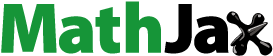
Abstract
Epoxy-cashew nut shell liquid (E-CNSL) composites are prepared by open resin moulding method with varying CNSL content (16 to 30 vol. %.). The tensile properties, hardness and impact strength of E-CNSL composites were investigated as per ASTM standards. It is found that the addition of the CNSL in epoxy increases the elongation at break and tensile strength. The 16 vol. % CNSL addition showed maximum tensile strength, and further increased CNSL deteriorates the tensile properties of the resultant composites. Further, hybrid composites are prepared by reinforcing crumb rubber (CR), short banana fibre (BF) and friction dust (FD) in cashew nut shell liquid (CNSL) mixed epoxy. The samples were tested as per ASTM standards to investigate the basic mechanical properties. It is found that the hybrid composite made of 2.5 vol. % CR, 2.5 vol. % FD and 7.5 vol. % BF in epoxy with 16 vol. % of CNSL showed better properties. Further, the specific wear rate, coefficient of friction and rate of water intake is investigated for the hybrid composite and reported.
PUBLIC INTEREST STATEMENT
The development of useful materials by using discarded waste is one of the methods to contribute towards sustainable development. Further value addition to the recycled product would help in improving the market economy. In this research work, we have attempted to use the waste generated by automobile tyres, cashew industry waste, and agricultural waste to developing a value-added product. This material could be used as an alternative to asbestos based on our studies on mechanical properties, wear properties, and the water absorption rate.
1. 1.Introduction
Cashew nut shell liquid (CNSL), friction dust (FD) are the by-product of the cashew industry (Sharma et al., Citation2020). CNSL is a mixture of four major components, such as anacardia acid, cardanol, cardol, and 2-methyl cardol (Paramashivappa et al., Citation2001). The long unsaturated hydrocarbon chain in the CNSL structure provides additional reacting sites. Hence, it is a versatile material and can synthesize a diverse range of polymers and resins with CNSL (Aggarwal et al., Citation2007).
Banana fibre (BF) is one of the biodegradable natural fibres. It has high tensile strength, small elongation, lightweight, and has a multicellular structure. These properties have attracted the industries, and now BF has become one of the replacements for synthetic fibre in many fibre-reinforced polymer composites used in automobiles.
Epoxy is used for many structural applications due to its excellent mechanical properties and low shrinkage. However, brittleness, low toughness and low degradation temperature (compared to phenolics) of epoxy limit its applications further (Varley et al., Citation2000). It is a petrochemical-based product, price is increasing, and it is not eco-friendly. Hence, from the point of view of environment and cost, researchers are making attempts by modifying the epoxy resin by blending it with bio-based material to make it partially biodegradable and reduce its brittleness. Research studies show that the epoxy-phenolic matrix enhances toughness and heat resistance. Further, to improve the epoxy matrix toughness and make it partially biodegradable, researchers tried to modify the epoxy matrix by mixing CNSL and its derivatives (Cardona et al., Citation2012; Unnikrishnan & Thachil, Citation2006). Agarwal et al. developed epoxy-cardanol-based paint and found an increase in tensile strength and elongation and increased bond strength with steel (Aggarwal et al., Citation2007). Unnikrishnan & Thachil (Unnikrishnan & Thachil, Citation2006) modified epoxy using phenol, cardanol and CNSL, they found the modified epoxy systems exhibit remarkable improved tensile strength, elongation, energy absorption and heat-resistant capacity. As the CNSL contains both phenol and cardinal, it is a suitable biobased resin to modify the epoxy resin. Cardona et al. (Citation2012) demonstrated that due to the introduction of cardanol in a phenolic resin, the cardanol molecules go inside the phenolic molecular network. The flexibility will be enhanced and reduces cross-linking. The increased content of cardanol up to 40 Wt. % increased the flexural strength and fracture toughness of cardanol-phenol. Further, Lorwanishpaisarn et al. developed epoxy-CNSL/polycaprolactone copolymer and found developed material is a promising alternative for bio-related smart material, dual-activated sensors and coatings with self-healing ability (Lorwanishpaisarn et al., Citation2019). Eksik et al. developed nanocomposite with cashew nut shell-derived epoxy reinforced with graphene platelets and found promising properties suitable for high-performance applications (Eksik et al., Citation2016). Avancha et al. developed jute felts reinforced CNSL modified soy resin composites and found increased water-resistant due to the addition of 4 wt.% CNSL. Improved tensile and dynamic mechanical properties were also noticed. They recommended developed composites for applications in railway and automobile interiors, furniture, toys, etc. (Avancha et al., Citation2020).
In the present work, the short BF extracted from the banana tree stem used as one of the reinforcements, CR and FD fillers are used as friction modifier in the proposed composites. The CNSL is mixed with epoxy and used as a matrix, attempted to determine the mechanical, tribological properties of resultant composites.
2. Materials and methods
2.1. Materials
Commercial grade bisphenol-A-based unmodified liquid epoxy resin was obtained from M/s Atul, Gujarat, India, 1041 Phenalkamine hardener (a green product) derived from Cardanol used as an epoxy-curing agent was obtained from M/s Adarsha chemical industries, Karkala, India. The CNSL was used as a bio-resin to modify the epoxy resin, and CNSL-based FD fillers were used as a friction modifier obtained from the same industry. The short BF were procured from the local suppliers in Mysore, Karnataka, India, used as reinforcement. The CR obtained from M/s. Venus rubber, Bangalore, used as friction modifying fillers.
2.2. Fabrication of composites and samples
A homogeneous mixture of epoxy resin and CNSL at different volume fractions (16%, 20%, 23%, 26%, and 30%) was prepared in a batch by stirring 30 min at 1500 rpm using a magnetic stirrer. The hardener 1014 was added to the modified epoxy in the ratio of 100:80, and the mixing process was continued for 5 min. The resultant mixture involving E-CNSL (Epoxy/CNSL) with hardener was carefully poured into the cavity of the open mould prepared by wire cut machining to obtain physical, mechanical, wear, and water absorption specimens as per ASTM standards. The E-CNSL samples in the mould were cured at room temperature for about 24 hours. Similarly, CNSL16-CR-FD-BF composite samples were prepared by homogeneous mixing of 16 Vol % CNSL blended epoxy (E-CNSL16) at a different volume fraction of CR, FD and BF (varied 2.5%, 5.0% and 7.5%). shows the various ingredients used in different stages to prepare hybrid composite material. The designation of samples and material combination details are reported in .
Table 1. Sample designation and material combination
2.3. Characterization and testing
The tensile properties of E-CNSL and all types of E-CNSL16-CR-FD-BF composite samples were investigated as per ASTM-D-638 using the tensile testing machine of 50 kN capacity (Make: BISS ITW Model: AC-05-01-T2). The Shore-D surface hardness (shore D) of the composite samples was tested as per ASTM-D-2240-86 using a durometer. The impact strength (I) was tested as per ASTM: D 256 using the Izod impact testing machine (pendulum type, PSI, India). The water absorption test was carried out as per ASTM-D-570. As per ASTM: G 99–05, a pin-on-disc tribometer was used to conduct a sliding wear test for E-CNSL16-CR2.5-FD2.5-BF7.5 composite samples. Molded specimens of size 8 mm diameter 20 mm length were used for the sliding wear tests. In each experimental trial, the wear loss (W) was estimated using Equationequation (1)(1)
(1) .
where WC and WW are the weight of the wear sample before sliding wear test (g) and after wear test (g) respectively. The specific wear rate (KS) was calculated using Equationequation (2)(2)
(2)
where L = Normal applied load (N), Sliding distance , where d = Track diameter on sliding disc, duration of sliding = t, speed of the sliding disc = N rpm. The sliding velocity of (V) of the pins was calculated as
m.s−1. Plot of coefficient friction (µ), specific wear rate versus sliding velocity at different normal load, and the sliding distance range was reported.
3. Results and discussion
3.1. Tensile properties of E-CNSL composites
) shows the load versus elongation behavior of neat epoxy and E-CNSL composite samples subjected to tensile loading. The addition of the CNSL up to 16 vol. % improves tensile strength (σ) and strain (e). The tensile plot compares the area under the tensile load versus elongation curve of neat epoxy, which is lesser than the area under load versus elongation curve of E-CNSL. It indicates that the addition of the CNSL toughening occurs without scarifying the σ of the epoxy matrix. This property was attributed to the synergistic effect of epoxy molecules and phenol molecules present in the E-CNSL matrix. The addition of 20 vol. % and 23 vol. % of CNSL of the epoxy, leads to more linear chain formation in the matrix structure. This change results in enhanced flexibility. However, slightly decreasing the resultant E-CNSL matrix’s crosslinking ability is responsible for slightly reduced σ. The optimum value of the CNSL content is 16% by volume, considering σ. Further, increased CNSL content with epoxy deteriorates the σ due to reduced crosslinking ability and improved linear chain structure. The higher content of CNSL in epoxy deteriorates the tensile load carrying capacity of the resultant material due to poor structural integrity. Hence, above 23 vol. % with CNSL addition to epoxy is not beneficial.
Figure 2. Tensile load versus elongation plot of (a) Neat Epoxy (E) and Epoxy-CNSL composites (b) Epoxy-CNSL-CR-FD-BF hybrid composites
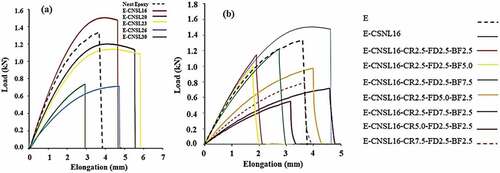
and ) suggest that in addition to strengthening, the modulus (E) of the epoxy is enhanced by adding 16 vol. % of CNSL. However, further addition leads to a more linear chain formation, and a reduction in crosslinking structure, which increases flexibility and worsens the E. However, the E, σ and Ɛ of E-CNSL samples up to 23% of CNSL is a marginal difference.
Table 2. Mechanical properties of neat epoxy (E) and epoxy-CNSL(E-CNSL) samples
3.2. Shore hardness of E-CNSL composites
The shore hardness (H Shore D) of E-CNSL samples has slightly decreased as the content of CNSL increases. This decrease is attributed to reduced cross-linking structure and increased linear chain structure with increased CNSL to epoxy matrix. Due to this, the material becomes more elastic. Hence, the E-CNSL becomes softer, and the plastic deformation takes at a lower compressive load compared to neat epoxy. From the basic mechanical properties, the optimum CNSL content in the blend of the E-CNSL matrix is 16 vol. %. Hence, to make a hybrid composite, we have selected a combination of CR, FD, BF, while the CNSL content in the blend matrix maintained at 16% by volume.
3.3. Mechanical properties of epoxy/CSNL16-CR-FD-BF hybrid composites
) and show the tensile load versus elongation behavior of E-CNSL16-CR-FD-BF hybrid composite samples. It is observed that due to the addition of the CR and FD to E-CNSL16, the σ, E, and H Shore D have decreased. The rate of decrease of these properties is proportional to the content of CR and FD. This decrease is due to the contribution of the inherent property of CR and FD, which leads to the E-CNS16-based hybrid composites becoming more elastic.
Table 3. Mechanical properties of neat epoxy (E), E-CNSL16 and E-CSNL16-CR-FD-BF (hybrid) samples
We have observed that the E-CNSL16-CR-FD-BF composites perform based on the content of CR and FD. The material behaves as rigid, at lower content of these two ingredients in E-CNSL16, keeping the modulus very nearer to neat E-CNSL16. The composite consisting of the high content of BF showed better σ and elongation. However, the addition of CR and FD makes the composite more elastic, and the modulus of the composites has decreased. The rubber content influences the shore hardness. The high-volume percent of rubber decreased the hardness of the resulting composites.
3.4. Water absorption study
shows the % age of water absorption as a function of immersion time of neat epoxy, E-CNSL composites, and E-CNSL16-CR2.5-FD2.5-BF7.5 composites. The neat epoxy composite water absorption is linear with an immersion time of up to 24 h, and further immersion will not increase the water absorption due to saturation. This observation is attributed to the fact that neat epoxy samples follow the Fickian diffusion law. However, there is an increase in water absorption with an increase in immersion time for all the E-CNSL composites. However, all types of E-CNSL composites exhibit a low rate of absorption than E-CNSL16-CR2.5-FD2.5-BF7.5 composites. The composite consists of 16 vol. % CNSL with BF, FD, and CR shows a higher rate of water absorption as compared to other E-CNSL and neat epoxy composites. This increase can be attributed to higher voids in the hybrid composites due to FD particle and BF, and the hygroscopic nature of BF and FD present in the composite. Further, the neat epoxy samples, E-CNSL composites, and E-CNSL16-CR2.5-FD2.5-BF7.5 samples exhibit less than 1% water absorption, better for an outdoor application. This decrease is attributed to the effect of phenalkamine hardener derived from cardanol used as a curing agent.
3.5. Friction and wear
), 4(b) and 4(c) show the tribological behavior of E-CNSL16-CR2.5-FD2.5-BF7.5 composite samples subjected to sliding wear test using pin-on-disc test rig. We can observe from ) that as the sliding speed increases the wear rate decreased for a sliding distance of 500 m and 1000 m, respectively. Further, continuing sliding up to 1500 m, the specific wear rate is independent of a selected range of sliding speed. Also, the specific wear rate decreased with prolonged sliding distance. As the sliding duration increases due to increased sliding distance, wear debris detached from the hybrid material, which are collected on the steel disc, creates a film, as shown in (d). This film acts as a solid lubricant that separates the contact between the hybrid composite sample pin surface with the steel disc’s surface. This step develops a stable boundary layer, reliable lubrication, and avoids further wear. Further, we have observed a good range of friction coefficient, which is required for the braking effect.
Figure 4. Specific wear rate and coefficient of friction of E-CNSL16-CR2.5-FD2.5-BF7.5 composites at (a) 30 N, (b) 60 N, and (c) 90 N, (d) digital photo of hybrid composite wear debris film formed on the wear track of steel disc
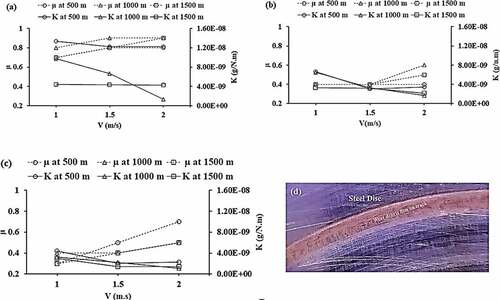
We can see a lower range of specific wear rate and coefficient of friction at higher loads of 60 and 90 N as compared to lower load of 30 N, as shown in (a), 4(b) and 4(c). We can also observe a similar range of coefficient of friction and specific wear rate for higher sliding distance. This trend can be attributed to the ingredients such as FD, BF, CR, and CNSL that support the wear-resistant property of hybrid composites. The FD maintains the friction coefficient, and the debris obtained by the friction dust creates a stable lubricant film. Also, the CR particles and CNSL jointly support the hybrid composite’s elastomeric behavior and help in the increased real area of contact by elastic deformation, thus increasing the load-carrying capacity.
Further, the specific wear rate versus load-carrying capacity (PV), coefficient of friction versus load-carrying capacity of hybrid composite is plotted, as shown in ) and 5(b). At higher PV values, the specific wear rate is lower as the proposed hybrid material has a high load-carrying capacity and wear-resistant property. However, the higher material loss due to wearing was observed at lower sliding speed and lower sliding distance due to the contribution of the initial wear of irregular asperities on the surface. The present hybrid material exhibits the uniform friction coefficient between 0.4 and 0.6 at a higher duration of sliding and higher speed. Further, with lower specific wear rate of the order of 4.00 × 10−9 g.N−1.m−1 is found to be attractive, particularly because of functional service life at higher PV values. Based on this, we can recommend this material for further investigation of tribo-behavior at higher temperatures.
4. Conclusions
Addition of CNSL up to 16 vol% increases the elongation at break and tensile strength of the epoxy. Hence, the mechanical properties indicate that the optimum CNSL content in the E-CNSL matrix is 16 vol. %. The composite samples prepared by reinforcing 2.5 vol. % CR, 2.5 vol. % FD and 7.5 vol. % BF in epoxy/16 vol. % of CNSL showed improved mechanical properties. These composites showed better mechanical and tribological properties. They are made up of automotive, agricultural, and cashew industry wastes and are partially bio-based. We recommend this composite is required to test further at high temperature, and it may be the asbestos-free alternative materials for brake applications in automobiles.
Disclosure statement
We declare that there is no conflict of interest on this research work.
Additional information
Funding
Notes on contributors
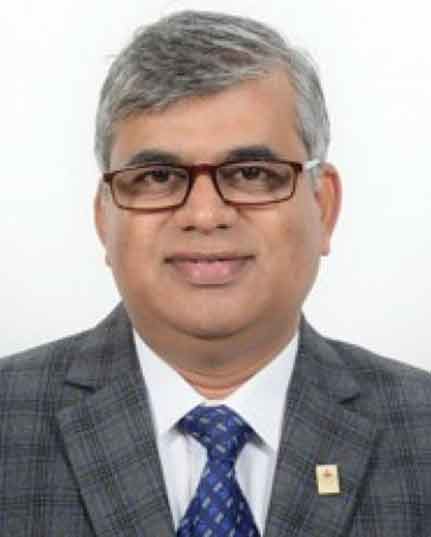
T. Shivakumar
Dr B. Shivamurthy is an associate professor in the department of mechanical and manufacturing engineering at Manipal Institute of Technology, Manipal, India. He has received a B. E. degree in Mechanical Engineering from Mysore University, M. Tech. degree from Sri Jayachamaraendra College of Engineering, Mysore, and Ph.D. from the department of metallurgical and materials engineering, NITK Surathkal, India. He has more than 10 years of industrial experience in the field of polymer processing. He has contributed substantially to the erection and commissioning of the polymer plant. For the last 20 years, he has been involved in teaching graduate, undergraduate, and research students. Also, he has been an active researcher in polymer nanocomposites, tribology, ballistic materials, EMI shielding materials, special coatings, and surface engineering. He has guided several undergraduate and postgraduate students in addition to Ph.D. research scholars. He has published several research articles in national and international journals of repute.
References
- Aggarwal, L. K., Thapliyal, P. C., & Karade, S. R. (2007). Anticorrosive properties of the epoxy-cardanol resin-based paints. Progress in Organic Coatings, 59(1), 76–11. https://doi.org/10.1016/j.porgcoat.2007.01.010
- Avancha, S., Behera, A. K., Sen, R., & Adhikari, B. (2020). Accelerated weathering analysis of jute reinforced cashew nut shell liquid modified soy based green composite. SPE Polymers, 1(2), 81–89. https://doi.org/10.1002/pls2.10020
- Cardona, F., Kin‐Tak, A. L., & Fedrigo, J. (2012). Novel phenolic resins with improved mechanical and toughness properties. Journal of Applied Polymer Science, 123(4), 2131–2139. https://doi.org/10.1002/app.34719
- Eksik, O., Maiorana, A., Spinella, S., Krishnamurthy, A., Weiss, S., Gross, R. A., & Koratkar, N. (2016). Nanocomposites of a Cashew Nut Shell Derived Epoxy Resin and Graphene Platelets: From Flexible to Tough. ACS Sustainable Chemistry & Engineering, 4(3), 715–1721. https://doi.org/10.1021/acssuschemeng.5b01684
- Lorwanishpaisarn, N., Kasemsiri, P., Jetsrisuparb, K., Knijnenburg, J. T. N., Hiziroglu, S., Pongsa, U., Chindaprasirt, P., & Uyama, H. (2019). Dual-responsive shape memory and self-healing ability of a novel copolymer from epoxy/cashew nut shell liquid and polycaprolactone. Polymer Testing, 81, 106159. https://doi.org/10.1016/j.polymertesting.2019.106159
- Paramashivappa, R., Kumar, P. P., Vithayathil, P. J., & Rao, A. S. (2001). Novel method for isolation of major phenolic constituents from cashew (Anacardium occidentale L.) nut shell liquid. Journal of Agricultural and Food Chemistry, 49(5), 2548–2551. https://doi.org/10.1021/jf001222j
- Sharma, P., Gaur, V. K., Sirohi, R., Larroche, C., Kim, S. H., & Pandey., A. (2020). Valorization of cashew nut processing residues for industrial applications. Industrial Crops and Products, 152(15), 112550. https://doi.org/10.1016/j.indcrop.2020.112550
- Unnikrishnan, K. P., & Thachil, E. T. (2006). The modification of commercial epoxy resin using cardanol-formaldehyde copolymers. International Journal of Polymeric Materials, 55(5), 323–338. https://doi.org/10.1080/009140390945178
- Varley, R. J., Hodgkin, J. H., Hawthorne, D. G., Simon, G. P., & McCulloch, D. (2000). Toughening of a trifunctional epoxy system Part III. Kinetic and morphological study of the thermoplastic modified cure process. Polymer, 41(9), 3425–3436. https://doi.org/10.1016/S0032-3861(99)00503-0