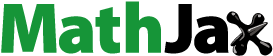
Abstract
One of the uses of particle board is in the design of speaker/woofer casing, but with increasing demand, the cost is skyrocketing, effects of which lead to the high cost of end-use woofer gadgets. Cement–paper composite reinforced with snail shell powder/banana fiber was developed as an alternative. The fiber was grouped into two; untreated banana fiber (UBF) and treated banana fiber (TBF) (treated with 1 M NaOH). Fibers were infused into the composite at 0%, 0.5%, 1%, 1.5%, 2%, and 2.5% by weight of paper pulp while snail shell powder was added at 15 wt.% constant proportion for all samples produced. Curing was carried out for 28 and 56 days, respectively. The composite boards produced were examined for physical, mechanical, and microstructural properties. Results obtained indicated an uptrend in water absorption and thickness swelling at increasing fiber loading. Internal bond strength, screw holding strength, moduli of rupture, and elasticity were observed to be enhanced with increment in fiber proportion. It was further noticed that alkaline TBF performed better than the untreated fiber, hence recommended for paperboard production. Experimental trend and performance analysis engaged in revealed hydration to be the most efficient experimental variable and important for overall property maximization in cement–paper composite. Performance evaluation conducted showed effective property index was noticed to be highest for composite board doped with 2.5 wt.% TBF.
PUBLIC INTEREST STATEMENT
Speaker woofers are often made from particle board and with increasing use of the boards in the production of the woofers, prices keep going up on account of the high cost of binder and high cost of the processing route in terms of energy consumption and equipment maintenance. A consequence of such leads to the high cost of end-use electronic gadgets. A way of tackling the high cost is by the development of a cheaper alternative or complement. Recycling and reuse of waste paper as a complementary or alternative material in the fabrication of speaker woofer provides an avenue for cost minimization. The current study focused on readily available materials in the development of paperboard from the recycling of waste paper, banana fiber, and snail shell powder using cement as the binder. The outcome of the study showed that a possible alternative speaker woofer/casing board material can be developed with the use of waste paper.
1. Introduction
Speaker woofers are often made from particleboards and with increasing use of the boards in the production of the woofers, prices keep escalating owing to the high cost of binder and high cost of the processing route in terms of energy consumption and equipment maintenance. A consequence of such reflects in the high cost of end-use electronic gadgets. A way of tackling the high cost is by the development of a cheaper alternative or complement. Recycling and reuse of waste paper as complementary material in the fabrication of speaker woofer provides an avenue for cost minimization. Cement–paperboards are boards made from a blend of cement and paper pulp. One way of recycling this paper waste is by its use in the production of cement–paperboards (Zaki et al., Citation2019). Cement–paper composites are cast into molds and allowed to undergo curing for specific days after which they can be trimmed and employed for different applications (Subramani & Angappan, Citation2015). Up to 450 million tons of paper are generated globally every year and analysts claimed; a rise to 500 million tons at the end of 2020 was expected (Ali et al., Citation2013). From this fact, there is a tendency for an abundance of waste paper which can be recycled for different beneficial applications. Cement–paper composite is used as papercrete and paperbricks due to lightweight, thermal insulation, and impact resistance (Akinwande et al., Citation2021; Khandelwal et al., Citation2015), for soundproof applications based on sound insulation properties, for furniture in homes, and wall partitioning (Zhu et al., Citation2013). Owing to the good thermal and noise insulation characteristics, paperboards can be a good alternative in the development of materials for speaker/woofer casings/boxes and as such, this study aimed at the development of paperboards for such use. Speaker boxes must be strong, stiff, attractive, affordable, light, have high resonance, good damping property, and high strength-to-weight ratio (Drotleff & Zhou, Citation2001). This study, therefore, investigated the physio-mechanical properties of cement–paper composites reinforced with banana fiber and snail shell (African giant snail) powder. The selection of cement as a binder in the composite development is traced to the binding prowess of cement (Dunuweera & Rajapakse, Citation2018; Qi et al., Citation2016) coupled with long-term strength impartation ability. Similarly, cement introduction enhances bond strength based on hydrate formation (Dybel & Walach, Citation2017), effectuating the long-term strength and durability of material (Suganya & Rajkumar, Citation2018). In comparison with particle board in which wood particles are bounded by urea-formaldehyde, cement-bonded paperboards tend to pose higher strength and by extension longevity in service. Natural fibers like bagasse (Balaji et al., Citation2018), banana (Balaji et al., Citation2020a), coir (Andi-Cakir et al., Citation2014), sisal (Silva et al., Citation2010), and others have been utilized to reinforce base materials for different applications. Balaji et al. (Citation2019) developed hybrid polymer composites reinforced with sisal/banana/coir fiber effect of which led to property enhancement of epoxy matrix. Banana fibers are processed from the trunk of banana trees (). Banana (Musa spp.) is produced in 133 countries of the world, with over 130 million tons produced annually (Olumba & Onunka, Citation2020). Plantation is carried out on 9.52 million hectares with India and China leading (Nayar, Citation2010). In Africa, the plant is cultivated in 41 countries according to Idicula et al. (Citation2004), hence banana fiber can be in abundance with adequate production techniques. The choice of banana as fiber () reinforcement in this study is based on its relatively high mechanical properties and strength to weight ratio (Vidyasri et al., Citation2019). The lignocellulose fiber has found application in various research which include polymers (Barragan-Lucas et al., Citation2018; Idicula et al., Citation2010, Citation2004; Rashid et al., Citation2020), concrete, and bricks (Kumaat et al., Citation2018; Mostafa & Uddin, Citation2015), and particle board (Barragan-Lucas et al., Citation2018). The results of the investigations proved banana fiber to be a good reinforcement in the matrix as reported by Balaji et al. (Citation2020b), giving an impetus for its use in this study.
Alkaline treatment of these fibers was employed for fiber surface modification as concluded in Hashim et al.(Citation2017) and Ramli et al. (Citation2017), in which alkaline treatment was reported to evoke higher property enhancement in the composite matrix when compared with the untreated counterpart. Previous studies (Ahmad et al., Citation2019) showed that modification of fiber surface exposes the rough surface which enhanced wetting of fiber with the matrix. On this premises, 5% NaOH solution was employed in surface modification as adopted by Udhayasankar et al. (Citation2019) onto investigating the influence of alkaline treatment on the properties of the composite developed. Paper pulp is a porous engineering material (Gronquist et al., Citation2014) that readily absorbs water owing to inherent capillary pores. Also, cellulose present is a complex long-chain polymer molecule that has OH− ion attached to the end of the chain and readily attaches to OH− group in the water thereby absorbing water (Kalia et al., Citation2011). The hydrophilicity makes paper highly prone to water uptake (Drelich et al., Citation2011). Understanding of this point initiates the need for fillers, to reduce porosity in the pulp; of which the filler must be less susceptible to water. Snail shell powder has high CaO content (Kaewdaeng & Nirunsin, Citation2019) and is employed as fillers in various applications including polymer and concrete (Ketebu & Farrow, Citation2017; Onuegbu & Igwe, Citation2011). These shells are gotten as a waste by-product after the snail content has been removed. Use of this snail shell was noticed to result in enhancement of properties of composite developed as reflected in Syamimi et al. (Citation2019) and Oladele et al. (Citation2020) for polymer and concrete (Ayodele & Popoola, Citation2019; Olivia et al., Citation2015). Amu et al. (Citation2019) revealed that pulverized snail shell ash enabled pozzolanic reaction, enhancing the formation of calcium silicate hydrate (C–S–H) in cement stabilized laterite; and further confirmed in investigations of Adetayo et al. (Citation2019) and Oyejobi et al. (Citation2019). Based on the outcome realized in those investigations, snail shell powder (African giant snail) was employed as filler in this study for property enhancement of paper-cement composite by blending with the varied proportion of banana fiber (untreated and treated).
2. Materials and methods
Materials used are waste paper, cement, snail shell, and banana fiber. Reagents employed are distilled water and 1 M NaOH solution. Waste cardboards were shredded with the use of a paper shredder and transferred into a container. Water is added and allowed to soak for 7 days after which the “wet-paper” was transferred into a paper pulp grinder and ground to produce waste paper pulp. Afterward, the slurry was poured into a sack and pressed under 10 MPa for water to drip off before been packed in another clean container and air-dried for 20 days (). Snail shell obtained from a local merchant was thoroughly washed with distilled water and dried in an autoclave at 50°C for 2 hours. Sequel to this was the milling and pulverization of the shell; then sieving to −45 µm. The snail powder () was further heated in the autoclave at 50°C for 24 hours. Natural banana fiber obtained from the merchant was washed in distilled water and in the presence of detergent, to remove impurities attached to the fiber. Fifty percent of the fiber was subsequently treated with 1 M sodium hydroxide by immersing the fibers in the solution for 12 hours maintained at 40°C, after which they were removed, washed with distilled water, and air-dried for 3 days. The treated fibers were labeled treated banana fiber (TBF) while the untreated were classified as untreated banana fiber (UBF). Ordinary Portland cement employed as a binder was obtained from a local merchant and examined for properties in line with ASTM C150/C150M-20 (Citation2020) and examined to conform with IS Citation8112 (2013) standards.
Samples were produced by blending paper pulp with 15 wt.% of cement (by weight of paper pulp), 15 wt.% (by weight of paper pulp) snail shell powder and varied amount of banana fiber addition (cut to 30 mm length) at 0, 0.5, 1, 1.5, 2, and 2.5 wt.% (for untreated and treated) as indicated in . The choice of 0, 0.5, 1, 1.5, 2 and 2.5 wt.% of the fiber is on account of feat reported in (Akinwande et al., Citation2021). The blend was mixed manually in a container, in the dry state after which water was added at a water–cement (w/c) ratio of 0.35, with subsequent mechanical mixing. The slurry was transferred into prepared cuboid moulds of dimension 150 × 100 × 30 (mm3), 150 × 75 × 30 (mm3) and 100 × 30 × 30 mm3. The pressure of 5 MPa was applied on samples for 5 minutes to ensure sufficient compaction of the blend. Fresh board samples were covered with a polythene sheet and left to cure for 28 and 56 days (ASTM C192/C192M-19, Citation2019). These samples were tested for physio-mechanical and microstructural properties after the curing process.
Table 1. Mix proportion in composites samples
3. Experimental procedure
A preliminary test was carried out on materials used which involve microstructural examination of the untreated and TBFs, and snail shell particulate. Ordinary Portland cement used was tested for specific gravity, fineness, setting time, and soundness in line with ASTM D5965–19 (Citation2019), IS Citation4031-1 (1996), ASTM C403/C403M-16 (Citation2016), and IS Citation8142 (1976), respectively. Test carried out on samples include water absorption, thickness swelling, internal bond strength, screw holding strength, and bending test which entailed moduli of rupture and elasticity. Three samples representing each mix proportion were utilized for each test and the average result obtained was recorded. Water absorption and thickness swelling were investigated in consonance with ASTM D7433–19 (Citation2019) and TSE-TS EN 317 (Citation1999), respectively. Samples of dimension 150 × 100 × 30 mm3 were initially weighed when dry as M1 and immersed in water for 24 hours. Saturated mass after 24 hours’ immersion was weighed as M2 and water absorption evaluated using EquationEquation (1)(1)
(1) . Likewise, thickness swelling was assessed by initially measuring the thickness (t1) of the board samples before been immersed in water for 24 hours. Thickness at the water-saturated point after 24 hours was measured as t2 and percentage swelling was probed using EquationEquation (2)
(2)
(2) . According to ASTM D Citation5651–13 (2013) internal bond strength was examined by gluing metal plates to both sides of the board samples. The boards were then pulled across the surface using a universal testing machine (Tensilon RTG-1250). As per IS 2380–14, samples of 150 × 75 × 30 mm3 were tested for screw holding strength with the head of the screw facing up which was driven at 1.5 mm/min on the screw testing machine. Evaluation of the bending strength was done on samples of dimension 100 × 30 × 30 mm3 using the universal testing machine as per IS 2380–9 at a loading speed of 10 mm/min and measured by a three-point bending test method. Furthermore, property values obtained were subjected to experimental trend analysis and performance evaluation as carried out in Akinwande (Citation2020) and Akinwande et al. (Citation2021) to evaluate efficiencies of experimental variables in this study; which are fiber addition, alkaline treatment, and curing/hydration period.
Materials used in the study were tested for their inherent properties as indicated in .
Table 2. Properties of Cement
Table 3. Chemical composition of snail shell powder additive
Table 4. Chemical composition of treated and untreated banana fiber
shows the chemical composition of snail shell powder additive while shows the properties of ordinary Portland cement utilized in the preparation of samples.
Chemical and elemental composition was carried out on banana fiber and snail shell powder coupled with surface morphology of snail shell powder as well as that of UBF and TBF fibers and results are as expressed in for snail shell powder, for the chemical composition of the fibers used and for the surface morphology and EDAX result.
X-ray fluorescence test revealed that Silica (SiO2) is present in snail shells at an amount of 14.98% (), which contributes to matrix strengthening as expounded in Vaiciukyniene et al. (Citation2012). Oladele and Isola (Citation2016) and Oladele et al. (Citation2016) also indicated that CaO presence in particulates introduced into epoxy amount to the strengthening of composite developed. highlights the chemical composition of banana fiber in the untreated state and after alkaline treatment. Distinct properties noted were in the increment in cellulose content from 61.4% in the untreated to 72.61% after treatment. Other contents of hemicellulose, lignin ash, and moisture content were reduced after treatment. shows the surface morphology of (a) untreated banana fiber and (b) treated banana fiber. ) reveals a smooth surface of the fiber owing to impurities adhesion by wax over the surface of the fiber. Alkaline treatment led to the removal of this wax and impurities exposing the rough surface of the fibers; getting ready for adhesion to the matrix (). Microstructural image and EDX analysis of snail shell powder areas revealed in with calcium taking the largest share, while silicon was 13.6%. The presence of these elements in such proportion presents promising properties in terms of strength enhancement of developed samples.
4. Results and discussion
In the course of the discussion, some abbreviations are made UBF represents untreated banana fiber, TBF represents alkaline treated banana fiber while BF represents banana fiber.
4.1. Properties of developed composites
4.1.1. Water absorption (24 hours immersion)
The variation in water absorption at curing days are as presented in for (a) 28 days and (b) 56 days with (c) experimental trend index (d) efficiency values of the experimental variables
Figure 5. Variation in water absorption at curing days of (a) 28 days and (b) 56 days with (c) experimental trend index (d) efficiency values of the experimental variables
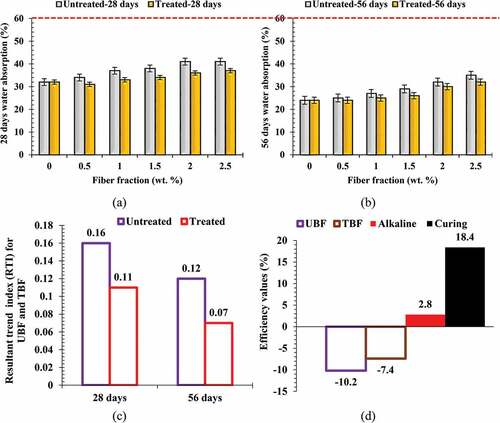
Effect of fiber loading and curing days on water absorption of banana fiber/snail shell powder reinforced cement–paper composite is as highlighted in . Water absorption increased with banana fiber loading from 0 to 2.5 wt.%, which is also confirmed by Prasad et al. (Citation2016), who reported increased water absorption with increasing fiber loading. The uptrend in water uptake is linked to the hydrophilic nature of the fiber and pulp. Natural fibers contain cellulose, hemicellulose, and lignin hence readily absorb water owing to the hydroxyl functional group (Clemon, Citation2002; Li et al., Citation2007; Tanasa et al., Citation2019). Comparing treated and untreated fiber, samples reinforced with treated fiber absorb lesser water than the ones with untreated fiber. This can be credited to stronger and better wettability between TBF and the matrix compared with the untreated (Mohd Nazarudin et al., Citation2013). On the other hand, water absorption reduced gradually with curing ages for both UBF and TBF. Higher curing age results in less water absorption tendency. This feat occurred on the dint of formation of stable hydrates during the curing process. The hydrates fill in pores within the matrix thereby lessening water uptake tendencies. Also, the C–S–H phase formed enhances interfacial adhesion between BF and paper matrix; forming a water-impermeable coat (Wang et al., Citation2018). The results obtained in this study ranged between 32% and 42% and the trend slightly similar to the findings of Shawia et al. (Citation2014), in which values lied between 10.7% and 40.6% for cement boards reinforced with natural fibers. Results reported are lower than values of 80% reported by Hosseinpourpia et al. (Citation2017). In line with IS Citation3087 (Citation2005), samples containing 0–1.5 wt.% BF (cured for 28 days), 0%–2% BF (cured for 56 days) have water absorption value less than 40 %. In the same way, samples loaded with 0–2.5% BF which were cured for 28 and 58 days also met the requirement. Going by ASTM D1037–12 (Citation2012), all samples tested had below 60%, and are fit for general-purpose particleboard and speaker/woofer casing.
Experimental trend analysis and performance evaluation on water absorption.
explains the trend index for water absorption at 28 and 56 days. Coldwater absorption was reduced at 28 days period, for samples containing both UBF and TBF. The resultant trend index for UBF-28 and TBF-28 are +0.16 and +0.11 indicating an uptrend direction, in that water absorption rose with fiber loading and contrary to the course of the investigation since a reduction in water absorption is the target. The trend difference, therefore, is −0.05 [57.7° cw] implying a positive influence of alkaline treatment resulting in a downward trend of water absorption on the incorporation of TBF. Likewise, under the 56-curing age, the trend index is +0.12 for UBF and +0.07 for TBF; a trend difference of −0.05 [75° cw] implying that the introduction of TBF gave a reduction in water absorption. The resultant direction index over curing days as per untreated and treated fiber is +0.01 [50° cw] for the 28th day and +0.09 [53° cw] for the 56th day. The implication of this is; alkaline treated BF coupled with curing produced a positive result than untreated on water uptake property of developed composite.
Analysis of the performance of experimental variables () depict efficiency values of 10.2 % [−] for untreated alkaline addition to cement–paper matrix; that is, UBF was 10.2% efficient in increasing water absorption. The efficiency is negative since increasing water absorption is detrimental to the purpose of this work as long as a reduction in water absorption is a target. Alkaline-TBF presented an efficiency of 7.4 % [−], implying 7.4 % efficiency in water absorption. Comparing these two experimental variables of untreated and treated fiber addition, it can be inferred that alkaline treatment reduced negative water absorption efficiencies in fiber-reinforced composites as reflected in the lower negative value of TBF efficiency. Further evaluation revealed; NaOH treatment of banana fiber was 2.8 % [+] in reducing water absorption while curing duration is 18.4 % [+] effective in reducing water absorption. From these efficiency values, curing duration is inferred to be the most efficient experimental variable for water absorption.
4.1.2. Thickness swelling
The swelling was discovered to increase as fiber loading increased. This observation is similar to the experience reported underwater absorption. The increase in swelling is attributable to water uptake by the composite causing swelling. With lengthened curing days, it was observed that thickness swelling depreciated gradually. A strong bond formed with the matrix as a result of the formation of more stable C–S–H phases, over curing ages, lower water penetration, and consequently, reduced swelling. Treated BF was noted to give better performance than the untreated in that thickness swelling value is lower in the case of TBF when compared with UBF. Just as indicated under water absorption, increased wetting is held responsible for the observation. Besides, lowering of hemicellulose and lignin content via alkaline treatment led to a reduction in free OH− ion (Sawawi et al., Citation2020), which resulted in diminished interaction between fiber and water molecules effectuating reduced water intake. Values attained by thickness swelling are lower than values recorded by Hassan et al. (Citation2020), which had a maximum value of 28.99%. Values obtained in this study ranged from 24 down to 12%, a result similar to the outcome of Pan et al. (Citation2007). Thickness swelling of less than 25% was recommended for general use in line with ASTM D1037–12 (Citation2012) stipulations. Therefore, all samples produced met the standard.
Experimental trend analysis and performance evaluation on thickness swelling.
From , it was observed that the resultant trend index for UBF- and TBF-reinforced composites cured for 28 days are +0.21 and +0.14 reflecting the upward trend in thickness swelling. The difference in trend index is −0.07 [60° cw] indicating a decrease in thickness swelling on the addition of TBF 56 days curing reflecting +0.18 and +0.11 resultant trend index for UBF and TBF reinforced composites. This results in a trend difference of −0.09 [16.2° cw] between UBF and TBF; which depicts a downtrend in thickness swelling by blending of TBF in the composite matrix. The resultant trend difference magnitude for 56 days is +0.05 [50° cw] for untreated BF and −0.12 [53° cw] for treated with resultant trend difference magnitude of −0.07 [252° cw] indicating a downward direction in thickness swelling across the curing ages.
Figure 6. Variation in thickness swelling at curing days of (a) 28 days and (b) 56 days with (c) experimental trend index (d) efficiency values of the experimental variables
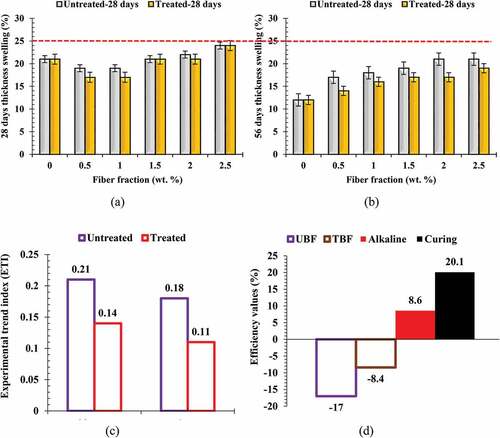
Evaluation of the experimental variables () reveals UBF was 17% [−] efficient in increasing thickness swelling. TBF yielded 8.4% [−] efficiency in increasing thickness swelling, which is detrimental to the purpose of the investigation (a reason for the negative signs). Nonetheless, alkaline treatment of the fiber gave 8.6% [+] efficiency in lowering thickness swelling and this explains the reason for the 8.6% efficiency of TBS. Curing duration reflected the highest efficiency of 20.1% [+] in minimizing thickness swelling.
4.1.3. Internal bond strength (IBS)
: Variation in internal bond strength at curing days of (a) 28 days and (b) 56 days with (c) experimental trend index (d) efficiency values of the experimental variables.
Results of internal bond strength (IBS) of composite developed is as indicated in . IBS was realized to rise gradually with fiber loading. TBF was further observed to perform better than UBF as per bond strength. Alkaline treatment was reported to cause some disruption in hydrogen bonding within cellulose structure (Suryanto et al., Citation2014) effectuating fiber surface roughness. Enhanced rough surfaces in fiber enable interfacial wetting of fiber to matrix eventually promoting bond strength. As curing days increased, there was a proportional rise in IBS linked to a stronger matrix formed. Abdullah and Lee (Citation2016) attributed the enhancement in strength to the presence of cement; being a good binder and with lengthened curing ages, the bond becomes stronger, the reason for higher IBS value at age of 56 days as compared with 28 days. Findings from Hassan et al. (Citation2020), Sekino and Korai (Citation2018), and Tay et al. (Citation2016) corroborated observations made in this study. In line with BS EN 312-Citation2010 (2016), 0.24 MPa is acceptable for general purpose boards. In that case, all samples fit in for use as general-purpose boards as well as speaker/woofer casing.
Experimental trend analysis and performance evaluation on internal bond strength.
explains the trend index for internal bond strength at 28 and 56 days. Internal bond strength progressively for samples containing both UBF and TBF cured for 28 and 56 days. The resultant trend index for UBF-28 and TBF-28 are +0.22 and +0.26 indicating an upward trend direction in that internal bond strength was enhanced with increasing fiber loading. Trend difference, therefore, is +0.04 [18° cw] implying the positive influence of alkaline treatment in improving bond strength of cement paper board composite. Considering curing age of 56 days, the trend index is +0.29 for UBF and +0.47 for TBF; a resultant trend difference of +0.18 [223° cw] implying enhancement in bond strength by alkaline treatment of banana fiber. The resultant trend difference over curing days are +0.69 [119° cw] and +0.83 [65° cw] for UBF and TBF respectively signifying a trend difference magnitude of +0.14 [73° cw].
Evaluation of the experimental variables () shows UBF was 14.7 % [+] efficient in improving internal bond strength. TBF performed better in that it was 21.8% efficient in improving the strength depicting alkaline treatment amounted to a 7.1% enhancement of internal bond strength. Curing duration had the highest efficiency of 32.5% in enriching internal bond strength.
4.1.4. Surface screw holding strength (SSHC)
Screw holding strength was evaluated on the surface of the board to appraise the withdrawal strength of the board. As presented in , surface holding strength was observed to rise with higher fiber content for both untreated and treated BF, an attribute linked to increased internal bond strength and fiber attachment to the matrix. Maail (Citation2006) utilized core-kenaf in semen gypsum board and the value of screw holding strength rose with increasing autoclave and conventional curing duration. Similar behavior was exhibited in this study in that the curing age amounted to a higher strength value. In Maail (Citation2006), the strength varied from 0.105 to 0.2024 kN a bit lower than values reported in this report, SSHS varied from 0.243 to 1.466 kN. The discrepancy can be associated with a stronger cement matrix as compared with the gypsum matrix. It was noted that, as indicated in , higher values were recorded under 56 days relative to the values observed under 28 days of curing age. In line with ANSI 208. 1 (Citation2009), 1000 N is the standard requirement for surface screw holding strength inferring that samples are reinforced with 1–2.5 wt.% UBF and TBF satisfied the prescription.
Experimental trend analysis and performance evaluation on the surface screw holding strength.
Figure 7. Variation in surface screw holding strength at curing days of (a) 28 days and (b) 56 days with (c) experimental trend index (d) efficiency values of the experimental variables
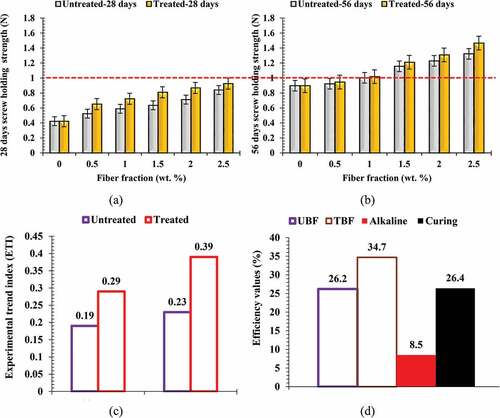
highlights the trend index for screw holding strength at 28 and 56 days. The strength increased consistently for samples containing both UBF and TBF. The resultant trend index for UBF-28 and TBF-28 are +0.19 and +0.29 indicating an uptrend in strength with a rise in fiber loading. Trend difference of +0.10 [128° cw] implies the positive influence of alkaline treatment amounting to an uptrend in strength on account of alkaline treatment. Also, under the 56 day-curing age, the trend index is +0.23 for UBF and +0.39 for TBF; a trend difference of +0.16 [125° cw] alluding to the fact that introduction of TBF gave enhancement in strength. The resultant direction index over curing days are +1.27 [199° cw] and +1.69 [272° cw] for UBF and TBF, respectively, with a trend magnitude difference of +0.42 [59.5° cw]. The implication of this is; alkaline treated BF coupled with curing produced a more positive result than untreated in optimizing screw holding strength of the developed composite.
Examination of experimental variables () depicts efficiency values of 26.2% [+] for untreated alkaline addition to cement–paper matrix; that is, UBF was 26.2% efficient in increasing the strength, positive since property maximization is the target for developed composite. Alkaline TBF presented an efficiency of 34.7% [+], implying 8.5% efficiency in improving screw holding strength while curing duration is 26.4% [+] effective in reducing water absorption. From these efficiency values, it can be deduced that curing duration is the most efficient experimental variable.
4.1.5. Modulus of rupture (MOR)
The outcome showcased for MOR in this study () presented increasing values of MOR at additional fiber loading which can be linked to an improvement in internal bond strength recorded between 0 and 2.5 wt.% BF. TBF performed better than UBF owing to increased cellulose crystallinity (Wu et al., Citation2011). According to Zheng et al. (Citation2012), NaOH treatment tears down the amorphous portion thereby promoting cellulose crystallinity, a consequence of which evokes improvement of bonding in the composite. A study carried out by Cao et al. revealed improvement in MOR with alkaline treatment. The strong interfacial adhesion between fiber and matrix promotes even stress distribution within the matrix.
Figure 8. Variation in modulus of rupture at curing days of (a) 28 days and (b) 56 days with (c) experimental trend index (d) efficiency values of the experimental variables
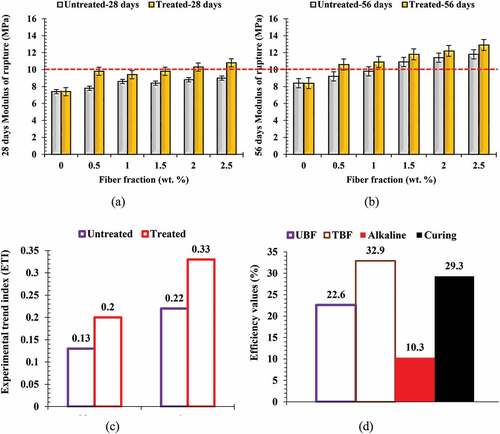
Curing ages also contributed to the enhancement of the modulus of rupture (Yeon et al., Citation2019). As days of curing rose, hydration reaction continued, producing more hydrates, the fallout of which amounted to a boost in strength. Standard values indicated by IS Citation3087 (Citation2005): is 10 MPa, therefore, samples blended with 2 and 2.5 wt.% TBF (cured for 28 days), 1.5–2.5% UBF (cured for 56 days) and 0.5–2.5% (cured for 56 days) satisfied the requirement. It can be observed that with higher curing ages, more samples met the requirement affirming the importance of curing in cement paperboards.
Experimental trend analysis and performance evaluation on the modulus of rupture (MOR).
From , it was revealed that resultant trend index for UBF and TBF reinforced composites cured for 28 days are +0.13 and +0.2 reflecting the upward trend in modulus of rupture; with a trend difference value of +0.07 [96.9° cw], depicting improvement in MOR on the addition of TBF. 56 days curing reflects +0.22 and +0.33 resultant trend index for UBF and TBF reinforced composites. This resulted in a trend difference of +0.11 [90° cw] between UBF and TBF connoting a rise in MOR by the blending of TBF in the composite matrix. The resultant trend difference magnitude for samples cured for 56 days is +0.39 [83° cw] as regards untreated BF and +0.50 [53° cw] for treated BF with resultant trend difference magnitude of +0.11 [50.8° cw] revealing an uptrend in MOR across all curing days.
Evaluation of the experimental variables () reveals UBF was 22.6% [+] efficient in increasing MOR. TBF gave 32.9% [+] efficiency in enhancing MOR which is beneficial to the purpose of the investigation (a reason for the positive + signs). Additionally, alkaline treatment of the fiber yielded 10.3% [+] efficiency in optimizing MOR while curing duration reflected the highest efficiency of 29.3 % [+] in maximizing the modulus of rupture of composite developed.
4.1.6. Modulus of elasticity (MOE)
Similar to MOR, MOE improved progressively with fiber loading which can be associated with the flexibility and stretching ability of the fiber. Putting curing age into perspective, curing age of 28 days produced a higher value for MOE than 56 days () and it’s based on the hardened matrix, decreasing flexibility of the fiber. The value obtained in this study between 28 and 56 days is in tandem with the findings of (Chen et al., Citation2015; Yano et al., Citation2020) though contrary to the investigation of Atuanya et al. (Citation2011). ABNT NBR 14810-2 (Citation2018) stipulates 1.8 GPa for MOE, therefore, composite samples reinforced with 2 and 2.5% TBF (cured for 28 days) met the requirement. MOE in this study lies between 1.54 and 1.94 MPa, which falls within the values reviewed by Batiancela et al. (Citation2003) for natural fibers reinforced boards.
Experimental trend analysis and performance evaluation on the modulus of elasticity (MOE).
Figure 9. Variation in modulus of elasticity at curing days of (a) 28 days and (b) 56 days with (c) experimental trend index (d) efficiency values of the experimental variables
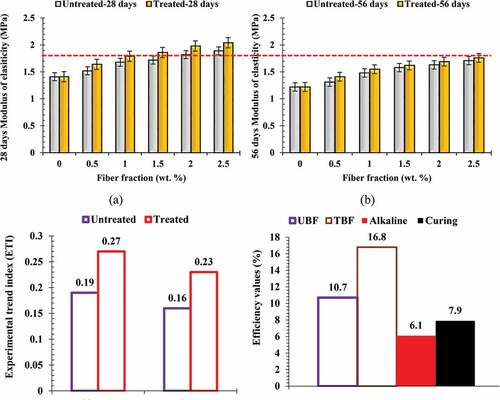
The resultant trend index as highlighted in indicates that the trend index for UBF and TBF reinforced composites which were cured for 28 days are +0.19 and +0.27 and going by the values, the trend difference between UBF and TBF under 28-day curing age is +0.08 [75.8° cw]. Under 56 curing age, the trend index for UBF is +0.16 and that of TBF is +0.23 with a trend difference of +0.07 [78.8° cw].
Evaluation of the experimental variables () reveals UBF was 10.7% [+] efficient in enhancing MOE, while TBF kindled 16.8% [+] efficiency in enhancing modulus of elasticity. Alkaline treatment of the fiber yielded 6.1% [+] efficiency in improving the modulus of rupture. Curing duration reflected an efficiency of 7.9% [+] indicating that curing is the least contributor in enhancing modulus of elasticity.
From the table, curing is the most efficient experimental variable.
depicts the efficiencies of each experimental variable as per each property examined. The blending of NaOH alkaline TBF gave the highest efficiency of 34.7% for screw holding strength, with an alkaline treatment efficiency of 8.5% over untreated fiber. A consequence of this lies in the fact that alkaline treatment of banana fiber significantly boasts the screw holding strength of the composite board. Curing duration is the highest in the case of water absorption, thickness swelling, and internal bond strength with values of 18.4% [+], 20.1% [+], and 32.5% [+] respectively. From this result, curing is the most significant experimental variable in reducing water uptake and thickness swelling and conversely efficient in improving bond strength of the composites produced. As for screw holding strength, modulus of rupture, and modulus of elasticity, TBF had the most significant impact in that it was 34.7% [+], 32.9 % [+], and 16.8% [+] efficient for each property accordingly. Hence, alkaline treatment has a colossal impact in boasting the aforementioned properties for paperboard.
Table 5. Experimental variable efficiency table
Overall, as presented in , efficiency values of 6.95% [+] and 19.07% [+] were obtained for UBF and TBF addition to the composites, depicting alkaline efficiency of 12.2% [+]. Curing was evaluated to be 28.9% [+] efficient in the overall been the most significant variables as far as this research is concerned. Therefore, curing stays as the most effective variable input in enhancing optimum properties of banana fiber/snail shell powder paperboard, and in conjunction with that NaOH treatment of fiber has great relevance in property enhancement.
4.2. Optimization: compliance and property indices
Compliance index was evaluated as implemented in Akinwande (Citation2020), and was computed by initially comparing property value for each sample tested with values stipulated in the standards. In cases where property value satisfied existing standards, 1 was applied in , and 0 was used for property values that fell short of the standard. The procedure expressed in Akinwande (Citation2020),; Akinwande et al. (Citation2020), and Folorunso and Akinwande (Citation2021) was followed in evaluating the compliance index using Equation (3) EquationEquation (1)(1)
(1) .
Table 6. Response index for composites in comparison with standard values
From , all compliance index of above 0.5 was attained on the incorporation of 0–2.5wt.% of both UBF and TBF in the cement–paper matrix. The implication of this is that a minimum of 50% compliance level with 6 existing standards adopted for comparison in this study was attained on the incorporation of 0–2.5 wt.% fiber to cement–paper composite. The highest compliance index of 0.83 (83% compliance with all standards adopted in the study) was observed with samples reinforced with 2 and 2.5 wt.% TBF (cured for 28 days), 1.5–2.5 wt.% UBF (cured for 56 days) and 1–2.5 wt.% TBF (cured for 56 days). To analyze for optimum mix, further evaluation involves evaluation of the effective property index as evaluated in (Akinwande, Citation2020) using EquationEquations (3)(3)
(3) and (Equation4
(4)
(4) ). EquationEquation (3)
(3)
(3) was employed for properties whose higher value is favorable for the proposed application while EquationEquation (2)
(2)
(2) was employed for properties whose lower value is beneficial for the same application. Effective property index was obtained via EquationEquation (5)
(5)
(5) .
Table 7. Compliance index of composites reinforced with fiber proportion (0–2.5%)
From , the highest EPI of 0.9 was attained when 2.5 wt.% TBF was incorporated into cement–paper composite which was cured for 56 days. It was noted that with increasing fiber loading, EPI appreciated emphasizing the relevance of fiber inclusion in enhancing the properties of the paper-cement board. Similarly, TBF produced better performance when compared with their untreated counterpart. It was also noted that curing ages contributed to performance enhancement in that EPI had higher values under curing age of 56 days than 28 days. The Highest EPI of 0.9, 0.87, 0.85, and 0.84 was obtained under 56 days of curing for alkaline TBF (in 2.5, 2, 1.5, and 1 wt.%, respectively) affirming that alkaline treatment is beneficial for composite development. These observations are in the fact that the experimental variables are important for property enhancement with curing been the most efficient as confirmed in .
Table 8. Effective Property Index (EPI) of developed composite reinforced with 0–2.5 wt.% UBF and TBF
highlights a reflection of the impact of both untreated and alkaline treatment banana fiber on mean property indices of composites at 28 and 56 days curing ages. ) reflects the mean property index which revealed the fact that fiber loading 0–2.5 wt.% ensured resultant property enhancement amounting to increasing mean property index over the days, even as alkalineTBFs outperforming the untreated fibers.
Figure 11. Measurement of alkaline treatment and curing potential through (a) mean property index (b) efficiency of alkaline treatment and hydration
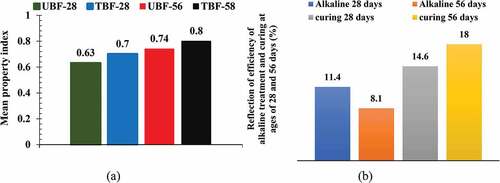
Comparing the values, property enhancement by input processes of alkaline treatment and hydration as represented for both 28 days and 56-day curing lengths (). TBF outpaced UBF by 11% for a curing period of 28 days while for 56 days period, TBF outperformed by 8.1%. By implication, alkaline treatment on the 28th day yielded better performance than 56 day period. That is alkaline treatment is more efficient in enhancing the overall property of developed composite when the curing period is 28 days than when extended to 56 days. On the other hand, the effect of hydration/curing as reflected for the two curing ages showed that hydration at 56 days outperformed hydration/curing at 28 days. From this 56 days curing better improved overall properties when compared with 28 days. Also going by the values, 56 days curing manifested the highest efficiency; therefore, hydration is more efficient in achieving mean property improvement than alkaline treatment though the two are significantly important for property enhancement.
5. Microstructural analysis
reflects the microstructural images of samples compliance index of 0.83 (83% compliance level) and were reinforced with 1–2.5 wt.% TBF; cured for 56 days. Common features among the four images is the banana fiber having strong interfacial adhesion with the paper matrix, a consequence of the strong adhesion reflected in the enhancement of properties of the samples, the aftermath of which resulted in 83% compliance and effective property index (EPI) of 0.84, 0.85, 0.87, and 0.9. Another significant feature highlighted in the images is the distribution of snail shell particles which partially filled pores amounting to a reduction in water absorption and thickness swelling. These particles also led to the enhancement of mechanical properties. reveales the high magnification fluorescence sketch of paperboard composite revealing different features at the microstructural level.
6. Conclusions
Cement–paper composites were developed by the incorporation of untreated and alkaline (1 M NaOH) TBF (0.5%, 1%, 1.5%, 2%, 2.5% by weight of paper pulp) and snail shell powder into a cement–paper matrix in the view to developing paperboard material for speaker/woofer casings. The following conclusions were arrived at:
i. Water absorption, thickness swelling increased slightly with untreated and alkaline TBF.
ii. Internal bond strength, screw holding strength, modulus of rupture, and modulus of elasticity appreciated progressively with untreated and alkaline TBF.
iii. Alkaline treated was observed to be effective in property enhancement of composites owing to the higher performance of TBF over the untreated counterpart; depicted by alkaline efficiency of 12.12% [+].
iv. Results of the experimental trend analysis indicated that the overall efficiency of alkaline treatment is 12.12% [+] and curing is the most efficient experimental variable with a value of 28.9% [+].
v. Performance evaluation showed that the highest performance index of 0.9 was realized for composite samples doped with 2.5 wt.% alkaline TBF.
vi. Optimum mix proportion was 2.5 wt.% TBF, 15 wt.% snail shell powder, 15 wt.% cement and 67.5 wt.% waste paper pulp.
vii. The developed composite can also find applications as ceiling tiles and furniture. The results realized in this paper show that alternative speaker/woofer casing can be developed by recycling papers with snail shell powder. The same alternative material can be further investigated in the development of ceiling boards, automobile dashboards, and household furniture.
Additional information
Funding
Notes on contributors
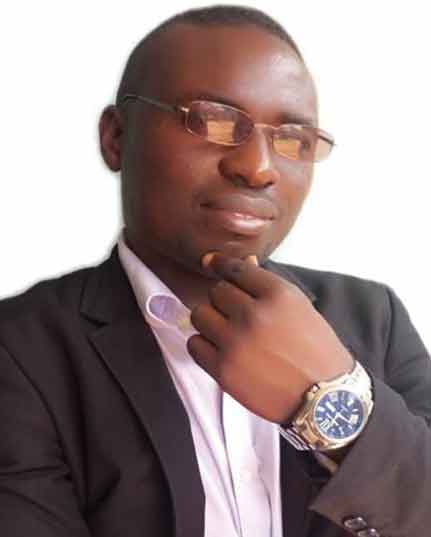
Adediran Adeolu Adesoji
Abayomi Adewale Akinwande possesses a bachelor’s degree from the Department of Metallurgical and Materials Engineering, Federal University of Technology, Akure, Ondo State, Nigeria where he also barged his Master’s degree (Advanced materials engineering option). His research interests include waste recycling and management, advanced materials and composite development, engineering economics, cement, and structural materials development, mechanical behavior of materials, and failure analysis. He has authored over 20 papers published locally and internationally and is he’s currently engaging in series of research works.
References
- Abdullah, A. C., & Lee, C. C., 2016. Effect of treatments on properties of cement –fiber bricks utilization rice husk, corncob and coconut coir. Int. High-Performance Built Environment Conference- A Sustainable Built Environ. Conf. 2016 Series (SBE16), iHBE 2016.
- ABNT NBR 14810-2. (2018). Associacao Brasileira de Normas tecnicas. Medium Density Particleboards Part2: Requirement and Test Methods. Sao Paulo.
- Adetayo, O., Amu, O., & Alabi, S. (2019). Improvement of Cement Stabilized Structural Lateritic with Pulverized Snail Shell. Journal of Civil Engineering, 14, 95–23. https://doi.org/10.1515/sspjce-2019-0021
- Ahmad, R., Hamid, R., & Osman, S. A. (2019). Physical and chemical modifications of plant fibres for reinforcement in cementitious composites. Advances in Civil Engineering, 2019(4), 18. Article ID 5185806. https://doi.org/10.1155/2019/5185806
- Akinwande, A. A. (2020). Evaluation of the property values of coir-fiber reinforced cement stabilized bricks applying experimental trend/performance analysis (Akinwande’s Approach). International Journal of Advanced Academic Research, 6(9), 90–118. https://doi.org/10.46654/ij.24889849
- Akinwande, A. A., Adediran, A. A., Balogun, O. A., Olasoju, O. S., & Adesina, O. S. (2021). Influence of alkaline modification on selected properties of banana fiber paperbricks. Scientific Reports, 11(1), 1–18. https://doi.org/10.1038/s41598-021-85106-8
- Akinwande, A. A., Barnabas, A. A., Alao, A. O., Balogun, O. A., & Shittu, S. A. (2020). Jute/egg Shell Biofiller reinforced cement-paper composite as sustainable materials for application in automobile dashboard: Experimental Performance Analysis (EPA). International Journal of Advanced Acad. Res, 6(9), 81–89. https://doi.org/10.46654/ij.24889849.e6917
- Ali, A., Hashmi, H. N., & Baig, N. (2013). Treatment of the paper mill effluent-A review. Annals of the faculty of engineering. Humedoara, 11(3), 337–403. http://annals.fih.upt.ro/pdf-full/2013/ANNALS-2013-3-56.pdf
- Amu, O. O., Adetayo, O. A., & Alabi, O. J. (2019). Modification of cement stabilized structural lateritic pulverized snail shell. Acta Technica Corviniensis, 12(4), 63–68. https://media.proquest.com/media/hms/PFT/1/n2CdD?_s=KNBV4x9gV3KGPsqiPBFifINZ5fw%3D
- Andi-Cakir, O., Sarikanat, M., Tufekci, H. B., Demirci, C., & Erdogan, U. H. (2014). Physical and mechanical properties of randomly oriented coir fiber–cementitious composites. Composites Part B: Engineering, 61(2004), 49–54. https://doi.org/10.1016/j.compositesb.2014.01.029
- ANSI 208. 1. (2009). Particleboards American National Standard Institute. Composite Panel Association.
- ASTM C150/C150M-20. (2020). Standard Specification for Portland cement Mortar. ASTM International. https://doi.org/10.1520/C0150_C0150M-20
- ASTM C192/C192M-19. (2019). Standard practice for making and curing concrete test specimen in the laboratory. ASTM International. https://doi.org/10.1520/C0192_C0192M-19
- ASTM C403/C403M-16. (2016). Standard test method for time of setting of concrete mixtures by penetration resistance. ASTM International. https://doi.org/10.1520/C0403_C0403M-16
- ASTM D 5651-13. (2013). Standard test method for surface bond strength of wood-base fiber and particle panel materials. ASTM International. https://doi.org/10.1520/D5651-13
- ASTM D1037-12. (2012). Standard test method for evaluating properties of wood-base fiber and particle panel materials. ASTM International. https://doi.org/10.1520/D1037-12
- ASTM D5965-19. (2019). Standard test methods for density of coating powders. ASTM International. https://doi.org/10.1520/D5965-19
- ASTM D7433-19. (2019). Standard test method for measuring surface water absorption of overlaid wood based panels. ASTM International. https://doi.org/10.1520/D7433-19
- Atuanya, C. U., Ibhadode, A. O. A., & Igboanugo, A. C. (2011). Potencial of using recycled low-density polyethylene in wood composites board. Afri. Journal of Environmental Science and Technology, 5(5), 389–396. https://doi.org/10.5897/AJEST11.065
- Ayodele, F. O., & Popoola, O. O. (2019). Potencial of snail shell and palm kernel shell powders in improving engineering properties of clay. Journal of Applied Science Environment Management, 23(8), 1437–1444. https://doi.org/10.4314/jasem.v2318.5
- Balaji, A., Karthikeyan, B., Swaminathan, J., & Sundar Raj, C. (2018). Thermal behavior of cardanol resin reinforced 20 mm long untreated bagasse fiber composites. International Journal of Polymer Analysis and Characterization, 23(1): 70–77. 2017. 1387448. https://doi.org/10.1080/1023666X.2017.1387448.
- Balaji, A., Purushothaman, R., Udhayasankar, R., Vijayaraj, S., & Karthikeyan, B. (2020a). Study on mechanical, thermal and morphological properties of banana fiber-reinforced epoxy composites. Journal of Bio- and Tribo-Corrosion, 6(2), 60. https://doi.org/10.1007/s40735-020-00357-8
- Balaji, A., Sivaramakrishman, K., Karthiskeyan, B., Purushothaman, R., Swaminathan, J., Kannan, S., Udhayasankar, R., & Madieen, A. H. (2019). Study on mechanical and morphological properties of sisal/banana/coir fiber-reinforced hybrid polymer composites. Journal of the Brazilian Society of Mechanical Sciences and Engineering, 41(9), 386. https://doi.org/10.1007/s40430-019-1881-x
- Balaji, A., Udhayasankar, R., Karthikeyan, B., Swaminathan, J., & Purushothaman, R. (2020b). Mechanical and thermal characterization of bagasse fiber/coconut shell particle hybrid biocomposites reinforced with cardanol resin. Results in Chemistry, 2(2020), 100056. https://doi.org/10.1016/j.rechem.2020.100056
- Barragan-Lucas, A. D., Llerena-Miranda, C., Quijano-Aviles, M. F., Choez-Guaranda, I. A., Maldonado-Guerrero, L. C., & Manzano-Santana, P. (2018). Effect of resin content and pressing temperature on banana pseudo-stem particle boards properties using factorial design. Engineering Sciences, 91(4), e20180302. https://doi.org/10.1590/0001-3765201920180302
- Batiancela, M. A., Acda, M. N., & Cabangon, R. J. (2003). Particleboard from waste tea leaves and wood particles. Journal of Composite Materials, 1(1), 1–6. https://doi.org/10.1177/002199831340196
- BS EN 312-2010. (2016). British Standard (European Norm). Particleboards specifications. British standard group. The United Kingdom. https://doi.org/10.3403/30202520U.
- Chen, X., Liu, H., Xia, N., Shang, J., Tran, V. C., & Guo, K. (2015). Preparation and properties of oriented cotton stalk board with konjac glucomannan-chitosan-polyvinyl alcohol blend adhesive. Bioresources, 10(2), 3736–3748. https://doi.org/10.15376/biores.10.2.3736-3748
- Clemon, C. (2002). Wood-plastic composites in the United States: The Interfaces of two Industries. Journal of Production, 52(6), 10–18.
- Drelich, J., Chibowski, E., Meng, D., & Terpilowski, K. (2011). Hydrophilic and Super hydrophilic Surfaces and Materials. Soft Matter, 7(21), 9804–9828. https://doi.org/10.1039/C1SM05849E
- Drotleff, H., & Zhou, X. (2001). Attractive room acoustic design for multi-purpose halls. Acta Acustica United with Acustica, 87, 500–504.
- Dunuweera, S. P., & Rajapakse, R. M. G. (2018). Cement types, composition, uses and advantages of nanocement, environmental impact on cement production, and possible solutions. Advances in Materials Science and Engineering, 2018(4), 11. Article ID 4158682. https://doi.org/10.1155/2018/4158682.
- Dybel, P., & Walach, D. (2017). Evaluation of the development of bond strength between two concrete layers. IOP Conf. Series: Materials Science and Engineering, 245(3), 032056. https://doi.org/10.1088/1757-899X/245/3/032056
- Folorunso, D. O., & Akinwande, A. A. (2021). Applications of Compliance to Cost Ratio (C-CR) analysis in the determination of optimum mix of insulating bricks in masonry. Journal of Minerals and Materials Characterization and Engineering, 9(2), 134–147. https://doi.org/10.4236/jmmce.2021.92010
- Gronquist, S., Hakala, T., Kamppuri, T., Liita, T., Maloney, T., & Suurnakki, A. (2014). Fiber porosity development of dissolving pulp during mechanical and enzymatic processing. Cellulose, 21(5), 1–10. https://doi.org/10.1007/s10570-014-0352-x
- Hashim, M. Y., Amin, A. M., Marwah, O. M. F., Othman, M. H., Yunus, M. R. M., & Huat, N. C. (2017). The effect of alkali treatment under various conditions on physical properties of kenaf fiber. Journal of Physics: Conference Series, 914, 12030. https://doi.org/10.1088/1742-6596/914/1/012030
- Hassan, K. T. S., Kherallah, I. E. A., Settway, A. A. A., & Abdallah, H. M. (2020). Physical and mechanical properties of particleboard produced from some timber trees irrigated with treated wastewater. Alexandria Science Exchange Journal, 41(1), 77–83. https://doi.org/10.21608/asejaiqjsae.2020.77058
- Hosseinpourpia, R., Adomopoulos, S., Mai, C., & Hemmila, V., 2017. Effect of bio-based additives on physio-mechanical properties of medium density fiberboards. 28th Int. Conf. on Wood Science Technology, 153–157.
- Idicula, M., Kuruvilla, J., & Thomas, S. (2010). Mechanical performance of short banana/sisal hybrid fiber reinforced polyester composites. Journal of Reinforced Plastics and Composites, 29(1), 12–29. https://doi.org/10.1177/0731684408095033
- Idicula, M., Neelakantan, I. N. R., Oommen, Z., Kuruvilla, J., & Sabu, T. (2004). A study of the mechanical properties of randomly oriented short banana and sisal hybrid fiber reinforced polyester composites. Journal of Applied Polymer Science, 96(5), 1699–1709. https://doi.org/10.1002/app.21636
- IS 2380 (Part IV): Method of tests for wood particle boards and boards from other lignocellulosic materials (Wood and other Lignocellulosic Products). Bureau of Indian Standards. Manak bhavan, 9 Bahadur Shah Zafar Marg, New Delhi.
- IS 2380 (Part XIV): Method of tests for wood particle boards and boards from other lignocellulosic materials (Wood and other Lignocellulosic Products). Bureau of Indian Standards. Manak bhavan, 9 Bahadur Shah Zafar Marg, New Delhi.
- IS 3087, 2005. Particle boards of wood and other lignocellulose materials (medium density) for general purposes-specification (Wood and other Lignocellulosic Products). Bureau of Indian Standards. Manak bhavan, 9 Bahadur Shah Zafar Marg, New Delhi.
- IS 4031-1:1996: Method of physical tests for hydraulic, cement Part 1: Determination of fineness by dry sieving (cement and concrete). Bureau of Indian Standards. Manak bhavan, 9 Bahadur Shah Zafar Marg, New Delhi.
- IS 8112:2013: Ordinary Portland cement 43 grade specification. Bureau of Indian Standards. Manak bhavan, 9 Bahadur Shah Zafar Marg, New Delhi.
- IS 8142-1976, Method of tests for determining setting time of concrete by penetrometer test. Bureau of Indian Standards. Manak bhavan, 9 Bahadur Shah Zafar Marg, New Delhi.
- Kaewdaeng, S., & Nirunsin, R. (2019). Synthesis of calcium oxide from river snail shell as a catalyst in production of biodiesel. Applied Environmental Research, 4(1), 31–37. https://doi.org/10.35762/AER.2019.41.1.4
- Kalia, S., Dufresne, A., Cherian, B., Kaith, B. S., Averous, L., Njuguna, J. A., & Nassiopoulos, E. (2011). Cellulose-based bio- and nanocomposites: A review. International Journal of Polymer Science, 2018(837875), 1–35. https://doi.org/10.1155/2011/837875
- Ketebu, O., & Farrow, S. (2017). Comparative study on cementitious content of ground mollusc snail and clam shell and their mixture as an alternative to cement. . International Journal of Engineering Trends and Technology, 50(1), 8–11. https://doi.org/10.14445/22315381/IJETT-V50P202
- Khandelwal, S., Prajapat, K. L., Kumar, M., Bhantia, L., Sharma, A., & Sharma, V. (2015). Review on Papercrete. International Journal of Combined Research and Development, 4(6), 668-672. http://www.ijcrd.com/files/Vol_4_issue_6/56021.pdf
- Kumaat, E. J., Mondoringin, M. R. I. A. J., & Manalip, H. (2018). BASIC BEHAVIOUR OF NATURAL BANANA STEM FIBER REINFORCED CONCRETE UNDER UNIAXIAL AND BIAXIAL TENSILE STRESS. International Journal of GEOMATE, 14(44), 166–175. https://doi.org/10.21660/2018.44.01637
- Li, X., Tabil, L., & Panigrahi, S. (2007). Chemical treatments of natural fiber for use in natural fiber-reinforced composites: A review. Journal of Polymers and the Environment, 15(1), 25–33. https://doi.org/10.1007/s10924-006-0042-3
- Maail, R. S., 2006. Physical and mechanical properties of cement-gypsum board from Core-Kenaf (Hibiscus Cannabinus L.) using autoclave curing technology. Conf. Proceedings: 19th Int. Inorganic-Bonded Fiber Composite Conference, Sao Paulo, Brazil. 178–185.
- Mohd Nazarudin, Z., Mohd Ariff, J., Masitah, A. K., Nur Shafiquah, O., Maizatulusina, O., Syaidatul Hazira, M. N., & Mohamad Nurul, A. M. T. (2013). The effect of alkaline treatment on water absorption and tensile properties of non-woven kenaf polyester composite. Advanced Materials Research, 812, 258–262. https://doi.org/10.4028/www.scientific.net/AMR.812.258
- Mostafa, M., & Uddin, N. (2015). Effect of banana fibers on the compressive and flexural strength of compressed earth blocks. Buildings, 5(1), 282–296. https://doi.org/10.3390/buildings5010282
- Nayar, N. M. (2010). The bananas: Botany, origin, dispersal. Book: Horticultural Reviews, 36, 117–164. https://doi.org/10.1002/9780470527238.ch2
- Oladele, I. O., Adediran, A. A., Akinwekomi, A. D., Adegun, M. H., Olumakinde, O. O., & Daramola, O. O. (2020). Development of Ecofriendly snail shell particulate-reinforced recycled waste plastic composites for automobile application. The Scientific World Journal, 2020, 8. Article ID 74622758. https://doi.org/10.1155/2020/7462758.
- Oladele, I. O., & Isola, B. A. (2016). Development of bone particulate reinforced epoxy composite for biomedical application. Journal of Applied Biomedical Application, 1(1), 35–40. https://doi.org/10.15406/jabb.2016.01.00006
- Oladele, I. O., Makinde-Isola, B. A., Adediran, A. A., Oladejo, M. O., Owa, A. F., & Olayanju, T. M. A. (2020). Mechanical and wear behaviour of pulverised poultry eggshell/sisal fiber hybrid reinforced epoxy composites. Materials Research Express, 7(4), 045304. https://doi.org/10.1088/2053-1591/ab8585
- Olivia, M., Mifshella, A., & Darmayanti, L. (2015). Mechanical properties of seashell concrete. Procedia Engineering, 125, 760–764. https://doi.org/10.1016/j.proeng.2015.11.127
- Olumba, C., & Onunka, C. (2020). Banana and plantain in West Africa: Production and marketing. African Journal of Food, Agriculture, Nutrition and Development, 20(2), 15474–15489. https://doi.org/10.18697/ajfand.90.18365
- Onuegbu, G., & Igwe, I. (2011). The effects of filler contents and particle sizes on the mechanical and end-use properties of snail shell powder filled polypropylene. Materials Sciences and Applications, 2(7), 811–817. https://doi.org/10.4236/msa.2011.27110
- Oyejobi, D. O., Raji, S. A., Aina, S. T., & Siva, A. (2019). Physio-chemical and microstructural characteristics of selected pozzolanic materials for cement and concrete production. Nigerian Journal of Technological Development, 16(3), 111–119. https://doi.org/10.4314/njtd.v16i3.4
- Pan, Z., Zheng, Y., Zhang, R., & Jenkins, B. M. (2007). Physical properties of thin particleboard made from saline eucalyptus. Industrial Crops and Products, 26(2), 185–194. https://doi.org/10.1016/j.indcrop.2007.03.006
- Prasad, N., Agarwal, V. K., & Sinha, S. (2016). Banana fiber reinforced low-density polyethylene composites: Effect of chemical treatment and compatibilizer addition. Iranian Polymer Journal, 25(3), 229–241. https://doi.org/10.1007/s13726-016-0416-x
- Qi, L., Liu, J., & Liu, Q. (2016). Compound Effect of CaCO3 and CaSO4·2H2O on the Strength of Steel Slag - Cement Binding Materials. Materials Research, 19(2), 269–275. https://doi.org/10.1590/1980-5373-MR-2015-0387
- Ramli, S., Sheikh, M., Fadzullah, S., & Mustafa, Z. (2017). The effect of alkaline treatment and fiber length on pineapple leaf fiber reinforced polylactic acid biocomposites. Journal Technology, 79, 111-115. https://doi.org/10.11113/jt.v79.11293
- Rashid, A. A., Khalid, M. Y., Imran, R., Ali, U., & Koc, M. (2020). Utilization of banana fiber-reinforced hybrid composites in the sports industry. Materials, 13(14), 3167. https://doi.org/10.3390/ma13143167
- Sawawi, M., Mohammad, N. H., Sahari, S. K., Junaidi, E., & Razali, N. T. (2020). Effects of chemical treatment on mechanical properties of oil palm Empty Fruit Bunch (EFB) with Urea Formaldehyde (UF) resin particleboard type. International Journal of Recent Technology and Engineering, 8(5), 1330–1334.
- Sekino, N., & Korai, H. (2018). The evaluation of long-term mechanical properties of wood-based panels by indoor exposure tests. Journal of Wood Science, 64(4), 377–389. https://doi.org/10.1007/s10086-018-1720-1
- Shawia, N. B., Jabber, M. A., & Mamouri, A. F. (2014). Mechanical and physical properties of natural fiber cement board for building partitions. Physical Sciences Research Int, 2(3), 49–53.
- Silva, F. A., Filho, R. D. T., Filho, J. M., & Fairbairm, E. M. R. (2010). Physical and mechanical properties of durable sisal fiber–cement composites. Construction and Building Materials, 24(5), 777–785. https://doi.org/10.1016/j.conbuildmat.2009.10.030
- Subramani, T., & Angappan, V. (2015). Experimental investigation of papercrete concrete. International Journal of Application or Innovation in Engineering and Management, 4(5), 134–143.
- Suganya, S., & Rajkumar, V. (2018). Significant effects of cementitious materials on strength gain properties of concrete with partial replacement of fine aggregate by quarry dust. . International Journal of Engineering & Technology, 7(4), 2051–2057. https://doi.org/10.14419/ijet.v7i4.16064
- Suryanto, H., Marsyahyo, E., Irawan, Y., & Soenoko, R. (2014). Effect of alkali treatment on crystalline structure of cellulose fiber from mendong (Fimbristylis Globulosa) Straw. Key Engineering Materials, 4(5), 594-595, 720–724. https://doi.org/10.4028/www.scientific.net/KEM.594-595.720
- Syamimi, N. F., Islam, M. R., Sumdani, M. G., & Rashidi, N. M. (2019). Mechanical and thermal properties of snail shell particle-reinforced bisphenol-a bio-composites. Polymer Bulletin, 77, (1234567890), 1–17. https://doi.org/10.1007/s00289-019-02878-w
- Tanasa, F., Zanoaga, M., Teaca, C. A., Nechifor, M., & Shahzad, A. (2019). Modified hemp fibers intended for fiber-reinforced polymer composites used in structural application: A review. 1. Methods of Modification. Polymer Composites, 41(1), 1–27. https://doi.org/10.1002/pc.25354
- Tay, C. C., Hamdan, S., & Osman, M. S. B. (2016). Properties of Sago Particleboards Resinated with UF and PF Resin. . Advances in Materials Science and Engineering, 2016, 1–12. Article ID 5323890. https://doi.org/10.1155/2016/5323890
- TSE-TS EN 317, 1999: Particleboards and fiberboards-determination of swelling in thickness after immersion in water. (European Norm) Turkish Standard Institute, Ankara, Turkey.
- Udhayasankar, R., Karthikeyan, B., & Balaji, A. (2019). Comparative mechanical, thermal properties and morphological study of untreated and NaOH-treated coconut shell-reinforced cardanol environmental-friendly green composites. Journal of Adhesion Science and Technology, 34(16), 1–21. https://doi.org/10.1080/1694243.2020.1727643
- Vaiciukyniene, D., Vaitkevicius, V., Kantautas, A., & Sasnauskas, V. (2012). Utilization of by-product waste silica in concrete - based materials. Materials Research, 15(4), 561–567. https://doi.org/10.1590/S1516-14392012005000082
- Vidyasri, K., Srividya, K., Ram, N. R., Sumanth, C. M., & Sd., V. (2019). Strength analysis of banana and americana hybrid composite. International Journal of Research and Analytical Reviews, 6(2), 767–772. https://www.ijrar.org/archive.php?vol=6&issue=2
- Wang, S., Peng, X., Tang, L., Cao, C., & Zeng, L. (2018). Contact-hardening behavior of calcium silicate hydrate powders. Materials, 11(12), 2367. https://doi.org/10.3390/ma11122367
- Wu, J., Zhang, X., Feng, Y., Yuan, H., Tang, Y., & Zhang, X. (2011). Production of fiberboard using corn stalk pretreated with white-rot fungus Trametes hirsute by hot pressing without adhesive. Bioresource Technology, 102(24), 11258–11261. https://doi.org/10.1016/j.biortech.2011.09.097
- Yano, B. B. R., Silva, S. A. M., Almeidia, D. H., Aquino, V. B. M., Christoforo, A. L., Rodrigues, E. F. C., Carvalho, A. N., Jr, Silva, A. P., & Lahr, F. A. R. (2020). Use of sugarcane bagasse and industrial timber residue in particleboard production. Bioresources, 15(3), 4753–4762.
- Yeon, K. S., Kim, K. K., Yeon, J., & Lee, H. J. (2019). Compressive and Flexural Strengths of EVA-modified mortars for 3D additive construction. Materials, 12(16), 1–14. https://doi.org/10.3390/ma12162600
- Zaki, H. M., Salih, S. A., & Gorgis, I. N. (2019). Characteristics of paper-cement composites. Journal of Engineering, 25(4), 122–138. https://doi.org/10.31026/j.eng.2019.04.09
- Zheng, M. X., Li, L., Zheng, M. Y., Wang, X., Ma, H., & Wang, K. (2012). Effect of alkaline pretreatment on cellulose structural changes of corn stover. Environmental Science & Technology, 35, 21–37. https://doi.org/10.3969/j..1003-6504.2012.06.007
- Zhu, X., Kim, B. J., Wang, Q., & Wu, Q. (2013). Recent advances in the sound insulation properties of bio-based materials. BioResources, 9(1), 1764-1786. https://doi.org/10.15376/biores.9.1.1764-1786