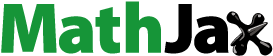
Abstract
For off-grid, standalone solar-fed water pumping has become a very viable option for small householder farmers. Appropriate configuration and control to suit this specific application are required. Buck, boost, and buck-boost converters are used to ensure impedance adaption between the solar PV generation and the load. However, these converters have switching harmonic problems. This problem is solved by the use of a single-ended primary inductor converter. Thus, a single-ended primary inductor converter is designed to overcome these drawbacks. Therefore, the objective of this paper is to design a single-ended primary inductive converter with a PI-like fuzzy controller. In this paper, synchronous SEPIC converter with PI-like fuzzy controller for PV-fed pumping system is modeled and designed. The system performance at different input conditions is evaluated. PI and PI-like fuzzy controllers have been compared using MATLAB/SIMULINK. PI-type fuzzy controller is less sensitive to input parameters variation than PI due to auto-tuning capability. Less than 2% output variation is recorded between 200 and 1000 W/m2 irradiance. This show that output voltage is less sensitive to the input solar radiation with this SEPIC converter control. The steady-state result obtained in speed and flow rate were 141.4 rpm and 1.56 l/s, respectively, and the voltage error was 1.4 V. Thus, PI-like fuzzy controller was used to reduce the steady-state error. The results obtained with PI-like fuzzy controller in speed and flow rate were 143.6 rpm and 1.624 l/s at 6 m head, respectively. The voltage error is 0.2 V which is less than the PI converter error (1.4 V).
PUBLIC INTEREST STATEMENT
There has been growing interest in standalone solar-fed water pumping for small householder farmers due to easy to use, less cost. Fuzzy logic-based PI-like fuzzy Synchronous SEPIC converter control system is one of the intelligent methods of speed and flow rate control system that aims at constant speed and flow rate. Effectiveness of fuzzy logic controller depends on the set of linguistic variables and values. These should be considered to obtain optimal results in terms of maintaining speed and flow rate. PI-like fuzzy approach is used due to its ability to maintain speed and flow rate with minimum voltage error and is less sensitive to input parameters. In Ethiopia, most of the populations use petroleum-powered pumps with high running cost and low performance. Thus, solar-fed water pumping has become very viable option for small householder farmers with PI-like fuzzy synchronous SEPIC converter control system to improve pumping system performance.
1. Introduction
Eco-friendly irrigation powered by photovoltaic systems can make a difference for millions of farmers in Africa. Ninety percent of the farmers in Africa currently depend on rainfall to cultivate their crops. Time intensive and inefficient manual irrigation systems, expensive and polluting petroleum-powered pumps, and cleaner and relatively cheap to run solar pump systems are among the possible options for farmers to adapt to changing patterns due to climate change (Belay et al., Citation2017; Sharp, Citation2016). For domestic and irrigation applications in developing countries, photovoltaic-based water pumping systems are used to draw water from the source. It is a cost-effective method than wind turbine for remote area applications (Allouhi et al., Citation2019).
For off-grid or limited access to central electric grid areas and high diesel cost, which affects the requirement of water, standalone photovoltaic water pumping systems have become a very competitive solution for small-scale irrigation applications (Shebani & Iqbal, Citation2017; Mohammed Wazed et al., Citation2018). Hence, photovoltaic has a less environmental impact and low running cost.
In Ethiopia, solar PV-fed water supply and irrigation systems are gaining interest than other forms of renewable energy resources due to the available resource and significant reduction in investment cost. Therefore, an efficient and cost-effective design of photovoltaic-powered pumps for small householder farmers is required.
In the study by Senpagapandi et al. (Citation2017), performance analysis of a DC photovoltaic water pumping system with direct connection and DC–DC converter has been performed. The study results showed that the DC–DC converter coupled system has better performance than a direct connection for their ability to be matched to the output of the solar panel.
In the study by Shebani and Iqbal (Citation2017), dynamic modeling of a solar PV water pumping system with permanent magnet DC motor (PMDC) was presented in MATLAB/SIMULINK environment. Fractional open-circuit voltage (FOVC) based maximum power point tracking (MPPT) was done with and without a storage device. The result obtained shown that system efficiency improvement was achieved when the PMDC motor runs at a specific speed rather than at a PV peak.
In the study of Sado and Hassan (Citation2018), generalized method of PV-powered water pump using PMDC was developed. The result obtained from the simulation shown that the PMDC pumping system was economical, efficient, and has better discharge than the AC pumping system. For PV pumping applications, the PMDC motor was preferred among other types because it can provide high starting torque.
Various types of DC/DC converters, such as buck, boost, and buck-boost converters, are used to ensure impedance adaption between the solar PV generation and the load. A single-ended primary inductor converter (SEPIC) is another DC/DC converter designed to overcome the drawback of the above converters. It is positively regulated, has wide operation ranges and has better efficiency (Khather & Ibrahim, Citation2020; Vaigundamoorthi et al., Citation2020). Moreover, synchronous SEPIC converters are DC-DC converter that can maintain a constant output voltage under varying input conditions such as voltage reduction as hard shade is applied and load condition. Solar radiation and ambient temperature are factors that affect the efficiency of PV-powered pumping systems. The DC power required to fuel the DC water pump generated by the PV module is linearly dependent on the radiation (Tiwari & Kalamkar, Citation2018).
In the studies by Salilih et al. (Citation2020) and Motahhir et al. (Citation2018), effects of solar radiation and ambient temperature on the performance of a PV pumping system have been demonstrated. The results of this paper have shown that the increase in temperature yields a significant decrease in pump flow rate. The simulation result obtained from the same work indicated that the increase in solar radiation yields a better pump flow rate at a constant temperature. This shows that the variation in ambient temperature and radiation results in a variation in the flow rate.
The fuzzy logic controller has now become feasible for power converters like SEPIC due to the recent advancement of microcontrollers. Complexity, nonlinearity, and/or impreciseness make SEPIC converters difficult to model. SEPIC converters have a time-varying structure and consist of parasitic elements. A fuzzy controller is best suited for such kinds of problems. Despite its advantages, there is no defined procedure or trial and error in designing and undetermined performance until the design is finished, which are the problems with the fuzzy controller. This control technique relies on the human capacity to understand the system’s behavior which determines how effective linguistic rules of the Fuzzy Controllers are and is based on qualitative control rules (Perry et al., Citation2007).
There are different PI converter controller-related studies in which PI converter controller has been used for constants speed and flow. In this study, PI-like fuzzy converter controller system has been used for constant speed and flow rate. The existing literature review explored that many researchers used different methods to maintain constant speed and flow rate. This study contributes to the existing literature by proposing PI-like fuzzy synchronous SEPIC converter control system that maintains a constant flow rate and speed with less sensitive to input parameters variation and minimum steady state error.
In this study, a synchronous SEPIC converter is designed and simulated using MATLAB/SIMULINK environment for solar-powered pumps of small-scale farmers. The speed and flow rate performance at different input conditions with a PI-like Fuzzy controller is evaluated. The synchronous converters are now becoming favorable than other types due to their reduced voltage ripple, current ripple, better efficiency, and elimination of the use of MPPT techniques (Meligy et al., Citation2020; Murdianto et al., Citation2019; Hussein et al., Citation2020). Therefore, it is necessary to design the SEPIC converter to work at its maximum yield of the pump at variable input conditions.
1.1. Materials and methods
This study aims to model and design of the PI-like fuzzy controller to improve the flow rate and speed with minimum voltage error. The method adopted in this paper to study the model and design PI-like fuzzy controller is a survey of relevant literature, modeling of arrays, SEPIC converter, DC motor and centrifugal pump, design of SEPIC converter for the specific pump motor, design of the PI-like fuzzy controller for constant output voltage of the converter, simulation of conventional PI and PI-like fuzzy controller for the overall systems using MATLAB/SIMULINK. The results of the controller are discussed and conclusions are drawn from .
2. Photovoltaic array model and design
A photovoltaic array is made up of combined series/parallel modules, which are composed of usually series PV cells. A photovoltaic cell is a PN junction semiconductor that absorbs light and converts it into electrical energy in the form of DC with a photovoltaic effect (Premkumar et al., Citation2020; Zou et al., Citation2020).
The operating of a solar cell can be represented by the equivalent circuit model which consists of a current source diode, parallel resistor expressing leakage current, and series resistor describing an internal resistance ().
Figure 2. Generalized equivalent circuit model of PV cell (Nguyen et al., Citation2020)
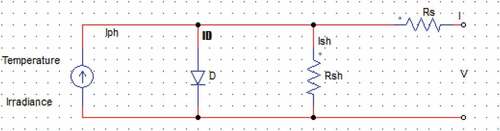
The photovoltaic panel is composed of cells placed in parallel Np or series Ns. It is modeled by a current source connected with a parallel diode with shunt and series resistors.
The output current, I is given by (Mahmoud & Xiao, Citation2018)
Where: —photo current
—diode current
—module saturation current
But the photovoltaic is expressed as (Motahhir et al., Citation2018)
Where: —short circuit current (A)
—short circuit current of cell at 25°C and 1000 W/m2
T—operating temperature (K)
—solar irradiation (W/m2)
Module shunt saturation current, , is given by (Gul et al., Citation2019)
To find saturation dark current, , it is important to define module reverse saturation current as (Meyer, Citation2017)
Where: q—electron charge =
—open circuit voltage
n—Ideality factor of the diode
k—Boltzmann’s constant =
Then saturation dark current, is given by (Meyer, Citation2017)
Where: —nominal temperature = 298.5 K
- band gap energy of semiconduction = 1.1 eV
Finally, the output current I is detailed as (Gul et al., Citation2019)
But thermal voltage is
Typically, is very large and
is very small. It is common to neglect these resistances to simplify the model. The simplified voltage, current characteristics of photovoltaic cell is given by
The typical output power characteristics of a PV array under various degrees of irradiation and temperature are illustrated in . It is demonstrated that a particular optimal voltage for each radiation and temperature corresponds to the maximization of power output. Therefore, the output power from the array can be drawn by adjusting the output voltage or current.
For photovoltaic panel and array configuration, it is important to determine the solar panel rating. For this design, a 370WDC pump that can deliver up to 6500 l/h at 6 m head is selected. Assume the operating hours of the pump is 4 h/day. The Wh per day will be 1480 Wh/day.
Considering the clearance and 7 hours peak sun hour in Ethiopia, commercially available 250 W solar panel is selected ().
Table 1. Parameters of the COPEX M250 module 25°C and 1000 W/m2
2.1. Synchronous SEPIC converter design and operation
A SEPIC converter consisting of a switch S with duty cycle α, a diode, two inductors L1 and L2, two capacitors C1 and C2, and motor load are presented in .
Figure 4. Conventional SEPIC converter (Morelo et al., Citation2020)
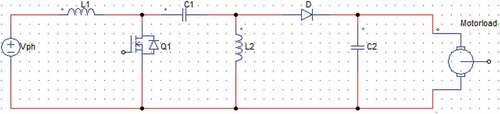
To create continuous conduction mode and remove the inverse voltage, the diode (D) swiped by the switch Q2 (). The term synchronization comes from synchronizing the pulse of the MOSFET/IGBT switch. The two switches Q1 and Q2 are controlled by two complementary PWM signals (Nagarajan et al., Citation2017).
In continuous conduction of SEPIC converter, there are two modes of operations that Q1 is ON, Q2 is OFF and Q1 is OFF, Q2 is ON.
Operation mode 1: When Q1 is ON and Q2 is OFF, the current flows through L1 and therefore L1 and L2 are charging whereas C1 is discharged.
Operation mode 2: When Q1 is OFF and Q2 is ON, the inductors L1 and L2 discharges and the capacitor C1 discharges.
2.1.1. Design process of Synchronous SEPIC converter
For continuous conduction mode (CCM) of a SEPIC converter duty cycle (Iii & Issn, Citation2016; Leema Rose & Sankaragomathi, Citation2016) is given by
The output voltage,, of the Synchronous SEPIC converter considering the input voltage
from the solar PV output is given by
The input current from the SEPIC converter, is calculated as
Where: —output current
—Input current
One of the initial steps in designing any PWM switching controller is to decide how much inductor ripple current, to permit. The switching frequency,
is selected to keep ripple current low and to reduce inductor size. A general rule is to use 20–40% of the input current, the ripple current is given by
(Iii & Issn, Citation2016; Leema Rose & Sankaragomathi, Citation2016).
Permitting the peak-to-peak ripple current to be roughly 30% of the maximum input current at the minimum input voltage determines the inductance. The ripple current flowing at equal values of the inductors L1 and L2 are given by (Iii & Issn, Citation2016)
The output current of the SEPIC converter is given by
Synchronous SEPIC AC coupling capacitor is selected using
And the capacitor C2 is calculated by
Where
The selection of SEPIC capacitor, C1 depends on the PMS currents which is given by
The SEPIC capacitor must be rated for a large PMS current. The voltage rating of the SEPIC capacitor must be greater than max input voltages. The peak-to-peak ripple voltage on Cs
2.2. Permanent magnet (PMDC) motor model
In this motor, the permanent magnet is used as field winding so the motor does not require external excitation. The equivalent circuit of a PMDC motor (Shebani & Iqbal, Citation2017; Humaidi & Ibraheem, Citation2019; Senthil Kumar et al., Citation2018) ()
The supply voltage (Vs) (Senthil Kumar et al., Citation2018) can be written as
Where: Vs is DC source voltage (V)
—the armature current (A)
Ra—armature resistance (Ω)
La—armature inductance (H)
—torque constant (vᐧ.s/rad)
—motor speed (rpm)
Electrical torque (Nm) is given by
The motor speed as a function of the electrical torque and load torque (Nm) is given by
Where: —inertia constant (kgᐧm2)
—Constant (N*m*s)
Rearranging all the above equations, the dynamic model of a PMDC motor can be described as
The parameters for the PMDC are presented in .
Table 2. Parameters of PMDC
2.3. Water pump model
A centrifugal pump load is expressed by using the following equation which indicates the load torque (Shebani & Iqbal, Citation2017; Senthil Kumar et al., Citation2018; Al-obaidi, Citation2020; Al-Obaidi, Citation2020)
The flow rate according to Senpagapandi et al. (Citation2017) and Al‐Obaidi (Citation2020) can be given by
Where: p—input power required (W)
—fluid density (kg/m3)
H—total head
—gravitational acceleration (9.8 m/s2)
—flow rate (m3/s)
—efficiency of the pump
2.4. PI-like fuzzy controller SEPIC model
Fuzzy logic control is one of the emerging intelligent methods that has been developed and used for controller design in order to replace the conventional controllers. It also provides the accuracy of a dynamic model of the system to be controlled. It is based on linguistic variables and rules latter than numerical values and complex equations. FLC is used where an exact mathematical formulation of the problem is difficult due to non-linear time-varying nature of response, large unpredictable disturbance, etc. (Yousefi et al., Citation2018).
The voltage error () and the change in voltage error (
) from the SEPIC to the PMDC motor are the inputs of PI-like fuzzy logic controller (El Khateb et al., Citation2014). The output of the PI-like fuzzy controller is the duty cycle (D) of the PWM signal, which regulates the output voltage of the synchronous SEPIC converter. The Synchronous pulse from FLC output is also fed to the synchronous converter.
The first input is the error in voltage ()
The second input is the change in error ()
The output variable is the duty cycle (D)
Where: —reference Voltage
—measured voltage in the kth sample
D(k)—duty cycle sent to the PWM
—Change in voltage error
—Voltage error
The block diagram of control model is shown in .
For simplicity triangular membership function are used (Azam et al., Citation2020). A five-term fuzzy set (BN—Big Negative, SN—Small Negative, ZO—Zero, SP—Small Positive, BP—Big Positive) are defined and selected for each input.
The fuzzy output changes the pulse duties which determine the motor speed and the flow rate of the pump by controlling the output voltage of the synchronous SEPIC converter. Therefore, stable speed and flow rate will be maintained in the case of variable solar inputs, such as irradiation and temperature.
The structure of the proposed PI-like fuzzy knowledge-based controller consists of normalization, fuzzification, membership function definition, rule base, defuzzification, and denormalization. All the functions are defined on a normalized interval [−1, 1] (Azam et al., Citation2020; Oudda & Hazzab, Citation2016a; Oudda & Hazzab, Citation2016b).
PI-like FLC consists of the following rules of the term (El Khateb et al., Citation2014)
If is <This> and
is <This> then
is The fuzzy rule base to control the duty cycle is composed of 25 rules ().
Table 3. Fuzzy rules
3. Simulation result
The simulation results of this study are based on the following parameters (). Those designed and determined parameters are used to test the performance of PI and PI-fuzzy controller models in MATLAB/SIMULINK environment.
Table 4. Simulation parameters
MATLAB/SIMULINK is used to model of PI controller for Synchronous SEPIC converter. The model () represents a model of the PI controller. The DC source with inductors, capacitors and MOSFETs are used to represent the source and PI controller, respectively.
The output voltage of the SEPIC converter by using the PI feedback controller is 103.2 V (). The PI controller has 1.4 V steady-state error with a ripple. The ripple can be adjusted by using the appropriate value of inductors and capacitors.
The steady-state simulation result obtained in speed is 141.4 rpm (). Due to 1.4 V error in voltage output of the SEPIC converter, it is difficult to find the P and I values from the precise tuning of the PI controller. Therefore, in this paper, PI-like fuzzy controller is preferred to reduce the steady-state error.
The simulation result obtained for the flow rate is 1.56 l/s (). Due to a large error in voltage output of the SEPIC converter, the flow rate is less than that of PI-like fuzzy controller. Thus, in this paper, PI-like fuzzy controller is preferred to increase the flow rate.
MATLAB/SIMULINK is used to model PI-like converter to reduce the steady-state error (). The model represents solar PV input, fuzzy controller, converter, and model of motor and pump as subsystem (). The motor and pump models are used as an input at “A” for the overall system model. Rules are formulated and loaded to control the system accordingly.
For PI-fuzzy controller, the flow rate from the simulation is 1.624/s (). Due to less error in voltage output of the SEPIC converter, the flow rate is increased in the case of PI-like fuzzy controller. This shows that PI-like fuzzy controller solves the drawbacks of the PI controller.
It has been tested with two different irradiances such as 200 and 800 W/m2 at a fixed ambient temperature of 26.5°C. The result obtained demonstrated that the expected flow rate of 1.624 l/s at 6 m head and 143.6 rpm () has been achieved in both cases. The voltage error is 0.2 V.
3.1. Sensitivity analysis of SEPIC
Sensitivity analysis is the study of how a certain system responds to a variation of its inputs. It is
an analysis method for systematically changing variables in a model to determine the effects of such changes to its output. Sensitivity analysis is used to evaluate a system output on small changes in the input. Solar radiation is the most important parameter in the sensitivity analysis of the SEPIC output. In this study, a sensitivity analysis is done for SEPIC converter control. As the solar radiation is increased, there is a small change in SEPIC converter output (). The SEPIC converter output is less sensitive to solar radiation inputs which less than 2%.
Table 5. Solar input for SEPIC converter
Sensitivity of the system output y to variations in the system input x is defined as,
4. Conclusion
Synchronous SEPIC converter is designed and simulated for small-scale farmers. The speed and flow rate performance at different input conditions of PI-like Fuzzy controller is evaluated. Error in voltage, change in error, and duty cycle were the major factors for PI-Fuzzy controller logical rule formulation. PI-fuzzy controller improves the speed of the system from 141.4 to 143.6 rpm. It also improves the flow rate from 1.575 to 1.624 l/s. In addition, PI-fuzzy controller reduces the error in voltage.
It is concluded that PI-like fuzzy controller steady-state error is much less that the PI controller. A fuzzy PI controller is presented, which can provide improved performance such as well-damped output voltage for synchronous SEPIC converters. PI-type fuzzy controller is less sensitive to input parameter variation due to auto-tuning capability.
Thus, with different input parameters constant flow rate and speed are achieved with minimum steady-state error. It is, therefore, important for the long life of the pump. It is also relatively easy to implement on the hardware platform. These features also make it suitable for high-voltage and high-power applications. The PI-like FLC is, however, known to give poor performance in starting response due to the internal integrating operation.
4.1. Limitations
The major concern of this study is the model and design of PI-like fuzzy synchronous SEPIC converter control without considering the effects of starting response of the PI-like FLC. Improving the starting response of the PI-like FLC is suggested.
Abbreviations
DC: Direct current
AC: Alternative current
W: Watt
Wh: Watt hour
PV: Photovoltaic
SEPIC: Single ended primary inductor converter
FOVC: Fractional open circuit voltage
PMDC: Permanent magnet DC
MPPT: Maximum power point tracking
PI: Proportional integral
V: Volt
Availability of data and materials
All data generated or analyzed during this study are included in this published article.
Acknowledgements
We would like to acknowledge our friends who were very interested, encouraged, and helped us to do this research. We also thank Amhara regional agricultural office to their permission and community members to give necessary information to conduct the research.
Additional information
Notes on contributors
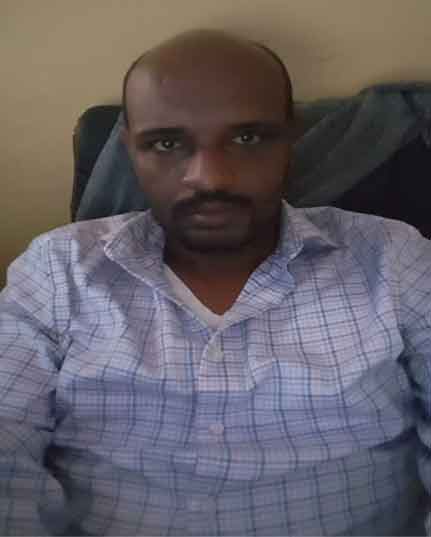
Tewodros Gera Workineh
Mr. Tewodros Gera is a lecturer at faculty of electrical and computer engineering, Bahir Dar University. He obtained his first and second degrees in Electrical Power Engineering in Adama University.
Mr. Biniyam Zemene is a lecturer at faculty of electrical and computer engineering, Bahir Dar University. He obtained his first degree in Electrical Engineering in Adama University and his second degrees in Electrical Power Engineering in Bahir Dar University.
Asst. Professor Abraham Hizkiel is a lecturer at faculty of electrical and computer engineering, Bahir Dar University. He obtained his first degree in Electrical Power Engineering in Debre Markos University and second degree in Electrical Power System Engineering in Bahir Dar University.
Mr. Elias Mandefro is a lecturer at faculty of electrical and computer engineering, Bahir Dar University. He obtained his first and second degree in Electrical Power Engineering in Bahir Dar University.
References
- Allouhi, A., Buker, M. S., El-houari, H., Boharb, A., Benzakour Amine, M., Kousksou, T., & Jamil, A. (2019). PV water pumping systems for domestic uses in remote areas: Sizing process, simulation and economic evaluation. Renewable Energy, 132, 798–20. https://doi.org/10.1016/j.renene.2018.08.019.
- Al-obaidi, A. R. (2020). Experimental comparative investigations to evaluate cavitation conditions within a centrifugal pump based on vibration and acoustic analyses techniques. Arch. Acoust, 45(3), 541–556. https://doi.org/10.24425/aoa.2020.134070.
- Al-Obaidi, A. R. (2020, June). Detection of cavitation phenomenon within a centrifugal pump based on vibration analysis technique in both time and frequency domains. Experimental Techniques, 44(3), 329–347. https://doi.org/10.1007/s40799-020-00362-z.
- Al‐Obaidi, A. R. (2020, June). Investigation of the influence of various numbers of impeller blades on internal flow field analysis and the pressure pulsation of an axial pump based on transient flow behavior. Heat Transfer, 49(4), 2000–2024. https://doi.org/10.1002/htj.21704.
- Azam, M. H., Hasan, M. H., Hassan, S., & Abdulkadir, S. J. Fuzzy type-1 triangular membership function approximation using fuzzy C-means. 2020 Int. Conf. Comput. Intell., no. October, pp. 115–120, 2020, [Online]. Available: https://ieeexplore.ieee.org/document/9247773/
- Belay, A., Recha, J. W., Woldeamanuel, T., & Morton, J. F. (2017). Smallholder farmers’ adaptation to climate change and determinants of their adaptation decisions in the central rift valley of ethiopia. Agriculture & Food Security, 6(1), 1–13. https://doi.org/10.1186/s40066-017-0100-1.
- El Khateb, A., Rahim, N. A., Selvaraj, J., & Uddin, M. N. (2014). Fuzzy-logic-controller-based SEPIC converter for maximum power point tracking. IEEE Transactions on Industry Applications, 50(4), 2349–2358. https://doi.org/10.1109/TIA.2014.2298558.
- Gul, S., Haq, A. U., Jalal, M., Anjum, A., & Khalil, I. U. (2019). A unified approach for analysis of faults in different configurations of PV arrays and its impact on power grid. Energies, 13(1), 156. https://doi.org/10.3390/en13010156.
- Humaidi, A. J., & Ibraheem, I. K. (2019). Speed control of permanent magnet dc motor with friction and measurement noise using novel nonlinear extended state observer-based anti-disturbance control. Energies, 12(9), 1651. https://doi.org/10.3390/en12091651.
- Hussein, A. A., Chen, X., Alharbi, M., Pise, A. A., & Batarseh, I. (2020). Design of a grid-tie photovoltaic system with a controlled total harmonic distortion and tri maximum power point tracking. IEEE Transactions on Power Electronics, 35(5), 4780–4790. https://doi.org/10.1109/TPEL.2019.2946586.
- Iii, V., & Isn, I. (2016). Design of Synchronous SEPIC and Synchronous zeta converter for stand-alone photovoltaic system. RSIS international, III(V), 149–155.
- Khather, S. I., & Ibrahim, M. A. (2020). Modeling and simulation of SEPIC controlled converter using PID controller. Int. J. Power Electron. Drive Syst, 11(2), 833–843. https://doi.org/10.11591/ijpeds.v11.i2.pp833-843.
- Leema Rose, J., & Sankaragomathi, B. (2016). Design, Modeling, Analysis and Simulation of a SEPIC converter. Middle-East J. Sci. Res, 24(7), 2302–2308. https://doi.org/10.5829/idosi.mejsr.2016.24.07.23750.
- Mahmoud, Y., & Xiao, W. (2018). Evaluation of shunt model for simulating photovoltaic modules. IEEE Journal of Photovoltaics, 8(6), 1818–1823. https://doi.org/10.1109/JPHOTOV.2018.2869493.
- Meligy, R., Rady, M., El Samahy, A., & Mohamed, W. (2020). Proportional-integral-like fuzzy controller of a small-scale linear fresnel reflector solar plant. IET Renewable Power Generation, 14(14), 2620–2628. https://doi.org/10.1049/iet-rpg.2020.0024.
- Meyer, E. L. (2017). Extraction of saturation current and ideality factor from measuring Voc and sc of photovoltaic modules. International Journal of Photoenergy, 2017, 1–9. https://doi.org/10.1155/2017/8479487.
- Mohammed Wazed, S., Hughes, B. R., O’Connor, D., & Kaiser Calautit, J. (2018). A review of sustainable solar irrigation systems for Sub-Saharan Africa. Renewable and Sustainable Energy Reviews, 81, 1206–1225. https://doi.org/10.1016/j.rser.2017.08.039.
- Morelo, A. J., Trujillo, S. C., & Hoyos, F. E. (2020). Simulation, bifurcation, and stability analysis of a SEPIC converter controlled with ZAD. Int. J. Electr. Comput. Eng, 10(1), 728–737. https://doi.org/10.11591/ijece.v10i1.pp728-737.
- Motahhir, S., El Ghzizal, A., Sebti, S., & Derouich, A. (2018). Modeling of photovoltaic system with modified incremental conductance algorithm for fast changes of irradiance. International Journal of Photoenergy, 2018,13. https://doi.org/10.1155/2018/3286479.
- Murdianto, F. D., Nansur, A. R., Septiarini, N. A., Widarsono, K., & Purwanto, E. (2019). SEPIC converter with coupled inductor using fuzzy logic controller to optimized battery charging process. Journal of Physics: Conference Series, 1367(1), 012074. https://doi.org/10.1088/1742-6596/1367/1/012074.
- Nagarajan, R., Chandramohan, J., Yuvaraj, R., Sathishkumar, S., & Chandran, S. (2017). Performance analysis of synchronous sepic converter for a stand-alone PV system. International Journal of Emerging Technologies in Engineering Research (IJETER) ,5(5), 12–16.
- Nguyen, B. N., Nguyen, V. T., Duong, M. Q., Le, K. H., Nguyen, H. H., & Doan, A. T. (2020). Propose a MPPT algorithm based on thevenin equivalent circuit for improving photovoltaic system operation. Frontiers in Energy Research, 8(February). https://doi.org/10.3389/fenrg.2020.00014.
- Oudda, M., & Hazzab, A. (2016a). Fuzzy logic control of a SEPIC converter for a photovoltaic system. Journal of Fundamentals of Renewable Energy and Applications, 6(4). https://doi.org/10.4172/2090-4541.1000212.
- Oudda, M., & Hazzab, A. (2016b). Photovoltaic system with SEPIC converter controlled by the fuzzy logic. Int. J. Power Electron. Drive Syst, 7(4), 1283–1293. https://doi.org/10.11591/ijpeds.v7i4.pp1283-1293.
- Perry, A. G., Feng, G., Liu, Y. F., & Sen, P. C. (2007). A design method for PI-like fuzzy logic controllers for DC-DC converter. IEEE Transactions on Industrial Electronics, 54(5), 2688–2696. https://doi.org/10.1109/TIE.2007.899858.
- Premkumar, M., Subramaniam, U., Sudhakar Babu, T., Elavarasan, R. M., & Mihet-Popa, L. (2020). Evaluation of mathematical model to characterize the performance of conventional and hybrid PV array topologies under static and dynamic shading patterns. Energies, 13(12), 3216. https://doi.org/10.3390/en13123216.
- Sado, K. A., & Hassan, L. H. (2018). Modeling and Implementation of a PV-powered DC water pump system for irrigation in Duhok city. Academic Journal of Nawroz University, 7(4), 228. https://doi.org/10.25007/ajnu.v7n4a294.
- Salilih, E. M., Birhane, Y. T., & Arshi, S. H. (2020). Performance analysis of DC type variable speed solar pumping system under various pumping heads. Solar Energy, 208(September), 1039–1047. https://doi.org/10.1016/j.solener.2020.08.071.
- Senpagapandi, S., Sathish, R., & Nirmal, S. A. (2017). Design of Synchronous SEPIC DC-DC converter of a stand alone photovoltaic system. IEEE, 2, 26–33.
- Senthil Kumar, A., Prasath Vijay Raj, T., Tharagesh, A., & Prasanna, V. (2018). Design and analysis of a permanent magnet DC motor. Lect. Notes Electr. Eng, 442, 237–249. https://doi.org/10.1007/978-981-10-4762-6_22.
- Sharp, G. (2016). Food Production and Consumption. Capitalism Nature Socialism, 27(4), 117–124. https://doi.org/10.1080/10455752.2016.1245915.
- Shebani, M. M., & Iqbal, T. (2017). Dynamic Modeling, Control, and Analysis of a solar water pumping system for libya. Journal of Renewable Energy, 2017, 1–13. https://doi.org/10.1155/2017/8504283
- Tiwari, A. K., & Kalamkar, V. R. (2018). Effects of total head and solar radiation on the performance of solar water pumping system. Renewable Energy, 118(December), 919–927. https://doi.org/10.1016/j.renene.2017.11.004.
- Vaigundamoorthi, M., Ramesh, R., Prabhu, V. V., & Kumar, K. A. (2020). MPPT oscillations minimization in PV system by controlling non-linear dynamics in SEPIC DC-DC converter. Int. J. Electr. Comput. Eng, 10(6), 6268–6275. https://doi.org/10.11591/IJECE.V10I6.PP6268-6275.
- Yousefi, H., Hafeznia, H., & Yousefi-Sahzabi, A. (2018). Spatial site selection for solar power plants using a gis-based boolean-fuzzy logic model: A case study of Markazi Province, Iran. Energies, 11(7), 1648. https://doi.org/10.3390/en11071648.
- Zou, H., Dai, G., Wang, A. C., Li, X., Zhang, S. L., Ding, W., Zhang, L., Zhang, Y., & Wang, Z. L. (2020). Alternating current photovoltaic effect. Advanced Materials, 32(11), 1–11. https://doi.org/10.1002/adma.201907249.