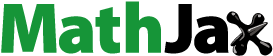
Abstract
Micronized methane fermentation residue sludge can be used as a liquid fertilizer because the micronized solid particles can be directly sprayed. Thus, the objective of this study was to clarify the effect of the micronization method on the particle-size distribution and eluted phosphate-ion concentration of sludge micronized by ultrasonication or ball milling. Although the average particle size in the sludge micronized by ball milling was ~15 µm smaller than that micronized by ultrasonication, many finer particles (<10 µm) were observed in the ultrasonication-micronized sludge. Compared with untreated sludge, the concentration of the eluted phosphate ions of ultrasonication-micronized sludge was almost 15% higher, whereas that of the ball-milled sludge changed insignificantly. These results indicate that the particle sizes in the ball-milled and ultrasonication-micronized sludge were different, resulting in different phosphate ion elution behavior. Thus, the particle size and phosphate ion concentration can be controlled by changing and/or combining micronization techniques and optimizing their operating conditions.
1. Introduction
A large amount of organic waste is generated every year, including excreta from humans and livestock, and food from households and food-processing plants. For example, 1.3 billion metric tons of food waste is generated annually, which corresponds to almost one-third of the food produced globally (Huang et al., Citation2020). The continual increase in organic waste is a global problem (Patel et al., Citation2021). In some developing countries, organic wastes that are not treated appropriately are becoming a crucial public-health problem. The generated organic waste is normally incinerated and then landfilled, but this generates carbon-dioxide emissions. Furthermore, it is challenging to secure new landfill sites to dispose of the increasing amounts of future organic waste.
Reducing carbon dioxide emissions is desirable to mitigate their serious effects on the environment, such as global warming. From the above viewpoints, it is crucial to establish a method to use large amounts of organic waste instead of disposing of it.
One promising method to use organic waste is the methane fermentation process, in which anaerobic microorganisms decompose the organic waste and convert it into methane gas (Seghezzo et al., Citation1998); the residue obtained after recovering methane gas is referred to as methane fermentation residue sludge. Although methane fermentation uses some of the organic waste as a fuel resource, its ratio to the organic waste is still low, resulting in a large amount of remaining sludge. In addition, only 3% of methane fermentation sludge is used as a fertilizer; and the vast majority is incinerated or landfilled (R1 Report Citation2020). Although the liquids and solids in the sludge can be used as a liquid fertilizer and compost, respectively, the solid–liquid separation process is expensive (Siddique et al., Citation2020).
Various attempts have been made to reduce the sludge volume to be landfilled. Gorazda et al. (Citation2017) used the burned ash of sludge as a fertilizer; however, the applied method is time-consuming and expensive. Q Wang et al. (Citation2019) also attempted to use the burned ash of sludge as an adsorbent for heavy metal ions in polluted water; however, the adsorbed amount of heavy metal ions depends on the composition of the coexisting ions. Although Das et al. (Citation2020) extracted oil from the sludge by hydrothermal liquefaction treatment, the process is complicated and costly. Mojapelo et al. (Citation2021) used sludge as a raw material to fabricate lightweight concrete, replacing 7.5% of the sand in the concrete. Zat et al. (Citation2021) reutilized sludge as a raw material to produce eco-friendly bricks. However, up to 15 mass% reduction of the water content is necessary, implying an additional process for water reduction.
In our previous study, we developed a novel liquid fertilizer by micronizing the methane fermentation residue sludge, which can be directly sprayed by a boom sprayer (Mori et al., Citation2022). In this process, the solids in the sludge are micronized below 100 µm, corresponding to the nozzle diameter of a typical boom sprayer. Thus, the process enables the use of all of the methane fermentation residue sludge without any solid–liquid separation process. However, in our previous study, only ball milling was investigated for micronization of the sludge, although other possible micronization methods exist, such as ultrasonication.
Ultrasonication has been extensively investigated for the dispersion and micronization of the particles in a slurry. Thus, the aim of the present study was to examine the possibility of using ultrasonication to micronize methane fermentation sludge and compare the result to that of the sludge micronized by ball milling in our previous study.
The efficiency of the methane fermentation process can be improved by applying ultrasonication to soft matter such as organic solids in the sludge. Several studies have reported that ultrasonication of organic waste increases the amount of generated methane gas and its recovery ratio (Q-H Wang et al., Citation1995; Pilli et al., Citation2011; Rasapoor et al. Citation2019and Karouach et al. Citation2020). Although studies have reported micronization of organic waste before methane fermentation, the micronization of methane fermentation residue sludge has not been investigated to date.
When micronizing organic waste before methane fermentation, the phosphate ion concentration reportedly increases as the solid particle size decreases (Agyeman & Tao, Citation2014; Izumi et al., Citation2010). Our previous study revealed that the phosphate ion concentration increased more than one month after micronizing the methane fermentation sludge by ball milling (Mori et al., Citation2022). Because phosphorous is one of the three major nutrients for plants, its concentration should be properly controlled in a fertilizer. Therefore, in this study, we investigated the effect of ultrasonication on the particle size distribution of the solid and the phosphate ion concentration in the methane fermentation residue sludge. Through comparison of ultrasonication and ball milling as micronization methods for methane fermentation residue sludge, we propose a strategy for controlling the particle size and eluted phosphate-ion concentration in the micronized sludge.
2. Materials and methods
2.1. Materials
The methane fermentation residue sludge used in this study was similar to that in our previous study (Mori et al., Citation2022). The sludge was sampled from a methane fermentation facility in Maniwa City, Japan, where the raw material for methane fermentation was obtained from a mixture of food waste, livestock excretion, and septic tank sludge. The mixture was anaerobically digested at 30–37 °C; the hydrological residence time was 35 d. The sludge composition is shown in Table S1.
2.2. Micronization of methane fermentation residue sludge
The prepared sludge (200 g) was poured into a 300-mL beaker and ultrasonicated using an ultrasonic homogenizer (US-150 T, Nippon Seiki Co., Ltd.). The ultrasonication time was changed from 0.5 to 120 min, and the process was conducted under cooling using an ice bath to prevent any increase in the sludge temperature. The frequency and power of the ultrasonication system were 20 kHz and 150 W, respectively.
For comparison, pulverization of the sludge by ball milling was conducted. The sludge (200 g) and zirconia balls (1200 g) were placed in a polyethylene pot and then rotated in a ball mill (LB-140, Teraoka Co., Ltd.). This weight ratio of the sludge to the zirconia balls corresponds to a 1:1 volume ratio, which was the condition that gave the highest pulverization efficiency of the sludge in our previous study (Mori et al., Citation2022). The polyethylene pot used for ball milling had a diameter of 12 cm and height of 20 cm. The rotation speed was 112 rpm, and the ball milling time was 0.5, 1, or 2 h. The diameter of the zirconia balls was 1, 3, or 5 mm.
2.3. Characterization of micronized sludge
After micronization, the particle size distribution of the sludge was measured using the laser diffraction method (SALD-2300, Shimadzu) before and after micronization. The sampled sludge was diluted with water by a factor of approximately 500 for particle size measurements. The refractive index of the sludge was unknown because the sludge was mixed. Hence, the refractive index of starch (1.50), a similar component, was used to calculate the particle size distribution of the sludge.
The phosphate ion concentration and total phosphorus amount in the sludge were measured using the molybdenum blue method (Matsumoto & Sakai). The detailed procedure was as described in the standard JIS K Citation0120:2016 (2019).
The micronized sludge was directly observed using a digital microscope (VHX-7000, Keyence Corporation). The base glass plates with spacer particles (Micropearl GS-L200, nominal particle size: 200.0 ± 10.0 µm, Sekisui Chemical) on both sides were prepared in advance. The spacer particles were fixed onto the commercial glass slides using a water glass. Before observing the slurry, the single layer of the spacer particles was confirmed by optical microscopy. A small amount of the prepared slurry was dropped onto the base glass plate and covered with another glass slide to prepare the sample for observation. The sample was subsequently placed under a digital microscope and observed in the transmissive mode.
After centrifuging the sludge, the liquid and solids of the sludge samples were dropped on the glass slides and completely dried. Subsequently, the dried samples were observed with the digital microscope and analyzed by laser-induced breakdown spectroscopy (EA-300, Keyence Corp.) to detect phosphorus.
3. Results
3.1. Particle size of micronized sludge samples
Figure shows the effect of ultrasonication time on the particle size distribution of the solids in the sludge. The particle size distribution shifted to the smaller side as the ultrasonication time increased. Particularly, when the ultrasonication time was 30 min or longer, smaller particles below several tens of micrometers were generated. This result indicates that particles with a size of ~50 µm can be easily and selectively micronized by ultrasonication. However, the ratio of the larger particles over 100 µm also increased, resulting in a wider particle size distribution. Here, we observed some particle aggregation after a relatively long ultrasonication time, as noted in a previous report (Pourmohammadi & Abedi, Citation2020).
Figure illustrates the effect of ball milling time on the particle size distribution of the sludge. As mentioned in our previous study (Mori et al., Citation2022), the particle size of the sludge decreased with an increase in the ball milling time. In contrast to ultrasonication, all values of D10, D50, and D90 decreased with increasing ball milling time, indicating a decrease in the overall particle size distribution. Furthermore, smaller and larger particles were observed when the ball milling time was more than 30 min. Moreover, the particle size distribution of the ball-milled sludge did not demonstrate any significant changes when the ball milling time was 30 min or longer.
3.2. Phosphate ion concentration of micronized sludge samples
Figure ) illustrates the phosphate ion concentration of the sludge samples micronized by ultrasonication and ball milling. The phosphate ion concentration was measured immediately after ultrasonication and ball milling.
Considering the initial phosphate concentration fluctuation in the sludge due to the difference in the holding time after sampling, the increasing rate of the phosphate ion concentration, X (-) was defined as follows:
where C(t) is the phosphate ion concentration of the treated sludge at an arbitrary time (mol/L), C0 is the phosphate ion concentration of the untreated sludge (mol/L), and CT is the phosphate ion concentration of the sludge in which all solids were completely dissolved (mol/L).
Figure ) shows the increasing rate of phosphate ion concentration in the ultrasonicated and ball-milled sludge samples. The phosphate ion concentration increased until 30 min of ultrasonication and remained constant even when the ultrasonication time exceeded 30 min. In contrast, no significant changes were observed in the phosphate ion concentration of the ball-milled sludge regardless of the ball milling time. These results suggest that the increase in the phosphate-ion concentration should be affected by the difference in the micronization mechanism between ball milling and ultrasonication.
For using the micronized sludge as a liquid fertilizer, the changes in the phosphate ion concentration over time were examined by changing the holding time of the micronized sludge (Figure ). The change in the phosphate-ion concentration as its increasing rate, X, was demonstrated. Figure S1 illustrates the change in the phosphate-ion concentration with time in the raw sludge placed in a tank. The phosphate ion concentration of the untreated sludge remained constant with time. As shown in Figure , no significant changes were observed in the phosphate-ion concentration of sludge samples micronized by ultrasonication and ball milling. These results indicate that the elution rate of phosphate ions from the sludge particle should be sufficiently high compared to the day-unit keeping time.
4. Discussion
In this section, the differences in the micronization mechanism between ultrasonication and ball milling are discussed. Initially, we focus on the changes in the particle size distribution of the sludge micronized by ultrasonication and ball milling. Figure shows the volume ratio of the particles below 100 µm to the volume of all particles in the micronized sludge.
Figure 5. Effect of the processing time on the phosphate-ion concentration ratio in the sludge samples micronized by (a) ultrasonication and (b) ball milling.
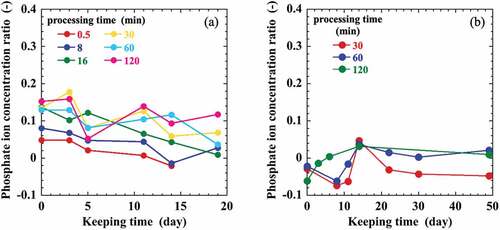
The value of 100 µm corresponds to the nozzle diameter of a typical boom sprayer, indicating that the particles over 100 µm may get stuck in the nozzle. The volume ratio of the particles below 100 µm increased with an increase in ball milling time, suggesting that the coarse particles in the raw sludge were micronized by ball milling. In contrast, the volume ratio of the particles below 100 µm increased with ultrasonication time until 8 min and decreased when the time exceeded 8 min. This result indicates particle aggregation with micronization when the ultrasonication time exceeds 8 min. It was reported that ultrasonication can micronize or disperse and aggregate the particles in slurries (Kenmochi et al., Citation1999).
Subsequently, we compared the particle size distributions obtained when the sludge samples were micronized by ball milling and ultrasonication for 30 min (Figure S2). For ball milling, the shape of the cumulative distribution was similar to that of the raw sludge, which shifted to the smaller side, as shown in Figure . This result indicates that particles in all size ranges were micronized by ball milling. Conversely, for ultrasonication, the particles of approximately several tens of micrometers were micronized, generating smaller particles below 10 µm; however, the larger particles of approximately 100 µm remained in the ultrasonicated sludge, as shown in Figure . These results confirm that the size of the particles micronized by ball milling and ultrasonication is different, with finer particles generated for the ultrasonicated sludge. However, the volume ratio of the particles below 100 µm to that of all particles for the ball-milled sludge was larger than that for the ultrasonicated sludge.
Figure shows optical images of the raw, ultrasonicated, and ball-milled sludge samples. Several large particles, which were not observed in the ultrasonicated and ball-milled sludge samples, such as fibrous material, were observed in the raw sludge. Comparing the ultrasonicated and the ball-milled sludge samples shows that although fine shapeless particles and comparatively large, black-colored particles were present in the ultrasonicated sludge, few particles were observed in the ball-milled sludge. These results support the previous discussion on the particle size distribution in the sludge.
Figure 6. Effect of processing time on the ratio of particles below 100 µm in the micronized sludge samples.
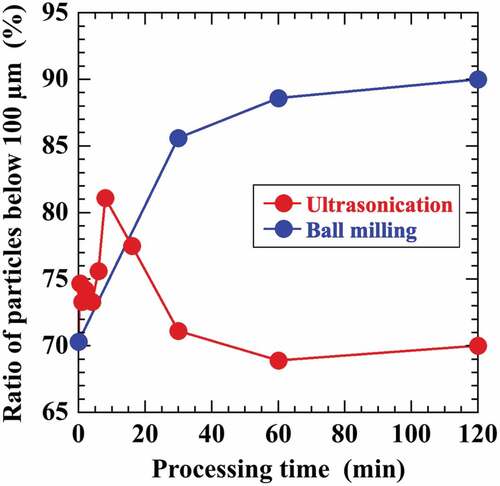
Figure illustrates additional results for ball milling, in which the particle size distribution was measured when changing the media ball diameter.
Generally, the particle size in ball-milled sludge decreases with the decrease in the media ball diameter (Kondo et al., Citation1993). In the present study, although the obtained particle size for ball milling decreased with a decrease in the media ball diameter, its effect on the particle size distribution was limited. This phenomenon was observed because the smaller particles in the sludge were not sandwiched by the media balls owing to their smaller inertia (Kushimoto et al. Citation2019). In particular, although the smaller particles in the sludge could be micronized at a certain level, their inertia decreased. Hence, the particles moved away before being sandwiched by the liquid flow generated by the approaching media balls. In contrast, a strong shear force was generated by ultrasonication-induced cavitation. Thus, finer particles were generated when applying ultrasonication to the sludge.
The change in the phosphate ion concentration of the sludge can be explained by combining the change in the particle size distribution. The above-mentioned results imply that the phosphate ion concentration increased only for the ultrasonicated sample, in which the finer particles were generated, and no changes were observed in the phosphate ion concentration of the ball-milled sludge. Therefore, it is assumed that the particles micronized by ultrasonication originally included more phosphorous. The composition of the solid and liquid in the sludge before and after micronization was examined by ultrasonication and ball milling to verify the assumption. Optical images of the elemental analysis by laser-induced breakdown spectroscopy are shown in Figure .
We investigated 25 different points in each image to determine the presence of phosphorus. The liquid in the sludge was completely dried for further examination, and the obtained solid was investigated. Phosphorus was detected for all liquids across the raw, ultrasonicated, and ball-milled sludge samples. However, phosphorous was detected only for the solids of the ultrasonicated sludge as shown in . Thus, an increase in the phosphate ion concentration was observed only in the ultrasonicated sample owing to the particle-size differences in the sludge samples micronized by ultrasonication and ball milling. In particular, more phosphorus can be included in the particles of approximately several tens of micrometers, and only ultrasonication can micronize the particles, increasing the phosphate ion concentration in the sludge.
Thus, by combining ball milling and ultrasonication, the particle size and phosphate ion concentration of the sludge can be independently controlled to a certain extent to control the particle size and phosphate ion concentration, respectively.
Furthermore, compared to ultrasonication ball milling can suppress the odor generated by the sludge. This result was observed because the sludge could contact air more effectively for ball milling, possibly causing the anaerobic methane zymogenic microorganisms to die, preventing further fermentation. Considering a large-scale treatment for real applications, suppressing odor generation is important; thus, ball milling is suitable.
Considering the feature of ball milling and ultrasonication of the methane fermentation sludge, a possible process for producing liquid fertilizer is proposed. First, the methane fermentation sludge is micronized by ball milling, and then further micronized by ultrasonication, obtaining a liquid fertilizer with a solid particle size below 100 µm, which corresponds to the nozzle diameter of a boom sprayer, and a high phosphate-ion concentration. Careful process design, including the optimization of the ultrasonication and ball milling conditions, and the appropriate combination of these micronization techniques, is necessary for practical applications.
5. Conclusions
In continuation of our previous study, the use of the methane fermentation residue sludge as a novel liquid fertilizer by micronization was investigated in this study. We compared the particle size distribution and phosphate ion concentration in the sludge samples micronized by ultrasonication and ball milling. The different micronization effects of ball milling and ultrasonication on the sludge were identified by measuring the particle size distribution of the solid in the micronized sludge, and also by direct observation and elementary analysis of the sludge. Based on the overall experimental results and discussion, the following conclusions are drawn:
Ultrasonication can preferentially micronize the particles of approximately several tens of micrometers in the methane fermentation residue sludge, whereas ball milling can only micronize the particles with a wide size range in the sludge.
The phosphate ion concentration in the ultrasonicated sludge increases, whereas no significant changes occur in the ball-milled sludge. The phosphorus ion concentration increases with an increase in ultrasonication time until 30 min of ultrasonication.
The phosphate ion concentration of the ultrasonicated sludge increases because the particles of approximately several tens of micrometers contain more phosphorus, which can be micronized by ultrasonication, enhancing the elution of phosphate ions from the sludge particles.
The particle size distributions and phosphate ion concentrations in the ultrasonicated and ball-milled sludge samples are different. In addition, only ball milling can suppress the odor generated by the sludge. Thus, the combination of ball milling and ultrasonication can control the particle size and phosphate-ion concentration separately, and avoid odor generation, which is especially important for large-scale sludge treatment. To promote practical application of these methods, further investigation is required to optimize the process parameters of ultrasonication and ball milling to increase the process efficiency and reduce the cost.
Highlights
Ultrasonication preferentially micronizes sludge particles of several ten microns.
Eluted phosphate ion concentration in the sludge increases by ultrasonication.
Ultrasonication for 30 min maximizes the phosphate ion concentration in the sludge.
Acknowledgements
This study was partially supported by the Grant-in-Aid for Scientific Research (B) [22H00575, 18KT0044] from the Japan Society for the Promotion of Science. The authors are grateful to Maniwa Rikyo for providing the sludge. The authors also thank Mr. Kenta Kitamura for his assistance and useful discussion on particle characterization in the sludge.
Disclosure statement
No potential conflict of interest was reported by the author(s).
Data availability statement
The data that support the findings of this study are available from the corresponding author upon reasonable request.
Additional information
Funding
References
- Agyeman, F. O., & Tao, W. (2014). Anaerobic co-digestion of food waste and dairy manure: Effects of food waste particle size and organic loading rate. Journal of Environmental Management, 133, 268–13. https://doi.org/10.1016/j.jenvman.2013.12.016
- Das, P., Khan, S., AbdulQuadir, M., Thaher, M., Waqas, M., Easa, A., Attia, E. S. M., & Al-Jabri, H. (2020). Energy recovery and nutrients recycling from municipal sewage sludge. Science of the Total Environment, 715(136775), 136775. https://doi.org/10.1016/j.scitotenv.2020.136775
- Gorazda, K., Tarko, B., Wzorek, Z., Kominka, H., Nowak, A. K., Kulczycka, J., Heneclik, A., & Smol, M. (2017). Fertilisers production from ashes after sewage sludge combustion – A strategy towards sustainable development. Environmental Research, 154, 171–180. https://doi.org/10.1016/j.envres.2017.01.002
- Huang, C. H., Liu, S. M., & Hsu, N. Y. (2020). Understanding global food surplus and food waste to tackle economic and environmental sustainability. Sustainability, 12(7), 2892. https://doi.org/10.3390/su12072892
- Izumi, K., Okishio, Y., Nagao, N., Niwa, C., Yamamoto, S., & Toda, T. (2010). Effects of particle size on anaerobic digestion of food waste. International Biodeterioration & Biodegradation, 64(7), 601–608. https://doi.org/10.1016/j.ibiod.2010.06.013
- JIS K 0120:2016. (2019). Kojyo Haisui Shiken Houhou. Japanese Standards Association Group.
- Karouach, F., Bakraoui, M., Gnaoui, Y. E., Lahboubi, N., & Bari, H. E. (2020). Effect of combined mechanical–ultrasonic pretreatment on mesophilic anaerobic digestion of household organic waste fraction in Morocco. Energy Reports, 6, 310–314.
- Kenmochi, T., Shirai, K., & Yoshie, M. (1999). Development of the turbid water agglomeration and sedimentation technology using ultrasonic; Port and Airport Research Institute Material No. 939. Japan: Port and Harbour Research Institute Ministry of Transport. p. 1–10.
- Kondo, Y., Hashizuka, Y., Nakahara, M., Yokota, K., & Ishizaki, K. (1993). Influence of combination of ball diameters and rotation speed on grinding performance of alumina by ball milling. Journal of the Ceramic Society of Japan, 101(1175), 819–823. https://doi.org/10.2109/jcersj.101.819
- Kushimoto, K., Ishihara, S., & Kano, J. (2019). Development of ADEM-CFD model for analyzing dynamic and breakage behavior of aggregates in wet ball milling. Advanced Powder Technology : The International Journal of the Society of Powder Technology, Japan, 30, 1131–1140.
- Matsumoto, K., & Sakai, K. Formation of molybdenum blues and its application to determination of phosphorus. Kagaku to Kyoiku, 35, 420–423.
- Mojapelo, K. S., Kupolati, W. K., Ndambuki, J. M., Sadiku, E. R., & Ibrahim, I. D. (2021). Utilization of wastewater sludge for lightweight concrete and the use of wastewater as curing medium. Case Studies in Construction Materials, 15, e00667. https://doi.org/10.1016/j.cscm.2021.e00667
- Mori, T., Murakami, K., & Yabe, M. (2022). Investigation of the direct utilization possibility of methane fermentation residue sludge as liquid fertilizer by micronization. Environmental Technology, 1–11. https://doi.org/10.1080/09593330.2021.2020908
- Patel, P., Modi, A., Minipara, D., & Kumar, A. (2021). Microbial biosurfactants in management of organic waste. Sustainable Environmental Clean-up Green Remediation, 211–230. https://doi.org/10.1016/B978-0-12-823828-8.00010-4
- Pilli, S., Bhunia, P., Yan, S., LeBlanc, R. J., Tyagi, R. D., & Surampalli, R. Y. (2011). Ultrasonic pretreatment of sludge: A review. Ultrasonics Sonochemistry, 18(1), 1–18. https://doi.org/10.1016/j.ultsonch.2010.02.014
- Pourmohammadi, K., & Abedi, E. (2020). The effect of pre and post-ultrasonication on the aggregation structure and physicochemical characteristics of tapioca starch containing sucrose, isomalt and maltodextrin. International Journal of Biological Macromolecules, 163, 485–496. https://doi.org/10.1016/j.ijbiomac.2020.06.205
- R1 Report of Survey on Actual Situation about Recycling of Waste 2020. Ministry of the Environment.
- Rasapoor, M., Adl, M., Baroutian, S., Iranshahi, Z., & Pazouki, M. (2019). Energy performance evaluation of ultrasonic pretreatment of organic solid waste in a pilot-scale digester. Ultrasonics - Sonochemistry, 51, 517–525.
- Seghezzo, L., Zeeman, G., Van Lier, J. B., Hamelers, H. V. M., & Lettinga, G. (1998). A review: The anaerobic treatment of sewage in UASB and EGSB reactors. Bioresource Technology, 65(3), 175–190. https://doi.org/10.1016/s0960-8524(98)00046-7
- Siddique, M. N. I., Khalid, Z. B., & Ibrahim, M. Z. B. (2020). Effect of additional nutrients on bio-methane production from anaerobic digestion of farming waste: Feasibility & fertilizer recovery. Journal of Environmental Chemical Engineering, 8(1), 103569. https://doi.org/10.1016/j.jece.2019.103569
- Wang, Q.-H., Kakimoto, K., Ogawa, H. I., Fujisaki, K., & Kato, Y. (1995). Effect of pretreatment on the solubilization and anaerobic digestion of waste activated sludge. Journal of the Japan Society of Waste Management Experts, 6(4), 157–164. https://doi.org/10.3985/jswme.6.157
- Wang, Q., Li, J.-S., & Poon, C. S. (2019). Recycling of incinerated sewage sludge ash as an adsorbent for heavy metals removal from aqueous solutions. Journal of Environmental Management, 247, 509–517. https://doi.org/10.1016/j.jenvman.2019.06.115
- Zat, T., Bandieira, M., Shattler, N., Segadase, A. M., Cruz, R. C. D., Mohamad, G., & Rodriguez, E. D. (2021). Potential re-use of sewage sludge as a raw material in the production of eco-friendly bricks. Journal of Environmental Management, 297, 113238. https://doi.org/10.1016/j.jenvman.2021.113238