Abstract
Incorporation of nanoparticles in polymeric matrices to develop polymer nanocomposite with an idea to maximize the “nano-effect” derived out of the nanoparticles and to minimize the disadvantages of the polymer is an emerging area of research. Nanoparticles in the form of nanosheets, nanotubes, nanofibrils and quantum dots are incorporated in polymers to fabricate polymer nanocomposites, which possess tunable mechanical, thermal, electrical, magnetic and optical properties. However, to realize a quality composite, it is imperative to ensure that the selected nanoparticles are uniformly distributed within the matrix and have good compatibility with the matrix material. Thus, one should ensure strict control over the selection and operating parameters of the fabrication method of polymer nanocomposites. The paper presents a review of various fabrication techniques employed to obtain nanoparticle-filled polymer nanocomposites. An effort is also made to understand the effect of such nanoparticles on the mechanical and thermal properties of polymer nanocomposites.
PUBLIC INTEREST STATEMENT
Polymer composites have carved a niche in the field of materials science due to the ever-increasing demand for lightweight and high strength materials. The advent of nanotechnology has attracted the attention of both industry and academia, as this opens up enormous opportunities to manipulate the matter of interest at atomic and molecular level. The researchers can tune the material properties at its molecular or supramolecular level to come up with high-performance nanomaterials with improved mechanical, thermal, electrical and magnetic properties. Such nanomaterials can bring down the bulk and scale of the materials considerably allowing for convenient handling and portability of the applications. Nanomaterials are such small materials whose dimensions are in nanoscale (1 nm to 100 nm). Polymer nanocomposites are an effort to amalgamate the advantages of such nanomaterials into polymer composites through the incorporation of nanoparticles as fillers in the selected matrices.
1. Introduction
Polymer nanocomposites (PNCs) are a new class of high-performance materials which are composed of polymeric matrices reinforced with organic or inorganic nanoparticles (NPs) as fillers possessing at least one of their dimension in nanoscale (10–100 nm) which are dispersed homogeneously in the selected matrix and are processed via mechanical blending and/or co-polymerization techniques (Huang et al., Citation2012). The reinforcing materials can be of any form ranging from simple fibres and particles to complex-layered materials and clusters which are dispersed within a natural or synthetic polymeric matrix. The basic idea behind the use of nano-scale fillers is to derive the property of high-aspect ratio of such nano-materials due to their large surface area for a fixed volume (Fan et al., Citation2015; Ren et al., Citation2014) . Such nanomaterials impart superior properties to the PNCs by magnifying the reinforcing effect. Invariably, the properties of such PNCs are dictated by the size of the nano-filler (Xie et al., Citation2018) and the soundness of interface structure between the selected matrix and the nano-filler material (Papageorgiou et al., Citation2014). Owing to their high-aspect ratio, it is observed that the addition of a very low weight percent of nano-scaled filler can bring about a largely pronounced improvement in mechanical, thermal, electrical and magnetic properties of the PNCs (Chaharmahali et al., Citation2014). Polymer composites have proved their mark by delivering reliable performances in applications such as aerospace, automotive, biomedical, surface coatings, energy storage and dielectrics (Huang & Jiang, Citation2015; Naskar et al., Citation2016; Njuguna et al., Citation2012; Tamayo et al., Citation2016).
2. Classification of PNCs
PNCs are categorically classified into three types based on the geometrical dimensions of the incorporated NPs (Fu et al., Citation2019). The first category, which is of layered PNCs, comprises of such PNCs in which the two-dimensional nanoparticles in sheet form possessing a thickness ranging from 1 to few nm and length ranging from a few 100 to 1000 nm, are used as fillers. Under this category, generally PNCs are filled with either nanoclay (Uddin, Citation2008), graphene (Pandey et al., Citation2008) or titanium carbide sheets (H. Zhang et al., Citation2016). The second category comprises of such PNCs in which the nanoparticles possess any two dimensions which is at nano-scale range and a comparatively large third dimension. Such dimensions impart the fillers a slightly elongated shape and thus fibres and tubes having nm length, essentially form the fillers for PNCs in the second category. Carbon nanotubes (Naz et al., Citation2016), carbon and cellulose fibres (Dufresne, Citation2018; Ladani et al., Citation2018), naturally occurring tubular clay called as halloysite (Krishnaiah et al., Citation2017) are few examples of tubular and fibril nanofillers used in PNCs. The third category of PNCs is composed of such PNCs which incorporate those nanofillers that have all their three dimensions in nm. Most of the spherical nanofillers having identical three dimensions are used as fillers in PNCs falling under the third category. Examples of such spherical nanofillers include spherical silica, quantum dots and NP aggregates (Vengatesan & Mittal, Citation2016).
2.1. PNCs incorporating layered filler
The most widely used nano-scaled layered filler is the layered silicate in the fabrication of PNCs. The crystal structure of layered silicates is composed of a centrally placed octahedral sheet of metal atoms, which is sandwiched between two external tetrahedral silica sheets such that the oxygen ions of the central octahedral sheet is also shared by the tetrahedral silica sheets (Schoonheydt et al., Citation2018). Such nano-scaled layered silicate has dimensions in the range of ≈1 nm thick and a 100–1000 nm long. These individual layers are often stacked one above the other with a minute gap between the sheets. Such minute gap is often termed as “interlayers” or “intergalleries” that are filled with a positively charged ion. The concentration of such ion is not constant and is different between different layers. These layered silicates exhibit extreme hydrophilicity and are thus rendered not suitable to be directly incorporated within most of the polymeric matrices as direct interaction may lead to poor interaction between the filler and the matrix phase. Hence, nanoclay is often pretreated with ion-exchange treatment to improve its compatibility with most of the polymeric matrices.
Based on the nature of the various composite phase components intended for use and the route of processing, three primary PNCs can be fabricated in which layered silicates are used as fillers in various polymeric matrices as illustrated in .
Figure 1. Different types of PNCs incorporating layered silicate fillers (Fu, S. et al., Citation2019)
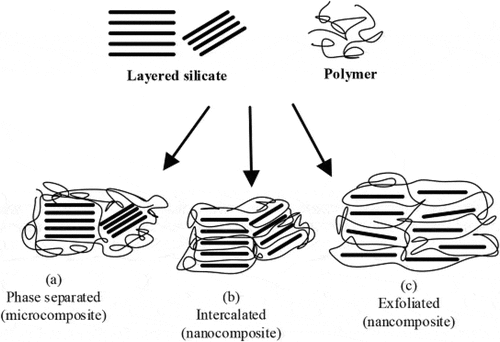
) depicts a microcomposite which is formed when the selected polymer matrix material does not intercalate between the layered silicate sheets. ) illustrates a PNC in which the polymer chain is intercalated into the intergalleries of the layered silicate resulting in a multi-tier ordered structure of alternating polymer and filler components. Exfoliated PNCs are obtained when the silicate layers are uniformly dispersed within the selected polymeric matrix as shown in ).
Through the study of the available literature, it is established that there are four important processing routes that are employed to fabricate PNCs with layered silicate as fillers (Alexandre & Dubois, Citation2000; Mittal, Citation2009). These fabrication processes are: (1) exfoliation-adsorption, (2) in-situ intercalative polymerization, (3) melt intercalation and (4) template synthesis. Exfoliation-adsorption technique is best-suited for polymers, which are highly soluble in water and the silicate layers should demonstrate high expandability to generate intercalated PNCs. In this method, initially, the silicate layers are exfoliated or allowed to expand in a solvent (toluene, water or chloroform). This is followed by thorough mixing of the polymer and exfoliated layered silicate solution, which results in the intercalation of the polymer chain in the intergallaries of the layered silicate through the solvent displacement. When the remaining solvent is evaporated, a multi-layered structure of alternating polymer and inorganic filler layers is formed (Kredatusová & Brožek, Citation2012).
In-situ intercalative polymerization is a technique in which the exfoliation of the silicate layers is first achieved in a monomer (solution) and the polymerization of the monomer is achieved between the exfoliated layers. The initiation of polymerization can be brought about by the application of heat or by diffusing an initiator or catalyst in the solution prior to exfoliation of silicate layers (Xu et al., Citation2016). depicts the in-situ polymerization technique.
In melt intercalation, the layered silicate compatible with the selected polymer is introduced into the molten polymer in the absence of solvent. The polymer intercalates between the layers of the silicate resulting in intercalated composite. illustrates the melt intercalation technique.
Melt intercalation method is widely adapted owing to its compatibility with industrial mass production techniques such as extrusion and injection molding. The absence of solvent renders the process safe and environment-friendly (G. Zhang et al., Citation2017).
The template synthesis technique is widely used for the production of two-layer hydroxide-based PNCs and its use for producing PNCs with layered silicate fillers is still in its nascent stage (Prevot & Tokudome, Citation2017). In this method, polymer templates are used to grow layered silicates. This technique is suitable for such polymers, which show greater affinity to water and are readily soluble in it (Weber, Citation2017). In this method, the polymer promotes the hydrothermal crystallization of layered silicates and remains entrapped within the growing silicate layers.
2.2. PNCs incorporating nanofibre and/or nanotube filler
Carbon nanotubes (CNTs) and carbon nanofibres (CNFs) have emerged as the most sought-after fillers to fabricate high-performance PNCs owing to their excellent structural rigidity and thermal stability. The various methods used to fabricate PNCs with CNTs as filler include: (1) Solution mixing method, (2) Melt mixing method, (3) In-situ polymerization and (4) Electrospinning technique.
Solution processing or solution mixing () is one of the convenient ways of fabricating CNT-filled PNCs. In this method, the CNTs are introduced into a suitable solvent and are thoroughly blended with the aid of high shear homogenization techniques or sonication method or magnetic/mechanical stirring. This results in homogeneous dispersion of CNTs within the polymeric material. This is followed by the dissolution of the polymer within the solution of solvent and CNT. The solvent is then removed either through evaporation or via coagulation to obtain the CNT-filled PNC.
Another method to fabricate CNT-filled PNCs is through melt processing or melt mixing. This method is widely used to produce CNT-filled thermoplastic-based PNCs owing to its highly economical processability and conduciveness to be incorporated for large-scale production processes (Grady, Citation2011). In this method, CNTs are mixed with the thermoplastic matrix material in required weight percentage. The application of heat results in the formation of viscous liquid of thermoplastic matrix material. The viscous liquid is then made to enter the compounder or screw extruder with an attached high-shear mixer. This results in high shear mixing of the CNTs within the thermoplastic matrix and results in a uniform dispersion of the CNTs within the PNCs. depicts a typical twin-screw extruder used in industries to disperse CNTs in a thermoplastic matrix. The extruded PNC can be then sent into an injection molding machine to obtain the desired end product with required geometrical shape.
Figure 5. Melt processing technique(W. Khan et al., Citation2016)
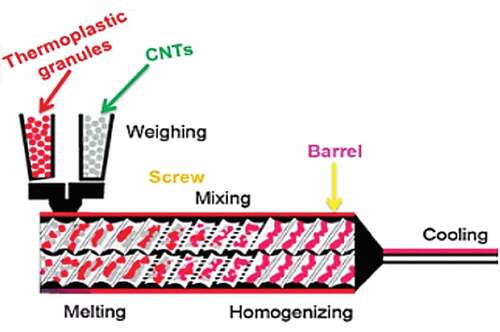
For polymer matrices which exhibit least affinity to water and are thermally unstable, in-situ polymerization is the only viable processing route to fabricate CNT-based PNCs (Chang & Liu, Citation2010). However, in-situ polymerization is also used in cases wherein there is complete absence of the above-mentioned limitations for obtaining good-quality PNCs with higher loading of CNTs within the matrix. In this method, CNTs are initially dispersed in a suitable monomer solution and then the polymerization is ensued to form PNCs. Functionalization of the CNTs or the employment of grafting techniques can yield extremely good results for dispersing large quantity of CNTs in the matrix with perfect interphases between the various phases of the PNCs (Oh et al., Citation2010). depicts the in-situ polymerization technique to obtain CNT filled PNCs.
Electrospinning is another novel method which is used to fabricate PNC-based nanofibres (Lee et al., Citation2018). In this method, a circuit formed by interconnecting an automatic syringe fixed with a fine-tipped needle, a direct current source and an earthed collector plate, is used to produce nanofibres of PNCs. The CNTs are dispersed in the selected polymeric resin through sonication and this solution is electrically charged during the ejection of the polymer solution jet through the needle tip. The flow of jet is somewhat halted due to the surface tension of the polymer solution. The applied voltage should be sufficiently high to induce electrical stresses to overpower the surface tension and facilitate the stretching of the jet from the needle tip so that nanofibres are formed. The PNC nanofibres solidify during their travel from the needle-tip to collector terminal. Various operating parameters dictate the morphology and uniformity in dimensions of the electrospun nanofibres such as the viscosity of the polymer solution, needle tip dimensions, applied voltage strength, distance between the needle-tip and the collector, geometry of the collector plate etc. (Q. Chen et al., Citation2011). (Santos et al., Citation2018) depicts the electrospinning technique.
Figure 7. electrospinning technique (Santos, J. P. F., et al., Citation2018)
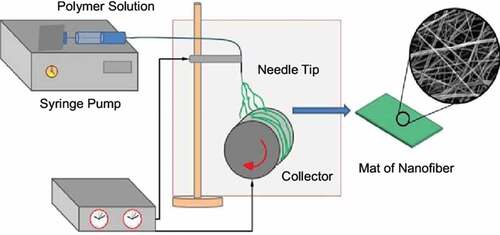
2.3. PNCs incorporating spherical NPs as filler
NPs as fillers are widely used to fabricate high-performance PNCs as the processing of such PNCs is often easy and suitable for mass production. But, it is mandatory to achieve a uniform dispersion of the selected NPs within the polymeric matrices and often a challenge as the near spherical NPs tend to agglomerate owing to an increased surface forces of attraction. The available literature highlights three methods to fabricate defect-free, good quality PNCs filled with NPs and those methods include direct mixing, in-situ polymerization and solution mixing techniques.
Direct mixing methods such as melt mixing, miscible solvent mixing and powder metallurgy techniques are effectively used to prepare PNCs filled with NPs. However, all such methods suffer a major drawback whenever large quantity of NPs are to be incorporated resulting in severe clustering/agglomeration of NPs within the polymeric matrix. Hence, it is needless to say that proper surface treatment of NPs is essential to process PNCs with uniformly dispersed NPs (Kango et al., Citation2013). In in-situ polymerization, the NPs are dispersed in a suitable monomer and the resultant solution is polymerized to obtain PNCs. In few of the published research, it is found that in-situ polymerization is not suitable for very small NPs measuring less than 10 nm (Rahman & Padavettan, Citation2012; Reynaud et al., Citation2001).
Another popular method to disperse metal-oxide NPs within the polymeric matrix is the sol-gel technique (Guo et al., Citation2007, Citation2009; De Oliveira et al., Citation2010). This method combines in-situ formation of the required NPs followed by in-situ polymerization to fabricate particle-filled PNCs. This method is also widely used to homogeneously disperse different inorganic NPs in various organic polymer matrices to fabricate hybrid PNCs (Haeri et al., Citation2017; Pandey & Mishra, Citation2011). Sol-gel technique has enabled the dispersion of very tiny particles whose dimensions are extremely less than the polymer chain length. But, this method suffers from a major disadvantage in that the choice of polymer material used in this method is strictly limited to alcohol and/or water soluble resins, which are able to bind with the hydroxyl groups of the organic phase through the generation of a hydrogen bond (S.-D. Jiang et al., Citation2014; Zhou et al., Citation2017). Another hindrance in this technique is its effect on the formation of the particle (inorganic) network structure, which possess a challenge in the employment of control over the size and dispersion of the particle fillers in hybrid PNCs.
In order to overcome the above-mentioned limitations, a novel method has been proposed to synthesize hybrid PNCs called the site selective molecular hybrid method (Goda, Citation2018). This method is widely used to disperse fine silica particles in a silane modified polymer matrix. In this technique, polymerization of an alkoxysiloxane compound is ensued to produce polyalkoxysiloxane having a functional group similar to glycidyl group. With the aid of this glycidil-like group, the introduction of the polyalkoxysiloxane in the required positions of the polymer is carried out. A sol-gel hardening reaction is produced at the site of introduction of polyalkoxysiloxane to produce very fine silica as the formation of siloxane bond is cut-short by the polymer (Naito et al., Citation2018). The major advantage of this new method is the erudite control over the structure enabling the generation of application specific materials.
3. Inorganic metal-oxide NPs as fillers in PNCs
Incorporation of inorganic nano-scaled particles in various polymeric matrices has gained widespread attention owing to the ease of handling and manufacturing, tailorability of material properties and economic viability (Saba et al., Citation2014). Usually in particle-filled PNCs, the continuous polymeric phase is attached to the NPs via a covalent or coordination bond. When metal-based NPs are incorporated in PNCs, a polymeric film is produced on the surface of metal NPs and this condition allows for the generation of a unique interphase between the polymer and the particle (Ciprari et al., Citation2006). Metal-oxides derived out of pure metals exhibit different structural geometries in comparison with their base metal and also possess unique metallic, semiconducting or insulating characteristics. Metal-oxides possessing a bulk crystal structure impart the PNCs of the required structural rigidity. Due to the nanoscopic scale, most metal-oxides possess discrete energy levels leading to the transport of electrons, which result in a change in electron band-gap. Thus, metal-oxide-filled PNCs exhibit some unique electronic, chemical and physical properties. The incorporation of highly conductive metal-oxide NPs within the non-conducting polymer matrix can result in a PNC with enhanced conductivity, which can be tailored by changing the loading of the conductive metal-oxide NPs. Hence, most of the properties of the PNCs depend upon the metal-oxide particle loading, its geometry and its adhesion and dispersion within the selected polymeric matrix.
In one of the researches (Salahuddin et al., Citation2017) comparing the effect of zinc oxide (ZnO) NPs and nanotubes dispersed in epoxy composites, it is found that the addition of as low as 0.8% ZnO has remarkably improved the mechanical properties of the epoxy PNCs. The tensile strength improved by 27% and toughness was increased by 105% compared with neat epoxy. Greater flexibility of the PNCs was found for ZnO nanotube addition of 1 wt.% and ZnO NP addition of 0.8 wt.%. Another published work highlighted the effect of obtaining NP dispersion through chemical route and aims to investigate the interfacial bonding, resistance to UV absorption and the solvent effect on the dispersion of NPs (Wong et al., Citation2014). The research group fabricated ZnO NP (in varied wt.%)-filled epoxy PNCs by dissolving ZnO in two different solvents, vinamely, isopropyl alcohol and ethanol, and then this was mixed with epoxy resin and glass fibre-reinforced epoxy PNCs were fabricated through hand layup route. It was reported that isopropyl alcohol blending had a positive effect on the dispersion of ZnO NPs, mechanical and UV absorbability properties of the PNCs.
It is known that surface treatment of NPs helps in reducing their surface energy and allowing for uniform dispersion of treated NPs uniformly within the matrix material. Such well-dispersed NPs eventually promote attractive mechanical, thermal and electrical properties in a PNCs. However, one of the researches (Wong et al., Citation2016) highlight that silane surfactant treatment of ZnO NPs had no effect for UV absorption in ZnO/DGEBA/micro-HGF composite. Some of the published work studied the effect of ZnO NP on the curing behavior of the epoxy resin (Ramezanzadeh et al., Citation2011), and it was reported that high volume percent addition of ZnO NPs-induced steric hindrance, which adversely affected the curing behavior of epoxy PNCs. Also, it is highlighted that addition of more than 3.5 wt.% of ZnO NPs resulted in the reduced reaction of epoxy resin and the cross-linker that will adversely affect the PNC properties.
The size along with the wt.% addition of the NPs incorporated also has a bearing on the final properties of the PNCs. In one of the work (Al-Turaif, Citation2010), it is found that the incorporation of 17 nm and 50 nm sized TiO2 at 3 wt.% addition resulted in improved tensile strength of epoxy PNCs, whereas for 200-nm-sized TiO2, the improvement in tensile strength was observed at 5 wt.% addition of TiO2 NP. In the same work, it is also highlighted that improvement in flexural properties of epoxy PNCs is found at as less as 1 wt.% addition of TiO2 and further increment in wt.% addition of NPs did not yield any increment in flexural properties. In contrast to ZnO NPs, it is found that TiO2 NPs act as catalysts and facilitate curing in epoxy PNCs (Parameswaranpillai et al., Citation2013). Yet another work involving in-situ synthesis of epoxy/TiO2 PNCs indicate that the addition of TiO2 NPs improved the thermal resistance of the PNCs by reducing the glass transition temperature of the epoxy PNCs. The work also suggests that higher loading of TiO2 resulted in the reduction of mechanical properties owing to severe agglomeration of NPs (Al-Ajaj et al., Citation2013). The addition of TiO2 NP in epoxy polymer matrix improved the hygrothermal behavior of epoxy PNCs for as low as 0.1 wt.% addition of TiO2 NPs (Nayak & Ray, Citation2018).
4. Effect of size and dispersion of NPs in PNCs
An NP is a scientific term coined to classify such small particles which cannot be deciphered through naked eyes and are known to possess at least one dimension which is less than 100 nm. A more stringent definition defines NPs as such particles whose properties are dependent directly on their size [57]. This definition restricts the size of the NP to be smaller than 10–20 nm. As stated in the aforesaid paragraphs, the size and dispersion of the NPs play a significant role in determining the final properties of the PNCs. This is because of the pronounced increment in surface properties with the reduction in particle size. As the particle size reduces, the surface-to-volume ratio increases. This implies that whenever a material is composed of nano-scaled particles, the surface area of such material increases and such nano-sized materials have a greater number of surface particles. This can be explained through the consideration of a typical case, wherein a 10 nm particle possesses nearly 20% of its particles at its surface as opposed to a 3 nm particle, which has almost 50% of its particles at the surface. This property of the nanomaterials renders them highly reactive. Most of the materials, which are chemically inert in their bulk form, are often found to be severely reactive when they are brought down to nanoscale form. When nanomaterials are incorporated in polymeric matrices, such surface properties largely influence the interfacial properties between the matrix and the reinforcing NPs, tendency of the formation of aggregates/agglomeration of NPs within the matrix and finally leads to the enhancement or reduction in the material property of the PNC. It is found that the high surface area of the NPs results in setting up of an intense Vander Waal’s forces of attraction between the particles which result in agglomeration of NPs (Zare, Citation2016). Such agglomeration has a negative impact on the mechanical properties of the PNCs as the material is devoid of active interphases due to lack of interfacial area (Chen et al., Citation2015; Shin et al., Citation2015).
In order to realize the nano-effect of NPs on the final properties of the PNCs, it is also mandatory to ensure a uniform dispersion of NPs within the selected polymeric matrices as such dispersion has an impact on the polymer chain structure. The uniform dispersion of the NPs in the polymer matrix is controlled by various factors such as interphases between the polymer and NP, size of NPs and the weight/volume percent of NPs in the polymeric matrix (Gam et al., Citation2012; Holt et al., Citation2014). Researchers have also studied the influence of shape of NPs on the interfacial reactions in a PNC. The shapes of the NPs are found to bear a direct relation with the surface area to volume ratio and thus influence their interaction with the polymeric matrix material (Li et al., Citation2012).
5. Methods to obtain uniform dispersion of NPs in PNCs
In order to extract maximum out of the reinforcing NPs, it is all the more important to ensure that the selected NPs are uniformly dispersed within the polymeric matrix and a strong interfacial adhesion between the matrix and the reinforcing phase is established. The attainment of these conditions has always posed a challenge in the fabrication of PNCs due to the tendency of the NPs to form into aggregates/clusters/agglomerates due to the strong force of attraction between the particles. Researchers emphasize that the knowledge of the surface characteristics of the NPs is a must to overcome the problem of uniform dispersion of the same within the selected matrix. For instance, if the NP surface exhibits greater affinity to moisture and such a particle is to be incorporated as a filler in a nonpolar polymeric matrix, then it is highly advisable to convert the surface properties of the NP to render it hydrophobic (R. Chen et al., Citation2009; Chen et al., Citation2010). Hence, surface modification of the nano-fillers is carried out to ensure a uniform dispersion of the NPs within the polymeric matrix. Most of the polymeric matrices demonstrate a greater degree of hydrophobicity, while the inorganic nano-fillers are generally hydrophilic. Thus, the surface modification techniques are aimed to decrease the hydrophilicity and increase the hydrophobicity of the inorganic nano-fillers so that they become compatible with the matrix material (Müller et al., Citation2017).
The surface modification of inorganic NPs can be brought about either by physical methods or through chemical interactive techniques between the NP and the surface modifier. Physical methods involve the setting up of forces such as electrostatic, hydrogen bonding and van der Waals forces between the nano-fillers and the polymeric matrix material by coating the inorganic NPs with a surfactant with a low molecular weight or by a polymer which has a reasonably high molecular weight (Rong et al., Citation2006). In surfactant treatment, the strong surface forces on the inorganic NP allows for the adherence of one of the surfactant’s polar group onto its surface through the setting-up of strong electrostatic forces of attraction. This interaction results in the formation of ionic bonds between the surfactant molecules and the NP, which in turn results in the reduction of surface energy of the modified NP (Gu et al., Citation2016; Hussain et al., Citation2017; Yao et al., Citation2017). The modified NP with reduced surface energy shows little tendency to attract the neighboring NPs and the chances of formation of aggregates are reduced to a greater extent (Kalia et al., Citation2014). Another physical technique employed for surface modification of the NPs is the encapsulation technique. In this method, inorganic NPs are encapsulated by a previously formed polymer material or the polymeric encapsulation material is grown over the NP through in-situ techniques. When encapsulation is brought about by the preformed polymeric material, one has to ensure that the preformed polymeric material called hyperdispersant (Tien et al., Citation2014) is composed of functional groups such as hydroxyl (found in phenols and alcohols), carboxyl (found in carboxylic acids), carbonyls (found in ketones, aldehydes and quinones) and nitro (found in organic compounds of nitrogen). These functional groups ensure that a proper bonding between the NP and the polymeric material is setup (Dasari et al., Citation2016). However, it is observed that encapsulation through in-situ generation of polymer coating is found to form a uniform coating over the NP (G. Li et al., Citation2015). Solution or emulsion polymerization routes are employed to cover the NPs by in-situ generation of a polymeric membrane (Liang et al., Citation2017; M. U. Khan et al., Citation2016). Here, emulsion polymerization ensues on the NP surface through the adsorption of the monomer molecule onto the NP surface which results in the formation of an adsorbed layer. The second step polymerization now occurs within this adsorbed layer which ensures the creation of a strong polymeric shell within which the NP is encapsulated (Huang & Jiang, Citation2015; Morsi et al., Citation2016).
The major drawback in the aforesaid physical techniques is it is highly possible that the polymeric coatings over the NPs tend to desorb from the particle surface. To overcome this limitation, researchers suggest the formation of covalent bonds between the matrix and the NP through ensuing chemical reactions setup by modifiers. One such widely used method is the coupling agent treatment (Pour & Ghaemy, Citation2014). A wide variety of coupling agents are employed to improve the wettability of the NPs with the matrix material. A few of the widely used coupling agents include silane, zirconate and titanate (Mallakpour & Madani, Citation2015). Although the use of such coupling agents is an easy and economical method for surface modification of NPs, it is observed that a uniform surface coverage of the NP is hard to achieve in this method (Tong et al., Citation2018). Grafting of macromolecules over the NP surface is found to overcome such limitations (C.-C. Lin et al., Citation2014). Polymer grafting techniques are successfully employed to modify the NPs into a novel amphiphile, which shows an increased hydrophilicity as well as lipophilicity (S. K. Kumar et al., Citation2017). This characteristic feature improves the spatial organizing ability of the NPs within the polymeric matrix. Polymer grafting of NPs is obtained through the application of “grafting to” or “grafting from” techniques. In “grafting from” method, the functional monomers are made to adhere to the particle surface followed by polymerization resulting in a uniformly coated NP. Whereas in “grafting to” technique, preformed polymers consisting of highly reactive end groups are made to chemically react with the surface functional groups of the NPs. It is found that the “grafting from” technique is more easy and reliable method for surface treatment of NPs.
Another technique which is widely employed to obtain uniform dispersion of the NPs in the matrix is through ultrasonication. In this technique, large amount of energy transfers obtained via ultrasonic cavitation is utilized to create disruption in the physical and/or chemical interactions between the particles and other phases of the composite (Pokharel & Lee, Citation2014). Ultrasonic energy is used to create long-chain radicals, which interact chemically with the nano-clay surface through the breakage of carbon bonds in nano-clay-reinforced composites (R. Wang et al., Citation2014). This allows for uniform distribution of the nano-clay within the selected matrix and also improves the wettability of the filler phase with the matrix phase (Tomić et al., Citation2016). Ultrasonication is also known to break-up the NP aggregates and contributes to a significant reduction in the formation of NP aggregates/clusters/agglomerates within the selected matrix (Ghaleb et al., Citation2014; Shanshool et al., Citation2016). Several research findings have also highlighted the advantages of ultrasonication technique to increase the basal spacing and uniform dispersion of layered silicates in composites filled with nano-clay (Naderi-Samani et al., Citation2017).
Mechanical alloying is another method used to tailor the particle geometry to synthesize NPs and also to alter the surface dynamics of such NPs so as to ensure uniform dispersion and excellent wettability with the matrix material during the fabrication of nanocomposites (Mehrizi et al., Citation2016). High energy ball milling is used to breakdown the particles to nano-scales. Surfactants are employed during the ball milling process to ensure that the produced NPs do not agglomerate through the creation of steric hindrance which lowers the surface tension of the particles (Ullah et al., Citation2014).
6. Influence of NPs on the mechanical properties of PNCs
PNCs, in recent years, have evolved as multi-functional materials catering to the need of high-technological applications such as aerospace, automobile, biomedical devices, electronic and energy storage applications. In order to enhance the reliability of PNCs in various applications, it is all the more important to understand the influence of NPs on the mechanical properties of the composite. Several researchers have put forward theories which throw light upon the synergies between the polymeric matrix material and the chemistry and/or geometry of the NPs along with interfacial interactions between the filler and the matrix that by and large influence the mechanical properties of the PNCs (Choi et al., Citation2015; Khoshkava & Kamal, Citation2013; Kutvonen et al., Citation2012; Maghsoudlou et al., Citation2019). It is well understood that the nano-scale filler particles, the polymer matrix material and additional substitute materials that are added to obtain a healthy interphase play a crucial role in the evolution of the final mechanical property of the multiphase material. It is also important to understand the interaction mechanism between various phases in the PNCs that give rise to novel microstructures and the multilevel complex stress transfer between such phases (Crosby & Lee, Citation2007). Out of several mechanisms that influence the final mechanical property of the composite, one mechanism that has a strong bearing on the mechanical property is the particle-to-particle interaction within the selected polymeric matrix. The tendency of the NPs to form as agglomerated clusters/aggregates due to increased surface area and the subsequent development of a strong interactive forces of attraction between the particles tend to negatively influence the mechanical properties of the PNCs by imposing restriction on the effective interfacial area (Bazrgari et al., Citation2018; Kang et al., Citation2017; Machrafi et al., Citation2016). Such agglomeration is also dependent on the orientation and shape of the NPs (Sharifzadeh et al., Citation2020). An effective stress transformation mechanism from the brittle matrix to strong NPs can be set up in a PNCs provided there is a big interfacial area to sustain the applied loads (Choi et al., Citation2015; H. Li et al., Citation2018; Razavi et al., Citation2018; Shin et al., Citation2015). Published reports indicate that the interfacial area depends on the density and size of the nano-scaled fillers. The reduction in the size and density of the nano-fillers results in the creation of larger interfacial area and thus helps in the improvement of the final mechanical properties of the PNCs (Ashraf et al., Citation2018). Thus, the size of the NP is also an important parameter, which needs due consideration for the improvement in material’s mechanical properties. Along with the particle size, it is also seen that the interphase thickness plays a crucial role in determining the tensile properties of the composite material (Ansari et al., Citation2016; Msekh et al., Citation2018; Zare & Garmabi, Citation2015). This is because, the bonding between the NPs and the matrix is stiff in the interfacial region and this stiff bonding will enable the PNCs to withstand loads and retard the possibility of failure(Sharifzadeh et al., Citation2014). Some of the published work highlight the fact that this crucial interface thickness is related to the quantity of the adsorbed polymer chains of high molar mass onto the surfaces of NPs and this condition can be tailored by varying the loading of NPs(Sharifzadeh & Cheraghi, Citation2021). It is reported that small-sized NP producing a thin and weak interphase is not beneficial for the improvement in the tensile strength of the composite material. This is also true for a large-sized NP producing a thicker interphase. Hence, one cannot negate that both particle size and interphase thickness should be synergized for an optimum tensile strength of the material. In order to obtain a greater reinforcing effect and thereby an improved mechanical property, it is essential to incorporate smaller NPs with thicker interphases.
The effect of volume/weight percentage of NPs within the selected polymer matrix also has a bearing on the final material property (Abedini et al., Citation2019; Doniavi et al., Citation2016). With the study of the available research, it is found that the type of matrix material used to play a vital role in determining the final mechanical properties of the PNCs filled with high volume percent of nano-scale particles (Ürk et al., Citation2016).
High volume percent of nano-fillers is beneficial for nanocomposites where the matrix material is an elastomer rather than a thermoset polymer. This difference can be attributed to the fact that the initial tensile modulus of a thermoset resin is very high as compared to an elastomer. High volume fraction of NPs provides the required densification through particle entanglement in polymeric chains for elastomer matrices with a lower modulus (Mokhireva et al., Citation2017). Generally, it is observed that improvement in mechanical properties is obtained when low volume/weight percent of nano-fillers are incorporated in thermoset resin matrices (Boumaza et al., Citation2016). In most of the thermoset matrices, higher weight percent of NP filler additions results in the formation of particle aggregates of micrometer size that act as stress risers in the nanocomposite, thereby reducing the mechanical properties of the composite material(Martone et al., Citation2010; Nejad et al., Citation2019). Therefore, one has to be judicious not only in the selection of appropriate nano-filler but also in determining as to how much volume/weight percent of the selected nano-filler has to be incorporated so as to achieve the desirable property of the PNCs. Addition of too large or too little quantity of the nanofiller might not yield the desired result. The optimum addition of the nanofiller alone can result in achieving the intended material property suitable to the specific application. lists few of the published work highlighting the effect of NPs on the mechanical properties of PNCs.
Table 1. Summary of the mechanical properties of NP-reinforced PNCs
7. Influence of NPs on the Thermal Properties of PNCs
One of the important demerits of polymer matrix composites is its poor thermal conductivity. This demerit has hindered the wide spread use of polymer composites in applications such as heat exchangers, electrical, electronic and thermal storage devices. This inherent difficulty has also led to a challenging technological development opportunity and researchers are trying to find a way to increase the thermal conductivity and stability of the polymer composites through the application of scientific knowledge. Studying the material properties and understanding the kinematics of heat transfer not only at the micrometer scale but also at the nanometer and atomic level scales has yielded in-depth knowledge and expertise to come up with polymer composites which can perform reliably at higher operating temperatures.
The primary reason behind the poor thermal conductivity of polymer composites is the complex chain structure in a polymer. It is a well-understood phenomenon that heat transfer at a faster pace happens in bulky materials with closely packed molecules. Any minute gap in the material will eventually lead to photon scattering due to which the thermal conductivity reduces. Most of the polymeric chain structures have such gaps/discontinuities throughout the length of the chain, due to which the thermal conductivity reduces. Conductive nanofillers, when incorporated in such polymeric matrices, will bridge the gap and allow for the proper conduction of the energy through the material (H. Chen et al., Citation2016; Pak et al., Citation2012). Amongst the various conductive nanofillers, carbon-based fillers have attracted both industry and academia alike owing to their ability to impart the nanocomposite with enhanced thermal and electrical conductivity (Riquelme et al., Citation2016; Thomassin et al., Citation2013).
Carbon nanotubes (CNT) have garnered widespread attention and have become the candidate nanofillers in many polymeric matrices which require an increased thermal and electrical conductivity. Both single-walled CNTs (SWCNT) and multi-walled CNTs (MWCNT) have been profusely used as conductive fillers in various applications. The attractive features of CNTs arise out of the superior covalent sigma bonding between the carbon atoms. This rigid structure render CNTs extremely stiff and at the very same time to be light in weight. This special atomic structure of CNTs render superior structural stiffness and a very low coefficient of thermal expansion. However, as understood from aforesaid paragraphs, surface treatment of NPs is carried out to disperse them uniformly within the polymeric matrix by reducing the chances of agglomeration. Similarly, functionalization of CNTs is carried out before they are incorporated in PNCs. One of the research findingss report that carboxylic functionalization of MWCNTs yielded improvement in both thermal and electrical conductivity of the PNCs, while in case of SWCNTs, such functionalization reduced the thermal conductivity enhancement (Gulotty et al., Citation2013).
Nanoclay is another such promising NP which is widely used as filler in various polymeric matrices to develop nanocomposites with superior thermal and electrical conductivity. Natural clay platelets are formed as stacked structures wherein the stacked clay sheets range from a few to nearly 1000 sheets. For superior conductivity, normally intercalated and/or exfoliated clay is used as nano-filler in different polymeric matrices as such clay is known to be best for ionic conduction (Choudhary & Sengwa, Citation2011; Tang et al., Citation2012).
It is also important to have a near match of surface energies of the filler material and the polymer resin so that there is improved wettability of the conducting fillers with the selected resin matrix. Few ceramic fillers which are known to possess such match in surface energy along with high thermal conductivity. Boron nitride is one such NP possessing surface energy matching with that of epoxy resin and thus it is used as filler to fabricate epoxy nanocomposites with high thermal and electrical conductivity. Nanosheets of exfoliated hexagonal boron nitride incorporated as fillers in epoxy matrices have found to improve the thermal enhancement factor by over 100% (Z. Lin et al., Citation2014). Liquid exfoliation techniques of boron nitrite have enabled the production of such nanocomposites on large scale. Different functionalization methods of boron nitride also have a strong bearing on the enhancement of thermal conductivity of epoxy nanocomposite. A study indicate that covalent functionalization of boron nitride is most suitable to improve the heat resistance capabilities and conductivities of epoxy nanocomposites in comparison with non-covalent functionalization of boron nitride (Yu et al., Citation2012).
It is also found that even though conductive nano-fillers improve the conductivity of PNCs at lower weight percent addition, the remarkable increase in such conductivity is found when a slightly higher weight percent of fillers are added and such fillers are uniformly distributed within the matrix with little or no agglomeration (Tessema et al., Citation2017). It is also reported that at higher filler loading, thermal conductivity reduces due to ununiformed dispersion of the nanofiller within the matrix because of excessive agglomeration (Machrafi et al., Citation2016).
The shape of the NPs also has a bearing on the final thermal conductivity of the PNCs. In one of the studies, it is shown that spherical silica NP is less effective in increasing the thermal conductivity of the epoxy nanocomposites in comparison with nano-scaled silica fiber (Ren et al., Citation2014). This is mainly due to the formation of a continuous network of hair-like silica fibers within the epoxy resin which is devoid of discontinuities and thus lowers the possibilities of phonon scattering. Also, spherical NPs tend to agglomerate readily as against irregular shaped NPs (Fernandes et al., Citation2013). lists few of the published work highlighting the effect of NPs on the thermal properties of PNCs.
Table 2. Summary of the thermal properties of NP-reinforced PNCs
8. Influence of NPs on the thermo-mechanical properties of PNCs
Modern technological applications are often subjected to severe operating conditions with wide variations in temperatures and/or pressures. As the temperature varies, there is a generation of thermal stresses within the material that have a bearing on its mechanical properties. Under such variable conditions, the materials that are employed should sustain vagaries in temperatures without losing their strength/stiffness. The use of thermally conductive NPs as fillers results in a rapid increase in material temperature upon heating and this phenomenon is used to develop PNCs that can be used as reversible adhesives that can be bonded/de-bonded upon heating. Under such cyclical heating, the PNCs should possess excellent thermo-mechanical properties so that they perform the required function reliably. Hence, the study of thermo-mechanical properties of PNCs is also very important. It is reported that when thermally conducting NPs are used in PNCs which are subjected to repeated cycle of electro-magnetic heating within the melting point range followed by cooling, resulted in the introduction of thermo-oxidative degradation which severely reduces the toughness of the PNCs. Also, it is to be noted that when NPs with high thermal conductivity such as Fe3O4 is used as fillers in PNCs that are subjected to electro-magnetic heating, there is formation of agglomerated NPs and/or voids within the PNCs due to the generation of eddy currents within the PNCs [140]. This phenomenon can be overcome by subjecting the NPs to chemical functionalization prior to their addition into the polymeric matrices. In one such study, the spherical SiC NPs-filled PS and PMMA PNCs were subjected to heating and the effect of temperature on the mechanical properties of the PNCs is evaluated. Here, it is found that the content of NPs within the polymeric matrix has two effects. On the positive side, as the loading of NPs within the polymeric matrix increases, the coefficient of thermal conductivity of the interphase region between the NPs and the matrix also increases. However, on the negative side as the content of NPs increases, there is a reduction in the thickness of the interphase which makes the PNC susceptible to temperatures. Here, it is found that the PNCs with 4 vol%. SiC when heated up to their glass transition temperature, experienced plastic deformation much earlier than the PNCs with only 1 vol%. SiC NPs (Sharifzadeh & Cheraghi, Citation2021). To enable the PNCs to fare well under cyclical heating/cooling regimes, researchers have suggested the use of the concept of hybridization, wherein more than one type of NPs are used as fillers in the PNCs. A study reports that the use of CNT along with GO NPs and CNFs with GOs as fillers in polymeric matrices creates a better synergy leading to uniform dispersion and the formation of a strong interphase between the matrix and NPs. This synergy between the NPs creates a thorough conductive paths within the bulk of the PNC that enable the material to withstand stresses (Charitos et al., Citation2021). It is reported that for PNCs to have superior thermo-mechanical properties, it is important that there is a uniform dispersion of the NPs within the matrix. The uniform dispersion of the NPs in the polymeric matrix leads to a somewhat reduced relaxation mobility in polymeric material at the interphases which enables the PNCs to withstand high temperatures without compromising on the strength (A. Kumar et al., Citation2017; Park et al., Citation2019).
9. Conclusion
The success of polymer nanocomposites depends upon the selection of proper fabricating route and this in turn depends upon the type of nanoparticles that are being used as nanofillers. Layered silicate nanoparticle-filled PNCs can be fabricated through exfoliation-adsorption, In-situ intercalative polymerization, melt intercalation and template synthesis. In order to fabricate PNCs filled with nanotubes the fabrication techniques such as solution mixing method, melt mixing method, in-situ polymerization and electrospinning technique can be incorporated. While incorporating NPs as fillers in PNCs, the advisable fabrication methods include direct mixing, in-situ polymerization and solution mixing techniques. The uniform dispersion of the NPs is most crucial, yet most difficult part in the fabrication of quality PNCs. Surface modification of NPs either through physical methods or through chemical route are effective in reducing the surface energy of the NPs and thus preventing the agglomeration of the NPs within the polymeric material. Such modified NPs can be uniformly distributed within the matrix with less difficulty. The uniform distribution of the NPs provides stiffness to the matrix material and will aid in the enhancement of the mechanical and thermal properties of the PNCs. Futuristically, one can work on hybridization through the incorporation of more than one type of NPs and efforts can be done to analyze the synergistic effects of such hybridization. Also, the effect of NPs on the environment has to be studied carefully to avoid the environmental hazards through the use of NPs.
Disclosure statement
No potential conflict of interest was reported by the author(s).
Additional information
Funding
Notes on contributors
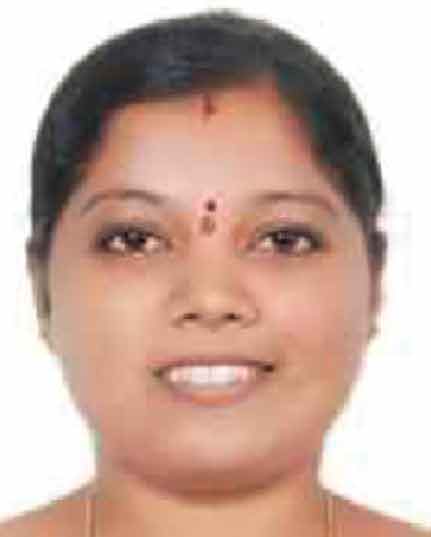
Anupama Hiremath
Dr.Anupama Hiremath is an Assistant Professor in the Department of Mechanical and Manufacturing Engineering at Manipal Institute of Technology, Manipal. She has received her Ph.D. in the field of materials science from Visvesvaraya Technological University in 2020. She has more than 15 years of teaching graduate students of Mechanical Engineering and has been involved in research of composite materials since the days of her graduation. Her research interests include metal matrix composites, polymer matrix composites, self-healing materials and bio-based materials. She has published several research articles in the National and International Journals of repute.
References
- Abedini, A., Asiyabi, T., Campbell, H. R., Hasanzadeh, R., & Azdast, T. (2019). On fabrication and characteristics of injection molded ABS/Al2O3 nanocomposites. The International Journal of Advanced Manufacturing Technology, 102(5–8), 1747. https://doi.org/10.1007/s00170-019-03311-2
- Al-Ajaj, I. A., Abd, M. M., & Jaffer, H. I. (2013). Mechanical properties of micro and nano TiO2/epoxy composites. International Journal of Mining and Metallurgy Engineering, 1 (2), 2320. https://scholar.googleusercontent.com/scholar?q=cache:WeX3r9zvC6wJ:scholar.google.com/+Al-Ajaj,+I.+A.,+Abd,+M.+M.,+%26+Jaffer,+H.+I.+(2013).+International+Journal+of+Mining+and+Metallurgy+Engineering,+1,+2320.&hl=en&as_sdt=0,5
- Alexandre, M., & Dubois, P. (2000). Polymer-layered silicate nanocomposites: Preparation, properties and uses of a new class of materials. Materials Science and Engineering: R: Reports, 28(1–2), 1. https://doi.org/10.1016/S0927-796X(00)00012-7
- Al-Turaif, H. A. (2010). Effect of nano TiO2 particle size on mechanical properties of cured epoxy resin. Progress in Organic Coatings, 69, 241. https://doi.org/10.1016/j.porgcoat.2010.05.011
- Ansari, R., Hassanzadeh-Aghdam, M. K., & Darvizeh, A. (2016). On elastic modulus and biaxial initial yield surface of carbon nanotube-reinforced aluminum nanocomposites. Mechanics of Materials, 101, 14. https://doi.org/10.1016/j.mechmat.2016.07.008
- Ashraf, M. A., Peng, W., Zare, Y., & Rhee, K. Y. (2018). Effects of size and aggregation/agglomeration of nanoparticles on the interfacial/interphase properties and tensile strength of polymer nanocomposites. Nanoscale Research Letters, 13(1), 214. https://doi.org/10.1186/s11671-018-2624-0
- Bazrgari, D., Moztarzadeh, F., Sabbagh-Alvani, A. A., Rasoulianboroujeni, M., Tahriri, M., & Tayebi, L. (2018). Mechanical properties and tribological performance of epoxy/Al2O3 nanocomposite. Ceramics International, 44(1), 1220. https://doi.org/10.1016/j.ceramint.2017.10.068
- Boumaza, M., Khan, R., & Zahrani, S. (2016). RETRACTED: An experimental investigation of the effects of nanoparticles on the mechanical properties of epoxy coating. Thin Solid films, 620, 160. https://doi.org/10.1016/j.tsf.2016.09.035
- Chaharmahali, M., Hamzeh, Y., Ebrahimi, G., Ashori, A., & Ghasemi, I. (2014). Effects of nano-graphene on the physico-mechanical properties of bagasse/polypropylene composites. Polymer Bulletin, 71(2), 337. https://doi.org/10.1007/s00289-013-1064-3
- Chang, C.-M., & Liu, Y.-L. (2010). Functionalization of multi-walled carbon nanotubes with non-reactive polymers through an ozone-mediated process for the preparation of a wide range of high performance polymer/carbon nanotube composites. Carbon N. Y, 48(4), 1289. https://doi.org/10.1016/j.carbon.2009.12.002
- Charitos, I., Georgousis, G., Klonos, P. A., Kyritsis, A., Mouzakis, D., Raptis, Y., Kontos, A., & Kontou, E. (2021). The synergistic effect on the thermomechanical and electrical properties of carbonaceous hybrid polymer nanocomposites. Polymer Testing, 95, 107102. https://doi.org/10.1016/j.polymertesting.2021.107102
- Chen, H., Ginzburg, V. V., Yang, J., Yang, Y., Liu, W., Huang, Y., Du, L., & Chen, B. (2016). Progress in Polymer Science, 59, 41.
- Chen, J., Wang, G.-T., Yu, -Z.-Z., Huang, Z., & Mai, Y.-W. (2010). Critical particle size for interfacial debonding in polymer/nanoparticle composites. Composites Science and Technology, 70(5), 861. https://doi.org/10.1016/j.compscitech.2010.02.004
- Chen, J., Wei, H., Bao, H., Jiang, P., & Huang, X. (2019). Millefeuille-inspired thermally conductive polymer nanocomposites with overlapping bn nanosheets for thermal management applications. ACS Applied Materials & Interfaces, 11(34), 31402. https://doi.org/10.1021/acsami.9b10810
- Chen, J., Yu, Y., Chen, J., Li, H., Ji, J., & Liu, D. (2015). Chemical modification of palygorskite with maleic anhydride modified polypropylene: Mechanical properties, morphology, and crystal structure of palygorskite/polypropylene nanocomposites. Applied Clay Science, 115, 230. https://doi.org/10.1016/j.clay.2015.07.012
- Chen, Q., Zhang, L., Rahman, A., Zhou, Z., Wu, X.-F., & Fong, H. (2011). Hybrid multi-scale epoxy composite made of conventional carbon fiber fabrics with interlaminar regions containing electrospun carbon nanofiber mats. Composite in Part A Applied Scientific Manufactures, 42, 2036. https://doi.org/10.1016/j.compositesa.2011.09.010
- Chen, R., Maclaughlin, S., Botton, G., & Zhu, S. (2009). Preparation of Ni-g-polymer core–shell nanoparticles by surface-initiated atom transfer radical polymerization. Polymer (Guildf), 50(18), 4293. https://doi.org/10.1016/j.polymer.2009.07.012
- Choi, J., Shin, H., Yang, S., & Cho, M. (2015). The influence of nanoparticle size on the mechanical properties of polymer nanocomposites and the associated interphase region: A multiscale approach. Composite Structures, 119, 365. https://doi.org/10.1016/j.compstruct.2014.09.014
- Choudhary, S., & Sengwa, R. J. (2011). Dielectric spectroscopy and confirmation of ion conduction mechanism in direct melt compounded hot-press polymer nanocomposite electrolytes. Ionics (Kiel), 17(9), 811. https://doi.org/10.1007/s11581-011-0585–8
- Ciprari, D., Jacob, K., & Tannenbaum, R. (2006). Characterization of polymer nanocomposite interphase and its impact on mechanical properties. Macromolecules, 39(19), 6565. https://doi.org/10.1021/ma0602270
- Crosby, A. J., & Lee, J.-Y. (2007). Polymer nanocomposites: the “nano” effect on mechanical properties. Polymer Reviews, 47(2), 217. https://doi.org/10.1080/15583720701271278
- Dasari, A., Yu, -Z.-Z., & Mai, Y.-W. (2016). Polymer nanocomposites (pp. 35). Springer.
- de Oliveira, P. W., Becker-Willinger, C., & Jilavi, M. H. (2010). Sol-Gel derived nanocomposites for optical applications. Advanced Engineering Materials, 12(5), 349. https://doi.org/10.1002/adem.201000116
- Doniavi, A., Babazadeh, S., Azdast, T., & Hasanzadeh, R. (2016). An investigation on the mechanical properties of friction stir welded polycarbonate/aluminium oxide nanocomposite sheets. Journal of Elastomers & Plastics, 49(6), 498. https://doi.org/10.1177/0095244316674352
- Dufresne, A. (2018). Cellulose nanomaterials as green nanoreinforcements for polymer nanocomposites. Philosophical Transactions of the Royal Society A: Mathematical, Physical and Engineering Sciences, 376(2112), 20170040. https://doi.org/10.1098/rsta.2017.0040
- Fan, L.-W., Zhu, Z.-Q., Zeng, Y., Xiao, Y.-Q., Liu, X.-L., Wu, -Y.-Y., Ding, Q., Yu, Z.-T., & Cen, K.-F. (2015). Transient performance of a PCM-based heat sink with high aspect-ratio carbon nanofillers. Applied Thermal Engineering, 75, 532. https://doi.org/10.1016/j.applthermaleng.2014.10.050
- Fernandes, N. J., Koerner, H., Giannelis, E. P., & Vaia, R. A. (2013). Hairy nanoparticle assemblies as one-component functional polymer nanocomposites: Opportunities and challenges. MRS Communications, 3(1), 13. https://doi.org/10.1557/mrc.2013.9
- Fu, S., Sun, Z., Huang, P., Li, Y., & Hu, N. (2019). Some basic aspects of polymer nanocomposites: A critical review. Nano Materials Science, 1(1), 2. https://doi.org/10.1016/j.nanoms.2019.02.006
- Gam, S., Meth, J. S., Zane, S. G., Chi, C., Wood, B. A., Winey, K. I., Clarke, N., & Composto, R. J. (2012). Polymer diffusion in a polymer nanocomposite: Effect of nanoparticle size and polydispersity. Soft Matter, 8(24), 6512. https://doi.org/10.1039/c2sm25269d
- Ghaleb, Z. A., Mariatti, M., & Ariff, Z. M. (2014). Properties of graphene nanopowder and multi-walled carbon nanotube-filled epoxy thin-film nanocomposites for electronic applications: The effect of sonication time and filler loading. Composite in Part A Applied Scientific Manufactures, 58, 77. https://doi.org/10.1016/j.compositesa.2013.12.002
- Goda, H. (2018). In Nanoparticle technology handbook (pp. 695). Elsevier.
- Grady, B. P. (2011). Carbon nanotube-polymer composites: Manufacture, properties, and applications. John Wiley & Sons.
- Gu, H., Ma, C., Gu, J., Guo, J., Yan, X., Huang, J., Zhang, Q., & Guo, Z. (2016). An overview of multifunctional epoxy nanocomposites. Journal of Materials Chemistry C, 4(25), 5890. https://doi.org/10.1039/C6TC01210H
- Gulotty, R., Castellino, M., Jagdale, P., Tagliaferro, A., & Balandin, A. A. (2013). Effects of functionalization on thermal properties of single-wall and multi-wall carbon nanotube–polymer nanocomposites. ACS Nano, 7(6), 5114. https://doi.org/10.1021/nn400726g
- Guo, Z., Liang, X., Pereira, T., Scaffaro, R., & Hahn, H. T. (2007). CuO nanoparticle filled vinyl-ester resin nanocomposites: Fabrication, characterization and property analysis. Composites Science and Technology, 67(10), 2036. https://doi.org/10.1016/j.compscitech.2006.11.017
- Guo, Z., Shin, K., Karki, A. B., Young, D. P., Kaner, R. B., & Hahn, H. T. (2009). Fabrication and characterization of iron oxide nanoparticles filled polypyrrole nanocomposites. Journal of Nanoparticle Research, 11(6), 1441. https://doi.org/10.1007/s11051-008-9531-8
- Haeri, S. Z., Ramezanzadeh, B., & Asghari, M. (2017). A novel fabrication of a high performance SiO2-graphene oxide (GO) nanohybrids: Characterization of thermal properties of epoxy nanocomposites filled with SiO2-GO nanohybrids. Journal of Colloid and Interface Science, 493, 111. https://doi.org/10.1016/j.jcis.2017.01.016
- Holt, A. P., Griffin, P. J., Bocharova, V., Agapov, A. L., Imel, A. E., Dadmun, M. D., Sangoro, J. R., & Sokolov, A. P. (2014). Dynamics at the polymer/nanoparticle interface in poly(2-vinylpyridine)/silica nanocomposites. Macromolecules, 47(5), 1837. https://doi.org/10.1021/ma5000317
- Huang, T.-C., Yeh, J.-M., & Lai, C.-Y. (2012). Advances in polymer nanocomposites (pp. 605). Elsevier.
- Huang, X., & Jiang, P. (2015). Core-shell structured high-k polymer nanocomposites for energy storage and dielectric applications . Advanced Materials, 27(3), 546. https://doi.org/10.1002/adma.201401310
- Hussain, T., Ahmad, M. N., Nawaz, A., Mujahid, A., Bashir, F., & Mustafa, G. (2017). Surfactant incorporated Co nanoparticles polymer composites with uniform dispersion and double percolation. Journal of Chemistry, 2017. https://doi.org/10.1155/2017/7191590
- Jia, Z.-R., Gao, Z.-G., Lan, D., Cheng, Y.-H., Wu, G.-L., & Wu, H.-J. (2018). Effects of filler loading and surface modification on electrical and thermal properties of epoxy/montmorillonite composite. Chinese Physics B, 27(11), 117806. https://doi.org/10.1088/1674-1056/27/11/117806
- Jiang, C., Jin, C., Wei, M., Yan, S., & Chen, D. (2018). Mechanical and thermal properties improvement of unsaturated polyester resin by incorporation of TiO2 nanoparticle surface modified with titanate. Materials Research Express, 5(11), 115008. https://doi.org/10.1088/2053-1591/aadc42
- Jiang, S.-D., Bai, Z.-M., Tang, G., Hu, Y., & Song, L. (2014). Fabrication and characterization of graphene oxide-reinforced poly(vinyl alcohol)-based hybrid composites by the sol–gel method. Composites Science and Technology, 102(2014), 51. https://doi.org/10.1016/j.compscitech.2014.06.029
- Kalia, S., Kango, S., Kumar, A., Haldorai, Y., Kumari, B., & Kumar, R. (2014). Magnetic polymer nanocomposites for environmental and biomedical applications. Colloid in Polymer Science, 292, 2025. https://doi.org/10.1007/s00396-014-3357-y
- Kang, W.-S., Rhee, K. Y., & Park, S.-J. (2017). Influence of surface energetics of graphene oxide on fracture toughness of epoxy nanocomposites. Composites Part B: Engineering, 114, 175. https://doi.org/10.1016/j.compositesb.2017.01.032
- Kango, S., Kalia, S., Celli, A., Njuguna, J., Habibi, Y., & Kumar, R. (2013). Surface modification of inorganic nanoparticles for development of organic–inorganic nanocomposites—A review. Progress in Polymer Science, 38, 1232. https://doi.org/10.1016/j.progpolymsci.2013.02.003
- Khan, M. U., Reddy, K. R., Snguanwongchai, T., Haque, E., & Gomes, V. G. (2016). Polymer brush synthesis on surface modified carbon nanotubes via in situ emulsion polymerization. Colloid and Polymer Science, 294(10), 1599. https://doi.org/10.1007/s00396-016-3922-7
- Khan, W., Sharma, R., & Saini, P. (2016). Carbon Nanotub. Prog. their Polym. Compos. https://doi.org/10.5772/62497
- Khoshkava, V., & Kamal, M. R. (2013). Effect of Surface Energy on Dispersion and Mechanical Properties of Polymer/Nanocrystalline Cellulose Nanocomposites. Biomacromolecules, 14(9), 3155. https://doi.org/10.1021/bm400784j
- Kredatusová, J., & Brožek, J. (2012). Preparation of clay mineral polymer nanocomposites by adsorption in solution. Applied Clay Science, 62, 94. https://doi.org/10.1016/j.clay.2012.04.009
- Krishnaiah, P., Ratnam, C. T., & Manickam, S. (2017). Development of silane grafted halloysite nanotube reinforced polylactide nanocomposites for the enhancement of mechanical, thermal and dynamic-mechanical properties. Applied Clay Science, 135, 583. https://doi.org/10.1016/j.clay.2016.10.046
- Kumar, A., Ghosh, P. K., Yadav, K. L., & Kumar, K. (2017). Thermo-mechanical and anti-corrosive properties of MWCNT/epoxy nanocomposite fabricated by innovative dispersion technique. Composites Part B: Engineering, 113, 291. https://doi.org/10.1016/j.compositesb.2017.01.046
- Kumar, S. K., Ganesan, V., & Riggleman, R. A. (2017). Perspective: Outstanding theoretical questions in polymer-nanoparticle hybrids. The Journal of Chemical Physics, 147(2), 20901. https://doi.org/10.1063/1.4990501
- Kutvonen, A., Rossi, G., Puisto, S. R., Rostedt, N. K. J., & Ala-Nissila, T. (2012). Influence of nanoparticle size, loading, and shape on the mechanical properties of polymer nanocomposites. The Journal of Chemical Physics, 137(21), 214901. https://doi.org/10.1063/1.4767517
- Ladani, R. B., Bhasin, M., Wu, S., Ravindran, A. R., Ghorbani, K., Zhang, J., Kinloch, A. J., Mouritz, A. P., & Wang, C. H. (2018). Fracture and fatigue behaviour of epoxy nanocomposites containing 1-D and 2-D nanoscale carbon fillers. Engineering Fracture Mechanics, 203, 102. https://doi.org/10.1016/j.engfracmech.2018.04.033
- Lee, J. K. Y., Chen, N., Peng, S., Li, L., Tian, L., Thakor, N., & Ramakrishna, S. (2018). Polymer-based composites by electrospinning: Preparation & functionalization with nanocarbons. Progress in Polymer Science, 86, 40. https://doi.org/10.1016/j.progpolymsci.2018.07.002
- Li, G., Yu, S., Sun, R., & Lu, D. (2015). Clean and in-situ synthesis of copper–epoxy nanocomposite as a matrix for dielectric composites with improved dielectric performance. Composites Science and Technology, 110, 95. https://doi.org/10.1016/j.compscitech.2014.12.010
- Li, H., Zare, Y., & Rhee, K. Y. (2018). The percolation threshold for tensile strength of polymer/CNT nanocomposites assuming filler network and interphase regions. Materials Chemistry and Physics, 207, 76. https://doi.org/10.1016/j.matchemphys.2017.12.053
- Li, Y., Kröger, M., & Liu, W. K. (2012). Nanoparticle Geometrical Effect on Structure, Dynamics and Anisotropic Viscosity of Polyethylene Nanocomposites. Macromolecules, 45(4), 2099. https://doi.org/10.1021/ma202289a
- Li, Y., Zhang, H., Porwal, H., Huang, Z., Bilotti, E., & Peijs, T. (2017). Mechanical, electrical and thermal properties of in-situ exfoliated graphene/epoxy nanocomposites. Composite in Part A Applied Scientific Manufactures, 95, 229. https://doi.org/10.1016/j.compositesa.2017.01.007
- Liang, C., song, P., Gu, H., Ma, C., Guo, Y., Zhang, H., Xu, X., Zhang, Q., & Gu, J. (2017). Nanopolydopamine coupled fluorescent nanozinc oxide reinforced epoxy nanocomposites. Composite in Part A Applied Scientific Manufactures, 102, 126. https://doi.org/10.1016/j.compositesa.2017.07.030
- Lin, -C.-C., Ohno, K., Clarke, N., Winey, K. I., & Composto, R. J. (2014). Macromolecular Diffusion through a Polymer Matrix with Polymer-Grafted Chained Nanoparticles. Macromolecules, 47(15), 5357. https://doi.org/10.1021/ma501113c
- Lin, Z., Mcnamara, A., Liu, Y., Moon, K., & Wong, C.-P. (2014). Exfoliated hexagonal boron nitride-based polymer nanocomposite with enhanced thermal conductivity for electronic encapsulation. Composites Science and Technology, 90, 123. https://doi.org/10.1016/j.compscitech.2013.10.018
- Ma, L., Wang, G., & Dai, J. (2017). Preparation and properties of graphene oxide/polyimide composites by in situ polymerization and thermal imidization process. High Performance Polymers, 29(2), 187. https://doi.org/10.1177/0954008316634177
- Machrafi, H., Lebon, G., & Iorio, C. S. (2016). Effect of volume-fraction dependent agglomeration of nanoparticles on the thermal conductivity of nanocomposites: Applications to epoxy resins, filled by SiO2, AlN and MgO nanoparticles. Composites Science and Technology, 130, 78. https://doi.org/10.1016/j.compscitech.2016.05.003
- Maghsoudlou, M. A., Isfahani, R. B., Saber-Samandari, S., & Sadighi, M. (2019). Effect of interphase, curvature and agglomeration of SWCNTs on mechanical properties of polymer-based nanocomposites: Experimental and numerical investigations. Composites Part B: Engineering, 175, 107119. https://doi.org/10.1016/j.compositesb.2019.107119
- Mahmoudian, M., Poursattar Marjani, A., Hasanzadeh, R., Moradian, M., & Mamaghani Shishavan, S. (2020). Optimization of mechanical properties of in situ polymerized poly(methyl methacrylate)/alumina nanoparticles nanocomposites using Taguchi approach. Polymer Bulletin, 77(6), 2837. https://doi.org/10.1007/s00289-019-02885-x
- Mallakpour, S., & Madani, M. (2015). A review of current coupling agents for modification of metal oxide nanoparticles. Progress in Organic Coatings, 86, 194. https://doi.org/10.1016/j.porgcoat.2015.05.023
- Martone, A., Formicola, C., Giordano, M., & Zarrelli, M. (2010). Reinforcement efficiency of multi-walled carbon nanotube/epoxy nano composites. Composites Science and Technology, 70(7), 1154. https://doi.org/10.1016/j.compscitech.2010.03.001
- Mehrizi, M. Z., Beygi, R., & Eisaabadi, G. (2016). Synthesis of Al/TiC–Al2O3 nanocomposite by mechanical alloying and subsequent heat treatment. Ceramics International, 42(7), 8895. https://doi.org/10.1016/j.ceramint.2016.02.144
- Mittal, V. (2009). Polymer Layered Silicate Nanocomposites: A Review. Materials (Basel), 2(3), 992. https://doi.org/10.3390/ma2030992
- Mokhireva, K. A., Svistkov, A. L., Solod’ko, V. N., Komar, L. A., & Stöckelhuber, K. W. (2017). Experimental analysis of the effect of carbon nanoparticles with different geometry on the appearance of anisotropy of mechanical properties in elastomeric composites. Polymer Testing, 59, 46. https://doi.org/10.1016/j.polymertesting.2017.01.007
- Morsi, R. E., Labena, A., & Khamis, E. A. (2016). Core/shell (ZnO/polyacrylamide) nanocomposite: In-situ emulsion polymerization, corrosion inhibition, anti-microbial and anti-biofilm characteristics. Journal of the Taiwan Institute of Chemical Engineers, 63, 512. https://doi.org/10.1016/j.jtice.2016.03.037
- Msekh, M. A., Cuong, N. H., Zi, G., Areias, P., Zhuang, X., & Rabczuk, T. (2018). Fracture properties prediction of clay/epoxy nanocomposites with interphase zones using a phase field model. Engineering Fracture Mechanics, 188, 287. https://doi.org/10.1016/j.engfracmech.2017.08.002
- Müller, K., Bugnicourt, E., Latorre, M., Jorda, M., Echegoyen Sanz, Y., Lagaron, J. M., Miesbauer, O., Bianchin, A., Hankin, S., Bölz, U., Pérez, G., Jesdinszki, M., Lindner, M., Scheuerer, Z., Castelló, S., & Schmid, M. (2017). Review on the Processing and Properties of Polymer Nanocomposites and Nanocoatings and Their Applications in the Packaging, Automotive and Solar Energy Fields. Nanomaterials, 7(4), 74. https://doi.org/10.3390/nano7040074
- Naderi-Samani, H., Razavi, R. S., Loghman-Estarki, M. R., & Ramazani, M. (2017). The effects of organoclay on the morphology and mechanical properties of PAI/clay nanocomposites coatings prepared by the ultrasonication assisted process. Ultrasonics Sonochemistry, 38, 306. https://doi.org/10.1016/j.ultsonch.2017.03.009
- Naito, M., Yokoyama, T., Hosokawa, K., & Nogi, K. (2018). Nanoparticle technology handbook. Elsevier.
- Naskar, A. K., Keum, J. K., & Boeman, R. G. (2016). Polymer matrix nanocomposites for automotive structural components. Nature Nanotechnology, 11(12), 1026. https://doi.org/10.1038/nnano.2016.262
- Nayak, R. K., & Ray, B. C. (2018). Influence of seawater absorption on retention of mechanical properties of nano-TiO2 embedded glass fiber reinforced epoxy polymer matrix composites. Archives of Civil and Mechanical Engineering, 18(4), 1597. https://doi.org/10.1016/j.acme.2018.07.002
- Naz, A., Kausar, A., Siddiq, M., & Choudhary, M. A. (2016). Comparative Review on Structure, Properties, Fabrication Techniques, and Relevance of Polymer Nanocomposites Reinforced with Carbon Nanotube and Graphite Fillers. Polymer-Plastics Technology and Engineering, 55(2), 171. https://doi.org/10.1080/03602559.2015.1055504
- Nejad, S. A., Majzoobi, G. H., & Sabet, S. A. R. (2019). Role of sonication time on mechanical properties of graphene oxide/epoxy nanocomposites under quasi-static loading conditions. Iranian Polymer Journal, 28(10), 895. https://doi.org/10.1007/s13726-019-00752-0
- Njuguna, J., Pielichowski, K., & In, F. J. (2012). Advances in Polymer Nanocomposites (pp. 472). Elsevier.
- Oh, W.-C., Ko, W.-B., & Zhang, F.-J. (2010). The functionalization and preparation methods of carbon nanotube-polymer composites: A review. Elastomers Compos, 45, 80.
- Pak, S. Y., Kim, H. M., Kim, S. Y., & Youn, J. R. (2012). Synergistic improvement of thermal conductivity of thermoplastic composites with mixed boron nitride and multi-walled carbon nanotube fillers. Carbon N. Y, 50(13), 4830. https://doi.org/10.1016/j.carbon.2012.06.009
- Panchagnula, K. K., & Kuppan, P. (2019). Improvement in the mechanical properties of neat GFRPs with multi-walled CNTs. Journal of Materials Research and Technology, 8(1), 366. https://doi.org/10.1016/j.jmrt.2018.02.009
- Pandey, D., Reifenberger, R., & Piner, R. (2008). Scanning probe microscopy study of exfoliated oxidized graphene sheets. Surface Science, 602(9), 1607. https://doi.org/10.1016/j.susc.2008.02.025
- Pandey, S., & Mishra, S. B. (2011). Sol–gel derived organic–inorganic hybrid materials: synthesis, characterizations and applications. Journal of Sol-Gel Science and Technology, 59, 73. https://doi.org/10.1007/s10971-011-2465-0
- Papageorgiou, G. Z., Terzopoulou, Z., Bikiaris, D., Triantafyllidis, K. S., Diamanti, E., Gournis, D., Klonos, P., Giannoulidis, E., & Pissis, P. (2014). Evaluation of the formed interface in biodegradable poly(l-lactic acid)/graphene oxide nanocomposites and the effect of nanofillers on mechanical and thermal properties. Thermochimica Acta, 597, 48. https://doi.org/10.1016/j.tca.2014.10.007
- Parameswaranpillai, J., George, A., Pionteck, J., & Thomas, S. (2013). J. Polym, 2013, 183463. https://doi.org/10.1155/2013/183463
- Park, C., Jung, J., & Yun, G. J. (2019). Thermomechanical properties of mineralized nitrogen-doped carbon nanotube/polymer nanocomposites by molecular dynamics simulations. Composites Part B: Engineering, 161, 639. https://doi.org/10.1016/j.compositesb.2019.01.002
- Pokharel, P., & Lee, D. S. (2014). High performance polyurethane nanocomposite films prepared from a masterbatch of graphene oxide in polyether polyol. Chemical Engineering Journal, 253, 356. https://doi.org/10.1016/j.cej.2014.05.046
- Pour, Z. S., & Ghaemy, M. (2014). Thermo-mechanical behaviors of epoxy resins reinforced with silane-epoxide functionalized α-Fe2O3 nanoparticles. Progress in Organic Coatings, 77(8), 1316. https://doi.org/10.1016/j.porgcoat.2014.04.001
- Prevot, V., & Tokudome, Y. (2017). 3D hierarchical and porous layered double hydroxide structures: An overview of synthesis methods and applications. Journal of Materials Science, 52(19), 11229. https://doi.org/10.1007/s10853-017-1067-9
- Rahman, I. A., & Padavettan, V. (2012). Synthesis of silica nanoparticles by sol-gel: Size-dependent properties, surface modification, and applications in silica-polymer nanocomposites—A review. J. Nanomater, 2012, 1. https://doi.org/10.1155/2012/132424
- Ramezanzadeh, B., Attar, M. M., & Farzam, M. (2011). Effect of ZnO nanoparticles on the thermal and mechanical properties of epoxy-based nanocomposite. Journal of Thermal Analysis and Calorimetry, 103, 731. https://doi.org/10.1007/s10973-010-0996-1.
- Razavi, R., Zare, Y., & Rhee, K. Y. (2018). A model for tensile strength of polymer/carbon nanotubes nanocomposites assuming the percolation of interphase regions. Colloids Surfaces A Physicochemical Engineering, Asp, 538, 148. https://doi.org/10.1016/j.colsurfa.2017.10.063
- Ren, L., Pashayi, K., Fard, H. R., Kotha, S. P., Borca-Tasciuc, T., & Ozisik, R. (2014). Engineering the coefficient of thermal expansion and thermal conductivity of polymers filled with high aspect ratio silica nanofibers. Composites Part B: Engineering, 58, 228. https://doi.org/10.1016/j.compositesb.2013.10.049
- Reynaud, E., Jouen, T., Gauthier, C., Vigier, G., & Varlet, J. (2001). Nanofillers in polymeric matrix: A study on silica reinforced PA6. Polymer (Guildf), 42(21), 8759. https://doi.org/10.1016/S0032-3861(01)00446-3
- Riquelme, J., Garzón, C., Bergmann, C., Geshev, J., & Quijada, R. (2016). Development of multifunctional polymer nanocomposites with carbon-based hybrid nanostructures synthesized from ferrocene. European Polymer Journal, 75, 200. https://doi.org/10.1016/j.eurpolymj.2015.12.007
- Rong, M. Z., Zhang, M. Q., & Ruan, W. H. (2006). Surface modification of nanoscale fillers for improving properties of polymer nanocomposites: A review. Materials Science and Technology, 22(7), 787. https://doi.org/10.1179/174328406X101247
- Saba, N., Tahir, P. M., & Jawaid, M. (2014). A review on potentiality of nano filler/natural fiber filled polymer hybrid composites. Polymers (Basel), 6(8), 2247. https://doi.org/10.3390/polym6082247
- Salahuddin, N. A., El-Kemary, M., & Ibrahim, E. M. (2017). High-performance flexible epoxy/ZnO nanocomposites with enhanced mechanical and thermal properties. Polymer Engineering & Science, 57(9), 932. https://doi.org/10.1002/pen.24520
- Santos, J. P. F., Arjmand, M., Melo, G. H. F., Chizari, K., Bretas, R. E. S., & Sundararaj, U. (2018). Electrical conductivity of electrospun nanofiber mats of polyamide 6/polyaniline coated with nitrogen-doped carbon nanotubes. Materials & Design, 141, 333. https://doi.org/10.1016/j.matdes.2017.12.052
- Schoonheydt, R. A., Johnston, C. T., & In, B. F. (2018). Surface and interface chemistry of clay minerals. Developments in Clay Science; Elsevier. 9, 1. https://doi.org/10.1016/B978–0–08–102432–4.00001–9
- Senthil Kumar, M. S., Raju, M. S., Sampath, N., & Chithirai Pon, P. S. (2018). Influence of nanoclay on mechanical and thermal properties of glass fiber reinforced polymer nanocomposites. Polymer Composites, 39(6), 1861. https://doi.org/10.1002/pc.24139
- Shanshool, H. M., Yahaya, M., Yunus, W. M. M., & Abdullah, I. Y. (2016). Investigation of energy band gap in polymer/ZnO nanocomposites. Journal of Materials Science: Materials in Electronics, 27(9), 9804. https://doi.org/10.1007/s10854-016-5046-8
- Sharifzadeh, E., & Cheraghi, K. (2021). Temperature-affected mechanical properties of polymer nanocomposites from glassy-state to glass transition temperature. Mechanics of Materials, 160, 103990. https://doi.org/10.1016/j.mechmat.2021.103990
- Sharifzadeh, E., Ghasemi, I., Karrabi, M., & Azizi, H. (2014). A new approach in modeling of mechanical properties of nanocomposites: Effect of interface region and random orientation. Iranian Polymer Journal, 23(11), 835. https://doi.org/10.1007/s13726-014-0276-1
- Sharifzadeh, E., Tohfegar, E., & Safajou Jahankhanemlou, M. (2020). The influences of the nanoparticles related parameters on the tensile strength of polymer nanocomposites. Iranian. Journal of Chemical Engineering, 17(1), 65. https://dx.doi.org/10.22034/ijche.2020.234505.1337
- Shen, W., Zhang, T., Ge, Y., Feng, L., Feng, H., & Li, P. (2021). Multifunctional AgO/epoxy nanocomposites with enhanced mechanical, anticorrosion and bactericidal properties. Progress in Organic Coatings, 152, 106130. https://doi.org/10.1016/j.porgcoat.2020.106130
- Shin, H., Yang, S., Choi, J., Chang, S., & Cho, M. (2015). Effect of interphase percolation on mechanical behavior of nanoparticle-reinforced polymer nanocomposite with filler agglomeration: A multiscale approach. Chemical Physics Letters, 635, 80. https://doi.org/10.1016/j.cplett.2015.06.054
- Suresh, S., Nisha, P., Saravanan, P., Jayamoorthy, K., & Karthikeyan, S. (2018). Investigation of the thermal and dielectric behavior of epoxy nano-hybrids by using silane modified nano-ZnO. Silicon, 10(4), 1291. https://doi.org/10.1007/s12633-017-9604-3
- Tamayo, L., Azócar, M., Kogan, M., Riveros, A., & Páez, M. (2016). Copper-polymer nanocomposites: An excellent and cost-effective biocide for use on antibacterial surfaces. Materials in Science Engineering C, 69, 1391. https://doi.org/10.1016/j.msec.2016.08.041
- Tang, C., Hackenberg, K., Fu, Q., Ajayan, P. M., & Ardebili, H. (2012). High ion conducting polymer nanocomposite electrolytes using hybrid nanofillers. Nano Letters, 12(3), 1152. https://doi.org/10.1021/nl202692y
- Tessema, A., Zhao, D., Moll, J., Xu, S., Yang, R., Li, C., Kumar, S. K., & Kidane, A. (2017). Effect of filler loading, geometry, dispersion and temperature on thermal conductivity of polymer nanocomposites. Polymer Testing, 57, 101. https://doi.org/10.1016/j.polymertesting.2016.11.015
- Thipperudrappa, S., Kini, A. U., & Hiremath, A. (2019). An experimental study to evaluate the effect of TiO 2 nanoparticles on the strength and stability of unidirectional glass fiber reinforced epoxy composites. Materials Research Express, 6(11), 115347. https://doi.org/10.1088/2053-1591/ab5031
- Thipperudrappa, S., Ullal Kini, A., & Hiremath, A. (2020). Influence of zinc oxide nanoparticles on the mechanical and thermal responses of glass fiber-reinforced epoxy nanocomposites. Polym Compos, 41(1), 174. https://doi.org/10.1002/pc.25357.
- Thomassin, J.-M., Jerome, C., Pardoen, T., Bailly, C., Huynen, I., & Detrembleur, C. (2013). Polymer/carbon based composites as electromagnetic interference (EMI) shielding materials. Materials Science and Engineering: R: Reports, 74(7), 211. https://doi.org/10.1016/j.mser.2013.06.001
- Tien, P., Lin, C. H., Wang, C.-Y., & Sura, R. K. (2014). Thermal grease having low thermal resistance. U.S. Patent Application No. 14/348,959.
- Tomić, M. D., Dunjić, B., Bajat, J. B., Likić, V., Rogan, J., & Djonlagić, J. (2016). Anticorrosive epoxy/clay nanocomposite coatings: Rheological and protective properties. Journal of Coatings Technology and Research, 13(3), 439. https://doi.org/10.1007/s11998-015-9762-4
- Tong, Y., Zhang, L., Bass, P., Rolin, T. D., & Cheng, Z.-Y. (2018). Influence of silane coupling agent on microstructure and properties of CCTO-P(VDF-CTFE) composites. Journal of Advanced Dielectrics, 8(2), 1850008. https://doi.org/10.1142/S2010135X1850008X
- Uddin, F. (2008). Clays, nanoclays, and montmorillonite minerals. Metallurgical and Materials Transactions A: Physical Metallurgy and Materials Science, 39(12), 2804. https://doi.org/10.1007/s11661-008-9603-5
- Ullah, M., Ali, M., & Hamid, S. B. A. (2014). Reviews on Advanced Materials Science, 37(2014), 1. https://www.ipme.ru/e-journals/RAMS/no_13714/01_13714_ali.pdf
- Ürk, D., Demir, E., Bulut, O., Çakıroğlu, D., Cebeci, F. Ç., Lütfi Öveçoğlu, M., & Cebeci, H. (2016). Understanding the polymer type and CNT orientation effect on the dynamic mechanical properties of high volume fraction CNT polymer nanocomposites. Composite Structures, 155, 255. https://doi.org/10.1016/j.compstruct.2016.05.087
- Vengatesan, M. R., & Mittal, V. (2016). Spherical Fibrous Fill. In Compos (pp. 1). Wiley-VCH.
- Wang, J., Li, Q., Liu, D., Chen, C., Chen, Z., Hao, J., Li, Y., Zhang, J., Naebe, M., & Lei, W. (2018). High temperature thermally conductive nanocomposite textile by “green” electrospinning. Nanoscale, 10(35), 16868. https://doi.org/10.1039/C8NR05167D
- Wang, R., Schuman, T., Vuppalapati, R. R., & Chandrashekhara, K. (2014). Fabrication of bio-based epoxy–clay nanocomposites. Green Chemical Engineering, 16(4), 1871. https://doi.org/10.1039/C3GC41802B
- Weber, B. (2017). Synthesis of coordination polymer nanoparticles using self-assembled block copolymers as template. Chemistry - A European Journal, 23(72), 18093. https://doi.org/10.1002/chem.201703280
- Wong, T., Lau, K., Tam, W., Etches, J. A., Kim, J.-K., & Wu, Y. (2016). Effects of silane surfactant on Nano-ZnO and rheology properties of nano-ZnO/epoxy on the UV absorbability of nano-ZnO/epoxy/micron-HGF composite. Composites Part B: Engineering, 90, 378. https://doi.org/10.1016/j.compositesb.2016.01.005
- Wong, T., Lau, K., Tam, W., Leng, J., & Etches, J. A. (2014). UV resistibility of a nano-ZnO/glass fibre reinforced epoxy composite. Materials & Design (1980-2015), 56, 254. https://doi.org/10.1016/j.matdes.2013.11.014
- Xie, B., Zhu, Y., Marwat, M. A., Zhang, S., Zhang, L., & Zhang, H. (2018). Tailoring the energy storage performance of polymer nanocomposites with aspect ratio optimized 1D nanofillers. Journal of Materials Chemistry A, 6(41), 20356. https://doi.org/10.1039/C8TA07364C
- Xu, T., Liao, M.-T., & Han, W. (2016). Polyacrylamide/metakaolinite nanocomposites by in-situ intercalative polymerization. Particulate Science and Technology, 34(5), 602. https://doi.org/10.1080/02726351.2015.1096873
- Yao, H., Hawkins, S. A., & Sue, H.-J. (2017). Preparation of epoxy nanocomposites containing well-dispersed graphene nanosheets. Composites Science and Technology, 146, 161. https://doi.org/10.1016/j.compscitech.2017.04.026
- Yazman, Ş., & Samancı, A. (2019). A comparative study on the effect of CNT or alumina nanoparticles on the tensile properties of epoxy nanocomposites. Arabian Journal for Science and Engineering, 44(2), 1353. https://doi.org/10.1007/s13369-018-3516-4
- Yu, J., Huang, X., Wu, C., Wu, X., Wang, G., & Jiang, P. (2012). Interfacial modification of boron nitride nanoplatelets for epoxy composites with improved thermal properties. Polymer (Guildf), 53(2), 471. https://doi.org/10.1016/j.polymer.2011.12.040
- Zare, Y. (2016). Study of nanoparticles aggregation/agglomeration in polymer particulate nanocomposites by mechanical properties. Composite in Part A Applied Scientific Manufactures, 84, 158. https://doi.org/10.1016/j.compositesa.2016.01.020
- Zare, Y., & Garmabi, H. (2015). Thickness, modulus and strength of interphase in clay/polymer nanocomposites. Applied Clay Science, 105, 66. https://doi.org/10.1016/j.clay.2014.12.016
- Zhang, G., Wu, T., Lin, W., Tan, Y., Chen, R., Huang, Z., Yin, X., & Qu, J. (2017). Preparation of polymer/clay nanocomposites via melt intercalation under continuous elongation flow. Composites Science and Technology, 145, 157. https://doi.org/10.1016/j.compscitech.2017.04.005
- Zhang, H., Wang, L., Chen, Q., Li, P., Zhou, A., Cao, X., & Hu, Q. (2016). Preparation, mechanical and anti-friction performance of MXene/polymer composites. Materials & Design, 92, 682. https://doi.org/10.1016/j.matdes.2015.12.084
- Zhou, K., Gao, R., Gui, Z., & Hu, Y. (2017). The effective reinforcements of functionalized MoS 2 nanosheets in polymer hybrid composites by sol-gel technique. Composite in Part A Applied Scientific Manufactures, 94, 1. https://doi.org/10.1016/j.compositesa.2016.12.010