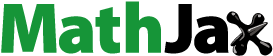
Abstract
In this article, the influence of varying the weight percentage of glass fiber on the water uptake, tensile and flexural strengths of glass fiber-polyester composites are evaluated. The composites are fabricated by hand lay-up process and further subjected to water immersion for a varied time period (between 0 and 180 days) at ambient temperature. Tests for Tensile and flexural strengths are conducted according to the specifications of ASTM. The test results indicate that the increase in the weight percentage of glass fiber enhanced the tensile strength (by 9–17%) and flexural strength (by 10–17%). Higher retention rates of tensile and flexural strengths are detected at higher weight percentages of glass fiber. An 86% retention rate of tensile strength and a 92% retention rate of flexural strength is detected with 50 wt.% glass fiber reinforced, water immersed specimen. The causes for the failure of specimens under tensile load are discovered with the help of SEM images. The experimental data and the data generated by the ExpDec1 model are significantly closer to each other, which indicates that the ExpDec1 model can be used for predicting the values based on the days of immersion.
PUBLIC INTEREST STATEMENT
There is a developing market for the use of high-performance, lightweight composites to replace traditional metals in a variety of applications. Polymer matrix composites (PMC) are frequently utilised as structural materials in a variety of applications. In many applications, PMCs are subjected to wet service conditions in their designed lifespan. Because of wet service conditions, PMCs degrade its properties. In this article, research is carried out on experimental investigation and durability prediction analysis on tensile and flexural strengths of glass fiber-polyester composites upon immersion in water at ambient temperature.
1. Introduction
Composite materials, mostly “polymer matrix composite” (PMCs), are most frequently employed in a wide variety of applications viz., marine, automotive, domestic, construction, etc., (Kini et al., Citation2018). In recent years, “glass fiber reinforced polymer” (GFRP) matrix composites received significant attention as an alternative to conventional metals due to their excellent functional properties(Chawla, Citation2012).
Glass fiber is used as reinforcement in polymer matrix composites in the majority compared to other fibers because of its ease of availability, handling, and lower price (Bhat et al., Citation2019). Glass fiber with unidirectional, bi-directional, or random orientation is used in the production of GFRP. A practical and inexpensive reinforcement is obtained by a random-orientated mat or chopped strand mat (CSM) for several applications. Chopped strand mat provides excellent strand integrity, reasonable wettability and exhibits strength uniformity in all directions(Shettar, Shettigar et al., Citation2020).
Due to its lower cost and excellent corrosion resistance, polyester resin is an extremely popular and widely utilized polymer resin in construction and marine applications. Polyester resin is versatile because of its capability to alter the polymer monomer chains in preparation. The main advantages of polyester resin are dimensional stability, cost, ease of handling, and properties(Dholakiya, Citation2012), (Wang et al., Citation2011).
Understanding the influences of moisture on the retention of various properties of GFRP subjected to long-term immersion in water is crucial. Many researchers explored the impact of moisture absorption on GFRP composites (Zhong et al., Citation2019)–(Rafiq & Merah, Citation2019). The moisture absorption by composites depends upon the fiber weight percentage, temperature, and soaking span(Pandian et al., Citation2014). The absorbed moisture will be in the form of bound and unbound water molecules, which causes revocable and irrevocable changes in the matrix(Shettar et al., Citation2018). Hence, the properties of the composite deteriorate. Matrix degradation influences the interface of matrix and fiber, which in turn directs to delamination of GFRP laminate (Kini, Shettar, Sharma, Hiremath, Gowrishankar et al., Citation2019).
Kini et al. (Kini, Shettar, Sharma, Hiremath, Gowrishankar et al., Citation2019) studied the effects of water immersion on the glass fiber-epoxy composites with a varying weight percentage of glass fiber. In this study, the specimens were subjected to water immersion for 70 days before investigating their tensile and flexural strengths. The results disclose that water immersion has a negative influence on the composite properties. An escalation in the weight percentage of glass fiber has reduced moisture uptake, hence reducing the influence of water immersion on the composite properties. Fraga et al. (Fraga et al., Citation2007) researched the water uptake behavior of polyester matrix and glass fiber composites. Specimens are immersed in distilled water at 20°C for different time laps. Results revealed that polyester matrix absorbed more water than glass fiber-polyester composites because the matrix is more hydrophilic than the glass fibers.
The primary objective of the current study is to investigate the ambient temperature water immersed glass fiber-polyester composites for their tensile and flexural strengths. The second objective is to understand the effects of varying glass fiber weight percentages on the water uptake in addition to the aforesaid strengths under dry and water immersion conditions. The third objective is to explore the property retention and durability prediction analysis by mathematical modeling, which is an essential composite property to carry out before its practical application.
2. Methodology
2.1. Composite preparation
E-Glass fiber of 450 GSM (CSM, Random Orientation) and polyester resin (1 Kg of polyester resin is mixed with 15 ml of MEKP catalyst and 12 ml of cobalt accelerator) are utilized for the composite preparation and supplied by Sri Mookambika Poly Products, Udupi, India. Three varieties of composites are prepared with various weight percentages of glass fiber, i.e., 30, 40, and 50 wt.%. Laminates with a dimension of 300 mm × 300 mm × 3 mm are fabricated by hand lay-up technique and further subjected to compression moulding. The laminates are compressed using a manual compressing machine with a stopper to maintain a consistent thickness of 3 mm. Because of the hand lay-up process, the thickness of casted composites is not uniform before compression moulding. The laminates are kept compressed overnight and cured under the Sun for two days. The cured laminate is used to cut composite specimens to the required dimensions as per ASTM standards.
2.2. Water immersion
Composite samples are immersed in water for 10, 20, 30, 40, 50, 60, 120, and 180 days at ambient temperature. Water uptake tests are carried out according to ASTM D570-98. Dry samples are initially weighed using a digital balance. The samples are then subjected to immersion in tap water at room temperature and atmospheric pressure for time periods as mentioned above.
Samples are removed from the water, dried with a paper napkin, and weighed at the end of 10, 20, 30, 40, 50, 60, 120, and 180 days. The water uptake is evaluated based on changes in weight and time periods.
The percentage of water uptake is given by:
2.3. Testing
The ASTM D3039 standard has been followed for the conduction of tensile tests on a Universal Testing Machine (UTM). For each variety and condition of composite, a minimum of 5 specimens are prepared in a rectangular shape (250 mm X 25 mm X 3 mm). The rough surfaces are smoothed by an emery paper. The test speed (crosshead motion) is maintained at 2.0 mm/min.
The ASTM D7264 standard has been followed for the conduction of the three-point flexural test. A minimum of 5 specimens of each set and condition are cut with dimensions 175 mm X 13 mm X 3 mm. A “ZWICK-ROELL Z020, LOADCELL 20 kN” machine is used to determine the flexural properties of composites. A support span to thickness ratio of 20:1 and a test speed of 2.0 mm/min are maintained during testing.
2.4. Failure mode analysis
In order to fit into the specimen chamber, the SEM specimens are cut to the appropriate dimensions. The specimens are then securely placed on a holder. In order to achieve good imaging, the surface of the specimens must necessarily be electrically conductive. It is also essential for the specimens to be electrically grounded during electron irradiation in order to avoid the electrostatic charge accumulation on the specimens’ surface. When scanned by an electron beam, GFRP specimens tend to charge, especially with the use of secondary electrons. This generally leads to scanning faults. Thus, a low vacuum sputtering equipment is utilised to deposit an ultra-thin electrically conductive substance, such as silver onto the samples. SEM (ZEISS EVO18) images are used to understand the reason for the failure of the specimens under tensile load. Also, SEM images are carefully inspected to learn about the effects of water immersion on the composites.
3. Results and discussion
3.1. Water uptake
As represented in , the overall water uptake of composites decreases gradually as the weight percentage of glass fiber increases. It is observed that water uptake rises with an increased period of immersion, for all cases. However, the rates of water absorption declined over time. The weight percentage of composite has reduced as a result of chemical interaction between polyester and water molecules in the composite at the end stages of longer immersion duration(Nemati Giv et al., Citation2020). The moisture absorption is observed with polyester only because of the “no moisture-absorption property” of glass fiber(Chaichanawong et al., Citation2016). Merah & Mohamed (Merah & Mohamed, Citation2019) reported that the amino-methyl and hydroxyl functional groups which have water-affinity can be found in polyester. Kini et al.(Kini, Shettar, Sharma, Hiremath, Gowrishankar et al., Citation2019) reported that the glass fiber weight percentage increase creates a convoluted path for movement of water molecules and declines the moisture uptake.
3.2. Tensile strength
It is observed from that a rise in wt.% of glass fiber increased the tensile strength. The tensile strength of the composite with 30 wt.% of glass fiber is observed to be 145 MPa, whereas it increased to 158 and 170 MPa at 40 and 50 wt.% of glass fiber, respectively. The composite stiffness increases leading to increased resistance to deformation at a higher weight percentage of glass fiber, which can be comprehended from the stress vs. strain curves (). An increase in stress to failure and reduction in strain to failure can also be from (D. K. Rajak et al., Citation2019), (D. Rajak et al., Citation2019). Rudresh & Ravikumar (Rudresh & Ravikumar, Citation2017) reported that the increase in the fiber–matrix interface area guarantees good load transfer between reinforcement and matrix. This interface area increase is observed with higher glass fiber wt.% in the composites. At an elevated level of stress, the increased glass fiber wt.% causes the inception of plastic deformation (Nuruzzaman et al., Citation2016)–(Shettar, Kini et al., Citation2020).
Table 1. Tensile strength (MPa) of GFRP composites with days of immersion
As shown in and , water-immersed samples exhibit decreased tensile strength for all three variants of composites. Increasing the glass fiber weight percentage declined the reduction in tensile strength. For an immersion period of 180 days, the reduction in tensile strength is observed to be at 15% for a composite with 50 wt.% glass fiber in comparison to 19 & 25% for composites with 40 and 30 weight percentages, respectively. Similarly, for all the immersion periods (no of days), the maximum decrease in tensile strength is observed at 30 wt.% of glass fiber. Immersion of composites in water may affect any or all the composite constituents (Fiber, Matrix, and Interface) due to infiltration of water into the composite. The extent of water absorption by polyester resin is generally governed by the structure of the network, the polarity of molecules, and the degree of crystallinity. Also, damages to the interface of fiber and matrix are caused by the moisture absorbed, which triggers de-bonding and further leads to delamination(DHAKAL et al., Citation2007). Huang & Sun (Huang & Sun, Citation2007) reported that the weakening of bonding between fiber and matrix, and softening of matrix material are also reasons for the decreased composite strength.
As represented in , the retention rate of tensile strength is higher in composites reinforced with 50 wt.% of glass fiber than the specimens with 40 and 30 weight percentages reinforcement for all time periods (no of days) under consideration. For an immersion period of 180 days, the retention rate of tensile strength is observed to be at 85% for a composite with 50 wt.% glass fiber in comparison to 81 & 74% for composites with 40 and 30 weight percentages, respectively. The resistance to moisture absorption by the composite is improved with increases in wt.% of glass fiber(Shettar, Shettigar et al., Citation2020) (Shettar, Kini et al., Citation2020).
3.3. Flexural strength
The three-point bending test for flexural strength demonstrates the material’s behavior to concurrent compressive and tensile loadings. The flexural strength of composites is enhanced with a rise in glass-fiber weight percentages because plastic deformation’s instigation arises at a greater stress level (). As presented in , the flexural strength of the composite is 302 MPa at 30 wt.% of glass fiber, whereas it increased to 333 and 353 MPa at 40 and 50 wt.% of glass fiber, respectively. An increase in glass fiber wt.% toughens the composite and also improves the load-bearing capacity(Elkazaz et al., Citation2020).
Table 2. Flexural strength (MPa) of GFRP composites with days of immersion
As presented in and , the flexural strength of all the three glass fiber weight percentage composites decreased upon immersion in water at ambient temperature. A considerable reduction in flexural strength of composite samples with the increase in immersion time can be noted, and a similar trend is reported by Nemati Giv et al.,(Nemati Giv et al., Citation2020). Increasing glass fiber weight percentage declined the reduction of flexural strength from 16% at 30 wt.% of glass fiber to 14 and 09% at 40 and 50 wt.% of glass fiber, respectively, for an immersion period of 180 days. Similarly, for all the immersion periods (no of days), the maximum and minimum decrease in flexural strength is observed at 30 and 50 wt.% of glass fiber, respectively. Capillary action may cause molecules of water to seep into the composite fiber–matrix interface. A hydrolysis reaction of unsaturated groups within the resin could cause degradation of polyester resin and the interface of fiber and matrix (HELBLING & KARBHARI, Citation2007).
As presented in , for an immersion period of 180 days, the retention rate of flexural strength is observed to be at 91% for a composite with 50 wt.% glass fiber in comparison to 86 & 84% for composites with 40 and 30 weight percentages, respectively. An increase in the weight percentage of glass fiber leads to a composite with decreased permeability.
3.4. SEM analysis
A scanning electron microscope is used to examine the fractured surface of the composites. shows SEM images of the fractured surface of composite samples in both dry and wet conditions. Reasons for failure of the specimens under tensile load are fiber pull-out, matrix fracture, fiber-matrix de-bonding, and fiber breakage. In dry condition (), there is a strong bonding between fiber and matrix, and failure of specimens is due to primarily fiber pull-out. In water immersed conditions (), failure of the specimens is due to degradation of matrix viz., matrix cracking/rupture, flaking, and degradation of the fiber–matrix interface. It can be noticed from that fiber pulled out without any matrix traces at prolonged water immersion because of fiber–matrix interface degradation. The reduction of the strength of composites under water immersion conditions is because of aforesaid reasons.
3.5. Durability prediction analysis
An indirect indication of the durability of the composite is obtained simply by comparison of the performance of the composite under given test conditions. To make a direct estimate of the durability of composite, it is necessary to apply some form of extrapolation technique to their experimental data. The durability prediction equation (EquationEq. 1)Eq.1
Eq.1 is derived based on the nonlinear exponential regression with the help of experimental data (Rao & Husain, Citation2016). The durability equation for the composite is being established by the ExpDec1 model** (One-phase exponential decay function with time constant parameter) and equation as follows (Yang et al., Citation2020);
** Decay models are applicable on data sets where data items are associated with points in a metric space (locations), and there is a notion of “significance” of a data item to a location, which decays (decreases) with the distance between the item and the location. This decrease is modeled by a decay function.
3.5.1. Tensile strength
The relationship between tensile strength Vs. Immersion time (days) for experimental data and data generated by the ExpDec1 model using the origin 2020 software are presented in . The curves of experimental values and data generated by the ExpDec1 model are very closer to each other, indicating that EquationEquation 1Eq.1
Eq.1 and constant values Viz., A1, t1, and y0 can be used to predict the values based on the days of immersion.
Figure 7. Tensile strength Vs. immersion time (days) (a) 30 wt.% of glass fiber (b) 40 wt.% of glass fiber (c) 50 wt.% of glass fiber
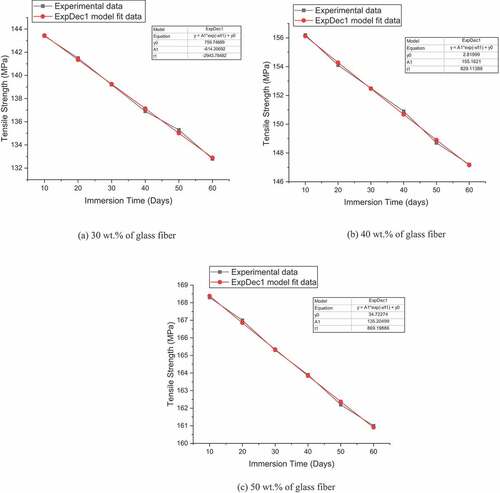
presents the values of the experimental and predicted tensile strength (MPa) of GFRP composites. The percentage of error is very minimal for the duration of immersion up to 60 days. To check the competence of EquationEquation 1Eq.1
Eq.1 and its values, tensile tests are carried out for all three sets of GFRP under a long duration of immersion, i.e., 120 and 180 days. Tensile strength values of GFRP are 120.2 and 107.7 MPa at 30 wt.% of glass fiber, 138.1 and 128.4 MPa at 40 wt.% of glass fiber 153.4 and 145.3 MPa at 50 wt.% of glass fiber for 120 and 180 days of immersion, respectively. The percentage of errors for 120 and 180 days of immersion are varied in minimal in all three sets of GFRP composites. The durability estimation composite is possible with prediction models.
Table 3. Experimental and predicted tensile strength (MPa) of GFRP composites
3.5.2. Flexural strength
The correlation between flexural strength Vs. Immersion time (days) for experimental data and data generated by the ExpDec1 model are represented in . The curves of experimental and ExpDec1 model fit data are very nearer to each other.
Figure 8. Flexural strength Vs. immersion time (days) (a) 30 wt.% of glass fiber (b) 40 wt.% of glass fiber (c) 50 wt.% of glass fiber
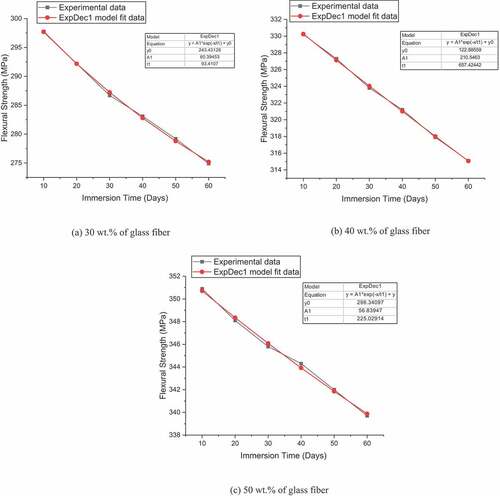
exhibits the values of experimental and predicted flexural strength (MPa) of GFRP composites. For the duration of immersion up to 60 days, the error percentage is negligible. For the purpose of testing the competence of EquationEquation 1Eq.1
Eq.1 and its values, flexural tests are performed for all three sets of GFRP over a long immersion span of 120 and 180 days. Flexural strength values of GFRP are 260.8 and 253.6 MPa at 30 wt.% of glass fiber, 299.2 and 284.9 MPa at 40 wt.% of glass fiber, and 331.1 and 323.2 MPa at 50 wt.% of glass fiber for 120 and 180 days of immersion, respectively. In all three sets of GFRP composites, the percentage of errors for 120 and 180 days of immersion differs in minimum. The composite estimate of durability is possible with prediction models.
Table 4. Experimental and predicted flexural strength (MPa) of GFRP composites
4. Conclusions
In the present work, investigations are carried out to learn the effect of water immersion at ambient temperature on the tensile and flexural strengths of glass fiber-polyester composites. Composites are fabricated by hand lay-up process with varying weight percentages of glass fiber, i.e., 30, 40, and 50 wt.%. Composite specimens are immersed in water at ambient temperature. Tensile and flexural tests are carried out for unaged and aged specimens. SEM images are carefully inspected to learn about the effect of water immersion on the composites. The following conclusions are made on the basis of the study carried out:
The composite’s tensile and flexural strengths are 145 MPa and 302 MPa at 30 wt.% of glass fiber, respectively, whereas tensile and flexural strengths are increased to 158 and 333 MPa 40 wt.% of glass fiber and 170 MPa and 353 at 50 wt.% of glass fiber, respectively
Water-immersed samples show decreased tensile and flexural strengths for all three glass fiber weight percentages. Tensile strength of composite specimens immersed for 180 days reduced by 15–25%, and flexural strength reduced by 9–16%.
The retention rate of tensile and flexural strengths is higher at 50 wt.% glass fiber, i.e., 86 and 92%, respectively, compared to 30 and 40 wt.% of glass fiber.
SEM images of the fractured surface revealed the reasons for the failure of the specimens under tensile load viz., fiber pull-out, matrix fracture, fiber-matrix de-bonding, and fiber breakage.
The error percentages between experimental and predicted values are very minimal (i.e., less than 1%) for the duration of immersion up to 60 days.
The predictive mathematical models show good agreement between experimental data and theoretical values. The percentage of errors for long term of immersion are varied in minimal (between 0.407% and 0.825%) in all three sets of GFRP composites. Therefore, durability estimation composite can be estimated reasonably
Additional information
Funding
Notes on contributors
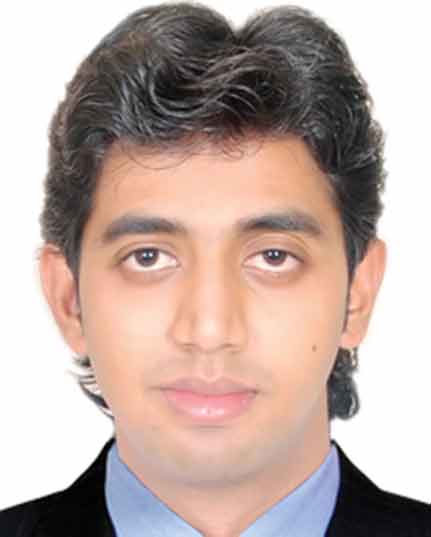
Manjunath Shettar
Mr. Suhas Kowshik, Dr. Gowrishankar M C, Dr. Manjunath Shettar, Mr. Ritesh Bhat, Dr. Gurumurthy B M are the faculty members in the Department of Mechanical and Manufacturing Engineering, Manipal Institute of Technology, Manipal Academy of Higher Education, Manipal, Karnataka, India. The authors’ areas of interest are polymer matrix composites’ characterization, hygrothermal aging and degradation behavior of polymer composites, drilling of polymer composites etc. In this manuscript, the authors found the influence of varying wt.% of glass fiber on the water uptake, tensile and flexural strength of glass fiber-polyester composites.
References
- Bhat, R., Mohan, N., Sharma, S., Pratap, A., Keni, A. P., & Sodani, D. (2019, June). Mechanical testing and microstructure characterization of glass fiber reinforced isophthalic polyester composites. J. Mater. Res. Technol, 8(4), 3653–3661. https://doi.org/10.1016/j.jmrt.2019.06.003
- Chaichanawong, J., Thongchuea, C., & Areerat, S. (2016, May). Effect of moisture on the mechanical properties of glass fiber reinforced polyamide composites. Adv. Powder Technol, 27(3), 898–16. https://doi.org/10.1016/j.apt.2016.02.006
- Chawla, K. K. (2012). Composite Materials. Springer New York.
- DHAKAL, H., ZHANG, Z., & Richardson, M. (2007, June). Effect of water absorption on the mechanical properties of hemp fibre reinforced unsaturated polyester composites. Compos. Sci. Technol, 67(7–8), 1674–1683. https://doi.org/10.1016/j.compscitech.2006.06.019
- Dholakiya, B. (2012). Unsaturated polyester resin for specialty applications. In Polyester. InTech.
- Elkazaz, E., Crosby, W. A., Ollick, A. M., & Elhadary, M. (2020, February). Effect of fiber volume fraction on the mechanical properties of randomly oriented glass fiber reinforced polyurethane elastomer with crosshead speeds. Alexandria Eng. J, 59(1), 209–216. https://doi.org/10.1016/j.aej.2019.12.024
- Fraga, A. N., Frullloni, E., de la Osa, O., Kenny, J. M., & Vázquez, A. (2007, February). Relationship between water absorption and dielectric behavior of glass fiber reinforced unsaturated polyester resin. J. Compos. Mater, 41(4), 393–402. https://doi.org/10.1177/0021998306063789
- HELBLING, C., & KARBHARI, V. M. (2007). Durability of composites in aqueous environments. In Vistasp, M. K. (Ed.), Durability of Composites for Civil Structural Applications (pp. 31–71). Elsevier.
- Huang, G., & Sun, H. (2007, January). Effect of water absorption on the mechanical properties of glass/polyester composites. Mater. Des, 28(5), 1647–1650. https://doi.org/10.1016/j.matdes.2006.03.014
- Kini, U. A., Shettar, M., Sharma, S., Hiremath, P., & Gowrishankar, M. C. (2018, October). Investigation on effect of cold soaking on the properties of nanoclay-GFRP composite. Mater. Res. Express, 6(1), 015206. https://doi.org/10.1088/2053-1591/aae967
- Kini, U. A., Shettar, M., Sharma, S., Hiremath, P., & Gowrishankar, M. C. (2019). Investigation on effect of cold soaking on the properties of nanoclay-GFRP composite. Mater. Res. Express, 6(1), 01-09. https://doi.org/10.1088/2053-1591/aae967
- Kini, U. A., Shettar, M., Sharma, S., Hiremath, P., Gowrishankar, M. C., Hegde, A., & Siddhartha, D. (2019, March). Effect of hygrothermal aging on the mechanical properties of nanoclay-glass fiber-epoxy composite and optimization using full factorial design. Mater. Res. Express, 6(6), 065311. https://doi.org/10.1088/2053-1591/ab0d68
- Merah, N., & Mohamed, O. (2019, January). Nanoclay and water uptake effects on mechanical properties of unsaturated polyester. J. Nanomater, 2019, 1–11. https://doi.org/10.1155/2019/8130419
- Nemati Giv, A., Rastegar, S., & Özcan, M. (2020, January). Influence of nanoclays on water uptake and flexural strength of glass–polyester composites. J. Appl. Biomater. Funct. Mater, 18, 228080002093018. https://doi.org/10.1177/2280800020930180
- Nuruzzaman, D. M., Iqbal, A. K. M. A., Oumer, A. N., Ismail, N. M., & Basri, S. (2016, February). Experimental investigation on the mechanical properties of glass fiber reinforced nylon. IOP Conf. Ser. Mater. Sci. Eng, 114, 012118. https://doi.org/10.1088/1757-899X/114/1/012118
- Pandian, A., Vairavan, M., Jebbas Thangaiah, W. J., & Uthayakumar, M. (2014). Effect of moisture absorption behavior on mechanical properties of basalt fibre reinforced polymer matrix composites. J. Compos, 2014, 1–8. https://doi.org/10.1155/2014/587980
- Rafiq, A., & Merah, N. (2019, January). Nanoclay enhancement of flexural properties and water uptake resistance of glass fiber-reinforced epoxy composites at different temperatures. J. Compos. Mater, 53(2), 143–154. https://doi.org/10.1177/0021998318781220
- Rajak, D., Pagar, D., Menezes, P., & Linul, E. (2019, October). Fiber-reinforced polymer composites: Manufacturing, properties, and applications. Polymers (Basel), 11(10), 1667. https://doi.org/10.3390/polym11101667
- Rajak, D. K., Pagar, D. D., Kumar, R., & Pruncu, C. I. (2019, November). Recent progress of reinforcement materials: A comprehensive overview of composite materials. J. Mater. Res. Technol, 8(6), 6354–6374. https://doi.org/10.1016/j.jmrt.2019.09.068
- Rao, P. S., & Husain, M. M. (2016). Prediction analysis on mechanical properties of hygrothermal ageing GFRP composite laminates. Indian J. Eng. Mater. Sci, 23(4), 288–296. http://nopr.niscair.res.in/bitstream/123456789/39804/1/IJEMS%2023%284%29%20288-296.pdf
- Rudresh, B. M., & Ravikumar, B. N. (2017, July). Effect of short glass fiber loading on the mechanical behaviour of PA66/PTFE blend composites, Trans. Indian Inst. Met, 70(5), 1285–1294. https://doi.org/10.1007/s12666-016-0925-5
- Shettar, M., Chaudhary, A., Hussain, Z., Kini, U. A., & Sharma, S. (2018). Hygrothermal studies on GFRP composites: A Review. MATEC Web of Conferences, 144, 02026. https://doi.org/10.1051/matecconf/201714402026
- Shettar, M., Kini, U. A., Sharma, S., Hiremath, P., & Gowrishankar, M. C. (2020, January). Hygrothermal chamber aging effect on mechanical behavior and morphology of glass fiber-epoxy-nanoclay composites. Mater. Res. Express, 7(1), 015318. https://doi.org/10.1088/2053-1591/ab6405
- Shettar, M., Shettigar, P., Manjunath, M., & Rao, U. S. (2020, July). Study on effect of water soaking conditions on properties and morphology of glass fiber–cement–polyester composites. J. Mater. Res. Technol, 9(4), 8697–8704. https://doi.org/10.1016/j.jmrt.2020.05.117
- Wang, R. M., Zheng, S. R., & Zheng, Y. P. (2011). Matrix materials. In Ru-Min, W., Shui-Rong, Z., Ya-Ping, Z. (Eds), Polymer Matrix Composites and Technology (pp. 101–548). Elsevier.
- Yang, J., Zhang, T., & Sun, Q. (2020, January). Experimental study on flexural fatigue properties of reinforced concrete beams after salt freezing. Adv. Mater. Sci. Eng, 2020, 1–15. https://doi.org/10.1155/2020/1032317
- Zhong, Y., Cheng, M., Zhang, X., Hu, H., Cao, D., & Li, S. (2019, March). Hygrothermal durability of glass and carbon fiber reinforced composites – A comparative study. Compos. Struct, 211, 134–143. https://doi.org/10.1016/j.compstruct.2018.12.034