Abstract
Lean implementation in the service sector has a dilemma related to defining the gap of the lean system and identifying the flaws in the processes which affect the overall performance and efficiency. This paper presents an innovative model that can help service companies to improve lean implementation and integrate appropriate Key Performance Indicators (KPIs) with the strategic goals. The aim of this paper is to also investigate different forms of waste that affect services performance by using the data of a global best practice. It also aims to apply and integrate the KPIs with Lean Management Tools to overcome the potential limitations of the traditional ones. As a first step of improvement, designing a new KPI lean method can lead to determining and reducing all different forms of existing wastes. Furthermore, such a method is expected to (i) improve the existing processes; (ii) enhance performance, (iii) increase time efficiency; and (iv) improve work accuracy. A new model that focuses on low-performance processes has been designed. The proposed model is also used to develop KPIs that are measurable and capable of detecting flaws and identify the possible improvements. When the model is continuously applied by service providers, the waiting time and non-adding value activities are expected to be significantly minimized. Likewise, monitoring and control of internal processes and activities can be improved. Furthermore, lean management is advantageous for the telecommunication sector as it allows a quick response to rapid changes in the telecom technology and, thus, improves the customer satisfaction.
1. Introduction
Nowadays, companies in the service sector use “Lean Management” to improve operational excellence, enhance continuous improvement and reduce processes waste. However, the lean concept is not always measurable neither aligned with companies’ strategies and objectives. This paper presents an innovative model that can help service companies to improve lean implementation and integrate appropriate Key Performance Indicators (KPIs) with the strategic missions and goals of these companies. Developing such a model is crucial due to the importance of the service sector as an economic activity began to emerge from early history of civilization to represent later 58% of the world’s GDP and employment of most modern economies.
The telecommunications industry has added a new aspect in the modern era. Thus, nowadays, it is considered as one of the most important sectors in economy and technology. Telecommunication companies face a lot of challenges within their systems, because they always need to be prepared to introduce the most modern technology to the markets and adapt with the rapid changes. Also, customers always want the best of the best in this sector so telecom companies must consider the changing in the consumer tastes by having an agile and flexible system with a high performance (Belwal & Amireh, Citation2018). Lean management is one of the key concepts that help organizations to maintain competitiveness and gain leverage in their business field. Lean management is defined as an optimization methodology that focuses on reducing cost and cycle time by eliminating the seven known kinds of wastes via scientific ways to determine what is important in terms of exceeding the common thinking patterns to improve the performance and efficiency of a process in any system (Ante et al., Citation2018; Goshime et al., Citation2019; Prado-Prado et al., Citation2020). Implementing and adopting the philosophy and the tools of manufacturing in all sectors not just the industrial one is called lean management (Bednarek et al., Citation2020). In this paper, lean management is the appropriate concept because it focuses on the telecommunication sector, as one of the service sectors. A better lean performance can be obtained by identifying the appropriate KPIs whose measurable values indicate the efficient achievements of the strategic objectives of an organization and meeting its goals. In general, KPIs are internal standards to measure the waste in a process and, thus, define its success or failure.
Progression in telecom technologies has become an unavoidable phenomenon because it is facing an increase in customers’ expectations of the service quality. This pattern of customer demand and the highly competitive environment are forcing the telecommunication companies to reject the traditional customer satisfaction model. Lean thinking is capable of affecting the Jordanian market positively, but currently lean thinking has not been really implemented in the service sector in Jordan. According to a survey conducted using Procera networks, the second in the list of worst customer services after the government services is the telecommunications industry (Narvekar, Citation2018).
The objectives and importance of this paper is to justify the use of lean management to (i) achieve excellency in the service sector, (ii) evaluate lean implementation within a company; (iii) use aligned KPIs with lean management to support and improve leading companies’ performance, quality, and efficiency; (iv) identify the areas where improvement is required by studying the current work performance; (v) analyze the root causes of the declination in performance levels; (vi) increase a processes performance level by modifying service provision operations and, thus, improving customer satisfaction; (vii) create an environment with continuous learning and process improvement; and (viii) recommend sustainable improvement methods to achieve an on-going lean environment.
ZAIN Telecommunication Company’s system was studied and investigated in detail, in order to develop and improve the performance of processes and achieve a high level of excellence. The company’s strategy focuses on: continuous improvement, customer satisfaction, achieving a high level of performance, and increasing competitiveness levels. Therefore, it was necessary to study their quality manual. ZAIN is currently considering meeting the customer requirements and monitoring information related to customers perception, in addition to adopting continuous improvement techniques as basic measurements of the performance of the quality management system. This study focuses on the company’s objectives and how they are affected by the company’s processes and policies which we think can be guaranteed by implementing lean management’s tools and principles. For a leading company such as ZAIN, their goal is not limited to achieving a good performance level, as they have already achieved it, but to basically being a fully customer focused organization that (i) performs a high level of accuracy; (2) competes for the first place in the market; and (iii) achieves an on-going journey of improvement which is considered to be the most important lean principles. A lean organization depends on an extensive and continuous improvement operation that has many aspects and indicates that the availability of a wide variety of tools is valid to conduct forms that ascertain lean objectives and principles. This study uses “seven waste” determining and eliminating methods to point out non-added value steps and to enhance the overall performance. Being not able to observe wastes and deal with them properly in any business system leads to a deterioration in efficiency and disruption of tools that control and reduce costs. in addition, it has negative effects on the relationship with customers and competitors. For telecom operators, tracking waste can be very difficult because of the nature of their business, their need to adapt to on-going variables and their constant quest to increase their competitiveness. In order to achieve flexibility in dealing with any possible changes, cost reduction and raising the level of customer satisfaction, systems of such institutions should be adapted to reduce any type of waste which can only be guaranteed with a full lean thinking culture. Lean thinking provides a workplace environment that strives always to continuous improvement by encouraging each and every employee in the organization to implement lean tools in the work processes from top to bottom. Traditional improvement approaches cannot increase the performance efficiency as a low-hanging fruit has already been harvested. In addition to that, outdated total quality management methods are not capable of meeting current changes. Also, lean management tools do not stop at curing the symptoms but they track the root causes of wastes on a long term. They also enable organizations to deliver a sustainable improvement and a competitive advantage. The main objective of this study is to propose a model for lean management that can be implemented in the telecommunication companies and in the service sector, where the gaps in the lean implementation are defined by the world best practice, after comparing the level of performance indicators for a company with the best global levels of these performance indicators. Furthermore, implementing the proposed model allows a company to better monitor and control the internal processes and activities by identifying well-constructed KPIs. The performance improvement, as a result, will affect different levels of activities (i.e., strategies and daily operations).
Supporting managers in their decisions to identify the processes which have wasted more than others in the telecommunication sector or in service sectors, in general, is the main practical implication of this paper. Furthermore, it can help managers to compare the performance of their processes with the best practice. On the other side, the theoretical implication of this research is summarized by utilizing the performance indicators and its worldwide best practice to identify how much the service sector is a lean system. As proved, telecommunication sector is one of the fastest improving service sectors. This requires a very fast response to these improvements for the sustainability of a company. However, it is one of the worst sectors in terms of the quality of customer service, where lean management can be a solution for both problems.
The research paper is organized as follows: the related studies are discussed in Section 2. Section 3 briefly describes the methodology of this research, whereas Section 4 discusses the results obtained for the model implementation. Finally, Section 5 concludes the whole paper and presents some future pointers to research.
2. Literature review
The Japanese made the philosophy of “Lean” in 1950s. Lean implementation started in manufacturing sectors where Japanese companies were delivering high-quality products at lower costs compared to western businesses. Lean methodology depends heavily on defining waste and applying lean tools to reach customer satisfaction and improve the quality in industries. Lean in service evolution started by Levitt (Citation1972) who transferred manufacturing logic to service operations. According to Womack and Jones (Citation1996), there are five lean principles to guide organizations in lean management. Such principles are Value, The value stream, Flow, Pull and Perfection. Several researchers have continued working on their work which is related to lean in the service sector. Comm and Mathaisel (Citation1998) explained how lean could be used and implemented further in the service sector. Lovelock and Wright (Citation2001) focused on some service aspects and developed a method to categorize services into service classes and delivery methods. Allway and Corbett (Citation2002) explained the overlapping between manufacturing and services sectors. Jones and Mitchell (Citation2006); Swank (Citation2003) focused on the flow of activities through the healthcare system. They adopted approaches to lean improvement such as a mapping process which is a tool used to identify inefficiency in the process and areas of waste. Apte and Goh (Citation2004) studied lean implementation in information-based services with a case study. Ahlstrom (Citation2004) presented the lean service principles and their implementation. Chase and Apte (Citation2007) explained the challenges faced in the service sector. Venkat and Wakeland (Citation2006) used simulation to study processes utilized in the service sector. Maleyeff (Citation2006) explained that there were many characteristics in the service system including the flow of information, the flow of a process across a function, and categorization of wasteful activities. He established a lean model aimed at enhancing the processes within companies and minimizing the seven wastes. Gray and Abbasi (Citation2007) studied the lean methodology to improve social and healthcare fields. Jørgensen et al. (Citation2007) explained the difficulties in lean. Sustainable lean implementation required performance improvement and development capabilities. Jones and Mitchell (Citation2006) and Kollberg et al. (Citation2007) focused on the supply chain of inputs and the purchasing practices in the healthcare system, and on applying lean supply partnership and inventory reduction approaches to improve responsiveness and reduce cost. Bicheno (Citation2008) wrote a book to introduce a set of tools for lean services.
Barraza et al. (Citation2009) explained that lean thinking was applied to improve the services given to public through the local councils and followed a case study approach in specific Spanish contexts. Piercy and Rich (Citation2009) discussed that the quality of a service and cost reduction are the most expected aspects of service businesses. They described a new meaning of a lean service. Their study covered processes such as total quality management (TQM), six sigma and kaizen initiatives. The study also found that lean was confused with six sigma, but this did not affect the implementation of a lean system. Qu et al. (Citation2011) identified many types of wastes such as service design waste, service item waste, service ability waste, service process waste and service delay waste. This study focused on waste analyses in the service sector. Alsmadi et al. (Citation2012) studied the difference in the lean practices and their relationships to a company performance between both manufacturing and service sectors in the UK. The outcomes showed that service organizations were interested in the soft practices of lean. In addition, they showed that the manufacturing services performance was not as expected in terms of supplier feedback, total productive maintenance and setup time. Additionally, the results confirmed a positive relationship between lean and a company performance. Ming-Te et al. (Citation2013) investigated the relationship between lean production and service and the improvement of the entire performance of the production and service. Azevedo and Sholiha (Citation2015) discussed that the product service system (PSS) started to make innovative strategy to face competitive global markets. One of the important aspects to be considered was the cost effect. They observed that the traditional costing system was not able to deal with company’s transformation. They explained that lean accounting with its value stream costing (VSC) might be able to provide comprehensive cost information and support company’s transformation into a successful company in the global market. Bertoni et al. (Citation2015) discussed that the tools and methods that were developed in Value Driven Design had to be applied at the initial design stages in the development of a lean product service. Bhasin (Citation2015) focused on the critical success factors of implementing lean to sustain a continuous improvement culture in the long run. Sassanelli et al. (Citation2015) explained that success of Product Service Systems (PSS) depends on the decisions taken when PSSs were designed, developed, and engineered. Niewiadomski et al. (Citation2018) explained the barriers to effective implementation of lean management principles and studied empirical exemplification in the agriculture sector. Some places within the service sector such as health, finance, banks, telecommunication, and insurance have mostly applied lean principles. Among these sectors, the health sector has applied them the most. Recently lean management has been widely used in many sectors like construction processes, maintenance operations, hospitals performance, the food sector and higher education institutions (Eldeep et al., Citation2022; Klein et al., Citation2022; Rundall et al., Citation2021; Shou et al., Citation2021; Yeshitila et al., Citation2021). Furthermore, some recent studies have focused on developing the soft and hard skills during the lean training (Lista et al., Citation2022). Yeshitila et al. (Citation2021) integrated the safety system and the occupational safety system with the lean thinking. In addition, the human side was also considered in their study, where accidents and incidents in the oil and gas industry were considered as a part of the waste which had been reduced by the lean management.
According to Zuhdi (Citation2012), the global competition between the telecom companies changed with the beginning of the internet age. This opened the doors for new entrants to the telecommunications market. Rapid technological changes forced telecom companies to invest heavily in their network infrastructure and new technologies to meet the needs of customers and provide them with high quality of the service. Also, telecom companies faced challenges related to increasing their profit after spending massive costs on network upgrades and continuous developments. According to Sujata et al. (Citation2015), another challenge was that the telecom companies, especially the cellular and telephone companies, were facing the beginning of Over The Top service providers. Due to the global competition in the telecom industry nowadays, companies need to provide a high-quality service to its customers to stay at the top of this competition. Lee (Citation2013) suggested that the telecom companies need to provide high-quality services to its customers to compete globally. In general, customers’ satisfaction can increase when a high-quality service is provided and, as a result, customers can become loyal to the service providers. Therefore, effective customer service always leads to a customer satisfaction (Khan & Afsheen, Citation2012). For telecom companies providing a high-quality service, quality management, one of the most critical management strategies, has to be included. Lean management is one of the quality management tools which provide better results by continuous improvement and waste reduction (Chiarini, Citation2013).
According to Cruz Villazón et al. (Citation2020), the KPIs, which are used for lean management, are classified into seven categories, namely, financial, strategic, tactic, operational, life cycle, safety, and sustainability KPIs. Under the umbrella of these categories, more than 30 KPIs are listed. Many other studies listed the KPIs which were used to develop the lean system (Ante et al., Citation2018; Singh et al., Citation2021; Todorov et al., Citation2019). The majority of these indicators focus on the performance of the lean system. In this research work, the indicators used are those employed to measure the performance of the processes.
The telecom companies have to consider their procedure as a production line instead of treating each division individually. Narvekar (Citation2018) explained that telecom companies should see all segments of their processes as continuous lines that produce only what their clients’ need. Each process defined should add value to the services delivered. According to Narvekar (Citation2018) telecom companies waste almost 30% of the process-related costs. A lean approach can help these companies to reduce waste. Their research suggested that the telecom companies may become unable to compete if they do not implement lean in their processes and departments. Lately, Abu Salim et al. (Citation2018); Salim et al. (Citation2018) identified the reality of the lean management in Jawwal Company from the point of view of its employees. Also, they identified creativity levels of the workers in Jawwal in many dimensions such as problem solving, acceptance of risks, decision making, changeability, and encouragement of creativity. Msallam et al. (Citation2019) identified the extent of the technical colleges’ commitment to the application of the lean management. Shamsuzzaman et al. (Citation2018) implemented lean in the telecommunication sector to improve the order fulfillment process. In their study, they reduced the fulfillment process time by more than 40%. Sinha et al. (Citation2020) utilized the internal and external customers’ feedback to improve the service quality in the telecommunication sector, where AP et al. (Citation2020) investigated the effect of lean management on the overall improvement of the telecommunication sector in Nigeria. Lestari and Dachyar (Citation2020) presented a case for Indonesia to incorporate lean in quality function deployment in the telecommunication sector. Selvaraju et al. (Citation2019) investigated the critical success factors of Lean Six Sigma and their effects on the performance of the telecommunication supply chain. A green lean for a public sector, where telecommunication sector is considered as one of the public sectors, is developed by Sandhya and Raju (Citation2018). Lorenz et al. (Citation2020) studied the agile principles as a way for a rapid response in Swiss telecommunication company. Therefore, the literature gap identified is the utilization of the best practice in other companies to identify wastes in various processes whose performance indicators are usually compared with the best values provided by KPI institute (KPI-Institute, Citation2020).
3. Methodology
The aim of this study is to design an innovative model for the development of leading companies in the industrial service sector. Therefore, a sophisticated service company was sought to be a practical model from which this idea emerged. This approach is used to guarantee that the model reflects a realistic actual business experience rather than just a theoretical plan. Lean management can improve companies as it focuses on more than just doing the job efficiently, but continuously developing it to precede customer expectations and be a strong competitor of companies in the same field. This can be attributed to that implementing lean management tools on service companies includes eliminating all types of waste and non-added value steps in various processes using several methods. A survey consisting of 28 various questions divided into five categories has been designed and carried-out in order to understand and measure lean implementation at ZAIN Company using lean assessment tools and gap analysis.
One of the most important requirements to enhance the implementation of lean management is the scientific employment of lean management tools, which depends significantly on numerical data and a continuous measurement process whose pivotal impact has been observed on the model proposed in this study. In ZAIN telecom company, it can be noticed that the design of an evolutionary model for the level of lean implementation in it and in a service company, in general, needs to start from the ability of measuring the implementation level effectively for the basic operations, where the current lean implementation cannot be numerically measured and conducted dependently from the organization’s vision and mission. Therefore, the performance indicators which are considered to be perfect tools used in the measurement process are very critical. To overcome these limitations, this study developed a new model that integrates KPIs and the lean strategic objectives related to the company’s strategy to be used in developing and enhancing the performance of the service industrial sector (Cortes et al., Citation2016). In order to construct this model, DMAIC method, which is a lean six sigma method, was used to organize research and development process (Gershon & Rajashekharaiah, Citation2013). In general, it includes five steps that are based on several tools, methods, and models, as shown in Figure . The assumptions made in this study are that (i) there is no interaction between the processes’ performances and, thus, processes are assumed to be independent, this means that improving or changing a process does not affect the performance of other processes; (ii) changing a KPI has no impact on other KPIs; and (iii) the results obtained by KPI institute are valid and correct. In real cases, there is an interaction between processes and, thus, a change on one process or KPI affects actually other processes and KPIs to a level related to the level of its relationship with these processes and KPIs.
Figure 1. Methodology and the five main DMAIC steps for integrated lean KPIs implementation.
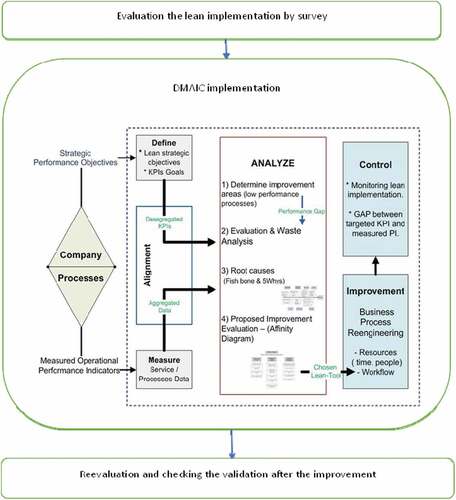
The DMAIC is started by the Defining process that has been conducted through the several steps as follows: Defining the company’s strategic goals and objectives. After a brief study for ZAIN’s quality manual and interviewing its managers, it was shown that their main objectives are: achieving a high performance and quality, providing the best and the most innovative service in the class, and increasing customer satisfaction levels (Atkinson, Citation2004). Defining lean objectives that achieve the company’s strategy. The objectives of the lean management which are closely related to the company’s strategy have been identified. Such objectives are high-performance efficiency, continuous improvement, customer satisfaction, eliminating the non-added value effort and increasing competitiveness. Defining the requirements that represent the company’s lean strategy. As lean objectives are determined, they can then be translated into detailed functional measurable requirements that can be utilized to improve the performance by being leaner oriented. Choosing the appropriate KPIs for lean implementation. The KPIs that will be improved using lean management were chosen based on the previously mentioned requirements. Using ARENA software, the audit process was conducted before and after re-engineering to compare the results and to observe the improvement of KPIs and how that can enhance the process in the future. Further explanation of used tools and results is presented in the next sections of this paper. Aligning KPIs results with lean wastes. Measurement process to measure the performance of the systems, then identified the improvement area and the waste, followed by improvement and controlled process.
The validity of the model is checked after implementation, and the survey which is conducted before the implementation is repeated after the implementation. The results obtained are explained in the discussion section.
Results
The questionnaire was distributed to the whole target population, which is 63 managers and supervisors in the company. It is worth mentioning that 55 responses were received. The survey did not contain details to picture the performance of lean implementation. Its questions were designed by conducting a survey about measuring lean implementation based on Servqual model (Ghimire et al., Citation2020). The questionnaire was presented to the target group using a five-point Likert scale, which is selected after estimating the expected answers for each question, whereas the 5-point scale was the most appropriate scale to collect valuable feedback. Furthermore, the 28 questions of the survey were developed and selected based on the literature related to lean implementation in the service sector. The results of the questionnaire are shown in Table .
Table 1. Questionnaire for lean implementation in Zain telecommunication company and score results
The output resulting from conducting the survey was the “Gap Analysis”. In general, the gap analysis, as a graphical display of the group responses, shows the answers space for each question for comparison purposes. The gap analysis presented in Figure shows that lean implementation is required to improve the performance.
The definition step, as a merging process, was performed by examining the relationships between ZAIN’s strategy and the goals of lean management to determine the most important aspects required. The KPIs were then classified according to the requirements for achieving the main fundamental lean aspects. Such KPIs focus on the requirements necessary to achieve each of the lean management strategic objectives.
In order to monitor KPI values, they were expressed as mathematical formulas used to identify a target value for each. In this project, such formulas and the target values were determined by specialists in the KPI institute (KPI-Institute, Citation2020), where the target values are the best practice in the whole world. Such KPIs are shown in more detail in Table .
Table 2. The requirements and the KPIs defined in Step 1
The measurement step aims to determine low-performance processes by calculating the current KPIs values using the formulas associated with each functional requirement, followed by comparing the actual values with the target values. The processes of interest in this case study are: Corrective and Preventive Actions procedure, Improvement Project procedure, Mobile Device Management procedure, Internal Audit procedure, Information Security Management procedure, Document Control procedure, Handling Customers’ Complaints procedure and Enterprise Risk Management procedure. The results of this step are summarized in Table , which shows that 82% of the indicators did not reach the target value.
Table 3. KPI average results
The analysis step focuses on the low-performance procedures identified in the measurement step by implementing waste analysis, cause and effect diagram, five whys, and affinity diagram. According to Lean culture, waste analysis, as one of the main principles of lean management, focuses on removing any non-added value activities from the customer’s perspective. One of the most basic classifications of waste types is the “Seven Wastes” (i.e., delay, duplication, unclear communication, incorrect inventory, unnecessary movement, errors and opportunity lost), which has been used to identify the types of wastes in each process.
The cause-and-effect diagram and 5 why’s tools were then implemented to track the root causes and discuss the most effective ones among them. In order to enhance the outcome of the analysis process, the appropriate development method was selected using the Affinity Diagram, which is an organized output from a brainstorming session for a group that includes experts and employees as the most knowledgeable of the processes. Once the ideas were collected from such a group, they are clustered according to their similarity. The result of this step is shown in Table , where the waste types are explained for the lowest performance procedures.
Table 4. Waste analysis in low-performance procedures
After studying and analysing the root causes, it was found that the causes that led to the largest amount of waste were related to the following practices: insufficient training, inaccurate data and unclear communication between management and employees. As a validation of the mentioned main causes, the following data was collected in order to show the problem’s size. The data showed that there were six lean training that were conducted during 3 years. It also showed that the percentage of the average reporting frequency between the management and employees was 45% of the requested level for 3 years. Conducting interviews was required to understand some of the practices that negatively affect lean implementation. The results showed that 73.6% of employees were unsatisfied with the management’s communication level with the employees, 68.74% of employees said that the employees’ allocating process was not good. The 5 why’s technique was then implemented to identify the root causes behind not conducting audits on schedule, where Internal Audit process was carried out two times annually for each department by a team of auditors consisting of nine employees. The flaw in this process was discovered to be the delayed implementation of the scheduled audits because of the rigid method of selecting auditors (i.e., an auditor is specified for a specific department with a specific deadline). In case one of the auditors is not available at the specified time for the audit process, it is postponed, and this may lead to postpone the following audit which leads to a cumulated state of postponing. In order to identify the root causes of the delay in improvement projects implementation, the 5 why’s technique was conducted. It was noted that the percentage of planned process improvements which were implemented is few due to that the planned improvements are not aligned with strategic goals, and the planned improvement projects are not consistent with the actual workflow. After a deep study, it was found that these factors resulted from the fact that there is no real motivation for the employees to suggest improvement initiatives, in addition to not taking the resources allocated during the planning process. Dealing with customer complaints is a critical process, as this impacts their overall satisfaction with the company, so it was necessary to identify the root causes that affect the time spent solving these problems in addition to the causes that led to them. By implementing the 5 why’s technique for further analysis, it was found that most of the complaints were about poor quality. While studying the aspects of low performance in the customer complaints process, it was found that a large number of customer complaints were due to poor quality and that a long time was taken to solve their complaints. During studying the process in detail, it was found that this phenomenon was related to the inability of first-line employees to efficiently solve customer problems and repeatedly registering a specific complaint when received repeatedly from the same client.
Improvement step uses Business Process Re-Engineering method, which is discovered in the analysis step as the most appropriate method for the investigated case in this study as it helps organizations to enhance performance indicators validity (e.g., quality, lead time, cost, service, etc.) through re-visualizing the workflow to overcome its defects. Such a step is utilized to reduce process time, increase the business volume and improve customer service (Bitner et al., Citation2008). One of the most important tools that can be employed through the presented model is concurrent engineering, where the work is done simultaneously instead of cascading the tasks consecutively. The improvement areas cannot be determined only through a specific department because they affect and are affected by all departments, so concurrent engineering should be implemented in the planning stage. It can be seen how these adjustments can affect time reduction and repetition and, thus, can improve the overall performance efficiency, competitiveness, and customer satisfaction. Figure summarizes the development of improvement procedure. The improvement processes were designed as a series of processes but in case a failure or error occurs in any of these processes, the case is returned back to any of the previous processes for adjustment and correction.
Internal Audit Procedure Improvement was conducted using Lean principles and business process re-engineering (BPR) in order to make the process more effective and reduce delay (Zaini & Saad, Citation2019). To achieve these improvements, concurrent engineering is necessary to be applied through holding an annual meeting for all departments with the audit team in order to prepare the audit plan together and make sure it suits all departments to reduce delays by the auditees. The auditors’ allocating process has been edited so that when it is time for auditing in a specific department, any available auditor at that time should conduct the audit. Therefore, there should be no time wasted waiting for a specific auditor to perform specific auditing. Using ARENA software, we simulated the audit process before and after re-engineering to compare the results and to observe the improvement of KPIs and how that can enhance the process in the future. Partial future system performance evaluation was conducted using ARENA® simulation software, where the model developed for these processes was constructed by connecting the appropriate blocks which show the flows of processes. Such a step was followed by comparing the results before and after the process of re-engineering. The simulation model showed that the average delay time for the audit was reduced by about 70%. Finally, to improve customer complaints procedure, a process of re-engineering is implemented for the complaints receiving process which, in general, includes improving the performance of the first-line employees and developing the process of receiving complaints to reduce redundancy and errors. Improving the performance can be achieved through good training of the first-line employees to provide them with the skills needed to deal with the customer and the necessary knowledge of the technical details about complaints they usually have to deal with. The effort to resolve complaints can be greatly reduced by streamlining and organizing receiving complaints process. Complaints can be classified so that a specific complaint is registered more than once if it is received repeatedly from the same client (Bonaccorsi et al., Citation2011).
The control step consists of monitoring the lean implementation progress and evaluating it continuously using the presented model of KPIs designing. The aim of this step is to monitor the improved process and forecast the impact of different proposed improvements on the future performance by developing a continuous and automatic monitoring plan. This monitoring plan will track the success of the updated process. Once it is in place, the company monitors and continually updates the current effective method. The monitoring plan is based on (i) quality control plan to document what is required to keep an upgraded process at its existing level; (ii) Statistical process control (SPC) for checking a process performance; and (iii) using 5S to establish a workshop suitable for visual control.
4. Discussion of results
With the improvement project reaching its final stages, the results of the improvement actions became clear as shown in Table . The benefits obtained by the model developed to achieve lean objectives are outlined for each process.
Table 5. Improvement actions and their benefits
These benefits mentioned in the previous Table had shown to be effective as can be noticed in the results of the gap analysis was held after the improvements have been implemented, which shows the reduction in the gap in the areas were determined to be the weakest among the studied areas were taken in consideration during the before gap analysis. The Gap Analysis results are shown in Figure . Where the result shows the capability of the model to improve the performance, which is a good indication of the validity of the model.
Essentially, gap analysis was used to show the weakest area which is far away from the target and used to figure out the improvement areas to fill that gap between the current and target states (i.e., bridging the gap) by outlining the factors that contribute to that using DMAIC method. Gap analysis was implemented on the survey presented in Appendix A in order to evaluate the lean performance in ZAIN Company. The gap analysis shown in Figure shows a weak performance that is drifted away from the desired one. Using the gap analysis, the weakest areas that were identified in Figure and had significant improvement are “Process & System” and “Customer Focus”. This can be conducted using Lean methodologies and tools (Kulshreshtha, Citation2019). Based on the questionnaire presented earlier, it can be concluded that the area of development of lean management in the company is still wide and the level of its application is still at its medium levels. When planning to implement lean management it has been shown that the traditional approach does not guarantee achieving the objectives, this being due to many limitations such as not taking into consideration the system’s nature, the separation between lean objectives and the company’s strategy, dealing with the system’s components as individuals, and unjustified performance measurements of the future system.
The flexibility of the resources in the service sector that are required to achieve the lean objectives was one of the professional inferences. This was noticeable from the results obtained for most of the procedures (e.g., the internal audit procedure). Such procedures, for instance, required human resources to achieve the main activities. In addition, during the planning of these procedures, a specified person(s) was selected for each activity. Without flexibility, the implementation of the plan’s activities could be delayed.
This study seeks to ensure that the proposed improvements can have an impact on the operational performance and on the strategic improvement objectives of the company where they were conducted to guarantee the most efficient emergence of the company’s strategy and its implementation. This work combined key performance indicator (KPI) concept with lean principles to design an accurate measurement to support lean implementation. The aim of this new approach is to build indicators and methods to evaluate future lean implementation aligned with the strategic missions of the company and to activate the interactions between the system’s components. The most obvious effect of this modern paradigm is that it can transform any institution into a lean organization through performance measurement as a substantial part of the overall system serves lean objectives.
5. Conclusions and recommendations
In this research work, the performance measurement indicators were integrated with the principles of lean management and its objectives via developing a model. Such a model was implemented in a telecommunication company in the service sector, and it can also be used by similar or other service and industrial sectors after performing technical adjustments to the model to suits their system’s nature and their future goals. Such a model is supported by measurement systems that are capable of detecting flaws, identifying areas where improvements are required and defining tools required to achieve a permanent lean management culture, which grows continuously and eliminate different formulating waste types. Therefore, the proposed model can help companies to be at the top of their businesses internationally by focusing on the objectives and achievements of lean management implementation. The proposed model was implemented in ZAIN Company, as a telecommunication company. The implementation of the model that was directed to focus on the strategy of the company itself was highly effective, as it linked this strategy with lean management and goals. Then, the strategy was translated into more detailed, precise and measurable requirements that were capable of producing useful KPIs that can be used in making decisions. The decisions resulted from numerical data analysis were activated through the business re-engineering process, where improvements mainly focused on the process activities and their functionality to work in a highly efficient manner (i.e., less time and effort, and better and more accurate results). According to the re-engineering process, the low-performance processes that negatively affected the level of lean in ZAIN were defined and then improved. Likewise, waiting time in the internal audit process was reduced by approximately 70%. Furthermore, the project improvement procedure’s workflow was modified so that activities with non-added value were eliminated. In addition, the method of receiving and classifying complaints received from customers was improved by resolving complaints faster and, thus, increasing customer satisfaction. As proven in this paper, the presented model can be considered practical and capable of developing operations on a strategic level to enhance the lean implementation in institutions. Therefore, it is recommended that service-sector companies apply this model in their systems and integrate it into their development plans to enhance the overall performance level. For the model to work as expected, one needs to pay attention to the data collected, in other words the data need to be accurate and precise. In addition, a continuous measurement process should be maintained to ensure the activation of the appropriate KPIs. It is also recommended to analyze the data collected so that the causes of problems are always clear and ready to help in solving such problems. Furthermore, a permanent control and monitoring process to sustain the improvement process is another crucial requirement. In the future, it is advantageous to develop an intelligent as well as dynamic lean management system that can adopt new telecommunication technologies and adapt to include them. Such an intelligent lean management system can have a significant implication in reducing the waste of assets and efforts when the companies upgrade their systems to adopt any new technology in the telecom sector. This idea is summarized by making the lean system an intelligent and dynamic one, in other word this means that a company system can perceive the changes that happened or will happen and respond to them in an efficient way based on a built-in algorithm developed based on the history of the system.
However, this study is limited to the data collected from the company and from its employees. Thus, the accuracy of this data is critical. Although, this study is implemented in a telecommunication company, it can be adapted to any other service company by updating the KPIs.
Acknowledgements
Researchers would like to thank Zain Telecommunication Company – Jordan for all the support they have provided to conduct this study.
Disclosure statement
No potential conflict of interest was reported by the author(s).
Additional information
Funding
References
- Abu Salim, S. S., Msallam, A. A., Al-Hila, A. A., Abu Naser, S. S., & Al Shobaki, M. J. (2018). The dimensions of the lean management of jawwal between theory and practice. International Journal of Academic Management Science Research (IJAMSR), 2(10), 52–19. http://dstore.alazhar.edu.ps/xmlui/handle/123456789/185
- Ahlstrom, P. (2004). Lean service operations: Translating lean production principles to service operations. International Journal of Services Technology and Management, 5(5–6), 545–564. https://doi.org/10.1504/IJSTM.2004.006284
- Allway, M., & Corbett, S. (2002). Shifting to lean service: Stealing a page from manufacturers’ playbooks. Journal of Organizational Excellence, 21(2), 45–54. https://doi.org/10.1002/npr.10019
- Alsmadi, M., Almani, A., & Jerisat, R. (2012). A comparative analysis of Lean practices and performance in the UK manufacturing and service sector firms. Total Quality Management & Business Excellence, 23(3–4), 381–396. https://doi.org/10.1080/14783363.2012.669993
- Ante, G., Facchini, F., Mossa, G., & Digiesi, S. (2018). Developing a key performance indicators tree for lean and smart production systems. IFAC-PapersOnLine, 51(11), 13–18. https://doi.org/10.1016/j.ifacol.2018.08.227
- AP, A., EK, A., Nm, I., Ee, I., & Tan, A. W. K. (2020). Lean management and performance of telecommunication firms: The mediating role of workplace structure. Cogent Business & Management, 7(1), 1761637. https://doi.org/10.1080/23311975.2020.1761637
- Apte, U. M., & Goh, C.-H. (2004). Applying lean manufacturing principles to information intensive services. International Journal of Services Technology and Management, 5(5–6), 488–506. https://doi.org/10.1504/IJSTM.2004.006280
- Atkinson, P. (2004). Creating and implementing lean strategies. Management Services, 48(2), 18. https://nzbef.org.nz/wp-content/uploads/2019/05/Article-Creating-and-Implementing-Lean-Strategies.pdf
- Azevedo, A., & Sholiha, M. A. (2015). Innovative costing system framework in industrial product-service system environment. Procedia Manufacturing, 4, 224–230. https://doi.org/10.1016/j.promfg.2015.11.035
- Barraza, M. F. S., Smith, T., Dahlgaard‐Park, S. M., & Mi Dahlgaard‐Park, S. (2009). Lean- kaizen public service: An empirical approach in Spanish local governments. The TQM Journal, 21(2), 143–167. https://doi.org/10.1108/17542730910938146
- Bednarek, M., Buczacki, A., Bielakowski, L., Gladysz, B., & Bryke, M. (2020). Postgraduate studies on lean management—a review of initiatives. Education Sciences, 10(8), 197. https://doi.org/10.3390/educsci10080197
- Belwal, R., & Amireh, M. (2018). Service quality and attitudinal loyalty: Consumers’ perception of two major telecommunication companies in Oman. Arab Economic and Business Journal, 13(2), 197–208. https://doi.org/10.1016/j.aebj.2018.11.003
- Bertoni, A., Bertoni, M., Panarotto, M., Johansson, C., & Larsson, T. (2015). Expanding value driven design to meet lean product service development. Procedia CIRP, 30, 197–202. https://doi.org/10.1016/j.procir.2015.02.153
- Bhasin, S. (2015). Lean management beyond manufacturing (Vol. 10). Springer.
- Bicheno, J. (2008). The lean toolbox for service systems. PICSIE books.
- Bitner, M. J., Ostrom, A. L., & Morgan, F. N. (2008). Service blueprinting: A practical technique for service innovation. California Management Review, 50(3), 66–94. https://doi.org/10.2307/41166446
- Bonaccorsi, A., Carmignani, G., & Zammori, F. (2011). Service value stream management (SVSM): Developing lean thinking in the service industry. Journal of Service Science and Management, 4(4), 428. https://doi.org/10.4236/jssm.2011.44048
- Chase, R. B., & Apte, U. M. (2007). A history of research in service operations: What’s the big idea? Journal of Operations Management, 25(2), 375–386. https://doi.org/10.1016/j.jom.2006.11.002
- Chiarini, A. (2013). Waste savings in patient transportation inside large hospitals using lean thinking tools and logistic solutions. Leadership in Health Services, 26(4), 356–367. https://doi.org/10.1108/LHS-05-2012-0013
- Comm, C. L., & Mathaisel, D. F. (1998). Evaluating teaching effectiveness in America’s business schools: Implications for service marketers. Journal of Professional Services Marketing, 16(2), 163–170. https://doi.org/10.1300/J090v16n02_09
- Cortes, H., Daaboul, J., Le Duigou, J., & Eynard, B. (2016). Strategic lean management: Integration of operational performance indicators for strategic lean management. IFAC-PapersOnLine, 49(12), 65–70. https://doi.org/10.1016/j.ifacol.2016.07.551
- Cruz Villazón, C., Sastoque Pinilla, L., Otegi Olaso, J. R., Toledo Gandarias, N., & López de Lacalle, N. (2020). Identification of key performance indicators in project-based organisations through the lean approach. Sustainability, 12(15), 5977. https://doi.org/10.3390/su12155977
- Eldeep, A. M., Farag, M. A., & Abd El-hafez, L. (2022). Using BIM as a lean management tool in construction processes–A case study. Ain Shams Engineering Journal, 13(2), 101556. https://doi.org/10.1016/j.asej.2021.07.009
- Gershon, M., & Rajashekharaiah, J. (2013). How many steps to quality? From Deming cycle to DMAIC. International Journal of Productivity and Quality Management, 11(4), 475–489. https://doi.org/10.1504/IJPQM.2013.054271
- Ghimire, P., Ghimire, P., & Acharya, M. (2020). SERVQUAL Questionnaire based Health Service Quality Assessment in a Private Hospital of Western Nepal. Nepal Journal Of Medical Sciences, 5(1), 79–85. https://doi.org/10.3126/njms.v5i1.36958
- Goshime, Y., Kitaw, D., & Jilcha, K. (2019). Lean manufacturing as a vehicle for improving productivity and customer satisfaction: A literature review on metals and engineering industries. International Journal of Lean Six Sigma, 10(2), 691–714. https://doi.org/10.1108/IJLSS-06-2017-0063
- Gray, J. M., & Abbasi, K. (2007). How to get better value healthcare. Journal of the Royal Society of Medicine, 100(10), 480-480. https://doi.org/10.1177/014107680710001019
- Jones, D., & Mitchell, A. (2006). Lean Thinking for the NHS (Vol. 51). NHS confederation London.
- Jørgensen, F., Matthiesen, R., Nielsen, J., & Johansen, J. (2007). Lean maturity, lean sustainability. In J. Olhager, & F. Persson (Eds.), Advances in production management systems (pp. 371–378). Boston: Springer.
- Khan, S., & Afsheen, S. (2012). Determinants of customer satisfaction in telecom industry a study of telecom industry peshawar KPK Pakistan. Journal of Basic and Applied Scientific Research, 2(12), 12833–12840.
- Klein, L. L., Vieira, K. M., Marçal, D. R., & Pereira, J. R. L. (2022). Lean management practices perception and their influence on organizational performance in a public higher education institution. The TQM Journal. https://doi.org/10.1108/TQM-11-2021-0311
- Kollberg, B., Dahlgaard, J. J., & Brehmer, P. O. (2007). Measuring lean initiatives in health care services: Issues and findings. International Journal of Productivity and Performance Management, 56(1), 7–24. https://doi.org/10.1108/17410400710717064
- KPI-Institute. (2020). KPI Institute Homepage. http://kpiinstitute.org/
- Kulshreshtha, R. (2019). Analysis on the implementation of lean tools and techniques in IT engineering service industry in Ireland. Dublin Business School.
- Lee, H. S. (2013). Major moderators influencing the relationships of service quality, customer satisfaction and customer loyalty. Asian Social Science, 9(2), 1. https://doi.org/10.5539/ass.v9n2p1
- Lestari, D. P., & Dachyar, M. (2020). Improvement of service quality for customer satisfaction with lean six sigma method and development quality function deployment. Case: Telecommunication company in Indonesia. International Journal of Advanced Science and Technology, 29(7), 3605–3613. http://sersc.org/journals/index.php/IJAST/article/view/17661
- Levitt, T. (1972). Production-line approach to service. Harvard Business Review, 50(5), 41–52. https://hbr.org/1972/09/production-line-approach-to-service
- Lista, A. P., Tortorella, G. L., Bouzon, M., Thürer, M., & Jurburg, D. (2022). Soft and hard skills development in lean management trainings. International Journal of Lean Six Sigma, 13(5), 1137–1158. https://doi.org/10.1108/IJLSS-06-2021-0116
- Lorenz, R., Bäckert, L., & Heck, J. (2020). Principles of operational agility: A case study of a swiss telecommunication company. Die Unternehmung, 74(2), 173–186. https://doi.org/10.5771/0042-059X-2020-2-173
- Lovelock, C., & Wright, L. (2001). Principles of service marketing and management. Prentice Hall.
- Maleyeff, J. (2006). Exploration of internal service systems using lean principles. Management Decision, 44(5), 674–689. https://doi.org/10.1108/00251740610668914
- Ming-Te, L., Kuo-Chung, M. A., & Pan, W.-T. (2013). Using data mining technique to perform the performance assessment of lean service. Neural Computing and Applications, 22(7), 1433–1445. https://doi.org/10.1007/s00521-012-0848-y
- Msallam, A. A., Abu-Naser, S. S., Al Shobaki, M. J., & Al-Habil, W. I. (2019). Computerized management information systems and its relationship to improving the job performance of the employees of the palestinian cellular telecommunications company-jawwal. International Journal of Academic Information Systems Research (IJAISR), 3(1), 15–28. http://ijeais.org/wp-content/uploads/2019/01/IJAISR190103.pdf
- Narvekar, S. (2018). implementing agile lean in telecom industry. Harrisburg University of Science and Technology. http://digitalcommons.harrisburgu.edu/pmgt_dandt/29
- Niewiadomski, P., Pawlak, N., & Tsimayeu, A. (2018). Barriers to effective implementation of lean management principles-empirical exemplification in the industry of agricultural machinery. LogForum, 14(4), 563–576. https://doi.org/10.17270/J.LOG.2018.308
- Piercy, N., & Rich, N. (2009). Lean transformation in the pure service environment: The case of the call service centre. International Journal of Operations & Production Management, 29(1), 54–76. https://doi.org/10.1108/01443570910925361
- Prado-Prado, J. C., García-Arca, J., Fernández-González, A. J., & Mosteiro-Añón, M. (2020). Increasing competitiveness through the implementation of lean management in healthcare. International Journal of Environmental Research and Public Health, 17(14), 4981. https://doi.org/10.3390/ijerph17144981
- Qu, L., Ma, M., & Zhang, G. (2011). Waste analysis of lean service. Paper presented at the 2011 international conference on management and service Science. https://doi.org/10.1109/ICMSS.2011.5998793
- Rundall, T. G., Shortell, S. M., Blodgett, J. C., Henke, R. M., & Foster, D. (2021). Adoption of Lean management and hospital performance: Results from a national survey. Health Care Management Review, 46(1), E10–E19. https://doi.org/10.1097/HMR.0000000000000287
- Salim, S. S. A., Msallam, A. A., Al Hila, A. A., Abu-Naser, S. S., & Al Shobaki, M. J. (2018). The role of the lean management in promoting the creativity of jawwal from the point of view of its employees. International Journal of Academic Information Systems Research (IJAISR), 2(11), 15–33. http://dstore.alazhar.edu.ps/xmlui/handle/123456789/186
- Sandhya, G., & Raju, R. (2018). Development of a Green Lean Six Sigma model for public sectors. International Journal of Lean Six Sigma, 9(2), 238–255. https://doi.org/10.1108/IJLSS-02-2017-0020
- Sassanelli, C., Pezzotta, G., Rossi, M., Terzi, S., & Cavalieri, S. (2015). Towards a lean Product Service Systems (PSS) design: State of the art, opportunities and challenges. Procedia CIRP, 30, 191–196. https://doi.org/10.1016/j.procir.2015.02.123
- Selvaraju, M., Bhatti, M. A., Sundram, V. P. K., & Azmir, S. (2019). The influence of critical success factors of Lean Six Sigma towards supply chain performance in telecommunication industry, Malaysia. Int. J Sup. Chain. Mgt, 8(6), 1062. https://ojs.excelingtech.co.uk/index.php/IJSCM/article/view/3197
- Shamsuzzaman, M., Alzeraif, M., Alsyouf, I., & Khoo, M. B. C. (2018). Using lean six sigma to improve mobile order fulfilment process in a telecom service sector. Production Planning & Control, 29(4), 301–314. https://doi.org/10.1080/09537287.2018.1426132
- Shou, W., Wang, J., Wu, P., & Wang, X. (2021). Lean management framework for improving maintenance operation: Development and application in the oil and gas industry. Production Planning & Control, 32(7), 585–602. https://doi.org/10.1080/09537287.2020.1744762
- Singh, C., Singh, D., & Khamba, J. (2021). Understanding the key performance parameters of green lean performance in manufacturing industries. Materials Today: Proceedings, 46, 111–115.
- Sinha, A. A., Rajendran, S., Nazareth, R. P., Lee, W., & Ullah, S. (2020). Improving the service quality of telecommunication companies using online customer and employee review analysis. Quality Management Journal, 27(4), 182–199. https://doi.org/10.1080/10686967.2020.1809581
- Sujata, J., Sohag, S., Tanu, D., Chintan, D., Shubham, P., & Sumit, G. (2015). Impact of over the top (OTT) services on telecom service providers. Indian Journal of Science and Technology, 8(S4), 145–160. https://doi.org/10.17485/ijst/2015/v8iS4/62238
- Swank, C. K. (2003). The lean service machine. Harvard Business Review, 81(10), 123–130. https://hbr.org/2003/10/the-lean-service-machine
- Todorov, M., Jovanoskiz, B., & Minovski, R. (2019). Key performance indicators for lean: Literature review and recommendations. Int J Mod Stud Mech Eng, 5(1), 27–36. http://dx.doi.org/10.20431/2454-9711.0501002
- Venkat, K., & Wakeland, W. W. (2006). Using simulation to understand and optimize a lean service Process. Simulation Series, 38(2), 242.
- Womack, J. P., & Jones, D. T. (1996). Beyond Toyota: How to root out waste and pursue perfection. Harvard Business Review, 74(5), 140–172. https://hbsp.harvard.edu/product/96511-PDF-ENG
- Yeshitila, D., Kitaw, D., & Jilcha, K. (2021). Applying lean thinking to improve operational safety in oil and gas industry. Open Journal of Safety Science and Technology, 11(3), 120–141. https://doi.org/10.4236/ojsst.2021.113009
- Zaini, Z., & Saad, A. (2019). Business process reengineering as the current best methodology for improving the business process. Journal of ICT in Education, 6, 66–85. https://doi.org/10.37134/jictie.vol6.7.2019
- Zuhdi, M. (2012). Strategic management in the telecom industry to create competitive advantage. Universidade de Aveiro (Portugal), ProQuest LLC. https://www.proquest.com/docview/1894043283?pq-origsite=gscholar&fromopenview=true