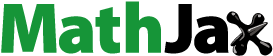
Abstract
This paper presents the results of an experimental study of the fatigue and fracture behavior of Bambusa Vulgaris-Schrad bamboo. Mechanisms of crack initiation and growth are elucidated under monotonic and cyclic compressive failure or flexural loading. The microscopic studies of fatigue and fracture explore the effects of fiber/crack/ply orientation on crack growth and toughening mechanisms in single-edge notched and double -edge notched fracture mechanics bend specimens, which are studied in the “crack-arrestor” and “crack-divider” orientations. The compressive fatigue behavior of Bambusa Vulgaris-Schrad bamboo is also investigated in smooth un-notched specimens. The resulting stress-life behavior is shown to occur in a regime in which the maximum stresses exceed the critical conditions for the onset of progressive fiber buckling and shear band formation. This results ultimately in the nucleation and propagation of interlaminar cracks and shear cracks across the Bambusa Vulgaris-Schrad structures. The implications of the results are discussed for the design of robust bamboo structures.
PUBLIC INTEREST STATEMENT
Bamboo composites have found applications in bionic structures, tall sky scrapper buildings, aerospace structures, and automotive components due to their eco-friendly nature and excellent combinations of strength and stiffness to weight ratios. However, the understanding of fatigue behavior of these structures is essential to avoid failure during service conditions. This paper presents the results of failure of Bambusa Vulgaris-Schrad bamboo under monotonic and cyclic loading. The failure mechanisms of the smooth bamboo samples were first studied under compressive monotonic and cyclic loading before elucidating their cracking phenomena under bending for crack divider and crack arrestor orientations. Crack growth resistance curve were then obtained to provide insights into the toughening mechanisms and toughness of the bamboo. Finally, specimens in both crack orientations were subjected to cyclic loading under bending to study their failure mechanisms. The results are then discussed for the design of robust bamboo structures.
1. Introduction
Bamboos are giant grasses that belong to the family Poaceae and subfamily Bambusoidae (Sangeetha et al., Citation2015; Yeasmin and Gantait, Citation2015). They have been used increasingly in construction due to their: availability in most parts of the world, fast growth rates, fabricability, and excellent balance of strength/stiffness to weight ratios (Busari et al., Citation2015; Chen et al., Citation2018). Bamboos are also easily processed into eco-friendly building materials for the fabrication of flooring, ceiling, walls, windows, doors, fences, housing roofs, trusses, rafters and purlins, structural construction materials for bridges, water transportation facilities and scaffoldings (Busari et al., Citation2015).
Bamboo is a natural composite (Chen et al., Citation2018; Low et al., Citation2015; Van Der & Van Den Dobbelsteen, Citation2006) that consists of cellulose/hemicellulose fibers in a matrix of lignin. Its eco-friendly nature and excellent combinations of strength and stiffness to weight ratios have also enabled bamboo to find increasing applications in high-performance structures. These include bionic structures; tall sky scrapper buildings, aerospace structures, and automotive components (Abdul Khalil et al., Citation2012).
Bambusa Vulgaris-Schrad bamboo can be used for several applications. These include: the production of bamboo boards (Ogunsanwo et al. Citation2015); construction of residential houses and bridges; an alternative raw material for pulp and paper production (Eromosele & Olorunfemi, Citation2019), and suitable raw material for the manufacturing of furniture (Adewole and Bello Citation2013).
Since the robustness of the above structures requires an understanding of the possible fatigue and fracture mechanisms, there have been significant efforts to study the fatigue and fracture behavior of bamboo (Amada & Untao, Citation2001; Chen et al., Citation2018; Song et al., Citation2017). The initial work (Tan et al., Citation2011) has provided new insights into the underlying crack/microstructural interactions that give rise to crack-tip shielding by crack bridging in moso culm bamboo structures. Functionally graded configurations of fibers were also found to occur in moso culm bamboo, with the highest fiber densities occurring in the outer plies, where the stresses experienced by the bamboo “cantilevers” were highest.
Amada and Untao, (Amada & Untao, Citation2001) have studied the dependence of the fracture toughness of bamboo on the fiber volume fractions. Low et al. (Low et al., Citation2015), as well as Amada and Untao (Amada & Untao, Citation2001), have also investigated the fracture toughening mechanisms that occur in Mousou bamboo (Phyllostachys edulis Riv.). They have shown that toughening in bamboo is lower in regions of higher fiber density and higher in regions of lower fiber density (Amada & Untao, Citation2001; Mannan et al., Citation2018; Tan et al., Citation2011).
Song et al., (Song et al., Citation2017) have studied the fatigue behavior of bamboo strips subjected to three-point flexural cyclic loading, while Keogh et al. (Keogh et al., Citation2015) have investigated the fatigue behavior of bamboo, with a focus on determining the number of cycles to failure for a range of applied cyclic loading conditions. They showed that bamboo culm samples displayed fatigue failure when loaded in compression along its diameter (Song et al., Citation2017), whiles no evidence of fatigue failure was observed when the samples were loaded in compression in the axial direction (Keogh et al., Citation2015).
Prior work (Banga et al., Citation2015; Taylor, Citation2018; Zou et al., Citation2019) have also explored the role of porosity in the fatigue and fracture of bamboo, while Tan et al. (Tan et al., Citation2011) have conducted extensive analytical, computational, and experimental studies of the structure and mechanical properties of bamboo. The latter includes work by Askarinejad et al. (Askarinejad et al., Citation2016), who studied the basic deformation and toughening mechanisms associated with the mixed-mode fracture of moso culm bamboo, and the deformation and fracture behavior of bamboo fiber at the nanoscale (Youssefian et al., Citation2017; Youssefian & Rahbar, Citation2015).
Although the above studies (Askarinejad et al., Citation2016; Onche et al., Citation2020; Tan et al., Citation2011; Taylor, Citation2018) have provided much needed fundamental insights, our basic understanding of the mechanisms of deformation and cracking are still limited under monotonic and cyclic loading conditions. This is particularly true for failure under cyclic loading conditions that are responsible for a significant fraction (about 90%) of failures in engineering components/structures in service (Soboyejo, Citation2002).
In this study, we present the results of an experimental study of the fatigue and fracture behavior of Bambusa Vulgaris-Schrad under monotonic and cyclic loading. The underlying fatigue and fracture mechanisms are elucidated for single and double notched specimens oriented for crack growth in the crack divider () and crack arrestor () orientations. The implications of the results are then discussed for structural applications of bamboo.
Figure 1. Schematics of bend specimens: (a) crack arrestor orientation; (b) crack divider orientation; (c) cracking from four point bend specimen with a single notch, and (d) cracking from four point bend specimen. (e) Schematics of crack initiation and growth in the bamboo specimen under four-point bending
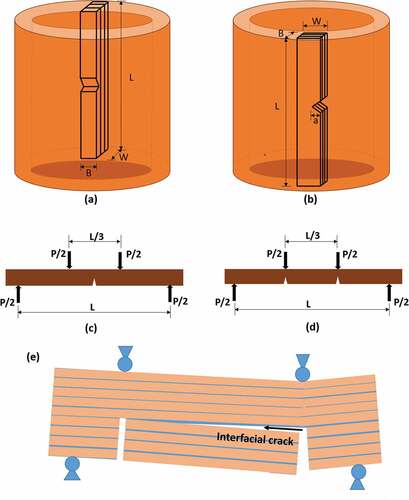
2. Theory
2.1. Fracture toughness
The stress intensity factor, , at the tip of the crack in a single notched specimen, under four-point bending (), is given by (Donadon et al., Citation2007)
where, is the distance from the outer to inner loading support, while
is the applied force and crack geometry factor,
is given by (Mccormack et al., Citation2012)
In the case of a double edge notched bend specimen with similar initial notch dimensions (), the stress intensity factor () at the notch tips is given by (Mccormack et al., Citation2012)
where, is the force and
is a constant.
In analyzing the effect of double versus single notch, McCormack et al. (Mccormack et al., Citation2012) have shown that the fracture toughness from the Double Notch Four Point Bend (KDN) tests should be increased by 1.04 to account for the presence of the second notch and interactions between the two notches to compare the data with the results from the single-notch test. Crack initiation and growth from the notch of a bamboo specimen can occur along the interface between fibers () as well as across the matrix cutting through the fibers. In the case of a crack along the interface, Charalambides et al. (Charalambides et al., Citation1990) have previously shown the analytical solutions for the crack driving force at the tip of the interfacial crack between two dissimilar materials under bending. The energy release rate () at the tip of the crack under deformation can be expressed as (Tan et al., Citation2011)
where, is the composite fracture toughness and
. In the case of specimens subjected to cyclic deformation, the dependence of the fatigue crack growth rate (da/dN) on the range of the energy release rate, ΔG, can be analyzed using the following power law expression (Soboyejo, Citation2002):
where C and m are material constants.
3. Materials and experimental methods
3.1. Materials characterization
Bambusa Vulgaris-Schrad was harvested from the University of Ile-Ife Farm at the Obafemi Awolowo University in Osun State, Nigeria. The bamboo was left to dry for 6 months at room temperature (23 ± 1°C) under relative humidity between 13 and 18% (a sample of the dried bamboo is shown in ). Microstructural samples were cut from the dried bamboo and polished with Emery paper (400, 800, and 1200 grit) to reveal the three orthogonal faces.
Figure 2. (a) Dried sample of bamboo, (b) 3D isometric projection of polished sample, (c) transverse and (d) longitudinal sections showing the parenchyma cells and vascular bundles
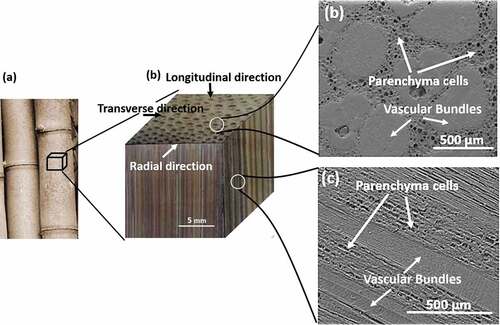
The isometric projection of the 3D image of the Bambusa Vulgaris-Schrad, showing a gradation of the vascular bundles within the parenchyma cells, is presented in . Optical microscopy (OM) and Scanning Electron Microscopy (SEM) images of the bamboo structure are presented, respectively, in . The volume fraction of the fibers was also characterized using the Image J software package (Image J, NIH, Bethesda, MD).
The moisture content of the dry bamboo was determined to be 4.47 ± 0.05% using a method described previously (Onche et al., Citation2020). Wang et al. (Wang et al., Citation2013) have shown that, for a relative humidity of 15.22%, the corresponding moisture content for the Moso bamboo used in their work was 4.30%, while for 27.19% relative humidity, the corresponding moisture content was 6.04%. Hence, the relative humidity of 18% and corresponding moisture content of 4.52% obtained for the Bambusa Vulgaris-Schrad bamboo that was used in this work are within the range of values reported in an earlier study (Wang et al., Citation2013).
3.2. Mechanical testing
3.2.1. Compressive monotonic loading
Before studying the mechanical behavior of Bambusa Vulgaris-Schrad under cyclic loading, four samples of compression specimens of the bamboo of dimensions of 6 mm (radial direction) by 12 mm (tangential direction) by 12 mm (axial direction) were saw-cut from internodes at the middle section, after removing the cortex and inner layers for compression test in the longitudinal direction. The faces of the compression specimens were then polished successively with emery paper (400, 800, and 1200 grit).
Compression tests were carried out on the above specimens using an Instron 8872 servo-hydraulic mechanical testing system (Instron 8872, Instron, Norwood, MA, USA). The specimens were loaded at a displacement rate of 0.5 mm/min. In-situ optical microscopic observations of local displacements were also used to measure the local displacements within the gauge uniform cross-sections of the compressive samples. In this way, Young’s moduli were determined from the ratios of the stresses and the strains.
3.2.2. Fracture tests
Four-point bend fracture experiments were carried out on five samples of single- and double-notched specimens obtained from the middle section of the bamboo culm in the crack divider (LT) () and crack arrestor (LR) orientations (). Schematic illustrations of the fixtures and loading conditions (for the four-point bend tests) are presented in , for single-notched and double-notched specimens, respectively. The dimensions of the specimens used were 11.0–11.3 mm (width), 5.5–5.7 mm (thickness) for the LT configuration and 6.0 mm (width), 3.0 mm (thickness) for the LR configuration while the span (L) between the two notches is L ~ 45 mm. The initial notch lengths (ao) in the specimens were ao = 0.45 W. The notches on the specimens were cut using aBridgeport grinding machine (Bridgeport Machines, Bridgeport, Connecticut, USA). Fracture toughness tests were then carried out in an Instron 8872 servo-hydraulic testing system (Instron 8872, Instron, Norwood, MA, USA). The specimens were tested under displacement control at aramp rate of 0.5mm/min. Cracking phenomena in the specimens were observed in-situ with avideo camera (Sony, Model FDR-AX33, Japan) and aProscope digital microscope (Proscope HR, Bodelin Technologies, Oregon, USA).
3.2.3. Fatigue test experiments
The fatigue behavior of the Bambusa Vulgaris-Schrad bamboo specimens was studied under compression or bending loading conditions. In the case of the compression fatigue tests, smooth samples with dimensions of 12 mm (axial direction) by 12 mm (tangential direction) by 6 mm (radial direction) were prepared from the middle section culms of the bamboo. The cortex and inner layers were then removed. The specimens were then loaded in a direction that was parallel to the longitudinal fibers in an Instron 8872 servo-hydraulic system (Instron 8872, Instron, Norwood, MA, USA) that was instrumented with a 25 kN load cell. The cyclic deformation of the specimens was then carried out at a frequency of 10 Hz and a stress ratio () of ∞. Fatigue tests were carried out at stress ranges corresponding to 90%, 95%, 100%, 110% and 120% of the monotonic buckling stress established in the experiments conducted under monotonic loading. Each test was loaded until the onset of catastrophic failure. The underlying deformation and cracking phenomena were also examined using an in-situ digital video camera (FDR-AX33, Sony, Japan).
Specimens with widths of 11.0 mm, heights of 5.5 mm, and spans, S (between the two notches) of ~ 45 mm, were used for the crack divider (LT) orientation, while the width of 6 mm, the height of 3 mm, and a span of ~ 45 mm were used for the crack arrestor (LR) orientation. The initial notch lengths (ao) for the specimens were ao = 0.45 W. The notches on the specimens were cut using a Bridgeport grinding machine (Bridgeport Machines, Bridgeport, Connecticut, USA). The specimens were then axially loaded in an Instron 8872 servo-hydraulic system (Instron 8872, Instron, Norwood, Massachusetts, USA) instrumented with a 5 kN load cell.
The bend specimens were used to conduct studies of fracture and fatigue. The fracture experiments were conducted at ramp rates of 0.5 mm/min and 0.3 mm/min for the crack divider (LT) and crack arrestor (LR) orientations, respectively, while the fatigue crack growth experiments were conducted at acyclic frequency of 10 Hz and a stress ratio of 0.1. In all cases, the growth of cracks was observed in-situ and measured using a Proscope digital microscope (Proscope HR, Bodelin Technologies, Oregon, USA).
4. Results and discussion
4.1. Microstructure of Bamboo
A typical optical image obtained from a polished bamboo surface is presented as an isometric projection in . This corresponds to a low magnification image of the aligned fibers in the vertical and transverse directions. Higher magnification SEM images obtained for both the transverse and longitudinal images of the bamboo are presented in respectively, showing the parenchyma cells and vascular bundles. The volume fraction of the vascular fiber bundles was found to be ~ 45% in the middle sections. Osorio et al., (Osorio et al., Citation2018) reported that the composition of the G. Angustifolia bamboo used was 51% parenchyma tissue, 40% fiber, and 9% conducting cells. The volume fraction of the fiber bundles used for this work falls within the range of these values.
4.2. Monotonic compression
The compressive failure mechanism is presented in , while a typical stress-strain curve obtained for the monotonic compressive loading of the bamboo (in the longitudinal direction) is presented in . This shows a failure load of ~114 MPa. clearly shows the occurrence of progressive buckling and the kinking of the fibers during the compressive monotonic loading of the bamboo under monotonic loading, as well as the interfacial delamination at the fiber-lignin interface.
Figure 3. (a) Compressive failure of bamboo under monotonic loading; the image shows buckling, kinking and cracking. (b) A typical stress-strain curve of the monotonic loading
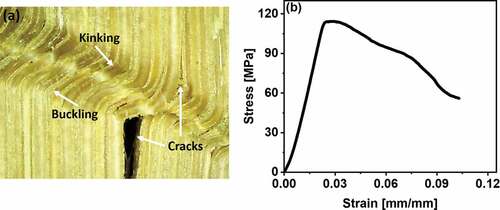
The stress-strain curve () also shows a region of linearity, which corresponds to the region of elastic behavior, while the maximum stress corresponds to the onset of buckling. Beyond the peak stress, progressive buckling and kinking of the fibers occur, leading ultimately to interfacial cracking between lignin and hemicellulose, and and translaminar cracking.
4.3. Fracture and toughening mechanisms
The failure mechanisms observed in the single- and double-notched specimens (that were subjected to four-point bend tests in ther crack arrestor and crack divider orientations) are presented in . presents representative in-situ optical microscopy images of the double-notched specimens (oriented for crack growth in the crack divider orientation) under monotonic loading. A representative optical microscopy image of a double-notched bend specimen (in the crack arrestor orientation) is presented in . Cracks were observed to initiate at both notches in most specimens that were tested in both orientations. However, in a few cases, the cracks propagated from only one notch, which acts as the dominant crack, while the crack from the second notch remained shielded ().
Figure 4. Optical images of notches and crack/microstructure interactions in the crack divider orientation in a double notched specimen: (a) Initial notch; (b) interlaminar cracks with bridging segments; (c) interlaminar and initial deflected cracks; (d) interlaminar and deflected cracks across plies (e) interlaminar and deflected crack profiles with bridging segments, and (f) interlaminar and deflected crack profiles with bridging ligaments
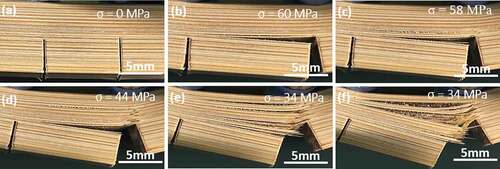
Figure 5. (a) An optical image of notches and crack/microstructure interactions in the crack arrestor orientation in a double notched specimen showing interlaminar and deflected crack profiles with bridging ligaments. (b-c) Optical images of notches and crack/microstructure for single-notched specimen interactions in crack arrestor (b) and crack divider (c) orientations. These images show interlaminar and deflected crack profiles with bridging ligaments
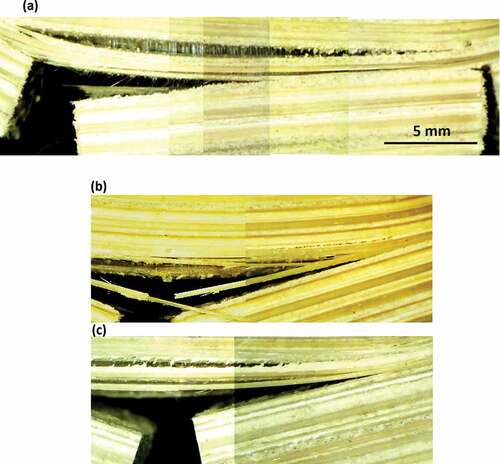
The cracks were initiated in a direction that was perpendicular to the direction of the applied load (i.e. parallel to the fiber axes from one notch towards the other). Furthermore, as the loading on the specimen was increased, crack growth from one of the notches stopped, while crack growth from the other notch continued until the other crack reached the interlaminar boundary. The stopping of the non-propagating crack is attributed to the effects of crack-tip shielding and local microstructural differences at the crack-tips (Lu et al., Citation2018; Seelig & Giessen, Citation2007; Soboyejo, Citation2002). The local microstructural differences resulted in differences in the crack growth from initially identical notches. Hence, as the cracks extended, the different crack lengths resulted in the shielding of the slightly smaller crack by the larger crack. This caused the stoppage of the slightly smaller crack and the continued extension of the slightly larger crack.
Once the slightly larger cracks reached the interlaminar boundaries, they kinked into the inter-laminar boundaries, it started to grow along the boundaries in the transverse direction (—4f). There was also some evidence of ligament crack bridging during crack extension along the interfaces. Furthermore, as the cracks widened due to increasing applied loads, the crack that shielded the other opened up, as the crack growth cuts across the adjacent ply into the next interface(s). In this way, the cracks extended in the longitudinal and transverse directions until they extended across the plies and within the interlaminar boundaries.
In the case of crack growth in the crack arrestor orientation, similar crack/microstructure interactions are observed, as the cracks extend from the notches into the interlaminar boundaries (). In the process, the cracks get bridged by some of the fibers. As the applied load increases, the plastic zone size increases, and the cracks cut across adjacent plies into adjacent interlaminar boundaries. Finally, the cracking extends across the widths of the specimens, leaving behind strips of bridging ligaments.
(a and b) present the optical images of the single-notched specimens under monotonic loading. Some evidence of ligament crack bridging during crack extension along the interfaces were also noticed in the single-notched specimens for both the crack arrestor () and crack divider () orientations similar to the crack growth profiles in the double-notched specimens. The more dominant crack is the mode II crack profile in both the LT and LR orientations.
4.4. Four-point bending force-displacement curves
Typical force-displacement curves obtained from the four-point bend tests on the single- and doubled-notched bend specimens are presented in for both the crack arrestor and divider orientations. These show that the strength of the bamboo in the divider orientation is greater than that in the crack arrestor orientation. The vascular bundles in the bamboo increase from the inner layer to the outer. Hence, the inner layer is softer than the outer layer, due to the lower fiber volume fraction in the inner layer.
Figure 6. Load-displacement curves for four-point bending of single- and double-notched specimens in the (a) crack divider and (b) crack arrestor orientations
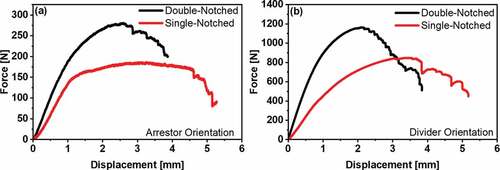
The crack in the arrestor orientation () initiates from the softer layer where there is more lignin/hemicellulose concentration than the cellulose fibers in the radial direction and this is responsible for the lower strength values of 281 N and 186 N for the arrestor orientations in the double- and single notched specimens, respectively. The crack in the crack divider orientation () initiates and cuts across a uniform cross section of the vascular bundles in the tangential direction with significantly higher strength values. This is responsible for the high strength values of 1164 N and 848 N for the crack divider orientation in the single- and double-notched specimens, respectively.
In both , the double-notched specimens exhibited higher strengths than the single-notched samples that were both subjected to four-point (pure) bending. The shear forces in a single-notched specimen under four-point bending are concentrated on the single notch while in a doubled notched specimen subjected to four-point bending the shear forces are initially distributed along the two notches. Hence, at the onset of loading, cracks begin to grow from both notches However, as the loading increases, local microstructural differences at the crack-tips and crack-tip shielding differences result in the onset of catastrophic failure from a dominant crack in the double notched specimen.
4.5. Fracture toughness
Typical crack growth resistance curves obtained for the single- and double-notched specimens are presented in for both arrestor () and divider () orientations. The estimated mode II energy release rate values obtained for a single notched specimen, under four-point bend, are 1.432 ± 0.461 and 1.700 ± 0.216 KJ/m2 () for LR and LT orientations, respectively. In the case of a double edge notched bend specimens with similar initial notch dimensions, the average energy release rate GDN values are 0.700 ± 0.179 and 1.100 ± 0.158 KJ/m2 () for LT and LR orientations, respectively. The results show that fracture toughness of specimens in divider orientation are slightly higher than those in the arrestor orientation. However, these values are very close for both single-and double-notched specimens.
4.6. Fatigue behavior
The compressive stress-life (S-N) plot obtained for the Bambusa Vulgaris-Schrad bamboo is presented in . Fatigue failure was only observed at stress ranges where maximum stresses exceeded the critical conditions for buckling. Above this condition, the compression fatigue specimens exhibited fatigue lives that decreased with increasing stress amplitude.
For cyclic loading at a stress amplitude equal to 120% of the critical buckling stress, the initiation of fatigue damage was associated with the onset of fiber buckling (). This was followed by interlaminar cracking () and kink band formation ().
Figure 9. Optical images of failure at different number of cycles for stress amplitude at 120% of buckling load: (a) 0 cycles; (b) 45 cycles; (c) 47 cycles; (d) 48 cycles, (e) 49 cycles, and (e) 50 cycles
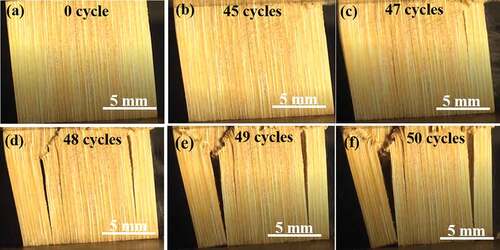
For a stress amplitude that is equal to 95% of the critical buckling stress, optical images of the fatigue damage mechanisms are presented in . These show clear evidence of progressive fiber buckling (), interlaminar cracking (), and shear/kink-band formation and interlaminar failure after ~ 2610–2628 cycles ().
Figure 10. Optical images of failure at different number of cycles for stress amplitude at 95% of buckling load: (a) 0 cycles; (b) 2138 cycles; (c) 2567 cycles; (d) 2619 cycles, and (e) 2628 cycles
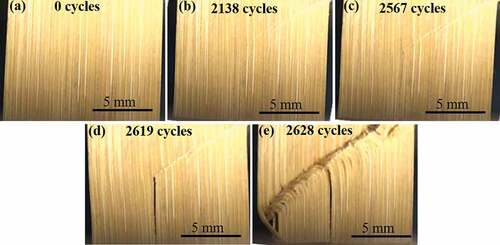
Most of the compression fatigue specimens did not fail at stress amplitudes corresponding to 90% of the critical buckling stress, although one of 10 specimens did show some signs of buckling. However, this specimen did not fail even when cycled for 400,000 cycles. Hence, the current results suggest that fatigue failure does not occur in Bambusa-Vulgaris Schrad bamboo when the peak stresses are significantly below the critical buckling stress.
The above results are consistent with prior reports by Ali et al. (Ali et al., Citation2016), who have also shown that fatigue damage in bamboo is associated with interfacial debonding/cracking, matrix cracking, and fiber buckling/fracture ().
In the case of cyclic deformation of double edge notched specimens that were deformed under pure four-point bending, optical images of fatigue cracks are presented in for crack growth in the arrestor orientation. After a few cycles, cracks initiated from the two notches before one crack became dominant over the other. The dominant cracks were observed to initiate from the notches. They then deflected into the interlaminar interfaces, where they grew along the interfaces between the plies (—11e).
Figure 11. Optical images of fatigue cracks of bamboo under cyclic deformation: (a) Initial notch; (b) initiated cracks along the interface; (c-d) interlaminar growing cracks, and (e) fatigue interlaminar crack profile with lignin cracking
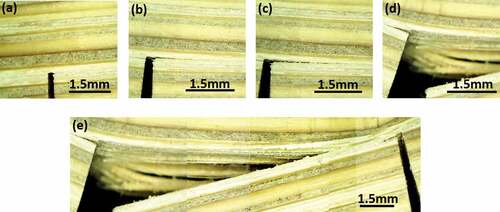
The dependence of the crack lengths on the number of fatigue cycles is presented in and 14b, for both the crack divider and crack arrestor orientations. The corresponding fatigue crack growth data are also presented in . In the case of fatigue crack growth in the crack divider orientation, the initial crack growth rates were slower in the mode I direction than in the predominantly mode II direction (at the interfaces between the plies) (). However, the crack growth rates were comparable in the crack arrestor orientation, as shown in .
4.7. Implications
The implications of the above results are significant for the design of robust bamboo structures. First, they show that the onset of global buckling is very important in the design of bamboo structures that are resistant to failure under monotonic and cyclic loading. In both cases, the incremental deformation, beyond the onset of global buckling, leads to the initiation of interlaminar cracking along the fiber axis. The associated matrix deformation also gives rise to kink/shear band formation, as the incremental deformation propagates across the layered structure of the bamboo.
In the case of crack growth from double notches with nominally identical initial dimensions, the current work suggests that, although the cracks initiate and grow at similar initial conditions, the local differences in the microstructures encountered by the growing cracks result in differences in the crack growth that occurs from the two notches. These differences result in the shielding of the slightly smaller cracks than the slightly bigger cracks. Ultimately, this results in the complete retardation of the shielded smaller cracks.
Beyond this, the propagating cracks extend into the interlaminar boundary, before deflecting and propagating as predominantly mode II cracks along the interfaces. Similar interlaminar cracking can also occur across multiple plies, as the cracks extend between and across adjacent plies and interfaces. This leaves behind bridged crack configurations in the crack arrestor and crack divider orientations. It also enables the toughening of the bamboo structures under monotonic and cyclic loading conditions.
Finally, it is important to note that the current work shows that the robustness of bamboo structures can be characterized using fracture mechanics approaches. These can be applied to the modeling of the crack driving forces under monotonic and cyclic loading conditions that simulate potential service conditions. Furthermore, the resulting critical crack driving forces depend strongly on the crack/microstructure interactions and the crack-tip shielding phenomena that occur within the crack-divider or crack-arrestor orientations. Further work is clearly needed to apply these concepts to the design of robust engineering structures and components. These are some of the opportunities for future work. The study of economic assessment of the use of Bambusa Vulgaris-Schrad bamboo is also necessary in the future, considering the growing interest of bamboo for structural applications.
5. Summary and concluding remarks
This paper presents the results of an experimental study of the fatigue and fracture behavior of Bambusa Vulgaris Schrad bamboo in the crack divider (LT) and crack arrestor (LR) orientations. The onset of compression fatigue and fracture is shown to be associated with the onset and progression of the global buckling of the cellulose fibers. This is combined with interlaminar cracking and kink/shear band formation, before final failure.
The initiation of mode I cracks from single or double notched specimens occurs initially in the mode II direction in the crack divider and crack arrestor orientations. In both scenarios, the cracks deflect into the interfaces between adjacent plies. The subsequent extension of cracks then continues along the interlaminar interfaces until translaminar or interfacial cracks are induced in adjacent layers. These leave behind uncracked ligaments that contribute to the overall levels of crack-tip shielding/toughening.
The estimated mode II energy release rate values obtained for a single notched specimen, under four-point bend, are observed to be higher than the values for double edge notched bend specimens for both the LT and LR orientations. The results also show that fracture toughness of specimens in divider orientation are slightly higher than those in the arrestor orientation. However, these values are very close for both single-and double-notched specimens.
Acknowledgements
This work is supported by the World Bank (Pan African Materials Institute supported by the World Bank African Centers of Excellence Program – Grant No: P126974) and Worcester Polytechnic Institute. Authors are also grateful to Tertiary Education Trust Fund (TETFund), Nigeria.
Additional information
Funding
Notes on contributors
Winston O. Soboyejo
Emmanuel O. Onche is a PhD student at the African University of Science and Technology (AUST), Abuja, Nigeria and a visiting scholar to the Worcester Polytechnic Institute (WPI), MA. USA. He obtained his Master of Science degree in Metallurgical Engineering from the Donetsk Polytechnic Institute, Ukraine.
References
- Abdul Khalil, H. P. S., Bhat, I. U. H., Jawaid, M., Zaidon, A., Hermawan, D., & Hadi, Y. S. (2012). Bamboo fibre reinforced biocomposites: A review. Materials and Design, 42, 353–16. . https://doi.org/10.1016/j.matdes.2012.06.015.
- Adewole, N. A., & Bello, K. O. (2013). Recycling of bamboo (Bambusa Vulgaris Schrad) recovered from scaffold into material for furniture production. Innovative Systems Design and Engineering, 4, (9). 73 -79
- Ali, A., Rassiah, K., Othman, F., Pueh, L. H., Earn, T. T., Hazin, M. S., Muhammad, M., & Megat, H. (2016). Fatigue and fracture properties of laminated bamboo strips from gigantochloa scortechinii polyester composites. Bio Resources, 11(4), 9142–9153.
- Amada, S., & Untao, S. (2001). Fracture properties of Bamboo. Composites Part B:Engineering, 32(5), 451–459. https://doi.org/10.1016/S1359-8368(01)00022-1
- Askarinejad, S., Kotowski, P., Youssefian, S., & Rahbar, N. (2016). Fracture and mixed-mode resistance curve behavior of Bamboo. Mechanics Research Communications, 78, 79–85. https://doi.org/10.1016/j.mechrescom.2016.02.001
- Banga, H., Singh, V. K., & Choudhary, S. K. (2015). Fabrication and study of mechanical properties of bamboo fibre reinforced bio-composites. Innovative Systems Design and Engineering, 6(1), 84–99.
- Charalambides, P. G., Cao, H. C., Lund, J., & Evans, A. G. (1990). Development of a test method for measuring the mixed mode fracture resistance of bimaterial interfaces. Mechanics of Materials, 8, 269–283. https://doi.org/10.1016/0167-6636(90)90047-J
- Chen, G., Luo, H., Sujun, W., Guan, J., Luo, J., & Zhao, T. (2018). Flexural deformation and fracture behaviors of Bamboo with gradient hierarchical fibrous structure and water content. Composites Science and Technology, 157, 126–133. https://doi.org/10.1016/j.compscitech.2018.01.034
- Donadon, M. V., Falzon, B. G., Iannucci, L., & Hodgkinson, J. M. (2007). Intralaminar toughness characterisation of unbalanced hybrid plain weave laminates. Stroke, 38(5), 1597–1611. https://doi.org/10.1016/j.compositesa.2006.12.003
- Eromosele, O. J., & Olorunfemi, O. F. (2019). Microstructural examination of culm fibres of Bambusa Vulgaris Schrad. ex. J. C. Wendl. American Research Journal of Biosciences, 4(1), 1–5.
- https://doi.org/10.2147/IJN.S79107
- Keogh, L., O’Hanlon, P., O’Reilly, P., & Taylor, D. (2015). Fatigue in Bamboo. International Journal of Fatigue, 75, 51–56. https://doi.org/10.1016/j.ijfatigue.2015.02.003
- Lu, X., Rawson, S. D., & Withers, P. J. (2018). Effect of hydration and crack orientation on crack-tip strain, crack opening displacement and crack-tip shielding in elephant dentin. Dental Materials, 34(7), 1041–1053. https://doi.org/10.1016/j.dental.2018.04.002
- Mannan, S., Parameswaran, V., & Basu, S. (2018). Stiffness and toughness gradation of bamboo from a damage tolerance perspective. International Journal of Solids and Structures, 143, 274–286. https://doi.org/10.1016/j.ijsolstr.2018.03.018
- Mccormack, J., Wang, X. S., Stover, S. M., Gibeling, J. C., & Fyhrie, D. P. 2012. Analysis of miniature single- and double-notch bending specimens for estimating the fracture toughness of cortical bone. J Biomed Mater Res Part A, 100A, 1080–88. https://doi.org/10.1002/jbm.a.34005.
- Ogunsanwo, O. Y., Terziev, N., Panov, D., and Daniel, G. (2015). Bamboo (Bambusa vulgaris Schrad.) from moist forest and derived savanna locations in South West Nigeria - properties and gluability. BioRes. 10(2), 2823–2835.
- Onche, E. O., Azeko, S. T., Obayemi, J. D., Oyewole, O. K., Ekwe, N. B., Rahbar, N., & Soboyejo, W. O. (2020). Compressive deformation of Bambusa Vulgaris-Schrad in the transverse and longitudinal orientations. Journal of the Mechanical Behavior of Biomedical Materials, 108(March), 1–8. https://doi.org/10.1016/j.jmbbm.2020.103750
- Osorio, L., Trujillo, E., Lens, F., Ivens, J., Verpoest, I., & Van Vuure, A. W. (2018). In-depth study of the microstructure of Bamboo fibres and their relation to the mechanical properties. Journal of Reinforced Plastics and Composites, 37(17), 1099–1113. https://doi.org/10.1177/0731684418783055
- Sangeetha, R., Diea, Y.K.T., Chaitra, C, Malvi, P.G. and Shinomol, G.K. (2015). The Amazing Bamboo: A Review on its Medicinal and Pharmacological Potential. Indian Journal of Nutrition, 2(1), 106
- Seelig, T., & Giessen, E. (2007). Effects of microstructure on crack tip fields and fracture toughness in PC/ABS polymer blends. International Journal of Fracture, 145(3), 205–222. https://doi.org/10.1007/s10704-007-9117-y
- Soboyejo, W. 2002. Mechanical Properties of Engineered Materials. https://doi.org/10.1201/9780203910399
- Song, J., Surjadi, J. U., Dayong, H., & Yang, L. (2017). Fatigue characterization of structural Bamboo materials under flexural bending. International Journal of Fatigue, 100, 126–135. https://doi.org/10.1016/j.ijfatigue.2017.03.016
- Tan, T., Rahbar, N., Allameh, S. M., Kwofie, S., Dissmore, D., Ghavami, K., & Soboyejo, W. O. (2011). Mechanical properties of functionally graded hierarchical Bamboo structures. Acta Biomaterialia, 7(10), 3796–3803. https://doi.org/10.1016/j.actbio.2011.06.008
- Taylor, D. (2018). Measuring fracture toughness in biological materials. Journal of the Mechanical Behavior of Biomedical Materials, 77, 776–782. https://doi.org/10.1016/j.jmbbm.2017.07.007
- Van Der, L. P., & Van Den Dobbelsteen, A. A. J. F. (2006). An environmental, economic and practical assessment of bamboo as a building material for supporting structures. 20, 648–656. https://doi.org/10.1016/j.conbuildmat.2005.02.023
- Wang, H., Wang, H., Wanju, L., Ren, D., & Yan, Y. (2013). Effects of moisture content on the mechanical properties of Moso Bamboo at the macroscopic and cellular levels. Bio Resources, 8(4), 5475–5484. https://doi.org/10.15376/biores.8.4.5475-5484
- Yeasmin, L., Ali, N., Gantait, S. and Chakraborty, S. (2015). Bamboo: an overview on its genetic diversity and characterization. 3 Biotech, 5, 1–11
- Youssefian, S., Jakes, J. E., & Rahbar, N. (2017). Variation of nanostructures, molecular interactions, and anisotropic elastic moduli of lignocellulosic cell walls with moisture. Scientific Reports, 7(1), 1–10. https://doi.org/10.1038/s41598-017-02288-w
- Youssefian, S., & Rahbar, N. (2015). Molecular origin of strength and stiffness in Bamboo fibrils. Scientific Reports, 5(1), 1–13. https://doi.org/10.1038/srep11116
- Zou, Z., Jin, W., & Zhang, X. (2019). Influence of moisture content on mechanical properties of Bamboo Scrimber. Journal of Materials in Civil Engineering, 31(7), 1–9. https://doi.org/10.1061/(ASCE)MT.1943-5533.0002746