Abstract
The aim of this study was to investigate the properties of concrete with waste paper ash (WPA) as cement replacing material. The chemical composition of WPA was reported, and Portland cement was partially replaced with 0%, 5%, 10%, 15%, and 20% of WPA to explore its effect on both fresh and hardened properties of C—25 concrete. The result of this study indicated that the chemical compositions of WPA were not classified as Pozzolanic material. Setting times of blended cement paste with WPA were lengthened and its consistency was also increased. The cement paste with replacement up to 10% showed a normal consistency within the standard range. The workability of concrete was tested immediately after preparing the concrete mix, whereas the compressive strength was tested after 7 and 28 days of curing. The results indicated that the workability of concrete containing WPA decreases as the WPA content increases. This study also revealed that there is a significant improvement in the compressive strength of concrete. Replacement of ordinary Portland cement by WPA up to 10% results in better compressive strength than that of the control mix. An improvement of 5.6% & 1.2% was observed, respectively, when compared with the 28-day compressive strength of the control mix. But the compressive strength decreases as the WPA replacement increases over 10%. Maximum compressive strength of 37.89 MPa was obtained for concrete containing 5% of WPA.
PUBLIC INTEREST STATEMENT
A human being, to improve his daily life, has a responsibility to protect his natural environment, His effort of research, invention, investigation, and exploration has to be toward the protection of his environment. Hence, the study is oriented towards concrete, where cement is used as a major ingredient to influence its properties in both fresh and hardened states. Cement, being the most important ingredient of concrete, its production process is both uneconomical and environmentally unfriendly. In order to solve these problems, the utilization of different Supplementary Cementitious Materials which have lower emission of CO2, lower cost of production, and lower energy consumption, was being implemented. The research in this field was developed to examine the effects of the waste paper powder, as a supplementary Cementitious Material, on the characteristic properties of concrete, in both fresh and hardened states. Accordingly, there is a significant improvement in some properties of concrete.
1. Introduction
Concrete is one of the most versatile and widely used building materials in the construction industry (Ramkumar et al., Citation2020). It is composed of aggregates, Portland or blended cement, water, and other cementitious materials and/or chemical admixtures (Matalkah et al., Citation2019, Citation2018). It contains some amount of entrapped air and purposely entrained air obtained by use of an admixture or air-entraining cement (Kosmatka et al., Citation2003). The annual production of concrete is rapidly increasing. This is because many developing countries are experiencing rapid urbanization and population growth, making the demand for housing and infrastructure development greater than ever before (Almalkawi et al., Citation2018). Cement is the most important ingredient of concrete. It is, however, expensive and environmentally unfriendly (Ighalo & Adeniyi, Citation2020). About 10% of anthropogenic CO2 emissions come from cement use (Jexembayeva et al., Citation2020). Therefore, the need for economical and more environment-friendly materials led the way to the use of supplementary cementing materials in concrete. The use of different cement replacing materials has become a common practice in the construction industry.
Currently, several supplementary pozzolanic materials are being utilized as partial replacement of cement. Such materials include pumice (Kumar et al., Citation2020), sugarcane bagasse ash (Moretti et al., Citation2018), recycled tire aggregates (Li et al., Citation2019), ceramic waste (Vaidevi et al., Citation2020), paper pulp (Sumit & Raut, Citation2013), silica fume (Ofuyatan et al., Citation2021), fly ash (Azimi-Pour et al., Citation2020; Guo et al., Citation2020), eggshell (Ofuyatan et al., Citation2020), paper sludge, waste glass powder (Rahman et al., Citation2018; Wang & Wang, Citation2017), waste paper sludge ash (Devi, Citation2016) and blast furnace slag (Ofuyatan et al., Citation2021). These studies observed that the compressive strength reduces with increased partial replacement. However, care is ensured that the threshold of quality is maintained. Essentially, there is a trade-off between the negative environmental effects (100% concrete) and reduced concrete performance but the lesser environmental impact (<100% concrete).
Paper is an example of valuable materials that can be recycled (Oriyomi & Oluwatobi, Citation2014). Disposable paper available in abundance throughout the world is composed mainly of short, natural, and cellulose fibers. Waste paper arises from several sources such as newspapers, office and printing papers, etc. Each has a different type of fiber quality, and mixing these papers of different qualities will reduce the purity of the highest quality fiber. Therefore, an investigation concerning the potential use of the different waste paper ash ratio as construction materials is essential to gain awareness into their behavior and properties. More than 450 million tons of paper is produced worldwide per annum and it is expected that the demand for paper will reach 500 million tons per annum by the end of 2020 (Ali et al., Citation2013). Also, Asmare (Asmare, Citation2015) predicted that the demand for paper to be imported to Ethiopia by the year 2015/16 was 157,956.7 tons. This demand for paper is increasing yearly because of education expansion policies and the overall economic development of the country.
Waste materials can be used directly or recycled to produce the same or another product (Ighalo & Adeniyi, Citation2020). This has the benefit of not only reducing the amount of waste but can also provide significant cost reduction for the production of new materials. By considering these two main issues (the environmental impact and production cost), there is a need for alternative cementitious material. This can be done in two ways. The first way is by using another binding material instead of cement. This is currently not possible due to the unavailability of such a binding material. The second way is the partial replacement of cement with an appropriate material. The second option is more feasible in contemporary times. The replacement of cement in concrete by various wastes may create a tremendous saving of energy and costs and also lead to important environmental benefits (Konkanov et al., Citation2020).
This study was targeted at investigating the properties of concrete produced by using waste paper ash (WPA) to ascertain their suitability to be used as a cement replacing material in concrete.
2. Materials and methods
2.1. Materials
The main materials used for this study were Portland cement (OPC), fine aggregate, coarse aggregate, waste paper (office copy paper), and potable water. The cement was Dangote Ordinary Portland Cement (OPC) of grade 42.5 r, which is obtained commercially. This cement complies with the requirements of Ethiopian Standards, ES C. D5 201. The river sand, passing through a 4.75 mm sieve, was used as a fine aggregate. The sand is free from clay, silt and organic impurities. To investigate its properties for the required application, different tests were carried out, which include gradation and fineness modules, specific gravity and absorption capacity, moisture content, silt content and unit weight. The silt content was found to be 4.54%, which is below the 5% limit of Ethiopian standard (MUDHC, Citation2014). Fineness modulus is found to be 2.8, which is in the range of ASTM C33 standard 2.3 to 3.1 (ASTM, Citation2001). The physical properties of the sand used in the study are shown in .
Table 1. Properties of the sand used in the study
Coarse aggregates used in this research were crushed granite, supplied from a local quarry, with a maximum size of 20 mm. Similar to the fine aggregates, the coarse aggregates were tested for their physical properties such as fineness modulus, specific gravity, gradation, and bulk density etc. These are shown in . Waste paper was collected from different offices and burned using an incinerator at a temperature of 850°C, to avoid the formation of crystalline ash which is less reactive to lime. The burned powder was then sieved using a sieve size of 7.4 µm. According to Neville (Neville, Citation2011), there is no simple relation between strength and cement particle size. So, particle size distribution analysis was neglected.
Table 2. Properties of coarse aggregate used in the study
2.2. Mix design and concrete production
ACI method of mix design (Committee, A., Citation2008) was used in designing the mixes based on collected data. The mix was prepared for C-25 concrete with a design strength (target mean strength) of 33.5 MPa. The mixing proportion was found to be 1:2.35:3. After determining the relative amount of materials to be used for the specimens, WPA was thoroughly blended with cement at 5%, 10%, 15%, and 20%. Each of the developed concrete mixes was coded based on their composition (shown in ). The aggregates and sands were then added and mixed dry for one minute. After the addition of water, all the materials were mixed for another two minutes. Finally, prepared specimens were submerged in a curing tanker and cured for 7 days and 28 days at room temperature according to ASTM Standard (ASTM C192) (ASTM, Citation2000).
Table 3. Consistency of blended cement paste
2.3. Tests on the cement paste
A normal consistency test was carried out to determine the amount of water required to prepare a standard cement paste. The normal consistency was measured by a Vicat apparatus. It measures the resistance of the paste to the penetration of a plunger or needle of 500 g, released at the surface of the paste. The water content was varied for each of the pastes produced until a normal consistent paste is obtained.
Setting time test was performed to determine the initial setting time and final setting time of cement paste with normal consistency. The initial setting time of the paste was determined by the duration of 25 mm penetration of the Vicat needle into the paste in 30 seconds after it has been released, while the final setting time was determined by measuring the time related to zero penetration of the needle into the paste.
2.4. Tests for concrete properties
To determine the workability of the fresh concrete, the slump test was conducted according to ASTM C 143. As specified by this method, concrete was placed in the slump cone in three approximately equal layers and consolidated by rodding each layer 25 times with a smooth, straight steel tamping rod. After the top layer was compacted, the excess concrete was struck off and the mould was removed slowly. Then, the slump was determined by measuring the difference in level between the height of the inverted cone and that of the highest point of the subsided concrete and reported as a slump.
A compressive strength machine (Model: EIE-TM-042) was used to determine the compressive strength of the concrete (capacity of 1000 KN). Cubes (150 mm × 150 mm × 150 mm) were cast for each percentage replacements of cement by WPA and cured for 7 and 28 days. After the successful curing of concrete, all specimens are tested in a compression testing machine by applying a compressive load. The load was increased at 140 kg/cm2 until failure. The highest load was observed and recorded. The experiments were performed in triplicates. The density of the concrete was determined by measuring its volume and weight and computing mathematically.
3. Results and discussion
3.1. Chemical compositions of waste paper ash
The chemical composition of the mineral admixtures is very essential in determining their suitability as a material for blending cement. The chemical composition of WPA was studied in the Geological Survey of Ethiopia (using XRF) and compiled in based on the finding of laboratory investigation. These results indicate that the key chemical compositions, which are SiO2 + Al2O3 + Fe2O3 (33.59%), are less than 70%. According to the ASTM C-618 specification, the WPA was not fulfilling the requirements of pozzolanic material. Based on this finding, the principal constituents present in WPA are lime (CaO) and silica (SiO2). The chemical activity of admixtures in cement is dependent essentially on their lime, silica and alumina contents, which are the main essential compounds needed for cement hydration for strength development. The silica content of WPA was higher than that of OPC. This indicates that WPA would produce satisfactory results in terms of strength. However, the alumina content was very low (2.65%). Alumina makes a little direct contribution to the strength of Portland cement. Iron oxide content (1.74%), which is also low, has no effect on cement but acts as a flux to aid cement and gives the grey color. The other minor constituents like TiO2, MnO2 and P2O3 were less than 1% and do not affect the strength and properties of cement products.
Table 4. Chemical composition of waste paper ash (WPA)
Several published works of literature have reported the chemical composition of paper pulp. Sumit and Raut (Sumit & Raut, Citation2013) studied elemental analysis of waste paper pulp and observed that the pulp mainly contains Si (60%) and Ca (14%). From their study, paper ash mainly contained Si (29.20%) and Ca (50.88%). The loss on ignition (LOI) value for the bagasse ash was found to be 12.52%, which was slightly higher than that specified by the standard (10%). The loss of ignition shows the extent of carbonation and hydration of free lime and free magnesia due to the exposure of cement to the atmosphere. The maximum loss on ignition (at 1000°C) permitted by BS EN 197–1: 2000 is 5% (Standard, E, Citation2000) and by ASTM C 150–07 is 3% except for Type I cement (2.5%) (ASTM, Citation2007); 4% is acceptable for cements in the tropics.
3.2. Setting times of the blended paste
The setting times of the blended paste containing WPA are given in . The set time was determined from an average of three sets of samples for each type of blended cement pastes. It was observed that the common effect of the WPA has lengthened the setting times of blended cement paste. This is due to the reaction that is responsible for the setting of cement. This is the reaction of C3A with both water and gypsum (CaSO4.2H2O), but the amount of C3A found in WPA is lower when compared with that of OPC. So this lower amount of C3A retarded the setting time of blended cement paste. The Ethiopian standard limits the initial setting time of cement not to be less than 45 minutes and the final setting time not to exceed 10 h. The results of this study indicated that the addition of WPA retarded the setting time; however, this retardation was within limits as specified by the Ethiopian standard.
Table 5. Setting times of the blended cement paste
3.3. Consistency of blended cement paste
A certain minimum quantity of water is required to be mixed with cement to ensure a complete chemical reaction between water and cement. Less water than this quantity would lead to an incomplete chemical reaction, thus resulting in the reduction of strength. Also, more water would increase the water-cement ratio and so would reduce its strength. The correct proportion of water to cement is required to achieve proper strength while using cement in structure. To get the proper amount of water, a normal consistency test of blended cement pastes was carried out. The normal consistency of blended pastes containing WPA is shown in . The control paste or the paste without WPA had a normal consistency of 29%. All the pastes containing WPA showed normal consistency higher than the control paste. The usual range of water to cement ratio for normal consistency is between 26% and 33% (Sumit & Raut, Citation2013). The pastes with replacement up to 10% showed consistency within this range; however, after 10% replacement the results showed higher values of consistency.
3.4. Workability of the concrete
To determine the workability of the fresh concrete, the slump test was conducted according to ASTM C 143. A slump test is conducted on fresh concrete for all percentages of WPA replacement. The slump values of all the mixtures are presented in . These results indicate that the slump decreased with the increase in WPA content. This effect can be attributed to the fact that WPA has a high water absorption capacity compared to cement and thus the content of water in the mix is reduced (hence less workable concrete is produced). The second reason is due to the lower density of WPA giving it a higher porosity resulting in higher water demand. Even though the slump value is decreased as the percentage of WPA is increased, until the percentage is 20% the slump value is within the specified limit, which is 30–50. The highest slump was seen for the control concrete mix. The effect of replacing Portland cement with paper pulp on the workability of concrete has been examined by several researchers and they observed that the workability decreased when a higher amount of paper ash content was included (Ardalan et al., Citation2017; Hameed, Citation2012). Sumit and Raut (Sumit & Raut, Citation2013) reported that the slump increased with up to 5% replacement of cement. Above 5%, the slump decreased as the paper pulp content in the concrete mixtures was increased.
3.5. Compressive strength of the concrete
A compression test was conducted on hardened concrete using a compression testing machine of 2000 KN capacity. After the successful curing of concrete, all specimens were tested in a compression testing machine by applying a compressive load. shows the measured compressive strengths of concrete cubes with various content of WPA after 7 and 28 days of curing. It can be observed that the strength properties of concrete increases as the percentage of WPA increases by up to 10%. Onwards, the strength decreased when compared with the control specimen. An improvement of 5.6% and 1.2% was observed for 5% and 10% replacement when compared with 28-day compressive strength of control mix of ordinary Portland cement. This is due to the higher amount of silica found in WPA than cement. However, the degree of improvement in strength appeared to be highly dependent on the cement replacement level. It was observed that the concretes with 15% and 20% WPA had shown a reduction of compressive strength. For all partial replacement levels, the compressive strength was higher after 28 days of curing compared to the 7 days’ results. The effects of paper ash on the compressive strength of concrete did not vary from the findings of previous researchers. Several published literature (Sumit & Raut, Citation2013; Yun et al., Citation2007) reported similar observations. Yun et al. (Yun et al., Citation2007) worked on the mechanical properties of papercrete concluded that the average compressive strength, which includes a 5% paper-cement replacement ratio, was 34 MPa. Also, Sumit and Raut (Sumit & Raut, Citation2013) concluded that the compressive, splitting tensile and flexural strength increased up to 10% addition of WPA and further increased reduced the strengths gradually.
3.6. Density of the concrete
The weight and the dimension of the concrete cubes are measured just before the compressive strength tests after curing for 7 and 28 days. The samples had a similar volume of 0.00338 m3, and their weight was also measured. The computed densities are shown in . The results of this study revealed that WPA reduces the hardened density of concrete as its percentage in the mix increases. The percentage of reduction was increased as the amount of WPA increased. But these densities of the concrete fall within the range of 2200–2400 kg/m3, which is considered to be of normal weight concrete (Kosmatka et al., Citation2003). The above findings are not different from those of other researchers. Yun et al. (Yun et al., Citation2007) studied the physical properties of the papercrete and concluded that the density of papercrete decreased when the replacement ratio of WPA of papercrete increased. The physical properties of papercrete were also reported by Shivangni et al. (Shivangni et al., Citation2015). They concluded that the density of the papercrete tended to decrease at a higher WPA (Shivangni et al., Citation2015).
Table 6. The density of the concrete
4. Conclusion
The results of this study showed that waste paper ash (WPA) cannot be classified as pozzolanic material. As prescribed by ASTM C 618, to classify particular material as pozzolanic materials, its chemical composition (SiO2+ Al2O3+ Fe2O3) has to be greater than 70% (but was less in this study). Higher replacement of cement by WPA resulted in higher normal consistency (implying higher water demand for certain workability) and longer setting time. The workability of concrete containing WPA decreases as the WPA content increases. Significant improvement was seen in the compressive strength of concrete. Replacing ordinary Portland cement with 5% to 10% of WPA results in better compressive strength than that of the conventional concrete for all curing ages. But beyond 10% replacement that there is a gradual reduction in compressive strength. The density of the concretes containing WPA has shown a reduction. It was found that a reduction of unit weight up to 2.05% was observed when 20% of the cement was replaced by WPA.
Compliance with Ethical Standards
This article does not contain any studies involving human or animal subjects.
Disclosure statement
The authors declare that there are no conflicts of interest.
Additional information
Funding
Notes on contributors
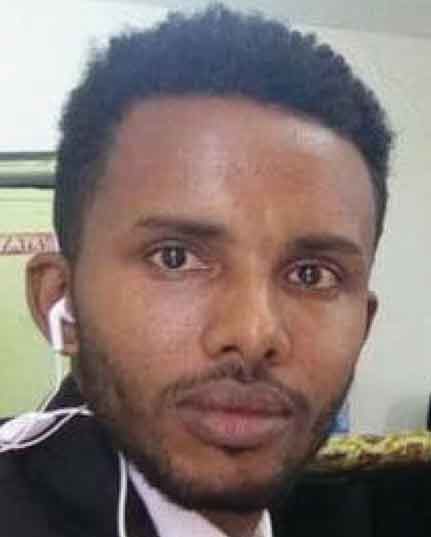
Bikila Meko
Bikila Meko Kejela is a lecturer and a young researcher in the Department of construction technology and management at Wolkite University, Ethiopia. He has a Bachelor of Science in Construction Technology and Management and a Masters in Science in Construction Engineering and Management. His major research interest includes advanced concrete engineering, alternative construction material, and green construction project management.
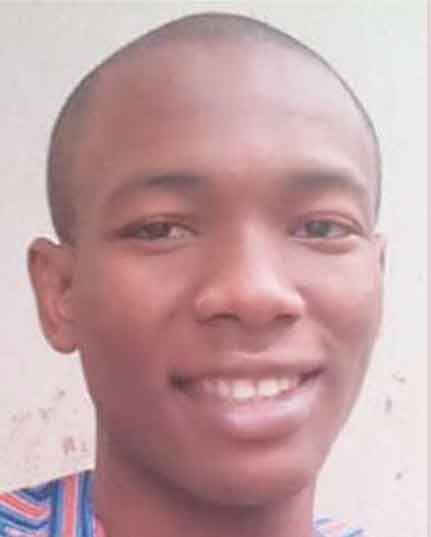
Joshua Ighalo
Joshua O. Ighalo obtained a Bachelor’s Degree in Chemical Engineering (2015) from the University of Benin, Benin-city, Nigeria. He also obtained a Masters’ Degree in Chemical Engineering (2020) from the University of Ilorin, Ilorin, Nigeria. He is an academic staff member of the Department of Chemical Engineering, Nnamdi Azikiwe University, Awka. His research interest includes computer-aided modeling and optimization of chemical process systems, biofuels, solid waste management, and environmental pollution control. He is currently working on a variety of problems across these research areas.
References
- Ali, A., Hashmi, H. N., & Baig, N. (2013). Treatment of the paper mill effluent – A review. Annals of Faculty Engineering Hunedoara - International Journal of Engineering, 11(3), 337–11.
- Almalkawi, A. T., Salem, T., Hamadna, S., Darsanasiri, A., Soroushian, P., Balchandra, A., & Al-Chaar, G. (2018). Physio-microstructural properties of aerated cement slurry for lightweight structures. Materials, 11(4), 597. https://doi.org/10.3390/ma11040597
- Ardalan, R. B., Joshaghani, A., & Hooton, R. D. (2017). Workability retention and compressive strength of self-compacting concrete incorporating pumice powder and silica fume. Construction and Building Materials, 134, 116–122. https://doi.org/10.1016/j.conbuildmat.2016.12.090
- Asmare, G. (2015). Pulp Production from Cotton Stalks using Kraft Pulping. Addis Ababa University.
- ASTM. (2000). Standard practice for making and curing concrete test specimens in the in ASTM standards. Farmington, 4, 1–8.
- ASTM. (2001). American Society for Testing and Materials, “Standard Specification for Concrete Aggregates” (Vol. 04). ASTM Standards.
- ASTM. (2007). American Society for Testing and Materials “Standard Specification for Portland Cement”.
- Azimi-Pour, M., Eskandari-Naddaf, H., & Pakzad, A. (2020). Linear and non-linear SVM prediction for fresh properties and compressive strength of high volume fly ash self-compacting concrete. Construction and Building Materials, 230, 117021. https://doi.org/10.1016/j.conbuildmat.2019.117021
- Committee, A.. (2008) . Building Code Requirements for Structural Concrete (ACI 318-08). American Concrete Institute.
- Devi, S. (2016). A review on cement replacement in construction Industry. International Journal of Civil Engineering and Technology, 3(5), 68–71.
- Guo, Z., Jiang, T., Zhang, J., Kong, X., Chen, C., & Lehman, D. E. (2020). Mechanical and durability properties of sustainable self-compacting concrete with recycled concrete aggregate and fly ash, slag and silica fume. Construction and Building Materials, 231, 117115. https://doi.org/10.1016/j.conbuildmat.2019.117115
- Hameed, A. H. (2012). Effect of superplasticizer dosage on workability of self compact concrete. Diyala Journal of Engineering Sciences, 5(2), 66–81.
- Ighalo, J. O., & Adeniyi, A. G. (2020). A perspective on environmental sustainability in the cement Industry. Waste Disposal and Sustainable Energy, 2(3), 161–164. https://doi.org/10.1007/s42768-020-00043-y
- Ighalo, J. O., & Adeniyi, A. G. (2020). Utilization of Recycled Polystyrene and Aluminum Wastes in the Development of Conductive Plastic Composites: Evaluation of Electrical Properties. In C. M. Hussain (Ed.), Handbook of Environmental Materials Management (pp. 1–9). Springer Nature.
- Jexembayeva, A., Salem, T., Jiao, P., Hou, B., & Niyazbekova, R. (2020). Blended cement mixed with Basic Oxygen Steelmaking Slag (BOF) as an alternative green building material. Materials, 13(14), 3062. https://doi.org/10.3390/ma13143062
- Konkanov, M., Salem, T., Jiao, P., Niyazbekova, R., & Lajnef, N. (2020). Environment-friendly, self-sensing concrete blended with byproduct wastes. Sensors, 20(7), 1925. https://doi.org/10.3390/s20071925
- Kosmatka, S. H., Kerkhoff, B., & Panarese, W. C. (2003). Design and Control of Concrete Mixtures (14th edition). Portland Cement Association.
- Kumar, B. A., Sangeetha, G., Srinivas, A., Awoyera, P., Gobinath, R., & Ramana, V. V. (2020). Models for predictions of mechanical properties of low-density self-compacting concrete prepared from mineral admixtures and pumice stone, in Soft computing for problem solving (pp. 677–690). Springer.
- Li, N., Long, G., Ma, C., Fu, Q., Zeng, X., Ma, K., Xie, Y., & Luo, B. (2019). Properties of self-compacting concrete (SCC) with recycled tire rubber aggregate: A comprehensive study. Journal of Cleaner Production, 236, 117707. https://doi.org/10.1016/j.jclepro.2019.117707
- Matalkah, F., Salem, T., Shaafaey, M., & Soroushian, P. (2019). Drying shrinkage of alkali activated binders cured at room temperature. Construction and Building Materials, 201, 563–570. https://doi.org/10.1016/j.conbuildmat.2018.12.223
- Matalkah, F., Salem, T., & Soroushian, P. (2018). Acid resistance and corrosion protection potential of concrete prepared with alkali aluminosilicate cement. Journal of Building Engineering, 20, 705–711. https://doi.org/10.1016/j.jobe.2018.08.001
- Moretti, J. P., Nunes, S., & Sales, A. (2018). Self-compacting concrete incorporating sugarcane bagasse ash. Construction and Building Materials, 172, 635–649. https://doi.org/10.1016/j.conbuildmat.2018.03.277
- MUDHC. (2014). Ministry of Urban Development Housing and Construction, Standard Technical Specifications for Building Works.
- Neville, A. M. (2011). Properties of concrete (5th ed). Trans-Atlantic Publications, Inc.
- Ofuyatan, M. O., Adeniyi, A. G., & Ighalo, J. O. (2021). Evaluation of fresh and hardened properties of blended silica fume self-compacting concrete (SCC). Research on Engineering Structures and Materials, 1–13. http://doi.org/10.17515/resm2020.228ma1023
- Ofuyatan, M. O., Adeniyi, A. G., Ijie, D., Ighalo, J. O., & Oluwafemi, J. (2020). Development of high-performance self compacting concrete using eggshell powder and blast furnace slag as partial cement replacement. Construction and Building Materials, 256, 119403. https://doi.org/10.1016/j.conbuildmat.2020.119403
- Oriyomi, M. O., & Oluwatobi, J. I. (2014). Assessment of the suitability of paper waste as an engineering. Material Engineering, Technology & Applied Science Research, 4(6), 724–727. https://doi.org/10.48084/etasr.485
- Rahman, A., Barai, A., Sarker, A., & Moniruzzaman, M. (2018). Light weight concrete from rice husk ash and glass powder. Bangladesh Journal of Scientific and Industrial Research, 53(3), 225–232. https://doi.org/10.3329/bjsir.v53i3.38270
- Ramkumar, K., Rajkumar, P. K., Ahmmad, S. N., & Jegan, M. (2020). A review on performance of self-compacting concrete–use of Mineral Admixtures and steel fibres with artificial neural network application. Construction and Building Materials, 261, 120215. https://doi.org/10.1016/j.conbuildmat.2020.120215
- Shivangni, K., Kishan, L. P., & Mukul, K. (2015). Review on papercrete. IJCRD, 4(6), 1-16.
- Standard, E. (2000). Composition, specifications and conformity criteria for common cements. in BS EN standards.
- Sumit, A. B., & Raut, S. P. (2013). Utilization of waste paper pulp by partial replacement of cement in concrete. International Journal of Engineering Research and Applications (IJERA), 1, 300–309.
- Vaidevi, C., Kala, T. F., & Kalaiyarrasi, A. (2020). Mechanical and durability properties of self-compacting concrete with marble fine aggregate. Materials Today: Proceedings, 22(2), 829–835.
- Wang, -C.-C., & Wang, H.-Y. (2017). Assessment of the compressive strength of recycled waste LCD glass concrete using the ultrasonic pulse velocity. Construction and Building Materials, 137, 345–353. https://doi.org/10.1016/j.conbuildmat.2017.01.117
- Yun, H., Jung, H., & Choi, C. (2007). Mechanical properties of papercrete containing waste paper. Architectural Institute of Korea.