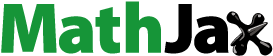
Abstract
In a bid to develop a cheaper alternative material for particleboard, fiber/particulate reinforced cement-paper composites were produced. The paper-cement matrix had 12 wt. % of cement and the matrix was reinforced with 10 wt. % fixed amount of coconut shell powder and varied amount of palm kernel fiber (0, 0.5, 1.0, 1.5, 2.0, and 2.5 wt. %). Two separate groups of samples were produced; one containing untreated fiber (UPKF), in varied proportions of 0–2.5 wt. % and the second containing alkaline-treated fiber (TPKF), in varied proportion of 0–2.5 wt. % fiber. Samples produced were cured for 28 and 49 days and examined for physical, mechanical, and thermal properties as well as microstructural features. The result obtained revealed improvement in properties of samples as fiber proportion increased. Comparison of the properties obtained indicates that alkaline-treated samples gave a better performance than the untreated counterparts, which was reflected in the sum of property ratio for each mix. The value for TPKF samples was higher than the value for UPKF samples. Also, samples cured for 49 days had better performance than the ones cured for 28 days for both UPKF and TPKF. Evaluation of the three experimental variables, fiber addition, alkaline treatment, and curing length proved that curing was more effective in enhancing the properties of the composites developed, especially the mechanical properties.
PUBLIC INTEREST STATEMENT
Most particleboards used for partitioning walls of buildings be it offices, houses, and relevant structures are made from trees of which these trees are cut down. The continuous felling of these trees contributes greatly to climate change which has resulted in hot weather conditions in recent times. Alternative wall partitioning material can be produced from waste paper which will be cheaper and environmentally friendly. In this way, waste paper that could have been disposed of is given economic value coupled with the fact that environmental pollution is reduced. Recycling of this waste by blending with cement provides paperboard, which is strong enough for wall partitioning. Industries can be established for recycling waste paper in the production of paperboards as a cheaper alternative to paperboard for wall partitioning or relevant use.
1. Introduction
Particleboards are composite boards that are made of wood products in form of wood shavings, flakes, and dust and are used in several applications like ceiling boards, furniture, wall partitioning, and speaker and woofer boxes (Rivela et al., Citation2006; Wimmer et al., Citation2011). They are fused with the use of binders like urea formaldehyde which is commonly used based on low cost. Phenol formaldehyde is another form of binder, also some polymer resins are equally employed in binding (Dorieh et al., Citation2018). In the course of production, additives like fibers, stalks, and particulate fillers are introduced for matrix reinforcement (Bunda et al., Citation2020; Ejiogu et al., Citation2018) and enhancement of properties. Challenges faced in the use of these boards are the susceptibility to water and moisture absorption which with time degrades the product. Properties of particleboard include its lower cost as compared with plywood, esthetic and ease of transport as well as installation owing to lightweight. These are eco-friendly materials that require little maintenance. Wood products are produced from the felling of trees and continuous production of these boards requires more falling of trees which in turn contributes to further deforestation and degradation of the environment. The consequence of this act amounts to more challenges of climatic changes and global warming since these trees are important in fighting climate change and for biodiversity (Stern & Kaufmann, Citation2014). These trees are needed for clean air since they absorb CO2 for photosynthesis and emits O2 as a by-product (Johnson, Citation2016). A study by (Guller & Buyuksari, Citation2011; Nyang et al., Citation2019) revealed; global demand for particleboards keeps rising with population increase. To reduce dependability on forest trees for the production of particleboards, alternative raw materials are sourced examples of which include sugarcane bagasse, (Mendes et al., Citation2015) bamboo, grass, fibers, and other agro-byproducts (Zheng et al., Citation2007). These alternatives are lignocellulosic materials which have served as alternative materials for particleboard production. Waste paper can be another alternative lignocellulosic material and can be utilized for the production of boards meant for the same application particleboards are employed (Amiandamhen & Osadolor, Citation2020). Papers that are used in the everyday activities of man especially in modern civilization, are materials made from the processing of cellulose fibers heaved from tress (Lavanya et al., Citation2011); just like wood-based particleboards. However, these papers are often disposed of quickly based on their nature of application in short term. For instance, newsprints which are produced and read every day has short-term use in that after been read that day, they become wastes in most cases, except for few instances where they are kept for reference purpose. After intellectual consumption of the contents, these papers are disposed of almost immediately and are in most cases thrown into landfills. (Ezeudu et al., Citation2018) claimed that 421 million tons of papers and cardboards were consumed globally in 2018, that’s an average of 1.15 million tons of paper every day. Since they are needed in short term, waste papers can be recycled for many purposes one of which is paperboards. Instead of cutting down new trees, these waste papers, been tree products, can be repulped and recycled as alternatives or supplements to particleboards. This idea births the study of incorporation of binder-like cement into waste paper pulp for the production of paperboards as carried out in this study. To improve the mechanical properties of particleboards, additives are introduced in form of fillers and fibers (Sanjay et al., Citation2016). These fillers have a high surface area, hence provides a large site for reaction and reinforcement (Xian, Citation2012). Coconut shell powder was considered in this study as filler due to its strong and hard properties. Moreso, coconut shell powder has been claimed to be good additive in cementitious product (Tomas & Ganiron, Citation2013) and also, use of such agro-waste provides a means of adding economic value to a material which could behave contributed to environmental degradation (Animesh et al., Citation2017). Natural fibers have been utilized in several studies and investigations for reinforcement of matrix, be it polymer or ceramic concrete (Kavitha, Citation2017; Mohammed et al., Citation2015). One of these fibers is palm kernel fiber which is a lignocellulose product, just like the aforementioned materials and has been successful in improving properties of developed polymer composites (Akindapo et al., Citation2017; Obiukwu et al., Citation2016) and cement composites (Ahmad & Md.:, Citation2008; Momoh & Osofer, Citation2020). Alkaline treatment of palm kernel fiber was also employed on the backdrop of the fact that alkaline treatment enhances wetting of fiber with matrix according to (Ji et al., Citation2018; Mazzanti et al., Citation1981; Tan et al., Citation2017). On that note, the present study was geared toward property evaluation of paperboard employing locally source materials like coconut shell, palm kernel fibers, and waste paper with the view of producing locally made paperboard as an alternative or supplementary to particleboards for wall partitioning.
2. Materials preparation and development
2.1. Materials preparation
Waste papers, cement, oil palm pressed fruit (PKF) fiber ()) and coconut shell ()), distilled water, detergents, and 1.3 M NaOH solution were used in the study. Waste papers were shredded using a paper shredder and transferred into a container, half-filled with hot water which was initially heated to 100 ⁰C. The paper was soaked in the water for 4 days. Dewatering was done by pouring the paper slurry into a sack and left for another 4 days, allowing the water to drip off, thereby resulting in paper pulp ()). Further draining of the pulp was effected, spreading the pulp on a wooden table for 2 days. Coconut shells (CS), procured from a grocery store was broken as the copra (white kernel) was removed and separated from the shell. Fiber attachments to the shell were detached, and the shell was treated by immersing in 1.3 Molar NaCl solution. After stirring for 40 min, CS was washed in distilled water and sun-dried for 24 h. Following this was the shattering of the shell with a hammer, and the broken pieces were ground, milled, and sieved to −75 µm using an electric sieve shaker as per ASTM D6913/D6913M-17 (Citation2017). Ordinary Portland cement (grade 43) employed for binding and strengthening, conforms with IS 8112 (Citation2013) as analyzed according to ASTM C150/C150M-20 (Citation2020) procedures. Oil palm pressed fruit fibers (OPF) engaged were gotten from a palm oil production mill in Akure town, Ondo State, Nigeria. The fibers were initially washed using detergents dissolved in distilled water, further rinsed in fresh distilled water followed by sun-drying for 24 hours. PKF fibers were grouped into two equal proportions (50:50) with one portion grouped as untreated palm kernel fiber (UPKF). The other portion was treated in 1.3 Molar NaOH solution in a shaker water bath, which was heated to 40⁰C and maintained for 6 h, after which the fibers were washed in distilled water and sundried for 24 h. Representative samples of some of the untrimmed board composites are shown in ).
2.2. Materials development
Samples development involved blending of paper pulp with 12 wt. % of cement, 10 wt. % coconut shell (CS) powder and varied amount of palm kernel fiber addition (cut to 40 mm length) at 0, 0.5, 1, 1.5, 2 and 2.5 wt. % (for untreated and treated). The blend was mixed manually in a container, and water was added at a water-cement (w/c) ratio of 0.36 to 0.42, with subsequent mechanical mixing. Paper slurry blend realized afterward was poured into prepared cuboid moulds of dimension 150 × 75 x 30 (mm3), 30 x 30 × 30 (mm3), and 200 × 10 x 10 (mm3) according to specification stipulated in IS 2380 (Citation1977). Filled moulds were transferred into the hydraulic press compact molder and compressed at 0.25 MPa for 5 min to ensure sufficient compaction of the blend. The curing process of samples was done in line with ASTM C192/C192M-19 (Citation2019) by keeping samples in 4 different polythene bags labeled “Group” 28 A, “Group” 49 A for untreated fiber (UPKF), “Group” 28 B and “Group” 49 B for alkaline-treated palm kernel fiber (TPKF) according to curing ages respectively. Sets of samples in bags labeled 28 A and 28 B were brought out after 28 days of curing, sun-dried for 24 hours, to ensure dryness in the samples. Thereafter, the samples were probed for physical, thermal, and mechanical properties, and the results obtained were analyzed. The same procedure was followed for samples in bags labeled 49 A and 49 B after 49 days. shows the mix proportion for samples with fiber content for both untreated and treated palm kernel fiber.
Table 1. Mix proportion of composite developed for untreated (UPKF)/treated palm kernel fiber (TPKF)
2.3. Properties of materials
2.3.1. Chemical, elemental compositions, and microstructural analysis
Chemical and elemental composition analyses were performed on paper pulp, cement, CSP untreated (UPKF), and treated (TPKF) fiber, and the results are expressed in for coconut shell powder, for paper and fibers. Also, microstructural analysis was conducted on the fiber used and the result presented in .
Table 2. Chemical composition of coconut shell powder additive
Table 3. Cellulose, hemicellulose, and lignin content present in paper, treated and untreated fiber
LOI is Loss on Ignition
Results of the chemical composition analysis show that coconut shell powder has a higher proportion of silica when compared to other compounds present () and the sum of SiO2, Al2O3, and Fe2O3 content is ≥70%, which makes coconut shell powder a possible pozzolana with cement. ) highlights the features present in untreated palm kernel fiber which include fusion of the fiber due to the presence of impurities on the surface of the fibers. Impurities lead to poor interfacial adhesion between fiber and reinforcement (Oladele et al., Citation2019). Also, lignin and hemicellulose are reported to be responsible for the hydrophilic nature of treated fibers. However, alkali treatment reduced the amount of lignin, hemicellulose, and other impurities present in the fiber () while cellulose of the fiber is modified causing a rather depreciation in hydrophilic tendency of palm kernel fiber as shown in ), where fibers have rough surface when compared to ).
2.4. Test methodology
In carrying out the test, samples were sundried for 24 h, and the average values obtained from testing three samples representing each mix proportion were recorded.
2.4.1. Examination of physical properties of samples
a.Porosity and cold water immersion
Porosity and cold water absorption were investigated in conformity with BS Citation1881-122:2011 (Citation2011) and ASTM C1585–13(Citation2013) by initially measuring the weight in air for samples (W1) and after which samples were soaked in water at 27 ⁰C room temperature for 24 h. Weights of soaked samples were measured when suspended in air (W2) and water (W3). Apparent Porosity (AP) and cold water absorption (WA) were evaluated using the expression in Equations (1) and (2), respectively. Moisture absorption was examined by initially measuring sun-dried sample in air (M1) and exposing in open air for 24 h, after, the mass was measured as (M2). Moisture absorption was therefore appraised using Equation (3).
b. Bulk density
Bulk density (BD) was analyzed in agreement with (IS 2386–3) and their values obtained with the use of Equation (4).
c. Linear and volumetric shrinkage
Linear and volumetric shrinkage were computed by initially measuring length (L1) and volume (V1) after samples were prepared; final length (L2) and volume (V2) after curing ages of 28 and 49 days. Following ASTM C 596-18 (Citation2018), the values were determined with Equations (5) and (6) for linear and volumetric shrinkage, respectively.
Volume was calculated as length x breadth x thickness (mm3) both before immersion in water and after saturated in water.
2.4.2. Examination of mechanical properties of samples
a. Bursting strength
Bursting strength refers to the strength required by a paper material to resist pressure meant to rupture it. It values for a material in this case, cement-paper composite is dependent on production process. Following the procedures outlined in BS 3137 (Citation1972) bursting strength was measured via ZwickRoell burst tester, at 27 ⁰C room temperature and evaluated.
b. Tensile test,
Tensile strength perpendicular to the surface was evaluated using the universal testing machine and carried out on a sample of dimension 50 × 50 x 25 (mm3) as indicated in IS 2380 (Part V):1977. The direction of loading was perpendicular to the face of the board sample; at a loading rate of 0.8 mm/min.
c. Impact test, Surface Hardness, and Abrasion
Impact test was carried out on samples in consonance with ASTM C496-17 (Citation2017). Surface hardness was employed in evaluating hardness as seen in ASTM 293/C293M (Citation2016), noting the applied load (L) and the mean of the diagonals (d). The depth of indentation resulting from the application of a load of 0.5 kg for a period of 15 s was observed and measured using Equation (7). Wear loss was evaluated in line with ASTM D256-10 (Citation2018) and expressed in Equation (8) as weight loss index.
Where M1 stands for weight before abrasion test and M2 stands for weight after abrasion
2.4.3. Experimental trend analysis and performance evaluation
From the results obtained for all properties, experimental trend analysis and performance evaluation were carried out as applied by Akinwande (Citation2020) to determine the trend and efficiencies of the three experimental variables namely; fiber addition, alkaline treatment, and curing length (duration) efficiencies. This is expedient to identify the order of importance of the variables and the magnitude of their influence since they determined property values obtained for each mix proportion.
3. Results and discussion
In the discussion of results, untreated fiber reinforced samples cured for 28 and 49 days are designated UPKF-28 and UPKF-49 accordingly, while those of treated samples are designated TPKF-28 and TPKF-49 for curing ages of 28 and 49, respectively. PKF represents palm kernel fiber while CSP stands for coconut shell powder.
3.1. Analysis of physical properties
3.1.1. Effects of fiber treatment and curing days on porosity
The porosity of fiber/particulate reinforced cement-paper composite depends on interfacial bonding (strength), cement hydration, and curing ages (Frias & Cabrera, Citation2000). show the porosity of samples incorporated with UPKF and TPKF cured for 28 and 49 days, respectively. With increasing fiber proportion, there was a slight and gradual increase in the value up to 2.5 wt. % as seen in ). The gradual increase can be associated with additional porosity inherent in the fibers. Fibers have inherent pores which contributed gradually to porosity. A different observation came to bear when considering values obtained for samples cured for 49 days ()), in that, with increased fiber addition, porosity almost remained constant 0.5 wt. % to 2.5 wt. % for both UPKF and TPKF addition, owing to gradual filling of pores during curing. With increased curing days, porosity trended downwards based on increased hydration reaction. Generally, the reduction experienced at 49 days when compared to what was obtained at 28 days curing age was as a result of hydrates filling up pores during reaction between cement and non-evaporated water in the course of curing (Tomasz & Tomasz, Citation2019). Therefore, the influence of fiber addition and fiber treatment in reducing porosity was not as significant as the length of curing. IS 3087 (Citation2005) gave values less than 40% for porosity of Grade 1 multilayer flat pressed boards. Therefore, samples doped with coconut/palm kernel fiber additive which were cured for 49 days have met the requirement.
Figure 3. Effects of untreated and treated fiber addition on porosity at curing days of (a) 28 days (b) 49 days with experimental trend analysis (3 c) property evaluation of experimental variables (3d) property evaluation of experimental variables
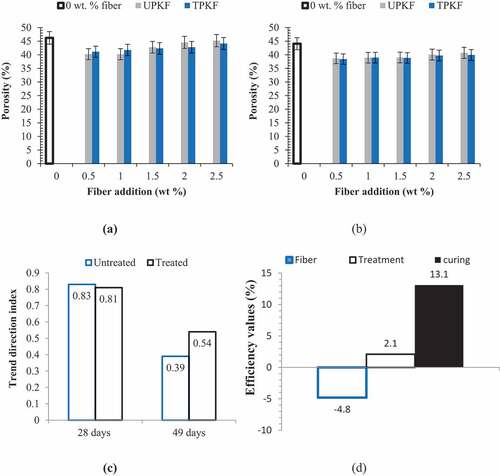
Experimental trend analysis and performance evaluation on porosity
For porosity ()), the trend direction for UPKF-28 (untreated palm kernel fiber reinforced samples cured for 28 days) reinforced samples gave a trend direction index of +0.53, implying an uptrend. Meanwhile, the trend direction index of UPKF-49 (untreated palm kernel fiber reinforced samples cured for 49 days) was +0.39 as highlighted in ), giving a resultant difference of +0.14 [72⁰ acw], this explains the reduction in porosity for samples cured for 49 days when compared with those cured for 28 days. Trend direction index for TPKF-28 days was calculated to be +0.56 and +0.40 for TPKF-49 days, a resultant difference of +0.16 [60⁰ acw]. Considering the resultant trend difference in magnitude for 28 and 49 days, the value is +0.03. The relevance of the value is that porosity eventually reduced when considering direction from 28 to 49 days. Since property value is dependent on the influence of additives (in this case treated and untreated fiber and curing length (number of days). It is expedient to evaluate how these experimental variables affect the outcome of the result. Fiber addition efficiency was 4.8% [negative] ()) indicating fiber addition was less effective in reducing porosity led to a slight increment in porosity. Alkaline treatment was 2.1% [positive] effective in reducing porosity. In contrast to that, curing duration (length) was evaluated to be 13.1% [positive] efficient in lowering the same property, attributable to more hydrates filling up pores. Thus, the inference made was that curing length is the most effective of the three experimental variables in reducing porosity.
3.1.2. Effects of fiber treatment and curing days on cold water absorption
The property can be linked to the inherent nature of paper pulp which has an affinity for water, ascribed to free cellulose OH− which is ready to adhere to another OH− bond (Hubbe et al., Citation2013; Przybysz et al., Citation2016), thus, absorbing more water. The micropores on paper pulp surface also promoted water absorption (Santamaria et al., Citation2007). shows a reducing trend in water absorption at both 28 and 49 days, for both treated and untreated.
Figure 4. Effects of untreated and treated fiber addition on water absorption at curing days of (a) 28 days and (b) 49 days with (c) experimental trend analysis and (d) property evaluation of experimental variables
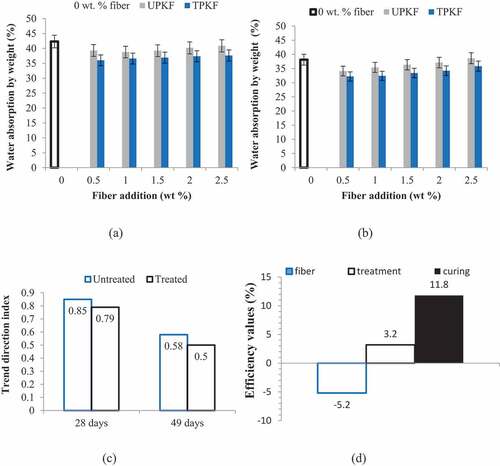
From 0.5 wt. % fiber addition up to 2.5 wt. % fiber, water absorption increased gradually when considering both untreated and treated as obtained under 28 and 49 days curing. Untreated fibers are known to be hydrophilic (Ali et al., Citation2016; Rashid et al., Citation2016), hence their addition to matrix increased water absorption tendency which explains the increase in water absorption recorded between 0.5 and 2.5% addition of UPKF under both curing ages. However, the water absorption in TPKF was lesser than that for UPKF for both curing days as a result of reduced hydrophilic nature in TPKF, which is directly linked to alkaline treatment of fiber (. Alkaline treatment (Bakri et al., Citation2016; Li et al., Citation2018) modifies the fibers based on the removal of pectin, wax, and lignin, thereby enhancing active surface area in the fiber. When comparing water absorption at 28 days and 49 days for all samples, water absorption reduced in the case of day 49 relative to day 28 which is hinged on reduced porosity associated with filling of the pores with more hydrates as curing days increased. For TPKF having a lesser value for water absorption, it can be traced to alkaline treatment which led to maximization of surface friction coefficient (Ren et al., Citation2019). These eventually resulted in enhanced chemical reactivity bringing about a strong bond during hydration reaction. The consequence of this lies in the fact that lesser pores are created based on the filling of the pores with hydrates. Nonetheless, the effect may not be significant enough owing to higher inherent pore volume associated with paper pulp as observed in this study. Sequel to this, water absorption tends to increase in TPKF, though, at a reduced rate when compared with the water absorption rate in the case of the untreated. This result recorded between 0.5 wt. % and 2.5 wt. % of UPKF and TPKF addition is in coherence with observation made in Ghanem et al. (Citation2020), where curing was observed to reduce water absorption, while fiber addition increased water absorption and contrary to Tangbo et al. (Citation2019) where water absorption increased with curing days. In line with IS 3087 (Citation2005), <20% is permissible for water absorption for flat pressed grade 1 board, adaptable wall partitioning of which no sample representing each mix proportion met the requirement. On this note, surface coatings of the boards with non-water absorbing materials like was or polymer resin is recommended in reducing water absorption.
Experimental trend analysis and performance evaluation on water absorption
) explains the trend direction index for water absorption at 28 and 49 days. Coldwater absorption reduced for 28 days for samples containing both UPKF and TPKF. The resultant trend direction index for UPKF-28 and UPKF-49 days are +0.85 and +0.58 while for treated, the values are +0.79 and +0.5, respectively. It can be deduced that the trend direction was negative to the course of this study since lower water absorption is beneficial. The trend difference index was −0.27 [57⁰ acw] for UPKF while that of TPKF was −0.29 [66⁰ cw], showing that after 49 days, water absorption reduced (or trended downwards) when compared to values obtained for samples cured for 28 days curing. Performance of fiber, alkaline treatment, and curing length on water absorption was evaluated. 5.2% [negative], 3.2% [positive] and 11.8% [positive] were recorded for fiber addition efficiency, alkaline treatment efficiency and curing length efficiency, respectively. Deduction made from this is that fiber addition resulted in further absorption of water and its 8.2% effective in doing so. Alkaline treatment was a little effective by 3.2% in reducing water absorption even as curing length was 11.8% effective in lowering water absorption ()). Reduction in water absorption, which is favorable for the material developed, was more predominant under curing age of 49 days than that of 28-day owing to C-S-H gel coat which is water impermissible, and pore reduction with increased curing age.
3.1.3. Effects of fiber treatment and curing days on moisture absorption
Moisture (water vapor) absorption from open-air is a function of capillary suction occasioned by the volume of voids on the surface of the samples. Moisture absorption was noticed to reduce from 0 wt. % of UPKF (untreated palm kernel fiber) to 0.5 wt. % of fiber by 17.6%, after which the value was increasing gradually with additional weight percent of UPKF. Paper and UPKF possess hydrophilic nature, hence increased presence of UPKF at the surface, resulting in increased moisture absorption. On the other hand, fiber treatment resulted in a reduction in water vapor absorption tendency with additional TPKF (treated palm kernel fiber) up to 2.5 wt. % ()). Under 28 days curing age, moisture absorption was noticed to decrease by 22% and 34% at 0.5 wt. % UPKF and TPKF content, respectively ()). It was further observed that moisture absorption increased marginally with further addition of UPKF, while in the case of TPKF, moisture absorption decreased marginally down the trend with a gradual rise in TPKF content.
Figure 5. Effects of untreated and treated fiber addition on moisture absorption at curing days of (a) 28 days and (b) 49 days with (c) experimental trend analysis and (d) property evaluation of experimental variables
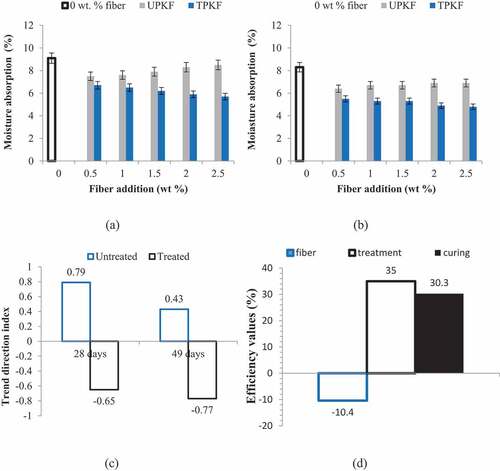
Thus, curing days and fiber treatment degrades moisture absorption tendencies owing to neutralized fiber surface and reduced void diameter (Elawady et al., Citation2014; Zhang et al., Citation2011). Moisture content <7% (IS 3478 Citation1966), is acceptable for boards; and based on that, cement-composite boards reinforced with 0.5–2.5 wt. % TPKF (cured for 28 days) and the ones doped with 0.5–2.5 wt. % UPKF and TPKF (cured for 49 days) fit in for the expected application. BS EN 300 (Citation2006) stipulated ≤12%, of which all composite samples met the requirement.
Experimental trend analysis and performance evaluation on moisture absorption
In ), the trend direction index was +0.79 and +0.43 for untreated palm kernel fiber cured for 28 days and 49 days, respectively, depicting an uptrend for each curing age. Values for treated palm kernel fiber cured for 28 days and 49 days are −0.65 and −0.77, respectively, which reveal a downtrend under the respective curing ages. The trend difference index was −0.36 [82⁰ acw] and −0.12 [152⁰ cw] for UPKF and TPKF, respectively, which confirms the reduction in amount of moisture absorption at 49 days relative to 28 days. From subsequent evaluation ()), fiber addition efficiency of 10.4% [negative] showed that fiber addition contributed to moisture absorption, at the same time, alkaline treatment efficiency of 35% [positive] implies that the treatment contributed significantly to lowering moisture absorption. Curing length efficiency of 30.3% [positive] also indicates curing of samples is effective in reducing moisture absorption. From the values, it can be deduced that alkaline treatment is more effective in reducing moisture absorption than curing, though the two can be employed simultaneously.
3.1.4. Effects of fiber treatment and curing days on bulk density
The bulk density of samples at ages of 28 and 49 days was measured and evaluated and results presented in . The incorporation of fiber resulted in a reduction in bulk density owing to the larger volume occupied by the light fibers (Ruat & Gomez, Citation2016). Bulk density was also observed to increase when curing days increased to 49 days. The reason for this is higher hydration reaction with additional curing days and enhanced bonding amounting to improved compactment (Iffat., Citation2015; Raheem et al., Citation2013).
Figure 6. Effects of untreated and treated fiber addition on bulk density at curing days of (a) 28 days and (b) 49 days with (c) experimental trend analysis and (d) property evaluation of experimental variables
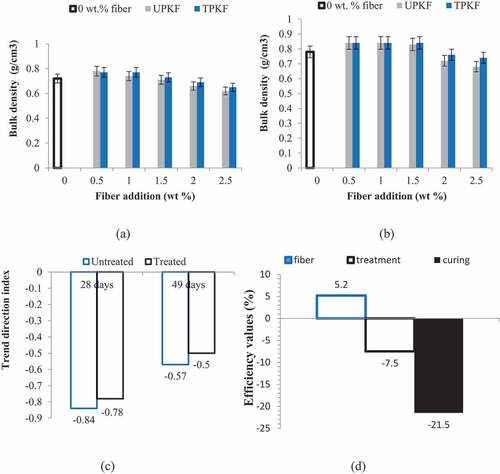
There is a slight difference in the reduction of bulk density when comparing samples containing the same proportion of UPKF and TPKF from 0.5 to 2.5 wt. % of fiber (). The outcome obtained in this work agrees with results recorded in (Balboul et al., Citation2014; Okeola et al., Citation2018) where depreciation of bulk density was noted with increased additives. ) depicts a slight percentage reduction in bulk density from 0.5 to 2.5 wt. fraction of fiber presence in the composites for both untreated and treated. However, bulk density was observed to rise when moving from 28 days to 49 days based on increased hardening as curing age increased ()). Densities of the composite developed lied between 0.5 and 1 g/cm3 and are classified as medium density boards (IS 12406 Citation2003) and still fit in for wall partitioning.
Experimental trend analysis and performance evaluation on bulk density
Critical trend analysis carried out presented direction trend index of −0.64 and −0.58 for UPKF-28 and TPKF-28 while that of UPKF-49 and TPKF-49 were −0.57 and −0.5, respectively ( affirming the downtrend with rising fiber loading. Trend difference index recorded were +0.27 [57⁰ cw] and +0.28 [64⁰ cw] for UPKF and TPKF which implies that an upward trend was experienced when considering density from 28 to 49 days. Fiber addition efficiency of 5.2% [negative] shows the performance of fiber addition is 5.2% effective in reducing the bulk density. Alkaline treatment efficiency on the other hand has a value of 7.5% [positive] and curing length efficiency is 21.5% [positive].
3.1.5. Effects of fiber treatment and curing days on Linear and volumetric expansion in water
Results for linear and volumetric expansion are represented in , respectively. Linear expansion was observed to be marginal <5% for both of the fibers at 0 to 2.5 wt. % presence (, while for volumetric, it ranged from 0.90 to 3.1% for 28 and 49 days of curing as expressed in . Shrinkage can be traced down to the fact that non-evaporated water also known as free water present in fresh samples during curing conditions undergoes hydration reaction with cement content within the structure (Yang et al., Citation2017).
Figure 7. Effects of untreated and treated fiber addition on linear shrinkage at curing days of (a) 28 days and (b) 49 days with (c) experimental trend analysis and (d) property evaluation of experimental variables
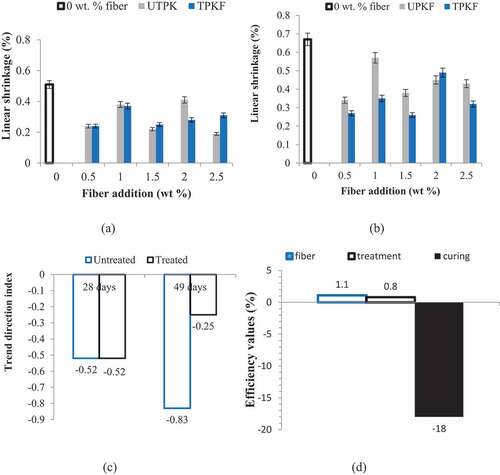
With this, pores are formed, and a way of reducing these pores and stabilizing give rise to shrinkage with curing ages even as expressed in Holt and Levis (Citation2004), Bentz and Jensen (Citation2004), and Hussein et al. (Citation2015). Proper curing method and prolonged curing ages ensures effective hydration in cement-paper matrix (Siddiqui et al., Citation2013). The values obtained for linear and volumetric shrinkage; shrinkage increased with curing days while alkaline treatment had a slight effect on shrinkage. There is no standard stipulated for linear and volumetric shrinkage for application for wall partitioning, that notwithstanding, shrinkage should be reduced to the barest minimum for dimensional stability.
Experimental trend analysis and performance evaluation on linear shrinkage
Performance of experimental variables showed resultant trend direction index of −0.52 and −0.52 for UPKF-28 and TPKF-28 as observed in ). Also, the resultant trend direction index for UPKF-49 was −0.83 and for TPKF-49, it is −0.25. The result of experimental trend analysis conducted on linear shrinkage revealed a trend difference index −0.31 [107 ⁰ acw] for UPKF and +0.27 [93 ⁰ cw] for TPKF. Performance evaluation carried out on experimental variables (which determines the outcome of result) for each property revealed marginal efficiency for fiber, alkaline treatment, and curing length, was 1.1% [positive], 0.8% [positive], and 18% [negative]. These can be interpreted as follows; fiber addition and alkaline treatment had little or no effect on linear shrinkage while curing length/duration was 18% efficient in increasing linear shrinkage. The (negative) for curing length depicts the fact that the increase in shrinkage was not favorable to the purpose of this study, in the sense that lower linear shrinkage indicates dimensional stability needed for optimal performance in service.
Experimental trend analysis and performance evaluation on volumetric shrinkage
A similar occurrence was obtained for volumetric shrinkage as seen in ); trend direction index of +0.26 and +0.16 for UPKF-28 and TPKF-28 while for UPKF and TPKF, the value was +0.35 and +0.43, respectively. The trend difference index was +0.09 [4⁰ acw] for UPKF and +0.27 (108⁰ acw) for TPKF. Marginal efficiency for fiber, alkaline and curing duration was 0% [neutral], 0.5% [positive] and 10.8% [negative] (). Interpreting this, fiber and alkaline treatment did not affect volumetric shrinkage while curing length was 10.8% effective in increasing volumetric shrinkage. Likewise, as reported for linear shrinkage, the (negative) for curing length depicts the fact that an increase in shrinkage was detrimental to the purpose of this study since lower volumetric shrinkage indicates higher dimensional stability, needed for optimal performance in service.
3.2. Analysis of mechanical properties
3.2.1. Effects of fiber treatment and curing days on tensile strength
Results of tensile strength are as shown in from where it can be deduced that there was a slight increase in the strength from 0 to 2 wt. % of fiber, followed by a decrease in strength at 2.5 wt. % addition for UPKF-28. The rise in strength from 0 to 2 wt. % UPKF can be linked to a strong bond within the matrix while the fall in value at 2.5 wt. % UPKF loading is based on fiber entanglement. As for UPKF-49, there was a progressive increment in strength from 0.5 wt. % to 2 wt. % before experiencing reduction in strength at 2.5 wt % incorporation based on the fiber entanglement. Samples containing TPKF exhibited a rise in tensile strength up to 2.5 wt. %, a point where maximum value was noted attributable to improved interfacial adhesion between fiber and matrix, relative to 0 wt. % for both 28 and 49 curing ages. Tensile strength was observed to reduce when comparing values attained at 49 curing age with their counterparts at 28 curing age owing to increased hardened matrix at curing age 49, which reduced flexibility and stretching of the fibers though slightly contrary observation was made in Amuthakkannan et al. (Citation2013). In general fiber, inclusion enhances tensile strength (Hasan et al., Citation2016). As par IS 3087 (Citation2005), ≥0.8 MPa is acceptable for particle board of which composites samples containing 2.5 wt. % UPKF (cured for 28 days) and 2 and 2.5 wt. % TPKF (cured for 49 days) met the requirement.
Experimental trend analysis and performance evaluation on tensile strength
) explains the trend direction index for tensile strength at 28 and 49 days. Tensile strength increased for 28 days for samples containing both UPKF (untreated fiber palm kernel fiber) and TPKF (treated fiber palm kernel fiber). Trend direction index for UPKF-28 (UPKF cured for 28 days) and UPKF-49 (UPKF cured for 49 days) are +0.52 and +0.33 implying an uptrend in values while for TPKF-28 and TPKF-49, the values are +0.44 and +0.31, respectively, which also indicate an uptrend. Trend difference index was −0.19 [253⁰ acw, 2 cycles) for UPKF while that of TPKF was −0.13 [223⁰ acw]; which depicts the fact that there was value reduction comparing tensile strength at 49 days relative to 28-day curing. Performance of fiber, alkaline treatment, and curing length (days) were accessed. ) shows that values of 7% [positive], 5.4% [positive] and 7.8 % [negative] were obtained for fiber addition efficiency, alkaline treatment efficiency and curing length (duration) efficiency serially. Fiber addition and alkaline treatment enhanced tensile strength. Meanwhile, curing duration was less effective based on the reduction in strength observed under 49 days. It is therefore inferred that fiber addition, alkaline treatment improved tensile strength of paper-cement composites, while longer curing days may lead to lowering of tensile strength.
3.2.2. Effects of fiber treatment and curing days on impact strength
The result of the impact test carried out on materials for samples reinforced with UPKF and TPKF shows a progressive rise from 0 wt. % to 2.5 wt. % fiber inclusions (). The strong bond and enhanced interfacial strength amounted to strong resistance to fracture by impact. Impact energy per unit area recorded for UPKF and TPKF was 3.05 and 3.4 J/m2 for samples cured for 28 days, a difference of 11% for samples containing 2.5 wt. % fibers, while impact energy per unit area recorded for UPKF and TPKF cured for 49 days are 3.75 and 4.12 J/m2 a difference of 12%.
Figure 10. Effects of untreated and treated fiber addition on impact strength at curing days of (a) 28 days and (b) 49 days with (c) experimental trend analysis and (d) property evaluation of experimental variables
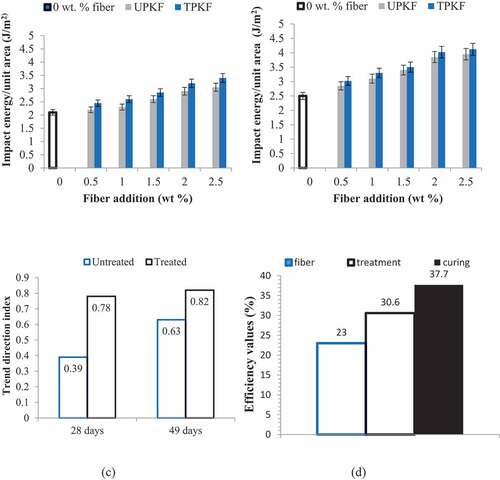
This feat is traceable to enhanced interfacial adhesion between fiber and matrix and crosslink between the fibers and inherent fiber of paper pulp promoting crack arresting abilities of the fibers. The observation made in , confirms the postulation of Zhang et al. (Citation2007); increase in impact strength with the inclusion of fiber. Increased strength with fiber loading is attributable to stress distribution within the matrix by the fiber presence. No standard value was stipulated for impact strength for wall partitions, but the property remains important for resistance to impact, hence high impact strength to weight/specific gravity ratio is expedient.
Experimental trend analysis and performance evaluation on impact resistance
Analysis for resultant trend direction index reported values of +0.39 and +0.68 for UPKF and TPFK reinforced samples cured for 28 days ()), and values of +0.63 and +0.82 for resultant trend direction factor for UPKF and TPFK reinforced samples cured for 49 days. This validates the fact that the resultant direction for measure of impact strength, trends upward for both curing days. Furthermore, the difference between the values (+0.25 for UPKF and +0.14), further confirms that fiber addition aided enhancement of the properties under increased bond strength between fiber and matrix, which was further enhanced by fiber treatment. Experimental variables performance represented in ) revealed fiber addition was identified to be 23% [positive] effective in improving impact strength while alkaline treatment and curing duration were 30.6% [positive] and 37.7% [positive] effective in enhancing impact strength accordingly. It’s reasonable to pinpoint the fact that employment of the alkaline-treated fiber and curing length would give higher resultant improvement in impact strength
3.2.3. Effects of fiber treatment and curing days on abrasion resistance
In ), abrasion resistance was observed to improve as fiber amount content increased due to strong interfacial bonding. TPKF, posed reduced values when compared with UPKF counterparts. Fiber treatment was effective in improving fiber wetting with the matrix as a result of higher surface charge and freeness. Results obtained under 49 days ()), revealed that curing was higher relative to results obtained under 28 days, implying that, higher curing ages increased abrasion resistance, which is as a result of tricalcium silicate and calcium silicate hydrates formed during curing. Going by ASTM C1186-08 (2012), composites sample cured for 49 days and doped with 0.5 to 1.5 wt. % of the fiber met the existing standard.
Experimental trend analysis and performance evaluation on abrasion resistance
The resultant trend direction index of 0 was obtained for UPKF (), and +0.38 for TPKF under curing age of 28 days showing that the trend of abrasion resistance for TPKF increased from UPKF by a resultant trend difference of +0.38 when fibers were treated. The resultant trend direction factor under 49 days curing was +0.86 and +0.94, a difference value of +0.08. This articulates the fact that there was an uptrend in abrasion resistance as a result of fiber treatment. Analysis of performance represented in ) revealed that fiber addition efficiency is 10.8% [positive], while that of alkaline treatment is 24.5% [positive]. Curing efficiency is 33.7% [positive], and this implies curing is effective in improving abrasion resistance.
3.2.4. Effects of fiber treatment and curing days on bursting strength
The presence of fibers promoted interfacial bonding and led to improvement in the bursting strength of samples produced. With an increasing proportion of fiber, bursting strength increased under 49 days. This is due to strong hydrates formed during curing. Furthermore, fiber treatment was found to be effective based on increased TPKF samples relative to values obtained from UPKF samples. A sharp rise was observed from 1.5 wt. % addition in the case of treated fiber which can be attributed to increased fiber to pore volume at that point (). Higher bursting strength is beneficial to wall partitions particleboards; hence maximization is the goal.
Experimental trend analysis and performance evaluation on bursting strength
Analysis of resultant trend index () depicts value for UPKF-28 and TPKF-28 as +0.17 and +0.47, respectively. Under 49 days, the trend index obtained for the UPKF trend was +0.4 while that of TPKF trend was +0.51. Trend difference of +0.23 [243⁰ cw] for UPKF and +0.04 [15⁰ cw] for TPKF, demonstrates a continuous positive trend from 28 to 49 days of curing. Analysis of performance of experimental variables indicates that resultant fiber addition efficiency was 10.6% [positive]. Alkaline treatment efficiency was obtained to be +10.4% [positive] efficient (0–49 days) and marginal curing efficiency was 10.6% [positive].
3.3. Microstructural analysis
shows the microstructural image for samples containing 0 to 2.5 wt. % TPKF. It is evident in the presence of pores, capillary pores, which explain the high rate of water absorption observed in samples with 0 wt. % fiber. Also, ), revealed that the paper pulp matrix has inherent fibers as highlighted. The addition of fiber and coconut shell particulate increased the mechanical properties of the matrix with good interfacial adhesion between the matrix and fiber as observed in .
Figure 13. SEM images of samples containing varying amounts of treated fiber (0, 0.5, 1.0, 1.5, 2.0, and 2.5 wt. %) represented in a, b, c, d, e, and f, respectively
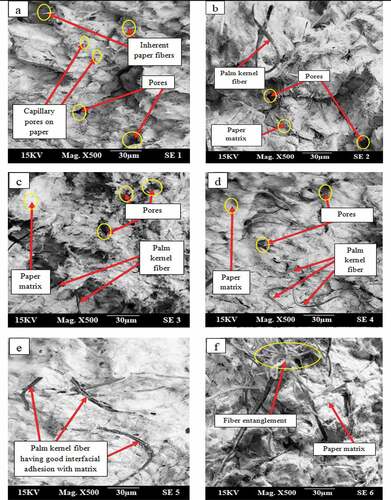
The treatment of the fibers highlights the interfacial adhesion shown in the SEM images of the composite, which resulted in improved properties compared to their untreated counterpart. shows the presence of a fiber entanglement as a result of the clustering of fibers. The consequence of this was noticed in slightly reduced tensile strength under 14 days curing age. The addition of treated fibers gave higher performance as a result of enhanced interfacial adhesion to the matrix as revealed in .
3.4. Comparison of UPKF and TPKF using property ratio (sum)
Further evaluation and analysis were made to compare the performance of UPKF and TPKF samples as evaluated in the study of Akinwande (Citation2020). The property ratio was evaluated for each sample as indicated in . Equation (9) was utilized for properties whose increasing value is favorable for the material developed and 10 for properties whose decreasing value is favorable for the same. The property ratios were summed up (Equation 11) for each mix proportion and the result presented in
Table 4. Effective property index (EPI) for each mix proportion
From , it can be noted that EPI increased with fiber addition from 0 to 2.5 wt. %. This implies that with increasing fiber content, the overall property of samples was enhanced. The Difference in EPI observed between TPKF and UPKF, gave positive (+) values indicating that overall property was better enhanced with alkaline treatment. On average, for the entire study, UPKF has an average EPI of 1.32, while TPKF had an average of 1.49. This shows that alkaline treatment is improved the overall properties of samples by 12.9%.
4. Conclusions
In the process of developing a cheaper alternative for wall partitioning, untreated and alkaline-treated palm kernel fiber were employed in reinforcing paper-cement composites and the following observations are arrived at;
porosity increased slightly with increasing fiber loading under 28 days curing while under 49 days, porosity remained almost constant. Bulk density was observed to reduce with fiber loading. Effect of curing on porosity was revealed with lower porosity for 49 days relative to 28 days, however in the case of bulk density, increased curing day evoked appreciation in bulk density.
inclusion of the UPKF and TPKF resulted in a rise in water absorption but water absorption was lesser for TPKF reinforced composites. 49-day water absorption was lower than 28-day water absorption for all samples associated with a longer curing length.
increasing UPKF loading resulted in rising moisture absorption while in the case of TPKF, increasing proportion amounted to progressive reduction in moisture absorption.
UPKF and TPKF had a marginal effect on linear and volumetric shrinkage while curing duration increased shrinkage.
Fiber inclusion enhanced resistance to abrasion and tensile, impact, and bursting strength with TPKF outperforming UPKF.
Microstructural analysis showed that alkaline treatment of fiber-enhanced interfacial adhesion is responsible for enhanced performance of in TPKF reinforced samples compared to the UPKF samples.
Alkaline treatment of fiber was noted to be 12.9% in improving overall properties of samples compared with the untreated counterparts while curing was most effective in property enhancement.
It can therefore be concluded that alkaline modification of palm kernel fiber and lengthened hydration period are effective in developing paper-cement composites for wall partitioning.
Acknowledgements
The authors appreciate the funding support for the APC from Landmark University, Omu-Aran, Kwara State, Nigeria through SDG 17 Research Group (Partnership to Achieve the Goals)
Additional information
Funding
Notes on contributors

Adeolu Adesoji Adediran
Adeolu Adesoji Adediran (Ph.D.) is a Lecturer in the Department of Mechanical Engineering, Landmark University, Omu-Aran, Kwara State, Nigeria. He is a registered Engineer with the Council for the Regulation of Engineering in Nigeria (COREN) and a member of several professional bodies. His research interest is in Advanced Materials, Physical Metallurgy, Mechanical Behavior of Materials, Composite Materials, Fracture Mechanics, and Failure Analysis. He has supervised several undergraduate and post-graduate students. He has published both in local and international journals. He is currently the Coordinator, Landmark International Office, and Linkages.
References
- Ahmad, H., & Md.:, N. N. (2008). Mix design of palm oil fiber concrete. Conf. Proceedings: Int. Conf. on Civil Engineering. Pahang, Malaysia.
- Akindapo, J. O., Orueri, D. U., Garba, D. K., & Ogabi, R. (2017). Production of a safety helmet using palm kernel fiber and shell particulates. International Journal of Science and Engineering Invention, 6(2), 44–25.
- Akinwande, A. A. (2020). Evaluation of the property values of coir-fiber reinforced cement stabilized bricks applying experimental trend/performance analysis (Akinwande’s approach). International Journal of Advanced Academic Research, 6(9), 90–118. https://doi.org/10.46654/ij.24889849
- Ali, A., Shaker, K., Nawab, Y., Jabbar, M., Hussain, T., Militky, J., & Baheti, V. (2016). hydrophobic treatment of natural fibers and their composites-A review. Journal of Industrial Textiles, 47(8), 1–47. https://doi.org/10.1177/1528083716654468
- Amiandamhen, S. O., & Osadolor, S. O. (2020). Recycled waste paper-cement composite panels reinforced with kenaf fibers: Durability and mechanical properties. Journal of Material Cycles and Waste Management, 22(5), 1492–1500. https://doi.org/10.1007/s10163-020-01041-2
- Amuthakkannan, P., Manikandan, V., Winowlin Jappes, J. T., & Uthayakumar, M. (2013). Effect of fiber length and fiber content on mechanical properties of short basalt fiber reinforced polymer matrix composites. Materials Physics and Mechanics, 16, 107–117.
- Animesh, K., Tiwari, J., & Soni, K. (2017). A review of partial replacement of fine aggregate and coarse aggregate by waste glass powder and coconut shell. International Journal of Engineering Research & Technology, 4(10), 187–190.
- ASTM 293/C293M. (2016). Standard test method for flexural strength of concrete (using simple beam with center-point loading). ASTM International.
- ASTM C 596-18. (2018). Standard test method for drying shrinkage of mortars containing hydraulic cement. ASTM International.
- ASTM C150/C150M-20. (2020). Standard specification for portland cement mortar. ASTM International.
- ASTM C1585-13. (2013). Standard test method for measurement of rate of absorption of water by hydraulic-cement concrete. ASTM International.
- ASTM C192/C192M-19. (2019). Standard practice for making and curing concrete test specimen in the laboratory. ASTM International.
- ASTM C496-17. (2017). Standard test method for splitting tensile of cylindrical concrete specimen. ASTM International.
- ASTM D256-10. (2018). Standard test method for determining izod pendulum impact resistance of plastics. ASTM International.
- ASTM D6913/D6913M-17. (2017). Standard test method for particle-size distribution (gradation) of soils using sieve analysis. ASTM International.
- Bakri, M. K., Jayamani, E., Hamdan, S., Rahman, M., Soon, K., & Kakar, A. (2016). Fundamental study on the effect of alkaline treatment on natural fibers structures and behaviors. Journal of Engineering and Applied Sciences, 11, 8759–8763.
- Balboul, N., Jaber, M., & Fadhel, A. (2014). Mechanical and physical properties of natural fiber cement board for building partitions. Physical Sciences Research International, 2(3), 49–53.
- Bentz, D. P., & Jensen, D. M. (2004). Mitigation strategies for autogenously cracking. Cement and Concrete Composites, 26(6), 677–685. https://doi.org/10.1016/S0958-9465(03)00045-3
- BS 1881-122:2011. (2011). Testing concrete. Method for determination of water absorption. British Standard Group.
- BS 3137. (1972). Methods for determining the bursting strength of paper. British Standard Group.
- BS EN 300. (2006). Oriented strand boards. Definition, classification and specifications (pp. 2006). British Standard (European Norm.
- Bunda, J. C., Diloy, J. C. D., Gatbunton, T. L., Tabigne, J. R. D., & Abaya, S. D. (2020). Utilization of rice straws as fiber reinforcement in rice husk ash cement bonded board. International Journal of Civil and Structural Engineering, 8(1), 94–104.
- Dorieh, A., Mahmoodi, N. O., Mamaghani, M., & Pizzi, A. P. (2018). Comparison of the properties of urea-formaldehyde resins by the use of formalin or urea formaldehyde condensates. Journal of Adhesion Science and Technology, 32(23), 2537–2551. https://doi.org/10.1080/01694243.2018.1492780
- Ejiogu, I. K., Odiji, M. O., Ayejagbara, M. O., Shekarri, T. N. B., & Ibeneme, U. (2018). Mechanical Properties of Urea Formaldehyde Particle Board Composite. American Journal of Chemical and Biochemical Engineering, 2(1), 10–15. https://doi.org/10.11648/j.ajcbe.20180201.12
- Elawady, E., El Hefnawy, A. A. E., & Ibrahim, R. A. F. (2014). Comparative study on strength, permeability and sorptivity of concrete and their relation with concrete durability. International Journal of Engineering and Innovative Technology, 4(4), 132–139.
- Ezeudu, O. B., Agunwamba, J. C., Ezeasor, I. C., & Madu, C. N. (2018). Sustainable production and consumption of paper and paper products in Nigeria: A review. Resources, 8(53), 1–23. https://doi.org/10.3390/resources80110053
- Frias, M., & Cabrera, J. (2000). Pore size distribution and degree of hydration of metakaolin-cement pastes. Cement and Concrete Research, 30(4), 561–569. https://doi.org/10.1016/S0008-8846(00)00203-9
- Ghanem, H., Machaka, M., Khatib, J., Elkordi, A., & Baalbaki, O. (2020). Effect of palm fibers addition on absorption characteristic and mechanical properties of concrete. 5th International Conference on Sustainable Construction Materials and Technologies. https://doi.org/10.18552/2019/IDSCMT5098.
- Guller, C., & Buyuksari, U. (2011). Effect of production parameters on the physical and mechanical properties of particleboards made from peanut (Arachis Hypogaea L.) hull. Bioresources, 6(4), 5027–5036. https://doi.org/10.15376/biores.6.4.5027-5036
- Hasan, H., Alhussainy, F., Sheikh, M., & Hadi, M. (2016). Direct tensile test of high strength concrete with and without steel fibers. Proceedings in Australian Conference on the Mechanics of Structures and Materials (ACMSM24), Perth Australia.
- Holt, E., & Levis, M. (2004). Cracking risks associated with early age shrinkage. Cement and Concrete Composites, 26(5), 521–530. https://doi.org/10.1016/S0958-9465(03)00068-4
- Hubbe, M., Ayoub, A., Daystar, J. S., Venditti, R. A., & Pawlak, J. J. (2013). Enhanced absorbent products incorporating cellulose and its derivatives: A review. BioResources, 8(4), 6556–6629. https://doi.org/10.15376/biores.8.4.6556-6629
- Hussein, A. A., Abd El-Hameed, G. D., Hadhood, H. M., & El-Attar, A. G. (2015). Properties of normal and high strength fiber reinforced concrete using recycled aggregate and different fibers. World Applied Sciences Journal, 33(11), 1676–1685. https://doi.org/10.5829/idosi.wasj.2015.33.11.15620
- Iffat., S. (2015). Relation between density and compressive strength of hardened concrete. Concrete Research Letters, 6(4), 182–189.
- IS 12406. (2003). Medium density fiber boards for general purpose- specifications (wood and other lignocellulose products). Bureau of Indian Standards.
- IS 2380. (1977). Methods of test for wood particle boards and boards from lignocellulose materials. Bureau of Indian Standards.
- IS 2386-3. (1963). ordinary Portland cement 43 grade specification. Bureau of Indian Standards.
- IS 3087. (2005). Practical boards of wood of wood and other lignocellulose materials (medium density) for general purposes. Specifications. Bureau of Indian Standards.
- IS 3478. (1966). Specification for high-density wood particle boards (wood and other lignocellulose products). Bureau of Indian Standards.
- IS 8112. (2013). Ordinary Portland cement 43 grade specification. Bureau of Indian Standards.
- Ji, Y., Peng, Y., Strand, A., Fu, S., Sundberg, A., & Retulainen, E. (2018). Fiber evolution during alkaline treatment and its impact on handsheet properties. Bioresources, 13(4), 7310–7324. https://doi.org/10.15376/biores.13.4.7310-7324
- Johnson, M. P. (2016). An overview of photosynthesis. Essays in Biochemistry, 60(3), 255–273. https://doi.org/10.1042/EBC20160016
- Kavitha, S. (2017). A review on natural fibers in the concrete. International Journal of Advanced Engineering and Technology, 1(1), 32–35.
- Lavanya, D., Kulkarni, P., Dixit, M., Raavi, P. K., & Krishna, L. N. V. (2011). Sources of cellulose and their applications-A review. International Journal of Drug Formulation and Research, 2, 19–38.
- Li, J., Yang, Z., Hu, X., Hong, G., Zhang, S., & Song, W. (2018). The effect of alkali treatment on properties of dopamine modification of bamboo fiber/polylactic acid composites. Polymers (Basel), 10(4), 403. https://dx.doi.org/10.3390/polym10040403
- Mazzanti, V., Bonanno, A., Mollica, F., & Filippone, G. (1981). Influence of alkaline treatment on hemp fibers filled poly (lactic acid). AIP Conference Proceedings, 20016. 2018. https://doi.org/10.1063/11.5045878.
- Mendes, R., Mendes, L., Olibeira, S., & Freire, T. (2015). Use of sugarcane bagasse for particleboard production. Key Engineering Materials, 634, 163–171. https://doi.org/10.4028/www.scientific.net/KEM.634.163
- Mohammed, L., Ansari, M. N. M., Pua, G., Jawaid, M., & Islam, M. S. (2015). A review on natural fiber reinforced polymer composite and its applications. International Journal of Polymer Science, 2015, 15. Article ID 243947. https://doi.org/10.1155/2015/243947.
- Momoh, E. O., & Osofer, A. I. (2020). Recent developments in the application of oil palm fibers in cement composites. Frontiers of Structural and Civil Engineering, 14(1), 94–108. https://doi.org/10.1007/s11709-019-0576-9
- Nyang, G. M., Muumbo, A. M., & Ondieki, C. M. M. (2019). Production of particle boards from sugarcane bagasse and euphorbia sap. International Journal of Composite Materials, 9(1), 1–6. https://doi.org/10.5923/j.cmaterials.20190901.01
- Obiukwu, O., Opara, I., & Udeani, H. (2016). Study on the mechanical properties of palm kernel fiber reinforced epoxy and Poly-Vinyl Alcohol (PVA) composite material. International Journal of Engineering and Technologies, 7, 68–77. https://doi.org/10.18052/www.scipress.com/IJET.7.68
- Okeola, A. A., Abuodha, S. O., & Mwero, J. (2018). Experimental investigation of the physical and mechanical properties of sisal fiber-reinforced concrete. Recent Advancements in Fiber Reinforced Concrete and Its Application, 6(3), 1–16. https://doi.org/10.3390/fib6030053
- Oladele, I., Oghie, I. I., Adediran, A., Akinwekomi, A., Adetula, Y., & Olayanju, T. (2019). Modified palm kernel shell fiber/particulate cassava peel hybrid reinforced epoxy composites. Results in Materials, 5, 100053. https://doi.org/10.1016/j.rinma.2019.100053
- Przybysz, P., Dubowik, M., Kucner, M. A., Przybysz, K., & Przybysz, K. B. (2016). Contribution of hydrogen bonds to paper strength properties. Plos One, 11(5), 1–10. https://doi.org/10.1371/journal.pone.0155809
- Raheem, A. A., Soyingbe, A. A., & Emenike, J. A. (2013). Effects of curing methods on density and compressive strength of concrete. International Journal of Applied Science and Technology, 3(4), 55–64.
- Rashid, M., Samad, S. A., Gafur, M. A., Qadir, R., & Chowdhury, A. M. S. (2016). Effect of reinforcement of hydrophobic grade banana (Musa ornata) bark fiber on the physicomechanical properties of isotactic polypropylene. International Journal of Polymer Science, 2016, 1–9. Article ID 9017956. https://doi.org/10.1155/2016/9017956
- Ren, Z., Wang, C., Zou, Q., Yousfani, S. H. S., Anuar, N. I. S., Zakaria, S., & Liu, X. (2019). Effect of alkali treatment on interfacial and mechanical properties of kenaf fiber reinforced epoxy unidirectional composites. Sains Malaysiana, 48(1), 173–181. https://dx.doi.org/10.17576/jsm-2019-4801-20
- Rivela, B., Hospido, A., Moreira, M. T., & Feijoo, G. (2006). Life cycle inventory of particleboard: A case study in the wood Sector. The International Journal of Life Cycle Assessment, 11(2), 106–113. https://doi.org/10.1065/Ica2005.05.206
- Ruat, A. N., & Gomez, C. P. (2016). Thermal and mechanical performance of oil palm fiber reinforced mortar utilizing palm oil fly ash as a complementary binder. Construction and Building Materials, 126, 476–483. https://dx.doi.org/10.1016/j.conbuildmat.2016.09.034
- Sanjay, M. R., Arpitha, G. R., Naik, L. L., Gopalakrishna, K., & Yogesha, B. (2016). Applications of natural fibers and its composites: An overview. Natural Resources, 7(3), 108–114. https://doi.org/10.4236/nr.2016.73011
- Santamaria, J., Fuller, B., & Fafitis, A. (2007). Structural properties of a new material made of waste paper. Computational Methods and Experimental Measurements XIII, 46, 1–11. https://doi.org/10.2495/cmem070561
- Siddiqui, M. D., Nyberg, W., Smith, W., Blackwell, B., & Riding, K. (2013). Effect of curing water availability and composition on cement hydration. ACI Materials Journal, 110, 315–322.
- Stern, D., & Kaufmann, R. (2014). Anthropogenic and natural causes of climate change. Climatic Change, 122(1–2), 1–2. https://doi.org/10.1007/s10584-013-1007x
- Tan, M. Y., Kuan, H. T. N., & Lee, M. C. 2017. Characterization of alkaline treatment and fiber content on the physical, thermal and mechanical properties of ground coffee waste/oxo-biodegradable HDPE biocomposites. International Journal of Polymer Science, 12. Article ID 6258151. https://doi.org/10.1155/2017/6258151.
- Tangbo, M. U., Gado, A. A., & Ibrahim, M. (2019). Determining properties of a lightweight papercrete containing paper sludge, pumice, cementitious material and pumice aggregate for sustainable construction. Environmental Technology and Science Journal, 10(1), 114–125.
- Tomas, U., & Ganiron, Jr. (2013). Sustainable management of waste coconut shells as aggregates in concrete mixture. Journal of Engineering Science and Technology Review, 6(5), 7–14. https://doi.org/10.25103/jestr.065.02
- Tomasz, T., & Tomasz, Z. (2019). Effect of hydration and carbonation progress on the porosity and permeability of cement pastes. Materials, 12, 192, 1–20. https://doi.org/10.3390/ma12010192
- Wimmer, R., Weigl, M., & Schoneberg, S. (2011. Particleboards made from hardwoods-what is the significance. Conference Proceeding: International Scientific Conference on Hardwood Processing, Blacksburg Virginia.
- Xian, D.: Effect of nanoclay fillers on wood adhesives and particle board properties [MSc. Thesis]. University of British Columbia 2012.
- Yang, J., Wang, Q., & Zhou, Y. (2017). Influence of curing time on the drying shrinkage of concrete with different binders and water-to-binder ratios. Advances in Materials Science and Engineering, 2017, 1–10. Article ID 2695435. https://doi.org/10.1155/2017/2695435
- Zhang, M. H., Sharif, M. S. H., & Lu, G. (2007). Impact resistance of high strength fiber reinforced concrete. Magazine of Concrete Research, 59(3), 199–210. https://doi.org/10.1680/macr.2007.59.3.199
- Zhang, P., Wittmann, F. H., & Zhao, T. J. (2011). Quantitative determination of capillary absorption of concret. Basic Research on Concrete and Applications. Proceedings. ASME Int. Workshop, (pp. 9–20).
- Zheng, Y., Pan, Z., Zhang, R., Jenkins, B. M., & Blunk, S. (2007). Particleboard quality characteristics of saline jose tall wheatgrass and chemical treatment effect. Bioresources Technology, 98(6), 1304–1310. https://doi.org/10.1016/j.biortech.2006.04.036