Abstract
Nigerian bentonite has low fluid loss control and poor rheological properties which are key API specifications. Foreign and imported bentonites are sodium-based, while local bentonites are calcium-based, and there is a need for beneficiation. The periwinkle shell used for fluid loss control and Mucuna solannie for rheology are abundant. The elemental compositions and the rheology and fluid loss of the samples were determined by the use of 15 g and 30 g, respectively, of bentonite. Fluid loss, rheology and YP/PV measurements were conducted on local and foreign bentonites to justify the need for beneficiation. With 15 g and 30 g of local bentonite, 27 ml and 11 ml, 600 rpm readings of 18 and 34, with 1.6 and 3.7 were obtained for fluid loss, rheology and YP/PV, respectively. The beneficiated local bentonite with periwinkle and Mucuna solannie gave acceptable results at 4 g-5 g concentrations, with slight deviations observed in rheology measurements. Also, 14 ml and 12 ml, 600 rpm readings of 23 and 26, with 0.85 and 0.6, respectively, for fluid loss, rheology and YP/PV were observed at 4 g-5 g. However, this research work improved the quality of local bentonite using periwinkle shell and Mucuna solannie, with 7 g of each in 250 ml water as projected optimum amounts, in order to make it more suitable for drilling and attain API specification at 600 rpm reading of 30. The results proved that the beneficiated local bentonite is able to compete with foreign bentonite and also met API specifications when added in the right quantities. Another approach to beneficiation other than atomic exchange has been highlighted.
PUBLIC INTEREST STATEMENT
There is an abundance of mineral resources in Nigeria. Though efforts have been made to utilize these materials for socio-economic benefit, a lot still remains to be done. Nigerian bentonite finds applications in the manufacturing and processing industries, but its application in the area of drilling of wells in the oil and gas industry is limited, due to on-conformance to standard specifications such as the American Petroleum Institute (API). Bringing Nigerian bentonite to the specifications to make it suitable for drilling has been a subject of research; hence, this article presents an approach to enhance the properties of the mineral for applications in oil and gas well drilling operations. Their widespread uses would showcase areas of application for periwinkle (highly abundant) and Mucuna solannie (culinary uses and cultivated locally in commercial quantities), both environmentally friendly. Employment opportunities would be created and economic impact on the nation would be positive.
1. Introduction
Studies on the improvement of local bentonites for use in drilling applications in different regions of the world are not new, particularly in Nigeria (Afolabi et al., Citation2017; Al-Homadhi, Citation2009; Joel & Nwokoye, Citation2010). Nigeria as a country is blessed abundantly with essential clay materials, but, unfortunately, does not use it due to its poor performance in drilling as it does not meet API standard for a drilling mud. Hence, most of the used bentonites in Nigerian drilling operations are imported. The only major use of Nigerian bentonite clay was in the early stages of oil discovery in Nigeria, in the 1950s, and by Shell Petroleum Development Company (SPDC) in 2001, where it was used to drill over 600 wells. Many Nigerian researchers have been trying to look for ways to make this abundant resource more of a blessing than a waste. Several attempts to use Nigerian bentonite in its raw form in drilling mud formulations have been found to be unproductive as it contains impurities and exhibits high fluid loss.
Reviewed works of Falode et al. (Citation2008), James et al. (Citation2008), and Abdullahi et al. (Citation2011) have shown that there is a need for the improvement, that is, beneficiation of our local bentonite from the calcium-based clay to a sodium-based clay. This implies that subjecting these clays to treatment will definitely improve their quality and likely attain API requirements. Some researchers have found out that the use of starch to beneficiate the mud gave the best filtration properties, while the use of potash provided the best rheological properties. Similarly, another local biomaterial has been used. Research by Uwaezuoke et al. (Citation2017) has discovered that Mucuna solannie has the capability of improving the rheological properties of drilling muds. Mucuna solannie is also a readily available vegetable plant legume in Nigeria, and can also be channeled to the oil industry if maximized.
According to estimates from the Nigerian Mining Corporation and the Raw Materials Research Development Council (RMRDC, 2007), deposits of local bentonite clays in Nigeria have been modestly projected to be above 700 million metric tons (Aigbedion & Iyayi, Citation2007; RMRDC, 2007; James et al., Citation2008; Omole et al., Citation2013) with the bulk of it lying in Afuze, Edo State, Mid-Western Nigeria which holds about 70–80 million metric tons of bentonite clay (Nweke et al., Citation2015). In addition, barite deposits in Nigeria have been identified in Taraba and Bauchi states, which hold about 7.5 million metric tons. Other regions with appreciable deposits of bentonite clays are the North-East region which comprises Borno, Adamawa and Gombe States (Ahmed et al., Citation2012; Falode et al., Citation2008; Inegbenebor et al., Citation2014; James et al., Citation2008; Obaje, Citation2013). Also, the Abakaliki formation in South-East Nigeria is a notable formation with substantial quantities of bentonite clays (Nweke et al., Citation2015). In addition, deposits of bentonite clay have been reported in Lagos, Anambra and Abia States. It can be said that these deposits of bentonite clay cut across almost all the states of the Federation (Inegbenebor et al., Citation2014).
These clay deposits have the potential to be a major source of foreign income earner if properly harnessed. The Niger Delta region of Nigeria has been estimated to hold a probable reserve of about 4 billion tons of clay deposits alone, while the North-East region of Nigeria has in total 700 million tons in its pure untreated form (Agwu et al., Citation2015; Emofurieta, Citation2001). Furthermore, estimation of the Nigerian bentonite reserve has been spearheaded by the Raw Materials Research Development Council (RMRDC), which is a research parastatal of the Federal Government of Nigeria. The RMRDC in 2010 put forward the location and estimated values of proven reserves of bentonite clays in Nigeria as shown in (). Besides the proven reserve of bentonite deposits identified, other locations with bentonite deposits in different parts of Nigeria have been found but need further investigation for reserve estimation, quantification and characterization.
Table 1 Proven bentonite reserves of some clay deposits in Nigeria as at 2010 (Agwu et al., Citation2015)
The first characterization study of bentonite clay deposits in Nigeria can be traced to the work of Oyawoye and Hirst (Citation1964). They carried out a mineralogical study using X-Ray Diffraction (XRD) and thermal analysis of clay samples obtained from Ropp in the Plateau Province of the old Northern Nigeria. The number of locations sampled in their study was just one. The clay sample was a calcium montmorillonite with the major oxides being Silicon oxide (47.38%), Aluminum oxide (21.27%), and Ferric oxide (10.66%).
Beneficiation is simply a procedure for removing impurities or associated minerals that are not needed, thereby improving the quality of the bentonite clay (Olugbenga et al., Citation2013). Some wet beneficiation procedure may prove ineffective if the bentonite clay is not allowed to properly hydrate and homogenize with the chemicals used for the beneficiation study. (Ahmed et al., Citation2012; Ajugwe et al., Citation2012) carried out mineralogical studies on bentonite clays obtained from the Pindiga formation in Gombe State, North-East Nigeria. Experimental findings indicate that the clay samples contain montmorillonite, which is predominantly rich in calcium, and this is more stable when compared to Magnesium, Potassium and Sodium based montmorillonite. Compositional analysis of the clay samples showed that it contains oxides of aluminum, silicon, calcium and iron. Obaje (Citation2013) investigated bentonite clays in Borno State, North-East Nigeria, and like previous works done on bentonite clays in that region, discovered that it was rich in montmorillonite containing predominantly calcium and requires beneficiation to improve the quality of the clay.
Dewu et al. (2011a, b) carried out mineralogical characterization of clay samples obtained from the Fika formation in North-East Nigeria. The mineralogy of the clay samples was mainly calcium-based montmorillonite and would require beneficiation with sodium carbonate to convert it to sodium-based montmorillonite via ion exchange. The mineralogical and elemental study of Nigerian bentonite clay deposits carried out by researchers in the 80s, 90s and early 2000s have revealed that the beneficiation of these bentonite clays is a necessary step if recourse must be made to it for application in the oil and gas industry. This is important as most of the clay deposits studied so far do not meet the requirements of the American Petroleum Institute (API) in terms of rheological properties.
Nweke et al. (Citation2015) carried out mineralogical characterization of clay samples from the Abakaliki formation in the Niger Delta part of Nigeria. The minerals present are mainly montmorillonite and illite with traces of kaolinite. Elemental analysis indicates high calcium and potassium oxides. Olugbenga et al. (Citation2013) also characterized bentonite clay samples from the Niger Delta region of Nigeria. Their mineralogical study using X-Ray Diffraction (XRD) on the clay sample indicated that it was a montmorillonite rich in calcium and chemically stable.
1.1. Periwinkle shells
They are usually picked off the rocks by hand or caught in a drag from a boat. Periwinkles are considered a delicacy in African and Asian cuisines. The common periwinkle is sold by fishmongers at seafood markets in large cities around the world, and is also commonly found in seafood restaurants as an appetizer or as a part of a seafood platter. In some countries, pubs may serve periwinkles as a snack. In Nigeria, periwinkle shells can be seen scattered all over the ground in markets, where they are trampled upon or used to fill up holes and muddy areas. It is a very common commodity and hence, very easy to source.
1.2. Mucuna solannie
It is very widespread in Africa, from Sierra Leone east to DR Congo, and south to Angola. It is also found in the Caribbean region, tropical America and islands of the Pacific Ocean. Occasionally, it is cultivated, such as practiced in Nigeria. A black dye is obtained from all parts of Mucuna solannie, which is used in Nigeria to dye fibre and leather black. Cooked young fruits are eaten as a vegetable. In Nigeria, Mucuna solannie is occasionally cultivated for that purpose. The ripe seed is eaten, pounded and cooked, preferably in soups. Oil extracted from the seed can be used in the preparation of resin, paint, polish, wood varnish, skin cream and liquid soap. The Edo people in Nigeria use leaf sap to stop diarrhoea. Mucuna solannie will probably remain of minor importance locally as a source of black dye, but this project has brought another significance to this plant in the oil industry, and hence, it can be exploited for better use to society.
1.3. Significance of study
Although water-based mud formulations with foreign (imported) bentonite exist, this research highlighted the deficiencies of Nigerian bentonite. Local materials were utilized to improve its performance in terms of fluid loss and rheological properties and to enable it to satisfy API specifications. The study presents an alternative approach to beneficiation other than ion-exchange. A study on the combination of periwinkle and Mucuna solannie powders to improve Nigerian bentonite for oil and gas well drilling has not been undertaken, based on the available literature. The temperature stability of the formulations that might be in question was guaranteed by the high carbon content in Mucuna solannie (), which was exhibited by muds formulated from it as presented in previous works. Most materials that contain carbon exhibit valuable features such as suitable surface chemistry, chemical inertness, mechanical resistance, high surface area, optimum porosity, and ultimately thermal stability.
2. Materials and method
2.1. Sample acquisition and preparation
The locally sourced materials include local bentonite, foreign bentonite, periwinkle shells and Mucuna solannie plant. The local and foreign bentonites were bought from a licensed dealer, in a local store in Port Harcourt, Nigeria. The periwinkle shell () and Mucuna solannie () powder were sourced from a market in Nigeria, and needed to be processed in order to be used. The periwinkle shell was obtained without the other parts, that is, it was obtained with just the shell alone and organism removed. This made processing easier as it just needed to be washed to remove extraneous particles. With distilled water in a large pot at ambient temperature of 31 ± 2 °C, the shells were added to prevent cracking. The shells were covered with 5 inches of extra water. By the use of tongs, the periwinkle shells were each picked and agitated and placed in glassware. Both soaking and washing lasted for about 45 minutes since boiled water was not used. The use of boiled water would have taken a shorter time, say 7 minutes, depending on quantity. Also, bleach was not used. It was then sun-dried at 32 ± 1 °C for 5 days to remove moisture. Crushing was done in a mill to powder form with a hammer mill (Model RLA 201–800,014, UK). The powder was grinded further with a Hamilton Beach dry grinder (Model: 80,385) and sieved with 200 mesh sieve for quality assurance and quality check (QA/QC). Similarly, a sample of Mucuna solannie powder was obtained in the same manner associated with the method used by Uwaezuoke et al. (Citation2017) from a Nigerian market. The processed samples were packed in high-density polyethylene (HDPE, 0.77 mm thickness) bags and heat sealed with a sealing machine. A relative humidity of 76% was reported. They were stored in a refrigerator ready for use when required, in their preserved unrefined forms, and any redundant moisture contents would not affect shelf life.
2.2. Elemental composition measurements on additives using scanning electron microscope (SEM)—energy dispersion spectrum
The elemental composition of the additives needed to be known as it would tell their major elemental constituents. This became important because, since the objective was to improve the quality of local Nigerian bentonite, elemental composition of the additives responsible for the improvement was paramount.
2.2.1. SEM procedure
The Scanning Electron Microscope energy-dispersive X-ray spectroscopy (SEM-EDS) Phenom Prox model, manufactured by PhenomWorld Eindhoven, Netherlands was used to carry out the morphology analysis. Sample is placed on the aluminium holder stub using sticky carbon tape. The sample was insulated using gold and then grounded electrically. The samples each are then labeled on their stub, then dried in the oven at 60 °C. Nitrogen line was opened at 50 psi and the vent button was pressed to fill the area with nitrogen for proper purging of the chamber. The sample holder stub was then placed in the sample chamber holes and the door was shut and the rotary pump picked and a vacuum of 5 × 10−5 Pa was created. The filament light was switched on and the monitor too automatically switched on. At this stage, the accelerator voltage was 15kV and the filament was burned out. The atoms on the surface are excited by the electron beam, emitting specific wavelengths of X-rays that are characteristic of the atomic structure of the elements. An energy-dispersive detector (a solid-state device that discriminates among X-ray energies) can analyze these X-ray emissions. Appropriate elements are assigned, yielding the composition of the atoms on the specimen surface. The lowest scan mode of 10x is picked and the TV scan clicked. The magnification is then taken to 1000x at a slow scan, 2000, 3000 to 5,000. The energy dispersion spectrum scans on the intensity of each of the elements present and gives the molar concentration in %, and then the image was saved. This procedure is called the scanning electron microscope energy-dispersive X-ray spectroscopy (SEM-EDS) and is useful for analyzing the composition of the surface of a specimen.
2.2.2. XRD procedure
The XRD was powered and from the panel, the voltage and current were set at 45kV and 40 mA. The temperature was set at 21–23 °C. The computer system was switched on and the software of XRD was double clicked to run. The setting dialogue was clicked and all the required settings of power and temperature were checked to correspond to that of the XRD. Sample was poured into the sample holder and then placed in the sample chamber column. Then, the door was shut and confirmed from the computer. The measurement setting was then set for scan axis as Gonio. Start and end positions were also set, so was the angle and time of the scan. The scan began and then stopped at the required time and the result was saved to a file.
2.3. Measurements of rheological and fluid loss properties of local, imported and beneficiated Nigerian bentonite
In conjunction with elemental composition measurements that were conducted on the additives, rheology and low-temperature low-pressure (LTLP) fluid loss tests were conducted on the three samples of bentonite: local, foreign and beneficiated local bentonite. The American Petroleum Institute recommended test procedures for oil and gas well aqueous-based drilling fluids associated with the tests were used (API, 2010).
2.3.1. Rheological property determination
15 g and 30 g concentrations of foreign bentonite were used to run the rheology test according to API specifications. 15 g of foreign bentonite was measured with a digital scale. 250 ml of distilled water was measured using a measuring cylinder and poured into a mixer. The water was stirred for about 5 seconds, using the Hamilton Beach mixer, and bentonite was gradually added. The stirring process was allowed for a period of 30 minutes. The sample was introduced in a viscometer.
Fann Model 35 viscometer was set at 600 rpm and the dial reading was taken. 300 rpm, 200 rpm, 100 rpm, 6 rpm, and 3 rpm dial readings were also taken. This same process was repeated for 30 g of foreign bentonite.
Similarly, 15 g and 30 g concentrations of local bentonite were also used to run the rheology test. 15 g of local bentonite was measured. Also, 1 g of powdered periwinkle shell and 1 g of dry powdered Mucuna solannie were measured using the weighing balance. 250 ml of water was measured and allowed to agitate in a viscometer for about 5 s. The bentonite was added gradually, followed by the periwinkle shell. Lastly, the Mucuna solannie powder was added. After the mud (bentonite, periwinkle shell and Mucuna solannie mixture) was stirred for about 30 min, 600 rpm dial reading was taken. 300 rpm, 200 rpm, 100 rpm, 6 rpm, and 3 rpm dial readings were also taken. The process was used for 2 g, 3 g, 4 g, and 5 g of periwinkle shell and Mucuna solannie while the 15 g of bentonite was maintained.
2.3.2. Fluid loss determination
15 g and 30 g foreign bentonites were used for the fluid loss test at the same low-temperature and low-pressure. 15 g of foreign bentonite was measured. 250 ml of distilled water was also measured and introduced into the Hamilton beach mixer. The agitator was allowed to stir the water for about 5 seconds and the bentonite was gradually added. The stirring process was allowed for a period of 30 min, and poured into the cell of the API filter press. The filter press was pressurized to a pressure of 100 psi, and the 25 ml measuring cylinder was positioned to receive the filtrate. The filtrate amount was measured and recorded. The same process was repeated for 30 g of foreign bentonite and the result was recorded accordingly.
Similarly, 15 g and 30 g of local bentonite were used for the fluid loss test. 15 g of local bentonite was measured. Also, 1 g of powdered periwinkle shell and 1 g of powdered Mucuna solannie were measured. 250 ml of distilled water was measured and introduced into the Hamilton beach mixer, and allowed to agitate for about 5 s. The bentonite was added gradually, followed by the periwinkle shell, and the Mucuna solannie powder. The mud (bentonite, periwinkle shell, and Mucuna solannie mixture) was stirred for about 30 min and introduced into the API filter press. The filter press was pressurized to a pressure of 100 psi and a 25 ml measuring cylinder was positioned to receive the filtrate. This same process was repeated for 2 g, 3 g, 4 g, and 5 g of periwinkle shell and Mucuna solannie respectively, while the 15 g of bentonite was maintained.
3. Results and discussion
Presented are the X-ray Diffraction (XRD) and Scanning Electron Microscope (SEM) images for both additives (powdered periwinkle shell and Mucuna solannie). Also, the observations in the rheology and fluid loss tests performed according to the American Petroleum Institute (API) recommended procedures are highlighted.
3.1. Elemental compositions of the additives
It is seen from the () and Table A.1 that the periwinkle shell constitute primarily of calcium (about 78%) and silicon (about 12%), but it also contained a little amount of sodium (about 0.23%) which is the basic constituent of foreign bentonite. Hence, it can be deduced that the basic elemental supplement of periwinkle shell is calcium and silicon. Also, from () and Table A.2, it can be seen that Mucuna solannie constituted primarily of carbon (about 29%) and potassium (about 35%). It also contained sodium (about 1%) as its least constituent element. Hence, it can also be deduced that the major elemental supplement of Mucuna solannie to the beneficiation process were carbon and potassium. show the SEM images of periwinkle and Mucuna solannie, respectively.
Figure 3. Scanning electron microscope (SEM) image of periwinkle shell powder (Abdelmalik & Sadiq, Citation2019)
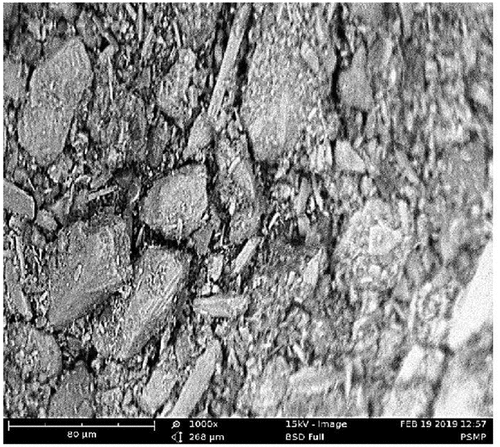
The analysis was made (Appendix A.3 and A.4) with regards to API specifications for a good bentonite. The parameters analyzed as specified by API include the fluid loss, dial reading at 600 rpm and yield point to plastic viscosity ratio ().
Table 2. Comparison—API bentonite specifications (AMOCO, 1994)
3.2. API fluid losses
The samples were compared based on their relation to fluid loss and rheological properties. The comparison highlighted the need for beneficiation, and also, revealed the success of the beneficiation process. According to API specification, dial reading at 600 rpm should be a minimum of 30 and yield point to plastic viscosity ratio (YP/PV) should be a maximum of 3 and LPLT fluid loss of 15 ml ().
From (), using a benchmark of 15 ml as corresponding to API specification, it can be seen that FB1, LB2, FB2, BB4 and BB5 met the requirements as they fall below 15 ml. Since our major concern is on beneficiating local bentonite, we can infer that using 4g-5g of periwinkle shell and Mucuna solannie respectively as additives when added to 15 g of local bentonite is optimum for the beneficiation of the fluid loss property.
Figure 9. Local bentonite (LB1—LB2), foreign bentonite (FB1—FB2) and beneficiated bentonite (BB1—BB5) fluid loss curve
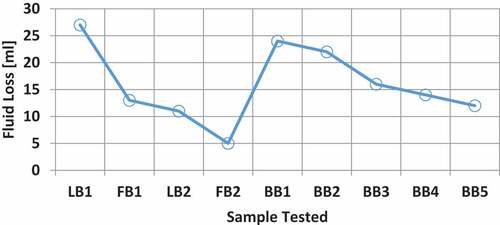
From the previous section, a need for beneficiation has been acknowledged, and the beneficiation process has been accomplished. However, there is a need for comparison in order to check if the aims for beneficiation have been met.
15 g of foreign bentonite exhibited a fluid loss of 13 ml which meets API standard, while the same amount of local bentonite had 27 ml which is very poor; hence, the need for beneficiation. However, when 1 g each of the additives (periwinkle shell and Mucuna solannie) was added to the local bentonite, the fluid loss reduced to 24 ml which did not still meet API standard. 2 g each of the additives was added which still didn’t meet the requirement. Also, 3 g each of the additives did not satisfy the requirements. However, when 4 g each of the additives was added, the local bentonite exhibited a fluid loss of 14 ml which met API standard. Increase in the quantity of additives proved to enhance the fluid loss property as 5 g each gave a fluid loss of 12 ml which is better than the 13 ml exhibited by the foreign bentonite.
3.3. Rheological properties
From (), the rheological properties of the samples, it can be seen that foreign bentonite had a dial reading of 27 at 600 rpm which does not meet API specification of a minimum of 30. However, local bentonite had a dial reading of 18 which deviates largely from API standard. Hence, there was a need for beneficiation. After adding 2 g each of the additives, the reading increased to 19 which are still low. The amount of additives was increased progressively in order to meet API specifications. However, it was not until about 5 g each of the additives was added did we notice significant increase as it gave a dial reading of 26. Nonetheless, from the gradient of the regression plot as shown (), it is seen that a dial reading of 30 can only be achieved at about 7 g each of additives. However, the test conducted did not get to that point.
() shows the YP/PV ratios for the local and foreign bentonites. From (), it can be seen that the beneficiated bentonite samples duly met API specifications as it showed YP/PV ratio of less than 3. Furthermore, it exhibited the best property as they can be said to have the lowest points on the curve.
Figure 11. Foreign bentonite (FB1—FB2) and beneficiated bentonite (BB1—BB5) dial reading at 600 rpm curve
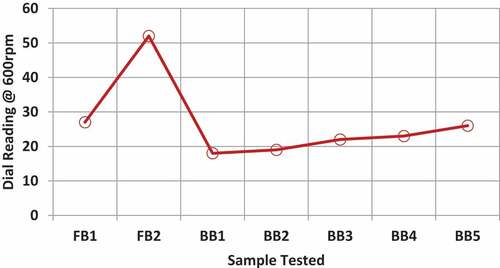
Figure 12. Local bentonite (LB1—LB2), foreign bentonite (FB1—FB2) and beneficiated bentonite (BB1—BB5) dial reading at 600 rpm curve
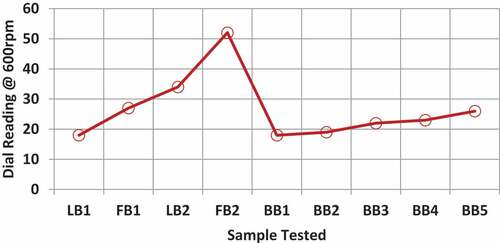
Figure 16. Local bentonite (LB1—LB2), foreign bentonite (FB1—FB2) and beneficiated bentonite (BB1—BB5) YP/PV ratio curve
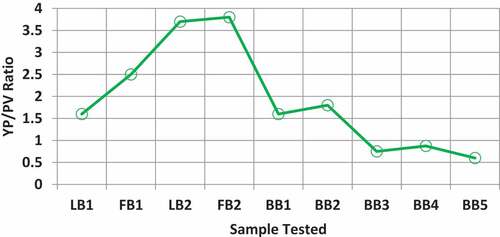
Also, 15 g of foreign bentonite had a ratio of 2.5, while that of local bentonite was 1.6; hence, both met API specification of not more than 3.0. This showed that local bentonite exhibited a better property as its result was less than that of foreign bentonite. However, further beneficiation revealed that this property could be made better, as it was observed that 5 g each of the additives reduced this ratio drastically to 0.6.
3.4. Moisture content
The moisture content of standard 22.5 g of bentonite was determined with Ohaus MB45 moisture analyzer, and 11.40% moisture was recorded after 50 minutes at 100 °C and atmospheric pressure.
4. Conclusion
From the results obtained and analysis made, it can be inferred that beneficiation of the Nigerian local bentonite is compulsory for it to be used in the oil industry. Also, the additives (periwinkle shell and Mucuna solannie) have proven to contain and provide enough properties to be able to enhance our local bentonite if added in substantial amounts. This is very good as it would help increase mining and production of local bentonite. Also, it would help in the sales of periwinkle shell and production of Mucuna solannie in large and commercial quantities, which would be a source of revenue to local farmers.
Furthermore, it can be inferred that converting local bentonite from being calcium-based to being sodium-based like the foreign bentonite may not be the only solution to the beneficiation process. As was observed from our results and analysis, periwinkle shell contained calcium as its major constituent element while Mucuna solannie contained potassium and carbon as its major constituent elements. Both additives contained very little and insignificant amount of sodium in them. Hence, making local bentonite to be sodium-based by the process of atomic exchange (Joel & Nwokoye, Citation2010) may not be the only solution to the beneficiation process.
Nomenclature/Abbreviations
API – American Petroleum Institute
FB – Foreign Bentonite
LB – Local Bentonite
MS – Mucuna solannie
OCMA – Oil Companies Materials Association
PV – Plastic Viscosity
PW – Periwinkle Shell
RPM – Revolutions per minute
YP – Yield point
Acknowledgements
This test was carried out in Spectral Laboratory Services (SLS), Kaduna, Nigeria. The authors appreciate the assistance, support and efforts of their technical staff, as well as dedication to duty.
Additional information
Funding
Notes on contributors
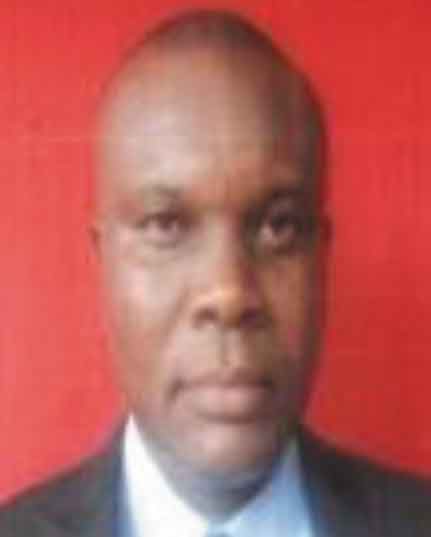
Uwaezuoke Nnaemeka
The author acquired B.Eng (Nigeria), M.Sc (Norway) and Ph.D (Nigeria) all in Petroleum Engineering. He lectures and conducts research in Petroleum Engineering within Drilling and Well Engineering in particular and other areas of interest in general. His current research area is in the advancement of local content in the oil and gas industry. Such fields include control of fluid loss and viscosity of drilling fluids by the use of local materials and cold and hot temperature rheology in general. He also has interest in the potential of local materials for the treatment of produced water in petroleum and natural gas production operations. He has published articles in reputable journals in vast areas of petroleum and natural gas engineering.
References
- Abdelmalik, A. A., & Sadiq, A. (2019). Thermal and electrical characterization of composite metal oxides particles from periwinkle shell for dielectric application. SN Applied Sciences, 1(4), 373. https://doi.org/10.1007/s42452-019-0388-5
- Abdullahi, A. S., Ibrahim, A. A., Muhammed, M. A., Kwaya, M. Y., & Mustapha, S. (2011). Comparative evaluation of rheological properties of standard commercial bentonite and a locally beneficiated bentonitic clay from a marine deposit in upper Benue basin Nigeria. Br. J. Appl. Sci. Tech., 1(4), 211–17. https://doi.org/10.9734/BJAST/2011/445
- Afolabi, R. O., Oyinkepreye, D. O., & Efeovbokhan, V. E. (2017). Properties and application of Nigerian bentonite clay deposits for drilling mud formulation: recent advances and future prospects. Appl. Clay Sci, 143, 39–49. http://dx.doi.org/10.1016/j.clay.2017.03.009
- Agwu, O. E., Okon, A. N., & Udoh, F. D. (2015). A review of Nigerian bentonitic clays as drilling mud society of petroleum engineers, lagos. SPE-178264-MS, 1–18. https://doi.org/10.2118/178264-MS
- Ahmed, A. S., Salahudeen, N., Ajinomoh, C. S., Hamza, H., & Ohikere, A. (2012). Studies on the mineral and chemical characteristics of pindiga bentonitic clay. Petrol. Technol. Dev. J., 1, 1–8.
- Aigbedion, I., & Iyayi, S. E. (2007). Formation evaluation of Oshioka field using geophysical well logs. Middle-East J. Sci. Res., 2(3–4), 107–110.
- Ajugwe, C., Oloro, J., & Akpotu, D. (2012). Determination of the rheological properties of drilling mud from locally sourced clay from various geographical areas. Journal of Engineering Applied Sciences, 4, 38–49.
- Al-Homadhi, E. S. (2009). Improving local bentonite performance for drilling fluids applications. J. King Saud Univ., Eng. Sci., 21(1), 45–52. https://doi.org/10.1016/S1018-3639(18)30522-1
- Dewu, B. B., Funtua, I. I., Oladipo, M. O., Arabi, S. A., Mohammed-Dabo, I. A., Muhammad, A. M., & Hamidu, I. (2011b). Evaluation and beneficiation of bentonic clays from pindiga formation in benue trough. Am. J. Eng. Appl. Sci., 4(4), 497–503. https://doi.org/10.3844/ajeassp.2011.497.503
- Dewu, B. B., Oladipo, M. O., Funtua, I. I., Arabi, S. A., Mohammed-Dabo, I. A., & Muhammad, A. A. (2012a). Evaluation of the rheological and other physical properties of bentonitic clays from fika formation in parts of north-eastern Nigeria. Pet. Technol. Dev. J., 1.
- Emofurieta, W. O. (2001). The characteristics of the Nigerian bentonite. Geociecaias Rev. Univ. Aveiro, 15, 39–47.
- Falode, O. A., Ehinola, O. A., & Nebeife, P. C. (2008). Evaluation of local bentonitic clay as oil well drilling fluids in Nigeria. Appl. Clay Sci., 39, 19–27. https://doi.org/10.1016/j.clay.2007.04.011
- Inegbenebor, A. I., Sanya, O. O., Ogunniran, K. O., Inegbenebor, A. O., & Adekola, A. O. (2014). Potentially exploitable base-metal containing bentonite clay minerals of Ibeshi-Ikorodu South-Western Nigeria for oil bleaching. Covenant J. Phys. Life Sci., 2(2), 123–137.
- James, O. O., Mesubi, M. A., Adekola, F. A., Odebunmi, E. O., & Adekeye, J. I. (2008). Beneficiation and characterization of a bentonite from north-eastern Nigeria. J. N. C. Acad. Sci., 124(4), 154–158. https://www.jstor.org/stable/24336367
- Joel, O. F., & Nwokoye, C. U. (2010). Performance evaluation of local bentonite with imported grade for utilization in oil field operations in Nigeria. Society of Petroleum Engineers, 6–10. https://doi.org/10.2118/136957-MS
- Nweke, O. M., Igwe, E. O., & Nnabo, P. N. (2015). Comparative evaluation of clays from abakaliki formation with commercial bentonite clays for use as drilling mud. afr. J. Environ. Sci. Technol, 9(6), 508–518. http://dx.doi.org/10.5897/AJEST2015.1904
- Obaje, S. O. (2013). Suitability of borno bentonites as drilling mud. Int. J. Sci. Technol., 3(2), 151–152.
- Olugbenga, A. G., Garba, M. U., Soboyejo, W., & Chukwu, G. (2013). Beneficiation and characterization of a bentonite from Niger delta region of Nigeria. Int. J. Sci. Eng. Invest, 2(14), 14–18.
- Omole, O., Adeleye, J. O., Falode, O., Malomo, S., & Oyedeji, O. A. (2013). Investigation into the rheological and filtration properties of drilling mud formulated with clays from northern Nigeria. J. Petrol. Gas Eng, 4(1), 1–13. http://dx.doi.org/10.5897/JPGE09.017
- Oyawoye, M. O., & Hirst, D. M. (1964). Occurrence of a montmorillonite mineral in Nigerian younger granites at Ropp Plateau Province, northern Nigeria. Clay Miner. Bull, 5(32), 427. https://doi.org/10.1180/claymin.1964.005.32.02
- Raw materials research and development council, 2007. Technical Brief on Mineral Raw Materials in Nigeria
- Uwaezuoke, N., Igwilo, K. C., Onwukwe, S. I., Obah, B. (2017). Optimization of mucuna solannie mud rheological parameters. Journal of Petroleum Engineering and Technology, 7(1), 15–26p.
- Raw Materials Research Development Council. (2007). Technical Brief on Mineral Raw Materials in Nigeria - Bentonite. RMRDC, Abuja. http://library.rmrdc.gov.ng/rawmaterials.php?type=mineral
Appendix A
A.1: Elemental composition of periwinkle shell
A.2: Elemental composition of Mucuna solannie
A.3: API filtrate volume of the additives
A.4: Rheological properties of the additives