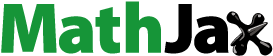
Abstract
Polymer materials, such as polymer concrete, have long played an important role in the construction industry. A cement and water-free building binder is formed by polymerizing monomers and initiators, and this process has many advantages in terms of green concrete. Compared with polymerized monomers, the initiator needs to provide the energy required to lower the polymerization threshold, and these energetic properties lead to thermal hazards. Azo compounds are one type of energetic polymerization initiator that can cause serious fire and explosion hazards. If the safety measures for phase changes in reactions (for example, in an endothermic process or a cooling system) fail, serious fires and explosions will occur. To ensure the thermal safety of an overall reaction process, 2,2ʹ-azobis (2,4-dimethylvaleronitrile) (ABVN), which is usually used for polymerization, was selected in this study. The exothermic mode and basic thermal hazard of ABVN were analyzed using a C80 microcalorimeter, which has low interference from the external temperature. The results of this study reveal the reaction form of ABVN through kinetic analysis. The thermal hazard of ABVN during actual thermal decomposition was analyzed using a thermal equilibrium calculation, and the storage and transport hazard characteristics of 25.0 kg and 50.0 kg ABVN packages were also determined. The results show that ABVN exhibits obvious thermal hazard characteristics when the temperature is higher than 35 °C (SADT<35 °C). Therefore, with the TMR value as the basis for design safety, the TCL is recommended to avoid high-temperature environments.
PUBLIC INTEREST STATEMENT
Polymer materials have always played an important position in the construction industry, such as polymer concrete, which has many advantages in terms of green concrete. Compared with polymerized monomers, the initiator needs to provide the required energy to lower the polymerization threshold, and the property of its energetic material causes the possibility of thermal hazards. Azo compounds belong to this type of energetic polymerization initiator, which has caused serious fire and explosion hazards. To ensure the thermal safety of an overall reaction process, 2,2ʹ-Azobis (2,4-dimethylvaleronitrile) (ABVN), which is usually used for polymerization, was selected in this study by the calorimetric method and an analytical approach. Combined with mathematical studies which are used to examine the introductory kinetics and thermal equilibrium of the ABVN. Herein, we highlight key discoveries on ABVN, while providing a critical safety parameter for future opportunities in real chemical process and its emerging safety-controlled area.
1. Introduction
1.1. The importance of polymers in construction materials
In the field of construction, various studies have been conducted based on the concept of green concrete, in which the cement in traditional concrete is replaced with sustainable materials as binders to prevent the diffusion of carbon dioxide. Such materials are imperative in improving the environmental impacts of the concrete industry. Based on their use and function, polymers can be roughly divided into three categories (Ohama, Citation1973). This trend has led to the development of polymer concretes formed by polymer technology and various monomers in the traditional polymerization industry, and the material properties and extensibility of these materials need to be researched (British Standards Institution, Citation2012).
Polymer resins can be obtained as monomers or prepolymers in liquid form. In the presence of an initiator and a catalyst, liquid monomers are converted into polymer resins. The percentages of initiator and catalyst depend on the type and temperature of the polymer resin used. Unlike from conventional concrete, polymer concrete has various advantages, such as a high strength and durability (Ohama, Citation2003; Saravana Karthika et al., Citation2019).
1.2. Research status of polymerization products and raw materials of azo compounds
Polymerization reactions and their products are used in various industries due to scientific advances (Zeng et al., Citation2019). With the requirement and purpose of reducing impacts on the external environment, improved polymeric products, such as polymer blends, are highly regarded as having lower hazard characteristics (Qi et al., Citation2020; Ze et al., Citation2018; Zhang et al., Citation2021) in research prospects (Vanjeri et al., Citation2019; Xi et al., Citation2019). Although the products are considered to be low risk, the essential polymerization initiator may pose thermal hazards. Different polymerization modes have been derived over time. The azo polymerization initiator in this study is an important part of polymerization (Brown et al., Citation2000).
1.3. Potential hazards of azo polymerization initiators
Azo compounds (azos), which often show unstable properties, have long been used as polymerization initiators in industrial processes (Gowda et al., Citation2002; Liu et al., Citation2017; Liu & Shu, Citation2015). The basic expression of an azo can be conveyed as R-N = N-R, in which the structural formula is asymmetric, with the same aliphatic or aromatic hydrocarbon group on both sides, as represented by R (Baszkin & Ter‐Minassian‐Saraga, Citation1971). With enough energy, the covalent bond will break, releasing heat and free radicals (Chervin & Bodman, Citation2003; Levin et al., Citation2006; S.Y. Wang et al., Citation2017; Talouba et al., Citation2011; Whitmore & Wilberforce, Citation1993). If the released energy cannot be effectively channeled, it will accumulate in the closed system, for example, in a reactor or in storage, resulting in temperature increases and the generation of gas. Most equipment cannot withstand high temperatures and pressures, eventually causing fires and thermal explosions. (Liu et al., Citation2014; United Nations, Citation2018).
2,2ʹ-Azobis (2,4-dimethylvaleronitrile) (ABVN), a classic azo, is widely applied in chemical polymerization reactions but rarely used in process-safety-related research for industrial safety and comparative research objectives. The decomposition reaction of this substance does not require the participation of air components such as oxygen. The reaction is usually carried out in a closed environment, in which the pressure effect caused by uncontrolled reactions is more profound. As the initiator of the reaction, the temperature at which the decomposition reaction occurs is generally low (Liu et al., Citation2018, Citation2014). This ABVN has been shown to lead to thermal hazards in the past due to its reactive characteristics (Liu et al., Citation2017; Liu & Shu, Citation2015). Most studies have focused on single calorimetry or have lacked a thermal hazard analysis of the reaction kinetics and a determination of the thermodynamics, which are related to the storage and transportation conditions.
1.4. Analysis of thermal hazards and storage hazard characteristics of the substance
The reactivity and kinetic characteristics (Mao et al., Citation2020) of ABVN must be recognized to assess and avoid the associated thermal hazards. Instrumental analysis technology and calorimetric methods have been combined with a C80 microcalorimeter (C80) with several heating rates (β) (Kossoy & Akhmetshin, Citation2012; Kossoy et al., Citation2015). The initial dynamic analysis and reaction kinetics of ABVN have been determined (Brown et al., Citation2000; Burnham, Citation2000). The experiments in these previous studies were based on milligram-scale experiments to conveniently and quickly obtain the hazard parameters of the material base, and the results were used in conjunction with numerical simulations to amplify and evaluate the exothermic effects of the actual environment on the material itself in the mode of heat exchange as a hazardous feature (Kossoy & Hofelich, Citation2003; Kossoy & Koludarova, Citation1995; Kossoy & Sheinman, Citation2007; S.Y. Wang et al., Citation2017). Additional heat transfer models can be constructed to evaluate a large number of ABVNs and the different environmental conditions to establish specifications for appraising the reaction safety and thermal stability.
1.5. Analysis of the thermal hazards and storage hazard characteristics of the substance
Instrumental analysis data can be used to characterize the exothermic behavior of azos. This study constructed a record of the heat released by the thermal decomposition of ABVN with changes in the ambient temperature. The basic thermal hazard parameters of ABVN were deduced by simulating the heat release model through kinetic calculations. For example, using the reaction order (n), reaction equation (f(α)), and activation energy (Ea), the reaction mode of ABVN can be combined with the heat balance of the external environment to calculate the exothermic behavior at different temperatures. Temperature-related hazard parameters, such as TMR and TCL, can be used to determine the reaction rate and the amount of reactive substances consumed at a specific ambient temperature, respectively. In addition, when the ambient temperature exceeds a particular value (SADT, CT, and ET), the storage of a substance for a period of time may lead to thermal hazards or immediate reactive hazards.
2. Experimental
2.1. Sample
Approximately 150.0 mg of 98 mass% ABVN from ACE Chemical Industries, Ltd. was subjected to C80 microcalorimeter experiments. The ABVN was stored in a low-temperature (<4.0 °C) environment due to its low thermal stability.
2.2. C80 microcalorimeter
To simulate the self-exothermic mode of the material, it is important to reduce the influence of the external heat effect. Therefore, a C80 microcalorimeter, which can be heated and used for detection in a lower thermal heating mode, was selected as the experimental instrument for this study. The C80 recorded the relationship between the temperature change of the material and the corresponding heat release value to obtain various thermodynamic parameters. The heating rates were 0.25, 0.5, 1.0, and 2.0 °C/min. The test scope of the temperature range was deliberately set as 30–300 °C (Q. Wang et al., Citation2009).
3. Process simulation
3.1. Nonlinear fitting for determining the reaction mechanism of ABVN decomposition
The reaction mode promotes the hazard characteristics of different reactions, which is a key factor (Parulekar, Citation1998) in the design and consideration of real operations (Kossoy & Akhmetshin, Citation2012). The foundation of the reaction form is considered to be the transformation degree of the reaction (α):
dɑ/dt is constructed from the Arrhenius equation. The different reaction equations f(ɑ) are shown in Eqs. (1)—(Equation3(5)
(5) ) (Kossoy & Hofelich, Citation2003; Levin et al., Citation2006).
Single stage reaction X→Y:
where Ea is the apparent activation energy; R is the gas constant; T is the temperature of the sample; α is the degree of conversion of the reactant; k0 is the pre-exponential factor; n, n1, and n2 are the reaction orders; and z is the autocatalytic constant.
The heat release of a substance is closely related to the external environment. Even if heat is released, as long as the heat can be exchanged with the surface of the substance and the outside of the system, the temperature under actual conditions can be controlled. In contrast, if the heat released by a large amount of substances accumulates in the system and cannot escape effectively, the temperature will rise accordingly, and the reaction mode of the substance must be calculated using nonlinear methods (Chiang et al., Citation2018). Numerical models of the thermal explosion of simulated materials (Liu et al., Citation2019) can illustrate key thermodynamic parameters for process safety through an evaluation model of the relationship between heat exchange and temperature. Setting the boundary conditions for the simulation of an external vessel based on three heat transfer models (Gao et al., Citation2019) yields
where is the density; Cp is the specific heat capacity; λ is the thermal conductivity coefficient; T is the temperature; and W is the heat generated by the reaction.
Assuming that the initial temperature distribution in the container is evenly distributed yields
1st type:
2nd type:
3rd type:
where “wall” and “e” are expressed as the temperature change between the surface of the reactor and the environment, q is the heat flow, n is the unit outer normal on the boundary, and U is the heat transfer coefficient (Kossoy & Akhmetshin, Citation2007, Citation2012; Kossoy & Sheinman, Citation2007).
3.2. Applying thermokinetic parameters to acquire reaction hazard information for a scale-up method
The time required for the maximum response speed (TMRad) can be applied to different operating procedures with different heating modes, such as the adiabatic form that conforms to the real process state in which the heat of the material is not diluted by the container material and the isothermal form in which the temperature is maintained at a constant range for a long time, which conforms to the storage condition. As the characteristic times of TMRad and TMRiso pass, the reaction rate eventually reaches a maximum value, which can be determined based on adiabatic and isothermal conditions, respectively (Liu & Shu, Citation2015; T.S. Wang et al., Citation2013), as prominent features of process safety. However, due to the cost of instruments and consumables and relatively complex experimental procedures (Huang et al., Citation2010; Q. Wang et al., Citation2009), a replacement that is rapid and cheaper, such as the C80, should be considered in combination with amplification simulation for alternative schemes.
Kossoy and Akhmetshin (Kossoy & Akhmetshin, Citation2007) constructed TMRad with data from thermal calorimeter technology in the chemical industry and reaction processes. The rate of a reaction is directly related to thermal analysis signals such as temperature and exothermic heat, and it also affects the severity of thermal hazards, such as the possibility of runaway reactions when the process temperature reaches a particular temperature. Wang et al. (S.Y. Wang et al., Citation2017) combined the reaction structure and nonlinear fitting to obtain the reaction form containing the relevant thermal parameters described by Thermal Safety Software (ChemInform Saint-Petersburg (CISP), L, Citation2021) or the Kinetics program by the Netzsch Group (Opfermann, Citation2000; Opfermann & Hädrich, Citation1995). The C80 data curve was fitted by a nonlinear kinetic numerical model curve, and various kinetic parameters were obtained by substituting the reaction equations. Through simulation, a large number of substances and an evaluation model of temperature changes formed by the external environment were established.
3.3. Judging the safety and emergency response by the time required to process
Due to the self-reaction characteristics of energetic substances, long-term storage has an impact on the thermal safety of a material. Conditions such as poor ventilation or cooling system failure, which will lead to an increase in the ambient temperature, may lead to a runaway reaction. The degree of consumption of a material at different temperatures reflects the thermal hazard characteristics of that material. The consumption of more material at the same temperature indicates a fast reaction rate and a greater possibility of subsequent thermal hazards. Therefore, the hazard degree of a reaction under different temperature conditions can be evaluated based on the time of reaching the conversion limit for a material, the C80 data, and the following equations (Kossoy & Akhmetshin, Citation2007; S.Y. Wang et al., Citation2017; Q. Wang et al., Citation2009):
Nth-order reaction:
Autocatalytic reaction:
3.4. Thermal safety assessment for storage and transportation
The self-exothermic phenomenon in the storage process is caused by the energy-consuming material being consumed due to its own transformation. The mass storage of substances under specific packaging conditions hinders the heat transfer of a bulk material to the surrounding environment. The heat accumulation caused by a long residence time causes the temperature to rise above the reaction threshold and triggers the substance to form a decomposition reaction. Temperature is the key factor for ensuring that large amounts of a material can maintain thermal stability. If the temperature is properly controlled, the subsequent heat accumulation can be eliminated, even if self-heating occurs. If the temperature can be controlled below the value of the self-accelerating decomposition temperature (SADT), the effect of self-heating can be reduced. This value is defined for a substance being stored under ambient temperature conditions during commercial packaging, and the temperature of the packaging center increases within seven days by no more than 6 degrees (Kossoy et al., Citation2015). Simulations were performed for the use of ABVN in intense commercial activities under different industry conditions. The reaction of the upper heating rate is expressed in EquationEq. (9)(9)
(9) :
where Cp is the sample heat capacity, λ is the thermal conductivity, ρ is the density of ABVN, x is the package radius, and g is a geometry factor that varies based on the type of packaging.
The Society of the Plastics Industry, Inc. (SPI) provides guidance on how to obtain CT and ET values based on the SADT value. Keeping a substance under the CT ensures that the temperature of the substance is stable and does not reach the ET. If the material temperature exceeds the ET, emergency procedures must be in place to curb runaway temperatures (Kossoy & Sheinman, Citation2007; Lin et al., Citation2010; Lv et al., Citation2013).
4. Results and discussion
4.1. Analysis process and application of thermal hazard parameters
The use of initiators in the monomer stage of construction polymers can help the polymerization reaction proceed smoothly and reduce energy consumption, which is directly associated with the kinetic reaction characteristics of the initiator on decomposition. The nonlinear regression kinetic model was used to fit the C80 data and obtain an appropriate kinetic model, which was used to ascertain the thermal equilibrium of ABVN. The basic thermal parameters of the ABVN reaction were combined with kinetic models and numerical calculations. The reactive properties for the characterization of ABVN initiators, such as TMRad and TCL, are effective for controlling the temperature and determining the reaction time during the manufacture of construction polymers and can be used to predict the exothermic interaction between a large number of ABVNs and the surrounding environment. The full-scale experiments, which are cumbersome and expensive, were replaced by large-scale SADT, CT, and ET experiments by simulating the heat release and temperature changes of ABVN under different temperature environments based on the results of the C80 experiments. The storage method under actual operation, temperature control, and personnel safety operation mode can all be verified by this mode.
4.2. Nonisothermal C80 analysis
The C80 data reveal the elementary hazardous properties and kinetics. shows the C80 tests for ABVN at heating rates of 0.25, 0.5, 1.0, and 2.0 °C/min. A phase change of melting occurred at approximately 60.0 °C at the point on the thermal curve where the first peak of the ABVN crystal appeared. Then, the exothermic reaction occurred at the same time, which represents thermal decomposition followed by the phase change. The maximum qg was 1.8 mW/g at 125.0 °C, and the ∆Hd value was 820.0 J/g. Based on the abovementioned phenomenon, a large amount of heat can be generated through the decomposition reaction, and a fire or explosion may be caused by energy and gas products.
Figure 1. Thermal curves of heat flow vs. temperature for ABVN with heating rates of 0.25, 0.5, 1.0, and 2.0 °C min–1
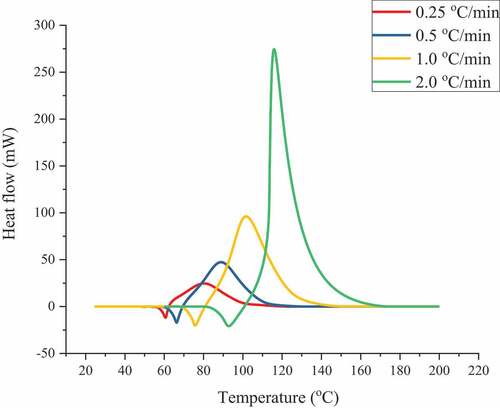
It should be noted that ABVN has a lower characteristic T0 value. According to the C80 analysis results, the thermal decomposition hazard analysis of a nonisothermal environment can provide the evaluation basis for the reaction characteristics and basic thermal hazards by T0. As long as the ambient temperature increases above 50 °C, decomposition reactions and subsequent thermal hazards may be triggered, which requires more attention to the storage environment and can provide a basis for the subsequent setting of different ambient temperatures to calculate the change in the heat release of ABVN.
4.3. Thermokinetics of ABVN decomposition
According to the experimental data and in combination with the kinetic analysis, basic thermal hazard parameters and corresponding reaction modes were achieved. and show the heat production rates obtained from the C80 experiment with ABVN at different heating rates and the mathematical simulation, and the results indicate the autocatalytic form. The corresponding kinetic parameters were determined using thermodynamic equations for the process conditions, as shown in and . According to the C80 and numerical methods, ABVN undergoes a multistage reaction, which constitutes the second stage of the decomposition reaction. The exothermic peak of the first stage has a larger reaction rate and an earlier occurrence time. The second stage is generated after a period of time after the first stage starts, and the heat release is at a low level. Therefore, the first stage is the main part of the reaction.
Table 1. Results of thermokinetic parameter evaluation for the ABVN at 0.25, 0.5, 1.0, and 2.0 °C min–1
Figure 2. ABVN heat production versus time curves with heating rates of heating rates of 0.25, 0.5, 1.0, and 2.0 °C min–1 by experiments and simulations
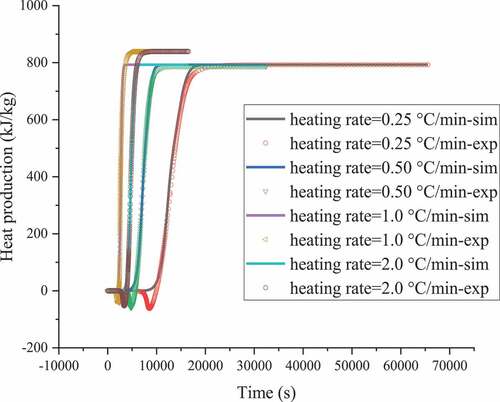
4.4. Amplify and analyze critical runway parameters through kinetic-based models
Based on the calculation model in sections 3.3 to 3.5, the fitting mode of the ABVN is represented in . The potential storage and transport hazards of a large number of ABVNs in a 25.0 kg box and 50.0 kg drum were assessed based on the UN packaging standard. Following Kossoy (Kossoy et al., Citation2015), the hazardous substances were wrapped in plastic bags and placed in an outer fiberboard container, and the chemicals did not fully contact the container, which is the cause of the deviation. lists the relevant parameters and boundary conditions of the fiberboard container.
Table 2. Physical parameters of packages for the ABVN
Figure 5. Simulation results of ABVN for TCL under different ambient temperatures from a heating rate of 2.0 °C min–1
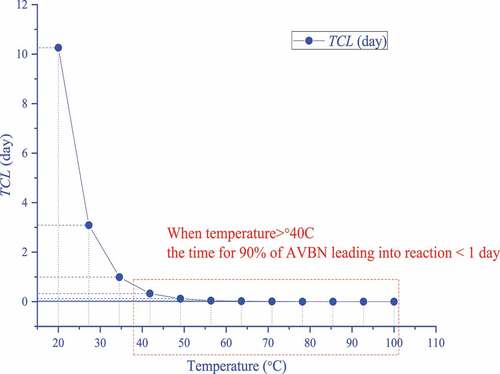
Figure 6. Simulation results of ABVN for TMRad under different ambient temperatures at a heating rate of 2.0 °C min–1
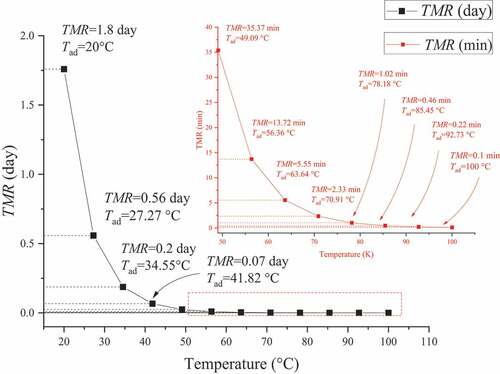
Figure 7. Simulation results of runaway reaction on reaction temperature versus reaction time for ABVN with box package (above) and drum package (below)
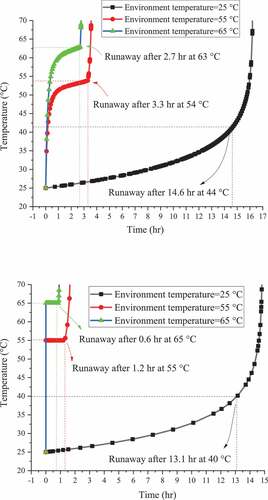
The thermodynamic model was used to calculate the TCL result shown in , and the SADT, CT, and ET values of ABVN, which are shown in , were simulated based on the heat balance under the set container of ABVN. More than 90% of the substances were consumed in one day due to participation in the decomposition reaction according to the TCL results. In terms of storage and transportation, the SADT is less than 34.0 °C. This means that if the ambient temperature of ABVN during mass storage exceeds 34 °C, the possibility of thermal hazards is high, and this value is lower than the operating temperature in actual processes. As long as temperature control measures are improper, hazards such as runaway reactions may arise. In addition, these results have little effect on the exothermic pattern of substances in different container structures.
Table 3. Results of thermal explosion simulation for the ABVN
The placement of ABVN in environments with different initial temperatures affected the changes in TMRad, as shown in . When the ABVN temperature is slightly higher than the ambient temperature (> 27.0 °C), the TMRad will be reduced, which means that there will be a decomposition reaction with the maximum reaction rate in one day. The change in the ambient temperature and the thermal stability of ABVN are directly related. The temperature during actual operation should be lowered to ensure a sufficient personnel reaction time, which is used to extend the storage period of the material and reduce the occurrence of unexpected thermal hazards.
shows the uncontrolled response induced by different ambient temperatures. The accelerated thermal decomposition rate caused by increasing temperatures established the shorter time required to reach the runaway reaction of ABVN. Even at room temperature (25.0 °C), the runaway phenomenon will still occur. The design of the container does not saliently affect the thermal safety of ABVNs. ABVN is still hazardous even at lower ambient temperatures to reduce the possibility of uncontrolled reactions. Care must be taken to prevent malfunctioning of the cooling system. ABVN was refrigerated below 0 °C to avoid thermal runaway of storage and transportation.
5. Conclusions
The reaction kinetic model of ABVN was discussed, and the calculation was based on the basic kinetic parameters using the heat balance model to calculate the heat release of a large number of ABVNs in different temperature environments and the corresponding temperature changes. This evaluation mode avoids tedious field experiments and reduces the cost of consumables and enables a small and convenient thermal analysis experiment to be used to obtain the thermal hazard mode of ABVNs. The hazard characteristics can be assessed by a series of thermal hazard parameters, which serve as the basis for process safety evaluation. The main findings are as follows:
Based on the basic thermokinetic parameters and hazard analysis derived from the C80 results, attention must be paid to the initial decomposition temperature, activation energy, and reaction enthalpy. These results can be used as a reference to determine the safe operating temperature and to establish related temperature alarm systems.
Based on the kinetics and in combination with environmental heat exchange analysis, when more ABVNs accumulate, even at room temperature (25 °C), a runway reaction will still occur, and when the ambient temperature exceeds 55.0 °C, the required heat removal efficiency will increase, and the growth of the reaction rate will shorten the time to reach a runway reaction, which may lead to process hazards if the operation does not immediately respond to temperature changes.
Combined with the estimation of the thermal hazard parameters TMRad and TCL and the hazard temperature indicators SADT, CT, and ET, when the temperature exceeds 40 °C, the decomposition reaction of ABVN intensifies, and the increase in the reaction rate causes the decomposition reaction heat to form a runaway reaction within one day. If the process further considers thermal safety during storage, ABVNs should be stored in an environment with good ventilation or even an independent cooling system, to ensure that the temperature remains below room temperature (< 25 °C).
List of symbols
Table
Disclosure of potential conflicts of interest
The authors declare no conflicts of interest.
Acknowledgements
The authors are grateful for the technical support from National Yunlin University of Science and Technology.
Additional information
Funding
Notes on contributors
I-Jyh Wen
Chia-Feng Tsai: Conceptualization, Methodology, Writing - Review & Editing, Data curation, Writing- Original draft preparation. To guarantee the safety design, I study on the reaction mechanism for process operation and evaluated thermal hazard based on thermal calorimetry technique associated with dynamic conditions.
I-Jyh Wen: Visualization, Investigation, Writing - Review & Editing. Thermal equilibrium which estimated of TMRad, TCL and runaway reaction on safe temperature and emergency response are described and fixed.
References
- Baszkin, A., & Ter‐Minassian‐Saraga, L. (1971). Chemical structures of surface‐oxidized and grafted polyethylene: Adsorption and wetting studies. Journal of Polymer Science: Polymer Symposia, 34(1), 243–18. https://doi.org/10.1002/polc.5070340122
- British Standards Institution. (2012). Testing hardened concrete: Shape, dimensions and other requirements for specimens and moulds, BSI.
- Brown, M. E., Maciejewski, M., Vyazovkin, S., Nomen, R., Sempere, J., Burnham, A., Opfermann, J., Strey, R., Anderson, H. L., Kemmler, A., Keuleers, R., Janssens, J., Desseyn, H. O., Li, C. R., Tang, T. B., Roduit, B., Malek, J., & Mitsuhashi, T. (2000). Computational aspects of kinetic analysis: Part A: The ICTAC kinetics project-data, methods and results, Thermochim. Acta, 355(1-2), 125–143. https://doi.org/10.1016/S0040-6031(00)00443-3
- Burnham, A. K. (2000). Computational aspects of kinetic analysis.: Part D: The ICTAC kinetics project–multi thermal history model fitting methods and their relation to isoconversional methods. Thermochimica Acta, 355(1–2), 165–170. https://doi.org/10.1016/S0040-6031(00)00446-9
- ChemInform Saint-Petersburg (CISP), L. (2021). Thermal safety software. CISP. Retrieved http://www.cisp.spb.ru
- Chervin, S., & Bodman, G. T. (2003). Method for estimating decomposition characteristics of energetic chemicals. Process Safety Progress, 22(4), 241–243. https://doi.org/10.1002/prs.680220412
- Chiang, C. L., Liu, S. H., Cao, C. R., Hou, H. Y., & Shu, C. M. (2018). Multiapproach thermodynamic and kinetic characterization of the thermal hazards of 2, 2ʹ-azobis (2-methylpropionate) alone and when mixed with several solvents, J. Journal of Loss Prevention in the Process Industries, 51, 150–158. https://doi.org/10.1016/j.jlp.2017.12.003
- Gao, P. F., Liu, S. H., Zhang, B., Cao, C. R., & Shu, C. M. (2019). Complex thermal analysis and runaway reaction of 2,2ʹ-azobis (isobutyronitrile) using DSC, STA, VSP2, and GC/MS, J. Journal of Loss Prevention in the Process Industries, 60, 87–95. https://doi.org/10.1016/j.jlp.2019.04.011
- Gowda, S., Abiraj, K., & Gowda, D. C. (2002). Reductive cleavage of azo compounds catalyzed by commercial zinc dust using ammonium formate or formic acid. Tetrahedron Letters, 43(7), 1329–1331. https://doi.org/10.1016/S0040-4039(01)02370-X
- Huang, C. C., Peng, J. J., Wu, S. H., Hou, H. Y., You, M. L., & Shu, C. M. (2010). Effects of cumene hydroperoxide on phenol and acetone manufacturing by DSC and VSP2. Journal of Thermal Analysis and Calorimetry, 102(2), 579–585. https://doi.org/10.1007/s10973-010-0953-z
- Kossoy, A. A., & Akhmetshin, Y. G. (2007). Identification of kinetic models for the assessment of reaction hazards. Process Safety Progress, 26(3), 209–220. https://doi.org/10.1002/prs.10189
- Kossoy, A. A., & Akhmetshin, Y. G. (2012). Simulation-based approach to design of inherently safer processes. Process Safety and Environmental Protection, 90(5), 349–356. https://doi.org/10.1016/j.psep.2012.03.007
- Kossoy, A. A., Belokhvostov, V. M., & Koludarova, E. Y. (2015). Thermal decomposition of AIBN: Part D: Verification of simulation method for SADT determination based on AIBN benchmark. Thermochimica Acta, 621, 36–43. https://doi.org/10.1016/j.tca.2015.06.008
- Kossoy, A. A., & Hofelich, T. C. (2003). Methodology and software for assessing reactivity ratings of chemical systems. Process Safety Progress, 22(4), 235–240. https://doi.org/10.1002/prs.680220410
- Kossoy, A. A., & Koludarova, E. Y. (1995). Specific features of kinetics evaluation in calorimetric studies of runaway reactions. Journal of Loss Prevention in the Process Industries, 8(4), 229–235. https://doi.org/10.1016/0950-4230(95)00018-V
- Kossoy, A. A., & Sheinman, I. Y. (2007). Comparative analysis of the methods for SADT determination. Journal of Hazardous Materials, 142(3), 626–638. https://doi.org/10.1016/j.jhazmat.2006.06.068
- Levin, M., Gonzales, N., Zimmerman, L., & Yang, J. (2006). Kinetics of acid-catalyzed cleavage of cumene hydroperoxide. Journal of Hazardous Materials, 130(1–2), 88–106. https://doi.org/10.1016/j.jhazmat.2005.07.068
- Lin, C. P., Tseng, J. M., Chang, Y. M., Liu, S. H., Cheng, Y. C., & Shu, C. M. (2010). Modeling liquid thermal explosion reactor containing tert-butyl peroxybenzoate. Journal of Thermal Analysis and Calorimetry, 102(2), 587–595. https://doi.org/10.1007/s10973-010-0954-y
- Liu, S. H., Cao, C. R., Lin, W. C., & Shu, C. M. (2019). Experimental and numerical simulation study of the thermal hazards of four azo compounds. Journal of Hazardous Materials, 365, 164–177. https://doi.org/10.1016/j.jhazmat.2018.11.003
- Liu, S. H., Lin, W. C., Hou, H. Y., & Shu, C. M. (2017). Comprehensive runaway kinetic analysis and validation of three azo compounds using calorimetric approach and simulation. Journal of Loss Prevention in the Process Industries, 49, 970–982. https://doi.org/10.1016/j.jlp.2017.05.014
- Liu, S. H., Lin, W. C., Xia, H., Hou, H. Y., & Shu, C.-M. (2018). Combustion of 1-butylimidazolium nitrate via DSC, TG, VSP2, FTIR, and GC/MS: An approach for thermal hazard, property and prediction assessment, Process Saf. Environmental Protection, 116, 603–614. https://doi.org/10.1016/j.psep.2018.03.010
- Liu, S. H., & Shu, C. M. (2015). Advanced technology of thermal decomposition for AMBN and ABVN by DSC and VSP2. Journal of Thermal Analysis and Calorimetry, 121(1), 533–540. https://doi.org/10.1007/s10973-015-4559-3
- Liu, S. H., Yu, Y. P., Lin, Y. C., Weng, S. Y., Hsieh, T. F., & Hou, H. Y. (2014). Complex thermal evaluation for 2,2ʹ-azobis(isobutyronitrile) by non-isothermal and isothermal kinetic analysis methods, J. Journal of Thermal Analysis and Calorimetry, 116(3), 1361–1367. https://doi.org/10.1007/s10973-013-3632-z
- Lv, J., Chen, L., Chen, W., Gao, H., & Peng, M. (2013). Kinetic analysis and self-accelerating decomposition temperature (SADT) of dicumyl peroxide. Thermochimica Acta, 571, 60–63. https://doi.org/10.1016/j.tca.2013.08.029
- Mao, X., Li, Y., Li, Y., Jiang, L., & Wang, X. (2020). Thermal properties of decomposition and explosion for CL-20 and CL-20/n-Al. Journal of Energetic Materials, 38(1), 98–110. https://doi.org/10.1080/07370652.2019.1668875
- Ohama, Y. (1973). Mix proportions and properties of polyester resin concretes. ACI Materials Journal, 40(11), 283–294. https://www.concrete.org/publications/internationalconcreteabstractsportal.aspx?m=details&i=17394
- Ohama, Y. (2003). Recent progress in research and development activities of polymer mortar and concrete in Japan In 4th Asia Symposium on Polymers in Concrete (pp. 39–47). Koriyama, Japan.
- Opfermann, J. (2000). Kinetic analysis using multivariate non-linear regression. Journal of Thermal Analysis and Calorimetry, 60(2), 641–658. https://doi.org/10.1023/A:1010167626551
- Opfermann, J., & Hädrich, W. (1995). Prediction of the thermal response of hazardous materials during storage using an improved technique. Thermochimica Acta, 263, 29–50. https://doi.org/10.1016/0040-6031(94)02392-2
- Parulekar, S. J. (1998). Modal analysis and optimization of isothermal autocatalytic reactions. Chemical Engineering Science, 53(13), 2379–2394. https://doi.org/10.1016/S0009-2509(98)00053-0
- Qi, L., Ma, Z., Han, J., & Xiao, Z. (2020). Effect of different BPS concentration on the thermal decomposition and thermal stability properties of GAP curing. Journal of Energetic Materials, 38(2), 191–205. https://doi.org/10.1080/07370652.2019.1679283
- Saravana Karthika, V., Mohan, A., Dinesh Kumar, R., & Chippymol, J. (2019). Sustainable consideration by characterization of concrete through partial replacement of fine aggregate using granite powder and iron powder. Journal of Green Engineering, 9(4), 514–525. http://www.jgenng.com/wp-content/uploads/2019/12/volume9-issue4-004.pdf
- Talouba, I. B., Balland, L., Mouhab, N., & Abdelghani-Idrissi, M. (2011). Kinetic parameter estimation for decomposition of organic peroxides by means of DSC measurements. Journal of Loss Prevention in the Process Industries, 24(4), 391–396. https://doi.org/10.1016/j.jlp.2011.02.001
- United Nations. (2018). Recommendations on the transport of dangerous goods: Model regulations (Twentieth Revised ed.).
- Vanjeri, V. N., Goudar, N., Kasai, D., Masti, S. P., & Chougale, R. B. (2019). Thermal and tensile properties study of 4-Hydroxycoumarin doped Polyvinyl alcohol/Chitosan blend films. Chemical Data Collections, 23, 100257. https://doi.org/10.1016/j.cdc.2019.100257
- Wang, Q., Rogers, W. J., & Mannan, M. S. (2009). Thermal risk assessment and rankings for reaction hazards in process safety. Journal of Thermal Analysis and Calorimetry, 98(1), 225–233. https://doi.org/10.1007/s10973-009-0135-z
- Wang, S. Y., Kossoy, A. A., Yao, Y. D., Chen, L. P., & Chen, W. H. (2017). Kinetics-based simulation approach to evaluate thermal hazards of benzaldehyde oxime by DSC tests. Thermochimica Acta, 655, 319–325. https://doi.org/10.1016/j.tca.2017.07.015
- Wang, T. S., Liu, S. H., Qian, X. M., You, M. L., Chou, W. L., & Shu, C. M. (2013). Isothermal hazards evaluation of benzoyl peroxide mixed with benzoic acid via TAM III test, J. Journal of Thermal Analysis and Calorimetry, 113(3), 1625–1631. https://doi.org/10.1007/s10973-013-3020-8
- Whitmore, M. W., & Wilberforce, J. K. (1993). Use of the accelerating rate calorimeter and the thermal activity monitor to estimate stability temperatures. Journal of Loss Prevention in the Process Industries, 6(2), 95–101. https://doi.org/10.1016/0950-4230(93)90006-J
- Xi, G. Q., Liu, T., Ma, C., Yuan, Q., Xin, W., Lu, J. J., & Ma, M. G. (2019). Superhydrophobic, compressible, and reusable polyvinyl alcohol-wrapped silver nanowire composite sponge for continuous oil-water separation. Colloids and Surfaces. A, Physicochemical and Engineering Aspects, 583, 124028. https://doi.org/10.1016/j.colsurfa.2019.124028
- Ze, D., Yingying, C., Liping, C., Wanghua, C., Jun, Z., & Beibei, X. (2018). Evaluation of isothermal kinetics of the thermal decomposition of guanidine nitrate in constant volume. Journal of Energetic Materials, 36(4), 412–423. https://doi.org/10.1080/07370652.2018.1473899
- Zeng, P., Chen, X., Qin, Y.-R., Zhang, Y.-H., Wang, X.-P., Wang, J.-Y., Ning, Z. X., Ruan, Q.-J., & Zhang, Y. S. (2019). Preparation and characterization of a novel colorimetric indicator film based on gelatin/polyvinyl alcohol incorporating mulberry anthocyanin extracts for monitoring fish freshness. Food Research International, 126, 108604. https://doi.org/10.1016/j.foodres.2019.108604
- Zhang, R., Gao, J., Wang, J., Zhu, Y., Pan, H., & Chen, L. (2021). Evaluation of thermal hazards based on thermokinetic parameters of 2,4-dinitroanisole. Journal of Energetic Materials, 1–15. https://doi.org/10.1080/07370652.2021.1898490