite structures on fracture behavior of epoxy-clay nanocomposites prepared by different dispersion methods. Journal of Nanomaterials, 2014, 1–12. https://doi.org/10.1155/2014/312813
- Basturk, S. B., & Celik Erbas, S. (2018). Mechanical and thermo-mechanical properties of nanoclay/epoxy composites: Synergistic effects of silanization and surfactant application. Materials Research Express, 5(9), 095017. https://doi.org/10.1088/2053-1591/aad60c
- Bhattacharya, M. (2016). Polymer nanocomposites—a comparison between carbon nanotubes, graphene, and clay as nanofillers. Materials (Basel), 9(4), 262. https://doi.org/10.3390/ma9040262
- Chawla, K. K. (2012). Composite materials. Springer New York.
- Domun, N., Hadavinia, H., Zhang, T., Sainsbury, T., Liaghat, G. H., & Vahid, S. (2015). Improving the fracture toughness and the strength of epoxy using nanomaterials – A review of the current status. Nanoscale, 7(23), 10294–10329. https://doi.org/10.1039/C5NR01354B
- Feiz, A., & Khosravi, H. (2019). Multiscale composites based on a nanoclay-enhanced matrix and E-glass chopped strand mat. Journal of Reinforced Plastics and Composites, 38(13), 591–600. https://doi.org/10.1177/0731684419836219
- Friedrich, K. (2018). Polymer composites for tribological applications. Advanced Industrial and Engineering Polymer Research, 1(1), 3–39. https://doi.org/10.1016/j.aiepr.2018.05.001
- Fu, S., Sun, Z., Huang, P., Li, Y., & Hu, N. (2019). Some basic aspects of polymer nanocomposites: A critical review. Nano Materials Science, 1(1), 2–30. https://doi.org/10.1016/j.nanoms.2019.02.006
- Islam, M. S., Masoodi, R., & Rostami, H. (2013). The effect of nanoparticles percentage on mechanical behavior of silica-epoxy nanocomposites. Journal of Nanoscience, 2013, 1–10. https://doi.org/10.1155/2013/275037
- Jeyakumar, R., Sampath, P. S., Ramamoorthi, R., & Ramakrishnan, T. (2017). Structural, morphological and mechanical behaviour of glass fibre reinforced epoxy nanoclay composites. The International Journal of Advanced Manufacturing Technology, 93(1–4), 527–535. https://doi.org/10.1007/s00170-017-0565-x
- Jumahat, A., Talib, A. A. A., & Abdullah, A. 2016 Wear properties of nanoclay filled epoxy polymers and fiber reinforced hybrid composites. 247–260
- Karippal, J. J., Narasimha Murthy, H. N., Rai, K. S., Sreejith, M., & Krishna, M. (2011). Study of mechanical properties of epoxy/glass/nanoclay hybrid composites. Journal of Composite Materials, 45(18), 1893–1899. https://doi.org/10.1177/0021998310389087
- Kini, U. A., Shettar, M., Sharma, S., Hiremath, P., G, M. C., Hegde, A., & S, D. (2019). Effect of hygrothermal aging on the mechanical properties of nanoclay-glass fiber-epoxy composite and optimization using full factorial design. Materials Research Express, 6(6), 065311. https://doi.org/10.1088/2053-1591/ab0d68
- Krushnamurty, K., Srikanth, I., Rangababu, B., Majee, S. K., Bauri, R., & Subrahmanyam, C. (2015). Effect of nanoclay on the toughness of epoxy and mechanical, impact properties of e-glass-epoxy composites. Advanced Materials Letters, 6(8), 684–689. https://doi.org/10.5185/amlett.2015.5817
- Kunnan Singh, J., Ching, Y., Abdullah, L., Ching, K., Razali, S., & Gan, S. (2018). Optimization of mechanical properties for polyoxymethylene/glass fiber/polytetrafluoroethylene composites using response surface methodology. Polymers (Basel), 10(3), 338. https://doi.org/10.3390/polym10030338
- Moghri, M., Shamaee, H., Shahrajabian, H., & Ghannadzadeh, A. (2015). The effect of different parameters on mechanical properties of PA-6/clay nanocomposite through genetic algorithm and response surface methods. International Nano Letters, 5(3), 133–140. https://doi.org/10.1007/s40089-015-0146-7
- Mohan, T. P., & Kanny, K. (2017). Tribological studies of nanoclay filled epoxy hybrid laminates. Tribology Transactions, 60(4), 681–692. https://doi.org/10.1080/10402004.2016.1204039
- Müller, K., Bugnicourt, E., Latorre, M., Jorda, M., Echegoyen Sanz, Y., Lagaron, J., Miesbauer, O., Bianchin, A., Hankin, S., Bölz, U., Pérez, G., Jesdinszki, M., Lindner, M., Scheuerer, Z., Castelló, S., & Schmid, M. (2017). Review on the processing and properties of polymer nanocomposites and nanocoatings and their applications in the packaging, automotive and solar energy fields. Nanomaterials, 7(4), 74. https://doi.org/10.3390/nano7040074
- Nanda, T., Sharma, G., Mehta, R., Shelly, D., & Singh, K. (2019). Mechanisms for enhanced impact strength of epoxy based nanocomposites reinforced with silicate platelets. Materials Research Express, 6(6), 065061. https://doi.org/10.1088/2053-1591/ab1023
- Patnaik, A., Satapathy, A., Chand, N., Barkoula, N. M., & Biswas, S. (2010). Solid particle erosion wear characteristics of fiber and particulate filled polymer composites: A review. Wear, 268(1–2), 249–263. https://doi.org/10.1016/j.wear.2009.07.021
- Rajak, D. K., Pagar, D. D., Kumar, R., & Pruncu, C. I. (2019). Recent progress of reinforcement materials: A comprehensive overview of composite materials. Journal of Materials Research and Technology, 8(6), 6354–6374. https://doi.org/10.1016/j.jmrt.2019.09.068
- Rashmi, R. N. M., Suresha, B., Devarajaiah, R. M., & Shivakumar, K. N. (2011). Dry sliding wear behaviour of organo-modified montmorillonite filled epoxy nanocomposites using Taguchi’s techniques. Materials & Design, 32(8–9), 4528–4536. https://doi.org/10.1016/j.matdes.2011.03.028
- Sahoo, B. P., & Tripathy, D. K. (2017). Introduction to clay- and carbon-based polymer nanocomposites: materials, processing, and characterization. In Properties and applications of polymer nanocomposites (pp. 1–24). Springer Berlin Heidelberg.
- Shettar, M., Achutha Kini, U., Sharma, S., & Hiremath, P. (2017). Study on mechanical characteristics of nanoclay reinforced polymer composites. Materials Today: Proceedings, 4(10), 11158–11162. https://doi.org/10.1016/j.matpr.2017.08.081
- Shettar, M., Kini, A., Sharma, S., & Hiremath, P. (2017). FRP-Nanoclay hybrid composites: A review (Vol. 904). MSF.
- Shettar, M., Kini, U. A., Sharma, S., Hiremath, P., & G, M. C. (2019a). Investigation and optimization of thermal shock effects on the properties and microstructure of Nanoclay-Glass Fiber Reinforced Epoxy Composites. Materials Research Express, 6(10), 105360. https://doi.org/10.1088/2053-1591/ab3f67
- Shettar, M., Kini, U. A., Sharma, S., Hiremath, P., & G, M. C. (2020). Hygrothermal chamber aging effect on mechanical behavior and morphology of glass fiber-epoxy-nanoclay composites. Materials Research Express, 7(1), 015318. https://doi.org/10.1088/2053-1591/ab6405
- Shettar, M., Kini, U. A., Sharma, S., Hiremath, P., & Gowrishankar, M. C. (2019b). Study on the mechanical properties of nanoclay-epoxy composites under different hygrothermal aging conditions. Materials Research Express, 6(8), 085333. https://doi.org/10.1088/2053-1591/ab2502
- Shettar, M., Kowshik, C. S. S., Manjunath, M., & Hiremath, P. (2020). Experimental investigation on mechanical and wear properties of nanoclay–epoxy composites. Journal of Materials Research and Technology, 9(4), 9108–9116. https://doi.org/10.1016/j.jmrt.2020.06.058
- Thomas, S., Abraham, J., Manayan Parambil, A., Krishnan, A., Maria, H. J., Ilschner, B., Lees, J. K., Dhingra, A. K., & McCullough, R. L. (2016). Composite materials Ullmann’s encyclopedia of industrial chemistry. Wiley-VCH Verlag GmbH & Co. KGaA.
- U A, K., Shettar, M., Sharma, S., Hiremath, P., & Gowrishankar, M. C. (2018). Investigation on effect of cold soaking on the properties of nanoclay-GFRP composite. Materials Research Express, 6(1), 015206. https://doi.org/10.1088/2053-1591/aae967
- Wang, C., Gao, X., & Li, Y. (2019). Mechanical properties improvement of nanoclay addition epoxy 3D orthogonal woven composite material. Fibers and Polymers, 20(7), 1495–1503. https://doi.org/10.1007/s12221-019-9116-4
- Withers, G. J., Yu, Y., Khabashesku, V. N., Cercone, L., Hadjiev, V. G., Souza, J. M., & Davis, D. C. (2015). Improved mechanical properties of an epoxy glass–fiber composite reinforced with surface organomodified nanoclays. Composites Part B: Engineering, 72, 175–182. https://doi.org/10.1016/j.compositesb.2014.12.008
- Zade, S. K., B, V. S., & S, K. V. S. (2018). Effect of nanoclay, glass fiber volume and orientation on tensile strength of epoxy-glass composite and optimization using Taguchi method. World Journal of Engineering, 15(2), 312–320. https://doi.org/10.1108/WJE-08-2017-0286