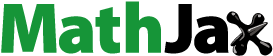
Abstract
The sustainability of fossil fuel is not guaranteed as it is gradually depleting. Alternative ways to this challenge are to generate biofuel from biomass and plastic solid wastes. Many studies have been done on the actualization of these alternatives. Hence, this study accumulates research from multidiscipline for the purpose of advancing biofuel production for sustainable energy. The necessary information needed by scientists having interest in biofuel production, including government policy, biomass selection, different conversion techniques and different ASTM standards for biodiesel properties are entrenched in this study. For vast biofuel production, there is a need for a collaborative work among fields from microbiologist, biochemist to engineering for the development of innovations, growth of cells, understanding of genetic engineering of algae strains and optimization of biofuel production. Also, a review on the recovery and recycling process of plastic solid waste was done. This is to ensure that the use of plastic solid waste to support energy sustenance will lead to no energy is wasted. Various ASTM standards for investigating the different properties of bio-oil were reviewed. The numerous plastic wastes that have not been utilized in the production of biofuel can be investigated to reduce the environmental pollution.
PUBLIC INTEREST STATEMENT
There is lots of untapped energy from biomass. Biomass can alternatively supply energy apart from the conventional fossil fuel origin. Therefore, biomasses including energy crops, non-edible crops, wastes, agricultural residues, edible crops, and wastes from plastics can serve to improve energy availability and reduce over-dependency on fossil fuel. It could also help to improve the environment by reducing the amount of greenhouse gas emissions, such as oxides of sulphur, carbon and nitrogen which are a result of global warming. The conversion routes include fermentation, pyrolysis, gasification, solvent extractions and so on.
1. Introduction
It was postulated initially by researchers that the world oil reserve would be insufficient by 1957 as against the later postulation by American Petroleum Institute (API) in 1999 that the oil could become insufficient by 2094. This implies that this product cannot be depended on and its long time availability is impossible (S. Adegoke et al., Citation2020; Elum et al., Citation2016; S. Kumar et al., Citation2012, Citation2018; Lujaji et al., Citation2010; Robert Ndong et al., Citation2009; Rodionova et al., Citation2016; Syahirah et al., Citation2020; L. Zhang et al., Citation2018). The present Nigeria’s crude oil and the gas reserves is reported to be over 30 billion bbl and 3.4 trillion cubic meters, respectively (Babatunde et al., Citation2018). When we talk of the major source of efficient energy in the world today, we talk of fossil-based fuel which include coal (24–29%), petroleum (33–37%), nuclear (9%) and natural gas (15%) contributing 88–90% energy and there usage being found in the generation of power, chemicals and as transportation fuel (Chandra et al., Citation2012; Huzir et al., Citation2018; Jahirul et al., Citation2012; Juliet Ben-Iwo et al., Citation2016; Matemilola et al., Citation2019; Sani et al., Citation2018; Stöcker, Citation2008; J. Zhang et al., Citation2019). This is shown in ). More also, petroleum fuels have been used for farming equipment, transportation of biomass and distillation of ethanol product in the production of biofuels. The problem resulting from the use of petroleum hydrocarbon is environmental pollution, which could lead to the death of living organisms and humans (S. Kumar et al., Citation2012, Citation2018; Madhu et al., Citation2019). While greenhouse gas (GHG) emission is also a serious mayhem, the fossil fuel, which is contributory to this, is non-renewable, and depleting at a very fast rate (Madhu et al., Citation2019). The gases that cause increase in temperature of our planet due to its enormous release into the atmosphere is known as greenhouse gas (Drewer et al., Citation2018). Even cultivation of lands for crop growth has been seen to be badly affected by the incessant cases of oil spill, gas flaring, chemical discharges and venting in some parts of the world (Robert Ndong et al., Citation2009). It is no longer news that biofuel, an energy chemical, is a possible renewable energy source compared to the limited, volatile and hurtful nature of fossil origin fuel. Biofuel is clean, environmentally favorable and efficient compared to fossil-based product especially as it is related to the petroleum fuel volatile prices. Therefore, there is a call for a renewable and an energetic alternative source of energy than before (Khan et al., Citation2016; Kumari & Singh, Citation2018; Nawaz et al., Citation2018; Nedayali & Shirneshan, Citation2016; Nisar et al., Citation2017; Papari & Hawboldt, Citation2015; Prasad et al., Citation2019; Radakovits et al., Citation2010).
Figure 1. Schematic of world fossil energy consumption (S. Adegoke et al., Citation2020; Elum et al., Citation2016; S. Kumar et al., Citation2012; Citation2018; Lujaji et al., Citation2010; Robert Ndong et al., Citation2009; Rodionova et al., Citation2016; L. Zhang et al., Citation2018) (b) Nigeria’s energy consumption (Elum et al., Citation2016) and (c) plastic supplied to Africa from 1990-2017 (Cai et al., Citation2011)
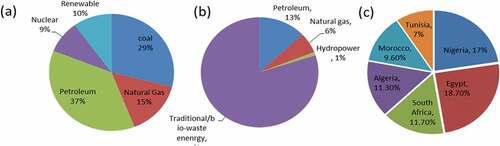
A renewable energy feedstock may has its source from waste of plants or animal (biomass) which is contributing about 46–50% of the global renewable energy consumption (Annisa & Widayat, Citation2018; Huzir et al., Citation2018; Jena & Das, Citation2011). It is important to utilize this natural environmental resource for the betterment of human kind. Biomass is the first renewable energy source deployed by human and had still remained the most useful source of energy for the production of biofuel. Biofuel is an alternative energy for transportation, lubrication, power and heat generation (Balogun & Salami, Citation2016). The negative narratives on biofuel production is in the aspect of its excess refining techniques, and its competition with food industries, (especially the edible feedstock during the first generation of biofuel production) which has led to the record of about 821 million people becoming impoverish in 2017 (Senthilkumar et al., Citation2018). More also, it has also caused reduction in biodiversity, soil pollution (Galadima et al., Citation2011), emission of more carbon in the air, more need of water for land involved in biofuel production, and reduction in overall growth advantages (Cai et al., Citation2011; Hasan & Rahman, Citation2017). However, as adopted by Brazil, one of the ways of lessening the negative effect of biofuel growth is by regulating both feedstock and biofuel production to some particular area best suitable for it (Matemilola et al., Citation2019). This was supported by Wang 2011 (Cai et al., Citation2011) in his statement that “in order to have a robust and lasting success in biofuel production, land availability, the type of land for biofuel production, location of the land, and the current status of the land are questions needed to be answered.
First-generation feedstock such as sugarcane, sugar beet, corn, and wheat which are food for both humans and animals, has been the source of biofuel (ethanol) production, and its impact on food accessibility and economics have been under contention (Rodionova et al., Citation2016; Syahirah et al., Citation2020). The following ethanol production companies are present in Nigeria: they include UNIKEM, Alconi/Nosak, Intercontinental Distilleries, Dura clean, and Allied Atlantic Distilleries with an annual capacity of 65.7, 43.8, 9.1, 4.4, 10.9 million liters, respectively. They use cassava, while some use imported crude ethanol to produce ethanol (Juliet Ben-Iwo et al., Citation2016). This has caused food shortages, especially in sub-Saharan Africa at about 2.5% increasing rate since 2014. That is why the international food policy research institute (IFPRI) has graded Nigeria high in the Global hunger index (GHI) (Matemilola et al., Citation2019). However, these issues can be resolved by applying the second and third generations of biofuel production but the extent of a particular raw material useful for biofuel production and its effect on the economy, people, environment, and policy regulation will determine its suitability (Chakrabarti & Prasad, Citation2012) Second-generation biofuel production utilizes waste materials (majorly lignocellulose material). About 5 to 8 million/year is assumed to be generated for biofuel production from agricultural biomass. This has prevented the competition with food industries which was responsible for an increase in the prices of food items and deforestation in the first generation of biofuel production (Syahirah et al., Citation2020). Matemilola et al. (Citation2019) opined that corn and oilseed could be increased by 65–75% in 2020 if they are used as biofuel feedstocks. However, if the second generation of biofuel production is utilized, corn and oilseeds may only rise by 45–50%. There is more to this, as there has been a current shift from plant biomass to biofilm cultivation for biofuel energy production (Pittman et al., Citation2011; Sikarwar et al., Citation2017).
The third-generation biofuel production employs the use of microalgae (Choudhary et al., Citation2020). Algae is a very diverse species of flora (over 40,000) with the ability to adapt in different biological environs. It has the quality of bringing forth triacylglycerol (TAG) of 20–50 dry cell weight such as lipids, carbohydrate, proteins, fatty acids, triglyceride compared to other higher flora such as cotton, oil palm without negatively impacting food crops (Abed et al., Citation2019). In addition, algae are crude oil sources (lipids). This makes microalgae a potential source of biofuel because they devour a lot of carbon dioxide while growing in wastelands, wastewaters, and saltwater making it an economical venture (Lundquist et al., Citation2010). Algae-biofuel production is of immense economic benefit when it is seen from the angle of being able to treat wastewater and also produce either biodiesel or biogas from algae saltwater-based acculturation and growth in wastewater. This is better than ethanol produced from corn which is always in competition with food for human consumption. The co-product from algae can serve as feeds for animals and pigments. Lundquist (Lundquist et al., Citation2010) fully gives details on the economics and design in the treatment of wastewater using algae.
Fourth-generation involves genetic engineering, aimed at storing alcohols, hydrocarbons which are mainly energy-producing agents in yeast, bacteria, and organisms in large quantity, this is also of great interest among researchers today (Radakovits et al., Citation2010; Rodionova et al., Citation2016; Sikarwar et al., Citation2017). Microalgae fatty acid genetic production is dimmed “not well understood”, however the use of microalgae such as C. protothecoides as biofuel-based feedstock having about 55% lipids, carbohydrate for hydrogen, and biodiesel generation is common. It also synthesizes some percentage of bioethanol and protein. However, it has not yet reached its full maximization for commercial purpose (Hu et al., Citation2008). The manipulation of central carbon metabolism in microalgae can lead to ethylene production (Rodionova et al., Citation2016). This had been done by the improvement in tools for genetic manipulation, though little had been done for eukaryotic microalgae for biofuel production. Radakonits et al. (Radakovits et al., Citation2010) explained that Eukaryotic microalgae could produce biodiesel and ethanol from their rich storage of triacylglycerol and starch. Therefore, the production of biofuel from algae is beneficial compared to fossil fuel-based fuel as it possesses the capacity to reduce; fossil fuel burning, surge in oil price, overdependence on fuel and importation and bring forth economic and industrial growth with a massive reduction in global warming and climate disorder. However, some are of the opinion that biodiesel cannot replace petrol-diesel completely (Chakrabarti & Prasad, Citation2012; Rodionova et al., Citation2016). Syahirah et al (Citation2020) has also said that fuel sourced from biomass could contribute to GHG because the properties of such fuel are synonymous with that of fossil fuel. One point to note is that, the continuous production of biofuel will extend the usefulness of biofuel industries and ensure clean energy sustainability (Babu et al., Citation2017; Li et al., Citation2016)
Moreover, to further enhance energy sustainability, plastic waste (polymers) constitutes a lot of environmental issues due to their non-biodegradability. They pile up on the land surface, sea surface, valleys, hills, oceans, railway lines, drainage areas, and waterside causing landfills and constituting a menace for humans (Babayemi et al., Citation2019; Baeyens & Baeyens, Citation2009; Capocelli, Citation2007; Sadef et al., Citation2016). Recycling program through the deployment of known technology has been on the ground to ensure the environment is gotten rid of these unused plastics thereby leading to a safe environment with improvement in the infrastructure, energy sustainability, economic development, and the social wellbeing of a nation. Jahirul et al. (Citation2012) opined that it is important to use these various recycling platforms to produce fuel having applications in trains, cars, and airplanes, and so on. Thermosets and thermoplastics are the main two types of plastics which have added to energy sustainability (Onwudili et al., Citation2009). Sorting of these types of plastics is done using differences in density. This process is adopted in Asia. However, many plastics’ densities are very close, making this process not very effective. Another sorting scheme is by the addition of tetra-nitromethane inside water. This process is quite costly and may lead to the pollution of the plastic that was recovered. The use of hydro-cyclones for sorting by density is dimmed to be efficient. Also, the use of a turboelectric sorting scheme whereby, there is a transfer of surface charges is another process (Baeyens & Baeyens, Citation2009). Sorting is not common in Africa, therefore open burning of plastics is done without precaution (Babayemi et al., Citation2019). Thermoplastic’s flexibility has the reason why it is used in packaging, soft drinks, food take-away packs, wire coating, greenhouses, casings, bags, and so on (Gu et al., Citation2017). Its durability, relatively low prices, capacity not to rust, low cost of production, and energy efficiencies has necessitated a whooping production of up to 280–300 million tons in 2011 and with the estimated growth of 4% from 2010 to 2016, while Europe alone contributes 19% (57 Mt) (Babayemi et al., Citation2019; Capocelli, Citation2007). Thermoplastics comprising of 80% of plastic in Western Europe are heated to melt at a specific temperature and solidify when cooled but thermosets thickens more when heated. Thermoplastics include Polyvinyl chloride (PVC), polyethylene terephthalate (PET), polypropylene (PP), low-density polyethylene (LDPE), and high-density polyethylene (HDPE) constituting 74% of all waste in plastic (Sriningsih et al., Citation2014). There are 40% of LDPE, HDPE, and PE from other wastes such as PP, PS, and PVC in Europe. 38 Mt of plastic are said to be consumed yearly in Europe (Onwudili et al., Citation2009). 8300 Mt of plastics were produced in the world from 1950 to 2015 while 230 Mt of plastics find their way into the Africa continent within this period (1990–2017) with 39 Mt coming to Nigeria, which is 17%. Egypt has the highest of about 43 Mt (18.7%), followed by South Africa, Algeria, Morocco, and Tunisia with 27 Mt, 26 Mt, 22 Mt, and 16 Mt respectively (Babayemi et al., Citation2019). This is shown in ). Recycled plastic waste up to 388 Kt has been used to generate textile production up to 378 Kt in 2002 (Baeyens & Baeyens, Citation2009).
Only about 50–60% of the world plastics are accessible to be collected with about 15% available for recycling to produce sacks, garden furniture, plastic fence, traffic cones, and pipes (Onwudili et al., Citation2009; Sadef et al., Citation2016). The remaining parts of the plastics is used for building, wiring, frames, pipe while some are allowed to litter around though the reused types are less energy-intensive compared to recycle ones. However, when plastic is reused, it helps to reduce carbon dioxide, nitrogen oxides, and sulphur oxides emissions (Baeyens & Baeyens, Citation2009). Polypropylene and sawdust wastes have been binded together using cement and expanded polystyrene as adhesives (Ohijeagbon et al., Citation2020). The chemical recycling process (pyrolysis) of these various waste polymers, such as LDPE, HDPE, PP, PET, PS, PVC could lead to a much better environment than landfill or incinerating processes (Adekunle et al., Citation2020).
In this review study, we shall discuss the growth of energy sustenance from both biomass and plastic wastes in the world. We shall discuss biomass generally and we shall pick few biomasses and discuss them broadly due to their level of importance around the world and how Nigeria can immensely benefit from it use. These would make us also discuss briefly few of the various conversion technologies while biotechnology and bio-economy would have been discussed. The benefits of biofuel and plastic-derived fuel will be discussed. Properties expected of a biodiesel used in internal combustion engine are discussed. Finally, ASTM standards for different biodiesel properties are discussed to conclude the study. From this study, we shall note that enormous energy can be supplied both from biomass and waste plastic recycling in Nigeria and in the world, if they are adequately harnessed.
1.1. The growth of energy, biodiesel and plastic recycling in the world
1.1.1. Energy usage
Importation of oil will not stop as long as there is industrialization, population increase, and over-dependence among developing countries such as Nigeria, Turkey, Iran, and so on (Durak, Citation2019; Shrivastava et al., Citation2019; Tüccar et al., Citation2018). Among the world’s population living in developing countries, which is about 80%, only about 40% of the total energy is being consumed by them. One of the yardsticks in measuring the extent of country growth in terms of economy and prosperity is per capita energy consumption. For energy sustenance, independence, economic growth of a country and energy resources are very important (Hossain et al., Citation2014; Kumar et al., Citation2018). The distribution of fossil fuel is not uniform compared to renewable resources (Demirbas, Citation2007). Iran produces the highest oil after Saudi Arabia in the Middle East; with the estimated production of 127 Mgal in 2004 to an estimated 211 Mgal by 2030. Gas production was 110 billion cubic feet in 2010, and an estimated production of 240 billion cubic feet by 2030 was proposed. The increase in energy usage is estimated from 153 TWhour in 2003 to 359 TWhour with a total amount of 92 BUSD to be expended on its production.
Iran’s energy demand rate will increase averagely by 2.6% from 2003 to 2030 (Nedayali & Shirneshan, Citation2016). Turkey’s dependency on fuel importation surges up to 30 Mt/year in recent years back resulting into a 70% increase in energy usage (Tüccar et al., Citation2018). Their increase in energy usage has had a strong effect on the incessant increase in price of fuel. Also, GHG emissions such as carbon dioxide, others include chlorofluorocarbon, hydrocarbon, SOx, NOx, methane, and so on inducing global warming and climate disorder are all challenging situations. Climate disorder is a situation, whereby there is a perpetual change in mean properties of the climate up to 30 years. Up to 1.6% of carbon dioxide is emitted from fuel combustion with no doubt that the gaseous emission will be abated (Syahirah et al., Citation2020). Generally, carbon dioxide emissions have increased approximately by 11% constituting about 73–75% from fossil-based fuel (Juliet Ben-Iwo et al., Citation2016; L. Zhang et al., Citation2018). This has resulted in the emergence of several known and unknown non-communicable diseases in the world today (Galadima et al., Citation2011).
India consumes a lot of energy, up to 80% of their consumption has been said to be imported and it has equally been said that about 300 BUSD to 500 BUSD worth of hydrocarbon oil is proposed to be imported by 2030. This is to be deployed for use in the industrial sector (7.2%), private transportation (18.95), agriculture (13.8%), power generation (9.7%) and commercial transportation (50.4%) (Juliet Ben-Iwo et al., Citation2016).
Nigeria is the sixth-largest oil exporter in the world and the largest oil producer in Africa. That is why Nigeria’s major “non-native” earning is 90–95% from fossil fuel (Galadima et al., Citation2011). Nigeria refinery could refine petroleum crude oil to the tune of 449.4 Mgals per day but as of 2013, its capacity was working at 22% production per day. This makes Nigeria a net importer of oil and at the receiving end of the ever-increasing tendencies of changing global fuel price (Juliet Ben-Iwo et al., Citation2016). Other sources of revenue such as agriculture and solid minerals have been abandoned due to oil and gas exploration that started as far back as 70 years ago in the Niger Delta. However, Nigerian came up with vision 2020 to look away from oil dependence to the actualization of a gross domestic product of 900 BUSD with the manufacturing sector contributing about 25% to her GDP, and a 4000 USD per capital income yearly. Unfortunately, this has not been achieved (Elum et al., Citation2016).
Asia uses more than North America in the amount of oil, hydropower generation, coal, and renewable power generation. Nigeria burns fossil fuel such as natural gas with 80% of gas flaring activities going on in this zone (highest giver of this deleterious gas into the atmosphere in sub-Sahara Africa) (Elum et al., Citation2016; Galadima et al., Citation2011)
United State of America surpasses Asia only in the amount of nuclear power (from 9% globally produced) and natural gas usage (Huzir et al., Citation2018). Of the world’s production of coal, Asia alone consumes 75% (Kumar et al., Citation2018). Nigeria uses about 13%, 6%, 1%, and 80% of oil, natural gas, hydroenergy, and traditional/bio-waste energy, respectively. This is shown in ). The traditional energy includes charcoal, animal dung amounting to 80% of total primary energy used (Juliet Ben-Iwo et al., Citation2016; Matemilola et al., Citation2019). This means every country is in search of sustainable energy production, which is a prerequisite for growth in the developing and developed countries (Robert Ndong et al., Citation2009). The increase in energy demand for transportation, electricity, and heat generation including the effect of political instability leading to the constant increase in the price of fuel and fast rate of fuel depletion, calls for an active alternative, which is renewable, clean and energy sustaining, to improve the living condition of the people. Biofuel which is renewable, clean, efficient, sustainable, economically viable, and an environmentally safe energy source is a good option (Agarwal et al., Citation2015; Annisa & Widayat, Citation2018; Balogun & Salami, Citation2016; Demirbas, Citation2007; Falowo et al., Citation2020; Huzir et al., Citation2018; Kumar et al., Citation2018; Matemilola et al., Citation2019; Nedayali & Shirneshan, Citation2016; Nisar et al., Citation2017; Prasad et al., Citation2019).
Transportation fuels include diesel, liquefied petroleum gas (LPG), gasoline, and compressed natural gas (CNG); and are sourced from fossil fuel. Transportation alone consumes about 30% of the total 99% fossil-based world energy production and a good alternative energy for this highly consumed fuel is in the production from biofuel (Nedayali & Shirneshan, Citation2016). Transportation contributes between 21% and 23% to global GHG emissions with about 11,830 metric tonnes of CO2 emanating from petroleum consumption in 2013 (Juliet Ben-Iwo et al., Citation2016). This is being proposed to increase by 80% in 2030 (Robert Ndong et al., Citation2009). 15 Bt of has been said to be supplied every year (Chandra et al., Citation2012). This GHG (CO2) emission is about 59.5% from transportation in Nigeria, which has caused a reduction in the life expectancy of the citizens (Juliet Ben-Iwo et al., Citation2016). However, the use of renewable energy will ensure safe, environmentally sound, and economic progress with an increase in GDP. An alternative fuel, biofuels sourced from biomasses supplies about 1.5% of overall energy (Kumari & Singh, Citation2018). As of now, up to 56% from the 1.5% overall biofuel energy consumed is being contributed to the transportation system (Syahirah et al., Citation2020). Biofuel is said to be carbon neutral (Pittman et al., Citation2011). The finding as regards biofuel exploration does not involve the aspect of boring holes to the underground like hydrocarbon exploration. However, biofuel feedstock can be sourced within every region where bushes and forests are present since the sources are from biomass, which is the third-largest among other energy sources. (Jahirul et al., Citation2012; Sikarwar et al., Citation2017).
1.1.2. Biofuel growth and greenhouse gas emission plans
Biofuel’s ability to control climate upheaval and fossil fuel dependence in no small measure as attracted political interest among many nations of the world (Jain et al., Citation2011). The growth of biofuel has been witnessed in Argentina, Brazil, Spain, USA, Malaysia, Indonesia, Italy, France, Germany and many European countries (Chyuan & Silitonga, Citation2020). Brazil, USA, and Sweden have used different compositions of biofuel blend for transportation and diesel engine (Abdullah et al., Citation2013). 25 vol%, 10 vol%, and 85 vol% of ethanol have been used in Brazil, USA, and Sweden, respectively (Stöcker, Citation2008). There was a blend mandate on biodiesel in Brazil up to 5% in Jan 2013. EU has also encouraged renewable energy usage up to 20% to lessen the GHG effect by 35% (Syahirah et al., Citation2020). The use of fossil oil and the bio-renewable energy mix is proposed to be achieved in Indonesia by 2025 with 20% less in fossil oil usage and 5% more in bioenergy usage (Annisa & Widayat, Citation2018). There is a proposed plan of GHG reduction to 80% from 2010 to 2050 by the climate panels of the United Nations (Stöcker, Citation2008). The Kyoto protocol for clean development mechanism encourages 15 wealthy developing countries of the world to commit funds to sustainable green energy. This is also meant to bring in jobs, encourage farming, reduce GHG emissions, improve on environmental quality and utilize carbon availability (Juliet Ben-Iwo et al., Citation2016). However, the greenhouse gas emission Kyoto protocol being proposed by the European body in 2002 has failed to bring its purpose forward and zero GHG emissions has not still been achieved, but the wide acceptance of the Kyoto Protocol inaugurated in 2005 has accelerated the targets of the national biofuel programs (Matemilola et al., Citation2019). The government of Australia wishes to attain the 60% GHG emissions mark by 2050 (Jahirul et al., Citation2012).
Ndong et al. (Robert Ndong et al., Citation2009) used Life cycle assessment (LCA) environmental analysis techniques to study the environmental effect of Jatropha curcas. He opined that the use of Jatropha as biodiesel is eco-friendly and has the capacity to reduce GHG emissions by 72%. This is supported by Juliet Ben-Iwo et al. (Juliet Ben-Iwo et al., Citation2016) and Abdullah et al. Citation2013 (Abdullah et al., Citation2013). Equally, the use of palm oil as biodiesel has caused a reduction of about 73% and 46% of unburned hydrocarbon gas and respectively compared to diesel (Abed et al., Citation2019)
The proposed government policy on tax increment on the production of fossil fuel and increased subsidies from the production from renewable energy sources have enabled a paradigm shift on the changing form of energy choices (Chakrabarti & Prasad, Citation2012). The EU 2009/28/EC, US energy independence and security act 2007 and Nigerian biofuel policy incentive 2007 allowed biofuel production without tax, funding for biofuel research, and removal of customs fees for biofuel related matters (Galadima et al., Citation2011; Juliet Ben-Iwo et al., Citation2016). The decrease in fuel usage by 5% in 2040 and increase in renewable energy by 9 to 12% have been proposed by energy information administration (EIA) in the US (L. Zhang et al., Citation2018). The use of petroleum-based mud has been prohibited through strict regulation enforced by different countries as a result of its toxicity on the environment (Oseh et al., Citation2019). The international energy agency stated that the production of biofuel increased three times between the years 2000 and 2007 and up to 1.6% was estimated for transportation fuel globally in 2012 (Kilbane, Citation2016). There had been subsidies in biodiesel production in China, which has lowered the biodiesel cost by 15%, and tax credits up to $1 per gallon for the production of biodiesel in the US. This was inaugurated in August 2012. US government has subsidized up to 3 billion in 2008 to cushion the high cost of biodiesel production and yet with a little reduction on GHG (Syahirah et al., Citation2020).
Nigeria inaugurated an initiative called the “National biofuel production program” in 2007, which provides soft loans for people in the local communities who are interested in biofuel production. This has encouraged the proposed production of biofuel (bioethanol and biodiesel) in some parts of the Northwest, Northcentral, and Southwestern axis with the proposed plan of 5.04 Bl of bioethanol and 900 Ml of biodiesel from Nigerian biomasses (Balogun & Salami, Citation2016; Galadima et al., Citation2011). Also, the Nigerian government, through the NNPC has established a memorandum of understanding with the Brazilian government (Petrobras and Coimex) and also Venezuela for the production of bioethanol from cassava. To achieve the objectives of the Nigerian energy commission for biofuel production (NECBP), it was suggested that there is a need to consider reviewing the refineries present in the country for biofuel production (Juliet Ben-Iwo et al., Citation2016). However, the issue relating to bad policies, political unrest, corruption, bad governance, bad follow-up on policies, high production cost, and bad communication act would affect the overall sustenance of the biofuel industry in Nigeria (Matemilola et al., Citation2019), (Cai et al., Citation2011).
On a global scene, there is a possibility that from 2012 to 2040, there will be a massive growth experienced in the production of fuel, such as biodiesel and ethanol from biomass (L. Zhang et al., Citation2018). An 11.4% increase was observed from 2012 to 2013 in the production of biodiesel as it increased from 0.148 Bbbl to 0.165 Bbbl (Chyuan & Silitonga, Citation2020). For every gallon of gasoline fuel and diesel fuel used, 0.008887 and 0.010180 metric tonnes of CO2 were said to be present (Juliet Ben-Iwo et al., Citation2016). Furthermore, there will be a reduction in GHG emissions from the production of biofuel (ethanol) from lignocellulose than from corn (Hasan & Rahman, Citation2017). This is corroborated by Crutzen et al. (Citation2008) that the production bioethanol from corn, maize, and so on are said to increase the emission of N2O in the atmosphere leading to the global warming saga. This is because the crops contain Nitrogen fertilizer while growing. However, fewer nitrogen plants such as grasses and wood may impact positively on global warming reduction.
1.1.3. Land usage
In a way to improve in the planting of feedstock for biodiesel production, it will involve clearing of trees, provision of fertilizer, and reduction in the available lands for cultivation of other types of crops for food (Syahirah et al., Citation2020; L. Zhang et al., Citation2018). This is because the feedstock cost and its availability control the end product and prices of biofuel (Hasan & Rahman, Citation2017). In Nigeria, 3% of agricultural practices are technologically inclined, while above 90% of agricultural practices involve the use of hand tools (Matemilola et al., Citation2019). Therefore, the use of hand tools for agricultural practices should be discouraged, while the mechanized system of agricultural practices should be encouraged in Nigeria. Biofuel production will lead to the development of rural settlements because this area has the largest population of people who lives as poor people. Many of the biofuel raw materials, such as rice, millets, animal wastes, and jatropha, are mostly found in rural settlements (Balogun & Salami, Citation2016). Biodiesel production would be less costly in the developing world than in the developed world because of the availability of land for biodiesel feedstock (Hasan & Rahman, Citation2017). About 10–15% of energy, equivalent to 45 exajoule is generated from 2% global available land area (Chandra et al., Citation2012; Syahirah et al., Citation2020). In the US, 6% of petroleum fuel would be out of use if lands are provided for cultivation for the production of biofuel with an annual production of 1.3 Bt of biomass (Syahirah et al., Citation2020). About 284.5 Ml of soybean biodiesel were recovered from 638000 ha of cultivated soybean land (Juliet Ben-Iwo et al., Citation2016). Note-worthily, 40% of the land meant for agricultural purposes was used for soybean plantation (Awalludin et al., Citation2015). With 144 Mt of biomass in Nigeria generated from 85 to 176 million hectares of land, this has a significant biofuel production potential of 2 Bl of ethanol and 900 Ml of biodiesel for 10% ethanol-gasoline blend and 20% biodiesel-diesel blend, respectively (Galadima et al., Citation2011). The availability of feedstock, the type of feedstock, the capital cost, the location of the refinery, and technological prowess are determinants for the achievement of this 10% blend of ethanol and biodiesel (Juliet Ben-Iwo et al., Citation2016). 5% of the land will be needed in the EU and 8% in the US to produce ethanol to reduce the usage of petroleum fuel up to 5%. However, for the production of biodiesel, between 13% and 15% of cropland should be made available in the US and EU, respectively. Biodiesel is not on a commercial scale and non-food biofuel production is not in sight in Nigeria (Juliet Ben-Iwo et al., Citation2016). It was proposed by the EU that by the end of 2005, 2% of bio-based gasoline and diesel will be available in the market for sale. The plan to increase it to 5.75% by 2010 was proposed too (Babayemi et al., Citation2019).
Seven percentage of Iran’s land is covered with forest, which is a good product for biofuel production (Kumar et al., Citation2018). Nigeria has an expanse of land in the north-central and northwest for biofuel feedstock, while the southwest possesses the necessary infrastructure and market for sale and exportation because of the presence of seaport in Lagos, Nigeria (Balogun & Salami, Citation2016). Nigeria posesses about 37.7%, 33.3%, 12.6%, 7.4%, and 9.5% of arable lands, pastures, other lands, permanent crops, and forest areas, respectively, from 71,000,000 ha of the agricultural land area (Juliet Ben-Iwo et al., Citation2016). Fortunately, over 146,000 ha have been provided for biofuel feedstock production being chaired by NNPC and some other private sector (Matemilola et al., Citation2019). There is an account of 320–702 Mha of land including marginal lands, agricultural/vegetable land for mixed crops all over Africa, China (23 million ha suitable for bio-physical feedstock), Europe, India, USA, and South America, however, while accounting for other types of land, such as savanna, grassland, and shrub-land, this has made the available land run to 1107–1411 Mha with an estimation of 385–472 Mha of idle land (mainly abandoned lands globally) (Cai et al., Citation2011). The definition of savanna, shrub-land, grassland are given in Van Leeuwen et al. (Citation2014). About 26–55% of global liquid fuel consumption will be achieved from the cultivation of the second-generation biofuel feedstock on this marginal grassland and croplands meant for food crops and pasture purposes (Cai et al., Citation2011).
1.2. Bio-economy management
Biodiesel is a product of trans-esterification. It is renewable, sulphur-free, non-toxic, biodegradable, environmentally friendly. It has high; flash point, oxygen content, and lubricity (Gonca & Dobrucali, Citation2016; Hu et al., Citation2008; Islam et al., Citation2011; Juliet Ben-Iwo et al., Citation2016; Kumar et al., Citation2018; Nisar et al., Citation2017; Prasad et al., Citation2019; Rodionova et al., Citation2016; Syahirah et al., Citation2020; J. Zhang et al., Citation2019). Biodiesel production is more expensive than petroleum products because of the wide process of purification. The presence of free fatty acid in some biomass like animal fat and waste cooking oil than others make them a candidate for much treatment for it to be useful (Demirbas, Citation2007). However, with the increase in petroleum product consumption due to the increased population and industrialization, there has been renewed interest in the increased consumption of biodiesel. This has caused a reduction in the importation of depleting diesel fuel. Also, the increase in biodiesel production can be ensured in the presence of eligible operational performances (Li et al., Citation2016). From the numerous edible oils consumed in Iran, 20% of waste from cooking oil could be a good product for its biodiesel blend with diesel. Hence, it has a close resemblance to diesel in terms of operation. Vegetable oil’s representation in different localities is different. Therefore, its use at different places depends largely on its availability. For instance, US biodiesel sources include corn oil, sunflower, and soybean (Juliet Ben-Iwo et al., Citation2016). However, in the EU, canola, sunflower, and frying oil are the three main biodiesel sources. Also, Asia countries like India, Indonesia, and Malaysia use palm oil (Awalludin et al., Citation2015). India has the largest production of cashew (Das & Ganesh, Citation2003). Nigeria is the fourth-largest producer of oil palm and number thirteen in soybean production (Juliet Ben-Iwo et al., Citation2016). Nesttlespurge (Jatropha curcas) and Karanja (Pongamia pinnata) are available in India in large quantity because of the vast tropical climate (Chakrabarti & Prasad, Citation2012). India has used Pongamia pinnata, being very available up to 55,000 tons/year, thereby making the blend of Pongamia and cottonseed oil to be used for biodiesel production (Madhu et al., Citation2019; Prasad et al., Citation2019). Canada has flair for the production of biofuel from saw wood. Hence, she has stopped the production of pulps and paper to the production of biofuel and useful chemicals. Waste and biomass solid are responsible for 78–80% of the total primary energy completely used up in Nigeria (Juliet Ben-Iwo et al., Citation2016). The entire income accrued from ethanol, biodiesel, and bio-methane in 2014 were 40.9 BUSD, 3.8 BUSD, and 19 MUSD, respectively (Kilbane, Citation2016). The cost of procuring almond seed to the point of extracting sweet almond seed oil (SASO) biodiesel is 82.75 USD/Bbl, while the cost of producing the same quantity of diesel is 127.3 USD (Oseh et al., Citation2019). Production of biodiesel from oilseed or animal fat includes 0.30 to 0.70 USD/l (Hasan & Rahman, Citation2017), while microalgae cost ranges from 0.44 USD/l to 8.76 USD/l with the advantage that algae rate of production per land is higher and its cost of production is cheaper than other plants (Pittman et al., Citation2011; Syahirah et al., Citation2020). USA has the ability to produce oil from algae to the tune of billions every year to provide support for aviation fuel (Lundquist et al., Citation2010). Biodiesel production from vegetable oil and grease wastes are 0.54–0.62 and 0.34–0.42 USD, respectively. In the first-generation, biodiesel costs 0.86 USD/l and ethanol production would cost 0.49 USD/l, whereas, in the second generation, the production cost of biofuel is between 1.15 and 7.85 USD/gal. Diesel prices include 0.20–0.24 and 0.18/l in European countries and the US, respectively (Demirbas, Citation2007) with the opinion that the cost of producing un-renewable fossil-based fuel is minimal compared to other forms of production (renewables) (Syahirah et al., Citation2020). Also, the energy used for bio-hydrogen production is higher compared to hydrogen from fossil fuel (Pittman et al., Citation2011). Generally, the production of biofuel is estimated to be 1.65USD/gal with feedstock cost, cost of processing accounting for the main cost of production (Syahirah et al., Citation2020).
1.3. Municipal solid waste management
There is a continuous increase in solid wastes (1.3 Bt in 2012), which was said to be likely doubled around the year 2025 (Babayemi et al., Citation2019). Hence, it is estimated that the cost of wastes management will increase from 205.4 BUSD to 357.5 BUSD by 2025 (Sadef et al., Citation2016). Waste generation in south Asia especially Bangladesh, India, and Pakistan, is a lot (Hossain et al., Citation2014). Also, plastic disposal has caused a big problem in developing countries (Khan et al., Citation2016). In the US, the amount of plastics wastes in the municipal increased by 1.1% in 2002, over 250 million was generated with only about 87.85 million recycled (Baeyens & Baeyens, Citation2009). EU’s municipal solid wastes is with a growth rate of 3% every year (Baeyens & Baeyens, Citation2009). It was recorded that
of municipal solid wastes are generated overall from the 250 kg used by each person in the year 1990. This amount has been seen to be twice in 10 years, reaching
(Baeyens & Baeyens, Citation2009). Nigeria accounts for 25 Mt of municipal solid waste generated annually, and what influences waste generation includes economics, population, and so on (Matemilola et al., Citation2019). Solid waste generation in Nigeria is a serious menace in the rural areas because of its ability to contribute to global warming (Onyelowe et al., Citation2019; N. Singh et al., Citation2014). The rate of waste growth is higher than the applied attention to reducing it negative impact on the environment. Pakistan generates about 55,000 tons of waste per day. In Lahore, an urban metropolis with about 35% of the 160 million populations, organic waste generated is 58.5%, biomass waste such as leaves and seeds, and vegetables are 51% while paper waste is 2.7%. In Lahore, a sum of 15.3 MUSD is being generated from recycled materials in one year (Sadef et al., Citation2016). The largest parts of the waste comes from the urban areas (2/3 times) with organic waste being the highest (N. Singh et al., Citation2014). About 70–75% of wastes are recycled in Japan, while the rest go to landfills (Sadef et al., Citation2016). From 1 metric ton of solid waste, 185 kg of methanol can be produced (Demirbas, Citation2007). From Pakistan, Sadef et al. (Citation2016) opined that of all the total organic waste (0.57 Mt) generated per year, a total of
of methane per kilogram of solid are produced, giving a total energy content of 2.43 TWhour. Considering other wastes, including inorganic contents, a total energy content of 1.72TWhour/year was discovered (Sadef et al., Citation2016). Soap stock and waste cooking oil could also result to waste management if they are used for the external phase of drilling fluid (Li et al., Citation2016). In this regard, researchers have developed an integrated waste management program to ensure the constant provision of energy without affecting the environment negatively. A life cycle assessment schemes was used to adopt the best and suitable technology for waste management (Gu et al., Citation2017; Di Maria & Micale, Citation2013). However, in Africa, where there is inadequate infrastructural equipment, waste management may be inefficient especially in poor city regions, and the lack of sufficient data, money, and the negative administrative policy has caused the system to fail (Babayemi et al., Citation2019). EU waste management framework directive in 2008/98/EC gives information on waste recycling/ reuse materials. This has made 50% of paper, plastic, metal, and glass to be utilized (Di Maria & Micale, Citation2013). A lot of money is going into waste management in developing countries because of the enormous waste generated, however, the quest to curtail them may also lead to environmental health hazards (Babayemi et al., Citation2019). The integrated waste management schemes are divided into six. This includes; point of generation of waste to disposal, waste sorting, collection, and finally processing (Adekunle et al., Citation2020; Baeyens & Baeyens, Citation2009; Gu et al., Citation2017; Ohijeagbon et al., Citation2020). Plastic containing coatings like paint could cause alteration of product properties. However, when the plastic is ground with a cryogenic method, it could help remove these coatings. In the case of many coatings, the abrasion technique can be used. Moreover, the use of solvent removal and dipping of coated plastic inside “hot water technique” as had insignificant negative effect on the property of the plastic (Baeyens & Baeyens, Citation2009). The waste collection takes about 70% of the total cost for waste management (Di Maria & Micale, Citation2013). Therefore, the regeneration of waste consisting of rubber, plastics, waste oil, carbon black to biogas is a way of waste management (Juliet Ben-Iwo et al., Citation2016).
1.4. Biotechnology
Drilling engineers are working tirelessly to meet the demand of the world even as more oil is been discovered through enhanced oil recovery methods. Up to 60 to 80% of oil in the underground deposit is opined to be either technically or economically irrecoverable. However, this amount of oil could be recovered via the microbial energy conversion method (Kilbane, Citation2016). It is said that 20 to 40% of methane could be recovered in oil through the microbial origin. Therefore, biotechnology processes help in converting irrecoverable petroleum crude oil and coal deposit resources into methane, which will result in to increase in energy production (Kilbane, Citation2016). The use of biotechnology has helped in the production of organic fertilizer for agricultural sustenance. More so, it has helped in preventing environmental pollution because about 60% of lands available for production have some elemental toxicity and mineral defects (Chyuan & Silitonga, Citation2020). The oil produced from Jatropha contains inedible phorbol ester which could be used for fertilizer production because of the presence of phosphorus, potassium, and nitrogen content (Abdullah et al., Citation2013). However, it has been reported that fertilizers addition into the soil may lead to soil acidification (Syahirah et al., Citation2020). The glycerol product could be used for soap making (Babu et al., Citation2017). About 4.76 g of soap could be produced from 3 liters of oil pressed from 12 kg of jatropha seeds (Chakrabarti & Prasad, Citation2012). Solid biofuel contributes about 69% to renewable energy provision globally; liquid biofuel contributes 4% and 0.5% to transportation and primary energy provision, respectively, while gaseous fuel contributes 1.5% (Juliet Ben-Iwo et al., Citation2016). There is an increase from 10556.6 Mtoe to 12928.4 Mtoe of the total primary energy consumed from 2004 to 2014 (Babu et al., Citation2017). The growth rate of solid, liquid and gaseous biofuel is 1, 11, and 15%, respectively, since 1990. China and India produce the highest bioenergy in 2010 with the share of 20 and 17%, respectively (Juliet Ben-Iwo et al., Citation2016).
One of the types of biofuel is ethanol, which has been produced as liquid biofuel. It is good for cosmetic, alcoholic beverages, and pharmaceutical production (Demirbas, Citation2007). Bioethanol is the commonest biofuel produced from food crops, while bio-butanol and propanol are less common (Pittman et al., Citation2011). Corn and sugarcane are the two main sources of bioethanol (Kumari & Singh, Citation2018). The type of ethanol extracted from corn requires about 15 MJ of energy for distillation, dehydration, and milling (36%) to transform its 1 liter to fuel with 44% less in carbon emission compared to petroleum gasoline. It is also proposed to attain GHG emissions reduction from 70 to 85% by 2050 (Syahirah et al., Citation2020). Ethanol is also extracted from maize or sugarcane bagasse. Sometimes, it is used with a blend (10%) with petrol fuel to form gasohol. However, the oxidation stability of the blend stock must be higher than the minimum value of the individual fuel that constitutes the blend (Charter, Citation2009). 372 kg/t of cans is produced from 28 kWh/t of cans in an ethanol plant located in Brazil (Syahirah et al., Citation2020). This has caused GHG reduction by almost 90% from 1980 to 1995 in Brazil (Juliet Ben-Iwo et al., Citation2016). Nigeria, like Brazil, has enough natural resources to process biofuel from biomass due to the presence of rainfall, favorable land scope, and cultivable soils. Millets, beans, sorghum, cotton, and groundnuts are available in northern Nigeria, while in the south; there are cassava, rice, yam, cocoa, coffee, oil palm, ginger, rubber, sugar, and so on (Juliet Ben-Iwo et al., Citation2016). Nigeria cultivates the highest cassava plantation in the world, thus, it uses for industrial purpose and foreign exchange. It contains carbohydrates and can be used to produce bio-ethanol. Cassava processing to ethanol has been in Nigeria since 1973. There is a plan to produce 30 Ml of ethanol from a 200 MUSD ethanol plant by Nigeria yeast and alcohol manufacturing company (Juliet Ben-Iwo et al., Citation2016).
Bio-ethanol has been used up to 85% blend with diesel oil but with engine modification. However, at 5% blend, it may require no engine modification (Kumar et al., Citation2018). Out of the 86% bioethanol production in the world in 2011, USA and Brazil alone are responsible for 57% (13.9 Bgal) and 24.9% (5.57 Bgal), respectively (Juliet Ben-Iwo et al., Citation2016). Biofuel production such as ethanol is about 0.9 to 1.7 MJ in the first generation of biofuel production but has increased in recent times by 3.3% (Syahirah et al., Citation2020). Sixty percentage of biofuel production usage is ethanol (Kumar et al., Citation2018). More than 85.6 Bl were reached as global ethanol produced in 2010 (Kumari & Singh, Citation2018).
Biofuel production in Nigeria is mostly from the first-generation source product. Sugarcane and algae conversions to biofuel are at the commercial and developmental stage, respectively (Juliet Ben-Iwo et al., Citation2016). There is currently the production of fuel from food crops in Nigeria; however, the process of converting food into fuel has been referred to as a “crime against humanity” by Jien Ziegler because of its devastating effect on the poor people (Matemilola et al., Citation2019). This has witnessed the constant increase in food prices and the unavailability of food. However, some are in contract with this notion that biofuel production will rather bring prosperity to the people, increase rural development, increase food production, and increase access to better health facilities (Rodionova et al., Citation2016). There is such a limited information on the development of biofuel from non-food crops deployed as a transportation fuel in Nigeria (Juliet Ben-Iwo et al., Citation2016).
Another type of biofuel is biodiesel, hydro-treated vegetable oil (HVO), and BTL (biomass to liquid fuels) (Charter, Citation2009). Biodiesel has increased in recent times by 4% (Kumar et al., Citation2018). Biodiesel is a renewable source of energy. It is non-toxic mono-alkyl esters of long-chain fatty acids with high flash point, high cetane value, and calorific value (Das et al., Citation2018). It has no sulphur, no aromatic material, and can be useful for the external phase of drilling mud due to the presence of asphaltenes and resins, which are important properties for its effectiveness (Oghenejoboh et al., Citation2013). However, a three double bond present in the ester may oxidize or polymerize. This could result in the creation of more acid or sludge in the fuel (Charter, Citation2009). Biodiesel has its source from vegetable oil, algae, soybean through the esterification process and has the capacity to recycle carbon dioxide (Rodionova et al., Citation2016). The properties of both biodiesel and petrol diesel are comparable; however, the viscosity and density of biodiesel could be higher as a result of glycerin content. The un-esterified portion of oil has high viscosity with a large branched molecular structure, while the esterified sample has straight-chain molecules, and free fatty acid contents (Oseh et al., Citation2019). They also have issues like poor thermal stability, low-energy density, low oxidation stability, too high viscosity, and formation of hydrolysis either in alkaline or acidic phase (Senthilkumar et al., Citation2018). They attack elastic materials used during completion and downhole drilling (Gonca & Dobrucali, Citation2016). They could form carboxylic acids and alcohol when the esters react with water at high temperature in alkaline presence (Ismail et al., Citation2014). The cost of biodiesel production is high because they are produced from the use of chemicals, which makes the cost of operation very high. It is also used by blending with/without diesel from petroleum-based products (Papari & Hawboldt, Citation2015). Dimethyl ether has also been used in percentage blend with biodiesel and diesel for use in CI engine (Kumar et al., Citation2018). However, the blending of biodiesel with other products must ensure that the standard properties of the oil have not change. Biodiesel is characterized in terms of cloud point, density, cetane value, acid value, iodine value, volatility, and gross heat of consumption (Chyuan & Silitonga, Citation2020). Iodine value, which is a function of unsaturated fats, helps to determine oxidation stability level (Abdullah et al., Citation2013). For instance, Malaysia’s iodine value of jatropha is 135.85 mg/g, while that of Nigeria is 105.20 mg/g. The unsaturated fatty acid of Malaysia and Nigeria jatropha is 72.70% and 78.95%, respectively (Abdullah et al., Citation2013). Sunflower, soybean, and some other unsaturated oils have good iodine number (maximum of 130) because of the presence of linoleic acid (a function of methyl ester plant giving the oil a high freezing point and high oxygen stability).
Another biotechnology is bio-oil. It is a dark brown liquid that encourages CO2 balance and storability. This is because of their high flash point, high energy density with the presence of various organic compounds. The compounds include phenols, carbonyls, and carboxyls that can be utilized to produce biodiesel (Jin-jiang et al., Citation2010). They are easily transported and stored. Bio-oil has been used in the engine, boilers, and turbine. It has been treated due to its thermal and chemical instability, low calorific value with much oxygen content, and high pH to produce hydrocarbon for better purpose through Hydro-de-oxygenation, hydro-treating, decarboxylation, and fluidized catalytic cracking (Choudhary et al., Citation2020; Ibarra-gonzalez & Rong, Citation2018; Jahirul et al., Citation2012; Roberts et al., Citation2013; Stöcker, Citation2008; L. Zhang et al., Citation2018). However, it goes through changes like congealing at certain conditions. Catalytic and non-catalytic pyrolysis processes are methods of treating the oil produced. These also include esterification, hydro-treating, and catalytic cracking processes (Jahirul et al., Citation2012; Jin-jiang et al., Citation2010; Syahirah et al., Citation2020). Jin-Jiang et al. (Oghenejoboh et al., Citation2013) used 732 and NKC-9 as a catalyst for the esterification of the organic acid present in the bio-oil to produce usable product (esters). A reduction of acid number up to 88.54 and 85.95% was discovered from the use of 732 and NKC −9, respectively, while the heating value increased, the water content, the viscosity, and densities were reduced at varying percentages. The bio-oil was found to show enhanced stability and corrosion control in the aging test conducted.
Four main approaches to improve bio-oil quality are shown in EquationEquations (1(1)
(1) –Equation4
(4)
(4) ) (Juliet Ben-Iwo et al., Citation2016; Stöcker, Citation2008)
Another biofuel is biogas (such as hydrogen, producer gases, butanol, dimethyl ether, methane) (Babu et al., Citation2017; Sikarwar et al., Citation2017; Syahirah et al., Citation2020). Biogas and methane can be produced from the decomposition of solid feedstock such as waste from food, municipal solid wastes, industrial waste, and animal waste in an inert environment (Adeleke et al., Citation2021). Also, cyanobacteria and eukaryotic microalgae possess triacylglycerol and photosynthetic electron for hydrogen, methanol, and ethanol production (Rodionova et al., Citation2016). Biogas is clean, cheap, and nontoxic. It can be used to generate electricity or used as transportation fuel (Juliet Ben-Iwo et al., Citation2016). Producer gas can be produced from un-watered material with high carbonaceous organic materials, such as wood, sugarcane bagasse, rice husks, pet coal, charcoal, seedcakes, and coconut shell (Bakar & Titiloye, Citation2013; H. Singh et al., Citation2021). The process includes gasifying in the presence of air oxygen or steam as an agent. Hydrogen has a low density compared to diesel fuel. It is a compound without colour or odor, which when it is supplied with oxygen, there is heat and water production (Syahirah et al., Citation2020). Bio-hydrogen is useful in CI engine, electricity generation, while the byproduct is water. It is not good for auto-ignition at high temperatures; it is only good for a spark-ignition engine. Production of hydrogen in highest percentage is available in fossil fuel up to 95% (Kumar et al., Citation2018). Hydrogen can also be produced through direct water bio-photolysis or indirect bio-photolysis process (Kumari & Singh, Citation2018). The direct photolysis involves two reactions, namely; oxygenic phototrophs and aerobic or anaerobic requirement condition in the presence of bidirectional hydrogenase enzymes (Fe–Fe or Ni–Fe). Indirect photolysis involves two steps, namely; carbonhydrate production to photo-fermentation and finally to hydrogen (Pittman et al., Citation2011). These are shown in EquationEquations (5(5)
(5) –Equation7
(7)
(7) )
Methanol is a product from natural gas. However, it could be made from biomass through an oxidation process. Bio-methanol production has been used as motor-fuels and fuel cells or powering Otto engines far back in Germany during World War II. Its use as a motor fuel, received attention in the 1970s as a result of higher price of fuel or fuel scarcity (Hasan & Rahman, Citation2017). Bio-methanol is commonly known as wood-alcohol in the 1920s because it is sourced from wood. Its synthesis is more expensive than methanol source from natural gas (Demirbas, Citation2007). Butanol is a linear 4-carbon aliphatic type of biofuel created in 1853 by Wirtz. It is receiving wide acceptance in the generation to come. It has merits like a high flash point, high cetane number, high heating value, lower vapour pressure with high alcoholic content; this makes it miscible with diesel (hydrophilic). This is produced mainly by fermentation process, which is energy-intensive and complex (fermentation occurs at low temperatures between 30°C and 65°C, yeast and bacteria, such as Clostridium beijenrinckia, breaks down polymeric sugar to monomeric sugar in a process called fermentation (Huzir et al., Citation2018)). Its blend with diesel has been reported with a major reduction in CO and hydrocarbon emissions (Juliet Ben-Iwo et al., Citation2016). Butanol, biodiesel, and diesel were blended in the ratio 10:10:80, and the blends were shown to have better properties such as thermal efficiency, density, and viscosity properties with a reduction in NOx emission (Lujaji et al., Citation2010). On a general note, bioethanol, biodiesel, and biogas are feasible in Nigeria. The use of microalgae and cyanobacteria are also in the process. The feasibility of biodiesel is still underway in Nigeria for commercial-scale, while biogas is more feasible for industrial scale, and it has encouraged a reduction in GHG. shows the properties of the various biotechnology products discussed.
Table 1. Properties of various biotechnology products
Bio-lubricant (tri-ester), which is produced through free radical processes from triglyceride ester, is another biofuel. Lubricant usage reached 46 billion/year in 2008, and it has the possibility of increasing by 2% annually (Annisa & Widayat, Citation2018). Its use has been seen in the world of agriculture, mining, transportation, automotive, forestry industry as transmission fluid and hydraulic oils. The incessant deployment of petroleum lubricant will bring unending hazard to the environment with its constant increase in double percentages from 2% to 8%. This is also seen in the constant reduction experienced in crude oil reserves by 3% yearly (Annisa & Widayat, Citation2018). Bio-lubricants help improves lubrication in moving engine parts for an overall reduction in energy loss. It has similar properties with petroleum lubricants with even better lubricity, flash point, and volatility. It is from a renewable source such as Jatropha, sunflower, and so on.
The future of biotechnology will be affected in the aspect of the price of petroleum fuel, the technology behind the production of biofuel, power politics, environmental concerns, socio-economic issues, competition with the food industry, general growth in mankind’s population, and improvement on other renewable resources. Biofuel is from a renewable and non-polluting energy sources while petroleum diesel is from a non-renewable, depleting energy source (petroleum resources) (Falowo et al., Citation2020; Nisar et al., Citation2017). Increasing the energy recovery from fossil fuel and deposits of coal, particularly in combination with carbon dioxide use, will be future work in the biotechnology world (Kilbane, Citation2016).
Biotechnology testing equipment include: XRD instrument, which could be done on a Bruker AXS D8-Advance powder X-ray diffractometer with Cu-Kα radiation having 20/min scan speed. SEM (model no: JEOL JSM-7600 F) determines the elemental, size, and shape of the catalyst. The SEM images will be seen on the FEI Quanta 200 F. Thermal transitions are usually obtained using TG/DTA (model no-STA 409 Nietzsche Geratebau GMBH, Germany) (Laskar et al., Citation2018). Gas Chromatography (GC) (HP-5890 GC pachard series 11, CBP-1 column) and Gas chromatography-mass spectrometry (GC-MS QP2010S Shimadzu) are used to delineate the major compounds present in the biofuel (Ikubanni et al., Citation2020; Sriningsih et al., Citation2014).
2. Biofuel sources
Biomasses are either plant or animal, biologically or chemically generated with the composition of oxygen, carbon, hydrogen, and some other inorganic elements (Durak, Citation2019; Juliet Ben-Iwo et al., Citation2016; Rodionova et al., Citation2016). The annual production of biomass is about 220 Bt on a dry weight basis, this is equivalent to 4500EJ of solar energy captured in a year (Chandra et al., Citation2012). Biomasses accessible in Nigeria are wood, crops, agricultural waste, forest residues, municipal solid waste, and animal wastes such as dung and poultry wastes (Adeleke et al., Citation2019). Wood biomass is more abundant in the south, while crop biomass is much in the North-central part of Nigeria (Matemilola et al., Citation2019). There has been an increased diversification plan being proposed by the Nigerian government leading to the production of ethanol and biodiesel from vast arrays of agricultural produce. This is said to lead to an increase in agricultural mechanization, substitute to fossil transportation fuel, heat generation, provisions of electricity, and rural settlement development (Galadima et al., Citation2011). Biomass plant grows in the sunlight, absorbs the solar energy, and stores this energy in its structural makeup. Biomass is the only carbon-neutral resource able to produce liquid transportation fuel and chemicals called biofuel (Huang et al., Citation2011). It became a subject of interest due to its ability to reduce greenhouse gas emissions as against petroleum-based fuel releasing ,
,
, which are all environmentally hazardous (Demirbas, Citation2007). Liquid biofuel is mostly deployed in the transportation sector, while gas is most deployed in heat and power generation (Sikarwar et al., Citation2017). Biofuel has been able to reduce dependency on petroleum-based fuel. It has increase energy security (Charter, Citation2009; Gonca & Dobrucali, Citation2016). Bio-fuel source has only been from edible crops such as maize, rapeseed or sunflower initially, and inedible source such as rubber, Jatropha, and so on. Edible biodiesel source includes sunflower, soybean, barley, castor, rapeseed, coconut, rice bran, peanut, and palm oil (Elaeis guineensis), olive oil, groundnut oil, frying oil, wheat, rice, and potato. These are referred to as the first-generation sources of biodiesel, but the growth of biofuel and its interaction with its feedstock portrays both controversy and unfavorable conditions for food security from the four dimensions, which include; access, availability, stability, and utilization (Matemilola et al., Citation2019). Edible sources of oil have accounted for 95% of biodiesel production. World war 11 was what spark the use of vegetable oil as an alternative to diesel oil sequel to the oil crises from world war 11 (Jahirul et al., Citation2012). It has been postulated that the effect of edible sources for biodiesel production would have a negative effect on food availability (Syahirah et al., Citation2020), however, the use of non-edible especially waste oils has been seen to improve in lowering toxic emissions and lower the cost of biofuel production (Nawaz et al., Citation2018). Non-edible includes Polanga oil, salmon oil, tobacco seed, sea mango oil (Cerbera odollam), winter rape, devdaru seeds (Polylthia longifolia), Mahua oil, fish oil, algal oil, neem oil, canola oil, linseed oil, vegetable oil from fatty acid distillates, sal oil (Shorea robusta), karanja oil, kusum oil (Schleichera triguga), pistachio, wild radish, greases, animal fats, and wastes oil. Edible and non-edible fall under energy crops, agricultural crops, forest residues, municipal solid waste, and so on (Annisa & Widayat, Citation2018; Kumar et al., Citation2018; Matemilola et al., Citation2019; Rodionova et al., Citation2016; Syahirah et al., Citation2020).
Energy crops include; 1. Trees such as eucalyptus, poplar, willow, 2. Grasses such as elephant grasses, sweet sorghum, sugarcane, phalaris, oil plants, and so on. They are meant for the production of fuel for energy use. Energy crops in Nigeria meant for ethanol and biodiesel production include rice, maize, sugarcane, sorghum, coconut, jatropha, cotton, groundnut, oil palm, respectively (Matemilola et al., Citation2019). Agricultural residues are referred to as by-products of agricultural crop production after gathering and processing. They include straw, bagasse, poultry litters, corn husk, rice husk, banana peel, coconut pod, cassava peel, palm kernel shell, and so on (Ikubanni et al., Citation2020; Muraina et al., Citation2017). This can be further used for fuel production. They are heterogeneous because they are made up of a varying quantity of moisture, density, particle size, and so on (Matemilola et al., Citation2019).
Forest residues are generated from forest woods through logging, trimming, or cutting. They include sawdust, wood chips, and so on. They are good for producing liquid, solid fuels for heat and electricity (Ajimotokan et al., Citation2019). Nigeria possesses the capacity to produce 1.8 Mt of sawdust yearly (Juliet Ben-Iwo et al., Citation2016; Matemilola et al., Citation2019). Municipal solid wastes are generated from homes, industries, or marketplaces (Das & Ganesh, Citation2003). They include papers (29%), glasses (5%), metals (9%), plastics (12%) and so on (N. Singh et al., Citation2014). Fuel-wood is common in the rural areas. This consists of the use of charcoal, which amounts to 40% of total Nigeria primary energy consumption. Ninety-five percentage of this is meant for cooking, industrial operation, and processing, while the remaining percent is for the service sector. This has led to deforestation and the release of more than enough hazardous substance such as CO2 into the air (Matemilola et al., Citation2019). On a general note, the wood waste contains the highest production followed by municipal solid waste, agricultural waste, and landfills having 64, 24, 5, 5%, respectively (Kumari & Singh, Citation2018).
2.1. Brief description of some biomass
The processes of biodiesel production must follow a specified method for optimum yield. Raw materials like animal fat congeal at normal temperature because it contains high saturated fatty acids, which makes it unsuitable for overall biodiesel purposes (Chakrabarti & Prasad, Citation2012). Thus, the necessity for biodiesel raw material physical property check before its utilization for biodiesel production (Das et al., Citation2018). shows the chemical composition of various biomasses. Properties of biodiesel feedstock-like free fatty acid content, un-saponification matter, phosphorous content, iodine value are important to be known for its treatment direction, economic implications, and it final quality. The feedstock for biodiesel is over 350, and its availability in different places depends on the quality of soil, climate, the methods of cultivation and gathering (Babu et al., Citation2017).
Table 2. Classification of biomass feedstock
Feedstock availability is crucial as it plays a major role in the biodiesel cost (75%) and quality (Jahirul et al., Citation2012; Juliet Ben-Iwo et al., Citation2016). Planting, gathering, and transporting feedstock to final fuel conversion are the three main energy cycle inputs (Syahirah et al., Citation2020). The amount of oil in the yield from one hectare of land is another major influence (Kumar et al., Citation2018).
One of the first-generation feedstock is starch crops, such as sorghum, a waterless resistant crop, which already contains fermentable sugar in the plant hollow stem. It offers better and more economic benefit than other starch-based crops (Galadima et al., Citation2011). Sugar is the main fermentable substance for bioethanol production. Sorghum is available in Nigeria and it is the second-highest producer after the USA (Pittman et al., Citation2011). Sorghum is planted on about 50% of Nigeria’s land (6.86 Mha) delivering about 70% of sorghum produced in sub-Saharan Africa alone. It is good for both local (such as fence and roofing) and industrial purposes (such as food and beverage drinks) (Galadima et al., Citation2011). Sorghum produces 1319.82 gallons per one hectare of ethanol, while corn produces 769.69 gallons per one hectare (Juliet Ben-Iwo et al., Citation2016). The use of sorghum for biofuel production will hamper both local and industrial usage causing the abandonment of other crops for sorghum. These may lead to deforestation, mono-cropping, environmental degradation, and soil erosion explosion (Hasan & Rahman, Citation2017; Sani et al., Citation2018). Corn is used in the USA for ethanol production. It has also been seen to improve GHG reduction by 40%. Corn is responsible for 8.4% of ethanol production while oil palm is responsible for 10% of biodiesel production. Sugarcane is present in Nigeria, though in a small proportion (Juliet Ben-Iwo et al., Citation2016). Nigeria is graded as the second-largest producer of sugar in Africa, and about 30,000 to 50,000 ha would be needed for sugar plantations to produce ethanol. This would cost the investor about 50 MUSD (Galadima et al., Citation2011). Cassava can be used to produce varieties of food, such as garri, flour, fufu, chips, and unfermented flour. It has better ethanol production capability than sorghum. Second-generation biofuel production uses inedible energy crop/biomass. Among the inedible, waste cooking oils are the most common, which is widely in use today (Nisar et al., Citation2017; Singh & Verma, Citation2019a). Sawdust is a lignocellulose material with no odor during its biodegradability process (Ajimotokan et al., Citation2019). It is meant to produce woody compost because of its high-water retention, porosity, bacteria tolerance, and low specific gravity (Maharani et al., Citation2010). Brown Devdaru seed oval-shaped fruits have a length of 1 −3 inches and 30–35 in height (Hossain et al., Citation2014). Rapeseed net energy gain is less due to co-products during biofuel production (Syahirah et al., Citation2020).
One of the widely used second-generation feedstock is Jatropha. It is mostly grown in the northern part of Nigeria. Jatropha could grow in tropical and sub-tropical regions, such as semi-arid climates, where perennial crops and marginal soil are. It is a good alternative to diesel base fuel (Chakrabarti & Prasad, Citation2012). Its ease and ability to resuscitate marginal fields have made this plant a top-notch in many countries of the world (Abdullah et al., Citation2013). Jatropha, also called physic nut, belongs to the Euphorbiaceous family. It has its existence from Central America, it was later brought in to Cape-Verde, and then to Guinea Bissau. However, it is now available in many tropical and subtropical regions like Kenya, Tanzania, India, Thailand, and places, where there is absence of enough water (Nisar et al., Citation2017). This is widely used in India leading to less demand for petroleum fuel to the tune of 18% and a reduction in the global warming saga to the tune of 52% (Galadima et al., Citation2011). Jatropha curcas and jatropha glandulifera are the two rampart species available in Nigeria (Matemilola et al., Citation2019). It produces oil to the tune of 28 to 38% (Robert Ndong et al., Citation2009), while other studies reported 30–40% (Matemilola et al., Citation2019), 35–40% (Nisar et al., Citation2017), 46 to 58% (Chakrabarti & Prasad, Citation2012), 55 to 60% (Islam et al., Citation2011). However, it is between 30 and 37 wt.% in India (Chakrabarti & Prasad, Citation2012). The oil can be esterified to produce Jatropha methyl ester. Jatropha that changes from yellow to dark brown and then to black during gathering grows as high as 6 m, it takes about 9 months to produce fruit and with a life expectancy of 50 years before turning into a tall bush (Islam et al., Citation2011).
Jatropha, made up of the inner part called the kernel and the outer part called the shell, flows a whitish substance at the latex to cause a permanent stain on the surface it has contact with, making it a source of dye. Its flowers have an attribute of a hermaphrodite. A rule of thumb approximates 30 kg of fruits to produce 18 kg of the seedlings with its seed composed of 58–62 % weight of its dry weight (Robert Ndong et al., Citation2009), 66–68% was recorded in another study (Chakrabarti & Prasad, Citation2012). The exocarp of the fruit is about 35–40% of the whole fruit. Jatropha can supply up to 3000 L/ha of oil (Matemilola et al., Citation2019), while the seed contributes to 9860 GJ/ha of net energy. Jatropha cultivation and production were further extended to be 5 Mha in 2010 and 13 Mha in 2015 (Robert Ndong et al., Citation2009). Property of Jatropha oil include good cold flow property because the pour point is within acceptable value range. Other properties includes low acid value, low viscosity compared to some oil, and good oxidation properties (Nisar et al., Citation2017). The inedibility of Jatropha seed makes it a good biodiesel source. It has the presence of unsaturated (oleic, a monounsaturated fatty acid) and saturated fatty acid in the Jatropha oil constituting 79 and 21%, respectively. The proximate analysis shows its content of moisture as 5.54–6.2%, crude oil content of 47.25%, fat content of 38%, carbohydrate content of 17%, fiber content of 15.5%, an ash content of 5.3%, and protein contents of 18–24.6% (Abdullah et al., Citation2013), (Islam et al., Citation2011). It is important to note that Jatropha oil has numerous applications such as the ability to cure; rheumatism, skin diseases, control wound from bleeding and act as insecticidal because of its alkaloids and jatrophine composition within it structure. It also has characteristics similar to diesel fuel and the ability of being used as a replacement for petroleum-based fuel (Abdullah et al., Citation2013). The oil is toxic to humans and animals like goats, rats, calves, sheep, and so on, thus the giving of the name hell oil (Islam et al., Citation2011). When Jatropha leaves grow in less than 3 months, they could be used to prepare a good stew. More so, some believe that once the embryo is removed, jatropha in Mexico and Central America are said to be eatable because it lacks phorbol esters, which are hazardous to humans (Crutzen et al., Citation2008). Nigerian jatropha seed oil does not contain lauric, capric, and myristic. However, it contains stearic, palmitic, linoleic, and oleic of 2.53%, 13%, 34.6%, and 48.8% respectively, which means it contains more carotene and less gossypol (Abdullah et al., Citation2013). It can act as bioremediation of contaminated soil in the Niger Delta, where oil exploration has caused harm to the soil (Juliet Ben-Iwo et al., Citation2016). There is the presence of 47.25% and 60.45% of Jatropha lipids in Nigeria and jatropha, respectively. Every part ranging from bark, leaf, fruit, and root of jatropha are useful. About 3 BUSD could be earned from 60 Mha of land cultivating jatropha (Galadima et al., Citation2011). Therefore, to effectively compete with fossil fuel, jatropha is a worthy biomass having so much related properties. Jatropha is a worthy feedstock to be researched upon for further industrial application (Abdullah et al., Citation2013). Presently, several countries are planting jatropha trees because of their ability to serve as a windbreakers, it protects soil from eroding and agricultural plants from being destroyed by plant-eating animals. Jatropha’s commercial strength after 4 years of planting could be up to 205 USD/year till the next 30 to 35 years. The plantation of Jatropha in India, Mozambique, Indonesia, Malawi, Malaysia, Brazil, Cambodia, Madagascar, and South Africa include; 1,000,000, 300,000, 55,000, 22,000, 20,000, 20,000, 17,000, and 15,000 respectively (Islam et al., Citation2011). Wang 2011 (Cai et al., Citation2011) reported about 30 Mha of usable land for jatropha plantation in India.
The second generation for biofuel production is energy-intensive and can multiply the land-use change (Huzir et al., Citation2018). However, microalgae does not have any problem with land-use change. Therefore, it can be most suitable for biofuel production. The energy potential in algae was founded by Meier in 1955 when he generated a gaseous substance (methane) from the carbohydrate parts of the cell (Hu et al., Citation2008). Microalgae photosynthesizes by the accumulation of sugar from solar and carbon dioxide interaction. It is divided into three broad types based on the one that consumes organic, inorganic carbon, or both (Syahirah et al., Citation2020). The one that consumes organic and inorganic is called atrophic and heterotrophic, respectively; while the one that consumes both is called mixotrophic. They become a source of carbon and energy when they are subjected to a stressful environment. Hence, they have been seen as the main source of biodiesel production in the third-generation of biofuel production. Just like the second-generation of biofuel production, it does not involve special cultivation of land, no fertilizer application or water (Juliet Ben-Iwo et al., Citation2016). Microalgae’s planting and gathering is in few hours to 10 days making it easy for management. Its oil, oxygen, and hydrogen production are much (Rodionova et al., Citation2016). About 100,000 l/ha of microalgae oil is produced yearly with about 80% of oil being generated from it. Mixotrophic has high oil content compared to heterotrophic (up to 69%). From microalgae biofuel production, there could be the production of glycerol between 5–20% dry cell weight (DCW) from the esterification process of its fatty acid and 80% hydrocarbon of carbon chain length category with up to 40% reduction in the emission of carbon dioxide (Hu et al., Citation2008; Radakovits et al., Citation2010; Syahirah et al., Citation2020). The planting and germination of microalgae depend largely on the nutrients available for their growth such as sunlight, availability of
and so on (Hasan & Rahman, Citation2017). Cyanobacteria (algae) and microalgae are numerous (about 40,000 species). Major ones are known in terms of colour such as cyanobacteria (blue-green algae), green algae, yellow-green algae, golden algae, red algae, brown algae, dinoflagellates, and pico-plankton living in different biological, marine, brackish, freshwater and hypersaline environs (Vardon et al., Citation2012). To support this, wastewater and food waste, supply fresh water and nutrient, respectively. However, fear arises from the fact that the presence of foreign substances could pollute the wastewater and inhibit microalgae survival. It grows in triple tendencies per day up to 100 times greater than higher flora. It prospers in seawater brine, and marginal lands, where many organisms may not exist (Jena et al., Citation2012). It uses wastewater nutrients such as nitrogen and phosphorus generated from different means such as municipal and
(generated from a gas plant using natural gas in agricultural industries. Algae help to reduce by sequestration the emissions of
causing greenhouse gas effect. Its by-products are useful for fertilizers and feeds (proteins) for animals (Hu et al., Citation2008; Pittman et al., Citation2011). Algae plants such as Chorella, C. vulgaris, and scenedesmus can be used for the removal of large portions of nitrogen, toxic metals, and phosphorus in wastewater (Pittman et al., Citation2011). Algae plants are advantageous in this regard because the numerous presences of this nutrient such as phosphorus and nitrogen may lead to what we call eutrophication. In the past, these nutrients have been removed by conventional means such as chemical processes and it has generated more of waste in landfills, however; the use of algae has been found to efficiently make use of these nutrients for its personal growth. Algae has played a bioremediation role in environmental sustainability (Rodionova et al., Citation2016). Cyanobacteria do not have enough lipids as conducted in the laboratory. However, it is the most common, being produced first by cultivation, then gathering, dewatering, cell disruption, lipids removal for the purpose of biodiesel production by trans-esterification means, and fermentation for ethanol production (Rodionova et al., Citation2016). Microalgae biofuel is said to be unstable. It production requires a double preparation mechanism including more energy required for gathering, drying, and extraction (Hu et al., Citation2008). Therefore, the harvesting techniques for microalgae needs to be improved upon for overall cost reduction of biofuel production (Vardon et al., Citation2012). Its harvesting techniques include centrifugal, bio-flocculation, and sedimentation or filtration process. The production of oil-based usable products from algae is still limited in terms of performance economically and footprint ecologically (Lundquist et al., Citation2010). Other factors responsible for algae production in wastewater include pH, temperature, oxygen, carbon dioxide, photosynthesis and organic carbon availability. A higher temperature may not be good for algae growth. Also, the presence of pathogenic bacteria and zooplankton may prevent algae from flourishing.
The fourth-generation involves a genetic generation of microalgae. It has more effect on reducing GHG by capturing more and reducing its emission into the atmosphere because from the 50% of GHG emission emanated from biofuel synthesis in the third generation, 57%, and 32% are as a result of synthesis and drying of microalgae (Hu et al., Citation2008). Genetic control can only be understood from the control mechanisms for the cell cycle and triacylglycerol’s synthesize relationship (Hu et al., Citation2008). However, it could not be used for all microalgae because there is neither gene nor biological information, thereby making the technology still limited in scope (Syahirah et al., Citation2020). Chlamydomonas reinhardtii, Chlorella variabilis, and some more microalgae species are undergoing modification genetically. However, Hu et al. (Citation2008) opined that cultured Oleaginuos algae can provide 200 bbls from one hectare of land, this is said to be greater than biodiesel production from soybean in the US (Rodionova et al., Citation2016). He further said the concept of biological production of both TAG and fatty acid in algae must be well understood for its wide production, and there must be engineering ability to culture algae for genetic control to final processing for biofuel production. Therefore, the improvement that will usher algae-biofuel massive production will be greatly determined by the massive development of algae culture systems to ensure high growth and sustained growth rates. However, more studies can be conducted on the negativity from managing genetic production of microalgae to the environment and the economy, including, improvement in the harvesting of microalgae skills, and the development of low capital cost-efficient strategies for biofuel production (Radakovits et al., Citation2010). shows the chemical composition of different biomasses.
Table 3. The chemical composition of different biomasses
2.2. Different conversion mechanisms
Biomass is a renewable energy source that has come to replace the depleting fossil fuel. The transformation of biomass into different usable energy has been the interest of engineers, scientists, and technologists. The primary biofuel is obtained naturally through the burning of wood; however, the method of open burning of waste has been discouraged. The secondary biofuel is obtained from different conversion methods from plants and animal wastes (Pittman et al., Citation2011). Biofuel could be produced from wastes or agricultural products by thermochemical, biochemical or hybrid means (Huang et al., Citation2011; Syahirah et al., Citation2020; L. Zhang et al., Citation2018). Biomass wastes are sources of carbonaceous substance and can be transformed into usable biofuel products through pyrolysis (Hossain et al., Citation2014). Catalytic pyrolysis, non-catalytic pyrolysis, gasification, and fermentation are all different methods that have received diverse interest for biodegradable and environmentally safe fuel (L. Zhang et al., Citation2018). The steam forming process is the cheapest method to produce hydrogen gas (Egorov & Strizhak, Citation2017).
Lignocellulose materials, composed of mainly hemicellulose and cellulose, could not be directly converted to biofuel. However, they would first be converted to simple sugars before finally being converted to biofuel such as ethanol, butanol, and other fuel products (Kilbane, Citation2016). The biochemical process uses anaerobic digestion or fermentation process to break down the hemicellulose and cellulose into biogas such as bio-methanol (Rodionova et al., Citation2016). Thermochemical process breaks down lignin to guiacol, phenolic compounds, which can be used to generate phenolic resins with higher molecular weight. More so, low molecular weight methane and carbon monoxide can be obtained alongside (Jahirul et al., Citation2012; Juliet Ben-Iwo et al., Citation2016; Stöcker, Citation2008). Biomass is composed of mainly cellulose, hemicellulose, and lignin content, in which their respective percentage composition affects the yield component and percentage yield. Cellulose is not easily hydrolyzed. Hemicellulose is easily hydrolyzed because hemicellulose links cellulose and lignin together (Syahirah et al., Citation2020). Hemicellulose dissolves in alkali, while cellulose is insoluble in solvents. Lignin is composed of 15–30% of biomass and does not yield easily to thermal disintegration unlike others (Chandra et al., Citation2012; Verma et al., Citation2000). Hence, cellulose and hemicellulose are preferable for the conversion process due to their easy disintegration (Papari & Hawboldt, Citation2015). However, Chen & Dixon (Citation2007) opined that lignin modification improves fermentable sugar yields for biofuel production. He further stated that the genetic reduction of lignin would significantly improve bioprocessing, and it will be far better than the serious reduction in sugar loss from the pretreatment process using acid; especially, when the hemicellulose part of the transgenic lines is exposed to enzymatic reaction.
2.2.1. Fermentation and anaerobic digestion
Fermentation process uses selected microorganisms such as Saccharonmyces cereviciae to ferment glucose/sucrose into ethanol, hydrogen, methanol, or succinic acid (Verma et al., Citation2000). The biomass waste involves treatment whereby the hemicellulose is separated from the cellulose, and the cellulose in the biomass is hydrolyzed into glucose. The hemicellulose can be converted into hexoses and pentose (Juliet Ben-Iwo et al., Citation2016). Bio-ethanol is the most common liquid fuel produced from hydrolysis and fermentation of cellulosic biomass such as starches (corn, potato, and corn) in the first generation (Jena et al., Citation2012). They are further distilled to remove foreign substances and for high-quality bioethanol production (Huzir et al., Citation2018). Municipal solid waste (MSW) could be biogenic or non-biogenic. The biogenic MSW could be anaerobically digested to produce biogas for household use, while some could be used as landfills; this emits pollutants such as or methane into the atmosphere. About 250 m3 of biogas could be generated from 1 tonne of solid waste (Juliet Ben-Iwo et al., Citation2016). For the production of biogas in the case of the anaerobic process, a digester loaded with waste is needed. It digests biomass waste containing 85–90% water content in the presence of microorganisms after two days or more. This conversion results into
and
with some traces of hydrogen sulphides, while the by-product could be used as fertilizers (Sadef et al., Citation2016). Singh et al. (Adeleke et al., Citation2021) opined that an anaerobic digester being fed with kitchen waste in every six days for a period of 30 days has been used to produce 0.00503
biogas. The fixed-type digester operated at the range of 28 to 38°C while an average increment of 7°C was noticed during this period of production. Food waste accounting for 27% of MSW generated from the households, restaurants, and hotels (hotel generates 45% of MSW) are mostly deposited in the dumpsites (N. Singh et al., Citation2014). Industrial or sewage waters can also be used to generate biogas for heat production because they contain organic or inorganic substances. They can be processed into biogas through an anaerobic digestion process. Animal waste such as wastes from cattle, goats, pigs, sheep, and livestock could generate about 0.03 m3 biogas from every 1 kg used (Juliet Ben-Iwo et al., Citation2016). This can be used to provide heat and power for the CI engine. Biogas generating plant is said to be in Lagos, Ogun state, and Kaduna in Nigeria but not in commercial size (Matemilola et al., Citation2019).
2.2.2. Pyrolysis, liquefaction and combustion
2.2.2.1. Solid waste pyrolysis
The four main thermochemical conversion processes include liquefaction, gasification, direct combustion, and pyrolysis (Egorov & Strizhak, Citation2017; Lissianski et al., Citation2002). Pyrolysis has been found to have the best and the most efficient thermochemical conversion process with its processing cost higher by $3.27 compared to cost of processing one gallon of gasoline fuel (Hossain et al., Citation2014; Syahirah et al., Citation2020). Hydrothermal liquefaction is the process of converting biomass into liquid by thermochemical steps in the presence of supercritical water, less temperature (250–350°C) and high pressure (5–20 MPa) (Huang et al., Citation2011). Hydrothermal liquefaction produces a higher heating value and lowers oxygen content compared to pyrolysis (Choudhary et al., Citation2020; Durak, Citation2019). During liquefaction, there is first, the process of hydrolysis where the biomass is broken into pieces, followed by the process of degradation into smaller components, such as dehydration, de-oxygenation, further to decarboxylation, and finally to depolymerization (Ibarra-gonzalez & Rong, Citation2018).
Pyrolysis is as old as 5500 years. It was first conducted in Mississippi, KioR Inc. plant in Columbus, where a large commercial plant of pyrolyzer was set up costing 215 MUSD (Juliet Ben-Iwo et al., Citation2016). Initially, pyrolysis process helps to produce tar, charcoal, coke, bronze, and iron product; but now, it decomposes biomasses at high/average temperature (400 to 600°C) condition in the absence of air (by introducing nitrogen gas) with a high heating rate and low holding time. Hence, it condenses the oil and gas mixture into oil in the condenser (Capocelli, Citation2007). A high heating rate, low residence time, and low temperature are essential for more liquid yield, up to whooping production of 75% from the fed dry biomass (Hossain et al., Citation2014). Before biomass can undergo the pyrolysis process, it should pass through cleaning and sorting processes. For instance, if Jatropha seed is to be made ready for transformation into biodiesel, it should be de-hulled and dried. The process of de-hulling, drying, and storing in a cool dry place is necessary for a quality yield of oil (A. Adeleke et al., Citation2020). Drying is classified into; reactive drying, non-reactive drying, and torrefaction (A. Adeleke et al., Citation2020; Adeleke et al., Citation2021, Citation2020; Balogun et al., Citation2021; Odusote et al., Citation2019). The drying of biomass in a non-reactive atmosphere (absence of oxygen) is the best as it reduces biomass weight. This further reduces the energy involved in grinding and moisture content to about 5–15 wt%. Storable jatropha must have a moisture content as low as 5 to 7 wt%). The drying increases biomass stability, reduces the corrosiveness of the liquid yield, and brings about more efficient solid to liquid conversion (Islam et al., Citation2011). The higher the moisture contents, the higher the time for drying. The reason for grinding biomass to about 2–6 mm size is to improve heat contact between the biomass and the heating agents. However, the cost of grinding increases the overall cost of production. The process of pre-treating wood by heating at 210–240°C in a tube furnace in catalyst presence has a consequence on the yield of oil, char, and gaseous substance (Jahirul et al., Citation2012). In the torrefaction of pinewood, there is a decrease in acetic acid yield with a 30% increase in aromatic compounds (A. Adeleke et al., Citation2020; Adeleke et al., Citation2021, Citation2020, Citation2019; Odusote et al., Citation2019). Potassium, calcium, and magnesium can improve the biomass disintegration reaction for biochar production. Also, sodium chloride, calcium chloride and magnesium chloride added with switchgrass ash before pyrolysis also has an effect on the molecular weight of products at high temperatures. Acetic acid and aldehyde are produced by this method (Bakar & Titiloye, Citation2013). Oilseeds and animal fats can be pyrolyzed to produce diesel products. Carboxylic acids, alkanes, alkenes, gases, and aromatics are produced in small proportions using the pyrolysis process. Organic products from biomass disintegration are dependent on feedstock composition as biomass and sewage sludge have low and high calorific values, respectively (Baeyens & Baeyens, Citation2009). Volatile organic compounds present in biomass include formic acid and acetic acid. They also include furanic from cellulose and hemicellulose disintegration, levoglucosan from cellulose disintegration, phenols from lignin decomposition including sugar with the presence of water and oligomers. This is the reason why pyrolysis oil produced from biomass (such as walnut, olive husk, and hazelnut shell at 700°C to 800°C for total disintegration to vapour molecules) gives high pour point, viscosity, flash point, and acceptable calorific value but low cetane value and more carbon residue (L. Zhang et al., Citation2018). Potassium, calcium, silicates, phosphate, and so on are all inorganic compounds and in few quantities compared to organic compounds up to 400 in pyrolysis process (Kumar et al., Citation2018). The inorganic compounds include alkaline metals and salts. While this depends on the biomass constituent, organic compounds depend on the mechanism of reaction in the reactor chamber. Enzymatic and thermochemical conversion method (pyrolysis) are more likely the best converting technology for soft/hardwood biomasses, but the hydrolysis process used for pretreatment during enzymatic conversion mechanism is very belaboring. The pretreatment method could be chemical, biological, physical, or physicochemical (Papari & Hawboldt, Citation2015). The use of a dual pretreatment process instead of applying a singular method has been encouraged (Kumari & Singh, Citation2018). From the pyrolysis of wood, about 50% of methanol with traces of hydrogen gas, phenol, acetone, and water are obtainable (L. Zhang et al., Citation2018)
Fuelwood is a major fuel for cooking. Over 55% of wood is used up as fuel-wood in advanced countries. About 62.3 million m3 was used up in 2008 (Juliet Ben-Iwo et al., Citation2016). The pyrolysis process could be slow, fast, or flash (Al Arni, Citation2017). Slow pyrolysis involves 0.1 to 1°C/s heating rate, a long residence time running to hours at 400–600°C to produce fuel gas and more char. However, it is mostly of low fuel quality. This has been successful in producing chemicals such as bio-methanol, fuel additives from lignocellulose biomasses, and polymers wastes (Jin-jiang et al., Citation2010). Flash pyrolysis involves the production of more oil at low temperature, short residence time, and fast rate of heating. Also, during the flash pyrolysis system (at highest heating rate >1000 and short residence time), gas and tar (50–75%) are produced at high temperatures, while more tar is produced at low temperatures (400–500°C) (Jahirul et al., Citation2012). Hossain et al. (Citation2014) used a fixed bed pyrolyzer to check the effect of the size, temperature, and running time on the yield of Devdaru seeds conversion into bio-oil, while rice husk, cow dung, and charcoal were the source of heat. It was recorded that the maximum yield of 51 wt.% was recovered at the sample size of less than 1.18 mm, 500°C, running time of 90 minutes, and a gas flow rate of 5 liters/min. The heating value of this Devdaru seeds oil was found to be 24.22 MJ/kg (Hossain et al., Citation2014). The pyrolysis process of solid to liquid conversion is endothermic unlike incineration that is exothermic process (Jahirul et al., Citation2012; Papari & Hawboldt, Citation2015)
During the pyrolysis process, three products are obtainable. The products include char, volatiles, and tar (including sugar, proteins, starches, lipids, water pentose, hydrocarbons in different amounts) (Choudhary et al., Citation2020; Ibarra-gonzalez & Rong, Citation2018; Khan et al., Citation2016). The tar tends to be the heavy hydrocarbons, while the volatiles is condensed at ambient temperature. The char contains carbon with a little hydrogen and heteroatom presence, which is good for; solving environmental pollution problems, cooking, electricity generation, and can serve as a chemical feedstock for other processes (Agarwal et al., Citation2015). Char can also be used for soil enhancement (because of curcumin and nitrogen presence). This is achieved by helping to remove various toxic substances present in the soil such as copper, chromium, zinc aromatic hydrocarbon compounds, poly-brominated di-phenyl ethers, and so on. It equally helps to reduce the effect of disease-killing agents and increase the enzymatic reaction in the soil. The dehydrating ability can also be seen from bio-char by it, being used as support for catalyst. The biochar is a function of high-fixed carbon, which is a function of biomass lignin content (Balogun et al., Citation2021; Oasmaa et al., Citation2010; L. Zhang et al., Citation2018).
Heat
water
carbondioxide, hydrogen gas, carbon-monoxide
methane
ethane
+ tar + char is referred to as pyrolysis process (Hossain et al., Citation2014). Tars are turned to hydrogen and methane when applied temperature is more than 500°C (Capocelli, Citation2007) With slow pyrolysis, more methane are produced while fast pyrolysis produces more of hydrogen (Shirazi, Citation2020).
2.2.2.2. Plastic waste pyrolysis process
It is important to state that pyrolysis circulated widely far back in 1978 in Germany, Austria, Italy, and Korea. It is considered the best option in the recycling process (Onwudili et al., Citation2009). Thus, the pyrolysis of plastic wastes to useful oil is also very important. Polyvinyl chloride (PVC) and polyethylene terephthalate (PET) are not a good product for catalytic pyrolysis due to dangerous gaseous emissions (L. Zhang et al., Citation2018). Pyrolysis of waste tires to fuel has been useful for various purposes as 25–35 wt.% of carbon black and up to 60–65 wt% of rubber could be produced from waste tires. The works done in the US from the use of recycled plastics for transportation and many other purposes have increased by four times i.e from 8.5 Mt in 1992 to 35.8 Mt in 2002; thereby, leading to fossil fuel conservation (Baeyens & Baeyens, Citation2009). The energy content from waste plastic is higher than that from biomass. The energy content in the case of tire waste crumbs is up to 16,039 Btu/lb because many of the plastics produced today for different purposes are from fossil fuel (Baeyens & Baeyens, Citation2009). The humongous availability of waste polymers in the environment is constituting an environmental nuisance. However, one of the solutions to this environmental nuisance is to utilize a pyrolyzer, which is a chemical recycling pathway. In the year 2007, plastic production reached 200 Mt, and in 2015, it got to 322 Mt (Onwudili et al., Citation2009) with the hope that if it keeps increasing by 5% every year, it possesses the capacity to increase to 0.25 Bt at the rate of in 2025. This is because of the increase in urbanization and economic progress (Capocelli, Citation2007). Plastic recyclable programs include the mechanical pathway (re-extrusion), which is used in automobile industries. Chemical and energy recovery with the mechanical route involve the process of treating the material physically. They are performed specifically on plastic such as PP, PS, and PE (Gu et al., Citation2017; Onwudili et al., Citation2009; Sriningsih et al., Citation2014). The chemical route uses chemical means to transform into usable petrochemical products. Polymerization occurs during the chemical recycling process with a significant change in the chemical structure of the waste. Thus, the name chemical recycling route (Stöcker, Citation2008). Energy recovery involves a partial or complete oxidation process for power and heat production. The thermochemical/thermolysis pathway involves the production of heat through mini or total oxidation to form char, gas, and oil. This process could be achieved through pyrolysis or gasification, hydrogenation at high pressure and temperature, and catalytic cracking (Baeyens & Baeyens, Citation2009; Okareh et al., Citation2020). It is discovered that the type of plastics, the size of the plastic feedstock, the heating rate, vapour, and solid residence time, temperature and pressure, the type of reactor structure, the power rating of a pyrolyzer, catalyst and nitrogen presence as carrier gas were the factors to be considered responsible for oil yield, liquid condensate, boiling point, and its final composition and application (Khan et al., Citation2016; Onwudili et al., Citation2009; L. Zhang et al., Citation2018). The reactors currently in use include vacuum, ablative, fixed bed, auger, plasma, free-fall reactor, pyros, microwave, solar, fluidized bed, and circulating fluidized bed (Das & Ganesh, Citation2003; S. O. Adegoke et al., Citation2021). The ablative configuration is quite complex considering the cone and plate moving part. Both ablative and vacuum pyrolyzers are said to have a low heating rate (S. O. Adegoke et al., Citation2021). Circulating fluid and bubbling fluidized beds are the most used because of their high-quality yield of the liquid product with high heating value and low formation of tar. However, the bubbling fluidized bed reactor is the most efficient reactor for woody biomass conversion to bio-oil because of its fast-heating rate. The use of a fixed bed pyrolysis reactor is seen as the most efficient method for solid transformation to liquid biofuel (Hossain et al., Citation2014). The word fixed bed means the feeder and the feed are fixed at high temperatures. Microwave has been employed for uniform heating and high efficiency in the pyrolysis of biomass (L. Zhang et al., Citation2018).
There is a need to consider optimal conditions for the pyrolyzer’s best oil yield. Khan et al. (Citation2016) opined that waste plastic (HDPE) oil pyrolyzed at the range of 330 and 490°C for 2 to 3 hours recorded the flashpoint of 15°C, at this temperature; there is a need for caution in terms of storage and transportation. It is lower than kerosene, furnace oil, and diesel. It also discovered that the first two hours of production experienced a maximum oil yield of 77.03%, whereas, from the second to third hour, there is a decrease in oil yield. Using a flash pyrolysis process, Onwudili et al. (Citation2009) pyrolyzed LDPE and PS. The composition of the individual oil and their mixtures were analyzed for their chemical compositions at the range of 300 to 500°C. It was discovered that the increase in LDPE oil yield received a downward trend at above 425°C because the sample has been converted to char and aliphatic hydrocarbon fuel. The disintegration to oil for PS was discovered around 350°C, while the increase in char content increases till 425°C. The compositions of PS oil were toluene, ethyl benzene, and styrene, which were mainly aromatic compounds. At 500°C, the amount of char produced was two times more than LDPE. This explains the effect of aromatic compounds in the production of char. When the two samples were pyrolyzed at the ratio of 7:3 of LDPE and PS, more wax came at 350°C, which were transformed into oil at 400°C. The oil produced from this mixture is greater than the individual pyrolysis process done at 450°C.
shows the properties of different plastic sources and petroleum-based oils.
Table 4. Properties of different plastic source and petroleum-based oils
2.2.3. Catalytic pyrolysis process
Pyrolysis may also involve the use of catalysts to help ensure a higher quality of the products yield. This will reduce the carbon number and raise the heating value (L. Zhang et al., Citation2018). The pyrolysis-catalytic treatment of cellulose leads to more yield of gaseous substances (18.4%) that do not condense. More so, the production of aromatic compounds (38.4%) is obtainable. Hence, there is a possibility of an overall production of high-quality liquid yield at a reduced working temperature (Jahirul et al., Citation2012; Stöcker, Citation2008). Treatment of oil through catalysts such as metal oxides, ethanol, 732 and NKC-9 resins, mesoporous materials, alkaline metals
,
, and alkali earth metallic species
, Ni-Based, novel metal, micro-porous substances (ZSM-5, Al-MCM-41, Al-MSU-F) and transition metals have increased the products energy density (Bakar & Titiloye, Citation2013; Huang et al., Citation2011; Laskar et al., Citation2018; Lissianski et al., Citation2002; Vardon et al., Citation2012; J. Zhang et al., Citation2019). This is achieved by removing oxygen presence and replacing it with another functional group. Hence, this affects the hydrogen–carbon ratio that will improve the stability of the oil and its chemical properties. The use of catalyst helps to produce some desired fuel. The selection of the type of catalyst with exact acidity and pore structure can lead to the production of gases, diesel, and gasoline. Iron catalyst and cobalt catalyst are used as catalyst to produce linear-olefins product containing
and
. The hydrocracking or steam splitting process breaks the carbon bond between carbon 20 and carbon 50 present in the structure. Then, converts it to low molecular weight products in a bid to obtain lighter fractions such as ethane, propane, kerosene, gasoline, and diesel, and so on (Babayemi et al., Citation2019). Catalytic pyrolysis works at low temperatures compared to gasification (Sriningsih et al., Citation2014). From the disintegration of cellulose, more CO is produced while hemicellulose disintegration produces less. Hemicellulose contains a yield of 29.4% of coke substance with a 39.1% yield of non-condensable gaseous substance (L. Zhang et al., Citation2018). More ketones, phenols, and esters can be produced from the blend of catalytic pyrolysis process of cellulose and lignin (Stöcker, Citation2008). The high composition of cellulose requires pyrolysis temperature between 350 and 550°C to disintegrate the biomass to a smaller molecule for biogas and oil production (Syahirah et al., Citation2020)
Sriningsih et al. (Citation2014) studied the presence of bi-functional catalysts during the hydrocracking of LPDE waste plastic. An activated Zeolite is made by soaking the natural zeolites into 6NHCL for 30 minutes and then oven-drying it. Also, some bi-functional catalysts (Ni/Z, Ni-Mo/Z, Co/Z, Co-Mo/Z) were co-used with the activated zeolites to ensure activity increase. The process of hydrocarbon production was carried out in 1 h at 350°C with hydrogen as steam at the rate of 20 ml/min. It was discovered that the use of Co-Mo/Z has the best yield up to 71.49% gasoline. The chemical structure of the fuel indicates the presence of 6 to 19 carbons depicting the presence of olefins, paraffin, and naphthenic. The use of silica-alumina, zeolites, and beta as catalysts were said to be costly. They also require great exactness in their preparation. However, the use of natural zeolite will reduce the cost of production (Stöcker, Citation2008). Its activation through metal addition will increase its surface area, pore, and acidity level. Zeolite’s pore sizes range from 0.4–1 mm with a micro-porous structure made up of alumino-silicates (Shirazi, Citation2020). Zeolites hydrogenation and hydrodeoxygenation have been used as a treatment for bio-oil through carbonium ion mechanism to produce lightweight hydrocarbons, aromatics (HCl, syngas, and hydrogenated solid residue (Bakar & Titiloye, Citation2013; Nicodème et al., Citation2018). Natural zeolites are present in Korea, Indonesia, Bulgaria, USA, Czechoslovakia, South Africa, Mexico, Japan, Yugoslavia, Cuba, and so on. Some studies have discussed the use of waste plastic through recycling in developing a bio-based fuel with a little/no negative effect on the environment. The oil produced from this process could be used as a fuel for CI engines (Abed et al., Citation2019; Sikarwar et al., Citation2017). S. Adegoke et al. (Citation2020) opined that a separate pyrolysis of polypropylene and Jatropha curcas seed can be blended at different ratios and serve as an alternative to diesel fuel in automobile/compression ignition engine (S. Adegoke et al., Citation2020).
Furthermore, the catalytic pyrolysis process helps to increase the temperature of the system, improve conversion mechanism, increase heating value, and reduce the cost of production without the catalyst being affected (Jahirul et al., Citation2012). However, pyrolysis working in the absence of catalyst usually reduces the cost of production (Khan et al., Citation2016). Co-pyrolysis of biomass and polymers (PE and PP) shows that furfural and furan from the disintegration of biomass components react with olefins in the polymer disintegration resulting in the formation of aromatics. In the same manner, the reaction between alkanes and olefins formed from polymer disintegration could lead to the inability of the product from biomass to coke. Styrene from the disintegration of polystyrene reacts with furfural to produce indene (L. Zhang et al., Citation2018). These compounds are all demerits of this process because it involves various workloads in the treatment and removal of those acid contents to the final usable products. This informs that numerous researchers can embark on the production through microalgae synthesis. It should be said that the energy gain from the use of algae as biodiesel is higher compared to corn and bagasse as ethanol (Demirbas, Citation2007).
2.2.4. Gasification
The plastic recycling technology by catalytic thermal degradation and gasification is also known for its ability to generate tar up to 10–45% weight during the gasification process. Gasification technology is expensive and not flexible (Nicodème et al., Citation2018). It requires high temperature of up to 600–800°C, and sometimes 800–900°C, where air is supplied to oxidize the hydrocarbon sample. This is to generate heat for carbon-monoxide and hydrogen production with a trace amount of carbon dioxide and methane (Juliet Ben-Iwo et al., Citation2016). Gasification requires more treatments to produce a usable fuel, therefore, making this method becoming obsolete (Baeyens & Baeyens, Citation2009). The gasification of biomass at high moisture content up to 35% can lead to the production of bio-syngas such as hydrogen gas (Ibarra-gonzalez & Rong, Citation2018; Lissianski et al., Citation2002). The syngas can be utilized in CI engines but with higher NOx emissions during usage (Chakrabarti & Prasad, Citation2012). At high temperature and pressure, syngas can turn to methanol, this can be up to 100 gallons from 1 ton of feedstock. Hydrogen gas increase from 33 to 40% as the temperature is increased from 500 to 750°C. Forest grasses, switch grasses, miscanthus, animal and municipal wastes, algae, and crop residues are burnt at 700°C in oxygen and, or steam presence to give hydrogen, CO, and (Pittman et al., Citation2011). By gasification, syngas consisting of carbon-monoxide, hydrogen, carbon-dioxide and methane at 18–20%, 18–20%, 8–10%, and 2–3%, respectively, are produced with traces of pentane, nitrogen gas, and steam used in the reaction (Al Arni, Citation2017). Methane and steam produce hydrogen at the range of 700 and 1000°C under 3 to 25 bar as displayed in EquationEquations (8
(8)
(8) –Equation9
(9)
(9) ) (Kumar et al., Citation2018)
or
EquationEquations (10(10)
(10) –Equation11
(11)
(11) ) shows the production of bio-methanol from the gasification reaction of carbohydrates and the partial oxidation of oxygen and water (Egorov & Strizhak, Citation2017).
The hydrocarbon production from Fischer-Tropsch synthesis is dependent on the applied temperature, catalyst, pressure, and residence time to produce ethane ), ethene (
), LPG (
), diesel (
), gasoline (
) and waxes (
) (Sikarwar et al., Citation2017). The technology of industrial application of Fischer Tropsch synthesis started in Germany in the early 19 century (Demirbas, Citation2007; Ibarra-gonzalez & Rong, Citation2018; Nicodème et al., Citation2018). With the presence of biomass components in Nigeria, gasification and anaerobic digestion process can be applied as biomass waste conversion process into usable fuel product (Juliet Ben-Iwo et al., Citation2016)
2.2.5. Other conversion routes
Hydrolysis, glycolysis, aminolysis, methanolysis, glycolysis, acid cleavages, and hydro-glycolysis are chemical transformation route (Baeyens & Baeyens, Citation2009). Forest residues such as sawdust, veneer log cores, edgings, slabs, and sawmill rejects could also be used for biofuel production through hydrolysis process (Juliet Ben-Iwo et al., Citation2016).
A hybrid route involves the case in which a semi-biochemical product is concluded by thermochemical means (Syahirah et al., Citation2020).
One of the physical conversion routes include solvent extraction method (Ibarra-gonzalez & Rong, Citation2018). Extraction is done using a screw press. In some cases, hexane is used as a solvent for extraction. Hand press and mechanical expeller have also been used with more yields from mechanical expeller up to 75–80% oil compared to the hand press with 60–65%. Of all solvent extractors, hexane is qualified to remove stanched oil contained in the expeller up to 1% remaining at 68°C, 0.5 to 0.75 mm size of seed in 8 hours reaction time and 6:1 of solvent to seed (Chakrabarti & Prasad, Citation2012). For instance, oil is solvent-extracted from algae while the residue from the extraction is used to produce biogas for electricity generation through anaerobic digestion. The remaining residue can be fed back to the algae pond (Lundquist et al., Citation2010). shows the different conversion routes and there qualities.
Table 5. Conversion routes and there qualities
2.3. Benefits of biofuel
Biofuel has helped the rural settlers by the use of biodiesel as a source of heat against the inaccessible or costly petroleum fuel. This has erased the stress of looking for firewood to cook food. The generation of fuel from biomass origin would lead to jobs generation for young men and women and reduce the reliance of fuel on the oil-producing countries (Lujaji et al., Citation2010). It will equally provide more money for those countries who embark on it massive production. Galadima et al. (Citation2011) did survey in Nigeria to see people’s views about biofuel production from biomass. He reported that about 97% of the respondent chose that the production of biofuel will lead to rural development, increase in GDP, increase in employment for teeming youth, energy sustainability, and a clean environmental (Babu et al., Citation2017). Biofuel production involves the use of both skilled and unskilled labor. It is unlike solar and wind energy, which does not create many jobs because it involves much advancement in technology (Balogun & Salami, Citation2016). Oil and gas companies only offer jobs for less than 1% out of over 200 million populations, this has led to an increase in the spate of migration of people for greener pasture due to an increase in the level of abject poverty battling with them (Galadima et al., Citation2011). The use of biofuel (biodiesel) has been seen in the drilling industries in the formulation of mud. The drilling fluids used in the drilling industries include oil, water, or synthetic-based fluids (Oghenejoboh et al., Citation2013). Water-based mud has been used in drilling formations in the past but the rising harsh situations such as high temperatures, lubricity, and viscosity in the formations encountered, calls for a better drilling fluid (Ismail et al., Citation2014). Water-based mud (WBM) could not handle the several difficult cases met in the field. Thus, the need for oil-based drilling fluid which offers better properties such as high lubricity, filtration control and absent shale swelling. Oil-based fluids have been used but it has a negative influence on the environment during it discharge. Aside from that, it is very costly and it causes lots of harm to the marine and land ecosystems. These are the reasons why researchers have developed an alternative fluid to oil drilling fluids with characteristics such as environmental friendliness, nontoxicity, and still meets up to the same performance from oil-based fluid though with some little unavoidable limitations (Li et al., Citation2016). For instance, biodiesel from palm corn, rice, and so on have shown very good biodegradability properties and have been used in formulating ester-based drilling mud. Ismail et al. (Citation2014) reported that rice bran has shown 50% lethal concentration being felt in the range of 10,000 to 100,000 rpm. It has also shown 80% biodegradation rate in the space of 28 days. However, Li et al. (Citation2016) recorded that ester-based drilling fluids from one end of synthetic material would lead to higher cost compared to diesel and mineral oil. Feedstock contributes greatly to the price of biodiesel with feedstock requiring up to 39% of the total cost of production while 33% is responsible for capital cost (Syahirah et al., Citation2020). Biodiesel cost of production as regards the procurement of chemicals and the availability of the feedstock are also very germane. Biodiesel was used first in Norway’s offshore field and since then, it has led to the development of biomass-based drilling fluid, which has been used in many of the drilling outlets (Ismail et al., Citation2014). Li et al. (Citation2016) synthesized a biodiesel-based invert emulsion drilling fluid (BBDF), which is different from the most common water-free system. He opined that BBDF could withstand 10% seawater and 15% drilling solid. The characteristics showed good filtration figures, high electric stability even when hot-rolled for 16 h at 120°C. The rheological parameters are also in conformity with standard values. Oseh et al. (Citation2019) recorded a flash point of 169°C of sweet almond seed oil (SASO) biodiesel, which is higher compared to diesel in terms of good fire property, safe in storage and transportation. The cetane number of SASO biodiesel is 57 against diesel which is 52. The low calorific value of SASO biodiesel is a result of low carbon and hydrogen content. The high mono-unsaturated property of SASO (71.1%) is responsible for cold flow properties and high kinematic viscosity, which also translates to higher values in the rheology properties. This is the reason for its inability to adapt to high solids loading at high fluid density (Ismail et al., Citation2014). The SASO acid value is 0.13 leading to a lower temperature of operation. This can be reduced by reducing its free fatty acid, free and total glycerin contents. The vegetable oil is processed from triglyceride to glyceride because triglyceride is the main ingredient containing a substance for bio-lubricant/biodiesel formation (Annisa & Widayat, Citation2018). Also, used lubricating oil containing heavy metals, un-burnt product, water, high molecular weight hydrocarbons accumulated from dust interference, and engine use are emptied in the water system. These have negative health impacts on aquatic and terrestrial life. Oghenejoboh et al. (Citation2013) revealed that re-refined used lubricating oil extracted from normal ethylprolidone was used to form base oil and compared with three other synthesized oil base fluids (paradril, emcald, and ty-chem-low tox). The re-refined base mud formulation reveals toxicity, low electrical stability compared to others, and bad filtration characteristics making the re-refined oil unsuitable as base fluid.
2.4. Esterification process for biodiesel production
Woody biomasses is one of the second-generation biofuel production having cellulose of about 41%, lignin of 27%, hemicellulose of 28%, and also 4% of extraneous organic compounds (Kumari & Singh, Citation2018). They are used in producing biodiesel to reduce the rivalry caused through the use of edible feedstock. The disadvantage of this second-generation program of biofuel production is the cost of production, due to several steps of treatments (degumming through esterification) mechanism needed for final usable products (Syahirah et al., Citation2020). The miscibility we discover when glycerol and methyl ester ought to have separated is as a result of what we call gumming. Degumming could be hydra-table or non-hydra-table. 0.2 wt.% of phosphoric acid, water and caustic acid heated at 80°C are substances used in degumming. A two-step method of purification to reduce biodiesel synthesis of high FFA having more than 2% was proposed. Firstly, acid esterification was done using 30 ml of oil with a specific amount of methanol and sulphuric acid and stirring at 900 rpm. Secondly, the application of base-catalyzed esterification at the optimum condition of 6.58 to 1 of methanol to oil molar ratio, respectively. 2 wt.% of catalyst and 2 h reaction time as led to 1.5% reduction from the initial value (Madhu et al., Citation2019). The alcohols mostly used include methanol and ethanol. Moreover, propanol, butanol, and octanol were also opined to be useful to produce biodiesel (Kumar et al., Citation2018).
Trans-esterification is a process used in the lowering oil molecular weight, viscosity by a factor of eight, and FFA to less than 2% by the reaction between 1 mole of triglyceride and alcohol, producing 1 mole of glycerol and 3 moles straight-chain molecules of methyl (butyl, 2-propyl and ethyl) ester in the presence of a catalyst (acid, base or enzyme) (Rodionova et al., Citation2016). The trans-esterification process was first performed in South Africa in producing biodiesel. This was used in heavy vehicle engines in 1853 before world war 11 (Chakrabarti & Prasad, Citation2012). The esterification without catalyst requires a high temperature of about 250–400°C with supercritical methanol (SCM) (Demirbas, Citation2007). The type of catalyst used is dependent on the free fatty acid present in the oil. This could be either homogenous or heterogeneous (J. Zhang et al., Citation2019). A free fatty acid is the most important determinant factor in feedstock selection for biodiesel. A homogenous base catalyst such as sodium or potassium hydroxide, carbonates, potassium alkoxides, and sodium methoxides requires a lot of water washing (Hossain et al., Citation2014). They absorb water during storage; that is, they are hygroscopic. The use of KOH as a catalyst becomes needful in the presence of free fatty acid lower than 3%. Degumming and more catalysts are added in the case of the high value of FFA (Shirazi, Citation2020). Ordinary vegetable oil contains high free fatty acid. Hence, it is unsuitable for either based fluid, bio-lubricants, or as diesel engine because of high viscosity and low cetane value, which may result in the formation of trumpet and coking (S. Kumar et al., Citation2012).Therefore, for vegetable oil with high amount of FFA, acid catalysts are recommended. The acids include para-toluene sulfonic acid, Lewis acid ( or
), hydrochloric acid, ferric sulfate acid or sulphur acid. The time required in this case will be more than the time required in the use of the base catalyst. However, acid catalysts are not as common as the base catalyst because the base catalyst is cheap and faster in its reaction rate but both require the use of water to neutralize the acid and base content that did not react in the remaining salt of the neutralization process (Kumar et al., Citation2018). If there are still traces of alcohol left in the ester, it can be removed by distillation (Oghenejoboh et al., Citation2013). Disposal of water-washing used in this process generates more waste to the environment, thereby causing pollution. Also, long hours of reaction and the removal of glycerol are pure demerits for this process (Shirazi, Citation2020). That is why, the use of supercritical fluid methods with its ability to react in a few numbers of minutes (2–4 min) in the absence of either base or acid catalyst has been proposed (Jain et al., Citation2011). The only demerits recorded here include the procurement of equipment of high temperatures and pressure and a high amount of methanol to oil molar ratio (40:1) needed. The production of some catalysts such as
,
,
hydroxyapatite-encapsulated,
nano-particles,
,
,
and
have been found to be an herculean task (Jin-jiang et al., Citation2010). Thus, the use of biomass-based heterogeneous catalyst sources has been proposed. The biomass include waste shell, animal bones, biomass ashes, waste coal, activated carbon-supported catalyst, mollusk shells, duck egg shells, calcine fish scale, sheep bone, aluminum oxide, zinc oxide, palm shell activated carbon, waste egg shell, fresh snail shell (Pila species, ampullariidae family), oyster shell, crab shell, and chicken manure, river mussels. to mention a few as the source of calcium oxide for bio-catalytic esterification process (Nisar et al., Citation2017; Singh & Verma, Citation2019a, Citation2019b, Citation2019c). Also, we have Brassica nigra plant, banana peel, calcined banana, and peduncle ash (Falowo et al., Citation2020). An heterogeneous catalyst could be acidic, basic, or enzymatic. It is easily reused and nontoxic. It has flexible separation technique, and it is said to be thermally stable. It is not corrosive and environmentally friendly unlike homogenous catalyst (Laskar et al., Citation2018). The acidic heterogeneous catalyst requires a high temperature, long mixing period, and high methanol to oil ratio. The use of enzymatic catalyst has been said to be efficient too. The problems of waste production leading to a generation of rodents and fleas causing environmental problems are removed. It requires just little energy and its use is recyclable (Sadef et al., Citation2016). Therefore. the production of catalysts from waste could be effective in the production of biodiesel. Falowo et al. (Citation2020) prepared a calcined sample from cocoa pod husk, plantain peel, and kola nut pod husk called CPK at 500°C for 4 hours. CPK (with the chemical properties of 47.67% potassium, 5.56% calcium, and 4.21% magnesium) was used as a catalyst on an oil sample blend containing honne, rubber, and neem oil at the ratio of 20:20:60, respectively. 98.45 wt.% of biodiesel was recovered from the esterification mixing of 12:1 of methanol to oil, CPK of 1.158 wt.%, and 6 min reaction time. In the same vein, an heterogeneous solid alkali catalyst was formed using animal waste modified with potassium hydroxide. It was used in the trans-esterification process for Jatropha oil to jatropha methyl esters with methanol to oil molar ratio of 9 to1, 6.0 wt.% of catalyst, 3 hours reaction time, and calcination temp of 900°C to produce biodiesel yield of 96.1% (Nisar et al., Citation2017). J. Zhang et al. (Citation2019) used calcined Brij35 made at 350°C and soaked in 50 wt.% KOH to produce a base catalyst for the production of 92.9% yielded microalgae biodiesel. This was done using,14 wt.% of base catalyst, 60°C reaction temperature, 6 ml/g of methanol, and 8 h mixing time. Singh & Verma (Citation2019c) synthesized calcium oxide from river mussels at 800°C in 1 hr. He used it to produce a biodiesel from waste cooking with the yield of 91.04% shows biodiesel yield from different bio-catalyst trans-esterification mixture. The parameters of great importance during esterification that influence the yield in percentage include the molar ratio of methanol to oil, the temperature of reaction factors, catalyst, reaction time, and speed of rotation.
Table 6. Biodiesel yield from different bio-catalyst transesterification mixture
The biodiesel conversion model is stated in EquationEquation (12)(12)
(12) . Biodiesel conversion formulae (Wang et al., Citation2008):
where C is the triglyceride to biodiesel (fatty acid methyl ester), is the integration value of the methyl esters, and
is the integration value of the methylene protons. 2 is the proton number in the methylene, while 3 is the proton number in the methyl ester.
2.5. Biodiesel for internal combustion (CI) engine
The first compression ignition engine using biodiesel was first brought to light far back in the 19th century by Dr. Rudolf Christian Karl Diesel with the use of peanut (Lujaji et al., Citation2010). It was exhibited in Paris but less attention was given to it due to the bearable price of diesel fuel (Hossein et al., Citation2019; Senthilkumar et al., Citation2018). However, from the initial energy scarcity in the 1970s and oil shock in 2008, the interest of people has been shifted to its production. Viscosity, cleanliness, sulphur content, volatility, ignition quality, and cold flow properties were the properties to be considered when selecting a good diesel. Cloud point, pour point, and cold filter plugging point (CFPP) are referred to as cold flow properties. Diesel has an aliphatic compound with carbon presence from 8 to 28 per molecule, while biomass such as jatropha oil has about 16 to 18 carbon atoms/molecule (Islam et al., Citation2011). Diesel’s particulate emission include ash, sulphate/water, carbon, unburned fuel and unburned HC in 14, 13, 41, 7, and 25% quantity, respectively (Agarwal et al., Citation2015). Diesel is a widely used engine fuel sequel to its reliability, cost-effectiveness, high efficiency among others. However, at a colder temperature, the solubility of this fuel decreases. At higher cold temperatures, it forms wax and extends into the filter orifice causing a blockage (Subhaschandra et al., Citation2021). The pour point can be improved upon to prevent this undesired occurrence at lower temperatures. Therefore, the production of biodiesel has less particulate emission due to the high content of elemental carbon and lower presence of organic compound, which can work at low temperatures (as low as—40°C) and would not lose its stability (Oseh et al., Citation2019).
Some oils have been used in blending capacity with diesel oil for application in compression ignition engines because of their comparable properties. Such oil includes Pongamia/neem blend oil, cooking oil/hone oils, Pongamia/jatropha/hone, soybean/rapeseed, rubber/neem oil, castor seed/waste fish oil (Das et al., Citation2018; Rajasekar & Selvi, Citation2014; H. Singh et al., Citation2021). shows the properties of biodiesel compared to diesel. Prasad et al. (Citation2019) studied a dual biodiesel blend with diesel fuel in 90:5:5 of diesel, Pongamia, and mustard oil, respectively. The applied temperature of 800°C for 10 hours in extreme stirring was done and the oil is allowed to settle for 12 hours. This is to ensure that the glycerin is separated and decanted from the product. Water is added to help neutralize the residual catalyst present in the oil. It also helps remove the glycerin that may eventually lead to soap formation. Then, the oil is heated to over 100°C to remove the residual water and the alcohol. Such blend oils have been used in tractors that use direct-injection diesel (Nedayali & Shirneshan, Citation2016). Polymeric depressants and other fuel additives like ethanol have been suggested to help the condition of diesel as stated by Hossein et al. (Nedayali & Shirneshan, Citation2016). He further stated that, 20 vol.% or more of Toluene-diesel blend has caused the most significant reduction in the cloud point. With the addition of 20% ethanol, the fuel pour point was significantly reduced in the experiment conducted in the laboratory. Biodiesel was recorded by Madhu et al. (Citation2019) to be almost non-toxic and sulphur-free, less; particulate matter and unburned hydrocarbon, ecologically friendly, high viscosity and less volatile, which causes deposits in the engine due to incomplete combustion (Chakrabarti & Prasad, Citation2012). It equally has lower emissions of carbon dioxide, carbon mono-oxide and NOx (Gonca & Dobrucali, Citation2016). There had been lower emissions of Nitrogen oxide over the total life cycle (Abed et al., Citation2019). However, Tüccar et al. (Citation2018) hold the opinion that the amount of NOx has not been reduced despite biodiesel usage. Hasan & Rahman (Citation2017) also hold the same opinion. This is based on the usage of crops that were grown with nitrogen fertilizer. More so, the production of biodiesel from agricultural produce such as rapeseed and bioethanol production from corn, maize, and so on are said to increase the emission of NOx in the atmosphere. Rajasekar & Selvi (Citation2014) hold the same view. Therefore, less nitrogen biomasses may impact more effectively on global warming reduction. Prasad et al. (Citation2019) discussed the mineral diesel and biodiesel blends of Pongamia and cottonseed oil at the ratio of 10%, 20%, and 30%. The thermal brake efficiency (BTE) of the biodiesel blend of 10, 20, and 30% were higher than mineral diesel, while the specific fuel consumption of the brake (BSFC) for biodiesel blends were lower than diesel. In another literature, it was stated that biodiesel leads to higher fuel consumption, engine power drop, and torque compared to diesel fuel. Nedayali & Shirneshan (Citation2016) opined that there is an increase in fuel consumption when castor oil blend was used than soybean oil blend at the same specific concentration. Overall, the B10 blend was said to have the best BTE and BSFC than the other blends because of less oxygen presence. This could have been as a result of oxidation in the other blends with a large amount of biodiesel concentration. He equally used biodiesel produced from waste cooking oil blended with diesel at a different ratio such as B10, B20, B50 B80, and B100, and the functionality of this blend was checked on diesel power generator for brake power, brake torque, brake supply fuel consumption, and brake thermal efficiency. The engine power rating of 1530 r/min and engine loads of 25, 50, 75, and 100% were varied. The blends of B20 and B50 have the best performance characteristic for usage in the diesel generator showing an increase in brake torque, power, and thermal efficiency with brake-specific fuel consumption decreasing as the engine load increases. Kumar et al. (Citation2018) are of the opinion that biodiesel is used in small or large proportion in diesel fuel to increase its efficiency and better its characteristic performance. The Jatropha blend of up to 25% in diesel fuel has been postulated best for diesel engines in terms of brake-specific fuel consumption and emissions (Tüccar et al., Citation2018). This is been considered better than 100% diesel in an unmodified CI engine. Though Jatropha biodiesel from seeds is used without any blend during world war 11 (S. Kumar et al., Citation2012). Sani et al. (Citation2018) established the fact that B10 is the best blend for BSFC, BTE checked parameters on CI engine when oil from watermelon seed (Citrullus lanatus) was used to generate biodiesel (Stöcker, Citation2008). Also, Gonca & Dobrucali (Citation2016) checked the effect of engine load and the percentage of biodiesel on the biodiesel blend-fueled engine. At constant biodiesel percentage and increase in engine load, effective power increases constantly, while efficient value goes up to a particular value and starts decreasing. However, when there is a constant increase in the biodiesel percentage at constant engine load and compression ratio, effective efficiency increases but the effective power increase to a level and starts decreasing. B20 is said to have good CI engine properties in terms of BSFC, BTE and best emission of particulate materials (Agarwal et al., Citation2015; Krishania et al., Citation2020; Shrivastava et al., Citation2019; Singh & Verma, Citation2019b). However, 30% biodiesel has the same properties as diesel in terms of calorific value, density, viscosity properties (Hasan & Rahman, Citation2017). Singh et al. (Subhaschandra et al., Citation2021) blended microalgae spirulina (L) biodiesel with diesel at different concentrations and checked the effect of varying engine loads and compression ratio on BSFC, BTE and emissions of the CI engine. It was discovered that B20 gave the best blend of high BTE, less BSFC and minimal emissions at an optimum condition of −63.63% load and 16.5 compression ratio. Krishania et al. (Citation2020) opined that B20 blended fuel from first generation to third generation has reduction in exhaust gas temperature, BTE and ignition delay. The first generation feedstocks used include soybean, palm, coconut and rapeseed; the second generation includes Karanja, cottonseed, jatropha curcas and jojoba while the third generation feedstocks include fish oil, waste cooking oil, spirulina and animal fats. S. Adegoke et al. (Citation2020) opined that the blend of Jatropha curcas seed oil and polypropylene plastic at 3:2 could stand very close as an alternative to diesel fuel. It was further shown that the physicochemical properties such as viscosity, density and so on were similar to the diesel fuel type used in the study. On a general note, biodiesel can supply electricity by using it in the place of diesel oil for CI engines.
Table 7. Properties of various biodiesels compared with diesel oil
3. Key properties in biodiesel for CI engine
For biodiesel use in the CI engine, the amount of ester constituent in the biodiesel must be a minimum of 96.5%. Anything lower than this may mean the tri-glycerides, catalyst, and the used methanol is still in the fuel, which could cause plugging and engine deposits. The overall quality of biodiesel is dependent on the component structure of fatty acid esters present in the biodiesel (Hu et al., Citation2008). Methanol is part of the solvent used in the production of biodiesel because of its possible reactivity nature. However, its excessive presence in the oil could lead to corrosion in the injectors and quick degradation of materials, less lubricity, and reduction in the flashpoint (Charter, Citation2009). Also, the oxidation of biodiesel leads to the production of hydrogen peroxide, which leads to more acid formation. The formation of hydrogen peroxide could disappear during re-esterification, however, the polymer that is formed does not disappear but they form gum leading to plugging of filter and engine failure. The presence of acid in fuel can cause corrosion to the metal parts. The presence of glycerin, mono, triglycerides could also affect the fuel by falling to the bottom of the tank and causing plugging and attracting polar agents such as water. It, then, leads to the formation of soap, which could damage the injectors, causing injector coking, and deposits at the engine seat. The density of biodiesel is usually higher than petroleum fuel diesel. The presence of foreign materials introduced into the biodiesel could contaminate and lead to an increase in the density of the biodiesel. The CI engine measures the rate of fuel entrance into the combustion chamber by volume. Hence, an increase in density will mean an increase in emission and less fuel consumption, while low density will cause an increase in fuel consumption (Khan et al., Citation2016).
Viscosity is a property of fuel with an enormous effect on the injector lubrication and atomization of fuel. The range of values for vegetable oil viscosity is 27.2–53.6 mm2/s. However, biodiesel is 3.59 to 4.63 mm2/s (Demirbas, Citation2007). A higher fuel viscosity can lead to increased exhaust smoke, high fuel consumption, poor combustion, increase in emissions, and less lubricity but less fuel leakages. At temperatures as low as −20°C, the minimum allowable viscosity is 2.0–5.0 mm2/s, while the viscosity at this temperature should not be above 48 mm2/s to prevent danger on the fuel injector pump (Durak, Citation2019). Tesfa et al. (Citation2010) in his study “Prediction models for density and viscosity of biodiesel and their effects on fuel supply system in CI engines” showed that high viscosity and high density could cause fuel pump malfunctioning and leakages, respectively. An increase in density may mean an increase in viscosity. Tüccar et al. (Citation2018) monitored the effects of the density and viscosity on the following biodiesel such as sunflower, canola, and corn oils when used in a four-stroke diesel engine. With the increase in biodiesel proportion, the viscosity and density were also going up. Therefore, the emission of CO was seen to reduce at high viscosity and density; however, CO2 and NOx emissions increased with an increase in viscosity and density. The higher the free fatty acid present, the more problems encountered in improving the quality of the oil; saponification and less yield in ester percentage occurs. Saponification value (SV) is obtainable using EquationEquation (13)(13)
(13) (Nawaz et al., Citation2018).
where B and S are the HCl of blank and sample values, respectively, while W and N are the weights of biodiesel and normality of HCl, respectively.
Calorific value is the amount of energy releases per unit quantity of fuel under standard conditions. The liquid with a high heating value and the gas with a high calorific value can be used as fuel in a gas turbine or as a transportation fuel and pyrolysis plants, respectively, because heat needed for conversion of biomass determines the energy efficiency (Syahirah et al., Citation2020). Biodiesel volumetric heat capacity is lower than diesel (Pittman et al., Citation2011).
The biomass calculation of high heating value is thus given in EquationEquation (14)(14)
(14) (Jahirul et al., Citation2012):
where C, H, O and N are carbon, hydrogen, oxygen and nitrogen contents, respectively.
Some biodiesel sourced from saturated vegetable oil/algae could produce biodiesel of high pour point which reduces its effectiveness in the cold seasonal period. However, such oil has good oxidative stability (Hu et al., Citation2008). If the oil contains high saturated acids, the final process of biodiesel will have high pour points, which will congeal at low temperatures. However, the presence of polyunsaturated molecules with double or triple bond will act as a stabilizer to the fuel (Abdullah et al., Citation2013). At high unsaturated acid, more of the problem-related to oxidative instability will surface but with good cold flow characteristics (Radakovits et al., Citation2010)
Flashpoint is the minimum temperature at which a fuel will cause a fire under a specified condition. The flashpoint of 100°C minimum will be good for transportation and storage (Chyuan & Silitonga, Citation2020). The measurement of a flashpoint in biodiesel helps to show the amount of methanol presence. The measure of fuel ignition and combustion quality is called cetane number with a minimum value of 51 (Tüccar et al., Citation2018). Fuel cetane number lower than 51 will give a hard start, noise, and an increase in smoke. The more the cetane value the higher the tendency of self-ignition. The use of cetane additive to improve the cetane number of biodiesel or the addition of diesel to biodiesel is advised (Das et al., Citation2018). Cetane number of biodiesel from jatropha and its corresponding seed oil yield is said to be high when compared with other oil from other seeds biodiesel, such as rapeseed, cottonseed, and so on (Abdullah et al., Citation2013). Iodine value and cetane number calculations are obtained using EquationEquations (15)(15)
(15) and (Equation16
(16)
(16) ), respectively (Nawaz et al., Citation2018).
where B is volume for blank while S is volume for sample S of 0.1 N Na2S2O3.5H2O.
where IV and SV are iodine and saponification value.
Water presence must not be visible in the biodiesel oil; a maximum of 500 mg/kg is advised. The presence of more than the recommended can lead to damage of plug fuel filter and lead to engine fuel starvation. Ash is the measure of inorganic contaminants and metal in the fuel. Its content in the fuel must be 0.001 maximum. Its presence in unacceptable quantity may lead to filter plugging. Carbon residue gives the tendency for accumulations at the injectors or in the combustion chamber. It must be kept at 0.05 maximum. Sulphur must be kept at 10 ppm maximum (Charter, Citation2009). Biodiesel is hygroscopic. It becomes unstable from the day it is produced causing polymerization of engine sump oil. It requires often changing of oil (Pittman et al., Citation2011). The presence of oxygen (10–11%) in the chemical formula of biodiesel will mean better combustion with less emission of and NO (Chyuan & Silitonga, Citation2020). Oxidation reaction occurs due to temperature changes and its visibility to oxygen and water presence in the air. However, anti-oxidant can be added in a specified quantity to increase its quality and effectiveness and prevention of sludge. The use of bio-oil directly on CI engine may cause fuel pump malfunctioning, piston ring malfunctioning, engine wear, poor separation into fine particles, difficulty in starting the engine, wax and gum formation, filter and injector coking, more CO emission due to acid, and moisture presence (Agarwal et al., Citation2015). Therefore, bio-oil production for transportation has not been in effect. More research on the effective char separation to retard bio-oil pollution is needed.
4. ASTM methods and oil acidity
pH is the measure of oil acidity, which includes corrosion without giving the percentage of acid presence. TAN method is used in measuring petroleum oil acidity. However, North America has used TAN for measuring fast pyrolysis oil in recent times. Oasmaa et al. (Citation2010) stated that TAN has been changed to AN (acid number) because the method used is not a measure of the total acid concentration of the oil consisting of both strong and weak acid. The acid number helps in measuring the amount of acid present in the fuel. It is the amount of KOH in mg that can neutralize a gram of oil. AN is considered better in measuring bio-oil because it does not take into consideration every weak acid with a dissociation number of less than 10–9. The presence of these weak acids in the oil is inconsequential and could not affect the oil in terms of corrosion (Oasmaa et al., Citation2010). The TAN methods include ASTM D664, D974, D1534, D3339, in which ASTM D664 and D974 are very common (Wang et al., Citation2008). They make use of potentiometric titration method, which involve the use of potentiometer for acid detection and conversion to electronic output. ASTM D974, 1534 and 3339 all use a colorimetric method, in which p-naphtholbenzein helps to show the effect of the pH indicator change added to the solution once the alkali solution has caused the change in colour by acid neutralization (Oasmaa et al., Citation2010). The ASTM D3339 has been more advantageous than D974 in calculating the acid number for bio-oil. The pH from biomass origin is from 2 to 3. ASTM D664 or D3339 has been selected as the TAN method for measuring the acidity of bio-oil and their hydro-treating products. ASTM D664 has been useful to measure higher values of TAN of bio-oil than the other mentioned (D3339) (Wang et al., Citation2008). ASTM D2500 helps to measure lower cloud points of liquid below 49°C. The conclusion on calculating the TAN of bio oil is by derivation which is 60–70% from volatile acids, such as hydroxyl, fatty, resin and phenolic acid (Oasmaa et al., Citation2010). shows the different testing methods for biodiesel oil.
Table 8. Different testing methods for biodiesels
The thermal degradation of hemicellulose is considered as the parameter that is responsible for acids such as acetic and formic acid considered as strong acid having lower pKa values, and carboxylic considered as weak acid in the bio-oil. This is responsible for oil instability and its high acidity (Jin-jiang et al., Citation2010). This oil consists of 3–6 wt.% of the volatile acids. Alcohols are neither acidic nor basic. They form alkoxides in an aqueous solution, however, they form oxonium ion when combined with strong acid. TAN method applied to bio-oil products has not been well established (Hossein et al., Citation2019).
5. Conclusion and recommendation
There is a global 95% dependency on petroleum base oil. Fossil fuel resources are depleting at a fast rate. There is an extended negative effect on the environment, and climate degradation. Hence, the production of biofuel from a clean renewable source is important as it will help increase capable internal jobs, increase rural growth and development. The present paper presented recycling of biomass and plastics for energy generation. It was gathered that biomass constitute 46–50% of global renewable energy consumption. It was also concluded that 15% of the world plastics are available for recycling purposes. Biomass and plastics can be effective for solid, liquid and gaseous fuel. Pyrolysis, liquefaction, gasification and combustion are part of the viable routes for biomass and plastic recycling for energy generation. To ensure a sustainable biofuel production, there is a need to ensure the availability of land for biofuel production without being vulnerable to the issues mentioned in this study, such as hunger, deforestation, soil erosion, destruction of biodiversity, and food scarcity. More production of biofuel using nonfood products should be encouraged and the use of abandoned/marginal lands for biofuel production may also be considered. Microalgae possess metabolic features such as a high survival rate in the different ecosystems and a wide variety of species, which are all good for biofuel generation. This pathway will be the greatest breakthrough in energy sustenance with no competition with food. Moreover, for an integrated waste management program in a country, there is a need for governmental financial support for good disposal of waste, a better policy framework, and information on waste composition. Source segregation collection of waste is an integral part of improving recycling, reuse, and recovery in the act of waste management. The recycling of plastic solid waste involving treatment and recovery process has added to the image of the environment and waste management. The process of re-using these plastic wastes in the environment has become the major research work of industries and researchers
Finally, there is a need for synergy among disciplines such as petroleum engineers, mechanical engineers, chemists, biologists, biochemists, and many others in this regard to see to the view in diverse ways biofuel production can be made cost-effective.
Nomenclature
Acknowledgements
This work is funded under the PTDF scholarship scheme (LSS- PTDF/ED/LSS/PHD/SAO/156/17), therefore, the authors wish to thank Petroleum Technology Development Fund for supporting this work financially.
Disclosure statement
No potential conflict of interest was reported by the author(s).
Additional information
Funding
Notes on contributors

Samuel Oluwafikayo Adegoke
Samuel Oluwafikayo Adegoke is a research assistant in the University of Ibadan, Nigeria. His areas of specialization include bio-inhibition, scale oilfield mitigation, and pyrolysis.
Adekunle Akanni Adeleke
Adekunle Akanni Adeleke is a Registered Engineer. He has been working on direct reduced iron technologies and iron and steel development, and bioenergy
Peter Pelumi Ikubanni
Peter Pelumi Ikubanni is a Registered Engineer. His research interests include design and development of machines, renewable energy and energy studies.
Chiebuka Timothy Nnodim
Chiebuka Timothy Nnodim is a lecturer in Landmark University, Nigeria. His research interests include industrial production and mechatronics engineering, and energy studies.
Ayokunle Olubusayo Balogun
Ayokunle Olubusayo Balogun is a lecturer in Landmark University, Nigeria. His research interests include heat and mass transfer, biomass studies, and renewable energy.
Olugbenga Adebanjo Falode
Olugbenga Adebanjo Falode is a Professor in the University of Ibadan, Nigeria. He is currently the head of department. His area of specialization include, wet chemistry, bio-inhibition, and flow assurance.
Seun Olawumi Adetona
Seun Olawumi Adetona is a lecturer in petroleum Training institute, Nigeria. His areas of interest include formulation of mud from local materials, biofuel production, and bio-oil synthesis.
References
- Abdullah, B. M., Yusop, R. M., Salimon, J., Yousif, E., & Salih, N. (2013). Physical and chemical properties analysis of Jatropha curcas seed oil for industrial applications. World Academy of Science, Engineering and Technology, 7(12), 531–45.
- Abed, K. A., Gad, M. S., El Morsi, A. K., Sayed, M. M., & Elyazeed, S. A. (2019). Effect of biodiesel fuels on diesel engine emissions. Egyptian Journal of Petroleum, 28(2), 183–188. https://doi.org/10.1016/j.ejpe.2019.03.001
- Adegoke, S., Falode, O., Adeleke, A., Ikubani, P., & Agboola, O. (2020). Production of an alternative fuel from a blend of polypropylene wastes and Jatropha distillates for oil well drilling. Aims Energy, 8(6), 1127–1142. https://doi.org/10.3934/energy.2020.6.1127
- Adegoke, S. O., Adeleke, A. A., Ikubanni, P. P., Falode, A. O., & Alawode, A. J. (2021). Design and fabrication of an ablative pyrolyzer for production of bio- lubricants and chemicals in oil well drilling application. 665(012007), 1–7. https://doi.org/10.1088/1755-1315/665/1/012007
- Adekunle, A. S., Adeleke, A. A., Obu, C. V., Ikubanni, P. P., Ibitoye, S. E., & Azeez, T. M. (2020). Recycling of plastics with compatibilizer as raw materials for the production of automobile bumper. Cogent, 7(1). https://doi.org/10.1080/23311916.2020.1801247
- Adeleke, A., Lasode, O. A., Odusote, J., Malathi, M., Ikubanni, P., & Paswan, D. (2020). Essential basics on biomass torrefaction, densification and utilization. International Journal of Energy Research, 45(2), 1375–1395. https://doi.org/10.1002/er.5884
- Adeleke, A. A., Odusote, J. K., Ikubanni, P. P., Agboola, O. O., Balogun, A. O., & Lasode, O. A. (2021). Tumbling strength and reactivity characteristics of hybrid fuel briquette of coal and biomass wastes blends. Alexandria Engineering Journal, 60(5), 4619–4625. https://doi.org/10.1016/j.aej.2021.03.069
- Adeleke, A. A., Odusote, J. K., Ikubanni, P. P., Lasode, O. A., Malathi, M., & Paswan, D. (2020). Heliyon the ignitability, fuel ratio and ash fusion temperatures of torre fi ed woody biomass. Heliyon, 6(3), e03582. https://doi.org/10.1016/j.heliyon.2020.e03582
- Adeleke, A. A., Odusote, J. K., Lasode, O. A., Ikubanni, P. P., Madhurai, M., & Paswan, D. (2019). Evaluation of thermal decomposition characteristics and kinetic parameters of melina wood. Biofuels, 1–7. https://doi.org/10.1080/17597269.2019.1646541
- Agarwal, A. K., Gupta, T., Shukla, P. C., & Dhar, A. (2015). Particulate emissions from biodiesel fuelled CI engines. Energy Conversion and Management, 94, 311–330. https://doi.org/10.1016/j.enconman.2014.12.094
- Ajimotokan, H. A., Ehindero, A. O., Ajao, K. S., Adeleke, A. A., Ikubanni, P. P., & Shuaib-Babata, Y. L. (2019). Combustion characteristics of fuel briquettes made from charcoal particles and sawdust agglomerates. Scientific African, 6, e00202. https://doi.org/10.1016/j.sciaf.2019.e00202
- Al Arni, S. (2017). Comparison of slow and fast pyrolysis for converting biomass into fuel. Renewable Energy, 124, 197–201. https://doi.org/10.1016/j.renene.2017.04.060
- Annisa, A. N., & Widayat, W. (2018). A review of bio-lubricant production from vegetable oils using esterification transesterification process. 24th Regional Symposium on Chemical Engineering, 156(06007), 1–7. https://doi.org/10.1051/matecconf/201815606007
- Awalludin, M. F., Sulaiman, O., Hashim, R., & Aidawati, W. N. (2015). An overview of the oil palm industry in Malaysia and its waste utilization through thermochemical conversion, speci fi cally via liquefaction. Renewable and Sustainable Energy Reviews, 50, 1469–1484. https://doi.org/10.1016/j.rser.2015.05.085
- Babatunde, B. B., Sikoki, F. D., Avwiri, G. O., & Chad-umoreh, Y. E. (2018). Review of the status of radioactivity profile in the oil and gas producing areas of the Niger delta region of Nigeria. Journal of Environmental Radioactivity, 202(2), 66–73. https://doi.org/10.1016/j.jenvrad.2019.01.015
- Babayemi, J. O., Nnorom, I. C., Osibanjo, O., & Weber, R. (2019). Ensuring sustainability in plastics use in Africa: Consumption, waste generation, and projections. Environmental Sciences Europe, 31(1), 1–20. https://doi.org/10.1186/s12302-019-0254-5
- Babu, V., Murthy, M. K., & Prasad Rao, A. (2017). Butanol and pentanol: The promising biofuels for CI engines – A review. Renewable and Sustainable Energy Reviews, 78, 1068–1088. https://doi.org/10.1016/j.rser.2017.05.038
- Baeyens, J., & Baeyens, J. (2009). Recycling and recovery routes of plastic solid waste (PSW): A review. Waste Management, 29(10), 2625–2643. https://doi.org/10.1016/j.wasman.2009.06.004
- Bakar, M., & Titiloye, J. O. (2013). Catalytic pyrolysis of rice husk for bio-oil production. Journal of Analytical and Applied Pyrolysis, 103, 362–368. https://doi.org/10.1016/j.jaap.2012.09.005
- Balogun, A. O., Adeleke, A. A., Ikubanni, P. P., Adegoke, S. O., Alayat, A. M., & Mcdonald, A. G. (2021). Case studies in thermal engineering physico-chemical characterization, thermal decomposition and kinetic modeling of Digitaria sanguinalis under nitrogen and air environments. Case Studies in Thermal Engineering, 26, 101138. https://doi.org/10.1016/j.csite.2021.101138
- Balogun, B., & Salami, A. T. (2016). Effects of biofuel production on selected local communities in Nigeria. Journal of Petroleum Technology and Alternative Fuels, 7(3), 18–30. https://doi.org/10.5897/JPTAF2015.0123
- Cai, X., Zhang, X., & Wang, D. (2011). Land availability for biofuel production. Environmental Science & Technology, 45(1), 334–339. https://doi.org/10.1021/es103338e
- Capocelli, M. (2007). Plastic to fuel technologies, researcher (pp. 1–11). University UCBM-Rome.
- Chakrabarti, P. P., & Prasad, R. B. N. (2012). Biodiesel production from Jatropha curcas oil, farming economics and biofuel. 1, 463–490. https://doi.org/10.1007/978-1-4614-4806-8-25
- Chandra, R., Takeuchi, H., & Hasegawa, T. (2012). Methane production from lignocellulosic agricultural crop wastes: A review in context to second generation of biofuel production. Renewable and Sustainable Energy Reviews, 16(3), 1462–1476. https://doi.org/10.1016/j.rser.2011.11.035
- Charter, W. F. (2009, March). biodisel GUIDELINES. Worldwide fuel charter committee.
- Chen, F., & Dixon, R. A. (2007). Lignin modification improves fermentable sugar yields for biofuel production. Nature Biotechnology, 25(7), 759–761. https://doi.org/10.1038/nbt1316
- Choudhary, P., Assemany, P. P., Naaz, F., Bhattacharya, A., Castro, J., Couto, E., Calijuri, M. L., Pant, K. K., & Malik, A. (2020). A review of biochemical and thermochemical energy conversion routes of wastewater grown algal biomass. Science of the Total Environment, 726, 137961. https://doi.org/10.1016/j.scitotenv.2020.137961
- Chyuan, H., & Silitonga, A. S. (2020). Patent landscape review on biodiesel production: Technology updates. Renewable and Sustainable Energy Reviews, 118, 1–9. https://doi.org/10.1016/j.rser.2019.109526
- Crutzen, P. J., Mosier, A. R., Smith, K. A., Winiwarter, W., Jolla, L., & Pleasant, M. (2008). N2O release from agro-biofuel production negates global warming reduction by replacing fossil fuels. Atmospheric Chemistry and Physics, 8(2), 389–395. https://doi.org/10.5194/acp-8-389-2008
- Das, M., Sarkar, M., Datta, A., & Santra, A. K. (2018). Study on viscosity and surface tension properties of biodiesel-diesel blends and their e ff ects on spray parameters for CI engines. Fuel, 220, 769–779. https://doi.org/10.1016/j.fuel.2018.02.021
- Das, P., & Ganesh, A. (2003). Bio-oil from pyrolysis of cashew nut shell — A near fuel. Biomass & Bioenergy, 25(1), 113–117. https://doi.org/10.1016/S0961-9534(02)00182-4
- Demirbas, A. (2007). Progress and recent trends in biofuels. Progress in Energy and Combustion Science, 33, 1–18.
- Di Maria, F., & Micale, C. (2013). Impact of source segregation intensity of solid waste on fuel consumption and collection costs. Waste Management, 33(11), 2170–2176. https://doi.org/10.1016/j.wasman.2013.06.023
- Drewer, J., Howard, D., & Mcnamara, N. (2018). Volatile organic compound (bVOC) fluxes associated with land-use change to bioenergy crops. Chapter 6. Greenhouse gas Balances of Bioenergy System Elsevier Inc. https://doi.org/10.1016/B978-0-08-101036-5.00006-977
- Durak, H. (2019). Characterization of products obtained from hydrothermal liquefaction of biomass (Anchusa azurea) compared to other thermochemical conversion methods. Biomass Conversion and Biorefinery, 9(2), 459–470. https://doi.org/10.1007/s13399-019-00379-4
- Egorov, R. I., & Strizhak, P. A. (2017). The light-induced gasification of waste-derived fuel. Fuel, 197, 28–30. https://doi.org/10.1016/j.fuel.2017.01.118
- Elum, Z. A., Mopipi, K., & Henri-Ukoha, A. (2016). Oil exploitation and its socioeconomic effects on the Niger Delta region of Nigeria. Environmental Science and Pollution Research, 23(13), 12880–12889. https://doi.org/10.1007/s11356-016-6864-1
- Falowo, O. A., V. ojumu, T., Ojumu, T. V., & Betiku, E. (2020). Sustainable biodiesel synthesis from honne-rubber-neem oil blend with a novel mesoporous base catalyst synthesized from a mixture of three agrowastes sorting/drying burning ash Ca …. Catalysts, 10(2), 190. https://doi.org/10.3390/catal10020190
- Galadima, A., Garba, Z. N., Ibrahim, M. B., & Luter, L. (2011). Biofuels production in Nigeria: The policy and public opinions biofuels production in Nigeria: The policy and public opinions. Journal of Sustainable Development, 4(4), 22–31. https://doi.org/10.5539/jsd.v4n4p22
- Gonca, G., & Dobrucali, E. (2016). Theoretical and experimental study on the performance of a diesel engine fueled with diesel e biodiesel blends. Renewable Energy, 93, 658–666. https://doi.org/10.1016/j.renene.2016.03.037
- Gu, F., Guo, J., Zhang, W., Summers, P. A., & Hall, P. (2017). From waste plastics to industrial raw materials: A life cycle assessment of mechanical plastic recycling practice based on a real-world case study. Science of the Total Environment, 601-602, 1192–1207. https://doi.org/10.1016/j.scitotenv.2017.05.278
- Hasan, M., & Rahman, M. (2017). Performance and emission characteristics of biodiesel – Diesel blend and environmental and economic impacts of biodiesel production: A review. Renewable and Sustainable Energy Reviews, 74, 938–948. https://doi.org/10.1016/j.rser.2017.03.045
- Hossain, A., Hasan, R., & Islam, R. (2014). Design, fabrication and performance study of a biomass solid waste pyrolysis system for alternative liquid fuel production. Global Journal of Reserches in Engineering, 14(5), 25–34.
- Hossein, A., Dehaghani, S., & Rahimi, R. (2019). An experimental study of diesel fuel cloud and pour point reduction using different additives. Petroleum, 5(4), 413–416. https://doi.org/10.1016/j.petlm.2018.06.005
- Hu, Q., Sommerfeld, M., Jarvis, E., Ghirardi, M., Posewitz, M., Seibert, M., & Darzins, A. (2008). Microalgal triacylglycerols as feedstocks for biofuel production: Perspectives and advances. The Plant Journal, 54(4), 621–639. https://doi.org/10.1111/j.1365-313X.2008.03492.x
- Huang, H., Yuan, X., Zeng, G., Wang, J., Li, H., Zhou, C., Pei, X., You, Q., & Chen, L. (2011). Thermochemical liquefaction characteristics of microalgae in sub- and supercritical ethanol. Fuel Processing Technology, 92(1), 147–153. https://doi.org/10.1016/j.fuproc.2010.09.018
- Huzir, N., Maniruzzaman, M., Ismail, S. B., Abdullah, B., Mahmood, N. A., Umor, N. A., & Muhammad, S. A. (2018). Agro-industrial waste to biobutanol production: Eco-friendly biofuels for next generation. Renewable and Sustainable Energy Reviews, 94, 476–485. https://doi.org/10.1016/j.rser.2018.06.036
- Ibarra-gonzalez, P., & Rong, B. (2018). A review of the current state of biofuels production from lignocellulosic biomass using thermochemical conversion routes. Chinese Journal of Chemical Engineering, 27(7), 1–13. https://doi.org/10.1016/j.cjche.2018.09.018
- Ikubanni, P. P., Oki, M., Adeleke, A. A., Adediran, A. A., & Adesina, O. S. (2020). Influence of temperature on the chemical compositions and microstructural changes of ash formed from palm kernel shell. Results in Engineering, 8, 100173. https://doi.org/10.1016/j.rineng.2020.100173
- Islam, A. K., Yaakob, Z., & Anuar, N. (2011). Jatropha: A multipurpose plant with considerable potential for the tropics. Scientific Research and Essays, 6(13), 2597–2605.
- Ismail, A. R., Ismail, N., Jaafar, M. Z., & Hassan, R. The application of biodiesel as an environmental friendly drilling fluid to drill oil and gas wells the application of biodiesel as an environmental friendly drilling fluid to drill oil and gas wells. Proceeding of the 5th Sriwijaya International Seminar on Energy and environmental science, Palembang, Indonesia. September 10-11 2014.
- Jahirul, M. I., Rasul, M. G., Chowdhury, A. A., & Ashwath, N. (2012). Biofuels production through biomass pyrolysis—A technological review. Energies, 5(12), 4952–5001. https://doi.org/10.3390/en5124952
- Jain, S. K., Kumar, S., & Chaube, A. (2011). Technical sustainability of biodiesel and its blends with diesel in C. I. engines: A review. International Journal of Chemical Engineering and Applications, 2(2), 101–109. https://doi.org/10.7763/IJCEA.2011.V2.84
- Jena, U., & Das, K. C. (2011). Comparative evaluation of thermochemical liquefaction and pyrolysis for bio-oil production from microalgae. Energy & Fuels, 25(11), 5472–5482. https://doi.org/10.1021/ef201373m
- Jena, U., Das, K. C., & Kastner, J. R. (2012). Comparison of the effects of Na2CO3, Ca3(PO4)2, and NiO catalysts on the thermochemical liquefaction of microalga Spirulina platensis. Applied Energy, 98, 368–375. https://doi.org/10.1016/j.apenergy.2012.03.056
- Jin-jiang, W., Jie, C., & Juan, F. A. N. (2010). Catalytic esterification of bio-oil by ion exchange resins. Journal of Fuel Chemistry and Technology, 38(5), 560–564. https://doi.org/10.1016/S1872-5813(10)60045-X
- Juliet Ben-Iwo, P. L., Manovic, V., & Longhurst, P. (2016). Biomass resources and biofuels potential for the production of transportation fuels in Nigeria. Renewable and Sustainable Energy Reviews, 63, 172–192. https://doi.org/10.1016/j.rser.2016.05.050
- Khan, M. Z. H., Sultana, M., Al-Mamun, M. R., & Hasan, M. R. (2016). Pyrolytic waste plastic oil and its diesel blend: Fuel characterization. Journal of Environmental and Public Health, 8, 1–6. https://doi.org/10.1155/2016/7869080
- Kilbane, J. J. (2016). Future applications of biotechnology to the energy industry. Frontiers in Microbiology, 7(86). https://doi.org/10.3389/fmicb.2016.00086
- Krishania, N., Rajak, U., & Kumar, P. (2020). Investigations of spirulina, waste cooking and animal fats blended biodiesel fuel on auto-ignition diesel engine performance, emission characteristics. Fuel, 276(9), 118123. https://doi.org/10.1016/j.fuel.2020.118123
- Kumar, N., Sonthalia, A., & Pali, H. S. (2018). Alternative fuels for diesel engines: New frontiers. https://doi.org/10.5772/intechopen.80614
- Kumar, S., Chaube, A., & Jain, S. K. (2012). Experimental evaluation of C.I. engine performance using diesel blended with Jatropha biodiesel. International Journal of Energy and Environment, 3(3), 471–484.
- Kumari, D., & Singh, R. (2018). Pretreatment of lignocellulosic wastes for biofuel production: A critical review. Renewable and Sustainable Energy Reviews, 90, 877–891. https://doi.org/10.1016/j.rser.2018.03.111
- Laskar, I. B., Rajkumari, K., Gupta, R., Chatterjee, S., Paul, B., & Rokhum, L. (2018). Waste snail shell derieved heterogeneous catalyst for biodiesel production by the transesterification of soybean RSC advances. The Royal Society of Chemistry, 8(36), 20131–20142. https://doi.org/10.1039/C8RA02397B
- Li, W., Zhao, X., Ji, Y., Peng, H., Li, Y., Liu, L., & Han, X. (2016). An investigation on environmentally friendly biodiesel-based invert emulsion drilling fluid. Journal of Petroleum Exploration and Production Technology, 6(3), 505–517. https://doi.org/10.1007/s13202-015-0205-7
- Lissianski, V., Zamansky, V., & Rizeq, G. (2002). Integration of direct combustion with gasification for reduction of nox emissions.Proceedings of the Combustion Institute,29(2), 2251–2258. https://doi.org/10.1016/S1540-7489(02)80274-7
- Lujaji, F., Bereczky, A., Janosi, L., Novak, C., & Mbarawa, M. (2010). Cetane number and thermal properties of vegetable oil, biodiesel, 1-butanol and diesel blends. Journal of Thermal Analysis and Calorimetry, 102(3), 1175–1181. https://doi.org/10.1007/s10973-010-0733-9
- Lundquist, T. J., Woertz, I. C., Quinn, N. W. T., & Benemann, J. R. (2010). A realistic technology and engineering assessment of algae biofuel production. Energy Biosciences Institute, University of California.
- Madhu, A., Sai Bharadwaj, A., Niju, S., Meera, K. M., & Anantharaman, N. (2019). Studies on esterification optimization of high FFA content Pongamia oil using box – Behnken design, horizons in bioprocess engineering (pp. 3–16). Springer.
- Maharani, R., Yutaka, T., Yajima, T., & Minoru, T. (2010). Scrutiny on physical properties of sawdust from tropical commercial wood species: Effects of different mills and sawdust’s particle size. Indonesian Journal For. Research, 7(1), 20–32. https://doi.org/10.20886/ijfr.2010.7.1.20-32
- Matemilola, S., Elegbede, I. O., Kies, F., Yusuf, G. A., Yangni, G. N., & Garba, I. (2019). An analysis of the impacts of bioenergy development on food security in Nigeria: Challenges and prospects. Environmental and Climate Technologies, 23(1), 64–83. https://doi.org/10.2478/rtuect-2019-0005
- Muraina, H. O., Odusote, J. K., & Adeleke, A. A. (2017). Physical properties of biomass fuel briquette from oil palm residues. Journal of Applied Sciences and Environmental Management, 21(4), 777–782. https://doi.org/10.4314/jasem.v21i4.19
- Nawaz, H., Nawaz, H., Nawaz, H., Nawaz, H., & Nouren, S. (2018). Biodiesel production from waste cooking oil: An efficient technique to convert waste into biodiesel. Sustainable Cities and Society, 41, 220–226. https://doi.org/10.1016/j.scs.2018.05.037
- Nedayali, A., & Shirneshan, A. (2016). Experimental study of the effects of biodiesel on the performance of a diesel power generator. Energy and Environment, 27(5), 553–565. https://doi.org/10.1177/0958305X15627550
- Nicodème, T., Berchem, T., Jacquet, N., & Richel, A. (2018). Thermochemical conversion of sugar industry by-products to biofuels. Renewable and Sustainable Energy Reviews, 88, 151–159. https://doi.org/10.1016/j.rser.2018.02.037
- Nisar, J., Razaq, R., Farooq, M., Iqbal, M., & Ali, R. (2017). Enhanced biodiesel production from Jatropha oil using calcined waste animal bones as catalyst. Renew. Energy, 101, 111–119. http://dx.doi.org/10.1016/j.renene.2016.08.048
- Oasmaa, A., Elliott, D. C., Korhonen, J., Jahirul, M., Rasul, M., Chowdhury, A., & Ashwath, N. (2010). Acidity of biomass fast pyrolysis bio-oils. Energy and Fuels, 24(12), 6548–6554. https://doi.org/10.1021/ef100935r
- Odusote, J. K., Adeleke, A. A., Lasode, O. A., Malathi, M., & Paswan, D. (2019). Thermal and compositional properties of treated Tectona grandis. Biomass Conversion and Biorefinery, 9(3), 511–519. https://doi.org/10.1007/s13399-019-00398-1
- Oghenejoboh, K. M., Ohimor, E. O., & Olayebi, O. (2013). Application of re-refined used lubricating oil as base oil for the formulation of oil based drilling mud - A comparative study. Journal of Petroleum Technology and Alternative Fuels, 4(4), 78–84. https://doi.org/10.5897/JPTAF2013.0089
- Ohijeagbon, I. O., Adeleke, A. A., Mustapha, V. T., Olorunmaiye, J. A., Okokpujie, I. P., & Ikubanni, P. P. (2020)Development and characterization of wood-polypropylene plastic-cement composite board. Case Studies in Construction Materials, 13, e00365. https://doi.org/10.1016/j.cscm.2020.e00365
- Okareh, O. T., Adegoke, S. O., Richard, R., Akintola, S. A., Adeleke, A. A., & Ikubanni, P. P. (2020). Fuel energy potential of pyrolysed municipal solid waste. Petroleum and Coal, 63(1), 234–244.
- Onwudili, J. A., Insura, N., & Williams, P. T. (2009). Composition of products from the pyrolysis of polyethylene and polystyrene in a closed batch reactor: Effects of temperature and residence time. Journal of Analytical and Applied Pyrolysis, 86(2), 293–303. https://doi.org/10.1016/j.jaap.2009.07.008
- Onyelowe, K., Onyelowe, F., Van, D., Ikpa, C., Salahudeen, B., Eberemu, A., Osinubi, K., Onukwugha, E., Odumade, A., Chigbo, I., Amadi, A., Igboayakata, E., Obimba-Wogu, J., Saing, Z., & Amhadi, T. (2019). Valorization and sequestration of hydrogen gas from biomass combustion in solid waste incineration NaOH oxides of carbon entrapment model (SWI- NaOH-OCE model). Materials Science for Energy Technologies, 3, 250–254 https://doi.org/10.1016/j.mset.2019.11.003
- Oseh, J. O., Norddin, M., Ismail, I., Ismail, A., Gbadamosi, A., Agi, A., & Ogiriki, S. (2019). Investigating almond seed oil as potential biodiesel-based drilling mud. Journal of Petroleum Science and Engineering, 181, 106201. https://doi.org/10.1016/j.petrol.2019.106201
- Papari, S., & Hawboldt, K. (2015). A review on the pyrolysis of woody biomass to bio-oil: Focus on kinetic models. Renewable and Sustainable Energy Reviews, 52, 1580–1595. https://doi.org/10.1016/j.rser.2015.07.191
- Pittman, J. K., Dean, A. P., & Osundeko, O. (2011). Bioresource technology the potential of sustainable algal biofuel production using wastewater resources. Bioresource Technology, 102(1), 17–25. https://doi.org/10.1016/j.biortech.2010.06.035
- Prasad, K. A., Ramana, S. C. V., & Naidu, M. (2019). Performance analysis of dual biodiesels of pongamia and cotton seed oils and numerical analysis of BTE and BSFC. International Journal of Engineering and Advanced Technology, 8(3), 672–683. https://www.researchgate.net/publication/331972358
- Radakovits, R., Jinkerson, R. E., Darzins, A., & Posewitz, M. C. (2010). Genetic engineering of algae for enhanced biofuel production, American society for microbiology. 9(4), 486–501. https://doi.org/10.1128/EC.00364-09
- Rajasekar, E., & Selvi, S. (2014). Review of combustion characteristics of CI engines fueled with biodiesel. Renewable and Sustainable Energy Reviews, 35, 390–399. https://doi.org/10.1016/j.rser.2014.04.006
- Robert Ndong, C. S., Montrejaud-Vignoles, M., Girons, O. S., Gabrielles, B., Pirot, R., & Domergue, M. (2009). Life cycle assessment of biofuels from Jatropha curcas in West Africa: A field study. GCB Bioenergy, 1(3), 197–210. https://doi.org/10.1111/j.1757-1707.2009.01014.x
- Roberts, I., Lamb, H. H., Larry, F., & Turner, T. L. (2013). Patents Process for conversion of biomass to fuel US7816570B2.
- Rodionova, M. V., Poudyal, R. S., Tiwari, I., Voloshin, R. A., Zharmukhamedov, S. K., Nam, H. G., Zayadan, B. K., Bruce, B. D., Hou, H. J. M., & Allakhverdiev, S. I. (2016). Biofuel production: Challenges and opportunities. International Journal of Hydrogen Energy, 42(12), 8450–8461. https://doi.org/10.1016/j.ijhydene.2016.11.125
- Sadef, Y., Nizami, A. S., Batool, S. A., Chaudary, M. N., Ouda, O. K., Asam, Z. Z., Habib, K., Rehan, M., & Demirbas, A. (2016). Waste-to-energy and recycling value for developing integrated solid waste management plan in Lahore. Energy Sources, Part B: Economics, Planning, and Policy, 11(7), 569–579. https://doi.org/10.1080/15567249.2015.1052595
- Sani, S., Kaisan, M. U., Kulla, D. M., Obi, A. I., Jibrin, A., & Ashok, B. (2018). Industrial crops & products determination of physico chemical properties of biodiesel from citrullus lanatus seeds oil and diesel blends. Industrial Crops and Products, 122, 702–708. https://doi.org/10.1016/j.indcrop.2018.06.002
- Senthilkumar, C., Krishnaraj, C., & Sircar, A. (2018). Statistical optimization and kinetic study on biodiesel production from a potential non-edible bio-oil of wild radish. Chemical Engineering Communications, 206(7), 1–10. https://doi.org/10.1080/00986445.2018.1538973
- Shirazi, L. (2020). Kinetic studies of butene oligomerization over HZSM-5 zeolites with different acidity. Petroleum and Coal, 62(3), 945–950.
- Shrivastava, P., Verma, T. N., & Pugazhendhi, A. (2019). An experimental evaluation of engine performance and emisssion characteristics of CI engine operated with Roselle and Karanja biodiesel. Fuel, 254, 115652. https://doi.org/10.1016/j.fuel.2019.115652
- Sikarwar, V., Zhao, M., Fennell, P., Shah, N., & Anthony, E. (2017). Progress in biofuel production from gasification Progress in energy and combustion science. 61, 189–248. https://doi.org/10.1016/j.pecs.2017.04.001
- Singh, H., Adeleke, A. A., Singh, C., Ikubanni, P. P., Orhadahwe, T. A., & Agboola, O. O. (2021). Agglomeration of pet coke and rice straw as mixed fuel for power generation. Petroleum and Coal, 63(2), 356–365.
- Singh, N., Cranage, D., & Lee, S. (2014). Green strategies for hotels: Estimation of recycling benefits. International Journal of Hospitality Management, 43, 13–22. https://doi.org/10.1016/j.ijhm.2014.07.006
- Singh, T. S., & Verma, T. N. (2019a). Taguchi design approach for extraction of methyl ester from waste cooking oil using synthesized CaO as heterogeneous catalyst: Response surface methodology optimization. Energy Conversion and Management, 182, 383–397. https://doi.org/10.1016/j.enconman.2018.12.077
- Singh, T. S., & Verma, T. N. (2019b). Biodiesel production from Momordica Charantia (L.): Extraction and engine characteristics. Energy, 189, 116198. https://doi.org/10.1016/j.energy.2019.116198
- Singh, T. S., & Verma, T. N. (2019c). An assessment study of using Turel Kongreng (river mussels) as a source of heterogeneous catalyst for biofuel production. Biocatalysis and Agricultural Biotechnology, 20, 101185. https://doi.org/10.1016/j.bcab.2019.101185
- Sriningsih, W., Saerodji, M. G., Trisunaryanti, W., I. falah, I., Falah, I. I., & Falah, I. I. (2014). Fuel Production from LDPE plastic waste over natural Zeolite supported Ni, Ni-Mo, Co and Co-Mo metals. Procedia Environmental Sciences, 20, 215–224. https://doi.org/10.1016/j.proenv.2014.03.028
- Stöcker, M. (2008). Renewable resources biofuels and biomass-to-liquid fuels in the biorefinery: Catalytic conversion of lignocellulosic biomass using porous materials. Angewandte Chemie International Edition, 47(48), 9200–9211. https://doi.org/10.1002/anie.200801476
- Subhaschandra, T., Rajak, U., & David, O. (2021). Optimization of performance and emission parameters of direct injection diesel engine fuelled with microalgae Spirulina (L.) – Response surface methodology and full factorial method approach. Fuel, 285, 119103. https://doi.org/10.1016/j.fuel.2020.119103
- Syahirah, N., Aron, M., Khoo, K. S., Chew, K., Show, P. L., Chen, W., & Nguyen, T. H. P. (2020). Sustainability of the four generations of biofuels – A review. International Journal of Energy Research, 44(12), 9266–9282. https://doi.org/10.1002/er.5557
- Tesfa, B., Mishra, R., Gu, F., & Powles, N. (2010). Prediction models for density and viscosity of biodiesel and their effects on fuel supply system in CI engines. Renewable Energy, 35(12), 2752–2760. https://doi.org/10.1016/j.renene.2010.04.026
- Tüccar, G., Tosun, E., & Uludamar, E. (2018). Investigations of effects of density and viscosity of diesel and biodiesel fuels on NOx and other emission formations. Academic Platform Journal of Engineering and Science, 6(2), 81–85. https://doi.org/10.21541/apjes.371015
- Van Leeuwen, T. T., Werf, G. R., Hoffmann, A., Detmers, R., Rucker, G., French, N., Archibald, S., Carvalho, J., Cook, G. D., de Groot, W. J., Hély, C., Kasischke, E. S., Kloster, S., McCarty, J. L., Pettinari, M. L., Savadogo, P., Alvarado, E. C., Boschetti, L., Manuri, S., Meyer, C. P., & Trollope, W. S. W. (2014). Biomass burning fuel consumption rates: A field measurement. Biogeosciences, 11(24), 7305–7329. https://doi.org/10.5194/bg-11-7305-2014
- Vardon, D. R., Sharma, B. K., Blazina, G. V., Rajagopalan, K., & Strathmann, T. J. (2012). Thermochemical conversion of raw and defatted algal biomass via hydrothermal liquefaction and slow pyrolysis. Bioresource Technology, 109, 178–187. https://doi.org/10.1016/j.biortech.2012.01.008
- Verma, G., Nigam, P., Singh, D., & Chaudhary, K. (2000). Bioconversion of starch to ethanol in a single-step process by coculture of amylolytic yeasts and Saccharomyces cerevisiae 21. Bioresource Technology, 72(3), 261–266. https://doi.org/10.1016/S0960-8524(99)00117-0
- Wang, H., Tang, H., Wilson, J., Salley, S. O., & Ng, K. Y. S. (2008). Total acid number determination of biodiesel and biodiesel blends. Journal of the American Oil Chemists’ Society, 85(11), 1083–1086. https://doi.org/10.1007/s11746-008-1289-8
- Zhang, J., Pereira, M., & Wang, R. (2019). in situ transesterification of microalgae over KOH supported on mesoporous CeO2 catalyst. Petroleum and Coal, 61(3), 508–516.
- Zhang, L., Bao, Z., Xia, S., Lu, Q., & Walters, K. (2018). Catalytic pyrolysis of biomass and polymer wastes. Catalysts, 8(12), 659. https://doi.org/10.3390/catal8120659