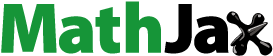
Abstract
The aim of the present research work is to improve the hardness-related properties by the combined effect of precipitation of secondary phases through aging treatment and dispersion strengthening. In this study, reinforcement material was cast in the form of rods as per the required composition. Turning operation was performed to convert them into chips using conventional lathe machine. Ball milling setup comprising hardened steel balls was then utilized to pulverize these grey cast iron (GCI) chips to obtain reinforcement particulates. Al 7075-based composites are manufactured with GCI reinforcements by two-step stir casting method. Precipitation hardening treatment is imparted to alloy and composites to enhance the mechanical properties. Hardness and tensile properties are analysed in both as-cast and age hardened conditions. Brinell hardness tester was employed for measurement of hardness. Composites reinforced with GCI particulates significant increase in hardness in comparison with base alloy. 80–100% increase in peak hardness aged at 200°C and 120–140% increase in peak hardness aged at 100°C observed for Al 7075-GCI compared with base alloy. The analysis of tensile behaviour was carried out in electronic tensometer. Ultimate tensile strength increased with the increase in weight percentage of reinforcements. An increase of 40–50% in UTS at peak aged condition obtained at 200°C and 60–70% in peak aged condition at 100°C for Al 7075-GCI composites compared with as-cast composites. Uniformity in reinforcement particle distribution in the matrix is confirmed by the SEM analysis of the composite. TEM analysis of as cast and aged alloy/composites reveal the precipitate size, shape and its dispersion in the matrix phase. Aging kinetics is accelerated by the increase in wt.% of reinforcement.
1. Introduction
The technological challenges faced by mankind in every era have forced humans to invent novel materials for enhancing desirable properties under various conditions (Young et al., Citation2003). The literature published in the area concentrates on the possibility to achieve uniform dispersion of reinforcements in the matrix through liquid stir casting technique, even though the difference in density of matrix and reinforcement exists. Study also throws light on the microstructure and mechanical properties in as cast and precipitation hardened conditions. Al 7075 alloys are extensively used in many application areas including aerospace, marine and automotive domains due to their favorable mechanical characteristics. They also exhibit attractive physical properties like lower density and higher strength to weight ratio (Toptan et al., Citation2013). Due to the demand for high-performance and low-cost materials research is on to replace monolithic materials with composites. Al 7075 alloy is generally reinforced with ceramic particulates like SiC, B4C, Al2O3, TiC, etc., which imparts superior mechanical properties to the alloy (Masoud Sabzi et al., Citation2019). Stir casting or vortex casting is one of the widely employed techniques for manufacturing of Al alloy based composites. By properly controlling the process parameters such as the stirrer speed, melt temperature, weight percentage of reinforcements uniformity in reinforcement distribution can be achieved (Mousavi et al, Citation2018).
Al matrix composites have proved to be superior candidates for high strength and wear resistance applications compared to unreinforced Al alloys. However it is well established that the ductility and machinability of AMCs are reduced due to the presence of ceramic reinforcement (Sabzi et al., Citation2019). Some of the ceramic particles will react with base material at the matrix reinforcement interface due to its affinity or thermodynamic instability. This leads to the generation of reactionary phases which may hamper the interfacial bonding and will degrade the composite’s interfacial strength, which deteriorates the mechanical properties (Rupa Dasgupta & Meenai, Citation2005).
In this study Al 7075 is selected as the matrix material as it is among the strongest aluminum alloys in which zinc and magnesium are the main alloying elements in its composition and thus have the potential to become an excellent candidate as a matrix for composites (Mousavi et al, 2018).
Two step stir casting is employed for the fabrication of composites as the method found to improve the wettability of the reinforcement particles and ensure uniform particle distribution (Kanayo et al., Citation2015). Pre heating of reinforcements decreases the humidity and increases the wettability with the base alloy (Pazhouhanfar et al., Citation2018). Pre heating also ensures the reinforcement surface to be oxidized and hence particles act as substrates for heterogeneous nucleation in composite during age hardening (Bhushan et al., Citation2019). Rao et al. (Citation2010) performed degasification of the melt during stirring by passing nitrogen gas resulting in removal of the dissolved gasses. Degasification results in loss of heat. Hence the melt is heated again before the introduction of reinforcement particles. Kalkanli and Yılmaz (Citation2008) performed age hardening heat treatment resulted in obtaining peak hardness values. 20–25% enhancement in hardness values were recorded following aging treatment which can be ascribed to precipitation of secondary phases. Chawla and Shen (Citation2001) observed that enhancement in volume% of reinforcement improved the desirable properties with reduction in ductile behaviour.
Grey cast iron (GCI) particulates are selected as reinforcement. GCI is one of the types of cast irons which has unique microstructure containing carbon in free and combined form. Carbon is present as cementite and graphite. Presence of GCI reinforcement can impart excellent wear resistance, as the flakes of graphite serve as solid lubricants. An additional damping capability is provided to the matrix material by the presence of graphite as the energy is absorbed by it during loading conditions (Jamaluddin Hindi et al., Citation2020).
The strength and hardness of an alloy can be enhanced by either cold working or thermal treatment. Age or precipitation hardening is the most widely employed heat treatment process for nonferrous alloys and composites (Rao et al. (Citation2010)).
The effect of addition of reinforcement on the microstructure and mechanical characteristics are widely reported. However very few literatures reveal the effect of metallic reinforcements. Based on the literature study we could not establish any reported work on the combined effect of precipitation hardening and metallic reinforcement on the Al 7075 matrix composites. Novelty of the work is the precipitation of Aluminium composites by the machined cast iron chips (scrap) and possibility for solid solution strengthening by precipitation hardening treatment. The main objective of this research work is to produce composite with novel reinforcement material having excellent property which could be a cheaper alternative to the conventional ceramic reinforced metal matrix composites.
2. Materials and methods
Al 7075 rods were procured from perfect metal works, Bengaluru, in T6 condition. The actual composition of the alloy lies within the AA standard chemical composition range (). GCI rods were cast in Servell Engineers, Manglore, as per the composition shown in which lies within the FG 150 standard chemical composition range.
Table 1. Comparison of actual and standard composition (wt.%) of Al 7075
Table 2. Comparison of actual and standard composition (wt.%) of GCI
Turning operation was performed on GCI rods to convert them into chips using conventional lathe machine. Ball milling setup comprising hardened steel balls was then utilized to pulverize these GCI chips. It works on principle of impact and attrition to reduce the size of material in microns range. Measured quantities of GCI chips were introduced into the mill. After each hour, these milled particles were removed and were measured for size using different grades of sieves with US mesh sizes of 35, 60, 120, and 250. This process was repeated until the average size of 50 µm was achieved using 250 mesh size.
The size of the reinforcement particles was measured using the laser diffraction technique. The laser beam is made to pass through the particles which in turn illuminates the dispersed particles. The intensity of light scattered by the particles is measured by using various detectors which are placed at wide range of angles. The pattern of scattering is then analysed to calculate the size of the particles in the sample zone that resulted in such a scattering pattern.
Stir casting technique was used in composite fabrication. Various quantities of reinforcement (2, 4 and 6 wt.%) were selected for comparative study. To enhance the wettability metered quantities of K2TiF6 particles were introduced into the melt (Baradeswaran & Perumal, Citation2014). Specially designed stir casting setup comprising titanium stirrer, thermocouple, crucible made from graphite, electrical resistance furnace, controlled inert atmosphere of argon gas. Preheating of reinforcement particles was carried out in an electrical furnace for 2 h at 250°C. Matrix material is heated above 750°C by placing in a graphite crucible which in turn placed in furnace. Impeller-based stirrer was then introduced into the melt rotating at 400 rpm for a duration of 10 min which resulted in formation of vortex in the molten metal (Pazhouhanfar et al., 2018). The preheated powder was then introduced into the vortex which avoids the sedimentation of reinforcement’s particles thereby achieving uniform distribution of particulates throughout the matrix. The stirring phenomena was performed in an inert gas atmosphere by maintaining nitrogen gas (P = 0.3 Kgf/cm2). The composite slurry was instantaneously transferred into low carbon steel permanent dies maintained at ambient temperature.
The general rule of mixture is employed for the computation of theoretical density as follows: Al 7075-GCI = Volf Al 7075 X
1D746Al 7075 + Volf GCI X
GCI.The experimental density value is computed as the ratio of weight (W) and volume (V) of specimen.
Analysis of reinforcement particle distribution is conducted by cubical specimen which are cut from the castings. Subsequent to coarse polishing by emery papers of 100–2000 grit size and fine polishing by diamond paste, Keller’s reagent is employed for etching to cause corrosion at grain boundaries to highlight the microstructure of the composite. SEM (ZEISS EVO MA18 with Oxford EDAX(X-act)) with EDAX used to evaluate dispersion of particulates in base matrix.
For Transmission electron microscopy, from the peak aged samples (Al 7075 alloy and Al 7075–6% wt. GCI, aged at 100°C), thin foils are obtained using slow speed diamond saw and mechanically thinned down to thickness ~0.1 mm. These thin foils are blanked to obtain discs of 3 mm diameter and further ground to reduce the thickness. Finally twin jet electro-polishing system is used to prepare TEM specimen using mixture of acetic and perchloric acids at a voltage of ~25 V and temperature ~6°C. When perforation starts, the electro-polishing unit gets switched-off automatically. The perforated 3 mm disc samples are studied in analytical transmission electron microscope (Model: Philips CM 200) using energy dispersive spectroscopy (EDS). Brinell hardness tester was employed for mesurement of hardness (ASTM E10-00) in as-cast and age hardened conditions for alloy and composites utilising 5 mm diameter steel ball indenter and 250 kgf load (SAROJ Brinell Hardness Testing Machine, Model:-B/3000/00, Sl#13/06/08-India). The average of at least five nearly identical indentation readings are noted for each specimen at different locations of the test samples in order to minimize potential segregation influence. The analysis of tensile behaviour was carried out as per ASTM-E8M standard in electronic tensometer. Solutionizing is carried out at 570°C in a muffle furnace for a duration of 2 h followed by quenching in demineralized water bath maintained at room temperature. Artificial aging is imparted on solutionized specimen in hot air oven at 100, 150 and 200°C for known durations (Kalkanli & Yılmaz, Citation2008). SEM (ZEISS EVO MA18 with Oxford EDS(X-act)) with EDAX is used to evaluate dispersion of particulates in base matrix.
3. Results and discussion
3.1. Analysis of shape and composition of reinforcement particles
The SEM images of GCI particles are shown in along with EDAX. The powder grits are similar shaped near spheroids or prismatic in nature whose size varies in the range of 40 to 100 microns. The grits are blunt cornered with aspect ratio near to one. The EDAX shows the presence of both Fe and C at grit location, indicating the presence of combined carbon.
3.2. Analysis of reinforcement particle distribution in composites
To obtain superior mechanical properties, homogeneous distribution of reinforcements in the metal matrix is the key (S.H. Mousavi Anijdan et al., Citation2021). The viability of stir casting method to produce the composite is examined using analysis of reinforcement particle distribution. Homogeneous particle distribution in the molten metal is a reflection of composite quality. During stir casting particulate composites care must be taken to see that there is minimum sedimentation and agglomeration of reinforcement particle in mixing or pouring stage. Existence of reinforcement and its uniformity in dispersion in matrix is studied by scanning electron microscopy. The mechanical properties of the composite rely heavily on the homogeneous distribution of reinforcements particles. Particulate composites with uniformity reinforcement dispersion without any agglomeration or sedimentation can be obtained by maintaining suitable stirrer speed and appropriate temperature of the melt. SEM micrographs were studied to confirm the uniformity in reinforcement particle dispersion in the matrix. shows the SEM image and EDAX spectra of Al 7075-GCI composites of compositions 2, 4 and 6 wt.% or reinforcement respectively. Both microstructures & EDAX spectra confirm the presence of GCI particles. Microstructural analysis reveals uniformity of reinforcement distribution. Good bonding at the matrix reinforcement interface was observed in SEM analysis which can be ascribed to the wetting agent and preheating of reinforcement.
Figure 2. SEM images of reinforcement distribution in a) Al 7075–2 wt.% GCI, b) Al 7075–4 wt.% GCI, c) Al 7075–6 wt.% GCI and d) EDAX spectum of Al 7075–6 wt.% GCI composite (e) Chemical composition.
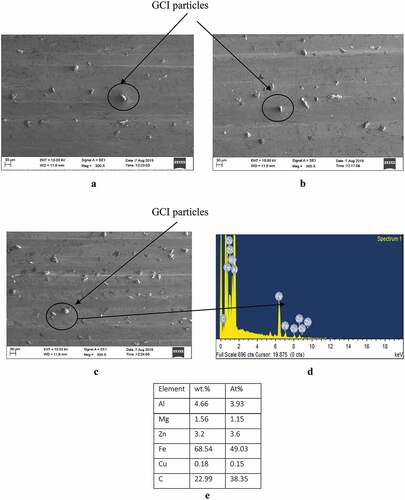
The particle distribution in the matrix accounts for the composite hardness. If the reinforcement particles are closer inter particle distance is uniform, higher hardness is achieved. The uniform particle distance periodically hurdles the dislocation movement in the grain and pileup these blocking points (reinforcements) for solid solution strengthening. The uniform particle distance also maintains uniform micro hardness values in the matrix.
3.3. Reinforcement particle size analysis using laser diffraction technique
The size of the reinforcement particles were measured using the laser diffraction technique. The laser beam is made to pass through the particles which in turn illuminates the dispersed particles. The intensity of light scattered by the particles is measured by using various detectors which are placed at wide range of angles. The pattern of scattering is then analysed to calculate the size of the particles in the sample zone that resulted in such a scattering pattern. The average particle size of GCI was found to be 50 microns ().
3.4. Evaluation of theoretical and experimental densities of composites
The method employed for the fabrication of particulate composites can be considered as an optimum one only if the porosity levels in the casting can be kept to a minimum. Desired high performance in any application can be expected from those composites whose porosity values are the least. Air bubbles getting entrapped in the slurry during the vortex formation while stirring is the primary source of porosity. Acceleration of aging kinetics will also depend on the optimum porosity levels as nucleation sites are increased due to it (Rupa Dasgupta & Meenai, Citation2005). Theoretical, experimental densities and porosity variation with weight percentage of GCI reinforcements are shown in . The density (theoretical and experimental) values are complementary of one another for all the wt.% of reinforcement considered. Due to higher mass of reinforcement particulates, increase in wt.% of reinforcement results in enhancement of densities. Since the bulk density of GCI particles (7.8 g/cc) are more than Al 7075 (2.7 g/cc) there is an increasing trend in overall density of GCI reinforced composites. As the wt.% of reinforcement particles increases, it leads to higher porosity. This can be attributed to longer processing time for the composites comprising higher wt.% of reinforcement as they entrap more amount of oxygen during stirring (Gowri Shankar et al., Citation2016).
3.5. Analysis of hardness variation in as-cast and age hardened conditions
Uniformity in reinforcement dispersion is confirmed by conducting hardness test on five specimen cut from the same casting in the increment of 15 mm from the bottom end of casting. Similar hardness values are noted in all the specimen cut from same casting, indicating uniformity in reinforcement dispersion. shows similarity in hardness values of specimen cut from castings of alloy and composites.
Incorporation of reinforcement into the liquid melt of matrix alloy during stir casting behaves as heterogeneous nucleation sites while solidifying, resulting in an improvement in mechanical properties and refinement of grain size of composites in as cast condition (Chuandong et al., Citation2017). Aging curves are plotted for alloy and composites for different aging temperatures. There is a gradual increase in hardness with time during aging process at all aging temperatures, until peak hardness is achieved. Further aging leads to reduction in the hardness and is termed as over-aging (Gowri Shankar et al., Citation2016). This phenomenon of variation in hardness with aging time is common among Al alloy and its composites (Mahathaninwong et al., Citation2012). The time required to attain peak hardness reduces with the increase in wt.% of reinforcement irrespective of aging temperatures ().
Figure 6. Aging curves (BHN vs. aging time) at 100, 150 & 200°C for a) Al 7075 alloy b) Al 7075–2 wt.% GCI, c) Al 7075–4 wt.% GCI and d) Al 7075–6 wt.% GCI.
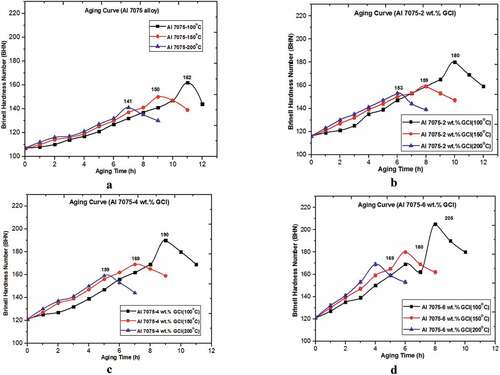
Age hardening results in profound improvement in hardness of GCI reinforced composites in comparison with unreinforced alloy. Due to higher hardness of reinforcement particles, it leads to higher hindrance to mobility of dislocations resulting in the precipitation of enormous quantity of secondary intermetallic phases while precipitation hardening treatment (Jitendra et al., Citation2019). Since diffusion kinetics is slower at lower aging temperature (100°C), the process is delayed (9 hr for Al 7075–6 wt.% GCI and 11 hr for Al 7075 alloy) . Enhancement in number of intermediate zones during precipitation, increase in number of finer intermetallics and decreased inter particle distance can be ascribed to achieving peak hardness at lower aging temperature. As the temperature increases critical size of the precipitates nucleated is larger which leads to coarser precipitates in turn resulting in the reduction of interface area. This phenomena results in lower strength and hardness (Mahmoud Chemingui et al., Citation2010). The combined effect of dispersion strengthening due to the hardness of reinforcements and precipitation strengthening due to the aging treatment results in significant enhancement in the hardness of Al 7075 composites. depicts the hardness variation for Al 7075-GCI composites. shows the standard deviation of hardness values for Al 7075-GCI composites.
3.6. Characterization of tensile behaviour
Al 7075 alloy and composites are subjected to tensile test in as-cast and peak aged conditions. Average of three values are taken after the experiments and readings are recorded as shown in . It can be concluded that superior tensile strength is exhibited by the composites compared to alloys both in as-cast and peak aged conditions. As-cast UTS of Al 7075–6 wt.% GCI, MMCs measure 180 MPa, when compared to 145 MPa for Al 7075 alloy. 10–40% rise in UTS value is obtained for composites over Al 7075 alloy in as-cast condition. shows standard deviation of UTS values for Al 7075-GCI composites
Figure 9. UTS (MPa) variation in as-cast and age hardened conditions for Al 7075 alloy and Al 7075-GCI composites.
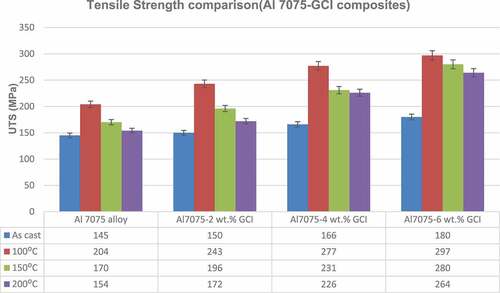
It is evident from the values obtained for UTS that there is a direct correlation between the content of GCI particles and the tensile strength in both as-cast and heat treated conditions. The UTS of composite has significantly increased compared to the alloy. The enhancement in UTS and modulus of elasticity can be attributed to the stronger interface between the matrix and reinforcement. UTS is directly proportional to the extent to which load is distributed from the matrix to the reinforcement.
3.7. Characterization of precipitates using TEM
The finer precipitates evolved during the aging treatment of Al 7075 alloy and Al 7075-GCI composites were analysed for its shape, size, composition and uniformity in dispersion using TEM-EDS-SADP facility. shows TEM images of Al 7075 alloy peak aged at 100°C in different magnifications along with EDS. Precipitate dispersion is shown in ), ) represents single precipitate at higher magnification. Analysis of TEM micrographs after age hardening revealed the presence of the precipitates in various forms and shapes. ) shows the EDAX spectrum which confirms the existence of Mg and Zn leading to the precipitation of MgZn2 (η) phase. Since the precipitate size is very small, EDAX shows significant percentage of matrix phase (Musa et al., Citation2016). SADP shown in ) of the corresponding precipitate further confirmed the presence of MgZn2 phase. Streaks and satellite spots in SADP indicates the presence of semi coherent MgZn2 particles in the Al 7075 alloy. Larger spots in SADP pertain to Al matrix and smaller spots can be attributed to the precipitated phase (MgZn2; Rao et al., Citation2010).
Figure 11. (a) TEM images of peak aged Al 7075 at 100°C at lower and (b) higher magnifications, (c) TEM image of a single precipitate (d) EDS spectra of the corresponding precipitate. e) SADP of corresponding precipitate.
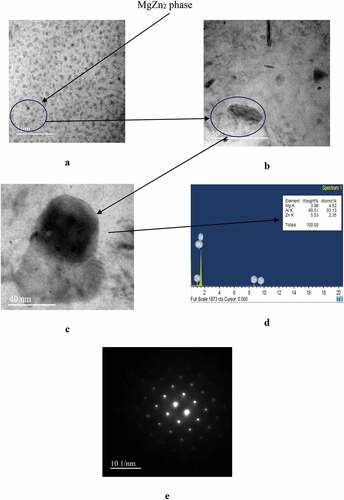
) shows bright field TEM photographs, EDS spectra and SADP of Al 7075–6 wt.% GCI. TEM images show the precipitation of semi-coherent η”, Al-Zn-Cu (rectangle shaped) phase in peak aging condition (100°C). The TEM photograph shown in figure reveals uniform dispersion of precipitated phases in the matrix. Peak aging condition results in strength enhancement mainly due to the presence of homogeneously distributed precipitates/intermetallics which maintains full or partial coherency with matrix. Eventhough the form and compsition of the precipitate remains the same for alloy and composites, peak strength and hardness of the latter can be attributed to enhancement in the density of precipitates and its uniformity in distribution (Reda et al., Citation2008).
4. Conclusions
The microstructural investigation revealed uniform distribution/dispersion of reinforcements in Al 7075 alloy reinforced with GCI composites without any defects fabricated via two step stir casting route. SEM-EDAX confirmed the presence of reinforcements.
By using particle size distribution analysis the average particle size of GCI was found to be 50 microns.
The density of composites is higher than that of the base matrix. Furthermore the density increases with increase in reinforcement content (2–6 wt.%) in the composites.
The Al 7075 alloy and its composites reinforced with GCI particulates positively respond to precipitation hardening treatment exhibiting a significant increase in hardness.
At lower aging temperature (100°C) for both alloy and composites, higher peak hardness is achieved with slower aging kinetics.
Precipitation of intermetallic phases in both alloy and composites during age hardening treatment is confirmed through TEM studies.
TEM images of Al 7075–6 wt.% GCI composites peak aged at 100°C showed precipitation and uniformity in dispersion of semi-coherent η˝-MgZn2 phase.
TEM study of composites reveals enhancement in precipitate and reinforcement strengthening due to the restriction posed to movement of dislocations.
The collective influence of harder reinforcement and precipitated phases during aging in Al 7075–6 wt.% GCI composite results in escalation of hardness in comparison with peak aged Al 7075 alloy.
Disclosure statement
No potential conflict of interest was reported by the author(s).
Additional information
Funding
Notes on contributors
Jamaluddin Hindi
Dr. Jamaluddin Hindi Assistant professor senior scale Department of Mechanical and Manufacturing Engineering, Manipal Institute of Technology, Manipal Academy of Higher Education, Manipal, India
Gurumurthy Bm
Dr. Gurumurthy B. M Assistant professor senior scale Department of Mechanical and Manufacturing Engineering, Manipal Institute of Technology, Manipal Academy of Higher Education, Manipal, India
Sathyashankara Sharma
Dr. Sathyashankara Sharma Professor Department of Mechanical and Manufacturing Engineering, Manipal Institute of Technology, Manipal Academy of Higher Education, Manipal, India
Achutha Kini
Dr. Achutha Kini Professor Department of Mechanical and Manufacturing Engineering, Manipal Institute of Technology, Manipal Academy of Higher Education, Manipal, India
Amar Murthy A
Amar Murthy A Assistant professor selection grade Department of Mechanical and Manufacturing Engineering, Manipal Institute of Technology, Manipal Academy of Higher Education, Manipal, India
Muralishwara K
Muralishwara K Assistant professor senior scale Department of Mechanical and Manufacturing Engineering, Manipal Institute of Technology, Manipal Academy of Higher Education, Manipal, India
References
- Baradeswaran, A., & Perumal, E. (2014). Study on mechanical and wear properties of Al 7075/Al2O3/graphite hybrid composites. Composites, 56(6), 464–15. https://doi.org/10.1016/j.compositesb.2013.08.013
- Bhushan, R. K., Kumar, S., & Das, S. (2019). Optimisation of porosity of 7075 Al alloy 10% SiC composite produced by stir casting process through Taguchi method. International Journal of Materials Engineering Innovation, 1(1), 116–129. https://dx.doi.org/10.1504/IJMATEI.2009.024031
- Chawla, N., & Shen, Y.-L. (2001). Mechanical behaviour of particle reinforced metal matrix composites. Advanced Engineering Materials, 3(6), 357–370. https://doi.org/10.1002/1527-2648(200106)<357::AID-ADEM357>3.0.CO;2-I
- Chuandong, W., Kaka, M., Zhang, D., Jialu, W., Xiong, S., & Luo, G. (2017). Precipitation phenomena in Al- Zn-Mg alloy matrix composites reinforced with B4C particles. Scientific Reports, 2(2), 1–11. https://doi.org/10.1038/s41598-017-10291-4
- Gowri Shankar, M. C., Sharma, S. S., Kini, A., Jayashree, P. K., & Gurumurthy, B. M. (2016). Study of wear behaviour and mechanical mixed layer on artificial aged Al6061 composite reinforced with B4C particles. Indian Journal of Science and Technology, 12(2), 1–9. https://doi.org/10.17485/ijst/2016/v9i12/88073
- Hindi, J., Achutha Kini, U., & Sharma, S. S. (2020). A study of sliding wear behaviour of al 7075 grey cast iron reinforced composite using taguchi’s orthogonal array design. International Journal of Mechanical and Production Engineering Research and Development, 10(1), 165–171.
- Jitendra, M., Mistrya, & Piyush, P. G. (2019). Experimental investigations on wear and friction behaviour of Si3N4 reinforced heat-treated aluminium matrix composites produced using electromagnetic stir casting process. Composites Part B, 16(1), 190–204. https://doi.org/10.1016/j.compositesb.2018.10.074
- Kalkanli, A., & Yılmaz, S. (2008). Synthesis and characterization of aluminium alloy 7075 reinforced with silicon carbide particulates. Materials and Design, 29(9), 775–780. https://doi.org/10.1016/j.matdes.2007.01.007
- Kanayo, K., Kazeem, A., & Sanusi, O. (2015). Microstructural characteristics, mechanical and wear behaviour of aluminium matrix hybrid composites reinforced with alumina, rice husk ash and graphite. Engineering Science and Technology, 18(2), 416–422. https://doi.org/10.1016/j.jestch.2015.02.003
- Mahathaninwong, N. T., Plookphola, J., Wannasina, Wisutmethangoon, S., & Angoonb, W. (2012). T6 heat treatment of rheocasting 7075 Al alloy. Materials Science and Engineering, 53(2), 91–99. https://doi.org/10.1016/j.msea.2011.10.068
- Mahmoud, C., Khitouni, M., Jozwiak, K., Mesmacque, G., & Kolsi, A. (2010). Characterization of the mechanical properties changes in an Al–Zn–Mg alloy after a two-step ageing treatment at 70°and 135°C. Materials and Design, 31(3), 3134–3139. https://doi.org/10.1016/j.matdes.2009.12.033
- Mousavi Anijdan, S. H., & Sabzi, M. (2018). The effect of pouring temperature and surface angle of vortex casting on microstructural changes and mechanical properties of 7050al-3wt% SiC composite. Materials Science & Engineering A, 737(8), 230–235. https://doi.org/10.1016/j.msea.2018.09.057
- Mousavi Anijdan, S. H., Sabzi, M., Najafi, H., Jafari, M., Eivani, A. R., Park, N., & Jafarian, H. R. (2021). The influence of aluminum on microstructure, mechanical properties and wear performance of Fe–14%Mn–1.05%C manganese steel. Journal of Materials Research and Technology, 15(4), 4768–4780. https://doi.org/10.1016/j.jmrt.2021.10.054
- Musa, Y., Ozyurek, D., & Guru, M. (2016). The effects of precipitate size on the hardness and wear behaviours of aged 7075 aluminium alloys produced by powder metallurgy route. Arab Journal of Science and Engineering, 41(7), 4273–4281. https://doi.org/10.1007/s13369-016-2078-6
- Pazhouhanfar, Y., & Eghbali, B. (2018). Microstructural characterization and mechanical properties of TiB2 reinforced Al6061 matrix composites produced using stir casting process. Materials Science and Engineering A, 7(1), 172–180. https://doi.org/10.1016/j.msea.2017.10.087
- Rao, R. N., Das, S., Mondal, D. P., & Dixit, G. (2010). Effect of heat treatment on the sliding wear behaviour of aluminium alloy (Al–Zn–Mg) hard particle composite. Tribology International, 43(3), 330–339. https://doi.org/10.1016/j.triboint.2009.06.013
- Reda, Y., Abdel-Karim, Elmahallawi, Abdel-Karim, R., & Elmahallawi, I. (2008). Improvements in mechanical and stress corrosion cracking properties in Al 7075 via retrogression and re aging. Materials Science and Engineering, 48(5), 468–475. https://doi.org/10.1016/j.msea.2007.08.025
- Rupa Dasgupta, T., & Meenai, H. (2005). SiC particulate dispersed composites of an Al–Zn–Mg–Cu alloy: Property comparison with parent alloy. Materials Characterization, 54(2), 438–445. https://doi.org/10.1016/j.matchar.2005.01.012
- Sabzi, M., Dezfuli, S. M., & Balak, Z. (2019). “Crystalline texture evolution, control of the tribocorrosion behavior, and significant enhancement of the abrasion properties of a Ni-P nanocomposite coating enhanced by zirconia nanoparticles”. International Journal of Minerals, Metallurgy, and Materials, 26(8), 1020–1030. https://doi.org/10.1007/s12613-019-1805-x
- Sabzi, M., & Mousavi Anijdan, S. H. (2019). Microstructural analysis and optical properties evaluation of sol-gel heterostructured NiO-TiO2 film used for solar panels. Ceramics International, 45(3), 3250–3255. https://doi.org/10.1016/j.ceramint.2018.10.229
- Toptan, F., Alves, A. C., Kerti, I., Ariza, E., & Rocha, L.A. (2013). Corrosion and tribocorrosion behaviour of Al–Si–Cu–Mg alloy and its composites reinforced with B4C particles in 0.05 M NaCl solution. Wear, 306(10), 27–35. https://doi.org/10.1016/j.wear.2013.06.026
- Toptan, F., Alves, A. C., Kerti, I., Ariza, E., & Rocha, L. A. (2013). Corrosion and tribocorrosion behaviour of Al–Si–Cu–Mg alloy and its composites reinforced with B4C particles in 0.05 M NaCl solution. Wear, 306(10), 27–35. https://doi.org/10.1016/j.wear.2013.06.026
- Young, S. P., Lee, S. B., & Kim, N. J. (2003). Microstructure and mechanical properties of strip cast Al-Mg-Si-X alloys. Materials Transactions, 44(12), 2617–2624. https://doi.org/10.2320/matertrans.44.2617